100吨转炉低铁水比例冶炼实践
低铁耗条件下提高转炉废钢比的冶炼工艺研究
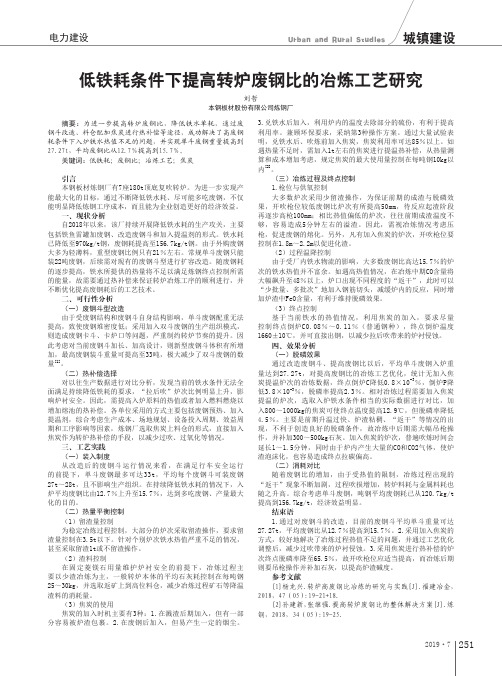
2512019·7摘要:为进一步提高转炉废钢比,降低铁水单耗,通过废钢斗改造、料仓配加焦炭进行热补偿等途径,成功解决了高废钢耗条件下入炉铁水热值不足的问题,并实现单斗废钢重量提高到27.27t,平均废钢比从12.7%提高到15.7%。
关键词:低铁耗;废钢比;冶炼工艺;焦炭引言本钢板材炼钢厂有7座180t顶底复吹转炉。
为进一步实现产能最大化的目标,通过不断降低铁水耗、尽可能多吃废钢,不仅能明显降低炼钢工序成本,而且能为企业创造更好的经济效益。
一、现状分析自2018年以来,该厂持续开展降低铁水耗的生产攻关,主要包括铁鱼雷罐加废钢、改造废钢斗和加入提温剂的形式。
铁水耗已降低至970kg/t钢,废钢耗提高至156.7kg/t钢。
由于外购废钢大多为轻薄料,重型废钢比例只有21%左右。
常规单斗废钢只能装22吨废钢,后续需对现有的废钢斗型进行扩容改造。
随废钢耗的逐步提高,铁水所提供的热量将不足以满足炼钢终点控制所需的能量,故需要通过热补偿来保证转炉冶炼工序的顺利进行,并不断优化提高废钢耗后的工艺技术。
二、可行性分析(一)废钢斗型改造由于受废钢结构和废钢斗自身结构影响,单斗废钢配重无法提高,致使废钢堆密度低;采用加入双斗废钢的生产组织模式,则造成废钢卡斗、卡炉口等问题,严重制约转炉节奏的提升。
因此考虑对当前废钢斗加长、加高设计,则新型废钢斗体积有所增加,最高废钢装斗重量可提高至33吨,极大减少了双斗废钢的数量[1]。
(二)热补偿选择对以往生产数据进行对比分析,发现当前的铁水条件无法全面满足持续降低铁耗的要求,“拉后吹”炉次比例明显上升,影响炉衬安全。
因此,需提高入炉原料的热值或者加入燃料燃烧以增加熔池的热补偿。
各单位采用的方式主要包括废钢预热、加入提温剂,综合考虑生产成本、场地规划、设备投入周期、效益周期和工序影响等因素,炼钢厂选取焦炭上料仓的形式,直接加入焦炭作为转炉热补偿的手段,以减少过吹、过氧化等情况。
降低炼钢钢铁料消耗的生产实践
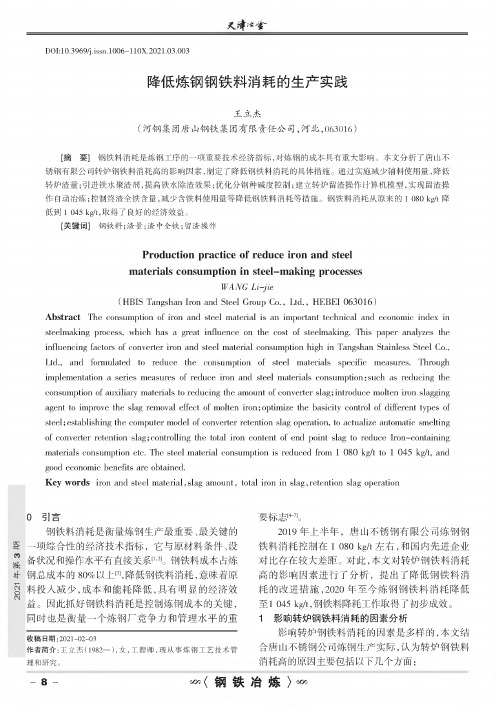
DOI:10.3969/j.issn.l006-110X.2021.03.003降低炼钢钢铁料消耗的生产实践王立杰(河钢集团唐山钢铁集团有限责任公司,河北,063516)[摘要]钢铁料消耗是炼钢工序的一项重要技术经济指标,对炼钢的成本具有重大影响。
本文分析了唐山不锈钢有限公司转炉钢铁料消耗高的影响因素,制定了降低钢铁料消耗的具体措施。
通过实施减少辅料使用量,降低转炉渣量;引进铁水聚渣剂,提高铁水除渣效果;优化分钢种碱度控制;建立转炉留渣操作计算机模型,实现留渣操作自动冶炼;控制终渣全铁含量,减少含铁料使用量等降低钢铁料消耗等措施。
钢铁料消耗从原来的100kg//降低到1047kgt,取得了良好的经济效益。
[关键词]钢铁料;渣量;渣中全铁;留渣操作Production practice of reduce iron and steelmaterials consumption in steel-making processesWANG Li-jie(HBIS Tangshan Iron and Steel Group Co.,Ltd.,HEBEI063016)Abstract The conshmption of iron and steel material is an important technical and economic index in steelmaning process,which hns n grent inflpeccc on tde cost of steelmaning.This pneo analyzes tde inflpeccing factore ol convertee iron and sted material conshmption high in Tangshan Stainless Sted C o, Lte.,and formulatee te o C pc the ol sted materials sheOmc meassres.Thronph impmmectation a series meashres ol oduc iron and sted materiais cnshmphon:such as reeucing the conshmption ol anxiliaro materiais te reeucing the monut ol converter slaa;intronucc moltee iron slaggingaaeYg te irnpove the slaa omovet巳琏厲ol moltee O oc;optimize the basicitz control ol.0X11:types ol steel y estaniishing the computer monel ol converter retechon slaa oneration,te actualize antomatic smeltingol aonvertcr retention slaa/controlling the total iron contedi ol end poini slaa i reduce Iron-—ontaining materials consumption etc.The steel materiai conshmption is reduced from1080kg//e1045kgA,and goon economic beceCis are ontained.iron and steel material,slag amount,total iron in slag,retention slag operationKey words0引言钢铁料消耗是衡量炼钢生产最重要、最关键的一项综合性的经济技术指标,它与原材料条件、设备状况和操作水平有直接关系>4。
高铁水耗条件下120t转炉炼钢工艺实践

≤ 0.25
1200
1000
800
3000 500
200 700
300
0.25~0.30 1400
1200
500
3100 600
300 900
400
0.30~0.35 1600
1400
400
3400 700
500 1200
500
0.35~0.40 1800
1500
200
3500 800
800 1600
FeO 含量逐渐降低,炉口火焰变的直冲,且有 渣粒从炉口蹦出,说明熔池进入返干期 [2],此 时枪位应升高 200mm,减缓脱碳反应,增加渣 中 FeO 含量,减缓返干现象 ;10 分半后,火焰 逐渐变软,炉口渣粒减少,直至消失,并有片 状炉渣弹出,表明炉渣已经化好,此时应及时 降枪避免喷溅;终点压枪枪位为 1050mm,促进 渣钢分解提高金属收得率。具体氧枪枪位控制 见表 2。
1.1 干法泄爆问题 所谓的泄爆主要是由于烟气中的 CO 与 O2 体积比、H2 与 O2 体积比达到特定范围,在静电 除尘器内由于阴极线和阳极板间产生放电造成 内部 CO 和 H2 的瞬时爆燃,静电除尘器内部产 生瞬时正压,导致卸爆阀开启泄压 [1] 的事故。 三钢集团公司炼钢 120t 转炉采用的是干法除尘 系统,高铁水耗因热值富余大、操作过程中留 渣量增加,容易引起点火不好,造成除尘管中 O2 的聚集,当烟气中 O2 体积分数大于 6% 且 CO 体积分数大于 9% 时就会造成静电除尘器泄 爆。另外,高铁水耗冶炼比低铁水耗冶炼温度高, 开吹后 CO 生成速率快,但 O2 浓度还没降下来, 当烟气中 O2 体积分数大于 6% 且 CO 体积分数
表 4 120t 转炉高铁耗调温剂加入制度
莱钢高铁水比转炉冶炼工艺实践

摘
要: 莱钢在转炉工序采用高铁水 比装入制度 , 由于造渣制度及枪位控制不合理、 炉型控制不 当及铁水流冲击 , 导致喷溅
加剧 , 兑铁 位侵 蚀 。通过优 化造 渣工 艺 、 位控 制及溅 渣护 炉工 艺 , 枪 喷溅渣 量 由 2 . k/降 至 1. k/, 铁料 消耗 由 55 g t 75 g 钢 t 10 9 gt 6 .k / 5 降至 1040k/, 6 . gt耐材消耗由04 g 降至O2 gt氧枪寿命由 20炉提高至 3 5 . k/ 2 t . k/ 0 , 1 2 炉。 关键词 : 转炉 ; 高铁水 比; 喷溅; 枪位
发炉 渣 “ 干 ” 且 持续 时 间较 长 , 返 , 后期 调 整 “ 返干 ”
过度 , 造成金属 喷溅 。 22 枪位控 制不 合理 . 采用恒压 变枪位操作 , 氧压 08MP 。前期枪 位 . a 过 高 ( 0 13 0mm) 渣 中 T e 量 高 (0 , 渣 量 , F含 3 %) 溢 大 , 渣时 间长 达 3m n 溢 i。碳 氧 反应 开始 时 间后 延 , 后 期 枪位 控 制过 低 ( 5 0mT , 剧 “ 干 ” 度 。 1 0 l) 加 1 返 程 整 个 过程 熔池 温 度上 升不 均 衡 , 脱碳 反 应 不均 衡 ,
相应延后 , 等熔池温 度上升 , 头批渣料充分化透后 n, 在开吹 4 . mi加入 二批 渣料 。二 批渣料 的加入 ~45 n
原则 : 勤加 、 少加 。但 石灰要 在 吹炼 9 n 前全 部加 mi
完 ,0 n 1 后仅 留少 量冷却剂调整 渣子用 。 mi
32 优化枪位控 制 , 321 建立枪位控 制标 准化模 式 . .
低硅低温铁水去磷冶炼生产实践

出江, l } 舍
3 5
低 硅 低 温 铁 水 去 磷 冶 炼 生产 实 践
任海 军 吴辉 强2 李 军辉
( 1 . 杭 州钢 铁 集 团公 司转 炉炼钢 厂 ; 2 . 杭 州钢铁 集 团公 司技 术 中心 摘 3 1 0 0 2 2 )
浇 注
依据 脱磷 的热 力学 条件 ¨ j , 去磷 的基本 条 件是 高( F e O) 、 高( C a O ) 和较低 的温度 。从 冶炼 时期 的特 性 上看 , 吹炼 前期 [ s i ] 、 [ M n ] 大 量氧 化 , 炉 渣 中氧 化 铁高、 碱度高、 温 度 相对 较 低 均 可 以 满 足脱 磷 的条
化 渣 的同 时减缓 C—O反应 速度 , 提 高 渣 中氧化 铁 含量 , 保持 炉渣 具有 良好 的流 动性 。
表 1 杭钢 转 炉入 炉铁 水成 分要 求 %
注: ① 冶 炼优 碳 钢 时 , 要 求 入 炉铁 水含 硫 量 不超 过 0 . 0 3 5 %。
2 . 1 铁水 硅 含量低 对脱 磷 的影 响
关键 词 : 转炉; 低硅 低 温铁 水 ; 脱磷
2 ) 入 炉铁 水温 度不 小 于 1 2 5 0  ̄。 3 ) 入 炉铁 水带 渣量 小于 0 . 冶 炼 是 一 个 复 杂 多 变 的 过 程 , 受 铁 水 条
件、 废 钢结 构 、 造渣材 料 质量 等 多种 因素 的影 响 , 冶
一 一
② 当铁 水成分 、 温度 达不到要 求 时 , 在 不影 响品种质 量 的情况下 , 由公司总调协调处理。
,
铁水 中 的 硅 , 是 转 炉 炼 钢 的 主 要 发 热 元 素 之 般铁 水含 硅量 以 0 . 5 %~ 0 . 8 %为 宜 。
一钢关于铁水对炼钢成本影响的报告5月份

一钢关于铁水对炼钢成本影响的报告公司领导:由于近几个月高炉供我厂转炉的铁水成分的波动,并且高炉刚开炉成分异常,加之我公司高炉检修铁水产量降低,铁水比降低之后,加大了我厂转炉区域操作难度,对转炉在吹炼过程中喷溅炉次、化渣剂用量、钢铁料用量等均有一定的影响。
现将两区域5月份各项指标与1月份平均值进行对比,对比结果如下:一、铁水对80吨成本影响1、铁水比降低对钢铁料的影响5月份80吨区域钢铁料、铁水单耗的对比如下,从上述数据可以看出,铁水消耗从原来的1022.52kg/t降低到950.55kg/t,降低71.97g/t,影响钢铁料消耗上升9.5kg/t。
铁水比降低影响我厂80吨钢铁料消耗升高9.5kg/t,折合成本9.97元/t。
2、铁水比降低对氧气用量的影响铁水比降低后,由于生铁比例增大,转炉冶炼所需热量不足,增加氧气消耗量。
计算铁水消耗每降低10kg/t,氧气消耗增加0.8m3/t,5月份铁水比降低影响氧气5.76m3/t,折合成本约2.99元/t。
3、铁水成分的影响由于1#450高炉复产,铁水成份波动较大,铁水硅含量平均为0.54%,加之5月份开始使用顺兴高炉铁水,顺兴铁水硅含量平均0.56%,两项合计使铁水硅含量整体较1月份升高0.054%,理论影响灰耗上升4.34kg/t,按照白灰单价342元/t计算,影响成本1.48元/t。
综上,5月份铁水比降低影响我厂80吨钢铁料消耗、氧气消耗及白灰消耗成本合计14.44元/t。
二、铁水对120吨成本影响1、铁水比降低对钢铁料的影响5月份120吨区域钢铁料、铁水单耗的对比如下,从上述数据可以看出,铁水消耗从原来的996kg/t降低到947kg/t,降低49kg/t,影响钢铁料消耗上升6.07kg/t。
铁水比降低影响我厂120吨钢铁料消耗升高6.07kg/t,折合成本7.88元/t。
2、铁水比降低对氧气用量的影响铁水比降低后,由于生铁比例增大,转炉冶炼所需热量不足,增加氧气消耗量。
转炉低铁水消耗冶炼工艺思考研究

24Metallurgical smelting冶金冶炼转炉低铁水消耗冶炼工艺思考研究高 勇(酒钢集团榆中钢铁有限公司,甘肃 兰州 730104)摘 要:当前在市场废钢供应量逐渐增加的形势下,降低铁水消耗是降低冶炼工艺成本的重要措施,同时也能够提高冶炼效益。
因此在当前社会经济发展进入新时期,为提高钢铁冶炼工艺质量和效率,需要采用转炉低铁水消耗冶炼工艺,降低生产成本。
鉴于此,本文主要阐述转炉低铁水消耗的可行性,通过降低铁水消耗的冶炼工艺试验,分析其具体措施,并思考转炉低铁水消耗冶炼工艺的生产效果,旨在进一步实现转炉低铁水比的稳定性,优化炼钢生产工艺,降低炼钢成本。
关键词:转炉;低铁水消耗;冶炼工艺中图分类号:TF713 文献标识码:A 文章编号:11-5004(2020)18-0024-2收稿日期:2020-09作者简介:高勇 ,男,生于1985年,汉族,甘肃平凉人,本科,工程师,研究方向:冶金工程及企业管理。
随着社会经济的快速发展,市场废钢供应量逐渐增加,在开展冶炼工艺时,实现环保以及钢铁去产能成为炼钢企业的首要任务。
并且在以消耗铁水为主的转炉炼钢工艺,可以通过降低铁水消耗,提高废钢比例,是提高冶炼工艺生产成本和降低成本的重要手段。
1 转炉低铁水消耗的可行性对于转炉低铁水消耗在实践中的实现是具有一定可行性的,结合钢铁冶金的原理,充分平衡转炉物料以及进行热平衡计算,能够得到钢种为低合金钢。
其所用铁水条件和终点钢水条件都有所改善。
一般情况下,以100kg 铁水为例,在不考虑废钢和冷料的添加量和脱氧合金化的基础上,钢水的获得率可以达到93.18%,与现场冶炼工艺生产数据相符合。
同时由于铁水的物理热实际上是转炉热量的最主要来源。
所以在不考虑炉渣带走热量的情况下,转炉热效率可以达到74.77%。
对于冶炼工艺过程中出现的富余热量一般可以熔化15.11kg 的废钢。
最后结合钢水获得率和富余热量,综合考虑废钢和脱氧合金化以及在没有外来补充热量的状况下,转炉的最小铁水比能够维持在82%~83%之间,即是最低铁水消耗为880kg/t ~890kg/t。
降低钢水氧含量工艺实践
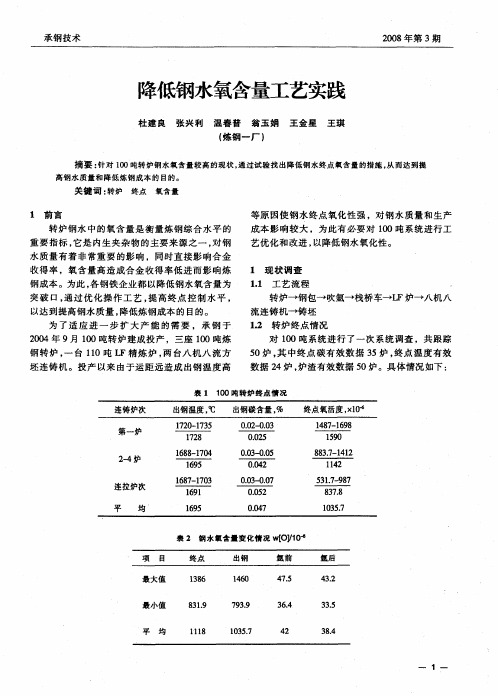
系
分 别 将 终 点 a(o)与 终 点 【C]、T、∑(FeO)的关 系 做 散点 图如 图 1—3。
===
2
、一
事
《 豁
呷o
、一
事
《 豁
一
2 ~
终 点 w([C]),%
图 1 终点 w([OD与终点 w ̄CD关系图
终 点 I’,℃
图 2 终点 wlⅡO】)与终点 T关系图
表 l 100吨 转 炉 终点 情 况
衰 2 钢水氧含量变化情况 wtOy ̄O
由于承钢 特有 的钒 钛资 源 ,为 了把钒 、钛 提取 出来 ,炼 钢 ~厂 自建厂 以来就 一 直 采用 “铁 水 提 钒一半 钢炼 钢 ” 的双 联 法炼 钢工 艺 ,半钢 中主要
元 素 如 Si、Ti、Mn已氧 化 (半 钢 条 件 见 表 4),半 钢
关键 词 :转炉 终点 氧含量
1 1前言 转 炉 钢水 中的 氧 含量 是 衡 量 炼 钢 综 合水 平 的
重 要 指标 ,它是 内生 夹 杂物 的主 要来 源 之 一 ,对 钢 水 质量 有 着 非 常重 要 的影 响 ,同时 直 接影 响合 金 收得 率 ,氧 含量 高 造 成合 金 收得 率 低进 而 影 响炼 钢成 本 。为此 ,各 钢铁 企业 都 以降 低钢 水 氧含 量 为 突 破 口 ,通 过 优 化 操 作 工 艺 ,提 高 终 点 控 制 水 平 , 以达 到 提高 钢水 质 量 ,降低 炼钢 成本 的 目的。
100t电炉兑铁水工艺实践
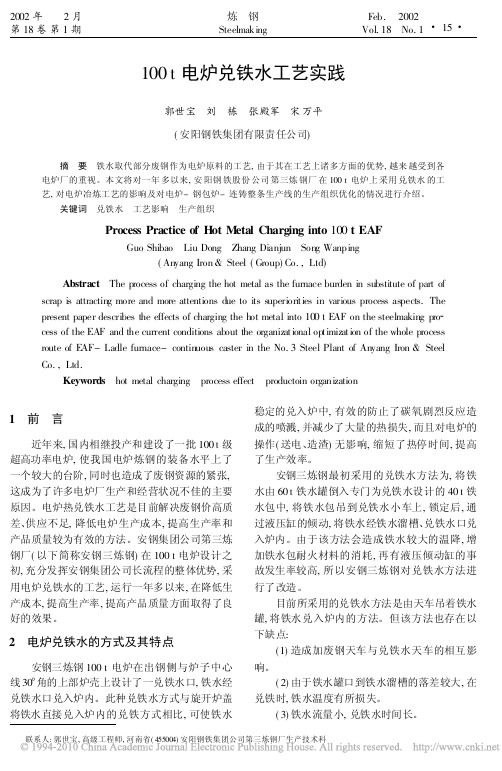
3. 6
兑铁水对整个生产组织的影响
安钢三炼钢 100 t 电炉 & 钢包炉 & 连铸生产
3. 5
兑铁水量对冶炼周期的影响
兑铁水后, 冶炼周期受兑铁量及氧气压力的
线为单线生产 , 这对生产组织提出了较高的要求。 由于连铸机的浇铸周期( 约 47 min) 与全废钢时电 炉冶炼周期( 59 min) 相差较大, 生产组织困难 , 连 浇炉数较低 ; 当兑入 25 % 的铁水后 , 冶炼周期缩 短至 52 min, 在浇铸 200 mm ! 1 400 mm 断面铸坯 时, 连 浇 炉数 由 4. 6 炉提 高 到 6. 9 炉 ; 在浇 铸 150 mm ! 1 250 mm 断面铸坯时 , 则实现了换包操 作, 连浇炉数最高达到了 35 炉 ; 随着兑铁量增加 至 35 % , 冶炼周期缩短至 47 min 左右, 与连铸浇 铸周期相当, 安钢三炼钢在 200 mm ! 1 400 mm 断 面上也实现了换包操作, 使得生产效率大幅提高。
17
9 000 Nm , 具有较强的供氧能力。不装铁水时, 氧 在竖炉中的行为较为复杂 , 加上吸入空气中大量 的氧和废钢中带入的氧化铁等, 使得氧在竖炉熔 化期的行为无法控制。而加入铁水后 , 有利于竖 炉内早期泡沫渣的形成 , 使竖炉较早地达到了近 似转炉的供氧条件 , 使氧的利用率升高。部分热 装铁水时泡沫渣形成早, 渣门处废钢温度升高快, 炉门氧枪可很容易将渣门附近的废钢熔化 , 并较 早进入炉内进行各种操作 , 加速冶炼的进程, 提高 电能利用率。
这种加料方式对铁水、 废钢及氧压提出了一 定的要求。 铁水在量上能得到保证, 即铁水的供应与电 炉冶炼周期相匹配, 使每炉钢都能兑入 45 % 的铁 水, 否则对电炉配料会造成较大影响; 要求铁水温 度在 1 300 # 左右, 否则将使兑铁水口因粘铁而变 小, 影响铁水的兑入。 废钢要求为堆比重较大的优质废钢, 保证一 料篮 55 % ( 即 66 t ) 的装入量。 氧气压力要求保持在 1. 6MPa, 否则将使冶炼 周期由 于脱碳时间的 延长而延长。但实际生产 中, 氧压难以保证。
低铁钢比工艺条件下降低转炉钢铁料消耗应用实践
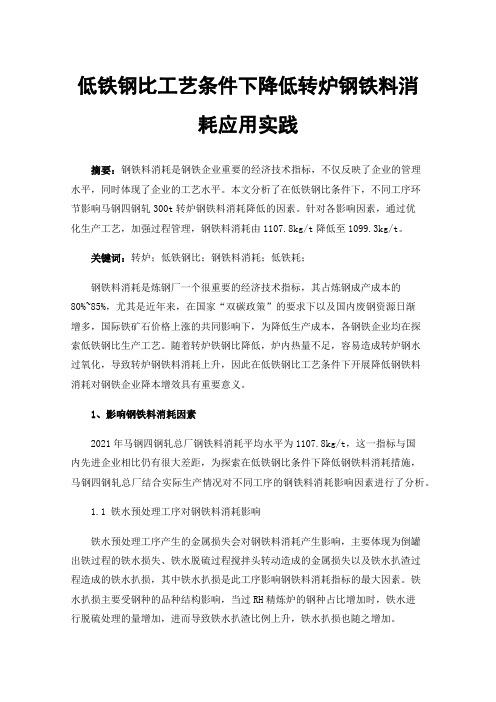
低铁钢比工艺条件下降低转炉钢铁料消耗应用实践摘要:钢铁料消耗是钢铁企业重要的经济技术指标,不仅反映了企业的管理水平,同时体现了企业的工艺水平。
本文分析了在低铁钢比条件下,不同工序环节影响马钢四钢轧300t转炉钢铁料消耗降低的因素。
针对各影响因素,通过优化生产工艺,加强过程管理,钢铁料消耗由1107.8kg/t降低至1099.3kg/t。
关键词:转炉;低铁钢比;钢铁料消耗;低铁耗;钢铁料消耗是炼钢厂一个很重要的经济技术指标,其占炼钢成产成本的80%~85%,尤其是近年来,在国家“双碳政策”的要求下以及国内废钢资源日渐增多,国际铁矿石价格上涨的共同影响下,为降低生产成本,各钢铁企业均在探索低铁钢比生产工艺。
随着转炉铁钢比降低,炉内热量不足,容易造成转炉钢水过氧化,导致转炉钢铁料消耗上升,因此在低铁钢比工艺条件下开展降低钢铁料消耗对钢铁企业降本增效具有重要意义。
1、影响钢铁料消耗因素2021年马钢四钢轧总厂钢铁料消耗平均水平为1107.8kg/t,这一指标与国内先进企业相比仍有很大差距,为探索在低铁钢比条件下降低钢铁料消耗措施,马钢四钢轧总厂结合实际生产情况对不同工序的钢铁料消耗影响因素进行了分析。
1.1 铁水预处理工序对钢铁料消耗影响铁水预处理工序产生的金属损失会对钢铁料消耗产生影响,主要体现为倒罐出铁过程的铁水损失、铁水脱硫过程搅拌头转动造成的金属损失以及铁水扒渣过程造成的铁水扒损,其中铁水扒损是此工序影响钢铁料消耗指标的最大因素。
铁水扒损主要受钢种的品种结构影响,当过RH精炼炉的钢种占比增加时,铁水进行脱硫处理的量增加,进而导致铁水扒渣比例上升,铁水扒损也随之增加。
1.2转炉工序对钢铁料消耗影响转炉工序影响钢铁料消耗因素较多,主要有以下几个因素:1)转炉渣量。
转炉冶炼过程中会有部分铁进入到转炉渣中,目前四钢轧转炉终渣全铁在16%左右,渣量增大会导致进入到转炉渣中的铁增加,因此会造成钢铁料消耗上升。
炼钢厂低温低硅铁水冶炼生产实践

影 响 化渣 的主 要原 因是 铁 水温 度过 低 导致 的热 得 多 。
量 不 足 、硅 含量 过 导致形 成 低熔 点 化合 物量 少 。 3.2 装 入 制度 适 时调 整
控 制 措 施 只有 :辅 料加 入 时机 控 制 和 氧枪 枪 位
为 了提 高 低 温 低 硅 铁 水 的 物 理 热 和 化 学
转 炉 脱 磷 的 全 程 控 制 为 J:前 期 快 速 化
· 6·
梅 山 科 技
2018年 第 2期
渣 ,利 用低 温 高 效 脱 磷 。 中期 确 保 炉 渣 流 动性 较 低 的情况 下 ,对 下一 炉 初 期 渣 的形 成 十分 有
持续 脱磷 ,后 期 保 证 炉 渣 流 动 性 、碱 度 、(FeO) 利 ,可 以有 效 的去 除磷 、硫 。梅 钢公 司二 转 炉现
关键 词 :低 硅 ;低 温 ;脱磷 ;250 t转 炉
Practice of Low Tem perature and Low Silicon M olten Iron Sm elting in M eishan Steelm aking Plant
ZHANG Jiandong WANG Longfei (Steelmaking Plant of Meishan Iron& Steel Co.,Nanjing 210039,China) K ey words:low silicon;low temperature; deph0sphorization;250t BOF
转 炉 冶 炼是 一 个 复 杂 多变 的过 程 ,受 铁 水 条件 ,废 钢结构 ,造 渣材 料质 量等 多种 因素 的影 响 ,冶炼 的钢水 质 量差别 很 大 。 目前 ,公 司二 炼 钢低 温低 硅铁 水 ([Si]% ≤0.25,T≤1 300℃ ) 占比在 8%左 右 ,由于 铁水 温 度 低 ,含硅 量 低 , 转炉 冶炼 过程 中 ,渣 中的 (SiO )总量 偏低 ,造 成 化渣 困难 … ,经 常 出 现冶 炼 终 点 钢 水 磷 含量 降 不下 来 的 现 象 ,给生 产 组 织 和产 品质 量 造成 了 较大 负面 影 响 。为 了 提 高 钢水 终 点 磷 符 合 率 , 对低 温低 硅铁水 冶 炼进 行分 析研 究 。
转炉低硅铁水冶炼工艺探索
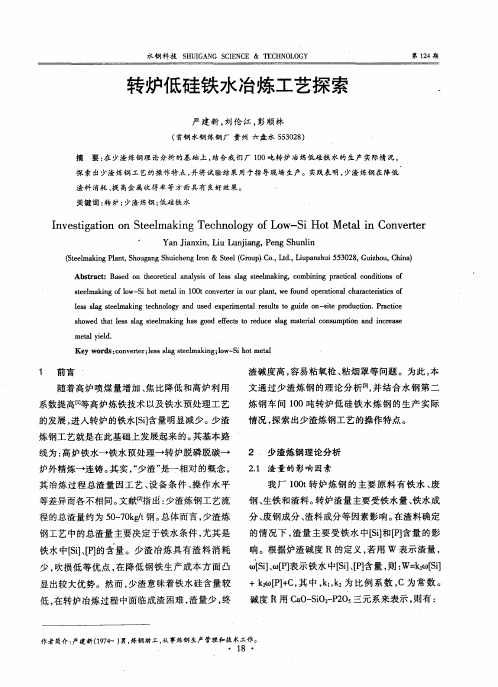
探 索 出 少渣 炼钢 工 艺 的操 作 特 点 , 并 将 试 验 结 果 用 于指 导 现 场 生 产 。实践 表 明 , 少渣 炼 钢 在 降低 渣料消耗、 提 高金 属 收得 率 等 方 面转 炉; 少 渣炼 钢 ; 低硅 铁 水
.
I n v e s t i g a t i o n o n S t e e l ma k i n g Te c h n o l o g y o f L o w— — S i Ho t Me t a l i n C o n v e r t e r
‘ Y a n J i a n x i n , L i u L u n j i a n g , P e n g S h u n l i n
( S t e e l ma k i n g P l a n t , S h o u g a n g S h u i c h e n g I r o n&S t e e l ( G r o u p ) C o . , L t d . , L i u p a n s h u i 5 5 3 0 2 8 , G u i z h o u , C h i n a )
1 前言
‘
渣碱 度高 , 容 易粘 氧枪 、 粘烟 罩等 问题 。为此 , 本
随着高 炉 喷煤量 增加 、 焦 比降低 和高 炉利 用 系数 提高【 1 等高 炉炼 铁技 术 以及铁 水预 处 理工 艺 的发 展 , 进入 转炉 的铁 水【 S i ] 含量 明显 减少 。少 渣
2 少 渣炼钢 理 论分析
2 . 1 渣 量 的影 响 因素 我厂 l O O t 转炉炼钢的主要原料有铁水 、 废
等差异而各不相同。 文献[ 2 ] 指 出: 少渣炼钢工艺流
程的 总渣量约 为 5 0 - 7 0 k  ̄t 钢。 总体而 言 , 少 渣炼
邯钢三炼钢“一罐到底”工艺生产实践

邯钢三炼钢“一罐到底”工艺生产实践杨彦君1高卫刚1黄文杰2(1.河北钢铁集团邯钢公司第三炼钢厂,邯郸 056015;(2. 2.河北钢铁集团邯钢公司生产制造部,邯郸 056015)摘要邯钢三炼钢厂推行“一罐到底”工艺,即把高炉出铁场的铁水罐与到炼钢转炉兑铁水的铁水罐合二为一,节省了转炉炼钢的铁水包,减少铁水二次倒罐环节,避免因倒罐引起的铁水温降、铁水损失和环境污染,经过近一年的生产实践,取得了较为理想的经济效益和社会效益。
关键词一罐到底生产实践效益The Experience Production of “Get the Ladle Done at One Go”in No.3 Steelmaking Plant of HansteelYang Yanjun1Gao Weigang1 Huang Wenjie2(1. No.3 Plant of Handan Iron and Steel Group Co.,Ltd.,Handan, 056015;2.Manufacturing Department of Handan Iron and Steel Group Co.,Ltd.,Handan, 056015)Abstract The process “get the ladle done at one go” used in No.3 steel making plant of Hansteel. The process of combining the hot metal ladle of the casthouse into one that for reladling to converter in realized. Thanks to this process , it releases the hot metal reladling operation step, it is good for the hot metal temperature protection and prevents the environment from pollution. This process has been made great benefits and approved practically after one year experience practically after one year experienced operation.Key words get the ladle done at one go, experience production, efficiency1 引言钢铁企业中高炉与转炉间工序界面即“铁钢”界面,包括高炉出铁、铁水运输及铁水预处理等许多环节,若不考虑铁水预处理环节,“铁钢”界面模式,按照其发展的历程,主要经历以下几个典型过程:(1)高炉-受铁罐-混铁炉-兑铁包-转炉的模式;(2)高炉-受铁罐-兑铁包-转炉的模式;(3)高炉-鱼雷罐车-兑铁包-转炉的模式;(4)高炉-受铁罐-转炉(即“一罐到底”)的模式等。
100 t转炉五孔氧枪喷头设计与应用
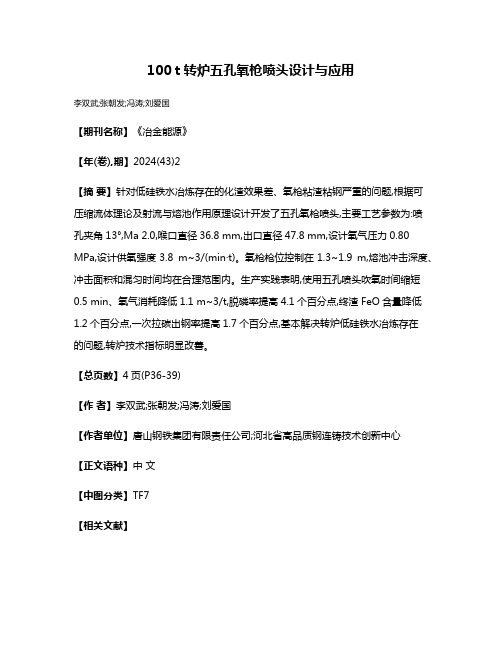
100 t转炉五孔氧枪喷头设计与应用
李双武;张朝发;冯涛;刘爱国
【期刊名称】《冶金能源》
【年(卷),期】2024(43)2
【摘要】针对低硅铁水冶炼存在的化渣效果差、氧枪粘渣粘钢严重的问题,根据可压缩流体理论及射流与熔池作用原理设计开发了五孔氧枪喷头,主要工艺参数为:喷
孔夹角13°,Ma 2.0,喉口直径36.8 mm,出口直径47.8 mm,设计氧气压力0.80 MPa,设计供氧强度3.8 m~3/(min·t)。
氧枪枪位控制在1.3~1.9 m,熔池冲击深度、冲击面积和混匀时间均在合理范围内。
生产实践表明,使用五孔喷头吹氧时间缩短
0.5 min、氧气消耗降低1.1 m~3/t,脱磷率提高4.1个百分点,终渣FeO含量降低
1.2个百分点,一次拉碳出钢率提高1.7个百分点,基本解决转炉低硅铁水冶炼存在
的问题,转炉技术指标明显改善。
【总页数】4页(P36-39)
【作者】李双武;张朝发;冯涛;刘爱国
【作者单位】唐山钢铁集团有限责任公司;河北省高品质钢连铸技术创新中心
【正文语种】中文
【中图分类】TF7
【相关文献】
1.鞍钢100t转炉氧枪喷头结构优化与应用
2.150 t转炉5孔氧枪喷头的设计与应用
3.100t转炉氧枪喷头的设计与优化
4.转炉氧枪喷头的设计与应用
5.5孔氧枪喷头在120t转炉上的设计与应用
因版权原因,仅展示原文概要,查看原文内容请购买。
炼钢全流程降低钢铁料消耗的实践攻关
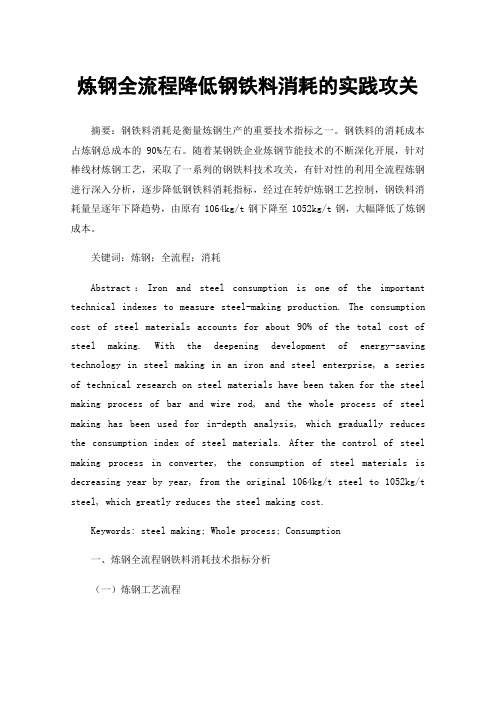
炼钢全流程降低钢铁料消耗的实践攻关摘要:钢铁料消耗是衡量炼钢生产的重要技术指标之一。
钢铁料的消耗成本占炼钢总成本的90%左右。
随着某钢铁企业炼钢节能技术的不断深化开展,针对棒线材炼钢工艺,采取了一系列的钢铁料技术攻关,有针对性的利用全流程炼钢进行深入分析,逐步降低钢铁料消耗指标,经过在转炉炼钢工艺控制,钢铁料消耗量呈逐年下降趋势,由原有1064kg/t钢下降至1052kg/t钢,大幅降低了炼钢成本。
关键词:炼钢;全流程;消耗Abstract:Iron and steel consumption is one of the important technical indexes to measure steel-making production. The consumption cost of steel materials accounts for about 90% of the total cost of steel making. With the deepening development of energy-saving technology in steel making in an iron and steel enterprise, a series of technical research on steel materials have been taken for the steel making process of bar and wire rod, and the whole process of steel making has been used for in-depth analysis, which gradually reduces the consumption index of steel materials. After the control of steel making process in converter, the consumption of steel materials is decreasing year by year, from the original 1064kg/t steel to 1052kg/t steel, which greatly reduces the steel making cost.Keywords: steel making; Whole process; Consumption一、炼钢全流程钢铁料消耗技术指标分析(一)炼钢工艺流程图1 某钢铁企业炼钢工艺流程简图(二)钢铁料消耗统计分析某钢铁企业第二钢扎厂钢铁料消耗统计口径如下:钢铁料消耗(kg/t)=(铁水+废钢)(kg)/合格钢坯产量(t)。
转炉设计

1转炉设计1.1炉型设计1. 原始条件炉子平均出钢量为100吨,钢水收得率取90.36%,最大废钢比取10%,采用废钢矿石法冷却。
铁水采用P08属于低磷生铁;氧枪采用三孔拉瓦尔型喷头.2. 炉型选择:根据原始条件采用锥球形炉型。
3. 炉容比:取V/T=1.004. 熔池尺寸的计算熔池直径: G= t B T 95.102936.01%1521002122=⨯+⨯=⋅+η (取B=15%)314.158.695.102m G V ===ρ 确定吹氧时间和吨钢耗氧量:本设计采用低磷铁水,取吨钢耗氧量为56.8)(/3钢t m 。
并取吹氧时间为12min ,则供氧强度min)]/([733.4128.563⋅==t m 取K =1.8则 )(27.51295.1028.1m D == 锥球型熔池深度的计算公式为 )(05.127.57.027.50363.014.157.00363.02323m D D V h =⨯⨯+=+= 确定D =5.27m, h =1.05m熔池其他尺寸确定球冠的弓形:)(527.027.510.010.01m D h =⨯==)(717.427.5895.0895.01m D D =⨯==炉底球冠曲率半径:)(797.527.51.11.1m D R =⨯==5. 炉帽尺寸的确定炉口直径:()m D d 530.227.548.048.00=⨯==炉帽倾角:取065=θ3) 炉帽高度帽H)(94.265tan )53.227.5(21tan 2100m d D H =-=-=θ 取mm H 400=口,则整个炉帽高度为:)(口锥帽m H H H 34.34.094.2=+=+= 由于我们采用水冷炉口炉帽部分容积为:口锥帽)(H d d Dd D H V 202002412ππ+++=)(56.384.053.24)53.253.227.527.5(94.2123222m =⨯⨯++⨯+⨯⨯=ππ6. 炉身尺寸确定1) 炉膛直径D D =膛=5.27m (无加厚段)2) 根据选定的炉容比为1.00,可求出炉子总容积为)(容31000100.1m V =⨯= )(帽池总身346.438.5615.14100m V V V V =--=--= 3) 炉身高度)(3.135.27446.4422m D V H =⨯=⨯=ππ身身 4) 炉型内高m H H h H 52.813.234.305.1=++=++=身帽内7. 出钢口尺寸的确定1) 出钢口直径)(15.0)(15.5301075.16375.163m cm T d T =≈⨯+=+=2) 出钢口衬砖外径)(0.915.066m d d T ST =⨯==3) 出钢口长度)(05.115.077m d L T T =⨯==4) 出钢口倾角β:取018=β8. 炉衬厚度确定炉身工作层选600mm,永久层115mm,填充层90mm,总厚度为600+115+90=805(mm )炉壳内径为 6.882805.05.27=⨯+=壳内D炉帽和炉底工作层均选600mm,炉帽永久层为150mm,炉底永久层用标准镁砖立砌,一层230mm,粘土砖平砌三层65×3=195(mm ),则炉底衬砖总厚度为600+230+195=1025(mm ),故炉壳内形高度为)(9.545025.18.52m H =+=壳内,工作层材质全部采用镁碳砖。
100T转炉45#钢生产工艺要点

100T转炉45#钢生产工艺要点(冶炼部分)1.工艺路线:混铁炉—提钒转炉—炼钢转炉—精炼—方坯保护浇铸2•原料条件:尽量组织用铁水(半钢)[S]W0.040%冶炼,以保高拉碳为原则控制冷料用量。
3.成份控制4.温度控制(表中温度为贺利氏测温偶头的夏季温度,冬季连拉炉次温度上调5C)。
5.1吹炼前期化好渣,化透渣,避免熔池温度上升过快及炉渣“返干”现象发生5.2吹炼终点:尽量一次拉成,保证C-T协调,补吹不大于两次。
终点[C]最佳控制为0.10〜0.20%;[S]W0.030%,[P]W0.015%。
5.3挡渣:用挡渣塞、挡渣锥或专用挡渣设施进行挡渣操作,确保渣层厚W出钢时间保证出钢口圆滑出钢时间三秒。
其中在出钢前加入,其余部分在加完合金料后加入,氧化性强靠上限,氧化性弱靠下限。
合金参考:用合金化。
根据出钢终点氧化性随合金料均匀加入炉调渣剂,出钢后加入顶渣袋炉。
5.7在冶炼此钢种时,转炉复吹必须执行切换。
精炼要求6.1吹氩时间三分钟,前分钟执行吹氩操作,其余执行弱吹氩操作。
吹氩过程中尽量少喂或不喂线,若氩前a[o]三,可喂米线进行调整,a[o]注:结合脱氧剂的加入量,氧化性强喂线量靠上限,氧化性弱喂线量靠下限。
注意事项开新炉前炉和大补炉后第炉禁止冶炼此钢种。
冶炼此钢种时,调度室提前炉通知转炉岗位和化验室,转炉岗位根据实际情况调整冷料用量,化验室提前做标样。
严禁使用新包,及时处理炉口积渣和包沿,要求钢包内无残渣和包底,保证红包出钢。
本制度自年月日起执行,原年月日工艺要点同时作废。
技术科大包保护管中间包浸入式水口结晶器铸坯三、拉钢前的准备要求结晶器使用寿命W分钟,内腔表面光滑,上下水缝无漏水。
要求使用干式料中间包烘烤达到小时以上并且中间包内保持清洁无杂物溢流口修砌符合排渣要求。
石英质(或铝碳质)浸入式水口和快换下水口必须烘烤后使用。
四、拉钢过程的控制生产断面():x大中包温度控制及浇注周期贺利氏偶头夏季温度,注:五流、六流拉钢时总蹲包时间W分钟,七流、八流拉钢时总蹲包时间W 分钟,调度室开作业卡要温度时蹲包温降按1・O°C/min计算(不区分冬夏季)。
- 1、下载文档前请自行甄别文档内容的完整性,平台不提供额外的编辑、内容补充、找答案等附加服务。
- 2、"仅部分预览"的文档,不可在线预览部分如存在完整性等问题,可反馈申请退款(可完整预览的文档不适用该条件!)。
- 3、如文档侵犯您的权益,请联系客服反馈,我们会尽快为您处理(人工客服工作时间:9:00-18:30)。
现代冶金
Modern Metallurgy
第47卷第3期2019年6月
Vol. 47 No. 3
Jun 2019
100吨转炉低铁水比例冶炼实践
黄彦飞
(盐城市联鑫钢铁有限公司,江苏盐城224000)
摘要:通过工艺优化和技术创新,增加转炉内热收入,减少过程热损失,铁水比例降低到67%,铁水消耗降低到730:g/t 钢,达到国内先进水平,经济效益十分显著#
关键词:转炉炼钢;铁水比例;铁水物理热;铁水化学热
中图分类号:TF71
引言
国家淘汰大批落后钢铁产能后,社会废钢库存 量趋于高位,废钢价格在低位徘徊,提高废钢比成为
各钢铁企业增加经济效益的主要手段和重要目标$
盐城市联鑫钢铁有限公司(以下简称“联鑫钢
铁”)现运行两座高炉(1080 >3 + 660 m 3),日产铁 水量8000 t 左右,2座100 t 转炉满负荷生产时产能
11000 t,铁水不足的情况严重制约了转炉的高效炼 钢$为此,炼钢厂进行了一系列的工艺优化和技术
创新,增加入炉内热收入,减少热支出和过程温降,
不断提高入炉废钢比,铁水比例降低到67%,实现 产能最大化$
收稿日期=2018-12-20
1主要工艺措施
1. 1增加转炉热收入
为了最大限度地提高废钢比,联鑫钢铁要求 高炉铁水罐到站温度"1400 @,较以前提高了
100 @ ;铁水Si 含量为0. 4%-0, 5%,较以前提高
了 0. 2% $
已知铁水热熔为0. 837 kJ/kg ,若铁水温度提高
100 @,则炉内热收入增加5607900 kJ,理论上可以
提高废钢加入量3.8吨/炉$
Si 元素的氧化放热反应如下
[Si ] + 2[O *= SiO z -29202(kJ/k g )
铁水Si 含量较原来提高了 0.2%,则炉内化学
热增加3913068 kJ ,理论上可以增加废钢量
2. 6吨/炉$
实践证明,铁水温度由1300 @提高至1400 @,
可以增加废钢加入量约3. 5吨/炉;铁水Si 含量提
高0. 2%,可以增加废钢加入量约2. 3吨/炉$
1.2废钢预热
联鑫钢铁炼钢厂新建造8条废钢斗内废钢预热
线,每条预热线有5个烧嘴,利用转炉煤气热源,对
废钢斗内废钢进行烘烤预热,能将废钢入炉温度提 高到500 @以上(为了避免废钢斗因烘烤温度高造
成变形,废钢斗周围采用通水冷却)$
已知废钢固态热熔为0. 699 kJ/kg ,液态热熔为
0. 837 kJ/kg ,熔化潜热为272 kJ/kg ,理论上可以增
加废钢量6. 5吨/炉$联鑫钢铁为斗内烘烤废钢,废
钢底部预热不彻底,实际可以增加废钢加入量 约4. 5吨/炉$
1.3合金烘烤
联鑫钢铁主要生产抗震钢筋,合金加入量为25 kg/t 左右,炉合金加入量为2. 5 t 左右,合金熔化、
溶解过程需要吸收大量热量,合金烘烤之前,出钢过
程温降为80 @左右,钢包烘烤不良时甚至达到100
@,转炉不得不高温放钢,以保证钢包温度$为了降 低铁水比,炼钢厂在中位料仓下方、合金溜槽上方设 立合金烘烤装置,出钢前能将合金预热到500 @以 上;同时将出钢口内径从!160 mm 扩大到0180
mm,出钢时间控制为1. 5-2. 5 min,出钢温降降低
到现在的40 @左右$
第3期黄彦飞,等:100吨转炉低铁水比例冶炼实践39 1.4采用投弹仪测温、定碳新技术
联鑫钢铁100t转炉没有副枪装置,原来转炉终点控制方法为拉碳法操作,终点倒炉测温取样,如温度、成分不合格需进行补吹操作;倒炉时间长,过程温降大$为降低铁水比,现采用投弹仪测温、定碳新技术,临近转炉吹炼终点时,投弹仪通过下料口向炉内熔池投掷探头进行测温、定碳,并根据温度及碳含量,控制拉碳时间,确保终点温度和成分满足出钢条件,转炉吹炼结束直接倒炉放钢,不用再往前倒炉、测温取样及倾炉,冶炼周期缩短了2>in/炉,炉内钢水温降减少810@$
1.5采用钢包系统保温技术
采用新型纳米绝热层替代原来的保温岩棉进行钢包隔热,包壳温度由原来的250@降低到现在的180@左右,钢包散热明显减少;创新钢包加盖方案,在吹氩站平台下方设置专用包盖悬架,出钢前钢包车开向出钢位时能自动挂到悬架上,脱离钢包;吹氩后钢包车开出时,靠包盖上的两个挂钩勾住钢包沿上的挂鼻,自动加盖,实现全程加盖保温,钢包运输及浇注过程温降减少15@左右,钢水温度更加均匀、稳定$
1.6采用钢包自动吹氩技术
原来吹氩管道阀门采用的是普通减压阀,阀门开度及流量调节精度差,过程吹氩强度不是太大就是太小,造成吹氩过程不必要的温降$为了保证吹氩质量同时减少过程温降,炼钢厂新上了钢包自动吹氩调节系统,不同吹氩阶段设定不同的吹氩流量和压力;尤其是软吹阶段,系统根据压力和流量关系,自动判定透气砖透气效果,自动精准调节氩气流量,既能保证软吹时钢水液面微动,又不会造成钢水裸露,降低了吹氩过程温降,同时避免了钢水的二次氧化$通过采用钢包自动吹氩技术,钢包吹氩过程温降由原来的25@左右降低到现在的18@左右,可以降低出钢温度7@,增加废钢消耗0.5t左右$1.7采用钢包连滑工艺
提高钢包水口滑板质量,钢包水口由原来的使用1次更换,到现在的3次再更换,每炉缩短钢包修砌时间约10>in,两座转炉周转钢包由原来的7-8个减少到目前的5个(备用1个)。
钢包内衬温度由原来的550@左右提高到700@左右,出钢温降减少了10@左右$
1.8炉内加焦炭增加热源
高位料仓放入焦炭,吹炼过程分批加入炉内,焦炭与氧气反应放出热量加热钢液$转炉内碳-氧放热反应如下:
[C*+[O*=CO#—11639(kJ/kg)
[C*+[O*=CO$#—34834(kJ/kg)
每炉加入焦炭300kg,设其中约90%氧化生产CO,10%氧化生产CO$,氧化放出的热量约有70%被熔池吸收,则理论上可以增加废钢量约为2吨/炉$实践证明,每炉加入300kg焦炭,可以增加废钢消耗约1.5吨/炉$
2其他措施
此外,联鑫钢铁炼钢厂还采取了诸多改进措施,将冶炼周期由原来的25min缩短到19>in,加快了钢包周转,减少了钢包过程温降;采用炉后钢包喂碳线、锰线微调合金成分,减少了强吹氩造成的钢包温降$
3结束语
通过以上措施的实施,联鑫钢铁炼钢厂铁水比例由原来的85%降低到现在的67%,铁水消耗由原来的910kg/1降低到现在的730kg/t,高炉8000t 铁水量可生产转炉钢产量由原来的9000t提高到现在的11000t,经济效益十分显著$。