生产线布局大全 SS
生产线布局大全
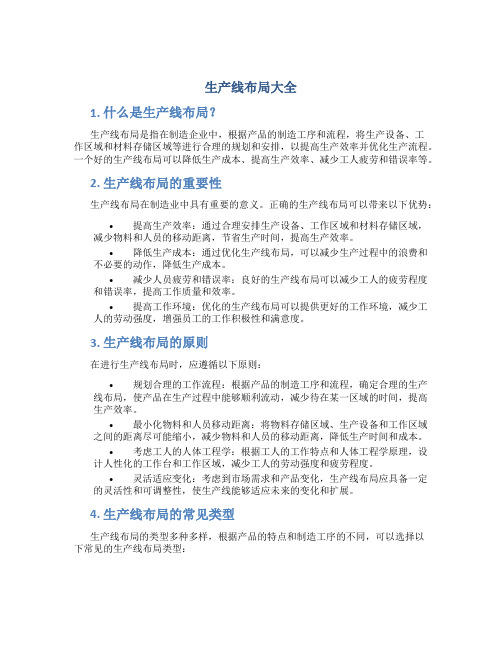
生产线布局大全1. 什么是生产线布局?生产线布局是指在制造企业中,根据产品的制造工序和流程,将生产设备、工作区域和材料存储区域等进行合理的规划和安排,以提高生产效率并优化生产流程。
一个好的生产线布局可以降低生产成本、提高生产效率、减少工人疲劳和错误率等。
2. 生产线布局的重要性生产线布局在制造业中具有重要的意义。
正确的生产线布局可以带来以下优势:•提高生产效率:通过合理安排生产设备、工作区域和材料存储区域,减少物料和人员的移动距离,节省生产时间,提高生产效率。
•降低生产成本:通过优化生产线布局,可以减少生产过程中的浪费和不必要的动作,降低生产成本。
•减少人员疲劳和错误率:良好的生产线布局可以减少工人的疲劳程度和错误率,提高工作质量和效率。
•提高工作环境:优化的生产线布局可以提供更好的工作环境,减少工人的劳动强度,增强员工的工作积极性和满意度。
3. 生产线布局的原则在进行生产线布局时,应遵循以下原则:•规划合理的工作流程:根据产品的制造工序和流程,确定合理的生产线布局,使产品在生产过程中能够顺利流动,减少待在某一区域的时间,提高生产效率。
•最小化物料和人员移动距离:将物料存储区域、生产设备和工作区域之间的距离尽可能缩小,减少物料和人员的移动距离,降低生产时间和成本。
•考虑工人的人体工程学:根据工人的工作特点和人体工程学原理,设计人性化的工作台和工作区域,减少工人的劳动强度和疲劳程度。
•灵活适应变化:考虑到市场需求和产品变化,生产线布局应具备一定的灵活性和可调整性,使生产线能够适应未来的变化和扩展。
4. 生产线布局的常见类型生产线布局的类型多种多样,根据产品的特点和制造工序的不同,可以选择以下常见的生产线布局类型:4.1 直线式布局直线式布局是最常见的生产线布局类型,也是最简单的一种。
生产设备按照产品的制造工序依次排列,形成一条直线。
这种布局适合于产品流程简单、制造周期短的情况。
4.2 U型布局U型布局是将直线式布局改为U型的形式,生产设备呈U形排列。
生产线布局方法

生产线布局方法生产线布局方法是一种重要的生产管理方法,它涉及到工厂内部生产线的规划和布局。
合理的生产线布局可以提高生产效率,降低生产成本,优化生产流程,提升产品质量。
本文将详细介绍几种常见的生产线布局方法,并探讨其优缺点。
1. 产品布局方法产品布局方法是按照产品的特点和生产工艺要求来布局生产线。
这种方法适用于产品种类少而相似的生产企业。
在产品布局方法中,相似的产品被放置在相邻的生产线上,这样可以减少生产过程中的切换和调整时间,提高生产效率。
然而,这种布局方法也有一些缺点,比如工艺相对复杂的产品可能会因为生产线之间的物料转移而导致生产过程中的错误。
2. 工艺布局方法工艺布局方法将生产线上的设备和工艺按照一定的顺序进行布局。
这种方法适用于具有复杂工艺流程的生产企业。
在工艺布局方法中,工序相同或者相似的设备被放置在相邻的位置,以便于操作人员进行监控和调整。
这种布局方法可以减少生产过程中的转移和运输时间,提高生产效率。
缺点是由于不同工艺的设备布置紧密,一旦出现故障可能会导致整个生产线停产。
3. 运输布局方法运输布局方法将生产线上的设备和工序按照物料运输路径进行布局。
这种方法适用于物料运输量大的生产企业。
在运输布局方法中,生产线上的设备被按照物料流动的方向进行布置,以减少物料运输的时间和成本。
这种布局方法可以确保物料在生产过程中的流动畅通,减少物料的堆积和阻塞。
然而,过于关注物料运输路径的设计可能会导致空间的浪费和设备利用率的降低。
4. 功能布局方法功能布局方法将生产线上的设备和工序按照功能进行布局。
这种方法适用于具有多种产品和复杂生产流程的企业。
在功能布局方法中,相同功能的设备被放置在相邻的位置,以便于操作人员进行监控和维护。
这种布局方法可以提高生产效率和产品质量,但却可能导致物料运输路径的延长和堆积,增加生产成本。
综上所述,生产线布局方法是一项重要的生产管理技术。
不同的布局方法适用于不同的生产企业,根据产品特点、工艺要求、物料运输量和生产流程等因素来选择合适的布局方法。
生产线布局(超详细)【精品课件】.ppt
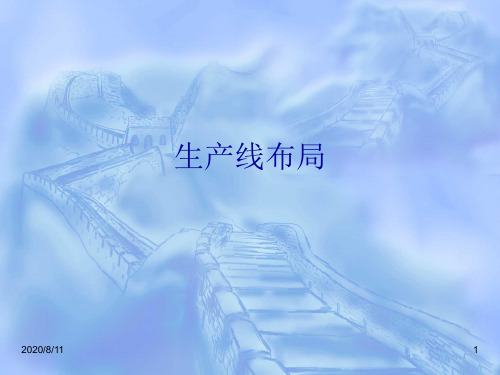
2020/8/11
12
鉴别七大浪费
六、来自工序不当的浪费
工作本身产生的浪费,当机器不正常运作而使操作人员 需要花额外时间,或当操作人员出于习惯或花了过多的 时间使清洁工作超过了规格的要求。
多余的检查也是过程浪费的另一个表现形式。
2020/8/11
13
鉴别七大浪费
七、不需要的动作的浪费
人们在工作设置中经常将工作中的动作搞混乱,实际做的动 作和工作要求的动作往往是不同的。
生产线布局
2020/8/11
1
精益生产五项基本原则
• 价值 (VALUE) : 决定于客户是否愿意为了它而付钱。
• 价值流 (VALUE STREAM) : 从产品设计到客户服务的所有
活动的描述和鉴别,都需要消除非增值活动。
• 流畅 (FLOW) : 消除所有工序的阻滞使价值流“流畅”而没有
中断。
作为一个确定的目的,工作是要作为一组精确的动作来考虑 的,哪些是增值的,那些是不增值的。
一个人在每天的恒定的工作中(例如一个很忙的人)可能实 际上只是很少一部分是增值工作。
工作中的不需要的动作被认为是浪费的,不增值的。
2020/8/11
14
生产布局前的准备工作
▪ 产能评估 ▪ 生产线顺流 ▪ 库存周转评估
1. 采用了看板管理,拉动生产方式 2. 车间布局U型布局; 3. 不同类型的机器摆放在一块; 4. 实现了单件流的生产; 5. 机器小型化 ; 6. 工序中间很少甚至没有库存; 7. 实现了作业标准化; 8. 对工人实行了多技能培训; 9. 具有完善的作业改善活动制度
2020/8/11
3
看谁摘的果子最多!
6
产生更严重的成本连锁反应……
生产线布局(超详细)_图文
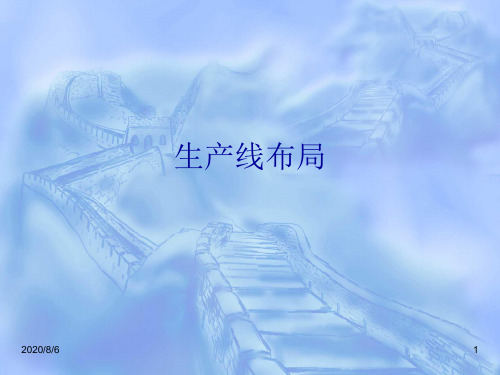
工艺原则布局
权重代码 密切程度
A
绝对必要
E
特别重要
I
重要
O
普通的
U
不重要的
X
不予考虑的
2020/8/6
线代号
29
工艺原则布局
▪ 医院相关图
1
3
5
2
4
6
2020/8/6
30
工艺原则布局
▪ 医院总体合理布局图
1
4
65
2
3
2020/8/6
31
工艺原则布局
▪ 布局方法 设部门或工艺有n个
布局方案=n!
▪ 使用范围:
• 批量小 • 体积大
▪ 布局特点
• 以产品为中心 • 不考虑物流成本和复杂程度
2020/8/6
18
工艺原则布局
▪ 定义:
• 将相似的设备或功能集中放在一起的布局方式 • 也称车间布局,如车床车间
▪ 使用范围
• 生产设备密集型 • 设备专业性 • 自动化程度高 • 资本密集型 • 产品重量轻
2020/8/6
次数
1 1 2 3 4 5 6 7 8
23 175 50
0
45 0 30 100 75 17 88
20
678 200 20 25 90 80 90 125 99 180 5 0 25 0 180 187
347 103 7
21
▪ 玩具厂各车间年物流成本示意图
2020/8/6
22
工艺原则布局
1. 采用了看板管理,拉动生产方式 2. 车间布局U型布局; 3. 不同类型的机器摆放在一块; 4. 实现了单件流的生产; 5. 机器小型化 ; 6. 工序中间很少甚至没有库存; 7. 实现了作业标准化; 8. 对工人实行了多技能培训; 9. 具有完善的作业改善活动制度
工厂生产车间流水线布局的七种方式

⼯⼚⽣产车间流⽔线布局的七种⽅式单元装配线的理想布局之⼀是花瓣型布局1.流畅原则:各⼯序的有机结合,相关联⼯序集中放置原则,流⽔化布局原则。
2.最短距离原则:尽量减少搬运,流程不可以交叉,直线运⾏。
3.平衡原则:⼯站之间资源配置,速率配置尽量平衡.4.固定循环原则:尽量减少诸如搬运,传递这种Non-Value Added的活动。
5.经济产量原则:适应最⼩批量⽣产的情形,尽可能利⽤空间,减少地⾯放置原则6.柔韧性的原则:对未来变化具有充分应变⼒,⽅案有弹性。
如果是⼩批量多种类的产品,优先考虑“U”型线布局、环型布局等7.防错的原则:⽣产布局要尽可能充分的考虑这项原则,第⼀步先从硬件布局上预防错误,减少⽣产上的损失!1逆时针排布逆时针排布,主要⽬的是希望员⼯能够采⽤⼀⼈完结作业⽅式、能够实现⼀⼈多机。
⼀⼈完结与⼀⼈多机要求⼀个员⼯从头做到尾,因此员⼯是动态的,称之为“巡回作业”。
⼤部分作业员是右撇⼦,因此如果逆时针排布的话,当员⼯进⾏下⼀道加⼯作业时,⼯装夹具或者零部件在左侧,员⼯作业并不⽅便,这也正是逆时针的⽬的——员⼯就会⾛到下⼀⼯位——巡回的⽬的也就达到了。
2出⼊⼝⼀致出⼊⼝⼀致,是指原材料⼊⼝和成品出⼝在⼀起。
为什么要求出⼊⼝⼀致呢?⾸先,有利于减少空⼿浪费。
假设出⼊⼝不⼀致,作业员采⽤巡回作业,那么当⼀件产品⽣产完了,要去重新取⼀件原材料加⼯的话,作业员就会空⼿(⼿上没有材料可以⽣产)从成品产出⼝⾛到原材料投⼊⼝,这段时间是浪费。
如果出⼊⼝⼀致的话,作业员⽴刻就可以取到新的原材料进⾏加⼯,从⽽避免了空⼿浪费。
第⼆,有利于⽣产线平衡。
由于出⼊⼝⼀致,布局必然呈现类似“U”的形状,这使得各⼯序⾮常接近,从⽽为⼀个⼈同时操作多道⼯序提供了可能,这就提⾼了⼯序分配的灵活性,从⽽取得更⾼的⽣产线平衡率。
3避免孤岛型布局孤岛型布局把⽣产线分割成⼀个个单独的⼯作单元,其缺陷在于单元与单元之间互相隔离,⽆法互相协助。
生产线布局方案规划
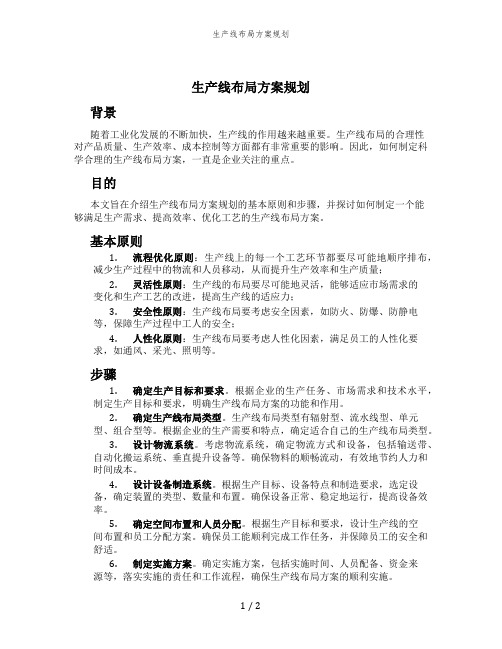
生产线布局方案规划背景随着工业化发展的不断加快,生产线的作用越来越重要。
生产线布局的合理性对产品质量、生产效率、成本控制等方面都有非常重要的影响。
因此,如何制定科学合理的生产线布局方案,一直是企业关注的重点。
目的本文旨在介绍生产线布局方案规划的基本原则和步骤,并探讨如何制定一个能够满足生产需求、提高效率、优化工艺的生产线布局方案。
基本原则1.流程优化原则:生产线上的每一个工艺环节都要尽可能地顺序排布,减少生产过程中的物流和人员移动,从而提升生产效率和生产质量;2.灵活性原则:生产线的布局要尽可能地灵活,能够适应市场需求的变化和生产工艺的改进,提高生产线的适应力;3.安全性原则:生产线布局要考虑安全因素,如防火、防爆、防静电等,保障生产过程中工人的安全;4.人性化原则:生产线布局要考虑人性化因素,满足员工的人性化要求,如通风、采光、照明等。
步骤1.确定生产目标和要求。
根据企业的生产任务、市场需求和技术水平,制定生产目标和要求,明确生产线布局方案的功能和作用。
2.确定生产线布局类型。
生产线布局类型有辐射型、流水线型、单元型、组合型等。
根据企业的生产需要和特点,确定适合自己的生产线布局类型。
3.设计物流系统。
考虑物流系统,确定物流方式和设备,包括输送带、自动化搬运系统、垂直提升设备等。
确保物料的顺畅流动,有效地节约人力和时间成本。
4.设计设备制造系统。
根据生产目标、设备特点和制造要求,选定设备,确定装置的类型、数量和布置。
确保设备正常、稳定地运行,提高设备效率。
5.确定空间布置和人员分配。
根据生产目标和要求,设计生产线的空间布置和员工分配方案。
确保员工能顺利完成工作任务,并保障员工的安全和舒适。
6.制定实施方案。
确定实施方案,包括实施时间、人员配备、资金来源等,落实实施的责任和工作流程,确保生产线布局方案的顺利实施。
结论生产线布局方案规划是企业运营管理的关键环节,对企业的生产效率和效益有非常重要的影响。
生产线布局(超详细)全解
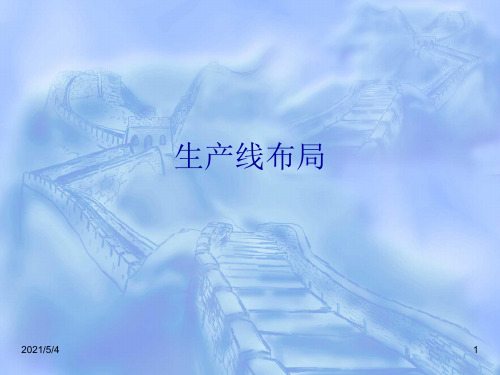
2021/5/4
44
产品原则布局
▪ 第四步:选择作业分配 工作
(以后续作业数量多少安 排作业)
2021/5/4
作业 A
B/D C/E F/G/H/I
J K
后续作业数量 6 5 4 2 1 0
45
产品原则布局
▪ 第五步对工作站安排作业,工作站周期:50.4秒
工作站 作业 时间(S)
工作站1 A
45
二、运输中的浪费
具有代表性的是,有些项目总是无工作性质地移动,时间 花费了在路途中,这是浪费。
2021/5/4
8
鉴别七大浪费
三、来自库存的浪费
库存代表着某些项目正等待某些事情的发生,这里的浪 费表现在:和保存着这些项目来等待有关联的成本,对 这些项目无增值而导致时间的损失。
安全库存是为了保证生产部门的正常运作和弥补不良品 的损失而存在的,但是安全库存不能够超出它们的正常 需要。
▪ 问:
• 金额如何计算出来的? • 组合布局方法或排列有多少种? • 如何排列的才是有效的?
2021/5/4
23
工艺原则布局
▪ 成本矩阵——方案一,总成本合计3474
11 2 3 4 5 6 7 82021/5/4
2
3
175 50
0
4
5
6
7
0
60 400 60
100 150 180 240
17 88 125 198
▪ 使用范围:
• 批量小 • 体积大
▪ 布局特点
• 以产品为中心 • 不考虑物流成本和复杂程度
2021/5/4
18
工艺原则布局
▪ 定义:
• 将相似的设备或功能集中放在一起的布局方式 • 也称车间布局,如车床车间
不同生产线的布置形式与平衡方法详细展开
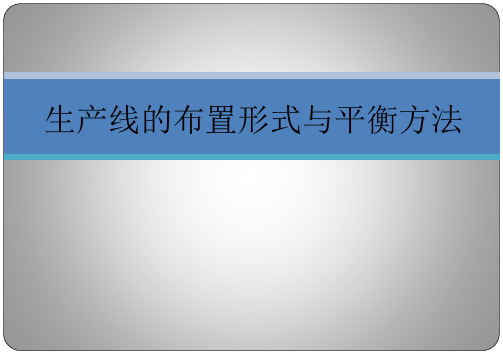
方便 程度放置 (不一定 适合
常较 低
工艺 均适用 作严 格要求,随意性大
物流)
将一个制程分成多个工位 数人作业, 按机器功能集 多适用于手工 有一定批量的生产规模 适用于较简单工艺 现场控制特别是物料
,由 数人在大工作台上 有 一定分工 中摆 放,专人 产 品,体积 ,物 料利用率提高,
和人 员管理较难
制动器生产线
35T冲床
本田后三角布局(老)
16T冲床
割皮台
装CLIP台
栈板
半成品放置桌
烘箱
检验台 修边桌
注塑机
本田后三角布局(新)
栈板
16T冲床
割皮台
装CLIP台
烘箱
周转台 注塑机
35T冲床
修边桌
材料放置架
检验台
• 生产线的布置原则:
1 短距离原则 2 顺序原则(单流向原则) 3 经济产量原则 4 平衡原则 5 设备、工夹具零故障原则 6 舒适原则 7 空间利用原则 8 柔性原则
踏入成长 快车道!
间1人作业时间(S) 6.32 16.88 8.18 9.96 23.17 15.87 14.64 21.36 6.48 122.9
• 生产线的平衡方法介绍:
ACT ASS’Y LINE TACT 分布图(改善后)
工序(作业)
时 间 (S )
4.5
4
3.5
3
2.5
2
1.5
1
0.5
0
1
2
3
4
5
6
7
8
适用于对机器 适用于各类型 不良品率低。
适用于较简单工艺 人员,物料分工明确
产品 由一个人完成全部 单人式 工作,有利 于控制质量,
生产线布局(超详细)_图文
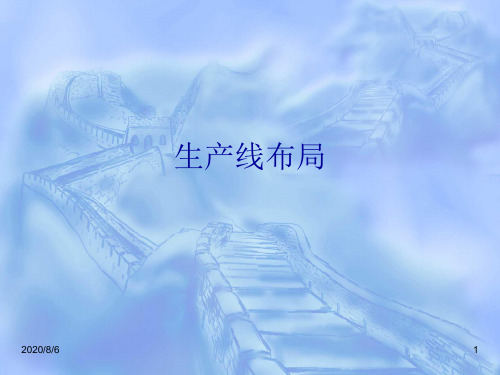
次数
1 1 2 3 4 5 6 7 8
23 175 50
0
45 0 30 100 75 17 88
20
678 200 20 25 90 80 90 125 99 180 5 0 25 0 180 187
347 103 7
21
▪ 玩具厂各车间年物流成本示意图
2020/8/6
22
工艺原则布局
2020/8/6
12
鉴别七大浪费
六、来自工序不当的浪费
工作本身产生的浪费,当机器不正常运作而使操作人员 需要花额外时间,或当操作人员出于习惯或花了过多的 时间使清洁工作超过了规格的要求。
多余的检查也是过程浪费的另一个表现形式。
2020/8/6
13
鉴别七大浪费
七、不需要的动作的浪费
人们在工作设置中经常将工作中的动作搞混乱,实际做的动 作和工作要求的动作往往是不同的。
2020/8/6
15
生产线布局类别
▪ 定位原则布局 ▪ 工艺原则布局 ▪ 产品原则布局 ▪ 成组技术(单元式)布局
2020/8/6
16
定位原则布局
▪ 定义:
• 将原材料和设备按照使用次序和移动的难易程度 在产品的四周进行生产
▪ 起源
• 19世纪初亨利福特的汽车装配线
2020/8/6
17
定位原则布局
2020/8/6
9
不合格品
率高
库
机器故障率高
调整时间太长
存
水
设备能力不平衡
缺勤率高
备件供应不及时
平
采购周期太长 技术服务 工人技能差 后勤服务差
不及时
图 17-1 库存水平高掩盖的管理问题多
生产线布局(超详细)PPT课件
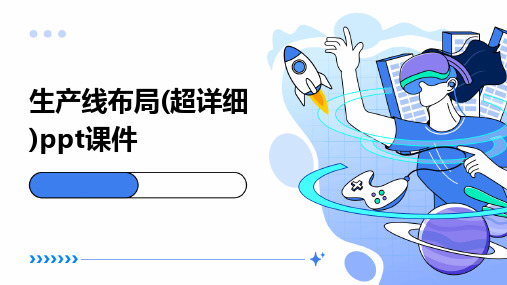
产品特性
产品的工艺要求、生产流程、 物料特性等对生产线布局有直 接影响。
人力资源
员工的技能、经验和工作习惯 对生产线布局的效率和效果有 重要影响。
环境因素
生产环境的要求、法律法规、 环保要求等对生产线布局有制 约作用。
02
生产线布局的类型
直线式布局
总结词
简单明了,便于管理,适合小批量生产
详细描述
布局评估的方法
01
02
03
04
生产流程分析
通过分析生产流程,评估生产 线布局的合理性,找出瓶颈环
节和浪费。
设备利用率评估
计算设备的平均利用率,判断 是否存在设备闲置或使用不足
的情况。
空间利用率评估
评估生产线布局的空间利用率 ,判断是否充分利用了生产空
间。
物流效率评估
分析生产线上的物流效率,判 断是否存在物料搬运距离过长
收集生产线布局相关 的数据,包括设备布 局、设备参数、生产 流程、物流路径等。
分析问题
根据收集的数据,分 析生产线布局存在的 问题和瓶颈环节。
制定方案
根据问题分析结果, 制定相应的布局调整 方案。
实施调整
按照制定的方案,逐 步实施生产线布局的 调整。
效果评估
在布局调整后,对生 产线的运行情况进行 评估,判断调整效果。
详细描述
该电子产品制造企业采用精益的生产线布局,以提高生产效率和降低成本。生产线布局 高效,各工序之间衔接紧密,以减少浪费。同时,大量采用自动
总结词
安全、卫生、人性化
VS
详细描述
该食品加工企业注重生产线的安全性、卫 生和人性化设计。生产线布局合理,保证 清洁度和卫生标准。同时,充分考虑员工 操作的舒适性和安全性,提高生产效率和 工作质量。
【培训】生产线布局PPT课件
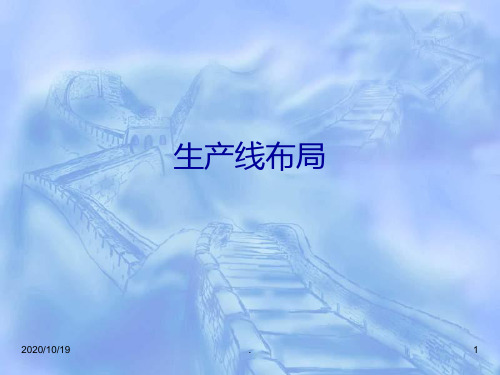
2020/10/19
.
45
产品原则布局
▪ 第五步对工作站安排作业,工作站周期:50.4秒
工作站 作业 时间(S)
工作站1 A
45
工作站2 D
50
工作站3 B
11
E
15
C
9
F
12
工作站4 G
12
H
12
I
12
J
8
工作站5 K
1. 采用了看板管理,拉动生产方式 2. 车间布局U型布局; 3. 不同类型的机器摆放在一块; 4. 实现了单件流的生产; 5. 机器小型化 ; 6. 工序中间很少甚至没有库存; 7. 实现了作业标准化; 8. 对工人实行了多技能培训; 9. 具有完善的作业改善活动制度
2020/10/19
.
3
看谁摘的果子最多!
2020/10/19
.
12
鉴别七大浪费
六、来自工序不当的浪费
工作本身产生的浪费,当机器不正常运作而使操作人员 需要花额外时间,或当操作人员出于习惯或花了过多的 时间使清洁工作超过了规格的要求。
多余的检查也是过程浪费的另一个表现形式。
2020/10/19
.
13
鉴别七大浪费
七、不需要的动作的浪费
人们在工作设置中经常将工作中的动作搞混乱,实际做的动 作和工作要求的动作往往是不同的。
如果按照工作单,每天应该生产160K个产品,那么:
节拍时间 =
每天有效时间 每天须生产数
= 1140 分钟 = 0.007 分钟/产品 160K 个产品
换句话说,每分钟生产140单位的产品。
2020/10/19
.
40
产品原则布局
工厂及生产线布局解析
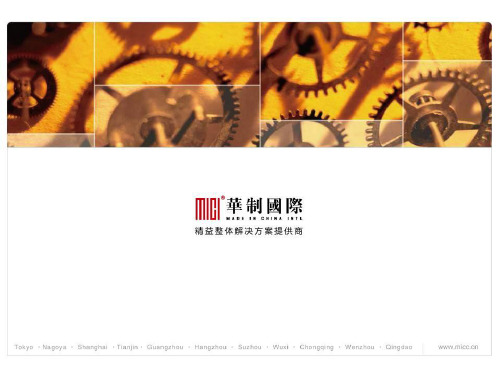
钳工
车床
齿
磨床
仓
剪板机
钻孔
库
划线
立床
摇臂钻
车床
车床
打压
钻孔
装仓 配库
优点
产品原则布置的优缺点
产品原则布置
缺点
1. 由于布置符合工艺过程,物流顺畅
2. 由于上下工序衔接,存放量少
3. 生产周期短
4. 物料搬运工作量少
5. 可做到作业专业化, 生产计划简单, 易于控制
6. 员工为多技能工,经常调换不同工 作岗位,使员工成长速度加快
钻床 钻床 滚齿机 滚齿机
焊接 焊接
装配 装配
优点
工艺布置原则
缺点
1. 机器利用率高,可减少设备数量 2. 设备柔性程度很高,更改产品品
种时不需要太大改变
3. 设备投资相对较少 4. 操作人员技能要求不高
1. 由于流程较长,搬运路线不确定,费 用高
2. 生产计划与控制非常复杂
3. 生产周期长
4. 库存量相对较大
4、固定化布置 即定位置形式 。
1、 产品原则布置(product layout) 根据产品制造的步骤安排各组成部 分.从理论上看,流程是一条从原料投入到成品完工为止的连续线.固 定制造某种部件或某种产品的封闭车间.其设备,人员安加工或装配的 工艺过程顺序布置.形成一定的生产线.适用于品种少,批量大的生产 方式.
服务设施布置
工厂总 体布置
车间内 部布置
服务设施 总体布置
服务设施 内部布置
4、设施布置的方法
1) 基本思路: 物料搬运占生产周期和生产成本的比重
很大; 尽量使物流较大的经济活动单元靠近,
以减少搬运距离和搬运量
工厂及生产线布局解析
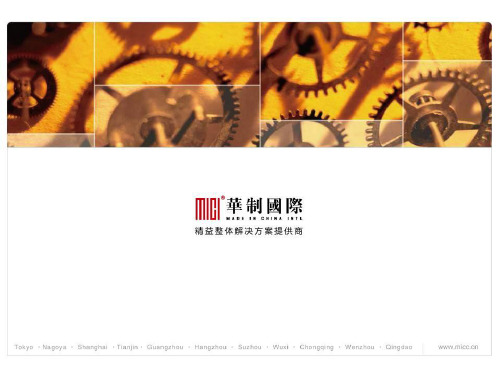
华制国际:徐结华
一、工厂 设施规划
1、 设施布置的目标和原则
空间、设备 及人员的利
用
顾客满意
目标: 最大化
资讯、物料及人 员的有效流动
员工士气 及安全
原则:
尽量简化搬运作业,减少搬运环节; 搬运前应安排下一工序; 搬运路线尽可能为直线,以缩短距离; 尽量减少交叉、回流
2、 设施布置的阶段和程式
5. 由于操作人员从事单一工作,员 工提升速度慢,且容易产生倦态
3、 成组原则布置(group layout) 这是实施成组加工的布置形式,是将企 业的多种产品、部件和零件,按照一定的相似性准则分类编组,是介于产品 原则布置和工艺原则布置之间.适应于中小批量生产.
车床
钻床
磨床
滚齿
装配
仓 库
铣床
装配
7. 可使用专用设备和机械化,自动化搬 运方法
1. 设备发生故障时将引起整个生产线 中断
2. 产品设计变化将引起布置的重大调 整
3. 生产线速度取决于最慢的机器
4. 相对投资较大,因为在生产线上的有 的机器负荷不満.
5. 对工人的技能要求高,不易于培训
6. 维修和保养费用高
这种布置形式的例子有汽车装配线,食品加工和家具制造业等.
方法:
原 材 料 进 厂
物料流向示意图
仓
准
备
车
库
间
机
装
加
配
车
车
间
间
目标:
热处理车间
减少个生产环节间的交叉往返运输时间。
成
出
品
库
厂
方法2:物料运量图
含义:
比较各种生产单元之间的运量大小及运输次数来确 定布置方案的一种方法。
2019年生产线布局(超详细)培训课件

2019/11/1
12
鉴别七大浪费
六、来自工序不当的浪费
工作本身产生的浪费,当机器不正常运作而使操作人员 需要花额外时间,或当操作人员出于习惯或花了过多的 时间使清洁工作超过了规格的要求。
多余的检查也是过程浪费的另一个表现形式。
2019/11/1
13
鉴别七大浪费
七、不需要的动作的浪费
人们在工作设置中经常将工作中的动作搞混乱,实际做的动 作和工作要求的动作往往是不同的。
6σ=?
2019/11/1
4
σ
2 3 4 5 6
2019/11/1
6σ标准
PPM 308,537
66,807 6,210 233 3.4
PPM等于 多少?
缺陷减少5倍 缺陷减少11倍 缺陷减少26倍 缺陷减少68倍
5
鉴别七大浪费
一、生产产生的不良引起的浪费
任何产品的不良都是浪费的一个主要来源。
2019/11/1
6.评估装配线平衡后的效率
E=T/(Na × Ct)
E——装配线平衡效率
T——完成作业所需的时间总量
Na——实际工作站数 Ct——生产节拍
7.如果不理想,重复第4步骤
就生产而言E是怎样的 数值较好?
2019/11/1
41
产品原则布局
案例 一玩具厂的玩具
车在流水线上 作业,每天需 生产500辆, 每天生产时间 为420分钟, 生产步骤及时 间如左表:
2019/11/1
27
工艺原则布局
系统布局设计(SLP) 可是往返次数与权重表
部门 1接待室 2射线室 3外科 4检查室 5实验室
2019/11/1
6护士站
- 1、下载文档前请自行甄别文档内容的完整性,平台不提供额外的编辑、内容补充、找答案等附加服务。
- 2、"仅部分预览"的文档,不可在线预览部分如存在完整性等问题,可反馈申请退款(可完整预览的文档不适用该条件!)。
- 3、如文档侵犯您的权益,请联系客服反馈,我们会尽快为您处理(人工客服工作时间:9:00-18:30)。
具有代表性的是,有些项目总是无工作性质地移动,时间 花费了在路途中,这是浪费。
2020/6/20
8
鉴别七大浪费
三、来自库存的浪费
库存代表着某些项目正等待某些事情的发生,这里的浪 费表现在:和保存着这些项目来等待有关联的成本,对 这些项目无增值而导致时间的损失。
安全库存是为了保证生产部门的正常运作和弥补不良品 的损失而存在的,但是安全库存不能够超出它们的正常 需要。
2020/6/20
12
鉴别七大浪费
六、来自工序不当的浪费
工作本身产生的浪费,当机器不正常运作而使操作人员 需要花额外时间,或当操作人员出于习惯或花了过多的 时间使清洁工作超过了规格的要求。
多余的检查也是过程浪费的另一个表现形式。
2020/6/20
13
鉴别七大浪费
七、不需要的动作的浪费
人们在工作设置中经常将工作中的动作搞混乱,实际做的动 作和工作要求的动作往往是不同的。
1
2
3
4
5
6
7
82020/6/20
24
工艺原则布局
• 布局第一个方案
2020/6/20
25
工艺原则布局
• 成本矩阵——方案二,总成本合计3376
1
2
3
4
5
6
7
82020/6/20
26
工艺原则布局
• 影响工艺原则布局的因素:
管理者思想 工艺之间关联环境要求,如隔壁车间的环境污染造成车间的环境洁净度 物流复杂性 设施条件 等等
2020/6/20
15
生产线布局类别
• 定位原则布局 • 工艺原则布局 • 产品原则布局 • 成组技术(单元式)布局
2020/6/20
16
定位原则布局
• 定义:
将原材料和设备按照使用次序和移动的难易程度在产品的四周进行生产
• 起源
19世纪初亨利福特的汽车装配线
2020/6/20
17
定位原则布局
6σ=?
2020/6/20
4
6σ标准
σ
2 3 4 5 6
2020/6/20
PPM
308,537 66,807 6,210 233 3.4
PPM等于 多少?
缺陷减少5倍 缺陷减少11倍 缺陷减少26倍 缺陷减少68倍
5
鉴别七大浪费
一、生产产生的不良引起的浪费
任何产品的不良都是浪费的一个主要来源。
2020/6/20
6
产生更严重的成本连锁反应……
更多的
“一人错误百人忙” 防火成本 的成本暴增曲线
更多的 救火成本
2020/6/20
更多的 返工成本
正常成本
救火、防火、多余监 督、过度控制、多余 检验、投诉处理、退 货维修、商誉损失、 顾客流失等效应连锁 扩大成本! 重工、返修、报废成本
日常管销/制造成本
7
鉴别七大浪费
作为一个确定的目的,工作是要作为一组精确的动作来考虑 的,哪些是增值的,那些是不增值的。
一个人在每天的恒定的工作中(例如一个很忙的人)可能实 际上只是很少一部分是增值工作。
工作中的不需要的动作被认为是浪费的,不增值的。
2020/6/20
14
生产布局前的准备工作
• 产能评估 • 生产线顺流 • 库存周转评估
生产线布局大全
精益生产五项基本原则
• 价值 (VALUE) : 决定于客户是否愿意为了它而付钱。
• 价值流 (VALUE STREAM) : 从产品设计到客户服务的所有
活动的描述和鉴别,都需要消除非增值活动。
• 流畅 (FLOW) : 消除所有工序的阻滞使价值流“流畅”而没有
中断。
• 拉动 (PULL) : 通过客户的需求来达到产品和工序能够畅通的
• 使用范围:
批量小 体积大
• 布局特点
以产品为中心 不考虑物流成本和复杂程度Leabharlann 2020/6/2018
工艺原则布局
• 定义:
将相似的设备或功能集中放在一起的布局方式
也称车间布局,如车床车间
• 使用范围
生产设备密集型
设备专业性
自动化程度高
资本密集型
2020产/6/2品0 重量轻
19
工艺原则布局
• 案例:玩具厂有8个车间,采用物料集中搬运方式, 每次只能搬运一个周转箱,车间之间运输成本为1元 ,每隔一个车间增加1元
2020/6/20
9
不合格品
率高
库
机器故障率高
调整时间太长
存
水
设备能力不平衡
缺勤率高
备件供应不及时
平
采购周期太长 技术服务 工人技能差 后勤服务差
不及时
图 17-1 库存水平高掩盖的管理问题多
2020/6/20
10
鉴别七大浪费
四、来自生产过剩的浪费
公司有时会生产比他们可能卖出去的更多的产品,因为他 们想要建立库存,作为一个安全保证措施来防止可能出错 而造成的后果,或者因为他们想要保证他们的设备和设施 的运转。
无论什么原因,没有直接的需求就生产的产品都是浪费。
如果有些项目的需求没有了,那这时,这些项目将不得不被放弃或者 降价处理。
其间,它们储存在仓库里,造成成本的增加和库存的浪费。
2020/6/20
11
鉴别七大浪费
五、来自时间等待的浪费
时间等待的浪费是很容易被鉴别的,它有很多的表现形态, 包括有:
• 为定单而等待 • 为批准而等待 • 为零部件而等待 • 为物料而等待 • 为前面过程中叙述的项目而等待 • 为设备的维修而等待
流动的一种能力。
• 尽善尽美(PERFECTION) : 通过持续改善的应用,来提倡“
第一次就做好”的一种能力。
2020/6/20
2
大规模生产和精益生产方式的区别
大规模生产方式
精益生产方式
1. 采用推动生产方式 2. 车间布局是按功能区划分; 3. 相同类型的机器摆放在一块; 4. 大批量的生产; 5. 机器适合于大批量生产 ; 6. 工序中间容易堆积库存 ; 7. 未实现作业标准化; 8. 工人一般只会一种操作; 9. 没有或只有个体的作业改善活动
2020/6/20
20
工艺原则布局
次数
车 间 之 间
1 2 3
的4
流5
动6
表7
8 2020/6/20
21
• 玩具厂各车间年物流成本示意图
2020/6/20
22
工艺原则布局
• 问:
金额如何计算出来的? 组合布局方法或排列有多少种? 如何排列的才是有效的?
2020/6/20
23
工艺原则布局
• 成本矩阵——方案一,总成本合计3474
1. 采用了看板管理,拉动生产方式 2. 车间布局U型布局; 3. 不同类型的机器摆放在一块; 4. 实现了单件流的生产; 5. 机器小型化 ; 6. 工序中间很少甚至没有库存; 7. 实现了作业标准化; 8. 对工人实行了多技能培训; 9. 具有完善的作业改善活动制度
2020/6/20
3
看谁摘的果子最多!