夏米尔慢走丝作业指导书
夏米尔慢走丝290,500操作说明书

夏米尔慢走丝操作说明书1.目的为正确操作线切割设备以维持线切割设备之精度及稳定性,延长其使用寿命,使线切割加工作业规范.标准化,而达到提升质量保证,提升加工效率的目的,以满足客户需求.2.适用范围适合于ROBOFIL290.ROBOFIL500型号之慢走丝.3.作业内容3.1 开机当电柜合闸通电的时候,数控恢复断电前的状态.如果想装软件,必须启动特别的启动屏幕,步骤如下:3.1.1 按通电开关.3.1.2 同时,按住控制板上任何一个键,直到显示启动屏幕.3.1.2.1 监控功能(MONITOR)是保留给CT维修服务人员的.3.1.2.2 装入功能(LOAD)用来装软件模块:系统.自诊断.3.1.2.3 初始化功能(INITALIZE)数控返回到初始状态(相当于装入软件的状态).3.1.2.4 继续功能(CONTINUE)用于退出特别启动屏幕,进入正常操作(象上面的操作一样,激活最后一个屏幕).3.2 安装软件3.2.1 系统软件一旦初始化菜单被激活,接着:* 把系统盘(磁盘A)插入驱动器A* 选择LOAD(F2)在装软件期间,磁盘驱动器二极管和屏幕右一指灯亮,数控显示装入过程的信息.装入结束后,NC在EXE方式下,以便执行装入下列文件的操作.(语言,CT-EXPERT.CAM- CT)3.2.2. 装入系统软件后,显示语言配置菜单:* 指明所需要的语言名,用RETURN确认* 根据指示插入所选择的语言盘* 按F1(寻找)输入必须的文件,设备即按所选语言配置.3.3 屏幕组织* 准备模式(PREPARATION) 符号: PREP 背景色: 绿色* 执行模式(EXECTION) 符号: EXE 背景色: 紫色* 信息模式(INFORMATION) 符号: INFO 背景色: 蓝色* 图形模式(GRAPIC) 符号: GRAPH 背景色: 橙色3.3.1 PREP 准备方式3.3.1.1 编辑器(EDITOR)该功能用来建立或修改ISO程序,控制程序PROFIL程序1): 寻找文本(FIND.TEXT)2): 寻找下一个(FIND NEXT)3): 块(BLOCK)4): 标记范围开始(MARK START>标记范围结束(MARK END)5): 保存文件(SAVE FILE)6): 退出(EXIT)3.3.1.2 CAM-CT* 准备ISO零件程序需要交替运用菜单功能与绘图功能.<此单节介绍略>3.3.1.3 专家系统(CT-EXPERT)* 这些程序可以手工或者由CT-EXPERT专家系统自动生成.* 与不使用CT-EXPERT专家系统相比,CT-EXPERT生成的TEC文件是分完整的.用一个TEC文件,一个ISO文件和一个命令文件就可能执行个加工操作.相反,当一个文件在CT-EXPERT中查询或者修改时,必须3.3.1.4 文件(FILES)* 本功能用于处理存储在(所用的)不同单元上的所有文件(选择一个单示其下的文件目录).* 可以对给定目录中的文件操作,或者从一个目录转到另一个目录.1): 拷贝(COPY)2): 删除(DELETE)3): 改变名称(RENAME)4): 显示(DESPLAY)5): 打印(PRINT)6): 转换单元(CHANGE UNIT)7): 格式化(INITIALISE)8): 退出(EXIT)3.3.1.5 表编辑(EDIT TABLES)1): TEC--规准表(工艺文件的定义)2): OFS--偏移量(补正量)3): VAR--变量(变量值代入)4): WIR--电极丝(使用线参数)3.3.2. EXECUTION执行方式* 配置机台* 调节多种参数* 运行测量功能* 在开始加式操作之前,执行所需要的测试3.3.2.1. 执行程序(PROGRAM EXECUTION)1). 切割(CUT)2). 空跑(DRY RUN)3). 检验(VERIFY)4). 绘图(DRAW ON SCREEN)5). 改变模式(CHANGE UNIT)3.3.2.2. 用户参数(USER PARAMETERS)1) HPA: 工件设度2) CLE: 补偿间隙3) SCF: 比例系数4) ROT: 工件旋转5) TFE: 补正量认可6) TRE: 斜度认可7) MIR,X: X镜像8) MIR,Y: Y镜像9) ZID: 下导头至平台距离10) ZSD: 上导头至工件顶部距离11) BLK: 单节执行12) CBC: 一个命令一个命令执行13) SIM: 加工与空跑转换14) TSIM: 模拟穿丝15) VSIM: 空跑速度16) BLD: 遇"/"跳过17) OSP: 选择性暂停18) ENG: 选择单位19) COE: 遇不错误继续执行20) ART: 断电后自动重启动21) ATH: 断丝后重穿丝22) CHRA: 选择表面精度的单位23) WIRE LN : 电极丝的消耗量24) MIOL: 测量允许的误差25) DVI: 缺省使用的源外设26) EXT: 缺省扩展27) DEIO: 电介液的导电率28) ATT: 开始切入路径的长度29) EAO: 遥控报警3.3.2.3: 电源参数(GENERAO PARAMETERS)* EL: 使用的电极丝号* PA: 工件的材料号1) FF: 暂时降低频率2) M : 切割方式3) V : 切割电压4) A : 脉冲宽度(放电时间)5) B : 休止时间6) S : 最大进给率7) AJ: 伺服基准平均电压8) TAC: 短脉冲时间9) IAL: 点火脉冲电流10) WS: 走丝速度11) WB: 线张力12) INJ: 水压13) ST: 保护策略3.3.2.4: 作图参数(DRAWING PARAMETERS) <略>3.3.2.5: 激活表(ACTIVE TABLES)1). TEC: 工艺表2). OFS: 补正值表3). VAR: 变量表4). PNT: 点表5). WIR: 电极丝准备表3.3.2.6: 测量(MEASURING)测量功能用于执行一系列操作,这些操作分成两类.* 机台调校测量* 电极丝相对于被加工工件位置的测量* 电极丝相对于被加工工件位置的测量1).找外轮廓中心(EXTERNAL CENTERING)2).找中心平面(MIDDLE) (寻沟槽)3).找拐角(CORNER)4).测角度(ALIGN ADGE)5).校孔ALIGN HOLES6).找边EDGE7).电极丝校垂直VERTICAL ALIGNMENT8).找中心CENTER9).工件校垂直PART ALIGNMERNT10).测ZID GUIDES SETUP11).喷嘴调节NOZZLE ADJUST12).垂直返回VERTICAL RETURN13).工件返回PART RETURN注意:1).一定要在加工状态下执行测量功能,例如,上导向器在低位置(工作位置),丝的张力正确(张力已校准,并且WB=精加工张力).水的离子浓度合适(即水电阻率要求范围)并保持恒温.2).被加工工件必须除油,去磁,去毛刺.3).每周一次,或者在每次加工高精度,斜度加工之前,特别是拆卸导向器后,要执行电极丝导向器设定功能.4).确信使用的电接触类型与所用电极丝的类型一致.5).开始测量前,要确认电极丝没有与被测量物短路.3.3.2.7. 手动(MANUAL)1).接触激活/不激活动力(TOUCH ACTIVE)2).返回断线点或轮廓(RETURN CONTOUR)3).电源参数(GENERATOR PARAMETERS)4).点动/连续方式(INCRE MENTAL MODE)5).接通/断开接触(SWITCH OFF CONTACT)6).激活/不激活(SWITCH OFF JET)7).软极限(SOFT LIMITS)3.3.2.8. 基准点(REFERENCE)机台配置的光栅尺每10MM有一个基准标记,任何一个基准标记都可以用来决定坐标轴的基准位置.3.3.2.9 服务(SERVICE)1).日期和时间(DATE HOUR)2).周期(CYCLES)3).语言(LANGUAGE)4).安全(SECURITY)3.3.3. INFO查询模式* 它汇集了所有涉及到机台配和加工操作监视的信息.3.3.3.1 观察画面(SURVEY)1). 机台坐标系(MACHINE)2). 工作坐标系(PART)3). 速度(SPEED)4). 压力(PRESURE)5). 去离子(DEIO)6). DO=0.000(补正值)3.3.3.2 加工画面(MACHINING)3.3.3.3 运行程序画面(RUNNING PROGRAMS)3.3.3.4 信息画面(MESSAGES)3.3.3.5 模态状况画面(MODAL STATE)3.3.3.6 空白画面(BLANK)3.3.3.7 参考点画面(REFERENCE)3.3.3.8 输入输出画面(INPUTS-OUTPUTS)3.3.3.9 断丝点画面(BREAKAGE POINTS)3.3.3.10 参考点画面(REFERENCE)3.3.3.11 输入输出画面(INPUTS-OUTPUTS)3.3.3.12 断丝点画面(BREAKAGE POINTS)3.3.3.13 服务画面(SERUICE)3.4 GRAPHIC 图形方式图形方式有一个图形页面,用于在操作者定义的平面上执行一个工件程序期间,在屏幕上显示电极丝行经的轨迹.3.5 常用命令词:3.5.1 CTA:用于机床坐标系的绝对加工移动.3.5.2 CTR:用于机床坐标系的相对加工移动.3.5.3 CPA:用于工件坐标系的绝对加工移动.3.5.4 CPR:用于工件坐标系的相对加工移动.3.5.5 GOH:用于移动Z轴,并根据新的工件高度H定位上导向器喷嘴的位置.3.5.6 GOP:把机床各轴移动到用SEP命令储存的点位.3.5.7 MOV:在机床坐标系中移动到所选定的数值.3.5.8 MVR:在机床坐标中相对移到所选定的数值.3.5.9 MPA:在工件坐标中移动到所选定的数值.3.5.10 MPR: 在工件坐标中相对移动到所选定的数值.3.5.11 REX:从当前规准表中取规准,传输给加工电源,参数根据工件高度H设定.3.5.12 SEP:点记忆.3.5.13 ZCL:时间计数器清靃.3.5.14 SMA:设定机床坐标系的X轴和Y轴坐标.3.5.15 SPA::设定工件坐标系的X轴和Y轴坐标.3.5.16 SPG:用来执行一个工件程序文件.3.5.17 TEC:用于选择含有即将使用的工艺规准表文件.3.5.18 CLS:清屏幕显示的图形页.3.5.19 CPY:用于拷贝原文件到另一前设,可以换名字.3.5.20 DLF:删除文件.3.5.21 LOOP:返回命令程序起点,并执行一定次数.3.5.22 SWA:存储电极丝按工作表面手动校直位置.3.6 加工前检查清单:3.6.1«电介液»功能检查:3.6.1.1过滤:确认过滤网压力表读数是否在设定范围,观察导电块冷却区是否有水浸泡.3.6.1.2 去离子度:15±2U.CM3.6.1.3 温度:20±0.53.6.2«腐蚀»功能的检查:3.6.2.1 导电块:是否被水浸泡,表面磨损情况及安装质量.3.6.2.2 接地电缆和编织线:各电缆连接是否牢固.3.6.3 «电极丝更换»的检查:3.6.3.1 丝的种类(直径.材料)3.6.3.2 走丝是否正常3.6.3.3 如果安装新的丝轴,检查丝轴的质量.丝是否有氧化.3.6.3.4 丝的校直和退火.3.6.4工件安装检查:深圳培训网3.6.4.1 夹治具的清洗.3.6.4.2 工件去毛刺.清洁.3.6.4.3 工件装夹.3.6.4.4 工件的调整.3.6.5参数调整和检查:3.6.5.1 绝对参考点找取.3.6.5.2 在更换(重新装)导向器之后,进行«导向器»设定循环.3.6.5.3 在更换喷嘴或更换导向之后,运行«喷嘴调节»过程.3.6.5.4 如果没有在命令程序内设定丝参数,就要在程序一开始加入该设定.3.6.5.5 在«EXE»方式下检查«用户»和«电源»参数什是否在工件切割时要求的参数值.3.6.5.6 在丝准备表内选择丝文件.(.WIR)3.6.5.7 选择需要的工艺文件.(.TEC)3.6.5.8 选择用户偏移文件.(USER.OFS)3.6.6程序运行.3.6.7开始切割.。
夏米尔慢走丝指令清单

准备功能G指令清单GOO 不加工的运动句法 G00<Xx><Yy><Zz><Cc><Rr>定义四轴联动,以线性插补方式运动到指定点(X、Y、Z、C)。
有C轴运动时,Rr表示电极相对于其中心的最大半径。
<Rr>不改变几何形状,但改善“C”轴伺服性能等价于PROFORM:GOTO/<,X,x><,Y,y><,Z,z><,C,c><,R,r>例ISO语言编程GO1 轮廓直线加工轨迹句法 G01<L1><Hh><Xx><Yy><Zz><Ee> <> 可选项定义轮廓直线加工轨迹。
等价于ROBFORM:X,x,Y,y(如用G17)LINE/ Y,y,Z,z(如用G19),L,I,H,h,E,e Z,z,X,x(如用G18)注:主加工轴为Z时使用LI代替Zz。
GO2 轮廓圆弧加工轨迹句法 G02<Xx><Yy><Zz><Ll><Hh><Ii><Jj><Kk><Ee><> 可选项定义顺时针圆弧加工轨迹。
注:一个整圆的编程至少要用两次ARC指令,才能完成。
等价于PROFORM:,X,x,Y,y(如用G17)ARC/DIR ,Y,y,Z,z(如用G19)L,I,H,h,E,e,Z,z,X,x(如用G18)GO3 轮廓圆弧加工轨迹句法 G03<Xx><Yy><Zz><L1><Hh><Ii><Jj><Kk><Ee><> 可选项定义逆时针圆弧加工轨迹。
注:一个整圆的加工,至少要两次ARC指令,才能完成。
数控线切割机安全操作作业指导书(09)

4.5.12.修改加工条件参数必须在机床允许的范围内进行。
4.5.13.加工中严禁触摸电极丝和被切割物,防止触电。
4.5.14.加工时要做好防止加工液溅射出工作箱的工作。
4.5.15.加工中严禁靠扶机床工作箱,以免影响加工精度。
4.2.2.检查确认工作液是否足够,不足时应及时添加。
4.2.3.无人加工或精密加工时,应检查确认电极丝余量是否充分、足够,若不足时应更换。
4.2.4.检查确认废丝桶内废丝量有多少,超过1/2时必须及时清理。
4.2.5.检查过滤器入口压力是否正常,压缩空气供给压力是否正常。
4.2.6.检查极间线是否有污损,松脱或断裂,并确认移动工作台时,极间线是否有干涉现象。
4.6.3.拆卸工件(板材)时,要注意防止工件(板材)失稳掉落。
4.6.4.加工完毕后要及时清理工件台面和工作箱内的杂物,搞好机床及周围的“5S”工作。
4.6.5.工装夹具和工件(板材)要注意做好防锈工作并放置在指定位置。
4.6.6.加工完毕后要做好必要的记录工作。
4.7.1.清除切屑、擦拭机床,使用机床与环境保持清洁状态。
5.3.慢走丝线切割机的丝驱动轮和导轮,每切割40小时要清洗一次,以保证轮子的清洁,同时应检查导轮运转是否灵活以及表面凹槽磨损情况,必要时需更换。
5.4.每切割40小时还需检查和清洗上下导丝嘴,利用专用工具将导丝器从导丝嘴上取出,将导丝嘴、导向器放入超声波或商用宝石清洗器中清洗。也可以放在弱酸类除垢液中浸泡片刻,特别注意清洗内部通道,然后用清水冲净。导向器和导丝嘴以及导电盒内璧务必擦干净后才能重新装入。
中山市小榄镇泰阳模具塑胶制品厂
慢走丝线切割作业指导书

XXXXX公司作成:确认:承认:XXXX公司编号WI-002线切割作业指导书制定日期2005/12/31分类指导书制定单位制造一课版本B页次 2 of 4确认对象确认内容使用工具资料及方法判断处理方法及注意事项加工的内容GP、合せ辅助穴对照作业指示票W寸法图导柱与导套对照作业指示票构造图一般只加工导套,导套一般正寸﹣50来加工。
有无特殊加工对照作业指示票时记事项如模具有无三次加工,有无ST3仕样,有无先后道加工的地方等等。
加工前机器确认清洁度,干燥度使用气枪等打扫垂直度使用ウィセ自动垂直器给电子、铜线查看生产情报,目测查看W机的生产情报即给电子,一般100h换一次铜线规格无特殊指示,一般情况下为φ0.2冷却水纯度50以上,单位为内部设计(二)、架板开始1、架板:(1).确认做冲针有两次加工时,拉住的位置一定要多(至少5mm以上),一般选位处进 线孔放电加工。
(2).确认正图、逆图,(逆图正面架则要开镜像)。
(3).确认是否テ-ハ加工,一般热处理板的中拔需テ-ハ加工,制品穴落料不够大或刀 口过多要テ-ハ加工。
另:热处理板下模(才型、ダィス刀口 一般2.0~2.2),其它下模(才型、ダィス刀口一般2.2~ 2.5) ,上型(ストリッパ-、シェダ一刀口一般3mm),其余特殊情况设计时再指示。
作成:确认:承认:XXXXX公司编号WI-002线切割作业指导书制定日期2005/12/31分类指导书制定单位制造一课版本B页次 3 of 41 、平行,绞基准。
当有些变更或其它原因没有平行穴时,采用W显示器坐标和百分表合起来,上下移动对平行。
变更或第二次架板时,应绞两个割过的孔并取其差异的中间值,差异超过0.02~0.03时应谨慎行事,没有十足把握应及时联络。
另对于KYS这种单面、多孔而又W不加的板,一般要绞两个或多个孔,以确其穴的好坏。
2、输入加工文件,一般根据加工顺序输入所有这块能加工的内容。
一般先中拔,再外形;再外形两次,中拔两次,再切落。
电火花慢走丝机床岗位作业指导书

慢走丝线切割机床岗位作业指导书
1 范围
本规程规定了设备在生产运行过程中的生产规程、操作规程、维护保养、安全环保、常见故障与排除等内容。
本规定适用于AGIE 120 、ROBOFORM 310、AGIE CHALLENGE 2、AGIE CLASSIC V2型号的慢走丝线切割机床。
2 规范性引用文件
下列文件对于本文件的应用是必不可少的。
凡是注日期的引用文件,仅所注日期的版本适用于本文件。
凡是不注日期的引用文件,其最新版本(包括所有的修改单)适用于本文件。
电加工岗位作业指导书
3 本作业指导书的组成
慢走丝线切割机床的性能参数
慢走丝线切割机床的生产控制要求
慢走丝线切割机床的操作
慢走丝线切割机床的维护保养
慢走丝线切割机床的安全、环保
慢走丝线切割机床常见故障分析及处理
4 性能参数
4.1 概述
慢走丝线切割机床是模具加工行业的重要机床之一,特别在XX模具生产中更为重要,由于XXXX的脆性和高硬度性能,是其他切削机床不可替代的设备之一。
它能加工出精度较高、表面质量好的复杂的几何型腔。
4.2 原理
慢走丝线切割机床应用电源的两个极性在一定的距离(通常为几个至几十个微米)内产生电火花,由于电火花产生的高温(高达上千度)使金属熔化脱离工件达到去除金属的目的。
通过控制丝运行的轨迹来控制加工产品的几何形状。
4.3 主要技术性能
表 1。
夏米尔慢走丝工艺参数

夏米尔慢走丝工艺参数全文共四篇示例,供读者参考第一篇示例:夏米尔慢走丝工艺是一种高精度加工工艺,适用于制造精密零部件和复杂形状的零件。
本文将从慢走丝工艺的基本原理、工艺参数及优势等方面进行介绍,希望能为读者提供一些参考。
夏米尔慢走丝工艺是一种使用线切割机床进行切割加工的工艺,通过电脉冲将工件表面的金属材料剥离下来,从而实现对工件进行加工的目的。
其工作原理是利用一根细丝作为电极,在脉冲电流的作用下,将工件材料熔化并冷凝成小颗粒,最终被冲击气流冲走,实现切割加工。
在夏米尔慢走丝工艺中,有一些重要的工艺参数需要进行调整和控制,以确保加工效果和加工质量。
其中包括放电电流、放电电压、脉冲宽度、工作液流量、工作速度等参数。
这些参数的设定将直接影响到加工速度、加工精度以及电极磨损程度等方面。
放电电流是夏米尔慢走丝加工中最为关键的参数之一,它的大小将直接影响到放电火花的能量和加工效果。
通常情况下,放电电流越大,放电火花的能量就越强,加工效率也就越高。
但是要注意的是,放电电流过大会导致加工表面粗糙度增大和电极磨损加剧的问题。
工作液流量是指在加工过程中用于冷却和冲洗工件表面的液体流量,其大小将直接影响到加工热量的排除和加工效果。
合理的工作液流量能够有效地降低加工温度和冷却工件,从而提高加工质量和延长电极寿命。
工作速度是指慢走丝机床在进行加工时的运行速度,其大小将直接影响到加工精度和加工效率。
通常情况下,工作速度越快,加工效率就越高,但同时也会影响到加工精度。
因此需要根据具体的加工要求和工件的材料性能来合理地选择工作速度。
各种参数的调整和控制需要经过多次试验和实践,才能找到最佳的加工参数组合。
在实际加工过程中,工艺师需要根据工件的要求和材料特性来进行针对性的调整,以达到最优的加工效果。
夏米尔慢走丝工艺具有高精度、高效率、适用性广等优点,在航空航天、汽车、电子、医疗器械等领域得到了广泛的应用。
通过不断的研究和实践,相信夏米尔慢走丝工艺在未来会有更广阔的发展空间,为制造业的发展注入新的活力。
OP-080慢走丝线切割机操作保养作业指导书1.0
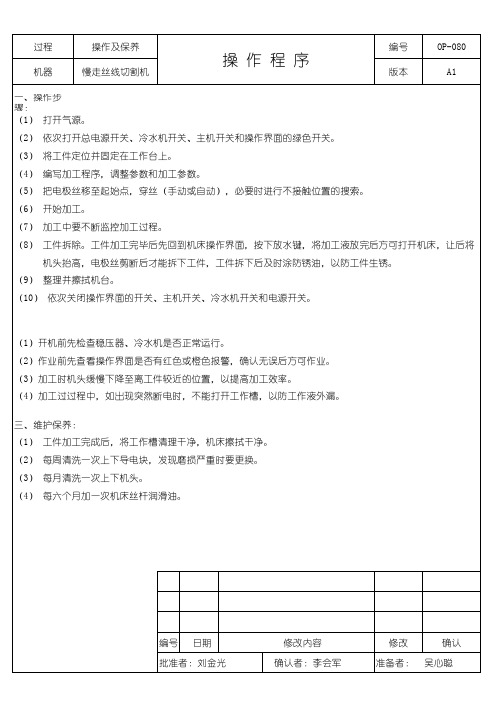
编号
日期
修改内容 确认者:李会军
修改 准备者:
批准和操作界面的绿色开关。
动),必要时进行不接触位置的搜索。
操作界面,按下放水键,将加工液放完后方可打开机床,让后将
,工件拆下后及时涂防锈油,以防工件生锈。
、冷水机开关和电源开关。
运行。
色报警,确认无误后方可作业。
置,以提高加工效率。
(8) 工件拆除。工件加工完毕后先回到机床操作界面,按下放水键,将加工液放完后方可打开机床,让后将 机头抬高,电极丝剪断后才能拆下工件,工件拆下后及时涂防锈油,以防工件生锈。 (9) 整理并擦拭机台。 (10) 依次关闭操作界面的开关、主机开关、冷水机开关和电源开关。
(1)开机前先检查稳压器、冷水机是否正常运行。 (2)作业前先查看操作界面是否有红色或橙色报警,确认无误后方可作业。 (3)加工时机头缓慢下降至离工件较近的位置,以提高加工效率。 (4)加工过过程中,如出现突然断电时,不能打开工作槽,以防工作液外漏。 三、维护保养: (1) 工件加工完成后,将工作槽清理干净,机床擦拭干净。 (2) 每周清洗一次上下导电块,发现磨损严重时要更换。 (3) 每月清洗一次上下机头。 (4) 每六个月加一次机床丝杆润滑油。
过程 机器 一、操作步骤: (1) 打开气源。
操作及保养
编号
操 作 程 序
慢走丝线切割机 版本
(2) 依次打开总电源开关、冷水机开关、主机开关和操作界面的绿色开关。 (3) 将工件定位并固定在工作台上。 (4) 编写加工程序,调整参数和加工参数。 (5) 把电极丝移至起始点,穿丝(手动或自动),必要时进行不接触位置的搜索。 (6) 开始加工。 (7) 加工中要不断监控加工过程。
能打开工作槽,以防工作液外漏。
慢走丝之统赢操作说明及后处理修改说明
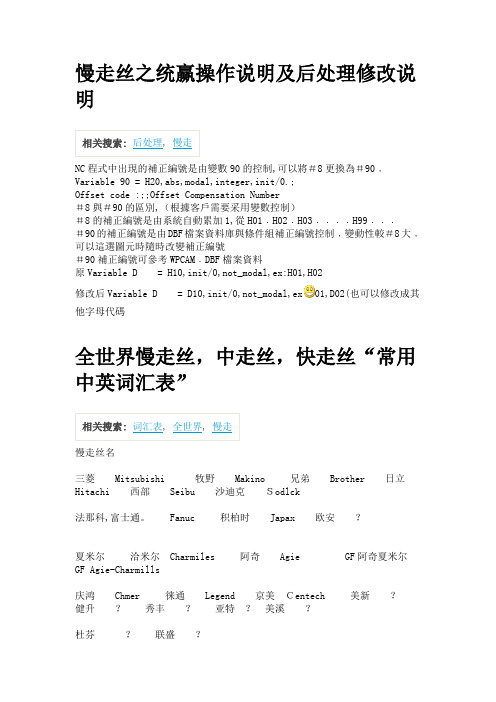
慢走丝之统赢操作说明及后处理修改说明相关搜索:后处理, 慢走NC程式中出現的補正編號是由變數90的控制,可以將#8更換為#90﹐Variable 90 = H20,abs,modal,integer,init/0.;Offset code :;;Offset Compensation Number#8與#90的區別,(根據客戶需要采用變數控制)#8的補正編號是由系統自動累加1,從H01﹒H02﹒H03﹒﹒﹒﹒H99﹒﹒﹒#90的補正編號是由DBF檔案資料庫與條件組補正編號控制﹐變動性較#8大﹐可以這選圖元時隨時改變補正編號#90補正編號可參考WPCAM﹒DBF檔案資料原Variable D = H10,init/0,not_modal,ex:H01,H02修改后Variable D = D10,init/0,not_modal,ex01,D02(也可以修改成其他字母代碼全世界慢走丝,中走丝,快走丝“常用中英词汇表”相关搜索:词汇表, 全世界, 慢走慢走丝名三菱Mitsubishi 牧野Makino 兄弟Brother 日立Hitachi 西部Seibu 沙迪克Sodlck法那科,富士通。
Fanuc 积柏时Japax 欧安?夏米尔洽米尔Charmiles 阿奇Agie GF阿奇夏米尔GF Agie-Charmills庆鸿Chmer 徕通Legend 京美Centech 美新?健升?秀丰?亚特?美溪?杜芬?联盛?三光科技Sanguang Technoloies 汉川?三光沙迪克Sanguang Sodlck 北京阿奇?中特?宝码?上海通用?安德?编程系统Esprit 无中文名你能取一个MasterCam 无中文名Ycut 立先Wpcam 统羸机台性能:最大工件尺寸Max workpiece size 最大工件重量Max workpiece weight X和Y轴行程X/Y Travel U,Vl轴行程U,VTreavl Z轴行程Z Travel 机械重量Net Wight机头移动距离Machine Head movement 电极直径Electrode pipe diameter 加工液容量Fluid capacity 加工液Dielectric fluid加工电源Input power 最大加工电流Max machineing current 机械高度Machine height 机台尺寸Machine size机器特性Features 穿线方法Thread type 半自动穿线Semi-auto thread 自动穿线Automatic thread驱动器Driver 伺服马达Servo motor 光栅尺位置检出装置Liner scale Positioning 线张力Wire tension 线速Wire feed垂直度Perpendicularity 锥度Taper 斜度Oblique 过滤方式Filtering element 纯水供液系统Pure water supply unit离子交换Ionexchange 冷却系统Coolant system 控制轴Axis control 最小设定单位Min setting 最小移动单位Min movment程序储存Program storage 轴旋转Axis rotating 镜像Mirror 线径补偿Offset 倍率scale 自动园角corner path转角暂停corner pause 加工电源Power supply 放电回路Discharge loop 电流current 停止时间Off time 放电时间On time辅助电流Auxiliary current 辅助停止时间Auxiliary offtime 伺服电压Servo Voltage 开路电压Open Voltage 精修功能Fine finish起始点回归Start point return 暂停点回归Hold point return 路径跟踪Path trcing 路径倒走Path retrace 起始点start point机台重置Restart 空跑Dry run 单节运行Single block execution 选择性停止Optional stop 斜度加工Taperdischarge选择性暂停Optional skip 呼叫子程序Subprogram 在线帮助On Line help 自动垂直校正Auto perpendicularity rectify自动寻边Auto edging 软件机台极限设定Soft limitsetting 自动找园中心Self centering 自动找外园中心Self O,Pcertering自动找沟Self centering in slit 座标Coordinate 参考点设定Reference point set 切割长度显示Cutting length display 回归参考点Home return加工时间计算working timer 切割速度显示Cutting speeddisplay 单节模拟Single block simulation 转角路径控制Cornering path control加工警告信息Alam message 喷水FW 浸水SW 材质Material 电极丝抗拉强度Wire tensile strength 廷伸率Elongation线芯材料core material 线轴Spool 转角内侧cornerinner 转角外侧corner outer 硬线Hard wire 软线Soft wire配合间隙自由配合Free fit 轻压配合Finger press fit 压入配合Handfit 松配合Rough fit 压配合Press fit 推入配合Push fit 滑动配合Easy push fit 轻转配合Easy running fit 轻滑配合Easyslide fit 精确配合Exact fit紧动配合Close running 特小间隙配合Close sliding fit 紧滑配合Close working fit 公差Tolerance 偏差Deviation火花位Wire overburn 修刀余量Stock to leave 总切割量Total offset 线切割速度Feedrate 电极丝半径Wire radius相关搜索:夏米尔, 代码Aa 锥度 A____ (角度)Cc 辅助平面旋转角度 C_____(角度)Ee 加工模式的选择 E____(正整数)Ff 多少秒闭锁时间 F____(常数)Hh 工件的厚度 H____(常数)Rr 基准面与辅助平面之间的距离 R____(常数)Ww 基准面与下部表面之间的距离G27 正常模式[取消模式 G28,G29,G30和G32]G28 锥形模式,旋转主轴类型[不变角]G29 尖角的锥形模式G30 恒定半径的锥形模式G32 扭转模式的约定和定义M03 起用电极丝进给M05 停用电极丝进给M06 自动穿丝M07 起用上部冲洗M08 起用下部冲洗M09 停用上部与下部冲洗M12 自动线切割M20 起用加工M21 停用加工多种慢走丝通用代码G代碼G00 快速移動G00 X___Y___U_ __V___G01 直線加工G01 X___Y___U_ __V___G02 順時針圓弧加工G02 X___Y___ I___ J____ G03 逆時針圓弧加工G03 X___Y____I___J____ G04G40 補正取消G40 X____Y____ G41 向左補正G41X____Y____G42 向右補正G42 X____Y____ G90 絕對值數據模式G90 (指定絕對坐標值)G91 相對值數據模式G91 (指定相對坐標值)G92 程式原點數據模式G92 X___Y____I____J____U____V ____M代碼M00 無條件停止工作M00 (當程式執行到M00單節時,機台將自動停止)M01 選擇性停止工作M01 (如果M01STOP按鍵按亮時,和M00功能相同)M02 程式結束 M02 (指定主程式結束)三菱(MITSU)線割機台代碼A 錐度 A____ (角度)L 程式編號L_____(正整數)N 程式中加工孔號N_____(正整數)R 圓弧半徑R_____(常數)K 旋轉角度K_____(角度)S 縮放比例S_____(常數)H 補正編號H_____(常數)E 加工條件E_____(正整數) F 加工速度F_____(正數)G22 呼叫副程式G22L__(正整數)G23 返回主程式G23G87 主程式與副程式圓角設定G87G88 自動化清角G88G89 取消自動化清角G89M20 自動穿線M20 M21 自動剪線M21 M80 噴水打開M80 M81 噴水關閉M81 M82 送線開始M82 M83 送線結束M83 M84 放電開始M84 M85 放電結束M85 M90 最適利進給打開M90M91 最適利進給結束M91慶鴻線割機台代碼A 錐度 A____ (角度)L(O) 程式編號L_____(正整數)N 程式中加工孔號N_____(正整數)R 圓弧半徑R_____(常數)K 旋轉角度K_____(角度)H(D) 補正編號H_____(常數)E(S) 加工條件E_____(正整數) F 加工速度F_____(正數)G22 呼叫副程式G22L__(正整數)G23 返回主程式G23G87 主程式與副程式圓角設定G87G94 定速切割G94 G95 伺服切割G95 M20 自動穿線M20 M21 自動剪線M21 M80 噴水打開M80 M81 噴水關閉M81 M82 送線開始M82 M83 送線結束M83 M84 放電開始M84 M85 放電結束M85 M90 最適利進給打開M90M91 最適利進給結束M91M98 呼叫副程式M98L(P)__ (正整數)M99 返回主程式M99沙迪克(SODICK) 線割機台代碼G05 X軸鏡象G05 G06 Y軸鏡象G06 G07 Z軸鏡象G07 G08 X.Y軸交換G08G09 取消鏡象与軸交換G09G26 圖形旋轉打開G26K___(角度) G27 圖形旋轉取消G27G50 取消錐度 G50 G51 向左側傾斜 G51G52向右側傾斜G52G74 打開四軸補正G74G75 關閉四軸補正G75G81 回歸机械原點G81G82 X或者Y方向分中G82G84 自動測垂直 G84X-G97 設定所有坐標系歸零G97XYT80 送線打開T80 T81 送線關閉T81 T82 加工液打開 T82T83 加工液關閉 T83T84 泵流打開 T84T85 泵流關閉 T85T86 噴流打開T86 T87 噴流關閉T87 T88 浸油加工T88 T89 噴水加工T89 T94 浸水加工T94 M05 忽視接触(短路)感知 M05M06 不放電M06M98 呼叫副程式M98L(P)__ (正整數)M99 返回主程式M99法蘭克(富士通FANUC) 線割機台代碼G10 設定補正值或者加工條件 G10P__R__(補正值設定)G10P__X__Y__Z__U__V__W__I__J_K_(加工條件設定 )G48 轉角R机能打開G48G49 轉角R机能關閉G49G50 取消錐度 G50X__Y__G51 向左側傾斜 G51 X__Y__ G52 向右側傾斜 G52 X__Y__G94 定速切割G94X__Y__F__G95 伺服切割G95X__Y__夏米爾(CHARMILL) 線割機台代碼Aa 錐度A_ ___ (角度)Cc 輔助平面旋轉角度C_____(角度)Ee 加工模式的選擇 E____(正整數)Ff 多少秒閉鎖時間 F____(常數)Hh 工件的厚度H____(常數)Rr 基准面与輔助平面之間的距离 R____(常數)Ww 基准面与下部表面之間的距离G27 正常模式[取消模式 G28,G29,G30和G32]G28 錐形模式,旋轉主軸類型[不變角]G29 尖角的錐形模式G30 恒定半徑的錐形模式G32 扭轉模式的約定和定義M03 起用電极絲進給M05 停用電极絲進給M06 自動穿絲M07 起用上部沖洗M08 起用下部沖洗M09 停用上部與下部沖洗M12 自動線切割M20 起用加工M21 停用加工还有很多!没有补全慢走丝线切割系统特征1.两平面,两轴直线,圆弧插补。
- 1、下载文档前请自行甄别文档内容的完整性,平台不提供额外的编辑、内容补充、找答案等附加服务。
- 2、"仅部分预览"的文档,不可在线预览部分如存在完整性等问题,可反馈申请退款(可完整预览的文档不适用该条件!)。
- 3、如文档侵犯您的权益,请联系客服反馈,我们会尽快为您处理(人工客服工作时间:9:00-18:30)。
株洲OKE硬质合金有限公司慢走式线切割工作岗位作业指导书1范围本作业指导书规定了模具车间夏米尔线切割工作岗位的操作,维护与保养和设备故障与分析基本操作规程。
本作业指导书适用于阿奇夏米尔FI240CCS慢走式线切割工作岗位。
2规范性引用文件3本作业指导书的组成技术参数操作规程维护与保养故障与排除4技术参数技术指标单位数值技术指标单位数值X轴行程mm 350 Y轴行程mm 220Z轴行程mm 220 U轴行程mm 350V轴行程mm 220 加工倾斜角度度 ±30定位精度μm 4 重复定位精度μm 3反向间隙μm 2 100毫米圆度精度μm <3最大加工速度mm2/min 500 最大工件尺寸mm 1000×550 台面尺寸mm 680×450 可侵泡最高工件高度mm 220最大工件质量kg 750 加工速度mm2/min 500最佳粗糙度um Ra0.2 标准丝直径mm 0.25丝架重量kg 0.8 走丝速度m/min 0.2-15最大穿丝高度mm 220 最小穿丝直径mm 0.6水温控制度±1最高环境温度度30总功率kw 10 输入电压v 400功率因数0.8 机床总高mm 2000机床总长mm 2050 机床总宽mm 2020机床毛重kg 3210 机床纯重kg 24505操作规程5.1工件准备5.1.1操作人员达到岗位后检查水、电、气,确定设备包括冷水机处于正常待机状态。
5.1.2按照图纸要求正确选用工装夹具,清洁待加工件表面,正确安装夹具,工件安装牢固。
确认工件安装在机床有效行程范围内。
5.2程序准备5.2.1仔细阅读图纸,在电脑上绘制几何图形,校验几何图形。
5.2.2确认程序起始位置,确认多工位程序位置与待加工件位置一致性。
5.2.3根据工艺要求确定偏移量,电参数、非电参数。
5.2.4根据图纸和工艺要求编制修整量。
5.2.5编制好程序经后处理传送到机床。
5.2.6检查机床、电器、加工电源、控制系统时、应切断电源、防止触电或损坏电路元件。
5.2.7为保证机床的运作灵活,导电块和轴承要定期检查或更换。
5.3启动准备5.3.1进入机床执行模式,调入待加工应用程序。
5.3.2绘制待加工件几何图形,对多型腔工件认真确定其起始点的一致性。
5.3.3根据工艺要求确定TEC、WIR文件,检验偏移量。
5.3.4对待加工有可能超出有效行程的工件应做模拟工作,对有可能发生机头与待加工件碰撞的工件应做模拟加工的同时手应该放在停止按钮上方,如有可能发生碰撞立刻按下停止按钮,直至确认不会发生碰撞。
5.3.5按所加工零件的尺寸、精度、工艺等要求,在线切割机床自动编程系统中编制线切割加工程序,并送控制台。
或手工编制加工程序,并通过软驱读入控制系统;5.3.6在控制台上对程序进行模拟加工,以确认程序准确无误;5.3.7再次确认工件准备无误,程序准备无误,按下启动按钮,加工开始。
5.4加工过程5.4.1合上机床主机上电源开关;5.4.2加工过程中严禁触摸工件、丝架、以免触电。
5.4.3禁止湿手按开关或接触电气部分,防止工作液等导电物进入电气部分。
5.4.4发生电气短路或火灾时,应首先切断电源,立即用干冰等合适灭火器灭火,严禁用水灭火。
5.4.5合上机床控制柜上电源开关,启动计算机,双击计算机桌面上YH图标,进入线切割控制系统。
5.4.6解除机床主机上的急停按钮。
5.4.7按机床润滑要求加注润滑油。
5.4.8开启机床空载运行二分钟,检查其工作状态是否正常。
5.4.9开启运丝筒。
5.4.10开启冷却液。
5.4.11选择合理的电加工参数。
5.4.12驱动器工作时禁止插拨软件。
5.4.13手动或自动对刀。
5.4.14点击控制台上的“加工”键,开始自动加工。
5.4.15加工初始阶段,眼看耳听机床工作是否正常。
5.4.16取废料,对于小的废料应及时从加工件内取出。
5.4.17加工过程中,操作人员要经常性的巡视机床的工作状况,直至加工结束。
5.5工作结束5.5.1加工结束后,移动机头离开工件。
5.5.2清洁夹具、工件表面,拆卸工件,如有必要夹具和工件一体拆卸。
5.5.3自检加工件,送专检处专检,获取检验结果。
5.5.4下班前,清洁工作液箱体、机床基准支承框架、导轨,关闭水泵。
5.5.5并关闭控制柜电源,关闭机床主机电源。
5.5.6保持机床、机床周围清洁,工装顶置存放。
6设备维护与保养制度6.1范围本规程规定了设备的检查与维护、润滑“五定”制度,常见故障及排除方法等内容。
本规程适用于模具车间夏米尔FL240CCS慢走式切割机的维护与保养。
6.2检测与维护为了确保设备长期处于一种较为理想的运行状态,需要对许多部件经常地进行检查与维护。
按照检查与维护的频率,分为“每日的检查与维护”、“每周的检查与维护”、“每季的检查与维护”、“每年的检查与维护”。
6.3每日的检查与维护6.3.1设备运行前及运行中每日必须检查与维护的项目内容见表2。
表2 日检与维护内容序号检查与维护部位检查与维护的具体内容责任工种1 检查电解液温度加工前把电解液温度设为20℃操作工2 检查过滤回路压力与更换过滤器报警时更换操作工3 精细过滤器的清洗有必要更换过滤器操作工4 检查去离子树脂当导电率显示值高于设定值并持续升高时更换操作工5 检查丝的质量和强度在更换线圈时检查丝的质量操作工6 检查上下导电块当导电块上的线痕大于线时更换导电块操作工7 检查导电块润滑水水要满过导电块的2/3 操作工8 检查丝的张力和线的稳定性用张力计来测量丝的张力,不足时调整操作工9 检查并调节精修水流的大小根据加工类型调节操作工6.3.2责任工种应按照要求对每天维护情况进行详细记录。
6.3.3责任工种在每天设备开动前及运行过程中根据具体情况进行检查与维护。
6.4每周的检查与维护6.4.1每周的检查与维护项目内容见表3表3 周检查与维护的内容序号检查与维护部位检查与维护的具体内容责任工种1 上喷嘴及上喷腔的质量压力表上的压力与以往有很大差别时更换操作工2 下喷嘴及下喷腔的质量压力表上的压力与以往有很大差别时更换操作工3 检查上下高压水的压力检查压力值与设定值是否一致操作工4 检查丝张力检查丝的张力值是否符合设定值操作工5 检查下导电器的清洁状况清洗或必要时更换操作工6 检查上导向器的清洁状况清洗或必要时更换操作工7 检查压丝轮当走丝不平稳或丝痕太大时更换操作工6.4.2每周的检查与维护项目内容由设备员将其纳入其月度检修计划任务中,与其他检修项目一起下达任务检修计划任务单。
6.4.3将“周检与维护内容”完成情况纳入各单位每周例进行的综合大检查工作中。
6.5每季的检查和维护6.5.1每季的检查和维护内容见表4表4 季度的检查与维护内容序号检查与维护部位检查与维护的具体内容责任工种1 检查或更换虹吸喷嘴组件必要时更换操作工2 检查/清洁穿丝嘴穿丝嘴已损坏、有裂痕磨损时更换操作工3 检查/更换上喷嘴宝石有裂痕时更换操作工4 清洁上机头清洁上机头操作工5 润滑X、Y、U、V和Z轴当出现1402或2110报警时加润滑脂操作工6.5.2每季的检查与维护内容根据实际情况,在每季度中某月的月度检修计划中安排,有设备员将其分解纳入该月度检修计划中,与其它检修项目一起下达检修任务单。
6.5.3在公司季度大检查前由各单位进行完成情况的自检,公司检查中将进行抽检。
6.6每年的检查与维护6.6.1每年的检查与维护内容见表5表5 年度检查与维护内容序号检查维护部位检查与维护的具体内容责任工种1 电解液水箱每半年更换电解液并清洗水箱操作工2 检查接地电缆质量检查电缆是否有磨损,断裂,分叉必要时更新操作工3 检查穿丝模块中的宝石导向器有必要时更换操作工4 检查上导向器的清洁状况清洗,必要时更换操作工5 检查下导向器的清洁状况用水或高压气清洗必要时更换操作工6 检查张力皮带的损耗检查丝的张力值操作工7 检查导电碳刷的状况必要时更换操作工8 检查喷嘴及穿丝管支撑组件清洗组件,必要时更换操作工9 油管中的油位油不足时加油操作工6.6.2每年的检查与维护内容根据实际情况,在每年中某月的月度检修计划中进行安排,有设备员见其分解耐人该月度计划任务中,与其他检修项目一起下达检修计划任务单。
6.6.3在公司年度大检查前由各单位进行完成情况的自检,公司检查中将进行抽查。
7润滑“五定”制度7.1设备的润滑部位及油量加注情况见表6。
责任工种应按规定的周期和数量加注指定牌号的润滑油脂。
表6 润滑“五定”内容序号润滑部位油脂牌号加油周期添加量责任工种1 润滑下机头后面齿轮012.648 一年两次TOPAS AK50油枪压油7次操作工7.2设备的润滑根据设备的实际情况,在月度设备检修计划中安排,并有专用的润滑笔记本,按规定进行填写。
8常见故障及排除方法8.1 设备的常见故障机排除方法见表7表7 常见故障及排除方法序号现象原因处理方法1 断丝在工件和上加工头之间1.上加工头调整不当2.上导电快湿润不够3.工件表面已氧化4.导电块损坏5.上加工头太脏6.上冲液调整不当或不合适1.检查喷嘴的调整情况2.目测或调整3.清洗4.检查质量/磨损/紧固情况5.当手动拉电极丝时,应当感觉不到任何明显阻力点;特别要清洗导向器6.检查高压冲液压了2 断丝在工件中部1.无冲液或上下冲液太弱2.射流中混有空气3.丝张紧力太高或张力波动4.TAC太高5.B太小6.Aj太低7.脉宽A太大8.电极丝质量不好9.走私速度太低10.下导电快湿润不够11.导电快损坏1.检查高压冲液压力2.净水箱中液面偏低;泵M15有问题;高压冲液回路泄漏或混入空气3.用张力检查4.按工艺检查5.按工艺检查6.按工艺检查7.按工艺检查8.检查电极丝质量9.按工艺检查10.目测或调整11.检查质量/磨损/紧固情况3 断丝在工件和下加工头之间1.下冲头液调整很差或不当2.走丝速度太低3.下加工头太脏1.检查高压冲液压力2.按工艺检查3.清洗加工头4 剪丝机构失效1.检查气源压力2.检查压力开关设定3.检查失效是否重复出现4.检查压缩空气管路是否有泄1.必要时调整2.必要时调整3.判断是否是电极丝的问题4.检查电磁阀Y5在穿丝循环中是否漏接通;检查Arma电路板上的保险丝F1和F2;检查管中的气流是否存在;调整螺杆必须开大;检查退火轮电刷;检查上导电块的状况。
5 电极丝不能穿过上导向器1.检查制动皮带2.检查电极丝质量3.检查参数设置1.必要时更换2.必要时更换3.缺省值770,必要时可修改6 电极丝不能穿过下导向器1.下导向器太脏或阻塞2.检查参数设置3.穿丝射流问题1.清洗导向器2.重新调整参数3.如果射流不存在,调整穿丝射流的流量调节器7 丝一直短路,机床不能加工1.检查丝是否卡在工件中2.检查丝是否堵在上或下导向器中3.取出电极丝1.修复2.修复3.激活点接触8 精加工后工件精度有问题1.规准设置不正确2.丝张力问题3.去离子问题4.走丝速度问题1.调整规准选择2.调整制动器3.更换去离子树脂4.进行电极丝校准循环9 精加工后工件表面有条纹1.丝张力变动问题2.电丝回路滚轮有故障3.电极丝在制动皮带上滑动4.电极丝回路太脏5.导向器磨损或紧固不良6.收丝驱动滚轮对丝的压力不正确1.调整制动器2.检查各滚轮是否转动自如3.检查皮带状况/磨损4.清洗上/下加工头5.清洗或更换6.检查驱动滚轮对丝压力的设定10 液面降低严重1.过滤器堵塞2.水泵不转3.管道有大量渗透1.更换过滤芯2.检查水泵接线3.检查管道及各连接处11 加工区供水不够正常1.水泵不转或反转2.管道内有空气3.管道折弯、卡住1.检查接线2.工作液箱内加水3.理顺管道4.更换过滤器12 电极丝对工作台平面的垂直度不好1.宝石导向器磨损2.电极丝垂直度校正失误3.UV轴回原点有误4.微动开关松动5.丝杆、导杆表面有异物6.丝杆导轨润滑不良1.更换新的2.重新校正3.见数控部分4.重新安装微动开关5.清除异物,檫干净6.给润滑13 工作液电阻率不上升1.离子交换树脂失效2.三相电泵运转不良3.仪表出故障1.更换新树脂2.检查电泵接线3.检查仪表接线14 刚开始切割工件时断丝1.进给不稳,开始切入速度太快或电流过大1.刚开始切入,速度应稍慢些,而视工件的材料厚薄,逐渐调整速度至2.切割时,工作液没有正常喷出3.钼丝在贮丝筒上松紧不一致,造成局部抖动厉害4.导轮及轴承已损或导轮轴向径向跳动大,造成抖丝厉害5.线架尾部挡丝棒没有调整好,挡丝位置不合适造成叠丝6.工件表面有毛刺,氧化皮或锐边合适位置2.排除工作液没有正常喷出的故障3.尽量绷紧钼丝,使之消除抖动现象4.如果绷紧钼丝,调整导轮位置效果不明显,则应更换导轮或轴承5.检查钼丝在档丝位置是否接触或靠向里侧6.去除工件表面的毛刺,氧化皮货锐化边等。