汽车件作业效率提升方案
汽车施工方案(3篇)

第1篇一、项目背景随着我国经济的快速发展,汽车行业作为国民经济的重要组成部分,对汽车产业的需求日益增长。
为了满足市场需求,提高汽车生产效率,降低生产成本,确保汽车产品质量,本项目针对汽车生产线进行施工改造。
以下是具体的施工方案。
二、项目目标1. 提高汽车生产效率,缩短生产周期。
2. 降低生产成本,提高企业竞争力。
3. 确保汽车产品质量,满足消费者需求。
4. 优化生产环境,提高员工工作舒适度。
三、施工范围1. 汽车生产线整体布局优化。
2. 汽车零部件生产线升级改造。
3. 汽车装配线自动化升级。
4. 质量检测设备更新。
5. 生产线环境改善。
四、施工组织1. 施工团队:由项目经理、施工员、技术员、质量员、安全员等组成。
2. 施工进度:按照项目总进度计划,分阶段实施。
五、施工方案1. 汽车生产线整体布局优化(1)分析现有生产线布局,找出不合理之处。
(2)根据生产需求,重新规划生产线布局,提高生产线效率。
(3)调整生产线设备位置,缩短物料运输距离,降低生产成本。
2. 汽车零部件生产线升级改造(1)对现有零部件生产线进行技术评估,找出升级改造方向。
(2)引进先进的生产设备,提高生产效率。
(3)优化生产工艺,降低生产成本。
(4)对生产线进行信息化改造,实现生产数据实时监控。
3. 汽车装配线自动化升级(1)分析现有装配线,找出自动化改造方向。
(2)引进自动化装配设备,提高装配效率。
(3)优化装配工艺,降低人工成本。
(4)实现装配线信息化管理,提高装配质量。
4. 质量检测设备更新(1)对现有质量检测设备进行评估,找出更新方向。
(2)引进先进的检测设备,提高检测精度。
(3)建立完善的质量检测体系,确保产品质量。
5. 生产线环境改善(1)对生产线进行绿化,改善工作环境。
(2)优化生产线照明,提高员工工作效率。
(3)加强生产线通风,确保空气质量。
六、施工实施1. 施工前准备:对施工人员进行技术培训,确保施工质量。
2. 施工过程中:严格按照施工方案执行,确保施工进度。
工业工程方案改善实例
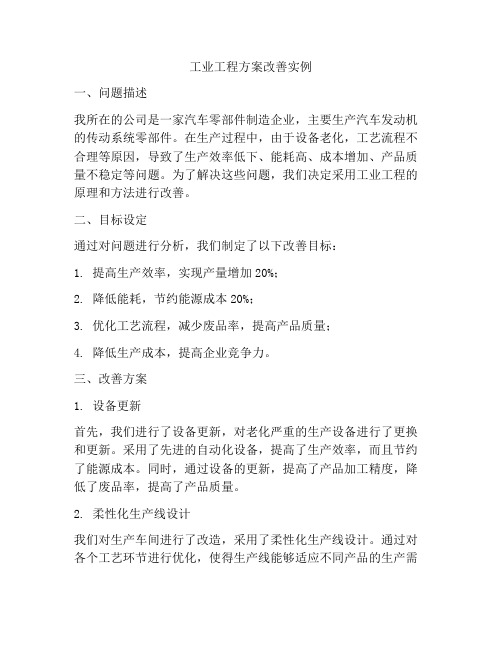
工业工程方案改善实例一、问题描述我所在的公司是一家汽车零部件制造企业,主要生产汽车发动机的传动系统零部件。
在生产过程中,由于设备老化,工艺流程不合理等原因,导致了生产效率低下、能耗高、成本增加、产品质量不稳定等问题。
为了解决这些问题,我们决定采用工业工程的原理和方法进行改善。
二、目标设定通过对问题进行分析,我们制定了以下改善目标:1. 提高生产效率,实现产量增加20%;2. 降低能耗,节约能源成本20%;3. 优化工艺流程,减少废品率,提高产品质量;4. 降低生产成本,提高企业竞争力。
三、改善方案1. 设备更新首先,我们进行了设备更新,对老化严重的生产设备进行了更换和更新。
采用了先进的自动化设备,提高了生产效率,而且节约了能源成本。
同时,通过设备的更新,提高了产品加工精度,降低了废品率,提高了产品质量。
2. 柔性化生产线设计我们对生产车间进行了改造,采用了柔性化生产线设计。
通过对各个工艺环节进行优化,使得生产线能够适应不同产品的生产需求,大大提高了生产线的灵活性和适应性。
这样一来,就可以有效降低产品的更换时间,提高了生产效率。
3. 作业分析与改进我们开展了对生产作业的分析,优化了作业流程。
合理安排工人的作业任务,减少了非生产性动作和浪费,提高了作业效率。
同时,我们还引入了一些辅助工具和工艺改进措施,进一步提高了生产效率和产品质量。
4. 绩效管理体系建立为了更好地监控生产过程和效果,我们建立了绩效管理体系。
制定了生产目标和绩效考核指标,对生产过程进行全面监控和评估。
通过绩效管理体系的建立,我们可以及时发现和解决生产中的问题,及时调整生产计划,保障生产效率和产品质量。
四、改善效果经过改善方案的实施,我们取得了以下改善效果:1. 生产效率提高了30%,产量增加了20%;2. 能源成本减少了25%,节约了大量能源费用;3. 产品质量稳定性得到了提高,废品率降低了15%;4. 生产成本降低了20%,企业利润大幅提升。
汽车零部件行业精益解决方案

汽车零部件行业精益解决方案汽车零部件行业是汽车制造行业的重要组成部分,也是一个高度竞争和成本敏感的行业。
为了在激烈的市场竞争中取得优势,汽车零部件行业需要采用精益生产和管理的解决方案。
精益解决方案的目标是通过去除浪费和提高效率来实现业务流程的优化。
首先,汽车零部件行业可以采用精益生产的原则来消除浪费。
精益生产认为一切没有增加客户价值的活动都是浪费的,应该尽可能减少或消灭。
汽车零部件行业可以通过分析和改善业务流程,找到并消除各种形式的浪费,如生产中的等待、库存积压、不必要的运输等。
其次,汽车零部件行业可以应用精益供应链管理来提高效率。
通过与供应商建立紧密的合作关系,共享信息和资源,降低库存、提高物流效率,以及更好地满足客户需求。
供应链管理的精益原则包括精确预测需求、及时交付、减少库存和提高供应商质量。
此外,汽车零部件行业可以使用精益Six Sigma方法来改进产品质量和降低成本。
Six Sigma是一种管理方法论,通过减少变异和消除缺陷来提高质量水平。
使用Six Sigma方法可以通过分析数据并识别根本原因来找到产品制造过程中可能存在的问题,并采取相应的措施进行改进。
还有,汽车零部件行业可以运用精益布局设计来优化生产环境。
通过优化工作布局和流程,以最小化工人劳动和运动来减少浪费和提高生产效率。
例如,可以将生产设备和工具的位置优化,以方便工人操作和减少运动。
此外,汽车零部件行业可以通过精益改进文化来实现持续改进和增强组织的灵活性。
建立一个鼓励员工提出改进建议和参与改进活动的文化,可以促进持续学习和适应市场变化的能力。
总之,汽车零部件行业可以通过采用精益生产和管理的解决方案来优化业务流程、提高效率和降低成本。
这些解决方案包括消除浪费、优化供应链、改善产品质量、优化生产布局和培养改进文化。
通过实施这些精益解决方案,汽车零部件行业可以在激烈的市场竞争中取得优势,实现可持续发展。
如何提高汽车零件生产的效率和质量

如何提高汽车零件生产的效率和质量近年来,汽车产业发展迅猛,汽车生产中的零件制造也成为关键的环节之一。
提高汽车零件生产的效率和质量,不仅可以降低生产成本,还能够提升汽车整体品质和竞争力。
本文将从优化生产流程、引入先进技术以及加强质量管理等方面,探讨如何提高汽车零件生产的效率和质量。
一、优化生产流程汽车零件生产的流程优化是提高效率和质量的关键。
首先,针对每一道工序进行全面的分析,并确定出合理的生产工艺和标准操作程序。
其次,合理安排生产作业的顺序和时间,避免不必要的等待和闲置时间,实现生产的连贯性和流程化。
此外,还需要通过优化物料供应链,确保物料的及时供应和合理储备,避免因物料短缺或过剩导致生产中断或浪费。
二、引入先进技术技术的进步是提高汽车零件生产效率和质量的重要手段。
可以引入先进的制造技术和设备,如自动化生产线、数控机床等,以提高生产效率和降低劳动强度。
同时,使用先进的检测设备和技术,如三坐标测量仪、红外线检测等,可以确保产品的精度和质量,提高产品合格率。
此外,借助信息化技术,如物联网、大数据分析等,可以实现生产的数字化管理和智能化控制,提升整体生产的效率和效益。
三、加强质量管理严格的质量管理是提高汽车零件生产质量的基础。
建立和完善质量管理体系,确保全面质量控制。
首先,制定严格的质量标准和工艺规范,明确产品质量要求和检验标准。
其次,进行全过程的质量监控和追溯,建立完善的质量档案记录和异常处理机制。
通过对原材料、半成品和成品进行全面的检验和测试,及时发现和纠正问题,确保产品符合质量要求。
另外,加强员工的质量意识和技术培训,提高员工的技术水平和工作质量。
四、推行持续改进持续改进是提高汽车零件生产效率和质量的长久之计。
建立改进机制,鼓励员工提出改进建议并给予相应奖励和激励,形成良好的改进氛围。
同时,开展管理创新和技术创新,引入新的管理理念和先进技术,不断优化生产流程和工艺,提升产品的竞争力。
另外,加强与供应商和客户的沟通与合作,了解市场需求和用户反馈,及时改进产品设计和制造过程,以适应市场的变化和需求的变化。
汽车运输车辆效率提升方案
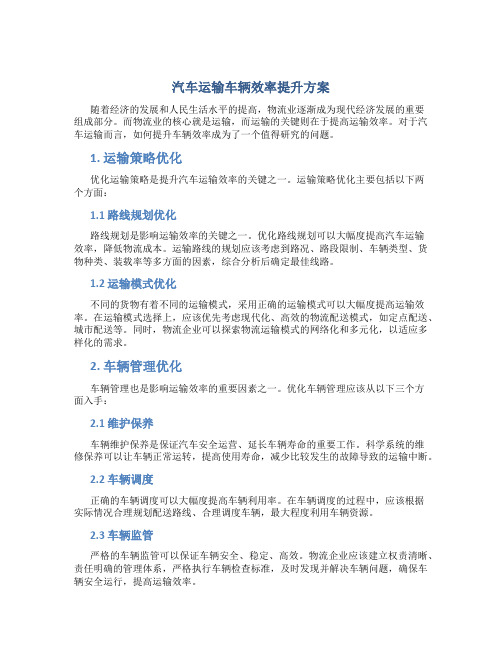
汽车运输车辆效率提升方案随着经济的发展和人民生活水平的提高,物流业逐渐成为现代经济发展的重要组成部分。
而物流业的核心就是运输,而运输的关键则在于提高运输效率。
对于汽车运输而言,如何提升车辆效率成为了一个值得研究的问题。
1. 运输策略优化优化运输策略是提升汽车运输效率的关键之一。
运输策略优化主要包括以下两个方面:1.1 路线规划优化路线规划是影响运输效率的关键之一。
优化路线规划可以大幅度提高汽车运输效率,降低物流成本。
运输路线的规划应该考虑到路况、路段限制、车辆类型、货物种类、装载率等多方面的因素,综合分析后确定最佳线路。
1.2 运输模式优化不同的货物有着不同的运输模式,采用正确的运输模式可以大幅度提高运输效率。
在运输模式选择上,应该优先考虑现代化、高效的物流配送模式,如定点配送、城市配送等。
同时,物流企业可以探索物流运输模式的网络化和多元化,以适应多样化的需求。
2. 车辆管理优化车辆管理也是影响运输效率的重要因素之一。
优化车辆管理应该从以下三个方面入手:2.1 维护保养车辆维护保养是保证汽车安全运营、延长车辆寿命的重要工作。
科学系统的维修保养可以让车辆正常运转,提高使用寿命,减少比较发生的故障导致的运输中断。
2.2 车辆调度正确的车辆调度可以大幅度提高车辆利用率。
在车辆调度的过程中,应该根据实际情况合理规划配送路线、合理调度车辆,最大程度利用车辆资源。
2.3 车辆监管严格的车辆监管可以保证车辆安全、稳定、高效。
物流企业应该建立权责清晰、责任明确的管理体系,严格执行车辆检查标准,及时发现并解决车辆问题,确保车辆安全运行,提高运输效率。
3. 技术创新提升在汽车运输方面,技术的创新可以提高车辆的效率和运行安全。
技术创新主要体现在以下两个方面:3.1 数据化管理物流企业可以采用数据化的管理模式,包括智能调度系统、GPS定位系统、LBS服务等。
通过数据化系统的运行,企业可以实时监控车辆运输情况,及时调整运作方案,提高运输效率。
汽车配件工厂5s管理方案
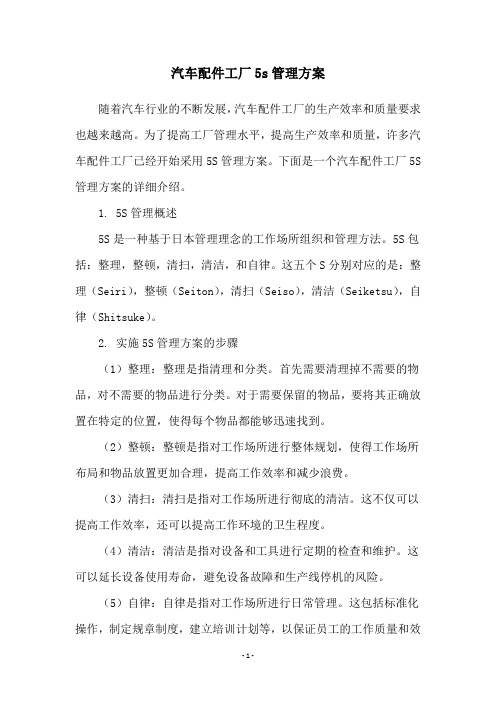
汽车配件工厂5s管理方案随着汽车行业的不断发展,汽车配件工厂的生产效率和质量要求也越来越高。
为了提高工厂管理水平,提高生产效率和质量,许多汽车配件工厂已经开始采用5S管理方案。
下面是一个汽车配件工厂5S 管理方案的详细介绍。
1. 5S管理概述5S是一种基于日本管理理念的工作场所组织和管理方法。
5S包括:整理,整顿,清扫,清洁,和自律。
这五个S分别对应的是:整理(Seiri),整顿(Seiton),清扫(Seiso),清洁(Seiketsu),自律(Shitsuke)。
2. 实施5S管理方案的步骤(1)整理:整理是指清理和分类。
首先需要清理掉不需要的物品,对不需要的物品进行分类。
对于需要保留的物品,要将其正确放置在特定的位置,使得每个物品都能够迅速找到。
(2)整顿:整顿是指对工作场所进行整体规划,使得工作场所布局和物品放置更加合理,提高工作效率和减少浪费。
(3)清扫:清扫是指对工作场所进行彻底的清洁。
这不仅可以提高工作效率,还可以提高工作环境的卫生程度。
(4)清洁:清洁是指对设备和工具进行定期的检查和维护。
这可以延长设备使用寿命,避免设备故障和生产线停机的风险。
(5)自律:自律是指对工作场所进行日常管理。
这包括标准化操作,制定规章制度,建立培训计划等,以保证员工的工作质量和效率。
3. 5S管理方案的优点(1)提高工作效率:通过整理、整顿、清扫、清洁和自律等步骤,可以优化工作场所的配置和物品放置,从而提高工作效率和生产效率。
(2)提高产品质量:通过5S的管理,可以及时发现并解决生产中出现的问题,减少缺陷产品的出现,提高产品质量。
(3)提高工作环境:通过5S的管理,可以改善工作环境,提高员工工作积极性和生产效率。
(4)降低生产成本:通过5S管理,可以减少生产过程中的浪费,降低生产成本。
4. 5S管理方案的总结汽车配件工厂5S管理方案是一种有效的管理方法,可以提高工厂的生产效率和质量。
实施5S管理方案需要全员参与,需要对员工进行培训,制定标准化操作规程,建立各项管理制度。
汽车运输车辆效率提升方案
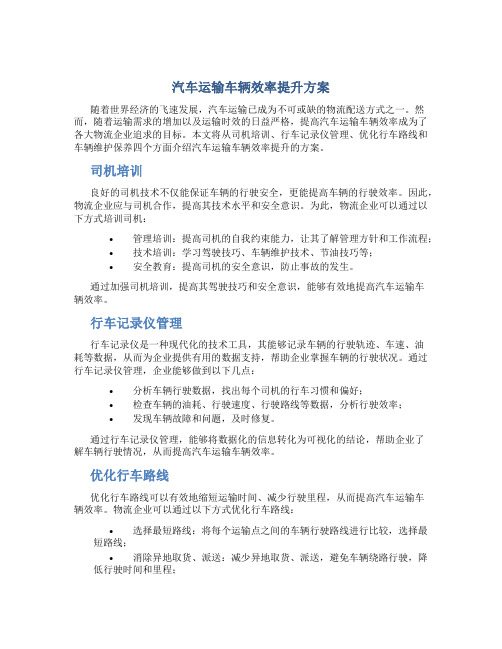
汽车运输车辆效率提升方案随着世界经济的飞速发展,汽车运输已成为不可或缺的物流配送方式之一。
然而,随着运输需求的增加以及运输时效的日益严格,提高汽车运输车辆效率成为了各大物流企业追求的目标。
本文将从司机培训、行车记录仪管理、优化行车路线和车辆维护保养四个方面介绍汽车运输车辆效率提升的方案。
司机培训良好的司机技术不仅能保证车辆的行驶安全,更能提高车辆的行驶效率。
因此,物流企业应与司机合作,提高其技术水平和安全意识。
为此,物流企业可以通过以下方式培训司机:•管理培训:提高司机的自我约束能力,让其了解管理方针和工作流程;•技术培训:学习驾驶技巧、车辆维护技术、节油技巧等;•安全教育:提高司机的安全意识,防止事故的发生。
通过加强司机培训,提高其驾驶技巧和安全意识,能够有效地提高汽车运输车辆效率。
行车记录仪管理行车记录仪是一种现代化的技术工具,其能够记录车辆的行驶轨迹、车速、油耗等数据,从而为企业提供有用的数据支持,帮助企业掌握车辆的行驶状况。
通过行车记录仪管理,企业能够做到以下几点:•分析车辆行驶数据,找出每个司机的行车习惯和偏好;•检查车辆的油耗、行驶速度、行驶路线等数据,分析行驶效率;•发现车辆故障和问题,及时修复。
通过行车记录仪管理,能够将数据化的信息转化为可视化的结论,帮助企业了解车辆行驶情况,从而提高汽车运输车辆效率。
优化行车路线优化行车路线可以有效地缩短运输时间、减少行驶里程,从而提高汽车运输车辆效率。
物流企业可以通过以下方式优化行车路线:•选择最短路线:将每个运输点之间的车辆行驶路线进行比较,选择最短路线;•消除异地取货、派送:减少异地取货、派送,避免车辆绕路行驶,降低行驶时间和里程;•车辆GPS导航:为每台车辆配备GPS导航系统,帮助司机更好地规划行车路线。
通过优化行车路线,减少车辆行驶里程和时间,能够有效地提高汽车运输车辆效率。
车辆维护保养车辆维护保养是保证汽车运输车辆效率的重要手段。
物流企业应注意以下几点:•做好车辆保养工作:定期更换机油、空气滤清器、刹车片、轮胎等,保证车辆良好的工作状态和正常的耗油量;•精心维护车辆:维护好汽车外观和内部设施,保持车辆整洁和舒适,提高司机的工作积极性;•进行车辆保险:购买综合保险,保证车辆在运输过程中的安全。
汽车抬吊专项方案
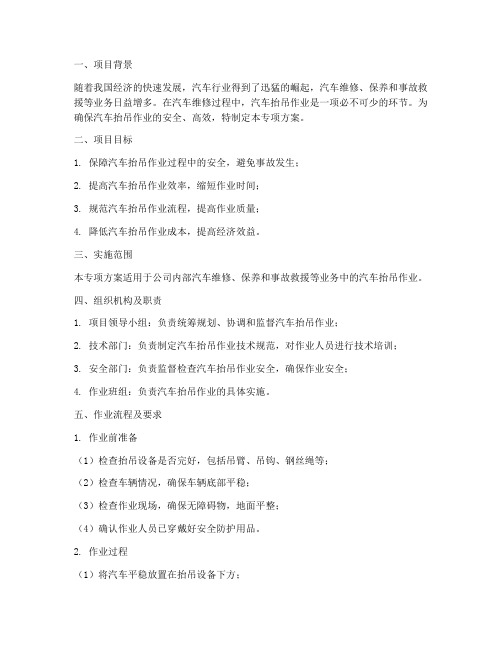
一、项目背景随着我国经济的快速发展,汽车行业得到了迅猛的崛起,汽车维修、保养和事故救援等业务日益增多。
在汽车维修过程中,汽车抬吊作业是一项必不可少的环节。
为确保汽车抬吊作业的安全、高效,特制定本专项方案。
二、项目目标1. 保障汽车抬吊作业过程中的安全,避免事故发生;2. 提高汽车抬吊作业效率,缩短作业时间;3. 规范汽车抬吊作业流程,提高作业质量;4. 降低汽车抬吊作业成本,提高经济效益。
三、实施范围本专项方案适用于公司内部汽车维修、保养和事故救援等业务中的汽车抬吊作业。
四、组织机构及职责1. 项目领导小组:负责统筹规划、协调和监督汽车抬吊作业;2. 技术部门:负责制定汽车抬吊作业技术规范,对作业人员进行技术培训;3. 安全部门:负责监督检查汽车抬吊作业安全,确保作业安全;4. 作业班组:负责汽车抬吊作业的具体实施。
五、作业流程及要求1. 作业前准备(1)检查抬吊设备是否完好,包括吊臂、吊钩、钢丝绳等;(2)检查车辆情况,确保车辆底部平稳;(3)检查作业现场,确保无障碍物,地面平整;(4)确认作业人员已穿戴好安全防护用品。
2. 作业过程(1)将汽车平稳放置在抬吊设备下方;(2)根据车辆型号和重量,选择合适的抬吊设备;(3)缓慢升起车辆,确保车辆平稳;(4)在抬吊过程中,密切关注车辆动态,防止倾斜;(5)完成抬吊作业后,将车辆缓慢放下,确保平稳着地。
3. 作业后检查(1)检查抬吊设备是否存在异常;(2)检查车辆底部是否存在损坏;(3)清理作业现场,确保无安全隐患。
六、安全措施1. 严格执行安全操作规程,确保作业安全;2. 定期对抬吊设备进行检查、维护,确保设备完好;3. 作业人员必须穿戴安全防护用品,如安全帽、防护手套、防滑鞋等;4. 设置安全警示标志,提醒作业人员注意安全;5. 作业现场配备应急物资,如急救包、灭火器等。
七、培训与考核1. 对作业人员进行安全操作规程培训,提高作业人员的安全意识;2. 定期组织作业人员进行技能考核,确保作业人员掌握必要的技能;3. 对作业人员进行安全教育,提高作业人员的安全意识。
起重(汽车)吊装专项施工方案(模板)

起重(汽车)吊装专项施工方案(模板)一、概述在进行起重(汽车)吊装作业时,需严格按照专项施工方案执行,以确保作业安全可靠。
本方案旨在规范起重(汽车)吊装作业流程,保障人员和设备的安全,提高作业效率。
二、准备工作1.施工前准备–确定吊装作业的具体要求和实施计划。
–组织相关人员参与方案讨论和制定。
–评估吊装现场的场地条件和周围环境,确保施工安全。
2.人员准备–指定吊装作业负责人,负责统筹协调整个作业流程。
–配备足够数量的吊装人员,确保各个环节顺利进行。
–进行必要的安全培训和演练,提高各级人员的应急处置能力。
3.设备准备–确保所有吊装设备完好无损,符合相关标准要求。
–对吊装设备进行定期检查和维护,确保安全使用。
–配备必要的辅助工具和安全设备,如安全带、安全帽等。
三、施工流程1.方案确认–根据实际情况确认吊装方案,包括吊装位置、吊装高度、安全措施等。
–确定吊装作业的具体步骤和顺序,制定详细的作业计划。
2.作业准备–按照方案要求将吊装设备和辅助工具放置到指定位置。
–做好各种预防措施,确保作业现场干净整洁、安全有序。
3.吊装作业–严格按照作业计划进行,保持通畅的作业通道,避免人员和设备交叉。
–各个吊装点的配重、加固等工作需有专人负责,确保吊装过程平稳进行。
4.安全检查–各吊装点吊装完成后,需进行安全检查,确保吊装设备完好,无异常。
–对吊装设备和作业现场进行清理整理,做到有序。
四、注意事项1.**严格遵守各项安全规定,确保作业安全可靠。
2.**注意防范作业现场的各类安全风险,保护好工作人员的人身安全。
3.**及时消除吊装作业中的问题和隐患,确保吊装顺利进行。
五、总结起重(汽车)吊装专项施工方案对于保障吊装作业的安全顺利进行至关重要。
只有严格遵守规定,做好预防措施,才能有效保护人员和设备安全,提高作业效率。
希望所有参与吊装作业的人员能够严格遵守本方案的要求,共同维护一个安全、有序的工作环境。
以上为起重(汽车)吊装专项施工方案(模板),请在实际作业中具体落实并根据实际情况进行适当调整。
大幅提升汽车覆盖件冲压模具加工效率的有效手段

4 .合 理 的 长 短 刀具 分 开加 工 在满足表 面加 工质量要 求 的前提下 ,尽量 长短 刀
具分开 加工 ,以提 高加 工效 率和 表面质 量 。现在 的大
制流畅的、适合高速加 工的刀轨 ,以充分体现设备
的高速加 工优势 。
3 .采用效率更高 的清角方法
分层 清角是 提 高粗 清 角 和 实 现 自动 化 的有 效 途 径 ,该方 法 可 以 自动 识 别 残 留 区域 ,对 残 留根 部 进 行 分层 去除 余 量 ,切 削 量 均匀 ,所 以 可 以 实现 高 速 进 给 ,提 高效 率 ,实现 自动 化 ,并 且 有 利 于提 高 刀 具 使用 寿命 ( 图 6 见 、图 7 。 )
编程 多花 1 ,数控 节约 lmi ,成 本上 考虑是 划 h O n 算 的 ,而且 对 于 有计 划地 统 一 安 排 生 产 来 说 ,这 不
是 浪费时 间 ,而 是 实实 在 在 地 缩 短 生 产 周期 。假 如 每 个程序 数 控 加 工 节 约 1 i,一个 工 件 加 工 下 来 , a rn 不止 2 、 0 0 3 个程 序 ,那 么可 以想 象 ,一 个 整车 的模 具 就因为 编 程 仔 细 了一 点 ,会 提 高 多 少 效 率 。所 以
合计
B 0 球 刀 4
5 7
一
平 均
15 00 15 0 0
25 mi h8 n 3 S 5 l mr 7 h2 i 2 lmi 1s h3 n 8
2o 0 o
以缩 短模 具 开 发 周 期 成 为 新 车 型 抢 占市 场 的 重 中
之重 。
要 牺牲 一点 数 控 时 间 ,但 总 的还 是 比传 统 的加 工 效
汽车制造业的生产效率提升方案
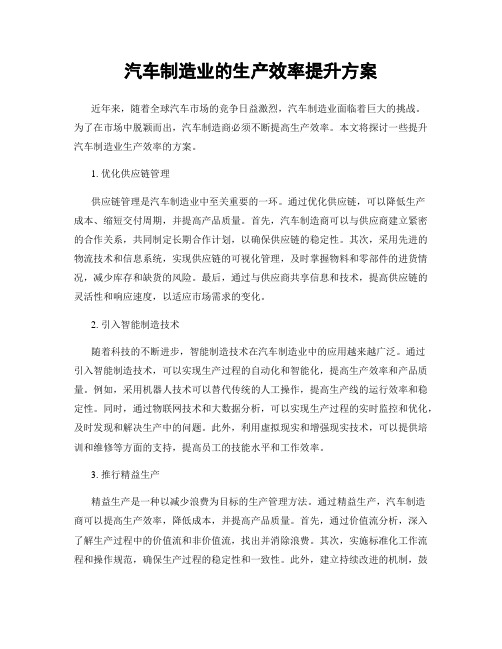
汽车制造业的生产效率提升方案近年来,随着全球汽车市场的竞争日益激烈,汽车制造业面临着巨大的挑战。
为了在市场中脱颖而出,汽车制造商必须不断提高生产效率。
本文将探讨一些提升汽车制造业生产效率的方案。
1. 优化供应链管理供应链管理是汽车制造业中至关重要的一环。
通过优化供应链,可以降低生产成本、缩短交付周期,并提高产品质量。
首先,汽车制造商可以与供应商建立紧密的合作关系,共同制定长期合作计划,以确保供应链的稳定性。
其次,采用先进的物流技术和信息系统,实现供应链的可视化管理,及时掌握物料和零部件的进货情况,减少库存和缺货的风险。
最后,通过与供应商共享信息和技术,提高供应链的灵活性和响应速度,以适应市场需求的变化。
2. 引入智能制造技术随着科技的不断进步,智能制造技术在汽车制造业中的应用越来越广泛。
通过引入智能制造技术,可以实现生产过程的自动化和智能化,提高生产效率和产品质量。
例如,采用机器人技术可以替代传统的人工操作,提高生产线的运行效率和稳定性。
同时,通过物联网技术和大数据分析,可以实现生产过程的实时监控和优化,及时发现和解决生产中的问题。
此外,利用虚拟现实和增强现实技术,可以提供培训和维修等方面的支持,提高员工的技能水平和工作效率。
3. 推行精益生产精益生产是一种以减少浪费为目标的生产管理方法。
通过精益生产,汽车制造商可以提高生产效率,降低成本,并提高产品质量。
首先,通过价值流分析,深入了解生产过程中的价值流和非价值流,找出并消除浪费。
其次,实施标准化工作流程和操作规范,确保生产过程的稳定性和一致性。
此外,建立持续改进的机制,鼓励员工提出改善意见,并及时落实。
最后,通过培训和激励机制,提高员工的技能和积极性,推动精益生产的实施。
4. 加强质量管理质量是汽车制造业的核心竞争力之一。
通过加强质量管理,可以提高产品的一致性和可靠性,满足消费者对产品质量的要求。
首先,建立完善的质量管理体系,包括质量控制、质量保证和质量改进等方面的工作。
年度汽车零部件行业工作总结提升零部件品质提高供应链效率
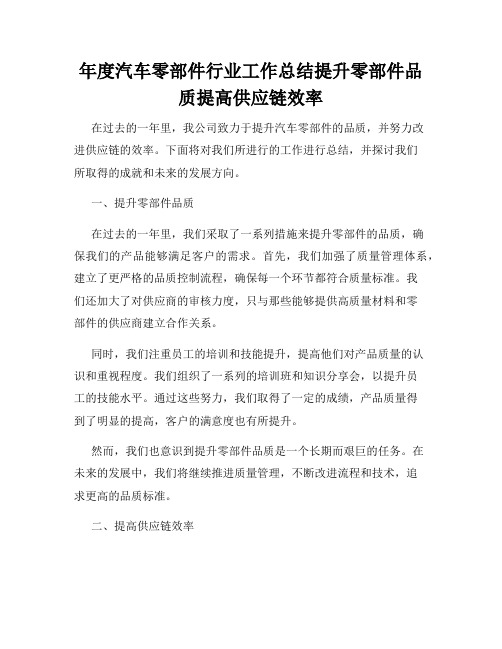
年度汽车零部件行业工作总结提升零部件品质提高供应链效率在过去的一年里,我公司致力于提升汽车零部件的品质,并努力改进供应链的效率。
下面将对我们所进行的工作进行总结,并探讨我们所取得的成就和未来的发展方向。
一、提升零部件品质在过去的一年里,我们采取了一系列措施来提升零部件的品质,确保我们的产品能够满足客户的需求。
首先,我们加强了质量管理体系,建立了更严格的品质控制流程,确保每一个环节都符合质量标准。
我们还加大了对供应商的审核力度,只与那些能够提供高质量材料和零部件的供应商建立合作关系。
同时,我们注重员工的培训和技能提升,提高他们对产品质量的认识和重视程度。
我们组织了一系列的培训班和知识分享会,以提升员工的技能水平。
通过这些努力,我们取得了一定的成绩,产品质量得到了明显的提高,客户的满意度也有所提升。
然而,我们也意识到提升零部件品质是一个长期而艰巨的任务。
在未来的发展中,我们将继续推进质量管理,不断改进流程和技术,追求更高的品质标准。
二、提高供应链效率供应链是我们公司运营的重要环节,影响着产品的交付能力和成本效益。
为了提高供应链效率,我们采取了一系列措施来简化流程、优化资源配置,并与供应商建立了更紧密的合作关系。
首先,我们引入了先进的物流管理系统,实现了物流信息的实时可视化和高效的货物追踪。
通过这个系统,我们能够更好地掌握库存情况和交付进度,提前做好物流安排,从而减少了时间的浪费和资源的损失。
其次,我们与供应商建立了长期稳定的合作关系,分享了更多的信息和资源。
我们共同制定了交付计划和库存管理方案,提前预测零部件的需求量,并进行合理的库存配置。
这样一来,我们能够更好地应对市场需求的变化,减少了库存积压和资金占用。
当然,供应链优化是一个不断迭代的过程,我们需要根据市场需求的变化和技术的进步来不断改进我们的工作。
在未来,我们将进一步加强与供应商的合作,完善物流管理系统,提高供应链的灵活性和响应能力。
总结:通过一年的努力,我们在提升零部件品质和提高供应链效率方面都取得了明显的成绩。
汽车零部件制造质量提升解决方案
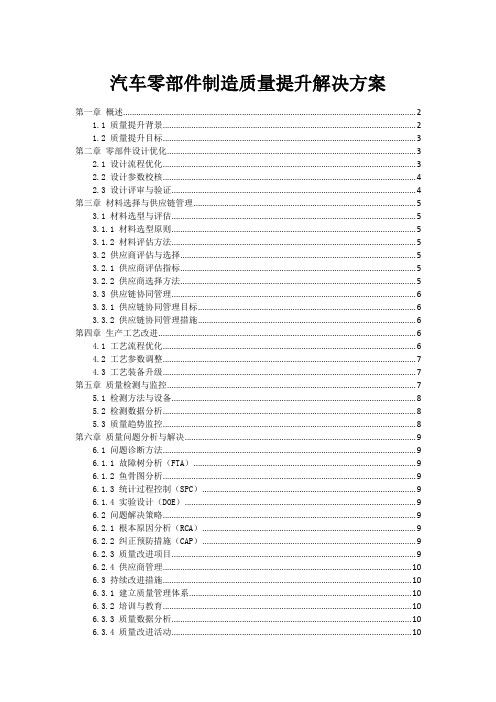
汽车零部件制造质量提升解决方案第一章概述 (2)1.1 质量提升背景 (2)1.2 质量提升目标 (3)第二章零部件设计优化 (3)2.1 设计流程优化 (3)2.2 设计参数校核 (4)2.3 设计评审与验证 (4)第三章材料选择与供应链管理 (5)3.1 材料选型与评估 (5)3.1.1 材料选型原则 (5)3.1.2 材料评估方法 (5)3.2 供应商评估与选择 (5)3.2.1 供应商评估指标 (5)3.2.2 供应商选择方法 (5)3.3 供应链协同管理 (6)3.3.1 供应链协同管理目标 (6)3.3.2 供应链协同管理措施 (6)第四章生产工艺改进 (6)4.1 工艺流程优化 (6)4.2 工艺参数调整 (7)4.3 工艺装备升级 (7)第五章质量检测与监控 (7)5.1 检测方法与设备 (8)5.2 检测数据分析 (8)5.3 质量趋势监控 (8)第六章质量问题分析与解决 (9)6.1 问题诊断方法 (9)6.1.1 故障树分析(FTA) (9)6.1.2 鱼骨图分析 (9)6.1.3 统计过程控制(SPC) (9)6.1.4 实验设计(DOE) (9)6.2 问题解决策略 (9)6.2.1 根本原因分析(RCA) (9)6.2.2 纠正预防措施(CAP) (9)6.2.3 质量改进项目 (9)6.2.4 供应商管理 (10)6.3 持续改进措施 (10)6.3.1 建立质量管理体系 (10)6.3.2 培训与教育 (10)6.3.3 质量数据分析 (10)6.3.4 质量改进活动 (10)6.3.5 持续跟踪与评估 (10)第七章人员培训与素质提升 (10)7.1 员工培训计划 (10)7.2 培训效果评估 (11)7.3 员工激励机制 (11)第八章设备管理与维护 (11)8.1 设备维护保养 (11)8.1.1 维护保养的意义 (11)8.1.2 维护保养措施 (12)8.2 设备故障处理 (12)8.2.1 故障处理原则 (12)8.2.2 故障处理流程 (12)8.3 设备升级与改造 (12)8.3.1 设备升级与改造的必要性 (12)8.3.2 设备升级与改造措施 (13)第九章质量管理体系建设 (13)9.1 质量管理体系构建 (13)9.1.1 确定质量方针和目标 (13)9.1.2 制定质量管理计划 (13)9.1.3 建立质量组织结构 (13)9.1.4 制定质量管理制度和程序 (13)9.1.5 质量培训与教育 (13)9.2 质量管理体系运行与维护 (13)9.2.1 质量管理体系的实施 (14)9.2.2 质量监测与评估 (14)9.2.3 质量改进与优化 (14)9.2.4 内部审计与监督 (14)9.3 质量管理体系认证 (14)9.3.1 认证准备 (14)9.3.2 认证申请与审核 (14)9.3.3 认证后的监督与维护 (14)第十章质量提升效果评估与持续改进 (14)10.1 质量提升效果评估方法 (15)10.2 持续改进计划 (15)10.3 质量提升成果分享与推广 (15)第一章概述1.1 质量提升背景我国经济的持续增长和汽车产业的快速发展,汽车零部件制造业作为汽车产业的重要组成部分,其质量水平直接影响着整车的功能、安全与可靠性。
文昌市汽车配件厂仓储效率提升策略探究

文昌市汽车配件厂仓储效率提升策略探究【摘要】商品的仓储活动是在商品的生产和流通过程中供求矛盾的集中体现,无论是一个国家,还是一个企业,都需要保持或进行某些仓储活动。
仓储是集中反映工厂物资活动状况的综合场所,是连接生产、供应、销售的中转站,因此,仓储效率对促进企业生产提高效率起着重要的辅助作用。
本文通过对文昌市汽车配件厂的仓储现状和问题的研究及对其仓储的各个作业环节进行了分析,结合科学的仓储管理理论,从人员安排、出入库流程、仓库软硬件设施、仓库布局等方面提出了调整优化方案,并对出入库流程和仓库布局进行了重组,确保新的仓储方案能够解决问题,使得配件厂仓储内部的各个作业流程更加合理,以达到提高仓储效率的目的,从而提升企业的仓储效率,进而提升企业的竞争力。
【关键词】仓储仓储管理仓储效率马克思曾在《资本论》中写过:“没有商品储备,就没有商品流通。
正是有了这种储备,流通过程以及包含流通在内的再生产过程的不断进行,才得到保证。
”在现在这种社会分工和专业化生产条件下,为了保证社会再生产过程的顺利进行,就得存储一定量的物资,用以满足一定时间内社会生产和消费的需要。
仓储效率指的是在日常作业中,主要体现在对仓储三大资源的利用情况,即对人工、空间和设备的使用情况来衡量,以达到储存空间的最大化利用和搬运路径和时间最优化为目标。
衡量仓储效率的指标有很多,具体有:仓储货物流量(吞吐量)、订货批量与订货周期、平持持有库存、安全存货、订货前置时间、存货周转率、仓储空间利用率、作业周期时间、作业计划标准等等。
一、文昌市汽车配件厂仓储情况简介文昌市汽车配件厂是一家集研发,生产,销售于一体的专业厂家,位于海南省文昌市文城镇文建路7号,成立于1998年。
公司经营范围涉及各种车辆修配和生产汽车配件。
其主要生产产品有汽车发动机配件系列,如汽油泵、柴油泵、气缸垫、曲轴、连杆、皮带等;汽车制动零部件系列,如刹车片、刹车蹄、刹车鼓、压缩机、真空加力器、制动分泵、制动踏板总成等;汽车电器系列,如起动机、发电机、电机、雨刮电机、传感器、分电器、继电器等,公司的原材料仓库存放共计三千多种的零配件。
提升汽车零件生产效率的工艺改进方法

提升汽车零件生产效率的工艺改进方法在现代社会中,汽车产业已经成为了一个重要的支柱产业。
为了满足市场对汽车的需求,汽车制造商需要提高生产效率,以保证产品质量和交货时间。
本文将介绍一些可以用于提升汽车零件生产效率的工艺改进方法。
一、制定合理的生产计划生产计划是提高生产效率的基础。
制造商需要根据市场需求和预期销量,制定合理的生产计划。
该计划应考虑零件供应链的各个环节,并合理安排生产时间和资源,以避免生产过剩或不足的情况。
二、优化生产线布局良好的生产线布局可以减少零件在生产过程中的运输时间和劳动强度。
制造商可以通过重新规划和调整生产线,将工序进行合理分配,缩短零件的运输距离,并减少工人的劳动强度。
此外,合理的生产线布局还可以减少生产过程中的浪费,提高生产效率。
三、引进自动化设备自动化设备的引入可以大大提高生产效率。
制造商可以考虑使用自动化机器人和智能控制系统来替代部分繁重和重复性工作。
这样不仅可以提高生产效率,还可以减少人力成本和人为错误。
四、精益生产方法精益生产方法是一种通过减少浪费和提高价值创造来提高生产效率的方法。
制造商可以通过分析生产流程,识别和消除各类浪费,如等待时间、过度生产、库存过剩等。
同时,制造商还可以通过优化零件加工和装配流程,减少非必要的动作和运动,提高工作效率。
五、供应链管理供应链管理的优化可以提高零件的供应速度和准确性。
汽车制造商可以与供应商建立密切的合作关系,共享信息和资源,并采用先进的技术来加强供应链管理。
此外,制造商还可以采用定制化的供应链解决方案,以满足不同型号和规格汽车零件的需求。
六、实施员工培训和激励机制员工的技能和积极性对产品质量和生产效率有着重要影响。
制造商可以通过加强员工培训,提高员工的技术水平和工作能力。
同时,制造商还可以激励员工通过奖励机制来激发员工的积极性和创造力,进一步提高生产效率。
七、持续改进和创新持续改进和创新是保持竞争力和提高生产效率的关键。
制造商应建立一个持续改进的机制,鼓励员工提出改进建议并予以实施。
汽车零部件制造企业生产效率提升解决方案
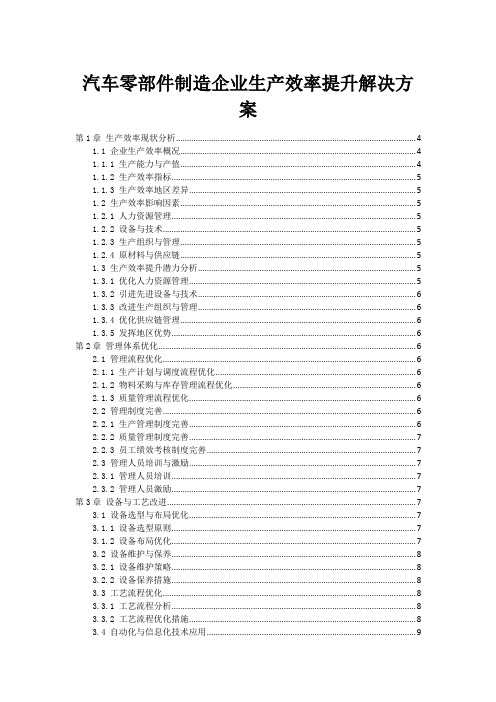
汽车零部件制造企业生产效率提升解决方案第1章生产效率现状分析 (4)1.1 企业生产效率概况 (4)1.1.1 生产能力与产值 (4)1.1.2 生产效率指标 (5)1.1.3 生产效率地区差异 (5)1.2 生产效率影响因素 (5)1.2.1 人力资源管理 (5)1.2.2 设备与技术 (5)1.2.3 生产组织与管理 (5)1.2.4 原材料与供应链 (5)1.3 生产效率提升潜力分析 (5)1.3.1 优化人力资源管理 (5)1.3.2 引进先进设备与技术 (6)1.3.3 改进生产组织与管理 (6)1.3.4 优化供应链管理 (6)1.3.5 发挥地区优势 (6)第2章管理体系优化 (6)2.1 管理流程优化 (6)2.1.1 生产计划与调度流程优化 (6)2.1.2 物料采购与库存管理流程优化 (6)2.1.3 质量管理流程优化 (6)2.2 管理制度完善 (6)2.2.1 生产管理制度完善 (6)2.2.2 质量管理制度完善 (7)2.2.3 员工绩效考核制度完善 (7)2.3 管理人员培训与激励 (7)2.3.1 管理人员培训 (7)2.3.2 管理人员激励 (7)第3章设备与工艺改进 (7)3.1 设备选型与布局优化 (7)3.1.1 设备选型原则 (7)3.1.2 设备布局优化 (7)3.2 设备维护与保养 (8)3.2.1 设备维护策略 (8)3.2.2 设备保养措施 (8)3.3 工艺流程优化 (8)3.3.1 工艺流程分析 (8)3.3.2 工艺流程优化措施 (8)3.4 自动化与信息化技术应用 (9)3.4.1 自动化技术 (9)3.4.2 信息化技术 (9)第4章供应链管理优化 (9)4.1 供应商选择与评价 (9)4.1.1 供应商选择标准 (9)4.1.2 供应商评价方法 (9)4.2 物料采购策略 (10)4.2.1 集中采购与分散采购 (10)4.2.2 竞争性谈判与框架协议 (10)4.2.3 供应商管理库存(VMI) (10)4.3 库存管理与控制 (10)4.3.1 库存分类管理 (10)4.3.2 库存控制方法 (10)4.3.3 库存分析与优化 (10)4.4 物流与配送优化 (10)4.4.1 物流网络优化 (10)4.4.2 配送策略优化 (11)4.4.3 物流信息化建设 (11)第五章产品研发创新 (11)5.1 产品设计优化 (11)5.2 材料替代与升级 (11)5.3 产品标准化与模块化 (11)5.4 研发团队建设与激励 (11)第6章质量控制与改进 (12)6.1 质量管理体系建设 (12)6.1.1 制定质量方针和目标 (12)6.1.2 建立质量管理组织架构 (12)6.1.3 制定质量管理规章制度 (12)6.1.4 质量管理培训与教育 (12)6.2 质量检测与监控 (12)6.2.1 检测设备与方法的选型 (12)6.2.2 检测过程控制 (12)6.2.3 检测数据分析 (12)6.2.4 不合格品的处理 (12)6.3 质量问题分析与改进 (12)6.3.1 质量问题诊断 (13)6.3.2 制定改进措施 (13)6.3.3 改进措施的落实与跟踪 (13)6.3.4 持续改进 (13)6.4 质量文化培育 (13)6.4.1 质量意识教育 (13)6.4.2 质量活动开展 (13)6.4.3 质量激励政策 (13)6.4.4 质量文化建设 (13)第7章人力资源管理优化 (13)7.1 员工招聘与选拔 (13)7.1.1 岗位需求分析:明确各岗位的职责、技能和素质要求,为招聘提供准确的依据。
汽车维修服务质量效率保证措施方案3篇

汽车维修服务质量效率保证措施方案汽车维修服务质量效率保证措施方案3篇为确保事情或工作顺利开展,常常需要提前准备一份具体、详细、针对性强的方案,方案指的是为某一次行动所制定的计划类文书。
那么制定方案需要注意哪些问题呢?下面是小编收集整理的汽车维修服务质量效率保证措施方案,仅供参考,希望能够帮助到大家。
汽车维修服务质量效率保证措施方案1本厂如能中标,将会采取以下措施为定点维修单位提供及时便捷、优质高效的维修服务:一、建立完善的质量保证系统。
(1)建立更规范、灵活的经营和管理机制(包括生产管理体制、质量控制、人才培训、市场开发、战略规划等方面的机制),完善严格管理,确保为客户提空高效优质的服务。
(2)加强硬件投入,提高设备科技含量。
在原有设备的基础上,继续引进更先进的设备,以适应汽车维修服务不断发展的需要;同时加快建立与各大品牌汽车厂家协作关系,寻求更大的.技术、设备及配件支持。
二、提供优惠合理的维修服务价格我与南宁、崇左等地较大的配件供应商均有长期合作关系,我厂材料配件部门通过电脑网络可随时掌握配件市场的最新行情,以便为客户提供优质优价的配件:同时我厂还与各牌汽车厂家在南宁市、崇左市的特约配件供应商保持良好关系。
三、建立完善的售前、售中、售后服务系统。
进一步完善汽车维修运作程序,实行报修、审批、修理、检验、竣工、出厂一条龙管理,对主要零配件实行严格监控下以旧换新制度,进一步完善各部门的电脑管理,实行维修价格公开,为客户维修车辆提供质量跟踪服务。
四、提供三位一体的维修。
建立零配件供应、汽车维修、质量跟踪、咨询为一体的经营框架。
确保全方位地为客户提供优质优先高效的服务。
五、维修质量保证1、承诺按照交通部《机动车维修管理规定》第四章“质量管理”规定执行:在保修期内,因维修质量造成的机械事故和经济损失,由本厂负责和赔偿。
2、承诺维修合格出厂车辆和质量保证里程为:(1)整车修理或总成修理保证期为车辆行驶20000公里或100天内;(2)二级维护质量保证期为车辆行驶5000公里或30天内;(3)一级维护、小修及专项修理质量保证期为车辆行驶20xx公里或10天内;3、承诺对公务用车维修质量实行“出厂质量保证期制度”。
汽车行业“降本增效”活动方案

汽车行业“降本增效〞活动方案“降本增效〞对提升公司整体效益有着重大意义,为确保降低本钱、提升效率和增加效益目标实现,切实增强员工的节约意识、本钱意识、效率意识和创新意识,我公司在全体员工中广泛开展“降本增效、从我做起〞的工作,针对此工作的展开,我公司拟定了2021年“降本增效〞的活动方案,汇总如下:一、针对用电设备方面节约用电,控制用电量1.空调:在夏季办公内采用自能风降温,尽量少用空调等电器设备。
在夏季使用空调时,也必须将空调调至26度,并随手关门,下班前一小时将空调关闭,下班后,关闭电源总开关。
2.打印机:打印机在不用的时候处于关机状态,除了合同用彩打,其他文件打印尽量使用普通打印机。
3.照明:工作时间尽量采用自能光,在光照允许的情况下,尽量不开启室内照明设备。
车间区域及库存区实行隔灯照亮方法,隔一灯开一灯,在不影响工作情况下尽量少开灯。
4.电脑:下班及时关闭电脑电源。
二、针对公司的采购用品控制本钱,降低消耗采取新方法,降低办公用品等非生产用的采购本钱及消耗;控制减少消耗品的使用量,提高循环使用物质寿命,提高废料回收率等。
针对各个部门采取措施如下:1.市场部:物料制作,多比照,找廉价又好的广告公司。
2.售后部:售后前台工单打印纸和三件套合理使用;控制油漆用量;及时的回收一些剩余的油品和没用完的养护品,二次利用。
3.行政部:节约办公用纸,标准用纸制度。
4.客服部:客服车友会活动,把预算本钱控制到最低;客户配合电访礼品合理采购分配,控制本钱;5.装潢部:在日常贴膜施工中,做到不铺张不浪费,裁切标准。
制定出单卷膜及单车膜的损耗率,做到赏罚清楚。
在日常采购装潢产品中,尽量集中采购,减少托运费。
三、提高效率,提升效益1.售后车间定期的维护举升机,烤漆房,气泵等设备,减少故障的发生,延长使用寿命;2.提高一次修复率,减少返修,带来的人力和材料的浪费;3.加强废件的处理,保持好空间的正常运转;四、成立“降本增效〞小组,按照降本增效工作方案内容,逐项开展工作。
提高汽车零件生产效率的关键技巧

提高汽车零件生产效率的关键技巧为了满足汽车市场的不断增长需求,提高汽车零件的生产效率变得尤为重要。
高效的生产过程可以确保零件的质量,缩短生产周期,并降低成本。
本文将介绍几个关键的技巧,帮助企业提高汽车零件生产效率。
一、优化生产流程优化生产流程是提高生产效率的首要任务。
首先,需要对现有的生产流程进行全面的评估和分析。
识别出可能存在的瓶颈和浪费,并采取相应的措施进行改进。
其次,借助现代化的生产设备和技术,提高生产线的自动化水平。
引入自动化设备和机器人技术,可以减少人工操作,提高生产速度和准确性。
最后,建立科学的生产计划和排程,确保物料和资源的合理调配,避免产能的浪费和短缺。
二、培训和提升员工技能员工是生产效率提升的关键因素之一。
通过培训和提升员工的技能,可以提高他们的专业水平和工作效率。
首先,企业应该为员工提供必要的培训,使其掌握先进的生产技术和操作方法。
其次,通过定期的技能培训和知识分享会,持续提升员工的专业素养。
此外,鼓励员工参与相关的学习和研究活动,积极推动技术创新和自主开发,提高生产效率。
三、优化供应链管理供应链管理对于汽车零件生产效率的提升至关重要。
建立稳定的供应链合作伙伴关系,确保物料的及时供应和质量可控。
同时,通过建立信息化的供应链管理系统,实现对供应链的全面监控和协调,及时识别和解决问题。
此外,压缩供应链的时间和成本,降低物料库存和运输成本,对于提高生产效率也起到了积极的作用。
四、持续改进和创新持续改进和创新是保持竞争优势和提高生产效率的重要手段。
企业应该建立一个改进和创新的文化氛围,鼓励员工提出改进意见和创新性的工作方案。
同时,利用现代化的信息技术,实施数据分析和绩效管理,对生产过程进行监控和分析,及时发现问题并采取措施进行改进。
此外,与相关的研发机构和高校合作,积极追求科技创新和研发成果的转化,推动生产效率的不断提高。
五、质量管理和维护保证产品质量是汽车零件生产效率提高的关键。
建立和实施有效的质量管理体系,对生产过程和产品进行全面的质量控制和检测。
- 1、下载文档前请自行甄别文档内容的完整性,平台不提供额外的编辑、内容补充、找答案等附加服务。
- 2、"仅部分预览"的文档,不可在线预览部分如存在完整性等问题,可反馈申请退款(可完整预览的文档不适用该条件!)。
- 3、如文档侵犯您的权益,请联系客服反馈,我们会尽快为您处理(人工客服工作时间:9:00-18:30)。
2017/3/16 作成:么广辉
效率?
相对作业目的所采用的工具及方法,是否最 合适并被充分利用! 效率可以作为衡量实际执行情况与理论标准规划 之间的相符程度
一、生产率的定义
生产率是经济学上一个用来衡量生产系统转换效率的指 标,一般定义为“生产率就是产出与投入之比”。即
产出(O) 生产率(P) 投入(I)
2)合并(Combine)对于无法取消而又必要者,看是否能合并,以达到省时 简化目的。如合并一些工序或动作,或由多人于不同地点从事的不同操作,
改为由一人或一台设备完成。
3)重排(Rearrange)经过取消、合并后,可再根据“何人、何处、何时” 三提问进行重排,使其能有最佳的顺序、除去重复、办事有序。 4)简化(Simple)经过取消、合并、重排后的必要工作,就可考虑能否采用 最简单的方法及设备,以节省人力、时间及费用。
确认每日实际投入 和标准投入差异,即:标准作 业执行度
找出影响效率的原因,步步分析改善
作为生产管理指标之一,纵向横向管控
作业效率分析--提升实际产出
生产效率管理
班组 前处理 PVC 打磨
Xx车间生产效率管控表
标准节 标准 单台工 出勤 工作时 内部损 外部损失 生产效 作业效 内部转 外部转 产量 投入工时 产出工时 拍 人力 时 人数 间 失工时 工时 率 率 嫁率 嫁率 3.08 3.00 3.00 11 23 22 0.56 1.15 1.10 15 31 27 14.10 13.60 12.43 240 227 240 211.5 421.6 335.61 135.52 261.05 264.00 0.00 0.00 0.00 25.05 64.08% 72.68% 0.00% 11.84% 36.27 61.92% 67.75% 0.00% 8.60% 31.59 78.66% 86.84% 0.00% 9.41%
例如,某一单元观测时间为0.8min, 评比为110%,宽放为5%,则正 常时间为0.88min,标准时间为0.924min
标准时间的计算方法
作业效率分析—降低投入标准 标准时间的形成
• 宽放的定义 1.操作过程中,作业人员的疲劳,需休息,以资恢复. 2.满足操作人员的个人需要. 3.领班之作业指示或外人干扰. 4.工作准备与清扫. 5.操作时之机器干扰. 6.材料不良 以上等因个人私务,疲劳或暂停工作所给予的时间称之. 宽放的种类:
实际作业时间 157s
宽放时 间:16S
核算产能时间:实际作业时 间*(1+10%)≦顾客节拍 T.T 173s
线速: ≦顾 客节拍T.T
宽放参考
作业效率分析—降低投入标准 生产线平衡 • 调整各工序间的作业时间,使差距很小。
各工序间的作业时间 差距越小,生产线就 越平衡。
木桶理论
降低瓶颈工位的时间,会提高产 能 旧的瓶颈被消除,会有新的瓶颈 出现 减少非瓶颈工位时间,与产能增 加无任何贡献. 当木桶每个木板高度一致的时候, 即流水线每个工位时间一样的时候, 木桶盛水量最大,流水线产能最 大.
相关人员工作描述
一线员工: 熟悉标准作业,完全按照标准作业操作,有问题及时反馈 班组长: 1、准确记录每天每人实际工作时间,班组整体停线时间,产出数量,停线原因 2、熟练掌握简单生产效率分析,标准作业时间制定 3、每日巡检标准作业,周度抽检 生产管理人员: 1、核算每日生产效率,区分生产效率、作业效率、转嫁率 2、周度分析影响作业效率因素,选取80/20前三项立案改善
转嫁工时:停线时间*受影响
出勤人数
10.12 10.13 10.17 10.18 10.21
7:30-7:50
20分钟
17:10-17:20 11:55-13:05 9:05-9:40 11:00-12:30 9:27-9:45
15:00-15:42 6:30-6:50 7:35-7:45
10分钟 70分钟 35分钟 90分钟 18分钟
作业效率分析—降低投入标准
1、确定有效工作时间
实际工作时间: 7.67H 非计划能开线时 间:休息、5s时 间
正常上班时间8H
2、确定目标作业循环时 间
1、汇总各作业单元时间,根据 不同节拍,按作业时间、工艺、 治具限制等重新划分工位作业内 容。 2、不同作业岗位,可以不同宽 放(参考下表); 3、满足宽放后作业循环时间CT ≦顾客节拍T.T
均衡生产编程;现场IE改善:动作改善、 流程改善;减少异常停线 产品流程价值分析;现场IE改善;作业方 式优化,
作业效率分析—降低投入标准 标准时间的构成 观察时间
私事 疲劳 程序 特别 宽放 宽放 宽放 宽放
评比因素
标准时间=正常时间+(正常时间× 宽放百分数)=正常时间 × (1+宽放率)
作 业 时 间
工序 1 2 3 4 5
作 业 时 间
工序 1
1人 2人
2
3
4
5
1、分割作业 省略工序
2、合并作业 省略工序
3、减人
作业效率分析—降低投入标准 生产线平衡
分析时的“ECRS”四大原则
1)取消(Elminate)取消为改善的最佳效果,如取消不必要的工序、操作、
动作,这是不需要投资的一种改进,是改进的最高原则。
• 世界性的宽放标准
联合国国际劳工标准局 固定宽放 介于9%~11% 项 私事宽放 基本疲劳宽放 目 男 女 5% 7% 4% 4%
作业效率分析—降低投入标准
测量标准时间应注意
• • • • 识别完整的作业单元(周期) 单纯的作业 人机联合作业 每个作业循环的加工数量 拆解动作,如目检、搬运、组装、等待、调整等等 判定作业为正常状态 测量数据次数 剔除异常,求平均数
再作业 纯作业工时 标准 效率 (实动工时-再作业) 工时 生产 损失 量 良品完成工时作业者责任 工时 (生产量*ST) 损失工时
无价值
有价值
作业效率 = 产量*标准工时/投入时间=实际产量/标准产量=标准作业时间/实际作业时间
作业效率提升工作规划之一:
建立每日基于标准作业的工时效率统计、分析、管理考核
20分钟 42分钟
烘房入口沥水滚床感应器 涂装前处理 故障 焊装储存线故障 焊装厂 总装厂储存线故障 总装厂 全厂影响 焊装储存线故障 焊装厂 总装厂储存线无吊具 不同班组的各种停线, 总装厂 全厂影响 转化为责任工时,统一 焊装储存线故障 焊装厂 总装储存线断断续续故障 做80/20分析及则责任 总装厂 7次 考核
1.生理宽放:因操作人员领生理需要或为操作人员工作书市所给予的时间;如
饮水,如厕,擦汗,…视工作环境而定.
2.疲劳宽放:作业员位恢复疲劳所要的休息时间,可为团体及精神两种.
标准时间的形成
3.作业迟延宽放:作业员在施工期间,非由于本身能力所可控制而发生无可 避免之非工作时间,所增列之时间,如:清扫清理,工作指示,外人干扰,材 料不良,作业人员偶尔停顿. 4.特殊宽放 a.管理宽放:如 开会. b平衡宽放:生产线多人配因个人效率不同而给予宽放时间.(建议不加宽 放) c.小批量宽放:是生产批量大小而给予之宽放.(建议不要算)
节拍时间
29
10 0 工人 A
18
10 工人 工人 12 工人
15 工人
7
工人
B
C
D
E
F
生产线平衡
40 30 20
12 节拍时间
24s
7
15
10
29 18
10
0 工人 A
工人
工人
工人
工人
工人
B
C
D
E
F
作业效率提升工作规划之二:
可代替每 日节拍
纯人员效率,衡 面漆 2.95 32 1.57 48 12.10 240 580.8 377.60 0.00 56.16 65.01% 71.97% 0.00% 9.67% 量标准作业执行 精饰 3.07 27 1.38 35 12.27 239 429.45 330.18 0.00 64.05 76.88% 90.36% 0.00% 14.91% 情况;新人培训 合计 3.00 115 5.77 154 64.50 1186 1978.96 1368.35 0.00 213.12 69.14% 77.49% 0.00% 10.77% 熟练程度 投入工时:出勤人数*工作时 生产异常记录 精确区分、量化损 间 失工时,及时把握 异常时 日期 时间段 异常描述 归类 责任人/单位 对策 间 作业效率与生产效 产出工时:产量*最新标准工 焊装厂吊具故障,损失 率起伏原因 10.9 14:28-15:07 39分钟 焊装厂 3.25工时 时
作 业 效 率 提 升
作业效率分析--提升实际产出
作业效率体系 工时组成:
总出勤工时(投入工时) (投入人员*作业时间) 作业工时 投入工时 直接工时 直接人员*作业时间 实动工时 (直接工时-无作业工时) 无作业 工时 间接 工时 间接人员的出勤时间班组长、调度、统计、 工具管理、搬运、物料人员 可控工时(物料供应不足、部品不良,调机 时间)不可控工时(停电,灾害等) 工程/工艺更改、不合格批次返工外加 工、部品不良 作业不良、生产线不良修理、生产线不 平衡
作业效率分析—降低投入标准 生产线平衡 1、缩短瓶颈时间 提高产能
1人
作 业 时 间
工序 1 2 3 4 5
作 业 时 间
工序 1 2 3 4 5
作 业 时 间
工序 1 2
2人
3
4
5
1、分割作业2、缩Fra bibliotek时间3、增加人员
作业效率分析—降低投入标准 生产线平衡 2、减少人员
作 业 时 间
工序 1 2 3 4 5