输液瓶橡胶盖注射模具设计说明
(数控模具设计)输液瓶橡胶盖注射模具设计精编

(数控模具设计)输液瓶橡胶盖注射模具设计1引言1.1概述输液瓶盖由于使用的需要,都采用橡胶制成,能够保证玻璃瓶内液体药品的密封。
目前市场上输液瓶橡胶塞都是用丁基橡胶,尤其是卤化丁基橡胶。
丁基橡胶(异丁烯—异戊二烯共聚物,即2-甲基-1-丙烯和2-甲基-1,3-丁二烯共聚物)是使用三氯化铝作催化剂将异丁烯和1%-3%的异戊二烯在-100℃下共聚制备的[1]。
溴化丁基橡胶除了保持了丁基橡胶原有的低透气性,高衰减性,耐老化性,耐天侯性,耐臭氧性及耐化学药品性等特性外,仍增添了普通丁基橡胶所不具备的以下特性[2]:(1)硫化速度快;(2)和天然像胶,丁苯橡胶的相容性能好;(3)和天然橡胶,丁苯橡胶的粘接性能提高;(4)可单独用氧化锌硫化,硫化方式多样化;(5)有较好的耐热性。
丁基橡胶是生产引用瓶塞的理想材料[3]。
1.2国内外对异戊橡胶的研究医用胶塞丁基化是国内HIIR的第二大需求市场,为保证医药安全,国家医药主管部门规定国内所有药用胶塞壹律停止使用普通天然橡胶瓶塞。
医用胶塞生产厂商正在扩大丁基橡胶瓶塞生产能力,主要是用卤化丁基橡胶,以适应国内需要。
溴化丁基橡胶由于硫化速度快、硫化效率高、硫化程度高、硫化剂用量少、可实现无硫无锌硫化等特点,从而赋予了溴化丁基橡胶瓶塞良好的物理性能和化学性能,使其具有良好的吸湿性,在冷冻干燥制品中应用较好。
对于低分子量的凝血酶抑制溶液,用溴化丁基橡胶胶塞其稳定性显著提高;同时其化学指标可控制在壹个较好的范围内,进而有力保证了和氨基酸、血液制品等大输液产品的相容性。
欧美国家的丁基胶塞厂家多数采用溴化丁基橡胶,目前我国也有壹些X公司全部使用溴化丁基橡胶生产胶塞。
目前国内较大的生产线有10多条,总生产能力达100亿只之上[4]。
合成丁基橡胶和卤化丁基橡胶的工艺路线目前有低温淤浆工艺和溶液法工艺。
低温淤浆工艺是最早开发的合成丁基橡胶的工艺,壹般是以氯甲烷作聚合介质,三氯化铝作引发剂,反应温度控制在-100-90℃。
【毕业设计论文】瓶盖注射模设计-毕业设计说明书[1][1]【有对应的CAD图】
![【毕业设计论文】瓶盖注射模设计-毕业设计说明书[1][1]【有对应的CAD图】](https://img.taocdn.com/s3/m/5cfc08b9b1717fd5360cba1aa8114431b90d8e4b.png)
毕业设计题目瓶盖塑模设计说明书目录一、 塑件的分析…………………………………………… (1)二、 塑件的形状尺寸………………………………………… (2)三、 形腔数目的决定及排布………………………………… (3)四、 分型面的选择…………………………………………… (4)五、 浇注系统的设计………………………………………… (5)六、 注射机的型号和规格校核…………………………… (6)七、 成型零部件的工作尺寸计算…………………………… (7)八、 导柱导向机构的设计………………………………… (11)九、 推出机构的设计…………………………………… (13)十、 温控系统的设计………………………………… (14)十一、设计小结………………………………………… (16)十二、参考文献………………………………………… (16)共 16 页第1页第一部分塑料PSPS:聚苯乙烯一、基本特性:聚苯乙烯无色透明、无毒无味。
落地有清脆的金属声、密度为1.054g/cm。
聚苯乙烯的力学性能与聚合方法、相对分子质量大小、定向度和质量有关,相对分子质量越大机械强度越高。
它有优良的电性能(尤其是高频绝缘性能)和一定的化学稳定性。
它能耐碱、硫酸、磷酸、10%-30%的盐酸、稀醋酸及其他的有机酸。
但不耐硝酸及氧化剂的作用,对水、乙醇、汽油、植物油及各种盐溶液也有足够的抗蚀能力。
但耐热性能低,热变形温度一般在70-80度,只能在不高的温度下作用。
主要用途: 在工业中做仪表、灯罩、化学仪器、零件、透明模型等。
在电器方面做良好的绝缘材料、接线盒电池盒等。
在日用品方面广泛的用于包装材料、各种容器、玩具等。
成型特性: 1.无定形料、吸湿性小,不易分解,性脆易裂,热膨胀系数大,易产生应力开裂。
2.流动性能较好,溢边值0.03mm左右。
3.塑件壁后均匀,不宜有镶件,缺口,尖角,各方面应圆滑连接。
4.可用螺杆或柱塞式注射机加工,喷嘴可用直通式或自锁式。
瓶盖注射模具设计
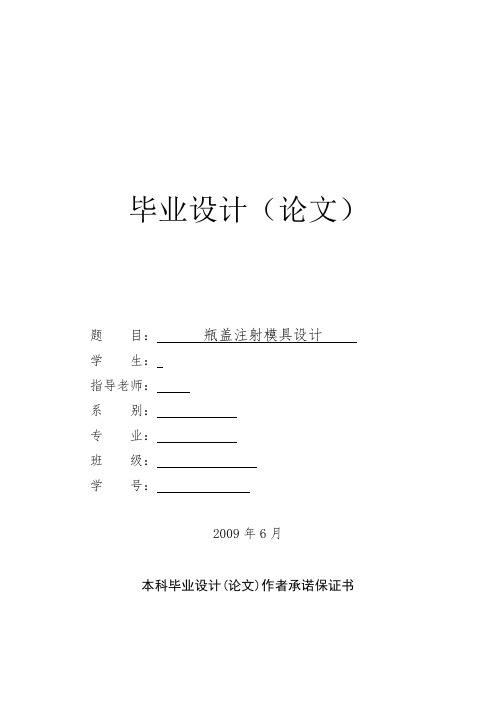
毕业设计(论文)题目:瓶盖注射模具设计学生:指导老师:系别:专业:班级:学号:2009年6月本科毕业设计(论文)作者承诺保证书本人郑重承诺:本篇毕业设计(论文)的内容真实、可靠。
如果存在弄虚作假、抄袭的情况,本人愿承担全部责任。
学生签名:2009 年 6 月 1 日本科毕业设计(论文)指导教师承诺保证书本人郑重承诺:我已按有关规定对本篇毕业设计(论文)的选题与内容进行了指导和审核,该同学的毕业设计(论文)中未发现弄虚作假、抄袭的现象,本人愿承担指导教师的相关责任。
指导教师签名:年月日目录1概论 51.1课题的背景及意义 61.2 各种模具的分类和占有量错误!未定义书签。
1.3我国塑料模具技术的现状及发展趋势62注塑件的设计 82.1材料选择82.2结构设计92.2.1塑件结构分析92.2.2壁厚92.2.3脱模斜度92.2.4圆角92.3塑件的尺寸精度及表面质量102.3.1尺寸精度102.3.2塑件的表面质量103 注射成型的准备 103.1注射成型工艺简介103.2注射成型工艺条件113.3注射机的选择123.3.1注射机简介123.3.2注射机基本参数123.3.3选择注射机134 模具设计 144.1分型面的确定144.2型腔数目的确定及型腔的排列144.3浇口的确定154.4浇注系统的设计154.4.1主流道154.4.2分流道164.4.3冷料穴164.5型芯型腔结构的确定164.5.1螺纹型芯的结构设计164.6模架的确定164.6.1型腔壁厚和底板壁厚计算164.6.2模架的选用184.7注射机的校核194.7.1最大注射量的校核204.7.2锁模力的校核204.7.3喷嘴尺寸的校核204.7.4定位圈尺寸校核204.7.5模具外形尺寸校核204.7.6模具闭合高度校核204.8模具材料的选择214.9导向与定位机构214.10推出机构的设计224.11脱螺纹机构设计234.11.1链传动结构设计234.11.2齿轮的选用244.11.2按齿根强度校核254.12轴承的选用264.12.1轴承类型选择264.12.2滚动轴承的失效形式264.12.3滚动轴承的校核计算264.13成型零件工作尺寸的计算284.13.1型芯、型腔工作尺寸计算284.13.2螺纹型环工作尺寸的计算324.14排气设计334.15温度调节系统设计334.15.1模具温度对塑料制品质量的影响334.15.2对温度调节系统的要求334.15.3冷却系统设计345模具总装配图 35. 366 结果分析 366.1脱螺纹机构设计总结366.2洗洁精瓶盖塑料模具设计总结36致谢 37参考文献 38瓶盖注射模设计摘要:本次设计的零件为洗洁精瓶盖塑件属于小型塑件,其形状相对简单,生活中使用比较普遍,针对其成型特点设计了塑件结构及其注塑成型模具。
瓶盖注塑模具设计.ppt

瓶盖注塑模具设计1. 引言注塑模具是一种用于制造塑料制品的工具,常用于生产各种类型的瓶盖。
瓶盖注塑模具设计的目标是实现高效、精确和可靠的生产过程,以满足市场的需求。
本文档将介绍瓶盖注塑模具设计的关键要素,包括模具的结构、选材、制造工艺和检验方法等。
2. 模具设计要素在进行瓶盖注塑模具设计之前,需要考虑以下几个要素:2.1 瓶盖形状和尺寸瓶盖的形状和尺寸将直接影响到模具的设计。
设计师需要根据瓶盖的要求确定模具的尺寸和形状,包括瓶盖的直径、高度、壁厚等。
2.2 模具结构模具的结构决定了瓶盖的成型过程和质量。
常见的模具结构包括单腔模具、多腔模具和家模具等。
不同的模具结构会影响到注塑工艺和成本。
2.3 材料选用模具的选材是瓶盖注塑模具设计的重要环节。
常用的模具材料包括优质钢材和合金钢等。
合理选择材料能够提高模具的硬度、耐磨性和使用寿命。
2.4 模具制造工艺模具制造工艺决定了模具的精度和寿命。
常见的模具制造工艺包括加工中心加工、电火花加工和线切割等。
合理选择工艺可以提高模具的制造效率和质量。
2.5 模具调试和调整模具调试和调整是确保瓶盖注塑模具正常运行的关键环节。
设计师需要根据生产工艺和成型效果进行模具调试和调整,以提高模具的稳定性和生产效率。
3. 模具制造过程瓶盖注塑模具的制造过程主要包括以下几个步骤:3.1 模具设计在模具设计阶段,设计师需要根据瓶盖的要求和生产工艺,绘制出模具的结构设计图,确定模具的尺寸、形状和材料。
3.2 模具加工模具加工是将设计好的模具结构图转化为实际模具的过程。
常见的模具加工方法包括数控机床加工、车床加工和磨床加工等。
通过精密加工,可以保证模具的精度和质量。
3.3 模具装调模具装调是将制造好的模具安装到注塑机上,并进行调试和校准的过程。
在这个过程中,操作人员需要调整模具的位置、温度和注塑参数,以确保模具的正常运行和瓶盖的质量。
3.4 模具测试模具测试是对制造好的模具进行性能测试的过程。
输液瓶橡胶盖注射模具设计
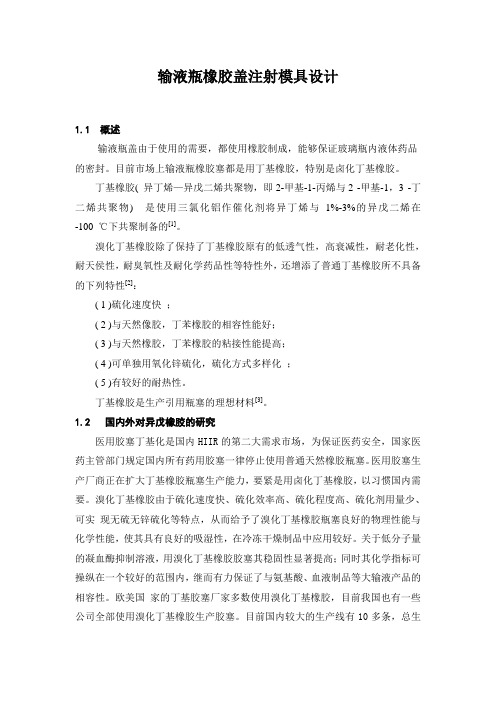
输液瓶橡胶盖注射模具设计1.1 概述输液瓶盖由于使用的需要,都使用橡胶制成,能够保证玻璃瓶内液体药品的密封。
目前市场上输液瓶橡胶塞都是用丁基橡胶,特别是卤化丁基橡胶。
丁基橡胶( 异丁烯—异戊二烯共聚物,即2-甲基-1-丙烯与2 -甲基-1,3 -丁二烯共聚物) 是使用三氯化铝作催化剂将异丁烯与1%-3%的异戊二烯在-100 ℃下共聚制备的[1]。
溴化丁基橡胶除了保持了丁基橡胶原有的低透气性,高衰减性,耐老化性,耐天侯性,耐臭氧性及耐化学药品性等特性外,还增添了普通丁基橡胶所不具备的下列特性[2]:( 1 )硫化速度快;( 2 )与天然像胶,丁苯橡胶的相容性能好;( 3 )与天然橡胶,丁苯橡胶的粘接性能提高;( 4 )可单独用氧化锌硫化,硫化方式多样化;( 5 )有较好的耐热性。
丁基橡胶是生产引用瓶塞的理想材料[3]。
1.2国内外对异戊橡胶的研究医用胶塞丁基化是国内HIIR的第二大需求市场,为保证医药安全,国家医药主管部门规定国内所有药用胶塞一律停止使用普通天然橡胶瓶塞。
医用胶塞生产厂商正在扩大丁基橡胶瓶塞生产能力,要紧是用卤化丁基橡胶,以习惯国内需要。
溴化丁基橡胶由于硫化速度快、硫化效率高、硫化程度高、硫化剂用量少、可实现无硫无锌硫化等特点,从而给予了溴化丁基橡胶瓶塞良好的物理性能与化学性能,使其具有良好的吸湿性,在冷冻干燥制品中应用较好。
关于低分子量的凝血酶抑制溶液,用溴化丁基橡胶胶塞其稳固性显著提高;同时其化学指标可操纵在一个较好的范围内,继而有力保证了与氨基酸、血液制品等大输液产品的相容性。
欧美国家的丁基胶塞厂家多数使用溴化丁基橡胶,目前我国也有一些公司全部使用溴化丁基橡胶生产胶塞。
目前国内较大的生产线有10多条,总生产能力达100亿只以上[4]。
合成丁基橡胶与卤化丁基橡胶的工艺路线目前有低温淤浆工艺与溶液法工艺。
低温淤浆工艺是最早开发的合成丁基橡胶的工艺,通常是以氯甲烷作聚合介质,三氯化铝作引发剂,反应温度操纵在-100-90℃。
小瓶盖塑料注塑模具设计说明书
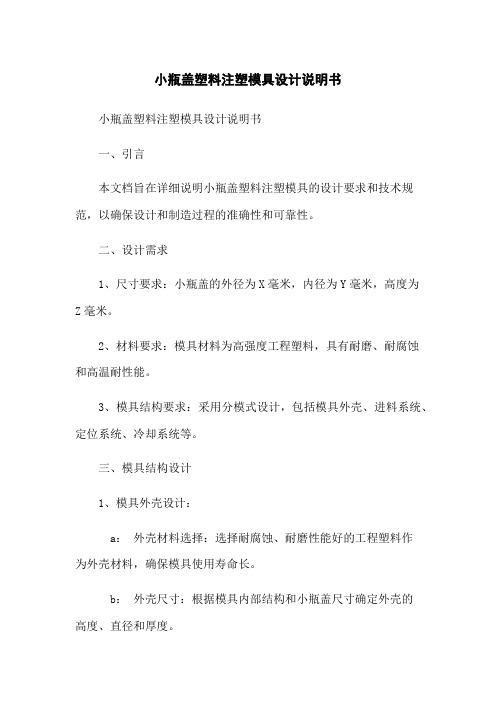
小瓶盖塑料注塑模具设计说明书小瓶盖塑料注塑模具设计说明书一、引言本文档旨在详细说明小瓶盖塑料注塑模具的设计要求和技术规范,以确保设计和制造过程的准确性和可靠性。
二、设计需求1、尺寸要求:小瓶盖的外径为X毫米,内径为Y毫米,高度为Z毫米。
2、材料要求:模具材料为高强度工程塑料,具有耐磨、耐腐蚀和高温耐性能。
3、模具结构要求:采用分模式设计,包括模具外壳、进料系统、定位系统、冷却系统等。
三、模具结构设计1、模具外壳设计:a:外壳材料选择:选择耐腐蚀、耐磨性能好的工程塑料作为外壳材料,确保模具使用寿命长。
b:外壳尺寸:根据模具内部结构和小瓶盖尺寸确定外壳的高度、直径和厚度。
c:模具外壳装配:确保外壳的装配牢固,能够承受注塑过程中的压力和冲击。
2、进料系统设计:a:进料口位置:进料口位于模具外壳上方,方便塑料材料的注入和冷却。
b:进料系统结构:进料系统包括进料管道、进料阀门和喷嘴等组成,确保塑料均匀流动。
3、定位系统设计:a:定位杆:在模具内部设置定位杆,以确保小瓶盖注塑时的位置准确性。
b:定位孔:在小瓶盖上开设定位孔,使得小瓶盖能够准确地套在定位杆上。
4、冷却系统设计:a:冷却通道:在模具内部设置冷却通道,以降低注塑过程中的温度,提高生产效率和产品质量。
b:冷却介质:选择高效的冷却介质,如冷水或冷气等,快速降低模具温度。
四、模具制造要求1、加工工艺:采用先进的数控加工设备和工艺,确保模具的加工精度和表面光洁度。
2、查漏测试:在模具制造过程中进行查漏测试,确保模具没有任何渗漏。
五、附录本文档涉及以下附件:1、小瓶盖的详细尺寸图纸。
2、模具的3D设计图纸。
六、法律名词及注释1、注塑模具:指用于塑料注塑成型的模具,可分为热流道模具和冷流道模具。
2、工程塑料:指具有高强度、耐磨、耐腐蚀和高温耐性能的塑料材料。
3、渗漏:指模具在注塑过程中出现塑料渗漏的现象,对产品质量产生负面影响。
模具毕业设计58瓶盖注射模设计说明书

塑料模设计说明书系别:机械工程系专业:模具设计与制造班级:姓名:学号:指导老师:12月13日一、塑件工艺特性1、塑件所使用的材料的种类及工艺特性的分析:聚苯乙烯是通用热塑性塑料。
聚苯乙烯树脂是无色、透明并有光泽的非结晶型线型结构的高聚物。
其原料来源广泛,石油工业的发展促进了聚苯乙烯大规模的生产。
目前,它的产量仅次于聚乙烯和聚氯乙烯,居于第三位。
2、塑件的成型特点分析:聚苯乙烯成型性能优良,其吸水性小,成型前可不进行干燥;收缩小,制品尺寸稳定;比热容小,可很快加热塑化,且塑化量较大,故成型速度快,生产周期短,可进行高速注射;流动性好,可采用注射、挤出、真空等各种成型方法。
但注射成型时应防止淌料;应控制成型温度、压力和时间等工艺条件,以减少内应力。
3、塑件结构分析:从塑件外型看,总体为一个圆形阶梯壳体零件,表面要求光滑,并带圆弧,有较细长的排气孔和装配孔。
二、塑件的体积与质量的计算该产品材料为ps,查资料得知其密度为1.054 g/cm3,收缩率为0.6%~0.8%。
利用PRO/E计算得塑件的体积V=4.894cm3塑件质量:M=Vρ=1.054g/cm3×4.894cm3≈5.158g三、注塑机的确定根据原材料和塑料制件的各种参数,初定注射机的型号为:G54-S200/400,其有关参数如下:(参照教材表4.2)注塑机的最大注塑量:200~400cm3;螺杆直径:55mm注射压力:109MPa ;注射行程:160mm注射方式:螺杆式;锁模力:2540KN最大成型面积:645 cm3;最大开合模行程:260cm最大模厚:406mm ;最小模厚:165mm喷嘴圆弧半径:R18mm ;喷嘴孔直径:Ф4mm注塑机拉杆空间:290×368mm 动、定模固定尺寸:532×634mm四、注射模设计1、型腔的确定该塑料结构简单,采用的是一模两腔,为了实现各型腔均匀进料和达到同时充满型腔的目的,采用平衡式布局。
医用输液器注塑模具设计研究内容

医用输液器注塑模具设计研究内容下载温馨提示:该文档是我店铺精心编制而成,希望大家下载以后,能够帮助大家解决实际的问题。
文档下载后可定制随意修改,请根据实际需要进行相应的调整和使用,谢谢!并且,本店铺为大家提供各种各样类型的实用资料,如教育随笔、日记赏析、句子摘抄、古诗大全、经典美文、话题作文、工作总结、词语解析、文案摘录、其他资料等等,如想了解不同资料格式和写法,敬请关注!Download tips: This document is carefully compiled by the editor. I hope that after you download them, they can help you solve practical problems. The document can be customized and modified after downloading, please adjust and use it according to actual needs, thank you!In addition, our shop provides you with various types of practical materials, such as educational essays, diary appreciation, sentence excerpts, ancient poems, classic articles, topic composition, work summary, word parsing, copy excerpts, other materials and so on, want to know different data formats and writing methods, please pay attention!医用输液器注塑模具设计研究1. 研究背景在医疗行业中,输液器是常见的医疗器械之一,用于输液过程中药液的输送。
瓶盖注塑模具设计
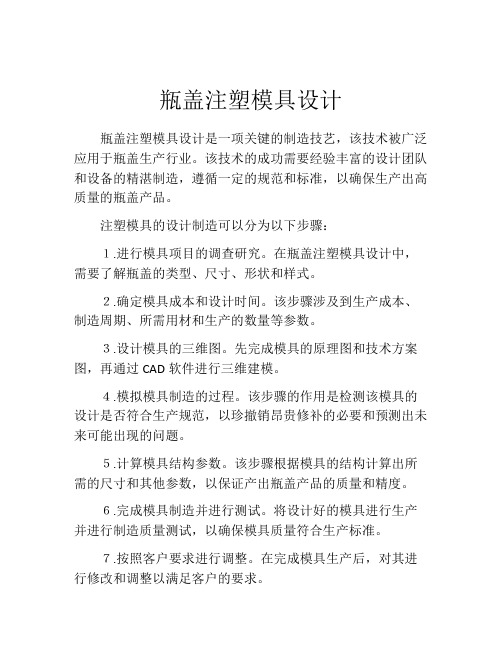
瓶盖注塑模具设计瓶盖注塑模具设计是一项关键的制造技艺,该技术被广泛应用于瓶盖生产行业。
该技术的成功需要经验丰富的设计团队和设备的精湛制造,遵循一定的规范和标准,以确保生产出高质量的瓶盖产品。
注塑模具的设计制造可以分为以下步骤:1.进行模具项目的调查研究。
在瓶盖注塑模具设计中,需要了解瓶盖的类型、尺寸、形状和样式。
2.确定模具成本和设计时间。
该步骤涉及到生产成本、制造周期、所需用材和生产的数量等参数。
3.设计模具的三维图。
先完成模具的原理图和技术方案图,再通过CAD软件进行三维建模。
4.模拟模具制造的过程。
该步骤的作用是检测该模具的设计是否符合生产规范,以珍撤销昂贵修补的必要和预测出未来可能出现的问题。
5.计算模具结构参数。
该步骤根据模具的结构计算出所需的尺寸和其他参数,以保证产出瓶盖产品的质量和精度。
6.完成模具制造并进行测试。
将设计好的模具进行生产并进行制造质量测试,以确保模具质量符合生产标准。
7.按照客户要求进行调整。
在完成模具生产后,对其进行修改和调整以满足客户的要求。
瓶盖注塑模具设计的需要考虑各种因素。
例如模架、模具部件、模具材料、尺寸和胶管尺寸等。
在设计模具时,必须保证有适当的空间以便于后期修复和调整。
模具的结构和制造质量是直接影响到瓶盖生产工艺和产品精度的因素之一。
使用高质量的钢材和其他金属材料使得模具的抗压、抗腐蚀和氧化能力更强。
在制造模具时还需要保证其精度和质量在高温和高压条件下仍然能够稳定性工作,保证生产稳定和高效率。
总之,瓶盖注塑模具设计是一项非常重要的制造工艺,需要高度专业的技术知识和经验。
通过合理设计和细致制造,可以生产出高精度、高质量的瓶盖产品。
瓶盖注塑模具设计(有全套图纸)

本科毕业设计(论文)通过答辩
目录 摘要 1 塑料的成型基础·····························································································································1
关键词:CAD;ProE 等软件;浇注系统;冷却系统
本科毕业设计(论文)通过答辩
The injecting model design of coverof the bottle bit of shampoo
ABSTRACT Mold CAD, ProE, software technology is 80-90 years before the emergence of a new design technology, These software technologies greatly enhance the wider use of the product and mold design quality products and the best performance. The software's main task is to help designers of the injection process, interpretation of the data and
矿泉水瓶盖注射模具设计说明书

毕业设计(论文)矿泉水瓶瓶盖注塑模设计系别:机械与电子工程系专业(班级):机械设计制造及其自动化11级升本作者(学号):任方成(51101090008)指导教师:王贤才完成日期:2013年5月16日目录中文摘要 (3)英文摘要 (4)1 前言 (5)1.1 本研究领域的现状和国内外的发展趋势 (5)1.1.1 概述 (5)1.1.2 国外的发展情况 (5)1.1.3 国内的发展情况 (6)1.2 本课题的研究内容、要求、目的及意义 (6)1.2.1 本课题的研究内容 (6)1.2.2 本课题的研究要求 (7)1.2.3 本课题的研究目的 (7)1.2.4 研究意义 (7)2 注塑模具设计部分 (8)2.1 塑件分析 (8)2.2 塑料材料的成型特性 (8)2.3 设备的选择 (9)2.3.1 塑件的体积 (9)2.3.2 锁模力的校核 (11)2.3.3 开模行程的校核 (12)2.4 浇注系统的设计 (12)2.4.1 主流道的设计 (12)2.4.2 分流道的设计 (12)2.4.3 冷料穴的设计 (14)2.4.4 设计所用的浇口形式 (14)2.4.5 分型面的设计 (15)2.4.6 排气槽的设计 (15)2.5 成型零部件的设计和计算 (15)2.5.1 成型零部件的设计 (15)2.5.2 成型零件工作尺寸的计算 (15)2.5.3 型腔壁厚计算 (18)2.6 脱模机构的设计和计算 (20)2.6.1 脱模阻力的计算 (20)2.6.2 脱模机构的设计 (21)2.7 脱螺纹机构的设计 (21)2.7.1 脱螺纹的形式 (21)2.7.2 旋转脱螺纹扭距的计算 (21)2.7.3 对主流道凝料能否脱出的校核 (22)2.7.4 止转装置的设计 (23)2.7.5 驱动装置和传动装置的设计和计算 (23)2.8 合模导向机构的设计 (27)2.8.1 顶出系统的导向 (27)2.8.2 成型零件的导向及定位 (28)2.9.1 冷却系统的设计 (28)2.9.2 模具冷却时间的计算 (29)2.9.3 冷却参数的计算 (30)2.10 支承与连接零件的设计与选择 (31)2.10.1 非标零件的设计 (31)2.10.2 标准零件的选取 (31)结论 (32)谢辞 (33)参考文献 (34)图2-1塑件2D图 (8)图2-2浇口套 (13)图2-3分流道的设计 (14)图2-4主流道冷料穴和拉料装置 (14)图2-5分流道浇口 (15)图2-6型芯与塑件 (16)图2-7支撑柱 (28)图2-8导柱和导套的设计 (28)图2-9冷却水道的设计 (29)表2-1聚丙烯的力学性能 (8)表2-2聚丙烯的热性能及电性能 (9)表2-3聚丙烯的物理性能 (9)表2-4聚丙烯的工艺参数 (9)表2-5一模两腔 (11)表2-6设计中所用螺钉 (31)表2-7设计中所用螺母 (31)矿泉水瓶盖注射模具设计摘要:本文详细介绍了矿泉水瓶盖注射模具的设计。
输液瓶橡胶盖注射模具设计

输液瓶橡胶盖注射模具设计输液瓶橡胶盖注射模具设计
注射模具是制造塑料制品的重要工具之一,常用于生产如输液瓶等医用器械。
输液瓶橡胶盖注射模具是制造输液瓶橡胶盖的专用模具,本文将结合实际案例,详细介绍输液瓶橡胶盖注射模具的设计要点。
一、产品分析
输液瓶橡胶盖是常用于输液瓶的塑料配件,主要用于密封输液瓶口部,防止外部污染。
输液瓶橡胶盖一般由橡胶材料制成,口径大小和高度不尽相同,通常采用注射成型工艺制造。
二、模具设计
1. 模具结构
输液瓶橡胶盖注射模具通常采用两板式结构设计,由上模板、下模板、导柱、导套、滑块、顶出机构等组成。
上下模板及导柱导套需精加工,确保模件加工精度和表面质量,减少模具使用过程中的磨损。
2. 模具材料
模具材料一般采用优质钢材制造,其中上模板和下模板需优先选用优质钢材,经过调质、淬火等热处理工艺后,具备高强度和良好的耐磨性能,确保模具使用寿命和稳定性。
3. 模具结构布局
为了提高模具运行效率和减少模具更换时间,应考虑合理的模具结构布局,如:将输液瓶橡胶盖集中在模具中心,尽量减少模具中小零部件的使用,同时顶出机构、导柱等重要位置的阻拦避免均匀累积,以利于后续模具维护和修理工作的进行。
三、结论
输液瓶橡胶盖注射模具是一种极为实用的注射模具,其设计建立在产品、工艺、使用寿命等多个方面考虑的基础之上。
设计合理的输液瓶橡胶盖注射模具可以显著提高生产效率和产品质量,降低生产成本,具有广泛的应用前景。
大输液塑料瓶盖模具设计

大输液塑料瓶盖模具设计07机械2班董国强07210010201 零件名称:大输液塑料瓶盖生产批量:大批量未注公差取MT5级精度据统计,我国13亿人口每年输液总需求约为45亿瓶,2008年,大输液生产量已超过60亿瓶(袋),约50%大输液仍沿用传统的玻璃瓶、天然橡胶塞和不易开启的铝盖包装。
这种包装方式存在许多缺点,特别是天然橡胶塞易老化,气密性差,针刺时易掉屑,而胶塞中的添加剂在药液中蚀溶以及在穿刺抽药时胶屑脱落下来的不溶性微粒可阻塞人体微循环,还可引起血小板溶解性出血。
鉴于此,目前大输液包装有向塑料瓶(PP或PE 瓶)和软袋(PVC或非PVC)发展趋势。
一、塑件结构分析750g 输液塑料瓶外瓶盖塑件形状如图1所示,材料为EVA,该材料具有流动性好、成型收缩大、冷却慢、易变形、质软、易脱模等优点。
塑件尺寸如图2所示,尺寸精度及表面质量一般。
塑件底部有一条高2.5mm、深1mm 的环形槽,可箍紧在瓶颈处。
塑件顶部有一防伪拉环,拉开防伪拉环即可启封药液。
二、模具设计方案根据塑件大小、形状、精度、工艺要求和生产批量,模具设计采用如下方案。
1、型腔数目及排列方式由于瓶盖为小塑件,用量大,希望腔数尽可能多,以提高生产效率。
综合考虑注塑机的锁模力、注射量及瓶盖的精度和经济性因素,采用1模32腔,型腔分布如图3所示,为对称结构,其中01~32为注塑型腔,塑液经主流道、支流道注塑至各型腔。
模具的闭合高度、安装定位等均应符合注塑机的技术参数。
2、分型面选择塑件底部环形槽与瓶体的配合有严格的要求,塑件成型后必然留在动模型芯上,根据塑件的结构特点,将模具分型面设在瓶盖的底端面,这是截面轮廓最大部位,与开模方向垂直,成型收缩率取1.8%。
3、浇注系统设计根据塑件结构,模具设计成三板式,采用点浇口,浇口设置在塑件顶部中心位置,EVA是一种对剪切速率敏感的塑料,采用点浇口进料方式,可以提高EVA熔体的剪切速率,降低熔体黏度,提高熔体的充模能力。
药用瓶盖毕业设计塑料模具设计说明书
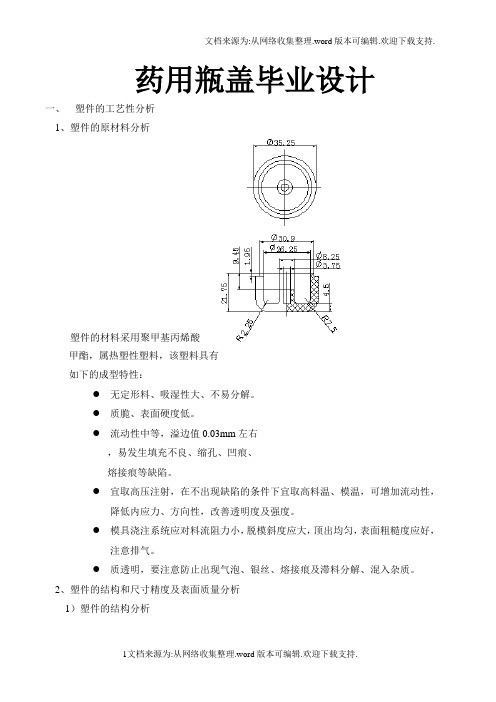
药用瓶盖毕业设计一、塑件的工艺性分析1、塑件的原材料分析塑件的材料采用聚甲基丙烯酸甲酯,属热塑性塑料,该塑料具有如下的成型特性:●无定形料、吸湿性大、不易分解。
●质脆、表面硬度低。
●流动性中等,溢边值0.03mm左右,易发生填充不良、缩孔、凹痕、熔接痕等缺陷。
●宜取高压注射,在不出现缺陷的条件下宜取高料温、模温,可增加流动性,降低内应力、方向性,改善透明度及强度。
●模具浇注系统应对料流阻力小,脱模斜度应大,顶出均匀,表面粗糙度应好,注意排气。
●质透明,要注意防止出现气泡、银丝、熔接痕及滞料分解、混入杂质。
2、塑件的结构和尺寸精度及表面质量分析1)塑件的结构分析该零件的总体形状为圆形,结构比较简单。
2)塑件尺寸精度的分析该零件的重要尺寸,如,30.9±0.09mm的尺寸精度为3级,次重要尺寸3.75±0.07mm的尺寸精度为4级,其它尺寸均无公差要求,一般可采用8级精度。
由以上的分析可见,该零件的尺寸精度属中等偏上,对应模具相关零件尺寸的加工可保证。
从塑件的壁厚上来看,壁厚最大处为4.5mm,最小处为2.25mm,壁厚差为2.25mm,较为均匀。
3)表面质量的分析该零件的表面要求无凹坑等缺陷外,表面无其它特别的要求,故比较容易实现。
综上分析可以看出,注射时在工艺参数控制得较好的情况下,零件的成型要求可以得到保证。
3、塑件的体积重量计算塑件的重量是为了选用注射机及确定模具型腔数。
计算得塑件的体积:V=9132mm3计算塑件的质量:公式为W=Vρ根据设计手册查得聚甲基丙烯酸甲酯的密度为ρ=1.18kg/dm3,故塑件的重量为:W=Vρ=9132×1.18×10-3=10.776g根据注射所需的压力和塑件的重量以及其它情况,可初步选用的注射机为:SZ-60/40型注塑成型机,该注塑机的各参数如下表所示:4、塑件的注射工艺参数的确定根据情况,聚甲基丙烯酸甲酯的成型工艺参数可作如下选择,在试模时可根据实际情况作适当的调整。
瓶盖注塑模设计说明
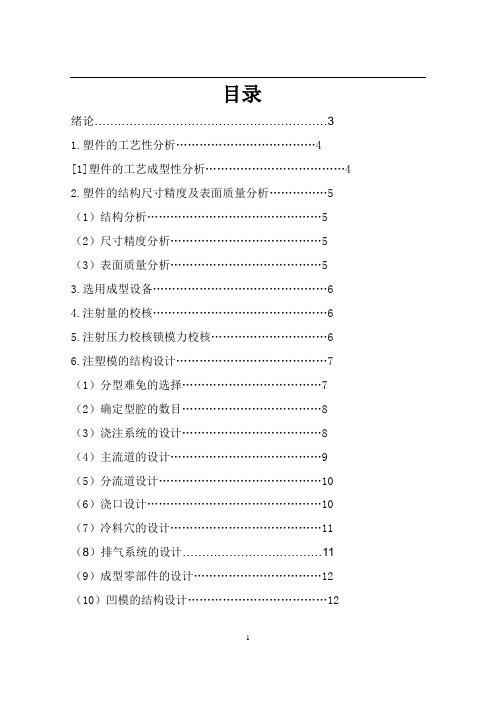
目录绪论 (3)1.塑件的工艺性分析 (4)[1]塑件的工艺成型性分析 (4)2.塑件的结构尺寸精度及表面质量分析 (5)(1)结构分析 (5)(2)尺寸精度分析 (5)(3)表面质量分析 (5)3.选用成型设备 (6)4.注射量的校核 (6)5.注射压力校核锁模力校核 (6)6.注塑模的结构设计 (7)(1)分型难免的选择 (7)(2)确定型腔的数目 (8)(3)浇注系统的设计 (8)(4)主流道的设计 (9)(5)分流道设计 (10)(6)浇口设计 (10)(7)冷料穴的设计 (11)(8)排气系统的设计 (11)(9)成型零部件的设计 (12)(10)凹模的结构设计 (12)(11)凸模的结构设计 (12)7成型零件的计算 (13)(1)型腔的工件尺寸的计算 (13)(2)型芯的设计 (14)(3)螺纹型芯的计算 (14)(4)侧壁和底板厚度的计算 (15)(5)型腔侧壁厚度的计算 (16)(6)凹模底板厚度的计算 (16)8.成型零件材料的选用 (16)(1)核膜导向机构设计 (17)(2)抽芯机构的设计 (17)(3)滑块的设计 (17)(4)抽芯距的确定 (18)9.其他零件的设计 (18)10.模具加热与冷却系统的计算 (19)11.模具闭合高度的确定 (21)12.注塑机有关参数的设计 (21)13模具的安装与调试 (21)(1)模具的安装 (21)(2)模具的调试 (22)绪论模具在汽车,拖拉机,飞机,家用电器,工程机械,动力机械,冶金,机床,仪器仪表,轻工,日用五金等制造业中,起着极其重要的作用。
随着国民经济的飞速发展,模具工业近年来也得到快速普及和发展。
各种模具是大批量制造各种工业产品广泛采用工装设备。
模具的种类繁多,形式多样,模具的主要特点是单件生产,每套模具都需要进行一次新的设计。
随着模具工业的迅速发展,对模具的使用寿命、加工精度等提出了更高的要求。
模具材料性能的好坏和使用寿命的长短,将直接影响加工产品的质量和生产的经济效益。
点滴瓶盖注塑模设计

点滴瓶盖注塑模设计点滴瓶盖是一种常见的医疗器械,用于将药物以滴定方式给予患者。
它通常由塑料材料制成,并采用注塑模具进行生产。
本文将详细介绍点滴瓶盖的注塑模设计方案。
首先,点滴瓶盖的注塑模设计需要考虑以下几个方面:1.材料选择:点滴瓶盖常用的材料包括聚丙烯(PP)、聚乙烯(PE)等。
根据产品的需求以及工艺要求,选择适合的材料。
2.模具结构设计:点滴瓶盖通常由两个部分组成,上盖和下盖。
注塑模具应该采用分模结构,以便更好地进行脱模。
同时,注塑模具应该考虑到点滴瓶盖的尺寸、形状和其他细节要求,确保生产出的产品能够符合设计要求。
3.流道设计:流道是塑料材料流动的通道,注塑模具的流道设计应该考虑到材料的流动性,以及产品的填充情况。
在点滴瓶盖的注塑模设计中,流道的位置和尺寸应该合理,以确保产品的均匀填充,并避免出现气泡等缺陷。
4.冷却系统设计:冷却系统是注塑模具中起冷却作用的部分。
在点滴瓶盖的注塑模设计中,冷却系统的设计应该考虑到产品的结构和尺寸,以确保产品能够在注塑过程中迅速冷却,从而提高生产效率和产品质量。
5.脱模设计:脱模是指将注塑成型的产品从模具中取出的过程。
在点滴瓶盖的注塑模设计中,应该考虑到产品的外形和内部结构,以确保产品能够顺利地脱模,并且不会产生划痕或其他损坏。
除了以上几个方面,点滴瓶盖的注塑模设计还需要考虑到产品的尺寸精度、注塑工艺参数等。
在设计过程中,可以使用CAD软件进行模具的三维设计,帮助模具设计师更好地了解产品的结构和细节要求。
总结起来,点滴瓶盖的注塑模设计需要考虑到材料选择、模具结构设计、流道设计、冷却系统设计、脱模设计等方面。
通过合理的注塑模设计,可以生产出符合设计要求的点滴瓶盖产品,提高生产效率和产品质量。
- 1、下载文档前请自行甄别文档内容的完整性,平台不提供额外的编辑、内容补充、找答案等附加服务。
- 2、"仅部分预览"的文档,不可在线预览部分如存在完整性等问题,可反馈申请退款(可完整预览的文档不适用该条件!)。
- 3、如文档侵犯您的权益,请联系客服反馈,我们会尽快为您处理(人工客服工作时间:9:00-18:30)。
1 引言1.1 概述输液瓶盖由于使用的需要,都采用橡胶制成,可以保证玻璃瓶液体药品的密封。
目前市场上输液瓶橡胶塞都是用丁基橡胶,尤其是卤化丁基橡胶。
丁基橡胶( 异丁烯—异戊二烯共聚物,即2-甲基-1-丙烯与2 -甲基-1,3 -丁二烯共聚物) 是使用三氯化铝作催化剂将异丁烯与1%-3%的异戊二烯在-100 ℃下共聚制备的[1]。
溴化丁基橡胶除了保持了丁基橡胶原有的低透气性,高衰减性,耐老化性,耐天侯性,耐臭氧性及耐化学药品性等特性外,还增添了普通丁基橡胶所不具备的以下特性[2]:( 1 )硫化速度快;( 2 )与天然像胶,丁苯橡胶的相容性能好;( 3 )与天然橡胶,丁苯橡胶的粘接性能提高;( 4 )可单独用氧化锌硫化,硫化方式多样化;( 5 )有较好的耐热性。
丁基橡胶是生产引用瓶塞的理想材料[3]。
1.2国外对异戊橡胶的研究医用胶塞丁基化是国HIIR的第二大需求市场,为保证医药安全,国家医药主管部门规定国所有药用胶塞一律停止使用普通天然橡胶瓶塞。
医用胶塞生产厂商正在扩大丁基橡胶瓶塞生产能力,主要是用卤化丁基橡胶,以适应国需要。
溴化丁基橡胶由于硫化速度快、硫化效率高、硫化程度高、硫化剂用量少、可实现无硫无锌硫化等特点,从而赋予了溴化丁基橡胶瓶塞良好的物理性能和化学性能,使其具有良好的吸湿性,在冷冻干燥制品中应用较好。
对于低分子量的凝血酶抑制溶液,用溴化丁基橡胶胶塞其稳定性显著提高;同时其化学指标可控制在一个较好的围,进而有力保证了与氨基酸、血液制品等大输液产品的相容性。
欧美国家的丁基胶塞厂家多数采用溴化丁基橡胶,目前我国也有一些公司全部使用溴化丁基橡胶生产胶塞。
目前国较大的生产线有10多条,总生产能力达100亿只以上[4]。
合成丁基橡胶和卤化丁基橡胶的工艺路线目前有低温淤浆工艺和溶液法工艺。
低温淤浆工艺是最早开发的合成丁基橡胶的工艺,一般是以氯甲烷作聚合介质,三氯化铝作引发剂,反应温度控制在-100-90℃。
溶液法工艺是以烷烃为溶剂,在卤代烷基铝的催化下,与-90-50℃,异丁烯与共轭双烯共聚合成丁基橡胶[5]。
1.3 输液瓶橡胶盖的成型模具采用注射成型模具是指安装在橡胶注射机热板上,由注射机将已经在注射机筒塑化、预热接近硫化温度的胶料,通过注射剂注射嘴和模具的浇注系统注入型腔硫化橡胶制品的模具。
从结构上讲,橡胶注射成型模具更接近塑料注射成型模具,同一制品的注射成型模具结构比压制成型模具和压铸成型模具结构要复杂得多,因而造价也要高很多。
但是注射模具成型生产效率高,产品质量稳定,自动化程度高,因此注射成型模具一般只用于批量生产,在大批量生产中优势更明显[6]。
注射模具结构式是由注射机的形式和橡胶制品形状及构造等因素决定的。
一般由动模和定模两部分构成。
定模安装在注射机的固定热板上,与注射机喷嘴相接,动模安装在注射机的活动热板上。
动定模合模后形成型腔和浇注系统。
橡胶注射模具的结构主要包括浇注系统、型腔部分、余胶和排气部分、合模导向机构、产品定出机构、模具与注射机的安装六部分[7]。
浇注系统为橡胶由注射机喷嘴到模具型腔之间的通道,一般由主流道、分流道、浇口和冷料井四部分组成。
多腔模具和一部分单腔模具的浇注系统四部分都有,有的橡胶产品的单腔模具则只有主流道和型腔。
型腔是成型橡胶制品的部分,其复杂程度由橡胶制品本身决定,一般由两块或两块以上的模块组成。
橡胶注射模具在分型面处开设余胶槽,一般产品不需专门开设排气槽,余胶槽和分型面本身就能满足排气要求。
对于有些产品可在试模后在料流末端补充加工排气槽。
合模导向机构是为保证模具各模板之间的准确对中定位而设计的,简单的模具包括导向销、定位孔两部分,复杂的模具则增加有销套等零件。
橡胶具有很高的弹性,大多数制品质地柔软。
所以,多数橡胶注射成型的制品不需要顶出装置。
但是对于一些带有金属骨架的制品和硬度较高的橡胶制品,还有一部分多腔模具,为实现产品的一次取出都需要有专门的顶出机构。
另外还包括一些需要活动模芯结构的产品[8]。
模具与注射机上、下热板的安装方式根据注射机的具体情况设计[9]。
1.4 输液瓶橡胶盖注射成型工艺设备以及国外最新技术橡胶由于本身粘度高、易焦烧的特性,使得它从模压成型到注射成型经历了一段漫长的时间,到目前为止,橡胶注射成型已经历了3个阶段:柱塞式注射、螺杆往复式注射和螺杆-柱塞式注射[10]。
柱塞式注射成型机注射成型方法是:将胶料从喂料口喂入料筒后由料筒外部的加热器对胶料进行加热、塑化,使胶料达到易于注射而又不会焦烧的温度为止。
最后由柱塞将已塑化胶料高压注入模具中。
螺杆式注射成型机注射成型方法是:胶料从喂料口进入挤出机后,在螺杆的旋转作用下受到强烈的剪切。
胶温很快升高,当胶料沿螺杆移动到螺杆前端时,已得到充分而均匀的塑化,螺杆一边旋转一边向后移动。
当螺杆前端积聚的胶料达到所需要的注射量时,轴向动力机构以强大的推力推动螺杆向前移动,从而将胶料注入模腔。
螺杆-柱塞式注射成型机注射成型工艺过程为:首先将冷胶料喂入螺杆塑化系统,胶料经螺杆塑化后,挤入到柱塞注射系统中。
最后由柱塞将胶料注射到模腔中,为了使胶料按照一定的顺序流动,在螺杆挤出机的端部安装一个止逆阀。
胶料塑化后通过止逆阀进入注射系统中并将柱塞顶起,这时胶料不会从喷嘴出去,因为喷嘴通道狭窄,阻力大。
当柱塞将胶料以高压从喷嘴注入模腔时,因为止逆阀的作用,胶料不会倒流进入挤出机中[11]。
注射成型是一种设定硫化温度后,把已塑化预热过的混炼胶快速注入模具,在短时间使橡胶制品成型的硫化方法[12]。
注射成型的成型周期短,成型制品质量可由几克到几十千克,能一次成型外形复杂、尺寸精确的模塑品。
成型方法适应性强,生产效率高。
近年来在许多橡胶加工方法中,通过注射成型制造各种制品正在不断增加,制品质量一致性好[13]。
随着橡胶注射成型工艺的发展,人们在提高制品精度、节约原材料、降低能耗、减少制品缺陷等方面进行了大亮研究,从而使橡胶注射成型工艺得到了很大的发展[14]。
最新技术有以下几种:抽真空注射成型工艺、冷流道注射成型工艺、气体辅助注射成型工艺[15]。
注射硫化温度一般在170℃~200℃之间。
在高温、高压、高剪切力下胶料的门尼粘度低、流动性好,胶料钻缝现象严重。
因此对注射模具加工精度、配合间隙等要求很高,特别是模具的水平平行度、镶件与板面的配合间隙、模具分型面的表面粗糙度都要求高于普通模具l--2级[16].。
1.5 输液瓶橡胶盖模具设计小结国外关于橡胶成型更多采用了压制成型。
而由于输液瓶盖用量大,而且结构简单,更倾向于大批量生产,因此输液瓶的橡胶盖多采用了注射成型。
输液瓶橡胶盖结构和大小原因,更加适宜于螺杆-柱塞式注射成型机,可以调高制品精度,节约原料,降低能耗等。
2 模具结构设计2.1 橡胶件的材料选择和塑件图2.1.1 橡胶件材料选择橡胶件使用溴化丁基橡胶,具体编号是燕化公司的IIR-1751。
其具体参数是:表 2.1溴化橡胶材料参数不饱和度 1.68%数均相对分子量Mn 236 600重均相对分子量Mw 498 400Mn/Mw 2.11硬度(邵氏A)60300%定伸强度7.78MPa拉断伸长率582%拉伸强度17.48MPa撕裂强度42.35KN/m 永久变形28%滞后损失21.9%弹性7%g/cm 密度 1.123门尼粘度ML(1+8)125℃51.02.1.2 橡胶件图橡胶件是输液瓶瓶塞结构见图1。
图2.12.2 模具结构的确定2.2.1 模具结构形式和腔数确定丁基橡胶的瓶塞具有注射成型条件,而且可以大批量生产,所以模具结构形式为注射成型。
瓶塞批量大、规格小、形状简单和精度偏低的制品,为了提高生产效率、降低成本,在设备加工条件允许的情况下,应采用多孔结构,直径约为20mm左右的制品可以采用6个型腔数。
型腔的布置如图2所示,均匀分布。
图2.22.2.2 分型面的确定由于制件很简单,可以很明显确定分型面,在冠部和塞紧部分分界的平面。
2.3 收缩率的确定通过查表取丁基橡胶的常用平均收缩率为1.6%。
2.4.1 注射机的选择计算橡胶件的体积:2223318.813.28=6[3.3 3.14() 5.5 3.14() 6.6 3.14()420910222V cm -⨯⨯⨯+⨯⨯-⨯⨯=⨯ 由此可以选择橡胶注射机的型号为XZL-系列角型(C 型)橡胶注射成型机。
这种型号注射机适用于高精度中小型橡胶制品的注射硫化成型。
其主要技术参数如表2.2。
表 2.2XZL-系列角型(C 型)橡胶注射机参数工作界面尺寸 400400mm mm ⨯ 原料模具最小厚度 50mm 模具定位圈尺寸 100mm 最大合模行程 350mm 注射容量 1602cm 装机容量 16.5KW 冷却水容量20L/min2.4.2 注射机的校核a 12V V V =+a V ——总注射胶料体积; 1V ——成型全部胶料零件的体积;3V ——浇注系统的胶料体积所以34.2091014.209a V cm =+=可知小于注射机的理论注射容量的80%。
2.4.2.2 开模行程的校核12j H H H +≤1H ——开模距离,mm ;2H ——取出或顶出产品所需空间,mm ; j H ——注射机最大开模行程,mm 。
12(124)20350+-=≤所以开模行程符合要求。
2.4.2.3 喷嘴尺寸和定位圈要求由注射机的参数可以得到,喷嘴尺寸为半径16mm ,定位圈尺寸为半径100mm 。
所以定位圈的尺寸如图3所示。
图2.3定位圈使用45号钢制成,热处理达到HRC50~55。
2.5 浇注系统从注射机的喷嘴到制品浇口的通道称作浇注系统,包括主浇道、分浇道、浇口和冷料井四个部分。
2.5.1 主浇道设计主流道的锥度选择5°,浇道壁的表面粗糙度为0.8。
可知注射机主喷嘴是球面的,半径为16mm,所以主浇道始端的球面半径选择大于喷嘴直径,定为20mm。
主浇道小端直径取3.5mm。
主流道衬套与模板之间的配合应该是不能相对移动的,所以采用H7/n6的配合。
主流道衬套的形状和尺寸如图2.5所示。
图2.4主流道衬套采用T8A,热处理HRC53~57。
2.5.2 分浇道分浇道在动模上的分型面上,选择U形分浇道断面,如图2.5所示。
图2.5分浇道的分布形式采用均衡式,如图2.2所示。
2.5.3 冷料井冷料井设计在主浇道对面的动模板上,形状为倒锥形,如图2.6所示。
图2.62.5.4 浇口设计考虑到橡胶之间的形状、模具结构以及型腔分布,采用侧浇口。
形状如图2.7所示。
图2.72.6 成型零件的结构设计成型零件主要包括型芯、型腔。
2.6.1 型腔结果后设计由于制品简单,所以型腔设计为整体式,直接在模板上加工而成。
见图2.8。