2021石蜡加氢精制装置简介和重点部位及设备
蜡油加氢裂化装置设备操作规程
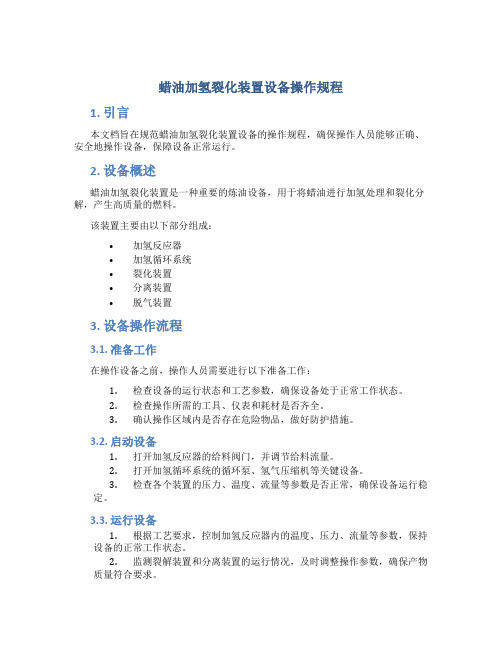
蜡油加氢裂化装置设备操作规程1. 引言本文档旨在规范蜡油加氢裂化装置设备的操作规程,确保操作人员能够正确、安全地操作设备,保障设备正常运行。
2. 设备概述蜡油加氢裂化装置是一种重要的炼油设备,用于将蜡油进行加氢处理和裂化分解,产生高质量的燃料。
该装置主要由以下部分组成:•加氢反应器•加氢循环系统•裂化装置•分离装置•脱气装置3. 设备操作流程3.1. 准备工作在操作设备之前,操作人员需要进行以下准备工作:1.检查设备的运行状态和工艺参数,确保设备处于正常工作状态。
2.检查操作所需的工具、仪表和耗材是否齐全。
3.确认操作区域内是否存在危险物品,做好防护措施。
3.2. 启动设备1.打开加氢反应器的给料阀门,并调节给料流量。
2.打开加氢循环系统的循环泵、氢气压缩机等关键设备。
3.检查各个装置的压力、温度、流量等参数是否正常,确保设备运行稳定。
3.3. 运行设备1.根据工艺要求,控制加氢反应器内的温度、压力、流量等参数,保持设备的正常工作状态。
2.监测裂解装置和分离装置的运行情况,及时调整操作参数,确保产物质量符合要求。
3.定期对设备进行巡视,并检查设备的运行状态和仪表的准确性。
4.注意设备周围的安全环境,及时排除可能存在的危险因素。
3.4. 停止设备1.逐步减少加氢反应器的给料流量,并关闭给料阀门。
2.停止加氢循环系统的循环泵、氢气压缩机等关键设备。
3.关闭各个装置的阀门,并排空介质。
4.对设备进行清理和维护,并记录设备停运情况。
4. 安全注意事项在操作蜡油加氢裂化装置时,操作人员需要严格遵守以下安全注意事项:•遵守操作规程和工艺要求,确保设备运行的稳定性和安全性。
•穿戴个人防护装备,包括安全帽、防护服、手套等。
•注意设备周围的危险区域,不要擅自进入。
•注意设备的运行参数和仪表的指示,及时发现异常情况并报告。
•禁止在设备周围吸烟或使用明火。
•熟悉并使用相应的应急设备和灭火器材。
5. 结束语通过遵守本操作规程,操作人员能够正确、安全地操作蜡油加氢裂化装置设备,并确保设备正常运行。
石蜡加氢精制工艺应注意什么
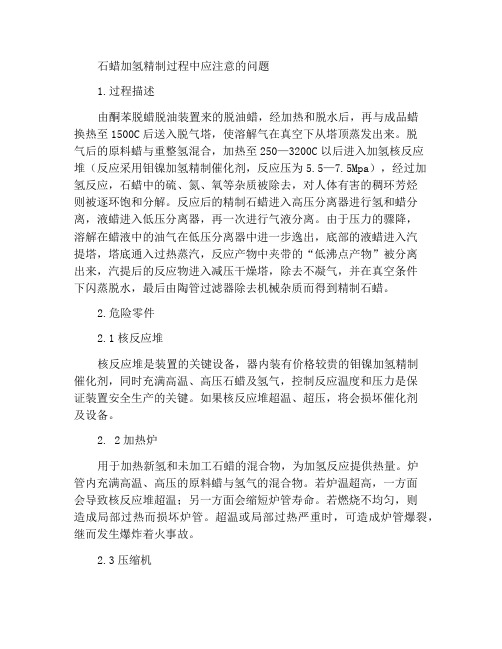
石蜡加氢精制过程中应注意的问题1.过程描述由酮苯脱蜡脱油装置来的脱油蜡,经加热和脱水后,再与成品蜡换热至1500C后送入脱气塔,使溶解气在真空下从塔顶蒸发出来。
脱气后的原料蜡与重整氢混合,加热至250—3200C以后进入加氢核反应堆(反应采用钼镍加氢精制催化剂,反应压为5.5—7.5Mpa),经过加氢反应,石蜡中的硫、氮、氧等杂质被除去,对人体有害的稠环芳烃则被逐环饱和分解。
反应后的精制石蜡进入高压分离器进行氢和蜡分离,液蜡进入低压分离器,再一次进行气液分离。
由于压力的骤降,溶解在蜡液中的油气在低压分离器中进一步逸出,底部的液蜡进入汽提塔,塔底通入过热蒸汽,反应产物中夹带的“低沸点产物”被分离出来,汽提后的反应物进入减压干燥塔,除去不凝气,并在真空条件下闪蒸脱水,最后由陶管过滤器除去机械杂质而得到精制石蜡。
2.危险零件2.1核反应堆核反应堆是装置的关键设备,器内装有价格较贵的钼镍加氢精制催化剂,同时充满高温、高压石蜡及氢气,控制反应温度和压力是保证装置安全生产的关键。
如果核反应堆超温、超压,将会损坏催化剂及设备。
2. 2加热炉用于加热新氢和未加工石蜡的混合物,为加氢反应提供热量。
炉管内充满高温、高压的原料蜡与氢气的混合物。
若炉温超高,一方面会导致核反应堆超温;另一方面会缩短炉管寿命。
若燃烧不均匀,则造成局部过热而损坏炉管。
超温或局部过热严重时,可造成炉管爆裂,继而发生爆炸着火事故。
2.3压缩机为加氢反应提供氢气。
一旦发生故障,新氢中断,将会导致装置停产,同时造成加热炉、核反应堆超温。
3.注意事项3.1核反应堆必须严格监视核反应堆压力及温度变化,发现压力超高,必须立即打开高压分离器的紧急排气阀以降低压力;若核反应堆床层温度超高,则适当降低炉温及适当加大氢气量;若床层温度局部超高,则适当降温操作维持生产,待检修时调试分配盘。
3.2加热炉经常检查加热温度和压力的控制,入炉物料压力不得大于7.5MPa,炉出口温度不大于3300C。
石化公司加氢精制装置设计方案
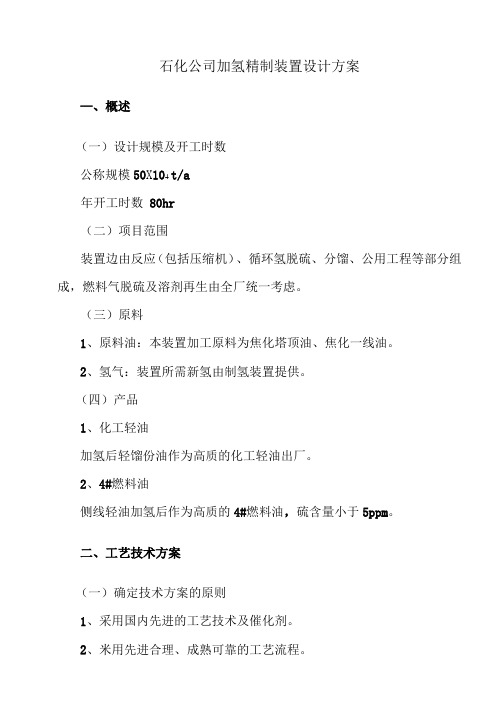
石化公司加氢精制装置设计方案—、概述(一)设计规模及开工时数公称规模50X104 t/a年开工时数80hr(二)项目范围装置边由反应(包括压缩机)、循环氢脱硫、分馏、公用工程等部分组成,燃料气脱硫及溶剂再生由全厂统一考虑。
(三)原料1、原料油:本装置加工原料为焦化塔顶油、焦化一线油。
2、氢气:装置所需新氢由制氢装置提供。
(四)产品1、化工轻油加氢后轻馏份油作为高质的化工轻油出厂。
2、4#燃料油侧线轻油加氢后作为高质的4#燃料油,硫含量小于5ppm。
二、工艺技术方案(一)确定技术方案的原则1、采用国内先进的工艺技术及催化剂。
2、米用先进合理、成熟可靠的工艺流程。
3、选用性能稳定、运转周期长的机械设备。
4、提高自动控制、安全卫生和环境保护水平。
(二)国内外加氢技术现状加氢精制是指油品在催化剂、氢气和一定的压力、温度条件下,含硫、氮、氧的有机化合物分子发生氢解反应,烯烃和芳烃分子发生加氢饱和反应的过程。
加氢精制的目的是脱硫、脱氮和解决色度及贮存安定性的问题,满足日益严格的环保要求。
常规的加氢精制工艺已有几十年的历史,技术上非常成熟。
新进展主要体现在高活性、高稳定性、低成本新型催化剂的研究和开发上。
荷兰AKZO公司目前最好的脱硫催化剂是KF-752和KF-840.KF-752的活性已是60年代中期相应产品的1.7倍,多用于直馏原料。
对于二次加工原料则采用KF-840O埃克森研究和工程公司(ER&E)于1992年实现商业应用的催化剂RT-601,采用新型A12O3载体,使用先进的促进剂浸渍技术,催化剂活性高,特别适合于加工重质、劣质原料。
在加工直硫柴油时,活性与市场上最好的催化剂相当。
独联体的列宁石油化工科学生产联合体开发的KrM-70催化剂也具有很高活性。
在压力为3.0MPa,空速为3.0h-i,温度为350°C时,可将直硫柴油的硫含量由1.03%降至0.26m%,脱硫率达到99.7%o国内近年来也已开发了多种具有世界先进水平的、高性能的馏分油加氢精制催化剂。
加氢精制装置工艺原理与操作

3.空速
空速:指单位时间内通过单位体积催化剂的物 料体积数。空速越高则装置生产能力越大,但 反应物料在反应中停留时间越短,不利于反应 的完全进行,产品质量受到影响。如空速过低 ,则生产能力降低,在反应器中停留时间过长 会增加裂解导致产品收率降低,催化剂上易积 碳。所以空速是有一定限制的,它受到原料油 性质、催化剂使用性能、产品质量要求等因素 限制,不能随便提高或降低。
合反应。如:
CmH2m+2 —→ Cm-nH2(m-n)+2+CnH2n
烷烃
烷烃
烯烃
CnH2n+H2 —→CnH2n+2
烯烃
烷烃
芳烃加氢: 苯
+3H2 -→ 环已烷
中石加化氢经精济制技装术置研工究艺院原(理咨与询操公作司) China Petrochemical Consulting Corporation
Hale Waihona Puke 装置特点三套加氢精制装置全部采用热高分和热低分;采用炉前 混氢工艺;采用常压汽提和减压干燥;石蜡加氢装置和 微晶蜡加氢装置均有原料预处理系统;使用三种不同的 催化剂;润滑油加氢为FV-10,石蜡加氧为RJW一1,微 晶蜡加氢为RJW一2;装置还采用了二台21/4Cr一1Mo材 质的热壁反应器,一台21/4Cr一1Mo材质的冷壁反应器 及一台21/4Cr一1Mo材质的热高分,必须了解在371℃一 493℃温度范围内进行操作所引起的脆化现象,同时必 须了解在温度低于121℃时可能出现的脆性破坏。
硫醇
烷烃
RSR`+2H2-→R`H+RH+H2S
硫醚
石蜡加氢装置低分气尾氢回收工艺

( 抚顺 石化公 司石 油二厂 , 辽 宁 抚顺 1 3 0 1 0 4)
摘
要 :通过对石蜡加 氢装置 自产低分气 的组成分析 ,及改造思路的探索 ,找出将低分气做 为补充氢源的
可行性 ,从 而开发 出低分气 新的附加值 ,避免简单烧掉或放空造成的资源浪 费,进一步完善了加氢工艺流程的 合理性 ,开辟出一条新 的降低成本之路。通过估算 ,2 0万 t 的石蜡加氢装置每天可 回收氢气约 760m , a 8 ,按
T e eo d iin l au f h i g s n v i s u c s , e s i t f sn et i g s a o lme tr od v l p a d t a l eo et l a d a o d r o r ewa t f a i l y o i g t l a sc mp e n ay o v t a a e e b i u h a
Re e r h o heTa l y o e c v r o e so s a c n t i H dr g n Re o e y Pr c s f Pa a n Hy O e a i n Eq pm e r f dr g n tO ui i nt
WAN G H a -he g is n ( uh nP  ̄ c e c l mp n . Reiey L a nn u h n 1 3 0 , Chn ) F s u e o h mia Co a yNo2 f r , io igF s u 1 0 4 n ia
h d o e u c sd s u s d T e y o e a i np o e s si r v d t e r a ep o u t n c s. y e t t g y r g n s r ewa ic s e . h n h d g n t r c s o r o wa mp o e d c e s r d ci o t B si i , o o ma n a o t7 6 0 m h d o e a er c ce v r a o 0 k / a a n h d o e ai n e u p e t t a o s y t e b u 8 y r g n c n b e y ld e ey d y f r2 0 t p r f y a i r g n t q im n , h ti t a , h o s
加氢装置主要危险性分析

加氢装置主要危险性分析2工艺设备的火灾危险性加热炉用来为反应提供热量,如炉管壁温超高,会缩短炉管寿命;当超温严重、炉管强度降低到某一极限时,可能导致炉管爆裂,造成恶性爆炸事故。
材质缺陷、施工质量低劣、高温腐蚀、阀门不严、违章操作、点火等造成炉管和燃料系统泄漏,是炉区发生火灾的主要原因。
炉管焊口、回弯头等处是容易发生火灾的主要部位。
按《石油化工企业设计防火规范》的有关规定,加热炉属于丙类火灾危险设备。
反应器是石蜡加氢装置的关键设备,包括加氢精制第一反应器和加氢精制第二反应器。
器内主要介质为石蜡、氢气,且器内操作温度高、压力高,反应器在发生泄漏或超温超压时,有火灾爆炸的危险性。
高压氢与钢材长期接触还会使钢材强度降低(氢脆),出现裂纹,导致物理性火灾爆炸。
例如:美国某炼油厂加氢裂化装置,在操作压力17.2MPa的高压反应器上,有一道47.5cm的裂口。
使可燃气休喷出,引起装里泄压,造成重大火灾。
按《石油化工企业设计防火规范》的有关规定,以反应器为主要反应设备的加氢精制属于甲类火灾危险设备。
高压分离器包括热高压分离器(操作条件:17.3MPa,240℃)和冷高压分离器(操作条件:17.2MPa、140℃)。
高压分离器不仅是反应产物的气液分离设备,又是反应系统的压力控制点。
分离器内压力非常大,如液面控制不好,液面过高,会造成循环氢带液而损坏循环氢压缩机;液面过低,容易发生高压系统窜入低压系统而发生爆炸事故。
其玻璃液面计、压力表、安全阀、调节阀,任何一个部件失灵都可能导致重大事故的发生。
新氢和循环氢压缩机是本装里的重要设备,其主要功能是保证反应系统氢气循环,为反应过程提供操作用全部高压氢气(出口压力18.7MPa),由于气体经过压缩产生高温、高压,所以压缩机缸体、部件、轴密封、管线、阀门、仪表等处容易发生泄漏和损坏,泄漏气体容易发生火灾爆炸事故。
此外,高压分离器液面过高导致循环氢带液,也会使压缩机失去平衡,产生振动,严重时会损坏设备,造成氢气漏气,引起燃爆。
蜡油加氢装置简介

100万吨/年蜡油加氢装置装置简介中国石化股份有限公司上海高桥分公司炼油事业部2007年3月编制:何文全审核:严俊校对:周新娣目录第一章工艺简介一、概述中国石化股份有限公司上海高桥分公司炼油事业部是具有五十多年历史的加工低硫石蜡基中质原油的燃料——润滑油型炼油企业,根据中国石化股份有限公司原油油种变化和适应市场发展的需求,上海高桥分公司到2007年以后除了加工大庆原油、海洋原油等低硫原油外,将主要加工含硫2.0%左右的含硫含酸进口原油。
由于常减压生产的减压蜡油和延迟焦化装置生产的焦化蜡油中含有较多的不饱和烃及硫、氮等有害的非烃化合物,这些产品无法达到催化裂化装置的要求。
为了使二次加工的蜡油达到催化裂化装置的要求,必须对焦化蜡油和减压蜡油进行加氢精制,因此上海高桥分公司炼油事业部进行原油适应性改造时,将原100万吨/年柴油加氢精制装置改造为100万吨/年蜡油加氢装置。
本装置的建设主要是为了催化裂化装置降低原料的硫含量和酸度服务。
本装置由中国石化集团上海工程有限公司设计,基础设计于2005年6月份完成,2005年8月份进行了基础设计审查,工程建设总投资2638.73万元,其中工程费用2448.74万元。
2006年7月降蜡油含硫量由原设计2.44%提高至3.28%,工程建设总概算增加820.8万元。
二、装置概况及特点1.装置规模及组成蜡油加氢精制装置技术改造原料处理能力为100万吨/年,年开工时数8400小时。
本装置为连续生产过程。
主要产品为蜡油、柴油、汽油。
本装置由反应部分、循环氢脱硫部分、氢压机部分(包括新氢压缩机、循氢压缩机)、加热炉部分及公用工程部分等组成。
2.生产方案混合原料经过滤后进入缓冲罐,用泵升压,经换热、混氢,再经换热进入加热炉,加热至350℃后进反应器进行加氢,反应产物经换热后进热高分进行气液分离,气相进一步冷却,进冷高分进行气液分离,气相进新增的循环氢脱硫塔脱硫后作为循环氢与新氢混合,组成混合氢循环使用;液相减压后至热低分,热低分的液相至催化裂化装置。
加氢装置主要危险性分析

编号:SM-ZD-11160 加氢装置主要危险性分析Organize enterprise safety management planning, guidance, inspection and decision-making, ensure the safety status, and unify the overall plan objectives编制:____________________审核:____________________时间:____________________本文档下载后可任意修改加氢装置主要危险性分析简介:该安全管理资料适用于安全管理工作中组织实施企业安全管理规划、指导、检查和决策等事项,保证生产中的人、物、环境因素处于最佳安全状态,从而使整体计划目标统一,行动协调,过程有条不紊。
文档可直接下载或修改,使用时请详细阅读内容。
1物料的火贝爆炸危险性某石蜡加氢装置所用原料蜡分别来自本厂生产的58#,66#脱油蜡,溶剂脱油装置生产的70#和喷雾脱油装置生产的75#脱油蜡。
新氢为重整氢,组成见表1;白土为活性白土;燃料气来白瓦斯管网,组成见表2。
产品主要是油蜡和微油蜡,还有部分轻烃和污油产生。
此外,新鲜的催化剂使用二甲基二硫作为硫化剂。
上述物料在生产过程中大多处于高温、高压条件,一旦出现泄漏,易引发火灾爆炸事故。
(1)石蜡石蜡是高质石油馏分,呈白色至淡黄色,常温下为固态。
石蜡主要由C16以上的正构烷烃组成,也含有少量异构烷烃和带侧链的环烷烃。
随着分子量增高,异构烷烃和长侧链环烷烃的含量逐渐增多,其平均分子量为300~500,闪点大于120℃,按火灾危险性分类原则,石蜡属于丙类火灾危险物质。
(2)氢气氢气是无色无味的气体,爆炸极限(V%)为4.0%~75.0%,引燃温度为560℃,按照可燃气体火灾危险性分类原则,氢气属于甲类火灾危险物质。
氢气与空气混合能形成爆炸性混合物,遇热或明火即会发生爆炸,气体比空气轻,在室内使用或储存时,漏气上升滞留屋顶不易排出,当达到其爆炸下限浓度时,遇火星会引起爆炸。
制氢装置简介
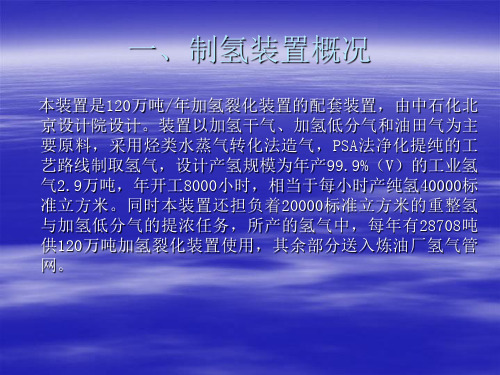
中压蒸汽
锅炉给水、发生并 过热蒸汽部分
中变冷 却分液
制氢PSA 部分
中压蒸 汽外送
低分气湿法 脱硫部分
重整氢 PSA
氢气
十、制氢工艺流程简述(一)
自装置外来的50℃,2.2MPa(G)的加氢裂化低分气 进入加氢裂化低分气冷却器(E-1102)壳层冷却后, 进入加氢低分气分液罐(D-1102)分液,从加氢低 分气脱硫塔(C-1102)底进入,在塔中与来自硫磺 回 收 装 置 的 甲 基 二 乙 醇 胺 ( MDEA ) 贫 液 逆 流 接 触 (MDEA浓度25%wt),脱除气体中的硫化氢,脱硫后 的低分气送本装置中重整氢提浓PSA单元,MDEA溶液 送回硫磺回收装置再生。
水蒸汽 合计
公斤/小时 5937.50 5952.97 43800.00 55690.47
吨/日 142.50 142.87 1051.20 1336.57
万吨/年 4.75 4.76 35.04 44.55
工业氢
3628.46 87.08 2.90
出
PSA尾气
27941.00 670.58 22.35
十五、制氢工艺流程简述(六)
自中变反应器出来的变换气依次经过中变气/原料气换热器 (E-1201)温度降至367℃和中变气/脱氧水换热器(E1202A/B)温度降至156.5℃后,进入中变气第一分液罐(D1203)分出凝液,然后在中变气除盐水换热器(E-1203)与 除盐水换热到137.8℃后进入中变气第二分液罐(D-1204), 分出凝液后,进入中变气空冷器(A-1201)冷却到60℃,再 经中变气第三分液罐(D-1205)分液后,进入中变气水冷器 (E-1204),水冷到40℃的中变气经中变气第四分液罐(D1206)分液后进入中变气PSA提纯单元。
(完整ppt)290万加氢裂化装置简介

初期 0.7973
172/187 194/201 209/222
237 <5 <1 55 -54 27
末期 0.7992
国标
172/188 194/201 209/222
237 <5 <1 55 -54 25
不大于2000
不低于38 不高于-47 不小于25
保证值
2000 max 38 min -47 max 25 min
290万吨/年加氢裂 化装置简介
中国石油华北石化公司
目录
• 一、装置概述 • 二、原料及主要产品性质 • 三、工艺技术方案 • 四、关键设备选型 • 五、仪表控制
中国石油华北石化公司
目录
• 六、能耗及物料平衡 • 七、平面布置 • 八、工艺流程简图 • 九、设备图片
中国石油华北石化公司
一、装置概述
中国石油华北石化公司
工艺技术方案
• 紧急泄放系统方案 为确保催化剂、高压设备及操作人员的安 全,设置2.1MPa/min和0.7MPa/min两个 紧急泄压系统
中国石油华北石化公司
工艺技术方案
• 反应部分共设置了两个循环氢加热炉和两 个加氢裂化反应器(并联使用),原料油 自高压进料泵出口分为两路,经换热后分 别与从两个循环氢加热炉出口来的循环氢 气混合,进入加氢裂化反应器,反应器生 成物经换热后合并进入热高压分离器进行 气液分离。
轻石脑油主要技术指标
产品 密度(20℃),g/cm3
初期 0.6413
末期 0.6418
硫,μg/g 氮,μg/g
<0.5
<0.5
<0.5
<0.5
保证值 10 Max
中国石油华北石化公司
加氢精制工艺流程图

加氢精制工艺流程图加氢精制是炼油中的一项重要工艺,用于去除石蜡、柴油和航空煤油等产品中的杂质,提高产品质量和性能。
下面是一份加氢精制工艺的流程图解释。
加氢精制工艺流程图1. 原料处理:原料(石蜡、柴油和航空煤油等)在加氢精制前需要经过处理。
这包括物料输送、分离和质量检测等步骤。
物料输送通过管道将原料送至下一个处理单元。
2. 加热和加氢反应器:原料在加热炉中被加热至适宜的温度,接着进入加氢反应器。
加氢反应器是一个重要的设备,其中加氢催化剂用于去除原料中的硫化物、氮化物和氧化物等杂质。
催化剂可以在高温和高压的条件下促进加氢反应。
3. 气液分离器:经过加氢反应后,产物中的气体和液体需要进行分离。
气液分离器根据密度和性质的不同,将气体和液体分开。
分离后的底液进入下一个处理单元。
4. 液相处理:底液中仍然含有一些杂质,因此需要进行进一步处理。
液相处理可以包括脱硫、脱氮、脱碳等步骤,以进一步提高产品质量。
这些处理可以通过吸附、蒸馏和萃取等方法完成。
5. 产品分馏:经过液相处理后,得到的产品需要进行分馏。
分馏是将不同沸点的组分分开,以便得到纯净产品。
在加氢精制过程中,通常会得到不同品位的产品,例如石蜡、柴油和航空煤油等。
6. 产物处理:加氢精制后的产品需要进行最终的处理,以满足产品质量要求。
这可能包括去除残余杂质、调整产品性能和添加化学添加剂等步骤。
7. 产品储存和出口:最终的纯净产品将被储存于相应的储罐中,以便后续销售和出口。
储存过程需要注意保持产品的稳定性和安全性。
加氢精制工艺流程图显示了加氢精制的主要步骤和设备。
这些步骤和设备可以根据实际情况进行调整和优化,以适应不同的原料和产品要求。
加氢精制工艺的目标是提高产品质量和性能,以满足市场需求。
随着技术的不断发展,加氢精制工艺也在不断改进,为炼油行业提供更高效和环保的解决方案。
蜡油加氢装置优化方案
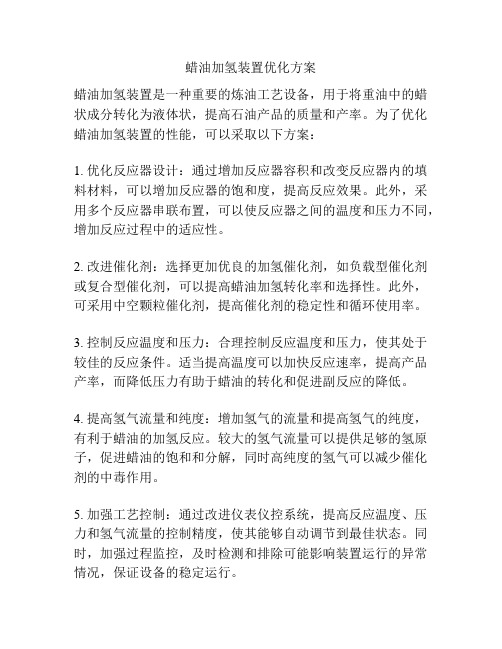
蜡油加氢装置优化方案
蜡油加氢装置是一种重要的炼油工艺设备,用于将重油中的蜡状成分转化为液体状,提高石油产品的质量和产率。
为了优化蜡油加氢装置的性能,可以采取以下方案:
1. 优化反应器设计:通过增加反应器容积和改变反应器内的填料材料,可以增加反应器的饱和度,提高反应效果。
此外,采用多个反应器串联布置,可以使反应器之间的温度和压力不同,增加反应过程中的适应性。
2. 改进催化剂:选择更加优良的加氢催化剂,如负载型催化剂或复合型催化剂,可以提高蜡油加氢转化率和选择性。
此外,可采用中空颗粒催化剂,提高催化剂的稳定性和循环使用率。
3. 控制反应温度和压力:合理控制反应温度和压力,使其处于较佳的反应条件。
适当提高温度可以加快反应速率,提高产品产率,而降低压力有助于蜡油的转化和促进副反应的降低。
4. 提高氢气流量和纯度:增加氢气的流量和提高氢气的纯度,有利于蜡油的加氢反应。
较大的氢气流量可以提供足够的氢原子,促进蜡油的饱和和分解,同时高纯度的氢气可以减少催化剂的中毒作用。
5. 加强工艺控制:通过改进仪表仪控系统,提高反应温度、压力和氢气流量的控制精度,使其能够自动调节到最佳状态。
同时,加强过程监控,及时检测和排除可能影响装置运行的异常情况,保证设备的稳定运行。
6. 加强设备维护:定期对蜡油加氢装置进行检修和维护,清洗和更换催化剂,清除堵塞物,保持设备的良好状态。
加强设备维护,延长装置的使用寿命,提高装置的运行稳定性和可靠性。
综上所述,通过优化反应器设计、改进催化剂、控制反应温度和压力、提高氢气流量和纯度、加强工艺控制和设备维护,可以有效提高蜡油加氢装置的性能,提高产品的质量和产率。
石蜡加氢精制

石蜡加氢技术的研究摘要本文介绍了石蜡的基本性质及分类,并对石蜡加氢技术的原理、工艺、应用及有关装置进行初步研究。
关键词石蜡;石蜡加氢;催化剂;精制石蜡类产品广泛地应用于造纸、食品、蜡烛及冶金、电子等多种领域。
我国是石蜡生产大国, 其总产量和出口量均居于世界榜首。
石蜡加工工艺经过半个多世纪的发展, 在早期的冷榨、发汗、白土吸附等工艺的基础上逐渐开发出了溶剂脱蜡、溶剂喷雾脱油、加氢精制等新工艺。
其中石蜡加氢精制工艺生产的石蜡具有质量好、收率高、操作灵活以及环境友好等优点, 成为世界各国普遍采用的主要精制工艺。
1、石蜡1.1石蜡简介石蜡是矿物蜡的一种,也是石油蜡的一种;它是从原油蒸馏所得的润滑油馏分经溶剂精制、溶剂脱蜡或经蜡冷冻结晶、压榨脱蜡制得蜡膏,再经溶剂脱油、精制而得的片状或针状结晶。
又称晶形蜡,碳原子数约为18~30的烃类混合物,主要组分为直链烷烃(约为80%~95%),还有少量带个别支链的烷烃和带长侧链的单环环烷烃(两者合计含量20%以下)。
主要质量指标为熔点和含油量,前者表示耐温能力,后者表示纯度。
其中以前二者用途较广,主要用作食品及其他商品(如蜡纸、蜡笔、蜡烛、复写纸)的组分及包装材料,烘烤容器的涂敷料、化妆品原料,用于水果保鲜、提高橡胶抗老化性和增加柔韧性、电器元件绝缘、精密铸造等方面,也可用于氧化生成合成脂肪酸。
1.2石蜡的分类根据加工精制程度不同,可分为全精炼石蜡、半精炼石蜡和粗石蜡3种。
粗石蜡含油量较高,主要用于制造火柴、纤维板、篷帆布等。
半精炼石蜡为颗粒状白色固体.其相对密度随熔点的上升而增加。
产品化学稳定性好,含油量适中,具有良好的防潮和绝缘性能,可塑性好。
半精炼石蜡生产的蜡烛火焰集中,无烟,不流泪。
用于蜡烛、蜡笔、蜡纸,一般电讯器材以及短路及轻工,化工原料。
1.3石蜡的性质1.3.1石蜡的化学性质化学中,石蜡是固态高级烷烃混合物的俗名,分子式C n H2n+2,其中n=20-40。
蜡油加氢装置简介

蜡油加氢装置简介 Document serial number【KKGB-LBS98YT-BS8CB-BSUT-BST108】100万吨/年蜡油加氢装置装置简介中国石化股份有限公司上海高桥分公司炼油事业部2007年3月编制:何文全审核:严俊校对:周新娣目录第一章工艺简介一、概述中国石化股份有限公司上海高桥分公司炼油事业部是具有五十多年历史的加工低硫石蜡基中质原油的燃料——润滑油型炼油企业,根据中国石化股份有限公司原油油种变化和适应市场发展的需求,上海高桥分公司到2007年以后除了加工大庆原油、海洋原油等低硫原油外,将主要加工含硫2.0%左右的含硫含酸进口原油。
由于常减压生产的减压蜡油和延迟焦化装置生产的焦化蜡油中含有较多的不饱和烃及硫、氮等有害的非烃化合物,这些产品无法达到催化裂化装置的要求。
为了使二次加工的蜡油达到催化裂化装置的要求,必须对焦化蜡油和减压蜡油进行加氢精制,因此上海高桥分公司炼油事业部进行原油适应性改造时,将原100万吨/年柴油加氢精制装置改造为100万吨/年蜡油加氢装置。
本装置的建设主要是为了催化裂化装置降低原料的硫含量和酸度服务。
本装置由中国石化集团上海工程有限公司设计,基础设计于2005年6月份完成,2005年8月份进行了基础设计审查,工程建设总投资2638.73万元,其中工程费用2448.74万元。
2006年7月降蜡油含硫量由原设计2.44%提高至3.28%,工程建设总概算增加820.8万元。
二、装置概况及特点1.装置规模及组成蜡油加氢精制装置技术改造原料处理能力为100万吨/年,年开工时数8400小时。
本装置为连续生产过程。
主要产品为蜡油、柴油、汽油。
本装置由反应部分、循环氢脱硫部分、氢压机部分(包括新氢压缩机、循氢压缩机)、加热炉部分及公用工程部分等组成。
2.生产方案混合原料经过滤后进入缓冲罐,用泵升压,经换热、混氢,再经换热进入加热炉,加热至350℃后进反应器进行加氢,反应产物经换热后进热高分进行气液分离,气相进一步冷却,进冷高分进行气液分离,气相进新增的循环氢脱硫塔脱硫后作为循环氢与新氢混合,组成混合氢循环使用;液相减压后至热低分,热低分的液相至催化裂化装置。
加氢纯化装置参数

加氢纯化装置参数
加氢纯化装置是一种化工设备,其主要作用是将原油中的杂质去除,将脱蜡油变为可直接用作加工和使用的工业级石油化工产品。
为了实现高效、可靠的加氢纯化过程,这些装置需要具备一系列参数,下面列出了一些主要的参数:
1.工作压力:加氢纯化装置需要在一定的压力范围内运行,一般为20-50MPa左右。
在这个压力范围内,可以保证反应的充分、彻底,从而达到高质量、高产量的加氢纯化效果。
2.工作温度:加氢纯化过程需要在高温下进行,一般为300-400℃左右。
这个温度范围可以使原油中的蜡质充分裂解,烃类分子结构也会改变,使得脱蜡油的品质得到较大提升。
3.氢气流量:氢气是加氢纯化过程中的主要反应物,其流量大小决定了反应速率和反应余度。
一般来说,氢气的流量与进料油的比例约为100:1。
4.反应器体积:加氢纯化反应器的大小直接影响了反应系统的处理能力和生产效率。
选择合适的反应器体积可以保证反应的充分、稳定和高效完成。
5.催化剂种类和用量:金属氧化物催化剂是加氢纯化反应中最常用的催化剂,其种类、用量和物理化学性质对反应的效果和稳定性都有很大的影响。
加氢纯化装置的参数选取和优化,需要结合原油的基本性质和反应动力学原理进行分析和测试。
只有通过充分的实验研究和优化,才能够使加氢纯化工艺的效果和经济效益得到最大化的发挥。
石蜡的加氢精制

石蜡的加氢精制摘要:数量大、质量低劣的含硫油加工技术已构成我国石油炼制过程中要重点解决的问题。
开展包括加氢精制在内的加氢技术已是加快和协调国民经济的当务之急。
加氢是指在催化剂存在下,将产品与氢的加和反响。
加氢技术,主要是指,在炼厂加工过程中以石油为原料的加氢反响。
本文介绍了加氢精制的开展历程及精制过程中所涉及的化学反响。
主要阐述了加氢精制的工艺及流程,并对不同方法进展了比照。
关键字:加氢精制,开展历程,化学反响,工艺,流程概述我国现在的炼油工业得到了极大的开展,随着国民经济的的快速开展,对能源的需求量也随之迅猛增长,其中石油是重要的能源之一,对其需求量也在日趋增加。
加氢精制边和是指在保持原料油分子骨架构造不发生变化或变化很小的情况下,将杂质脱除,以到达改善油品质量为目的的加氢反响,即“在有催化剂和氢气存在下,将石油馏分中含硫、氮、氧及金属的非烃类组分;加氢脱除,以及烯烃、芳烃发生加氢饱和反响〞。
我国石蜡产量和出口量均居世界第一位,加工技术也居世界前列,尤其是以生产高质量石蜡产品为目的的石蜡加氢精制技术居世界领先地位。
加氢精制是石油蜡类产品精制的主要方法之一,可以在保持产品的熔点、油含量、针入度等特性指标根本不变的同时实现产品的深度精制。
1.石蜡加氢精制技术的开展历程1.1国外加氢精制技术的开展国外石油蜡加氢精制技术研究经历了上世纪60~70年代活泼期后渐趋稳定,自1992年关于苏曼公司一套石蜡类产品高压加氢装置投产的文章发表和1993年巴西石油公司一项石蜡及微晶蜡加氢精制的专利公开以来,鲜有文献报道。
在技术创新方面,国外某公司将石蜡加氢装置与废气脱硫装置配套,既可以回收加氢尾气中的硫,又减轻了石蜡精制过程对环境的影响。
除此之外,没有其他实质性新技术公开。
目前,由于润滑油生产工艺的变化,国外一些公司石蜡生产能力有所降低,但也有新的生产能力形成,虽然石油蜡产量总体呈下降态势,但降低幅度不大。
美国石蜡生产与中国有所不同,其吸附精制仍占有较大份额。
蜡油介绍

2.66
7.18
102.66
277.18
1.89
5.10
1.02
2.75
4.76
12.85
8.63
23.30
25.67
69.31
19.97
53.92
10.57
28.54
30.15
81.41
102.66
277.18
Page : 9
装置工艺组成
反应部分,设备、管道、仪表编号130-X-2XXX(高压部分) 分馏部分,设备、管道、仪表编号 130-X-3XXX 公用工程部分,设备、管道、仪表编号 130-X-4XXX 热工部分,设备、管道、仪表编号 130-X-5XXX 机泵机组部分,管道、仪表编号X-6XXX(厂商部分)
压力达15.46MPa、轴功率均在5000kw以上,16台高压空冷管束采用Inconel-Alloy825材质,12台高压
换热器有10台采用螺纹锁紧环式,最大单台重量~120t。 装置工艺管道涉及的材质有TP347、TP321、304、316、P11、P22、15CrMoG、A106、 20#、20G 、L245、 Q235B等,其中高压SHA类管道~6km/550t,重量占工艺管道总量的30%以上,是整个装置施工的重点和 难点,尤其是铬钼钢的焊接更是关键。 装置地下采取防渗措施,地管及地下构筑物施工困难;
- 1、下载文档前请自行甄别文档内容的完整性,平台不提供额外的编辑、内容补充、找答案等附加服务。
- 2、"仅部分预览"的文档,不可在线预览部分如存在完整性等问题,可反馈申请退款(可完整预览的文档不适用该条件!)。
- 3、如文档侵犯您的权益,请联系客服反馈,我们会尽快为您处理(人工客服工作时间:9:00-18:30)。
2021石蜡加氢精制装置简介和重点部位及设备Security technology is an industry that uses security technology to provide security services to society. Systematic design, service and management.( 安全管理 )单位:______________________姓名:______________________日期:______________________编号:AQ-SN-02272021石蜡加氢精制装置简介和重点部位及设备一、装置简介(一)装置发展及类型1.装置发展石蜡精制工艺有白土精制、渗透精制、硫酸精制和加氢精制四种类型,其中白土精制和渗透精制都不容易脱净蜡中的稠环芳烃,难以生产对于纯度要求很高的食品工业用蜡:而硫酸精制方法的主要缺点是产品产率低,劳动条件恶劣,有大量的废渣产生,污染环境。
无论在生产成本上,产品产率和质量及环境保护上,石蜡加氢精制均比其他精制工艺有明显的优越性。
因此,在国外主要炼油厂中,石蜡加氢精制己逐步代替其他精制工艺。
1957年加拿大萨尼亚炼油厂首先宣布用钼钻铝催化剂加氢精制生产白石蜡,由于该工艺对蜡中稠环芳烃组分有很好的加氢转化能力,容易制取食品级纯度商品蜡而进一步为人们重视;其后催化重整工艺的兴起,为炼油厂提供了廉价的氢气来源,尤为石蜡加氢精制装置的建设创造了有利条件。
1962年一套处理量为1.5X104t/a、10.OMPa的石蜡和凡士林加氢精制装置在西德汉堡建成。
1963年美国大西洋公司费城炼油厂建成日处理量300t/a的石蜡加氢精制装置,代替原来的石蜡硫酸和渗透精制工艺。
我国从20世纪70年代初正式开始研究石蜡加氢精制催化剂和工艺,1979年11月大庆石化总厂首次采用5053催化剂进行处理量6X104t/a的低压石蜡加氢装置开工投产。
1981年10月石油工业部对481—2B催化剂及中压石蜡加氢精制工艺组织技术鉴定,本工艺先后在东方红炼油厂(现中石化燕山分公司炼油厂)、抚顺石油一厂、荆门炼油厂、大连石油七厂、茂名炼油厂实现工业化。
1983年11月第一套采用石蜡加氢专用催化剂处理量为6X104t/a的石蜡加氢装置在东方红炼油厂投产,1984年另两套石蜡加氢装置在抚顺石油一厂和荆门炼油厂投产,1986年又两套石蜡加氢装置在大连石油七厂和茂名炼油厂相继投产。
2.装置的主要类型20世纪60年代以来国外陆续发展的蜡加氢精制工艺有十多种,可归纳为五种类型见表2—85。
类型工适用于含硫<10X10—6 的原料,选用芳烃饱和性能很强的非抗硫催化剂。
类型I目前仅在白油加氢精制上应用,因为对原料的质量有严格要求,蜡加氢精制仅有小型试验道,未见工业生产上应用。
类型ⅡA适用于对成品蜡质量要求不高的加氢精制,产品不能保证满足食品蜡要求。
有些工厂采用这种工艺加氢后再经白土补充精制生产食品蜡。
类型Ⅱn适用于高质量蜡或食品蜡的生产。
由于氢分压高,产品的光安定性和热稳定性都很好,催化剂的运行寿命也长。
类型Ⅱ。
是现阶段国外应用最广泛的蜡加氢精制工艺。
类型Ⅲ是组合ⅡA 和I的两段反应形式,装置复杂一些,但在较低压力下可得到优质产品。
本类型不适用于微晶蜡加氢精制。
类型Ⅳ是为了在中压高温下制取优质产品而设计的。
类似ⅡA 型。
但采用两个反应器串联,本类型虽然因采用了两上反应器,增加装置投资费用,但可在稍低压力下取得质量比较好的产品,并有较强的操作灵活性。
(二)装置的单元组成与工艺流程1.组成单元石蜡加氢装置的基本组成单元如下:(1)原料预处理单元:部分脱除原料中的溶剂和水;(2)换热器及加热炉单元:提供热交换及反应所需热量;(3)反应器及高低分单元:提供反应进行的场所并对反应生成物进行气液分离;(4)汽提塔与干燥塔单元:脱除生成腊中所含的轻质烃、硫化氢及水等。
2.工艺流程工艺原则流程图见图2—28。
图2—28石蜡加氢精制原则流程1一反应进料加热炉;2一反应器;3一原料脱气塔;4--常压汽提塔;5一减压干燥塔;6--热高压分离器;7一热低压分离器;8--分液罐;9---馏出物罐;10--冷凝水箱;11一反应物产/进料换热器;12--脱气塔进料加热器;13一汽提塔顶冷却韶;14--干燥塔顶冷却器;15--成品石蜡冷却器;16--过滤器;17一原料泵;18一反应进料泵;19---成品泵;20--馏出油泵;21一补充氢压缩机;22一循环氢压缩机;23一真空泵原料蜡由罐区来,经过原料预处理泵、原料反冲洗过滤器后与成品蜡进行换热,进入预处理塔中脱除原料蜡中残存的水分及溶剂;经高压原料泵升压到7.5-8.5MPa的压力后与反应生成蜡换热;后和与反应生成蜡换热的高压氢气混合进入加热炉加热到230—310℃,进入反应器顶部,在压力4.9—6.5MPa、温度230-310~C 和催化剂的作用下与氢气进行反应。
反应生成物从反应器底部出来经过换热后依次经过高、低压分离器。
由高压分离器分离出的气体经空冷器、水冷器进入循环氢分液罐,由循环氢分液罐分离出来的氢气卸人高分卸压线,或卸人氢气管网进行再利用。
由低压分离器分离出的气体经捕雾器后去加热炉作燃料。
由低压分离器分离出的反应生成蜡靠自压进入减压汽提塔,除去残存在蜡中的气体及轻馏分后,进入干燥的塔去除水分等;然后再进入出装置冷却器冷至75-85℃,作为成品蜡送至石蜡成型装置。
由装置处来的氢气,经新氢阀组调节压力,通过新氢冷却器后入新氢分液罐分液,从新氢分液罐顶部出来进入新氢压缩机(机1#2#3#)一段人口,由一段出口出来的氢气进入中间冷却器冷却分液后人压缩机二段人口,被压缩的氢气从二段出口出来后进行换热后于加热炉前与原料蜡混合人炉,加热后进行反应。
在开停工过程中,由循环氢分液罐顶部出来的氢气作为循环氢,人循环氢压缩机压缩后进蜡系统,进行系统的氢气循环。
(三)化学反应过程1。
石蜡加氢精制反应的特点石蜡加氢精制是在催化剂的作用下,在比较缓和的反应条件下(5.5-7.OMPa,230—310℃)采用加氢的方法,将原料中的含氧、含氮、含硫化合物等杂质和大部分稠环芳烃脱除,以改善石蜡的颜色、嗅味、光安定性等指标使之符合相应的质量标准。
2.石蜡加氢精制化学反应类型石蜡加氢精制过程的主要反应分为以下几种类型:(1)含氧、含氮、含硫化合物等非烃类的加氢分解反应;(2)烯烃和芳烃(主要是稠环芳烃)的加氢饱和反应;烯烃饱和与芳烃的转化通过加氢反应降低其不饱和度,烯烃饱和为烷烃;多环芳烃转化为少环芳烃。
(3)微量胶质、沥青质的脱除,胶质、沥青质(稠环的芳香烃)变为少环的芳香烃。
此外还有少量的开环、断链和缩合反应。
(四)主要操作条件及工艺技术特点1.主要操作条件石蜡加氢主要工艺操作条件如表2—86所示。
2.工艺技术特点(1)石蜡加氢精制属于典型的滴流床液相加氢过程,特点是要求反条件温和而能达到深度加氢精制。
反应条件温和是国为加氢精制过程中不允许出现碳—碳键的裂解和烃类异构化反应,以防止蜡中含油量的回升和主要质量指标变化。
深度加氢精制是除去杂质和有毒物质,充分满足食品、医药用蜡高质量标准的要求。
(2)热高压分离工艺。
反应生成物人高压分离器,温度在200℃左右进行热氢和热蜡的分离,为此,后处理系统省去加热炉,简化流程。
(五)催化剂及助剂1.催化剂的性质催化剂的性质见表2—87。
2.催化剂使用过程中质量变化趋势及工艺调整方法催化剂在使用过程中,由于杂质对催化剂孔隙的堵塞及活性重金属的部分流失,其质量的变化趋势为:催化剂活性下降、反应器床层压降增大。
工艺上的调整主要是提高反应温度为(或)压力以补偿催化剂活性的损失。
3.催化剂的预硫化加氢精制催化剂中的金属在出厂时是以氧化态的形式存在的。
但在实际应用时,由于金属硫化态具有更高的活性和更大的强度,因此需对催化剂进行预硫化。
最常用的硫化剂是二硫化碳(CS2)、二甲基硫醚(DMS)及二甲基二硫化物(DMDS)等。
4.判定催化剂报废、需更换的指标(1)安全要求:反应器床层压降不应超过0.55MPa。
超过此规定值则可判定该批催化剂报废,需更换。
(2)质量要求:在提高反应温度和(或)压力以补偿催化剂活性损失的方法无效时,则可判定该批催化剂报废,需更换。
.(六)原料及产品的性质量.石蜡加氢精制主要原材料的性质主要原材料的性质列于表2—88。
2.石蜡加氢精制主要产品的性质主要产品性质列于表2—89。
二、重点部位及设备从装置的平稳生产和安全角度进行考虑进行分类(一)重点部位1.反应器及高压换热器部分反应器是原料蜡和氢气进行加氢精制反应的场所,温度为230-310℃,系统压力为5.0—7.0MPa。
反应器和高压换热器等高压部位若发生泄漏,易发生自燃着火;严重时会导致装置切断进料,进行停工处理。
2;循环氢卸压系统从高压分离器分离出来的氢气经过高分捕雾器去除夹带的蜡沫,然后经水冷器冷却后,进入循环氢分液罐。
循环氢分液罐顶部出来的氢气经过压控卸人高压瓦斯线。
系统内介质为纯度大于90%的氢气,如有泄漏未及时发现并未进行隔离,遇火星将发生严重的爆炸事故。
(二)重点设备1.石蜡加氢装置的重点设备为新氢压缩机。
新氢压缩机为装置的心脏,保证反应系统的正常反应压力及循环。
如压缩机发生故障,首先要关闭高分泄压阀,保持系统压力,缓慢降压进行停工处理。
防止压力下降过快使催化剂及高压设备受损。
2.装置的重点控制阀为高分减压阀。
高压分离器内分离的液相经过减压自控阀进入低压分离器再次进行气液分离。
由于高低分之间的压差可达5.0—6.0MPa,因此要严格控制好高压分离器液面,防止液面跑空造成气相窜入低压系统,而使低压分离器超压损坏,设备甚至发生爆裂事故。
XXX图文设计本文档文字均可以自由修改。