常温磷化液
常温低温型磷化
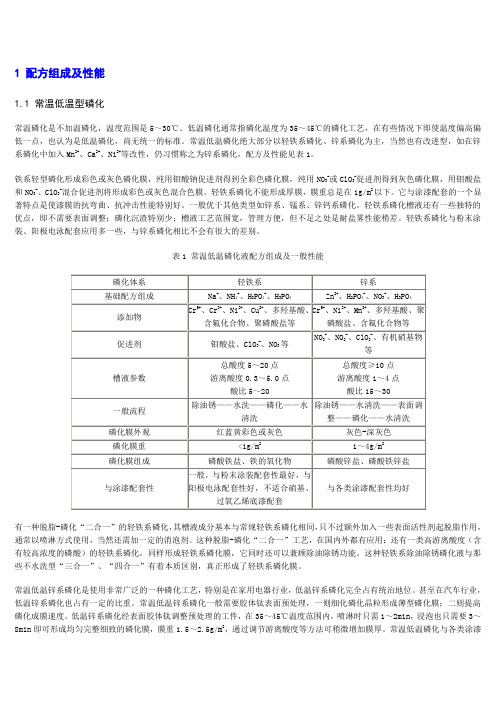
1 配方组成及性能1.1 常温低温型磷化常温磷化是不加温磷化,温度范围是5~30℃。
低温磷化通常指磷化温度为35~45℃的磷化工艺,在有些情况下即使温度偏高偏低一点,也认为是低温磷化,尚无统一的标准。
常温低温磷化绝大部分以轻铁系磷化、锌系磷化为主,当然也有改进型,如在锌系磷化中加入Mn2+、Ca2+、Ni2+等改性,仍习惯称之为锌系磷化,配方及性能见表1。
铁系轻型磷化形成彩色或灰色磷化膜,纯用钼酸钠促进剂得到全彩色磷化膜,纯用NO3-或ClO3-促进剂得到灰色磷化膜,用钼酸盐和NO3-、ClO3-混合促进剂将形成彩色或灰色混合色膜。
轻铁系磷化不能形成厚膜,膜重总是在1g/m2以下。
它与涂漆配套的一个显著特点是使漆膜的抗弯曲、抗冲击性能特别好。
一般优于其他类型如锌系、锰系、锌钙系磷化。
轻铁系磷化槽液还有一些独特的优点,即不需要表面调整;磷化沉渣特别少;槽液工艺范围宽,管理方便,但不足之处是耐盐雾性能稍差。
轻铁系磷化与粉末涂装、阳极电泳配套应用多一些,与锌系磷化相比不会有很大的差别。
表1 常温低温磷化液配方组成及一般性能有一种脱脂-磷化“二合一”的轻铁系磷化,其槽液成分基本与常规轻铁系磷化相同,只不过额外加入一些表面活性剂起脱脂作用,通常以喷淋方式使用,当然还需加一定的消泡剂。
这种脱脂-磷化“二合一”工艺,在国内外都有应用:还有一类高游离酸度(含有较高浓度的磷酸)的轻铁系磷化,同样形成轻铁系磷化膜,它同时还可以兼顾除油除锈功能。
这种轻铁系除油除锈磷化液与那些不水洗型“三合一”、“四合一”有着本质区别,真正形成了轻铁系磷化膜。
常温低温锌系磷化是使用非常广泛的一种磷化工艺,特别是在家用电器行业,低温锌系磷化完全占有统治地位。
甚至在汽车行业,低温锌系磷化也占有一定的比重。
常温低温锌系磷化一般需要胶体钛表面预处理,一则细化磷化晶粒形成薄型磷化膜;二则提高磷化成膜速度。
低温锌系磷化经表面胶体钛调整预处理的工件,在35~45℃温度范围内,喷淋时只需1~2min,浸泡也只需要3~8min即可形成均匀完整细致的磷化膜,膜重1.5~2.5g/m2,通过调节游离酸度等方法可稍微增加膜厚。
常温六合一磷化液1
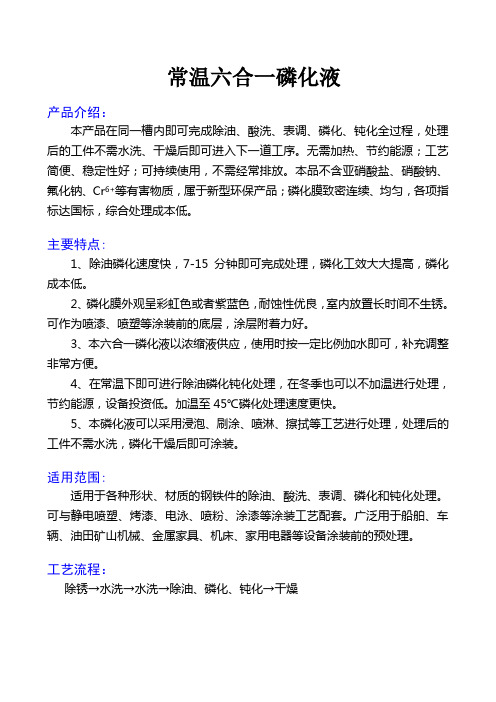
常温六合一磷化液产品介绍:本产品在同一槽内即可完成除油、酸洗、表调、磷化、钝化全过程,处理后的工件不需水洗、干燥后即可进入下一道工序。
无需加热、节约能源;工艺简便、稳定性好;可持续使用,不需经常排放。
本品不含亚硝酸盐、硝酸钠、氟化钠、Cr6+等有害物质,属于新型环保产品;磷化膜致密连续、均匀,各项指标达国标,综合处理成本低。
主要特点:1、除油磷化速度快,7-15分钟即可完成处理,磷化工效大大提高,磷化成本低。
2、磷化膜外观呈彩虹色或者紫蓝色,耐蚀性优良,室内放置长时间不生锈。
可作为喷漆、喷塑等涂装前的底层,涂层附着力好。
3、本六合一磷化液以浓缩液供应,使用时按一定比例加水即可,补充调整非常方便。
4、在常温下即可进行除油磷化钝化处理,在冬季也可以不加温进行处理,节约能源,设备投资低。
加温至45℃磷化处理速度更快。
5、本磷化液可以采用浸泡、刷涂、喷淋、擦拭等工艺进行处理,处理后的工件不需水洗,磷化干燥后即可涂装。
适用范围:适用于各种形状、材质的钢铁件的除油、酸洗、表调、磷化和钝化处理。
可与静电喷塑、烤漆、电泳、喷粉、涂漆等涂装工艺配套。
广泛用于船舶、车辆、油田矿山机械、金属家具、机床、家用电器等设备涂装前的预处理。
工艺流程:除锈→水洗→水洗→除油、磷化、钝化→干燥配制与维护:1、配制方法:按本品配制浓度(5%),将槽体清洁干净后加入30%的水,然后加入六合一磷化液搅匀,将剩余的水倒入搅匀即可使用。
2、按期打捞槽底沉渣、液面油污或翻槽。
3、当处理效果明显下降时,应补充磷化剂使指标在规定范围内。
4、最好使处理的工件与液体作相对运动。
5、磷化膜彻底干燥以前,应禁止手摸、雨淋或沾水。
6、处理槽最好用玻璃钢、不锈钢、聚氯乙烯板等耐酸材料制作。
检测方法:总酸度(TA):取磷化槽液10mL,加50mL蒸馏水,用酚酞为指示剂,以0.1mol/L的标准NaOH溶液滴定至溶液变粉红色时为终点,所耗用的NaOH 标液的毫升数为总酸度。
2024年锌系常温磷化液市场前景分析

2024年锌系常温磷化液市场前景分析1. 概述锌系常温磷化液是一种常用的防腐涂层材料,广泛应用于汽车、航空航天、机械制造等领域。
本文将对锌系常温磷化液市场的前景进行分析。
2. 锌系常温磷化液的特点锌系常温磷化液具有以下特点:•高效防腐:锌系常温磷化液可以形成一层紧密的磷酸锌转化膜,有效防止金属表面的氧化和腐蚀。
•良好的涂装性能:锌系常温磷化液具有良好的附着力和均匀性,可以提供优异的涂层外观和涂装性能。
•环保性:锌系常温磷化液的配方中不含重金属和有害物质,对人体和环境无害。
3. 市场需求分析3.1 汽车行业汽车制造是锌系常温磷化液的主要应用领域之一。
随着汽车产量的增加和对涂层防腐性能要求的提高,锌系常温磷化液在汽车行业的需求将持续增长。
3.2 机械制造业在机械制造业中,锌系常温磷化液被广泛应用于金属制品的防腐涂层。
随着机械制造业的发展,对于高效防腐涂层的需求也在增加,锌系常温磷化液将得到更广泛的应用。
3.3 航空航天行业在航空航天行业中,对于金属构件的防腐性能要求非常高。
锌系常温磷化液以其优良的防腐性能被广泛应用于航空航天领域,随着航空航天技术的不断发展,对锌系常温磷化液市场的需求也将继续增加。
4. 市场竞争分析锌系常温磷化液市场存在着一定的竞争。
目前市场上的主要竞争对手包括国内外一些知名的涂料厂商。
这些竞争对手不仅拥有先进的技术和生产设备,还具备较强的销售能力和品牌影响力。
为了在市场竞争中占据优势,企业需要不断提高产品质量、降低成本,并注重品牌宣传和市场推广。
5. 市场前景展望锌系常温磷化液市场的前景看好。
随着消费者对产品质量和环保性的要求日益提高,锌系常温磷化液作为一种高效防腐涂层材料可以满足市场需求。
预计未来几年,锌系常温磷化液市场将保持稳定增长,特别是在汽车、机械制造和航空航天行业的应用将持续扩大。
6. 结论综上所述,锌系常温磷化液作为一种高效防腐涂层材料,具有良好的市场前景。
在市场竞争激烈的环境中,企业需要提高产品质量和品牌影响力,以满足不断增长的市场需求。
常温磷化
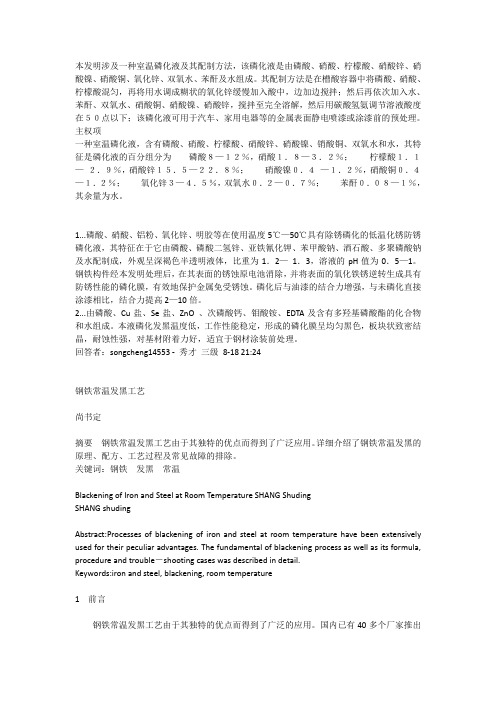
本发明涉及一种室温磷化液及其配制方法,该磷化液是由磷酸、硝酸、柠檬酸、硝酸锌、硝酸镍、硝酸铜、氧化锌、双氧水、苯酐及水组成。
其配制方法是在槽酸容器中将磷酸、硝酸、柠檬酸混匀,再将用水调成糊状的氧化锌缓慢加入酸中,边加边搅拌;然后再依次加入水、苯酐、双氧水、硝酸铜、硝酸镍、硝酸锌,搅拌至完全溶解,然后用碳酸氢氨调节溶液酸度在50点以下;该磷化液可用于汽车、家用电器等的金属表面静电喷漆或涂漆前的预处理。
主权项一种室温磷化液,含有磷酸、硝酸、柠檬酸、硝酸锌、硝酸镍、销酸铜、双氧水和水,其特征是磷化液的百分组分为磷酸8—12%,硝酸1.8—3.2%;柠檬酸1.1—2.9%,硝酸锌15.5—22.8%;硝酸镍0.4—1.2%,硝酸铜0.4—1.2%;氧化锌3—4.5%,双氧水0.2—0.7%;苯酐0.08—1%,其余量为水。
1...磷酸、硝酸、铝粉、氧化锌、明胶等在使用温度5℃—50℃具有除锈磷化的低温化锈防锈磷化液,其特征在于它由磷酸、磷酸二氢锌、亚铁氰化钾、苯甲酸钠、酒石酸、多聚磷酸钠及水配制成,外观呈深褐色半透明液体,比重为1.2—1.3,溶液的pH值为0.5—1。
钢铁构件经本发明处理后,在其表面的锈蚀原电池消除,并将表面的氧化铁锈逆转生成具有防锈性能的磷化膜,有效地保护金属免受锈蚀。
磷化后与油漆的结合力增强,与未磷化直接涂漆相比,结合力提高2—10倍。
2...由磷酸、Cu盐、Se盐、ZnO 、次磷酸钙、钼酸铵、EDTA及含有多羟基磷酸酯的化合物和水组成。
本液磷化发黑温度低,工作性能稳定,形成的磷化膜呈均匀黑色,板块状致密结晶,耐蚀性强,对基材附着力好,适宜于钢材涂装前处理。
回答者:songcheng14553 - 秀才三级8-18 21:24钢铁常温发黑工艺尚书定摘要钢铁常温发黑工艺由于其独特的优点而得到了广泛应用。
详细介绍了钢铁常温发黑的原理、配方、工艺过程及常见故障的排除。
关键词:钢铁发黑常温Blackening of Iron and Steel at Room Temperature SHANG ShudingSHANG shudingAbstract:Processes of blackening of iron and steel at room temperature have been extensively used for their peculiar advantages. The fundamental of blackening process as well as its formula, procedure and trouble-shooting cases was described in detail.Keywords:iron and steel, blackening, room temperature1前言钢铁常温发黑工艺由于其独特的优点而得到了广泛的应用。
如何配制常温磷化液
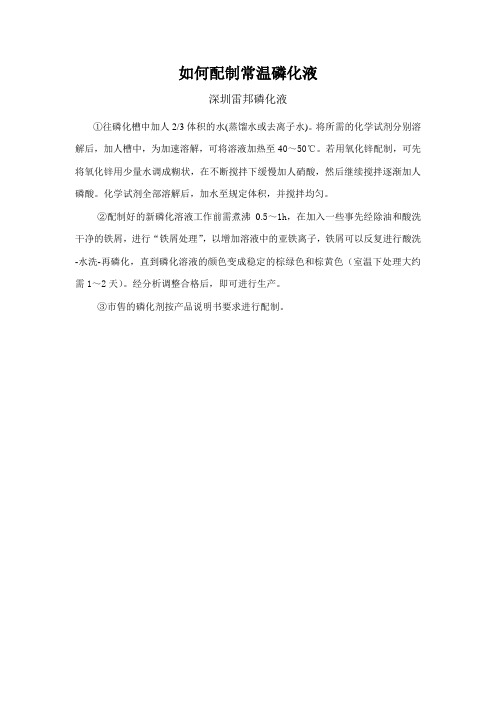
如何配制常温磷化液
深圳雷邦磷化液
①往磷化槽中加人2/3体积的水(蒸馏水或去离子水)。
将所需的化学试剂分别溶解后,加人槽中,为加速溶解,可将溶液加热至40~50℃。
若用氧化锌配制,可先将氧化锌用少量水调成糊状,在不断搅拌下缓慢加人硝酸,然后继续搅拌逐渐加人磷酸。
化学试剂全部溶解后,加水至规定体积,并搅拌均匀。
②配制好的新磷化溶液工作前需煮沸0.5~1h,在加入一些事先经除油和酸洗干净的铁屑,进行“铁屑处理”,以增加溶液中的亚铁离子,铁屑可以反复进行酸洗-水洗-再磷化,直到磷化溶液的颜色变成稳定的棕绿色和棕黄色(室温下处理大约需1~2天)。
经分析调整合格后,即可进行生产。
③市售的磷化剂按产品说明书要求进行配制。
常温四合一磷化液
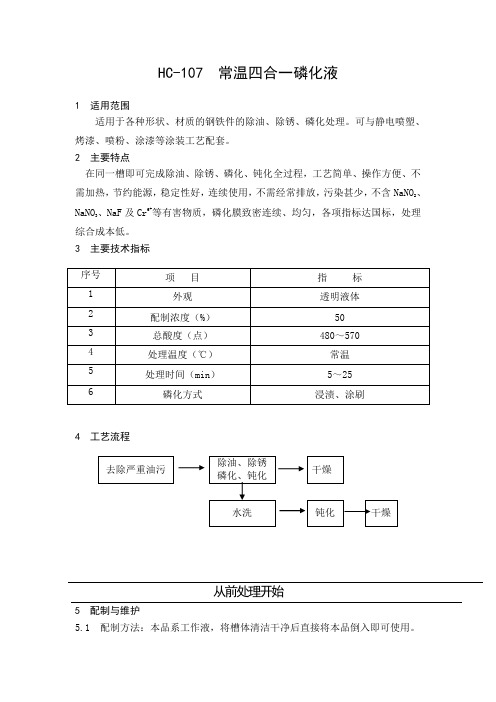
HC-107 常温四合一磷化液
1 适用范围
适用于各种形状、材质的钢铁件的除油、除锈、磷化处理。
可与静电喷塑、烤漆、喷粉、涂漆等涂装工艺配套。
2 主要特点
在同一槽即可完成除油、除锈、磷化、钝化全过程,工艺简单、操作方便、不
、需加热,节约能源,稳定性好,连续使用,不需经常排放,污染甚少,不含NaNO
2、NaF及Cr6+等有害物质,磷化膜致密连续、均匀,各项指标达国标,处理NaNO
3
综合成本低。
3主要技术指标
4工艺流程
从前处理开始
5 配制与维护
5.1 配制方法:本品系工作液,将槽体清洁干净后直接将本品倒入即可使用。
5.2 按期打捞槽底沉渣、液面油污或翻槽。
5.3 当处理效果明显下降时,应补充磷化剂使指标在规定范围内。
5.4 最好使处理的工件与液体作相对运动。
5.5 磷化膜彻底干燥以前,应禁止手摸、雨淋或沾水。
5.6 处理槽最好用玻璃钢、不锈钢、聚氯乙烯板等耐酸材料制作。
5.7 检测方法
总酸度(TA):取磷化槽液10mL,加50mL蒸馏水,用酚酞为指示剂,以0.1mol/L的标准NaOH溶液滴定至溶液变粉红色时为终点,所耗用的NaOH标液的毫升数为总酸度,用“点”来表示。
5.8 槽液调整:1m3槽液,补加磷化液2kg,可提高总酸度约1点。
将磷化粉配制成浓缩液后进行补加。
6 包装储存
25kg塑料桶包装,储存于阴晾干燥处,注意防止破损泄漏;运输过程中防止雨淋、潮湿。
7注意事项
装卸时轻拿轻放,防止破损飞溅到眼睛里,配制或使用过程中应配戴防护用品(如耐酸橡胶手套,工作服),如接触皮肤或眼睛立即用水冲洗。
常温磷化液的配方
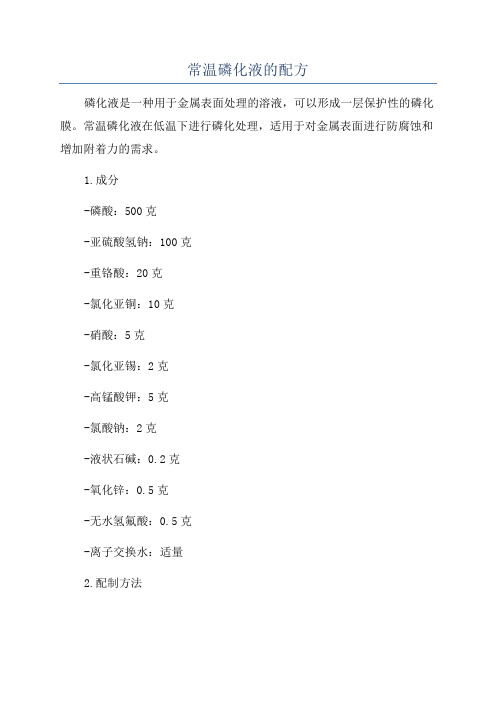
常温磷化液的配方
磷化液是一种用于金属表面处理的溶液,可以形成一层保护性的磷化膜。
常温磷化液在低温下进行磷化处理,适用于对金属表面进行防腐蚀和增加附着力的需求。
1.成分
-磷酸:500克
-亚硫酸氢钠:100克
-重铬酸:20克
-氯化亚铜:10克
-硝酸:5克
-氯化亚锡:2克
-高锰酸钾:5克
-氯酸钠:2克
-液状石碱:0.2克
-氧化锌:0.5克
-无水氢氟酸:0.5克
-离子交换水:适量
2.配制方法
1)首先用离子交换水稀释磷酸,将500克磷酸稀释至1000毫升,搅拌均匀。
2)将亚硫酸氢钠加入到磷酸溶液中,搅拌溶解。
3)在容器中加入重铬酸、氯化亚铜、硝酸、氯化亚锡、高锰酸钾、氯酸钠和液状石碱,搅拌均匀。
4)在溶液中加入氧化锌搅拌溶解。
5)最后,在溶液中加入少量无水氢氟酸,搅拌均匀。
3.使用方法
1)首先,将金属零件清洗干净,去除表面的油脂和污垢。
2)将金属零件完全浸泡在配制好的磷化液中,保持一定时间。
浸泡时间的长短取决于所需的磷化层厚度。
3)期间可以加热溶液,加快反应速度。
加热时需要注意控制温度,防止溶液过热。
4)磷化结束后,将金属零件从磷化液中取出,用清水彻底冲洗干净。
5)最后,将金属零件晾干或用热风吹干。
常温磷化液的配方
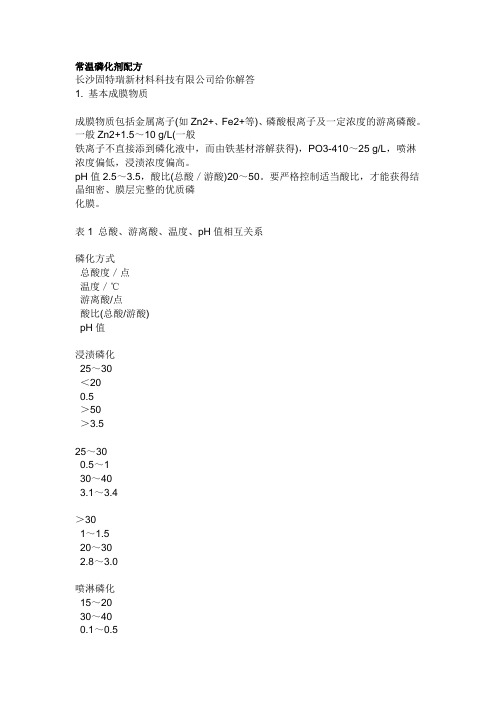
常温磷化剂配方长沙固特瑞新材料科技有限公司给你解答1. 基本成膜物质成膜物质包括金属离子(如Zn2+、Fe2+等)、磷酸根离子及一定浓度的游离磷酸。
一般Zn2+1.5~10 g/L(一般铁离子不直接添到磷化液中,而由铁基材溶解获得),PO3-410~25 g/L,喷淋浓度偏低,浸渍浓度偏高。
pH值2.5~3.5,酸比(总酸/游酸)20~50。
要严格控制适当酸比,才能获得结晶细密、膜层完整的优质磷化膜。
表1 总酸、游离酸、温度、pH值相互关系磷化方式总酸度/点温度/℃游离酸/点酸比(总酸/游酸)pH值浸渍磷化25~30<200.5>50>3.525~300.5~130~403.1~3.4>301~1.520~302.8~3.0喷淋磷化15~2030~400.1~0.550~803.5~3.9常温磷化液的配方硝酸锌25克磷酸二氢锌10克硝酸钙5克硝酸镍0.5克柠檬酸0.5克氟化钠0.2克温度:常温酸比1:20-25 亚硝酸钠0.2克常温磷化技术华南理工大学化工所(广州510641) 夏正斌涂伟萍杨卓如陈焕钦摘要从磷化膜形成过程、磷化液组成、促进剂的选择等方面综述了常温磷化技术的现状与发展趋势。
关键词常温磷化磷化膜涂装前处理促进剂常温磷化是当前研究最活跃、技术进步最快磷化技术〔1,2〕,它克服了高、中温磷化的能耗大、成本高、效率低等缺点,具有低能耗、低成本、低污染、快速等特点,因而受到普遍关注,近几年相关报道很多〔3~8〕。
1 磷化机理磷化反应是一种典型的局部多相反应,本质上属电化学反应。
当金属浸入磷化液中,在其表面形成许多微腐蚀电池,轻微浸蚀发生,且在溶液金属界面处,酸浓度降低。
张安富〔9〕较详细地讨论了磷化过程的热力学数据并指出,在常温下金属的氧化能力弱,须添加少量氧化剂,作为磷化反应促进剂,使得金属表面的混合电位低于氧化促进剂的电极电位。
2 磷化过程及磷化膜组成周谟银〔10〕采用腐蚀电压和电流两种方法研究了磷化过程,指出磷化可分成从基体开始腐蚀、成膜到过腐蚀等7个阶段。
常温铁系磷化

常温铁系磷化液前述1、碳钢、碳钢类合金钢等黑色金属的涂装前磷化;2、后期配套喷漆、喷粉、喷塑、电泳涂装,增加附着力的场合。
选用本品为最佳选择。
科学属性●理想的磷化效果;磷化膜呈蓝彩相间的颜色;●形成的磷化膜,与漆膜具有极佳的附着力;●兼具防锈效果;●本剂处理后表面无浮灰、无结晶物、无明显的油腻感,属清洁型产品;●兑水使用,与水形成稳定透明的防锈液;●无需表调,不会产生大量沉渣,高性价比产品;●不影响加工精度;●常温浸泡施工或喷淋施工即可,使用方便。
基本项目本剂可以重复使用多次,为节省药剂成本,建议厂家做好药剂回收工作,如回收的药剂携带杂质,为保护产品质量和不阻塞喷嘴,现场需经过必要的过滤或沉淀后再使用。
1、当本剂在使用一段时间后其有效成分必然消耗,则需进行适当的补加,以满足正常的质量要求,可根据处理平方进行大致计算,平均每公斤药剂处理20-30平方左右,即每升工作液处理2-3平方;现场每升工作液处理0.5平方时就需进行补加,补加量为每立方米槽液加入25公斤药剂。
2、当槽液使用周期过长,槽液的颜色会逐渐呈现深蓝色,可根据磷化效果考虑重新配槽。
3、如有条件,也可根据游离酸度,进行补加,以维护磷化的正常进行。
详情请咨询:淄博拓新达新技术开发有限公司其它1、处理前,工件表面应清洁、无异物;对于酸洗或脱脂后的工件,应确保水洗干净,最好要经过中和水洗处理,防止酸性物质或碱性物质对本剂的破坏;2、要使用新鲜水质配置工作液,禁止使用高硬度水质、污染性水质、高氯离子含量水质;3、由于工件材质的差异、施工条件的差异,处理后的防锈膜会呈现紫色、蓝色、灰色、棕色、浅黄色,或者几种颜色的混合相间色,以上颜色均为正常颜色。
如出现明显的黄点,且干燥后可以随意擦掉,为不正常颜色,应寻找工艺原因或致电供应商技术部门;4、本品处理后,严禁水洗;5、本品为有机弱酸性产品,建议施工时,穿戴防护劳保用品,如防护工作服、防护眼镜、防护眼镜等。
常温锌系磷化液
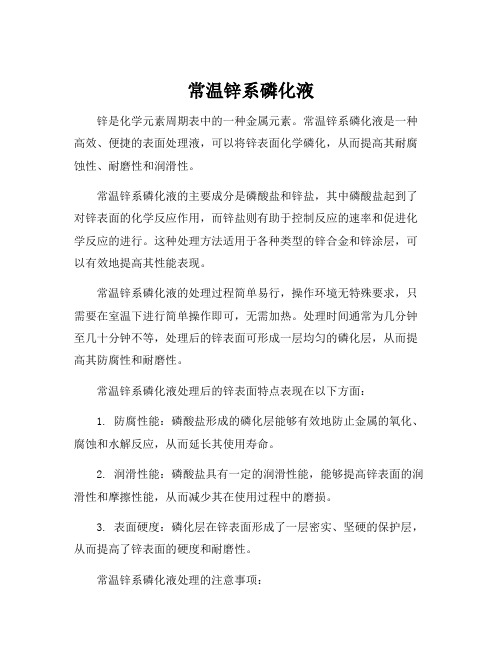
常温锌系磷化液
锌是化学元素周期表中的一种金属元素。
常温锌系磷化液是一种高效、便捷的表面处理液,可以将锌表面化学磷化,从而提高其耐腐蚀性、耐磨性和润滑性。
常温锌系磷化液的主要成分是磷酸盐和锌盐,其中磷酸盐起到了对锌表面的化学反应作用,而锌盐则有助于控制反应的速率和促进化学反应的进行。
这种处理方法适用于各种类型的锌合金和锌涂层,可以有效地提高其性能表现。
常温锌系磷化液的处理过程简单易行,操作环境无特殊要求,只需要在室温下进行简单操作即可,无需加热。
处理时间通常为几分钟至几十分钟不等,处理后的锌表面可形成一层均匀的磷化层,从而提高其防腐性和耐磨性。
常温锌系磷化液处理后的锌表面特点表现在以下方面:
1. 防腐性能:磷酸盐形成的磷化层能够有效地防止金属的氧化、腐蚀和水解反应,从而延长其使用寿命。
2. 润滑性能:磷酸盐具有一定的润滑性能,能够提高锌表面的润滑性和摩擦性能,从而减少其在使用过程中的磨损。
3. 表面硬度:磷化层在锌表面形成了一层密实、坚硬的保护层,从而提高了锌表面的硬度和耐磨性。
常温锌系磷化液处理的注意事项:
1. 处理液对皮肤和眼睛有刺激作用,操作时应穿戴好防护用具。
2. 处理前应将锌表面清洗干净,保证处理效果。
3. 处理完毕后应彻底清洗,避免残留处理液对环境和使用造成影响。
综上所述,常温锌系磷化液是一种高效、便捷的表面处理工艺,能够提高锌表面的防腐性和耐磨性,增强其使用寿命。
在实际工程中应注意安全操作,正确使用,方可取得良好的处理效果。
磷化液参数
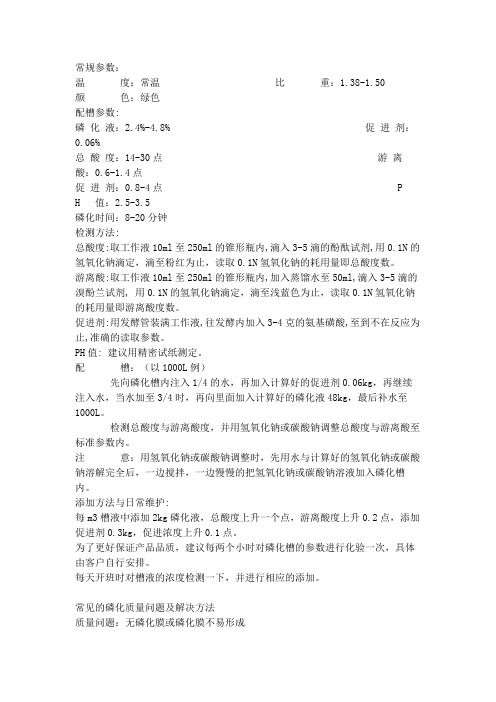
常规参数:温度:常温比重:1.38-1.50颜色:绿色配槽参数:磷化液:2.4%-4.8% 促进剂:0.06%总酸度:14-30点游离酸:0.6-1.4点促进剂:0.8-4点 P H 值:2.5-3.5磷化时间:8-20分钟检测方法:总酸度:取工作液10ml至250ml的锥形瓶内,滴入3-5滴的酚酞试剂,用0.1N的氢氧化钠滴定,滴至粉红为止,读取0.1N氢氧化钠的耗用量即总酸度数。
游离酸:取工作液10ml至250ml的锥形瓶内,加入蒸馏水至50ml,滴入3-5滴的溴酚兰试剂, 用0.1N的氢氧化钠滴定,滴至浅蓝色为止,读取0.1N氢氧化钠的耗用量即游离酸度数。
促进剂:用发酵管装满工作液,往发酵内加入3-4克的氨基磺酸,至到不在反应为止,准确的读取参数。
PH值: 建议用精密试纸测定。
配槽:(以1000L例)先向磷化槽内注入1/4的水,再加入计算好的促进剂0.06kg,再继续注入水,当水加至3/4时,再向里面加入计算好的磷化液48kg,最后补水至1000L。
检测总酸度与游离酸度,并用氢氧化钠或碳酸钠调整总酸度与游离酸至标准参数内。
注意:用氢氧化钠或碳酸钠调整时,先用水与计算好的氢氧化钠或碳酸钠溶解完全后,一边搅拌,一边慢慢的把氢氧化钠或碳酸钠溶液加入磷化槽内。
添加方法与日常维护:每m3槽液中添加2kg磷化液,总酸度上升一个点,游离酸度上升0.2点,添加促进剂0.3kg,促进浓度上升0.1点。
为了更好保证产品品质,建议每两个小时对磷化槽的参数进行化验一次,具体由客户自行安排。
每天开班时对槽液的浓度检测一下,并进行相应的添加。
常见的磷化质量问题及解决方法质量问题:无磷化膜或磷化膜不易形成外观现象:工件整体或局部无磷化膜,有时发蓝或有空白片产生原因:(1)工件表面有硬化层;(2)总酸度不够;(3)处理温度低;(4)游离酸太低;(5)脱脂不净或磷化时间偏短;(6)工件表面聚集氢气;(7)磷化槽液比例失调,如P2O5含量过低;(8)工件重叠或工件之间发生接触。
常温锌系磷化液资料
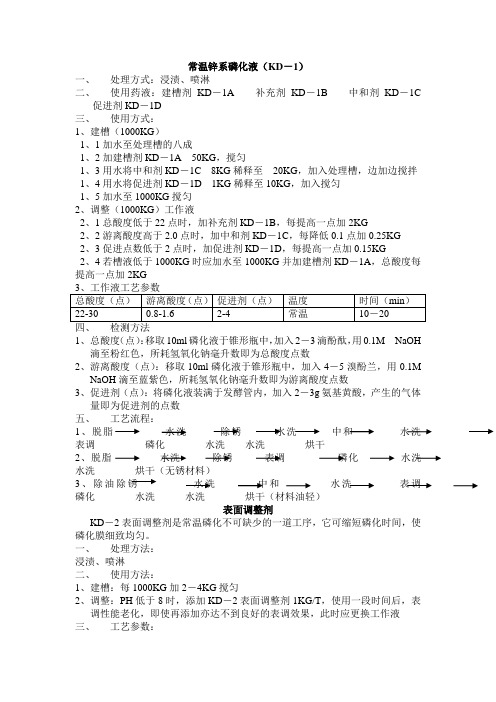
常温锌系磷化液(KD-1)一、处理方式:浸渍、喷淋二、使用药液:建槽剂KD-1A补充剂KD-1B中和剂KD-1C促进剂KD-1D三、使用方式:1、建槽(1000KG)1、1加水至处理槽的八成1、2加建槽剂KD-1A50KG,搅匀1、3用水将中和剂KD-1C8KG稀释至20KG,加入处理槽,边加边搅拌1、4用水将促进剂KD-1D1KG稀释至10KG,加入搅匀1、5加水至1000KG搅匀2、调整(1000KG)工作液2、1总酸度低于22点时,加补充剂KD-1B,每提高一点加2KG2、2游离酸度高于2.0点时,加中和剂KD-1C,每降低0.1点加0.25KG 2、3促进点数低于2点时,加促进剂KD-1D,每提高一点加0.15KG2、4若槽液低于1000KG时应加水至1000KG并加建槽剂KD-1A,总酸度每提高一点加2KG1、总酸度(点):移取10ml磷化液于锥形瓶中,加入2-3滴酚酞,用0.1M NaOH滴至粉红色,所耗氢氧化钠毫升数即为总酸度点数2、游离酸度(点):移取10ml磷化液于锥形瓶中,加入4-5溴酚兰,用0.1MNaOH滴至蓝紫色,所耗氢氧化钠毫升数即为游离酸度点数3、促进剂(点):将磷化液装满于发酵管内,加入2-3g氨基黄酸,产生的气体量即为促进剂的点数五、工艺流程:1、脱脂水洗除锈水洗中和水洗表调磷化水洗水洗烘干2、脱脂水洗除锈表调磷化水洗水洗烘干(无锈材料)3、除油除锈水洗中和水洗表调磷化水洗水洗烘干(材料油轻)表面调整剂KD-2表面调整剂是常温磷化不可缺少的一道工序,它可缩短磷化时间,使磷化膜细致均匀。
一、处理方法:浸渍、喷淋二、使用方法:1、建槽:每1000KG加2-4KG搅匀2、调整:PH低于8时,添加KD-2表面调整剂1KG/T,使用一段时间后,表调性能老化,即使再添加亦达不到良好的表调效果,此时应更换工作液三、工艺参数:PH值:8-9温度:常温时间:30-60S脱脂剂(KD-6)KD-6脱脂剂是由高效表面活性剂的复配物、碱金属盐、乳化剂等合成,具有极强的去污、乳化分散、增溶能力,是一种先进的低温高效脱脂剂。
常温铁系高耐蚀磷化液

常温铁系高耐蚀磷化液
一主要用途
Dw-022常温铁系磷化液系常温条件下使用的轻铁系磷化液,广泛应用于钢铁工件的喷塑、电泳、喷漆、喷塑等表面涂装前的磷化处理,主要用于变形较大工件涂装前磷化。
与粉末涂装、阳极电泳配套应用多一些。
二性能特点
铁系磷化液与涂漆配套的一个显著特点是使漆膜的抗弯曲、抗冲击性能特别好。
一般优于其他类型如锌系、锰系、锌钙系磷化。
轻铁系磷化槽液还有一些独特的优点,即不需要表面调整;磷化沉渣特别少;槽液工艺范围宽,管理方便,但不足之处是耐盐雾性能稍差。
轻铁系磷化与粉末涂装、阳极电泳配套应用多一些,与锌系磷化相比不会有很大的差别。
三理化指标
四、使用方法
工艺流程:
1、除油 -- 水洗–- 除锈-- 水洗 --磷化—干燥(晒干、
吹干或烘干)
2、除油除锈活化液一步 - 水洗 - 磷化—干燥(晒干、吹干
或烘干)
其中:1 适用于油污重的工件。
(多为冷轧板)
2 适用于少油污、有锈蚀或氧化皮的工件。
(多为热轧板)
按配槽比例(本剂:水=1:9重量比)进行加水稀释,搅拌均匀即可使用。
喷淋浸泡皆可。
槽液在使用过程中,需要定时进行补加。
并定期清理沉渣。
当成膜质量不好:出现挂灰或局部返锈的情况。
添加常温铁系磷化液后效果仍不明显时,可考虑进行更换槽液。
具体调整方法:当PH大于3.5时,在每立升槽液中,补加浓缩液8-12kg,PH下降0.5单位
五、注意事项
1、常温铁系磷化液原有较强腐蚀性,严禁溅入眼、口、皮肤衣物;如误触,立即清水冲洗,严重者,应及时就医;
2、阴凉处密封保存,长期有效。
常温铁系磷化液

YL-302常温铁系磷化液
本品是一种环保型、高浓度、快速、节能的铁系磷化液,该产品适合于冷轧板、热轧板、型钢等表面喷涂前的磷化处理。
一、技术指标
二、主要特点
1、常温磷化,不需加热,属节能型产品。
2、性能优异,磷化膜薄而致密,使得油漆的抗弯曲、抗冲击性能显著提高。
3、质量稳定,铁离子进入槽液中的数量甚少,大大提高槽液的稳定性,并解决了传统铁系磷化抗水洗性差,膜层易挂灰的问题。
4、管理方便,不需表调,不需钝化,不需控制酸比和添加促进剂。
三、使用方法及工艺参数
1、处理工序:脱脂→水洗→除锈→水洗→中和水洗→水洗→磷化→自然晾干或烘干
2、将本品配成5%工作液,搅拌均匀即可使用。
3、工艺参数:
FA:3~6Pt处理时间:5~15min
TA:15~18Pt处理温度:10~50℃
4、由于连续处理过程中浓度不断变化,所以要定期测定游离酸度及总酸度,保持各项指标在所规定的工艺浓度范围之内,每吨工作液每添加3.5-4公斤本品的浓缩液,游离酸上升0.2pt,总酸度上升1pt。
四、包装与储运
本品采用塑料桶包装,每桶净重20或25公斤,储存温度0~40℃。
特别声明:本公司所提供的技术信息基于本公司对现有产品的认识,用户对本公司提供的产品,应该进行试验以验证是否适合所拟订的工艺和用途,对于使用过程影响因素很多,提醒用户不可未经试验就照搬使用。
- 1、下载文档前请自行甄别文档内容的完整性,平台不提供额外的编辑、内容补充、找答案等附加服务。
- 2、"仅部分预览"的文档,不可在线预览部分如存在完整性等问题,可反馈申请退款(可完整预览的文档不适用该条件!)。
- 3、如文档侵犯您的权益,请联系客服反馈,我们会尽快为您处理(人工客服工作时间:9:00-18:30)。
新型常温磷化液
一、概述
磷化处理是指用酸性磷酸盐溶液处理金属,经过化学和电化学反应使其表面形成一层主要由难溶磷酸盐组成的膜层,其目的是为了在一定程度上提高金属的耐蚀性和抗粘着磨损能力。
由于磷化处理工艺简单,操作容易,成本低廉,故广泛应用于机械、汽车、航空、造船以及家庭日用品制造等工业。
石油钻采工具在设计和加工制造时,对连接螺纹都要求进行磷化处理,中石油行业标准《钻具螺纹电刷镀镀铜和磷化方法(SY/T5711─95)》明确规定了石油钻具螺纹的磷化方法及标准。
传统磷化工艺分为高温磷化(80~98℃)、中温磷化(60~70℃)、低温磷化(35~55℃)和常温磷化(35℃以下)。
就其膜层质量和耐蚀性来讲,高、中温磷化要高于低、常温磷化。
但是,由于这些传统磷化工艺都需要将工件浸渍在磷化液中或对其进行连续喷淋,才能实现磷化的目的,因此,使其在一些大型工件应用中受到限制,例如修复后的石油钻具(钻杆)接头螺纹部位,就无法应用传统的磷化工艺对其磷化。
石油钻具是钻井施工中传递扭矩、输送钻井液的重要工具,工作中钻具与钻具连接和卸扣非常频繁,钻具接头螺纹腐蚀与磨损现象较为严重。
为了提高钻具接头螺纹的使用寿命,新出厂的钻具,接头螺纹部位都进行了高温磷化或者槽镀铜处理。
修复钻具(钻杆),由于体积太大且接头螺纹的工况条件与整体钻杆不同,因此,如何提高修复钻具(钻杆)接头螺纹的使用寿命,是石油界科技人员一直在探讨的问题。
二、修复钻具(钻杆)接头螺纹磷化现状
正因为磷化能在一定程度上提高金属的耐蚀性和抗粘着磨损能力,而且工艺简单、操作容易,成本低廉,因此,磷化处理一直是所有从事钻具修理企业采用的钻具螺纹处理工艺。
中石油行业标准《钻具螺纹电刷镀镀铜和磷化方法(SY/T5711─95)》中规定石油钻具螺纹的磷化方法,是依据上世纪八十年代大庆石油管理局研制的一种应用“磷化膏”对钻具螺纹磷化工艺而制定的。
该项技术是在常温下采用刷涂的方法进行施工,比较适合于大批量的修复钻具应用,很快在国内修复钻具的企业得到推广和应用。
该工艺中的“磷化膏”像稀泥一样,施
工时把它刷涂于接头螺纹上,待一定时间后再用水把它冲洗掉。
若涂状物发干了,则要用钢丝刷和其他金属钝器才能除掉,整个操作过程很繁琐,工人的劳动强度大,生产效率低。
而且该工艺形成的磷化膜防腐性能较差,目前该项工艺已基本被淘汰。
钢铁件的“四合一”磷化法,是集除油、除锈、磷化、钝化综合为一步完成的磷化工艺技术,它是上世纪八十年代表面处理界最为推崇的高效磷化法。
该磷化液溶液的游离酸度与总酸度比值为1:10~15,处理时间5~15分钟,其优点是游离酸度较稳定,容易掌握,磷化时间短,生产效率高,磷化膜耐腐蚀性能与高温磷化的基本相同。
相关产品有江苏的太仓牌“四合一”磷化法、武汉的祥和牌常温“四合一”磷化粉等。
但是,应用效果表明,由于采用该技术产生磷化膜膜层薄、孔隙率高、防腐能力差,所以,该项技术只适用于作电泳涂漆的底层。
另外,该磷化液必须在50~70℃温度下进行磷化,属于中温磷化,不适合修复钻具应用。
三、新型常温磷化液的研制
我们对常温“四合一”磷化液的研制工作开始于2006年,在SY/T5711─95标准列出的磷化液的启示下,经过多年的研究和试验,2009年终于取得了技术突破,配制出了新型常温磷化液。
1、钢铁件的磷化反应机理
(1)水解反应
磷化液的基本成分是一种或多种重金属的磷酸二氢盐溶液,它们在一定浓度和PH条件下,发生水解反应:
3M(H2PO4)2→3MHPO4+3H3PO4 (a)
3MHPO4→M3(PO4)2+H3PO4 (b)综合为:3M(H2PO4)2→M3(PO4)2+H3PO4 (c)M是指Zn、Ni、Mn等金属离子,其中H3PO4将发生三级离解:
H3PO4→H++H2PO4-
H2PO4_→H++HPO42-
HPO42-→H++PO43-
(2)酸蚀反应
当钢铁浸入磷化液中时,发生的第一个反应是溶解金属下来的酸蚀反应。
酸蚀反应对形成涂膜是非常重要的,因为它既可净化金属表面,又能提高涂膜附着力。
.Fe+2H+→Fe2+ + H 2↑(d)酸蚀反应时,消耗了H+,破坏了磷化液中的水解平衡,从而使反应(c)向右移动,促使成膜反应进行。
(3)成膜反应
金属离子溶解到溶液中,与溶液中的磷酸盐发生反应形成磷酸盐和磷酸一氢盐沉积在金属表面,产生磷化晶粒,晶粒继续生长,并与金属表面发生化学结合,形成连续的磷化膜。
磷化液的类型决定了成膜反应的类型和产物,即磷化膜成分。
钢铁件在锌系磷化液中产生的磷化膜成分主要是Zn3(PO4)2·4H2O和Zn2Fe(PO4)2·4H2O:
Fe+2 Zn(H2 PO4)2→Zn3 (PO4)2+ FeHPO4+ H2 (e)
3Zn(H2 PO4)2+4H2O→Zn3 (PO4)2·4H2O+4 H3PO4(f)
Fe(H2 PO4)2+2 Zn(H2 PO4)2+4H2O→Zn2Fe(PO4)2·4H2O+4 H3PO4(g)
2.游离酸度和总酸度对对磷化膜的影响
游离酸度指游离的磷酸浓度。
磷化液中需要有一定的游离酸才能保证铁的溶解,使磷化膜结晶细致。
游离酸度过低,磷化膜薄,甚至没有磷化膜。
游离酸度过高则与铁作用加快,会使磷化反应时间延长,磷化膜晶粒粗大多孔,耐蚀性降低。
总酸度主要来源于磷酸盐、硝酸盐和酸的总和。
总酸度高会使晶核生成速度快,能加速磷化反应,使膜层结晶细致。
总酸度过低,磷化膜薄。
但总酸度太高,晶核生成太快,使膜层疏松,防锈能力下降。
3.常温磷化液研制
由上述化学反应式可知,磷化过程除成膜反应外其他所有化学反应都是吸热的,因此,提高温度可使磷化反应速度加快,并使磷化膜的附着力提高,这也是为什么高、中温磷化质量要高于低、常温磷化(高、温型,形成磷化膜厚达1 0~30g/m2,膜抗蚀力强,结合力好;中温型,磷化膜厚度为1~7 g/m2,耐蚀性与高温磷化膜基本相同;常、低温型,膜厚为0.2~7 g/m2)的原因。
由此也可见,只从磷化机理上要搞出与高、中温磷化质量相近的常温磷化液,是
违背科学规律的。
但是,研究中发现,若取消或降低现有“四合一”磷化液的一些硝酸和硝酸盐的含量,并提高了溶液的游离酸度和总酸度,再加入了氧化剂和促进剂,配制出新型常温“四合一”磷化液,其应用效果可以达到高、中温磷化的质量。
4. 封闭剂的研制
与高、中温磷化相比,常温磷化主要是磷化膜层薄、耐蚀性差。
涂层耐蚀性差的其中一个主要原因是由涂层的孔隙而引发的。
在此研究过程中,我们根据热喷涂涂层封闭剂的渗透封闭原理,研制出了适合于超精细磷化膜的封闭剂。
该封闭剂具有很强的渗透性,不但能封闭磷化膜的微孔,而且还能在磷化膜的外表形成一层很薄的保护膜,进一步增强了磷化膜的耐蚀能力和减磨性能。
配制出新型常温“四合一”磷化液和封闭剂
四、新型常温磷化液的特点和性能
1、特点
研制的新型常温磷化液为无色、无味、无毒透明液体,PH值1~3,溶液相对密度为 1.17~1.18,游离酸度(点)308~375,总酸度(点)670~780,工作温度10~40℃。
该磷化液属锌系磷化液,其磷化膜主要有磷酸锌和磷酸氢铁组成。
磷化膜的颜色为浅灰→深灰,闪烁有光,均匀细致,附着力强的
结晶(结晶大部分为磷酸锌,小部分为磷酸氢铁),厚度为0.2~7 g/m2。
新型常温磷化液是集除油、除锈、磷化、钝化综合为一步完成,在常温下不需要专用作业场地和专用设备,可采用浸渍、喷淋、刷涂的方法对工件进行磷化,处理后工件不用水冲洗的磷化工艺技术。
它具有施工方便、效率高、劳动强度低、无环境污染、成本低等优点。
2、性能
新型常温磷化液产生的磷化膜可起减摩作用,并具有一定的防腐功能,与研制的封闭剂配合使用,其耐蚀性要高于高温磷化,应用到钻具螺纹上,可起到良好的防腐、防粘扣作用,延长钻具使用寿命;应用到油漆底层,可增强油漆层与工具的附着力;应用到冷拔、冷冲加工,可提高产品质量延长模具使用寿命。
由于磷化膜的颜色呈浅灰→深灰,而且均匀细致、闪烁有光,应用到井下钻采工具螺纹上,除能起到防腐、防粘扣作用外,还有一个最大的特点,就是增加工具的美观感。
五、使用方法
该磷化液可根据被处理工件的形状及处理部位,选择采用进行浸渍、喷淋、刷涂工艺。
新型常温磷化液是在室温下施工的,磷化过程中的化学反应及膜的生成比较缓慢,反应过程中吸热、放热不断交替发生,所以磷化工作面不可水洗、雨淋,要自然晾干,以保证磷化反应彻底。
在雨季及湿度大的季节施工时,应用热风把磷化面吹干,以加速磷化反应速度。
锈蚀或油污严重的工件要先用5-10%的NaOH水溶液进行除油,再用10-15%的HCl水溶液除锈,水洗后再进行磷化处理,以延长磷化液的寿命和保证磷化质量。
磷化液的游离酸度和总酸度及锌离子浓度随着磷化液的使用时间延长都会逐渐降低,工作中要不断补加新液。
应用于钻具及油管螺纹磷化时,用鞋刷蘸取该磷化液在螺纹丝扣刷涂三次,每隔十分钟一次。
最后一次刷完后,再用棉织物(吸水性好)把残留在丝扣中的磷化液擦干净,否则多余的磷化液干后会形成黑灰色胶状的磷酸盐,影响磷化膜美观。
待磷化表面干燥后再刷涂与本磷化液配套使用的封闭剂,磷化工作结束。
油管螺纹的磷化方法(母扣要用鞋刷)。