第五章工艺规程设计
机械加工工艺规程的制定 机械制作技术基础复习与测试题

第五章机械加工工艺规程的制定1.生产过程与工艺过程的含义是什么?两者的主要组成部分有哪些?[解]机械的生产过程是指机械从原材料开始直到制成机械产品之间的各个相互联系的劳动过程的总和。
它包括毛坯制造—零件的加工及热处理—机械的装配及检验—油漆及包装过程等直接生产过程.还包括原材料的运输和保管以及设计、工艺装备(刀,夹,量具等)的制造、维修等生产技术准备工作。
工艺过程是生产过程的重要组成部分,包括直接改变工件的形状(铸造,锻造等)、尺寸(机械加工)、位置(装配)和材料性质(热处理)使其成为预期产品的过程。
机械加工的工艺过程一般由工序、安装或工位、工步、走刀等组成。
2.生产纲领的含义是什么?划分生产类型的主要依据有哪些因素?[解]生产纲领即指年产量,它应计入备品和废品的数量。
可按下式计算:N零=N×n×(1+α)(1十β)。
生产类型的划分主要考虑年产量,产品本身的大小和结构的复杂性。
3.经济精度的含义是什么?它在工艺规程设计中起什么作用?[解]经济精度是指在正常的机床、刀具、工人等工作条件下,以合适的工时消耗所能达到的加工精度。
因此,在经济精度的范围内,加工精度和加工成本是互相适应的。
有关资料表格中列出各种加工方法所能达到的经济精度及表面租糙度是拟定零件工艺路线的基础,用以从中选择最合适的加工方法和加工设备。
4.何谓结构工艺性?对机械零件结构工艺性有哪些要求?[解]结构工艺性是指机器和零件的结构是否便于加工,装配和维修。
衡量工艺性的主要依据是能够可靠保证产品质量,且加工劳动量小、生产成本低,材料消耗少。
5.试分析下列加工情况的定位基准:(1)拉齿坯内孔时;(2)珩磨连杆大头孔时;(3)无心磨削活塞销外圆时;(4)磨削床身导轨面时;(5)用浮动镗刀块精镗内孔时;(6)超精加工主轴轴颈时;(7)箱体零件攻螺纹时;(8)用与主轴浮动连接的铰刀铰孔时。
[解]以上都是自为基准的加工例子,即以加工面本身作为定位基准。
焊接工艺规程的编制

第二节 焊接工艺评定
• 但如果本企业因设备或检测手段不完备,可将试件的下料和坡口加工、 试板的无损检测、试板取样及加工、力学性能试验及其他性能的检验 等一些程序委托其他单位完成,但承包商或制造厂对整个评定工作及 试验结果负全部责任。
• 二、焊接工艺评定的程序 • 焊接工艺评定一般过程是:拟定焊接工艺评定指导书、施焊试件和
可做如下定义:焊接工艺规程是一种经评定合格的书面焊接工艺文件, 用来指导工人按法规的要求焊制产品。具体地说,焊接工艺规程可用 来指导焊工和焊接操作者施焊产品接头,以保证焊缝的质量符合法规 要求。 • 焊接工艺规程必须由生产该焊件的企业自行编制,不得沿用其他企 业的焊接工艺规程,也不得委托其他单位编制用以指导本企业焊接生 产的焊接工艺规程因此,焊接工艺规程也是技术监督部门检查企业是 否具有按法规要求生产焊接产品资格的证明文件之一,目前已成为焊 接结构生产企业认证检查中的必查项目之一。
制取试样、检验试件和试样、测定焊接接头是否具有所要求的使用性 能、提出焊接工艺评定报告以对拟定的焊接工艺进行评定。焊接工艺 评定验证施焊单位拟定的焊接工艺的正确性,并评定施焊单位能力。 • (1)统计焊接结构中应进行焊接工艺评定的所有焊接接头的类型及 各项有关数据。
上一页 下一页 返回
第二节 焊接工艺评定
• 例如,锅炉膜式水冷壁是由许多钢管和扁钢拼焊而成,其拼接接头如 图5-1所示。
• 为了使产品能适应某种先进焊接工艺,在不影响产品使用功能的前 提下可以改变其结构设计。例如,锅炉膜式水冷壁可以改用鳍片管拼 焊的结构,如图5-2所示。
上一页 下一页 返回
第一节 焊接结构工艺过程分析
• 这样的结构易于实现机械化和自动化装配及焊接,且生产率大大提高, 如图5-3所示。
机械加工工艺教案

点
与
难
点
重点:基准的选择。
难点:工序基准和定位基准的区别、精基准选择的四个原则及粗基准选择的四个原则。
课
堂
讨
论
如何避免粗基准的重复使用?
作
业
5.3、5.4、5.17
备
注
周
次
第 3 次课
章
节
名
称
第五章机械加工工艺规程的制定
授
课
方
式
多媒体与课堂讲授相结合
教 学
时 数
2小时
内
容
与
要
求
5.4工艺路线的拟定
周
次
第1次课
章
节
名
称
第五章机械加工工艺规程的制定
授
课
方
式
多媒体与课堂讲授相结合
教学
时数
2小时
内
容
与
要
求
5.1零件制造的工艺过程
5.2工艺规程的作用及设计步骤
掌握工艺过程的组成,了解生产类型对工艺过程的影响,初步了解工艺规程的作用设计步骤。
重
点
与
难
点
重点:工序、安装、工位、各种生产类型的特点。
课
堂
讨
论
备
注
周
次
第4次课
章
节
名
称
第五章机械加工工艺规程的制定
授
课
方
式
多媒体与课堂讲授相结合
教 学
时 数
2小时
内
容
与
要
求
5.6尺寸链
5.7工序尺寸的确定
掌握极值法计算尺寸链的方法,了解概率法计算尺寸链的方法
第五章中试放大与生产工艺规程

三、中试放大的前提条件-1
• 1.小试合成路线已确定,小试工艺已 成熟,产品收率稳定且质量可靠。成 熟的小试工艺应具备的条件是:
– 合成路线确定; – 操作步骤明晰; – 反应条件确定; – 提纯方法可靠等。
三、中试放大的前提条件-2
• 2. 小试工艺的考察已完成。已取得小试 工艺多批次稳定翔实的实验数据;进行 了3~5批小试稳定性试验说明该小试工 艺稳定可行。
数学模型的建立
• 合理简化过程,提出物理模型模拟实际过程。 • 对物理模型进行数学描述,得到数学模型。 • 用计算机研究数学模型各参数变化对过程的
影响。 • 数学模拟放大法以过程参数间的定量关系为
基础,能进行高倍数放大,缩短放大周期。
数学模拟的前提和发展方向
• 数学模拟进行工程放大,主要取决于预测 大设备的行为的数学模型的可靠性。
3)制定生产工艺
• 在大型设备和车间投入生产,试制若 干批号后,制定出生产工艺规程。
• 生产工艺规程
二、中试放大的重要性
一般要经过一个将小型试验放大50~100倍 的中试放大,以便进一步考察研究在一定 规模的装置设备中各步化学反应条件变化 的规律,以解决小型实验所不能解决或未 发现的问题。
为什么要经过中试放大阶段? Answer should be from reasons and aims!
Example-1
• Preparation and purification of chlormethine • Ethanol as solvent • EtOH + Dichloromethane
HO
CH3NH2
O HOAc
N
HO
POCl3, DMF
Cl
机械加工工艺规程的制定

工艺过程组成
工艺过程组成
2)安装
工件加工前,使其在机床或夹具中相对刀具占 据正确位置并给予固定的过程,称为装夹。(装夹 包括定位和夹紧两过程)
安装是指工件通过一次装夹后所完成的那一部 分工序。
1、生产纲领: 指包括备品、备件在内的该产品 的年产量。产品的年生产纲领就是产品的年生产量。 零件的年生产纲领由下式计算
N=Qn(1+a)(1+b)
式中:
N:零件的生产纲领(件/年); Q:产品的年产量(台/年); n:单台产品该零件的数量(件/年); a:备品率,以百分数计; b:废品率,以百分数计。
第五章 机械加工工艺规程设计
本章主要介绍以下内容: 5.1 零件制造的工艺过程 5.2 工艺规程的作用及设计步骤 5.3 零件工艺性分析与毛坯的选择 5.4 定位基准的选择 5.5 工艺路线的拟定 5.6 加工余量的确定 5.7 尺寸链和工序尺寸的确定 5.8 时间定额和经济分析
重点、难点:定位基准的选择;尺寸链和工序尺寸 的确定
定义:全年中重复制造同一产品。 特点:产品品 种少、产量大,长期重复进行同一产品的加工。
5.2 各种生产类型工艺过程的主要特点
工艺过程特点 工件的互换性
单件生产
一般是配对制造,没有互换 性,广泛用钳工修配
毛坯的制造方 法及加工余量
铸件用木模手工造型;锻件 用自由锻。毛坯精度低,加 工余量大
生产类型
5)走刀
走刀(又称工作行程)是指刀具相对工件加工 表面进行一次切削所完成的那部分工作。每个工步 可包括一次走刀或几次走刀。
机械制造技术基础习题
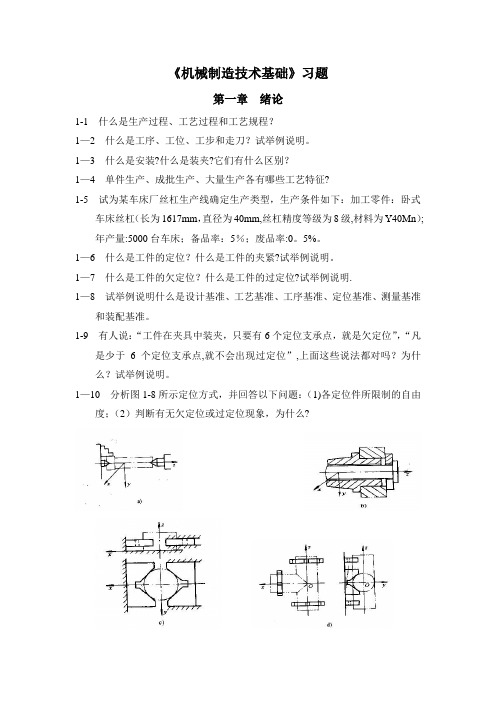
《机械制造技术基础》习题第一章绪论1-1 什么是生产过程、工艺过程和工艺规程?1—2 什么是工序、工位、工步和走刀?试举例说明。
1—3 什么是安装?什么是装夹?它们有什么区别?1—4 单件生产、成批生产、大量生产各有哪些工艺特征?1-5 试为某车床厂丝杠生产线确定生产类型,生产条件如下:加工零件:卧式车床丝杠(长为1617mm,直径为40mm,丝杠精度等级为8级,材料为Y40Mn);年产量:5000台车床;备品率:5%;废品率:0。
5%。
1—6 什么是工件的定位?什么是工件的夹紧?试举例说明。
1—7 什么是工件的欠定位?什么是工件的过定位?试举例说明.1—8 试举例说明什么是设计基准、工艺基准、工序基准、定位基准、测量基准和装配基准。
1-9 有人说:“工件在夹具中装夹,只要有6个定位支承点,就是欠定位”,“凡是少于6个定位支承点,就不会出现过定位”,上面这些说法都对吗?为什么?试举例说明。
1—10 分析图1-8所示定位方式,并回答以下问题:(1)各定位件所限制的自由度;(2)判断有无欠定位或过定位现象,为什么?图1—8 习题1—10图第二章 金属切削原理与刀具2-1 什么是切削用两三要素?在外圆车削中,它们与切削层参数有什么关系? 2—2 确定外圆车刀切削部分几何形状最少需要几个基本角度?试画图标出这些基本角度。
2—3 试述刀具标注角度和工作角度的区别.为什么车刀作横向切削时,进给量取值不能过大?2-4 刀具切削部分的材料必须具备哪些基本性能?2-5 常用的硬质合金有哪几类?如何选用?2—6 怎样划分切削变形区?第一变形区有哪些变形特点?2-7 什么是积屑瘤?它对加工过程有什么影响?如何控制积屑瘤的产生? 2-8 试述影响切削变形的主要因素及影响规律.2—9 常用的切屑形态有哪几种?它们一般都在什么情况下生成?怎样对切屑形态进行控制?2—10 切削力为什么要分解为三个分力?各分力的大小对加工过程有什么影响?2-11 在CA6140型车床上车削外圆,已知:工件材料为灰铸铁,其牌号为HT200;刀具材料为硬质合金,其牌号为YG6;刀具几何参数为:0010=γ, 10,10,45,8''00-=====s r r k k λαα(s λ对三向切削分力的修正系数分别为75.0,5.1,0.1===f s p S C s F F F k k k λλλ),mm r 5.0=ε;切削用量为:min /80,/4.0,3m v r mm f mm c p ===α。
机械制造技术基础(第2版)课后习题答案

《机械制造技术基础》部分习题参考解答第五章工艺规程设计5-1 什么是工艺过程?什么是工艺规程?答:工艺过程——零件进行加工的过程叫工艺过程;工艺规程——记录合理工艺过程有关内容的文件叫工艺规程,工艺规程是依据科学理论、总结技术人员的实践经验制定出来的。
5-2 试简述工艺规程的设计原则、设计内容及设计步骤。
5-3 拟定工艺路线需完成哪些工作?5-4试简述粗、精基准的选择原则,为什么同一尺长方向上粗基准通常只允许用一次?答:粗、精基准的选择原则详见教材P212-214。
粗基准通常只允许用一次的原因是:粗基准一般是毛面,第一次作为基准加工的表面,第二次再作基准势必会产生不必要的误差。
5-5加工习题5-5图所示零件,其粗、精基准应如何选择(标有 符号的为加工面,其余为非加工面)?习题5-5图a)、b)、c)所示零件要求内外圆同轴,端面与孔轴线垂直,非加工面与加工面间尽可能保持壁厚均匀;习题5-5图d)所示零件毛坯孔已铸出,要求孔加工余量尽可能均匀。
习题5-5图解:按题目要求,粗、精基准选择如下图所示。
5-6为什么机械加工过程一般都要划分为若干阶段进行?答:机械加工过程一般要划分为粗加工阶段、半精加工阶段、精加工阶段和光整加工阶段。
其目的是保证零件加工质量,有利于及早发现毛坯缺陷并得到及时处理,有利于合理使用机床设备。
5-7 试简述按工序集中原则、工序分散原则组织工艺过程的工艺特征,各用于什么场合?5-8什么是加工余量、工序余量和总余量?答:加工余量——毛坯上留作加工用的材料层;工序余量——上道工序和本工序尺寸的差值;总余量——某一表面毛坯与零件设计尺寸之间的差值。
5-9 试分析影响工序余量的因素,为什么在计算本工序加工余量时必须考虑本工序装夹误差和上工序制造公差的影响?5-10习题5-10图所示尺寸链中(图中A0、B0、C0、D0是封闭环),哪些组成环是增环?那些组成环是减环?习题5-10图解:如图a),A0是封闭环,A1, A2, A4, A5, A7, A8是增环,其余均为减环。
第五章 中试放大与生产工艺
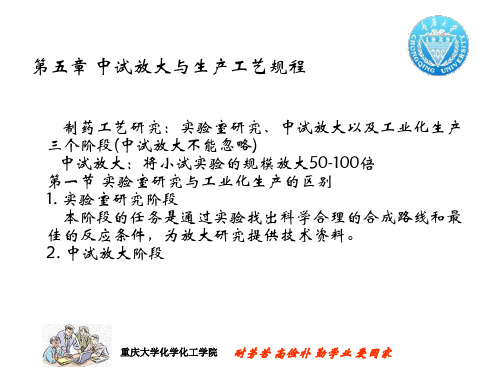
▲副产品和三废的回收、综合利用及处理问题在中试 阶段不可能全部解决。
重庆大学化学化工学院 耐劳苦 尚俭朴 勤学业 爱国家
第二节 放大试验的基本概念和方法
中试放大的方法有逐级经验放大法、相似放大法和 数学模拟放大法。 1.相关概念
重庆大学化学化工学院 耐劳苦 尚俭朴 勤学业 爱国家
什么是中试放大?
采用金属或玻璃制造的小型工业器械.应用工业级原料, 按照实验室最佳工艺条件进行操作。通过一系列的实验研 究之后,可以核对、校正和补充实验室获得的数据。
▲为什么要进行中试放大 G.E.Davis(第一部《化学工程手册》的作者)指出:
与原体第之间的存在一定的相似性进行放大。 ⑵相似理论 几何相似:几何相似要求两个大小不同体系的对应
尺寸具有比例性。 运动相似:运动相似要求具有时间的比例性,即在
几何相似的两体系中,各对应点的运动速率相同。 动力相似:动力相似要求具有力的比例性,即在几
何相似的两体系中,各对应点承受的作用力相同。 热相似:热相似要求在几何相似的两体系间,各对
“在实验室中几克物料的小实验,对于指导大型工厂 的建设工作并没有什么作用。但用数公斤物料进行的 试验,则无疑可提供大型工厂需要的全部数据。” 可 见,工业化设计工作要在一定规模的完整试验基础上 才能进行。
重庆大学化学化工学院 耐劳苦 尚俭朴 勤学业 爱国家
确定工艺路结后,每步化学合成反应或生物合成反应 一般不会因小试、中试放大和大型生产条件不同而有明 显变化,但各步最佳工艺条件,则随试验规模和设备等 外部条件的不同而有可能需要调整。这是因为:
4.化学反应工程理论指导放大 化学反应工程理论指出,“放大效应”的主要原因
《机械制造基础》第5章 机械加工工艺规程的制定

河南科技大学教案首页课程名称机械制造基础任课教师邓效忠第五章机械加工工艺规程的制定计划学时14教学的目的和要求:要求学生掌握定位基准和表面加工方法的选择原则,能够拟定工艺路线,会运用工艺尺寸链确定工序尺寸及其公差,使学生具有编制中等复杂零件加工工艺规程的能力。
重点:工件定位基准的选择;工序顺序的确定;工艺尺寸链及其应用。
难点:工艺尺寸链及其应用。
思考题:1.什么叫基准?基准分哪儿种?2.精、粗定位基准的选择原则各有哪些?如何分析这些原则之间出现的矛盾?3.零件表面加工方法的选择原则是什么?4.制定机械加工工艺规程时,为什么要划分加工阶段?5.切削加工顺序安排的原则是什么?6.什么叫工序集中?什么叫工序分散?各用于什么场合?7.什么叫工序余量?影响工序余量的因素是什么?8.什么叫尺寸链?它具有哪些特征?9.什么叫工艺规程?它有什么作用?10.如何确定尺寸链中的增环、减环和封闭环?第5章机械加工工艺规程设计5.1 概述一、机械加工工艺规程及其作用将产品或零部件的制造工艺过程的所有内容用图、表、文字的形式规定下来的工艺文件汇编称为工艺规程。
二、工艺规程设计所需的原始资料⑴零件图和产品整套装配图;⑵产品的生产纲领和生产类型;⑶产品的质量验收标准;⑷毛坯情况;⑸本厂的生产条件和技术水平;⑹国内外生产技术发展情况。
三、工艺规程设计的步骤⑴零件的工艺性分析。
⑵确定毛坯。
⑶拟定工艺路线,选择定位基准。
⑷确定各工序的设备和工装。
⑸确定主要工序的生产技术要求和质量验收标准。
⑹确定各工序的余量,计算工序尺寸和公差。
⑺确定各工序的切削用量。
⑻确定工时定额。
⑼填写工艺卡。
5.2 机械加工工艺规程设计一、零件的结构工艺性分析结构工艺性是指产品的结构是否满足优质、高产、低成本制造的一种性质。
零件结构工艺性举见教材表5-4。
二、确定毛坯三、定位基准的选择粗基准是指未经机械加工的定位基准,而精基准则是经过机械加工的定位基准。
1.粗基准的选择原则粗基准选择的主要目的是:保证非加工面与加工面的位置关系;保证各加工表面余量的合理分配。
第五章 机械加工工艺规程制定
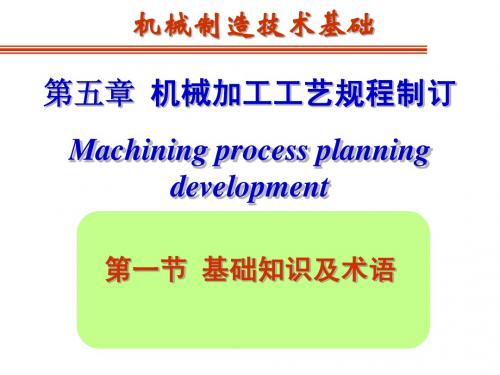
第一节 基础知识及术语
一、生产过程和工艺过程 生产过程 在机械产品制造中,将 原材料(或半成品)转变为成 品的全过程。
第一节 基础知识及术语
工艺过程 在生产过程中,毛坯的制造、零件的机械加工与热处理、 产品的装配等工作将直接改变生产对象的采用形状、尺寸、 相对位置和性质等,使其成为成品和半成品的过程。 主要内容 毛坯和零件成形——铸造、锻压、冲压、 毛坯和零件成形——铸造、锻压、冲压、焊接 、压制、烧结、 压制、烧结、 注塑、 注塑、压塑 … 机械加工——切削、磨削、 机械加工——切削、磨削、特种加工 材料改性与处理——热处理、电镀、转化膜、涂装、 材料改性与处理——热处理、电镀、转化膜、涂装、热喷涂 … 机械装配——把零件按一定的关系和要求连接在一起, 机械装配——把零件按一定的关系和要求连接在一起,组合成 部件和整台机械产品, 包括零件的固定、 连接、 调整、 平衡、 部件和整台机械产品 ,包括零件的固定、 连接、 调整、 平衡 、 检 验和试验等工作
第一节 基础知识及术语
获得尺寸精度的方法 试切法 试切—测量—调整—再试切,反复进行直到被加工 尺寸(工序尺寸)达到要求精度为止的加工方法。 调整法 在机床上先调整好刀具和工件在工序尺寸方向上的 相对位置,并在一批工件的加工过程中保持这个位置不变,以 保证工件工序尺寸精度的方法。 定尺寸刀具法 用刀具的相对尺寸来保证工件被加工部位工 序尺寸的方法。 主动测量法 在加工过程中,利用自动测量装置边加工边测 量加工尺寸,并将测量结果与要保证的工序尺寸比较后,或使 机床继续工作,或使机床停止工作的方法。 自动控制法 在加工过程中,利用测量装置或数控装置等自 动控制加工过程的加工方法。
尺寸链例题#(精选.)

第五章 工艺规程设计例1:图示零件,2面设计尺寸为 2522.00 +mm ,尺寸60012.0-mm 已经保证,现以1面定位用调整法精铣2面,试计算工序尺寸。
解:(1)建立尺寸链设计尺寸2522.00 +mm 是间接保证的,是封闭环,A 1(60012.0-mm )和A 2为组成环。
(2)计算根据 A 0=∑=m i i A 1-∑-+=11n m i i A A 2 = A 1-A 0=35ES 0=∑=mi i ES 1-∑-+=11n m i i EI EI 2=ES 1-ES 0=-0.22 EI 0=∑=mi i EI 1-∑-+=11n m i i ES ES 2=EI 1-EI 0=-0.12则:工序尺寸A 2=3512.022.0--=34.88010.0-mm 。
例2:下图所示工件外圆、内孔及端面均已加工完毕,本序加工A 面,保证设计尺寸8±0.1 mm 。
由于不便测量,现已B面作为测量基准,试求测量尺寸及其偏差。
解:(1)建立尺寸链设计尺寸8±0.1是mm 是封闭环,A 1、A 2、A 3是组成环。
(2)计算根据 A 0=∑=m i i A 1-∑-+=11n m i i AA 1 = A 0-A 2+A 3=18ES 0=∑=m i i ES 1-∑-+=11n m i i EI ES 1=ES 0-ES 2+EI 3=0EI 0=∑=mi i EI 1-∑-+=11n m i i ES EI 1=EI 0-EI 2+ES 3=-0.05 则:测量尺寸A 1=180 05.0-=17.9505.00 + mm 。
例3:一带有键槽的内孔要淬火及磨削,其设计尺寸如图所示。
保证键槽尺寸034 0436..+ mm 的有关工艺过程如下: 1)镗内孔至中01 0396..ϕ+(005 0198.R .+)mm ; 2)插键槽至尺寸A 1;3)淬火(变形忽略不计);4)磨内孔,同时保证内孔直径005 040.ϕ+(0025 020.R +)mm 和键槽深度 034 0436..+mm 两个设计尺寸的要求。
机械制造工艺学12篇

第一章 导 论 第二章 机床夹具设计基础 第三章 切削过程及控制 第四章 机械加工质量分析与控制 第五章 工艺规程设计
第1章 导论
一、机械制造业在国民经济中的地位和作用; 二、机械制造工艺学的定义、内容及特点; 三、先进制造技术的特点及发展趋势; 四、课程性质与学习要求。
一、机械制造业在国民经济中的地位和作用
2)传统制造技术主要着眼点是实现生 产的优质、高效和低成 本,而发展先进制造技术的目的除了实现优质、高效、的成本 外,敏捷制造、可持续发展也成为其追求的重要目标。
3)先进制造技术比传统制造技术更加重视技术与管理的结合, 重视制造过程的组织和管理体制的精简及合理化,从而产生了 一系列技术与管理相结合的新的生产方式。
如下差距:
–工业生产能耗和物耗高。万元产品能耗是发达国家的5 倍,物耗高40% –劳动生产率低下,平均相当于发达国家的1/15~1/20。 –工业产品质量差,技术含量低,缺乏市场竞争力。基础 机械、大型成套设备等级比发达国家低1~2个等级,综合 技术水平落后20余年。 –企业研发投入不足,自主创新能力差。企业投入的科研 经费不到发达国家的1/30。
机械制造是将设计输出的指令和信息输入机械制造系统, 加工出合乎设计要求的产品的过程。
机械制造工艺学(machinery technology)
定义1:是研究机械制造系统、机械制造过程和制造手段的 科学。
定义2:是研究集机械、电子、光学、信息科学、材料科学、 生物科学、激光学、管理学等最新成就为一体的一个新兴技 术与新兴工业,归纳总结机械制造工艺的科学理论与实践, 探索解决工艺过程中遇到的实际问题,从而揭示出一般规律 的一门科学。
1. 先进制造技术的内涵及其主要特点 先进制造技术是传统制造业不断吸收机械、电子、信息、
汽车制造工艺学习题答案作者曾东建贺曙新徐雳石美玉第五章机械加工工艺规程的制定

3.调整卡片 调整卡片是对自动、半自动机床或某些齿轮加工机床等进行调 整用的一种工艺文件。表5—3为调整卡片的一种格式。
4.检验工序卡片 检验工序卡片是检验人员使用的文件。其中列有检验内容、 使用的设备及量检具等,其格式如表5—4所示。
5.机械加工工序操作指导卡 机械加工工序操作指导卡是随着汽车零件加工质量要求不断 提高而出现的一种文件。在一些加工质量重要控制点上,通常 由它来代替工序卡片。机械加工工序操作指导卡,在传统工序 卡片的基础上,另外规定了操作规范及工序质量控制内容。操 作规范要为工人规定规范的操作动作,还要规定机床的工作状 态,规定每个尺寸及形位精度的测量方法等。工序质量控制的 内容包括控制项目、工艺要求、所用量具、自检频次、管理手 段、重要度等级等内容。其格式见表5—5。
五、工序的集中与分散
选定了一个零件的加工工艺方案,并划分了加工阶段之后,在一定条件下, 可以根据零件加工的工艺特点和生产加工过程组织方式,使零件加工工序的 数目不同。这种不同,正是应用工序集中与工序分散两种不同的原则,对工 序进行不同的组合来实现的。
所谓工序分散,就是将零件的加工分散在较多的工序内完成。其工艺特点 为:每道工序所包含的加工内容较少,工序数目较多,工艺路线长;每道工 序的工装夹具比较简单,调整、维护方便,生产准备工作量少;涉及的设备 数量、种类较多,操作人员需求量大,生产占用面积广。
图5-7 外圆表面加工流程框图
2.孔的加工
图5-8 孔加工流程框图
3.平面加工
图5-9 平面加工流程框图
三、 加工阶段的划分 (一)加工阶段划分原则
(1)粗加工阶段 主要任务是除去大部分多余的金属层,使半成 品零件从形状和尺寸上尽量接近成品的形状和设计图样的尺寸 的要求,以提高零件生产率。 (2)半精加工阶段 为精加工做准备,以及满足设计图样中零件 的部分精度要求。 (3)精加工阶段 保证零件加工后,各主要表面达到产品设计图 样规定的精度要求,最终获得零件设计图所需要的表面质量、 设计尺寸和规定的技术要求。 (4)光整加工阶段 对于精度要求特别高,表面粗糙度值特别小 的表面,通过光整加工进一步提高精度,改善表面质量。
机械制造技术基础(第2版)第五章课后习题答案
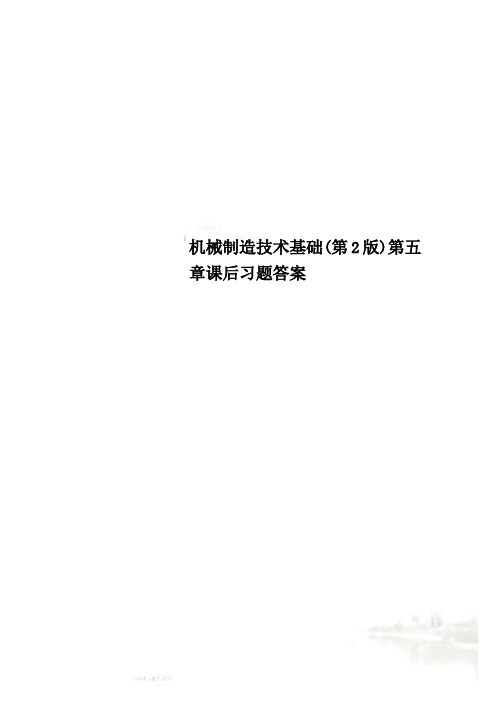
机械制造技术基础(第2版)第五章课后习题答案《机械制造技术基础》部分习题参考解答第五章工艺规程设计5-1 什么是工艺过程?什么是工艺规程?答:工艺过程——零件进行加工的过程叫工艺过程;工艺规程——记录合理工艺过程有关内容的文件叫工艺规程,工艺规程是依据科学理论、总结技术人员的实践经验制定出来的。
5-2 试简述工艺规程的设计原则、设计内容及设计步骤。
5-3 拟定工艺路线需完成哪些工作?5-4试简述粗、精基准的选择原则,为什么同一尺长方向上粗基准通常只允许用一次?答:粗、精基准的选择原则详见教材P212-214。
粗基准通常只允许用一次的原因是:粗基准一般是毛面,第一次作为基准加工的表面,第二次再作基准势必会产生不必要的误差。
5-5加工习题5-5图所示零件,其粗、精基准应如何选择(标有 符号的为加工面,其余为非加工面)?习题5-5图a)、b)、c)所示零件要求内外圆同轴,端面与孔轴线垂直,非加工面与加工面间尽可能保持壁厚均匀;习题5-5图d)所示零件毛坯孔已铸出,要求孔加工余量尽可能均匀。
习题5-5图解:按题目要求,粗、精基准选择如下图所示。
5-6 为什么机械加工过程一般都要划分为若干阶段进行?答:机械加工过程一般要划分为粗加工阶段、半精加工阶段、精加工阶段和光整加工阶段。
其目的是保证零件加工质量,有利于及早发现毛坯缺陷并得到及时处理,有利于合理使用机床设备。
5-7 试简述按工序集中原则、工序分散原则组织工艺过程的工艺特征,各用于什么场合?5-8什么是加工余量、工序余量和总余量?答:加工余量——毛坯上留作加工用的材料层;工序余量——上道工序和本工序尺寸的差值;总余量——某一表面毛坯与零件设计尺寸之间的差值。
5-9 试分析影响工序余量的因素,为什么在计算本工序加工余量时必须考虑本工序装夹误差和上工序制造公差的影响?5-10习题5-10图所示尺寸链中(图中A0、B0、C0、D0是封闭环),哪些组成环是增环?那些组成环是减环?习题5-10图解:如图a),A0是封闭环,A1, A2, A4, A5, A7, A8是增环,其余均为减环。
第五章 中试放大与生产工艺规程
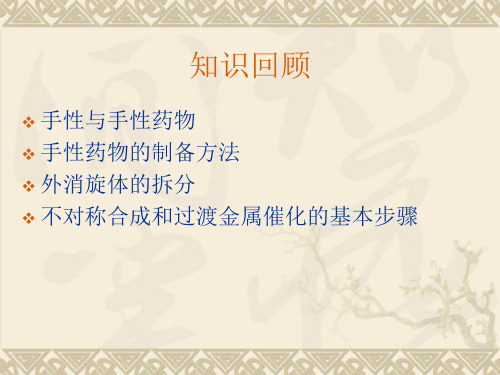
4.反应条件的进一步研究 前已提及,实验室阶段获得的最佳反应条件不一 定能全符合中试放大要求。为此,应该针对主要的影 响因素, 如放热反应中的加料速度,反应罐的传热面 积与传热系,以及冷却剂等因素进行深入的研究,掌 握它们在中试装置中的变化规律,从而得到更合适的 反应条件。
维生素C的生产工艺
曲克芦丁主要成分的生产工艺
磺胺索嘧啶的合成
第二节 物料平衡
物料平衡指产品理论产量与实际产量或物料的理论 用量与实际用量之间的比较。 通过物料平衡计算,得到进入与离开某一过程或设 备的各种物料的数量、组分以及组分的含量,即产 品的质量、原辅材料消耗量、副产物量、“三废” 排放量,水、电、蒸汽消耗量等。 这些指标与操作参数有密切关系。操作参数的最佳 选择、操作人员的操作技术以及管理水平决定了这 些基本指标的优劣,或者说这些基本指标的优劣是 制药工艺优化程度、操作技艺和管理水平的综合反 映。
确定工艺路线后,每步化学合成反应或生物合成 反应一般不会因小试验、中试放大和大型生产的条件 不同而有明显变化,但各步的最佳工艺条件,则随试 验规模和设备等外部条件的变化而有所不同。如果把 实验室里使用玻璃仪器条件下所获得的最佳工艺条件 原封不动地搬到工业生产中去,常常会出现下列结果: 收率低于小规模实验收率,甚至得不到产品;产品质 量不合格;发生溢料或爆炸等安全事故以及其它不良 后果。
第五章 中试放大与生产工艺规程
第一节 中试放大 第二节 物料平衡 第三节 生产工艺规程
化学制药工业利用化工原料或自然界中的天然 物质,通过化学合成及生物合成等方法,制备化学 结构明确,具有治疗、诊断、预防疾病或改善人体 机能等作用的产品,这种由原料到成品之间若干个 相互联系的劳动过程的总和称为生产过程,生产过 程还包括对原辅材料、中间体和成品的质量监控等。 根据生产工序的繁杂程度,生产规模的大小,一个 药品的生产过程可分为若干个生产岗位。
- 1、下载文档前请自行甄别文档内容的完整性,平台不提供额外的编辑、内容补充、找答案等附加服务。
- 2、"仅部分预览"的文档,不可在线预览部分如存在完整性等问题,可反馈申请退款(可完整预览的文档不适用该条件!)。
- 3、如文档侵犯您的权益,请联系客服反馈,我们会尽快为您处理(人工客服工作时间:9:00-18:30)。
第五章工艺规程设计(2天津科技大学机械工程学院主讲:王平第三节成组加工工艺规程设计一、概述●成组技术是利用事物之间的相似性,将许多具有相似信息的研究对象归并成组,并用大致相同的方法来解决这一组研究对象的设计和制造问题;应用成组技术组织生产,可以扩大同类零件的生产数量,故能用大批量生产方式组织中小批量产品的生产。
●成组技术起源与20世纪50年代,现在其应用已遍及产品设计、制造加工和生产管理等诸多领域。
二、零件的分类编码●零件编码就是用数字表示零件的特征,代表零件特征的每一个数字成为特征码。
●目前世界上已有几十种分类编码系统。
●我国1984年制定了“机械零件编码系统(简称JLBM-1系统”。
●该系统由名称类别码、形状及加工码和辅助码共15个码位组成。
●如图5-32和表5-8、表5-9、表5-10、表5-11、表5-12.三、成组加工工艺规程设计1.为产品零件划分零件组(1特征码位法(2码域法(3特征位码域法2.为零件组编制成组加工工艺规程(1综合零件法(2综合工艺路线法第四节计算机辅助机械加工工艺规程设计一、计算机辅助工艺规程设计方法1. 派生法在成组工艺基础上,将编码相同或相近的零件组成成零件组,然后使用综合零件法,为每一组零件制定成组工艺规程,存储在数据库中;具体应用时,调出该工艺规程进行编辑修改即可。
如图5-36所示。
2. 创成法它根据输入零件的图形和信息,按存储在计算机内的工艺决策算法和逻辑推理方法,从无到有地生成零件的工艺规程。
3.综合法是一种以派生法为主、创成法为辅的工艺规程设计方法,兼取两者之长。
二、派生法计算机辅助工艺规程设计原理1.工艺信息数字化(1零件编码矩阵化(2零件组特征矩阵化(3综合零件的设计●(4零件上各种形面的数字化●(5工序工步名称编码●(6综合加工工艺路线的数字化●(7工序工步内容矩阵2.计算机辅助工艺规程设计系统数据库●(1特征矩阵文件●(2综合工艺路线●(3工序、工步文件●(4工艺数据文件3.计算机辅助工艺规程设计第五节机器装配工艺规程设计一、概述1.机器装配与装配工艺系统图●装配——按照规定的技术要求,将零件或部件进行配合和联接,使之成为半成品或成品的过程。
●零件是组成机器的最小单元。
●套/合件是在基准零件上装上一个或若干个零件构成的。
●组件是在基准件上,装上若于个零件和套件构成的,为此而进行的装配工件称为组装。
●部件是在基准件上装上若干个组件、套件和零件构成的,为此而进行的装配工作称为部装。
●机器则是在基准件上,装上若干部件、组件、套件和零件构成的,为此而进行的装配工作称为总装。
2.装配精度与装配尺寸链●机器由零、部件组装而成,机器的装配精度与零、部件制造精度直接有关。
可以从查找影响此项装配精度的有关尺寸入手,建立以此项装配要求为封闭环的装配尺寸链。
●在根据机器装配精度要求来设计机器零、部件尺寸及其精度时,必须考虑装配方法的影响,装配方法不同,解算装配尺寸链的方法截然不同,所得结果差异甚大。
对于某一给定的机器结构,设计师可以根据装配精度要求和所采用的装配方法,通过解算装配尺寸链来确定零、部件有关尺寸的精度等级和极限偏差。
二、保证装配精度的四种装配方法(一互换装配法●采用互换法装配时,被装配的每一个零件不需作任何挑选、修配和调整就能达到规定的装配精度要求。
1.完全互换装配法●优点:装配质量稳定可靠;装配过程简单,装配效率高;易于实现自动装配;产品维修方便。
●缺点:当装配精度要求较高,尤其是在组成环数较多时,组成环的制造公差规定得严,零件制造困难,加工成本高。
例5-4:如图5-47.2.统计互换装配法●又称不完全互换装配法,其实质是将组成环的制造公差适当放大,使零件容易加工,这会使极少数产品的装配精度超出规定要求,但这是小概率事件,很少发生人从总的经济效果分析,仍然是经济可行的。
●优点:与完全互换法装配相比,组成环的制造公差较大,零件制造成本低;装配过程简单,生产效率高。
●缺点:装配后有极少数产品达不到规定的装配精度要求,须采取相应的返修措施。
●适于在大批大量生产中装配那些装配精度要求较高且组成环数又多的机器结构。
●见例5-5,P264.(二分组装配法●采用分组装配法装配时,组成环仍按加工经济精度制造,不同的是要对组成环的实际尺寸逐一进行测量并按尺寸大小分组,装配时被装零件按对应组号配对装配,达到规定的装配精度要求。
●优点:零件的制造精度不很高,但却可获得很高的装配精度;组内零件可以互换,装配效率高。
●缺点:额外增加了零件测量、分组和存贮的工作量。
分组装配法适于在大批大量生产中装配那些组成环数少而装配精度又要求特别高的机器结构。
具体方法:●(1将组成环制造公差同向放大3~5倍;●(2组成环零件加工好后进行精密测量;●(3将测量的零件分成3~5组,并以颜色标记;●(4对应的分组进行装配,即大销配大孔,小销配小孔。
发动机活塞销和活塞的装配常采用分组装配法。
(三修配装配法●采用修配法装配时,各组成环均按加工经济精度加工,装配时封闭环所积累的误差通过修配装配尺寸链中某一组成环尺寸(此组成环称为修配环的办法,达到规定的装配精度要求。
为减少修配工作量,应选择那些便于进行修配(装拆方便,修刮面小的组成环作修配环。
●优点:组成环均能以加工经济精度制造,但却可获得较高的装配精度。
●缺点:增加了修配工作量,生产效率低,对装配工人技术水平要求高。
●修配装配法常用于单件小批生产中装配那些组成环数较多而装配精度又要求较高的机器结构。
修配法例题,例5-6:(四调整装配法装配时用改变调整件在机器结构中的相对位置或选用合适的调整件来达到装配精度的装配方法,称为调整装配法。
1.可动调整法优点:组成环的制造精度虽不高,但却可获得比较高的装配精度;在机器使用中可随时通过调节调整件的相对位置来补偿由于磨损、热变形等原因引起的误差,使之恢复到原来的装配精度;它比修配法操作简便,易于实现。
缺点:需增加一套调整机构,增加了结构复杂程度。
可动调整装配法在生产中应用甚广。
2.固定调整法●在以装配精度要求为封闭环建立的装配尺寸链中,组成环均按加工经济精度制造,由于扩大组成环制造公差带来的封闭环尺寸变动范围超差,可通过更换不同尺寸的固定调整环进行补偿,最终达到装配精度要求;该方法,称为固定调整装配方法。
●固定调整装配方法适于在大批大量生产中装配那些装配精度要求较高的机器结构。
在产量大、装配精度要求较高的场合,调整件还可以采用多件拼合的方式组成。
●这种调整装配方法比较灵活,它在汽车、拖拉机生产中广泛应用。
例5-7 固定调整法的应用3.误差抵消调整法●在机器装配中,通过调整被装零件的相对位置,使误差相互抵消,可以提高装配精度,这种装配方法称为误差抵消调整法。
●调整装配法的主要优点:组成环均能以加工经济精度制造,但却可获得较高的装配精度;装配效率比修配装配法高。
●不足之处是要另外增加一套调整装置。
●可动调整法和误差抵消调整法适于在成批生产中应用,固定调整法则主要用于大批量生产。
三、装配工艺规程设计1.研究产品装配图和装配技术条件2.确定装配的组织形式(1 固定式装配●全部装配工作都在固定工作地进行,这种装配方式称作固定式装配。
●固定式装配又可分为集中式固定装配和分散式固定装配。
(2 移动式装配●被装配产品(或部件不断地从一个工作地移动到另一个工作地,每个工作地重复地完成某一固定的装配工作,这种装配方式称作移动式装配。
移动式装配又有自由移动式和强制移动式两种。
3.划分装配单元,确定装配顺序,绘制装配工艺系统图●在划分装配单元确定装配基准件之后即可编排装配顺序,并以装配工艺系统图的形式表示出来。
编排装配顺序的原则是:先下后上,先内后外,先难后易,先精密后一般。
4.划分装配工序,进行工序设计●划分装配工序,进行工序设计的主要任务是:●1划分装配工序,确定工序内容;●2确定各工序所需设备及工具,如需专用夹具与设备,须提交设计任务书;●3制订各工序装配操作规范,例如过盈配合的压人力、装配温度、拧紧固件的额定扭矩等;●4规定装配质量要求与检验方法;●5确定时间定额,平衡各工序的装配节拍。
5.编制装配工艺文件●单件小批生产中,通常只绘制装配工艺系统图,装配时按产品装配图及装配工艺系统图规定的装配顺序进行;●成批生产中,通常还要编制部装、总装工艺卡,按工序标明工序工作内容、设备名称、工夹具名称与编号、工人技术等级、时间定额等;●在大批量生产中,不仅要编制装配工艺卡,还要编制装配工序卡,用它指导工人做装配工作。
此外,还应按产品装配要求,制订检验卡、试验卡等工艺文件。
第六节机械产品设计的工艺性评价一、概述●机械产品设计除了应满足产品使用性能外,还应满足制造工艺的要求,否则就有可能影响产品生产效率和产品成本,严重时甚至无法生产。
●机械产品设计的工艺性评价——就是评价所设计的产品在满足使用要求的前提下制造、维修的可行性和经济性。
这里所说的经济性是一个含意宽广的术语,它应是材料消耗要少。
制造劳动要少、生产效率要高和生产成本要低的综合。
●对机械产品设计进行工艺性评价须与具体生产条件相联系,如图5-55所示。
二、机械产品设计的机械加工工艺性评价1.零件结构要素必须符合标准规定●零件结构要素螺纹、花键、齿轮、中心孔、空刀槽等的结构和尺寸都应符合国家标准规定。
零件结构要素标准化了,不仅可以简化设计工作,而且可以使用标准的和通用的工艺装备,缩短零件的生产准备周期,可以降低生产成本。
2.尽量采用标准件和通用件●设计产品时应尽量选用标准件和通用件,上述两类零件在产品中所占的比例是评定产品设计标准化程度的一个重要指标。
●标准化系数A :100%B T A J+=⨯∑∑∑3.在满足产品使用性能的条件下,零件图上标注的尺寸精度等级和表面粗糙度要求应取经济值●尺寸公差规定过严,表面粗糙度值规定过小,必然会无谓地增加产品制造成本。
●在没有特殊要求的情况下,表面粗糙度值应与该表面加工精度等级相对应。
4.尽量选用切削加工性好的材料●材料的切削加工性——指在一定生产条件下,该材料切削加工的难易程度。
●材料强度高,切削力大、切削温度高、刀具磨损快、切削加工性差;材料强度相同时,塑性较大的材料由于加工变形和硬化程度较大、切削力大、切削温度高、刀具磨损快,切削加工性差;●在钢材中适当添加磷、硫等元素,可以降低钢的塑性,可提高钢的切削加工性。
5.零件上有便于装夹的定位基面和夹紧面●在设计零件图时,须充分考虑零件加工时可能采用的定位基面和夹紧面,应尽量选用在夹具中能够进行稳定定位的表面作设计基准。
如果零件上没有合适的设计基准、装配基准能作定位基面,应考虑设置辅助基面。
辅助基面应标注相应的尺寸公差、形位公差和表面粗糙度值。
6.保证能以较高的生产率加工●(1被加工表面形状应尽量简单●(2尽量减少加工面积●(3尽量减少加工过程的装夹次数●(4尽量减少工作行程次数7.保证刀具能正常工作8.加工时工件应有足够的刚性加工时,工件要承受切削力和夹紧力的作用,工件刚性不足易产生变形,影响加工精度。