电渣重熔钢中非金属夹杂物含量及成分的控制
H13钢中夹杂物控制及电渣重熔中的转变行为研究

H13钢中夹杂物控制及电渣重熔中的转变行为研究摘要钢铁材料中的夹杂物及其形态控制一直是研究热点。
本文研究了H13钢中夹杂物的型态与尺寸分布,探讨了电渣重熔对夹杂物的转变行为,以提高H13钢的质量。
通过对H13钢中夹杂物的形态与尺寸进行分析,发现钢中夹杂物主要为氧化物、碳化物和硫化物等,且分布不均匀。
电渣重熔可能引起夹杂物的改变,其中碳化物转变为碳化亚铁;硫化物转变为MnS和MnS-CaS混合物。
研究结果表明,电渣重熔可以有效地改善钢中夹杂物的分布及形态,提高H13钢的质量,为钢铁材料中的夹杂物及其形态控制提供了参考意见。
关键词:H13钢;夹杂物;电渣重熔;形态控制;质量提高AbstractThe control of inclusions and their morphology insteel materials has always been a research hotspot. This paper studies the morphology and sizedistribution of inclusions in H13 steel, and explores the transformation behavior of inclusions in electric slag remelting, in order to improve the quality of H13 steel. By analyzing the morphology and size ofinclusions in H13 steel, it is found that theinclusions in the steel are mainly oxides, carbides, and sulfides, and their distribution is uneven. The electric slag remelting may cause the change of inclusions, where carbides convert to Fe3C andsulfides convert to MnS and MnS-CaS mixture. Theresults show that electric slag remelting can effectively improve the distribution and morphology of inclusions in steel, and improve the quality of H13 steel, providing reference for the control ofinclusions and their morphology in steel materials.Keywords: H13 steel; inclusions; electric slag remelting; morphology control; quality improvemenThe inclusion morphology and distribution in steel is an important factor affecting its mechanicalproperties and service life. Inclusions can lead to local stress concentration and reduce material toughness, ductility and fatigue resistance. Therefore, controlling the inclusions and their morphology is of great significance for improving the quality and performance of steel.Electric slag remelting is a technology that can effectively reduce the content and improve the distribution and morphology of inclusions in steel.The process involves melting the steel in an electric furnace with a slag layer, and then remelting it under a high-voltage electric field. The electric field drives the inclusions to move and coalesce, and the slag layer on the surface can absorb and remove the inclusions. Through this process, the content of inclusions in steel can be significantly reduced, and the morphology and distribution of inclusions can be improved.In the electric slag remelting process, carbides in steel tend to convert to Fe3C, which is a more stable form of carbides. Meanwhile, sulfides tend to convert to MnS and MnS-CaS mixture, which are easier to be absorbed by the slag layer. The distribution of inclusions in steel is also significantly improved, with a more uniform dispersion and smaller size.The improvement of inclusion morphology anddistribution in steel through electric slag remelting can effectively enhance the mechanical properties and service life of the material. In particular, for high-quality steel products such as H13 steel, the control of inclusion morphology is particularly important. The results of this study provide guidance and reference for the control of inclusion morphology anddistribution in steel materials, and promote the development of high-quality steel productsThe control of inclusion morphology and distributionin steel is significant for the improvement of mechanical properties and service life of the material. This can be achieved through various techniques suchas electric slag remelting, desulfurization, and vacuum degassing. Electric slag remelting has been found to be an effective method for enhancing the cleanliness of steel by reducing the size, number, and distribution of inclusions.The morphology of inclusions in steel refers to their shape and size, while distribution refers to their dispersion in the steel matrix. Inclusions can significantly affect the mechanical properties of steel, such as ductility, toughness, and fatigue strength. Therefore, controlling the morphology and distribution of inclusions is necessary for the production of high-quality steel products.H13 steel is a high-quality steel product withexcellent properties such as high temperature strength, wear resistance, and toughness. The control ofinclusion morphology and distribution is particularly important for H13 steel to ensure its superiorproperties. In order to achieve this, a comprehensive understanding of the formation mechanism of inclusions and control measures is required.One of the methods commonly used for controlling inclusion morphology in steel is electric slag remelting. This process involves heating the steel to its melting point and then passing an electric current through it while it is covered by a layer of slag. The electric current generates heat, which melts the steel and the slag, creating a liquid pool. Inclusions that are present in the initial steel are absorbed by the slag, while new inclusions are formed due to the interaction between the slag and the steel.The incorporation of alloying elements such as Aluminum, Titanium, and Zirconium in the slag can effectively control the morphology and size of inclusions. These elements react with impurities present in the steel and form compounds that are absorbed by the slag. Additionally, stirring the slag during remelting can improve the distribution of inclusions.Desulfurization and vacuum degassing are alsoeffective methods for controlling inclusion morphology and distribution in steel. Desulfurization involvesremoving sulfur from the steel, which improves its ductility and toughness. Vacuum degassing removesother gases such as hydrogen and nitrogen, which can form inclusions during solidification.In conclusion, the control of inclusion morphology and distribution is essential for the production of high-quality steel products. Electric slag remelting, desulfurization, and vacuum degassing are effective techniques for achieving this. For H13 steel, the control of inclusion morphology is particularly important, and the results of this study provideuseful guidance for the production of this high-quality steel productAside from controlling inclusion morphology and distribution, there are other factors that contribute to the production of high-quality steel products. One important factor is the chemical composition of the steel. The addition of elements such as chromium, nickel, and molybdenum can greatly enhance the mechanical properties of the steel, including hardness, toughness, and corrosion resistance.Another crucial aspect is heat treatment. Heat treatment processes, such as annealing, quenching, and tempering, can significantly affect the microstructureand properties of the steel. For example, annealing can refine the grain structure and improve ductility, while quenching and tempering can increase the hardness and strength of the steel.Furthermore, the manufacturing process itself can also play a critical role in producing high-quality steel products. Proper temperature control, mechanical processing, and surface finishing can all help to ensure that the final product meets the required specifications and standards.In summary, the production of high-quality steel products is a complex and multi-faceted process that requires careful control of various factors, including inclusion morphology and distribution, chemical composition, heat treatment, and manufacturing processes. By implementing effective techniques and procedures, steel manufacturers can achieve the desired properties and performance of their products, ensuring their suitability for a wide range of applications in industries such as automotive, construction, and energyIn conclusion, producing high-quality steel productsis a challenging task that involves the careful management of several critical factors such asinclusion morphology, chemical composition, heat treatment, and manufacturing processes. Effective implementation of appropriate techniques and procedures can ensure that the steel products exhibit the desired properties and performance required for their intended applications. The manufacturing of high-quality steel products supports various industries such as automotive, construction, and energy。
钢中非金属夹杂物对质量的影响及控制技术

钢中非金属夹杂物对质量的影响及控制技术夹杂物概念及分类1内生夹杂物钢在冶炼过程中,脱氧反应会产生氧化物等产物,若这些产物在钢液凝固前未浮出,将留在钢中;Mn+FeO → Fe+MnOSi+2FeO → SiO2+2Fe2Al+3FeO → 3Fe+Al2O3Ti+2FeO → 2Fe+TiO2溶解在钢液中的氧、硫、氮等杂质元素在降温和凝固时,或固溶体中析出,最后留在钢锭中。
内生夹杂物分布比较均匀,颗粒也较小,正确的操作和合理的工艺措施可以减少其数量和改变其成分、大小和分布情况,不过一般是不可避免的。
2外来夹杂物钢在冶炼和浇注过程中悬浮在钢液表面的炉渣、或由炼钢炉、出钢槽和钢包等内壁剥落的耐火材料或其他夹杂物在钢液凝固前未及时清除而留于钢中。
它是金属在熔炼过程中与外界物质接触发生作用产生的夹杂物。
这类夹杂物一般特性是外形不规则,尺寸比较大,也无规律,又称为粗夹杂。
这类夹杂物通过正确的操作是可以避免的。
按化学成分分类按变形能力分类按形态与分布分类A类(硫化物类):具有高的延展性,有较宽范围形态比的单个灰色夹杂物,一般端部呈圆角。
B类(氧化铝类):大多数没有变形,带角,形态比小(一般<3),黑色或带蓝色的颗粒,沿轧制方向排成一行,至少有3个颗粒。
C类(硅酸盐类):具有高的延展性,有较宽范围形态比(一般≥3)的单个黑色或深灰色夹杂物,一般端部呈锐角。
D类(球状氧化物类):不变形,带角或圆形的,形态比小(一般<3),黑色或带蓝色的,无规则分布的颗粒。
Ds类(单颗粒球状类):圆形或近似圆形,直径≥13μm的胆颗粒夹杂物。
非金属夹杂物对钢性能的影响对使用性能的影响1、疲劳性能↓2、冲击韧性↓塑性↓3、耐腐蚀性↓对于尺寸小于10μm的夹杂物促进组织形核,焊接时组织晶粒长大。
(1)由于加入Nb、V、Ti等合金元素,在连铸、加热过程中都会析出,形核C、N化合物(一种微型夹杂物)(2)钙化处理的硫化物、硅酸盐类以及细小的氧化亚铁可以细化晶核。
重轨钢中非金属夹杂物控制的研究

甘
肃
冶
金
V 13 N . o. 4 o3
GAN U ME A L RG S T L U Y
J n ,01 u .2 2
文章编号 :6 24 6 ( 02 0 -0 60 17 - 1 2 1 ) 3 3 - 4 0 3
重 轨钢 中非金 属 夹 杂物 控 制 的研 究
12 S]+[ /[i O]=12 i , s / SO ( )
包和铸坯中夹杂有所增大。
4 控 制措 施
非 金属夹 杂 物是 钢 中非 金属 元 素碳 、 、 、 、 氮 硫 磷
氧的化合物 , 以氧、 的化合物为主 , 硫 严重影 响钢轨
的物理 化学性 能 。重 轨钢 中非金 属夹 杂物 来源非 常
W
A¨ [
2 装 备及 工艺情 况
攀 钢 重 轨 钢 生 产 基 本 工艺 流 程 与 工 艺 参 数 如 下 : 水预 处理 ( 铁 脱硫 、 渣 ) +2 顶 底 复 吹提 钒 扒 _ 1Ot
w[ × 。 H] 1‘w[ ] 1. A 。 T 0 X 6
25 . 2 0 2. 5
l ( O )= / ao I2l ( S] + . 8 g [ ] 12l s2 / w [ i ) 6 2 - w g i- g
1 1 15 / 5 7 .5 T () 1
复 杂 : 料本 身含 有 的夹 杂物 ; 及 时去除 的脱 氧产 原 未
物和脱硫产物 ; 钢液和熔渣 、 耐火材料的相互作用; 大包 下 渣 、 中间包 和结 晶器 卷渣 ; 注过程 中产 生 的 浇 二 次氧 化产 物 , 在 随 后 的 热冷 加 工 过 程 中发 生 形 并
科技成果——重轨钢中非金属夹杂物控制关键技术

科技成果——重轨钢中非金属夹杂物控制关键技术技术开发单位北京科技大学技术领域钢铁冶金成果简介铁路作为一种现代化交通运输工具,在世界范围内具有广阔的发展前景。
目前铁路发展的整体趋势是高速和重载化,对重轨钢质量提出了更高的要求,不仅要求高洁净度,高强度、高韧性,而且必须具有良好的抗疲劳性能。
重轨钢生产过程及使用过程中,非金属夹杂物是影响其质量最重要的原因之一,常引起探伤不合、易产生疲劳裂纹等,主要是由于其钢中非金属夹杂物控制存在以下三个难题:(1)夹杂物尺寸大且化学成分复杂;(2)冶炼工艺复杂,尤其在于脱氧及精炼等重要环节;(3)尖晶石类夹杂物突出,严重恶化钢轨性能。
因此合理控制重轨钢中的非金属夹杂物,对重轨钢产品质量的提升及铁路事业的进步具有重要意义。
(1)重轨钢冶炼脱氧及原辅料成分设计技术。
重轨钢采用无铝脱氧工艺,但是在脱氧剂的使用方式及用量上缺乏理论指导,因此,重轨钢脱氧过程中必须对脱氧剂的使用方式及用量进行合理优化控制,本项目提出仅在转炉出钢时加入少量硅钙钡脱氧剂控氧,同时配合精炼扩散脱氧,能将钢中T.O.含量控制在10ppm以下,不仅有效节约了生产成本,而且促进了夹杂物的去除、有效降低了夹杂物的尺寸。
在重轨钢冶炼原材料的控制方面,国内企业生产时更倾向于买价格低廉的铁合金等原材料,从而降低生产成本,但是对于铁合金及铁合金对重轨冶炼的影响研究几乎为空白。
本项目提出了使用低铝铁合金,降低钢中的酸溶铝含量,抑制钢中高Al2O3夹杂物的形成,从而提升夹杂物变形能力,有效防止因脆性夹杂物造成的疲劳缺陷。
(2)重轨钢中硫化物夹杂控制技术。
由于MnS有良好的变形能力,而且重轨钢轧制过程中变形量大,MnS夹杂物可能延伸很长,可能成为夹杂物超标和引起超声波探伤不合的重要原因之一。
此外,大尺寸长条状MnS可能成为裂纹的起点,在应力作用下首先在和钢基体的交界处形成裂纹源。
本项目首先通过优化精炼造渣制度进一步去除钢中S含量,提出将钢中得S降低到40ppm以下。
IF钢中成分及夹杂物的过程控制研究共3篇
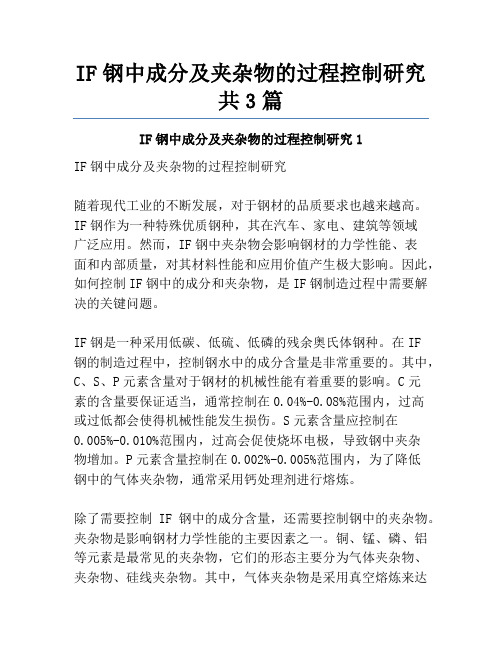
IF钢中成分及夹杂物的过程控制研究共3篇IF钢中成分及夹杂物的过程控制研究1IF钢中成分及夹杂物的过程控制研究随着现代工业的不断发展,对于钢材的品质要求也越来越高。
IF钢作为一种特殊优质钢种,其在汽车、家电、建筑等领域广泛应用。
然而,IF钢中夹杂物会影响钢材的力学性能、表面和内部质量,对其材料性能和应用价值产生极大影响。
因此,如何控制IF钢中的成分和夹杂物,是IF钢制造过程中需要解决的关键问题。
IF钢是一种采用低碳、低硫、低磷的残余奥氏体钢种。
在IF钢的制造过程中,控制钢水中的成分含量是非常重要的。
其中,C、S、P元素含量对于钢材的机械性能有着重要的影响。
C元素的含量要保证适当,通常控制在0.04%-0.08%范围内,过高或过低都会使得机械性能发生损伤。
S元素含量应控制在0.005%-0.010%范围内,过高会促使烧坏电极,导致钢中夹杂物增加。
P元素含量控制在0.002%-0.005%范围内,为了降低钢中的气体夹杂物,通常采用钙处理剂进行熔炼。
除了需要控制IF钢中的成分含量,还需要控制钢中的夹杂物。
夹杂物是影响钢材力学性能的主要因素之一。
铜、锰、磷、铝等元素是最常见的夹杂物,它们的形态主要分为气体夹杂物、夹杂物、硅线夹杂物。
其中,气体夹杂物是采用真空熔炼来达到控制的。
夹杂物控制主要采用铝剂、钝化剂来控制,将夹杂物和夹杂物粒子分散固溶。
夹杂物控制涉及到工艺流程中的温度、时间、气氛等多个因素。
其中,温度是控制夹杂物形成和发展的最主要因素。
在熔炼过程中,温度不稳定会导致夹杂物粗化、合并,影响到产品的质量。
时间是影响夹杂物生成的另一个因素。
时间越长,夹杂物的净化越好,但同时也会增加钢材的消耗和制造成本,因此需要在时间与效果之间做出平衡。
气氛对于夹杂物的控制也是至关重要的。
在IF钢制造过程中,要求钢水在加工过程中不氧化,因此需要高纯氧化铝和氮气配制的高保护因素。
总而言之,IF钢中成分及夹杂物的过程控制是IF钢提高品质的关键。
钢中非金属夹杂对质量的影响及控制措施解析

- 强化内生类夹杂物去除效果; - 严格“杜绝”二次氧化; - 对夹杂物成分、尺寸、分布、性能的控制。
2. 开发新工艺,降低成本,提高对夹杂物控制效率:
- 缩短或取消LF精炼; - 强化LF、VD、RH精炼; - 针对不同类型钢材,对夹杂物实行“重点控制”。
发生交互反应是一种普遍现象; ⑵脱氧的钢液与卷入的炉渣 (包括保护渣)或耐火材料接触时,
总会或多或少地起反应,因此仍保持原来的内生或外来夹杂 物的成分和结构是不多见的;
★
1.4 按夹杂物尺寸分类
1) 亚显微夹杂,粒径<lμm。在纯净钢中亚显微夹杂包括氮 化物、硫化物和氧化物,总数约为1011个/cm3,其中氧化物 夹杂个数约占108/cm3。一般认为这种微小氧化物对钢质(除 硅钢片外)多半无害,对它在钢中的作用,目前研究得不够。
夹杂物对钢板冲击的影响
当夹杂物颗粒比较大(>50μm),特别是夹 杂物含量较多、尺寸较大时,明显降低钢的冲击。 且冲击功曾几何状下降,尤其冲击断口出现夹渣时, 冲击值几乎为个位数。主要原因是夹杂物阻碍了冲 击的扩展功能量的释放。
夹杂物对钢板厚拉(Z向)的影响
当厚拉断口出现夹杂物含量较多、尺寸较大时, 明显降低钢的Z向性能,性能几乎为个位数。尤其 是硫化物夹杂和氧化铝夹杂,破坏钢板基体组织的 连续性,厚度方向被该类别夹杂物穿晶破坏。
1.5 按化学成分分类
A类夹杂:硫化物 FeS、MnS B类夹杂: 氧化铝、氧化铁 Al2O3+FeO C类夹杂:硅酸盐、氮化物 2MnO.SiO2 TiN、BN、NbN等 D类夹杂:球状氧化物类 小型氧化物 FeO、MnO、TiO2等 Ds类夹杂:单个大型球状氧化物类
金属冶炼过程中的非金属夹杂物控制

扫描电镜(SEM)
总结词
扫描电镜是一种高分辨率的显微镜,能够观察金属材料表面和内部的微观结构,适用于非金属夹杂物的检测和表 征。
详细描述
扫描电镜利用电子束扫描金属材料的表面,通过收集和分析反射回来的电子信号,形成高分辨率的图像。该方法 能够观察夹杂物的形貌、大小、分布和成分等信息,具有较高的精度和分辨率。
对金属材料性能的影响
力学性能
非金属夹杂物会降低金属的力学性能,如强度、韧性、疲劳寿命等 。夹杂物的存在会导致应力集中,降低材料的抗拉强度和疲劳极限 。
物理性能
非金属夹杂物对金属的物理性能也有显著影响。例如,夹杂物会降 低金属的导电性、导热性和磁性等。
工艺性能
非金属夹杂物还会影响金属的加工性能,如焊接、热处理、塑性加工 等。夹杂物的存在可能导致焊缝开裂、热处理时组织不均匀等问题。
X射线衍射(XRD)
总结词
X射线衍射是一种用于分析金属材料 晶体结构和相组成的检测方法,可以 用于非金属夹杂物的鉴别和定量分析 。
详细描述
X射线衍射利用X射线照射金属材料, 通过分析衍射图谱来判断材料的晶体 结构和相组成。该方法能够鉴别夹杂 物的矿物组成和含量,具有较高的精 度和可靠性。
04
非金属夹杂物的控制技术与实践
金属冶炼过程中的非金属 夹杂物控制
汇报人:可编辑 2024-01-06
目录
• 非金属夹杂物的基本概述 • 非金属夹杂物的来源与控制策略 • 非金属夹杂物检测与表征技术 • 非金属夹杂物的控制技术与实践 • 非金属夹杂物控制的效果评估与优化建议 • 案例分析:某钢厂非金属夹杂物控制实践
01
非金属夹杂物的基本概述
定期检查熔炼炉内衬,确保其完 好无损,防止剥落物混入金属溶 液。
电渣重熔过程中夹杂物的控制115

摘要:非金属夹杂物在钢的性能中起着重要的作用。它在钢中的分布不仅破坏了基体的连续性,而且导致材料的塑性、韧性和疲劳性能降低,并且微孔和裂纹容易在夹杂物和钢的界面形成疲劳断裂或者引起其他缺陷,因此,在炼钢过程中,必须要正确控制夹杂物。电渣重熔(ESR)技术能有效的去除钢中的非金属夹杂物,并能对钢中夹杂物的分布进行改善,随着钢的质量要求的不断提高,一般重熔技术已不能满足洁净钢的生产要求。
4结论
(1)电极中的非金属夹杂物受到浮力、重力、曳力、升力以及附加质量力作用,随熔渣运动,最终大部分的夹杂物分别在渣池与空气接触面和渣池与结晶器侧壁接触面被捕获,小部分夹杂物仍在渣中随熔渣运动,极少数夹杂物会穿过凝固界面,进入钢锭中。
(2)重熔过程中直径大的夹杂物的去除率大于直径小的夹杂物。夹杂物粒径从1μm增加到10μm时:在电流为1200A时,夹杂物去除率从90.49%增加到99.28%;在电流为1500A时,夹杂物去除率从91.40%增加到99.80%;在电流为1800A时,夹杂物去除率从84.55%增加到99.99%。
2实验结果与分析
2.1显微组织分析
1Cr13钢电渣重熔显微组织中夹杂物的形貌。黑褐色粒状物经锻压后无变形只是破碎,初步确定为脆性夹杂。中浅灰色似纺锤体的物质经锻压后沿变形方向延伸成带状,具有良好的塑性,初步确定为塑性夹杂。
2.2扫描电镜及能谱分析
本实验采用金相法与微观区域成分分析相结合,用金相显微镜和能谱分析测试仪对1Cr13钢锻件成分进行分析,测定尺寸大于1μm夹杂物的元素组成,并对个别元素进行面扫描分析,通过能谱仪对其进行成分分析,得出各元素的质量分数谱线。在本测试中Fe、Cr是1Cr13钢的主要成分,在进行夹杂物成分分析时不予考虑。夹杂物中的Fe、Cr、F、O、Si和Ca元素进行能谱分析可以看出,F(wt%)=14.68%、Si(wt%)=3.3%、O(wt%)=11.61%、Ca(wt%)=0.33%,对比1Cr13锻件用钢的化学成分,O、F、Si和Ca都超出标准。1Cr13钢夹杂物中块状的脆性夹杂物中含有的主要元素有O和Si,且分布较为集中,而F元素含量居高,由此可以推断1Cr13钢锻件中的块状脆性夹杂物为SiO2,但只占小部分,而CaF2夹渣占大部分。夹杂物中进行Mn元素和Mn、S元素的面扫分析可以看出,浅灰色似纺锤体的夹杂物主要以MnS形式存在,并对夹杂物中的Mn元素进行能谱分析得出,Mn(wt%)=0.23%,Mn(wt%)=0.18%,对比1Cr13锻件用钢的化学成分,均未超出标准。
导电结晶器电渣重熔中非金属夹杂物的去除

第20卷第5期 2010年5月 中国冶金China Metallurgy Vol.20,No.5May 2010导电结晶器电渣重熔中非金属夹杂物的去除刘福斌, 臧喜民, 姜周华, 耿 鑫(东北大学材料与冶金学院,辽宁沈阳110004)摘 要:导电结晶器电渣重熔渣池局部发热密度最高值在电极角部和结晶器壁附近,电极端部下方仍存在“高温区”,对非金属夹杂物去除提供热力学与动力学条件。
电渣重熔过程中非金属夹杂物的去除主要发生在自耗电极端头熔滴形成阶段以及熔滴穿过熔渣层阶段。
综合自耗电极端部熔化至熔滴形成过程阶段、熔滴滴落并穿过渣池至金属熔池阶段和金属熔池至铸锭凝固非金属夹杂物的上浮阶段的去除率,导电结晶器电渣重熔去除非金属夹杂物的能力不低于传统电渣重熔。
关键词:导电结晶器;电渣重熔;夹杂物中图分类号:TF 744 文献标志码:A 文章编号:100629356(2010)0520005204R emoval of Non 2Metallic Inclusions in Current 2ConductiveMould ESR ProcessL IU Fu 2bin , ZAN G Xi 2min , J IAN G Zhou 2hua , GEN G Xin(School of Materials and Metallurgy ,Northeastern University ,Shenyang 110004,Liaoning ,China )Abstract :Maximum local Joule heat generation density values of current 2conductive mould ESR slag bath occur in the area which is close to the electrode corner and the slag/mould interface.“High temperature zone ”still is under the electrode.Removal of non 2metallic inclusion during remelting occurred mainly in the first stage of consumable e 2lectrode forming molten drop and the second stage of molten drop passing through the slag bath.Analyzing removal ratio of non 2metallic inclusions during the stage of forming molten drop ,the stage of molten drop passing through the slag bath and the rising stage of non 2metallic inclusion in molten metal bath ,the ability of removal of non 2metal 2lic inclusion of current 2conductive mould ESR is not lower than the traditional ESR 。
电渣重熔马氏体时效钢中的非金属夹杂物研究

材 料 开 发 与 应 用2010年4月文章编号:1003-1545(2010)02-0018-05电渣重熔马氏体时效钢中的非金属夹杂物研究张 伟,徐玉松,陆敏松,李国一(江苏科技大学材料科学与工程学院,江苏镇江 212003)摘 要:本文应用电子扫描法(SE M +ED S)和金相法,对真空感应熔炼(V I M )及随后进行电渣重熔(ESR )的改进型18N i Nb 马氏体时效钢中的非金属夹杂物进行了定性和评级分析。
结果表明,电渣重熔对去除钢中的硫化物和尺寸较大的单颗粒夹杂效果明显,电渣重熔后钢中的夹杂物主要为细小的氧化物夹杂,数量明显减少、且呈弥散分布,进一步提高了18N i Nb 合金钢的钢锭质量。
关键词:18N i N b ;马氏体时效钢;电渣重熔;非金属夹杂物;纯净度中图分类号:TF 744 文献标识码:A收稿日期:2009-10-19作者简介:张伟,1984年生,男,汉族,江苏连云港人,硕士研究生,研究方向:有色金属冶金。
马氏体时效钢以无碳(或超低碳)铁镍马氏体为基体,400~550e 时效时能产生金属间化合物沉淀硬化的超高强度钢,广泛应用于航空、航天以及军事等尖端领域[1-3]。
作为超高强度钢最重要的性能指标是断裂韧性,而夹杂物含量对材料韧性有较大影响,为了减少杂质的含量,本文采用真空感应熔炼+电渣重熔的冶金工艺研究了改进型18N i N b 马氏体时效钢在不同工艺状态下的夹杂物形态及分布状况。
真空感应熔炼可以精确控制合金成分,并通过与气相有关的反应提高合金的纯净度,是目前超高强度合金钢的主要熔炼方法之一,电渣重熔则是广泛应用于优质钢生产的一种重熔工艺,它对去除钢中夹杂物和在钢锭凝固方面的优越性,对提高合金钢的机械性能,有明显的效果。
18N i 马氏体时效钢作为一种应用广泛的超高强高韧性钢,对其纯净度有更加苛刻的要求。
因为非金属夹杂物的弹性模量、变形能力等与合金基体都有很大的差别,容易造成应力集中,会促进疲劳裂纹的萌生和扩展,有些会导致严重的安全事故。
纯铁电渣重熔的碳和硫控制
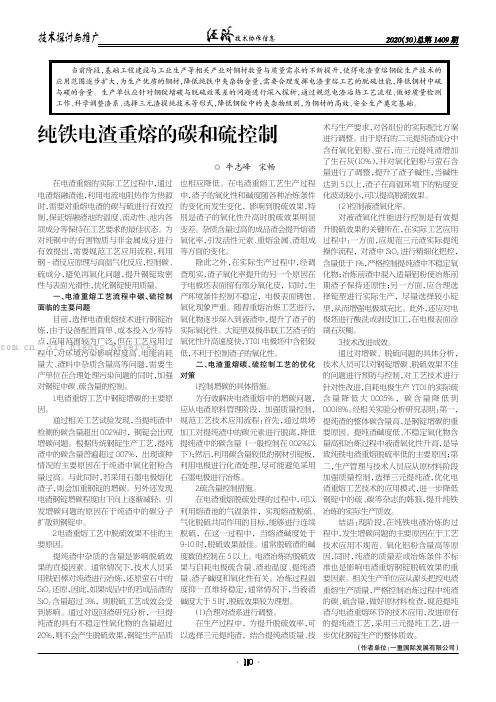
在电渣重熔的实际工艺过程中,通过电渣熔融渣池,利用电流电阻热作为热源时,需要对重熔电渣的碳与硫进行有效控制,保证熔融渣池的温度、流动性、池内各项成分等保持在工艺要求的最佳状态。
为对纯钢中的有害物质与非金属成分进行有效提出,需要规范工艺应用流程,利用钢-渣反应原理与高温气化反应,控制碳、硫成分,避免再氧化问题,提升钢锭致密性与表面光滑性,优化钢锭使用质量。
一、电渣重熔工艺流程中碳、硫控制面临的主要问题目前,选择电渣重熔技术进行钢锭冶炼,由于设备配置简单、成本投入少等特点,应用范围较为广泛,但在工艺应用过程中,对环境污染影响程度高、电能消耗量大、渣料中杂质含量高等问题,需要生产单位在合理处理污染问题的同时,加强对钢锭中碳、硫含量的控制。
1.电渣重熔工艺中钢锭增碳的主要原因。
通过相关工艺试验发现,当提纯渣中检测的碳含量超出0.02%时,钢锭会出现增碳问题。
根据传统钢锭生产工艺,提纯渣中的碳含量普遍超过0.07%,出现该种情况的主要原因在于纯渣中氧化铝粉含量过高。
与此同时,若采用石墨电极熔化渣子,则会加重钢锭的增碳。
另外还发现电渣钢锭增碳程度由下向上逐渐减轻。
引发增碳问题的原因在于纯渣中的碳分子扩散到钢锭中。
2.电渣重熔工艺中脱硫效果不佳的主要原因。
提纯渣中杂质的含量是影响脱硫效果的直接因素。
通常情况下,技术人员采用铁铝棒对纯渣进行冶炼,还原萤石中的SiO 2还原,因此,如果成品中的若成品渣的SiO 2含量超过3%,则脱硫工艺成效会受到影响。
通过对返回渣研究分析,一旦提纯渣的具有不稳定性氧化物的含量超过20%,则不会产生脱硫效果,钢锭生产品质也相应降低。
在电渣重熔工艺生产过程中,渣子的氧化性和碱度随各种冶炼条件的变化而发生变化,影响到脱硫效果,特别是渣子的氧化性升高时脱硫效果明显变差。
杂质含量过高的成品渣会提升熔渣氧化率,引发活性元素、重熔金属、渣组成等方面的变化。
除此之外,在实际生产过程中,经调查现实,渣子氧化率提升的另一个原因在于电极坯表面留有部分氧化皮,同时,生产环境条件控制不稳定,电极表面锈蚀、氧化现象严重。
钢中非金属夹杂对质量的影响及控制措施
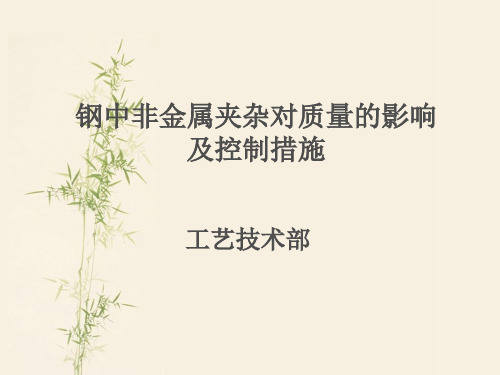
内生夹杂和外来夹杂有明显的差别
1)内生夹杂的典型特征是尺寸小,数目多,较均匀地分布在铸 坯的各个部位,夹杂物的成分与钢液成分有很强的依赖关系。 2)外来夹杂往往尺寸较大,形状不规则,具有偶发性,成分和 结构复杂,它与钢液成分没有直接关系,分布位置不定。 3)实际炼钢过程中的夹杂物很少为单纯的内生夹杂或外来夹杂 ,它们经常是共生的,其原因是: ⑴在炼钢过程中各阶段,内生夹杂以外来夹杂为核心析出,并 发生交互反应是一种普遍现象; ⑵脱氧的钢液与卷入的炉渣 (包括保护渣)或耐火材料接触时, 总会或多或少地起反应,因此仍保持原来的内生或外来夹杂 物的成分和结构是不多见的;
VN颗粒
VN颗粒
钙化处理硫化物
当非金属夹杂物尺寸大于50um时,降低了钢的塑性、韧性 和疲劳寿命,使钢的冷热加工性能乃至某些物理性能变坏。 一般 我们钢水中夹杂物尺寸都为大于50um。 大型夹杂物不利用钢板 韧性、塑性以及强度指标。除了这些性能外,还有降低抗酸性能、 疲劳性能、表面光洁度 以及焊接性能。
钢中非金属夹杂对质量的影响 及控制措施
工艺技术部
前言
研究重要意义
非金属夹杂物危害:
质量缺陷:
铸坯:表面裂纹,内部裂纹,偏析等; 钢材:裂纹,“翘皮”,线形缺陷等。
钢材性能:
冲压开裂、冷拉断裂等; 延性,低温韧性,抗疲劳破坏,非轧制方向性能,切 削,焊接,耐蚀,电磁性能等。
2
夹杂物控制技术发展趋势
氧化铝夹杂
冲击为3J P460NL1
夹杂+FeO夹杂
延伸 9
12Cr2Mo1VR
多处铝酸盐夹杂
16MnDR 探伤不合国标 I级
多处铝酸盐夹杂
冶金质量分析第六次四、钢中非金属夹杂物的

§3 钢中的金属杂质及冶金控制
——降低微量元素有害影响的方法(4)
(三)限制由原材料带入的有害元素数量 钢及合金中的有害元素往往是在炼钢过程中由原材料
(矿石、合金元素、废钢等)带入的。严格选择和控
制原材料中有害元素的含量水平,是降低钢与合金有 害元素含量的重要途径。
第四章 习题
1. 钢中氢氮对钢性能有何影响?如何减少钢液中 的氢和氮含量? 2. 钢中常见的非金属夹杂物来源于哪些方面?有 哪些类型和各有和特点? 3. 钢中的非金属夹杂物对钢性能有哪些影响?原 因何在? 4.如何改善和控制钢中的非金属夹杂物? 5. 微量有害元素对钢质量有何影响?如何控制? 举例说明。
第三章习题
电弧炉和氧气顶吹转炉在炼钢设备和操作上有何不同? 电弧炉炼钢法有何特点?为什么电弧炉钢中的磷、硫 和夹杂物含量一般低于转炉钢? 为什么氧气顶吹转炉炼钢速度最快? 感应炉熔炼有何特点?产品质量如何? 综合分析电弧炉、转炉钢的产品特点(产品范围、气 体含量、夹杂物数量及钢产量)? 不同炼钢方法的选用原则是什么?
①非金属夹杂物是非铁磁性相,它在钢中的存在减少了 铁磁性基体的体积分数,破坏了金属基体的连续性; ②夹杂物的存在(在晶界上或晶内)使钢基体内可能产 生内应力,因而基体磁化不均匀,磁性下降。 细小分散的夹杂物要比粗大聚集的夹杂物对磁性的危 害大; 长条的针状夹杂物比球状的危害大; 多角形铝的氧化物危害最大。
随 RE / S 比值的增加,夹杂物在钢材中的形态变 化顺序为:细长条MnS→变形能力较低的
(RE,,Mn)S→呈纺锤形的稀土硫氧化物RE2O2S→圆形
或碎块状不变形的稀土硫化物RE2S3或RE3S4→不规则 的点状或串状稀土硫化物RES。
二)钢中非金属夹杂物的控制
钢中非金属夹杂物的检测

钢中非金属夹杂物的检测一.概述非金属夹杂物是钢中不可避免的杂质,它的存在使金属基体的均匀连续性受到破坏。
非金属夹杂在钢中的形态、含量和分布情况都不同程度地影响着各种性能,诸如常规力学性能、疲劳性能、加工性能等。
因此,非金属夹杂物的测定与评定引起人们的普遍重视。
夹杂物的含量和分布状况等往往被认为是评定钢的冶金质量的一个重要指标,并被列为优质钢和高级钢的常规项目之一。
钢中非金属夹杂物按其来源和大小,大体可分为两大类:1.显微夹杂物或称内在夹杂物,这类夹杂物是钢冶炼和凝固过程中,由于一系列物理和化学反应所生成。
例如,在冶炼过程中,由于加入脱氧剂而形成氧化物和硅酸盐等。
这些夹杂物来不及完全上浮进入钢渣,而残留在钢液中,即为内在夹杂。
如:Al、Fe-si等脱氧剂可以形成下列夹杂:3FeO+2Al 3Fe+ Al2O32FeO+ Si SiO2+2FenFeO+mSiO2 nFeO·mSiO2nAl2O3+mSiO2 nAl2O3·mSiO2另外,钢在凝固冷却过程中,S、N等元素,由于溶解度的降低而生成硫化物、氮化物等也将残留在钢中。
2.宏观夹杂物或称外来夹杂物,这类夹杂物是在钢的冶炼或浇铸过程中,由于耐火材料等外来物混入造成。
其特点是大而无固定形状。
就对钢而言,宏观夹杂物的危害更大。
夹杂物的检验方法也有宏观检验法和显微检验法两种。
非金属夹杂物的显微检验法是指借助于金相显微镜在规定的实验条件下,检验金相试样中非金属夹杂物的方法。
该法的主要优点是可以确定夹杂物的类型、分布、数量和大小,可以发现极细小的夹杂物。
但是,由于受试样尺寸及取样位置、数量的限制。
所以显微检验法的评定结果在很大程度上存在偶然性。
往往会过分夸大细小夹杂物的重要性而将那些试样以外或检验面以外的较大夹杂物遗漏,所以,显微检验法总是与宏观检验法相辅相成、互相补充的。
如果非金属夹杂物的宏观检验对优质钢来说是必不可少的检验项目之一,那么显微检验法则是特殊用途钢(如轴承钢、重要用途的合金结构钢等)广泛采用的检验方法。
夹杂物分类,来源和降低钢中夹杂物含量的技术措施

夹杂物分类、来源和降低钢中夹杂物含量的技术措施冶093 孙苏皖099014200摘要:非金属夹杂物降低了钢的塑性、韧性和疲劳寿命,使钢的冷热加工性能乃至某些物理性能变坏,对钢的强度、延伸性、韧性、切削性、抗腐蚀性能、表面光洁度、焊接性能等各方面的性能有着直接的影响。
夹杂物对钢的性能影响的具体程度决定于一系列因素,比如夹杂物的数量、颗粒大小、形态及分布等。
关键词:挡渣出钢;中间包污染;二次氧化;结晶器液面波动一.钢中夹杂物的分类分类方法很多,但常见的有以下四种:1.按来源分类,可分为两类:(1)外来夹杂物:耐火材料、熔渣或两者的反应产物混入钢中并残留在钢中的颗粒夹杂称为外来夹杂。
包括从炉衬或包衬、或从汤道砖、中包绝热板、保护渣进入钢水中的夹杂物(有人还将钢水二次氧化生成的夹杂物包括在内)。
这类夹杂颗粒较大,易于上浮,但在钢中,它们的出现带着偶然性且不规则。
(2)内生夹杂物:在冶炼、浇注和凝固过程中,钢液、固体钢内进行着各种化学反应,对于在冶炼过程中所形成的化合物、脱氧时产生的脱氧产物、或在钢水凝固过程产生的化合物,当这些化合物来不及从钢水中彻底排出而残存在钢中者,叫做内在的非金属夹杂物。
内生夹杂物形成的时间可分为四个阶段:①一次夹杂(原生夹杂):钢液脱氧反应时生成的脱氧产物;②二次夹杂:在出钢和浇注过程中温度下降平衡移动时生成的夹杂物;③三次夹杂(再生夹杂):凝固过程中生成的夹杂;④四次夹杂:固态相变时因溶解度变化生成的夹杂。
一般说来外来夹杂物颗粒较大,在钢中比较集中,而内生夹杂物则与此相反。
从组成来看,内生夹杂物可以是简单组成,也可以是复杂组成;可以是单相的,也可以是多相的。
在铸坯凝固以及随后的冷却过程中,夹杂物不仅与钢基体保持平衡,而且夹杂物本身也不断发生改变,例如析出新的化合物以趋于稳定状态。
在轧制或热处理时,每次加热都为夹杂物和钢基体之间趋向平衡提供了条件,在室温下所观察到的夹杂物,实际上是经过了一系列复杂变化的结果。