铁水硅高条件下转炉的冶炼操作
以铁水硅为主线的转炉冶炼操作

况, 铁水 可在 要求基 础上 多装 1 。 吨 当铁 水 s 含 量 在 0 5 ~0 7 i .% . %时按 正 常装 入
量 控制 。 当铁水 s 大 于 0 7 i .%时 , 据冶 炼 过程 热 量情 根 况, 废钢 可适 当 加完 时 间尽 量早 。 当铁水 硅含 量大 于 0 7 .%时 , 一批 料 按 要 求 第
减 轻 酸性 渣 对 炉衬 的侵 蚀 , 此 阶段 , 采 用较 高 在 应
58
办 冶 全
g\ 寻辑 } ∞ ∞ ∞奉 0 Ⅲ基 砌
20 5 第 期 0年 月 二 1
啦
的枪位 , 使渣中(e ) FO 稳定在 2% ~ 0 5 3 %的水平 , 减 少高熔 点且 致 密 的 2 a S0 的 形 成 而 阻 碍 石 灰 C O. i2 的熔解 , 在石灰 化完 后 , 如果不继续加石灰就应采用 低枪位操作 , 此时氧压控制最好采用氧压上 限操作。 吹炼过 程 , 别是 脱 碳 开 始 加 剧后 ( 概 在 吹 特 大 氧 9分钟左 右 )渣 中的氧化铁 也 大量 被 消耗 , 了 , 为 防止冶炼 中期 炉 渣 返 干 , 适 当 提 枪 , 渣 中 ( 应 使 ∑ FO 保 持在 1% ~1%的范 围内 , e) 0 5 同时 以低 氧压操 作 为主便 于转炉 化渣 , 氧压按 要求范 围下 限控制 。 冶炼后 期 是进 一 步 调 整好 炉 渣 的氧 化 性 和 流 动 性 , 于准 确 地 控制 终 点 。适 当 提枪 化 渣 , 便 而后 再 降低 枪 位进 行 低 枪位 操 作 , 同时将 氧 压 开大 , 以 降低钢中氧化铁含量 , 提高钢水收得率 。具体操作
注: 参考加入量是在 炉渣总碱度 为 2 8 石 灰有效 氧化钙 为 .,
含钒铁水转炉提钒渣冶炼方案(初稿)

含钒铁水转炉提钒渣冶炼方案目录1.钒相关基础知识 (4)1.1钒元素的发现与发展 (4)1.2国内钒的发展 (5)1.3钒的矿物简介 (6)1.4钒及其化合物的性质 (6)1.4.1金属钒的性质 (6)1.4.2金属钒的制备: (7)1.4.3钒的主要氧化物 (7)1.4.4含钒化合物的理化性能 (8)1.5钒在钢铁上的应用 (9)1.6钒的生产方法 (10)2.转炉提钒基本原理 (11)2.1转炉提钒的意义 (11)2.2转炉提钒的原理 (12)2.3铁质初渣与金属熔体间的氧化反应 (12)2.4转炉提钒脱钒、脱碳规律 (12)2.5铁水中钒与碳氧化的转化温度 (13)2.6影响转炉提钒的主要因素 (15)2.6.1铁水成分的影响 (15)2.6.2 铁水中钒的影响 (15)2.6.3.铁水硅的影响 (15)2.6.4.吹炼终点温度对钒渣中全铁含量影响 (16)2.6.5.供氧制度的影响 (17)3.提取钒渣方法 (17)3.1顶底复吹转炉提钒 (17)3.2转炉单联法提钒 (18)3.3攀钢转炉提钒工艺 (20)3.3.1转炉提钒工艺流程图 (20)3.3.2攀钢转炉提钒工艺过程 (20)3.3.3攀钢转炉提钒主要设备参数 (21)3.3.4攀钢转炉提钒用原材料 (21)3.3.5 不同氧枪的提钒效果 (22)3.3.6攀钢转炉提钒冷却制度 (23)3.3.7攀钢转炉提钒终点控制 (24)3.3.8出半钢和倒钒渣 (24)3.3.9攀钢提钒钒渣 (25)4.八钢炼钢提钒渣方案 .......................................................................... 错误!未定义书签。
1.钒相关基础知识1.1钒元素的发现与发展钒(V),呈银灰色,原子序数为23,原子量为50.942,在元素周期表中属VB族,具有体心立方晶格。
1801年,墨西哥矿物学家德尔·里奥在研究铅矿时,发现一种化学性质与铬、铀相似的新元素,其盐类在酸中加热时呈红色,故名为红色素。
转炉炼钢技能大赛题库(名词解释40题)
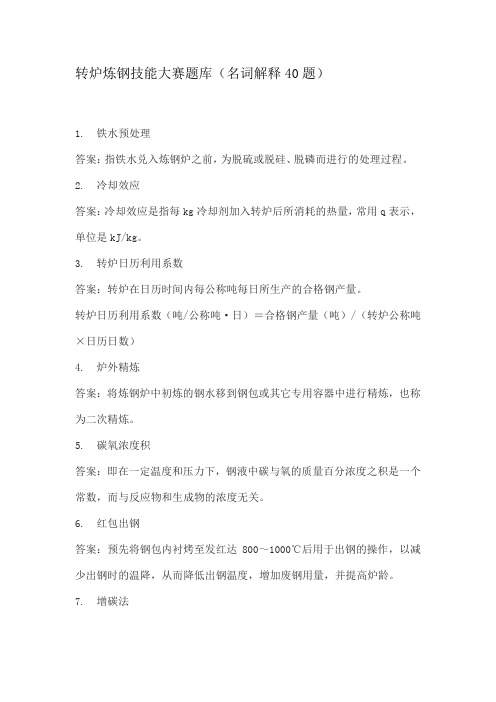
转炉炼钢技能大赛题库(名词解释40题)
1. 铁水预处理
答案:指铁水兑入炼钢炉之前,为脱硫或脱硅、脱磷而进行的处理过程。
2. 冷却效应
答案:冷却效应是指每kg冷却剂加入转炉后所消耗的热量,常用q表示,单位是kJ/kg。
3. 转炉日历利用系数
答案:转炉在日历时间内每公称吨每日所生产的合格钢产量。
转炉日历利用系数(吨/公称吨·日)=合格钢产量(吨)/(转炉公称吨×日历日数)
4. 炉外精炼
答案:将炼钢炉中初炼的钢水移到钢包或其它专用容器中进行精炼,也称为二次精炼。
5. 碳氧浓度积
答案:即在一定温度和压力下,钢液中碳与氧的质量百分浓度之积是一个常数,而与反应物和生成物的浓度无关。
6. 红包出钢
答案:预先将钢包内衬烤至发红达800~1000℃后用于出钢的操作,以减少出钢时的温降,从而降低出钢温度,增加废钢用量,并提高炉龄。
7. 增碳法。
转炉冶炼工艺

转炉冶炼工艺炼钢就是造渣。
造渣的目的:脱P、减少喷溅、保护炉衬。
造渣制度:确定合适的造渣方式,渣料的加入数量和时间、成渣速度。
渣的特点:一定的碱度、良好的流动性、合适的FeO及MgO、正常泡沫式的熔渣。
单渣法:铁水硅高磷低,或冶炼要求低。
双渣法:铁水硅高磷高,或冶炼要求高。
留渣法:利用终渣的热及FeO,为下炉准备。
成渣的速度:转炉冶炼时间短,快速成渣是非常重要的,石灰的溶解是决定冶炼速度的重要因素。
石灰的溶解:开始吹氧时渣中主要是SIO,MNO,FEO,是酸性渣,加入石灰,石灰溶解速度,可用下面的公式表示J=K(CaO+1.35MgO-1.09SiO2+2.75FeO+1.9MnO-39.1)形成2CAO*SIO2,渣难溶解。
FeO、MnO、MgO可加速石灰溶解,因为可以降低炉渣粘度,破坏2CaO*SiO2的存在。
采用软烧活性石灰、加矿石、萤石及吹氧加速成渣。
成渣的途径:低枪位操作,渣中FeO含量下降很快,磷接近终点时,渣中铁才回升。
适用于低磷铁水,对炉衬寿命有好处。
高枪位操作:渣中FeO含量保持较高水平,碳接近终点时,渣中铁才会下降。
适用于高磷铁水,对炉衬侵蚀严重;FeO高,炉渣泡沫化严重,易产生喷溅。
终点的控制方法:一次拉碳法、增碳法、高拉补吹法。
按出钢要求的终点碳和温度进行吹炼,当达到要求时提枪,操作要求较高。
优点:终点渣FeO低,钢中有害气体少,不加增碳剂,钢水洁净。
氧耗较小,节约增碳剂。
增碳法:所有钢种均将碳吹到0.05%左右,按照钢种加增碳剂。
优点:操作简单,生产率高,易实现自动控制,废钢比高。
高拉补吹:当冶炼中,高碳钢种时终点碳按钢种规格略高一些进行拉碳,待测温取样后按分析结果与规格的差值决定补吹时间。
造渣是转炉炼钢过程中的一个重要内容,渣系的好坏直接关系到炼钢过程能否顺利进行,有时甚至造成溢渣或喷溅,从而降低钢的收得率及粘枪,因此要尽量避免溢渣和喷溅。
技术科安龙飞。
转炉冶炼操作的关键点
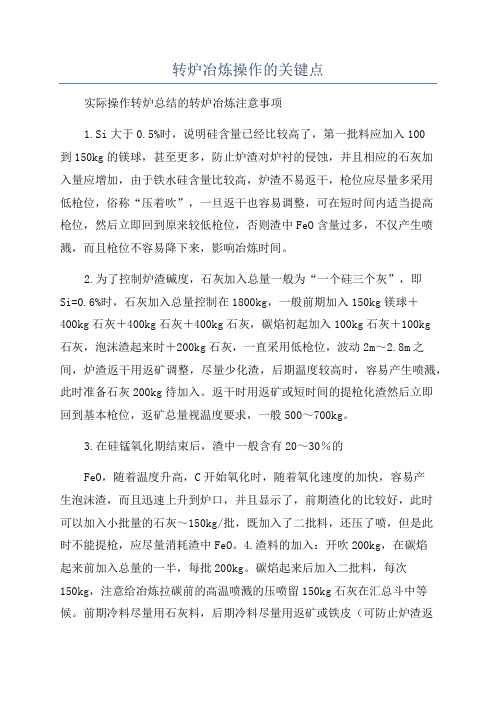
转炉冶炼操作的关键点实际操作转炉总结的转炉冶炼注意事项1.Si大于0.5%时,说明硅含量已经比较高了,第一批料应加入100到150kg的镁球,甚至更多,防止炉渣对炉衬的侵蚀,并且相应的石灰加入量应增加,由于铁水硅含量比较高,炉渣不易返干,枪位应尽量多采用低枪位,俗称“压着吹”,一旦返干也容易调整,可在短时间内适当提高枪位,然后立即回到原来较低枪位,否则渣中FeO含量过多,不仅产生喷溅,而且枪位不容易降下来,影响冶炼时间。
2.为了控制炉渣碱度,石灰加入总量一般为“一个硅三个灰”,即Si=0.6%时,石灰加入总量控制在1800kg,一般前期加入150kg镁球+400kg石灰+400kg石灰+400kg石灰,碳焰初起加入100kg石灰+100kg石灰,泡沫渣起来时+200kg石灰,一直采用低枪位,波动2m~2.8m之间,炉渣返干用返矿调整,尽量少化渣,后期温度较高时,容易产生喷溅,此时准备石灰200kg待加入。
返干时用返矿或短时间的提枪化渣然后立即回到基本枪位,返矿总量视温度要求,一般500~700kg。
3.在硅锰氧化期结束后,渣中一般含有20~30%的FeO,随着温度升高,C开始氧化时,随着氧化速度的加快,容易产生泡沫渣,而且迅速上升到炉口,并且显示了,前期渣化的比较好,此时可以加入小批量的石灰~150kg/批,既加入了二批料,还压了喷,但是此时不能提枪,应尽量消耗渣中FeO。
4.渣料的加入:开吹200kg,在碳焰起来前加入总量的一半,每批200kg。
碳焰起来后加入二批料,每次150kg,注意给冶炼拉碳前的高温喷溅的压喷留150kg石灰在汇总斗中等候。
前期冷料尽量用石灰料,后期冷料尽量用返矿或铁皮(可防止炉渣返干)。
5.Si小于0.4%时,说明硅含量已经比较低了,相应的石灰加入量应减少,由于硅含量比较低,碳焰起来的较早,应及时提前加入二批料。
铁水硅低时炉渣容易返干,注意提前提枪化渣。
6.不论硅高低,开吹时尽量采用30秒高、30秒次高再到正常的低枪位,可以帮助化好前期渣。
高硅铁水转炉双联脱硅工艺的探索及实践

高硅铁水转炉双联脱硅工艺的探索及实践张浩;张春辉【摘要】八钢欧冶炉开炉初期铁水硅高,铁水硅含量平均5.1%.高硅铁水在转炉无法进行常规的单渣、双渣冶炼.八钢炼钢厂120t转炉为了消化高硅铁水,通过探索实践,采用了\"双联脱硅\"工艺,将脱硅与脱碳、脱磷分步进行,由两座转炉联合完成冶炼,成功解决了欧冶炉高硅铁水带来的喷溅问题.\"双联脱硅\"工艺日处理能力为5000~6000t.文章介绍了双联脱硅工艺的试验探索、工艺流程及转炉冶炼的制度.分析了\"双联脱硅\"工艺处理高硅铁水的生产成本.【期刊名称】《新疆钢铁》【年(卷),期】2018(000)004【总页数】5页(P6-10)【关键词】高硅铁水;喷溅;双联脱硅;冶炼制度【作者】张浩;张春辉【作者单位】新疆八一钢铁股份有限公司;新疆八一钢铁股份有限公司【正文语种】中文【中图分类】TF713.71 前言2015年6月18日八钢欧冶炉正式点火投产。
截至6月30日,欧冶1号炉已经突破了日产3000t铁水的产量设计。
欧冶炉开炉初期铁水中硅含量最高10.5%,最低1.2%,平均5.1%。
欧冶炉在投产后铁水硅居高不下,未能按照爬坡计划在一周内将铁水硅降至0.50%以内。
实际[Si]含量在1.2%以上的铁水占到了90%,持续时间长达一个月。
铁水中硅含量越高转炉冶炼的控制难度越大,当硅高于1.2%时,即使采用双渣冶炼也无法有效控制喷溅的发生。
YB/T5296-2011《炼钢用生铁》标准中规定生铁中硅的最大质量分数为1.25%。
当铁水中硅的含量超过此标准时,炼钢工序难以消化,一般采用铸铁机生产铸造生铁。
八钢公司炼铁系统配套的铸铁机铸铁能力为2000t/天,但是铁水硅越高,铁水流动性越差,容易粘接罐口和铸铁机模具,影响铸铁能力。
目前八钢铸铁能力处理不了欧冶炉高硅铁水。
同时每铸1吨铁产生的成本约30元。
为了有序衔接欧冶炉产线发挥欧冶炉节能、环保的优势。
转炉精炼操作流程
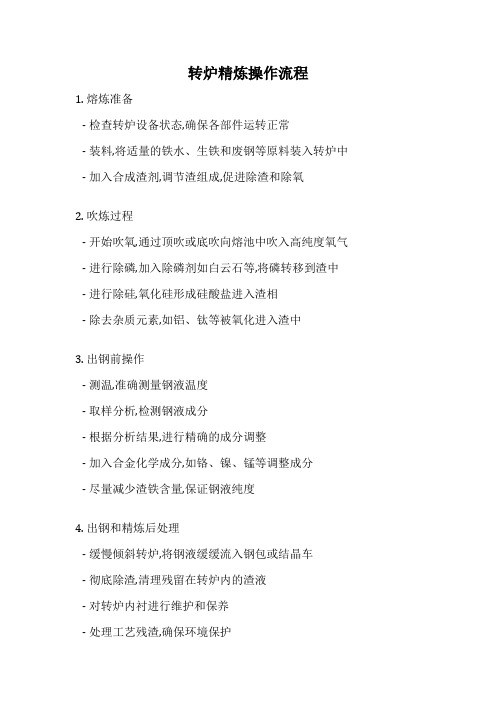
转炉精炼操作流程
1. 熔炼准备
- 检查转炉设备状态,确保各部件运转正常
- 装料,将适量的铁水、生铁和废钢等原料装入转炉中 - 加入合成渣剂,调节渣组成,促进除渣和除氧
2. 吹炼过程
- 开始吹氧,通过顶吹或底吹向熔池中吹入高纯度氧气 - 进行除磷,加入除磷剂如白云石等,将磷转移到渣中 - 进行除硅,氧化硅形成硅酸盐进入渣相
- 除去杂质元素,如铝、钛等被氧化进入渣中
3. 出钢前操作
- 测温,准确测量钢液温度
- 取样分析,检测钢液成分
- 根据分析结果,进行精确的成分调整
- 加入合金化学成分,如铬、镍、锰等调整成分
- 尽量减少渣铁含量,保证钢液纯度
4. 出钢和精炼后处理
- 缓慢倾斜转炉,将钢液缓缓流入钢包或结晶车
- 彻底除渣,清理残留在转炉内的渣液
- 对转炉内衬进行维护和保养
- 处理工艺残渣,确保环境保护
- 进行后续加工,如连铸或其他工序
以上是转炉精炼操作的基本流程,精细的参数控制和工艺调整需要专业的操作人员把控,以确保钢材质量。
转炉工艺操作规程
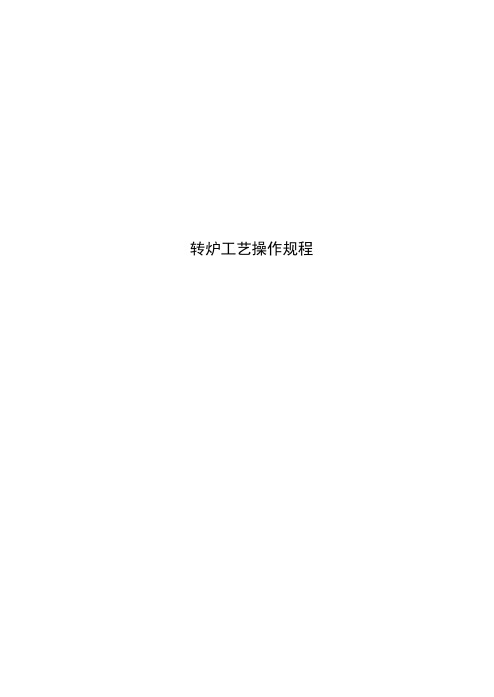
转炉工艺操作规程中铁炼钢部本标准适用于转炉冶炼工序。
1.工艺流程主操作本标准适用于转炉冶炼工序。
铁水1入炉铁水S含量按《冶炼标准》要求控制2入炉铁水计量误差范围不超过士500Kg3铁水带渣量:不超过1吨废钢理化性要求:符合原材料标准规定入炉废钢计量误差范围不超过士500Kg活性石灰理化性要求:符合原材料标准规定化学成分% :厂内活性石灰CaO > 91.3, SiO2< 2.8 , S< 0.025;厂外活性石灰CaO > 86.0, S< 0.045。
粒度范围:5~ 50 mm轻烧白云石理化性要求:符合原材料标准规定化学成分% : CaO >52.4, SiO2< 3.0, MgO >29.1, S< 0.040, P< 0.10粒度范围:5~ 30 mm轻烧镁球理化性要求:符合原材料标准规定化学成分% : MgO >65, CaO >5, S< 0.02粒度范围:5~ 30 mm锰矿理化性要求:符合原材料标准规定萤石理化性要求:符合原材料标准规定烧结矿理化性要求:符合原材料标准规定合成渣理化性要求:符合原材料标准规定硅铁理化性要求:符合原材料标准规定硅铁的化学成分锰铁理化性要求:符合原材料标准规定锰铁的化学成分硅锰理化性要求:符合原材料标准规定硅锰合金的化学成分硅钙包芯线理化性要求:符合原材料标准规定硅钙包芯线的化学成分铝线理化性要求:符合原材料标准规定增碳剂理化性要求:符合原材料标准规定增碳剂的化学成分钢包覆盖剂理化性要求:符合原材料标准规定本标准适用于转炉冶炼工序。
氧气氧气总管压力》1・2 Mpa;纯度》99.6%;氮气溅渣用氮气总管压力》1.2Mpa ;底吹用氮气总管压力》1.6Mpa ;纯度》99.99%;氩气氩气总管压力》1.6Mpa;纯度》99.99%;本标准适用于转炉冶炼工序。
1. 检测和计量系统确认完毕。
转炉炼钢生产3
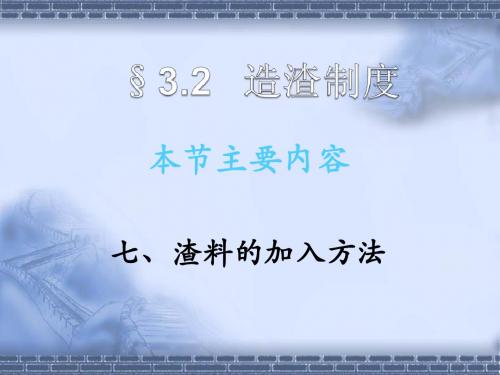
二、供氧压力
定义:供氧压力是指转炉车间内氧压测定点 的表压值,又叫使用压力,符号P用,单位是 MPa。因此,它与P0的关系为: P用= P0-0.1+(0.015~0.025)MPa 取值:炉容的大小和原材料不同波动在0.7~ 1.5MPa之间。一般来说炉子容量越大,供氧 压力越高;吹炼中高磷铁水时,渣量大,易 喷,可适当低些。 另外,国内各厂一般都采用分阶段衡压操作 (与分阶段定量装入相对应),即随炉龄增
一、供氧量和供氧强度
2 、供氧强度 定义:单位时间内每吨金属的耗氧量,常用 I表示,单位是m3/t· min。 计算公式:供氧强度I= =
供氧量(m 3 / min) 装入量(t) 每吨金属耗氧量( 3 / t ) m 供氧时间(min)
讨论:一定的生产条件下每吨金属的耗氧量是定 值,较高的供氧强度意味着供氧时间较短,即生 产率高。但实际生产中喷头的直径一定,只有通 过提高氧气的压力来实现,这样吹炼中喷溅严重 且氧气的利用率较低。一般情况下,随着转炉容 量的增大,H/D减小,生产中易喷,供氧强度减小,
计算公式:
每吨金属需氧量( 3 / t) 装入量(t) m 供氧量Q 供氧时间(min)
一、供氧量和供氧强度
1)每吨金属需氧量 它取决于铁水成分、所炼钢种的终点成 分及氧气利用率等因素,通常情况下为52~ 60m3/t。 2)供氧时间 国内不同容量转炉的供氧时间统计如下表: 转炉容量/t 12 30 50 120 供氧时间/min ~15 ~16 ~
§ 3.3 供氧制度
顶吹转炉是用带有拉瓦尔喷 头的水冷氧枪,将压力为0.7~ 1.5MPa的氧气从炉子的上方送入 炉内。实际生产中,氧枪喷头的 结构和尺寸已经确定,因此,转 炉的供氧制度主要是依据生产条 件确定合适的供氧量、供氧强度、
高炉炼铁

现代炼铁的主要方法,钢铁生产中的重要环节。
这种方法是由古代竖炉炼铁发展、改进而成的。
尽管世界各国研究发展了很多新的炼铁法,但由于高炉炼铁技术经济指标良好,工艺简单,生产量大,劳动生产率高,能耗低,这种方法生产的铁仍占世界铁总产量的95%以上。
高炉生产时从炉顶装入铁矿石、焦炭、造渣用熔剂(石灰石),从位于炉子下部沿炉周的风口吹入经预热的空气。
在高温下焦炭(有的高炉也喷吹煤粉、重油、天然气等辅助燃料)中的碳同鼓入空气中的氧燃烧生成的一氧化碳和氢气,在炉内上升过程中除去铁矿石中的氧,从而还原得到铁。
炼出的铁水从铁口放出。
铁矿石中不还原的杂质和石灰石等熔剂结合生成炉渣,从渣口排出。
产生的煤气从炉顶导出,经除尘后,作为热风炉、加热炉、焦炉、锅炉等的燃料。
简史和近况早期高炉使用木炭或煤作燃料,18世纪改用焦炭,19世纪中叶改冷风为热风(见冶金史)。
20世纪初高炉使用煤气内燃机式和蒸汽涡轮式鼓风机后,高炉炼铁得到迅速发展。
20世纪初美国的大型高炉日产生铁量达450吨,焦比1000公斤/吨生铁左右。
70年代初,日本建成4197米3高炉,日产生铁超过1万吨,燃料比低于500公斤/吨生铁。
中国在清朝末年开始发展现代钢铁工业。
1890年开始筹建汉阳铁厂,1号高炉(248米3,日产铁100吨)于1894年5月投产。
1908年组成包括大冶铁矿和萍乡煤矿的汉冶萍公司。
1980年,中国高炉总容积约8万米3,其中1000米3以上的26座。
1980年全国产铁3802万吨,居世界第四位70年代末全世界2000米3以上高炉已超过120座,其中日本占1/3,中国有四座。
全世界4000米3以上高炉已超过20座,其中日本15座,中国有1座在建设中。
50年代以来,中国钢铁工业发展较快,高炉炼铁技术也有很大发展,主要表现在:①综合采用精料、上下部调剂、高压炉顶、高风温、富氧鼓风、喷吹辅助燃料(煤粉和重油等)等强化冶炼和节约能耗新技术,特别在喷吹煤粉上有独到之处。
转炉冶炼的工艺流程

转炉冶炼的工艺流程
转炉冶炼的工艺流程如下:
1.准备阶段:主要原料包括铁水、废钢和铁合金。
根据需求,加入不同的造渣材料,如石灰、白云石、铁皮球、矿石和萤石。
2.吹炼阶段:温度逐渐上升,碳含量逐渐下降。
炉口由浓烟滚滚逐渐变得明亮。
在这一阶段,通过控制枪位位置,可以防止喷溅和返干。
3.脱碳阶段:脱碳速度降低,熔池温度上升。
炉口由烟气明亮逐渐变得稀疏透明。
此时,需要确定冶炼终点,即检查碳、硫、磷和温度是否满足要求。
4.出钢阶段:通过经验法,如炉口明亮度、副枪和吹氧累积量来确定何时结束吹氧并提升氧枪。
副枪系统的使用取消了人工取样和测温,这不仅可以节省时间,而且降低了对操作人员的技能要求。
转炉炼钢对铁水成分和温度有什么要求?
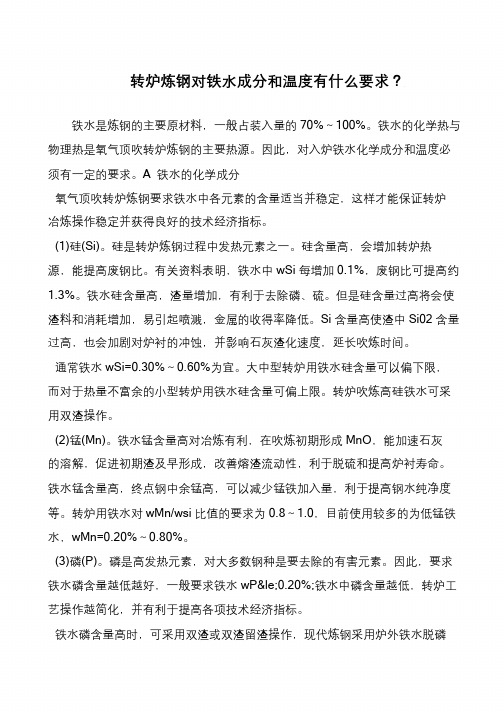
立志当早,存高远转炉炼钢对铁水成分和温度有什么要求?铁水是炼钢的主要原材料,一般占装入量的70%~100%。
铁水的化学热与物理热是氧气顶吹转炉炼钢的主要热源。
因此,对入炉铁水化学成分和温度必须有一定的要求。
A 铁水的化学成分氧气顶吹转炉炼钢要求铁水中各元素的含量适当并稳定,这样才能保证转炉冶炼操作稳定并获得良好的技术经济指标。
(1)硅(Si)。
硅是转炉炼钢过程中发热元素之一。
硅含量高,会增加转炉热源,能提高废钢比。
有关资料表明,铁水中wSi 每增加0.1%,废钢比可提高约1.3%。
铁水硅含量高,渣量增加,有利于去除磷、硫。
但是硅含量过高将会使渣料和消耗增加,易引起喷溅,金属的收得率降低。
Si 含量高使渣中Si02 含量过高,也会加剧对炉衬的冲蚀,并影响石灰渣化速度,延长吹炼时间。
通常铁水wSi=0.30%~0.60%为宜。
大中型转炉用铁水硅含量可以偏下限,而对于热量不富余的小型转炉用铁水硅含量可偏上限。
转炉吹炼高硅铁水可采用双渣操作。
(2)锰(Mn)。
铁水锰含量高对冶炼有利,在吹炼初期形成MnO,能加速石灰的溶解,促进初期渣及早形成,改善熔渣流动性,利于脱硫和提高炉衬寿命。
铁水锰含量高,终点钢中余锰高,可以减少锰铁加入量,利于提高钢水纯净度等。
转炉用铁水对wMn/wsi 比值的要求为0.8~1.0,目前使用较多的为低锰铁水,wMn=0.20%~0.80%。
(3)磷(P)。
磷是高发热元素,对大多数钢种是要去除的有害元素。
因此,要求铁水磷含量越低越好,一般要求铁水wP≤0.20%;铁水中磷含量越低,转炉工艺操作越简化,并有利于提高各项技术经济指标。
铁水磷含量高时,可采用双渣或双渣留渣操作,现代炼钢采用炉外铁水脱磷。
转炉精炼操作流程
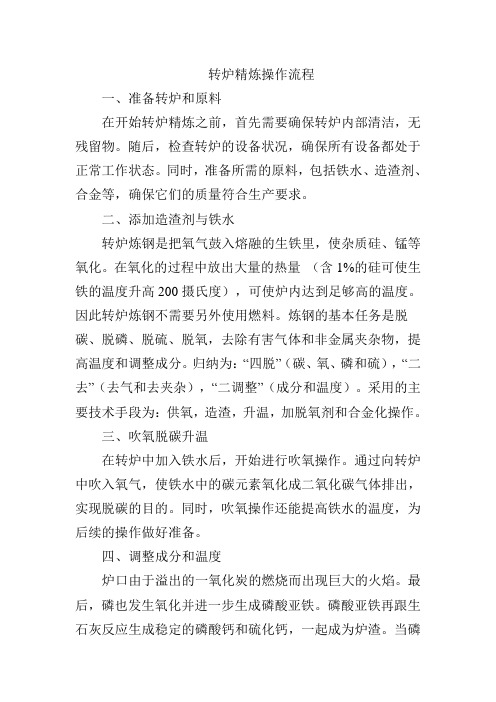
转炉精炼操作流程一、准备转炉和原料在开始转炉精炼之前,首先需要确保转炉内部清洁,无残留物。
随后,检查转炉的设备状况,确保所有设备都处于正常工作状态。
同时,准备所需的原料,包括铁水、造渣剂、合金等,确保它们的质量符合生产要求。
二、添加造渣剂与铁水转炉炼钢是把氧气鼓入熔融的生铁里,使杂质硅、锰等氧化。
在氧化的过程中放出大量的热量(含1%的硅可使生铁的温度升高200摄氏度),可使炉内达到足够高的温度。
因此转炉炼钢不需要另外使用燃料。
炼钢的基本任务是脱碳、脱磷、脱硫、脱氧,去除有害气体和非金属夹杂物,提高温度和调整成分。
归纳为:“四脱”(碳、氧、磷和硫),“二去”(去气和去夹杂),“二调整”(成分和温度)。
采用的主要技术手段为:供氧,造渣,升温,加脱氧剂和合金化操作。
三、吹氧脱碳升温在转炉中加入铁水后,开始进行吹氧操作。
通过向转炉中吹入氧气,使铁水中的碳元素氧化成二氧化碳气体排出,实现脱碳的目的。
同时,吹氧操作还能提高铁水的温度,为后续的操作做好准备。
四、调整成分和温度炉口由于溢出的一氧化炭的燃烧而出现巨大的火焰。
最后,磷也发生氧化并进一步生成磷酸亚铁。
磷酸亚铁再跟生石灰反应生成稳定的磷酸钙和硫化钙,一起成为炉渣。
当磷与硫逐渐减少,火焰退落,炉口出现四氧化三铁的褐色蒸汽时,表明钢已炼成。
这时应立即停止鼓风,并把转炉转到水平位置,把钢水倾至钢水包里,再加脱氧剂进行脱氧。
整个过程只需15分钟左右。
如果氧气是从炉底吹入,那就是底吹转炉;氧气从顶部吹入,就是顶吹转炉。
五、出钢与渣处理钢与生铁的区别:首先是碳的含量,理论上一般把碳含量小于2.11%称之钢,它的熔点在1450-1500℃,而生铁的熔点在1100-1200℃。
在钢中碳元素和铁元素形成Fe3C固熔体,随着碳含量的增加,其强度、硬度增加,而塑性和冲击韧性降低。
钢具有很好的物理、化学性能与力学性能,可进行拉、压、轧、冲、拔等深加工,其用途十分广泛。
六、合金化操作为了进一步提高铁水的性能,需要进行合金化操作。
转炉炼钢原理及工艺介绍
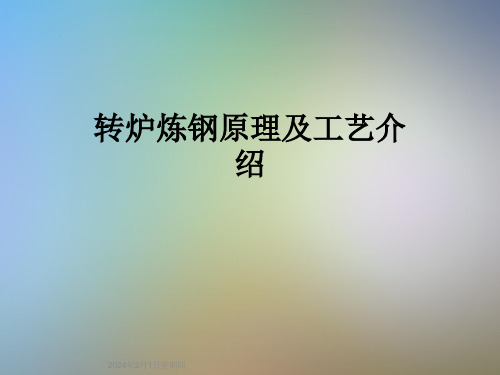
锰的氧化反应有三种情况:
(1)锰与气相中的氧直接作用
[Mn]+ 1/2{O2}=(MnO)
(2)锰与溶于金属中的氧作用
[Mn]+ [O2] =(MnO)
(3)锰的氧化与还原
3)锰与炉渣中氧化亚铁作用
[Mn]+(FeO)=(MnO)+ [Fe]
第三个反应在炉渣——金属界面上迸行,是锰氧化的主要反应。
锰的氧化还原与硅的氧化还原相比有以下基本特点:
1)在冶炼初期锰和硅一样被迅速大量氧化,但锰的氧化程度要低些
,这是由于硅与氧的结合能力大于锰与氧的结合能力;
2)MnO为弱碱性氧化物,在碱性渣中( MnO)大部分呈自由状态存
在。因此,在一定条件下可以被还原。由于锰的氧化反应是放热反应,故
温度升高有利于锰的还原。所以在生产实践中冶炼后期熔池中会出现回锰
1)在某一温度下,几种元素同时和氧相遇时,位置低的元素先氧化。如1500℃ 时,氧化顺序为Al、Si、C、V、Mn。
2)位置低的元素可将位置高的氧化物还原。炼钢过程中脱氧就是利用Al、Si等 元素将FeO还原。
3)CO的分解压曲线的斜率与其它氧化物的不同,它与Si、Mn、V等的氧化物分 解与压CO曲分线解有压一曲交线点相,交此点点对所应对的应温的度温为度15称30为℃氧,化当转t>化15温30度℃。时例,如Si,先S于iOC2被分氧解化压;曲当线 t<1530℃时,则C先于Si被氧化。1530℃即为Si、C的氧化转化温度。
• 所谓炼钢,就是通过冶炼降低生铁中的 碳和去除有害杂质,在根据对钢性能的要求 加入适量的合金元素,使其成为具有高的强 度、韧性或其他特殊性能的钢。
•二、炼钢基本原理
• 因此,炼钢的基本任务可归纳为:
转炉炼钢工艺操作规程
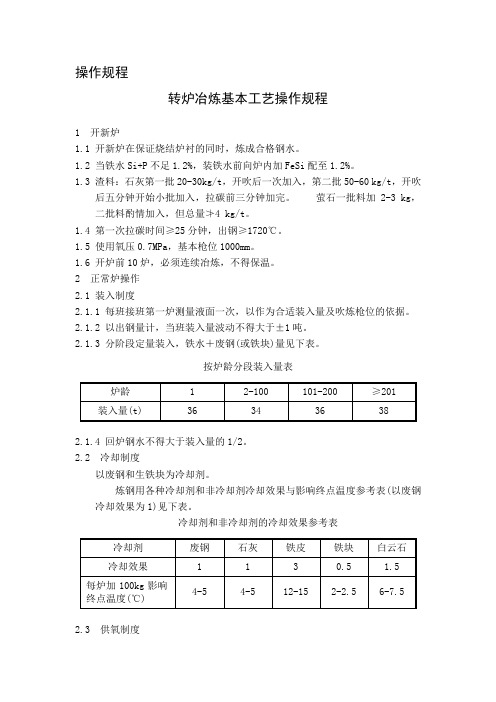
操作规程转炉冶炼基本工艺操作规程1 开新炉1.1 开新炉在保证烧结炉衬的同时,炼成合格钢水。
1.2 当铁水Si+P不足1.2%,装铁水前向炉内加FeSi配至1.2%。
1.3 渣料:石灰第一批20-30kg/t,开吹后一次加入,第二批50-60 kg/t,开吹后五分钟开始小批加入,拉碳前三分钟加完。
萤石一批料加2-3 kg,二批料酌情加入,但总量≯4 kg/t。
1.4 第一次拉碳时间≥25分钟,出钢≥1720℃。
1.5 使用氧压0.7MPa,基本枪位1000mm。
1.6 开炉前10炉,必须连续冶炼,不得保温。
2正常炉操作2.1 装入制度2.1.1 每班接班第一炉测量液面一次,以作为合适装入量及吹炼枪位的依据。
2.1.2 以出钢量计,当班装入量波动不得大于±1吨。
2.1.3 分阶段定量装入,铁水+废钢(或铁块)量见下表。
按炉龄分段装入量表2.1.4 回炉钢水不得大于装入量的1/2。
2.2 冷却制度以废钢和生铁块为冷却剂。
炼钢用各种冷却剂和非冷却剂冷却效果与影响终点温度参考表(以废钢冷却效果为1)见下表。
冷却剂和非冷却剂的冷却效果参考表2.3 供氧制度2.3.1 采用分期定压、恒压变枪位操作。
氧压低于0.4MPa不得吹炼。
各阶段氧压参考表2.3.2 枪位控制基本枪位900-1100mm,波动枪位800-1200mm。
枪位调整要做到勤动少动。
正常情况应控制≯200mm/次。
以基本枪位为主要吹炼枪位,为迅速成渣,在开始吹炼时或炉渣返干时允许适当提高枪位。
严禁过高枪位操作。
冶炼末期要采取低枪位操作,时间最少不少于60秒。
2.3.3 采用三孔喷头吹炼,喷头参数φ27×3-11,氧枪漏水时应及时换枪。
2.4 造渣制度要求吹炼全程化渣2.4.1 除后吹炉次外,均采用留渣操作工艺。
即出完钢后,先向炉内加入石灰、白云石混合物,稠化炉渣,后吹炉次必须倒净炉渣,不得先加石灰,后倒渣。
2.4.2 铁水Si>0.8%时应采用双渣操作。
4、转炉炼钢工艺制度(下)
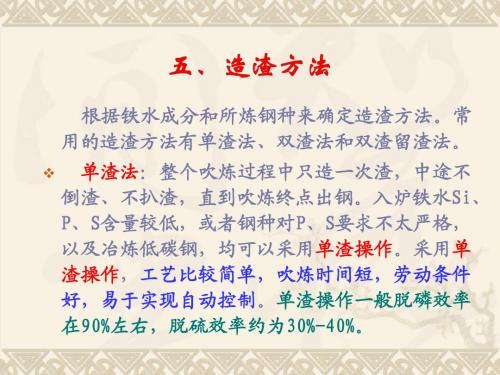
六、温度制度
在吹炼一炉钢的过程中,需要正确控制温度。
温度制度主要是指炼钢过程温度控制和终点温
度控制。
转炉吹炼过程的温度控制相对比较复杂,如 何通过加冷却剂和调整枪位,使钢水的升温和 成分变化协调起来,同时达到吹炼终点的要求, 是温度控制的关键。
热量来源:铁水的物理热和化学热,它 们约各点热量来源的一半。 热量消耗:习惯上转炉的热量消耗可分 为两部分,一部分直接用于炼钢的热量, 即用于加热钢水和炉渣的热量;一部分未 直接用于炼钢的热量,即废气、烟尘带走 的热量,炉口炉壳的散热损失和冷却剂的 吸热等。
双渣留渣法:将双渣法操作的高碱度、高氧 化铁、高温、流动性好的终渣留一部分在炉内, 然后在吹炼第一期结束时倒出,重新造渣。此 法的优点是可加速下炉吹炼前期初期渣的形成, 提高前期的去磷、去硫率和炉子热效率,有利 于保护炉衬,节省石灰用量。采用留渣操作时, 在兑铁水前首先要加废钢稠化冷凝熔渣,当炉 内无液体渣时才可兑入铁水,以避免引发喷溅。
加速渣料的熔化
加速石灰溶解的措施 1)适宜的炉渣成分 渣中的(FeO)是石灰溶解的基本熔剂,原因在于: (1)(FeO)可与CaO及2CaO· SiO2作用生成低熔点的盐,能有效 地降低炉渣的粘度,改善石灰溶解的外部传质条件; (2)(FeO)是碱性氧化渣的表面活性物质,可以改善炉渣对石 灰的润湿性,有利于熔渣向石灰表面的孔中渗透,增大二者之间的 接触面积; (3)Fe2+及O2-的半径是同类中最小的,扩散能力最强; (4)有足够的(FeO)存在时,可以避免石灰表面生成C2S而有 利于石灰的溶解。 因此,吹炼操作中应合理地控制枪位,始终保持较高的 (FeO)含量。(MnO)对石灰溶解的影响与(FeO)类似,生产中可 在渣料中配加适量锰矿。
铁的冶炼操作流程
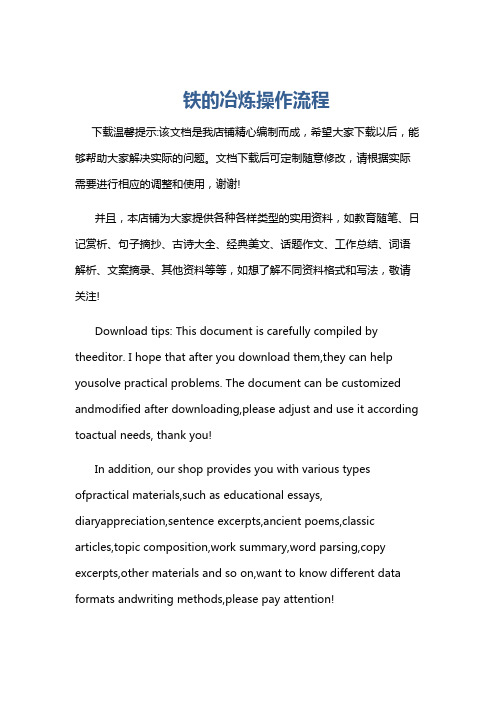
铁的冶炼操作流程下载温馨提示:该文档是我店铺精心编制而成,希望大家下载以后,能够帮助大家解决实际的问题。
文档下载后可定制随意修改,请根据实际需要进行相应的调整和使用,谢谢!并且,本店铺为大家提供各种各样类型的实用资料,如教育随笔、日记赏析、句子摘抄、古诗大全、经典美文、话题作文、工作总结、词语解析、文案摘录、其他资料等等,如想了解不同资料格式和写法,敬请关注!Download tips: This document is carefully compiled by theeditor. I hope that after you download them,they can help yousolve practical problems. The document can be customized andmodified after downloading,please adjust and use it according toactual needs, thank you!In addition, our shop provides you with various types ofpractical materials,such as educational essays, diaryappreciation,sentence excerpts,ancient poems,classic articles,topic composition,work summary,word parsing,copy excerpts,other materials and so on,want to know different data formats andwriting methods,please pay attention!铁的冶炼操作流程一、准备工作阶段。
在进行铁的冶炼之前,需要进行一系列准备工作。
- 1、下载文档前请自行甄别文档内容的完整性,平台不提供额外的编辑、内容补充、找答案等附加服务。
- 2、"仅部分预览"的文档,不可在线预览部分如存在完整性等问题,可反馈申请退款(可完整预览的文档不适用该条件!)。
- 3、如文档侵犯您的权益,请联系客服反馈,我们会尽快为您处理(人工客服工作时间:9:00-18:30)。
铁水硅高条件下转炉的冶炼操作总结及对策
9月份共有188炉造双渣,喷溅16炉,喷溅率8.5%。
造成石灰消耗、钢铁料消耗升高。
下表为8月份消耗与9月份造双渣消耗对比:
一、16炉喷溅原因分析:
除1#炉丙班、3#炉甲班没有喷溅外,其余10个小组都有喷溅,情况如下:
具体分析:
1、侥幸心理没造双渣,有5炉,造成4炉小喷,1炉中喷。
2、中期化渣早,控制不住,喷溅,有4炉。
通过分析此类喷溅特点是:倒渣后,吹炼枪位较高,在8~9分钟之间化渣,此类炉渣往往在提枪后30秒左右就能化透,比正常化渣时间提前了约2~3分钟。
炉渣呈泡沫渣,这时熔池内正处于碳氧强烈反应期,生成的大量的CO气泡携带着钢渣从炉口喷出。
3、中后期温度高造成的喷溅1炉。
分析为一次性加入冷料多,熔池温度骤然下降,温度上来后造成喷溅。
4、前期小喷7炉。
主要为泡沫渣喷溅。
渣量大,渣层厚,氧化铁聚集。
碱度低,生成的气体带动炉渣涌出。
5、从总体废钢来看,废钢数量较少,平均为每炉12吨;铁块每炉平均25吨。
二、铁水硅含量高,给转炉操作带来一定影响,造成金属、温度损失大,冶炼时间延长,为保证生产的顺利进行,特对铁水硅高条件下的转炉的操作做如下规定:
操枪工接到倒罐站兑铁情况后必须对硅量进行计算,铁水硅含量≥0.8 %时必须采用双渣操作,具体操作如下:
1、废钢的确定:铁水硅在0.8%~1.1%之间,铁水温度在1290~1310℃之间,加入废钢10吨,渣钢5吨,铁块为12~16吨;铁水硅>1.1%,铁水温度大于1310℃,加入废钢10吨,渣钢5吨,铁块为15~20吨。
2、头批渣料的确定:要求上炉留渣量大于1/2。
在留渣量为1/2左右时,头坯料为石灰6.5吨左右,轻烧白云石2.5吨左右;全部留渣时,要求石灰5.5吨左右,轻烧白云石2.5吨左右。
以保证前期石灰尽快熔化,炉渣碱度迅速达到1.7左右,氧化镁达到8%以上,减少炉衬的浸蚀。
3、硅高铁水降枪吹炼时火焰较少,火焰呈暗红色且火焰较直。
基本上没有碳花,较少看到碳焰。
由于留渣所以开始吹炼时枪位比正常高5~10cm,氧压正常使用。
以尽快熔化炉渣。
吹炼1~1.5分钟加入头批料。
开吹4~5分钟左右,Si、Mn氧化完毕,炉口碳焰上来之后,有稀薄渣从炉口溢出时,提枪倒渣。
4、倒渣后的冶炼操作:
①石灰的确定:倒渣后,铁水中的磷已去掉50%~70%,此时应确定以后
的渣料,倒渣后普碳钢、低合金的石灰加入量应按25~30Kg/t钢掌握;SS400按30~37Kg/t 掌握,SPHD按38~42Kg/t掌握。
②由于倒掉了一部分炉渣,氧化镁有所降低,应补充轻烧白云石500~800Kg/炉。
③温度的调节:适量使用矿石,吨钢用量约10Kg,其余使用铁皮球及生白云石调节。
生白云石用量吨钢约8Kg。
④枪位的控制:倒渣后,由于热量的损失,炉内需要升温来保证渣料的熔化,此时枪位应比正常吹炼枪位低5~10cm,达到快速升温。
同时有效抑制氧化铁的富集,防止喷溅。
吹炼10分钟左右,温度提上来后,再适当高枪位化渣。
三、此方法经过实践,基本能够正常冶炼,吹炼中喷溅基本能够得到控制。
下面为10月4日硅高时冶炼的一些数据:
铁水Si 1.02%~1.38%,共有9炉造双渣,硬线4炉,SS400 5炉;
硬线钢吨钢消耗石灰:74.5Kg。
轻烧:18.8 Kg;
SS4OO吨钢消耗石灰:68.8Kg。
轻烧:21 Kg;
其中全留渣4炉,其余5炉留渣量为1/2~1/3;
冶炼工艺基本是按照下发的铁水硅高冶炼操作要点执行。
技术科
2005/10/6。