材料成型工艺与设备
机械工程材料成型及工艺

机械工程材料成型及工艺在机械工程中,材料成型主要包括以下几个方面:锻造、压力加工、冷成型、热成型、焊接和铸造等。
这些成型方式根据材料的性质和产品的设计要求选择不同的加工方法和工艺。
锻造是一种通过加热和施加压力来改变原始材料形状的方法。
它可以改变材料的内部结构和物理性质,提高材料的强度和韧性,并将其加工成各种形状的零件。
锻造分为冷锻和热锻两种方式,冷锻适用于一些具有良好延展性的材料,而热锻主要适用于高硬度的合金材料。
压力加工是通过施加压力来使材料发生塑性变形的方法。
它主要包括拉伸、压缩、弯曲、剪切等加工过程。
压力加工可以使材料具有更高的强度、硬度和韧性,并且可以通过精确的控制来获得各种形状和尺寸的零件。
冷成型是指在常温下对金属材料进行塑性加工的方法。
它主要包括冲压、拉伸、挤压、弯曲等加工过程。
冷成型可以保持材料的硬度和强度,同时可以通过模具和设备的精确控制来得到高精度的成型零件。
热成型是指在高温下对金属材料进行塑性加工的方法。
它主要包括热挤压、热压缩、热拉伸、热弯曲等加工过程。
热成型可以使材料的塑性增加,改善材料的流动性和可塑性,从而得到复杂形状的零件。
焊接是将两个或多个材料通过加热或施加压力使其在原子层面上相互结合的方法。
它主要用于连接零件、修复损坏的零件和制造复合材料等方面。
焊接的方式有多种,包括电弧焊、气体焊、激光焊等,可根据不同的需求选择适当的焊接方式。
铸造是通过将熔融的金属或合金注入到模具中,经过冷却和凝固后得到特定形状的零件或产品的方法。
铸造是一种常用的成型方式,可以生产大批量、复杂形状的零件,同时也可以制造出内部空腔的零件。
总之,机械工程材料成型及工艺是实现产品设计和制造的重要环节。
不同的成型方式和工艺可根据材料的性质和产品的要求灵活选择,通过合理的加工和控制,可以获得高精度、高质量的零件和产品。
不同的材料及成型工艺的主要设备及其作用

不同的材料及成型工艺的主要设备及其作用一、概述在制造业中,材料和成型工艺是产品制造的关键因素。
随着科技的不断进步,越来越多的材料和成型工艺被应用于生产过程中。
为了实现高效、高质的制造,主要设备也经历了不断的改进和发展。
本文将对不同的材料及成型工艺的主要设备及其作用进行详细的介绍。
二、材料分类及对应设备1.金属材料金属材料在制造业中占有重要地位,常用的金属材料包括钢铁、铜、铝等。
针对这些金属材料的加工,主要设备包括:熔炼炉、轧机、冲压机、焊接机等。
这些设备的作用是熔炼金属、轧制金属板材、冲压金属零件以及焊接金属部件等。
2.塑料材料塑料材料因其轻便、耐腐蚀等特性广泛应用于各个领域。
针对塑料材料的加工,主要设备包括:注塑机、挤出机、热压成型机等。
注塑机的作用是将熔融状态的塑料注入模具中,冷却后得到所需形状的塑料零件;挤出机则是通过螺杆旋转产生的压力,将熔融状态的塑料挤出成连续的型材;热压成型机则是利用热压工艺将塑料片材热压成所需形状的制品。
3.复合材料复合材料是由两种或两种以上材料组成的新型材料,具有优异的性能。
针对复合材料的加工,主要设备包括:预浸料设备、热压罐、缠绕机等。
预浸料设备的作用是将树脂与纤维预先混合,制成预浸料;热压罐的作用是将复合材料在高温高压下固化成型;缠绕机则是通过将纤维缠绕在芯模上,制成所需形状的复合材料制品。
三、成型工艺与设备的作用1.注塑成型工艺与注塑机注塑成型工艺是一种常见的塑料加工工艺,主要设备为注塑机。
注塑机的作用是将熔融状态的塑料注入模具中,经过冷却固化后开模取出塑料制品。
注塑成型工艺的特点是生产效率高、适用范围广,可以生产各种形状和尺寸的塑料制品。
2.挤出成型工艺与挤出机挤出成型工艺是一种常见的塑料加工工艺,主要设备为挤出机。
挤出机的作用是将塑料原料加热熔融,通过螺杆将熔融状态的塑料推挤出模头,冷却后形成连续的型材或管材。
挤出成型工艺的特点是连续生产、生产效率高,可以生产各种规格的型材和管材。
手煳成型工艺及设备

• 2)、引发剂
• 引发剂可以产生自由基,引发树脂体系进行固化反应。引 发剂一般为过氧化物,其通式为 ROOR`。引发剂的主要类 型有:氢过氧化物、酸过氧化物、酮过氧化物、酯过氧化 物、二酰基过氧化物。
• 最常用的有: 过氧化二苯甲酰
促进剂及用量 0
0.01%环烷酸钴 0
0.01%环烷酸钴
固化时间 48×60min
84min 28×60min
60min
• 4) 阻聚剂 • 为了增加不饱和聚酯树脂的贮存稳定性,调节适
用期,常在聚酯树脂中加入阻聚剂。(一般在树 脂生产过程中就加入) • 最常用的阻聚剂有:对苯二酚、叔丁基对苯二酚、 硝基苯、亚硫酸盐等 自速由度基慢与10苯4倍乙,烯一的般反聚应酯速树度脂比制自品由固基化与时O,2的表反面应应 覆盖聚酯薄膜。若不用薄膜覆盖,也应使成型表 面形成与空气隔离的物质如蜡类,否则自由基与 周造成围表空面气固中化的不O2完、全H而23.3.1 不饱和聚酯树脂的固化
poor adhesion with a incompatible silane coupling agent.
good adhesion with a compatible silane coupling agent.
(4)玻璃纤维的处理方法 ①后处理法:(对于“纺织型浸润剂”) 第一步除去浸润剂,有两种方法。 a、洗涤法:在皂水或有机溶液中清洗,然后烘干。 b、热处理法:(250℃~450℃) 1h。 第二步用表面处理剂处理(要求产品质量较高时), 处理步骤为: 浸渍-水洗-烘干。
2.3.2.2 铺层控制
搭接产品外形发生变化 铺层的拼接形式
材料成形设备考试试题及答案

衢州学院2015—2016学年第1学期
《材料成型工艺及设备》课程期末考试试题答案(A) 专业、班级:机械设计制造及自动化3班姓名:学号:
三、简述题(每题5分三小题共15分)根据下面题意写出答案
题目一:简述曲柄压力机中飞轮的特点及其作用。
特点:半径大,质量大,中间薄,边缘厚
作用:储存和释放能量,带动曲柄转动使得整个曲柄连杆滑块进行运动
题目二:写出不小于3种液压机典型的结构形式。
1)梁柱组合式:典型的形式。
常见的有三梁四柱结构,由上横梁、下横梁、活动横梁,四个立柱与12个内外螺母组成一个框架。
2)单臂式:主要用于小型液压机,机架整体为铸钢结构或者钢板焊接结构,结构简单,刚性较差有时笨重。
3)双柱下拉式:两根立柱以及上下横梁组成一个可动封闭框架。
中心低稳定性好,抗偏心载荷性能好。
4)框架式:整个框架可整体焊接或者整体铸钢。
刚性好、导向精度高、疲劳能力较强。
题目三:卧式冷压室压铸机与立式冷压室压铸机相比,卧式冷压室压铸机的优缺点。
卧式与立式冷压室压铸机相比,其压室结构简单,故障少,维修方便,易于实现自动化;金属液流程短,压力和热量损失少,铸件致密性好。
但卧式冷压室压铸机压室内德金属液会与空气接触,产生氧化表面较大,而且氧化渣等杂质会进入模腔,影响压铸件质量。
四、补图题(每题5分四小题共20分)补全下列各题中的图
题目一:
题目二:请在空白处填写部件的名称。
题目三:请在空白处填写部件的名称。
1合模装置2注射装置3液压传动系统4电器控制系统题目四:请在空白处填写部件的名称。
胶粉、沥青、再生胶的生产工艺与设备
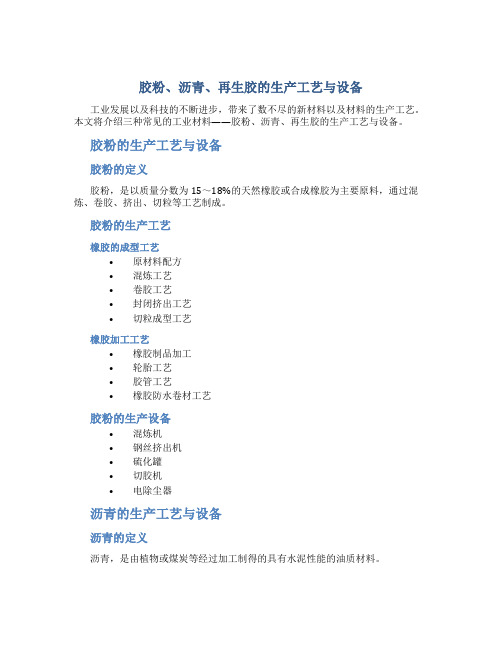
胶粉、沥青、再生胶的生产工艺与设备工业发展以及科技的不断进步,带来了数不尽的新材料以及材料的生产工艺。
本文将介绍三种常见的工业材料——胶粉、沥青、再生胶的生产工艺与设备。
胶粉的生产工艺与设备胶粉的定义胶粉,是以质量分数为15~18%的天然橡胶或合成橡胶为主要原料,通过混炼、卷胶、挤出、切粒等工艺制成。
胶粉的生产工艺橡胶的成型工艺•原材料配方•混炼工艺•卷胶工艺•封闭挤出工艺•切粒成型工艺橡胶加工工艺•橡胶制品加工•轮胎工艺•胶管工艺•橡胶防水卷材工艺胶粉的生产设备•混炼机•钢丝挤出机•硫化罐•切胶机•电除尘器沥青的生产工艺与设备沥青的定义沥青,是由植物或煤炭等经过加工制得的具有水泥性能的油质材料。
沥青的生产工艺裂变法生产沥青•原油裂解•轻油分离•催化剂再生•沥青提取储存与配制辅助剂•储罐的选用•辅助剂的选择沥青的生产设备•裂解炉•降温器•沥青蒸汽回收器•沥青储罐•沥青泵再生胶的生产工艺与设备再生胶的定义再生胶,是指废旧轮胎经过一系列工艺处理后,降解、分离、复合再制成新胶粉。
再生胶的生产工艺废旧轮胎处理•轮胎分拣•脱钢处理•脱油处理•磨粉处理再生胶生产工艺•封闭挤出•筛分•磨粉•除杂•包装再生胶的生产设备•脱油机•封闭挤出机•切片机•磨粉机•除杂机总结胶粉、沥青、再生胶是一种重要的材料,在各个领域都有广泛的应用。
通过本文所介绍的生产工艺与设备,可以更加清晰地了解这些材料的生产过程。
内高压成型设备的形变机理与成型工艺分析

内高压成型设备的形变机理与成型工艺分析内高压成型设备是一种常用于金属成型的工艺装备,通过在金属材料内部施加高压力,使其发生塑性变形,从而实现物体的成型。
本文将对内高压成型设备的形变机理与成型工艺进行分析,以便更好地理解和应用这种成型方法。
首先,我们来了解一下内高压成型设备的形变机理。
内高压成型通过施加高压力使金属材料产生塑性变形,这是由于金属材料的塑性本质决定的。
金属材料具有可塑性,即在一定条件下能够发生形状和尺寸的可逆变化。
在内高压成型过程中,金属材料受到高压力的作用,原子间的力发生改变,使得原子间的晶格结构发生塑性变形。
通过改变内部晶格的形态,金属材料得以在内部形成所需的形状,并通过外力的作用而保持该形状。
内高压成型设备的成型工艺包括以下几个关键步骤:模具设计、填充材料选择、压力控制和冷却处理。
首先是模具设计。
模具是内高压成型的重要组成部分,直接决定了成型产品的形状和尺寸。
模具应具备高压承受能力和良好的密封性,以保证金属材料能够在其内部形成所需形状。
在模具设计过程中,需要考虑到成型产品的结构特点,合理安排模具的形状和尺寸,以提高成型的效率和质量。
填充材料的选择也是一个重要的环节。
填充材料在内高压成型中起到填充模具空腔的作用,其性能将直接影响成型产品的质量。
常用的填充材料有铝、铜、镁等金属材料。
在选择填充材料时,需要考虑其塑性和热导性能,以满足成型工艺的要求。
压力控制是内高压成型的核心环节。
在成型过程中,施加的压力应适中,过大会导致金属材料的脆性断裂,过小则无法形成所需形状。
压力控制的关键在于找到一个合适的平衡点,既能保证形状的准确性,又能避免成型材料的失效。
随着设备技术的不断发展,自动化压力控制系统的应用也越来越广泛,有效提高了成型的精度和稳定性。
最后是冷却处理。
在内高压成型后,成型产品需要进行冷却处理,以保持其所需的形状和性能。
冷却处理可以通过自然冷却或加速冷却的方式进行。
自然冷却时间较长,但成型产品的性能稳定性较好;而加速冷却可以通过水冷或风冷等方式进行,可以缩短冷却时间,但易导致成型产品的内部应力较大,需要进行进一步的应力消除处理。
常见的材料成型及加工工艺流程
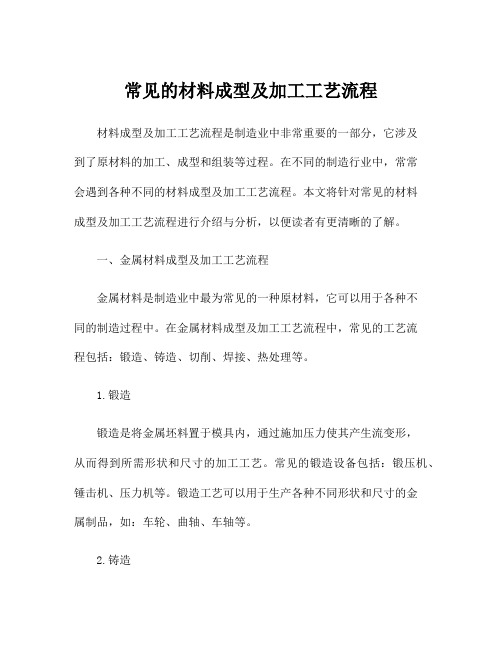
常见的材料成型及加工工艺流程材料成型及加工工艺流程是制造业中非常重要的一部分,它涉及到了原材料的加工、成型和组装等过程。
在不同的制造行业中,常常会遇到各种不同的材料成型及加工工艺流程。
本文将针对常见的材料成型及加工工艺流程进行介绍与分析,以便读者有更清晰的了解。
一、金属材料成型及加工工艺流程金属材料是制造业中最为常见的一种原材料,它可以用于各种不同的制造过程中。
在金属材料成型及加工工艺流程中,常见的工艺流程包括:锻造、铸造、切削、焊接、热处理等。
1.锻造锻造是将金属坯料置于模具内,通过施加压力使其产生流变形,从而得到所需形状和尺寸的加工工艺。
常见的锻造设备包括:锻压机、锤击机、压力机等。
锻造工艺可以用于生产各种不同形状和尺寸的金属制品,如:车轮、曲轴、车轴等。
2.铸造铸造是将金属熔化后,倒入模具中,经冷却后得到所需形状和尺寸的加工工艺。
常见的铸造工艺包括:砂型铸造、金属型铸造、压铸等。
铸造工艺可以用于生产各种不同形状和尺寸的金属制品,如:汽车零部件、机械零部件等。
3.切削切削是利用刀具对金属进行切削加工,从而得到所需形状和尺寸的加工工艺。
常见的切削设备包括:车床、铣床、磨床等。
切削工艺可以用于生产各种不同形状和尺寸的金属制品,如:螺栓、螺母、螺旋桨等。
4.焊接焊接是将金属件通过加热或加压等方法,使其熔化后再连接在一起,从而得到所需形状和尺寸的加工工艺。
常见的焊接方法包括:气焊、电弧焊、激光焊等。
焊接工艺可以用于生产各种不同形状和尺寸的金属制品,如:焊接结构、焊接零件等。
5.热处理热处理是将金属件加热至一定温度,使其组织结构发生改变后再冷却,从而得到所需性能的加工工艺。
常见的热处理方法包括:退火、正火、淬火、回火等。
热处理工艺可以用于提高金属制品的强度、硬度、韧性等性能,如:弹簧、轴承、齿轮等。
二、塑料材料成型及加工工艺流程塑料材料在制造业中也是一种非常常见的原材料,它可以用于各种不同的制造过程中。
材料成型工艺与设备1

二. 强度 强度
强度:
金属材料在外力的作用下抵抗塑性 变形和断裂的能力
按作用力性质分: 抗拉、抗压、抗剪和抗扭强度
• 塑性和强度是通过拉伸试验测定的:
σe σs
__
弹性极限
(σ0.2 )— 屈服极限
抗拉极限
σ b ____
塑性指标:
延伸率: 断面收缩率: δ 、ψ ↑
l l0 100% l0
§1. 铁碳合金的基本组织 §1 铁碳合金的基本组织
一. 铁素体 (F) (F)
铁素体:碳溶解在α-铁中形成的固溶体 (F) (α-固溶体) 晶格类型:体心立方 溶解度:600℃, 0.006%, 727℃, 0.02% 性能: 与纯铁相似. 塑性好δ=45-50%, σb≈250MPb, HB≈80 显微组织: 多边形晶粒
二. 碳素钢
二. 碳素钢
碳素钢: C < 1.5%, Si, Mn ,S ,P 杂质
低碳钢: C < 0.25%
中碳钢: 0.25 < C < 0.6% 高碳钢: 0.6 < C < 1.5% C↑→ P、Fe3C↑ → 硬度↑、塑性↓
▲ 普通碳素结构钢:
亚共析钢:
甲类钢(A0- A7):按机械性能供货
▲特征线: ACB — 液相线 DCE — 固相线 ▲结晶过程(以50%Pb,50%Sb合金为例)
L L Sb (Pb Sb) Sb
(室温组织)
490o C
252o C
第三章
铁碳合金
铁碳合金:以铁为基础的合金,基本上 由铁碳两种元素组成 钢和铁的总称
§1 铁碳合金的基本组织
复合材料成型工艺与设备

复合材料成型工艺与设备引言复合材料是由两种或两种以上不同性质的材料组成的复合结构材料。
它们通常具有较好的力学性能、化学稳定性和耐磨性,因此在航空航天、汽车制造、建筑等领域得到广泛应用。
复合材料的制备过程中,成型工艺和设备起着至关重要的作用。
本文将介绍复合材料的成型工艺和设备。
成型工艺复合材料的成型工艺主要包括手工层叠法、预浸法、自动化层叠法和注塑成型等多种方法。
手工层叠法手工层叠法是最简单的一种成型工艺,通过手工将纤维和树脂逐层叠加在一个具有一定形状的模具中,然后采用压实和固化的方式完成成型。
这种方法成本低廉,适用于小批量和特殊形状的产品制造,但生产效率低,一般只适用于简单形状的产品制造。
预浸法预浸法是将纤维与树脂预先浸渍,然后在一定的条件下进行成型。
该方法可有效提高生产效率和产品质量,广泛应用于复合材料制品的生产。
预浸法的关键是控制纤维和树脂的浸渍量和均匀性,以及固化过程中的温度、压力和固化时间。
自动化层叠法自动化层叠法通过机械手或自动化设备将预先浸渍好的纤维和树脂层叠在模具中,然后进行固化。
这种方法具有高度自动化和生产效率高的特点,适用于大批量和复杂形状的产品制造。
注塑成型注塑成型是一种将纤维和树脂混合后直接注入模具中进行成型的方法。
这种方法适用于复杂形状的产品制造,能够实现一次成型,并且可以在成型过程中进行纤维定向和树脂浸透的控制。
成型设备复合材料的成型设备通常包括模具、加热设备和压力设备等。
模具模具是复合材料成型过程中最关键的设备之一。
模具的形状和尺寸决定了最终产品的形状和尺寸。
模具材料通常选用高强度、耐磨、耐高温和耐腐蚀性能好的材料,如钢、铝合金等。
模具制作的精度和表面质量对最终产品的质量具有重要影响。
加热设备加热设备用于提供适当的温度条件以促进树脂固化和纤维的定向。
常用的加热设备包括热风循环炉、电加热板等。
在成型过程中,加热设备应能够提供均匀的温度场,确保整个产品的固化质量。
压力设备压力设备用于提供适当的压力,使纤维和树脂紧密结合,并去除成型过程中的气泡和缺陷。
成型加工的三要素
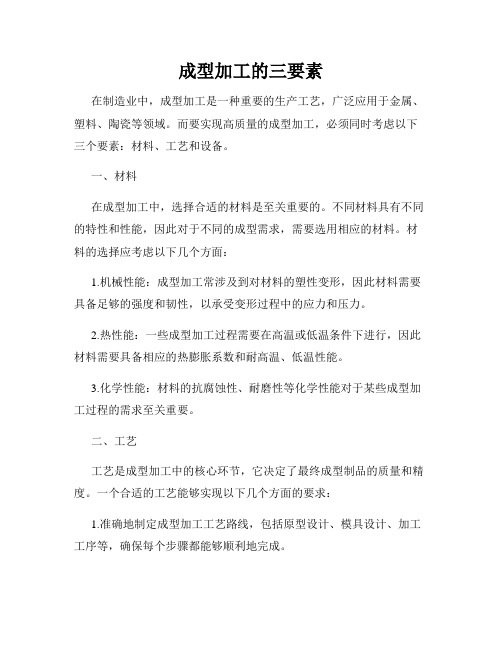
成型加工的三要素在制造业中,成型加工是一种重要的生产工艺,广泛应用于金属、塑料、陶瓷等领域。
而要实现高质量的成型加工,必须同时考虑以下三个要素:材料、工艺和设备。
一、材料在成型加工中,选择合适的材料是至关重要的。
不同材料具有不同的特性和性能,因此对于不同的成型需求,需要选用相应的材料。
材料的选择应考虑以下几个方面:1.机械性能:成型加工常涉及到对材料的塑性变形,因此材料需要具备足够的强度和韧性,以承受变形过程中的应力和压力。
2.热性能:一些成型加工过程需要在高温或低温条件下进行,因此材料需要具备相应的热膨胀系数和耐高温、低温性能。
3.化学性能:材料的抗腐蚀性、耐磨性等化学性能对于某些成型加工过程的需求至关重要。
二、工艺工艺是成型加工中的核心环节,它决定了最终成型制品的质量和精度。
一个合适的工艺能够实现以下几个方面的要求:1.准确地制定成型加工工艺路线,包括原型设计、模具设计、加工工序等,确保每个步骤都能够顺利地完成。
2.选择适当的成型加工方法,如冲压、注塑、铸造等,以满足产品的形状、尺寸和表面要求。
3.合理设定工艺参数,如温度、压力、速度等,以确保成型加工的稳定性和一致性。
三、设备除了材料和工艺,适当的设备也是成型加工的关键要素之一。
合适的设备能够提供以下方面的支持:1.高精度的设备能够保证成型加工的尺寸精度和表面质量,提高产品的质量和性能。
2.先进的设备能够提高生产效率,缩短生产周期,降低成本。
3.灵活多样的设备能够适应不同形状和尺寸的产品需求,提供定制化的解决方案。
综上所述,材料、工艺和设备是影响成型加工质量和效率的三个关键要素。
只有在这三个要素的合理协调下,才能够实现高质量和高效率的成型加工。
因此,在进行成型加工时,必须时刻重视这三个要素,并对其进行充分的调整和优化,以满足不同应用领域的需求。
复合材料成型工艺以及设备要求

生产中建立起来的成型方法有:
• 8. 模压成型 9. 注射成型
10. 挤出成型 11. 纤维缠绕成型 12. 拉挤成型 13. 连续板材成型 14. 层压或卷制成型 15. 热塑性片状模塑料热冲压成型 16. 离心浇铸成型 其中,9,10,15为热塑性树脂基复合材 料成型工艺
复合材料成型工艺以及设备要求
• 3) 其它影响因素 : 胶液体积 、环境温度与湿度 、制品
厚度与表面积大小 、交联剂蒸发损失 、 抑制聚合反应的助剂、填料加入量。 • 4) 配制方法
按配方比例先将引发剂等助剂和树脂 混合均匀备用,操作前再加入促进剂搅 拌均匀。加入引发剂的树脂胶液,贮存 期不能过长。一次配胶量不要过多。
3. 色料:改变制品外观。一般不使用有机颜料和 碳黑
复合材料成型工艺以及设备要求
3) 增强材料
1).玻璃纤维 A一玻璃纤维 E一玻璃纤维 (无碱) S一高强玻璃纤维 M一高弹玻 璃纤维和L一防辐射玻璃纤维 ,c-中碱 玻璃纤维 玻璃纤维制品 无捻粗纱、短切纤维毡 、 无捻粗纱布 、 玻璃纤维细布 、 单向 织物
• 2). 碳纤维聚丙烯睛(PAN)纤维、沥 青纤维和粘胶纤
• 3). Kevlar纤维
复合材料成型工艺以及设备要求
6.2.2 手糊成型模具与脱模剂
• 6.2.2.1 模具结构与材料 1) 模具结构 --单模和对模两类 2) 成整体式或拼装式
复合材料成型工艺以及设备要求
6.2.2.2. 模具材料
复合材料成型工艺以及设备要求
复合材料成型工艺以及设备要求
6.2 手糊成型工艺及设备
• 手糊成型又称接触成型。是用纤维增强 材料和树脂胶液在模具上铺敷成型,在室 温或加热无压(或低压)条件下固化,脱 模成制品的工艺方法。
材料工艺与设备范文

材料工艺与设备范文材料工艺是指将原材料经过一系列加工和制造过程,转化为最终产品的过程。
通过合适的工艺流程和设备,实现对原材料的加工和改造,以达到产品所需的性能要求和外观要求。
材料工艺的发展对于现代工业生产具有重要的意义,它不仅对产品质量和性能起着决定性的作用,还对产能和生产效率有着直接影响。
因此,合理选择和使用适当的材料工艺和设备,对于企业的发展和竞争力至关重要。
材料工艺的分类材料工艺可以分为原材料处理、加工工艺和成型工艺三个阶段。
原材料处理是指对原材料进行预处理,以去除其表面的污染物和杂质,保证产品的质量和安全性。
常用的原材料处理方法包括清洗、研磨、酸洗等。
加工工艺是指将经过预处理的原材料进行切割、焊接、冲压、旋压等加工操作,以实现产品的形状和尺寸要求。
加工工艺的选择要根据产品的要求和原材料的性质来确定。
成型工艺是指将经过加工的原材料按照一定的成型方法,转化为最终产品的工艺过程。
常见的成型工艺包括铸造、锻造、挤压、注塑等。
成型工艺的选择要根据产品的形状和结构,以及原材料的特性来确定。
材料工艺的设备材料工艺的设备是指用于实施材料加工和转化的各种机械装置和工具。
根据不同的工艺流程和产品要求,适用的设备也有所不同。
常见的材料工艺设备包括切割机、研磨机、冲压机、焊接机、注塑机等。
这些设备根据工艺的不同,可以实现不同的操作和加工过程。
例如,切割机可以将原材料按照要求的形状和尺寸进行切割;研磨机可以对原材料进行表面处理,提高产品的平滑度和光洁度;冲压机可以将原材料通过压力和模具进行成型,实现复杂的形状和结构;焊接机可以将不同部件进行连接,形成整体产品;注塑机可以将熔化的塑料注入模具中,形成具有预定形状的产品。
随着科技的进步和工业的发展,材料工艺设备也在不断创新和改进。
例如,出现了数控机床、激光切割机、自动焊接机等先进的设备,大大提高了加工和制造的精度和效率。
此外,随着环保意识的增强,节能和低碳的设备越来越受到关注和应用,以减少资源浪费和环境污染。
《复合材料工艺与设备》第六章层压成型工艺及设备

《复合材料工艺与设备》第六章层压成型工艺及设备第六章层压成型工艺及设备6层压成型工艺及设备6.1概述6.1.1层压工艺的发展现状及前景课件6.1.1层压工艺的发展现状及前景层压工艺:是指将浸有或涂有树脂的片材层叠,在加热加压条件下,固化成型玻璃钢制品的一种成型工艺。
起始于30年代,目前在航空、航天、汽车、船舶、电讯等工业广泛应用。
层压成型工艺制品已经成为不可缺少的工程材料之一。
主要产品有:玻璃布层压板、木质层压板、棉布层压板、纸质层压板、石棉纤维层压板、复合层压板等。
第六章层压成型工艺及设备6.1.2层压工艺特点及应用课件6.1.2层压工艺的特点及应用工艺特点:生产的机械化、自动化程度较高;产品质量稳定;但一次性投资较大,适合于批量生产。
层压板可分为:纸层压板、木层压板、棉纤维层压板、玻璃纤维层压板等品种。
电绝缘部件;薄板适合于各领域;可用于制造齿轮、轴承、皮带轮等结构材料;用于飞机、汽车、船舶、电气工程等领域。
主要应用范围:例如:复铜箔层压板,用于制造印刷电路板。
第六章层压成型工艺及设备6.2胶布制备工艺及设备6.2.1制备工艺6.2.1.1原材料增强材料:课件玻璃布,石棉布,合成纤维布,玻璃毡,石棉毡,石棉纸,牛皮纸等。
酚醛树脂、氨基树脂、环氧树脂、不饱和聚酯树脂、有机硅树脂等。
6.2.16.2.1制备工艺树脂:6.2.1.2胶布制备工艺过程玻璃纤维布经化学处理或热处理后,浸渍树脂胶液,并控制胶含量。
在一定温度、时间条件下烘干,使树脂由A阶转到B阶,即得到需要的玻璃纤维胶布。
如P136工艺流程图。
第六章层压成型工艺及设备6.2.1.3胶布制备工艺参数主要有:胶液粘度、浸胶时间、烘干温度与时间、牵引张力。
(1)、胶液粘度课件一般通过胶液浓度及环境温度来控制。
浓度的控制往往采用测试密度的方法来实现。
各种玻璃布所用的胶液密度见P137,表6-1。
(2)、浸胶时间一般控制在15~45,不同的布浸透时间不同。
复合材料工艺与设备

复合材料工艺与设备概述复合材料工艺与设备是指生产和加工复合材料的一系列流程和所使用的设备。
复合材料是一种由两种或多种不同材料组成的材料,具有很高的强度和轻质化的特点。
复合材料在航空航天、汽车、建筑、体育用品等领域得到广泛应用。
本文将介绍复合材料的常见工艺和所使用的设备。
工艺流程复合材料的生产和加工过程主要包括预处理、树脂浸渍、固化、成型和加工等环节。
1.预处理预处理阶段是为了确保复合材料的质量和性能,包括材料的清洁、去除表面污染物和氧化物等。
一般使用化学溶剂或机械方法进行清洗和表面处理。
2.树脂浸渍树脂浸渍是将纤维材料与树脂浸渍在一起形成复合材料的过程。
树脂是复合材料中起到粘合作用的关键材料,其中常用的树脂有环氧树脂、聚酰亚胺树脂等。
树脂浸渍过程包括浸渍、除泡、挤出等步骤。
3.固化固化是指树脂在一定温度和时间下发生化学反应,使复合材料具有一定的强度和硬度。
常用的固化方式有热固化和光固化。
热固化需要加热设备,而光固化则通过紫外线或可见光来触发化学反应。
4.成型成型是将浸渍且已固化的复合材料按照需要的形状进行加工和形成。
常见的成型方法有手工层压、热压和真空吸塑等。
成型过程需要注意材料的层间结构、纤维取向和树脂厚度等。
5.加工加工是指根据复合材料的用途和要求进行切割、修整、钻孔、打磨等加工工艺。
常用的加工设备有切割设备、钻孔设备、砂轮设备等。
设备介绍复合材料工艺所使用的设备主要包括涂胶机、自动抽屉加载机、固化炉、层压机和CNC加工中心等。
1.涂胶机涂胶机是将树脂均匀涂布在纤维材料上的设备。
它通过涂胶滚轮将树脂涂布在纤维上,确保树脂的浸渍均匀和厚度一致。
2.自动抽屉加载机自动抽屉加载机用于自动将纤维材料和树脂放入生产线中进行加工。
通过自动化的操作,提高生产效率和产品质量。
3.固化炉固化炉是用于固化树脂的设备,它提供一定的温度和环境条件,使树脂发生化学反应,形成固态的复合材料。
固化炉一般有恒温控制和可调湿度的功能。
热成型工艺与设备概述

热成型工艺与设备概述热成型设备是用于热成型工艺的专用设备,通常包括加热系统、模具、冷却系统、控制系统等组成部分。
加热系统用于将材料加热至所需的温度,通常采用电加热、燃气加热、蒸汽加热等方式。
模具是用于成型材料的工具,可以根据产品的形状设计不同的模具。
冷却系统用于控制产品的冷却速度,以保证产品的质量。
控制系统则用于监控和调节整个成型过程,确保产品符合要求。
热成型工艺和设备在现代工业生产中扮演着重要的角色,它不仅可以提高生产效率,降低生产成本,还能够生产出高质量的产品。
随着科技的发展和进步,热成型工艺和设备也在不断地进行创新和改进,以满足不同产品的生产需求。
同时,热成型工艺和设备也面临着一些挑战,比如如何提高能源利用率、如何进一步提高产品质量等问题,这需要各界共同努力,不断进行技术研发和创新,推动热成型工艺和设备的发展。
热成型工艺和设备在现代工业生产中的应用非常广泛,可以用于生产各种不同材料的制品,比如塑料制品、橡胶制品、金属制品等。
热成型工艺主要包括热压成型、热吹成型、热拉伸成型等,每种成型工艺都有其适用的材料和产品类型。
而热成型设备的技术水平和性能特点对产品的质量和生产效率具有重要影响。
热成型设备通常按照不同的工艺特点和产品类型进行设计和制造。
比如,热压成型设备通常包括传热系统、压力系统和控制系统。
传热系统通常由加热装置和冷却装置组成,加热装置通常采用电热管、燃气加热器等,通过传热媒介将热量传输到模具内,使塑料或橡胶材料达到软化或熔融状态。
压力系统则通过液压缸或气压缸对模具进行压合,将软化或熔融的材料填充模腔,并保持一定的成型压力。
控制系统则通过温度、压力、时间等参数的调节和监控,确保产品的成型质量和生产效率。
热吹成型设备常用于塑料制品的制造,包括吹塑机、注塑机等。
热吹成型设备通常由加料系统、加热系统、成型系统、冷却系统和控制系统组成。
加料系统用于将原料塑料颗粒或颗粒状的塑料熔融后送入模具。
加热系统通常采用电热器或红外加热器,将模具加热到一定温度,软化塑料颗粒。
- 1、下载文档前请自行甄别文档内容的完整性,平台不提供额外的编辑、内容补充、找答案等附加服务。
- 2、"仅部分预览"的文档,不可在线预览部分如存在完整性等问题,可反馈申请退款(可完整预览的文档不适用该条件!)。
- 3、如文档侵犯您的权益,请联系客服反馈,我们会尽快为您处理(人工客服工作时间:9:00-18:30)。
• 塑性和强度是通过拉伸试验测定的:
σe __ 弹性极限 σs (σ0.2 )— 屈服极限
σ b ____ 抗拉极限
8
塑性指标:
延伸率: 断面收缩率:
l l0 100%
l0
δ、ψ↑ —→ 塑性↑
强度指标:
屈服强度:
抗拉强度:
σ≧σs , 塑性变形; σ≧σb , 破坏
9
三. 刚度
三. 刚度
13
五. 冲击韧姓
冲击韧姓: 金属材料抵抗冲击载荷作用下断裂的能力. 指标: 冲击值.(一次摆锤弯曲试验测定(GB/T229-94))
k
Ak F
(J/m2 )
● 冲击韧性不能直接用于强度计算: (1) 冲击值受许多因素影响: 试样形状、表面粗糙 度、内部组织、温度等 (2)在冲击载荷下工作的机件,很少是受到大能量 一次冲击破坏的
学习本课程的基本要求:
了解常用金属材料的一般性质、应用范围和选择原则 初步掌握各种主要加工方法的实质、工作特点和基本
原理 了解各种主要加工方法的设备和工具的工作原理、大
致结构和应 用范围 初步掌握零件的结构性和常用金属材料的工艺性
3
第一篇 金属材料导论
金属材料: ● 纯金属:
● 合 金:以一种金属为基础,加入其它金属或非金
部分有界面分开的均匀组成部分.
固体合金中的相结构:
固溶体、 金属化合物、 机械混合物
29
一. 固溶体
固溶体: 溶质原子溶入溶剂晶格而仍保 持溶剂晶格类型的金属晶体.
晶格类型: 同溶剂 固溶强化:溶剂晶格畸变,塑性变形阻
力增加,强度、硬度升高。 例子:铁素体(C, α-Fe)
30
固溶体类型:
●置换固溶体: ●间隙固溶体:
31
固溶强化:
32
二. 金属化合物
金属化合物: 合金各组元的原子按一定的整 数比化合而成的新的金属晶体
晶格类型: 复杂 (既不是溶剂的也不是溶质 的晶格)
性能: 熔点高、硬度高、脆性大(塑性小) 例子: Fe3C
33
么么么么方面
Sds绝对是假的
三. 机械混合物
机械混合物:结晶过程所形成的两相混合组织。
晶格类型: 各相均保持其原有的晶格。
性能:介于各组成相之间。 取决于:各相的性能和比例、 各相的形状、大小和分布。
例子:珠光体 P (F + Fe3C)
35
§2 二元合金状态图的建立
§4. 二元合金状态图的建立
▪合金结晶过程: 形核、长大 ▪合金结晶冷却曲线: 无结晶平台,即结晶是在
(F)
(α-固溶体)
晶格类型:体心立方
溶解度:600℃, 0.006%,
727℃, 0.02%
性能: 与纯铁相似. 塑性好δ=45-50%,
σb≈250MPb, HB≈80
显微组织: 多边形晶粒
43
二. 奥氏体 (A)
奥氏体:碳溶解在γ-铁中形成的固溶体
(A)
(γ-固溶体) (>727℃)
亚共晶生铁:2.11 < C < 4.3%
共晶生铁:
C = 4.3%
过共晶生铁: 4.3 < C <6.69%
53
三. 结晶过程分析 共析钢: A → P(F+ Fe3C)
(室温组织)
54
亚共析钢:
A→A+F → F + P(F+ Fe3C) (室温组织)
过共析钢:
A → A + Fe3CⅡ → Fe3CⅡ + P(F+ Fe3C) (室温组织)
L 490oCL Sb 252oC(Pb Sb) Sb
(室温组织)
41
第三章 铁碳合金
铁碳合金:以铁为基础的合金,基本上 由铁碳两种元素组成 钢和铁的总称
§1 铁碳合金的基本组织
§1. 铁碳合金的基本组织 §1 铁碳合金的基本组织
42
一. 铁素体 (F) (F)
铁素体:碳溶解在α-铁中形成的固溶体
刚度:金属材料在受力时抵抗弹性变形的能力
指标: 弹性模数: 弹性范围内, 应力与应变的比.
E =σ/ε
弹性模数 ↑-→ 刚度↑
. 硬度
10
四. 硬度
硬度: 金属材料抵抗更硬的物体压入其内的能力。
(在小的体积范围内,抵抗弹性变形、塑性 变形或断裂的能力)
指标:布氏硬度 ( HB ) 洛氏硬度 ( HR )
25
晶轴:晶核生长线速度最大的方向
晶粒:
晶界:晶粒之间的接触面
多晶体:晶粒细↑→ 晶界多↑ →金属
的结合力↑ →机械性能↑
晶核数目↑→晶粒细↑ (铸造中的变质处理)
金属冷却速度↑ → 晶粒细↑(如金属型铸造, 砂型铸造比较冷速)
26
二. 金属的同素异构转变
同素异构性: 一种金属能以几种晶格类型存在的性质。 同素异构转变: 金属在固态时改变其晶格类型的过程。
(2)零件的加工工艺性
二. 化学性能
化学性能: 金属材料抵抗各种化学作用的能力 如: 耐酸性、耐碱性、抗氧化性等
考虑:零件的使用。 如: 医疗器械、化工设备防腐→不锈钢
16
三. 工艺性能
工艺性能: 铸造性、可锻性、焊接性、切削加工性能等。 是物理、化学及力学性能的综合。
17
第二章 金属和合金的晶体结构与结晶
46
四. 珠光体 (P)
四. 珠光体 (P) 珠光体:铁素体和渗碳体组成的机械混合物 晶格类型: 性能: 介于铁素体和渗碳体之间。
σb≈750MPa, HB≈180 显微组织: 铁素体片和渗碳体片相间
47
48
五. 莱氏体 (Le)
莱氏体(Le):奥氏体和渗碳体组成的机械混合 物(>727℃)
某一温度范围内进行的。 ▪合金状态图: 表示合金系结晶过程的简明图解。 ▪作用: 研究合金的成分、温度和结晶组织之间的
变化规律 ▪合金状态图的建立:实验的方法
简单的二元合金状态图:以铅锑合金为例
36
37
(1)状态图的建立:
作冷却曲线 → 测转变温度点 → 作温度—成分坐标图
B
38
39
(2)状态图的应用:
硫的危害:热脆 Fe, FeS → Fe+FeS (共晶体,熔点985℃<1148,沿晶界分布)
磷的危害:冷脆 形成α固溶体, 塑性↓↓
57
58
二. 碳素钢
二. 碳素钢
碳素钢: C < 1.5%, Si, Mn ,S ,P 杂质 低碳钢: C < 0.25% 中碳钢: 0.25 < C < 0.6% 高碳钢: 0.6 < C < 1.5% C↑→ P、Fe3C↑ → 硬度↑、塑性↓
14
六. 疲劳强度
六. 疲劳强度
疲劳强度: 当材料在无数次重复或交变载荷作用下而 不致引起断裂的最大应力.
指标: 疲劳强度极限σ-1
循环基数: 钢材: 107 有色金属、高强度钢:108
15
§2 金属材料的物理、化学 §2 金属及材工料艺的性物能理、化学及工艺性能
一. 物理性能
物理性能: 比重、熔点、热膨胀性、导热性和导电性 考虑:(1)零件的使用性
(二次结晶、重结晶)
铁的同素异构转变:
Fe 1394oC Fe 912oCFe
体心
面心
体心
钢的热处理:
27
28
§ 3 §3 合金的晶体结构合金的结构
组元: 组成合金的元素。 合金: 二元合金、 三元合金 …
(黄铜:Cu,Zn) (硬铝:Al,Mg,Cu) 相: 化学成分和晶体结构相同, 并与其他
低温莱氏体(Le´):珠光体和渗碳体组成的机械 混合物( <727℃)
性能:与渗碳体相似,硬而脆
49
§2 铁碳合金状态图
Fe-Fe3C 状态图
50
一. 铁碳合金状态图中主要点和线的含义
●特征点:
51
●特征线:
ABCD 线—— 液相线
AHJECF 线——固相线 AHJE 线——钢的固相线
ECF 线——铁的固相线(共晶线),莱氏体
属,经过熔炼、烧结或其它方法制成的具 有金属性质的材料。 (如:钢、黄铜、硅铝明)
金属材料:
● 好的物理、化学、力学性能 ● 好的工艺性能
金属制品: 占80–90%
4
第一章 金属材料的主要性能
§1 金属材料的力学性能 性能
力学性能: 材料在力的作用下所表现出来的性能. (机械性能) 包括:弹性、塑性、强度、硬度、冲击韧性和疲
59
▲ 普通碳素结构钢:
亚共析钢: 甲类钢(A0- A7):按机械性能供货 乙类钢 (B0- B7): 按化学成分供货
GS 线—— A3 ES 线—— Acm PSK 线——A1 (共析线),共析反应:珠光体
52
二. 铁碳合金的分类
钢: 0 < C < 2.11% 亚共析钢:0 < C < 0.77% 共析钢: C = 0.77% 过共析钢:0.77 < C < 2.11%
生铁: 2.11 < C < 6.69%
劳强度
5
一. 弹性和塑性
弹性: 受外力作用时产生变形,外力去掉后
能恢复原来形状的性质。
弹性变形: 大小与外力成正比 塑性: 在外力作用下,产生永久变形而不致
引起破坏的性质。
塑性变形: 大小不与外力成正比
6
二. 强度 强度
强度: 金属材料在外力的作用下抵抗塑性 变形和断裂的能力
按作用力性质分: 抗拉、抗压、抗剪和抗扭强度
§§1 金1属. 的金晶属体结的构 晶体结构