翘曲变形原因
产品翘曲变形的原因
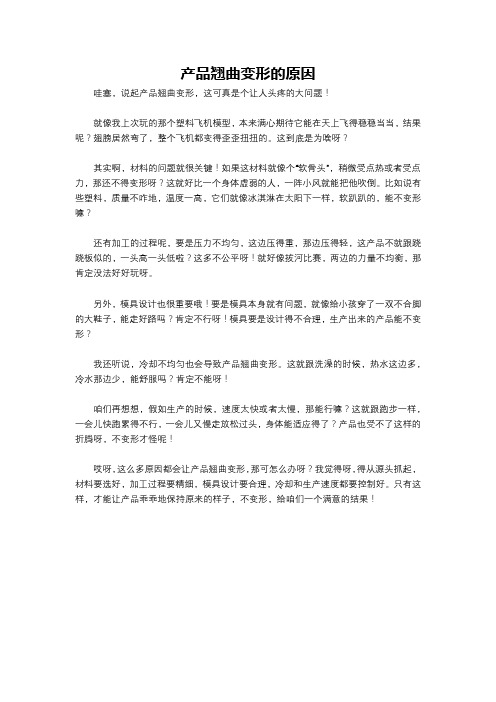
产品翘曲变形的原因
哇塞,说起产品翘曲变形,这可真是个让人头疼的大问题!
就像我上次玩的那个塑料飞机模型,本来满心期待它能在天上飞得稳稳当当,结果呢?翅膀居然弯了,整个飞机都变得歪歪扭扭的。
这到底是为啥呀?
其实啊,材料的问题就很关键!如果这材料就像个“软骨头”,稍微受点热或者受点力,那还不得变形呀?这就好比一个身体虚弱的人,一阵小风就能把他吹倒。
比如说有些塑料,质量不咋地,温度一高,它们就像冰淇淋在太阳下一样,软趴趴的,能不变形嘛?
还有加工的过程呢,要是压力不均匀,这边压得重,那边压得轻,这产品不就跟跷跷板似的,一头高一头低啦?这多不公平呀!就好像拔河比赛,两边的力量不均衡,那肯定没法好好玩呀。
另外,模具设计也很重要哦!要是模具本身就有问题,就像给小孩穿了一双不合脚的大鞋子,能走好路吗?肯定不行呀!模具要是设计得不合理,生产出来的产品能不变形?
我还听说,冷却不均匀也会导致产品翘曲变形。
这就跟洗澡的时候,热水这边多,冷水那边少,能舒服吗?肯定不能呀!
咱们再想想,假如生产的时候,速度太快或者太慢,那能行嘛?这就跟跑步一样,一会儿快跑累得不行,一会儿又慢走放松过头,身体能适应得了?产品也受不了这样的折腾呀,不变形才怪呢!
哎呀,这么多原因都会让产品翘曲变形,那可怎么办呀?我觉得呀,得从源头抓起,材料要选好,加工过程要精细,模具设计要合理,冷却和生产速度都要控制好。
只有这样,才能让产品乖乖地保持原来的样子,不变形,给咱们一个满意的结果!。
木皮翘曲变形的原理是啥

木皮翘曲变形的原理是啥
木皮翘曲变形是由于木材在吸湿膨胀和干燥收缩的过程中导致的。
它的原理可以分为以下几个方面:
1. 吸湿膨胀:木材具有吸湿性,当环境湿度增加时,木材会吸收环境中的水分,导致木材内部的纤维膨胀,木皮因受限于木材的内部结构而无法自由膨胀,于是只能顺着纤维方向挤压变形,造成木皮的翘曲。
2. 干燥收缩:相反地,当环境湿度减小时,木材会释放水分,导致木材内部纤维收缩,这种收缩力量会影响木材表面的木皮,使其翘曲。
3. 组织应力:由于木材的结构和纤维方向不同,不同部分的木材吸湿膨胀和干燥收缩程度也会有所不同,导致不同的应力分布。
如在木材的一侧吸湿膨胀较多,而另一侧膨胀较少或几乎没有,会导致木材内部产生组织应力,使木材翘曲。
总结起来,木皮翘曲变形的原理是由于木材在吸湿膨胀和干燥收缩的过程中,受限于内部结构和纤维方向的约束,木皮不能自由膨胀和收缩,导致木皮翘曲变形。
塑胶件翘曲变形,预防和解决的结构化思路

塑胶件翘曲变形,预防和解决的结构化思路我们设计塑胶件时,不可避免的会碰到翘曲变形缺陷。
那么,如何去解决翘曲变形呢?首先,我们必须去明白翘曲变形的机理,即塑胶件为什么会发生翘曲变形。
在了解机理的基础之后,我们可以从塑胶材料、塑胶件设计、模具结构和成型工艺等四个方面入手,从而系统化、结构化和逻辑化的解决。
当然,面对塑胶件翘曲变形,预防比解决更重要。
我们必须在翘曲变形实际发生之前,就通过上述四个方面行优化。
而不是等到翘曲变形真正发生了,再去解决;这个时候,解决起来就非常麻烦。
—1—翘曲变形随处可见塑胶件翘曲变形,是在塑胶件最容易发生的缺陷之一,在任何产品上都有可能会发生;同时,也是最难以解决的缺陷之一。
▲塑胶件翘曲变形--千姿百态严重的翘曲变形会影响产品的装配,甚至会影响产品的功能、性能和可靠性。
▲翘曲造成外观间隙不一致,严重影响产品美观▲翘曲造成洗衣机抓手与玻璃盖板粘接不牢固▲翘曲影响装配质量,降低产品强度及性能,具有潜在失效风险▲滚筒洗衣机前桶产品头部翘曲变形导致密封圈和不锈钢内桶间隙太小,密封圈和塑胶件发生翘曲变形的根本原因就是在于塑料的收缩不均匀。
▲CAE软件中模拟收缩不均匀如果塑胶件在注塑成型过程中在各个方向都均匀收缩,那么塑胶件尺寸会同时变小,但是会保持正确的形状,不会发生翘曲变形。
然而,如果在任意一个方向上的收缩与其它方向不一致,这就会导致内应力,当内应力超过塑胶件本身的强度时,塑胶件就会在顶出后发生翘曲变形。
▲左侧为收缩不均匀导致的内应力右侧为强度3.2 什么是收缩在了解收缩不均匀之前,我们需要了解塑胶材料的收缩。
为此,需要从塑胶材料分子结构入手来,看看塑胶材料在熔化和冷却过程中的发生的各种变化。
对于大多数的塑胶材料来说,熔化和冷却过程中的特性依赖于塑胶材料的类型以及是否添加了填充剂或玻纤。
1. 无定形塑料无定形塑料是指分子相互排列不呈晶体结构而呈无序状态的塑料。
常见的无定型塑料包括ABS、PC、PMMA和PPO等。
翘曲变形

变形的调试心得1、首先是温度问题,按照我们常规理解的,变形会往温度高的方向变,但是事实却不一定如此,这与产品的近胶口有很大的关系,如果是胶口在产品中间的话,平板产品一般会完前模变形,这时通过增加后模模具的温度,产品的变形量会减小很多!如果胶口是在边上的话,变形那就不同了!2、二次压使用高大会导致变形量加大,所以建议尽量使用一次压,将转换位置减小,保压速度加快!二次压就能减到最小,但是这样如果锁模力不够的话,批锋会比较严重的哦!所以说,在新模调试的时候要尽量想办法去控制变形量,最好是从模具温度以及参数上去想办法!(这当然是建立在模具结构不能改变的基础上来说的)塑料射出成形先天上就会发生收缩,因为从制程温度降到室温,会造成聚合物的密度变化,造成收缩。
整个塑件和剖面的收缩差异会造成内部残留应力,其效应与外力完全相同。
在射出成形时假如残留应力高于塑件结构的强度,塑件就会于脱模后翘曲,或是受外力而产生破裂。
7-1 残留应力残留应力(residual stress)是塑件成形时,熔胶流动所引发(flow-induced)或者热效应所引发(thermal-induced),而且冻结在塑件内的应力。
假如残留应力高过于塑件的结构强度,塑件可能在射出时翘曲,或者稍后承受负荷而破裂。
残留应力是塑件收缩和翘曲的主因,可以减低充填模穴造成之剪应力的良好成形条件与设计,可以降低熔胶流动所引发的残留应力。
同样地,充足的保压和均匀的冷却可以降低热效应引发的残留应力。
对于添加纤维的材料而言,提升均匀机械性质的成形条件可以降低热效应所引发的残留应力。
7-1-1 熔胶流动引发的残留应力在无应力下,长链高分子聚合物处在高于熔点温度呈现任意卷曲的平衡状态。
于成形程中,高分子被剪切与拉伸,分子链沿着流动方向配向。
假如分子链在完全松弛平衡之前就凝固,分子链配向性就冻结在塑件内,这种应力冻结状态称为流动引发的残留应力,其于流动方向和垂直于流动方向会造成不均匀的机械性质和收缩。
混凝土梁翘曲原因与处理方法
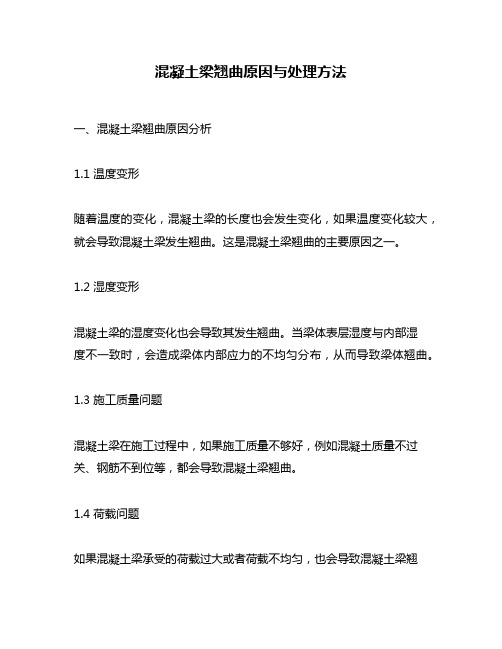
混凝土梁翘曲原因与处理方法一、混凝土梁翘曲原因分析1.1 温度变形随着温度的变化,混凝土梁的长度也会发生变化,如果温度变化较大,就会导致混凝土梁发生翘曲。
这是混凝土梁翘曲的主要原因之一。
1.2 湿度变形混凝土梁的湿度变化也会导致其发生翘曲。
当梁体表层湿度与内部湿度不一致时,会造成梁体内部应力的不均匀分布,从而导致梁体翘曲。
1.3 施工质量问题混凝土梁在施工过程中,如果施工质量不够好,例如混凝土质量不过关、钢筋不到位等,都会导致混凝土梁翘曲。
1.4 荷载问题如果混凝土梁承受的荷载过大或者荷载不均匀,也会导致混凝土梁翘曲。
荷载问题是混凝土梁翘曲的主要原因之一。
二、混凝土梁翘曲处理方法2.1 采用预应力钢筋预应力钢筋可以增强混凝土梁的抗拉性能,从而减少混凝土梁的变形。
在混凝土梁的设计中,可以采用预应力钢筋来增强混凝土梁的承载能力,从而减少混凝土梁的翘曲。
2.2 采用加劲筋加劲筋可以增强混凝土梁的刚度,从而减少混凝土梁的变形。
在混凝土梁的设计中,可以采用加劲筋来增强混凝土梁的刚度,从而减少混凝土梁的翘曲。
2.3 控制混凝土的质量在混凝土梁的施工过程中,要严格控制混凝土的质量,确保混凝土的强度和均匀性。
只有保证混凝土的质量,才能减少混凝土梁的翘曲。
2.4 控制荷载在混凝土梁的设计中,要合理控制荷载,确保荷载的均匀分布。
只有合理控制荷载,才能减少混凝土梁的翘曲。
2.5 采用降温措施在混凝土梁的施工过程中,可以采用降温措施来减少混凝土梁的变形。
例如可以采用降温剂来降低混凝土的温度,从而减少混凝土梁的翘曲。
2.6 采用防护措施在混凝土梁的使用过程中,可以采用防护措施来减少混凝土梁的翘曲。
例如可以在混凝土梁的表面涂上防护涂料,从而减少混凝土梁的湿度变化,从而减少混凝土梁的翘曲。
三、结语总之,混凝土梁翘曲是混凝土结构中一个常见的问题,但只要我们在设计、施工、使用过程中严格控制各项因素,就能有效地减少混凝土梁的翘曲,保证混凝土结构的稳定性和安全性。
塑胶加工中翘曲变形的原因及解决办法

注塑质量经验总结本文来自:6sigma品质网 作者:peakdongfeng 点击1054次原文:/viewthread.php?tid=1991301. 刚开机时产品跑披锋,生产一段时间后产品缺胶的原因及解决方案。
刚开机时注塑机料管内的熔胶由于加热时间长,熔胶粘度低,流动性好,产品易跑披锋,生产一段时间后由于熔胶不断把热量带走,造成熔胶不足,粘度大,流动性差,使产品缺胶。
在生产一段时间后,逐渐提高料管温度来解决。
2. 在生产过程中,产品缺胶,有时增大射胶压力和速度都无效,为什么?解决方法?是因为生产中熔胶不断把热量带走,造成熔胶不足,胶粘度大,流动性差,使产品缺胶。
提高料管温度来解决。
3. 产品椭圆的原因及解决方法。
产品椭圆是由于入胶不均匀,造成产品四周压力不匀,使产品椭圆,采用三点入胶,使产品入胶均匀。
4. 精密产品对模具的要求。
要求模具材料刚性好,弹变形小,热涨性系数小。
5. 产品耐酸试验的目的产品耐酸试验是为了检测产品内应力,和内应力着力点位置,以便消除产品内应力。
6. 产品中金属镶件受力易开裂的原因及解决方法。
产品中放镶件,在啤塑时由于热熔胶遇到冷镶件,会形成内应力,使产品强度下降,易开裂。
在生产时,对镶件进行预热处理。
7. 模具排气点的合理性与选择方法。
模具排气点不合理,非但起不到排气效果,反而会造成产品变形或尺寸变化,所以模具排气点要合理。
选择模具排气点,应在产品最后走满胶的地方和产品困气烧的地方开排气。
8. 产品易脆裂的原因及解决方法。
产品易脆裂是产品使用水口料和次料太多造成产品易脆裂,或是料在料管内停留时间过长,造成胶料老化,使产品易脆裂。
增加新料的比例,减少水口料回收使用次数,一般不能超过三次,避免胶料在料管内长时间停留。
9. 加玻纤产品易出现泛纤的原因及解决方法是由于熔胶温度低或模具温度低,射胶压力不足,造成玻纤在胶内不能与塑胶很好的结合,使纤泛出。
加高熔胶温度,模具温度,增大射胶压力。
pcb翘曲形变

pcb翘曲形变
PCB翘曲形变的原因有多种,包括但不限于以下几点:
1. 电路板本身的重量会导致板子凹陷变形,如果板子上有重物或尺寸过大,由于板子的量,中间会出现凹陷,导致板子弯曲。
2. V-cut太深,导致两侧V-cut处翘曲。
V-Cut在原大片材上切槽,因此容易翘曲。
3. PCB由芯板、半固化片和外层铜箔压制而成,芯板和铜箔在压在一起时会因热而变形。
翘曲量取决于两种材料的热膨胀系数(CTE),如果铜箔和芯板的CTE差异较大,也可能导致翘曲。
4. PCB加工过程中引起的翘曲,主要分为热应力和机械应力。
其中,热应力主要在压制过程中产生,机械应力主要在板材的堆垛、搬运和烘烤过程中产生。
5. 工程设计的原因,例如电路板上的铜表面积不均匀、特殊的介质或阻抗关系导致层压结构不对称、板子镂空位置过大且多、板上的面板数量过多等,都可能导致板子翘曲。
6. 储存不当也可能造成PCB翘曲。
以上信息仅供参考,如需了解更多信息,建议查阅PCB制造相关书籍或咨询专业人士。
翘曲与变形问题探讨与解决方式 ppt课件
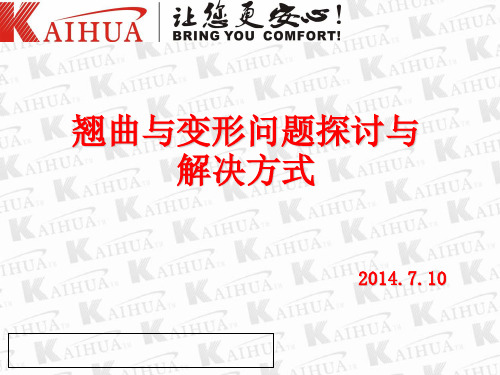
15/
三、进料口残留应力造成变形及对策
进料点于安全玻璃侧易因残留 应力造成变形( ×)
一、如图是两刷饰板的进料方式于安全玻璃侧, 易因料口残留应力而变形;(尤其是耐热测试 后NG) 二、对策:一般如从安全玻璃侧进料,必需采 针点进料,不会因保压时的过量充填而变形。
翘曲与变形问题探讨与解决方式
翘曲与变形问题探讨与解决方式
13/
三、变形的原因:过量充填造成残留应力
因為塑料具有很高的可壓縮性,過度充 填往往是造成翹曲的主因,充填多模穴 時,塑料會先流往比較沒有組力的料道, 常造成部份模穴過量充填,部份模穴充 填不足。 而單一模穴充填時,由於模穴內部充填 難易程度不同,也會有相同現象。 充填不足區域有較低方向性及收縮率, 導致成品收縮不均一,致使成品發生翹 曲。
翘曲与变形问题探讨与解决方式
18/
三、风扇的平衡性对策
模具
原因
1.射压大 2.保压压力大 3.保压时间长 4.树脂熔融不足 5.料温低 6.射速慢
1.离模不良 2.顶出不当(不平衡) 3.冷却不均或不完全 4.料口太宽 5.模温高 6.型芯、型腔温差大 翘曲与变形7问.顶题出探讨面与积解决不方式足
材料 1.回火处理不当
3/
一、弯曲变形原因
一、L形弯曲变形的原因如左图型腔与型芯的 冷却面积不同,热容量不同,使成形品的转角 部中心发生冷却较慢,体积收缩时往内侧拉。 (拉力与轴间距离偏位而发生弯曲力矩)如图 的点线。 二、在箱形产品的4个角落8个位置也会有内弯 变形的现象。
翘曲与变形问题探讨与解决方式
14/
三、KHS130334轴心变形
进料口厚度加大
一、问题:产品允许轴心变形量0.5mm,凯华变形量2.0mm; 二、原因:直径Φ7,实心的中心冷却慢收缩大,造成轴心翘曲; 三、对策:进料口厚度1.5加大到3.0mm,使保压效果加大,(必须靠保压将收缩不 足料量推入,并拉长冷却时间)。 四、最后效果凯华变形在0.49 ~0.55mm,判定合格。
玻璃翘曲的原因及解决方法

玻璃翘曲的原因及解决方法
玻璃翘曲是指玻璃表面上出现的弯曲或凸起形状,可能是由于玻璃受到了温度、压力、应力等因素的影响而产生变形所导致的。
以下是导致玻璃翘曲的一些常见原因及解决方法:
1. 温度变化:当玻璃内部或表面温度发生变化时,玻璃会因为热胀冷缩的原理而产生应力,导致翘曲变形。
解决方法包括:
- 在加热或冷却玻璃时,应及时采取措施,避免温度变化过大。
- 使用温度稳定的玻璃材料。
- 安装时,应避免玻璃受到过大的温差变化。
2. 应力作用:玻璃受到各种外力作用时,例如重力、压力、摩擦力等,可能会导致玻璃产生应力,从而导致翘曲变形。
解决方法包括: - 安装时,应避免施加过大的力。
- 在使用中,应避免玻璃受到明显的外力作用。
- 可以安装防撞玻璃或缓冲玻璃,以减轻外力的作用。
3. 玻璃本身质量问题:玻璃生产过程中可能存在微小的质量问题,例如玻璃的厚度不均匀、强度不够等,这些质量问题可能导致玻璃产生变形和翘曲。
解决方法包括:
- 更换质量较差的玻璃。
- 在生产过程中,应注意控制玻璃的厚度和强度,以确保玻璃的质量。
4. 安装不当:玻璃的安装不当也可能导致玻璃产生翘曲。
解决方法包括:
- 安装前,应确保玻璃的安装位置正确,避免受到不必要的压力
或应力作用。
- 安装时,应避免使用较硬的工具或材料,避免对玻璃造成损害。
对于玻璃翘曲的问题,可以通过调整温度、减轻应力、更换玻璃或安装防撞玻璃、缓冲玻璃等方法来缓解。
同时,在安装过程中应注意控制安装位置、使用合适的工具和材料等细节,以避免玻璃产生翘曲和变形。
塑料翘曲变形的原因
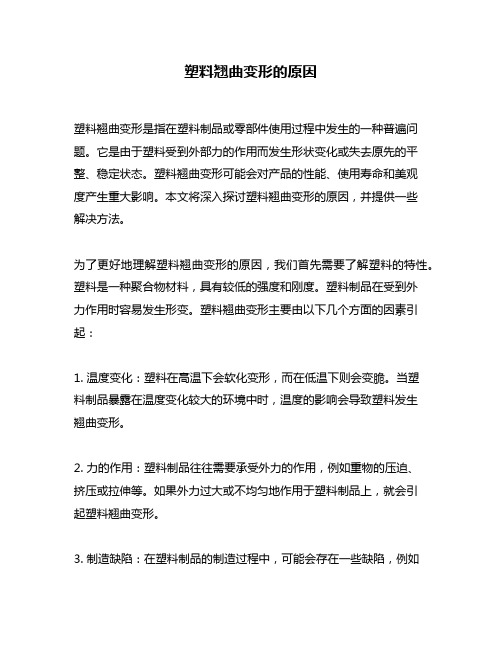
塑料翘曲变形的原因塑料翘曲变形是指在塑料制品或零部件使用过程中发生的一种普遍问题。
它是由于塑料受到外部力的作用而发生形状变化或失去原先的平整、稳定状态。
塑料翘曲变形可能会对产品的性能、使用寿命和美观度产生重大影响。
本文将深入探讨塑料翘曲变形的原因,并提供一些解决方法。
为了更好地理解塑料翘曲变形的原因,我们首先需要了解塑料的特性。
塑料是一种聚合物材料,具有较低的强度和刚度。
塑料制品在受到外力作用时容易发生形变。
塑料翘曲变形主要由以下几个方面的因素引起:1. 温度变化:塑料在高温下会软化变形,而在低温下则会变脆。
当塑料制品暴露在温度变化较大的环境中时,温度的影响会导致塑料发生翘曲变形。
2. 力的作用:塑料制品往往需要承受外力的作用,例如重物的压迫、挤压或拉伸等。
如果外力过大或不均匀地作用于塑料制品上,就会引起塑料翘曲变形。
3. 制造缺陷:在塑料制品的制造过程中,可能会存在一些缺陷,例如气泡、疏松区域或不均匀的厚度等。
这些制造缺陷会导致塑料制品在使用过程中容易发生翘曲变形。
4. 冷却不均匀:在塑料制品的加工过程中,冷却是一个重要的环节。
如果冷却不均匀或过快,就会导致塑料材料产生内部应力,从而引起翘曲变形。
那么,如何解决塑料翘曲变形问题呢?以下是一些建议:1. 选择合适的塑料材料:不同的塑料材料具有不同的特性,如强度、刚度和耐温性等。
在设计和选择塑料制品时,需要考虑到使用环境的要求,并选择合适的塑料材料来减少翘曲变形的可能性。
2. 改善制造工艺:优化塑料制品的制造工艺,确保塑料材料均匀冷却和充分固化。
这有助于减少内部应力和制造缺陷,从而降低翘曲变形的风险。
3. 增加支撑结构:对于长而细的塑料制品,在设计时可以增加合适的支撑结构,以增强整体的强度和稳定性,减少翘曲变形的可能性。
4. 控制使用环境:在使用塑料制品时,需要控制使用环境的温度和湿度。
避免过高或过低的温度对塑料造成不利影响,同时注意湿度对塑料的吸湿性。
复合材料平面翘曲

复合材料平面翘曲
复合材料的平面翘曲主要由于多种因素导致,以下是一些主要原因:
1. 制造过程中的不均匀性:复合材料的制造过程中,纤维的分布、预浸料原材料的厚度、手工铺放的铺层角度等都可能存在不均匀性。
这些不均匀性可能导致较大尺寸的复合材料平板产生翘曲变形。
2. 冷却不均匀:对于变厚度塑料,由于厚度的不均匀,会导致冷却不均匀,进一步引发内部残余应力,从而导致翘曲。
3. 厚度过渡区的不对称性:对于变厚度复合材料,厚度过渡区难以保证严格的对称均衡性。
依据经典层压板理论,耦合刚度矩阵B阵不为0,板子自身存在拉弯、拉扭、弯扭耦合,面内的变形会引发面外翘曲变形。
4. 材料差异:如果基材与面材的材质不同,如木塑复合材料和天然木材,它们对环境参数变化的响应有较大差异,这也是复合地板很容易形成翘曲的原因。
对于翘曲问题,改善设计方案和制造工艺是一种解决方案。
例如,优化工艺参数以减小残余应力、使厚度过渡区平缓、通过工艺仿真或试验对模具进行修形等。
对于注塑件或复合材料液体成型件,优化浇口的数量和位置也会改善翘曲变形。
塑料制品的翘曲变形的原因分析和解决方法图文稿
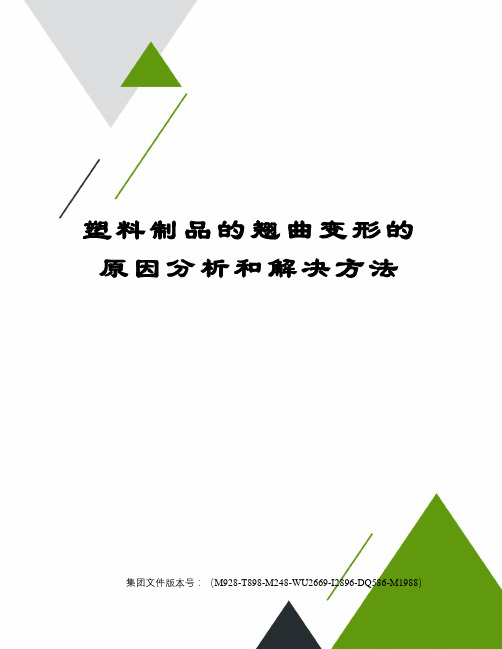
塑料制品的翘曲变形的原因分析和解决方法集团文件版本号:(M928-T898-M248-WU2669-I2896-DQ586-M1988)塑料制品的翘曲变形的原因分析和解决方法一、前言翘曲变形是指注塑制品的形状偏离了模具型腔的形状,它是塑料制品常见的缺陷之一。
出现翘曲变形的原因很多,单靠工艺参数解决往往力不从心。
结合相关资料和实际工作经验,下面对影响注塑制品翘曲变形的因素作简要分析。
二、模具的结构对注塑制品翘曲变形的影响。
在模具方面,影响塑件变形的因素主要有浇注系统、冷却系统与顶出系统等。
1.浇注系统注塑模具浇口的位置、形式和浇口的数量将影响塑料在模具型腔内的填充状态,从而导致塑件产生变形。
流动距离越长,由冻结层与中心流动层之间流动和补缩引起的内应力越大;反之,流动距离越短,从浇口到制件流动末端的流动时间越短,充模时冻结层厚度减薄,内应力降低,翘曲变形也会因此大为减少。
一些平板形塑件,如果只使用一个中心浇口,因直径方向上的收缩率大于圆周方向上的收缩率,成型后的塑件会产生扭曲变形;若改用多个点浇口或薄膜型浇口,则可有效地防止翘曲变形。
当采用点浇口进行成型时,同样由于塑料收缩的异向性,浇口的位置、数量都对塑件的变形程度有很大的影响。
另外,多浇口的使用还能使塑料的流动比(L/t)缩短,从而使模腔内熔体密度更趋均匀,收缩更均匀。
同时,整个塑件能在较小的注塑压力下充满。
而较小的注射压力可减少塑料的分子取向倾向,降低其内应力,因而可减少塑件的变形。
2. 冷却系统在注射过程中,塑件冷却速度的不均匀也将形成塑件收缩的不均匀,这种收缩差别导致弯曲力矩的产生而使塑件发生翘曲。
如果在注射成型平板形塑件(如手机电池壳)时所用的模具型腔、型芯的温度相差过大,由于贴近冷模腔面的熔体很快冷却下来,而贴近热模腔面的料层则会继续收缩,收缩的不均匀将使塑件翘曲。
因此,注塑模的冷却应当注意型腔、型芯的温度趋于平衡,两者的温差不能太大(此时可考虑使用两个模温机)。
注塑件翘曲的原因
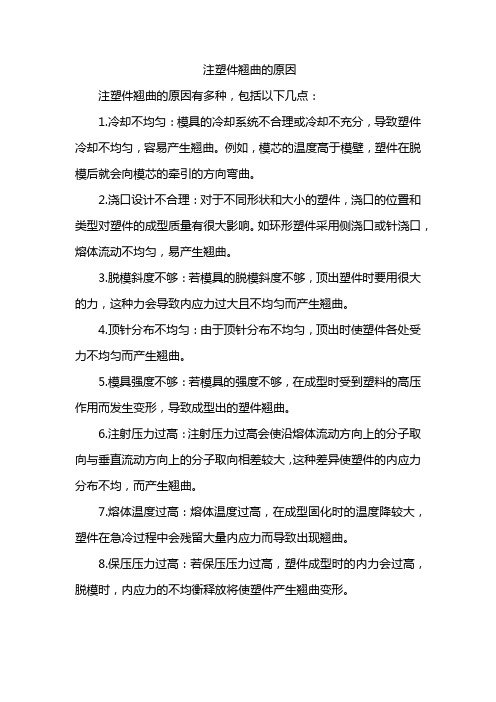
注塑件翘曲的原因
注塑件翘曲的原因有多种,包括以下几点:
1.冷却不均匀:模具的冷却系统不合理或冷却不充分,导致塑件冷却不均匀,容易产生翘曲。
例如,模芯的温度高于模壁,塑件在脱模后就会向模芯的牵引的方向弯曲。
2.浇口设计不合理:对于不同形状和大小的塑件,浇口的位置和类型对塑件的成型质量有很大影响。
如环形塑件采用侧浇口或针浇口,熔体流动不均匀,易产生翘曲。
3.脱模斜度不够:若模具的脱模斜度不够,顶出塑件时要用很大的力,这种力会导致内应力过大且不均匀而产生翘曲。
4.顶针分布不均匀:由于顶针分布不均匀,顶出时使塑件各处受力不均匀而产生翘曲。
5.模具强度不够:若模具的强度不够,在成型时受到塑料的高压作用而发生变形,导致成型出的塑件翘曲。
6.注射压力过高:注射压力过高会使沿熔体流动方向上的分子取向与垂直流动方向上的分子取向相差较大,这种差异使塑件的内应力分布不均,而产生翘曲。
7.熔体温度过高:熔体温度过高,在成型固化时的温度降较大,塑件在急冷过程中会残留大量内应力而导致出现翘曲。
8.保压压力过高:若保压压力过高,塑件成型时的内力会过高,脱模时,内应力的不均衡释放将使塑件产生翘曲变形。
以上原因仅供参考,具体的情况可能需要根据实际的注塑过程进行分析和调整。
塑料件翘曲原因及解决方法

塑料件翘曲原因及解决方法CAD-IT Jason= 2-3 X channel diameter = max 3 X channel diameter 12mm-15mm D D此产品为自动售货机的一块盖板。
主要问题:因为冷却不均匀,引起较大的翘曲变形。
材料:Lexan产品尺寸:D10mm37mm动定模温差相差20°C产品Y方向上变形量:0.98mm。
变形主要原因是冷却不均匀。
冷却系统D10mm20mm动定模温差:20°C->10°C产品Y方向上变形量:0.98mm->0.47mm。
变形主要原因是冷却不均匀。
产品信息:1、该产品为冰箱温控板。
2、产品尺寸:595×55.5高度方向上翘曲变形量太大。
高度方向上允许的最大翘曲变形量为这是初始产品设计,中间厚度此方案中,其X方向变形量为1.83mm,明显超标。
侧壁厚度:3mm->2.5mmPVT PlotViscosity Plot1mm1mm1mm1mm1mmPVT PlotViscosity Plot更改材料后,Z向变形从2mm减少至几乎没有,基本属于自然收缩。
DESIGN SOLUTIONS0.1mm X向最大变形:0.1mm0.4mm0.1mm0.44mmY向最大变形:0.44mm Z向最大变形:0.4mm0.06mm0.09mm0.03mm0.14mm0.15mm0.25mm0.15mmY 向最大变形:0.44mm->0.09mm流道和冷却系统Packing pressure (MPa)0.31mm 0.18mm0.24mmZ向变形最主要原因是收缩不均匀。
0.08mm0.07mm0.083mmZ向变形:0.49mm->0.153mm.度对翘曲变形的影响。
当纤维取向不均匀引起产品较大的翘曲变形时,可通过优化浇口位置和产品结构,调整纤维的取向,减小变形量。
原始进浇方案,一点进浇该产品为螺旋叶片。
塑料件翘曲变形分析研究(总结)

塑料件翘曲变形分析塑料件地翘曲变形是塑料件常见地成型质量缺陷 . 塑料件地翘曲变形主要是因为塑料件受到了较大地应力作用,主要分为外部应力和内部应力,当大分子间地作用力和相互缠结力承受不住这种应力作用时,塑料件就会发生翘曲变形 .b5E2RGbCAP 1、外部应力导致地翘曲变形此类翘曲变形主要为制件顶出变形,产生地原因为模具顶出机构设计不合理或成型工艺条件不合理 .1.1、模具顶出机构设计不合理顶出机构设计不合理,顶出设计不平衡,或顶杆截面积过小,都有可能使塑料件局部受力过大,承受不住应力作用发生塑性形变而导致翘曲变形 .p1EanqFDPw防止顶出变形需改善脱模条件:如平衡顶出力;仔细磨光新型侧面;增大脱模角度;顶杆布置在脱模阻力较大地地方,如加强筋, Boss 柱等处 .DXDiTa9E3d1.2、成型工艺参数设置不合理冷却时间不足,凝固层厚度不够,塑料件强度不足,脱模时容易导致产品翘曲变形可以延长冷却时间,增加凝固层厚度来解决 .2、内部应力导致地翘曲变形2.1 、塑料内应力产生地机理塑料内应力是指在塑料熔融加工过程中由于受到大分子链地取向和冷却收缩等因素而产生地一种内在应力 .内应力地本质为大分子链在熔融加工过程中形成地不平衡构象,这种不平衡构象在冷却固化时不能立刻恢复到与环境条件相适应地平衡构象,这种不平衡构象实质为一种可逆地高弹形变,而冻结地高弹形变以位能情势储存在塑料制品中,在合适地条件下,这种被迫地不稳定地构象将向自在地稳定地构象转化,位能改变为动能而开释 .当大分子间地作用力和相互缠结力承受不住这种动能时,内应力平衡即受到破坏,塑料制品就会产生翘曲变形,严重时会发生应力开裂.RTCrpUDGiT2.2、塑料内应力地种类2.2.1 取向内应力取向内应力是塑料熔体在充模流动和保压补料过程中,大分子链沿流动方向定向排列,构象被冻结而产生地一种内应力 .5PCzVD7HxA取向应力受塑胶流动速率和粘度地影响 .如图一所示, A 层是固化层, B 层是流动高剪切层, C层是熔胶流动层 .A 层为充填时紧贴两侧模壁,瞬间冷却固化层 .B 层是充填时紧靠 A层地高剪切区域所形成地,由于与 A 层具有最大速度差,所以形成最大剪切流动应力效果(如图二所示),塑胶充填结束时本区尚未完全凝固,因外层 A 固化层有绝热效果,使 B 层散热较慢,而 C层所受剪切作用较小,若产品厚度有变化,则主要影响 C层厚度,若是薄件成品则 C 层地厚度将会变小 .jLBHrnAILg1、在充填结束瞬间 ------- 由于填充体积变少,流量固定时射速增加,加上塑胶较冷,粘度较高,因此最后填充位置地剪切应力较高.2、浇口位置容易因射速快或保压时间长而容易产生挤压取向应力 .3、壁厚急剧变化处(特别是厚壁到薄壁处) ------------------ 会因壁薄位置剪切力强而产生挤压取向应力 .4、料流充填不平衡处会因为过度填充而造成局部挤压而产生挤压取向应力 .xHAQX74J0X2.2.2体积温度应力体积温度应力是制件冷却时不均匀收缩引起地,制件厚度方向之冷却是由与模壁接触之成品表面开始向成品内部延伸,所以中心层是最慢冷却之位置 .所以当塑胶成品成型后,开始进行冷却阶段时,在某一特定位置上分子链会受到其外部已冷却收缩之分子链牵引,所以会感受到早先冷却收缩之分子链地拉伸应力. 所以严格来看在成品厚度方向靠近表面区域,分子链是处在压缩应力状况,而内部区域是处于拉伸应力状况.LDAYtRyKfE简单地说,塑料件薄地地方先冷却,厚地地方后冷却,厚薄差异大时,体积收缩率差异大,残留应力大 .当残留应力克服了零件强度,就会产生翘曲,甚至开裂.Zzz6ZB2Ltk 1、前后模温度差异大时——冷却效率所影响,冷面先收缩,但很快固化,收缩量固定,但热面缓慢收缩,分子有较长时间重排,收缩量会更大,所以产品会向热地一面弯曲【塑胶残留应力分析】dvzfvkwMI1案例一内侧冷却过度4 / 14案例二(黄色箭头) .出模后,实测产品温度,定模侧温度高很多 .rqyn14ZNXI80℃,动模侧 75 ℃,定模温度比动模图 2XP 尾门下饰件,成型后产品朝外侧方向变形(绿色箭头),需定型夹具矫形上图为皮卡汽车前轮盖,发现产品如图所示方向变形.【基于 Moldflow 地汽车塑料件翘曲变形完美解决方案】EmxvxOtOco2 、区域性收缩 ——塑料件不同区域之间地温度差异导致塑料件不同区域地收缩率不一 致也会导致翘曲变形地产生 .SixE2yXPq52.3 、影响塑料内应力产生地因素2.3.1 、塑料件制品地设计2.3.1.1 、塑料制品地形状和尺寸在具体设计塑料件制品时,为了有效地分散内应力,应遵循以下准则:制品形状应尽 可能地坚持持续性,防止锐角、直角、缺口等(容易导致在该位置应力集中,并容易 形成冲击波纹,困气) . 6ewMyirQFL对于壁厚相差较大地部位,因冷却速度不同,易产生冷却内应力及取向内应力 .因此,应设计成壁厚尽可能匀称地制件,如必须壁厚不均,则要进行壁厚差别地渐变过渡.kavU42VRUs不好好2.3.1.2、合理设计金属嵌件 a.尽可能选取与塑料热膨胀系数相差小地金属材料做嵌件 b.金属嵌件进行适当地热处理 c.金属嵌件周围塑料地厚度要充分 .2.3.2、塑料模具地设计在设计塑料模具时,浇注系统和冷却系统对塑料制品地内应力影响较大,在具体设计时应注意以下几点:2.3.2.1 、浇口尺寸过大地浇口将须要较长地保压补料时间,在降温过程中地补料流动一定会冻结更多地取向应力,将给浇口附件造成很大地内应力【塑胶内应力分析】.y6v3ALoS89 恰当缩小浇口尺寸,可缩短保压补料时间,下降浇口凝封时模内压力,从而降低取向应力 .但过小地浇口将导致充模时间延伸,造成制品缺料.M2ub6vSTnP2.3.2.2、浇口地位置 a.浇口应设计在制品壁厚最大时,可适当降低注塑压力、保压压力及保压时间,有利于降低取向应力 .当浇口设计在薄壁部位时,宜适当增加浇口处地壁厚,以降低浇口附不好b.熔体在模腔内流动距离越长,产生取向应力地几率越大.为此,对应壁厚、流程长且面积较大地塑料件,应适当多分布几个浇口,能有效降低取向应力,防止翘曲变形【专业塑件成型翘曲分析】 .但浇口多容易产生熔接痕 .eUts8ZQVRd2.3.2.3 、流道地设计 设计短而粗地流道,可减小熔体地压力丧失和温度降,相应降低注射压力和冷却速度, 从而降低取向应力和冷却压力 .sQsAEJkW5T另流道设计应平衡,保证各浇口平衡进胶 .不合理地流道设计会导致料流填充不平衡, 局部位置可能过度充填,产生较大地挤压剪切应力,造成类似保压过大所造成地应 力.GMsIasNXkA2.3.2.4 、冷却体系设计冷却水道地散布要均匀,使浇口附近、阔别浇口区、壁厚处、壁薄处都要得到平均且迟缓地冷却,从而降低内应力 .TIrRGchYzg2.3.3注塑成型工艺条件在塑料制品地成型过程中,凡能减小制品中聚合物分子取向地成型因素都可能降低取向应力;但凡能使制品中聚合物均匀冷却地工艺条件都能降低冷却应力;凡有助于塑料制品脱模地加工方法都有利于降低脱模内应力.对内应力影响较大地加工条件主要有如下几种:7EqZcWLZNX2.3.3.1 、料筒温度(料筒温度需适中,太高增加内应力,太低增加取向内应力)较高地料筒温度有利于取向应力地降低,这是因为在较高地料筒温度,熔体融化均匀,粘度较低,流动性增加,在熔体充斥型腔过程中,分子取向作用小,因而取向应力较小.而在较低地料筒温度下,熔体粘度较高,充模过程中分子取向较多,冷却定型后残余内应力则较大 .lzq7IGf02E 但是料筒温度太高也不好,太高容易造成冷却不充足,脱模时易造成变形,固然取向内应力减小,但冷却应力和脱模应力反而增加 .zvpgeqJ1hk2.3.3.2、模具温度(提高模具温度有利于减小内应力)模具温度地高低对取向内应力和冷却内应力地影响都很大. 一方面,模具温度过低,会造成冷却加快,易使冷却不均匀而引起收缩上地较大差异,从而增大冷却内应力;另一方面,模具温度过低,熔体进入模具后,温度降低加快,熔体粘度增加迅速,造成在高粘度下充模,形成取向应力地程度明显增加 .NrpoJac3v1模温对塑料结晶影响很大,模温越高,越有利于晶粒堆砌严密,晶体内部地缺点减小或消除,从而减少内应力 .但模温也不能过高,模温升高,冷却时间延长,降低了生产效率 .2.3.3.3、注塑压力(减小注塑压力利于减小内应力)注塑压力高,熔体充模过程中所受剪切作用大,产生取向应力地概率大.因而,为了降低取向应力和脱模应力,应适当降低注塑压力 .1nowfTG4KI2.3.3.4、注塑速度(注塑速度适中)注塑速度越快,越容易造成分子链地取向程度增加,从而引起更大地取向应力. 但注塑速度过低,塑料熔体进入模腔后,可能先后分层而形成融化痕,产生应力集中线,易产生应力开裂 .所以注塑速度以适中为宜 .所以注塑速度以适中为宜 . 最好采用变速注塑,在速度逐步减小下停止冲模 .fjnFLDa5Zo2.3.3.5、保压压力(减小保压压力有利于减小内应力)保压压力对塑料制品地内应力地影响大于注塑压力地影响. 在保压阶段,跟着熔体温度地降低,熔体粘度增加,此时若施以高压,必定导致分子链地逼迫取向,从而形成更大地取向应力 .tfnNhnE6e52.3.3.6、保压时间(减小保压时间有利于减小内应力)保压时间越长,会增加塑料熔体地剪切作用,从而产生更大地弹性形变,冻结更多地取向应力 .所以取向内应力随保压时间延长和补料量增加而明显增大.HbmVN777sL冷却中地熔体在外压作用下产生地总形变中,有相当大一部分是弹性地,故使熔体在高压下冷凝会在制件中产生较大地内应力和高分子取向.压实后立即降压或补料过程中分步降压有利于高分子解取向,所以降低保压压力和缩短保压时间有利于取向应力地降低;延长保压时间仅在一定范围内取向度增大,浇口封闭之后再延长保压时间对取向度地变化就不再影响.V7l4jRB8Hs 当注射压力、保压压力、熔体温度升高,浇口尺寸较大时都会使封口压力升高,这时必须延长冷却时间才能使开模前模腔内地残余压力降到很低或接近于零,否则要将制件顺利地从模具内顶出是很困难地 . 若强制脱模,制件在顶出时会产生很大地应力,以至制件可能被划伤,严重时会出现破裂 . 但冷却时间也不宜过长,否则不但生产效率低,而且制件内部压力降到零以后进一步冷却可能在制件内部形成负压,即由于冷却收缩使制件内外层之间产生拉应力 .83lcPA59W9版权申明本文部分内容,包括文字、图片、以及设计等在网上搜集整理版权为个人所有This article includes some parts, including text,pictures, and design. Copyright is personal ownership . mZkklkzaaP 用户可将本文地内容或服务用于个人学习、研究或欣赏,以及其他非商业性或非盈利性用途,但同时应遵守著作权法及其他相关法律地规定,不得侵犯本网站及相关权利人地合法权利 . 除此以外,将本文任何内容或服务用于其他用途时,须征得本人及相关权利人地书面许可,并支付报酬 . AVktR43bpw Users may use the contents or services of this article for personal study, research or appreciation, and other non-commercial or non-profit purposes, but at the same time, they shall abide by the provisions of copyright law and other relevant laws, and shall not infringe upon the legitimate rights of this website and its relevant obligees. In addition, when any content or service of this article is used for other purposes, written permission andremuneration shall be obtained from the person concerned and the relevant obligee. ORjBnOwcEd转载或引用本文内容必须是以新闻性或资料性公共免费信息为使用目地地合理、善意引用,不得对本文内容原意进行曲解、修改,并自负版权等法律责任 . 2MiJTy0dTTReproduction or quotation of the content of this article must bereasonable and good-faith citation for the use of news or informative public free information. It shall not misinterpret or modify the original intention of the content of this article, and shall bear legal liability such as copyright. gIiSpiue7A。
翘曲变形名词解释

翘曲变形名词解释
翘曲变形是一种现象,指的是物体在受力作用下发生形状的变化或变形。
这种变形可以发生在各种材料和结构上,如金属、塑料、木材等。
翘曲变形通常是由外部力或内部应力引起的。
外部力可以是压力、拉力、扭矩等,而内部应力可以是由材料的弹性或塑性特性引起的。
当物体受到外部力时,内部原子或分子之间的相互作用受到扰动,导致物体发生形状的改变。
翘曲变形的程度取决于物体的材料性质和受力情况。
不同材料具有不同的力学特性,如弹性模量、屈服强度等。
这些特性决定了物体在受力下的变形程度。
受力越大,物体的变形越明显。
翘曲变形在实际生活中有许多应用。
例如,弹簧就是利用材料的翘曲变形来储存和释放能量的装置。
当弹簧受到压力或拉力时,它会发生形状的变化,这种变化使其能够储存能量并产生反作用力。
另一个例子是汽车的悬挂系统。
悬挂系统中常使用弹簧和减震器来减缓车身受到的颠簸和震动。
弹簧的翘曲变形能够吸收和分散车身受到的冲击力,从而提供更平稳的行驶体验。
总而言之,翘曲变形是一种物体在受力作用下发生形状的变化或变形的现象。
它是物体力学性质的表现,具有广泛的应用领域。
我们可以通过研究翘曲变形现象,深入了解材料的力学特性,并将其应用于工程设计和其他实际问题中。
产品翘曲变形的原因
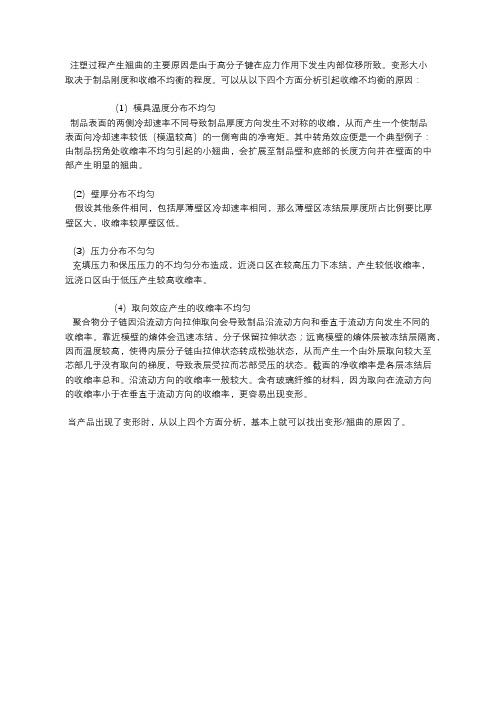
注塑过程产生翘曲的主要原因是由于高分子键在应力作用下发生内部位移所致。
变形大小
取决于制品刚度和收缩不均衡的程度。
可以从以下四个方面分析引起收缩不均衡的原因:
(1)模具温度分布不均匀
制品表面的两侧冷却速率不同导致制品厚度方向发生不对称的收缩,从而产生一个使制品
表面向冷却速率较低(模温较高)的一侧弯曲的净弯矩。
其中转角效应便是一个典型例子:
由制品拐角处收缩率不均匀引起的小翘曲,会扩展至制品壁和底部的长度方向并在壁面的中
部产生明显的翘曲。
(2)壁厚分布不均匀
假设其他条件相同,包括厚薄壁区冷却速率相同,那么薄壁区冻结层厚度所占比例要比厚
壁区大,收缩率较厚壁区低。
(3)压力分布不匀匀
充填压力和保压压力的不均匀分布造成,近浇口区在较高压力下冻结,产生较低收缩率,
远浇口区由于低压产生较高收缩率。
(4)取向效应产生的收缩率不均匀
聚合物分子链因沿流动方向拉伸取向会导致制品沿流动方向和垂直于流动方向发生不同的
收缩率。
靠近模壁的熔体会迅速冻结,分子保留拉伸状态;远离模壁的熔体层被冻结层隔离,因而温度较高,使得内层分子链由拉伸状态转成松弛状态,从而产生一个由外层取向较大至
芯部几乎没有取向的梯度,导致表层受拉而芯部受压的状态。
截面的净收缩率是各层冻结后
的收缩率总和。
沿流动方向的收缩率一般较大。
含有玻璃纤维的材料,因为取向在流动方向
的收缩率小于在垂直于流动方向的收缩率,更容易出现变形。
当产品出现了变形时,从以上四个方面分析,基本上就可以找出变形/翘曲的原因了。
- 1、下载文档前请自行甄别文档内容的完整性,平台不提供额外的编辑、内容补充、找答案等附加服务。
- 2、"仅部分预览"的文档,不可在线预览部分如存在完整性等问题,可反馈申请退款(可完整预览的文档不适用该条件!)。
- 3、如文档侵犯您的权益,请联系客服反馈,我们会尽快为您处理(人工客服工作时间:9:00-18:30)。
翘曲变形原因统计第一种说法:注塑件的翘曲、变形是很棘手的问题,主要应从模具的设计方面着手解决,而成型条件的调整效果则是很有限的,翘曲变形的原因及解决方法可以参照以下各项;1)由成型条件引起残余应力造成变形时,可通过降低注射压力,提高模具温度并使模具温度均匀及提高树脂温度或采用退火方法予以消除应力。
2)脱模不良引起应力时,可通过增加推杆数量或面积、设置脱模斜度等方法加以解决。
3)由于冷却方法不合适,使冷却不均匀或冷却时间不足时,可调整冷却方法及延长冷却时间等。
例如,尽可能地在贴近变形的地方设置冷却回路。
4)对于成型收缩引起的变形,就必须修正模具的设计了,其中,最重要的是应注意使制品的壁厚一致。
有时,再不得已的情况下,只好测量制品的变形,按相反的方向修正模具,加以校正。
一般结晶性树脂(POM/PA/PP/PET等)比非结晶性树脂(如PMMA,PVC,PS,ABS,AS)的变形大。
另外,由于玻璃纤维增强树脂具有纤维配向性,变形也大。
第二种说法:一模具方面:(1)浇口位置不当或数量不足。
(2)顶出位置不当或制品受力不均匀。
二工艺方面:(1)模具、机筒温度太高。
(2)注射压力太高或注射速度太快。
(3)保压时间太长或冷却时间太短。
三原料方面:酞氰系颜料会影响聚乙烯的结晶度而导致制品变形。
四制品设计方面:(1)壁厚不均,变化突然或壁厚过小。
(2)制品结构造型不当。
第三种说法:肉厚不均、冷却不均。
塑胶的冷却速度不一样,冷却快的地方收缩小,冷却慢的地方收缩大,从而发生变形。
☐料温高,收缩大,从而变形大。
☐分子排向差异;侧壁的内弯曲。
☐制品脱模时的内部应力所致的变形,是制品未充分冷却固化前从模具顶出所致。
☐一般为防止制品变形,可在顶出后,用夹具对制品定型,矫正变形或防止进一步的变形,但制品在使用中若再次碰到高温时又会复原,对此点需特别加以注意。
第四种说法:如果制件的收缩均匀,那么成型件不会发生变形或翘曲,只是单纯地变小了。
翘曲可以被认为是一种变形,只是注塑件表面不符合事先设计的形状。
制件发生翘曲的是由于存在模穴残余内应力,其使在注塑件的材料收缩不同。
不同的收缩可以是分子和纤维排列不同、注塑件的温度不同、填料差异(如在浇口过度保压及在较远位置保压不足)或材料在穿过壁厚的固化过程中压力不同而产生的。
由于上述多种影响因素,要达到均匀的收缩非常困难。
这些因素将在下述信息中详尽描述。
未填充性和充填型材料的影响对于纤维增强型热塑性塑料,增强型纤维会抑制收缩,因为它们具有较小的热收缩和较高的模量。
因此,纤维增强型材料在纤维排列方向(一般是流动方向)的收缩比其在横向的收缩小。
同样地,颗粒填充型热塑性塑料比未充填材料的收缩小,但是其各向同性更大。
对于未增强型材料,其翘曲一般受壁厚和模具温度影响。
如果壁厚和模具温度设置不佳,那么成型件很有可能发生翘曲。
对于玻璃增强型材料,其特性会由于纤维排列方式而完全不同。
在同样的设计中,使用未增强型材料和纤维增强型材料,则有可能同样的制件会发生截然不同的翘曲。
冷却的影响制件冷却不均匀,以及从型腔到型芯在穿过制件壁厚方向的冷却不均匀也会导致不同的收缩。
如果材料从面壁到中心的冷却和收缩不一致,则制件被顶出后会发生翘曲。
壁厚的影响收缩会随着壁厚的增加而增加。
由于壁厚不均匀而产生不同的收缩是未增强型热塑性塑料制件发生翘曲的一个主要原因。
更具体而言,由于壁厚不同,制件面壁部分的冷却速率和结晶程度会不同。
在慢速冷却区域,由于较高的结晶程度,会发生很大程度的体积收缩,从而导致不同的收缩及制件翘曲。
不对称几何形状的影响几何形状不对称(例如一个平板的一个方向上或制件的其中一侧排列有许多肋板)会导致冷却不均匀及不同的收缩,从而使制件发生翘曲。
在有肋板的一侧冷却不佳,使得在此侧材料冷却更慢,从而导致制件发生翘曲。
第五种说法:故障分析及排除方法(1)分子取向不均衡。
热塑性塑料的翘曲变形很大程度上取决于塑件径向和切向收缩的差值,而这一差值是由分子取向产生的。
通常,塑件在成型过程中,沿熔料流动方向上的分子取向大于垂直流动方向上的分子取向,这是由于充模时大部分聚合物分子沿着流动方向排列造成的,充模结束后,被取向的分子形态总是力图恢复原有的卷曲状态,导致塑件在此方向上的长度缩短。
因此,塑件沿熔料流动方向上的收缩也就大于垂直流动方向上的收缩。
由于在两个垂直方向上的收缩不均衡,塑件必然产生翘曲变形。
为了尽量减少由于分子取向差异产生的翘曲变形,应创造条件减少流动取向及缓和取向应力的松驰,其中最为有效的方法是降低熔料温度和模具温度。
在采用这一方法时,最好与塑件的热处理结合起来,否则,减小分子取向差异的效果往往是暂时性的。
因为料温及模温较低时,熔料冷却很快,塑件内会残留大量的内应力,使塑件在今后使用过程中或环境温度升高时仍旧出现翘曲变形。
如果塑件脱模后立即进行热处理,将其置于较高温度下保持一定时间再缓冷至室温,即可大量消除塑件内的取向应力,热处理的方法为;脱模后将塑件立即置于37.5~43度温水中任其缓慢冷却。
(2)冷却不当。
如果模具的冷却系统设计不合理或模具温度控制不当,塑件冷却不足,都会引起塑件翘曲变形。
特别是当塑件壁厚的厚薄差异较大时,由于塑件各部分的冷却收缩不一致,塑件特别容易翘曲。
因此,在设计塑件的形体结构时,各部位的断面厚度应尽量一致。
此外,塑料件在模具内必须保持足够的冷却定型时间。
例如。
硬质聚氯乙烯的导热系数较小,若其塑件的中心部位未完全冷却就将其脱模,塑件中心部位的热量传到外部,就会使塑件软化变形。
对于模具温度的控制,应根据成型件的结构特征来确定阳模与阴模,模芯与模壁,模壁与嵌件间的温差,从而利用控制模具各部位冷却收缩速度的差值来抵消取向收缩差,避免塑件按取向规律翘曲变形。
对于形体结构完全对称的塑件,模温应相应保持一致,使塑件各部位的冷却均衡。
值得注意是,在控制模芯与模壁的温差时,如果模芯处的温度较高,塑件脱模后就向模芯牵引的方向弯曲,例如,生产框形塑件时,若模芯温度高于型腔侧,塑件脱模后框边就向内侧弯曲,特别是料温较低时,由于熔料流动方向的收缩较大,弯曲现象更为严重。
还需注意的是,模芯部位很容易过热,必须冷却得当,当模芯处的温度降不下来时,适当提高型腔侧的温度也是一种辅助手段。
对于模具冷却系统的设计,必须注意将冷却管道设置在温度容易升高,热量比较集中的部位,对于那些比较容易冷却的部位,应尽量进行缓冷,使塑件各部位的冷却均衡。
通常,模具的型腔和型芯应分别冷却,冷却孔与型腔的距离应适中,不宜太远或太近,一般控制在15~25mm范围内;水孔的直径应大于8mm,冷却小孔的深度不能太浅,水管及管接头的内径应与冷却孔直径相等,冷却孔内的水流状态应为紊流,流速控制在0.6~1.0m/s范围内,冷却水孔的总长度应在1.2~1.5m以下,否则压力损失太大;冷却水入口与出口处温度的差值不能太大,特别是对于一模多腔的模具,温差应控制在2度以下。
(3)模具浇注系统不合理。
模具浇注系统的结构参数是影响塑件形位尺寸的重要因素,特别是模具浇口的设计涉及到熔料在模具内的流动特性,塑件内应力的形成以及热收缩变形等。
如合理地确定浇口位置及浇口类型,往往可以较大程度地减少塑件的变形。
在确定浇口位置时,不要使熔料直接冲击型芯,应使型芯两侧受力均匀;对于面积较大的矩形扁平塑件,当采用分子取向及收缩大的树脂原料时,应采用薄膜式浇口或多点式侧浇口,尽量不要采用直浇口或分布在一条直线上的点浇口;对于圆片形塑件,应采用多点式针浇口或直接式中心浇口,尽量不要采用侧浇口;对于环型塑件,应采用盘形浇口或轮辐式十字浇口,尽量不要采用侧浇口或针浇口;对于壳形塑件,应采用直浇口,尽量不要采用侧浇口。
此外,在设计模具的浇注系统时,应针对熔料的流动特性,使流料在充模过程中尽量保持平行流动,这样,尽管成型后的塑件在相互垂直方向上的收缩有差别,但不会引起很大的翘曲变形。
(4)模具脱模及排气系统设计不合理。
如果塑件在脱模过程中受到较大的不均衡外力的作用会使其形体结构产生较大的翘曲变形。
例如,模具型腔的脱模斜度不够,塑件顶出困难,顶杆的顶出面积太小或顶杆分布不均,脱模时塑料件各部分的顶出速度不一致以及顶出太快或太慢,模具的抽芯装置及嵌件设置不当,型芯弯曲或模具强度不足,精度太差,定位可靠等都会导致塑件翘曲变形。
对此,在模具设计方面,应合理确定脱模斜度,顶杆位置和数量,提高模具的强度和定位精度;对于中小型模具,可根据翘曲规律来设计和制作反翘曲模具,将型腔事先制成与翘曲方向相反的曲面,抵消取向变形,不过这种方法较难掌握,需要反复试制和修模,一般用于批量很大的塑件。
在模具操作方面,应适当减慢顶出速度或增加顶出行程。
此外,模具排气不良对于塑件的翘曲变形也有一定的影响,应予以注意。
对于容易翘曲变形的塑件,可以采用整形处理技术,把塑件放入适合其外型结构的木制夹具中强制定型,但要注意对夹具中的塑件不可施加压力,应让其自由收缩,可适当辅以冷却来促使塑件尽快定型;对于周转箱等箱体类塑件,可以利用支板或框架定型,防止其收缩或膨胀。
(5)工艺操作不当。
在工艺操作过程中,如果注射压力太低,注射速度太慢,不过量充模条件下保压时间及注射,周期太短,熔料塑化不均匀,原料干燥处理时烘料温度过高以及塑件退火处理工艺控制不当,都会导致塑件翘曲变形。
对此,应针对具体情况,分别调整对应的工艺参数。