凸轮升程数据
实验分析内燃机凸轮机构最大气门升程的影响

内燃机凸轮机构最大气门升程影响的实验分析Suat Saridemir,Hamit SaruhanDepartment of Manufacturing Engineering, Faculty of Technology, University of Düzce, Düzce, TurkeyDepartment of Mechanical Engineering, Faculty of Engineering, University of Düzce, Düzce, Turkey摘要:凸轮机构气门行程的设计对改善内燃及的动态性能是非常重要的,高速发动机不正常的振动导致随动件跳动,碰撞阀门表面和中心,进而导致凸轮系统的碰撞。
碰撞的程度取决于阀升程值和阀门关闭速度,凸轮和随动件碰撞时会引入大的力和压力。
由于不正常的振动,这可能会导致系统的早期失效。
本实验使用时域和频域分析方法研究,主要目的是研究和分析不同气门升程值和运转速度下凸轮系统的动态特性,两种最大的气门升程值为8和10毫米分别进行了运转速度为450,930,1440,1950和2430rpm条件下的实验。
从实验结果看,振幅随运转速度的增加而增加,统计分析获得的数据显示,10mm的气门升程比8mm气门升程产生更多的能量。
关键词:凸轮机构;气门行程的动态特性;振动分析;内燃机1.引言当今,越来越多的研究者热衷于提高内燃机(ICE))的性能,减少噪音及振动。
由于内燃机由许多承受大的负载的组件构成,内燃机的动态特性十分复杂[1]。
凸轮系统的运转是内燃机震动的一个震动源,凸轮从动件带动发动机气门运动,凸轮轴的旋转驱动随动件运动,定位弹簧使阀门始终压在凸轮表面。
由于弹簧力的作用,运转过程中系统会承受大的负载力。
阀弹簧的性能在凸轮从动装置的动态特性中起着重要作用,尤其是在高速运转的情况下。
因此,凸轮从动系统的动态特性主要影响因素是阀弹簧的性能。
LJ750发动机配气凸轮设计计算书

LJ750发动机配气凸轮型线设计计算书配气机构的设计思想:配气机构是发动机的重要组成部分,一台发动机的经济性能是否优越,工作是否可靠,噪声与振动能否控制在较低的限度,常常与其配其机构的设计是否合理密切关系。
特别对于高速大功率发动机,因对其较高性能指标的设计要求,配气机构的设计及其零部件的设计和制造就更加重要和严格。
配气机构的设计涉及到如下诸多问题:1.如果根据具体的机型的要求选取合理的函数凸轮型线并进行有关特性参数的计算和分析;2.配气机构方案选择及其气门的结构布置;3.对于高速配气机构来说,必须进行配气机构的动力学计算;4.在设计过程中,需要考虑很多重要的因素,如配气相位,平稳性(包括气门速度,加速度,脉冲数值大小及有无飞脱,落座反跳等),充气性能,润滑性能,凸轮与挺拄之间的接触应力等问题;因此,进行配气机构的设计往往需要很大的工作量,特别是为了获得一个最优的设计方案。
为了简化工作量,在目前国内外的设计中,常常采用参考某些成功机型的方法,来获得设计一台新发动机所需要的配气机构。
为此,在本设计了,参考了CBR900发动机的配气机构,通过对该机型配气机构的特性进行分析,并对提出的几种方案的凸轮型线进行的对比,最终获得了LJ750发动机配气机构的有关数据。
对比的结果最终还是采用了和CBR900发动机相同的配气结构,因此涉及到配气结构的许多动力学计算在这里都略去了。
本章主要介绍了多项动力凸轮设计的基本原理及其准则,并对CBR900发动机的凸轮型线进行了细致的分析和研究,在此基础上提出了LJ750发动机的配气机构。
一、凸轮型线类型的选择配气机构是发动机的一个重要系统,其设计好坏对发动机的性能、可靠性和寿命有极大的影响。
其中凸轮型线设计是配气机构设计中最为关键的部分,在确定了系统参数后,重要的问题是根据发动机的性能和用途,正确选择凸轮型线类型及凸轮参数。
凸轮型线有多种,如复合正弦,复合摆线,低次方,高次方,多项动力,谐波凸轮等。
16V240ZJB型柴油机标定功率为2650KW

16V240ZJB型柴油机,当第一缸活塞位于进气冲程42°20′是,凸轮的升程为0.38mm。
16V240ZJB型柴油机标定功率为2650KW16V240ZJB型柴油机的燃油系统设有燃油精滤器、低压输油管、喷油泵、高压输油管、喷油器、限压阀及喷油器和喷油泵的回油管路。
16V240ZJC型柴油机标定功率为2940KW1kg柴油机在完全燃烧时放出的热量,称为柴油机的热值。
A.安装活塞环时,两环切口彼此应错开大于90°。
B.表示研磨粗细的参数叫粒度。
补偿针阀开度过大,会引起柴油机悠车。
C.测量柴油机爆发压力时,各缸供油刻线不得超过0.5刻线。
柴油机才单位时间内所做的指示功称为指示功率。
柴油机的工况是用柴油机的功率和工作参数来表示的。
柴油机的机油压力偏低时,有时虽然与卸载继电器的动作值仍有段距离,不会使柴油机发生卸载,但却会危及增压器轴承的工作可靠性。
柴油机的进排气过程的控制机构是配气机构。
柴油机的冷却系统由水泵、节温器、冷却管系及气缸体、曲轴箱、气缸盖内的水腔等组成。
柴油机的性能指针和工作参数随运转工况而变化的函数关系,称为柴油机的特性。
柴油机的主轴承用来支撑曲轴。
柴油机调速试验,升降转速时,联合调节器波动不得超过3次。
柴油机对配气机构的要求是严格按照规定的曲轴转角位置,正确及时地开、闭各缸的进、排气门。
柴油机进行启动试验时,油水温度需高于20°C方可启动柴油机。
柴油机冒蓝烟的同时,也散发出臭味。
柴油机冒蓝烟的主要原因是机油进入燃烧室,随废气排出而造成的。
柴油机每千瓦小时所消耗的燃油的重量称为燃油消耗率。
柴油机喷油泵又称高压油泵。
柴油机运转时排气冒蓝烟,说明机油进入燃烧室,一部分机油参与燃烧形成积炭,另一部分没有燃烧的机油以微粒状态排入大气,形成蓝烟。
柴油机正常运转时,排出的废气以无色透明、浅灰色淡蓝色为好。
柴油机主机油泵出口管路的振动,主要是由于减压阀的开启压力及开启压力及开启通过油量的能力与主机油泵口出油的压力不匹配造成的。
发动机凸轮轴和挺柱磨损问题分析与解决
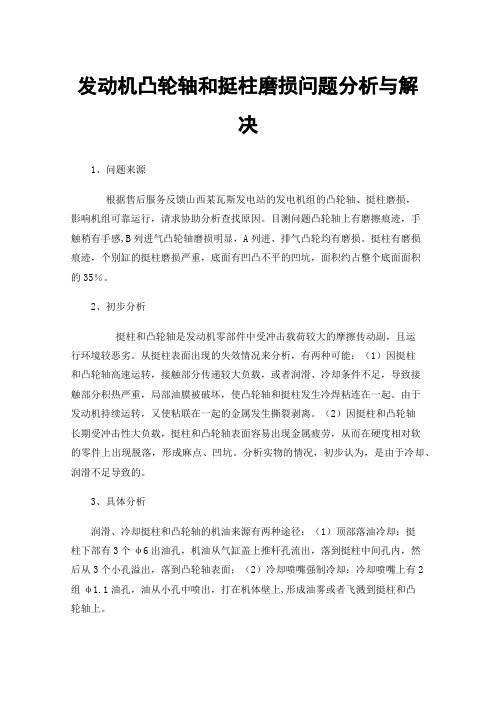
发动机凸轮轴和挺柱磨损问题分析与解决1、问题来源根据售后服务反馈山西某瓦斯发电站的发电机组的凸轮轴、挺柱磨损,影响机组可靠运行,请求协助分析查找原因。
目测问题凸轮轴上有磨擦痕迹,手触稍有手感,B列进气凸轮轴磨损明显,A列进、排气凸轮均有磨损。
挺柱有磨损痕迹,个别缸的挺柱磨损严重,底面有凹凸不平的凹坑,面积约占整个底面面积的35%。
2、初步分析挺柱和凸轮轴是发动机零部件中受冲击载荷较大的摩擦传动副,且运行环境较恶劣。
从挺柱表面出现的失效情况来分析,有两种可能:(1)因挺柱和凸轮轴高速运转,接触部分传递较大负载,或者润滑、冷却条件不足,导致接触部分积热严重,局部油膜被破坏,使凸轮轴和挺柱发生冷焊粘连在一起。
由于发动机持续运转,又使粘联在一起的金属发生撕裂剥离。
(2)因挺柱和凸轮轴长期受冲击性大负载,挺柱和凸轮轴表面容易出现金属疲劳,从而在硬度相对软的零件上出现脱落,形成麻点、凹坑。
分析实物的情况,初步认为,是由于冷却、润滑不足导致的。
3、具体分析润滑、冷却挺柱和凸轮轴的机油来源有两种途径:(1)顶部落油冷却:挺柱下部有3个φ6出油孔,机油从气缸盖上推杆孔流出,落到挺柱中间孔内,然后从3个小孔溢出,落到凸轮轴表面;(2)冷却喷嘴强制冷却:冷却喷嘴上有2组φ1.1油孔,油从小孔中喷出,打在机体壁上,形成油雾或者飞溅到挺柱和凸轮轴上。
3.1顶部落油冷却3.1.1复核问题挺柱用游标卡尺量得挺柱出口孔下部到底面的距离约为13(见图1),从机体图纸上量的:用于挺柱导向的下端面距离凸轮轴41.26(见图2)。
凸轮轴基圆直径φ43.5,凸轮轴最大升程8.12。
43.5/2+8.12+13=42.87>41.26图1所以,在最大升程时,挺柱的出油孔是被机体堵住的,且由于3个出油孔是沿径向均布的,所以,3个出油孔都是被堵住的。
图2查看凸轮轴的升程表,发现角度51°时,升程为6.63231;105°时,升程为6.63231,所以凸轮轴在转动360°中有54°,是没有或者很少的机油,从顶部落下冷却、润滑凸轮轴接触部位。
顶置凸轮配气机构气门升程的精确计算

・文摘・顶置凸轮配气机构气门升程的精确计算苏军申屠淼(江苏理工大学力学系 , 镇江 212013为使发动机布置得更紧凑 , 提高配气机构的刚性与减轻运动件的质量 , 以适应高转速的要求 , 许多现代的四冲程发动机都采用顶置凸轮配气机构 , 其中一些汽车、摩托车发动机的顶置凸轮配气机构的结构形式如图 1所示。
图 1顶置凸轮摇臂机构现对以上典型结构的气门升程的计算方法与公式进行了推演 , 以供应用参考。
假定摇臂为绝对刚体。
(1 将凸轮升程表换算为极坐标升程表 h ( 。
(2 建立 2个坐标系 , 一个为定坐标系 x Oy ; 另一个为随凸轮转动的动坐标系 x Oy (详见图 2 。
两坐标系原点 O 均在凸轮轴心 ; 横坐标 Ox垂直于凸轮轴图 2顶置凸轮配气机构简图线 , 平行于气缸盖底平面 ; 横坐标 Ox 垂直于凸轮轴线 , 并令其通过凸轮升程廓线过渡段的起点 ; 认定摇臂初始位置 , 即 =0°。
此时 Ox 与 Ox 的夹角为 : 0=180-arctg1-x 1-arctg 1R +S 1(1 式中 :x 1和 y 1为摇臂中心 O 1在定坐标系中的坐标 ; L 1为 O 1点至 M 点的距离 ; M 点为摇臂零件图中水平中心线与 OP 0的交点 ; S 1为 OP 0线上 R 3圆弧面至 M 点的弦高 ; R 为凸轮基圆半径。
(3 计算出 R 3圆弧的圆心 P 0在定坐标系 x Oy 中的坐标位置。
x P 0=(R +R 3 ・ cos 0y P 0=(R +R 3 ・ sin 0(2式中 :R 3为摇臂凸轮侧臂圆弧的半径。
当凸轮转过角度时 , 凸轮廓线与摇臂 R 3圆弧面的接触点在 C (x C , y C 点。
在凸轮转动中 , R 3圆弧面上的接触点 C 在 C L 和 C R 之间变动 ; 而 C 点在凸轮廓线上则是在 x Oy 坐标系中逆旋转方向而变动。
令 OC 与 Ox 的夹角为。
机械原理凸轮大作业程序、图与设计说明说
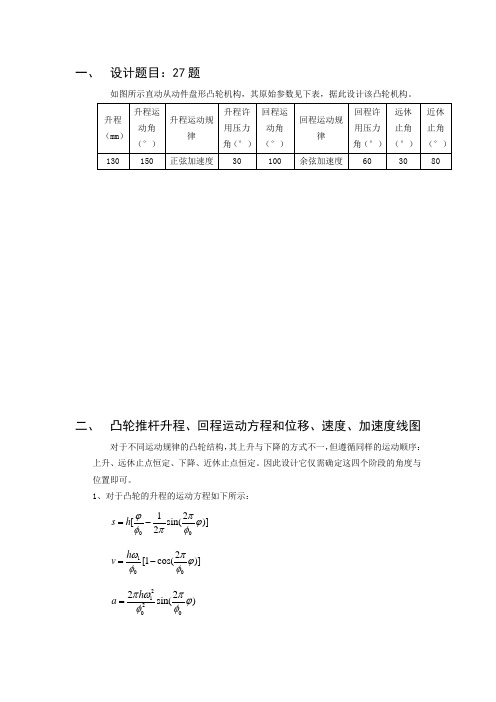
一、 设计题目:27题如图所示直动从动件盘形凸轮机构,其原始参数见下表,据此设计该凸轮机构。
二、 凸轮推杆升程、回程运动方程和位移、速度、加速度线图对于不同运动规律的凸轮结构,其上升与下降的方式不一,但遵循同样的运动顺序:上升、远休止点恒定、下降、近休止点恒定。
因此设计它仅需确定这四个阶段的角度与位置即可。
1、对于凸轮的升程的运动方程如下所示:12[sin()]2s h ϕπϕφπφ=-12[1cos()]h v ωπϕφφ=- 21222sin()h a πωπϕφφ=升程 (mm ) 升程运动角(°) 升程运动规律 升程许用压力角(°) 回程运动角(°) 回程运动规律 回程许用压力角(°) 远休止角(°) 近休止角(°) 130 150正弦加速度30100余弦加速度6030802、对于凸轮的回程运动方程如下所示:01{1cos[()]}2s h s πϕφφφ=+-+1011sin[()]s h v πωπϕφφφφ=--+2210121cos[()]2s h a πωπϕφφφφ=--+3、推杆位移线图(横坐标凸轮转过角度,单位:°;纵坐标推杆位移,单位:mm )4、推杆速度线图(横坐标图轮转过角度,单位°;纵坐标为推杆速度,单位mm/s)5、推杆加速度线图(横坐标为凸轮转过角度,单位:°;纵坐标为推杆加速度,单位:mm/s^2)三、 凸轮机构的ds sd ϕ-线图,凸轮的基圆半径和偏距1、根据ds s d ϕ-线图得无偏心距时最小基圆半径0116r =。
具体作图过程见下页。
2、查阅相关文献,知直动从动件盘形凸轮最小基圆半径求解公式为:00022(arctan)tan tan h r πππφαφα=-经计算得:0116.7835r =四、 滚子半径的确定及凸轮理论廓线和实际廓线的绘制查阅有关文献,得知在有偏置机构的凸轮最小基圆半径求解公式为 最小基圆半径:02cos p r r α=其对应的偏心距:0tan 2r e α=计算得:67.55p r =;33.78e =。
solidworks圆柱凸轮参数

solidworks圆柱凸轮参数-概述说明以及解释1.引言1.1 概述概述是文章引言部分的一部分,主要是对文章所研究的主题进行简要介绍和概括。
对于本篇文章《SolidWorks圆柱凸轮参数》来说,概述部分应该包括以下内容:圆柱凸轮是机械设计领域中常见的一种重要机械元件,广泛应用于各种机械传动系统中。
它通过将旋转运动转变为直线运动,实现了机械设备的各种运动要求。
圆柱凸轮的参数设计与优化是凸轮机构设计中的重点问题之一,直接关系到机械系统的性能和效率。
本文将围绕圆柱凸轮的参数进行研究,通过对凸轮形状、凸轮曲线、凸轮升程和凸轮转动速度等参数进行分析和探讨,旨在深入了解这些参数对凸轮机构运动性能的影响,并提出设计与优化方案。
文章将首先介绍圆柱凸轮的定义和作用,阐述其在机械传动中的重要地位和作用。
然后,将详细介绍圆柱凸轮的常见参数,包括凸轮形状的描述、凸轮曲线的建立方法、凸轮升程和凸轮转动速度等。
在此基础上,我们将进一步讨论圆柱凸轮的设计与优化问题,探索如何通过参数调整和凸轮优化技术提升凸轮机构的性能。
接下来,我们将介绍SolidWorks软件在圆柱凸轮设计中的应用,包括凸轮的建立、参数化设计和仿真分析等方面。
文章的结论部分将总结圆柱凸轮参数的重要性,并分析这些参数对系统性能的影响。
同时,也将探讨圆柱凸轮参数的优化方向和在实际工程中的应用前景。
通过本文的研究,将为工程师们提供更加全面准确的圆柱凸轮参数设计指导,帮助他们设计出更高效、稳定的凸轮机构,提升机械设备的性能和可靠性。
同时,也将为相关领域的学术研究提供理论基础和实践参考。
1.2文章结构文章结构部分的内容可以参考以下内容:文章结构部分旨在介绍本文的组织结构,让读者可以清晰地了解各个章节的内容和目的。
本文将按照以下大纲逐步展开对圆柱凸轮参数的探讨。
第一章中的引言部分将在1.1小节首先对圆柱凸轮进行概述,介绍其定义和作用。
随后,1.2小节将详细说明文章的结构和各章节的内容,为读者提供整体的框架。
发动机单程凸轮升程误差的评定方法

第 17 卷 标 准 化 报 道 Vol. 17 NO. 1 1996 第 1期 REPOR TING OF STANDARDIZATION
机械标准化
发动机单程凸轮升程误差的评定方法
刘兴富
(陕西省柴油机厂 )
摘要 针对发动机凸轮各项程公差具有形状公差和尺寸公差的双重属性 ,以及升程公差有分段要求的特
以上是解析校正方法 , 下面再介绍一种 简单、 直观的图解校正方法 (图 4)。 1 、 先将升程迭代数据 (见表 1 、 3) , 画成 升程误差曲线图 , 并标出公差带和各误差的 位置 (图 4a ); 2 、 再将各误差点投影到平行于△ h 轴的 y轴上 , 并作出各误差点的转换轨迹直线 (斜 率等于各点的升程变化率 ) , 标出公差带位置 (图 4b); 3 、 找到 最大误差点 a 的 转换轨迹 直线
可通过下式计算 △ h( i ) = △ hi+ h′ i △α ( 6)
— 41 —
4b); 4 、 将 ( y)轴上各误差投影点 , 还原成升程 误差曲线 (图 4c ) , ( y )轴就是校正 后的理想 检测起始位置 ,图 4c 就是校正后的升程误差
曲线图。 这里应提出 , 为简化作图过程 ,图解校正 时一般只作出图 4b 。
图 3 凸轮升程最大误差点 b, 最小误差 c
凸轮升程数据
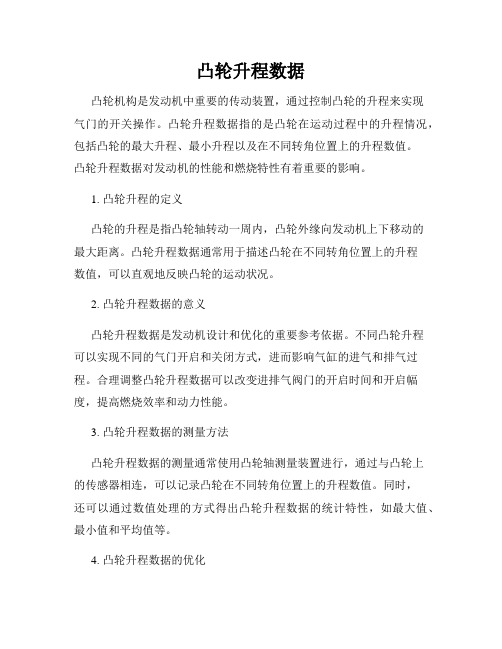
凸轮升程数据凸轮机构是发动机中重要的传动装置,通过控制凸轮的升程来实现气门的开关操作。
凸轮升程数据指的是凸轮在运动过程中的升程情况,包括凸轮的最大升程、最小升程以及在不同转角位置上的升程数值。
凸轮升程数据对发动机的性能和燃烧特性有着重要的影响。
1. 凸轮升程的定义凸轮的升程是指凸轮轴转动一周内,凸轮外缘向发动机上下移动的最大距离。
凸轮升程数据通常用于描述凸轮在不同转角位置上的升程数值,可以直观地反映凸轮的运动状况。
2. 凸轮升程数据的意义凸轮升程数据是发动机设计和优化的重要参考依据。
不同凸轮升程可以实现不同的气门开启和关闭方式,进而影响气缸的进气和排气过程。
合理调整凸轮升程数据可以改变进排气阀门的开启时间和开启幅度,提高燃烧效率和动力性能。
3. 凸轮升程数据的测量方法凸轮升程数据的测量通常使用凸轮轴测量装置进行,通过与凸轮上的传感器相连,可以记录凸轮在不同转角位置上的升程数值。
同时,还可以通过数值处理的方式得出凸轮升程数据的统计特性,如最大值、最小值和平均值等。
4. 凸轮升程数据的优化根据发动机工作状态和设计要求,可以对凸轮升程数据进行优化。
例如,在高速运行时可以增加凸轮升程,以增加气门开启时间,提高进气效率;而在低速运行时可以减小凸轮升程,以提高排气效率和汽缸充盈度。
凸轮升程数据的优化需要综合考虑多个因素,如排气阻力、燃烧特性和发动机可靠性等。
5. 凸轮升程数据与发动机性能凸轮升程数据对发动机的性能有着直接的影响。
合理的凸轮升程设计可以提高发动机的功率、扭矩和燃烧效率,同时还可以减少排放和噪音。
通过凸轮升程数据的优化,可以实现发动机在不同工况下的最优性能。
总结:凸轮升程数据是发动机设计中的重要内容,通过合理的凸轮升程设计可以优化发动机的性能和燃烧特性。
凸轮升程数据的测量和优化需要综合考虑多个因素,对于发动机制造厂商和设计师来说具有重要的指导意义。
通过凸轮升程数据的优化,可以提高发动机的功率、燃烧效率和可靠性,实现更加高效和环保的发动机性能。
凸轮测量测头转换及当量升程表计算方法

凸轮测量测头转换及当量升程表计算方法1 概述凸轮轴是影响发动机配气机构工作质量的关键部件,它的功能是保证发动机气门组有准确、平稳的良好运动规律。
凸轮的测量,主要是为评定凸轮轴上各凸轮的几何精度和装机后的动力特性提供依据,所以,在对凸轮进行测量时,应按设计要求选择与凸轮机构从动件(挺柱)相同形式和形状的测头,按设计要求给出的转角—升程表进行测量,以正确反映凸轮机构的运动规律。
2 测头转换测头转换,不是指简单地将一种测头换成另一种测头,而是指采用不符合设计要求形式和形状的测头进行凸轮测量时测量参数的转换。
在测量中,把不符合设计要求形式和形状的测头卸下,装上符合设计要求形式和形状的测头的一组操作称为测头换装。
测头转换和测头换装是两个截然不同的概念。
无论是确定凸轮的检测位置,还是测量凸轮的升程,都应采用与凸轮机构从动件(挺柱)相同形式和形状的测头。
例如,S195 型柴油机的配气凸轮的从动件是平面挺柱,测量时应采用平面测头:供油凸轮的从动件是滚柱挺柱,测量时应采用与滚柱挺柱直径相同的滚柱测头。
可是,常常是当同一根凸轮轴上各凸轮的从动件设计要求不同时,本应分别采用符合设计要求的不同形式和形状的测头进行测量,可是一些测量者为了省去在测量过程中换装测头的麻烦,竟用同一测头去测量凸轮轴上各个凸轮,这对某一个凸轮而言就引发了测头转换问题,尤其是在凸轮自动测量时,这种转换测头形式和形状的现象更为普遍。
图1 凸轮受检点相同时测头不同凸轮转角不同测头形式和形状转换后,改用当量升程表测量,原理上并不存在问题。
但是现行当量升程表,一般均以设计转角为依据而不是以设计受检点为依据来计算。
也就是说,如果测头转换后与转换前的转角一致,则凸轮受检点将不同:如果测头转换前后受检点相同,则凸轮转角不同。
例如,S195 型柴油机配气凸轮的“敏感点”m ,采用设计要求的平面测头测量时,凸轮转角ap=46°07'16"(图1a):采用Ø15mm 滚柱测头时,凸轮转角aG=16°53' (图1b):采用刀口测头时,凸轮转角aD= 6°52'28"(图1c)。
根据升程值用soliworks配合autocad画凸轮

Soliworks升程值画凸轮
1:凸轮曲线升程表94度为升程最高点,凸轮直径29.05
注释:凸轮升程表与凸轮直径,可用相关仪器测量得到,如下表1所示
1 2:凸轮直径+升程值=轨迹曲线值:
轨迹曲线值<角度值,如下表2所示:
表2 3:将表2的数值复制黏贴到文本文档,表头加入”spline”字符,不要有空格如下图3所示
图3
4:将文本文档格式改为“scr”格式,得到Autocad脚本
5:打开CAD画直径为φ29.05的圆,执行命令“scr”,就可以画出,依据曲线值的曲线如下图4,5所示
图4
图5
6:将CAD文件拖入soliworks得到如下图6所示曲线轮廓
图6 7:拉伸凸台/基体得到凸轮,如下图7所示
图7。
凸轮压力角的计算
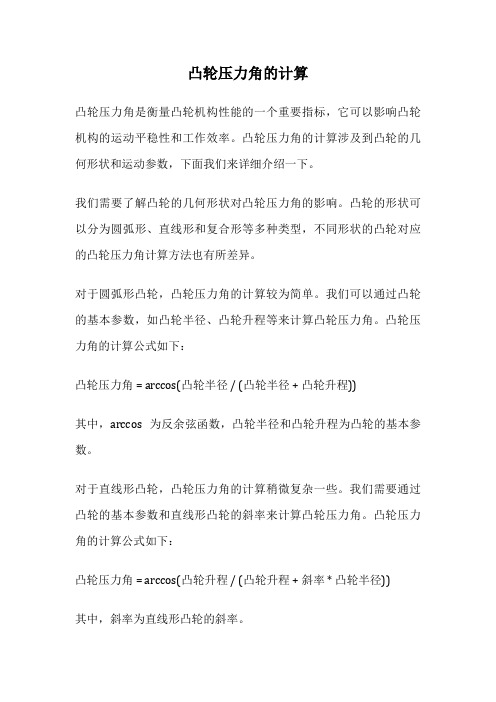
凸轮压力角的计算凸轮压力角是衡量凸轮机构性能的一个重要指标,它可以影响凸轮机构的运动平稳性和工作效率。
凸轮压力角的计算涉及到凸轮的几何形状和运动参数,下面我们来详细介绍一下。
我们需要了解凸轮的几何形状对凸轮压力角的影响。
凸轮的形状可以分为圆弧形、直线形和复合形等多种类型,不同形状的凸轮对应的凸轮压力角计算方法也有所差异。
对于圆弧形凸轮,凸轮压力角的计算较为简单。
我们可以通过凸轮的基本参数,如凸轮半径、凸轮升程等来计算凸轮压力角。
凸轮压力角的计算公式如下:凸轮压力角 = arccos(凸轮半径 / (凸轮半径 + 凸轮升程))其中,arccos为反余弦函数,凸轮半径和凸轮升程为凸轮的基本参数。
对于直线形凸轮,凸轮压力角的计算稍微复杂一些。
我们需要通过凸轮的基本参数和直线形凸轮的斜率来计算凸轮压力角。
凸轮压力角的计算公式如下:凸轮压力角 = arccos(凸轮升程 / (凸轮升程 + 斜率 * 凸轮半径))其中,斜率为直线形凸轮的斜率。
对于复合形凸轮,凸轮压力角的计算较为复杂。
我们需要通过凸轮的基本参数和凸轮曲线的方程来计算凸轮压力角。
复合形凸轮的凸轮压力角计算一般需要借助计算机软件或数值计算方法来求解。
需要注意的是,凸轮压力角的计算结果是一个角度值,一般以度数或弧度表示。
凸轮压力角的大小直接影响着凸轮机构的运动平稳性和工作效率。
一般来说,凸轮压力角越小,凸轮机构的运动越平稳,工作效率越高。
凸轮压力角的计算涉及到凸轮的几何形状和运动参数。
通过凸轮的基本参数和凸轮形状的特征,我们可以计算出凸轮的压力角,从而评估凸轮机构的性能。
在实际设计和应用中,我们需要根据具体的要求和条件选择合适的凸轮形状和参数,以实现凸轮机构的优化设计和高效运行。
gb3803-83汽车发动机凸轮轴修理技术条件.doc
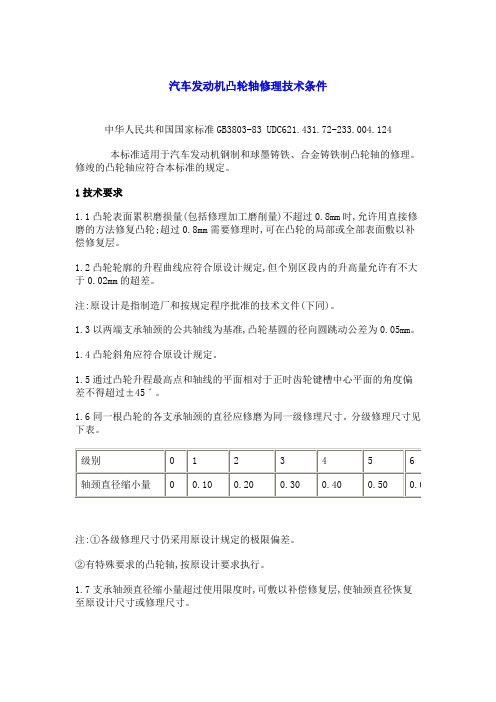
汽车发动机凸轮轴修理技术条件中华人民共和国国家标准GB3803-83 UDC621.431.72-233.004.124本标准适用于汽车发动机钢制和球墨铸铁、合金铸铁制凸轮轴的修理。
修竣的凸轮轴应符合本标准的规定。
1技术要求1.1凸轮表面累积磨损量(包括修理加工磨削量)不超过0.8mm时,允许用直接修磨的方法修复凸轮;超过0.8mm需要修理时,可在凸轮的局部或全部表面敷以补偿修复层。
1.2凸轮轮廓的升程曲线应符合原设计规定,但个别区段内的升高量允许有不大于0.02mm的超差。
注:原设计是指制造厂和按规定程序批准的技术文件(下同)。
1.3以两端支承轴颈的公共轴线为基准,凸轮基圆的径向圆跳动公差为0.05mm。
1.4凸轮斜角应符合原设计规定。
1.5通过凸轮升程最高点和轴线的平面相对于正时齿轮键槽中心平面的角度偏差不得超过±45ˊ。
1.6同一根凸轮的各支承轴颈的直径应修磨为同一级修理尺寸。
分级修理尺寸见下表。
注:①各级修理尺寸仍采用原设计规定的极限偏差。
②有特殊要求的凸轮轴,按原设计要求执行。
1.7支承轴颈直径缩小量超过使用限度时,可敷以补偿修复层,使轴颈直径恢复至原设计尺寸或修理尺寸。
1.8支承轴颈的圆柱度公差为0.005mm。
1.9以两端支承轴颈的公共轴线为基准,中间各支承轴颈的径向圆跳动公差为0.025mm。
1.10安装正时齿轮的轴颈,其尺寸应符合原设计规定。
以两端支承轴颈的公共轴线为基准,其轴颈的径向圆跳动和轴向止推端面的端面圆跳动公差为0.03mm。
1.11驱动汽油泵的偏心轮直径允许比原设计规定的最小极限尺寸小1.Omm,其偏心距应符合原设计规定。
1.12机油泵驱动齿轮不得缺损,轮齿工作表面不得有剥落,齿厚不小于原设计规定的最小极限尺寸的0.5Omm。
1.13支承轴颈表面光洁度不低于▽8;凸轮和驱动汽油泵的偏心轮的表面光洁度不低于▽7;轴向止推端面的表面光洁度不低于▽6;其他加工面的表面光洁度应符合原设计规定。
凸轮测量测头转换及当量升程表计算方法

凸轮测量测头转换及当量升程表计算方法1 概述凸轮轴是影响发动机配气机构工作质量的关键部件,它的功能是保证发动机气门组有准确、平稳的良好运动规律。
凸轮的测量,主要是为评定凸轮轴上各凸轮的几何精度和装机后的动力特性提供依据,所以,在对凸轮进行测量时,应按设计要求选择与凸轮机构从动件(挺柱)相同形式和形状的测头,按设计要求给出的转角—升程表进行测量,以正确反映凸轮机构的运动规律。
2 测头转换测头转换,不是指简单地将一种测头换成另一种测头,而是指采用不符合设计要求形式和形状的测头进行凸轮测量时测量参数的转换。
在测量中,把不符合设计要求形式和形状的测头卸下,装上符合设计要求形式和形状的测头的一组操作称为测头换装。
测头转换和测头换装是两个截然不同的概念。
无论是确定凸轮的检测位置,还是测量凸轮的升程,都应采用与凸轮机构从动件(挺柱)相同形式和形状的测头。
例如,S195 型柴油机的配气凸轮的从动件是平面挺柱,测量时应采用平面测头:供油凸轮的从动件是滚柱挺柱,测量时应采用与滚柱挺柱直径相同的滚柱测头。
可是,常常是当同一根凸轮轴上各凸轮的从动件设计要求不同时,本应分别采用符合设计要求的不同形式和形状的测头进行测量,可是一些测量者为了省去在测量过程中换装测头的麻烦,竟用同一测头去测量凸轮轴上各个凸轮,这对某一个凸轮而言就引发了测头转换问题,尤其是在凸轮自动测量时,这种转换测头形式和形状的现象更为普遍。
图1 凸轮受检点相同时测头不同凸轮转角不同测头形式和形状转换后,改用当量升程表测量,原理上并不存在问题。
但是现行当量升程表,一般均以设计转角为依据而不是以设计受检点为依据来计算。
也就是说,如果测头转换后与转换前的转角一致,则凸轮受检点将不同:如果测头转换前后受检点相同,则凸轮转角不同。
例如,S195 型柴油机配气凸轮的“敏感点”m ,采用设计要求的平面测头测量时,凸轮转角ap=46°07'16"(图1a):采用Ø15mm 滚柱测头时,凸轮转角aG=16°53' (图1b):采用刀口测头时,凸轮转角aD= 6°52'28"(图1c)。
凸轮的运动规律,压力角

2.等加速等减速运动规律(选学)
s
h
h/2
t/2
t/2
, t
a +a -a
, t
t/2
t/2
分两段:
等加速段
等减速段
s
等加速段
h/2
h
t/2
t/2
, t
根据式(3-3) 画出运动线图
v
t/2
t/2
, t
a
+a
t/2 t/2
, t
s
等减速段
t/2 t/2
h
h/2
3.简谐运动规律
简谐运动:(又称余弦加速度运动)
s
当一点在圆周上等速运动时,其 在直径上投影的运动即简谐运动
h
s
θ
h s (1 cos ) 2
, t
s
推程过程
h(升程)
, t
v
正弦曲线
/2
, t
余弦曲线
a
/2
, t
在推程的始末点加速度产 生有限数值的突变,即有 柔性冲击,故用于中低速 场合。
速度方程v=h/
s0Leabharlann t, t位移方程s=h/ 速度方程v=h/
加速度方程a=0 (在运动开始与运动终止处其加速度达到)
a
, t
a a -
v
a
s
等速运动规律的运动线图
h
v0 a
a -
, t
在始点 a ,在末点 a , 即始末点的理论加速度值为无穷 大,它所引起的惯性力亦应为无 穷大而产生强烈的冲击,这种冲 击称为刚性冲击或称为硬冲。因 此这种运动规律只适用于凸轮转 速很低的场合。
凸轮计算方法

v1.0 可编辑可修改凸轮计算方法图片:自动车床主要靠凸轮来控制加工过程,能否设计出一套好的凸轮,是体现自动车床师傅的技术高低的一个标准。
凸轮设计计算的资料不多,在此,我将一些基本的凸轮计算方法送给大家。
凸轮是由一组或多组螺旋线组成的,这是一种端面螺旋线,又称阿基米德螺线。
其形成的主要原理是:由A点作等速旋转运动,同时又使A点沿半径作等速移动,形成了一条复合运动轨迹的端面螺线。
这就是等速凸轮的曲线。
凸轮的计算有几个专用名称:1、上升曲线——凸轮上升的起点到最高点的弧线称为上升曲线2、下降曲线——凸轮下降的最高点到最低点的弧线称为下降曲线3、升角——从凸轮的上升起点到最高点的角度,即上升曲线的角度。
我们定个代号为φ。
4、降角——从凸轮的最高点到最低点的角度,即下降曲线的角度。
代号为φ1。
5、升距——凸轮上升曲线的最大半径与最小半径之差。
我们给定代号为h,单位是毫米。
6、降距——凸轮下降曲线的最大半径与最小半径之差。
代号为h1。
7、导程——即凸轮的曲线导程,就是假定凸轮曲线的升角(或降角)为360°时凸轮的升距(或降距)。
代号为L,单位是毫米。
8、常数——是凸轮计算的一个常数,它是通过计算得来的。
代号为K。
凸轮的升角与降角是给定的数值,根据加工零件尺寸计算得来的。
凸轮的常数等于凸轮的升距除以凸轮的升角,即K=h/φ。
由此得h=Kφ。
凸轮的导程等于360°乘以常数,即L=360°K。
由此得L=360°h/φ。
举个例子:一个凸轮曲线的升距为10毫米,升角为180°,求凸轮的曲线导程。
(见下图)解:L=360°h/φ=360°×10÷180°=20毫米升角(或降角)是360°的凸轮,其升距(或降距)即等于导程。
这只是一般的凸轮基本计算方法,比较简单,而自动车床上的凸轮,有些比较简单,有些则比较复杂。