高速线材表面质量缺陷的产生原因及排除方法
高速线材产品表面“裂纹”成因及判定
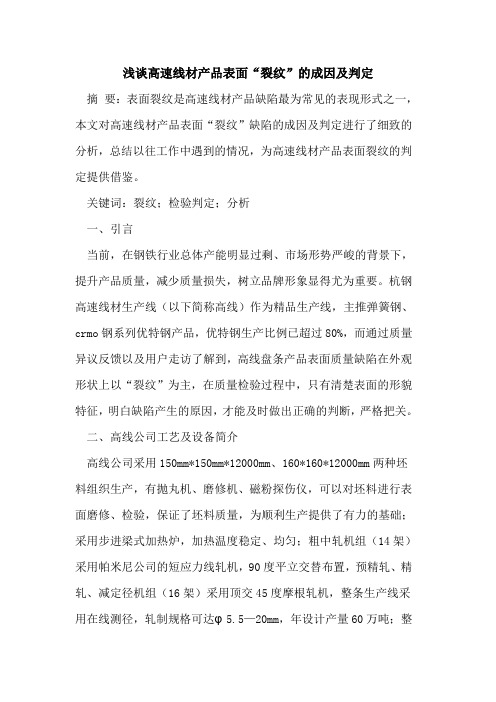
浅谈高速线材产品表面“裂纹”的成因及判定摘要:表面裂纹是高速线材产品缺陷最为常见的表现形式之一,本文对高速线材产品表面“裂纹”缺陷的成因及判定进行了细致的分析,总结以往工作中遇到的情况,为高速线材产品表面裂纹的判定提供借鉴。
关键词:裂纹;检验判定;分析一、引言当前,在钢铁行业总体产能明显过剩、市场形势严峻的背景下,提升产品质量,减少质量损失,树立品牌形象显得尤为重要。
杭钢高速线材生产线(以下简称高线)作为精品生产线,主推弹簧钢、crmo钢系列优特钢产品,优特钢生产比例已超过80%,而通过质量异议反馈以及用户走访了解到,高线盘条产品表面质量缺陷在外观形状上以“裂纹”为主,在质量检验过程中,只有清楚表面的形貌特征,明白缺陷产生的原因,才能及时做出正确的判断,严格把关。
二、高线公司工艺及设备简介高线公司采用150mm*150mm*12000mm、160*160*12000mm两种坯料组织生产,有抛丸机、磨修机、磁粉探伤仪,可以对坯料进行表面磨修、检验,保证了坯料质量,为顺利生产提供了有力的基础;采用步进梁式加热炉,加热温度稳定、均匀;粗中轧机组(14架)采用帕米尼公司的短应力线轧机,90度平立交替布置,预精轧、精轧、减定径机组(16架)采用顶交45度摩根轧机,整条生产线采用在线测径,轧制规格可达φ5.5—20mm,年设计产量60万吨;整条轧线设置有3把飞剪,起到剪切头尾及故障时的剪碎的作用,同时配备5段冷却水箱,控制轧件温度;散卷冷却采用斯泰尔摩控制冷却线,最后通过集卷机集卷后上p/f输送线,完成打包、称重、贴牌入库。
主要工艺流程如下:坯料准备→入炉、加热→出炉→高压水除鳞→粗轧→1#飞剪→中轧→2#飞剪→预精轧→1#水箱→3#飞剪→精轧→2、3#水箱→减定径→涡流探伤→4#水箱→测径仪→5#水箱→吐丝机→斯泰尔摩运输线→集卷→p/f输送线→检验、取样、切头尾→打捆→称重、挂牌→入库三、缺陷分布及检验情况高线盘条产品涉及16个规格,40多个钢种,以弹簧钢、crmo类钢等优特钢为主。
棒线材表面缺陷产生原因及消除方法

棒线材表⾯缺陷产⽣原因及消除⽅法线材⽿⼦产⽣原因及消除⽅法线材表⾯沿轧制⽅向的条状凸起称为⽿⼦,有单边⽿⼦也有双边⽿⼦。
⾼速线材轧机⽣产中由于张⼒原因,产品头尾两端很难避免⽿⼦的产⽣。
有下述情况时容易产⽣⽿⼦:(1)轧槽与导卫板安装不正;(2)轧制温度的波动较⼤或不均匀较严重,影响轧件的宽展量;(3)坯料的缺陷,如缩孔、偏析、分层及外来夹杂物,影响轧件的正常变形;(4)来料尺⼨过⼤。
预防及消除⽅法如下:(1)正确安装和调整⼊⼝导卫;(2)提⾼钢坯加热质量,控制好轧制温度;(3)合理调整张⼒;(4)控制来料尺⼨。
线材表⾯的凸起及压痕(轧疤)形成的原因线材表⾯连续出现周期性的凸起或凹下的印痕,缺陷形状、⼤⼩相似。
凸起及压痕主要是轧槽损坏(掉⾁或结瘤)造成的。
线材产品检验项⽬及影响尺⼨精度的主要因素线材产品检验包括六项内容:外形尺⼨,压扁实验,含碳量⽐较,快速碳分析,⼒学性能试验和⾼倍检验。
影响线材尺⼨精度有以下主要因素:有温度、张⼒,孔型设计、轧辊及⼯艺装备的加⼯精度、孔槽及导卫的磨损、导卫板安装和轧机的机座刚度、调整精度、轧辊轴承的可靠性和电传控制⽔平和精度等。
其中张⼒是影响线材产品尺⼨精度的最主要因数。
在轧制线材的过程中尽可能实现微张⼒或⽆张⼒轧制是⾼速线材轧制的宗旨。
孔型设计与轧件精度也有密切关系,⼀般讲椭圆—⽴椭圆孔型系列消差作⽤⽐较显著;⼩辊径可以减少宽展量,其消差作⽤⽐⼤辊径好。
孔型设计中应特别注意轧件尺⼨变化后的孔型适应性,即变形的稳定性、不扭转不倒钢不改变变形⽅位。
线材裂纹产⽣的原因及预防⽅法裂纹在线材中的分布是不连续的,垂直于线材表⾯或呈⼀⾓度陷⼊线材。
裂纹长短不⼀,通常呈直线形,偶尔也有横向裂纹或龟裂。
由钢坯上的缺陷经轧制后形成的裂纹常伴有氧化质点、脱碳现象,裂纹中间常存在氧化亚铁;由轧后控冷不当形成的裂纹⽆脱碳现象伴⽣,裂缝中⼀般⽆氧化亚铁,多呈横裂或龟裂。
从炼钢到轧钢都有可能产⽣裂纹。
高线盘条表面结疤缺陷初探
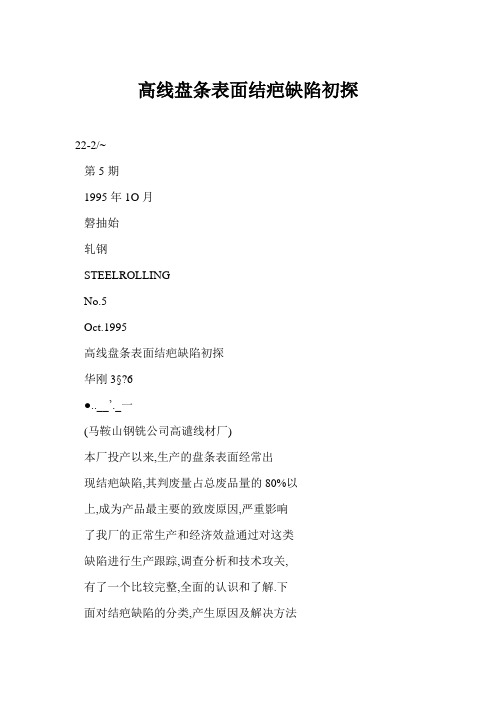
高线盘条表面结疤缺陷初探22-2/~第5期1995年1O月磐抽始轧钢STEELROLLINGNo.5Oct.1995高线盘条表面结疤缺陷初探华刚3§?6●..__’._一(马鞍山钢铣公司高谴线材厂)本厂投产以来,生产的盘条表面经常出现结疤缺陷,其判废量占总废品量的80%以上,成为产品最主要的致废原因,严重影响了我厂的正常生产和经济效益通过对这类缺陷进行生产跟踪,调查分析和技术攻关,有了一个比较完整,全面的认识和了解.下面对结疤缺陷的分类,产生原因及解决方法作一初步分析和探讨..1冶废结癌.原料钢坯内在或表面缺路造成的盘条结疤废品称为冶废结疤(台开坯轧制缺陷造成的结疤废品).I.I愿料缺陷.常见的原料缺陷有蛆下几种t①大块结疤;这种结疤一般有手掌大小,被压入钢坯表面或部分压入钢坯表面. @角部结疤:这种缺陷呈鱼鳞状连续或断续分布在钢坯的角部位置,大小不等,多为大部分压入角部,小部分翘起状.③面部小块结疤.这种缺陷为小块结疤压入钢坯,也有的呈翘起状.此种结疤呈连续或断续的.-④夹杂;有表面和钢坯内部夹杂两种.前一种夹杂在钢坯表面呈小块异色,多单独出现,也有几块连续出现的,表面看缺陷很小,但有一定深度.后一种夹杂为炼钢不良或切头不净所致.轧制后缺陷有时会呈现出来形成表面结疤.⑤表面清理不良;这种缺陷主要为火焰清理不干净,或清理时溶渣未吹净面被翻向两边,或在清理过程中钢坯某处被饶成较深凹坑-⑤凹坑:这种缺陷多为大块结疤在轧制过程中脱落而形成,此缺陷多单独出现,也有的在凹垸前后存在着连续的小块结疤.⑦气囊;由于在轧制过程中钢锭内部气囊没有被篷台而残留在钢坯内部.⑧裂缝,裂纹:钢坯表丽有较长裂纹,而且有一定深度.⑧耳子:这种缺艏多在钢坯的头尾部分.长度在lm以内,单边耳子居多.@折叠;折叠多呈面通条.仔细观察会发现在钢坯纵向某一直线上有隐约连续或麟续的裂纹面在钢坯断面上能看出裂纹与钢坯表面成夹角.2盘条冶废结绝一2.I点状弥散型细小结疤①敏蹈状态;.在线材表面弥散.附着约0.5~2聃m的细小薄层结疤,一般无根,在成品盘卷上几十圈至上百圈无规律断续分布,用手触摸略刮手,用劲擦拭会脱落留下疤痕.这种缺陷往往成批出现,数量很大.对于缺陷深度小于0.15ram的盘卷—般不判废,对于缺陷密集,深度超过负偏差的盘卷必须判废.②相对应的原料缺陷.面部小块结疤|角部小块结疤}表面清理不良}夹杂}钢坯氧化铁皮厚.@金相检验t凹坑的边上有块横向的折叠,其夹缝中的夹杂经船谱改鉴定为氧化铁皮并且,线材表面斯续地篷了一层很薄的皮.④成因分析;由于原料钢坯表面的小块?23?结疤等缺陷深度大于lmm,而我厂加热炉内烧损厚度只有0.3ram,这样原料缺陷不可避免地产生于成品表面.随着轧件的延伸而成弥散分布.另外,有时此种缺陷整批号,整炉号出现,可能与钢的内在质量不良有关2.2块状无根结疤①缺陷形态,线材袭面附着大块结疤,其边缘清晰,丽形状,大小不一,结疤底部与基体不粘连,在成品表面分布无规律.②相对应的原料缺陷t面部大块结疤,角部大结疤.⑧金相检验:结疤与基体之间有氧化铁皮存在,见图1.圉1结疤与基体之间的氧化铁皮x5O④成因分析:原料上的大块结疤经多道次轧制,随着轧件延伸和细化.由于结疤部份冷却软快,比轧件的变形系数小,不会细化得更小,因此作为大块结疤压入轧件.23凹坑,①缺陷形态:线材表面有形状,大小不完全相同的凹坑,凹境底部凹凸不平,深浅不一.这种缺陷通常与大块结疤同时出现.③相对应的原料缺陷;大块而部结疤,大块角部结疤,内部夹杂.③成因分析:原料带来的大块结疤在轧制过程中被压凡轧件表面,直到最后1~2 道次轧制或在吐丝机成圈时脱落,使得线材表面留下凹坑.丽另一些结疤没有脱落,形成凹坑与结疤共存的现象.24锯齿状结疤①缺陷形态线材表面出现很长一条结癌J其一与基体相连,另一侧翘起或压台在线材表面,这都份翘起或压台的边缘呈锯齿状.这种缺陷往往十几圈甚至上百圈连续出现,但盘卷其它部份表面良好.②相对应的原料缺陷t钢坯表面裂缝或裂纹,气囊,耳子,折叠.③金相检验:结疤根部与基体相连,其余部分与基体分离,呈裂口状,裂口两侧伴有轻微脱碳层,见图2.图2结疤根郭以外的部分呈裂口状×5O④成因分析,在轧制过程中.裂缝,折叠和耳子经过几道轧制呈折叠状.经过多次延伸后,折叠顶部较薄的部份出现撕裂,呈锯齿状粘着在成品表面.,?较厚的部分仍与机体相连.钢坯内部气囊在轧制过程中,搜被压合的部分被拉长,经过多次延伸后被移至轧件表面,破裂后呈折叠状.较薄的部分被撕裂呈锯齿状特着在成品表面|较厚的部分仍与机体相连.2.5翘皮状有根结疤①缺陷形态在线材表面出现的块状结疤一侧翘起,另一侧与基体相连,是有根鳍疤,其形状和大小不一致,在成品上一般相对集中出现在1圈至l0几圈上.②裙应的原斟缺陷:面部和角部的大块有根结疤,海理不良,夹杂.③金相检验:缺陷一部分与机体相连,翘起部分延续较长,中间夹着氧化铁皮,见图3口?24?图3翘皮状有根结疤踺陷的形态×100④成因分析:与块状结癌成困相似,是由于钢坯表面的大块有根结疤经轧制延伸而断裂形成的}钢坯清理不良也会形成这种缺陷.另外,钢坯内部夹杂在轧制中延伸并逐渐在表面上暴露出来,也会造成这种结疤.以上5种冶废结疤的共同特征是发生部位无规律,外貌不一致,不相似,大小,深浅不一.这是区别于轧制结疤最主要的依据.2轧废结疱生产过程中因设备,技术,操作等原因形成的结疤缺陷称为轧废结疤.典型的轧废结疤有以下几种.2.I周期性块状结疤①缺陷形态;线材表面上有抉状结疤.有时被完全压入线材表面以内.表面可见较清晰的结疤边缘曲线}有时略凸起在表面之上,成为凸块.结疤外貌形状和大小基本一致.在盘条上周期性发生.此种结疤为有根结疤,一般在某一轧线上连续发生,直至停机为止.②成困分析:这种结疤是由精轧机组辊环轧槽掉肉或辊环轧槽横向断裂.在轧件上造成凸块,被后续道次压入轧件表面所造成.根据辊环掉肉或断裂所处机架不同.结疤的大小和深浅及边缘清晰程度也不相同. 靠近成品道次的结疤较为明显.反之则结疤较大,压入较深,只可见边缘曲线.如果是成晶孔辊环掉肉或断裂,则在线材上只留下掉肉外貌极相似的凸块结疤发生的周期与该辊环直径和后几道延伸系数成正比. ③预防方法,经常检查辊环的使用情况,发现有纵向裂纹立刻更换定期检查冷却水的水质和辊环玲却水嘴,保证其畅通,减少裂纹和掉肉的发生.2.2锯齿状结疤①缺陷形态:在线材表面一铡或两侧连续出现结疤,结疤的一边与基体相连.另一边翘起或不压合在线材表面.其边缘呈锯齿状.选种缺陷在外貌上看与冶废锯齿状结疤基本相同,两者的区别仅在于轧废锯齿状结疤在盘卷上连续出现,并且在某一轧线上连续发生J而冶废锯齿结疤只在盘卷的十几圈至几十圈范围内,其它表面良好,而且不是连续发生.②成因分析;这种陷主要是瘩于轧辊轴向错位(即错辊),进口导卫装偏及进口导卫破碎等原因造成轧件单边或双边耳予, 经后几道轧成折叠再延伸拉裂而成锯齿状. @预防方法:防止轧辊错位.在安装进口导卫时防止导卫装偏,以及及时检查成品表面质量.’2.3点状结疤(粘钢结疤)①缺陷形态:在线材成品辊缝处单侧或双制附着点状细小结疤,或连续或断续.这种缺陷外貌上与冶废点状弥散结疤相似}区别在于轧废点状结疤一般只出现于成品辊缝处,并且通常在某一条精轧线上连续出现} 面冶废点状结疤则孙敖分布于线材表面.没有固定位置.②成因分析:主要是成品机架进口导卫粘钢所致.⑧预防方法:更换新导卫或减小成品道次的来料面积此种缺陷的判断有一定的难度,容易与冶废点状弥散型结疤相混.以上3种乳废结疤缺陷,其共同特点是缺陷形貌的相似性和周期性.n995年7月收修改稿)。
高速线材产品外部质量控制

高速线材产品外部质量控制路炜温东张家口宣龙高速线材有限责任公司075100摘要:简述高速线材产品外部质量要求,分析高速线材产品质量要求中精度、耳子、折叠、麻面、划痕、分层、裂纹、结疤等缺陷产生的原因,并根据生产实际提出相应的防止措施。
关键词:高速线材外部质量要求缺陷防止措施1 前言高速线材热轧盘条是热轧型钢截面尺寸最小的一种,由于截面积小、轧制道次多、盘卷供货、控冷工艺复杂,所以给产品的质量控制增加了难度。
宣钢高线厂从2001年第一条生产线投产,发展到今天拥有两条“精品线材”生产线、一条高强度大盘卷棒线材生产线。
在企业发展壮大的同时,积累了丰富的生产技术经验。
以下对线材产品外部质量控制及一些措施进行论述。
2 产品外部质量要求2.1精度:直径偏差和不圆度(见附表)附表:直径偏差和不圆度2.2表面质量钢材的表面是否有不允许存在的冶金缺陷,不得有耳子、折叠、麻面、划痕、分层、裂纹、结疤等缺陷。
3 缺陷产生的原因3.1 产品尺寸精度超差3.1.1允许直径偏差超标:(1)换辊、换槽后试轧时,成品架次压下量不足(辊缝值过大)及成品前架次的辊缝值调整不当都会使直径偏差过大。
(2)钢坯加热温度不均匀,轧件温度过低(主要指头、尾部)也会时允许偏差超差。
3.1.2不圆度超差:(1)换辊、槽后试轧时,成品架辊缝设定不当及成品前来料尺寸不合适,造成成品孔槽轧件未充满。
(2)试轧时,粗、中轧机架速度不匹配,造成机架间拉钢,也会使不圆度超差。
(3)轧制过程中,成品架入口滚动导卫轮烧坏及长时间轧制后轧槽磨损。
(4)成品架次错辊。
3.2 表面质量3.2.1 耳子线材表面平行与长度方向的条状凸起,产生于一侧为单边耳子,双侧尾双边儿子,断面上、下两个半圆错开的叫错边耳子。
3.2.1.1耳子产生的根本原因有以下几点:(1)过充满:前孔来料尺寸过大,到后架轧机充满轧制而形成耳子,调整时应把我好各架轧机的充满度,正确合理的调整辊缝,对于精轧机应该合理调整首架辊缝。
低碳钢高速线材的表面缺陷及冷镦开裂原因分析

理化检验 - 物理分册
杨卓青等 :一种新的钝化线形式
出了一种新的钝化 线形 式 ———J = 2 K ( 0. 5εF ) n · Δa ,该方程与材料的实测钝化线吻合较好 。
参考文献 :
[ 1 ] Begley J A , Landes J D. The J2Integral as a Fract ure Criterion[ A ] . Fract ure To ughness Proceeding of t he 1971 National Sympo sium o n Fract ure Mechanics , Part Ⅱ[ C ] . U SA : ASTM STP 514 , 1972. 1 - 20.
near cracks
图 5 线材表面平行裂纹形貌 Fig. 5 Parallel cracks appearance o n wire surface
图 3 线材表面单道线缺陷形貌 Fig. 3 Single liner defect s appearance o n wire surface
理化检验 - 物理分册
曾强国 :低碳钢高速线材的表面缺陷及冷镦开裂原因分析
样品
图2 图4 图6 图7 图8 图 10
Fe 29. 7 61. 8 92. 5 37. 6 11. 7 82. 0
表 1 各样品能谱微区成分分析结果
Tab. 1 Chemical compo sitio n of EDS micro2zone analyzing of each sample
关键词 : 低碳钢 ; 线材 ; 冷镦 ; 开裂
中图分类号 : T G356. 4 文献标识码 : A 文章编号 : 100124012 (2005) 0220069203
线材表面缺陷发生原因分析及其减少措施
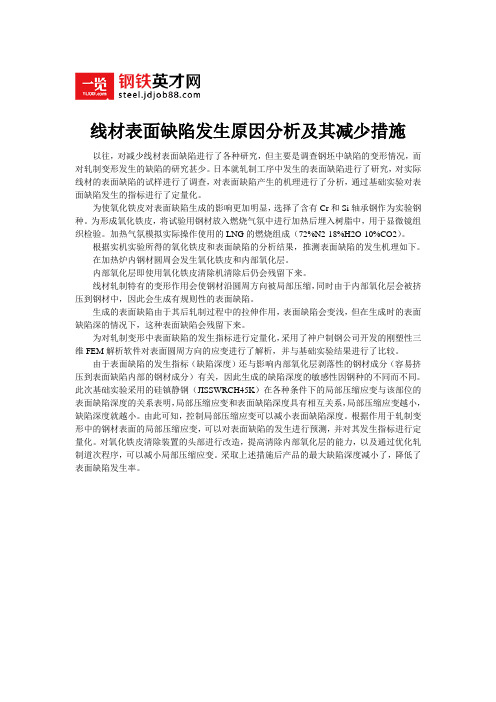
线材表面缺陷发生原因分析及其减少措施以往,对减少线材表面缺陷进行了各种研究,但主要是调查钢坯中缺陷的变形情况,而对轧制变形发生的缺陷的研究甚少。
日本就轧制工序中发生的表面缺陷进行了研究,对实际线材的表面缺陷的试样进行了调查,对表面缺陷产生的机理进行了分析,通过基础实验对表面缺陷发生的指标进行了定量化。
为使氧化铁皮对表面缺陷生成的影响更加明显,选择了含有Cr和Si轴承钢作为实验钢种。
为形成氧化铁皮,将试验用钢材放入燃烧气氛中进行加热后埋入树脂中,用于显微镜组织检验。
加热气氛模拟实际操作使用的LNG的燃烧组成(72%N2-18%H2O-10%CO2)。
根据实机实验所得的氧化铁皮和表面缺陷的分析结果,推测表面缺陷的发生机理如下。
在加热炉内钢材圆周会发生氧化铁皮和内部氧化层。
内部氧化层即使用氧化铁皮清除机清除后仍会残留下来。
线材轧制特有的变形作用会使钢材沿圆周方向被局部压缩,同时由于内部氧化层会被挤压到钢材中,因此会生成有规则性的表面缺陷。
生成的表面缺陷由于其后轧制过程中的拉伸作用,表面缺陷会变浅,但在生成时的表面缺陷深的情况下,这种表面缺陷会残留下来。
为对轧制变形中表面缺陷的发生指标进行定量化,采用了神户制钢公司开发的刚塑性三维FEM解析软件对表面圆周方向的应变进行了解析,并与基础实验结果进行了比较。
由于表面缺陷的发生指标(缺陷深度)还与影响内部氧化层剥落性的钢材成分(容易挤压到表面缺陷内部的钢材成分)有关,因此生成的缺陷深度的敏感性因钢种的不同而不同。
此次基础实验采用的硅镇静钢(JISSWRCH45K)在各种条件下的局部压缩应变与该部位的表面缺陷深度的关系表明,局部压缩应变和表面缺陷深度具有相互关系,局部压缩应变越小,缺陷深度就越小。
由此可知,控制局部压缩应变可以减小表面缺陷深度。
根据作用于轧制变形中的钢材表面的局部压缩应变,可以对表面缺陷的发生进行预测,并对其发生指标进行定量化。
对氧化铁皮清除装置的头部进行改造,提高清除内部氧化层的能力,以及通过优化轧制道次程序,可以减小局部压缩应变。
高速线材生产中的产品缺陷分析
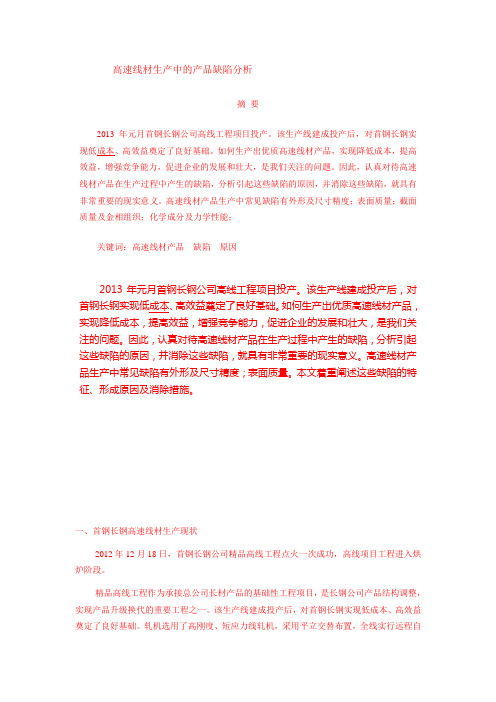
高速线材生产中的产品缺陷分析摘要2013年元月首钢长钢公司高线工程项目投产。
该生产线建成投产后,对首钢长钢实现低成本、高效益奠定了良好基础。
如何生产出优质高速线材产品,实现降低成本,提高效益,增强竞争能力,促进企业的发展和壮大,是我们关注的问题。
因此,认真对待高速线材产品在生产过程中产生的缺陷,分析引起这些缺陷的原因,并消除这些缺陷,就具有非常重要的现实意义。
高速线材产品生产中常见缺陷有外形及尺寸精度;表面质量;截面质量及金相组织;化学成分及力学性能;关键词:高速线材产品缺陷原因2013年元月首钢长钢公司高线工程项目投产。
该生产线建成投产后,对首钢长钢实现低成本、高效益奠定了良好基础。
如何生产出优质高速线材产品,实现降低成本,提高效益,增强竞争能力,促进企业的发展和壮大,是我们关注的问题。
因此,认真对待高速线材产品在生产过程中产生的缺陷,分析引起这些缺陷的原因,并消除这些缺陷,就具有非常重要的现实意义。
高速线材产品生产中常见缺陷有外形及尺寸精度;表面质量。
本文着重阐述这些缺陷的特征、形成原因及消除措施。
一、首钢长钢高速线材生产现状2012年12月18日,首钢长钢公司精品高线工程点火一次成功,高线项目工程进入烘炉阶段。
精品高线工程作为承接总公司长材产品的基础性工程项目,是长钢公司产品结构调整,实现产品升级换代的重要工程之一。
该生产线建成投产后,对首钢长钢实现低成本、高效益奠定了良好基础。
轧机选用了高刚度、短应力线轧机,采用平立交替布置,全线实行远程自动化控制,工艺装备达到了国际先进水平。
加热炉采用蓄热式高温燃烧技术,双层框架斜坡滚轮式炉底步进机械,热工自动化控制系统采用了国内先进技术,比常规加热炉节能45%。
轧机机组传动采用Siemens的SIMOREC-K全数字直流传动装置,所有传动电器均采用变频控制节能技术和无功补偿技术,节电率达35%以上,工业用水100%循环利用,实现零排放。
该工程项目于2013年元月份投产,可实现年产110万吨精品线材,主要产品品种有φ5.5—25mm全系列精品线材及中碳钢、高碳预应力钢丝及钢绞线、冷镦钢、爆破线、合金焊线等线材产品,可实现工业产值75亿元以上。
高速线材表面质量缺陷及控制措施
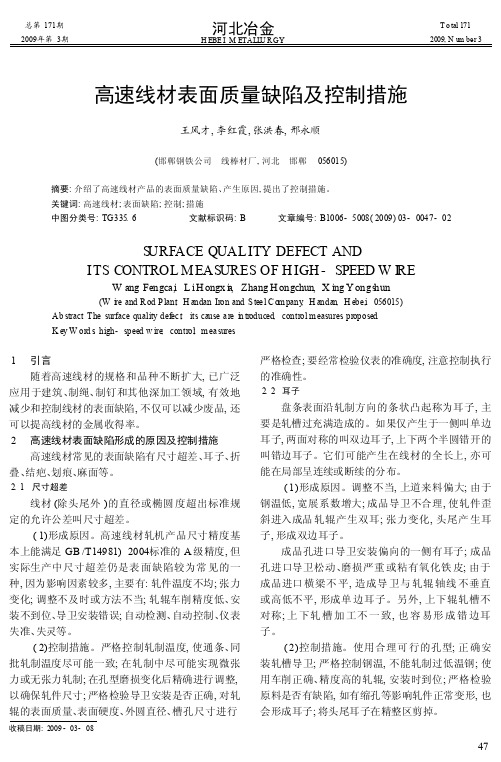
总第171期2009年第3期河北冶金H EBE I M ETALL U RGYT o tal1712009,N u m ber3收稿日期:2009-03-08高速线材表面质量缺陷及控制措施王风才,李红霞,张洪春,邢永顺(邯郸钢铁公司线棒材厂,河北邯郸056015)摘要:介绍了高速线材产品的表面质量缺陷、产生原因,提出了控制措施。
关键词:高速线材;表面缺陷;控制;措施中图分类号:TG335.6文献标识码:B文章编号:B1006-5008(2009)03-0047-02 S URF ACE QUALITY DEFECT ANDITS CONTROL MEAS URES OF H IGH-SPEED W I RE W ang Fengca,i L iH ongx i a,Zhang H ongchun,X ing Y ongs hun(W i re and R od P lan,t H andan Iron and S tee l C o m pany,H andan,H ebe,i056015)Ab strac:t The surface quality defec,t its cause a re i n troduced,control m easures proposed.K ey W ord s:high-speed w ire;contro;l m ea sures1引言随着高速线材的规格和品种不断扩大,已广泛应用于建筑、制绳、制钉和其他深加工领域,有效地减少和控制线材的表面缺陷,不仅可以减少废品,还可以提高线材的金属收得率。
2高速线材表面缺陷形成的原因及控制措施高速线材常见的表面缺陷有尺寸超差、耳子、折叠、结疤、划痕、麻面等。
2.1尺寸超差线材(除头尾外)的直径或椭圆度超出标准规定的允许公差叫尺寸超差。
(1)形成原因。
高速线材轧机产品尺寸精度基本上能满足GB/T14981)2004标准的A级精度,但实际生产中尺寸超差仍是表面缺陷较为常见的一种,因为影响因素较多,主要有:轧件温度不均;张力变化;调整不及时或方法不当;轧辊车削精度低、安装不到位、导卫安装错误;自动检测、自动控制、仪表失准、失灵等。
线材质量常见五大问题及措施.doc
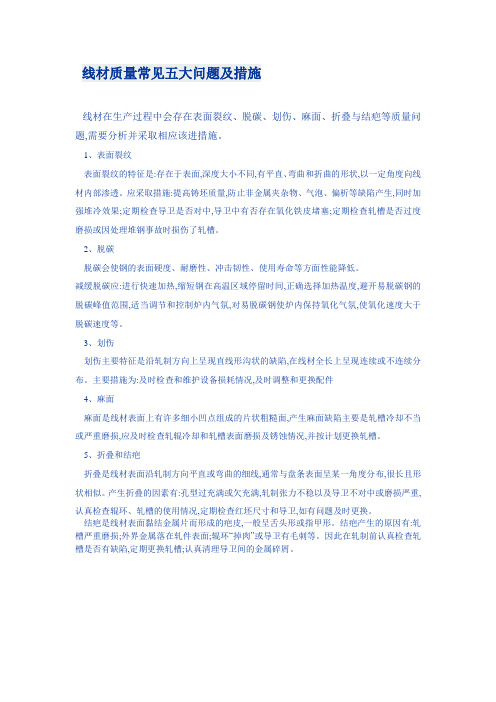
线材质量常见五大问题及措施线材在生产过程中会存在表面裂纹、脱碳、划伤、麻面、折叠与结疤等质量问题,需要分析并采取相应该进措施。
1、表面裂纹表面裂纹的特征是:存在于表面,深度大小不同,有平直、弯曲和折曲的形状,以一定角度向线材内部渗透。
应采取措施:提高铸坯质量,防止非金属夹杂物、气泡、偏析等缺陷产生,同时加强堆冷效果;定期检查导卫是否对中,导卫中有否存在氧化铁皮堵塞;定期检查轧槽是否过度磨损或因处理堆钢事故时损伤了轧槽。
2、脱碳脱碳会使钢的表面硬度、耐磨性、冲击韧性、使用寿命等方面性能降低。
减缓脱碳应:进行快速加热,缩短钢在高温区域停留时间,正确选择加热温度,避开易脱碳钢的脱碳峰值范围,适当调节和控制炉内气氛,对易脱碳钢使炉内保持氧化气氛,使氧化速度大于脱碳速度等。
3、划伤划伤主要特征是沿轧制方向上呈现直线形沟状的缺陷,在线材全长上呈现连续或不连续分布。
主要措施为:及时检查和维护设备损耗情况,及时调整和更换配件4、麻面麻面是线材表面上有许多细小凹点组成的片状粗糙面,产生麻面缺陷主要是轧槽冷却不当或严重磨损,应及时检查轧辊冷却和轧槽表面磨损及锈蚀情况,并按计划更换轧槽。
5、折叠和结疤折叠是线材表面沿轧制方向平直或弯曲的细线,通常与盘条表面呈某一角度分布,很长且形状相似。
产生折叠的因素有:孔型过充满或欠充满,轧制张力不稳以及导卫不对中或磨损严重,认真检查辊环、轧槽的使用情况,定期检查红坯尺寸和导卫,如有问题及时更换。
结疤是线材表面黏结金属片而形成的疤皮,一般呈舌头形或指甲形。
结疤产生的原因有:轧槽严重磨损;外界金属落在轧件表面;辊环“掉肉”或导卫有毛刺等。
因此在轧制前认真检查轧槽是否有缺陷,定期更换轧槽;认真清理导卫间的金属碎屑。
高速线材生产中的质量控制策略分析
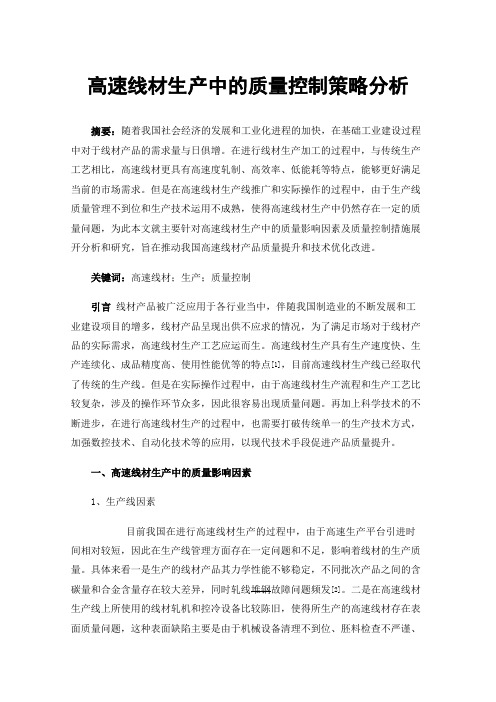
高速线材生产中的质量控制策略分析摘要:随着我国社会经济的发展和工业化进程的加快,在基础工业建设过程中对于线材产品的需求量与日俱增。
在进行线材生产加工的过程中,与传统生产工艺相比,高速线材更具有高速度轧制、高效率、低能耗等特点,能够更好满足当前的市场需求。
但是在高速线材生产线推广和实际操作的过程中,由于生产线质量管理不到位和生产技术运用不成熟,使得高速线材生产中仍然存在一定的质量问题,为此本文就主要针对高速线材生产中的质量影响因素及质量控制措施展开分析和研究,旨在推动我国高速线材产品质量提升和技术优化改进。
关键词:高速线材;生产;质量控制引言线材产品被广泛应用于各行业当中,伴随我国制造业的不断发展和工业建设项目的增多,线材产品呈现出供不应求的情况,为了满足市场对于线材产品的实际需求,高速线材生产工艺应运而生。
高速线材生产具有生产速度快、生产连续化、成品精度高、使用性能优等的特点[1],目前高速线材生产线已经取代了传统的生产线。
但是在实际操作过程中,由于高速线材生产流程和生产工艺比较复杂,涉及的操作环节众多,因此很容易出现质量问题。
再加上科学技术的不断进步,在进行高速线材生产的过程中,也需要打破传统单一的生产技术方式,加强数控技术、自动化技术等的应用,以现代技术手段促进产品质量提升。
一、高速线材生产中的质量影响因素1、生产线因素目前我国在进行高速线材生产的过程中,由于高速生产平台引进时间相对较短,因此在生产线管理方面存在一定问题和不足,影响着线材的生产质量。
具体来看一是生产的线材产品其力学性能不够稳定,不同批次产品之间的含碳量和合金含量存在较大差异,同时轧线堆钢故障问题频发[2]。
二是在高速线材生产线上所使用的线材轧机和控冷设备比较陈旧,使得所生产的高速线材存在表面质量问题,这种表面缺陷主要是由于机械设备清理不到位、胚料检查不严谨、加热轧制以及精整工艺不到位造成的。
三是生产线人员专业能力及综合素质有待提升,高速线材生产对于相关岗位工作人员提出了更高的要求,人员的操作技能水平直接影响着高速线材的生产质量,但是就实际情况来不少工作人员存在操作不规范等的情况,一定程度上增加了产品的质量控制风险。
高速线材表面结疤成因探讨

第32卷 第4期金 属 制 品2006年8月 Vol 132 No 14Steel W ire Pr oducts August 2006高速线材表面结疤成因探讨胡封轩 付军红 周桂兰(安阳钢铁集团公司 455004)摘 要 介绍安钢高速线材表面点状弥散型细小结疤、块状无根结疤、翘皮状有根结疤、点状结疤、锯齿状结疤、周期性块状结疤的鉴别和形成原因,提出稳定连铸坯拉速、降低钢水过热度、提高钢水质量及连铸操作水平,使铸坯的表面和内在质量全面提高,是解决高速线材表面结疤缺陷的关键所在。
关键词 高速线材;结疤;铸坯中图分类号 TG335.6+3I nqu i re i n to Surface Scabb i n g Cause of H i gh Speed SteelW i re RodHu Fe ngxuan Fu J unho ng Zho u Gu il a n(A nyang Iron and S teel Group Co . 455004)Abstract To intr oduce the distinguishing and f or mati on cause of such scabs as point dis persi on tiny,bl ock without r oot,turnup skin with r oot,point type,sa wt ooth,peri od bl ock on the surface of wire r od made in Angang high s peed wire r od m ill .It is pointed out that stabilizing pulling steel s peed of continuous cast billet,reducing over 2heating degree of molten steel ,raising molten steel quality and operati on level of continuous cast t o make the surface and internal quality of continu 2ous billet all raise are keys t o settling surface scab defect of high s peed wire r od .Keywords high s peed wire r od;scab;cast billet 线材表面的结疤缺陷,是安阳钢铁公司高线产品一次合格率偏低的主要原因,影响轧机的正常生产和经济效益。
线材产品质量缺陷
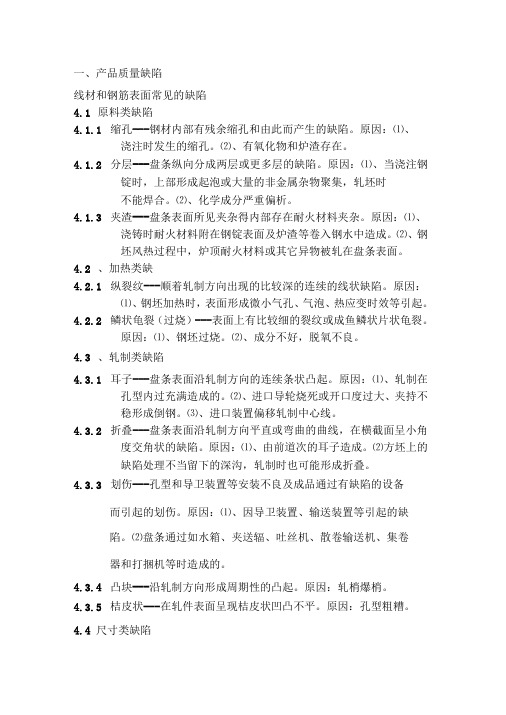
一、产品质量缺陷线材和钢筋表面常见的缺陷4.1原料类缺陷4.1.1缩孔---钢材内部有残余缩孔和由此而产生的缺陷。
原因:⑴、浇注时发生的缩孔。
⑵、有氧化物和炉渣存在。
4.1.2分层---盘条纵向分成两层或更多层的缺陷。
原因:⑴、当浇注钢锭时,上部形成起泡或大量的非金属杂物聚集,轧坯时不能焊合。
⑵、化学成分严重偏析。
4.1.3夹渣---盘条表面所见夹杂得内部存在耐火材料夹杂。
原因:⑴、浇铸时耐火材料附在钢锭表面及炉渣等卷入钢水中造成。
⑵、钢坯风热过程中,炉顶耐火材料或其它异物被轧在盘条表面。
4.2、加热类缺4.2.1纵裂纹---顺着轧制方向出现的比较深的连续的线状缺陷。
原因:⑴、钢坯加热时,表面形成微小气孔、气泡、热应变时效等引起。
4.2.2鳞状龟裂(过烧)---表面上有比较细的裂纹或成鱼鳞状片状龟裂。
原因:⑴、钢坯过烧。
⑵、成分不好,脱氧不良。
4.3、轧制类缺陷4.3.1耳子---盘条表面沿轧制方向的连续条状凸起。
原因:⑴、轧制在孔型内过充满造成的。
⑵、进口导轮烧死或开口度过大、夹持不稳形成倒钢。
⑶、进口装置偏移轧制中心线。
4.3.2折叠---盘条表面沿轧制方向平直或弯曲的曲线,在横截面呈小角度交角状的缺陷。
原因:⑴、由前道次的耳子造成。
⑵方坯上的缺陷处理不当留下的深沟,轧制时也可能形成折叠。
4.3.3划伤---孔型和导卫装置等安装不良及成品通过有缺陷的设备而引起的划伤。
原因:⑴、因导卫装置、输送装置等引起的缺陷。
⑵盘条通过如水箱、夹送辐、吐丝机、散卷输送机、集卷器和打捆机等时造成的。
4.3.4凸块---沿轧制方向形成周期性的凸起。
原因:轧梢爆梢。
4.3.5桔皮状---在轧件表面呈现桔皮状凹凸不平。
原因:孔型粗糟。
4.4尺寸类缺陷4.4.1横肋纵肋偏小---沿轧制方向形成的连续的偏小现象,原因:来料小,孔型充不满。
4.4.2、水平尺寸超标---沿扎制方向形成的连续超标现象。
⑴、来料大。
⑵、进口有倒钢现象。
[基础科学资料]高速线材表面红锈形成可能原因及其预防控制措施
![[基础科学资料]高速线材表面红锈形成可能原因及其预防控制措施](https://img.taocdn.com/s3/m/4a569f78482fb4daa58d4b62.png)
高速线材表面红锈形成可能原因及其预防控制措施线材表面氧化铁皮主要由FeO、Fe3O4和Fe2O3组成,毗邻铁层是比较疏松的FeO,呈蓝色,依次向外是比较致密的Fe3O4和Fe2O3,分别呈黑色和红色。
表面氧化铁皮的颜色随各种氧化成分比例的不同而变化,FeO较多时,表现为蓝灰色;当Fe2O3比例较高时,表现为红色,即俗称所说的“红锈”。
1.红锈形成的可能原因经过查阅相关资料,发现线材表面红锈的形成主要由以下5大原因所导致。
1.1钢的化学成分资料[1]表明,红锈的形成与钢中的硅含量有关,当钢中的硅含量低于0.20%时,称之为低Si钢,低Si钢铸坯氧化铁皮结构为1Fe2O3∶4Fe3O4∶95FeO,其氧化铁皮中气孔小,分布比较均匀,由于该氧化铁皮在高温下几乎没有延展性,由空冷引起的热应力会使氧化铁皮产生裂纹。
低硅钢铁皮中由于气孔小,应力松驰缓小,裂纹就将会沿气孔扩展到基底金属界面,除磷时,热应力就在氧化铁皮和基底金属界面作为剪切力起作用,使氧化铁皮从基底金属上剥离开,除磷后的氧化反应为:2Fe + O2=2FeO3FeO+1/2 O2=Fe3O42Fe3O4+ 1/2O2=3Fe2O3Fe + H2O =FeO + H2 3FeO + H2O =Fe3O4+ H2由于氧化过程是扩散过程,需要一定的时间、温度、浓度,在除磷后的条件下,主要发生的是铁基与氧气、水的反应,而FeO和氧气、水的反应则较缓慢,导致铁皮中FeO比例较高,所以低硅钢氧化铁皮呈蓝灰色。
当钢中的硅含量大于0.2%时,称之为高硅钢,在高温下高Si钢钢坯表面的FeO和钢坯基体结合在一起容易生成氧化物Fe2SiO4,,凝固后,形成类似锚状形貌,将FeO层钉扎住,增加了氧化铁皮的粘性,钉扎住的FeO很难在除鳞中完全被除掉,残余FeO造成Fe2O3的生成,导致氧化后Fe2O3比例增高,产生红锈。
综上所述,红锈的产生与钢在高温时的氧化铁皮剥离性有直接关系,含硅量较高尤其是Si>0.2%时,高温氧化铁皮剥离性差,容易残留铁皮,在随后的氧化过程中使Fe2O3比例增大,铁皮呈红色,即为红锈。
高速线材产品表面质量缺陷识别与控制.doc
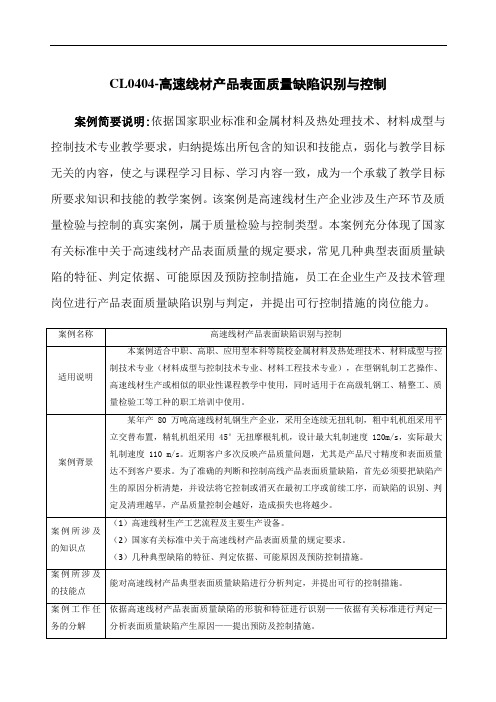
CL0404-高速线材产品表面质量缺陷识别与控制案例简要说明:依据国家职业标准和金属材料及热处理技术、材料成型与控制技术专业教学要求,归纳提炼出所包含的知识和技能点,弱化与教学目标无关的内容,使之与课程学习目标、学习内容一致,成为一个承载了教学目标所要求知识和技能的教学案例。
该案例是高速线材生产企业涉及生产环节及质量检验与控制的真实案例,属于质量检验与控制类型。
本案例充分体现了国家有关标准中关于高速线材产品表面质量的规定要求,常见几种典型表面质量缺陷的特征、判定依据、可能原因及预防控制措施,员工在企业生产及技术管理岗位进行产品表面质量缺陷识别与判定,并提出可行控制措施的岗位能力。
高速线材产品表面质量缺陷识别与控制1. 背景介绍钢材产品质量通常包括两个方面的内容:一是尺寸和外形,主要包括尺寸精度及表面质量;二是内在质量,主要包括化学成分、微观组织和力学性能等。
高速线材热轧盘条是热轧型钢中截面尺寸最小的一种。
由于截面积很小、轧制道次较多、一般呈盘卷供货,产品质量控制难度较大。
高线产品的尺寸精度及表面质量主要由轧制生产工艺控制,而内在质量除由轧制生产工艺控制外,还受前续工序的影响。
为了准确的判断和控制高线产品表面质量缺陷,首先必须要把缺陷产生的原因分析清楚,并设法将它控制或消灭在最初工序或前续工序,而缺陷的识别、判定及清理越早,产品质量控制会越好,造成损失也将越少。
2. 主要内容高速线材产品表面质量缺陷产生主要来自两个方面:一是上游原料带来的,二是在加热、轧制和精整环节中造成的。
《低碳钢热轧圆盘条GB/T701-2008》以及各类热轧盘条标准中关于表面质量都有以下规定:盘条应将头尾有害缺陷切除。
盘条的截面不应有缩孔、分层及夹杂。
盘条表面应光滑,不应有裂纹、折叠、耳子、结疤,允许有压痕及局部的凸起、划痕、麻面,其深度或高度(从实际尺寸算起) B级和C级精度不应大于0.10mm,A级精度不得大于0.20mm。
高速线材表面结疤原因分析及消除措施

经验交流山西冶金SHANXI M ETALLURGY Total 180No.4,2019DOI:10.16525/14-1167/tf.2019.04.69总第180期2019年第4期高速线材表面结疤原因分析及消除措施甘志涛,王扬发,郑团星(宝武集团广东韶关钢铁有限公司,广东韶关512123)摘要:对于线材表面产生的结疤,不同的缺陷形貌,产生的原因也不一样。
若不明确产生原因,会造成轧线的调整盲目,易导致批量缺陷产生,同时也影响现场的生产效率。
文中介绍了韶钢高速线材生产中,成品表面产生结疤的几种类型,分析每种类型结疤的产生原因,提出改进和消除的措施。
关键词:高速线材缺陷结疤坯料轧制中图分类号:TG335.6文献标识码:A文章编号:1672-1152(2019)04-0177-03收稿日期:2019-05-10第一作者简介:甘志涛(1988—),男,2012年7月毕业于江西理工大学金属材料工程专业,金属材料工程助理工程师,任线材工艺工程师。
结疤是线材盘条最常见的表面缺陷之一,通常定义为盘条表面与基体不完全紧密结合的点状或片状金属层。
盘条线材表面存在结疤缺陷,容易在下游工序的拉拔过程中造成钢丝表面缺陷,导致钢丝拉拔过程中在缺陷部位断裂,或冷锻时开裂,对于需要淬火热处理的钢丝,缺陷部位容易形成应力集中,导致淬火后断裂。
因此,盘条出现结疤时,在不能通过修磨、修剪等手段完全清除的情况下,只能降级使用或者判次判废处理,导致结疤在线材的废降品量比重很大。
2017年韶钢线材由于结疤缺陷降级判废占总表面缺陷降级判废量的14.7%,是线材生产中需要重点控制的缺陷。
1结疤的类型及产生的原因所谓结疤指的是线材盘条表面上与本体粘合一头或者不粘合的金属层,一般呈舌状,厚薄不均、大小不一。
结疤的定义较为宽泛,是多种类型表面缺陷的统称。
缺陷的特征不同,其产生的原因也不同,盘条表面的结疤既有线材工序造成的,也有坯料的缺陷造成的[1]。
高速线材表面质量缺陷的产生原因及排除方法
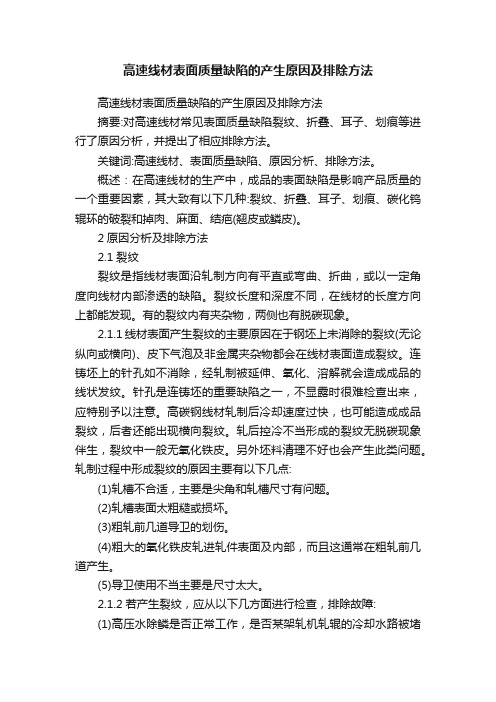
高速线材表面质量缺陷的产生原因及排除方法高速线材表面质量缺陷的产生原因及排除方法摘要:对高速线材常见表面质量缺陷裂纹、折叠、耳子、划痕等进行了原因分析,并提出了相应排除方法。
关键词:高速线材、表面质量缺陷、原因分析、排除方法。
概述:在高速线材的生产中,成品的表面缺陷是影响产品质量的一个重要因素,其大致有以下几种:裂纹、折叠、耳子、划痕、碳化钨辊环的破裂和掉肉、麻面、结疤(翘皮或鳞皮)。
2原因分析及排除方法2.1裂纹裂纹是指线材表面沿轧制方向有平直或弯曲、折曲,或以一定角度向线材内部渗透的缺陷。
裂纹长度和深度不同,在线材的长度方向上都能发现。
有的裂纹内有夹杂物,两侧也有脱碳现象。
2.1.1线材表面产生裂纹的主要原因在于钢坯上未消除的裂纹(无论纵向或横向)、皮下气泡及非金属夹杂物都会在线材表面造成裂纹。
连铸坯上的针孔如不消除,经轧制被延伸、氧化、溶解就会造成成品的线状发纹。
针孔是连铸坯的重要缺陷之一,不显露时很难检查出来,应特别予以注意。
高碳钢线材轧制后冷却速度过快,也可能造成成品裂纹,后者还能出现横向裂纹。
轧后控冷不当形成的裂纹无脱碳现象伴生,裂纹中一般无氧化铁皮。
另外坯料清理不好也会产生此类问题。
轧制过程中形成裂纹的原因主要有以下几点:(1)轧槽不合适,主要是尖角和轧槽尺寸有问题。
(2)轧槽表面太粗糙或损坏。
(3)粗轧前几道导卫的划伤。
(4)粗大的氧化铁皮轧进轧件表面及内部,而且这通常在粗轧前几道产生。
(5)导卫使用不当主要是尺寸太大。
2.1.2若产生裂纹,应从以下几方面进行检查,排除故障:(1)高压水除鳞是否正常工作,是否某架轧机轧辊的冷却水路被堵塞或偏离轧槽。
(2)导卫是否偏离轧制线,有无氧化铁皮堵塞在某个导卫中。
(3)轧槽是否过度磨损或因处理堆钢事故时损伤了轧槽。
(4)精轧机是否有错辊,导卫是否对中及尺寸是否对应于所轧的规格。
2.2折叠线材表面沿轧制方向平直或弯曲的细线,以任意角度渗入线材的表面内,在横断面上与表面呈小角度交角状的缺陷多为折叠,通常折叠较长,但亦有间断的不连续的,并在线材的长度方向上都有分布,折处的两侧伴有脱碳层或部分脱碳层,折叠中间常存在氧化铁夹杂。
高速线材表面结疤原因分析及改进
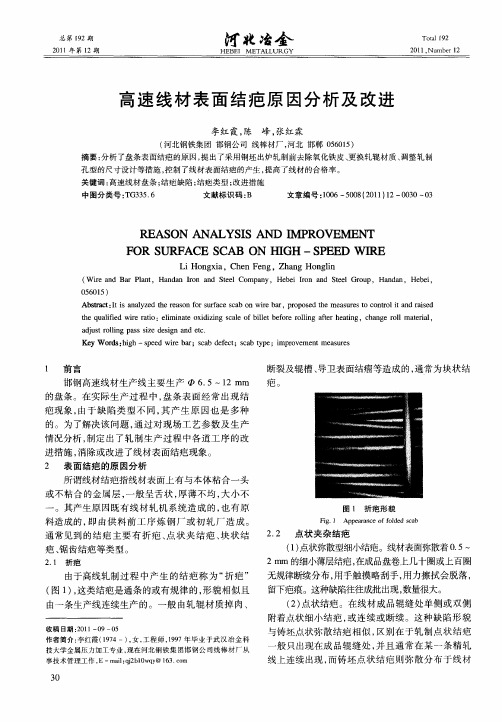
1 前 言
邯钢高速线材生产线主要生产 6.5~12 mE 的盘 条 。在 实 际生 产 过程 中 ,盘 条 表 面 经 常 出现 结 疤现象,由于缺 陷类型不 同,其产 生原因也是多种 的 。为 了解 决该 问题 ,通 过 对 现场 工 艺 参 数及 生 产 情 况分 析 ,制 定 出了轧 制 生 产 过程 中各 道 工序 的改 进措 施 ,消除或 改进 了线材 表面 结疤现 象 。 2 表面 结疤 的原 因分析
断裂 及辊 槽 、导 卫表 面结瘤 等造成 的 ,通 常为 块状 结 疤 。
图 1 折 疤 形 貌
Fig.1 Appearance of folded scab
2.2 点状 夹杂结 疤 (1)点状弥散型细小结疤。线材表面弥散着 0.5~
2 mrn的细小薄层结疤 ,在成品盘卷上几十圈或上百 圈 无规律断续分布,用手触摸略刮手 ,用力擦拭会脱落, 留下疤痕 。这种缺陷往往成批出现 ,数量很大 。
(2)点状 结 疤 。在 线 材 成 品辊 缝处 单侧 或 双 侧 附着 点状 细小 结 疤 ,或 连续 或 断续 。这种 缺 陷 形 貌 与铸 坯点 状弥 散结 疤 相 似 ,区别在 于轧 制 点状 结 疤 一 般 只出现在 成 品辊 缝 处 ,并 且 通 常在 某 一 条精 轧 线上连续出现 ,而铸坯 点状结疤则 弥散分布于线材
(2)翘皮 状有 根 结 疤 。在 线材 表 面 结 疤一 侧 翘 起 ,另 一 侧 与基 体 相 连 ,形状 和大 小 不一 致 ,在 成 品 上 一般 数 圈至 10多 圈 。
(3)周 期 性 块 状 结 疤 。线 材 表 面 上 有 块 状 结 疤 ,有 时被 完全压 入线 材表 面 以 内 ,表 面 可见较 清 晰 的结疤边 缘 曲线 ;有 时 略 凸 起 在 表 面 之 上 ,成 为 凸 块 。结 疤形 貌和 大 小 基 本 一致 ,在 盘条 上 周 期 性 发 生 ,此种 结 疤为有 根结 疤 ,一 般 在某一 轧线 上 连续 发 生 ,直 至停机 为止 。
高线缺陷

二、高线产品缺陷及分析:⑴、擦伤(划痕)1)、特性:一般呈直线形或弧形的沟痕,通常可见沟底,其深度由肉眼刚能见至几毫米,长度有几毫米至几米,连续或断续地呈现在线材的局部或全长。
2)、产生原因:a、导卫装置偏斜,加工不良,上边不圆滑。
b、导卫板或孔型粘附氧化铁皮,以及导卫板或孔型严重磨损。
c、活套量过大,轧件跳套;活套与轧直线不一致,拉钢时,轧件与活套棱角挂伤。
d、孔型侧壁磨损过多,与轧件接触产生弧形刮伤。
e、轧辊车削不当,有刀痕产生轧痕(或压痕)。
3)、防止办法:a、正确安装导卫。
b、按规定及时更换导卫或孔型。
c、按规定输入轧制速度,确保连轧常数,同时保证轧制线一致。
d、按导槽换辊制度导槽换辊。
e、提高车削质量和检验标准。
(2)、结疤:1)、特性:一般呈舌头形或指甲形,其宽而厚的一端与钢材基本相连,有时结疤外形呈一封闭的曲线,它嵌在线材表面,面积较大。
轧制产生的结疤容易翘起和张口,一般下面都有夹杂物。
2)、产生原因:a、在轧制过程中前一道次孔型有砂眼或因故损坏,当轧件通过该孔型后表面形成凸块,再轧制后,在成品线材表面产生周期性生根结疤。
b、在轧制过程中,由外界金属物落在轧件表面上,同时被带入孔型变形区,压入轧件表面,产生结疤,这样的结疤是不生根且无规律性。
c、轧件在孔型中打滑,使金属堆积于变形区周围表面上,再轧制时造成的。
d、由于轧辊表面刻痕不良,在轧件的表面上形成较高的凸起金属,再轧制时产生有规律的结疤。
e、钢坯表面有较大的翻皮和较大的皮下气泡破裂。
f、原料表面处理不良,有尖锐的棱角边产生。
3)防止办法:a、按导槽换辊制度导槽换辊,同时严格控制轧辊进厂检验。
b、轧制前应认真检查跑槽,导卫内是否有杂物,确保轧制线的清洁性。
c、导槽换辊后必须规定进行磨槽。
d、提高车削质量和检验标准。
e、加强钢坯进车间挑废检验工作。
(3)、耳子:1)、特性:耳子是指在线材表面平行与轴线的条状突起,有单面的或双面的产生于线材全长或局部或呈断续的。
线材表面缺陷原因分析及对策

线材表面缺陷原因分析及对策摘要:从设备管理的角度,分析设备问题影响材线表面的各种原因,针对设备存在的问题提出改进措施,表面缺陷得到有效控制。
关键词:线材;表面质量;设备前言线材表面质量是用户对公司实物的第一认知,直接影响到用户对公司产品的满意度。
线材在轧制过程中,设备与线材接触面状况对成品材表面影响极大。
1 影响线材表面质量的因素1.1钢坯表面氧化铁皮影响线材表面质量的原因分析炉温控制不合理,导致钢坯在高温段的停留时间长,钢坯表面氧化严重,经各架轧机轧制后,表面氧化铁皮不能及时脱落,最终嵌入线材表面,形成次材。
空燃配比控制不合理,炉膛为氧化气氛,钢坯表面氧化严重,最终导致线材表面产生缺陷。
高压水除鳞压力不足或是喷嘴安装不正确,不能将钢坯表面的氧化铁皮彻底清除,最终引起成品表面形成麻点、铁皮等缺陷,进而造成次品。
1.2导卫影响线材表面质量的原因分析由于导卫装配原因,导卫导辊转动不灵活或是导辊对轧件不能起到有效的支撑作用,最终导致轧件表面有划伤、折叠等缺陷。
由于油气润滑以及冷却水系统故障,造成导辊碎裂、粘钢、烧轴承等现象发生,进而导致轧件表面出现划伤。
由于导辊材质原因,在生产过程中有“掉肉”现象发生,进而导致线材表面出现划痕、结疤等缺陷。
由于导卫上线安装原因,导致轧件导入下游轧机时,不能对中相应轧机的孔型,进而导致线材表面出现耳子等缺陷。
1.3轧辊、辊环影响线材表面质量的原因分析由于轧辊、辊环的质量问题,导致轧辊、辊环在生产过程中有“掉肉”现象发生,进而导致线材表面出现划伤、结疤等缺陷。
由于轧辊、辊环的上线装配原因,各架料型控制不合适,最终导致线材表面出现折叠、耳子等缺陷。
1.4 活套轮影响线材表面质量的原因分析活套轮直接与线材表面接触,每条线装机量29个,其运行状态与红钢接触面光洁度对成品线材表面影响非常大。
活套轮高度参数不正确或设定变化范围大,活套轮安装偏离轧制中心线过多,造成辊轮表面磨损不光滑,造成线材表面出现划痕、划伤等问题。
- 1、下载文档前请自行甄别文档内容的完整性,平台不提供额外的编辑、内容补充、找答案等附加服务。
- 2、"仅部分预览"的文档,不可在线预览部分如存在完整性等问题,可反馈申请退款(可完整预览的文档不适用该条件!)。
- 3、如文档侵犯您的权益,请联系客服反馈,我们会尽快为您处理(人工客服工作时间:9:00-18:30)。
高速线材表面质量缺陷的产生原因及排除方法
摘要:对高速线材常见表面质量缺陷裂纹、折叠、耳子、划痕等进行了原因分析,并提出了相应排除方法。
关键词:高速线材、表面质量缺陷、原因分析、排除方法。
概述:在高速线材的生产中,成品的表面缺陷是影响产品质量的一个重要因素,其大致有以下几种:裂纹、折叠、耳子、划痕、碳化钨辊环的破裂和掉肉、麻面、结疤(翘皮或鳞皮)。
2原因分析及排除方法
2.1裂纹
裂纹是指线材表面沿轧制方向有平直或弯曲、折曲,或以一定角度向线材内部渗透的缺陷。
裂纹长度和深度不同,在线材的长度方向上都能发现。
有的裂纹内有夹杂物,两侧也有脱碳现象。
2.1.1线材表面产生裂纹的主要原因在于钢坯上未消除的裂纹(无论纵向或横向)、皮下气泡及非金属夹杂物都会在线材表面造成裂纹。
连铸坯上的针孔如不消除,经轧制被延伸、氧化、溶解就会造成成品的线状发纹。
针孔是连铸坯的重要缺陷之一,不显露时很难检查出来,应特别予以注意。
高碳钢线材轧制后冷却速度过快,也可能造成成品裂纹,后者还能出现横向裂纹。
轧后控冷不当形成的裂纹无脱碳现象伴生,裂纹中一般无氧化铁皮。
另外坯料清理不好也会产生此类问题。
轧制过程中形成裂纹的原因主要有以下几点:
(1)轧槽不合适,主要是尖角和轧槽尺寸有问题。
(2)轧槽表面太粗糙或损坏。
(3)粗轧前几道导卫的划伤。
(4)粗大的氧化铁皮轧进轧件表面及内部,而且这通常在粗轧前几道产生。
(5)导卫使用不当主要是尺寸太大。
2.1.2若产生裂纹,应从以下几方面进行检查,排除故障:
(1)高压水除鳞是否正常工作,是否某架轧机轧辊的冷却水路被堵塞或偏离轧槽。
(2)导卫是否偏离轧制线,有无氧化铁皮堵塞在某个导卫中。
(3)轧槽是否过度磨损或因处理堆钢事故时损伤了轧槽。
(4)精轧机是否有错辊,导卫是否对中及尺寸是否对应于所轧的规格。
2.2折叠
线材表面沿轧制方向平直或弯曲的细线,以任意角度渗入线材的表面内,在横断面上与表面呈小角度交角状的缺陷多为折叠,通常折叠较长,但亦有间断的不连续的,并在线材的长度方向上都有分布,折处的两侧伴有脱碳层或部分脱碳层,折叠中间常存在氧化铁夹杂。
2.2.1坯料中如存在缩孔、偏析、夹杂等缺陷,或者坯料修整不好都有可能产生类似折叠的缺陷。
轧制中可能产生折叠的原因有:
(1)孔型中过充满是折叠产生的主要原因。
(2)机架间张力太大也是产生折叠的原因之一。
(3)导卫对中不好可出现单侧充满从而造成折叠。
(4)轧机调整不当,轧件尺寸不对或导卫磨损严重也可能产生间断折叠。
(5)坯料加热温度不均匀。
2.2.2若产生折叠,应从以下几方面进行检查,排除故障:
(1)检查轧辊冷却,粗轧机中氧化铁皮堆积过多也可能是产生间断折叠的原因。
(2)是否有某个导卫偏离了轧制中心线引起过充满。
(3)导卫不正常,检查滑动导卫中是否有异物堆积,滚动导卫中导辊是否正常。
(4)通过轧机的轧件尺寸是否正确,是否过充满。
(5)检查张力情况。
检查坯料出炉温度,沿坯料长度上温度不均也可导致间断性过充满。
2.3耳子
线材表面沿轧制方向的凸起称为耳子,主要是轧槽过充满造成的。
坏料中如存在缩孔,偏析和夹杂等缺陷,会在轧制时导致轧件过充满。
2.3.1轧制中可能产生耳子的原因有:
(1)轧件尺寸不正确或辊缝调节不当。
(2)张力过大,导致线材头尾出现耳子。
(3)成品轧机上导卫对中不好或调整不当。
(4)坯料温度不均匀,高温段成品尺寸合适,而低温段则出现耳子。
(5)轧件抖动会产生断续耳子,一段在线材的一侧,另一段在线材的另一侧。
2.3.2若产生成品出耳子,应从以下几方面进行检查,排除故障:
(1)精轧机组入口轧件尺寸必须正确。
(2)工作辊径搭配,辊缝设定正确也很重要。
(3)检查轧机中的张力条件,如果速度适当,入口轧件和工作辊径正确,则精轧机中的张力应当是很小的。
(4)如果只是在线材一侧有耳子,则检查成品轧机入口导卫对中、对正是否良好。
(5)如果要消除轧件抖动现象,需进行检查并做到以下几点:精轧机组的辊环工作直径正确,入口轧件尺寸正确;辊缝调节正确;导卫调节正确;使用减震导卫;若钢种变化,轧件的宽展量也会变化,应做相应调整。
2.4划痕
划痕是线材表面沿长度方向上像沟的缺陷,其形状和大小各不相同,有的划痕沟侧有翻起的重叠边,也有很小的尖裂纹像划痕,划痕主要是成品通过有缺陷的设备,如导卫、活套、水冷箱、夹送辊、吐丝机、散卷输送线、集卷器及打捆机造成的。
2.4.1在轧制过程中产生划痕的原因有以下几方面:
(1)导卫中有堆积物。
(2)导卫安装不当或导辊断裂。
(3)导卫有毛刺。
(4)轧机的对中性不好,或导卫对中性不好。
(5)导卫开口度较大。
2.4.2轧件若产生划痕,应从以下几方面进行检查,排除故障:
(1)每次轧机停机以后要进行检查,通常要检查每个机架上的导卫,在检查时有必要用手电筒照明以便观察清楚。
(2)孔型或导卫对中性不好是产生划痕的最常见的原因,要定期检查。
2.5碳化钨辊环的破裂和“掉肉”
碳化钨辊环裂纹通常会在线材表面形成周期性缺陷,有时会在线材表面形成发纹,辊环“掉肉”有时会在线材的表面形成凸块或结疤。
2.5.1碳化钨辊环的破裂和“掉肉”形成原因有:
(1)由于碳化钨辊环的自身特性,冷却不当很容易断裂。
(2)辊环轧槽中的“掉肉”可能是由于冷却不当、辊环磨槽技术不当等造成。
(3)冷却水的酸碱度不合适。
2.5.2若产生碳化钨辊环的破裂和“掉肉”,应从以下几方面进行检查,排除故障:
(1)每次停机时都应检查辊环的使用情况,如果轧槽表面过早的剥落,应立即分析调查其原因。
(2)在运输与搬运时要小心轻放,要有适当的运输和存放工具。
(3)线材表面如存在凸块或结疤,则要测量从一个凸块或结疤到下一凸块或结疤的间距,以确定出现故障的架次。
(4)如果工作辊环或导卫中有剥落,则会相当的明显。
(5)辊环修磨不当会使辊环的表面过熟,辊环表面会呈“紫蓝”色,这样的辊环不应当再安装到轧机上去。
(6)定期检查轧机的冷却水的水质,必须控制好悬浮物的含量,单纯由钴组成粘结相的牌号PH值应保持在7.5-8.5之间,由钴镍铬组成粘结相的牌号PH值应小于7.5。
2.6麻面
在放大镜下能明显地看出在线材表面连续分布着不规则的凸凹缺陷,此即麻面。
2.6.1轧制过程中产生麻面缺陷的主要原因有:
(1)轧槽冷却不当或严重磨损。
(2)冷却水的PH值不合适,WC辊环中的粘结剂被腐蚀,从而使WC颗粒在轧制过程中脱落出来。
2.6.2若产生麻面,应从以下几方面进行检查,排除故障:
(1)严格按计划更换轧槽。
(2)交接班时要全面检查轧辊冷却和轧槽表面的情况。
(3)定期检查水质情况。
(4)检查轧辊的冷却水管是否堵塞。
2.7结疤(翘皮或麟层)
线材表面与线材基体部分结合或完全未结合的金属片层称为结疤。
前者是由成品以前几道次轧件上的凸起物件轧入基体形成的,后者是已脱离轧件的金属碎屑轧在轧件表面上形成的。
2.7.1坯料表面质量不好,漏检坯料上原有的结疤,或连铸坯表面未清除干净的翘皮、飞翅等均可形成结疤。
在轧制中产生结疤的原因有:
(1)坯料过热。
(2)坯料修磨不好。
(3)轧槽过度磨损。
(4)辊环“掉肉”。
(5)轧机导卫有毛刺。
2.7.2若产生结疤(翘皮或鳞层),应从以下几方面进行检查,排除故障:
(1)料过热会产生偏析,并且产生过量的氧化铁皮。
(2)轧制过程中较大块的氧化铁皮轧入轧件的表面形成结疤缺陷,因此要使用高压水除鳞消除氧化铁皮。
(3)偏析使坯料表面不平整,破裂碎片被轧入轧件内,在轧制后期破裂形成结疤,因此要控制好加热温度;
(4)轧机停稳以后,要仔细检查轧辊及导卫表面是否有毛刺、磨损、掉肉等问题。
3结语
高速线材表面质量缺陷的形成原因及故障排除方法并不复杂,现场操作人员要遵循以上原因进行分析,对排除方法要点要认真思考,经常不断地、定时的对导卫、轧辊、钢坯及加热、冷却水等进行检查,以减少高速线材表面质量缺陷的发生次数,排除时应力求分析准确解决迅速。