典型自动脱螺纹注射模设计
灯头接线盒罩自动脱螺纹注射模设计

生产 效 率高 , 可成 型 螺纹精 度 要求 高 的塑件 。 ]
1 产 品 结 构 及 工 艺 分 析
图 1是 灯 头 的 接 线 盒 壳 罩 。 其 外 径 为
是采 用 电动 机或 液 压 马 达 作 为 动 力 带 动 传 动 机
构使 螺纹 型 芯旋 转而 自动脱模 ; 二是 直接 利用 模 具开 模过 程 作为 动力 , 动传 动 机构 使螺 纹 型芯 带
现 代 甥 料 加 工 应 用
20 10 年 第 2 2卷 第 2期
M (D ER N ) PL A S I S PR O CES NG N D PPLI T C SI A A CA T 1 N S 0
灯 头 接 线 盒 罩 自动 脱 螺 纹 注 射 模 设 计
邓 万 国
( 东 省技 师 学 院 ,广 东 惠 州 ,5 6 0 ) 广 1 1 0
摘 要 :根 据 灯 头 接 线 盒 罩 的结 构 特 点 , 射模 采 用 大 导 程 螺 杆 和 螺 母 机 构 实 现 塑 件 成 型 后 的 自动 旋 转 脱 螺 纹 的 脱 模 过 注 程 。该 自动 脱 螺 纹 过 程 安 全 可 靠 平 稳 , 产 效 率 高 , 合 于 螺 纹 精 度 要 求 高 的 塑件 的成 型 。 生 适
m a i e oul i e ha s tc d m d ng m c nim
在 成 型带 有 内螺 纹 塑 件 时 , 纹 成 型后 的 螺
旋转 而 自动 脱模 。对 于后 者 也 有 2种方 式 : 种 1 是传 统 上常 用 的在 开模 时 通 过 齿 条 带 动齿 轮 进
脱模 是模 具 设计 的关 键 , 传统 的模 具 设计 方 法有
注塑内螺纹直接脱模结构设计方案

注塑内螺纹直接脱模结构设计方案一、整体思路。
咱们得想个办法,让带有内螺纹的塑料制品在注塑完后,能轻松地从模具里脱模,就像从被窝里钻出来一样容易,而且还不能把这个螺纹给搞坏喽。
二、具体结构设计。
1. 螺纹型芯部分。
首先呢,这个螺纹型芯不能是个死脑筋的结构。
咱们可以把它设计成两段式的。
就像火车有车头和车厢一样。
靠近模具型腔内部的那一段螺纹型芯,咱们可以让它稍微细一点,就像小一号的螺丝。
这一段的螺纹是完整的,用来成型产品的内螺纹。
然后外面再套上一段粗一点的“外套”,这个外套和里面的细螺纹型芯之间要有一定的间隙,这个间隙就像两个好朋友之间保持的小距离,不能太大也不能太小,大概在0.1 0.3毫米左右就行。
这个间隙是为了让里面的细型芯在脱模的时候有活动的空间。
2. 脱模动力装置。
为了让螺纹型芯能从产品里退出来,咱们得给它一个动力呀。
这时候可以在模具上安装一个小型的液压或者气动装置。
想象一下,这个装置就像一个小助手,在脱模的时候轻轻地推一下螺纹型芯。
不过这个推力得控制好,不能太猛,不然会把产品给弄坏的。
一般来说,根据产品的大小和材料的特性,这个推力在50 200牛顿之间比较合适。
另外,还可以在螺纹型芯上连接一个旋转机构。
这个旋转机构就像一个小陀螺,在液压或者气动装置推动螺纹型芯往外退的同时,让它慢慢地旋转。
因为内螺纹嘛,要是光直直地往外退,肯定会卡住的,就像你硬要把拧进去的螺丝直接拔出来一样困难。
这个旋转的速度也不能太快,每分钟大概转个5 10圈就差不多了。
3. 导向和限位结构。
在螺纹型芯的周围,要设置一些导向柱。
这些导向柱就像轨道一样,让螺纹型芯在脱模的时候只能按照规定的方向移动。
就像火车只能在铁轨上跑一样。
导向柱的表面要光滑得像溜冰场一样,这样可以减少摩擦,保证螺纹型芯移动得顺畅。
同时呢,还要有限位装置。
这个限位装置就像一个小警察,告诉螺纹型芯你只能移动到这个位置,不能再往前走了。
这样可以防止螺纹型芯过度脱模,把模具或者产品给损坏了。
滴灌带接头螺帽自动旋转脱反螺纹注射模设计

法 ;但 是 对 于 螺 纹 较 深 、树 脂 强 度 高 、螺 纹精 度 要 求 高 的 塑件 ,必 须 采 用 旋 转脱 出 的方 法 。在 旋 转 脱 螺 纹 结 构 中 ,又分 为 手 动脱 出和 自动 脱 出两 种 ,其 中手 动 脱 螺纹 生 产 效 率 低 ,但
所 以对 产 品 尺 寸 及 螺 纹 精 度 要 求 较 高 ,强 行 脱 螺纹 模 具 结 构 无 法 达 到 产 品使 用 要 求 ,必 须 采用 自动 旋 转 脱 螺
纹 模 具结 构 。
模部 分 。然 后 电机 开始 转 动 ,通 过 链 轮 、链 条 带 动 螺纹 型芯 转 动 ,与 此 同 时 , Ⅱ一 Ⅱ分 型面 依 靠 弹 簧 弹 力 、并
需 要 注 意 的 是 , 1一 I面 分 型 时 1 I
分 可靠 。 因螺 纹 型 芯经 常 处于 旋 转 状 态 ,无 法 直 接 冷 却 ,所 以模 具 设 计 时 在 螺 纹 型 芯 中心 部 分 增 加 冷 却 型 芯 ,
通 过铜 管 将 冷 却 水 引入 型芯 ,形成 环
链 轮 的 转 速 应 在 6 r mi 。链 轮 的传 0/ n 动 比为 :i ln = 2z,如 设 定 传 动 =n/ 2 z/ 1
模 具结 构简 单 ,适 应小 批 量 生 产 ; 自
模 具设 计 为 1模 8腔 ,采 用 热 流道 针 阀 式 点浇 口进 料 ,用 减 速 电机 通 过 链 条 传 动 完成 自动 脱 螺 纹 ,模 具 结 构 如
图 2所 示 。
动 脱 螺纹 效 率 高 ,质 量 稳 定 ,适 应 大 批 量 生产 。在 自动旋 转 脱 反 螺 纹 模 具
高效自动脱螺纹及凝料注射模具设计

20 年 1 月 08 1
塑料工业
C I A LA [ S I U r H N P S C D Sr RY ・ 3 3 ・
高效 A动脱螺纹及凝料注射模具设计
周细 枝 ,钱应 平 ,刘秋 菊
( 湖北工业 大学机械 工程 学院 ,湖北 武汉 4 06 ) 308 摘要 :以带 内螺纹 的护手霜瓶盖为例 ,通过分析制 品的结 构和注塑成型工艺 ,采用齿轮齿条机构 ,设 计 了高效 自 动脱 螺纹 和浇注系统凝料的注射模具 。重点在 于精确计算并 校核了齿轮齿条机构 ,实现了开模行程最小 化 ,成 型过程 ’
高效 化 ,可为类似塑件 的注射模具设计提供有价值 的参 考。
关键 词 :瓶盖 ;内螺纹 ;塑料模设计 中图分类号 :T 306 2 Q 2 .6 文献标识码 :A 文章编 号 :10 57 (08 l 0 3 2 05— 70 20 )l 一0 3 —0
D s no jc o ud t tmai a d E e t eR mo igo ei f net nMo l hAuo t n f ci e v f g I i c v n
A s at Tkn adc a o l cpwt t a sr r da a xm l,tes ut di e— b t c: aigahn r m b t a i i e l c w t e s nea p h t c r a jc r e t e hn r e h a n e r u n n e tnm li r es f e r ut e nlzd h jc o ol i uo a cadh he et erm v g i o n po s o o c w r aa e .T ei etnm udwt at t n i f c v e oi o dg c t p d e h y n i h m i g i n
内螺纹螺旋传动脱模的注塑模设计

( co l f l t cl Mehncl A c i cua E g er gJag a nv r t Wu a 3 0 6 C ia Sh o o e r a — c a i & rht tr ni e n ,i h nU i sy h n4 0 5 , hn ) E ci a e l n i n e i,
r od;Botl ap te c
中图分 类号 : G 4 ; Q 2 文 献标 识码 : T 2 1T 3 0 A
1引言
在注塑成 型具有内螺纹的塑料制品时 , 模具 的内螺纹 自动 脱模 机构 包括 瓣合式螺纹型芯结构 、 旋转 脱模机构等。采用瓣 合式结构时 ,塑料 制品上的螺纹一般需设计成 间断形式 ,且成 型后容易出现拼缝溢料痕迹。利用旋转运动时 , 通过使模具 内 的传动零件旋转 ,带动螺纹型芯或制品旋转并使两者分开实现 螺纹 自动脱模 【】 1 。旋转脱模机构的运动方式 包括利用直角式 注塑机的开合模丝杠旋转动作驱动旋转零件 ;卧式 注塑 时通过
o h en l he d ft i ra r . e n t t a Ke o d :I tr a h e d lsi ijcin mo l ;S rw—d ie ;De udn ;S rw y w r s i en ltra ;Pat net ud ce n c o rv n mo lig ce
★来 稿 1期 :0 5—0 3 20 6—2 1
开 模 动 作 ,利 用 模 具 上 的 齿条 齿 轮 或 蜗 轮 蜗 杆 ,经 由齿 轮 传 动
系, 驱动旋转 零件 【 , 】 依靠外 部电动机 、 2 3; 油缸 驱动旋转零件
等 【 ,】 14 。这些脱模结构均会使模具体积增大 , 无法利用标准模 架形式。本文针对某药检用瓶盖 ,设计了利 用卧式 注塑机顶出 动作 ,在推板和大升角传动螺杆之 间实现螺旋传动 ,将直线运 动转化成旋转运动 ,经 由齿轮传动 ,使 螺纹 型芯旋转 的自动脱
香水瓶盖内螺纹自动脱模注塑模设计

崩3镶件冷却系统
模具完成注射成型后,注塑机拉动动模.模具 首先从分型面I处开模,此时拉料杆35拉住流道凝 料脱离定模镶件32,实现流道凝料和塑料件的自动 分离j分型面I的开模距离为10 mm,由限位螺钉 44控制。之后模具再从分型面Ⅱ处打开,脱料板34 将流道凝料强行推离拉料杆35,实现流道凝料自动 脱落。分型面Ⅱ开模距离为120
nism;injection m01d
塑料件的内螺纹由螺纹型芯成型,在脱模过程 中,塑料件不转,螺纹型芯一边转动,一边脱离塑料 件。螺纹型芯转动的动力来源通常有齿条、来复线 螺杆、液压油缸和乌达4种…。其中前2种是将齿 条和来复线螺杆安装于定模上,通过模具的开合和 齿轮传动带动螺纹副芯转动,其结构较为简单,但因 齿条和来复线螺杆的长度受到限制,需采用较大的 齿轮传动比,这样必将加大模具的尺寸:利用“马 达+齿轮”的螺纹脱模机构时传动比不受限制,但 成本较高,结构也复杂。而“液压油缸+齿条”的螺 纹脱模机构则介乎它们之间,既可以采用较小的传 动比,又可以节约成本,且螺纹型芯转动平稳可靠。 笔者利用“液压油缸+齿条+齿轮”内螺纹自 动脱模机构,设计r香水瓶盖内螺纹自动脱模注塑 模。 l塑料件结构分析 塑料件为某名牌香水瓶盖,属于轴套类零件, 材料为尼龙(PA),收缩率取1.6%,详细结构见图 1。塑料件外形结构简单,但内部结构复杂,内圆周 表面除了有一段开19×3的梯形螺纹(螺纹长度
月-月
图2香水瓶盖注塑模具结构图
2.2冷却系统设计 本模具冷却系统由直通式冷却水道和环形冷 却水道组成,见图2中占一B视图和图3。由于动模 镶件28在脱模过程中和螺纹型芯的摩擦面积较大, 发热量较多,所以即使它与熔体的接触面积很小,也 要进行重点冷却。
2.3脱模系统设计
螺纹塑件的注射模设计

一
图 1 塑件 A
1 9 2 O 2 2 2 1 2 3 2 4
图 3 模 具 结 构 图 1 . 圈 定位
套筒
2浇 口套 .
3定模 型 芯 .
4定模 座 板 .
9 料杆 . 拉
5动 模 型芯 .
6 .
7导 套 .
8带 齿 轮 的 螺纹 型芯 .
1. 针 固定板 O 顶
tra , lb rtdmo eink yp it a dw ri rcs i d ti tru huigeet n hed e oae l d s e ons n ok gpoes n ea .ho g s jc o a d g n l n i
me ha s wi p i n e r r al n a c d mo d Ss r ie lf n eibiiy c nim t s lne a d g a ,g e ty e h n e l e v c i a d r la lt . h e
1. 针 底 板 1. 定 板 1 . 接 螺 纹 1. 1 顶 2固 3联 4动模 座板 1. 5螺纹 套 1. 6回程 杆 1 . 齿 轮 1. 轮 轴 1 . 锥 滚 子轴 承 7大 8齿 9圆
图 2 塑件 B
2 O
齿条
2 . 连接 块 1 T型
2 . 程 开 关挡 块 2行
2 . 磨块 3耐
2 . 缸 4油
・
3 6・
《 具制 ̄ 2 0 第 9期 模 0 8年
维普资讯
耐
① 斯I020’ 模90 耐 6模9#02手 g72机 飞:-8 i 90/#724  ̄ 合 77 N670 :- 2 : 帮 斯 7 好 2
E —ma ln c i ie@ n c ma hn . e : ie c ien t
螺纹塑件的注射模设计

萌商 册
/
] 塑料模 具 设 计 手册 编 写组
,
,
塑
料模 具 设 计 手 册 [ M ]
出版 社
。
北 京机 械 工 业
2002
05
— —
lF 齿 轮【
\
2
,
z
=
12
/
塑
—
_\
Io嫂暌嘲
燕
“
厂
j
齿黼
一
—
i
坐
|
生
,
★
作者简介
,
,。
何 文
工
男
,
,
湖 南郴 州人
,
,
19 6 9
年
\ 渤 ∥
、
‘
/
/
一
t: =
最 后 用 顶针和拉
料 杆 把 塑 件 和 浇 注 系统 的 冷 凝 料从 动 模
▲ 图4 芯 中顶 出
,
这样就完成了
一
个注 射周
期
布 局方式
,
。
侧 向浇
口
进料
,
螺纹型芯 的
、
脱模机 构 采 用 油 缸 带 动 齿 条 的脱 模 机 构
用龙记模架
,
齿轮运动
。
顶 出行 程 为 2 0 m
m
模架采
结束语
,
模具 所有 活动部 分保证 定
,
位准确
,
动作可 靠
不 得 有卡 滞 现 象
。
,
本文介绍 了2 件4 腔 模的设 计过程
。
固定 零 件 紧 固 无 松 动
其 模具 工 作过 程
重 点介 绍 了螺 纹 型 芯 脱模 机 构 的结 构特
典型自动脱螺纹注射模设计

2 . 纹 型芯 0螺
2 . 喷嘴 9热
2. 腔板 1型
3. 导柱 0斜
2 . 板 2. 块 2垫 3垫
3. 夫块 3. 位圈 1哈 2定
2 . 模板 4定
2. 位 圈 5定
2 . 浇道 6主
2. 流板 7分
3 . 次 推板 3二
3. 钉 4销
3. 钉 5螺
3 . 紧 轮 6张
维普资讯
1 - .
2 8
型一 腔一 ) .
模一
《 具 制 造 》 2 0 . o8总第 1 模 0 2N . 3期
血 型 技一自 术一
, 、
、
动 脱 螺 纹 注 射 模 设 计
400 ) 5 0 2 姚 起 剑 应 进
3 1 模 具 工 作 过 程 .
2 9
根据 塑件分析及用 户生产要求 , 具设计 为 1 8 模 模 腔 , 用 热 流 道 针 阀式 点 浇 口进 料 , 减 速 电 机 通 过链 采 用 条 传 动 完 成 自动脱 螺 纹 , 具 结 构 如 图 2所 示 。 模
目 目
I I
1 链轮 . 小
2链 条 .
3电 机 .
4电机 支 架 .
5限 位 螺 钉 .
6弹 簧 .
7顶 杆 .
8水 孔 .
9铜 管 1 . 封 圈 . 0密
I. 却 型 芯 1 . 模 板 1 . 板 1. 脚 1 . 链 轮 1. 推 轴 承 1 . 板 1. 次 推 板 冷 1 2动 3垫 4支 5大 6止 7垫 8一 1. 转 圈 9止
达 到 实用 要 求 。现 将 该 模 具 结 构 介 绍 给 大 家 , 同行 参 供
注射模脱螺纹机构类型分析

1 引言
低 。大批量生产时就需要 自动脱螺纹模具 。 自动脱
共有 3 种类型 : ①马 在 瓶盖行业 中, 有很 多瓶盖塑件 都有螺纹 , 而螺 螺纹机构按照动力传动方式来分 , ② 螺纹传动 ; ③齿轮齿条传动 。本文将着重 纹 的脱模方法有两种 : 一种是在材料允许 的情况下 , 达传动 ; 种螺纹旋脱机构的模具结构特点 。 利用材料 的弹性 变形通 过卸料板将 塑件强行从 型芯 介绍以上 3 . 2 旋脱 类模具 结构 上顶 出, 称为强制脱模法 , 简称强脱 ; 另一类是对螺纹 3
. 2 . 1 马达 式 较深 , 材料强度较高 、 螺纹精度要求高的塑件 , 必须采 3
用旋转脱模 的方法 , 简称旋脱 , 这种方 法需要 利用齿
马达有电机和液压马达 。电动机 由于转速过快 ,
较少采用 ; 液压马达由于转速相对较慢 , 轮、 齿条 、 丝杠等 , 把开模时动模的直线运动或电机的 动作不平稳 , 动作平稳 , 安全可靠 , 因此被广泛采用 。使用马达传 转动等动力来源转变成螺纹型芯的转动。
必须 有另外 两个与之互相 结合 的附件 , 即链轮 和链
条 。马 达 、 链轮 、 链条 3 个 最 重 要 的部 件 缺 一 不 可 , 方
可实现 马达传动。
l 处 放 大
能采用螺纹强脱 , 只能采用螺纹旋脱 , 如图 1 所示。
3 模 具 结构 分 析 3 . 1 强脱 类模具 结构
了 自动 脱 螺纹 机构 在模 具设 计 中的应 用 。
关 键词 : 瓶盖; 螺 纹;自动 脱 螺纹机 构
中图分 类 号 : T Q 3 2 0 . 6 6
文 献标 识码 : B
An a l y s i s o f T h r e a d De - Mo l d i n g Me c h a n i s m f o r t h e I n j e c t i o n Mo l d
《注射模设计》
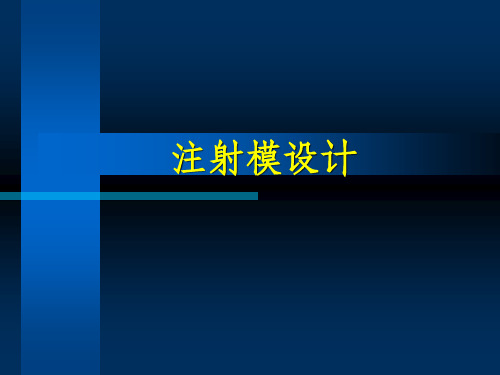
.
39
(二)型腔的布置
1.平衡式浇注系统
分流道到浇口及型腔,其形状、长宽尺寸、圆角、模 壁的冷却条件都完全相同,熔体能以相同的成型压 力和温度同时充满所用型腔。
缺点:流道 总长度要长 些,热量压 力损失大, 模板尺寸大。
.
40
(二)型腔的布置
2.非平衡式浇注系统 由于主流道到各型腔的分流道长度各不相同或 者各型腔形状尺寸不同而使得浇注系统不平衡。
.
16
一、分型面设计 (一)分型面的形式
分型面:是模具上开模时用于取出塑件和(或)浇 注系统冷凝料的可分离的接触表面。
分型面的分类:
1.按其位置与注射机开模运动方向的关系来分类:
垂直于注射机开模运动方向,平行于开模方向,倾 斜于开模方向
2.按分型面的形状来分类 :平面分型面,曲面分型面, 阶梯分型面和斜面分型面
定范围,也不意味浇口浇口越小越好。
.
46
(一)浇注系统流变学
(2)合理的选择剪切速率
在较低的剪切速率范围内,由于剪切速率的微 小变化会引起粘度的巨大变化。这将使注射成型难 以控制,使塑件出现表面不良、充模不匀、密度不 均、内应力高、翘曲以及收缩不均等毛病。所以,
要在ηa ~γ́ 曲线上选取这么一段剪切速率,使它
.
20
(二)选择分型面的原则
使塑件开模时留在动模侧:
.
21
(二)选择分型面的原则
简化模具制造:
.
22
(二)选择分型面的原则
有利于抽芯(活动型芯置于动模):
.
23
(二)选择分型面的原则
有利于抽芯(缩短抽芯距离):
.
24
(二)选择分型面的原则
螺纹脱模
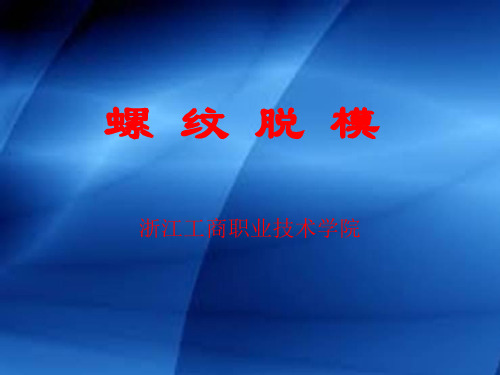
螺纹脱模方式
3) 机动脱螺纹,这是利用开模时的直线运动, 机动脱螺纹,这是利用开模时的直线运动, 通过齿条齿轮或丝杠的传动, 通过齿条齿轮或丝杠的传动, 带动螺纹型芯作旋 转运动而使螺纹脱模。这种模具结构较复杂, 转运动而使螺纹脱模。这种模具结构较复杂,但 省力、效率咼、质量好。 省力、效率咼、质量好。 4) 瓣合模脱螺纹,这是采用瓣合型芯或瓣合型 瓣合模脱螺纹, 环来脱螺纹。这种脱模方式, 制造简单, 环来脱螺纹。这种脱模方式, 制造简单,但在螺 纹部分有分型线,且容易产生飞边,清除较难, 纹部分有分型线,且容易产生飞边,清除较难, 螺纹精度不高。 螺纹精度不高。
带螺纹塑件的脱模强制脱螺纹带螺纹塑件的脱模内侧抽脱螺纹带螺纹塑件的脱模螺纹止动带螺纹塑件的脱模模内旋转脱螺纹带螺纹塑件的脱模模内旋转脱螺纹自动卸螺纹注射模成型带有内螺纹或外螺纹的塑件为了能自动卸螺纹在模具内设有能转动的螺纹型芯或螺纹型环
螺 纹 脱 模
浙江工商职业技术学院
塑件螺纹
很多塑件上带有螺纹, 很多塑件上带有螺纹,螺紋的种类主 要有两大类:内螺纹和外螺纹。 要有两大类:内螺纹和外螺纹。螺纹表面 均带沟槽, 均带沟槽,因此脱模的方式与一般塑件不 它需要有特殊的脱模机构。 同。它需要有特殊的脱模机构。
带螺纹塑件的脱模
强制脱螺纹
带螺纹塑件的脱模 内侧抽脱螺纹
带螺纹塑件的脱模 螺纹止动
带螺纹塑件的脱模
模内旋转脱螺纹
自动卸螺纹注射模
成型带有内螺纹或外 螺纹的塑件, 螺纹的塑件,为了能 自动卸螺纹在模具内 设有能转动的螺纹型 芯或螺纹型环。 芯或螺纹型环。
设计螺纹脱模机构的注意点
设计带螺纹塑件的脱模机构应注意的问题
1) 对塑件的要求:由于螺纹表面有沟槽,所以,内螺纹必须 对塑件的要求:由于螺纹表面有沟槽,所以, 由螺纹型芯, 外螺纹必须由螺纹型环成型,而脱模时必 由螺纹型芯, 外螺纹必须由螺纹型环成型, 须从螺纹型芯或螺纹型环上脱出, 须从螺纹型芯或螺纹型环上脱出,两者之间必须作相对转 因此,塑件的外形或端面须有防止转动的花纹或图案, 动,因此,塑件的外形或端面须有防止转动的花纹或图案, 否则难以脱出。 否则难以脱出。 2) 对模具的要求:塑件不能转动,模具应有相应的防转措施 对模具的要求:塑件不能转动, 给予保证。当塑件型腔和螺纹型芯同在动模上时, 给予保证。当塑件型腔和螺纹型芯同在动模上时,型腔可 以保证不使塑件转动。但当型芯和型腔分别处在动、 以保证不使塑件转动。但当型芯和型腔分别处在动、定模 上时,开模后,塑件就离开定模型腔,此时, 上时,开模后,塑件就离开定模型腔,此时,即使塑件外 形有防转花纹也不起作用, 形有防转花纹也不起作用,塑件会留在动模型芯上和它一 起转动而无法脱模,因此在模具上要另设止转机构。 起转动而无法脱模,因此在模具上要另设止转机构。
液压马达自动脱螺纹注塑模设计
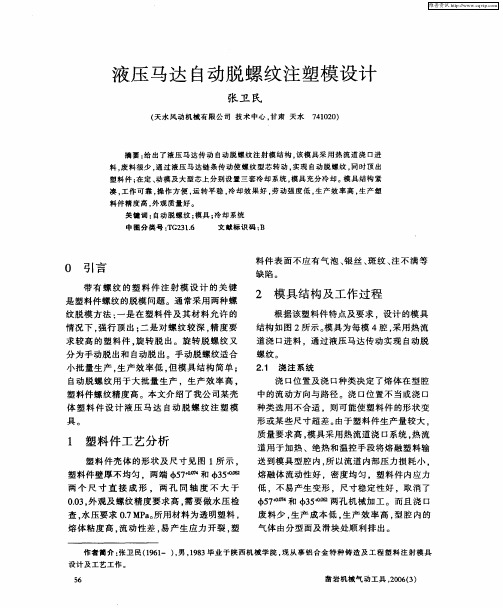
质量 要求 高 , 具 采用 热 流道 浇 口系统 , 流 模 热
道用 于加 热 、绝 热 和温控 手 段将 熔融 塑 料输 送 到模具 型腔 内 , 以流 道 内部 压力损 耗 小 , 所
熔 融体 流 动性 好 ,密度 均匀 ,塑料 件 内应 力
低 ,不 易 产生 变形 ,尺寸稳 定 性好 ,取 消 了 5 椰M和 3 艘 两 孔机 械 加 工 。而且 浇 口 7 5
废 料少 , 生产 成本 低 , 生产 效率 高 , 腔 内 的 型
气体 由分型 面及 滑块 处顺 利 排 出 。
作 者 简 介 : 卫 民 (9 1 ) 男 ,9 3 业 于 陕 西 机 械 学 院 。 从 事 铝 合 金 特 种 铸 造 及 工 程 塑 料 注 射 模 具 张 16 一 , 18 毕 现
维普资讯
液 压 马达 自动 脱 螺 纹 注 塑模 设 计
张 卫 民
( 水 风 动 机 械 有 限 公 司 技 术 中心 。 肃 天 水 天 甘 7 12 ) 4 0 0
摘 要 : 出 了液 压 马 达传 动 自动 脱 螺 纹 注 射 模 结 构 , 模 具 采 用 热 流 道 浇 口进 给 该 料 . 料很 少 。 过 液 压 马 达 链 条 传 动使 螺纹 型 芯 转 动 , 废 通 实现 自动 脱 螺 纹 , 时 顶 出 同
3 模 具 设 计 细 节
() 1 利用 塑料 件本 身 的结 构特 点 , 塑料 件
A—A
在 型腔 中不转 动 , 纹型 芯转 动 。 自动脱 螺 螺 在
纹 过程 中同时顶 出塑料 件 。一个 机构 多 用 。
I
() 2 由于壳 体生 产量 大 , 自动脱 螺纹需 旋 转 运动 , 以用 铜衬 套 , 所 螺纹 芯材 料 选用 耐磨 性 和淬 透 性好 的瑞 典 7 8 C 2 V) 1 ( rMo 。热 处 理 硬度 HR 5 ~ 5 C 0 5 。转 动 部分 采 用 圆锥 轴 承 以 减少 摩擦 阻力 ,同时 各转 动部 分 用润 滑脂 润
注射模的应用实例
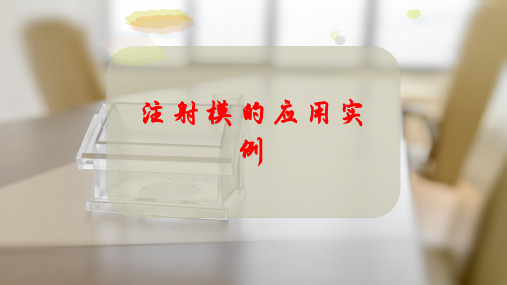
注射模的应用实例
1.1板凳注射模
如图1-155所示为聚碳酸酯板凳塑件及其注射模。鉴于塑料制件的形状特点,设计时采用推件板加推杆二级推出来 达到塑料制件的脱模目的。注射成型后,首先定模板1与推件板2分型,然后采用注射机的顶杆和液压缸分别推动接 块3、推件板2和推杆6顶出塑件,当推件板停止运动后,推杆继续推动,使塑件全部离开型芯4下直至推出模外。 弹簧5装置是为了使推杆能迅速复位。模具冷却采用冷却水道和模板曲字型通水办法,效率较高。
注射模的应用实例
1.2肥皂盒注射模
如图1-156所示为聚氯乙烯肥皂盒塑件及其注 射模。该模具采用摆钩式二级推出机构,推出 系统中的摆钩装置对称分布在模具的两侧。开 模后,推出系统在注射机顶杆的作用下,推板 12和推杆固定板11在摆钩18和销20连接状态 下同时向上移动。与此同时,推杆14推动推件 板15使塑件离开型芯3一定距离,完成第一次 推出。推板12和推杆固定板11继续向上移动, 撑板17使摆钩18左右分开,离开销子,推板 不再移动。此时推出系统的推杆10再移动一定 距离,将塑件推出,完成第二次推出。浇口尺 寸的宽度为4 mm,深0 22 mm。模具加工 时导向系统和推出系统的孔,要同时钻铰,以 保证同轴度。
注射模的应用实例
1.7斜三通注射模
如图1-161所示为硬聚氯乙烯斜三通塑件及其注射模。该模具为斜导柱分型抽芯机构。因塑件形状为从三个方向相 互贯穿的通孔,故需设计三组斜导柱抽芯结构。 为了满足塑件需较大的抽拔距离的要求,并确保滑动的1#型芯4、3#型芯13能符合常规要求,除了2#型芯8以外, 1#、3#型芯均设在加长了的导滑套1之中,使型芯移动200 mm后仍处在导滑套内。这不仅大大减少了模具的尺寸, 而且利用导滑套将模块锁紧,防止了型芯在注射充模压力下产生后退。
饮水瓶瓶盖内螺纹注射模设计

饮水瓶瓶盖内螺纹注射模设计古远明(河源职业技术学院,广东河源517000)【摘要】针对复杂结构的内螺纹瓶盖注射模设计,通过分析饮水瓶瓶盖的结构特点,使用MoldFlow模流分析,设计了圆形分流道截面形状及潜伏浇口,采用侧抽芯机构解决了瓶盖顶处内凹的脱模难题,采用旋转脱螺纹机构为电动机带动链条驱动齿轮使内螺纹自动脱模,解决了饮水瓶瓶盖自动脱模的难题,实现批量自动生产,提高了生产效率。
关键词:饮水瓶瓶盖;侧抽芯机构;内螺纹;注射模中图分类号:TQ320.66文献标识码:BDOI:10.12147/ki.1671-3508.2023.04.010Design of Injection Mold for theInner Thread of the Water Bottle CapGu Yuanming(Heyuan Technical College,Heyuan,Guangdong517000,CHN)【Abstract】According to the design of injection mold for the inner screw cap with complex structure,through analyzing the structural characteristics of the cap of drinking water bottle,the shape of circular sprue section and the latent gate were designed by MoldFlow mold flow analysis,the side core-pulling mechanism is used to solve the problem of demoulding the concave inside the top of the bottle cap,and the rotating demoulding mechanism is used to drive the chain drive gear for the motor to make the internal thread demoulding automatically,which solves the problem of automatic demoulding of the bottle cap of drinking water bottle,realize batch automatic production,improve production efficiency.Key words:water bottle cap;side core-pulling mechanism;internal thread;injection mold1瓶盖塑件结构工艺性分析饮水瓶瓶盖如图1所示,塑件材料为ABS热塑型高分子结构材料、缩水率为0.5%,塑件最大外形轮廓尺寸为ϕ59.52×30.87mm,拔模角度为1°,最小壁厚为0.96mm,塑件表面有一个ϕ10.2mm与ϕ9.18mm的阶梯孔,顶面ϕ5.1mm处为圆环凹槽需设计侧抽芯机构,内孔有M50×2.5×9.44Lmm的内螺纹需设计旋转脱螺纹机构,旋转脱螺纹机构生产效率高,能够实现批量自动化生产。
注射模伺服同步自动脱螺纹机构设计

( e at n fMe h nc la d E e tc lE g e r g h n e P ltc nc F s a . D pr me to c a ia n lcf a n i ei ,S u d oye h i, o h n i n n Gu n d n 2 30 hn ) ag o 5 8 0 。C ia g
而不能回转,故难以做出合格产品,在生产中也因
收稿日期 :08 0 —1。 20 - 7 5 作者简介: 畅国帏 (96 , 甘肃白银人, 16 一) 男, 副教授, 主要从事 塑料成型工艺、 模具设计和制造的教学, 地址: 广东省佛山市顺 德职业技术学院机电系。 电话)30 ̄ i ( ( 106 , 电子信箱)hr ca  ̄
K y w rs n c o o l;atm t hed s i i ;sro cnrl L (rga m b o i e od :iet n m ud uo a c t a tp n e v o t ;P C porm a l l c ji i r rp g o e g
c nr l r :sn ho i t n o t l ) Y c nz i oe r ao
( 模具工业>20 年 第3 卷第 1 期 08 4 1
4 5
注 射 模 伺 服 同 步 自动 脱 螺 纹 机 构 设 计
畅 国帏 ,许 中明, 胡作健 ( 德职业技术学院 机 电系, J 顷 广东 佛 山 580 ) 230
脱螺纹模具设计讲义(重点)

自动卸螺纹模具设计初级教程BY WELLDESIGN17.Nov,04前言:塑胶产品螺纹分外螺纹和内螺纹两种,精度不高的外螺纹一般用哈夫块成型,而内螺纹则大多需要卸螺纹装置。
今天简单介绍内螺纹脱模方法,重点介绍齿轮的计算和选择。
一、卸螺纹装置分类1、按动作方式分①螺纹型芯转动,推板推动产品脱离;②螺纹型芯转动同时后退,产品自然脱离。
2、按驱动方式分①油缸+齿条②油马达/电机+链条③齿条+锥度齿轮④来福线螺母二、设计步骤1、必须掌握产品的以下数据(见下图)①“D”——螺纹外径②“P”——螺纹牙距③“L”——螺纹牙长④螺纹规格/方向/头数⑤型腔数量2、确定螺纹型芯转动圈数U=L/P + UsU 螺纹型芯转动圈数Us 安全系数,为保证完全旋出螺纹所加余量,一般取0.25~1 3、确定齿轮模数、齿数和传动比模数决定齿轮的齿厚,齿数决定齿轮的外径,传动比决定啮合齿轮的转速。
在此之前有必要讲一下齿轮的参数和啮合条件。
三、齿轮的参数和啮合条件模具的卸螺纹机构中大多应用的是直齿圆柱齿轮,而且一般都是渐开线直齿圆柱齿轮,因此下面就以渐开线直齿圆柱齿轮为研究对象。
1、齿轮传动的基本要求①要求瞬时传动比恒定不变②要求有足够的承载能力和较长的使用寿命2、直齿圆柱齿轮啮合基本定律两齿轮廓不论在何处接触,过接触点所作的两啮合齿轮的公法线,必须与两轮连心线相交于一点“C”,这样才能保证齿轮的瞬时传动比不变。
将所有“C”点连起来就成了2个外切圆,称之为分度圆,分度圆圆心距即齿轮圆心距。
详见下图3、渐开线直齿圆柱齿轮参数分度圆直径------“d”表示分度圆周长--------“S”表示齿轮齿距--------“p”表示齿轮齿厚--------“sk”表示齿轮齿槽宽--------“ek”表示齿轮齿数--------“z”表示齿轮模数--------“m”表示齿轮压力角--------“ɑ”表示齿轮传动比--------“i”表示齿轮中心距--------“l”表示4、计算公式如下:①齿距 = 齿厚 + 齿槽宽即:p = sk + ek②模数的由来因为S = Z x P = πx dd = P / πx Zπ是无理数,为计算方便,将P / π规定为常数,即模数,用m 表示,故有公式如下:d = m x z即:分度圆直径等于模数乘以齿数。
牙膏盖内螺纹螺旋脱模机构的设计

内螺纹 自动 脱 模 机 构 包 括瓣 合 式 螺 纹 型 芯 结 构、旋转脱模机构等。采用瓣合式结构 ,塑件上 的螺纹一般需设计成间断形式 , 且成型后容易 出现拼缝溢料痕迹 。常规 的旋转脱 模机构 的运 动方式包括利用直角式 注塑机的 开合模丝 杠旋 转动作驱动旋转零件 ; 卧式注塑时通过开模动 作 ,利用模具上的齿轮齿条或蜗轮蜗杆 ,经由齿 轮传动系 ,驱动旋转零件 , 或依靠外部电动机 、 液压缸驱动旋转零件 等 。但这些脱 模机构 均会 使模具体积增大 ,导致无法利用标准模架。针对 牙膏盖这类塑件 ,文献[122]提出利用卧式注塑机 顶出动作 ,在推板和大升角传动螺杆之间实现螺 旋传动 ,将直线运动转化成旋转运动 ,经由推板 传动 ,使螺纹型芯旋转 ,实现塑件自动脱出。
0 引言
图 1 所示牙膏盖 ,外圆周表面有防滑竖纹 , 内孔带有长度 7 mm 的 M14 mm 内螺纹 ( 右 旋) ,两薄壁之间有厚度 2 mm 、高度 6 mm 的加 强筋 。
图 1 牙膏盖
在注塑成型具有内螺纹的塑件时 , 模具的 收稿日期 : 200 9 207 203 作者简介 : 田仲可 (1970 - ) ,男 ,副教授 。
m oti o n w as ch an g ed t o ro t at ar y m o ti o n , an d t he sc rew co re was aut o m at icall y de mo ld ed
f r om t he i nt er n al t h rea d vi a t he gea r s yst e m . Co mp a re d wit h ge ar2ra ck an d wo rm2g ea r de2 mol d in g m ech a nis ms , t he p r op os e d mec h an is m was co mp act i n s t ru ct u re , reli ab le i n op era2
- 1、下载文档前请自行甄别文档内容的完整性,平台不提供额外的编辑、内容补充、找答案等附加服务。
- 2、"仅部分预览"的文档,不可在线预览部分如存在完整性等问题,可反馈申请退款(可完整预览的文档不适用该条件!)。
- 3、如文档侵犯您的权益,请联系客服反馈,我们会尽快为您处理(人工客服工作时间:9:00-18:30)。
1、引言
塑料制件中,很多工业产品及民用产品均存在内外螺纹的设计,解决塑件螺纹脱模问题是此类模具设计的关键。
一般来讲,处理塑件螺纹问题有2类方法:一类是在塑件及树脂允许的情况下,采用强行脱出的方法;一类是螺纹较深、树脂强度高、螺纹精度要求高的塑件,必须采用旋转脱出的方法。
在旋转脱螺纹结构中又分为手动脱出和自动脱出2种,手动脱螺纹生产效率低,但模具结构简单,适应小批量生产;自动脱螺纹效率高,质量稳定,适应大批量生产。
在自动旋转脱螺纹模具结构中,必须解决结构设计的可靠性、稳定性及实用性等问题。
下面所述的链条传动自动脱螺纹模具结构,经长期使用,模具结构稳定、可靠,生产效率高,产品达到实用要求。
现将此模具结构介绍如下。
2、塑件分析
图1所示产品为润滑油壶瓶盖,材料为PP,产品特点是采用矩形螺纹,有防伪圈和止转槽设计,产品外观要求较高,且需求量大。
另外,瓶盖是由自动灌装线机器旋盖,所以对产品尺寸及螺纹精度要求较高,强行脱螺纹模具结构无法达到产品使用要求,必须采用自动旋转脱螺纹模具结构。
3、模具结构及工作过程
根据塑件分析及用户生产要求,模具设计为1模8腔,采用热流道针阀式点浇口进料,用减速电机通过链条传动完成自动脱螺纹,模具结构如图2所示。
图2模具结构
1.小链轮
2.链条
3.电机
4.电机支架
5.限位螺钉
6.弹簧
7.顶杆
8.水孔
9.钢管10.密封圈11.冷却型芯12.动模板13.垫板14.垫块15.大链轮16.止推轴承17.垫板18.一次推板19.止转圈20.螺纹型芯21.型腔板22.垫板23.垫块24.定模板25.定位圈26.主流道27.分流板28.隔热垫29.热喷嘴30.斜导柱31.哈夫块32.定位圈33.
二次推板34.销钉35.螺钉36.张紧轮
3.1模具工作过程
模具首先从Ⅰ—Ⅰ面分型,同时靠斜导柱拉开哈夫块,完成塑件防伪圈外凹部分的脱出,并使塑件留在动模部分。
然后电机开始转动,通过链轮、链条带动螺纹型芯转动,与此同时,Ⅱ—Ⅱ分型面依靠弹簧弹力开始分型,并依靠止转圈起防止塑件与螺纹型芯共同旋转的作用。
当螺纹完全脱出后,注射机顶出机构运动,通过顶杆顶动二次推板,使模具从Ⅲ—Ⅲ面分型,完成塑件防伪圈内凹部分的脱模,使塑件从模具中脱出,完成一个生产周期。
需要注意的是,Ⅱ—Ⅱ面分型时弹簧的压力应适中,压力过大易造成螺纹最后一扣破坏,压力过小则分型面不易打开,可以通过提高运动件的制造精度,调整弹簧压缩量来进行调节。
3.2浇注系统设计
由于塑件生产量较大,且质量要求高,设计时采用了热流道针阀式点浇口浇注系统。
因热流道是借助于加热、绝热和温控手段将熔融塑料输送至模具型腔内,所以流道内部压力损耗小,熔体流动性好,密度均匀,塑件内应力降低,变形程度大为减弱,尺寸稳定性则显著提高。
另外,热流道无流道废料,大大降低了生产成本,针阀式喷嘴自动切断浇口,提高了生产效率。
综上所述,对于大批量生产的塑料制品,热流道的选用是非常合理的选择。
3.3模具的冷却
为提高生产效率,防止塑件变形,并防止模具零件因热胀原因引起的咬死现象,模具的冷却系统必须充分可靠。
因螺纹型芯经常处于旋转状态,无法直接冷却,所以模具设计时在螺纹型芯中心部分增加冷却型芯,
通过铜管将冷却水引入型芯,形成环流,较好地完成了螺纹型芯的冷却。
定模型腔的冷却,采用8处直通水路,外部用软管连接形成循环,进行定模冷却。
3.4模具材料选择
由于瓶盖模具生产量大,脱模需旋转运动,模具对抛光没有特殊要求,所以模具材料应选用高耐磨性、淬透性材料。
据此,模具设计时对于关键零件选用了ASSAB公司的CALMAX635材料,热处理硬度56~60HRC,通过使用,效果较为满意。
4、模具传动部分设计
因链条传动运动中没有滑动,传动尺寸比较紧凑,不需要很大的张紧力,作用在轴上的载荷较小,效率较高,比较适合模具中传动的要求,而且市场上链条、链轮、电机采购方便,不需要专门加工,所以在传动设计中采用了链条传动。
4.1模具型腔中心距及链轮参数的确定
考虑模具型腔尺寸及结构设计尺寸的综合因素,型腔之间的中心距应在150mm之间较为合理。
通过对链轮的校核,设计时采用了链节距p=15.875,齿数z1=23的链轮,链轮的节圆直径D为:D=P/sin(180°/23)=15.875/sin(180°/23)≈117mm,可以满足模具设计中心距150mm的要求。
为增加链轮的啮合齿数,使传动更加平稳,设计时增加了两处张紧轮36,使用效果良好。
4.2电机转速及轴承的选择
因塑件旋转5圈即可将螺纹脱出,为保证模具的正常使用寿命,螺纹型芯的转速不宜太快,所以设计时按每5s完成一次旋转脱模计算,大链轮的转速应在60r/min。
链轮的传动比为:i=n1/n2=z2/z1,如设定传动比i≈0.5,则小链轮z2≈11,n2≈120r/min,所以选用减速电机的转速应在120r/min左右。
由于此模具使用的轴承既要起到定心的作用,又要承受注射压力对螺纹型芯的轴向推动作用力,所以轴承选用时必须同时承受径向载荷和轴向载荷,因向心推力滚子轴承可以同时满足上述条件,故设计时选用了此类轴承。
5、结束语
在众多脱螺纹模具结构中,通过比较,此种设计结构紧凑,运转平稳,传动、冷却等方面都达到较好的设计效果,是一种值得推广的、较好的典型自动脱螺纹模具结构。