伊特T6EDC-042-028-003-1R00-C1叶片泵
伊特T6ED-072-028-1R00-C1叶片泵型号解读
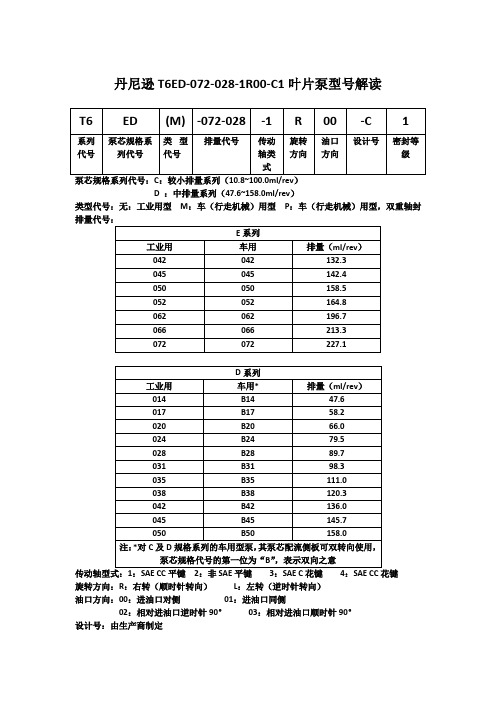
丹尼逊T6ED-072-028-1R00-C1叶片泵型号解读
泵芯规格系列代号:C:较小排量系列(10.8~100.0ml/rev)
D :中排量系列(47.6~158.0ml/rev)
类型代号:无:工业用型M:车(行走机械)用型P:车(行走机械)用型,双重轴封排量代号:
传动轴型式:1:SAE CC平键2:非SAE平键3:SAE C花键4:SAE CC花键
旋转方向:R:右转(顺时针转向)L:左转(逆时针转向)
油口方向:00:进油口对侧01:进油口同侧
02:相对进油口逆时针90°03:相对进油口顺时针90°
设计号:由生产商制定
密封等级:1=S1(适用于矿物油基液压油)常用的
4=S4(适用于抗燃液压液)
5=S5(矿物油基液压油及抗燃液压液,吸油口最高压力可达7bar)
以上是丹尼逊T6ED叶片泵的完整型号,再购买中能方便随时找到相应的型号,更多型号伊特液压随时欢迎咨询。
EATON 旋钮式手动控制阀门 E-VLSC-MC001-E 2009 12 版本说明书

EATON Screw-In Cartridge Valves E-VLSC-MC001-E December 2009 D-1.AAn Eaton BrandWhere measurements are critical request certified drawings. We reserve the right to change specifications without notice.Directional ControlsManual a nd p ilot o perated d irectional c ontrol v alves f or a pplicationsup to 350 bar (5000 psi) and 265 L/min (70 USgpm)EATON Screw-In Cartridge Valves E-VLSC-MC001-E December 2009D-2.A An Eaton BrandWhere measurements are critical request certified drawings. We reserve the right to change specifications without notice.Functional SymbolFlow Typical Model Cavity Rating PressurePageManual rotary valveL/min (USgpm) bar (psi)MRV3-10 C-10-3 23 (6) 210 (3000) D-100MRV13-10 C-10-3 23 (6) 350 (5000) D-110MRV13-12 C-12-3 46 (12) 350 (5000) D-120MRV3-16 C-16-3 64 (17) 210 (3000) D-130MRV13-16C-16-364 (17)350 (5000)D-140Flow Typical ModelCavityRatingPressurePageManual rotary valveL/min (USgpm) bar (psi)MRV4-10 C-10-4 11 (3) 210 (3000) D-150MRV14-10 C-10-4 11 (3) 350 (5000) D-160MRV14-12 C-12-4 23 (6) 350 (5000) D-170MRV4-16 C-16-4 45 (12) 210 (3000) D-180MRV14-16C-16-445 (12)350 (5000)D-190Flow Typical ModelCavityRatingPressurePageManual rotary valveL/min (USgpm) bar (psi)MRV5-10 C-10-4 11 (3) 210 (3000) D-200MRV15-10 C-10-4 11 (3) 350 (5000) D-210MRV15-12 C-12-4 23 (6) 350 (5000) D-220MRV5-16 C-16-4 45 (12) 210 (3000) D-230MRV15-16C-16-445 (12)350 (5000)D-240Flow Typical ModelCavityRatingPressurePageManual rotary valveL/min (USgpm) bar (psi)MRV6-10 C-10-4 11 (3) 210 (3000) D-250MRV6-16 C-16-4 11 (3) 300 (5000) D-256Flow Typical Model Cavity Rating PressurePageManual lever valve, spoolL/min (USgpm) bar (psi)MLV9-12-A C-12-460 (13.9)210 (3000)D-292Flow Typical ModelCavityRatingPressurePageManual lever valve, spoolL/min (USgpm) bar (psi)MLV9-12-BC-12-460 (15.9)210 (3000)D-293Flow Typical ModelCavityRatingPressurePageManual lever valve, spoolL/min (USgpm) bar (psi)MLV9-12-EC-12-460 (15.9)210 (3000)D-294Flow Typical ModelCavityRatingPressurePageManual lever valve, spoolL/min (USgpm) bar (psi)MLV9-12-F C-12-4 60 (15.9) 210 (3000) D-295EATON Screw-In Cartridge Valves E-VLSC-MC001-E December 2009 D-3.AAn Eaton BrandDWhere measurements are critical request certified drawings. We reserve the right to change specifications without notice.Functional SymbolFlow Typical Model Cavity Rating PressurePageCheck MO L/min (USgpm) bar (psi)3CP2A8795.5-15 (1.4-4)210 (3000)D-320Flow Typical ModelCavityRatingPressurePageManual pull valve, NC L/min (USgpm) bar (psi)MPV1-10 C-10-2 45 (12) 210 (3000) D-330MPV3-10C-10-245 (12)210 (3000)D-340Flow Typical ModelCavityRatingPressurePageManual push valve L/min (USgpm) bar (psi)MSV1-12 C-12-3 41.8 (11) 210 (3000) D-350MSV11-10 C-10-3 23 (6) 350 (5000) D-360MSV11-12 C-12-3 30 (8) 350 (5000) D-370MSV12-12C-12-338 (10)350 (5000)D-390Flow Typical ModelCavityRatingPressurePageManual push valve L/min (USgpm) bar (psi)MSV2-12C-12-338 (10)210 (3000)D-380Flow Typical ModelCavityRatingPressurePageManual push valve L/min (USgpm) bar (psi)MSV5-12 C-12-3 41.8 (11) 210 (3000) D-400MSV15-12C-12-341.8 (11)350 (5000)D-410Flow Typical ModelCavityRatingPressurePageManual push valve L/min (USgpm) bar (psi)MSV3-12 C-12-4 53.2 (14) 210 (3000) D-420MSV13-12C-12-4 53.2 (14) 350 (5000) D-430Flow Typical ModelCavity Rating PressurePageManual push valve L/min (USgpm) bar (psi)MSV4-12 C-12-4 53.2 (14) 210 (3000) D-440MSV14-12C-12-453.2 (14)350 (5000)D-450Flow Typical ModelCavityRatingPressurePageManual push valve L/min (USgpm) bar (psi)MSV6-12 C-12-4 53.2 (14) 210 (3000) D-460MSV16-12C-12-453.2 (14)350 (5000)D-470Flow Typical ModelCavityRatingPressurePageManual push valve L/min (USgpm) bar (psi)MSV17-10 C-12-4 20 (5.3) 350 (5000) D-480MSV7-12 C-12-4 45 (11.9) 210 (3000) D-490MSV17-12 C-12-4 20 (5) 350 (5000) D-5002EATON Screw-In Cartridge Valves E-VLSC-MC001-E December 2009D-4.A An Eaton BrandWhere measurements are critical request certified drawings. We reserve the right to change specifications without notice.Functional SymbolFlow Typical Model Cavity Rating PressurePagePilot to shift 2/2 valve L/min (USgpm) bar (psi)PTS7-10 C-10-3 30 (8) 210 (3000) D-510PTS17-10 C-10-3 30 (8) 350 (5000) D-520PTS17-12C-12-3114 (30)350 (5000)D-530Flow Typical ModelCavityRatingPressurePagePilot to shift 2/2 valve L/min (USgpm) bar (psi)1RDS702 A21145 80 (20) 420 (6090) D-560Flow Typical ModelCavityRatingPressurePageBrake sequence L/min (USgpm) bar (psi)1SB10 A893 10 (2.5) 350 (5000) D-540Flow Typical Model Cavity Rating PressurePageBrake release shuttle L/min (USgpm) bar (psi)1SB304 A5302 30 (8) 350 (5000) D-550Flow Typical Model Cavity Rating PressurePagePilot to shift valve L/min (USgpm) bar (psi)PTS1-10 C-10-4 30 (8) 210 (3000) D-570PTS11-12 C-12-4 76 (20) 350 (5000) D-580PTS11-10 C-10-4 30 (8) 350 (5000) D-590PTS1-16 C-16-4 132 (35) 210 (3000) D-600PTS11-16 C-16-4 132 (35) 350 (5000) D-610PTS1-20 C-20-4265 (70)210 (3000)D-620Flow Typical ModelCavityRatingPressurePagePilot to shift valve L/min (USgpm) bar (psi)PTS12-10 C-10-4 30 (8) 350 (5000) D-630PTS12-12 C-12-4 114 (30) 350 (5000) D-640PTS2-16 C-16-4 132 (35) 210 (3000) D-650PTS12-16 C-16-4 132 (35) 350 (5000) D-660PTS2-20 C-20-4 265 (70) 210 (3000) D-670EATON Screw-In Cartridge Valves E-VLSC-MC001-E December 2009 D-5.AAn Eaton BrandDWhere measurements are critical request certified drawings. We reserve the right to change specifications without notice.Functional SymbolFlow Typical Model Cavity Rating PressurePagePilot to shift valve L/min (USgpm) bar (psi)PTS13-10 C-10-4 30 (8) 350 (5000) D-680PTS13-12 C-12-4 113 (30) 350 (5000) D-690PTS3-16 C-16-4 132 (35) 210 (3000) D-700PTS13-16 C-16-4 132 (35) 350 (5000) D-710PTS3-20 C-20-4 265 (70) 210 (3000) D-720PTS6-16 C-16-4 132 (35) 210 (3000) D-790PTS16-16C-16-4132 (35)350 (5000)D-800Flow Typical ModelCavityRatingPressurePagePilot to shift valve L/min (USgpm) bar (psi)PTS14-12 C-12-4 114 (30) 350 (5000) D-730PTS14-16 C-16-4 132 (35) 350 (5000) D-740PTS5-16 C-16-4 132 (35) 210 (3000) D-770PTS15-16 C-16-4 132 (35) 350 (5000) D-780Flow Typical ModelCavity Rating PressurePagePilot to shift valve L/min (USgpm) bar (psi)PTS5-10 C-10-3 11 (3) 210 (3000) D-750PTS5-12C-12-3 105 (28) 350 (5000) D-760Flow Typical ModelCavity Rating PressurePagePilot to shift valve L/min (USgpm) bar (psi)PTS9-8 C-8-5S 19 (5) 280 (4000) D-810PTS9-10 C-10-5S 38 (10) 280 (4000) D-820PTS9-12 C-12-5S 76 (20) 280 (4000) D-830PTS9-16 C-16-5S 151 (40) 280 (4000) D-840PTS9-20C-20-5S 230 (60) 280 (4000) D-850Flow Typical Model Cavity Rating PressurePageHot oil shuttle L/min (USgpm) bar (psi)1HSH20 CVB-22-06-0 20 (5) 350 (5000) D-856EATON Screw-In Cartridge Valves E-VLSC-MC001-E December 2009D-6.A An Eaton BrandWhere measurements are critical request certified drawings. We reserve the right to change specifications without notice.This section gives the basic specifications for the complete line of Eaton's Integrated Hydraulics threaded cartridge non-solenoid directional control valves. Its purpose is to provide a quick, convenient reference tool when choosing Vickers cartridge valves or designing a system using these components.Two pressure ratings areshown for all products featured in this catalog – typical application pressure and fatigue pressure. The typical application pressure rating is the maximum recommended operating pressure for the valve in a given system. The fatigue pressure rating is the pressure for the valve to be free for infinite life from metal fatigue.Features and Benefits • P roducts in this catalog have been fatigue tested for one million cycles at 132% or 10 million cycles at 115% of rated pressure.• A ll operating parts arehardened steel, ground and honed for long life and low leakage.• D esigned for maximumflexibility and minimal space requirements.• A ll exposed cartridgesurfaces are zinc dichromate plated to resist corrosion.• A ll aluminum manifolds are gold anodized to resist corrosion.• D esired settings may be locked down.• A luminum knob and cap options are available on some models.• R eliable, economicaland compact.WARNINGFor pressure over 210 bar (3000 psi)use steel housing.Directional ControlsIntroductionFunctional SymbolFlow Typical Model Cavity Rating PressurePageSequence L/min (USgpm) bar (psi)DSV4-10 C-10-4 26 (6.9) 350 (5000) D-860DSV4-12C-12-4 113 (29.9) 350 (5000) D -866Flow Typical ModelCavityRatingPressurePageHot oil shuttle L/min (USgpm) bar (psi)1HSH701 A21145 80 (21) 420 (6000) D-870Flow Typical ModelCavity Rating PressurePagePilot to shift valve L/min (USgpm) bar (psi)PTS6-10 C-10-4 23 (6) 210 (3000) D-880PTS16-10 C-10-4 23 (6) 350 (5000) D-890PTS16-12C-12-4 76 (20) 350 (5000) D-900EATON Screw-In Cartridge Valves E-VLSC-MC001-E December 2009 D-7.AAn Eaton BrandDWhere measurements are critical request certified drawings. We reserve the right to change specifications without notice.90º90º50.8(2.00)50.8(2.00)88.95(3.502)65.9(2.595)50.69(1.996)67.82(2.670)22.23(0.875)Dowel Pin D2 and E2 Adjustment.20 in Mating Housing#29 (0.136 + 0.002) - 0.00045º90º321“D” Style367.82(2.670)50.64(1.994)46.21(1.819)90º50.8(2.00)(288.95(3.502)65.9(2.595)50.69(1.996)22.23(0.875)Dowel PinD2 and E2 Adjustment.20 in Mating Housing#29 (0.136+ 0.002) - 0.00045º90º321“D” Style 367.82(2.670)50.64(1.994)46.21(1.819)21“E2” StyleAlternative Adjusters For Light Duty Aluminum Housings Only 9,41,0(1.61)PortPort 1 to 258,0(2.28)Locating41,0(1.61)17,1 ±? 0.05(0.672 ± 0.002)Ø 3,45/3,50(#29 or 0.136)drill x 4,8(0.187) deepin mating housingThis hole omitted from detent plate of MRV3-10(V)-D2/E2Locating pin hole,four optional slots in detent plate RV3-*MRV3-*Locating Pin InstallationMRV3-**(V)-D(2)26,95 (1.061)(1.0.50) h ex25" -12 Th d.(0.43)11,0 (0.438)58,0(2.28)Port 3 to 1Port 1 to 2105 (4.13)Locating pin76,0(3.0)45°45°Mid position (not for 2-position models)7(25(224,9 ± 0.05(0.98 ± 0.002)Locating pin hole,four optional slots in detent plateØ 3,45 3,50(#29 or 0.136)drill x 4,8(0.187) deepin mating housingInstallation9,5 (0.37)41,0(1.61)Port 3 to 1Port 1 to 283,0(3.27)58,0(2.28)Locating pin45°45°M p (n 2m41,0(1.61)38,1(1.50)Ø 25,4 (1.0)42,0(1.65)50136)eephousingng pin hole,ptional slots ent plateMRV3-**(V)-D(2)MRV3-**(V)-E(2)ng Pin ation9,5 (0.37)(1.61)Port 1 to 283,0(3.27)58,0(2.28)Locating pin 45°Mid position (not for 2-position models)41,0(1.61)38,1(1.50)Ø 25,4 (1.0)42,0(1.65)17,1 ±? 0.05(0.672 ± 0.002)Ø 3,45/3,50(#29 or 0.136)drill x 4,8(0.187) deepin mating housingThis hole omitted from detent plate of MRV3-10(V)-D2/E2Locating pin hole,four optional slots in detent plateMRV3-**(V)-E(2)Locating PinInstallation D(2)Size 10Size 10E(2)Size 10Locating PIN Installation D(2)Size 12Size 12E(2)Size 12Locating PIN InstallationD(2)Size 16Size 16Locating PIN Installation 90º90º50.8(2.00)50.8(2.00)88.95(3.502)65.9(2.595)50.69(1.996)67.82(2.670)22.23(0.875)Dowel PinD2 and E2 Adjustment.20 in Mating Housing #29 (0.136 + 0.002) -0.00045º90º。
ATEX认证的低功耗小型液压阀门说明书

power ratings
hot/cold =
(W) 1/1,2
max. ambient temperature °C(2)
surface temperature
T6 85°C
T5 100°C
T4 135°C
40
55
60
ForversionswithLEDindicatorandelectricalprotection:
3xØ2 2 x Ø 3,5
9,7 == 15 ==
weight (1) 0,14
(1)withconnector.
Single subbase
Aluminiumorbrass
Adapter CNOMO size 30
(only for NC version) Aluminium
60 48
180°
function 2/2 way
NC 3/2 way
NC NO
MIX
connection
1
2
3
P
U
-
P
U
E
E
U
P
P2
U
P1
SEL
P:Pressure E:Exhaust
U2 P U1 U:Outlet
Subbasemountingsurface:ISO15218 (CNOMOE06.36.120N,size15)
ATEXU
31
2
(CFSCZN
prefix)
31
FEATURES • M ini-low consumption valves for use in potentially explosive atmospheres according to ATEX-Directive 2014/34/EU • EC type examination certificate (INERIS 10 ATEX 3016X) is in compliance with the European Standards EN 60079-0. EN 60079-15 and EN 60079-31 • Compact, monobloc solenoid pilot valve with spade-plug connector type DIN 43650, form C with 9,4 mm spacing • Version without integrated LED and electrical protection • Universal version for vacuum operation (3/2 way)
EX260-PEC1 产品名 一体化泵系统集成阀门 manifold 型号 EX260-PEC1说明

Doc. No.EX##-OMA1006SI Unit for ejector system integrated valve manifoldEX260-PEC1Safety InstructionsThese safety instructions are intended to prevent hazardous situations and/or equipment damage. These instructions indicate the level of potential hazard with the labels of "Caution", "Warning" or "Danger". They are all important notes for safety and must be followed in addition to International Standards (ISO/IEC)*1), and other safety regulations.*1) ISO 4414: Pneumatic fluid power -- General rules relating to systems.ISO 4413: Hydraulic fluid power -- General rules relating to systems.IEC 60204-1: Safety of machinery -- Electrical equipment of machines .(Part 1: General requirements)ISO 10218: Manipulating industrial robots -Safety.etc.Safety InstructionsRead and accept them before using the product.NOTE○Follow the instructions given below when designing, selecting and overseeing the product.•The instructions on design and selection (installation, wiring, environment, adjustment, operation,maintenance, etc.) described below must also be followed.*Product specifications•Use the specified voltage.Otherwise, failure or malfunction can result.•Reserve a space for maintenance.Allow sufficient space for maintenance when designing the system.•Do not remove any nameplates or labels.This can lead to incorrect maintenance, or misreading of the operation manual, which could cause damage or malfunction to the product.It may also result in non-conformity to safety standards.•Pay attention to the inrush current at power-up.Depending on the connected load, the initial charge current may cause the overcurrent protection and malfunction can result.•Product handling*Installation•Do not drop, hit or apply excessive shock to the fieldbus system.Otherwise, damage to the product can result, causing malfunction.•Tighten to the specified tightening torque.If the tightening torque is exceeded the mounting screws may be broken.IP67 protection cannot be guaranteed if the screws are not tightened to the specified torque.• When carrying the manifold, make sure that the connections are not stressed.Otherwise, the damage to connections can result. In addition, some combinations of the manifold may be very heavy, so use more than one person to carry or install the manifold.•Never mount a product in a location that will be used as a foothold.The product may be damaged if excessive force is applied by stepping or climbing onto it.*Wiring•Avoid repeatedly bending or stretching the cables or placing heavy load on them.Repetitive bending stress or tensile stress can cause breakage of the cable.•Wire correctly.Incorrect wiring can break the product.•Do not perform wiring while the power is on.Otherwise, damage to the fieldbus system and/or I/O device can result, causing malfunction.•Do not route wires and cables together with power or high voltage cables.Otherwise, the fieldbus system and/or I/O device can malfunction due to interference of noise and surge voltage from power and high voltage cables to the signal line.Route the wires (piping) of the fieldbus system and/or I/O device separately from power or high voltage cables.•Confirm proper insulation of wiring.Poor insulation (interference from another circuit, poor insulation between terminals, etc.) can lead to excess voltage or current being applied to the product, causing damage.•Take appropriate measures against noise, such as using a noise filter, when the fieldbus system is incorporated into equipment.Otherwise, noise can cause malfunction.*Environment•Select the proper type of protection according to the environment of operation.IP67 protection is achieved when the following conditions are met.However, when connected with JSY1000 manifolds, it is IP40.(1) The SI Unit is connected properly with fieldbus cable with M8 connector and power cable with M8 connector.(2) Suitable mounting of the SI Unit and manifold.(3) Be sure to fit a seal cap on any unused connectors.If using in an environment that is exposed to water splashes, please take measures such as using a cover.•Do not use in a place where the product could be splashed by oil or chemicals.If the product is to be used in an environment containing oils or chemicals such as coolant or cleaning solvent, even for a short time, it may be adversely affected (damage, malfunction etc.).•Do not use the product in an environment where corrosive gases or fluids could be splashed.Otherwise, damage to the product and malfunction can result.•Do not use in an area where surges are generated.If there is equipment that generates a large amount of surge (solenoid type lifter, high frequency induction furnace, motor, etc.) close to the fieldbus system, this may cause deterioration or breakage of the internal circuit of the fieldbus system. Avoid sources of surge generation and crossed lines.•When a surge-generating load such as a relay or solenoid is driven directly, use a fieldbus system with a built-in surge-absorbing element.Direct drive of a load generating surge voltage can damage the fieldbus system.•The product is CE marked, but not immune to lightning strikes. Take measures against lightning strikes in the system.•Prevent foreign matter such as remnant of wires from entering the fieldbus system to avoid failure and malfunction.•Mount the product in a place that is not exposed to vibration or impact.Otherwise, failure or malfunction can result.•Do not use the product in an environment that is exposed to temperature cycle.Heat cycles other than ordinary changes in temperature can adversely affect the inside of the product.•Do not expose the product to direct sunlight.If using in a location directly exposed to sunlight, shade the product from the sunlight.Otherwise, failure or malfunction can result.•Keep within the specified ambient temperature range.Otherwise, malfunction can result.•Do not operate close to a heat source, or in a location exposed to radiant heat.Otherwise, malfunction can result.*Adjustment and Operation•Perform settings suitable for the operating conditions.Incorrect setting can cause operation failure.•Please refer to the PLC manufacturer's manual etc. for details of programming and addresses. For the PLC protocol and programming refer to the relevant manufacturer's documentation.*Maintenance•Turn off the power supply, stop the supplied air, exhaust the residual pressure and verify the release of air before performing maintenance.There is a risk of unexpected malfunction.•Perform regular maintenance and inspections.There is a risk of unexpected malfunction.•After maintenance is complete, perform appropriate functional inspections.Stop operation if the equipment does not function properly.Otherwise, safety is not assured due to an unexpected malfunction or incorrect operation.•Do not use solvents such as benzene, thinner etc. to clean each unit.They could damage the surface of the body and erase the markings on the body.Use a soft cloth to remove stains.For heavy stains, use a cloth soaked with diluted neutral detergent and fully squeezed, then wipe up the stains again with a dry cloth.Fieldbus System/Industrial IoT Cybersecurity In recent years, factories have introduced industrial IoT, building up complex networks of production machines. These systems maybe subject to a new threat, cyberattack. To protect the industrial IoT from cyberattacks, it is important to take multiple measures (multi-layer protection) for IoT devices, networks and clouds.For this purpose, SMC recommends that the following measures are always taken into consideration. For further details of the following measures, please see security information published by your local country security agencies.1. Do not connect the devices via a public network.• If you unavoidably need to access the device orcloud via a public network, ensure to use a secure,private network such as VPN.• Do not connect an office IT network and factory IoT network.2. Build a firewall to prevent a threat from entering the device and system.• Set up a ro uter or firewall at network boundaries toallow minimum required communications.• Disconnect from the network or turn off the device if no continuous connection is required.3. Physically block an access to unused communication ports or disable them.• I nspect regularly each port if any unnecessarydevice is connected to the network system.• Operate necessary services (SSH, FTP, SFTP, etc.) only.• Set a transmission range of the device using awireless LAN or other radio system to the minimumrequired and use only devices approved according to the radio act in the country concerned.• Install a device generating radio waves in such place as there is no interference from indoor or outdoor. 4. Set up a secure communication method such as data encryption.• Encrypt data in every environment, including IoTnetworks, secure gate-way connections, for securecommunications.5. Grant access permissions by user accounts and limit the number of users.• Regularly review accounts and delete all unusedaccounts or permissions.• Establish an account lockout system to block anaccess to the account for a certain period if log-infails more than the given threshold.6. Protect passwords.• Change the default password when you firstuse the device or system.• Choose a long password (minimum 8characters) using a mix of different letters and characters to make the password more secure and harder to hack.7. Use the latest security software.• Install antivirus software on all computers todetect and remove viruses.• Keep the antivirus software up to date.8. Use the latest version of the device and system software.• Apply patches to keep the OS and applications up to date.9. Monitor and detect abnormalities in the network.• Keep monitoring t he network for anyabnormalities to take a prompt measure andissue an alert if any abnormality is detected.Install an intrusion detection system (IDS) and intrusion prevention system (IPS).10. Delete data from devices when disposed of. • Before disposi ng of any IoT devices, deletestored data or physically destruct media toprevent any misuse of the data.1.This document is an operation manual for a SI (Serial Interface) Unit which controls ejector system integrated valve manifold (JSY series). The SI Unit is a EtherCAT®-compatible device. EtherCAT® is registered trademark and patented technology, licensed by Beckhoff Automation GmbH, Germany. The SI Unit controls the manifold which has 5 pressure sensors max., and 24 valves output max.. For valve manifold, refer to the instruction manual for ejector system integrated valve manifold.Fig 1-1. The SI Unit structure2.Select the appropriate cables to mate with the connectors mounted on the SI Unit.2.1. Communication connectorECAT IN/OUT: M8 4 pin socket A-codedFig 2-1. Pin allocation of communication connectorWarningPay attention not to confuse the communication connector with the power connector. Incorrect connection may result in SI Unit failure. Check the printed character.2.2. Power connectorPWR IN: M8 4 pin plug A-codedPWR OUT: M8 4 pin socket A-codedFig 2-2. Pin allocation of power connectorPower-supply line for logic/sensors and power-supply line for valves are isolated. Be sure to supply power respectively.It can be used either with two different power supply or single-source power supply.NOTEThe recommended tightening torque is 0.2 Nm for both communication connectors and powerconnectors.2.3. FE terminalThe SI Unit must be connected to FE (Functional Earth) to divert electromagnetic interference. Connect a grounding cable from the FE terminal screw on the SI Unit to the nearest functional earth point. The grounding cable should be as thick and short as reasonably possible.The FE terminal and the metal parts of the communication/power connector are internally connected. The recommended tightening torque for FE terminal is 0.3 Nm.Fig 2-3. FE terminal3.1. ESI fileTo configure the SI Unit with your EtherCAT® master's software, the dedicated ESI (EtherCAT Slave Information) file is required. The ESI file contains all necessary information to configure the SI Unit on your master's software.The ESI file name is as follows. The ESI file can be downloaded from the SMC website.•ESI file: SMC_EX260-PECx_V10.xml3.2. Energy saving parameterNOTE•For energy saving function of ejector, see e.g. the catalogue for ejector system integrated valve manifold.The energy saving function is supported by ejector that can hold vacuum pressure.Check in advance whether your ejector is compatible with the energy saving function.•If there is an overlap OUT No. or order error in the set values, the Diagnosis history "Warning"occurs and SF LED flashes green and stops energy saving operation for sensor No. with error.•Incorrect OUT No. setting may result in unintended valve output.4.1. Input process data4.1.1. Pressure value of sensor No.x (of each 5 sensors)NOTE•Fixed at 0 for unconnected sensor.•Hold last data during happened sensor wire break and error etc..4.1.2. Valve-coil(s) short circuit diagnosis4.1.3. Unit diagnosis4.1.4. Sensor state of sensor No.x (of each 5 sensors)NOTEFor judgement of vacuum/pressure generation, refer to Section 5.1.1 and Section 6.4.2. Output process data4.2.1. Output5.NOTE*1) RO means Read only, WO means Write only, and RW means both Read and Write are allowed. Those with a trailing P are the Index assigned to the process data, and the format is the same.5.1. Sensor parameters(Index 0x8009/8019/8029/8039/8049)5.1.1. Pressure parameter (Subindex 0x01...0x08)NOTE•If the pressure parameter set values do not fulfil the conditions in (1)...(4) above, the Diagnosis history "Warning" occurs and SF LED flashes green and applicablevacuum/pressure state bit (Offset 0.0...0.3 in Section 4.1.4) is fixed at 0 for the applicable sensor.•If the pressure parameter set values do not fulfil the conditions in (2) above and the energy saving parameter is set to other than Disable, stop energy saving operation for the applicable sensor.5.1.2. Supply valve type (Subindex 0x09)NOTE•The setting must match supply valve type of actual ejector. If the settings are different from the actual specifications, energy saving operation is not possible.5.1.3. Valve protection (Subindex 0x0A)5.2. Output parameters5.2.1. Output counter (Index 0xF120)5.2.2. Output operation at network fault (Index 0xF800)5.2.3. Output counter limit monitoring(Index 0xF801)5.2.4. Output counter limit value (Index 0xF802)5.3. General parameters5.3.1. Number of sensors (Index 0xF803)NOTE•If the number of sensors detected by the SI Unit is greater than the set number, the unit will operate normally without occurring an error.5.4. Command parameters5.4.1. Zero offset (Index 0xB008/B018/B028/B038/B048/FB00)NOTE•Zero offset should be performed with sensor open to the atmosphere.Zero offset is performed only when the pressure value is within ±2 % F.S. of atmospheric pressure.•"Zero offset reset request" clears the zero offset correction.•"Zero offset of all sensors" is used to zero offset all sensors at once.5.4.2. Valve protection release (Index 0xFB01)NOTE•Valve protection release is performed for all ejectors at once.•If the valve protection occurs, the diagnostic bit will be deleted, and the SF LED will be turned off by the above requests.5.4.3. Output count reset (Index 0xFB02)NOTE•The Output count reset can be reset for each output individually and is entered according toa 4 byte (32 bit) number.Example: Set 0x00001234 -> Output count reset request of OUT2,4,5,9,12Example: Set 0x1234ABCD -> Output count reset request of OUT0,2,3,6,7,8,9,11,13,15,18,21•If output count over occurs, the diagnostic bit will be deleted, and the SF LED will be turned off by the above requests.6.Fig 6-1. Example of energy saving operation (Conditions under which release pressure is generated) • (1)When the vacuum instruction is ON, the supply valve is automatically closed when the vacuum pressure reaches P2.• (2)When the vacuum pressure drops by P2-H2, the supply valve is automatically opened again. • (3)Repeat steps (1) and (2) unless the valve protection is activated.• (4)The vacuum P1 state bit is set to 1 until the vacuum pressure reaches P1 and then drops to P1-H1. • (5)The vacuum P2 state bit is set to 1 until the release pressure reaches P2 and then drops to P2-H2. • (6)The pressure P3 state bit is set to 1 until the vacuum pressure reaches P3 and then drops to P3-H3. • (7)The pressure P4 state bit is set to 1 until the vacuum pressure reaches P4 and then drops to P4-H4. • The above pressure threshold/hysteresis combinations are set by CoE services, Refer to Section 5.1.1.Vacuum instruction (OUTx ON/OFF)Supply valve Release instruction (OUTy ON/OFF)Vacuum P2state bit Release Valve Vacuum P1state bit Pressure P3state bit Pressure P4state bitEnergy saving parameter set to OUTx-y, Supply valve type : N.C.Threshold of Vacuum P1Energy savingoperationThreshold of Pressure P3Threshold of Pressure P47.7.1. LED IndicationFig 7-1. LED Indicators of the SI UnitRUN ERR SF L/A1L/A2PWR PWR(V)Fig 7-2. LED lighting patterns 7.2. Diagnosis history8.8.1. DimensionsFig 8-1. Dimensions of the SI Unit8.2. SpecificationsNOTE*1: SI Unit power supply voltage specification. Supply power according to the solenoid valve used.9.(1) Seal capPart number: EX9-AWESThis cap is used to protect the M8 socket connector opening when the connector is not used.When a connector is not used, the seal cap can keep the SI Unit under IP67 rated protection.(2 pcs. are included with the SI Unit as an accessory.)Fig 9-1. EX9-AWES10.The state of the SI Unit is indicated by the LED indication.If a problem occurs on the SI Unit, you can use the following chart to troubleshoot.Also refer to the online diagnostics via the EtherCAT® master software to help identify the problem.10.1. Troubleshooting chartFig 10-1. Troubleshooting chart10.2. Troubleshooting tablesNOTE•The Diagnosis history (Section 7.2) allows identification of the OUT No. or sensor No. that is causing the problem.4-14-1, Sotokanda, Chiyoda-ku, Tokyo 101-0021 JAPANTel: + 81 3 5207 8249 Fax: +81 3 5298 5362URL https://Note: Specifications are subject to change without prior notice and any obligation on the part of the manufacturer.© 2022 SMC Corporation All Rights ReservedNo.EX##-OMA1006。
叶片式液压泵 T7CS 系列产品介绍说明书

T7CS, Denison 叶片泵主要技术信息泵理论排量Vi最高转速最高压力HF-0, HF-1HF-2HF-4, HF-5HF-0, HF-2HF-1, HF-4, HF-5系列规格间歇连续间歇连续cm 3/rev.rpmrpmbarbarbarbarT7C SE1758,325001800260230210175E2063,8E2270,3E2579,31500HF-0, HF-2 = 石油基抗磨液压油 HF-1 = 石油基液压油(非抗磨)HF-4 = 水乙二醇液HF-5 = 合成液压油(磷酸脂液等)注:更多的详细资料,或若上列性能参数不能满足您的特殊工况要求,请与当地的派克办事处联系。
主要特征性能稳定T7CS 系列叶片泵是为变速驱动而设计的,并且转速范围很宽。
和我们其他的T7系列叶片泵一样,随着时间的推移,性能仍然很稳定,使得该类叶片泵成为现代电液操作机器的理想解决方案。
寿命长压力平衡概念增加了泵的寿命。
而双唇口叶片增加了抗固体颗粒污染能力。
噪音低Denison 叶片泵技术在泵的整个工作范围和整个生命周期中允许低的噪音水平。
通用性和紧凑性T7CS 系列叶片泵提供了几种排量规格,最大达80 cc/rev,在不改变泵与电机连接的前提下,很好地扩展了T7BS 系列叶片泵的排量规格。
T7CS 系列叶片泵也可以选用SAE 花键轴,允许泵轴直接与电机轴相连接。
T7CS, Denison 叶片泵订货代号及安装尺寸型号T7CS - E25 - 4 R 00 - A 1 MW - MØ48SUCTION Ø25,4PRESSURE PST7CS 系列 - SAE J744SAE B 2孔安装法兰排量容积排量(cm3/rev.)E17 = 58,3E20 = 63,8E22 = 70,3E25 = 79,3传动轴类型1 = 平键轴(SAE B)3 = 花键轴(SAE B) 13齿4 = 花键轴(SAE BB) 15齿转向(从轴端方向看)R = 右转(顺时针)L = 左转(逆时针)修改代码Ex : NOP = 不喷漆油口形式MW = S = 特殊的法兰P = 1" - SAE J518 4螺栓法兰 公制螺纹密封等级1 = S1 BUNA N 5 = S5 VITON®设计序列号油口方向配置00 = 标准配置输入扭矩极限:轴Vi [cm 3/rev] x p max. [bar]Nm 116500262320600327420600327重量:23,0 kg转动惯量:7,5 Kgm 2 x 10-4P = 压油口S = 吸油口派克汉尼汾在中国的联系方式派克汉尼汾中国总部上海市金桥出口加工区云桥路280号邮编:201206电话:+86 - 21 - 2899 5000北京分公司北京经济技术开发区荣华南路2号院2号楼2201室邮编:100004电话:+86 - 10 - 8527 7300广州分公司广州市萝岗区科学城彩频路11号广东软件科学园F栋202室邮编:510663电话:+86 - 20 - 3212 1688大连办事处大连市高新园区火炬路3号纳米大厦11层1101室邮编:116023电话:+86 - 411 - 3964 6767西安办事处西安市高新区定昆池三路777号邮编:710065电话:+86 - 29 - 8111 8062成都办事处成都市锦江区锦东路568号摩根中心2栋10楼7号邮编:610066电话:+86 - 28 - 6180 6800长沙服务中心长沙市经济技术开发区板仓南路26号新长海数码中心2楼V24-V25室邮编:410005电话:+86 - 731 - 8985 1529派克汉尼汾香港有限公司香港九龙尖沙咀海港城港威大厦2座20楼01 - 04室电话:+86 - 852 - 2428 800819-06-B HYD-CH-4P-T7CSVSD。
Eaton Moeller 系列 Rapid Link 速控器 198868 说明书
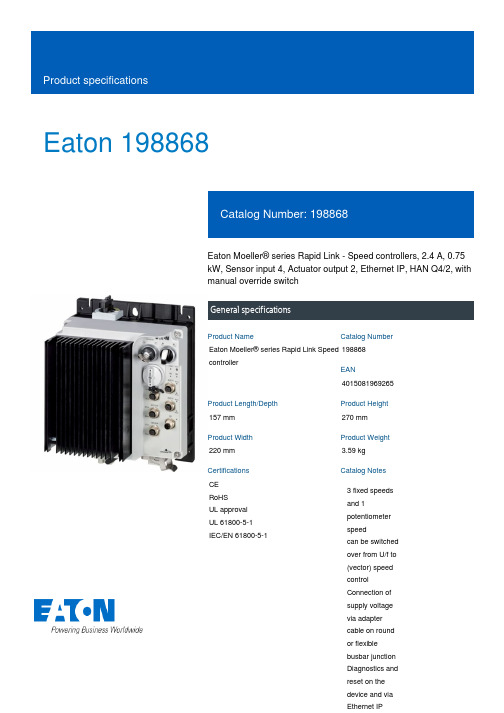
Eaton 198868Eaton Moeller® series Rapid Link - Speed controllers, 2.4 A, 0.75 kW, Sensor input 4, Actuator output 2, Ethernet IP, HAN Q4/2, with manual override switchGeneral specificationsEaton Moeller® series Rapid Link Speed controller1988684015081969265157 mm 270 mm 220 mm 3.59 kg CE RoHS UL approval UL 61800-5-1 IEC/EN 61800-5-1Product NameCatalog NumberEANProduct Length/Depth Product Height Product Width Product Weight Certifications Catalog Notes 3 fixed speeds and 1 potentiometer speedcan be switched over from U/f to (vector) speed control Connection of supply voltage via adapter cable on round or flexible busbar junction Diagnostics and reset on the device and via Ethernet IPParameterization: drivesConnect mobile (App) Parameterization: drivesConnectParameterization: FieldbusParameterization: KeypadIGBT inverterPTC thermistor monitoringSelector switch (Positions: REV - OFF - FWD)Key switch position OFF/RESETKey switch position HANDTwo sensor inputs through M12 sockets (max. 150 mA) for quick stop and interlocked manual operationThermo-click with safe isolationKey switch position AUTO2 Actuator outputsControl unitInternal DC linkPC connectionManual override switch3 fixed speeds1 potentiometer speed IP65NEMA 121st and 2nd environments (according to EN 61800-3)IIISpeed controllerEtherNet/IPC2, C3: depending on the motor cable length, the connected load, and ambient conditions. External radio interference suppression filters (optional) may be necessary.C1: for conducted emissions only2000 VAC voltagePhase-earthed AC supply systems are not permitted. Center-point earthed star network (TN-S network)Vertical15 g, Mechanical, According to IEC/EN 60068-2-27, 11 ms, Half-sinusoidal shock 11 ms, 1000 shocks per shaftResistance: 57 Hz, Amplitude transition frequency on accelerationResistance: According to IEC/EN 60068-2-6Resistance: 10 - 150 Hz, Oscillation frequencyResistance: 6 Hz, Amplitude 0.15 mm Above 1000 m with 1 % performance reduction per 100 m Max. 2000 m-10 °C40 °C-40 °C70 °CFeatures Fitted with:Functions Degree of protectionElectromagnetic compatibility Overvoltage categoryProduct categoryProtocolRadio interference classRated impulse withstand voltage (Uimp) System configuration typeMounting position Shock resistance Vibration AltitudeAmbient operating temperature - min Ambient operating temperature - max Ambient storage temperature - min Ambient storage temperature - max Climatic proofingIn accordance with IEC/EN 50178< 95 %, no condensationCurrent limitationAdjustable, motor, main circuit0.2 - 2.4 A, motor, main circuitDelay time< 10 ms, Off-delay< 10 ms, On-delayEfficiency97 % (η)Input current ILN at 150% overload2.5 ALeakage current at ground IPE - max3.5 mAMains current distortion120 %Mains switch-on frequencyMaximum of one time every 60 secondsMains voltage - min380 VMains voltage - max480 VMains voltage tolerance380 - 480 V (-10 %/+10 %, at 50/60 Hz)Operating modePM and LSPM motorsBLDC motorsSynchronous reluctance motorsU/f controlSensorless vector control (SLV)Output frequency - min0 HzOutput frequency - max500 HzOverload currentAt 40 °CFor 60 s every 600 sOverload current IL at 150% overload3.6 A45 Hz66 Hz0.75 kW400 V AC, 3-phase480 V AC, 3-phase0.1 Hz (Frequency resolution, setpoint value)200 %, IH, max. starting current (High Overload), For 2 seconds every 20 seconds, Power section50/60 Hz8 kHz, 4 - 32 kHz adjustable, fPWM, Power section, Main circuitAC voltagePhase-earthed AC supply systems are not permitted.Center-point earthed star network (TN-S network)1 HP≤ 0.6 A (max. 6 A for 120 ms), Actuator for external motor brakeAdjustable to 100 % (I/Ie), DC - Main circuit10 kAType 1 coordination via the power bus' feeder unit, Main circuit 24 V DC (-15 %/+20 %, external via AS-Interface® plug)Ethernet IP, built inPlug type: HAN Q4/2Specification: S-7.4 (AS-Interface®)Max. total power consumption from AS-Interface® power supply unit (30 V): 250 mANumber of slave addresses: 31 (AS-Interface®)C2 ≤ 5 m, maximum motor cable length C3 ≤ 25 m, maximum motor cable length C1 ≤ 1 m, maximum motor cable lengthMeets the product standard's requirements.Meets the product standard's requirements.Rated frequency - minRated frequency - maxRated operational power at 380/400 V, 50 Hz, 3-phase Rated operational voltageResolutionStarting current - maxSupply frequencySwitching frequencySystem configuration type Assigned motor power at 460/480 V, 60 Hz, 3-phase Braking currentBraking torqueRated conditional short-circuit current (Iq)Short-circuit protection (external output circuits) Rated control voltage (Uc)Communication interfaceConnectionInterfacesCable length10.2.2 Corrosion resistance10.2.3.1 Verification of thermal stability of enclosures10.2.3.2 Verification of resistance of insulating materials tonormal heatMeets the product standard's requirements.Meets the product standard's requirements.Meets the product standard's requirements.Does not apply, since the entire switchgear needs to be evaluated.Does not apply, since the entire switchgear needs to be evaluated.Meets the product standard's requirements.Does not apply, since the entire switchgear needs to be evaluated.Meets the product standard's requirements.Does not apply, since the entire switchgear needs to be evaluated.Does not apply, since the entire switchgear needs to be evaluated.Is the panel builder's responsibility.Is the panel builder's responsibility.Is the panel builder's responsibility.Is the panel builder's responsibility.Is the panel builder's responsibility.The panel builder is responsible for the temperature rise calculation. Eaton will provide heat dissipation data for the devices.Generation change from RA-SP to RASP 4.0Connecting drives to generator suppliesGeneration change RAMO4 to RAMO5Generation change from RA-MO to RAMO 4.0Generation Change RASP4 to RASP5Electromagnetic compatibility (EMC)Configuration to Rockwell PLC for Rapid LinkGeneration Change RA-SP to RASP5Rapid Link 5 - brochureDA-SW-drivesConnect - InstallationshilfeDA-SW-Driver DX-CBL-PC-3M0DA-SW-USB Driver PC Cable DX-CBL-PC-1M5DA-SW-drivesConnect - installation helpDA-SW-drivesConnect USB Driver DX-COM-PCKITDA-SW-USB Driver DX-COM-STICK3-KITDA-SW-drivesConnectMaterial handling applications - airports, warehouses and intra-logisticsProduct Range Catalog Drives EngineeringProduct Range Catalog Drives Engineering-ENDA-DC-00004184.pdfDA-DC-00004514.pdfDA-DC-00003964.pdfDA-DC-00004508.pdfeaton-bus-adapter-rapidlink-speed-controller-dimensions-005.eps eaton-bus-adapter-rapidlink-speed-controller-dimensions-004.eps eaton-bus-adapter-rapidlink-speed-controller-dimensions-003.eps eaton-bus-adapter-rapidlink-speed-controller-dimensions-002.epsETN.RASP5-2420EIP-412R000S1.edzIL034093ZU10.2.3.3 Resist. of insul. mat. to abnormal heat/fire by internalelect. effects10.2.4 Resistance to ultra-violet (UV) radiation10.2.5 Lifting10.2.6 Mechanical impact10.2.7 Inscriptions10.3 Degree of protection of assemblies10.4 Clearances and creepage distances10.5 Protection against electric shock10.6 Incorporation of switching devices and components 10.7 Internal electrical circuits and connections10.8 Connections for external conductors10.9.2 Power-frequency electric strength10.9.3 Impulse withstand voltage10.9.4 Testing of enclosures made of insulating material 10.10 Temperature rise Application notes BrochuresCatalogues Certification reports DrawingseCAD model Installation instructionsEaton Corporation plc Eaton House30 Pembroke Road Dublin 4, Ireland © 2023 Eaton. All rights reserved. Eaton is a registered trademark.All other trademarks areproperty of their respectiveowners./socialmediaIs the panel builder's responsibility. The specifications for the switchgear must be observed.Is the panel builder's responsibility. The specifications for the switchgear must be observed.The device meets the requirements, provided the information in the instruction leaflet (IL) is observed.Rapid Link 5MN034004ENMZ040046_ENMN040003_ENDA-MN-MZ040044ENrasp5_v31.stpramo5_v31.dwg10.11 Short-circuit rating10.12 Electromagnetic compatibility 10.13 Mechanical function Installation videos Manuals and user guidesmCAD model。
T6 叶片泵进出油口连接螺纹系列号说明

T6 单泵型号 T6C — 010 — 1 R 00 — B 1 M0
油口连接螺纹
油 口 法 兰 规 格 S T6C T6D T6E 1 1/2″ 2″ 3″ P 1″ 1 1/4″ 1 1/2″
油口螺纹 公制螺纹 M0 M0 M0 UNC螺纹 00 00 00
可省略 可省略 可省略
T6双联泵型号 双联泵型号
T6CC — 025 — 020 — 1 R 00 — C 1 M0
油口连接螺纹
油 口 法 兰 规 格 S 3″ T6CC 2 1/2″ 3″ 2 1/2″ T6DC T6EC T6ED 3″ 3 1/2″ 4″ 11/4″ 1 1/2″ 1 1/2″ 1″
3/4″
油口螺纹 P2 1″ 1″
3/4″
P1 1″
公制螺纹 M00 M10 M01 M11 M0 M0 M0UNC螺纹 0ຫໍສະໝຸດ 10 01 11 00 00 00
可省略 可省略 可省略
1″ 1″ 11/4″
注:1)油口连接螺纹系列号编制参照T7泵。
2)油口公制连接螺纹的尺寸: T6C 同 T7B; T6D 同 T7D; T6E 同 T7E; T6DC 同 T67DC; T6EC 同 T67EC; T6ED 同 T7ED。 3)T6CC 油口公制连接螺纹的间距尺寸同 UNC 油口。 公制螺纹的直径为: 3/4″——M10×19; 1″——M10×19; 2 1/2″——M12×22; 3″——M16×28。 4)T6泵进出油口公制连接螺纹的尺寸可详见附表。
T6CC-031-010-1R00-C1叶片泵型号解读

丹尼逊T6CC-031-010-1R00-C1叶片泵型号解读
泵芯规格系列代号:C:较小排量系列(10.8~100.0ml/rev)
类型代号:无:工业用型M:车(行走机械)用型P:车(行走机械)用型,双重轴封辅助类型代号:采用重载传动轴,仅适用于T6CC,T6CC*,T6DC及T6DC*
传动轴型式:1:非SAE平键3:SAE BB花键5:SAE B平键
旋转方向:R:右转(顺时针转向)L:左转(逆时针转向)
油口方向:00:进油口对侧01:进油口同侧
02:相对进油口逆时针90°03:相对进油口顺时针90°
设计号:由生产商制定
密封等级:1=S1(适用于矿物油基液压油)常用的
4=S4(适用于抗燃液压液)
5=S5(矿物油基液压油及抗燃液压液,吸油口最高压力可达7bar)
以上是丹尼逊T6CC叶片泵的完整型号,再购买中能方便随时找到相应的型号,如遇到特殊型号的,伊特液压随时欢迎咨询。
丹尼逊T6C-031-1R00-B1叶片泵型号解读

丹尼逊T6C-031-1R00-B1叶片泵型号解读
泵芯配流侧板类型:-0:单转向型-B:双转向型(仅使用于C/D系列车用性泵)
排量代号:
传动轴型式:1:SAE B平键2:非SAE B平键3:SAE B花键4:SAE BB花键
旋转方向:R:右转(顺时针转向)L:左转(逆时针转向)
油口方向:00:进油口对侧01:进油口同侧
02:相对进油口逆时针90°03:相对进油口顺时针90°
设计号:由生产商制定
密封等级:1=S1(适用于矿物油基液压油)常用的
4=S4(适用于抗燃液压液)
5=S5(矿物油基液压油及抗燃液压液,吸油口最高压力可达7bar)
以上是丹尼逊T6C叶片泵的完整型号,再购买中能方便随时找到相应的型号,如遇到特殊型号的,伊特液压随时欢迎咨询(微信:itty6868)。
丹尼逊液压泵叶片泵Denison vane pumps

T6E – 流量 42 to 85 GPM;(132.3 — 269ml/rev)
042 045 050 052 062 066 072 085
新 T7B – 流量 2 to 15 GPM。(5.8 — 50ml/rev)
002 003 004 006 008 011 012 013 015
额定流量按 1200 RPM 可有行走机械(车用)标准产品
7
叶片泵产品
不同的定子尺寸
定子圈外径
T6C-010 内部尺寸
T6C-028 内部尺寸
16
叶片泵产品
T6 叶片泵工作原理示图
17
叶片泵产品
T6 叶片泵工作原理剖视图
18
叶片泵产品
Denison 叶片泵特征
液压平衡转子 吸口
无侧向液压负载
IN
OUT
出口 齿轮泵: 无平衡功能,出口高 压力会造成较大的侧向负载力
19
叶片泵产品
Denison 叶片泵特征
整体式泵芯概念
所有泵唧零件均组合在一个泵芯组件内
20Biblioteka 叶片泵产品柱销式叶片顶销
较小的叶片撞击
高压油
21
叶片泵产品
柱销叶片设计优点
2002/6/30
叶片泵产品
传动轴扭矩限制
举例:对T6DC-050-014 泵,如何确定其在最高 间断压力下传动轴所需的扭矩?
泵排量: 050 = 9.64 in3/rev. : 014 = 2.81 in3/rev.
最高间断压力:3000 psi :
4000 psi
050所需扭矩:9.64 x 3000 = 28920
EATON CMA200高级CAN-Enabled电子水力切割移动阀门200LPM440条大气压CA

Subject title CMA200Advanced Independent-Metering Mobile Valve200LPM440 barCAN BusContents2EATON CMA200 Technical Document E-VLMB-BB002-E1 September 2016The CMA200 is an advanced CAN-Enabledelectro-hydraulic sectional mobile valve with independent metering that utilizes pressureand position sensors, on board electronics, and advanced software control algorithms. Where conventional mobile valves often compromiseon precision or response, the CMA delivers both. The CMA offers high performance with sub micron hysteresis, closed loop control over the spool position, and repeatable performance.CMA offers customers the next generation in advanced mobile valves with unlimited possibilities to differentiate your machine capabilities.Key Benefits of this advanced mobile valve include:• Precise control maintained for all load conditions• Reduction in metering losses / energy management• High valve responsiveness• Flow Sharing – Pre and Post Comp Capabilities• Flexibility in configuration / easily change parameters• Command factory-calibrated flow or pressure from eitherwork port• Easier communication with the valve• Reduced load on the Vehicle CAN bus• Advanced Diagnostics for improved reliability and productivity • Hose Burst Detection• Limp mode• Diagnostics on the inlet, tank, load sense, work port pressures, spool position, consumed flow, and oil temperature.• Platform can support future software development for future product development.• Reliable performance across a broad temperature rangeIntroductionEATON CMA200 Technical Document E-VLMB-BB002-E1 September 2016 3CMA200 Specificationsand PerformanceInlet Rated and Work Port 380 bar (5511 psi)Inlet Max and Work Port 440 bar (6382 psi)Tank* Max 30 bar (435 psi)FlowWork Port (max with highflow spools, measured withinternal pressure sensors) 200 lpm (53 gpm) @ 16 bar Δ P Max inlet flowwhen two sections are fully open.400 lpm (106 gpm) @ 35 bar P-T Leakage**Max Leakage withoutWork Port Valves 30 cc @100 bar @ 21 cstMax Leakage withWork Port Valves 40 cc @100 bar @ 21 cst ConstructionSectional Up to 8 sections per blockUp to 15 sections per VSMPort TypesSAE P1 & P2 = 1 1/16”-12 UN (SAE-12),T = 1 5/16”- 12 UN (SAE-16), LS =7/16”-20 UNF (SAE-04), A&B = 3/4”-16 UNF (SAE-08) OR 7/8”-14 UNF(SAE-10) OR 1 1/16”-12 UN (SAE-12) BSP P1 & P2=G 3/4, T=G 1, LS=G 1/4,A&B = G 1/2 OR G 3/4Inlet section optionsVariable Displacement(Load Sensing)Fixed DisplacementWork section optionsLow Flow Spools 100 lpm (26 gpm)High Flow Spools 200 lpm (53 gpm)Work Port Valves Anti-CavitationPort Relief & Anti-CaviationPort ReliefCompensation typeDigital On meter-in and meter-out ActuationPrimary CANEmergency Mechanical OverrideControl modesFlowPressureSpool PositionFloat Ambient (operating) -40°C to 105°CStandard Oil (operating)***** -40°C to 85°CExtended Oil (operating) -20°C to 105°CStorage -40°C to 105°CFiltrationISO 4406 18/16/13Pressure Reducing Valve 75 micronPilot Valve 100 micronElectromagnetic protectionEMC Directive 2014/30/EC ***Earth Moving ISO 13766: 2006 Construction EN 13309: 2010Agriculture ISO 14982:2009Electrical environmental****Ingress Protection IP67Thermal Cycling -40C to 105C for 1000 cycles Mechanical Shock 50G ½ sine wave, 11ms pulse Random VibrationMethod MIL STD 202G, Method 214-1 Limits Test Condition A Duration 8 hrs/axis # Of Axis 3 separatelyProfile Reference AppendixOil Temperature viscosityRecommended Viscosity 85 to 10 cStAbsolute Maximum Viscosity 2250 cStAbsolute Minimum Viscosity 7 cStElectricalInput Voltage 9 - 32 VDCPower Consumption Range Reference AppendixCAN Interface J1939 2.0B, CAN OpenElectrical interface connectorsDeutsch (VSM) DT06-12SB-P012Deutsch (VSE) DT06-12SA-P012Dynamic performanceLoop Time for Internal CAN 3msTypical Step Response 24 ms @ 15 cStTypical Frequency Response 17.5 Hz @ 15 cStPressures Temperatures* W ith manual override, tank limited to 10 bar (145 psi) maximum. Max 30bar is at constant rate.**Data taken from work port to tank and supply***Electronics are designed to power down and recover automatically undervarious power conditions (ie.. Load Dump, Ignition Cranking, Disconnectionof Inductive Loads). CE testing with J1939 at 250 kb/s****Additional Electrical Environmental tests were performed. ContactEaton for additional details, if desired.*****It is recommended that the CMA valves not be subjected to a thermaldifference of greater than 50°F (28°C).EATON CMA200 Technical Document E-VLMB-BB002-E1 September 20164Valve cross section:1. Pilot Valve2. Main Stage3. Linear Position Sensor4. Port Reliefs / Anti-Cavs5. Main Metering Spools6. Work Port A7. Work Port B 123475 6CMA200 Advanced Sectional Mobile ValvesCross SectionsEATON CMA200 Technical Document E-VLMB-BB002-E1 September 2016 5Principles of OperationThe work section is comprised of two independent spoolsthat act as a pair working to control double acting services, or alternatively as single spools controlling a single acting service (2 single axis services can be controlled from any work section).Demands to each work section are transmitted over a CAN Bus and power is provided to eachwork section via a single daisychain cable arrangement. Eachwork section has a single pilotvalve comprised of on-boardelectronics, embedded sensors,and two independent 3 position4 way pilot spools driven by alow power embedded microcontroller.The independent pilot spoolscontrol the mainstage spools.Closed loop control of eachwork section is done locallyby leveraging the on-boardelectronics and sensors.Each mainstage spool has itsown position sensor enablingclosed loop position control ofthe mainstage spool.Further, a pressure sensoris located in each work port,pressure line and tank line.With the up and downstreampressure information known atany time, flow delivered to theservice can be controlled bymoving the spools to create theappropriate orifice area for thedesired flow rate. Figure 1: CMA system with Load-Sensing Inlet & a single work-sectionFigure 2: CMA system with Fixed Displacement Inlet & a single work-sectionCMA200 Advanced Sectional Mobile ValvesEATON CMA200 Technical Document E-VLMB-BB002-E1 September 20166CMA200 Advanced Sectional Mobile ValvesFigure 3: Extension InletEATON CMA200 Technical Document E-VLMB-BB002-E1 September 2016 78There are multiple interconnection options for the CMA200 valve systems.The following illustrates possible system configuration options. Configuration is dependent on application requirement and is constrained by the following rules:• Sectional construction with up to 8 sections per bank • Maximum 15 sections per Valve System Module (VSM)• One VSM and CV required per system• If distance between an extension valve bank and the VSM or VSE is less than 6 meters, they can be connected using a daisy chain extension cable. See options on page 12• If distance between valve banks is greater than 6 meters, they must be connected using a VSE and external wiring harness. Max distance between a VSM and VSE is 30 meters. See page Total Interconnect CAN(ICAN) Wiring LengthsN e t w o r kUser CAN, or UCAN, is the machine’s CAN network that communicates with the VSM.If the VSM is at the end of the UCAN network, a 120 ohm termination resistor built into the VSM can be User Ca bles T ermina tion• No more than two (2) valve system extenders (VSE) per system • If more than 15 work sections are required, this can by accomplished by using additional CMA systems and theircorresponding VSM. Additional VSMs will appear as another Node on the User CAN Network.• If application specific Electromagnetic Compatibility testing indicates CAN cable shielding is needed, connect CAN shield as shownCMA Wiring Harness DetailsEATON CMA200 Technical Document E-VLMB-BB002-E1 September 2016 9Single block system5 UCAN HIGH A 2 SHIELD 4 UCAN LOW B10 ICAN HIGH B 12 BATTERY -1 BATTERY + 9-32 VDC7ICAN TERMINATE9ICAN LOW A8 ICAN HIGH A 11 ICAN LOW B 6 UCAN TERMINATE 3 UCAN LOW A 120OHMVSMUser CAN Connection1 BATTERY + 9-32 VDC 7 ICAN TERMINATE9ICAN LOW A8 ICAN HIGH A 11 ICAN LOW B 6SECOND VSE ID2 SECOND VSE ID RETURN NC NC NC 10 ICAN HIGH B12 BATTERY -Us5 UCAN HIGH A 3 UCAN LOW A 2 SHIELD 4 UCAN LOW B 10 ICAN HIGH B12 BATTERY -1BATTERY + 9-32 VDC7 ICAN TERMINATE 9 ICAN LOW A 8ICAN HIGH A11 ICAN LOW B 6 UCAN TERMINATE Valve Block 1Valve Block 2120OHMVSEVSM120OHMUser CAN ConnectionCASE SCREWDouble block system with valve system extender (VSE)5 UCAN HIGH A 2 SHIELD 4 UCAN LOW B10 ICAN HIGH B 12 BATTERY -1 BATTERY + 9-32 VDC 7ICAN TERMINATE9 ICAN LOW A 8 ICAN HIGH A 11 ICAN LOW B 6 UCAN TERMINATE 3UCAN LOW A120OHMVSMUser CAN Connection1 BATTERY + 9-32 VDC7 ICAN TERMINATE 9ICAN LOW A8 ICAN HIGH A 11 ICAN LOW B6 SECOND VSE ID2 SECOND VSE ID RETURN NCNC NC 10 ICAN HIGH B 12 BATTERY -5 UCAN HIGH A 3 UCAN LOW A 2 SHIELD 4 UCAN LOW B 10 ICAN HIGH B12 BATTERY -1BATTERY + 9-32 VDC 7ICAN TERMINATE 9 ICAN LOW A 8 ICAN HIGH A 11 ICAN LOW B6 UCAN TERMINATE Valve Block 1Valve Block 2120OHMVSEVSM120OHMUser CAN ConnectionCASE SCREWInterconnect CAN, or ICAN, is the CAN network between the VSM and VSE’s.120 ohm termination resistors in the VSM and VSE’s circuits can be connected with the installation ofwire jumpers each device. Two sets of ICAN pins are available in a VSM or VSE to allow daisy chaining ICAN if a VSM/VSE is in the middle of the CMA system. If no VSE’s exist in a system, it is still necessary to install a jumper to activate one 120 ohm termination resistor on the ICAN bus.Interconnect CAN T ermina tionCMA Wiring Harness DetailsEATON CMA200 Technical Document E-VLMB-BB002-E1 September 201610CMA Wiring Harness DetailsCMA Wiring Harness DetailsTEATON CMA200 Technical Document E-VLMB-BB002-E1 September 2016 11EATON CMA200 Technical Document E-VLMB-BB002-E1 September 201612Work Section Options – Software VersionsSo tware DescriptionPressure compensated flow control Load-independent flow controlFlow compensated pressure control Single service pressure control while either sinking or sourcing flow.Intelli floatLowers the load at a configurable rate and then enters full float modeStandard ratio flow share Pre or post comp capabilities in one valve block. All service flow demands are reduced by the (with priority capability) same ratio. Can also exempt services from flow-sharing to maintain priority. This feature prevents the pump from saturating when flow demands to the valve sum to be larger than thepump can provide.Intelligent twin spool flow control (IFC)V ersatile flow controller which maintains the desired flow independent of transitions between passive and overrunning loadsLoad damping A feature of IFC and UFC which reduces service oscillation induced by moving large structures, such as a boom.Electronic load sense enabled E nables operation with a compatible pump or when multiple CMA systems are presenton the same CAN networkElectronic work port relief valve Configurable electronically controlled relief valve against externally applied loads Electronic work port pressure limit (feed reducer) C onfigurable electronically controlled pressure limit applied to user flow demandswithout consuming additional pump flow Single spool flow controlSink or source flow on individual service ports Single spool position control Direct spool position control on each spool Smart Data D iagnostics on all on-board sensors. Inlet, Tank, LS, Work Port pressures, Spool Positions, oiltemperature sensor data availability.A - Standard software control featuresSo tware DescriptionTorque ControlAdvanced force or torque control for double-acting cylinders or motors Data control packageBroadcast of each spool’s flow consumptionCascade and Uniform Flow Share Cascade: maintains demanded flow to selected high priority services by reducing flow to lowest priority servicesU niform: All flow demands are reduced by the same absolute amount (i.e. all reduced by 1 lpm)So tware DescriptionHose burst detection P revents major oil spill events by monitoring flow consumption on each service and closing the spools for that circuit if a major leak is detected Limp modeI f a sensor fails, the valve will continue to work with reduced performance until the machine can be servicedU – Advanced control packageV – Advanced service packageT – All PackagesIncludes Standard, Advanced Control, and Advanced Service packagesEATON CMA200 Technical Document E-VLMB-BB002-E1 September 2016 13CMA200 Advanced Sectional Mobile ValveCMA200 Installation Views: 8 Section Inlet Block With Manual OverrideUnits: mmDimension /1/2/3/4/5/6/7/8A (mm)56.0112.0168.0224.0280.0336.0392.0448.0Weights (kg)26.534.642.850.959.167.375.483.6Number of sections A ’ sideSeries connectorEATON CMA200 Technical Document E-VLMB-BB002-E1 September 201614Dimension /1/2/3/4/5/6/7/8A (mm)56.0112.0168.0224.0280.0336.0392.0448.0Weights (kg)24.732.339.847.354.862.369.877.4Number of sections CMA200 Advanced Sectional Mobile ValveCMA200 Installation Views: 8 Section Inlet Block Without Manual OverrideUnits: mmboth endsEATON CMA200 Technical Document E-VLMB-BB002-E1 September 2016 15CMA200 Advanced Sectional Mobile ValveCMA200 Installation Views: 8 Section Extension Block With Manual OverrideUnits: mmBracket location Corientation. Brackets also available 3 tie rodsA ’ sideSeries connectorboth endsDimension /1/2/3/4/5/6/7/8A (mm)56.0112.0168.0224.0280.0336.0392.0448.0Weights (kg)24.332.440.648.756.965.173.281.4Number of sectionsEATON CMA200 Technical Document E-VLMB-BB002-E1 September 201616CMA200 Advanced Sectional Mobile ValveCMA200 Installation Views: 8 Section Extension Block Without Manual OverrideM10 X 1Units: mmDimension /1/2/3/4/5/6/7/8A (mm)56.0112.0168.0224.0280.0336.0392.0448.0Weights (kg)22.530.137.645.152.660.167.675.1Number of sectionsModel Code For Inlet Section1CMA200 Series2Communication Protocol J J1939C CAN OPEN0 None3Interface ModuleM VSME VSE0 None4Port T ypesS SAE P1 = 1 1/16”-12UN (SAE-12)P2 = 1 1/16”-12UN (SAE-12)T = 1 5/16”- 12UN (SAE-16)LS = 7/16”-20UNF (SAE-04)B BSP P1= G 3/4P2= G 3/4T = G 1LS= G 1/45Inlet Pressure ControllerV VariableDisplacementF Fixed Displacement0 none, Used on VSEor extension block6Active Pressure Port1 P13 P1 & P27Manual Override0 NoneM Manual Overrideon CV8Main Relief Setting(In bar)000 = None155 293172 310190 328207 345224 362241 379259 397276 4149Pa int T ypeK Std. Flat Black10 Se a ls1 Default11Special Features00 None12Software VersionXXA Standard Software13Design Code10 Design Code214CMA200 * * * * * * *** * * ** *** **59811131236710Note: A pressure limit can be set on the valve in software to any value in increments of 0.01 barusing available configuration software suite. This applies to both inlet and work port settings.Note: No relief valve is available for extension inlets.EATON CMA200 Technical Document E-VLMB-BB002-E1 September 2016 17EATON CMA200 Technical Document E-VLMB-BB002-E1 September 201618214CMZ200 * ** * *** ** * *** * * ** *** ** **5981113141236710Model Code – Work Section1 CMZ200 Series2 Body Port Thread Sizes A 3/4” 16 UNF (SAE-8)B 7/8” 14 UNF (SAE-10)C 1-1/16” 12 UN (SAE-12)D G 1/2”E G 3/4”3 Spool T ype at Position AHC 200 lpm, biasedto centerHT 200 lpm, biased to tankHP 200 lpm, biased to pressure LC 100 lpm, biased to centerLT 100 lpm, biased to tankLP 100 lpm, biased to pressure4 Valve Option at A0 NoneB Anti-cavitation valve with relief valveC Anti-cavitation valve S Relief valve 5 Relief Setting at Position ARV Setting in Bar 000 = None155 293 172 310 190 328 207 345 224 362 241 379 259 397 276 4146 Spool T ype at Position BHC 200 lpm, biased to centerHT 200 lpm, biased to tankHP 200 lpm, biased to pressure LC 100 lpm, biased to centerLT 100 lpm, biased to tankLP 100 lpm, biased to pressure7 Valve Option at B0 NoneB Anti-cavitation valve with relief valveC Anti-cavitation valve S Relief valve 8 Relief Setting at Position BRV Setting in Bar 000 = None 155 293 172 310 190 328207 345 224 362241 379 259 397276 4149 Manual Override T ype0 NoneA Lever-handle toward port AB Lever-handle toward port B 10 Pa int T ypeKStd. Flat Black11 Seal1 Default (NBR)12 Special Features00 None13 Software VersionXXA Standard SoftwareXXU Advanced Control PackageXXV Advanced ServicePackage XXT All Packages(Standard plus all Advanced Packages)14 Design Code10 Design CodeNote : A pressure limit can be set on the valve in software to any value in increments of 0.01 barusing available configuration software suite. This applies to both inlet and work port settings.Note : If an option without a relief is selected for port A or B, no relief valve setting should be selected in corresponding Relief Setting position (i.e., select 000). Likewise, when selecting a valve option with a relief, make sure to select a corresponding relief setting.Note : High flow or low flow spools must be selected for both work ports. They cannot be mixed (i.e. a high flow spool on work port A and low flow spool on work port B).NotesEATON CMA200 Technical Document E-VLMB-BB002-E1 September 2016 19© 2016 EatonAll Rights Reserved Printed in USADocument No. E-VLMB-BB002-E1 September 2016EatonHydraulics Group USA 14615 Lone Oak Road Eden Prairie, MN 55344USATel: 952-937-9800Fax: 952-294-7722/hydraulicsEatonHydraulics Group Europe Route de la Longeraie 71110 Morges SwitzerlandTel: +41 (0) 21 811 4600Fax: +41 (0) 21 811 4601EatonHydraulics Group Asia Pacific Eaton BuildingNo.7 Lane 280 Linhong Road Changning District,Shanghai 200335ChinaTel: (+86 21) 5200 0099Fax: (+86 21) 2230 7240。
丹尼逊叶片泵T6DCC[1]
![丹尼逊叶片泵T6DCC[1]](https://img.taocdn.com/s3/m/a30f44b265ce05087632137e.png)
(T6EDC)三联叶片泵T67DBB, T67DCB, T6DCC 系列T67DDBS, T6DDCS 系列 T67EDB(S), T6EDC(S) 系列型號说明 ............................................................................................................ 例 : T6EDC-072-042-020-1R00-A1F0 1.-072-025-020-1R00-A1F0 .............. 系列号SAE 安装型式 T67DBB T67DCB T6DCCT67DDBS T6DDCS T67EDBS T6EDCS ISO 安装T67EDB T6EDC2. T6EDC-072-025-020-1R00-A1F0 ........... 泵芯规格B CDEB02......... 5.8 003 ....... 10.8 014 ....... 47.6 042 ..... 132.3B03......... 9.8 005 ....... 17.2 017 ....... 58.2 045 ..... 142.4B04....... 12.8 006 ....... 21.3 020 ....... 66.0 050 ..... 158.5B05....... 15.9 008 ....... 26.4 024 ....... 79.5 052 ..... 164.8B06....... 19.8 010 ....... 34.1 028 ....... 89.7 057 ..... 179.8B07....... 22.5 012 ....... 37.1 031 ....... 98.3 062 ..... 196.7B08....... 24.9 014 ....... 46.0 035 ..... 111.0 066 ..... 213.3B10....... 31.8 017 ....... 58.3 038 ..... 120.3 072 ..... 227.1B12....... 41.0 020 ....... 63.8 042 ..... 136.0 085 ..... 269.0B15....... 50.0 022 ....... 70.3 045 ..... 145.7 025 ....... 79.3 050 ..... 158.0 028 ....... 88.8 031 ..... 100.03. T6EDC-072-025-020-1R00-A1F0 ........... 軸伸形式4. T6EDC-072-025-020-1R 00-A1F0 .................. 轉向顺时针 R 逆时针L5. T6EDC-072-025-020-1R 00-A1F0 .................. 油口6. T6EDC-072-025-020-1R00-A 1F0 .............. 设计號7. T6EDC-072-025-020-1R00-A 1F0 .......... 密封等级丁晴橡胶:矿物油1 氟橡胶:矿物油和防火油液58. T6EDC-072-025-020-1R00-A1F0 ......... 连接型式P3 = ¾” P3 = 1” 公制 UNC公制UNCT67DBB T67DCB 法兰式安装 M1 01 - - T6DCC 法兰式安装 M1 01 M000 T6DDCS 法兰式安装 M1 01 M000 T67DDBS 法兰式安装 M1 01 - - T67EDB 法兰式安装 支座安装 F1 P1 - - - T6EDC 法兰式安装 支座安装 F1 P1 - F0 P0 - T6EDCS法兰式安装 支座安装F1 P1-F0 P0軸伸最大扭矩 (N.m) 尺寸 (mm)T67DBBT67DCBT6DCC L1 L2 直径K1 x K2 H1 M11 平键 : No SAE (∅31) 721 721 83.6 49.3 31.750 – 31.700 6.35 x 6.30 34.62 平键 : SAE CC (∅38) 1108 1108 89.7 50.8 38.100 – 38.0759.52 x 9.47 42.43 花键 : SAE C z z55.2 38.0 Class 1-J498b, 12/24 d.p. - 14 牙4 花键 : SAE CC z z61.0 31.5 Class 1-J498b, 12/24 d.p. - 17 牙6 花键 : No SAE z76.0 48.0 Class 1-J498b, 12/24 d.p. - 14 牙油口尺寸 (mm)A1 B1 ∅C1 D1T1口螺纹公制UNCT67DBB T67DCB P1 1 ¼” 30.2 58.7 31.8 82.6 M12 x 22.3 7/16”-14UNC x 22.3 P2 1” 26.2 52.4 25.0 101.6 M10 x 19.0 3/8”-16UNC x 19.0 P3 ¾” 22.2 47.7 19.0 74.7 M10x19.0 3/8”-16UNC x 19.0 S 4” 77.8 130.2 101.6 127.0 M16x30.0 5/8”-11UNC x 30.0T6DCC P1 1 ¼” 30.2 58.7 31.8 82.6 M12 x 22.3 7/16” - 14UNC x 22.3 P2 1” 26.2 52.4 25.0 101.6 M10 x 19.0 3/8”-16UNC x 19.0P3M1-01 : ¾”M0-00 : 1”22.226.247.752.419.025.474.7 M10 x 19.0 3/8”-16UNC x 19.0S 4” 77.8 130.2 101.6 127.0 M16x30.0 5/8”-11UNC x 30.0軸伸最大扭矩 (N.m) 尺寸 (mm)T67DDBS / T6DDCS L1 L2 直径K1 x K2 H1M11 平键 : SAE-C 686 84.0 49.3 31.750 - 31.700 7.94 x 7.89 35.27M10 x 202 平键 : SAE-CC 1148 91.0 50.8 38.100 - 38.050 9.52 x 9.47 42.36M10 x 20 5 平键 : non SAE 883 84.0 60.0 34.900 - 34.850 7.94 x 7.89 38.42M10 x 20 3 花键 : SAE-C 971 56.038.0Class 1-J498b, 12/24 d.p. - 14 牙4 花键 : SAE CC z46.0 31.5 Class 1-J498b, 12/24 d.p. - 17 牙油口尺寸 (mm)A1 B1 ∅C1 D1T1口螺纹公制UNCT67DDBS P1 1 ¼” 30.2 58.7 31.8 82.6 M12 x 22.3 7/16” - 14UNC x 22.3 P2 1 ¼” 30.2 58.7 31.8 101.6 M12 x 24.0 7/16” - 14UNC x 24.0 P3 M1-01 : ¾” 22.2 47.7 19.0 74.7 M10 x 19.0 3/8” - 16UNC x 19.0 S 4” 77.8 130.2 101.6 115.0 M16x30.0 5/8” - 11UNC x 30.0T6DDCS P1 1 ¼” 30.2 58.7 31.8 82.6 M12 x 22.3 7/16” - 14UNC x 22.3 P2 1 ¼” 30.2 58.7 31.8 101.6 M12 x 24.0 7/16” - 14UNC x 24.0P3M1-01 : ¾”M0-00 : 1”22.226.247.752.419.025.474.7 M10 x 19.0 3/8” - 16UNC x 19.0S 4” 77.8 130.2 101.6 115.0 M16x30.0 5/8” - 11UNC x 30.0軸伸扭矩 (N.m) 尺寸 (mm)T67EDBT6EDCT6EDCS L1 L2 直径K1 x K2 H1 M11 平键 : ISO3019 (∅45) z z92.0 63.0 45h7 14h8 48.5 M12 x 24.02 平键 : SAE- D z100.063.5 44.450 - 44.40011.11 x 11.06 49.3 ½”UNCx24.03 花键: SAE D & E z75.0 48.8 Class 1-J498b, 8/16 d.p. - 13 牙油口尺寸 (mm)A1 B1 ∅C1 D1T1口螺纹公制UNCT6EDC T6EDCS P1 1 ½” 35.7 69.8 37.1 139.7 T6EDC : M12 x 30.0 T6EDCS : ½”-13UNC x 30.0 P2 1 ¼” 30.2 58.7 31.8 101.6 T6EDC : M12 x 24.0 T6EDCS : 7/16”-14UNC x 24.0P3F1-P1 : ¾”F0-P0 : 1”22.226.247.752.419.025.474.7 T6EDC : M10 x 19.0 T6EDCS : 3/8”-16UNC x 19.0S 4” 77.8 130.2 101.6 115.0 T6EDC : M16 x 30.0 T6EDCS : 5/8”-11UNC x 30.0。
双联叶片泵T6ED-050-045-1R00-C1型号解读

丹尼逊T6ED-050-045-1R00-C1叶片泵型号解读
泵芯规格系列代号:C:较小排量系列(10.8~100.0ml/rev)
D :中排量系列(47.6~158.0ml/rev)
类型代号:无:工业用型M:车(行走机械)用型P:车(行走机械)用型,双重轴封排量代号:
传动轴型式:1:SAE CC平键2:非SAE平键3:SAE C花键4:SAE CC花键
旋转方向:R:右转(顺时针转向)L:左转(逆时针转向)
油口方向:00:进油口对侧01:进油口同侧
02:相对进油口逆时针90°03:相对进油口顺时针90°
设计号:由生产商制定
密封等级:1=S1(适用于矿物油基液压油)常用的
4=S4(适用于抗燃液压液)
5=S5(矿物油基液压油及抗燃液压液,吸油口最高压力可达7bar)
以上是丹尼逊T6ED叶片泵的完整型号,再购买中能方便随时找到相应的型号,更多型号伊特液压随时欢迎咨询。
CAD版本消防泵一二次接线图

伊顿 MTL4500 FSM安全手册 电磁阀和报警驱动模块 说明书

FSM FUNCTIONAL SAFETY MANAGEMENTThese products are for use as elements within a Safety System conforming to the requirements ofIEC 61508:2010 and enable a Safety Integrity Level of up to SIL2 to be achieved for the instrumentloop in a simplex architecture.Eaton Electric Ltd, Luton is a certified Functional Safety Management company meeting therequirements of IEC 61508:2010 Part 1, Clause 6.* Refer to content of this manual for details2SM45-55-AO Rev 4 This manual supports the application of the products in functional-safety related loops. It must be usedin conjunction with other supporting documents to achieve correct installation, commissioning andoperation. Specifically, the data sheet, instruction manual and applicable certificates for the particularproduct should be consulted, all of which are available on the MTL web site.In the interest of further technical developments, Eaton reserve the right to make design changes.Contents1 Introduction31.1 Applicationandfunction 31.2 Variantdescription 31.3 Product build revisions coveredbythismanual 42 System configuration52.1 Associated system components 53 Selection of product and implications 64 Assessment of Functional Safety64.1 HardwareSafetyI ntegrity 64.2 Systematic Safety Integrity 74.3 S I LCapability 74.4 Example of use in a safety function 74.5 EMC 84.6 Environmental 85 Installation86 M aintenance97 Appendices97.1 Appendix A: Summary of applicablestandards 97.2 Appendix B: Proof test procedure 10 Analogue Output Modules† These modules have an inherent fault tolerance of 0.Duplication of modules in a voting architecture may be used to achieveHFT=1. SIL ratings in this table apply where the required safety functionis to repeat the loop current with ± 2%, and the safe state of the output is<3.6mA (downscale).3SM45-55-AO Rev 41 INTRODUCTION1.1 Application and functionThe MTL454x and MTL554x are isolator modules which enable an analogue 4-20mA control signal to bepassed to a device located in a hazardous area from a safe area. The output current available to the hazardous area is limited to comply with the requirements of the process explosion hazard. The modules are also designed and assessed according to IEC 61508 for use in safety instrumented systems up to SIL2 when the required function is to repeat the loop current within ±2%, and the safe state of the output is <3.6mA (downscale). Higher integrity levels for a SIF can be achieved by using the modules in a voting architecture.For ‘smart’ valve positioners using the HART protocol the units allow bi-directional communicationssuperimposed on the 4-20mA signal current.There are no configuration switches or operator controls to be set on the modules – they perform a fixed function related to the model selected. The MTLx546 models are single channel while the MTLx549 models are dual channel, although both channels must not be used in the same safety instrumented function.These modules are members of the MTL4500 and MTL5500 range of products.1.2 Variant DescriptionFunctionally the MTL4500 and MTL5500 range of modules are the same but differ in the following way:- the MTL4500 modules are designed for backplane mounted applications- the MTL5500 modules are designed for DIN rail mounting.In both models the hazardous area field-wiring connections (terminals 1-2, and 4-5) are made through the removable blue connectors on the top of the modules, but the safe area and power connections for the MTL454x modules are made through the connector on the base, while the MTL554x uses the removable grey connectors on the top and side of the module.Note that the safe-area connection terminal numbers differ between the backplane and DIN-rail mounting models.The analogue output models covered by this manual are:MTL4545Y single channel, open cct LFDMTL4546 and MTL5546single channel, open and short cct LFDMTL4546C, MTL4546Y , and MTL5546Y single channel, open cct LFDMTL4549, and MTL5549dual channel, open and short cct LFDMTL4549C, MTL4549Y , and MTL5549Y dual channel, open cct LFDNote: To avoid repetition, further use of MTLx54x in this document can be understood to include both DIN-rail and backplane models. Individual model numbers will be used only where there is a need todistinguish between them.MTL4500 and MTL5500 range1.3 Product build revisions covered by this manualThe information provided in this manual is valid for the product build revisions listed in the following table:The product build revision is identified by the field ‘CC’ in the module Product Identification Number that appears at thebottom left-hand corner of the side label:The CC field immediately precedes the 7-digit Serial Number field, DDDDDDD. Example:4SM45-55-AO Rev 45SM45-55-AO Rev 4The MTLx54x modules are designed to repeat the current signal from a safe-area source to a field device such as a current-to-pneumatic converter or valve positioner in the hazardous area. The shaded area indicates the safety relevant system connection, while the power supply connections are not safety-related. For simplicity the term ‘PLC’ has been used to denote the safety system performing the driving function of the process loop.Note: When using the MTLx549 dual-channel modules, it is not appropriate for both channels to be used in the same loop, or the same safety function, as this creates concerns of common-cause failures. Consideration must also be made of the effect of common-cause failures when both loops of a dual-channel module are used for different safety functions.2.1 Associated System ComponentsThere are many parallels between the loop components that must be assessed for intrinsic safety as well as functional safety where in both situations the contribution of each part is considered in relation to the whole.The MTLx54x module is a component in the signal path between safety-related actuators and safety-related control systems.The current to pressure converter, valve positioner, or other field device, must be suitable for the process and have been assessed and verified for use in functional safety applications as well as its certification for hazardous area mounting.The safety system PLC shall have a current output with a normal operating range of 4-20mA but capable of working over the extended range of 3 to 22mA for under- and over-range. Such controllers will normally also include a readback facility to enable the detection of open or short circuits in the wiring.The transmission of HART data is not considered as part of the safety function and is excluded from this analysis.Figure 2.1 – Analogue Output module system configuration – see the ‘Note’ in the text regarding use of dual channel modules3 Selection of product and implicationsThe analogue signal levels employed by the MTLx54x are within the operating range of 4-20mA under normalconditions.If the wiring between the isolator and field device are open circuit then the line-fault detect (LFD) operation of theisolator forces the current taken into the input terminals to fall to a low value, which is less than the expected under-range value of 3.6mA. The MTLx546 and MTLx549 models also detect when the resistance in the field wiring is lessthan fifty ohms indicating a short circuit condition, and this also is reflected into a low input current value.This diagnostic aspect can be used by logic solvers that include a readback facility to monitor the output current fromtheir output cards or modules. Thus the ability to detect that the actual current being passed is not the desired valuecan be used to determine the health of the instrument function. The same condition of the actual loop current fallingto a low level will also occur if the wiring between the logic solver and the isolator is open circuit.Using a field device and logic controller, as defined in section 2, with an MTLx54x then a system-loop can beimplemented that applies functional safety together with intrinsic safety to meet the requirements of protectionagainst explosion hazards. Note that the transfer of HART communications through the isolator is not considered aspart of the safety function of the isolator.It is important that the effect of electromagnetic interference on the operation of any safety function is reducedwhere possible. For this reason it is recommended that the cable connections from the logic solver to theisolator modules be a maximum of 30 metres and are not exposed to possible induced surges, keeping theminside a protected environment.Similarly, operation of the equipment outside of its environmental ratings induces component stress andtemperature above the normal ambient of 60°C is to be avoided to ensure required performance and reliability.4 Assessment of Functional Safety4.1 Hardware Safety IntegrityThe hardware assessment shows that MTLx54x analogue output modules:• have a hardware fault tolerance of 0• are classified as Type A devices (“Non-complex” component with well-defined failure modes)• have no internal diagnostic elementsThe definitions for product failure of the modules at maximum ambient temperature of 45°C were determinedas follows:-Analogue output isolator modules(FITs means failures per 109 hours or failures per thousand million hours)6SM45-55-AO Rev 4The above failure rates apply primarily to the analogue signal transfer only. The information for the line faultdetection function is provided for consideration in respect of the diagnostic capabilities of the safety logic-solver.• Reliability data for this analysis is taken from IEC TR 62380:2004 Reliability Data Handbook.• Failure mode distributions are taken principally from IEC 62061:2005 Safety of Machinery.It is assumed that the module is powered from a nominal 24Vdc supply. The product has been assumed tooperate at a maximum ambient temperature of 45°C under normal conditions.4.2 Systematic Safety IntegrityThe modules covered by this safety manual have a systematic safety integrity measure of SC 3.Note: Earlier versions of this manual (Revisions 1 and 2) inferred a systematic safety integrity of SC 2.Subsequent independent assessment of the design features and techniques/measures used to avoidsystematic faults has allowed the modules to be awarded SC 3. No change has been made to the productdesigns; the SC 3 systematic integrity measure therefore applies retrospectively to modules installed underprevious revisions of this manual.4.3 SIL CapabilityConsidering both the hardware safety integrity and the systematic capability, this allows the modules to beused in safety functions up to SIL2 in a simplex architecture (HFT=0), or in SIL 3 applications with hardware redundancy (HFT = 1 or greater), provided SFF >60% for the application.Note: Independent of hardware architecture and systematic capability considerations, the hardware probabilityof failure for the entire safety function needs to be calculated for the application to ensure the required PFH (for(for a low demand safety function) for the SIL is met.a high or continuous demand safety function) or PFDAVG4.4 Example of use in a safety functionIn this example the application context is assumed to be:• The safety function is to repeat current within ±2%• The safe state of the output is <3.6mA (downscale)• The logic solver will diagnose input currents below 3.6mA as faults and take appropriate action. (Here, it is important to understand that when the MTL module detects a line fault, it forces the input current to <0.9mA).The failure modes shown above can then be defined as:SM45-55-AO Rev 47Consequently, the failure rates for these categories are then (FITs):In this example the Safe Failure Fraction is 83.9%. *ne is not used in the calculation of Safe Failure Fraction.4.5 E M CThe MTL4500 and MTL5500 modules are designed for operation in normal industrial electromagneticenvironment but, to support good practice, modules should be mounted without being subjected to undueconducted or radiated interference, see Appendix A for applicable standards and levels.It is important that the effect of electromagnetic interference on the operation of any safety function is reducedwhere possible. For this reason it is recommended that the cable connections from the logic solver to theisolator modules be a maximum of 30 metres and are not exposed to possible induced surges, keeping theminside a protected environment.Any maintenance or other testing activity should only be conducted when the field loop is not in service, toavoid any possibility of introducing a transient change in the field signal.4.6 EnvironmentalThe MTL4500 and MTL5500 modules operate over the temperature range from -20°C to +60°C, and at up to95% non-condensing relative humidity.The modules are intended to be mounted in a normal industrial environment without excessive vibration, asspecified for the MTL4500 & MTL5500 product ranges. See Appendix A for applicable standards and levels.Continued reliable operation will be assured if the exposure to temperature and vibration are within the valuesgiven in the specification.5 InstallationThere are two particular aspects of safety that must be considered when installing the MTL4500 or MTL5500modules and these are:• Functional safety• Intrinsic safetyReference must be made to the relevant sections within the instruction manual for MTL4500 range (INM4500)or MTL5500 range (INM5500) which contain basic guides for the installation of the interface equipment tomeet the requirements of intrinsic safety. In many countries there are specific codes of practice, together withindustry guidelines, which must also be adhered to.Provided that these installation requirements are followed then there are no additional factors to meet theneeds of applying the products for functional safety use.To guard against the effects of dust and water the modules should be mounted in an enclosure providing atleast IP54 protection degree, or the location of mounting should provide equivalent protection such as inside anequipment cabinet.In applications using MTL4500 range, where the environment has a high humidity, the mounting backplanesshould be specified to include conformal coating.8SM45-55-AO Rev 46 M aintenanceTo follow the guidelines pertaining to operation and maintenance of intrinsically safe equipment in a hazardousarea, yearly periodic audits of the installation are required by the various codes of practice.In addition, proof-testing of the loop operation to conform with functional safety requirements should be carriedout at the intervals determined by safety case assessment.Proof testing must be carried out according to the application requirements, but it is recommended that this becarried out at least once every three years.Refer to Appendix B for the proof testing procedure of the MTL4500 or MTL5500 modules.Note that there may also be specific requirements laid down in the E/E/PE operational maintenance procedurefor the complete installation.If an MTL4500 or MTL5500 module is found to be faulty during commissioning or during the normal lifetime ofthe product then such failures should be reported to the MTL office. When appropriate, a Customer IncidentReport (CIR) will be notified to enable the return of the unit to the factory for analysis. If the unit is within thewarranty period then a replacement unit will be sent.Consideration should be made of the normal lifetime for a device of this type which would be in the region often years.7 Appendices7.1 Appendix A: Summary of applicable standardsThis annex lists all standards referred to in the previous sections of this document:SM45-55-AO Rev 4910SM45-55-AO Rev 47.2 Appendix B : Proof T est Procedure, MTL45/5500 Analogue Output Modules1. System –Normal operation test2. Input / Output characteristic functional safety test.3. System - Normal operation testConfirmation, through testing, that a safety function will operate as designed, is a necessary periodic activity to ensure that the probability of failure upon demand (PFDavg) is maintained.In many safety applications, where practical, the user may well prefer that these proof tests are conducted on the instrument loop as a whole, without dismantling or disconnecting the parts. This will help to ensure the integrity of the installation is continued after commissioning, but the disturbance to plant operations may not be acceptable.The tests given in this section of the manual will enable only the function of the isolator component of the safety loop to be proved. Proof tests of the other components of the loop must be conducted at the requisite intervals to maintain availability of the safety function. Alternative proof tests may be devised and applied provided they give a similar level of test that is appropriate to the safety function.The tests described here - see Figure 7.1 - compare the output current with the input current (A1) over the required range of operation, and measure the “error current” i.e. the difference between the two - as indicated on A2. The tests should be employed per channel, as appropriate.Ammeter A2 must be capable of handling either polarity of signal. If it is not an auto-ranging instrument, set it to a high range before switch on, then adjust sensitivity to obtain the required reading.Example MTLx54y Proof T est ProcedureTest sequence:1. System - Normal operation test2. Input /Output characteristic functional safety test3. System - Normal operation test1 System - Normal operation testMake sure that the module to be tested is operating normally in the target system, without errors and in energised mode. If the module is connected in a faulty or de-energised loop, restore normal fault free and energised conditions before testing.2 Input/Output characteristic functional safety testObserve normal anti-static precautions when handling equipment during device testing.Remove the unit from the target system and connect as shown in Figure 7.1Please note, that it is acceptable to leave the unit in the target system, when it is secured, that the terminals are disconnected from the system and available for test. Alternatively, for the backplane mounted MTL4500, use a separate backplane for this purpose to facilitate access to the power and output connections.470Ωload Figure 7.1Basic testarrangementDuring testing, the power supply, Vs - nominal 24.0V, min/max. range 20.0 to 35.0V - should be connectedbetween terminals 13 and 14 (+ve to terminal 14)Make the following measurements and, it is recommended, record the results in a table such as that shown onthe next page.The chosen “load” resistor can be any value between 100 and 800ΩOutput Measurements1. Adjust the current source to set the current (A1) through the range 4 to 20mA.2. The measured current imbalance (A2) over this range should not exceed ± 50 µA.3. Adjust the current source to set the current (A1) to 3.5mA, and then 21.5mA.4. The measured current imbalance (A2) over this range should not exceed ± 200 µA.5. Adjust the current source to set the current (A1) to 20mA.6. Apply a voltmeter to the product input port + and - terminals.7. The measured voltage (V1) at the product input port should not exceed +6V.3 System - Normal operation testDisconnect the test setup from the unit and connect the original system configuration. Make sure, that thetested unit is operating normally in the target system, without errors and in energised mode.SM45-55-AO Rev 411Date: ______/______/__________ Supply voltage Vs: ______________V dcModule type: _________________ Serial No: ______________________________Channel 1Channel 212SM45-55-AO Rev 4THIS PAGE IS LEFT INTENTIONALL Y BLANKSM45-55-AO Rev 413EUROPE (EMEA): +44 (0)1582 723633 ********************THE AMERICAS: +1 800 835 7075*********************ASIA-PACIFIC: +65 6645 9888***********************The given data is only intended as a productdescription and should not be regarded as a legal warranty of properties or guarantee. In the interest of further technical developments, we reserve the right to make design changes.Eaton Electric Limited,Great Marlings, Butterfield, Luton Beds, LU2 8DL, UK.Tel: + 44 (0)1582 723633 Fax: + 44 (0)1582 422283E-mail:********************© 2024 EatonAll Rights ReservedPublication No. SM45-55-AO Rev 4 230424April 2024AUSTRALIAMTL Instruments Pty Ltd,10 Kent Road, Mascot, New South Wales, 2020, Australia Tel: +61 1300 308 374 Fax: +61 1300 308 463E-mail:*********************BeNeLuxMTL Instruments BVAmbacht 6, 5301 KW Zaltbommel The NetherlandsTel: +31 (0)418 570290 Fax: +31 (0)418 541044E-mail:*********************CHINACooper Electric (Shanghai) Co. Ltd955 Shengli Road, Heqing Industrial Park Pudong New Area, Shanghai 201201Tel: +86 21 2899 3817 Fax: +86 21 2899 3992E-mail:****************FRANCEMTL Instruments sarl,7 rue des Rosiéristes, 69410 Champagne au Mont d’Or FranceTel: +33 (0)4 37 46 16 53 Fax: +33 (0)4 37 46 17 20E-mail:*******************GERMANYMTL Instruments GmbH,Heinrich-Hertz-Str. 12, 50170 Kerpen, Germany Tel: +49 (0)22 73 98 12 - 0 Fax: +49 (0)22 73 98 12 - 2 00E-mail:*******************INDIAMTL India,No.36, Nehru Street, Off Old Mahabalipuram Road Sholinganallur, Chennai - 600 119, IndiaTel: +91 (0) 44 24501660 /24501857 Fax: +91 (0) 44 24501463E-mail:***********************ITALYMTL Italia srl,Via San Bovio, 3, 20090 Segrate, Milano, Italy Tel: +39 02 959501 Fax: +39 02 95950759E-mail:******************JAPANCooper Crouse-Hinds Japan KK,MT Building 3F, 2-7-5 Shiba Daimon, Minato-ku,Tokyo, Japan 105-0012Tel: +81 (0)3 6430 3128 Fax: +81 (0)3 6430 3129E-mail:****************NORWAY Norex ASFekjan 7c, Postboks 147, N-1378 Nesbru, NorwayTel: +47 66 77 43 80 Fax: +47 66 84 55 33E-mail:*************RUSSIACooper Industries Russia LLC Elektrozavodskaya Str 33Building 4Moscow 107076, RussiaTel: +7 (495) 981 3770 Fax: +7 (495) 981 3771E-mail:*******************SINGAPORECooper Crouse-Hinds Pte Ltd100G Pasir Panjang Road, Interlocal Centre #07-08 Singapore 118523Tel: +65 6645 9888 Fax: +65 6645 9811E-mail:***********************SOUTH KOREACooper Crouse-Hinds Korea7F. Parkland Building 237-11 Nonhyun-dong Gangnam-gu,Seoul 135-546, South Korea.Tel: +82 6380 4805 Fax: +82 6380 4839E-mail:*******************UNITED ARAB EMIRATESCooper Industries/Eaton CorporationOffice 205/206, 2nd Floor SJ Towers, off. Old Airport Road, Abu Dhabi, United Arab EmiratesTel: +971 2 44 66 840 Fax: +971 2 44 66 841E-mail:*****************UNITED KINGDOM Eaton Electric Ltd,Great Marlings, Butterfield, Luton Beds LU2 8DLTel: +44 (0)1582 723633 Fax: +44 (0)1582 422283E-mail:********************AMERICASCooper Crouse-Hinds MTL Inc. 3413 N. Sam Houston Parkway W.Suite 200, Houston TX 77086, USA Tel: +1 281-571-8065 Fax: +1 281-571-8069E-mail:*********************。
Eaton 一体化电源系列 Type NR 油液开关说明书

GeneralEaton offers its Cooper Power™ series Type NR oil switch for switching inductive and capacitor currents, to meet the requirements of a wide range of applications. This switch is an electrically operated, single-phase switch. The switch also includes an operating handle for switch position indication or manual operation. Thenormal operation of this switch is managed with an electric motor requiring low-voltage input. Eaton offers two options for the electric motor, either 120 Vac, 60 Hz or 240 Vac, 60 Hz. The switch operation can be managed remotely, via electrical or electronic controls, or manually at the installation site when needed.Electrically operated Type NR oilswitchFigure 1. Untanked T ype NR oil switch.DescriptionThe Type NR oil switch is a single-phase device for use ondistribution circuits. Compact design makes these switches ideal for use on capacitor banks, especially pole-top installations. These switches are electrically operated and can be controlled by various electrical or electronic devices. An operating handle, which also serves as a contact position indicator, is provided for manually opening and closing the switch.otee:N The Type NR oil switch may not be manually closed into a faulted line. The making current rating to these switches applies to electrical operation only.Capacitor bank switching The standard Type NR single-phase oil switch is rated at 15.0 kV / 95 kV BIL and is capable of switching three-phase capacitor banks up to 3600 kVAR on 14.4 kV systems; with three (3) switches controlledby customer. Choosing the 125 kV BIL option enables switchingsolidly grounded capacitor banks up to 6400 kVAR on multigrounded wye systems up to 14.4 / 24.9 kV; with three (3) switches controlled by customer.The 22.0 kV / 125 kV BIL version of the Type NR oil switch can switch solidly grounded three-phase capacitor banks up to 2700 kVAR on 20 / 34.5 kV multigrounded-wye systems; with three (3) switches controlled by customer. OperationWith switch contacts closed, selecting the "OPEN SWITCH", or similar, position in the switch controls energizes the switch opencontacts on the electric motor. Through a gear and lever system, this releases a toggle which allows pre-loaded opening springs to snap open the switch contacts; loads a heavy spring in preparation for aclosing operation; positions selector switch contacts so that only the closing circuit can subsequently be energized; and interrupts the electric motor operating current when the first three functions have been completed. The opening circuit must remain energized for 4.0seconds.Similarly, selecting the "CLOSE SWITCH", or similar, position in theswitch controls energizes the switch close contacts on the electric motor. This releases the closing spring to close switch contacts and load opening springs; positions selector switch contacts for the subsequent opening signal, then interrupts the operating electricmotor current. The closing circuit must remain energized for 0.5 seconds.BUSHING TERMINALSaluminum conductors, either vertically or horizontallyLIFTING STRAPconvenient for hoisting entire switch or for lifting mechanism from tankACTUATOR HOUSINGmotor-driven mechanism for electri-cally opening and closing the switchSTATIONARY CONTACTSand durable arcing tips, accessible for easy inspection or cleaningBUSHINGSwet-process porcelain with light-gray glaze. Munsell Gray 70SLEET HOODprotects manual operat-ing handle: switch data permanently affixed on nameplateO-RING GASKETin confined assembly provides weather-proof head-tank sealallows hookstick operation and serves as contact position indicator* General purpose duty switches are rated for both capacitive and inductive current switching applications.T able 1. Summary of RatingsSwitch TypeApplicationMaximumOperating Voltage (kV)Rated Switching Current (A)NR General Purpose Duty15.0200*NRV22.0602Catalog Data CA230007ENEffective August 2015Electrically operated T ype NR oil switch/cooperpowerseriesT able 2. Ratings and SpecificationsDescriptionStandard15 kV with 17" Creepage15 kV with 125 kV BIL22 kVMaximum Design Voltage, kV 15.015.015.022.0Nominal Operating Voltage, kV 2.4-14.4 2.4-14.4 2.4-14.420.0Basic Insulation Level (BIL), kV 959512512560 Hertz Withstand Voltage, kV Dry, One Minute Wet, Ten seconds3530353042366050Continuous Current Rating, Amps20020020060Load Interrupting Ability (Inductive), Symmetric Amps 75-100% power factor 50-75% power factor < 50% power factor20010050A 20010050A 20010050A 606060Maximum Capacitive Current, Amps (parallel bank-max)200200200*60* High Frequency Transient Current, Amps 12000120001200012000 Transient Frequency, Hz 6000600060006000 High Frequency Damping Factor .40-.55.40-.55.40-.55.40-.55Momentary Rating, Amps asym.9000900090009000Short Time Current Amps 1/2 second,sym. 1 second, sym.60004500600045006000450060004500Close and Latch Rating, Amps asym.9000900090009000T able 3. Electrical Data (Control)DescriptionRatingNominal operating voltage (50/60 Hz only) (Vac)120240Operating voltage range (Vac)95-130190-260Closing-motor current (A)1.9.7Switch response time, opening (sec) 4.0 4.0Switch response time, closing (sec)0.50.5*The 125 kV BIL switch and the 22.0 kV switch are rated for single bank switching only.3Catalog Data CA230007ENEffective August 2015Electrically operated T ype NR oil switch /cooperpowerseriesT able 4. Basic NR and NRV Oil SwitchesDescriptionNominal/Maximum Voltage (kV)Continuous Current (A)Switch BIL (kV)Type NR Oil Switch 14.4/15.020095*Type NRV Oil Switch20.060125* 125 kV BIL option available for standard NR oil switchOrdering informationWhen ordering the Type NR electrically operated oil switch specify the Voltage Rating from Table 4. The basic Type NR oil switch is designed with a maximum operating voltage of 15.0 kV L -L with a continuous current rating of 200 A. The Type NRV oil switch is designed with a maximum operating voltage of 22.0 kV with a continuous current rating of 60 A.T able 5. NR / NRV Motor Control VoltageDescription120 Vac Actuating Motor (Standard)240 Vac Actuating MotorControl voltage requirementsSpecify the Type NR motor control voltage from Table 5. The Type NR oil switch is supplied with a 120 Vac motor control voltage as standard.T able 6. NR / NRV Switch BIL & Bushing Creep*DescriptionRating (kV)BIL (kV)Bushing Creep (in)NR Oil Switch 15.09512.0NR Oil Switch 15.09517.0NR Oil Switch 15.012516.0NRV Oil Switch22.012517.0Insulation and creep requirementsSpecify the NR oil switch insulation level and porcelain insulator creep using Table 6. The NR oil switch is designed with 95 kV BIL insulation level as a standard option with a porcelain bushing having 12 inches of creep. The 95 kV BIL insulation level is only available in the NR oil switch. The NRV oil switch has an insulation level of 125 kV BIL and a porcelain bushing with 17.0" of creep as a standard offering.T able 7. NR / NRV T ank OptionsDescriptionSwitch Rating (kV)Standard Tank 15.022.0Stainless Steel Tank 15.022.0Zinc Plated Tank15.022.0Specialized tank requirementsSpecify the required NR tank option from Table 7. The standard tank is manufactured from a mild formed steel and painted toprotect against the environment. There are available options for zinc plating and stainless steel tanks for highly corrosive and salt-fog contaminated environments.T able 8. NR / NRV Low Voltage ArresterDescriptionNone (Std)120 Vac Surge Arrester (Factory Installed)Surge protection requirementsThere is an available option for a factory-installed 120 Vac low voltage surge arrester to protect the motor control circuit from damaging effects of lightning. The arrester rating is determined by the motor control voltage. Contact the factory if a 240 Vac low voltage arrester is required.T able 9. NR / NRV Auxiliary SwitchDescriptionNone (Std)Auxiliary SwitchAuxiliary switch requirementsSpecify the Auxiliary switch from Table 9 if necessary for theswitching application. The Auxiliary switch is a SPDT switch, which allows the user to remotely obtain the close or open position of the Type NR oil switch.*Reference Figure 4 on page 9 for outline dimensions of the extra creep bushing"* Determined by motor control voltage4Catalog Data CA230007ENEffective August 2015Electrically operated T ype NR oil switch/cooperpowerseriesT able 10. NR / NRV Hold SwitchDescriptionNone (Std)Hold SwitchHold switch requirementsSpecify the Hold switch from Table 10 if necessary for theapplication. The close or open signals supplied to the Type NR oil switch must be applied for a minimum of 4.5 seconds. Specify the Hold switch option from Table 10 if the capacitor switchingapplication requires a signal for less than 4.5 seconds. The close or open signal has to be applied for 1 second for proper operation of the Type NR oil switch.T able 11. Factory-wired ReceptaclesDescription5-pin/3-conductor receptacle for standard three-wire control 6-pin/6-conductor receptacle for auxiliary switchReceptacle assembly requirementsSpecify the type of receptacle from Table 11 for the switchingapplication. The receptacle assemblies are mounted in the bottom of the actuator housing and provide a convenient, weather-proof connection to switch the control circuits. Receptacles are supplied with 5-pin. 3-conductor or 6-pin, 6-conductor configurations. Reference Figure 2 for 5-pin or 6-pin receptacle orientations. Consult the factory for additional receptacle options.5-pin Receptacle6-pin ReceptacleFigure 2. Receptacle assembly schematic.* Consult factory for available receptacle options5Catalog Data CA230007ENEffective August 2015Electrically operated T ype NR oil switch /cooperpowerseriesT able 13. Wildlife Protectors for T erminal BushingsDescriptionCatalog NumberNone (Std)–Wildlife Protectors (95 kV BIL Only)*CCM32A1Wildlife Protectors (125 kV BIL only)*CCM33A1Wildlife protector requirementsSelect required wildlife protectors based on the Type NR switch being ordered for the application. Wildlife protectors protect the energized terminals of the Type NR switch from incidental contact from wildlife, tree branches or line crews performed routinemaintenance of overhead equipment. Wildlife protectors must be ordered in a quantity of 2.T able 14. Mounting OptionsDescriptionCatalog NumberNone (Std)–NEMA ® X-Arm BrktHA00039Mounting option requirementsSelect the Type NR oil switch mounting method from Table 14. The standard Type NR switch is supplied with an integral bracket, which is used for pole-mounting or capacitor rack applications. A NEMA ®-style bracket is available for cross-arm applications.T able 12. Mating Plug and Conductor Cable OptionsDescriptionCatalog Number5-Pin Mating PlugCCR010P15-Pin / 3-Conductor Cable (6 ft)CCR003P65-Pin / 3-Conductor Cable (8 ft) CCR003P85-Pin / 3-Conductor Cable (10 ft) CCR003P105-Pin / 3-Conductor Cable (12 ft) CCR003P125-Pin / 3-Conductor Cable (14 ft) CCR003P145-Pin / 3-Conductor Cable (16 ft) CCR003P165-Pin / 3-Conductor Cable (18 ft) CCR003P185-Pin / 3-Conductor Cable (20 ft) CCR003P205-Pin / 3-Conductor Cable (22 ft) CCR003P225-Pin / 3-Conductor Cable (24 ft) CCR003P245-Pin / 3-Conductor Cable (26 ft) CCR003P265-Pin / 3-Conductor Cable (28 ft) CCR003P285-Pin / 3-Conductor Cable (36 ft) CCR003P366-Pin Mating PlugCCR009P16-Pin / 6-Conductor Cable (6 ft) CCR006P66-Pin / 6-Conductor Cable (8 ft) CCR006P86-Pin / 6-Conductor Cable (10 ft) CCR006P106-Pin / 6-Conductor Cable (12 ft) CCR006P126-Pin / 6-Conductor Cable (14 ft) CCR006P146-Pin / 6-Conductor Cable (16 ft) CCR006P166-Pin / 6-Conductor Cable (18 ft) CCR006P186-Pin / 6-Conductor Cable (20 ft) CCR006P206-Pin / 6-Conductor Cable (22 ft) CCR006P226-Pin / 6-Conductor Cable (24 ft) CCR006P246-Pin / 6-Conductor Cable (26 ft) CCR006P266-Pin / 6-Conductor Cable (28 ft)CCR006P286-Pin / 6-Conductor Cable (36 ft)CCR006P36Mating plug & conductor cable requirementsSpecify the type of mating plug and conductor cable configuration and length from Table 12 if required for the switching application.5-pin plugs accommodate up to 12 AWG wire and 0.375-0.500 inch O.D cables to allow connection to the 5-pin receptacle.6-pin plugs accommodate up to 16 AWG wire and 0.500-0.625 inch O.D cables to allow connection to 6-pin receptacles. The number of conductors tabulated for the receptacles in Table 12 above indicates the number of pins wired to the actuator terminal strip. Mating plugs are available as an accessory and should be ordered separately. Consult the factory for additional mating plug and conductor cable options.* Consult factory for additional Conductor C able options* Must be ordered in a quantity of (2)6Catalog Data CA230007ENEffective August 2015Electrically operated T ype NR oil switch/cooperpowerseriesStandard Type NR Oil Switch Catalog Number ConfigurationThe standard Type NR and NRV configurations are provided below. If you need Engineered To Order (ETO) models, please contact your Eaton representative for details.Table 4-S witch TypeNR (15 kV)Type NR (15.0 kV) CCM17B2-GType NRV (22.0 kV)CCM75B2-GTable 5-Control Motor120 Vac (Std)Table 6-BIL & Creep*95 kV BIL (15.0 kV Only)Table 7-Tank OptionsStandard TankTable 8-L V Surge ArresterNone (Std)Table 9-Auxiliary SwitchNone (Std)Table 10-Hold SwitchNone (Std)Table 11-Receptacle5 -Pin / 3-Conductor (Std)Table 12-Plug & CableNone (Std)Table 13-Bird GuardsW/O Bird Guards (Std)Table 14-Mounting OptionsNone (Std)Table 4-S witch TypeNRV (22.0 kV)Table 5-Control Motor120 Vac (Std)Table 6-BIL & Creep*125 kV BILTable 7-Tank OptionsStandard TankTable 8-L V Surge ArresterNone (Std)Table 9-Auxiliary SwitchNone (Std)Table 10-Hold SwitchNone (Std)Table 11-Receptacle5 Pin / 3-Conductor (Std)Table 12-Plug & CableNone (Std)Table 13-Bird GuardsW/O Bird Guards (Std)Table 14-Mounting OptionsNone (Std)*Reference Figure 3 on page 8 for NR oil switch outline dimensions*Reference Figure 5 on page 10 for NRV outline dimensions7Catalog Data CA230007ENEffective August 2015Electrically operated T ype NR oil switch /cooperpowerseriesFOR FACTORY-WIRED RECEPTACLEFigure 3. Outline dimensions of 95 kV BIL T ype NR oil switch with standard bushings, (15.0 kV Rating ONL Y).8Catalog Data CA230007ENEffective August 2015Electrically operated T ype NR oil switch/cooperpowerseriesFigure 4. Outline dimensions of 95 kV BIL T ype NR oil switch with 17" creepage bushings, (15.0 kV Rating ONL Y).9Catalog Data CA230007ENEffective August 2015Electrically operated T ype NR oil switch /cooperpowerseriesFOR FACTORY-WIRED RECEPTACLEFigure 5. Outline dimensions of 125 kV BIL T ype NR oil switch (15.0 and 22.0 kV).10Catalog Data CA230007ENEffective August 2015Electrically operated T ype NR oil switch/cooperpowerseriesCatalog Data CA230007EN Electrically operated T ype NR oil switchEffective August 201511/cooperpowerseriesElectrically operated T ype NR oil switch Eaton 1000 Eaton Boulevard Cleveland, OH 44122United States Eaton’s Cooper Power Systems Division 2300 Badger Drive Waukesha, WI 53188United States /cooperpowerseries© 2015 Eaton All Rights Reserved Printed in USA Publication No. CA230007EN Catalog Data CA230007EN Effective August 2015Eaton is a registered trademark.All other trademarks are property of their respective owners.For Eaton's Cooper Power series Type NR oil switch product information call 1-877-277-4636 or visit: /cooperpowerseries.。
- 1、下载文档前请自行甄别文档内容的完整性,平台不提供额外的编辑、内容补充、找答案等附加服务。
- 2、"仅部分预览"的文档,不可在线预览部分如存在完整性等问题,可反馈申请退款(可完整预览的文档不适用该条件!)。
- 3、如文档侵犯您的权益,请联系客服反馈,我们会尽快为您处理(人工客服工作时间:9:00-18:30)。
丹尼逊T6EDC-042-028-003-1R00-C1叶片泵型号解读
规格系列代号:C:较小排量系列(10.8~100.0ml/rev)
D:中排量系列(47.6~158.0ml/rev)
E:大排量系列(132.3~227.1ml/rev)
可提供三联规格组合有:DCC,DDCS和EDC
类型代号:无:工业用型
M:车(行走机械)用型
S:车(行走机械)用型,采用SAE J744C安装法兰,仅用于T6DDS及T6EDCS
传动轴形式:
T6EDCM:-1:ISO G45N平键-3:SAE D/E花键
T6EDCS:-2:SAE D/E平键-3:SAE D/E花键
旋转方向:R:右转(顺时针转向)L:左转(逆时针方向)
油口方向:00为标准的油口方向配置
密封等级:1:S1(使用与矿物油基液压油)
4:S4(使用于抗燃液压液)
5:S5(矿物油基液压油及抗燃液压液,吸口最高压力可达7bar)
以上是丹尼逊T6EDC三联叶片泵的完整型号,购买时能方便随时找到相应的型号,更多型号伊特液压随时欢迎咨询。