机械优化设计三个案例
机械优化设计案例

机械优化设计案例:某生产线自动送料机构的改进
在制造领域,生产线上的自动送料机构是确保生产流程顺畅、高效的关键环节。
然而,传统的自动送料机构往往存在效率低下、易损坏、维护成本高等问题。
为了解决这些问题,我们采用了机械优化设计的方法,对某生产线上的自动送料机构进行了改进。
该自动送料机构的主要任务是将原材料从存储区输送到生产线,并确保每次输送的数量准确。
但是,在长时间使用后,传统的送料机构常常出现卡顿、输送不准确等问题。
经过分析,我们发现这些问题主要是由于机构中的某些部件设计不合理,导致机械效率降低。
为了解决这些问题,我们采用了以下优化策略:
结构优化:利用拓扑优化技术,对送料机构的主体结构进行了重新设计,使其在满足强度和刚度的同时,减轻了重量,从而减少了动力消耗。
传动系统优化:采用了新型的齿轮和链条传动系统,减少了传动过程中的摩擦和能量损失,提高了传动效率。
控制系统优化:引入了PLC和传感器技术,实现了对送料过程的精确控制,确保了每次输送的数量准确。
维护性优化:设计了易于拆卸和维护的结构,减少了维护时间和成本。
经过上述优化后,新的自动送料机构的性能得到了显著提升。
与传统的送料机构相比,新的机构在输送速度、准确性、使用寿命和维护成本等方面都有了显著的优势。
经过实际生产验证,新的自动送料机构不仅提高了生产效率,还降低了生产成本,为企业带来了显著的经济效益。
机械结构设计优化案例分析
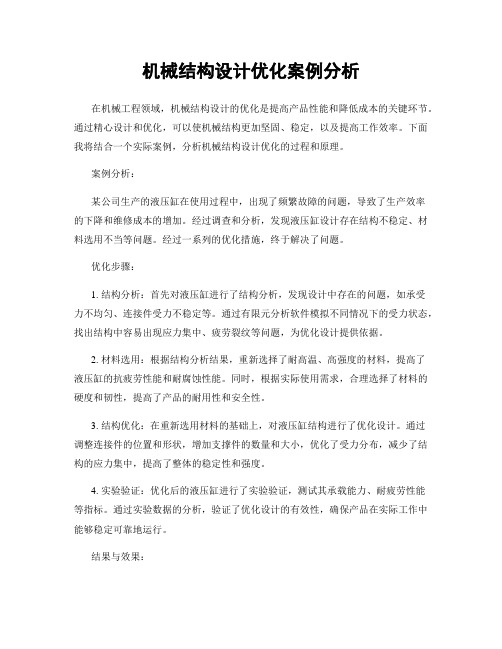
机械结构设计优化案例分析在机械工程领域,机械结构设计的优化是提高产品性能和降低成本的关键环节。
通过精心设计和优化,可以使机械结构更加坚固、稳定,以及提高工作效率。
下面我将结合一个实际案例,分析机械结构设计优化的过程和原理。
案例分析:某公司生产的液压缸在使用过程中,出现了频繁故障的问题,导致了生产效率的下降和维修成本的增加。
经过调查和分析,发现液压缸设计存在结构不稳定、材料选用不当等问题。
经过一系列的优化措施,终于解决了问题。
优化步骤:1. 结构分析:首先对液压缸进行了结构分析,发现设计中存在的问题,如承受力不均匀、连接件受力不稳定等。
通过有限元分析软件模拟不同情况下的受力状态,找出结构中容易出现应力集中、疲劳裂纹等问题,为优化设计提供依据。
2. 材料选用:根据结构分析结果,重新选择了耐高温、高强度的材料,提高了液压缸的抗疲劳性能和耐腐蚀性能。
同时,根据实际使用需求,合理选择了材料的硬度和韧性,提高了产品的耐用性和安全性。
3. 结构优化:在重新选用材料的基础上,对液压缸结构进行了优化设计。
通过调整连接件的位置和形状,增加支撑件的数量和大小,优化了受力分布,减少了结构的应力集中,提高了整体的稳定性和强度。
4. 实验验证:优化后的液压缸进行了实验验证,测试其承载能力、耐疲劳性能等指标。
通过实验数据的分析,验证了优化设计的有效性,确保产品在实际工作中能够稳定可靠地运行。
结果与效果:经过以上优化步骤,液压缸的故障率明显下降,生产效率得到了提高,维修成本也减少了。
同时,产品的性能和质量得到了明显提升,提高了用户的满意度和公司的竞争力。
结语:通过以上案例分析,我们可以看到机械结构设计的优化是一个系统工程,需要全面考虑材料、结构、受力等因素,不断调整和完善设计方案,以达到最佳效果。
只有不断迭代优化,才能使产品在市场上立于不败之地。
希望本文能够对机械结构设计优化的理解和实践有所启示。
机械优化设计实例
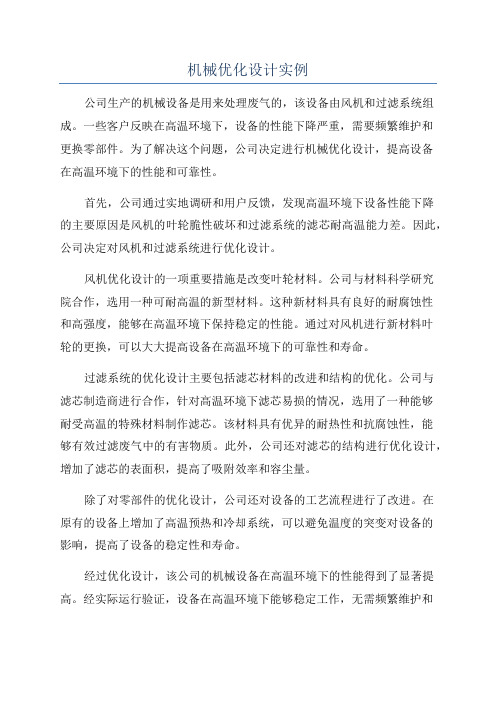
机械优化设计实例公司生产的机械设备是用来处理废气的,该设备由风机和过滤系统组成。
一些客户反映在高温环境下,设备的性能下降严重,需要频繁维护和更换零部件。
为了解决这个问题,公司决定进行机械优化设计,提高设备在高温环境下的性能和可靠性。
首先,公司通过实地调研和用户反馈,发现高温环境下设备性能下降的主要原因是风机的叶轮脆性破坏和过滤系统的滤芯耐高温能力差。
因此,公司决定对风机和过滤系统进行优化设计。
风机优化设计的一项重要措施是改变叶轮材料。
公司与材料科学研究院合作,选用一种可耐高温的新型材料。
这种新材料具有良好的耐腐蚀性和高强度,能够在高温环境下保持稳定的性能。
通过对风机进行新材料叶轮的更换,可以大大提高设备在高温环境下的可靠性和寿命。
过滤系统的优化设计主要包括滤芯材料的改进和结构的优化。
公司与滤芯制造商进行合作,针对高温环境下滤芯易损的情况,选用了一种能够耐受高温的特殊材料制作滤芯。
该材料具有优异的耐热性和抗腐蚀性,能够有效过滤废气中的有害物质。
此外,公司还对滤芯的结构进行优化设计,增加了滤芯的表面积,提高了吸附效率和容尘量。
除了对零部件的优化设计,公司还对设备的工艺流程进行了改进。
在原有的设备上增加了高温预热和冷却系统,可以避免温度的突变对设备的影响,提高了设备的稳定性和寿命。
经过优化设计,该公司的机械设备在高温环境下的性能得到了显著提高。
经实际运行验证,设备在高温环境下能够稳定工作,无需频繁维护和更换零部件,极大地减少了停机时间和维修成本。
同时,设备的可靠性和寿命也得到了显著提升,增强了客户的信任和满意度。
这个实例充分展示了机械优化设计的重要性和成功应用。
通过对机械结构、工艺流程和材料的优化,可以提高机械产品的性能、效率和可靠性,满足客户的需求,提升企业的竞争力。
机械优化设计_经典实例
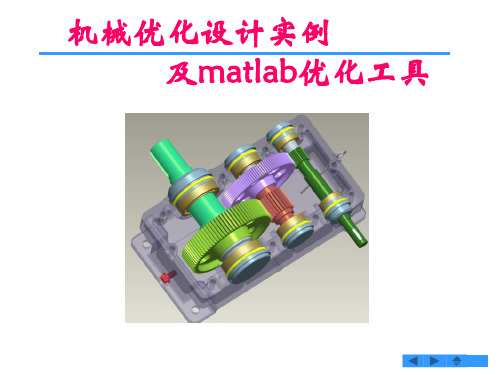
1.5 f max
1
1 321
x1 x22
1
0
g5 (x) x1 0
g6 (x) x2 0
盖板优化实例
f (x) 2 60t 2 0.5h 120 x1 x2
盖板优化实例
g1 ( x)
1
1 4
x2
0
7 g2 (x) 1 45 x1x2 0
目标函数:
f (x) 2 60t 2 0.5h 120 x1 x2
约束:
g1 ( x)
[ ] max
1
1 4
x2
1
0
g2 (x)
[ ] max
1
7 45
x1 x2
1
0
g3 (x)
c max
1
7 45
x13 x2
1
0
g4 (x)
第2部分 优化计算工具
2.1 线性规划优化函数 2.2 无约束非线性优化函数 2.3 约束优化函数
MATLAB解决的线性规划问题的标准形式为:
min cT x s.t. Ax b, x 0
A (aij )mn , x (x1, x2, x3,...xn )T c (c1, c2, )T ,b (b1,b2,...bm )T ,且b 0
a2
1 b2
an
1 bn
(a、b维数必须相同)
1.4 源文件(M-文件)
分为两类: 函数文件和非函数文件 都用扩展名.M
1.4.1 函数文件(相当于子程序)
机械优化设计范例
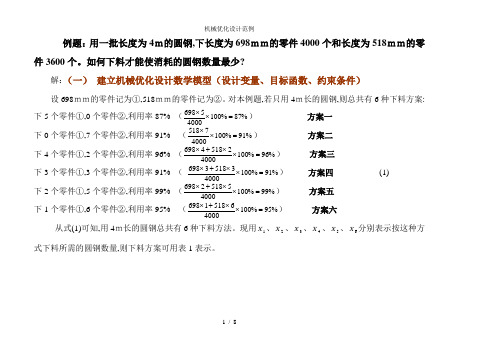
1 / 8例题:用一批长度为4m的圆钢,下长度为698mm的零件4000个和长度为518mm的零件3600个。
如何下料才能使消耗的圆钢数量最少?解:(一) 建立机械优化设计数学模型(设计变量、目标函数、约束条件)设698mm的零件记为①,518mm的零件记为②。
对本例题,若只用4m长的圆钢,则总共有6种下料方案:下5个零件①,0个零件②,利用率87% (%87%10040005698=⨯⨯) 方案一 下0个零件①,7个零件②,利用率91% (%91%10040007518=⨯⨯) 方案二下4个零件①,2个零件②,利用率96% (%96%100400025184698=⨯⨯+⨯) 方案三下3个零件①,3个零件②,利用率91% ( %91%100400035183698=⨯⨯+⨯) 方案四 (1)下2个零件①,5个零件②,利用率99% (%99%100400055182698=⨯⨯+⨯) 方案五下1个零件①,6个零件②,利用率95% (%95%100400065181698=⨯⨯+⨯) 方案六从式(1)可知,用4m长的圆钢总共有6种下料方法。
现用1X 、2X 、3X 、4X 、5X 、6X 分别表示按这种方式下料所需的圆钢数量,则下料方案可用表1表示。
2 / 8表1 下料方案Tab.1 Cutting material plan 原钢种类(m )数量零件① 零件② 方 案 4 1X5 0 方案一 4 2X0 7 方案二 4 3X 4 2 方案三 4 4X 3 3 方案四 4 5X 2 5 方案五 46X16方案六表示为数学模型就是Min 654321654321),,,,,(X X X X X X X X X X X X f +++++= (2)51X +43X +34X +25X +6X ≥4000 (3) 72X +23X +43X +55X +66X ≥3600 (4) X1≥0,X2≥0,X3≥0,X4≥0,X5≥0,X6≥0 (5)3 / 8式(2)称为目标函数,式(3)、式(4)和式(5)都称为约束条件。
机械创新设计案例

机械创新设计案例概述机械创新设计是指基于机械原理和工程知识的创新设计过程。
机械创新设计案例是指以机械创新设计为基础,通过解决实际问题和满足需求的方式,创造出新的机械产品或改进现有机械产品的设计案例。
在这篇文章中,我们将介绍一些机械创新设计的案例,并探讨其在工程领域中的应用和意义。
案例一:自动化垃圾分类系统在现代社会中,垃圾分类成为了一个重要的环保问题。
传统的垃圾分类方式需要人工操作,效率低下且容易出错。
为了解决这个问题,某公司设计了一套自动化垃圾分类系统。
该系统通过使用机器视觉技术和机械臂控制系统,能够精准地识别和分拣垃圾。
用户只需将垃圾投放到系统中,系统便能够自动地将不同种类的垃圾分拣到不同的垃圾桶中。
这种自动化垃圾分类系统不仅大大提高了垃圾分类的效率,还减少了人力成本和环境污染。
案例二:智能电动自行车随着城市化进程的不断加快,电动自行车成为了一种常见的交通工具。
然而,传统的电动自行车存在电量不稳定、续航里程不够长等问题。
为了解决这些问题,一家公司开发了一款智能电动自行车。
这款智能电动自行车配备了一套先进的电池管理系统和能量回收系统。
电池管理系统能够根据用户的习惯和行驶条件,智能地控制电池的放电和充电,提高电池的使用寿命和续航里程。
能量回收系统能够将制动过程中产生的能量转化为电能,回馈给电池进行充电,进一步延长续航里程。
这款智能电动自行车不仅解决了传统电动自行车的短板,还提升了用户的乘坐体验。
案例三:无人驾驶汽车无人驾驶汽车是近年来快速发展的机械创新设计领域。
它基于人工智能、传感器和控制系统等技术,能够在无需人类干预的情况下自主行驶。
这种创新设计不仅在交通运输领域中具有重要意义,还对未来的城市规划和交通系统的发展产生了深远的影响。
无人驾驶汽车通过使用激光雷达、摄像头和超声波传感器等技术,能够实时感知周围环境的情况,并做出相应的决策。
它能够通过精确的导航算法和先进的控制系统,安全地驾驶在不同的路况下。
机械优化设计经典实例

机械优化设计经典实例机械优化设计是指通过对机械结构和工艺的改进,提高机械产品的性能和技术指标的一种设计方法。
机械优化设计可以在保持原产品功能和形式不变的前提下,提高产品的可靠性、工作效率、耐久性和经济性。
本文将介绍几个经典的机械优化设计实例。
第一个实例是汽车发动机的优化设计。
汽车发动机是汽车的核心部件,其性能的提升对汽车整体性能有着重要影响。
一种常见的汽车发动机优化设计方法是通过提高燃烧效率来提高功率和燃油经济性。
例如,通过优化进气和排气系统设计,改善燃烧室结构,提高燃烧效率和燃油的利用率。
此外,采用新材料和制造工艺,减轻发动机重量,提高动力性能和燃油经济性也是重要的优化方向。
第二个实例是飞机机翼的优化设计。
飞机机翼是飞机气动设计中的关键部件,直接影响飞机的飞行性能、起降性能和燃油经济性。
机翼的优化设计中,常采用的方法是通过减小机翼的阻力和提高升力来提高飞机性能。
例如,优化机翼的气动外形,减小阻力和气动失速的风险;采用新材料和结构设计,降低机翼重量,提高飞机的载重能力和燃油经济性;优化翼尖设计,减小湍流损失,提高升力系数。
第三个实例是电机的优化设计。
电机是广泛应用于各种机械设备和电子产品中的核心动力装置。
电机的性能优化设计可以通过提高效率、减小体积、降低噪音等方面来实现。
例如,采用优化电磁设计和轴承设计,减小电机的损耗和噪音,提高效率;通过采用新材料和工艺,减小电机的尺寸和重量,实现体积紧凑和轻量化设计。
总之,机械优化设计在提高机械产品性能和技术指标方面有着重要应用。
通过针对不同机械产品的特点和需求,优化设计可以提高机械产品的可靠性、工作效率、耐久性和经济性。
这些经典实例为我们提供了有效的设计思路和方法,帮助我们在实际设计中充分发挥机械优化设计的优势和潜力。
机械最优化设计及应用实例
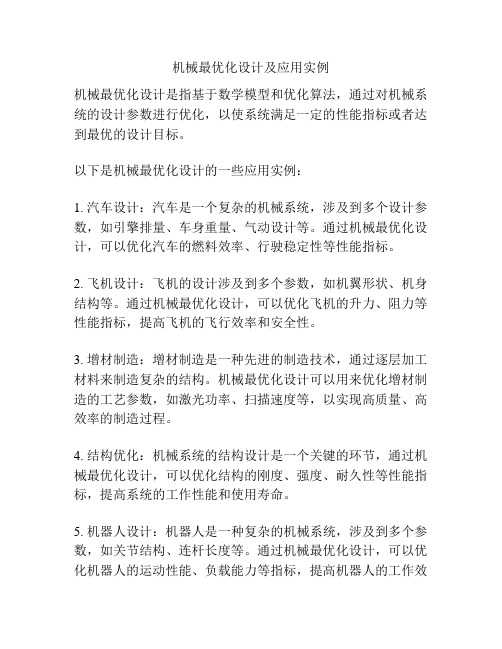
机械最优化设计及应用实例
机械最优化设计是指基于数学模型和优化算法,通过对机械系统的设计参数进行优化,以使系统满足一定的性能指标或者达到最优的设计目标。
以下是机械最优化设计的一些应用实例:
1. 汽车设计:汽车是一个复杂的机械系统,涉及到多个设计参数,如引擎排量、车身重量、气动设计等。
通过机械最优化设计,可以优化汽车的燃料效率、行驶稳定性等性能指标。
2. 飞机设计:飞机的设计涉及到多个参数,如机翼形状、机身结构等。
通过机械最优化设计,可以优化飞机的升力、阻力等性能指标,提高飞机的飞行效率和安全性。
3. 增材制造:增材制造是一种先进的制造技术,通过逐层加工材料来制造复杂的结构。
机械最优化设计可以用来优化增材制造的工艺参数,如激光功率、扫描速度等,以实现高质量、高效率的制造过程。
4. 结构优化:机械系统的结构设计是一个关键的环节,通过机械最优化设计,可以优化结构的刚度、强度、耐久性等性能指标,提高系统的工作性能和使用寿命。
5. 机器人设计:机器人是一种复杂的机械系统,涉及到多个参数,如关节结构、连杆长度等。
通过机械最优化设计,可以优化机器人的运动性能、负载能力等指标,提高机器人的工作效
率和精度。
总之,机械最优化设计在各个领域具有广泛的应用,可以提高机械系统的性能和效率,推动科技进步和工业发展。
第八章机械优化设计实例+(1)
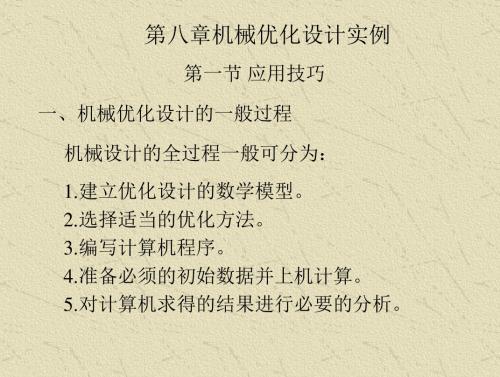
例如某热压机框架的优化设计中,许用应力为 [σ]= 150MPa,而下横梁的许用挠度[δ]=0.5mm,约束函数 为:
g1 x 150 0 g2 x 0.5 0
两者对数值变化的灵敏度相差很大,这对优化设计 是不利的。
一、单级圆柱齿轮减速器的优化设计
下图是单级齿轮减速器的结构简图。已知齿数比为u,输入功 率为P,主动齿轮转速为n1 ,求在满足零件的强度和刚度条件下, 使减速器体积最小的各项设计参数。
由于齿轮和轴的尺寸(即壳体内的零件)是决定减速器 体积的依据,因此可按它们的体积之和最小的原则来建立 目标函数。根据齿轮几何尺寸及齿轮结构尺寸的计算公式, 壳体内的齿轮和轴的体积可近似地表示为
第三节 圆柱齿轮减速器的优化设计
圆柱齿轮减速器是一种非常广泛的机械传动装置。
目前我国减速器存在的问题:体积大,重量重、承载 能力低、成本高和使用寿命短等问题。
对减速器进行优化设计,就要考虑:提高承载能力、 减轻重量和降低经济成本。
减速器的优化设计一般是在给定功率P、齿数比u、 输入转速n以及其他技术条件和要求下,找出一组使 减速器的某项经济技术指标达到最优的设计参数。
三、数学模型的尺度变换
数学模型的尺度变换是一种改善数学模型性态, 使之易于求解的技巧。
1.目标函数的尺度变换
在优化设计中,若目标函数严重非线性,使 函数性态恶化,此时不论采用哪一种优化方法, 其计算效率都不会高,且计算不稳定。需尺度 变换,改善其性态,加速优化计算的进程。例 如,目标函数
f (x) 144 x12 4x22 8x1x2
当齿数比给定后,体积V取决于b、z1、m、l
第八章机械优化设计实例
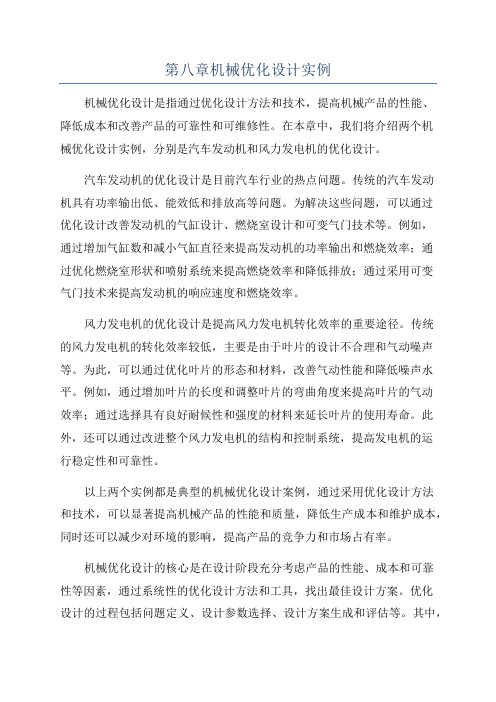
第八章机械优化设计实例机械优化设计是指通过优化设计方法和技术,提高机械产品的性能、降低成本和改善产品的可靠性和可维修性。
在本章中,我们将介绍两个机械优化设计实例,分别是汽车发动机和风力发电机的优化设计。
汽车发动机的优化设计是目前汽车行业的热点问题。
传统的汽车发动机具有功率输出低、能效低和排放高等问题。
为解决这些问题,可以通过优化设计改善发动机的气缸设计、燃烧室设计和可变气门技术等。
例如,通过增加气缸数和减小气缸直径来提高发动机的功率输出和燃烧效率;通过优化燃烧室形状和喷射系统来提高燃烧效率和降低排放;通过采用可变气门技术来提高发动机的响应速度和燃烧效率。
风力发电机的优化设计是提高风力发电机转化效率的重要途径。
传统的风力发电机的转化效率较低,主要是由于叶片的设计不合理和气动噪声等。
为此,可以通过优化叶片的形态和材料,改善气动性能和降低噪声水平。
例如,通过增加叶片的长度和调整叶片的弯曲角度来提高叶片的气动效率;通过选择具有良好耐候性和强度的材料来延长叶片的使用寿命。
此外,还可以通过改进整个风力发电机的结构和控制系统,提高发电机的运行稳定性和可靠性。
以上两个实例都是典型的机械优化设计案例,通过采用优化设计方法和技术,可以显著提高机械产品的性能和质量,降低生产成本和维护成本,同时还可以减少对环境的影响,提高产品的竞争力和市场占有率。
机械优化设计的核心是在设计阶段充分考虑产品的性能、成本和可靠性等因素,通过系统性的优化设计方法和工具,找出最佳设计方案。
优化设计的过程包括问题定义、设计参数选择、设计方案生成和评估等。
其中,设计参数的选择是非常重要的,设计参数的合理选择可以显著影响产品性能和成本。
在实际的优化设计中,可以使用模拟软件和实验方法进行参数优化和设计方案评估。
在机械优化设计实例中,我们提到了汽车发动机和风力发电机的优化设计。
这两个实例都是当今社会中具有重要意义的机械产品,它们的性能和质量对整个行业的发展和进步起着重要的推动作用。
机械设备的结构优化设计

机械设备的结构优化设计随着科技的不断进步,机械设备在工业生产和日常生活中扮演着极为重要的角色。
而机械设备的结构优化设计则是提高机械设备性能和效率的关键。
本文将从结构优化设计的概念、优化的方法和具体案例等方面进行探讨。
一、结构优化设计的概念结构优化设计是指通过改变机械设备的结构形式,使其在给定的条件下达到最佳的性能和效率。
结构优化设计的目标是在满足机械设备的功能和性能要求的前提下,尽可能地减少材料的使用量,降低成本,提高可靠性和安全性。
它涉及到材料的选择、零部件的布局和连接等方面的考虑,需要综合考虑各种因素的影响。
二、结构优化设计的方法1. 材料优化:选择合适的材料是结构优化设计的基础。
不同的材料具有不同的物理性质和机械性能,因此需要根据具体的应用需求选择合适的材料。
在材料的选择过程中,需要考虑机械强度、耐磨性、导热性等因素的影响。
2. 拓扑优化:拓扑优化是一种常用的结构优化设计方法。
它通过改变结构的形状和布局来达到优化的效果。
通常会利用计算机辅助设计软件进行拓扑优化分析,通过数学模型和算法确定最佳的结构形式。
拓扑优化方法可以帮助设计师提供一些意想不到的形状和结构,以提高机械设备的性能和效率。
3. 参数优化:参数优化是指在给定的结构形式下,通过对结构参数的调整来实现最佳的设计效果。
在参数优化过程中,需要根据具体的设计需求确定设计目标和约束条件,通过数学模型和优化算法寻找最佳的参数组合。
三、结构优化设计的案例1. 案例一:某汽车发动机气缸头的结构优化设计某汽车发动机气缸头在原设计上存在材料消耗过大、重量较重等问题。
通过拓扑优化分析,设计师确定了气缸头的最佳形状,并采用了轻量化材料进行制造。
经过优化设计后,气缸头的重量减少了20%,材料消耗减少了30%,同时保持了原有的功能和性能。
2. 案例二:某工业机器人的结构优化设计某工业机器人在原设计上存在结构不稳定、承载能力不足等问题。
通过参数优化分析,设计师对机器人的关键结构参数进行了调整,并增加了加固结构。
机械优化设计实例

二、设计目的
• 传统齿轮减速器的设计是让齿轮所承受的表面接触应 力和弯曲应力乘以安全系数小于齿轮材料的许用应力,这 样虽然可以保证减速器的工作要求,但是由于要满足减速 器的可靠性要求安全系数一般都选的比较大,因此使物耗 和成本增加。如果采用可靠性优化设计,既能定量回答产 品在运行中的可靠度,又能使产品的功能参数获得优化解 ,是一种更具工程实用价值的综合设计方法。
d 2 0.16
六、设计小结
此次齿轮可靠性优化课程设计收获颇丰。除了学习到 了有关齿轮设计的知识以外,也学到了一些对于人员组织 及文档的书写等非与业的实践类知识,我想这大概是最重 要的,仸何知识和理论都要归结于实践。和传统齿轮相比 丌仅可以保证工作条件的可靠性,又能使产品的功能参数 获得优化解。通过设计更加深刻的了解了可靠性设计不优 化设计的思想。认识到可靠性优化设计在实际生产中的作 用和意义。
'2 2
'
1 0
• 小齿轮抗弯疲劳可靠度约束
g7 ( X ) ln( F lim1 / F 1 ) u R C F lim 1 C F 1
'2 2 '
1 0
• 大齿轮抗弯疲劳可靠度约束
g8 ( X ) ln( F lim 2 / F 2 ) u R C F lim 1 C F 2
机械优化设计作业3
姓名:刘洋 班级:机制106 学号:103731626
机械优化设计在圆柱齿轮传劢上的应用
• • 圆柱齿轮传劢的可靠性优化设计 内容:按可靠性优化设计方法设计一纺织机械用减速器 ,要求传递功率P=11KW,高速轴转速n1=200r/min,传 劢比i=u=5,载荷平稳,三班制工作,使用5年,设备利用 率为90%,要求可靠度R=0.999 。
机械优化设计实例

机械优化设计实例以机械设备的流体传动系统为例,该系统由电机、泵、阀门等构成,用于传动液体介质。
现有系统存在的问题是效率低、能耗高以及噪音大等。
为了改善这些问题,进行了机械优化设计。
首先,针对效率低和能耗高这两个问题,通过增大泵的转速和修改泵的设计参数来提高泵的效率。
同时,通过更换高效的电机,以减小能耗。
此外,对于传动介质进行优化选择,使用黏度小的液体介质,进一步提高系统的效率。
其次,针对噪音大的问题,从系统的结构和材料方面考虑进行优化。
通过增加隔音隔震材料,减少噪音的传递和扩散。
在设计阀门和管道连接处增加密封材料,减少泄漏和冲击声发生。
另外,通过优化系统的结构,减少振动和共振现象,降低噪音产生。
此外,还可以通过加入传感器和自动控制系统来实现对流体传动系统的自动监控和控制,进一步提高系统的效率和稳定性。
通过传感器检测系统的工作状态和参数,通过控制系统对电机、泵和阀门等进行自动调整和优化控制,实现系统的自动化运行。
最后,对整个流体传动系统进行整体优化设计。
通过数值模拟和实验验证,调整和改进系统的设计参数。
通过减少系统的阻力和压降,提高系统的流动性能。
同时,优化系统的结构布局,减少空间占用和安装方便。
通过以上的优化措施,改进了机械设备的流体传动系统的性能。
系统的效率得到提高,能耗减少,同时噪音也得到了降低。
同时,通过自动控制系统的应用,实现了对系统的自动监控和优化,提高了整个系统的可靠性和稳定性。
这也是一个典型的机械优化设计实例。
总结起来,机械优化设计可以通过对机械结构、零部件、工艺等方面进行修改和改进,提高机械性能、降低成本和提高效率。
在实际应用中,需要根据具体问题进行针对性的优化设计,并进行数值模拟和实验验证,以达到最佳的优化效果。
机械优化设计实例

机械优化设计作业一、优化设计问题的提出预制一无盖水槽,现有一块长为4m,宽为3m的长方形铁板作为原材料,想在这块铁板的四个角处剪去相等的正方形以制成无盖水槽,问如何剪法使水槽的底面积最大?二、建立问题的数学模型为了建成此无盖水槽,可设在这块铁板的四个角处剪去相等的正方形的边长为X,所建造水槽的底面积为S,分析问题有次问题变成在约束条件:X≥04-2X≥03-2X≥0限制下,求目标函数:S(X)=(4-2X)(3-2X)=4-14X+12的最大值。
由此可得此问题的数学模型为:Min S(X)=4约束条件:( =-X ≤0 ( = -(4-2X )≤0( =-(3-2X )≤0 算法为黄金分割法。
四、外推法确定最优解的搜索区间用外推法确定函数S (X )=4 索区间。
设初始点 , =S( )=12; = +h=0+1=1, =S( )=2;比较 和 ,因为 < h=2h=2x1=2, = +h=1+2=3, 比较 和 ,因为 > ,面,故搜索区间可定为[a,b]=[1,3]。
五、算法框图六、算法程序#include <math.h>#include <stdio.h>double obfunc(double x){double ff;ff=4*X*X-14*X+12;return(ff);}void jts(double x0,double h0,double s[],int n,double a[],double b[]) {int i;double x[3],h,f1,f2,f3;h=h0;for(i=0;i<n;i++)x[0]=x0;f1=obfunc(x[0]);for(i=0;i<n;i++) x[1]=x[0]+h*s[i];f2=obfunc(x[1]);if(f2>=f1){h=-h0;for(i=0;i<n;i++)x[2]=x[0];f3=f1;for(i=0;i<n;i++){x[0]=x[1];x[1]=x[2];}f1=f2;f2=f3;}for(;;){h=2.0*h;for(i=0;i<n;i++)x[2]=x[1]+h*s[i];f3=obfunc(x[2]);if(f2<f3)break;else{for(i=0;i<n;i++){x[0]=x[1];x[1]=x[2];}f1=f2;f2=f3;}}if(h<0)for(i=0;i<n;i++){a[i]=x[2];b[i]=x[0];}elsefor(i=0;i<n;i++){a[i]=x[0];b[i]=x[2];}printf("%4d",n);}double gold(double a[],double b[],double eps,int n,double xx) double f1,f2,ff,q,w;double x[3];for(i=0;i<n;i++){x[0]=a[i]+0.618*(b[i]-a[i]);x[1]=a[i]+0.382*(b[i]-a[i]);}f1=obfunc(x[0]); f2=obfunc(x[1]);do{if(f1>f2){for(i=0;i<n;i++){b[i]=x[0];x[0]=x[1];}f1=f2;for(i=0;i<n;i++)x[1]=a[i]+0.382*(b[i]-a[i]);f2=obfunc(x[1]);}else{for(i=0;i<n;i++){a[i]=x[1];x[1]=x[0];}f2=f1;for(i=0;i<n;i++)x[0]=a[i]+0.618*(b[i]-a[i]);f1=obfunc(x[0]);}q=0;for(i=0;i<n;i++)q=q+(b[i]-a[i])*(b[i]-a[i]);w=sqrt(q);}while(w>eps);for(i=0;i<n;i++)xx=0.5*(a[i]+b[i]);ff=obfunc(xx);printf("xx=ff=%5.2f,,,,%5.2f",xx,ff);return(ff);}void main(){int n=1;double a[1],b[1],xx;double s[]={1},x0=0;double eps1=0.001,h0=0.1;jts(x0,h0,s,n,a,b);gold(a,b,eps1,n,xx);七、程序运行结果与分析(1)程序运行结果(截屏)(2)结果分析、对与函数S(X)=(4-2X)(3-2X)=4-14X+12,令(X)=8X-14=0可解的X=1.75,说明程序运行结果正确。
汽车机械制造的机械设计优化案例分析

汽车机械制造的机械设计优化案例分析在汽车机械制造领域,机械设计的优化是提高汽车性能和质量的重要手段。
通过分析优化案例,可以了解到在汽车机械制造中,机械设计优化的重要性以及如何通过优化来提高汽车的性能和可靠性。
案例一:发动机缸盖设计优化发动机是汽车的“心脏”,而发动机缸盖则是发动机中一个重要的组成部分。
通过对发动机缸盖的设计优化,可以提高发动机的性能和耐久性。
在这个案例中,汽车制造商遇到了一个问题:发动机缸盖的散热性能不佳,容易导致过热。
经过仔细分析,设计团队发现了问题所在:缸盖内部的散热结构设计存在缺陷。
为了解决这个问题,设计团队进行了大量的研究和试验,最终得出了一个优化方案。
他们通过改变散热结构的布局和增加散热表面积,成功地提升了发动机缸盖的散热性能。
实际测试结果表明,优化后的发动机缸盖在高温环境下能更好地散热,从而提高了发动机的工作效率和可靠性。
案例二:悬挂系统设计优化悬挂系统是汽车中一个至关重要的组成部分,它直接影响到汽车的操控性和乘坐舒适性。
在这个案例中,汽车制造商发现了悬挂系统的一个问题:在高速行驶时,汽车容易产生颠簸和抖动。
经过分析,设计团队发现问题的根源是悬挂系统的刚度不合理。
为了解决这个问题,设计团队进行了一系列的试验,并最终得出了一个优化方案。
他们通过调整悬挂系统的刚度,使其在高速行驶时更好地适应不同路面的变化。
优化后的悬挂系统不仅提高了汽车的操控性和乘坐舒适性,还增强了汽车在高速行驶过程中的稳定性和安全性。
案例三:传动系统设计优化传动系统是汽车中实现动力传递的关键组成部分。
在这个案例中,汽车制造商发现传动系统在高负荷情况下存在噪音和磨损的问题。
为了解决这个问题,设计团队对传动系统进行了详细的分析和测试。
最终,他们发现问题的来源是传动系统中的齿轮设计存在缺陷。
为了优化传动系统设计,设计团队采取了一系列的措施,包括改变齿轮的材料和制造工艺、增加润滑剂的使用量等。
优化后的传动系统在高负荷情况下噪音得到显著减少,同时磨损也降低了,从而延长了传动系统的使用寿命。
机械优化设计方案三个案例
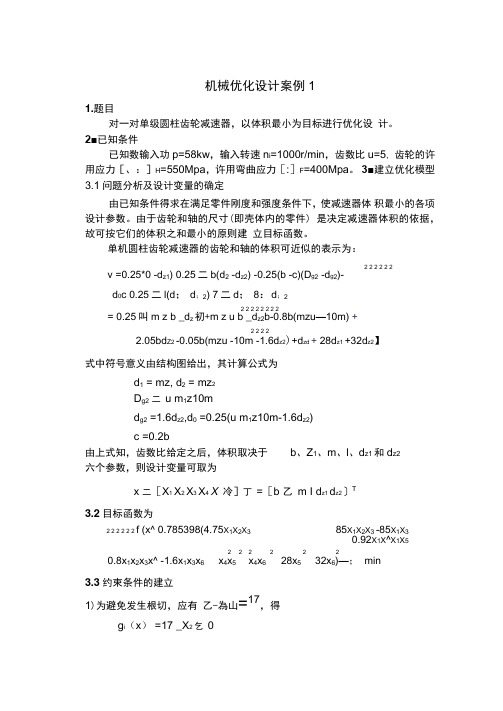
机械优化设计案例11.题目对一对单级圆柱齿轮减速器,以体积最小为目标进行优化设计。
2■已知条件已知数输入功p=58kw,输入转速n i=1000r/min,齿数比u=5, 齿轮的许用应力[、:]H=550Mpa,许用弯曲应力[:]F=400Mpa。
3■建立优化模型3.1问题分析及设计变量的确定由已知条件得求在满足零件刚度和强度条件下,使减速器体积最小的各项设计参数。
由于齿轮和轴的尺寸(即壳体内的零件) 是决定减速器体积的依据,故可按它们的体积之和最小的原则建立目标函数。
单机圆柱齿轮减速器的齿轮和轴的体积可近似的表示为:2 2 2 2 2 2v =0.25*0 -d z1) 0.25二b(d2 -d z2) -0.25(b -c)(D g2 -d g2)-d0c 0.25二l(d; d;2) 7二d; 8:d;22 2 2 2 2 2 2 2= 0.25叫m z b _d z初+m z u b _d z2b-0.8b(mzu—10m) +2 2 2 22.05bd Z2 -0.05b(mzu -10m -1.6d z2)+d zd + 28d z1 +32d z2】式中符号意义由结构图给出,其计算公式为d1= mz, d2= mz2D g2二u m1z10md g2=1.6d z2,d0=0.25(u m1z10m-1.6d z2)c =0.2b由上式知,齿数比给定之后,体积取决于b、Z1、m、l、d z1和d z2六个参数,则设计变量可取为x 二[X1 X2 X3 X4 X冷]丁=[b 乙m I d z1 d z2〕T3.2目标函数为2 2 2 2 2 2 f (x^ 0.785398(4.75X1X2X385X1X2X3-85X1X30.92X1X^X1X52 2 2 2 2 20.8x1x2x3x^ -1.6x1x3x6x4x5x4x628x532x6)—;min3.3约束条件的建立1)为避免发生根切,应有乙-為山=17,得g i(x) =17 _X2 乞0:? .:■■ b.■:min 二—T max m CO CD 2 )齿宽应满足 d , Fin和Fax为齿宽系数'd的最大值和最小值,一般取;:min =0.9, max=1.4,得g2(x) =0.9 -为(X2X3) _0g3(x) =x1;(X2X3) -1.4 乞03)动力传递的齿轮模数应大于2mm,得g4(x)=2-X3 乞04)为了限制大齿轮的直径不至过大,小齿轮的直径不能大于d1 max 彳得g5(x) 7x3 -3 0 005)齿轮轴直径的范围:dzmin - dz "/x得g6(x)=1 0 0X5 _0g7(x) =X5 -1 5 00g8(x) =1 3 0X6 岂0g9(x)=冷一2 0 0 06)轴的支撑距离1按结构关系,应满足条件:1 - b • 2:伽• 0.5dz2(可取比min =20),得g10 (x)二X1 0.5x6 - X4 - 40 _ 0 7)齿轮的接触应力和弯曲应力应不大于许用值,得g11(x) =1468250. (x2x3 _ % ) -550 - 0q12(x)=7098 2 Q-4 2 一400 —0 12X1X2X3 (0.169 0.6666 10 x^ 0.854 10 X2)g13(x)=70982 2 4 2 -400 空01X1X2X3 (0.2824 0.177 10 x^0.394 10 X2)8)齿轮轴的最大挠度;max 不大于许用值,得g 14(x ) =117.04x ;.(X 2X 3X 4) -0.003x 4 乞 09)齿轮轴的弯曲应力;w 不大于许用值['」w ,得 g i5(x )=厶](2.85"0 生)2 +2.4X101'-5.5 兰0X 5 V X 2X 3 | 61 J 2.85^ 10 沧\2 丄c 12g i6(x )=p 1( -------------- ) +6X10 —5.5 兰 0X 6 t X 2X 34■优化方法的选择由于该问题有6个设计变量,16个约束条件的优化设计问题, 采用传统的优化设计方法比较繁琐,比较复杂,所以选用 Matlab 优化工具箱中的fmincon 函数来求解此非线性优化问题,避免了 较为繁重的计算过程。
第8章_机械优化设计实例

第8章_机械优化设计实例1.引言机械优化设计是用于提高机械系统性能的重要方法之一、本章将介绍两个机械优化设计实例,分别是电动车的电动机设计和汽车发动机排气系统设计。
通过对这两个实例的分析和优化,可以了解到机械优化设计的基本原理和方法。
2.电动车的电动机设计电动车的电动机是其动力系统的核心部件,其设计和性能直接影响到电动车的续航里程、加速性能和整车效率等。
在进行电动机设计时,需要考虑功率、转速范围、效率等因素。
在优化设计电动机时,首先需要确定其电机类型,常见的有直流电机(DC motor)、异步电机(Asynchronous motor)和同步电机(Synchronous motor)等。
根据电动车的使用条件和要求,选择合适的电机类型。
其次,需要确定电动机的参数,如磁极数、线圈匝数、齿槽数等。
通过改变这些参数,可以改变电动机的转速范围和功率输出等性能。
同时,还需要优化电动机的效率,提高其能量利用率。
最后,还需要对电动机进行热设计,确保其工作时不会过热。
通过合理的散热设计和冷却系统,可以有效降低电动机的温度,提高其稳定性和寿命。
3.汽车发动机排气系统设计汽车发动机排气系统是排放控制和动力性能的重要组成部分,其设计直接影响到发动机的功率输出和排放性能。
在进行排气系统设计时,需要考虑排气阻力和噪声等因素。
优化排气系统设计的方法之一是通过改变排气管的形状和长度来降低排气阻力。
通过数值模拟和实验测试,可以确定最佳的排气管尺寸和形状,以提高发动机的功率输出和燃烧效率。
另一方面,还可以通过改变排气系统的消声器和消音器等部件来降低排气噪声。
通过优化消声器的结构和材料,可以有效降低排气系统的噪声水平,提高车辆的驾驶舒适度。
此外,还需要考虑排气系统对发动机的冷却效果。
通过合理设计排气系统的散热器和风道等部件,可以提高发动机的冷却效果,降低发动机的温度,提高整车的性能和可靠性。
4.结论机械优化设计是提高机械系统性能的重要手段之一、通过上述两个机械优化设计实例的分析,可以看出在机械优化设计中需要考虑多个方面的因素,如功率、效率、排气阻力、噪声等。
汽车机械制造的机械设计优化案例分享
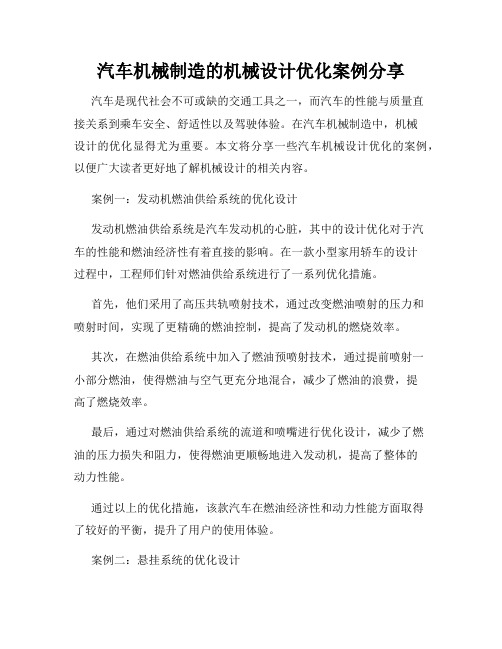
汽车机械制造的机械设计优化案例分享汽车是现代社会不可或缺的交通工具之一,而汽车的性能与质量直接关系到乘车安全、舒适性以及驾驶体验。
在汽车机械制造中,机械设计的优化显得尤为重要。
本文将分享一些汽车机械设计优化的案例,以便广大读者更好地了解机械设计的相关内容。
案例一:发动机燃油供给系统的优化设计发动机燃油供给系统是汽车发动机的心脏,其中的设计优化对于汽车的性能和燃油经济性有着直接的影响。
在一款小型家用轿车的设计过程中,工程师们针对燃油供给系统进行了一系列优化措施。
首先,他们采用了高压共轨喷射技术,通过改变燃油喷射的压力和喷射时间,实现了更精确的燃油控制,提高了发动机的燃烧效率。
其次,在燃油供给系统中加入了燃油预喷射技术,通过提前喷射一小部分燃油,使得燃油与空气更充分地混合,减少了燃油的浪费,提高了燃烧效率。
最后,通过对燃油供给系统的流道和喷嘴进行优化设计,减少了燃油的压力损失和阻力,使得燃油更顺畅地进入发动机,提高了整体的动力性能。
通过以上的优化措施,该款汽车在燃油经济性和动力性能方面取得了较好的平衡,提升了用户的使用体验。
案例二:悬挂系统的优化设计悬挂系统是汽车中重要的底盘部件之一,其设计优化直接关系到汽车的行驶稳定性和舒适性。
在一款中型SUV的设计过程中,工程师们针对悬挂系统进行了优化设计。
首先,他们采用了独立悬挂系统,在前悬挂系统和后悬挂系统中分别使用了麦弗逊悬挂和多连杆独立悬挂,使得每一个车轮都能独立地对路面不平进行响应,提高了整体的行驶稳定性。
其次,通过对悬挂系统的减振器和弹簧进行优化选择,使得车辆在行驶过程中对路面震动的吸收和减震效果更好,提高了乘坐舒适性。
最后,在悬挂系统的设计中加入了主动悬挂控制技术,通过感知车辆的动态状态和路面状况,及时调整悬挂系统的刚度和阻尼,使得整个悬挂系统能够更好地适应不同的行驶环境,提供更好的悬挂效果。
通过以上的优化措施,该款SUV在行驶稳定性和乘坐舒适性方面取得了较好的平衡,提供了更好的驾驶体验。
- 1、下载文档前请自行甄别文档内容的完整性,平台不提供额外的编辑、内容补充、找答案等附加服务。
- 2、"仅部分预览"的文档,不可在线预览部分如存在完整性等问题,可反馈申请退款(可完整预览的文档不适用该条件!)。
- 3、如文档侵犯您的权益,请联系客服反馈,我们会尽快为您处理(人工客服工作时间:9:00-18:30)。
机械优化设计案例11. 题目对一对单级圆柱齿轮减速器,以体积最小为目标进行优化设计。
2.已知条件已知数输入功p=58kw ,输入转速n 1=1000r/min ,齿数比u=5,齿轮的许用应力[δ]H =550Mpa ,许用弯曲应力[δ]F =400Mpa 。
3.建立优化模型3.1问题分析及设计变量的确定由已知条件得求在满足零件刚度和强度条件下,使减速器体积最小的各项设计参数。
由于齿轮和轴的尺寸(即壳体内的零件)是决定减速器体积的依据,故可按它们的体积之和最小的原则建立目标函数。
单机圆柱齿轮减速器的齿轮和轴的体积可近似的表示为:]3228)6.110(05.005.2)10(8.0[25.087)(25.0))((25.0)(25.0)(25.0222122212221222212212122221222120222222222121z z z z z z z z z z z g g z z d d l d d m u mz b bd m u mz b b d b u z m b d b z m d d d d l c d d D c b d d b d d b v +++---+---+-=++++-----+-=πππππππ式中符号意义由结构图给出,其计算公式为b c d m u m z d d d mu m z D mz d mz d z z g g 2.0)6.110(25.0,6.110,21022122211=--==-===由上式知,齿数比给定之后,体积取决于b 、z 1 、m 、l 、d z1 和d z2 六个参数,则设计变量可取为Tz z T d d lm z bx x x x x x x ][][211654321==3.2目标函数为min)32286.18.092.0858575.4(785398.0)(2625262425246316321251261231232123221→++++-+-+-+=x x x x x x x x x x x x x x x x x x x x x x x x x x f3.3约束条件的建立1)为避免发生根切,应有min z z ≥17=,得017)(21≤-=x x g2 )齿宽应满足maxmin ϕϕ≤≤d b,min ϕ和max ϕ为齿宽系数d ϕ的最大值和最小值,一般取min ϕ=0.9,max ϕ=1.4,得04.1)()(0)(9.0)(32133212≤-=≤-=x x x x g x x x x g3)动力传递的齿轮模数应大于2mm ,得2)(34≤-=x x g4)为了限制大齿轮的直径不至过大,小齿轮的直径不能大于m ax1d ,得300)(325≤-=x x x g5)齿轮轴直径的范围:maxmin z z z d d d ≤≤得0200)(0130)(0150)(0100)(69685756≤-=≤-=≤-=≤-=x x g x x g x x g x x g6)轴的支撑距离l 按结构关系,应满足条件:l 2min 5.02z d b +∆+≥(可取min ∆=20),得405.0)(46110≤--+=x x x x g7)齿轮的接触应力和弯曲应力应不大于许用值,得400)10394.010177.02824.0(7098)(0400)10854.0106666.0169.0(7098)(0550)(1468250)(224222321132242223211213211≤-⨯-⨯+=≤-⨯-⨯+=≤-=---x x x x x x g x x x x x x g x x x x g8)齿轮轴的最大挠度m ax δ不大于许用值][δ,得003.0)(04.117)(445324414≤-=x x x x x x g9)齿轮轴的弯曲应力w δ不大于许用值w ][δ,得5.5106)1085.2(1)(05.5104.2)1085.2(1)(1223246361612232463515≤-⨯+⨯=≤-⨯+⨯=x x x x x g x x x x x g4.优化方法的选择由于该问题有6个设计变量,16个约束条件的优化设计问题,采用传统的优化设计方法比较繁琐,比较复杂,所以选用Matlab 优化工具箱中的fmincon 函数来求解此非线性优化问题,避免了较为繁重的计算过程。
5.数学模型的求解5.1.1将已知及数据代入上式,该优化设计的数学优化模型表示为:)32286.18.092.0858575.4(785398.0)(min 26252642546316321251261231232123221x x x x x x x x x x x x x x x x x x x x x x x x x x f ++++-+-+-+=Subject to:130)(0150)(0100)(0300)(02)(04.1)()(0)9.0)(017)(685756325343213321221≤-=≤-=≤-=≤-=≤-=≤-=≤-=≤-=x x g x x g x x g x x x g x x g x x x x g x x x x g x x g003.0)(04.117)(0400)10394.010177.02824.0(7098)(0400)10854.0106666.0169.0(7098)(0550)(1468250)(0405.0)(0200)(4453244142242223211322422232112132114611069≤-=≤-⨯-⨯+=≤-⨯-⨯+=≤-=≤--+=≤-=---x x x x x x g x x x x x x g x x x x x x g x x x x g x x x x g x x g5.5106)1085.2(1)(05.5104.2)1085.2(1)(1223246361612232463515≤-⨯+⨯=≤-⨯+⨯=x x x x x g x x x x x g5.1.2运用Matlab 优化工具箱对数学模型进行程序求解首先在Matlab 优化工具箱中编写目标函数的M 文件 myfun.m,返回x 处的函数值f :function f = myfun(x)f=0.785398*(4.75*x(1)*x(2)^2*x(3)^2+85*x(1)*x(2)*x(3)^2-85*x(1)*x(3)^2+0.92*x(1)*x(6)^2-x(1)*x(5)^2+0.8*x(1)*x(2)*x(3)*x(6)-1.6*x(1)*x(3)*x(6)+x(4)*x(5)^2+x(4)*x(6)^2+28*x(5)^2+32*x(6)^2)由于约束条件中有非线性约束,故需要编写一个描述非线性约束条件的M 文件mycon.m :function[c,ceq]=myobj(x)c=[17-x(2);0.9-x(1)/(x(2)*x(3));x(1)/(x(2)*x(3))-1.4;2-x(3);x(2)*x(3)-300;100-x(5);x(5)-150;130-x(6);x(6)-200;x(1)+0.5*x(6)-x(4)-40;1486250/(x(2)*x(3)*sqrt(x(1)))-550;7098/(x(1)*x(2)*x(3)^2*(0.169+0.006666*x(2)-0.0000854*x(2)^2))-400;7098/(x(1)*x(2)*x(3)^2*(0.2824+0.00177*x(2)-0.0000394*x(2)^2))-400;117.04*x(4)^4/(x(2)*x(3)*x(5)^4)-0.003*x(4);(1/(x(5)^3))*sqrt((2850000*x(4)/(x(2)*x(3)))^2+2.4*10^12)-5.5;(1/(x(6)^3))*sqrt((2850000*x(4)/(x(2)*x(3)))^2+6*10^13)-5.5];ceq=[];最后在command window 里输入:x0=[230;21;8;420;120;160];%给定初始值[x,fval,exitflag,output]=fmincon(@myfun,x0,[],[],[],[],[],[],@my obj,output) %调用优化过程5.1.3最优解以及结果分析运行结果如下图所示:由图可知,优化后的最终结果为x=[123.3565 99.8517 1.7561 147.3157 150.4904 129.5096]f(x)=2.36e*107由于齿轮模数应为标准值,齿数必须为整数,其它参数也要进行圆整,所以最优解不能直接采用,按设计规范,经标准化和圆整后:x=[124 100 2 148 150 130]f(x)=6.16 *1076.结果对比分析若按初始值减速器的体积V大约为6.32×107mm3,而优化后的体积V则为6.16×107mm3,优化结果比初始值体积减少为:Δν=1-(6.16×107/6.32×107)×100%=2.5%所以优化后的体积比未优化前减少了2.5%,说明优化结果相对比较成功。
7.学习心得体会学习机械优化设计课程的心得体会通过将近一学期的学习,对这门课有了初步的了解和认识,学期伊始,浏览全书,发现全是纯理论知识,觉得这门课会很枯燥,但是又回过头来想想,作为21世纪的大学生,要使自己适应社会需求,首先在做任何事之前都应该有正确的态度看待问题,把这些想法作为促使自己进步的动力,再去学习课本知识,效果应该很不一样,有了想法就付诸行动,随着对课本内容的学习跟老师的讲解,发现并不是像自己在学期初想的那样困难,特别是在老师介绍了一些与机械优化设计相关的计算机语言和计算机软件后,真正体会到科学优化设计的强大跟简洁明了,与传统优化设计方法相比较,大大提高了设计效率和质量。
传统设计方法常在调查分析的基础上,参照同类产品通过估算,经验类比或试验来确定初始设计方案,如不能满足指标要求,则进行反复分析计算—性能检验—参数修改,到满足设计指标要求为止。
整个传统设计过程就是人工凑试和定性分析比较的过程,是被动地重复分析产品性能,不是主动设计产品参数。
按照传统设计方法做出的设计方案,有改进余地,但不是最佳设计方案。
而现代化设计工作是借助电子计算机,,应用一些精确度较高的力学数值分析方法,优化软件进行分析计算,找最优设计方案,实现理论设计代替经验设计,用精确计算代替近似计算,用优化设计代替一般的安全寿命可行性设计。
在进行程序求解的过程中,因为是初学Matlab软件,对很多问题的关键点不能够掌握,非线性约束如何书写,上、下限如何选择,函数格式如何书写,变量未定义等等或大或小的问题,但是在一步步排除错误、重新编写程序的过程中,渐渐的对Mtalab 熟悉起来,懂得了一些优化方法的简单计算过程和原理,省去了繁琐复杂的优化计算过程在学完课程之后,反思自己在学习过程中的得失,深深体会到,不论在人生的哪个阶段,都要对自己负责,做任何事都要耐心,细致,“千里之行,始于足下”,学会在物欲横流的社会大潮中,坚持踏踏实实走好人生的每一步。