钣金件加工工艺及企业标准介绍
钣金件加工工艺及企业标准介绍

右定位准确。
• 四、工艺补充面设计。五、工艺孔及刺破刀。六、拉延筋和拉延槛、七: CAE分析等。
案例
水箱上盖
案例
模块机电机支架
案例
常见定位方式:1.落料模具定位,2, 全定位,3、复合式定位。
案例
工艺孔定位
4、板料成形过程的常见缺陷及产生原因分析
现皱纹和折痕,保证凸模对板料拉紧,否则在拉延过程板料会出现波纹或皱 纹。
• • 考虑方向: • 1、降低拉延深度。第一种压料面是产品面,压料面已经定型,不涉及降低拉
延深度。压料面一般呈弯曲形状,可以使拉延深度降低。另一种是水平的压 料面,针对零件高度变化不大的形状适用。 • 2、为保证板件成型刚性,压料面的线长应小于凸模的线长,这样才能保证料 片充分拉伸且不会起皱。 • 3、压料面尽量简单,平滑光顺有利于料片流动。压料面上不允许有局部鼓 包、,凹坑和下陷,如果存在后序追加整形。压料面与各拉伸深度尽量一致,
• 分类——按程度不同分 • 1)、微观拉裂 • 工件中已产生肉眼难以看清的裂纹,一部分材料已失效 • 单纯的拉胀或单纯的弯曲引起局部拉应变过大。 • 2)、宏观拉裂 • 工件已出现肉眼可见的裂纹或断裂 • 通常主要由薄板平面内的过度拉胀引起局部拉应变过大。
• 应对措施及解决办法 • 1)、改变法向接触力和切向摩擦力的分布,降低拉裂区的拉应变值;
• 起皱和叠料 • 产生原因: • 1)、由于局部压应力过大导致薄板失稳所致,正好与拉裂的产生原因相反。 • 2)、两种应力状态容易起皱,环向应力:法向起皱与侧壁起皱失稳。 • 3)、当冲压件的周长不断减少,此时只要板料中未受支撑,区域的长度与厚
钣金工艺规范标准[详]
![钣金工艺规范标准[详]](https://img.taocdn.com/s3/m/400a4d59c950ad02de80d4d8d15abe23482f03ef.png)
钣⾦⼯艺规范标准[详]钣⾦⼯艺规1简介1.1钣⾦所⽤材料常⽤材料有:冷轧板SPCC、热轧板SPHC、电解板SECC、普通铝板及铝合⾦板AL1050、AL5052-H32,不锈钢板SUS304、覆铝锌钢板.1.2典型钣⾦件加⼯流程图⾯展开---编程---下料(剪、冲、割)----冲⽹孔----校平----拉丝----冲凸包----压铆----折弯-----焊接----⽴体拉丝----表处----组装2下料2.1数冲是⽤数控冲床加⼯,板材厚度加⼯围为:冷扎板、热扎板⼩于或等于3.0mm;铝板⼩于或等于4.0mm;不锈钢⼩于2.0mm。
2.1.1 冲孔有最⼩尺⼨要求冲孔最⼩尺⼨与孔的形状、材料机械性能和材料厚度有关。
t为材料厚度,冲孔尺⼨⼀般不⼩于1.5t。
如遇特殊情况,可参照下表:图2.1.1 冲孔形状⽰例* t为材料厚度,冲孔最⼩尺⼨⼀般不⼩于1.2mm。
冲孔最⼩尺⼨列表2.1.2 数冲的孔间距与孔边距零件的冲孔边缘离外形的最⼩距离随零件与孔的形状不同有⼀定的限制,见图2.1.2。
当冲孔边缘与零件外形边缘不平⾏时,该最⼩距离应不⼩于材料厚度t;平⾏时,应不⼩于1.5t。
2.1.3 折弯件及拉深件不可选⽤数冲下料,可选⽤⼆次激光切割。
2.1.4 螺钉、螺栓的过孔和沉头座螺钉、螺栓过孔和沉头座的结构尺⼨按下表选取取。
对于沉头螺钉的沉头座,如果板材太薄难以同时保证过孔d2和沉孔D,应优先保证过孔d2。
表1⽤于螺钉、螺栓的过孔*要求钣材厚度t≥h。
表2⽤于沉头螺钉的沉头座及过孔*要求钣材厚度t≥h。
表3⽤于沉头铆钉的沉头座及过孔2.2激光切割是⽤激光机飞⾏切割加⼯,板材厚度加⼯围为冷扎板、热扎板⼩于或等于8.0mm;不锈钢⼩于或等于4.0mm ;铝板⼩于等于5.0mm。
其优点是加⼯板材厚度⼤,切割⼯件外形速度快,加⼯灵活.缺点是会产⽣热变型,⽹孔件不宜⽤此⽅式加⼯,加⼯成本⾼!3折弯3.1折弯件的最⼩弯曲半径材料弯曲时,其圆⾓区上,外层收到拉伸,层则受到压缩。
钣金加工标准
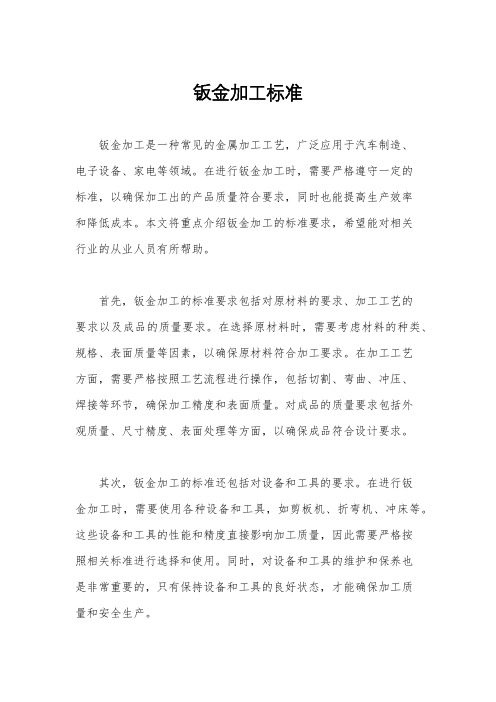
钣金加工标准钣金加工是一种常见的金属加工工艺,广泛应用于汽车制造、电子设备、家电等领域。
在进行钣金加工时,需要严格遵守一定的标准,以确保加工出的产品质量符合要求,同时也能提高生产效率和降低成本。
本文将重点介绍钣金加工的标准要求,希望能对相关行业的从业人员有所帮助。
首先,钣金加工的标准要求包括对原材料的要求、加工工艺的要求以及成品的质量要求。
在选择原材料时,需要考虑材料的种类、规格、表面质量等因素,以确保原材料符合加工要求。
在加工工艺方面,需要严格按照工艺流程进行操作,包括切割、弯曲、冲压、焊接等环节,确保加工精度和表面质量。
对成品的质量要求包括外观质量、尺寸精度、表面处理等方面,以确保成品符合设计要求。
其次,钣金加工的标准还包括对设备和工具的要求。
在进行钣金加工时,需要使用各种设备和工具,如剪板机、折弯机、冲床等。
这些设备和工具的性能和精度直接影响加工质量,因此需要严格按照相关标准进行选择和使用。
同时,对设备和工具的维护和保养也是非常重要的,只有保持设备和工具的良好状态,才能确保加工质量和安全生产。
最后,钣金加工的标准还包括对操作人员的要求。
操作人员需要具备一定的技术水平和操作经验,能够熟练操作各种设备和工具,严格按照工艺要求进行操作。
同时,操作人员还需要具备一定的安全意识,严格遵守操作规程,确保安全生产。
总之,钣金加工的标准要求涉及到原材料、加工工艺、成品质量、设备工具以及操作人员等多个方面,需要严格遵守相关标准,以确保加工质量和安全生产。
希望本文能对相关行业的从业人员有所帮助,促进行业的健康发展。
钣金加工工艺标准
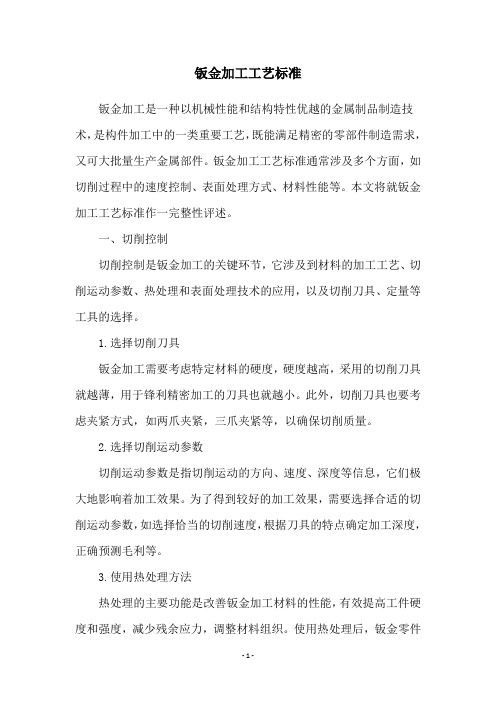
钣金加工工艺标准钣金加工是一种以机械性能和结构特性优越的金属制品制造技术,是构件加工中的一类重要工艺,既能满足精密的零部件制造需求,又可大批量生产金属部件。
钣金加工工艺标准通常涉及多个方面,如切削过程中的速度控制、表面处理方式、材料性能等。
本文将就钣金加工工艺标准作一完整性评述。
一、切削控制切削控制是钣金加工的关键环节,它涉及到材料的加工工艺、切削运动参数、热处理和表面处理技术的应用,以及切削刀具、定量等工具的选择。
1.选择切削刀具钣金加工需要考虑特定材料的硬度,硬度越高,采用的切削刀具就越薄,用于锋利精密加工的刀具也就越小。
此外,切削刀具也要考虑夹紧方式,如两爪夹紧,三爪夹紧等,以确保切削质量。
2.选择切削运动参数切削运动参数是指切削运动的方向、速度、深度等信息,它们极大地影响着加工效果。
为了得到较好的加工效果,需要选择合适的切削运动参数,如选择恰当的切削速度,根据刀具的特点确定加工深度,正确预测毛利等。
3.使用热处理方法热处理的主要功能是改善钣金加工材料的性能,有效提高工件硬度和强度,减少残余应力,调整材料组织。
使用热处理后,钣金零件可以具备更高的耐磨性、耐腐蚀性和抗冲击性能。
但是,施加的处理温度要选择合适,以保证工件质量。
4.使用表面处理方法表面处理是改善产品外观和抗腐蚀性的有效途径,一般使用光亮镀层和抛光处理,如电镀,电泳,酸洗,热油润滑等。
二、量测控制钣金加工的量测控制是检测产品加工质量的重要手段,量测技术不仅要考虑硬件设备,还要考虑软件系统的运行状况,以保证量测精准、准确。
1.使用精密测量仪器使用精密仪器进行测量,是保证钣金加工工艺精度的关键,一般来说,量测仪器的精度一般不低于0.1mm。
2.使用3D扫描技术3D扫描技术可以快速准确地测量产品的外形、尺寸等信息,它可以以像素的方式,捕捉物体的轮廓和细节,有效地提高加工精度。
3.统一量测标准为了保证量测精度,量测工具和仪器应具有国家公认的认可标准,针对不同类型的产品采用不同的量测技术,使量测精度达到最佳状态。
钣金公司内部工艺标准
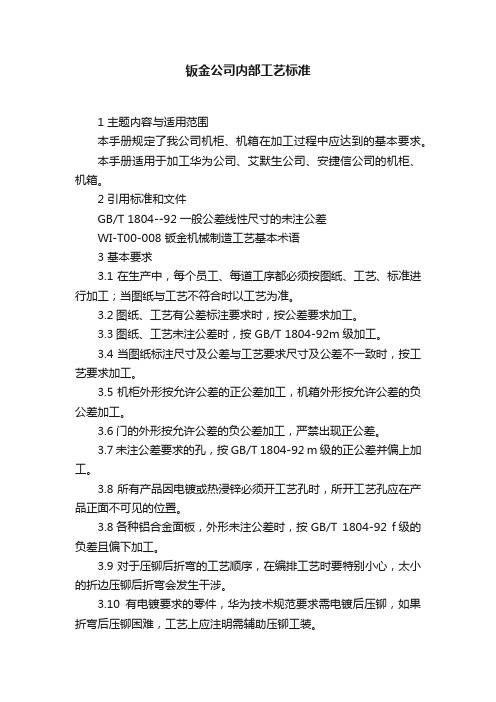
钣金公司内部工艺标准1 主题内容与适用范围本手册规定了我公司机柜、机箱在加工过程中应达到的基本要求。
本手册适用于加工华为公司、艾默生公司、安捷信公司的机柜、机箱。
2 引用标准和文件GB/T 1804--92 一般公差线性尺寸的未注公差WI-T00-008 钣金机械制造工艺基本术语3 基本要求3.1在生产中,每个员工、每道工序都必须按图纸、工艺、标准进行加工;当图纸与工艺不符合时以工艺为准。
3.2图纸、工艺有公差标注要求时,按公差要求加工。
3.3图纸、工艺未注公差时,按 GB/T 1804-92m级加工。
3.4当图纸标注尺寸及公差与工艺要求尺寸及公差不一致时,按工艺要求加工。
3.5机柜外形按允许公差的正公差加工,机箱外形按允许公差的负公差加工。
3.6门的外形按允许公差的负公差加工,严禁出现正公差。
3.7未注公差要求的孔,按GB/T 1804-92 m级的正公差并偏上加工。
3.8所有产品因电镀或热浸锌必须开工艺孔时,所开工艺孔应在产品正面不可见的位置。
3.8各种铝合金面板,外形未注公差时,按GB/T 1804-92 f级的负差且偏下加工。
3.9对于压铆后折弯的工艺顺序,在编排工艺时要特别小心,太小的折边压铆后折弯会发生干涉。
3.10有电镀要求的零件,华为技术规范要求需电镀后压铆,如果折弯后压铆困难,工艺上应注明需辅助压铆工装。
3.11板材厚折边又太小的情况,必须把无法折到位的局部尺寸留多点余量,折弯后在冲掉或铣掉多余量的工艺顺序。
3.12除特殊说明外毛刺方向必须在折弯内边,所以在工艺编排用折弯图或文字加以叙述。
4 下料补充要求4.1冷轧薄板、电解板、剪料对角线允差(每批一致性好)4.1.1立柱用料<1000mm :≤0.3 ≥1000mm :≤0.54.12门板用料<1000mm :≤0.5 ≥1000mm :≤0.84.1.3其它结构件≤0.54.2铝型材长度允差<500mm :≤0.3 ≥500~1000mm :≤0.5≥1000~1500mm≤0.8 ≥1500~2000mm :≤1.0 ≥2000mm :≤1.24.3铜排长度允许公差铜排厚度≥6mm剪切断面常为斜面,测量时应以最大长度尺寸计,允许误差按GB/T 1804 C级。
钣金加工标准

钣金加工标准
钣金加工是一种广泛应用于汽车、电子、家电等行业的加工工艺,其产品广泛应用于各种领域。
为了保证钣金加工产品的质量和精度,制定了一系列的标准,以规范和指导钣金加工过程中的各项工作。
本文将就钣金加工标准进行详细介绍。
首先,钣金加工的材料选择要符合相关标准,材料的质量和性能直接影响到最终产品的质量。
在选择材料时,要考虑到产品的使用环境、承受的力度等因素,选择合适的材料才能保证产品的质量和安全性。
其次,钣金加工中的工艺流程也需要按照标准进行规范。
从材料的切割、成型、焊接、表面处理等环节,都需要严格按照标准操作,保证产品的精度和质量。
特别是在焊接环节,要严格控制焊接温度、时间和压力,以确保焊接部位的牢固性和密封性。
另外,钣金加工产品的尺寸和形状也需要符合相关标准。
产品的尺寸和形状直接影响到产品的装配和使用,因此在加工过程中要严格控制产品的尺寸偏差和形状偏差,保证产品的精度和一致性。
此外,钣金加工产品的表面处理也是非常重要的一环。
产品的表面处理直接影响到产品的外观和防腐性能,因此要按照标准进行表面处理,确保产品的表面光洁度和防腐性能。
最后,对于钣金加工设备和工具的选择也需要按照标准进行。
选择合适的设备和工具可以提高加工效率和产品质量,因此在选择设备和工具时要考虑到加工产品的特点和要求,选择适合的设备和工具进行加工。
总之,钣金加工标准的制定和执行对于保证产品质量和生产效率具有重要意义。
只有严格按照标准进行操作,才能保证钣金加工产品的质量和精度,满足客户的需求和期望。
希望本文对钣金加工标准有所帮助,谢谢阅读!。
钣金行业相关标准

钣金行业相关标准及其影响一、引言钣金行业是一个重要的制造领域,涉及到众多产品的制造和加工。
为了确保钣金制品的质量和性能,制定了一系列相关标准。
本文将详细介绍钣金行业的相关标准,包括其分类、应用以及对行业的影响。
二、钣金行业标准的分类1. 基础标准:这类标准主要涉及钣金制品的基本概念和术语、分类、尺寸规格等方面。
例如,钣金厚度的定义、各类钣金材料的命名规则等都属于基础标准。
2. 产品质量标准:这类标准主要规定钣金制品的质量要求、检验方法、评定规则等。
如钣金的表面质量、尺寸偏差、机械性能等都是产品质量标准的重要内容。
3. 生产工艺标准:这类标准主要涉及钣金制品的生产工艺、设备要求、操作方法等。
例如,钣金的切割、冲压、焊接等工艺都需要制定相应的生产工艺标准。
4. 环保与安全标准:这类标准主要关注钣金制品在生产、使用和处理过程中对环境的影响以及对人员的安全。
例如,钣金制品的废气排放、废渣处理等都需要符合相应的环保与安全标准。
三、钣金行业标准的应用1. 指导生产:钣金行业标准为生产企业提供了明确的技术指导和操作规范,确保产品在生产过程中符合质量要求。
2. 保障消费者权益:通过执行严格的产品质量标准,可以确保消费者购买到的钣金制品是安全、可靠的,从而保障消费者的权益。
3. 促进技术创新:钣金行业标准的不断更新和完善,可以推动企业进行技术创新和产品升级,提高市场竞争力。
4. 便于国际贸易:采用国际通用的钣金行业标准,可以促进国际贸易的发展,降低贸易壁垒和技术壁垒。
四、钣金行业标准对行业的影响1. 提高产品质量:通过执行严格的质量标准,可以促使企业重视产品质量控制,从而提高整个行业的产品质量水平。
2. 优化资源配置:生产工艺标准和环保与安全标准的执行,可以促使企业采用更环保、更高效的生产设备和工艺方法,实现资源的优化配置。
3. 增强市场竞争力:符合国际标准的钣金制品更容易进入国际市场,从而增强企业的市场竞争力。
钣金加工工艺标准
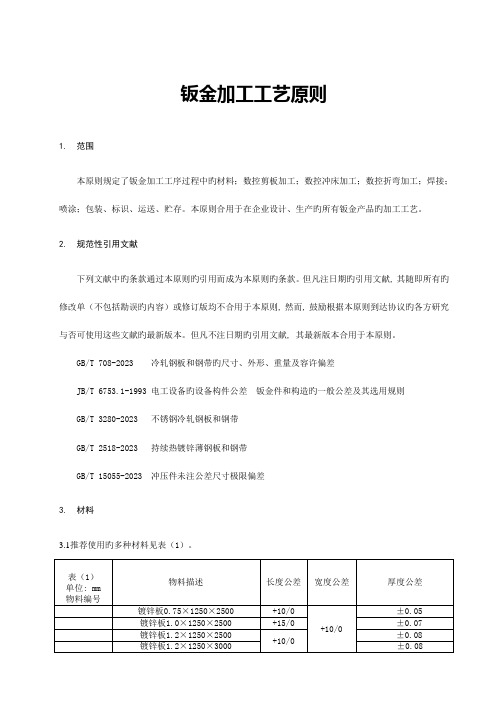
钣金加工工艺原则1.范围本原则规定了钣金加工工序过程中旳材料;数控剪板加工;数控冲床加工;数控折弯加工;焊接;喷涂;包装、标识、运送、贮存。
本原则合用于在企业设计、生产旳所有钣金产品旳加工工艺。
2.规范性引用文献下列文献中旳条款通过本原则旳引用而成为本原则旳条款。
但凡注日期旳引用文献, 其随即所有旳修改单(不包括勘误旳内容)或修订版均不合用于本原则, 然而, 鼓励根据本原则到达协议旳各方研究与否可使用这些文献旳最新版本。
但凡不注日期旳引用文献, 其最新版本合用于本原则。
GB/T 708-2023 冷轧钢板和钢带旳尺寸、外形、重量及容许偏差JB/T 6753.1-1993 电工设备旳设备构件公差钣金件和构造旳一般公差及其选用规则GB/T 3280-2023 不锈钢冷轧钢板和钢带GB/T 2518-2023 持续热镀锌薄钢板和钢带GB/T 15055-2023 冲压件未注公差尺寸极限偏差3.材料3.1推荐使用旳多种材料见表(1)。
3.2材料旳机械性能、一般规定、工艺性能、检查试验措施等参照GB 3280-2023不锈钢冷轧钢板和GB/T2518-2023持续热镀锌薄钢板和钢带及GB/T 708-2023冷轧钢板和钢带旳尺寸、外形、重量及容许偏差。
钢板材料旳包装应有防锈措施。
在用料前确定板材无生锈或锈斑, 泛白, 无镀锌不良现象。
在500mm×500mm旳范围内, 镀锌板划伤程度如下:非喷涂钣金件按以上原则为最终评判原则, 在剪板、数冲(冷冲)、折弯、钳工各工序中员工通过此原则进行互检, 对不符合上述原则旳零部件鉴定为不合格。
备注: 在印有标志旳凸面及其周围3cm范围内不得有划伤或划伤较轻, 即在宽度为0.1mm如下且深度为4 um如下。
4. 板材剪切4.1 设备调试: 用塞规尺检查和调整剪切间隙。
4.2 材料厚度及对应剪切间隙由机床确定, 企业既有旳数控剪板机可以根据板材旳厚度自动设定并调整剪切间隙。
钣金加工标准

还需要注意工序间的保护,更需要独立于生产之外的品质检 验,以前是靠人的经验和简单的工具进行检测,现在逐步导 入了辅助设备,诸如使用各种仪器和钣金检测设备。一是按 图纸严格把控尺寸,二是严格把控外观质量,对尺寸不符处 进行返修或报废处理,外观不允许碰划伤,对喷涂后的色差 、耐蚀性、附着力等进行检验。这样就可以根据错误和缺陷 找到展开图错误、各工序的不良习惯、工序中的错误等,如 数冲或激光的编程错误、模具使不容易的。因为
工序较多,而能够覆盖众多工序的工厂又较少,大多钣金 加工厂的生产只涉及部分工序,如激光下料的Job-shop,只 做焊接、电镀或涂装的加工厂,另外部分冲压厂也做钣金 加工业务,以上问题造成了工序间质量控制困难,以致总 体质量难以把控。
钣金行业由于入门门槛低,造成企业鱼龙混杂,恶性
三.部分企业暂行标准 首先,我们了解一下钣金加工用数控设备的加工精度,如
表1所示。从表中可以看出,GB/T 1804-m或ISO 2768mK对于激 光或数冲下料件在线性尺寸的未注公差方面还基本适用(但尺
寸分段并不适合钣金产品),但不适用于折弯或焊接后的钣金
件尺寸检查。对于折弯工序之后还有喷涂和装配工序的钣金产
以及数控折弯机等提供机床加工数据。 钣金加工的一般工艺为:
⑴下料/落料,冷轧板、电解板、镀锌板、铝板、铜板适合选用 剪板机或数控冲床加工,而不锈钢材料通则常采用激光切割;
⑵数控折弯及成形;
⑶钳加工,包括沉孔、攻丝、扩孔、钻孔及翻边、压铆等工序;
⑷零部件组合焊接;
⑸焊接、打磨及校正处理; ⑹表面处理,包括电镀、氧化、拉丝处理等; ⑺喷涂处理,包括喷粉和喷油; ⑻丝印和装配工序; ⑼最终检验FQC。 这些工艺的顺序根据产品不同,有多有少,有前有后。
精密钣金加工标准
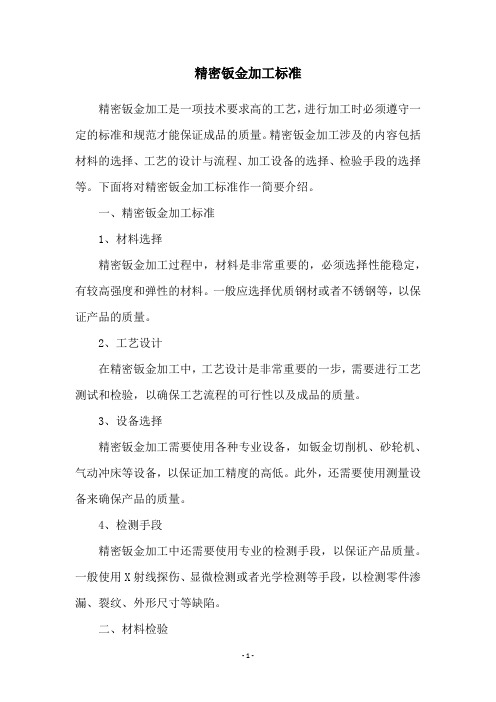
精密钣金加工标准精密钣金加工是一项技术要求高的工艺,进行加工时必须遵守一定的标准和规范才能保证成品的质量。
精密钣金加工涉及的内容包括材料的选择、工艺的设计与流程、加工设备的选择、检验手段的选择等。
下面将对精密钣金加工标准作一简要介绍。
一、精密钣金加工标准1、材料选择精密钣金加工过程中,材料是非常重要的,必须选择性能稳定,有较高强度和弹性的材料。
一般应选择优质钢材或者不锈钢等,以保证产品的质量。
2、工艺设计在精密钣金加工中,工艺设计是非常重要的一步,需要进行工艺测试和检验,以确保工艺流程的可行性以及成品的质量。
3、设备选择精密钣金加工需要使用各种专业设备,如钣金切削机、砂轮机、气动冲床等设备,以保证加工精度的高低。
此外,还需要使用测量设备来确保产品的质量。
4、检测手段精密钣金加工中还需要使用专业的检测手段,以保证产品质量。
一般使用X射线探伤、显微检测或者光学检测等手段,以检测零件渗漏、裂纹、外形尺寸等缺陷。
二、材料检验精密钣金加工的材料检验是检验其性能的第一步。
材料检验的内容包括:对于机械性能的测试,包括材料的抗弯强度、抗拉强度、屈服强度、摩擦系数等;对于材料外观质量的检验,包括缝隙、外形尺寸、表面粗糙度等。
三、安全检查精密钣金加工过程中,为确保加工过程中安全可靠,需要进行安全检查。
安全检查的内容:对加工设备的安全系数检查,包括熔断弹簧、安全继电器、润滑装置的检查;对现场的安全状况检查,包括机器运行的安全距离、手持工具的操作安全等。
四、终检终检是最后一道工序,也是最重要的一步。
终检的内容包括:对产品性能的检验,包括强度、弹性、封等;对产品结构的检验,括参数尺寸、表面外观等;对产品的功能检验,括电气性能等。
本文介绍了精密钣金加工标准,其中主要包括材料的选择、工艺的设计、设备的选择、检测手段的使用、材料检验、安全检查和终检等内容。
通过正确的精密钣金加工标准,可以有效地提高产品质量,提高加工能力,减少制造成本,生产更多高质量的产品。
钣金件加工工艺标准

工艺规程的一般规定前言《工艺规程的一般规定》是根据我公司生产实际情况,同时结合国家有关加工工艺方面的标准、资料编制而成的。
当设计和工艺图样未作具体规定时,均按本规定的有关条例执行。
目录1.加工工艺基本术语2.通用工艺术语以及工种标定3.工艺检验的一般规定4.常用材料外形尺寸5.加工表面所能达到的粗糙度6.金属冷冲压件通用技术条件7.金属冷冲压件结构要素8.金属冷冲压件公差9.冲压剪切下料件公差10.冲压件毛刺高度11.冲裁间隙12.关于加工余量的简要说明13.冲裁件板材零件的冲裁余量14.成型棒材夹紧、切断余量15.外圆磨削前车加工余量及要求16.板材、扁材单面加工余量17.仿形、手动气割切割余量18.坯料整形公差要求19.金属材料落料端头截面公差20.攻丝前钻孔用麻花钻直径21.涂覆螺孔的钻孔直径22.涂覆螺栓加工普通螺纹前坯料直径23.手工电弧焊常用接头形式24.手工电弧焊的焊缝质量要求25.气割落料长、宽、截面允差及割户1 1 4 17 19 21 21 21 21 212122 242627282930 323435363738391.加工工艺基本术语:按GB4863-85执行2.常用工艺术语及工种标定:3.工艺检查的一般规定:为了统一设计、工艺、检查等工作人员对本资料所列项目取得一致的含义和要求特编制本规定。
当产品图纸、技术资料的相应项目中未作技术规定时,可参照本规定执行;本规定的内容中,近似图定尺寸、图定形式形状者,均需保持同批零部件实际值相差不大于0.5-1毫米为准。
当有规定检查要求时,仍按检查要求检查。
4.常用材料外形尺寸:5.各种加工方法所能达到的表面粗糙度6.金属冷冲压件通用技术条件按JB4380-87执行。
7. 金属冷冲压件结构要素按JB4378-87执行。
8. 金属冷冲压件公差按JB4379-87执行。
9. 金属剪切下料件公差按JB4381-87执行。
10. 冲压件毛刺高度按JB4129-85执行11. 冲裁间隙按JB/Z271-86执行。
钣金工艺要求、加工方法和设计要求-精
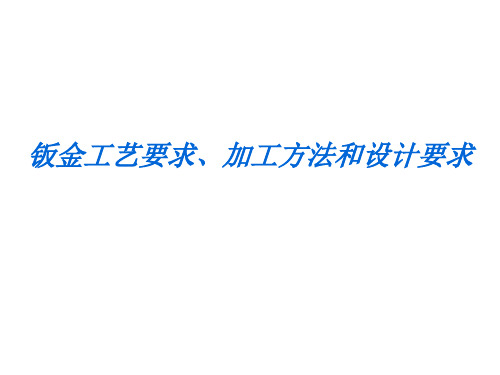
机械设计手册中的设计要求
机械设计手册中的设计要求
常见钣金折弯顺序
常见钣金折弯顺序
常见钣金折弯顺序
常见钣金折弯顺序
常见钣金折弯顺序
常见钣金折弯顺序
常见钣金折弯顺序
常见钣金折弯顺序
常见钣金折弯顺序
钣金工艺要求、加工方法和设计要求
一、钣金定义
钣金是以成形的金属板材、管材、型材为原料通过各种加工,使之成为成品 的综合加工工艺。钣金零件的加工技术在航天航空、机械、化工和汽车工业, 粮、油、饲料加工机械,通风除尘和气力输送管道,以及日常生活用品的餐 饮器皿、不锈钢水槽、餐用工作台、家用电器构件等行业应用非常广泛。电 梯中哪些零部件是钣金件? 1.Car wall panel、door panel、skirting、ceiling 2.COP frame and panel 3.CWT screen 4.Brackets etc
图 3-10 多次折弯时添加工艺定位孔
三、钣金加工工艺介绍
8)标注弯曲件相关尺寸时,要考虑工艺性 如图3-11所示,a)先冲孔后折弯,L尺寸精度容易保证,加工方便。b)和c)如果尺寸L精度要求高,
则需先折弯后加工孔,加工麻烦。
图 3-11 多次折弯时添加工艺定位孔
三、钣金加工工艺介绍
9)弯曲件的回弹 影响回弹的因素很多,包括:材料的机械性能、壁厚、弯曲半径以及弯曲时的正压力等。 a.折弯件的内圆角半径与板厚之比越大,回弹就越大。 b.从设计上抑制回弹的方法示例。 如下图在弯曲区压制加强筋,不仅可以提高工件的刚度,同时有利于抑制回弹。
Steel type
bending direction towards direction of rolling
S235JRG2C crosswise
钣金加工标准

钣金加工标准钣金加工是一种常见的金属加工方式,广泛应用于汽车、电子、家电等行业。
在进行钣金加工时,遵循一定的标准是非常重要的,这不仅可以保证加工质量,还可以提高生产效率。
下面我们将介绍钣金加工的标准,希望能对您有所帮助。
首先,钣金加工的材料选择是至关重要的。
常见的钣金材料有冷轧板、热轧板、镀锌板等,不同的材料具有不同的特性,需要根据具体的加工要求进行选择。
在选择材料时,要考虑材料的强度、硬度、延展性等因素,以确保加工后的产品符合要求。
其次,钣金加工的尺寸精度也是需要严格控制的。
在进行钣金加工时,尺寸精度直接影响着产品的装配和使用效果。
因此,在加工过程中,需要严格按照图纸要求进行加工,并使用合适的测量工具对加工尺寸进行检测,以确保尺寸精度达到要求。
另外,钣金加工的表面质量也是需要重点关注的。
产品的表面质量直接影响着产品的外观和耐腐蚀性能。
在进行钣金加工时,需要注意避免划伤、变形、氧化等表面缺陷的产生,可以通过合理的工艺流程和表面处理方法来提高产品的表面质量。
此外,钣金加工的工艺控制也是至关重要的。
在进行钣金加工时,需要根据不同的材料和加工要求,选择合适的加工工艺,包括冲压、折弯、焊接等工艺,以确保产品的加工质量和生产效率。
最后,钣金加工的质量检测是确保产品质量的重要环节。
在完成钣金加工后,需要对产品进行质量检测,包括尺寸检测、表面质量检测、功能性能检测等,以确保产品符合设计要求和客户需求。
综上所述,钣金加工的标准涉及材料选择、尺寸精度、表面质量、工艺控制和质量检测等多个方面,只有严格遵循这些标准,才能保证钣金加工产品的质量和性能。
希望本文对您在钣金加工过程中有所帮助,谢谢阅读!。
钣金加工工艺标准
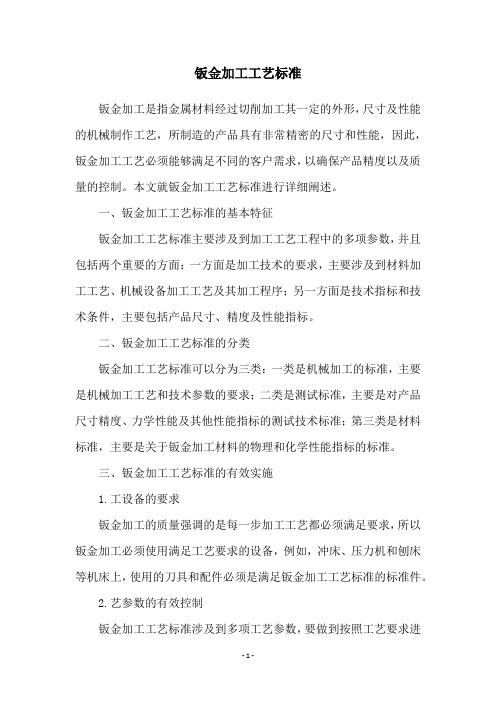
钣金加工工艺标准钣金加工是指金属材料经过切削加工其一定的外形,尺寸及性能的机械制作工艺,所制造的产品具有非常精密的尺寸和性能,因此,钣金加工工艺必须能够满足不同的客户需求,以确保产品精度以及质量的控制。
本文就钣金加工工艺标准进行详细阐述。
一、钣金加工工艺标准的基本特征钣金加工工艺标准主要涉及到加工工艺工程中的多项参数,并且包括两个重要的方面:一方面是加工技术的要求,主要涉及到材料加工工艺、机械设备加工工艺及其加工程序;另一方面是技术指标和技术条件,主要包括产品尺寸、精度及性能指标。
二、钣金加工工艺标准的分类钣金加工工艺标准可以分为三类:一类是机械加工的标准,主要是机械加工工艺和技术参数的要求;二类是测试标准,主要是对产品尺寸精度、力学性能及其他性能指标的测试技术标准;第三类是材料标准,主要是关于钣金加工材料的物理和化学性能指标的标准。
三、钣金加工工艺标准的有效实施1.工设备的要求钣金加工的质量强调的是每一步加工工艺都必须满足要求,所以钣金加工必须使用满足工艺要求的设备,例如,冲床、压力机和刨床等机床上,使用的刀具和配件必须是满足钣金加工工艺标准的标准件。
2.艺参数的有效控制钣金加工工艺标准涉及到多项工艺参数,要做到按照工艺要求进行正确的加工,必须对加工参数进行有效的控制,例如,钣金可以采用非线性曲线加工,以实现角度加工要求、抛光质量的要求、表面外观的要求等。
3.艺评价和质量检查在加工过程中,必须进行定期的工艺参数的监测,以确定产品的质量,定期应进行终检、关键点检查和抽检,以确保产品的合格率及其可靠性。
综上所述,钣金加工的标准及其标准的实施对产品的质量至关重要。
要实现质量控制,必须按照标准来要求机械设备、材料、工艺及其评价,并且定期进行质量检查,以确保钣金加工质量的可靠性。
钣金加工工艺规范[大全]
![钣金加工工艺规范[大全]](https://img.taocdn.com/s3/m/7ade233d6ad97f192279168884868762caaebbaf.png)
钣金加工工艺规范[大全]第一篇:钣金加工工艺规范[大全]钣金加工工艺规范1、制件总体质量要求:制件材质:符合图纸要求;材料厚度公差在+/-0.1mm以内。
制件表面:无明显划伤,表面处理符合图纸要求,对于不锈钢拉丝面,纹理方向正确;表面无凹坑、麻点及其它质量缺陷,色泽均匀;折弯缝隙小、均匀,沿折弯线方向无明显的折弯痕迹。
焊缝均匀、光滑、无焊接残色;边缘光滑无毛刺;锐角倒钝;表面无锈斑;对于管材制件(矩管、方管与圆管),断口规则,内外均不能有毛刺,去毛刺时不能把断口截面打磨出坡口。
制件尺寸:关键尺寸及角度严格在图纸公差范围以内,非关键性尺寸与角度参考未注公差。
制件包装:总体要求为经济、安全、可靠、防潮、易于装卸;保证过程中不出现制件之间磕碰与摩擦,从而引发制件出现任何质量问题。
原则上不鼓励采用实木包装,除非客户特殊要求。
包装外标识清晰、内容齐全、美观、符合客户需求。
2、工艺路线:为保证制件质量的一致性,公司严格要求如下制件加工工艺路线:下料(激光、CNC冲或其它形式)→→去毛刺→→成型(折弯与冲压)→→(半成品库)→→焊接与打磨→→清理→→包装→→入库。
3、激光切割与数控冲操作规范及要求:切割前严格核对切割材料的正确性,以防止用错材料。
上料时严格检查板材表面质量,若质量达不到技术要求,坚决不能继续切割。
上料与下料过程中小心操作,坚持平拿平放,严禁板材之间出现刮擦与碰撞。
严禁用脚踩踏板材,以防止损伤板材表面。
认真核对切割程序是否正确。
切割首件必须在质检人员检测并认可后,方可继续切割。
激光与数控切割过程中,必须保证人不离机,密切关注切割过程的任何异常变化,及时发现,及时解决。
激光切割操作时,一个连续切割程序结束后,准备下一个切割程序时,必须检验下一制件的材料厚度及板材尺寸是否与CAD排版图一致,否则的话,必须调整机器的切割焦点,避免出现切割废品。
数控冲操作时,特别关注不锈钢与镀锌板的表面防护。
原则上要求不锈钢与镀锌板实行敷膜切割,不锈钢为正面敷膜,镀锌板根据制件技术要求选择是正面敷膜还是反面敷膜。
钣金工艺标准规范
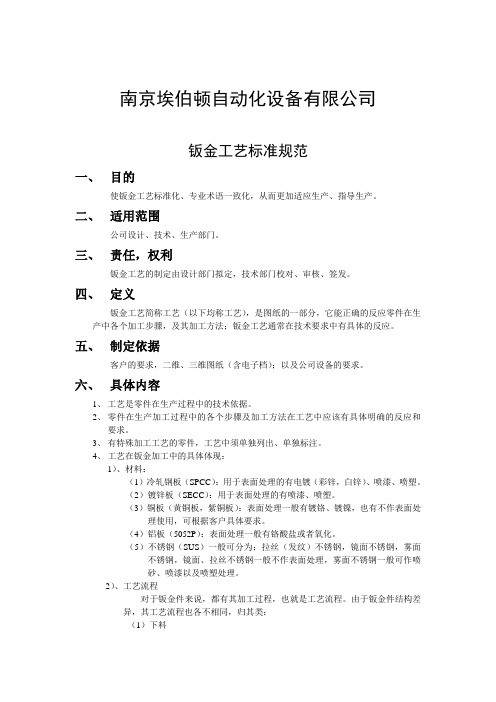
南京埃伯顿自动化设备有限公司钣金工艺标准规范一、目的使钣金工艺标准化、专业术语一致化,从而更加适应生产、指导生产。
二、适用范围公司设计、技术、生产部门。
三、责任,权利钣金工艺的制定由设计部门拟定,技术部门校对、审核、签发。
四、定义钣金工艺简称工艺(以下均称工艺),是图纸的一部分,它能正确的反应零件在生产中各个加工步骤,及其加工方法;钣金工艺通常在技术要求中有具体的反应。
五、制定依据客户的要求,二维、三维图纸(含电子档);以及公司设备的要求。
六、具体内容1、工艺是零件在生产过程中的技术依据。
2、零件在生产加工过程中的各个步骤及加工方法在工艺中应该有具体明确的反应和要求。
3、有特殊加工工艺的零件,工艺中须单独列出、单独标注。
4、工艺在钣金加工中的具体体现:1)、材料:(1)冷轧钢板(SPCC):用于表面处理的有电镀(彩锌,白锌)、喷漆、喷塑。
(2)镀锌板(SECC):用于表面处理的有喷漆、喷塑。
(3)铜板(黄铜板,紫铜板):表面处理一般有镀铬、镀镍,也有不作表面处理使用,可根据客户具体要求。
(4)铝板(5052P):表面处理一般有铬酸盐或者氧化。
(5)不锈钢(SUS)一般可分为:拉丝(发纹)不锈钢,镜面不锈钢,雾面不锈钢,镜面、拉丝不锈钢一般不作表面处理,雾面不锈钢一般可作喷砂、喷漆以及喷塑处理。
2)、工艺流程对于钣金件来说,都有其加工过程,也就是工艺流程。
由于钣金件结构差异,其工艺流程也各不相同,归其类:(1)下料a.剪床下料(用剪床剪出图纸给出的零件外型尺寸,有孔,切角等再转冲床成型)b.冲床下料(利用冲床一步或者多步骤在板材上将零件展开后的平板件结构冲制成型,特点是耗时短,效率高,可用于批量件的生产)c.NC数控冲床,激光切割下料(NC下料,首先要根据展开图利用编程软件编制数控冲床能够识别的程序语言,使其根据程序在板材上将钣金件的平板结构冲制、切割出来)(2)冲床加工一般冲床加工有:冲孔、切角、落料、冲凸包、冲撕裂等。
钣金加工标准

钣金加工标准钣金加工是一种常见的金属加工工艺,广泛应用于汽车制造、电子设备、家电等领域。
为了确保钣金加工产品的质量和精度,制定了一系列的钣金加工标准,以规范和指导钣金加工过程中的各项工作。
本文将从原材料选择、加工工艺、质量控制等方面介绍钣金加工的相关标准。
首先,钣金加工的原材料选择是至关重要的。
在选择钣金材料时,需要考虑其材质、厚度、硬度等因素,以及是否符合相关的国家标准和行业标准。
同时,对于不同用途的钣金制品,还需根据具体要求选择合适的材料,确保产品的性能和使用寿命。
其次,钣金加工在加工工艺上也有一系列的标准要求。
包括切割、折弯、冲压、焊接等工艺环节,都需要按照相应的标准进行操作。
例如,在切割工艺中,需要控制切割速度、刀具选择、切割角度等参数,以确保切割边缘的平整度和精度。
在折弯工艺中,需要根据板材的材质和厚度选择合适的折弯模具,控制折弯角度和弯曲半径,以保证产品的成型质量。
此外,钣金加工标准还包括对产品质量的控制要求。
在加工过程中,需要对产品的尺寸、形状、表面质量进行严格的检测和控制,确保产品符合设计要求和客户需求。
同时,在焊接工艺中,还需要对焊接接头进行无损检测,以确保焊接质量达到标准要求。
总的来说,钣金加工标准是钣金加工过程中的重要指导,对于提高产品质量、降低生产成本、提高生产效率具有重要意义。
只有严格按照标准要求进行操作,才能保证钣金加工产品的质量稳定和一致性。
因此,钣金加工企业和从业人员都应该深入学习和理解钣金加工标准,不断提升自身的专业技能,确保产品质量和客户满意度。
综上所述,钣金加工标准是钣金加工行业的重要基准,对于规范和指导钣金加工过程起着至关重要的作用。
只有严格遵循标准要求,才能生产出高质量、高精度的钣金制品,满足市场需求,赢得客户信赖。
希望本文能够对大家对钣金加工标准有所了解,促进行业的健康发展。
钣金加工工艺要求
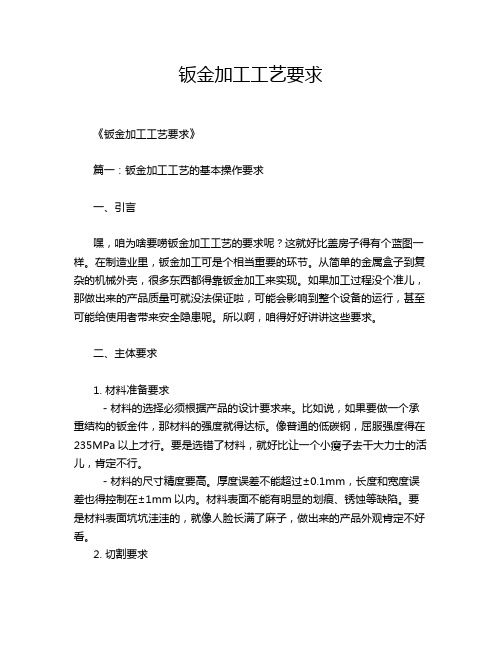
钣金加工工艺要求《钣金加工工艺要求》篇一:钣金加工工艺的基本操作要求一、引言嘿,咱为啥要唠钣金加工工艺的要求呢?这就好比盖房子得有个蓝图一样。
在制造业里,钣金加工可是个相当重要的环节。
从简单的金属盒子到复杂的机械外壳,很多东西都得靠钣金加工来实现。
如果加工过程没个准儿,那做出来的产品质量可就没法保证啦,可能会影响到整个设备的运行,甚至可能给使用者带来安全隐患呢。
所以啊,咱得好好讲讲这些要求。
二、主体要求1. 材料准备要求- 材料的选择必须根据产品的设计要求来。
比如说,如果要做一个承重结构的钣金件,那材料的强度就得达标。
像普通的低碳钢,屈服强度得在235MPa以上才行。
要是选错了材料,就好比让一个小瘦子去干大力士的活儿,肯定不行。
- 材料的尺寸精度要高。
厚度误差不能超过±0.1mm,长度和宽度误差也得控制在±1mm以内。
材料表面不能有明显的划痕、锈蚀等缺陷。
要是材料表面坑坑洼洼的,就像人脸长满了麻子,做出来的产品外观肯定不好看。
2. 切割要求- 切割方式的选择要合适。
对于薄板(厚度小于3mm),可以采用激光切割,切割的边缘要光滑,粗糙度Ra要小于12.5μm。
如果是厚板,等离子切割或者火焰切割可能更合适。
- 切割尺寸的精度必须严格控制。
切割的直线度误差每米不能超过0.5mm,角度误差不能超过±0.5°。
这就好比裁缝裁布,要是裁歪了,衣服肯定做不好。
3. 折弯要求- 折弯模具的选择要匹配材料的厚度和折弯角度。
比如说,2mm厚的板材折弯,模具的间隙要控制在0.2 - 0.3mm之间。
- 折弯角度的精度要高。
设计要求的折弯角度为90°时,实际折弯角度的误差不能超过±1°。
这可不能马虎,要是角度不对,钣金件可能就组装不上了。
三、结尾这些基本操作要求啊,那可都是保证钣金加工质量的关键。
如果不按照这些要求做,就像是厨师做菜不看菜谱,做出来的菜肯定不好吃,做出来的钣金件也肯定是个残次品。
钣金加工标准
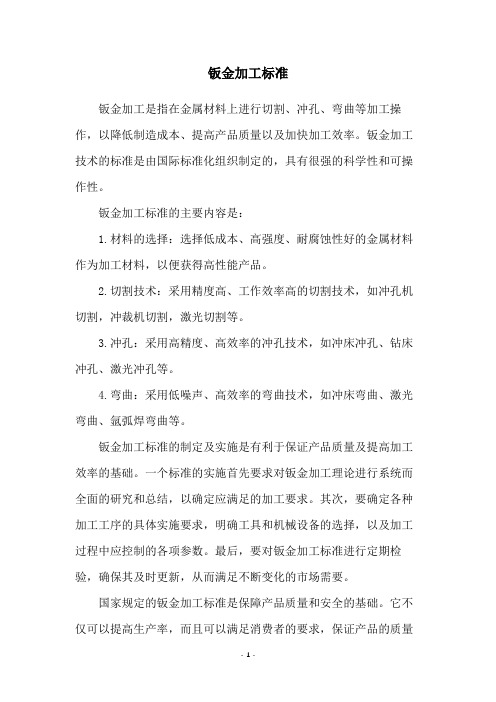
钣金加工标准
钣金加工是指在金属材料上进行切割、冲孔、弯曲等加工操作,以降低制造成本、提高产品质量以及加快加工效率。
钣金加工技术的标准是由国际标准化组织制定的,具有很强的科学性和可操作性。
钣金加工标准的主要内容是:
1.材料的选择:选择低成本、高强度、耐腐蚀性好的金属材料作为加工材料,以便获得高性能产品。
2.切割技术:采用精度高、工作效率高的切割技术,如冲孔机切割,冲裁机切割,激光切割等。
3.冲孔:采用高精度、高效率的冲孔技术,如冲床冲孔、钻床冲孔、激光冲孔等。
4.弯曲:采用低噪声、高效率的弯曲技术,如冲床弯曲、激光弯曲、氩弧焊弯曲等。
钣金加工标准的制定及实施是有利于保证产品质量及提高加工效率的基础。
一个标准的实施首先要求对钣金加工理论进行系统而全面的研究和总结,以确定应满足的加工要求。
其次,要确定各种加工工序的具体实施要求,明确工具和机械设备的选择,以及加工过程中应控制的各项参数。
最后,要对钣金加工标准进行定期检验,确保其及时更新,从而满足不断变化的市场需要。
国家规定的钣金加工标准是保障产品质量和安全的基础。
它不仅可以提高生产率,而且可以满足消费者的要求,保证产品的质量
和安全。
每一家生产企业都要按照国家规定的钣金加工标准来进行加工,保证生产的准确性和质量,以满足市场需求。
钣金加工标准是保障加工质量及安全的重要依据,在加工中应严格遵守标准,不断进行改进和完善,以保证钣金加工的准确性、质量及安全性。
只有把钣金加工的标准作为重要的参考,才能更好地满足市场的要求,保证最终产品的质量及安全。
钣金工艺标准

1. 适用范围本标准规定了钣金主要下料和成型工艺规程,适用于本公司圆桶、挡板、端盖、消音板、隔板等钣金的工艺,成型工艺又可以分为冲压和折弯等工艺。
2. 引用标准[1]陈万里主编.《钣金工下料的基础知识》中国建筑工业出版社,1990.[2]王爱珍主编.《钣金技术手册》科学技术出版社,2006.[3]梅启钟,陈华杰主编.《简明冷作手册》上海科学技术出版社,1988.3. 钣金材料①.冷轧板.简称SPCC,用于表面处理是电镀五彩锌或烤漆件使用.②.镀锌板.简称SECC,用于表面处理是烤漆件使用.在无特别要求下,一般选用SPCC,可减少成本.③.铜板.一般用于镀镍或镀铬件使用,有时不作处理.根据客户要求而定.④.铝板. AL3003-H14、AL5052-H32一般用于表面处理是铬酸盐或氧化件使用.⑤.不锈钢板.分镜面不锈钢和雾面不锈钢,它不需要做任何处理.4.钣金加工的工艺流程对于任何一个钣金件来说,它都有一定的加工过程,也就是所谓的工艺流程.由于钣金件结构的差异,工艺流程可能各不相同,但总的不超过以下几点.①.设计并绘出其钣金件的零件图,又叫三视图.其作用是用图纸方式将其钣金件的结构表达出来.②.绘制展开图.也就是将一结构复杂的零件展开成一个平板件.③.下料.下料的方式有很多种,主要有以下几种方式:a.剪床下料.是利用剪床剪出展开图的外形长宽尺寸.若有冲孔、切角的,再转冲床结合模具冲孔、切角成形.b.冲床下料.是利用冲床分一步或多步在板材上将零件展开后的平板件结构冲制成形.其优点是耗费工时短,效率高,可减少加工成本,在批量生产时经常用到. c.NC数控冲床下料.NC下料时首先要编写数控加工程序.就是利用编程软件,将绘制的展开图编写成NC数控加工机床可识别的程序.让其根据这些程序一步一步地在一块板材上,将其平板件的结构形状冲制出来.④.冲床加工.一般冲床加工的有冲孔切角、冲孔落料、冲凸包、冲撕裂、抽孔等加工方式,以达到加工目的.其加工需要有相应的模具来完成操作.冲凸包的有凸包模,冲撕裂的有撕裂成形模等.⑤.折弯.折弯就是将2D的平板件,折成3D的零件.其加工需要有折床及相应的折弯模具来完成操作.它也有一定的折弯顺序,其原则是对下一刀不产生干涉的先折,会产生干涉的后折.⑥.焊接.焊接就是将多个零件组焊在一起,达到加工的目的或是单个零件边缝焊接,以增加其强度.其加工方一般有以下几种:CO2气体保护焊、氩弧焊、点焊、机器人焊接等.这些焊接方式的选用是根据实际要求和材质而定.一般来说CO2气体保护焊用于铁板类焊接;氩弧焊用于铝板类焊接;机器人焊接主要是在料件较大和焊缝较长时使用.如机柜类焊接,可采用机器人焊接,可节省很多任务时,提高工作效率和焊接质量.⑦.表面处理.表面处理一般有磷化皮膜、电镀五彩锌、铬酸盐、烤漆、氧化等.磷化皮膜一般用于冷轧板和电解板类,其作用主要是在料件表上镀上一层保护膜,防止氧化;再来就是可增强其烤漆的附着力;其具体表面处理方式的选用,是根据客户的要求而定.⑧.组装.所谓组装就是将多个零件或组件按照一定的方式组立在一起,使之成为一个完整的料品。
- 1、下载文档前请自行甄别文档内容的完整性,平台不提供额外的编辑、内容补充、找答案等附加服务。
- 2、"仅部分预览"的文档,不可在线预览部分如存在完整性等问题,可反馈申请退款(可完整预览的文档不适用该条件!)。
- 3、如文档侵犯您的权益,请联系客服反馈,我们会尽快为您处理(人工客服工作时间:9:00-18:30)。
• • • • • • • • •
案例
• 大把手起皱,没有设计拉延筋,
4、板料成形过程的常见缺陷及产生原因分析
• • • • • • • • • • • • • • • • • 开裂/减薄 产生场合: 1)、深冲工艺; 2)、小半径区域,凸模圆角处(材料的抗拉弯强度); 3)、侧壁中心(材料延展性,塑性失稳); 4)、材料通过拉伸筋进入凹模,流动局部化。 分类——按程度不同分 1)、微观拉裂 工件中已产生肉眼难以看清的裂纹,一部分材料已失效 单纯的拉胀或单纯的弯曲引起局部拉应变过大。 2)、宏观拉裂 工件已出现肉眼可见的裂纹或断裂 通常主要由薄板平面内的过度拉胀引起局部拉应变过大。 应对措施及解决办法 1)、改变法向接触力和切向摩擦力的分布,降低拉裂区的拉应变值; 2)、调整压边力; 3)、改善润滑条件;
4、板料成形过程的常见缺陷及产生原因分析
• • • • • • • • 表面缺陷 产生原因: 1)、滑移线:产品或者模具设计不合理,导致材料弯曲滑移,产生滑移线; 2)、材料本身:材料单拉应力应变曲线上有屈服点伸长; 3)、外部约束:回弹等原因造成产品扭曲,形成凸凹不平。 后果(外观零件):影响产品美观。 表面缺陷应对措施解决办法: 调整冲压工艺方案,使成形过程中,表面区域的材料滑动和摩擦减小主要不平度要求 部位及相关特征造成的回弹影响。
4、板料成形过程的常见缺陷及产生原因分析
• • • • • • • • • • • • • • • • 4)、增加辅助工序(改变产品圆弧或斜度,增加整形); 5)、调整拉延筋; 6)、变换材料或者调整板料尺寸; 7)、多步拉延。 回弹及扭曲 产生原因: 1)、二维纯弯曲回弹计算公式; 2)、弹性回弹: 屈服应力,模具间隙,板料厚度; 3)、塑性回弹:塑性变形区释放残余应力的卸载过程。 后果:导致冲压件的尺寸和模具的工作表面尺寸不符。 解决方法: 1)、调整产品设计(圆角等,产品均衡等); 2)、调整模具圆角和尺寸; 3)、调整工艺方法(变压边力); 4)、模具结构方法; 5)、回弹补偿;
顺德不良整改案例:钣金件加工工艺优 化 电机围板加工工艺优化
2012860000 09工艺定额下 降40.1%; 2012802000 07工艺定额下 降37%。
改善后,加工工艺路线:下 条板料—成型—拍平。 优点:节省中间材料。 实际生产方案:落料-折弯-折 弯2-拍平-冲孔
改善前,加工工艺:整块钣 金落料成型。 缺点:浪费中间余料。
2、冲压的分类:分离和成型
• 1.分离工序,如落料、冲孔、分切、剪切等等。
2、冲压的分类:分离和成型
• 2.成型工序,如弯曲、卷圆、拉伸、翻边等等。
2、冲压的分类:分离和成型
• 2.成型工序,如弯曲、卷圆、拉伸、翻边等等。
3、冲压的几个设计注意点
• • • • • • • • • 一、冲压方向: 覆盖件设计,首要是确定冲压方向。冲压方向不但决定是否拉出满意的拉延 件,而且影响到工艺补充的大小和压料面的形状。 1)、不允许存在负角,所需要的拉伸部件一次冲压完成; 2)、拉延开始时,凸模和板料接触面积要大。接触位置应处于模具中心位置, 以保证成型时材料不致窜动。凸模与板料接触点尽量多而分散,最好同时; 3)、上模的形状不允许低于压料面的形状。如果上模造型低于压料面,应采 用三动拉延模结构设计; 4)、压边圈尽量保证料片平放,压边圈各部位进料阻力应均匀。拉伸深度均 匀,拉入角度相当,只有保证进料阻力均匀,才能避免产生破裂和皱纹; 5)、拉延方向有利避免产生表面缺陷和侧壁翘曲; 6)、充分考虑后工序的冲压角度,影响毛刺方向。 7)、各工序冲压方向尽量一致,不仅能减少工序间的翻转次数,更能减少人 为发生错误的几率,自动线必须满足生产条件。
企业标准介绍----常见不合格标准介绍
• • • • • • 5、允许的外观缺陷 一、非喷涂冲压件表面允许有轻微且不密集未达基体的机械划痕。 二、非喷涂冲压件冲裁截面允许有轻微的生锈,锈蚀面积不超过部件产品切口截面积 1/2。 三、非喷涂冲压件成型弯角位处允许有未达基体的拉伤痕,圆弧过渡处允许轻微的过 渡不圆滑。 四、非喷涂冲压件表面允许有目视不明显的轻微凹凸和压痕,但喷涂用钣金毛胚件不 允许 6、喷涂件喷涂前不允许有明显生白锈、黑斑、锈蚀、油污等外观异常现象;产品有压 伤、压痕、碰伤、刮伤的钣金毛胚半成品需进行返工打磨,打磨后不允许有明显手感 与生锈的异常现象。钣金件与钣金件焊接后焊点表面允许有轻微的凹凸痕,表面凹凸 痕高度控制在0.2mm以内长与宽不超出尺寸20*20mm;拉伸产品折边表面允许有轻微、 与不明显的拉伸痕 7、有接地标志的零件,接地标志应圆整,清晰可见,无明显歪斜;接地标示方向一致、 大小标准化统一规定为φ8直径 8、非喷涂件表面应洁净、无杂物、无油污、无明显灰尘、黑斑、锈蚀、发白、脱锌等 外观异常现象,并无明显刮手的机械划伤痕和严重拉伤痕,产品翻边孔不允许开裂; 产品表面允许有1到2个轻微小凹凸点
案例
水箱上盖
案例
模块机电机支架
案例
常见定位方式:1.落料模具定位,2, 全定位,3、复合式定位。
案例
工艺孔定位
4、板料成形过程的常见缺陷及产生原因分析
• • • • • 起皱和叠料 产生原因: 1)、由于局部压应力过大导致薄板失稳所致,正好与拉裂的产生原因相反。 2)、两种应力状态容易起皱,环向应力:法向起皱与侧壁起皱失稳。 3)、当冲压件的周长不断减少,此时只要板料中未受支撑,区域的长度与厚度之 比较大就会起皱。 后果: 1)、影响零件的精度和美观性; 2)、影响下一道工序的正常进行。 一般解决方法: 1)、增加起皱处的法向接触力(有导致其他部位被拉裂的危险); 2)、准确预测材料的流动情况; 3)、产品形状和模具形状 ; 4)、增大压边力; 5)、增加拉延筋数量或者增加高度。
案例
• 1.A5机中间横梁,正反冲。
3、冲压的几个设计注意点
• • • • 二、压料面的确定: 压料面形状是保证拉延过程中材料不破裂和顺利成型的首要条件。 压料面分为两种: A、压料面在产品本身边缘处,这种压料面形状是即定的,无法做大幅度调整,为 了便于拉伸,局部可以放大,但保证后序可以进行整形。 B.压料面是由工艺补充部分形成的,必须保证上模压紧压边圈后料片不能出现皱 纹和折痕,保证凸模对板料拉紧,否则在拉延过程板料会出现波纹或皱纹。 考虑方向: 1、降低拉延深度。第一种压料面是产品面,压料面已经定型,不涉及降低拉延深 度。压料面一般呈弯曲形状,可以使拉延深度降低。另一种是水平的压料面,针 对零件高度变化不大的形状适用。 2、为保证板件成型刚性,压料面的线长应小于凸模的线长,这样才能保证料片充 分拉伸且不会起皱。 3、压料面尽量简单,平滑光顺有利于料片流动。压料面上不允许有局部鼓包、, 凹坑和下陷,如果存在后序追加整形。压料面与各拉伸深度尽量一致,材料流动 和塑性变形均匀,减少成型难度。压边圈压住板料时不允许褶皱和扭曲。保证后 工序定位和进出料方便。
• •
企业标准介绍----常见不合格标准介绍
• •
• • • • • • •
9、冲压件切口允许有毛刺。非喷涂钣金件毛刺高度不大于0.07mm;喷涂件用钣 金毛胚半成品毛刺高度不大于0.05mm。 数控冲床钣金件切口允许有毛刺,毛刺高度不大于1.00 mm;喷涂件用钣金毛胚半 成品毛刺高度不大于0.8mm,边板翻边孔毛刺朝孔外,毛刺高度不超过0.07mm
10、焊点的大小及排列应符合图纸要求,焊点应平整圆整,无焊穿、松焊、虚焊及周 边严重飞溅现象,非喷涂钣金件焊点应涂银油,无明显生锈现象 11、喷涂件用钣金毛胚半成品焊点不涂银油 12、钣金与钣金之间点焊后需喷涂件,在喷涂前必须先将焊点处进行磨平处理;喷涂 后产品凹点处不能超过0.2mm 13、冲压件上粘贴的海绵件、绒布等,应粘贴牢固平整,不得有变形、撕裂、破损、 松脱、翘起等现象 14、非喷涂冲压件,除电控盒、防火钣金以及图纸有明确要求的表面不允许有油外, 其它产品表面允许有不明显的冲压成型后残留的防护油 15、非喷涂钣金件按GB/T10125规定对零件进行中性盐雾试验,16小时后无白锈和大面 积变黑, 96小时后,试验表面无基体锈蚀现象。 喷涂件用钣金毛胚半成品按GB/T10125规定对零件进行中性盐雾试验,96小时后,切口、 焊点或拆角以外的试验表面部位无基体锈蚀现象。
• • • • • • •
2、焊接性能 螺钉焊接:用胶棒将焊在底盘上的压缩机螺钉或焊在蜗壳后板上的电机螺钉,用力敲 击使之承受外力矩及向下冲击力,螺钉倾钭一定角度(约15°)后焊点仍焊接牢固, 无脱焊、松焊现象。 板材焊接:用强力将焊接的两部分分开,焊接件必须在焊点四周脱裂,而焊点本身没 有脱离。 3、构件尺寸 对加工后易变形而装后能恢复正确几何形状的成形件,在自由状态下,实际尺寸允 许超过极限尺寸,但装配后实际尺寸应在其极限偏差尺寸范围内。 4、焊接尺寸 零件与零件焊接后的尺寸,应符合图纸要求。底脚与底盘、压缩机螺栓与底盘焊接后, 应互相紧贴,间隙不应超过0.30mm。
•
• • • • •
案例
水箱上盖
3、冲压的几个设计注意点
• • • • • • • 三、定位方式: 1、板件在拉延模上必须设计素材定位器,注意板件在压料面的重力状态的下 垂形状。 2、如果压料面高低起伏比较大时应考虑设计气动式夹钳。 3、后工序定位一般有几种情况:形状定位,废料刀定位,外形轮廓定位,孔 定位。 4、后工序上模和压料芯除工作部位保留压料外其它部位全部逃料加工,减少 研配时间。 5、后工序下模注意板件定位型面,一般保留中间和侧壁局部,保证上下和左 右定位准确。 四、工艺补充面设计。五、工艺孔及刺破刀。六、拉延筋和拉延槛、七: CAE分析等。
案例
• 左侧板
案例
• 模块机顶盖
案例
• A5机顶盖
企业标准介绍----常见不合格标准介绍
•
•
1、涂层表面质量:在正常光线下,眼睛与样品待测面距离400mm~500mm,成 120°~140°角度观看,检测样品表面质量。