6磨削精度与表面质量
磨削原理
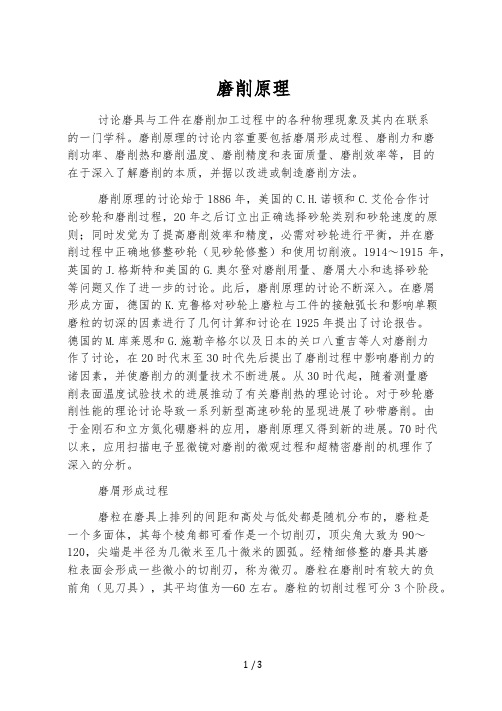
磨削原理讨论磨具与工件在磨削加工过程中的各种物理现象及其内在联系的一门学科。
磨削原理的讨论内容重要包括磨屑形成过程、磨削力和磨削功率、磨削热和磨削温度、磨削精度和表面质量、磨削效率等,目的在于深入了解磨削的本质,并据以改进或制造磨削方法。
磨削原理的讨论始于1886年,美国的C.H.诺顿和C.艾伦合作讨论砂轮和磨削过程,20年之后订立出正确选择砂轮类别和砂轮速度的原则;同时发觉为了提高磨削效率和精度,必需对砂轮进行平衡,并在磨削过程中正确地修整砂轮(见砂轮修整)和使用切削液。
1914~1915年,英国的J.格斯特和美国的G.奥尔登对磨削用量、磨屑大小和选择砂轮等问题又作了进一步的讨论。
此后,磨削原理的讨论不断深入。
在磨屑形成方面,德国的K.克鲁格对砂轮上磨粒与工件的接触弧长和影响单颗磨粒的切深的因素进行了几何计算和讨论在1925年提出了讨论报告。
德国的M.库莱恩和G.施勒辛格尔以及日本的关口八重吉等人对磨削力作了讨论,在20时代末至30时代先后提出了磨削过程中影响磨削力的诸因素,并使磨削力的测量技术不断进展。
从30时代起,随着测量磨削表面温度试验技术的进展推动了有关磨削热的理论讨论。
对于砂轮磨削性能的理论讨论导致一系列新型高速砂轮的显现进展了砂带磨削。
由于金刚石和立方氮化硼磨料的应用,磨削原理又得到新的进展。
70时代以来,应用扫描电子显微镜对磨削的微观过程和超精密磨削的机理作了深入的分析。
磨屑形成过程磨粒在磨具上排列的间距和高处与低处都是随机分布的,磨粒是一个多面体,其每个棱角都可看作是一个切削刃,顶尖角大致为90~120,尖端是半径为几微米至几十微米的圆弧。
经精细修整的磨具其磨粒表面会形成一些微小的切削刃,称为微刃。
磨粒在磨削时有较大的负前角(见刀具),其平均值为—60左右。
磨粒的切削过程可分3个阶段。
①滑擦阶段:磨粒开始挤入工件,滑擦而过,工件表面产生弹性变形而无切屑。
②耕犁阶段:磨粒挤入深度加大,工件产生塑性变形,耕犁成沟槽,磨粒两侧和前端堆高隆起;③切削阶段:切入深度连续增大,温度达到或超过工件材料的临界温度,工件材料明显地沿剪切面滑移而形成磨屑。
各种加工方法的加工精度
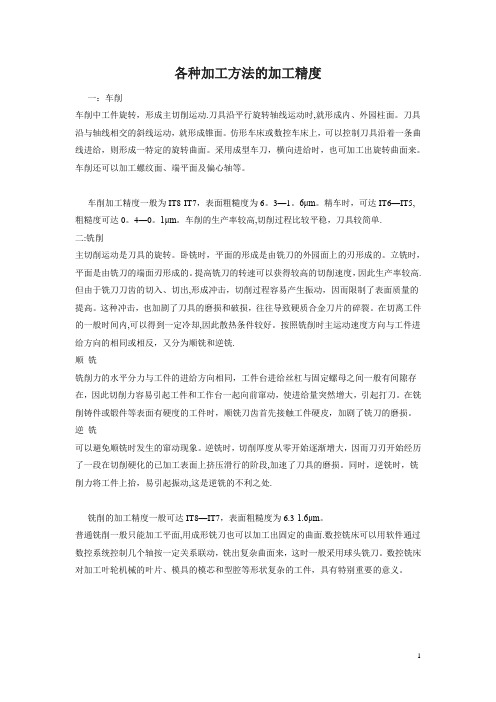
各种加工方法的加工精度一:车削车削中工件旋转,形成主切削运动.刀具沿平行旋转轴线运动时,就形成内、外园柱面。
刀具沿与轴线相交的斜线运动,就形成锥面。
仿形车床或数控车床上,可以控制刀具沿着一条曲线进给,则形成一特定的旋转曲面。
采用成型车刀,横向进给时,也可加工出旋转曲面来。
车削还可以加工螺纹面、端平面及偏心轴等。
车削加工精度一般为IT8-IT7,表面粗糙度为6。
3—1。
6μm。
精车时,可达IT6—IT5,粗糙度可达0。
4—0。
1μm。
车削的生产率较高,切削过程比较平稳,刀具较简单.二:铣削主切削运动是刀具的旋转。
卧铣时,平面的形成是由铣刀的外园面上的刃形成的。
立铣时,平面是由铣刀的端面刃形成的。
提高铣刀的转速可以获得较高的切削速度,因此生产率较高.但由于铣刀刀齿的切入、切出,形成冲击,切削过程容易产生振动,因而限制了表面质量的提高。
这种冲击,也加剧了刀具的磨损和破损,往往导致硬质合金刀片的碎裂。
在切离工件的一般时间内,可以得到一定冷却,因此散热条件较好。
按照铣削时主运动速度方向与工件进给方向的相同或相反,又分为顺铣和逆铣.顺铣铣削力的水平分力与工件的进给方向相同,工件台进给丝杠与固定螺母之间一般有间隙存在,因此切削力容易引起工件和工作台一起向前窜动,使进给量突然增大,引起打刀。
在铣削铸件或锻件等表面有硬度的工件时,顺铣刀齿首先接触工件硬皮,加剧了铣刀的磨损。
逆铣可以避免顺铣时发生的窜动现象。
逆铣时,切削厚度从零开始逐渐增大,因而刀刃开始经历了一段在切削硬化的已加工表面上挤压滑行的阶段,加速了刀具的磨损。
同时,逆铣时,铣削力将工件上抬,易引起振动,这是逆铣的不利之处.铣削的加工精度一般可达IT8—IT7,表面粗糙度为6.3-1.6μm。
普通铣削一般只能加工平面,用成形铣刀也可以加工出固定的曲面.数控铣床可以用软件通过数控系统控制几个轴按一定关系联动,铣出复杂曲面来,这时一般采用球头铣刀。
数控铣床对加工叶轮机械的叶片、模具的模芯和型腔等形状复杂的工件,具有特别重要的意义。
磨削表面质量
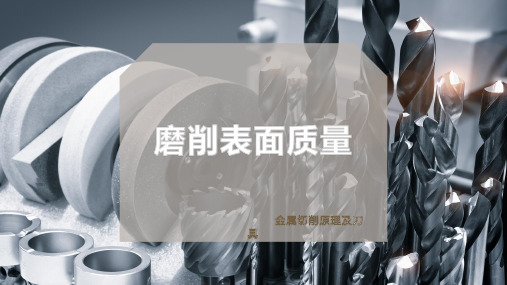
磨削表面质量包括磨削表面的粗糙度和磨削表面的物理力学性 能两方面。
1.1 磨削表面的粗糙度
磨削表面的粗糙度是由磨粒磨削后在加工表面上形成残留廓形 和工艺系统振动所引起的波纹所决定的。
其一般形式为:
R
K R
f
r
vw v
b
fa B
c
1.2 磨削表面的物理力学性能
1.磨削表面烧伤 磨削钢材时,开始钢材表面呈正常的金属光泽,随后逐渐转为黄褐
色甚至成为紫黑色,这就是磨削表面的烧伤现象。 若工件表面颜色为淡黄色,则其磨削温度约为400~500 ℃,其烧
伤深度较浅;若工件表面颜色为紫色,则其磨削温度约为800 ~900 ℃, 其烧伤深度较深。
影响磨削表面烧伤的因素主要有以下几点:
(1)磨削用量。砂轮线速度v及径向进给量fr的影响较砂轮线速度v及径向 进给量fr的增大,烧伤逐渐严重。工件速度vw的影响较小,只有当vw极 小时,才会出现烧伤。
磨削过程中,当形成的残余拉应力超过工件材料的强度极限时,工 件表面就会出现裂纹。
磨削裂纹极浅,呈网状或垂直于磨削方向。有时不在其表层,而存 在于其表层之下。有时在研磨或使用过程中,由于去除了其表面极薄金 属层后,残余应力失去平衡,因而形成微小裂纹。这些微小裂纹,在交 变载荷作用下,会迅速扩展,以造成工件的破坏。
(2)接触长度。砂轮与工件的接触长度大,易堵塞砂轮而不易冷却, 容易出现烧伤。
磨削表面烧伤的实质是使工件产生了金相组织变化,会破坏工件表 层组织,严重时会产生裂纹,严重影响工件的耐磨性和使用寿命。因此, 必须避免磨削烧伤。
2.磨削表面的残余应力与磨削裂纹 磨削表面的残余应力是由于磨削过程中金属体积发生变化
等因素形成的。 其中由于磨削温度的不均匀将形成热应力,一般为拉应力; 由于金相组织的变化将形成相变应力,可能为拉应力或压
jis磨床验收标准

JIS磨床验收标准一、型号与规格1. 本次验收的磨床型号为xxxx,规格符合要求。
2. 磨床的主要参数,如砂轮尺寸、最大磨削直径、最大磨削厚度等,均符合设计要求。
二、尺寸精度1. 磨床的床身导轨直线度误差不大于0.01mm/500mm。
2. 工作台面纵向移动直线度误差不大于0.01mm/500mm。
3. 工作台横向移动直线度误差不大于0.01mm/500mm。
4. 砂轮主轴轴向窜动不超过0.01mm。
5. 砂轮径向圆跳动不超过0.01mm。
三、表面粗糙度1. 磨削表面的粗糙度应符合设计要求,一般要求Ra不大于0.8μm。
2. 表面粗糙度的检测方法采用轮廓仪测量。
四、磨削精度1. 磨削工件的尺寸精度应符合设计要求,一般要求尺寸偏差不超过±0.01mm。
2. 磨削工件的几何形状精度应符合设计要求,如圆度、圆柱度等。
3. 磨削工件的表面粗糙度应符合设计要求。
4. 磨削工件的精度检测方法可采用千分尺、测微仪、轮廓仪等工具进行测量。
五、重复定位精度1. 磨床的重复定位精度应不大于0.01mm。
2. 重复定位精度的检测方法可采用激光干涉仪进行测量。
六、电气系统1. 磨床的电气系统应符合设计要求,运行稳定可靠。
2. 电气系统的元件和部件应符合相关标准,如电压、电流、绝缘电阻等。
3. 电气系统的安全保护装置应有效可靠。
七、液压系统1. 磨床的液压系统应符合设计要求,运行稳定可靠。
2. 液压系统的元件和部件应符合相关标准,如压力、流量、密封性等。
3. 液压系统的安全保护装置应有效可靠。
八、外观质量1. 磨床的外观质量应符合设计要求,表面光滑平整,无明显划痕和磕碰痕迹。
2. 外观质量的检测方法可采用目视观察和手感触摸等方法进行检测。
磨削生产工艺流程
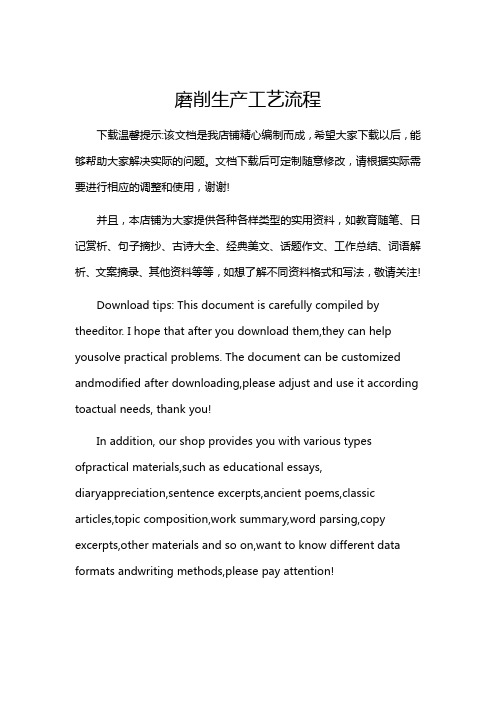
磨削生产工艺流程下载温馨提示:该文档是我店铺精心编制而成,希望大家下载以后,能够帮助大家解决实际的问题。
文档下载后可定制随意修改,请根据实际需要进行相应的调整和使用,谢谢!并且,本店铺为大家提供各种各样类型的实用资料,如教育随笔、日记赏析、句子摘抄、古诗大全、经典美文、话题作文、工作总结、词语解析、文案摘录、其他资料等等,如想了解不同资料格式和写法,敬请关注!Download tips: This document is carefully compiled by theeditor. I hope that after you download them,they can help yousolve practical problems. The document can be customized andmodified after downloading,please adjust and use it according toactual needs, thank you!In addition, our shop provides you with various types ofpractical materials,such as educational essays, diaryappreciation,sentence excerpts,ancient poems,classic articles,topic composition,work summary,word parsing,copy excerpts,other materials and so on,want to know different data formats andwriting methods,please pay attention!磨削生产工艺流程磨削生产工艺流程磨削生产工艺流程包括磨削准备、磨削加工、磨削后处理等步骤。
磨削加工中的磨削精度

磨削加工中的磨削精度是指在磨削过程中所能达到的精度程度。
磨削加工是一种高精度的加工方法,可以制造出高精度零件,能够满足不同的制造需求。
磨削加工由于其高精度,广泛应用于航空、汽车、机床、电子、仪器仪表等领域,并成为制造业中不可或缺的工艺。
我国在磨削技术方面有着悠久的历史,早在汉代就已经出现了磨轮,磨削技术的发展可以追溯到数千年前。
随着工业的迅速发展,磨削技术也不断地得到提高、完善。
从最初的手工磨削,到机械化磨削,再到电脑化磨削,每一步的发展都提高了磨削加工的精度。
在实际的磨削加工中,要提高磨削精度,需要从多个方面入手。
首先,选择合适的磨削机床非常重要,不同类型的机床适用于不同的磨削任务。
其次,磨削工具的选择也是决定磨削精度的一个重要因素。
以磨削刃磨为例,磨削刃磨是指在磨削过程中利用磨削工具对刃口进行磨削,这要求磨削工具具有高精度、高效率、高耐磨性等特点。
此外,还需要注意磨削工具的材质选择,不同的材质对磨削效果会有很大的影响。
除了选择合适的磨削机床和磨削工具,磨削精度还与磨削的过程参数密切相关。
磨削的过程参数包括切削速度、进给速度、磨削深度、磨削力、冷却液等方面,这些参数的优化能够显著影响磨削加工质量。
例如在切削速度选择方面,通常情况下磨削速度越高,磨削效率越高,但是同时也会增加磨削热量,导致磨削过程变形和表面质量下降,因此需要根据实际情况,选择适当的切削速度。
此外,正确调整磨削加工中的磨削参数也是提高磨削精度的关键。
在实际工作中,可以采用计算机模拟的方法对磨削过程进行模拟和优化,这可以帮助工程师更好地了解磨削过程中的物理和化学机制,同时可以帮助工程师查找和解决磨削中可能遇到的问题。
总之,对零部件的质量和性能有着重要的影响,提高磨削精度是制造高精度零部件和产品的关键。
在磨削加工中要选择适当的机床和磨削工具,同时优化磨削过程参数和磨削参数的调整,这些都可以帮助工程师提高磨削精度,生产出更好质量的产品,使制造业在市场中更具竞争力。
磨削加工基础知识

磨削加工基础知识磨削加工是一种高精度的加工方法,具有高效、精度高、表面质量好等优点,被广泛应用于机械制造、航空航天、光学、电子、仪器仪表、医疗器械等领域。
磨削加工的基础知识对于理解磨削加工的工艺特点和实现高精度、高效加工具有重要意义。
第一、磨削加工的原理与工艺特点磨削加工是利用磨削工具对工件进行高速旋转运动和相对移动,通过对工件表面的撞击和摩擦作用,使工件表面物质逐渐脱落,同时形成较高的表面质量。
磨削工具是一个至关重要的部分,其轮廓、材料、粒度、硬度等参数会直接影响磨削效果。
同时,磨削加工具有高效、高精度、表面质量好的特点。
磨削加工时,磨削工具旋转高速,加工效率非常高。
同时,由于磨削加工的切削深度非常小,可以实现高精度加工。
此外,通过加工工艺优化,还可以获得高精度的工件表面质量。
第二、磨削加工的工具与磨削方法磨削工具是磨削加工的核心之一。
常用的磨削工具有磨石、磨轮、砂布轮、抛光布轮等,它们由不同的材料和制造工艺制成,具有不同的加工能力。
常见的磨削方法有平面磨削、圆柱磨削、内圆磨削、外圆磨削、表面磨削等。
通过选择合适的磨削工具和磨削方法,可以实现不同形状和精度要求的工件加工。
第三、磨削加工的加工参数在进行磨削加工时,需要设置一系列加工参数,包括磨削工具的转速、磨削深度、进给量、磨削液的类型和流量等。
这些参数直接影响着工件的加工效果和工具的使用寿命。
例如,在选择磨削工具的时候,需要考虑工件的材料、精度和表面质量要求等因素,选择合适的材料、形状、粒度磨削工具。
在设置磨削深度和进给量时,需要根据工件材料是否易碎、磨削强度等因素进行综合考虑。
第四、磨削加工的提高磨削加工的加工精度和表面质量程度是衡量磨削加工质量的重要指标。
为了提高磨削加工的质量和效率,可以从以下方面进行优化。
首先是磨削工具的性能提升,如开发新型材料、制造工艺等。
其次是加工参数的优化,通过对加工深度、进给量和磨削液的改进,可以进一步提高加工效果和工具的使用寿命。
磨床主要磨削精度和各部件安装指标指标

磨床主要磨削精度和各部件安装指标指标磨床是一种专门用于金属材料的磨削加工设备,广泛应用于机械加工行业。
磨床的主要磨削精度和各部件安装指标是决定磨床加工质量和性能的重要参数。
下面将详细介绍磨床的主要磨削精度和各部件安装指标。
第一、磨床的主要磨削精度指标包括以下几个方面:1.平行度:平行度是指磨削面与床身导轨的平行度,主要影响磨削的垂直度和平行度。
要求加工的工件表面平行度高,需要床身导轨与磨削面之间的平行度保证在规定范围内。
2.垂直度:垂直度是指磨削面与工作台面的垂直度,主要影响磨削表面的垂直度和平面度。
磨床的磨削面与工作台面之间的垂直度需要高精度控制,以保证磨削表面的平整度和垂直度。
3.平面度:平面度是指工件表面平坦的程度,主要影响磨削表面的平整度和垂直度。
磨床的平面度要求较高,可以通过对磨床的床身导轨、工作台面等关键部件的加工和磨削精度进行控制。
4.圆度:圆度是指磨削的圆形工件表面的几何形状偏差,主要影响磨削的圆形度和直线度。
磨床对工件表面的圆度要求较高,需要通过对磨床主轴、工作台面等关键部件的加工和调试来保证。
第二、磨床的各部件安装指标包括以下几个方面:1.导轨安装:导轨是磨床的关键部件之一,直接影响磨床的稳定性和加工精度。
导轨的安装准确度包括导轨直线度、垂直度和水平度等。
2.主轴安装:主轴是磨床的关键部件之一,直接影响磨削表面的质量和精度。
主轴的安装准确度包括主轴与床身导轨的平行度、主轴与工作台面的垂直度等。
3.进给系统安装:进给系统是磨床实现精确进给运动的关键部件之一,直接影响磨削的平直度和表面粗糙度。
进给系统的安装准确度包括进给导轨的平行度、进给导轨与工作台面的垂直度等。
4.电气系统安装:磨床的电气系统是实现磨床各功能和动作的关键部件之一,直接影响磨床的控制精度和稳定性。
电气系统的安装准确度包括电机的定位准确度、传感器的安装位置和精度等。
综上所述,磨床的主要磨削精度和各部件安装指标是决定磨床加工质量和性能的重要参数。
磨盘的加工精度验收标准与方法

磨盘的加工精度验收标准与方法摘要:磨盘加工精度是评估加工质量的重要指标。
本文通过介绍磨盘加工精度的意义和影响因素,详细阐述了磨盘加工精度验收标准的制定和常用的验收方法。
同时,还提供了提高磨盘加工精度的建议,以确保加工过程的质量和效率。
关键词:磨盘加工精度;验收标准;验收方法;提高精度1. 引言磨盘是一种用于对工件进行磨削加工的工具,被广泛应用于机械制造、汽车工业、航空航天等领域。
磨盘加工精度是评估加工质量的重要指标,直接影响到工件的尺寸精度、表面质量和加工效率。
因此,建立科学合理的磨盘加工精度验收标准和方法,对于保证加工质量和提高生产效率具有重要意义。
2. 磨盘加工精度的影响因素磨盘加工精度受到多个因素的影响,主要包括磨盘材料、磨削参数、磨盘形状、工件材料和加工方式等。
2.1 磨盘材料磨盘材料的选择直接关系到磨盘的耐磨性、刚性和热稳定性。
优质的磨盘材料能够保证磨盘加工精度的稳定性和一致性。
2.2 磨削参数磨削参数包括进给速度、转速、磨削深度和磨削时间等,直接影响磨盘与工件的接触力和磨削量。
合理选择和控制磨削参数对于提高磨盘加工精度非常重要。
2.3 磨盘形状磨盘形状对于加工效果和精度有着重要影响。
磨盘的波纹度、平面度和圆度等需要根据具体的加工要求来选择和控制。
2.4 工件材料工件材料的硬度、韧性和热稳定性等特性也会对磨盘加工精度产生影响。
不同材料的工件需要针对性地选择合适的磨盘材料和加工参数。
2.5 加工方式磨盘加工有手工磨削、精密机床磨削、超高速磨削等多种方式,不同的加工方式对磨盘加工精度有不同的要求和适应性。
3. 磨盘加工精度验收标准的制定制定科学合理的磨盘加工精度验收标准是保证加工质量的重要手段。
以下是常见的磨盘加工精度验收标准指标:3.1 圆度圆度是评价磨盘加工精度的重要指标之一。
磨盘加工的工件应具有符合规范要求的圆度,通常以一个标准圆度值进行验收标准的设定。
3.2 平面度平面度是指工件与参考平面之间的偏差大小。
【金属切削原理】第12章:磨削详解
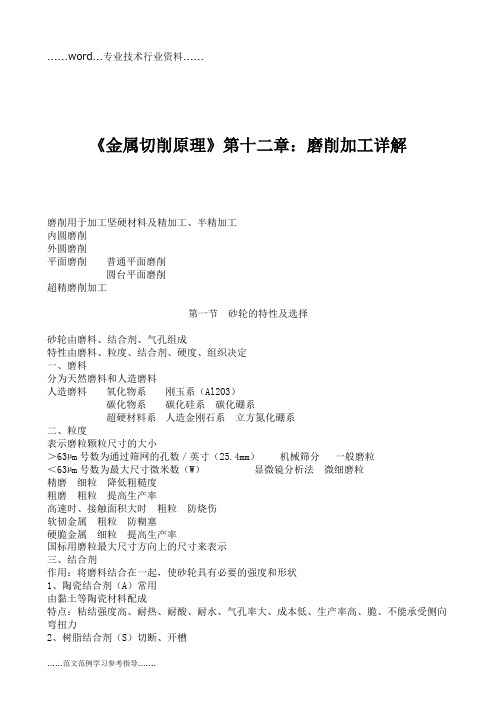
《金属切削原理》第十二章:磨削加工详解磨削用于加工坚硬材料及精加工、半精加工内圆磨削外圆磨削平面磨削普通平面磨削圆台平面磨削超精磨削加工第一节砂轮的特性及选择砂轮由磨料、结合剂、气孔组成特性由磨料、粒度、结合剂、硬度、组织决定一、磨料分为天然磨料和人造磨料人造磨料氧化物系刚玉系(Al2O3)碳化物系碳化硅系碳化硼系超硬材料系人造金刚石系立方氮化硼系二、粒度表示磨粒颗粒尺寸的大小>63µm号数为通过筛网的孔数/英寸(25.4mm)机械筛分一般磨粒<63µm号数为最大尺寸微米数(W)显微镜分析法微细磨粒精磨细粒降低粗糙度粗磨粗粒提高生产率高速时、接触面积大时粗粒防烧伤软韧金属粗粒防糊塞硬脆金属细粒提高生产率国标用磨粒最大尺寸方向上的尺寸来表示三、结合剂作用:将磨料结合在一起,使砂轮具有必要的强度和形状1、陶瓷结合剂(A)常用由黏土等陶瓷材料配成特点:粘结强度高、耐热、耐酸、耐水、气孔率大、成本低、生产率高、脆、不能承受侧向弯扭力2、树脂结合剂(S)切断、开槽酚醛树脂、环氧树脂特点:强度高、弹性好、耐热性差、易自砺、气孔率小、易糊塞、磨损快、易失廓形、与碱性物质易反应、不易长期存放3、橡胶结合剂(X)薄砂轮、切断、开槽、无心磨导轮人造橡胶特点:弹性好、强度好、气孔小、耐热性差、生产率低4、金属结合剂(Q)磨硬质合金、玻璃、宝石、半导体材料青铜结合剂(制作金刚石砂轮)特点:强度高、自砺性差、形面成型性好、有一定韧性四、硬度在磨削力作用下,磨粒从砂轮表面脱落的难易程度分为超软、软、中软、中、中硬、硬、超硬工件材料硬砂轮软些防烧伤工件材料软砂轮硬些充分发挥磨粒作用接触面积大软砂轮精度、成形磨削硬砂轮保持廓形粒度号大软砂轮防糊塞有色金属、橡胶、树脂软砂轮防糊塞五、组织磨粒、气孔、结合剂体积的比例关系分为:紧密(0~3)、中等(4~7)、疏松(8~14)(磨粒占砂轮体积%↘)气孔、孔穴开式(与大气连通)占大部分,影响较大闭式(与大气不连通)尺寸小、影响小开式空洞型蜂窝型前两种构成砂轮内部主要的冷却通道管道型5~50µm六、砂轮的型号标注形状、尺寸、磨料、粒度号、硬度、组织号、结合剂、允许最高圆周线速度P300x30x75WA60L6V35外径300,厚30,内径75第二节磨削运动一、磨削运动1、主运动砂轮外圆线速度 m/s2、径向进给运动进给量fr 工件相对砂轮径向移动的距离间歇进给 mm/st 单行程mm/dst 双行程连续进给 mm/s3、轴向进给运动进给量fa 工件相对砂轮轴向的进给运动圆磨 mm/r平磨 mm/行程4、工件速度vw线速度 m/s二、磨削金属切除率ZQ=Q/B=1000·vw·fr·fa/B mm^3/(s·mm)ZQ:单位砂轮宽度切除率Q:每秒金属切除量用以表示生产率B:砂轮宽度三、砂轮与工件加工表面接触弧长lc=sqrt(fr·d0)影响参加磨削磨粒数目及磨粒负荷,容屑,冷却条件四、砂轮等效直径将外圆(内圆)砂轮直径换算成接触弧长相等的假想平面磨削的砂轮直径结论:对砂轮耐用度影响内圆>平面>外圆第三节磨削的过程一、单个磨粒的磨削过程磨粒的模型锐利120°圆锥钝化半球实际磨粒:大的负前角,大的切削刃钝圆半径滑擦、耕犁、切削滑擦:(不切削,不刻划)产生高温,引起烧伤裂纹耕犁:(划出痕迹)磨粒钝或切削厚度小于临界厚度,工件材料挤向两侧隆起切削:切削厚度大于临界厚度,形成切屑v↑→隆起↓(线性)塑性变形速度<磨削速度二、磨削的特点1、精度高、表面粗糙度小高速、小切深、机床刚性2、径向分力Fn较大多磨粒切削3、磨削温度高磨粒角度差、挤压和摩擦、砂轮导热差4、砂轮的自砺作用三、磨削的阶段1、初磨阶段实际磨深小于径向进给量2、稳定阶段实际磨深等于径向进给量3、清磨阶段实际磨深趋向于0提高生产率缩短1、2提高质量保证3第四节磨削力及磨削功率一、磨削力的特征分解成三个分力Ft切向力 Fn法向力 Fa轴向力特征:1、单位切削力k很大磨粒几何形状的随机性和参数的不合理性7000~20000kgf/mm^2 其他切削方式k<700kgf/mm^22、Fn值最大Fn/Ft 通常2.0~2.5工件塑性↓、硬度↑→Fn/Ft↑切深小,砂轮严重磨损 Fn/Ft 可达5~103、磨削力随磨削阶段变化初磨、稳定、光磨二、磨削力及磨削功率摩擦耗能占相当大的比例(70~80%)切向力(N):Ft=9.81·(CF·(vw·fr·B/v)+µ·Fn)径向力(N):Fn=9.81·CF·(vw·fr·B/v)·tan(α)·(π/2) vw:工件速度v:砂轮速度fr:径向进给量B:磨削宽度CF:切除单位体积切屑所需的能 kgf/mm^2µ:工件-砂轮摩擦系数α:假设粒度为圆锥时的锥顶半角磨削功率P=Ft·v/1000 Kw理论公式精度不高,常用实验测定(顶尖上安装应变片)第五节磨削温度耕犁、滑擦和形成切屑的能量全部转化成热,大部分传入工件一、磨削温度砂轮磨削区温度θA:砂轮与工件接触区的平均温度影响:烧伤、裂纹的产生磨粒磨削点温度θdot:磨粒切削刃与切屑接触部分的温度温度最高处,是磨削热的主要来源影响:表面质量、磨粒磨损、切屑熔着工件温升:影响:工件尺寸、形状精度受影响二、影响磨削温度的因素切削液为降温的主要途径1、工件速度对磨粒磨削点温度的影响大于砂轮速度vw↑→acgmax↑→F↑→θdot↑大v↑→acgmax↓→θdot↑小→摩擦热↑↗acgmax:单个磨粒最大切削厚度 mm假设:磨粒前后对齐,均匀分不在砂轮表面平面磨:acgmax=(2·vw·fa/(v·m·B))sqrt(fr/dt)外圆磨:acgmax=(2·vw·fa/(v·m·B))sqrt((fr/dt)+(fr/dw))dt:砂轮直径m:每毫米周长磨粒数用于定性分析2、径向进给量Frfr↑→acgmax↑→θdot↑fr↑→接触区↑→同时参加切削磨粒数↑→θA↑3、其他因素fa↑→θdot↑、θA↑工件材料硬度↑、强度、↑韧性↑→θdot↑、θA↑θA↑→工件温升↑vw↑→被磨削点与砂轮接触时间↓→工件温升↗三、磨削温度的测量(热电偶)第六节砂轮的磨损及表面形貌一、砂轮的磨损类型磨耗磨损磨粒磨损破碎磨损磨粒或结合剂破碎(取决于磨削力与磨粒、结合剂强度)破碎磨损消耗砂轮多磨耗磨损通过磨削力影响破碎磨损阶段初期磨损磨粒破碎磨损(个别磨粒受力大,磨粒内部应力与裂纹)二期磨损磨耗磨损三期磨损结合剂破碎磨损二、砂轮的耐用度T砂轮相邻两次修整期间的加工时间 s各因素通过平均切削厚度来影响T经验公式:T=6.67·(dw^0.6)·km·kt/(10000·(vw·fa·fr)^2)dw:工件直径kt:砂轮直径修正系数km:工件材料修正系数粗磨时间常用单位时间内磨除金属体积与砂轮磨耗体积之比来选择砂轮三、砂轮的修整作用去除钝化磨粒或糊塞住的磨粒,使新磨粒露出来增加有效切削刃,提高加工表面质量工具单颗金刚石、单排金刚石、碳化硅修整轮、电镀人造金刚石滚轮、硬质合金挤压轮等使用单颗金刚石:导程小于等于磨粒平均直径,每颗磨粒都能修整深度小于等于磨粒平均直径,提高砂轮寿命四、表面形貌单位面积上磨粒数目越多→acgmax↓→磨粒受力↓→磨粒寿命↑→T↑磨粒高度分布越均匀→粗糙度↓磨粒间距均匀性越好→粗糙度↓第七节磨削表面质量与磨削精度一、表面粗糙度比普通切削小小于 Ra2~4µmvw↓、v↑、R工↑、R砂↑、细粒度→粗糙度↓细粒度→m↑→粗糙度↓B↑→acgmax↓→粗糙度↓磨粒等高性好→粗糙度↓二、机械性能1、金相组织变化烧伤:C↑、合金元素↑→导热性↓→易烧伤高温合金↑→磨削功率↑→θA↑→易烧伤影响:破坏工件表层组织,产生裂纹,影响耐磨性和寿命2、残余应力原因:相变引起金相组织体积变化温度引起热胀冷缩和塑性变形的综合结果光磨10次残余应力减少2~3倍光磨15次残余应力减少4~5倍fa↓、fr↓→拉应力↓3、磨削裂纹磨削速度垂直方向上的裂纹(局部高温急冷造成热应力)三、磨削精度1、磨床与工件的弹性变形2、磨床与工件的热变形3、砂轮磨损导致形状尺寸变化3、磨床与工件振动研磨加工是应用较广的一种光整加工。
六级精度齿轮齿形加工方案

六级精度齿轮齿形加工方案
六级精度齿轮齿形加工方案
为了满足现代工业对高精度齿轮的需求,六级精度齿轮的齿形加工方案变得尤为重要。
在齿形加工过程中,齿轮的准确性和表面质量是关键因素,在保证齿轮传动性能的同时,还要考虑生产效率和成本控制。
首先,选择合适的齿轮加工设备非常重要。
高精度齿轮加工通常需要使用先进的数控齿轮加工机床,例如齿轮磨床或齿轮滚齿机。
这些设备具有高刚性和高精度的导轨系统,可以保证齿轮的准确性和表面质量。
其次,合理的刀具选择和刀具磨制也是关键。
高精度齿轮加工常使用刀具磨削的方式进行,因为磨削可以提供更高的精度和表面质量。
刀具的选择应根据齿轮的材料和齿轮类型进行优化,以确保精密加工和长寿命。
接下来,加工过程中的参数设置也需要仔细考虑。
切削速度、进给速度和切削深度等参数都会对齿轮的准确性和表面质量产生影响。
通过合理地选择和控制这些参数,可以最大程度地降低误差和提高加工效率。
此外,采用适当的测量和检测手段对加工过程进行监控和调整也是必要的。
高精度齿轮加工常采用光学测量仪器、坐标测量机和轮廓仪等设备进行精密测量和表面质量检测,以保证齿轮的质量符合要求。
综上所述,六级精度齿轮齿形加工方案需要综合考虑设备选择、刀具优化、参数控制和测量检测等方面,以确保齿轮的高精度和表面质量。
这些措施的合理应用可以提高齿轮传动的可靠性和效率,满足现代工业对高精度齿轮的需求。
简述磨削的工艺特点

简述磨削的工艺特点磨削是一种常见的金属加工工艺,用于将工件的表面进行细磨、精磨和抛光,以达到提高工件精度和表面质量的目的。
磨削的工艺特点主要包括以下几个方面:1. 磨削具有高精度和高表面质量的特点。
相比于其他金属加工工艺,磨削可以实现更高的加工精度,达到更高的表面质量要求。
磨削可以将工件的精度提高到数微米甚至亚微米级别,使得工件表面光洁度达到较高的要求。
2. 磨削具有广泛的适用性。
磨削可以适用于各种形状的工件,包括平面、曲面、圆柱面、锥面等。
而且,磨削可以加工各种不同材料的工件,如钢、铸铁、铜、铝、塑料等。
这使得磨削成为一种非常常用的金属加工工艺。
3. 磨削可以实现高效率的加工。
尽管磨削相对于其他加工工艺来说,加工速度较慢,但是磨削可以同时进行多个工件的加工,从而提高了加工效率。
此外,磨削切削速度较低,磨削过程中不会产生较高的切削温度,从而减少了工件的热变形和残余应力。
4. 磨削可以实现较高的加工精度。
通过磨削工艺,可以实现工件的高精度要求。
磨削过程中,磨削刀具的尺寸几乎不会发生变化,因此可以保证工件的尺寸精度。
同时,磨削可以去除工件表面的氧化皮、毛刺等缺陷,提高工件的表面质量。
5. 磨削可以改善工件的机械性能。
磨削可以消除工件表面的残余应力,并提高工件的表面硬度。
此外,通过磨削可以改善工件的耐磨性、抗疲劳性和抗腐蚀性能,提高工件的使用寿命。
总结起来,磨削作为一种常见的金属加工工艺,具有高精度、高表面质量、广泛适用、高效率、高加工精度和改善机械性能的特点。
在实际的工程应用中,磨削工艺被广泛应用于各个行业,如航空航天、汽车制造、机械制造等领域。
磨削工艺的发展也为工件的加工质量提升和工艺效率提高提供了有效的手段。
机械加工技术(考卷及答案)

机械加工技术(考卷)一、选择题(每题2分,共20分)A. 车削B. 焊接C. 铸造D. 塑料成型A. VcB. apC. fD. n3. 下列哪种材料不属于难加工材料?A. 高强度钢B. 不锈钢C. 铝合金D. 钛合金A. 导向元件B. 传动元件C. 夹具D. 量具A. 铣床B. 车床C. 钻床D. 磨床A. 镗削B. 车削C. 铣削D. 珩磨A. VcB. apC. fD. nA. 数控加工B. 线切割C. 电火花加工D. 镗削加工二、填空题(每题2分,共20分)1. 机械加工的基本方法包括车削、_______、铣削、磨削、_______等。
2. 在机械加工中,切削三要素包括切削速度、进给量和_______。
3. 机械加工过程中,为了保证加工质量,需要对加工参数进行_______。
4. 常用的机械加工定位元件有定位块、定位销和_______。
5. 机械加工中的刀具材料主要包括高速钢、硬质合金、陶瓷和_______。
6. 在机械加工中,为了减小切削力,可以采用_________切削。
7. 机械加工误差主要包括系统误差和_______误差。
8. 数控加工具有加工精度高、生产效率高和_______等优点。
9. 机械加工中,为了保证加工质量,需要对工件进行_______、定位和夹紧。
10. 机械加工技术的发展趋势包括高精度、高效率、自动化和_______。
三、简答题(每题10分,共30分)1. 简述机械加工的基本过程。
2. 解释切削三要素对机械加工的影响。
3. 简述机械加工中的刀具磨损原因及预防措施。
四、案例分析题(20分)某企业在加工一批轴类零件时,发现部分零件尺寸超差。
请你分析可能导致这一问题的原因,并提出相应的解决措施。
五、计算题(10分)已知某零件加工过程中,切削速度Vc=100m/min,进给量f=0.2mm/r,切削深度ap=2mm,求该工序的切削功率。
一、选择题答案1. A2. A3. C4. C5. D6. B7. D8. C9. D10. A二、填空题答案1. 钻削、磨削2. 切削深度3. 优化4. 定位套5. 金属陶瓷6. 湿润7. 随机8. 灵活性9. 测量10. 绿色环保三、简答题答案1. 机械加工基本过程包括:毛坯制备、工件的装夹与定位、切削加工、检验和后续处理。
简述磨削加工的特点

简述磨削加工的特点
磨削加工是一种高精度加工方式,主要是通过磨料对工件进行切削,使其表面达到理想的精度、平滑度和形状精度。
它的特点如下:
一、高精度:通过磨削可以获得很高的表面精度和形状精度,最高可达0.1微米以下。
二、高效率:磨削加工可以同时加工多个表面,且一般能够满足光洁度要求,大大提高了加工效率。
三、材料选择范围广:磨削加工适用于各种材料的加工,包括各种金属、陶瓷、玻璃、塑料等。
四、适用于各种形状的工件:磨削加工可以加工各种形状的工件,包括平面、曲面、凸轮、齿轮等。
五、表面质量好:磨削加工可以消除工件表面原有的瑕疵和毛刺,使表面更加光滑、平整。
六、磨削精度可调:磨削加工可以根据需要调整磨料的硬度、颗粒度等参数,以达到不同的磨削精度和表面质量。
七、工艺复杂度高:磨削加工需要控制多种参数,包括磨料粒度、磨料硬度、磨削速度、进给量等,相对于其他加工方式,工艺复杂度更高。
综上所述,磨削加工具有高精度、高效率、适用性广、表面质量好等特点,但也存在工艺复杂度高的问题。
磨削表面质量
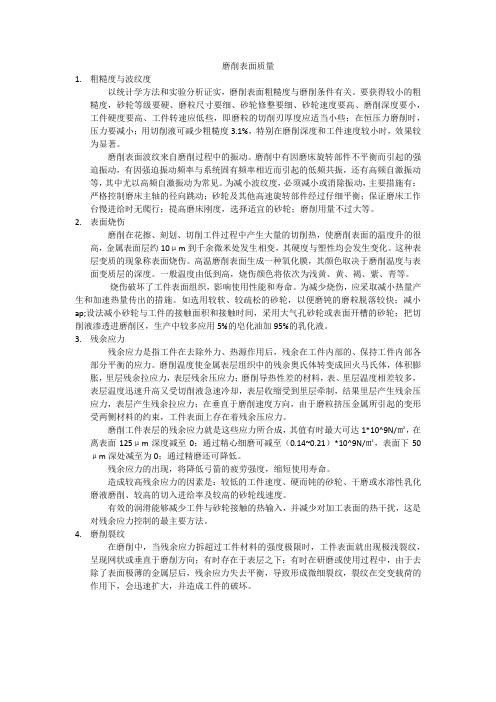
磨削表面质量1.粗糙度与波纹度以统计学方法和实验分析证实,磨削表面粗糙度与磨削条件有关。
要获得较小的粗糙度,砂轮等级要硬、磨粒尺寸要细、砂轮修整要细、砂轮速度要高、磨削深度要小,工件硬度要高、工件转速应低些,即磨粒的切削刃厚度应适当小些;在恒压力磨削时,压力要减小;用切削液可减少粗糙度3.1%,特别在磨削深度和工件速度较小时,效果较为显著。
磨削表面波纹来自磨削过程中的振动。
磨削中有因磨床旋转部件不平衡而引起的强迫振动,有因强迫振动频率与系统固有频率相近而引起的低频共振,还有高频自激振动等,其中尤以高频自激振动为常见。
为减小波纹度,必须减小或消除振动,主要措施有:严格控制磨床主轴的径向跳动;砂轮及其他高速旋转部件经过仔细平衡;保证磨床工作台慢进给时无爬行;提高磨床刚度,选择适宜的砂轮;磨削用量不过大等。
2.表面烧伤磨削在花擦、刻划、切削工件过程中产生大量的切削热,使磨削表面的温度升的很高,金属表面层约10μm到千余微米处发生相变,其硬度与塑性均会发生变化。
这种表层变质的现象称表面烧伤。
高温磨削表面生成一种氧化膜,其颜色取决于磨削温度与表面变质层的深度。
一般温度由低到高,烧伤颜色将依次为浅黄、黄、褐、紫、青等。
烧伤破坏了工件表面组织,影响使用性能和寿命。
为减少烧伤,应采取减小热量产生和加速热量传出的措施。
如选用较软、较疏松的砂轮,以便磨钝的磨粒脱落较快;减小ap;设法减小砂轮与工件的接触面积和接触时间,采用大气孔砂轮或表面开槽的砂轮;把切削液渗透进磨削区,生产中较多应用5%的皂化油加95%的乳化液。
3.残余应力残余应力是指工件在去除外力、热源作用后,残余在工件内部的、保持工件内部各部分平衡的应力。
磨削温度使金属表层组织中的残余奥氏体转变成回火马氏体,体积膨胀,里层残余拉应力,表层残余压应力;磨削导热性差的材料,表、里层温度相差较多,表层温度迅速升高又受切削液急速冷却,表层收缩受到里层牵制,结果里层产生残余压应力,表层产生残余拉应力;在垂直于磨削速度方向,由于磨粒挤压金属所引起的变形受两侧材料的约束,工件表面上存在着残余压应力。
影响磨削表面质量的因素
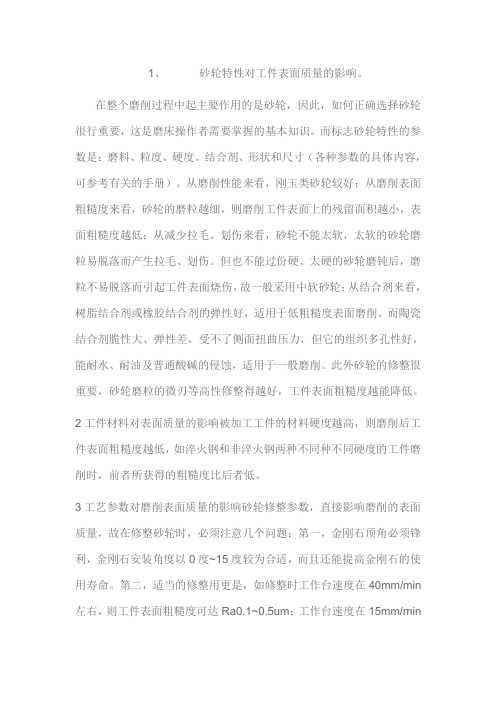
1、砂轮特性对工件表面质量的影响。
在整个磨削过程中起主要作用的是砂轮,因此,如何正确选择砂轮很行重要,这是磨床操作者需要掌握的基本知识。
而标志砂轮特性的参数是:磨料、粒度、硬度、结合剂、形状和尺寸(各种参数的具体内容,可参考有关的手册)。
从磨削性能来看,刚玉类砂轮较好;从磨削表面粗糙度来看,砂轮的磨粒越细,则磨削工件表面上的残留面积越小,表面粗糙度越低;从减少拉毛、划伤来看,砂轮不能太软,太软的砂轮磨粒易脱落而产生拉毛、划伤。
但也不能过份硬、太硬的砂轮磨钝后,磨粒不易脱落而引起工件表面烧伤,故一般采用中软砂轮;从结合剂来看,树脂结合剂或橡胶结合剂的弹性好,适用于低粗糙度表面磨削。
而陶瓷结合剂脆性大、弹性差,受不了侧面扭曲压力,但它的组织多孔性好,能耐水、耐油及普通酸碱的侵蚀,适用于一般磨削。
此外砂轮的修整很重要,砂轮磨粒的微刃等高性修整得越好,工件表面粗糙度越能降低。
2工件材料对表面质量的影响被加工工件的材料硬度越高,则磨削后工件表面粗糙度越低,如淬火钢和非淬火钢两种不同种不同硬度的工件磨削时,前者所获得的粗糙度比后者低。
3工艺参数对磨削表面质量的影响砂轮修整参数,直接影响磨削的表面质量,故在修整砂轮时,必须注意几个问题:第一,金刚石顶角必须锋利,金刚石安装角度以0度~15度较为合适,而且还能提高金刚石的使用寿命。
第二,适当的修整用更是,如修整时工作台速度在40mm/min左右,则工件表面粗糙度可达Ra0.1~0.5um;工作台速度在15mm/min 左右,则工件表面粗糙度可达Ra0.025~0.012um;工作台速度若在10mm/min左右,则工件粗糙度可达Ra0.01um。
第三,修整时横进给量的大小,对工件表面质量也有影响,横进给量大,工件表面粗糙,横进给量小,工件表面光滑,对低粗糙度磨削其横进给量控制在0.003~0.005um/行程为宜。
4、冷却液对工件表面质量的影响,冷却液具有吸热能力,能带走磨削区的大量磨削热,还能起润滑作用,可以减少砂轮与工件间的磨擦,防止工件表面烧伤和产生裂纹。
磨削工艺参数对轧辊表面粗糙度的影响

随着电子信息高新技术的发展,IC 框架材料已经得到 了广泛的应用,精轧机是框架材料生产的关键设备,轧辊是 轧机的重要部件,是实现轧制过程中金属变形的直接工具, 实际使用中对轧辊质量要求非常严格,主要的质量要求有强 度、硬度、耐用性、表面粗糙度等。强度、硬度、耐用性由轧 辊自身的性质决定,而表面粗糙度由磨削加工工艺确定。轧 辊磨削精度和表面粗糙度除了依靠精良的轧辊磨床之外,对 特定的加工辊选用与之相匹配的砂轮、和磨削工艺参数也是 至关重要的。
22
0.104 0.113 0.127 0.139 0.161 0.187
28
0.111 0.119 0.135 0.147 0.172 0.193
表 4 方法二 φ85 测量结果
工件转速(m/min) 砂轮转速(m/s)
45 40 35 30
25 20
14
0.098 0.108 0.119 0.134 0.168 0.179
磨 3μm、超精磨 2μm、无火花磨削 2 次的模式磨削时,粗
糙 度 值 最 低 为 0.099μm,表 面 较 光 洁。砂 轮 速 度 为 20m/
s,辊子转速 28m/min 采用粗磨 6μm、精磨 6μm、超精磨
6μm、无火花磨削 1 次的磨
表 5 方法一第二中间辊测量结果
工件转速(m/min) 砂轮转速(m/s)
1、图 2)。
表 1 方法一工作辊粗糙度测量结果
工件转速(m/min) 砂轮转速(m/s)
45 40 35 30 25 20
14
0.048 0.058 0.065 0.069 0.084 0.085
22
0.061 0.062 0.075 0.079 0.083 0.088
磨削加工中的磨削参数优化
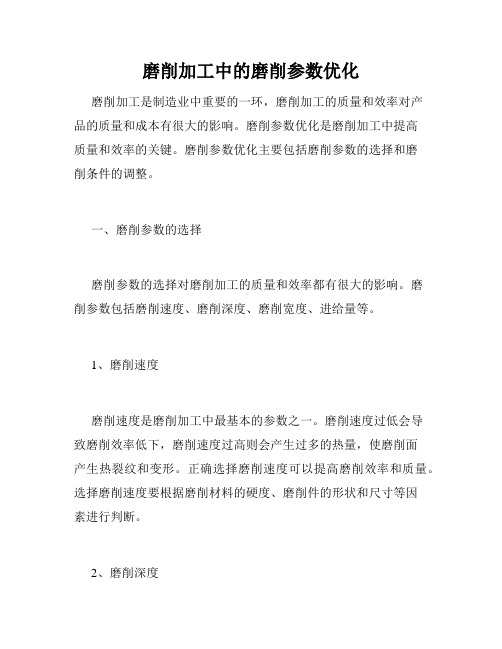
磨削加工中的磨削参数优化磨削加工是制造业中重要的一环,磨削加工的质量和效率对产品的质量和成本有很大的影响。
磨削参数优化是磨削加工中提高质量和效率的关键。
磨削参数优化主要包括磨削参数的选择和磨削条件的调整。
一、磨削参数的选择磨削参数的选择对磨削加工的质量和效率都有很大的影响。
磨削参数包括磨削速度、磨削深度、磨削宽度、进给量等。
1、磨削速度磨削速度是磨削加工中最基本的参数之一。
磨削速度过低会导致磨削效率低下,磨削速度过高则会产生过多的热量,使磨削面产生热裂纹和变形。
正确选择磨削速度可以提高磨削效率和质量。
选择磨削速度要根据磨削材料的硬度、磨削件的形状和尺寸等因素进行判断。
2、磨削深度磨削深度是指在一次磨削中,磨削轮的坐标和工件轴线的偏离量。
磨削深度越大,磨削时磨屑的排除越困难,因而对磨削的质量和效率会产生不利影响。
磨削深度的选择与磨削速度密切相关。
在确定最佳磨削速度的前提下,磨削深度应尽量小。
3、磨削宽度磨削宽度是指磨削轮和工件相互接触的长度。
磨削宽度的大小影响磨削的力和温度分布。
磨削宽度过小,容易产生表面质量差和热裂纹等问题。
磨削宽度过大,则容易产生磨削面的擦伤和变形。
正确选择磨削宽度可以保证磨削件的精度和表面质量。
4、进给量进给量是指工件和磨削轮之间相对运动距离的大小,即磨削轮在单位时间内对工件的磨削深度。
进给量的大小对于磨削加工中的表面质量、精度和效率都有很大的影响。
进给量过大可以提高磨削效率,但会降低表面精度。
进给量过小可以提高表面精度,但会降低磨削效率。
因此,选择进给量需要综合考虑磨削件的形状、材料和表面精度要求等因素。
二、磨削条件的调整磨削条件的调整是磨削参数优化的重要手段,正确的磨削条件可以提高磨削质量和效率。
磨削条件包括液压压力、冷却液喷射量、冷却液类型等。
1、液压压力液压压力是指对磨削件施加的压力,它直接影响磨削的力和温度分布。
不同的磨削件需要施加不同的液压压力,对于硬度较高的磨削件,需要适当提高液压压力,以避免磨削面出现裂纹和变形。
机械加工精度与表面处理考核试卷

B.热处理
C.焊接
D.电镀
12.在车削加工中,以下哪种情况会导致加工误差?()
A.机床导轨磨损
B.刀具磨损
C.工件材料不均匀
D.以上都对
13.下列哪种方法可以提高机械加工的表面光洁度?()
A.增大切削速度
B.减小切削速度
C.增大进给量
D.减小背吃刀量
14.关于表面处理技术,以下哪个是阳极氧化的作用?()
8.加工过程中,为了减少工件的热变形,可以采用______冷却的方法。
9.精密加工中,常用的加工方法有______磨削、激光加工等。
10.在金属切削加工中,刀具的前角和后角对切削力大小和加工表面质量有重要影响,适当增大前角可以减小______力。
四、判断题(本题共10小题,每题1分,共10分,正确的请在答题括号中画√,错误的画×)
1. D
2. C
3. B
4. D
5. D
6. D
7. D
8. B
9. D
10. D
11. C
12. D
13. A
14. B
15. D
16. D
17. D
18. A
19. D
20. B
二、多选题
1. ABCD
2. ABC
3. ABCD
4. ABC
5. ABCD
6. ABC
7. ABC
8. ABC
9. ABCD
B.刀具的材料
C.工件的材质
D.以上都对
2.在机械加工中,表面粗糙度的单位是?()
A. MPa
B. mm
C. μm
D. N
3.下列哪种方法可以改善机械加工表面的粗糙度?()
- 1、下载文档前请自行甄别文档内容的完整性,平台不提供额外的编辑、内容补充、找答案等附加服务。
- 2、"仅部分预览"的文档,不可在线预览部分如存在完整性等问题,可反馈申请退款(可完整预览的文档不适用该条件!)。
- 3、如文档侵犯您的权益,请联系客服反馈,我们会尽快为您处理(人工客服工作时间:9:00-18:30)。
2)磨床和工件的热变形 工件的热变形,是由于磨削热分布不均匀造成的。特别对于薄壁或 小型工件的影响尤其显著。这一变形,不像弹性位移可以用清火花 磨削反复磨削消除,而只能靠加大冷却液来抑制。磨床的热变形, 对工件的精度的影响也是重要的,对于液压传动来说,可以将油池 移出床身,以减少磨床的热变形 3)磨削切刃引起的塑性耕犁 当切刃通过以后,弹性变形部分回复,塑性变形的隆起部分保 留下来,这种尺寸误差也是磨削精度的影响因素 4)磨床和工件的振动 振动对工件的被磨削表面和砂轮工作面都会带来不良的影响, 因而对磨削精度的影响是非常严重的 5)砂轮磨损后其形状、尺寸的变化 一般正常磨削状态下,砂轮每转的损耗量在半径方向上的减少量是 砂轮切入量的1/5000~1/2000
6)导轨、轴承和轴等部件的非弹性变形
三、提高磨削精度的措施 1、磨床的检修
1) 床身导轨的检测与修刮 2) 滑鞍座导轨的检测与修刮
3) 砂轮主轴与轴瓦间的间隙调整 4) 砂轮主轴电机与砂轮的平衡 2、砂轮的修整 1) 用金刚笔精修、再用油石细修 2) 用金刚笔精修、再用精车后的砂轮细修 3、合理选用磨削用量
第六章 磨削精度与磨削表面质量
第一节、磨削精度
第二节 磨削表面粗糙度 第三节 磨削表面层质量
产品的质量与零件的加工质量和装配质量有着密切的关 系,而零件质量的好坏,不仅与材料性质、零件表面层组织 状态,也与加工精度、表面层粗糙度等几何因素有关。虽然 这些问题只产生在薄的表面层中,却错综复杂的影响着机械 零件的精度、耐磨性、配合性质的保持、抗腐蚀性和疲劳强 度,从而影响着产品的使用性能和使用寿命
烧伤与材料的临界烧伤温度Tb,磨削强度H、磨削温度QM有关
三、残余应力 1、概念 磨削残余应力是指磨削加工后,仍保留在工件内部的应力。
残余应力分为残余拉应力和残余压应力。
残余应力按其存在范围可以分为三类: Ⅰ类:宏观残余应力存在于整个工件或者工件局部较大的范围内, Ⅱ类,微观残余应力,存在于工件中晶粒大小范围内 Ⅲ类超微观残余应力,存在于位错 层错灯范围内 残余应力按其应力性质可以分为三类
第三节 磨削表面层的机械性能 磨削表面层机械性能是指磨削后零件表面层的显微硬度、 局部金相组织、与残余应力
一、磨削表面硬度变化规律及产生原因 磨削表面硬度变化是磨削产生的形变硬化与组织转变的综合反映。
形变硬化总是使硬度升高,而组织转变既有可能是硬度升高(如发 生磨削淬火),也有可能是硬度降低(如淬火钢发生回火软化,形 变硬化发生再结晶)。磨削表面的硬度变化大致可分为四种类型
x
图6-5 轮廓的算术平均偏差Ra
1 Ra y x dx l0
l
或近似为
1 n Ra y i n 1
2.微观不 平度的十点平均高度Rz 在取样长度l内,5个最大的轮廓峰高的平均值与5个谷深的 平均值之和 yp4
yp1 yp2 yp3 yp5
yv2 yv1
x yv3 yv4
yv5
2、磨削用量的影响, a.在磨削用量中 若降低砂轮速度,可减少单位时间内参与磨削的磨 粒数,则单颗磨粒负荷增大,工件塑性变形和犁沟两侧的隆起 增大,因此表面粗糙度增大;
b.若增大工件速度将减少工件单位长度上磨削的磨粒数,是单 颗磨粒的磨削厚度和金属切削量增大,将增大表面粗糙度; c.增大磨削深度,将增加塑性变形的程度,从而使表面粗糙度 增大。另外磨削加工系统的刚度是产生磨削振纹的重要因素。
2.磨削表面硬度变化对零件使用性能的影响 1)磨削表面硬度变化对零件耐磨性能的影响 磨削后零件表面硬度降低 抗磨损变形能力下降,耐磨性下降。表 面硬度升高抵抗变形的能力增加了 故耐磨性提高。但如果加工硬 化作用过大,尽管硬度提高很多,但过大的塑性变形会使金属基 体的微观连续性遭到破坏,而出现大量的微观裂纹及组织疏松, 反而使耐磨性降低。 磨削材料硬度与耐磨性的关系 HV0—磨前材料硬度
4、增加清火花磨削行程 所谓“清火花磨削”,是指砂轮与工件之间没有径向进给量。 仅依靠系统的弹性回复力所维持的砂轮对工件的磨削过程
第二节 磨削表面粗糙度
表面粗糙度 是指加工表面上具有的较小间距和峰谷所组成的微 观几何形状特性 一、表面粗糙度的表示 方法 Ra 1.轮廓算术平均偏差Ra 在取样长度l内,轮廓 上各点到中线之间的 偏差的算是平均值 l
△01、△02—在HV0的 尺寸磨损量
1—接触材料较硬
2—接触材料较软
2)磨削表面硬度变化对零件疲劳强度的影响 零件磨削表面的显微硬度的变化对疲劳强度的影响规律比较 复杂。表面层加工硬化能提高零件的疲劳强度,因为硬化层会阻 碍已有疲劳裂纹的扩展和新裂纹的产生,同时,硬化层还能显著 减少外部缺陷和粗糙度的有害影响 3)磨削表面硬度变化对零件耐腐蚀性能的影响 表面金相组织的变化一般都是零件的耐腐蚀性能下降,,变形 的晶粒、发生淬火或者回火软化的表层组织,会使零件表 面的组织部均匀性增加,因此易发生腐蚀。而磨削表面硬 度的提高并不能提高零件的耐腐蚀性能。只有当硬度提高 的同时,伴随组织致密度的提高,才能提高零件的腐蚀性 能
2.磨削过程误差 在磨削过程中,使砂轮与工件位置发生改变从而降低磨削精 度的主要原因有: 1)由磨削力引起的磨床 和工件的弹性变形 ε=ε1+ε2+(ε3·ε4)+ε5 ε1——砂轮轴的位移 ε2——砂轮的弹性位移 ε3——头架顶尖的位移 ε4——尾座顶尖的位移 ε5——工件的弹性位移 ε被称为残留余量 图6-2 磨削系统的弹性变形
3、磨削方式、 4、磨削行程数、 5、前道工序表面粗糙度、 6、切削刃形状、 7、修整条件 8、磨削液以 9、磨削振动
三、磨削表面粗糙度对零件使用性能的影响 1、磨削表面粗糙度对零件耐磨性能的影响
1—轻负荷
2—重负荷
图6-11 磨削表面粗糙度与零件耐磨性
2、磨削表面粗糙度对零件疲劳强度的影响 表面粗糙度越小,有利于疲劳强度的提高。 粗糙度大的表面,极易产生较大的应力集中,使表面的实际应力 比平均盈利高1.5~2.5倍,裂纹容易生成;粗糙度小时应力集中 较为分散均匀,使裂纹产生困难。 疲劳强度除与粗糙度的大小有关外,还与 波峰、波谷的尖锐 程度有关,尖锐的波谷应力集中较大裂纹容易产生,圆钝的 波谷产生应力钝化 裂纹生成相对较困难 3.磨削表面粗糙度对零件耐腐蚀性能的影响 减小加工表面的粗糙度可以提高零件的耐腐蚀性能 磨削表面的粗糙度越大,其波谷越容易积聚腐蚀性气体或液体, 这些气体或液体通过粗糙度表面的凹谷深处向内部渗透,与未 氧化的材料发生物理化学反应,产生腐蚀,凹谷越深,底部角 度越小,尤其表面有裂纹时,腐蚀作用越强烈,
l 图6-5 轮廓的算术平均偏差Ra
Rz y1源自5pi y vi
1
5
ypi ——第i个最大的轮廓高度; Yvi ——第i个最大的轮廓谷深
5
3.轮廓最大高度Ry
在取样长度l内,轮廓峰顶线和轮廓谷底线之间的距离 Ry=ypmax+yvmax 以上表示粗糙度的方法可以看出,Ry和Rz都有明确的直观性(物 理意义清楚)。但是都不能反映表面微观不平度的形状变化,指 仅仅代表轮廓的高度,并且在测量时,随取点的不同期结果差别 很大。Ra则能综合反映 表面微观几何特性,它不仅与违规轮廓 的高度有关,还和轮廓的形状有关,是一个综合指标。目前我国 采用Rz和Ra评定表面粗糙度
图6-12(c)为Ⅲ类硬度曲线完全受热软化作用的影响,磨后硬度 低于磨前硬度,部门发生软化其程度及层深受磨削条件的影响很大。 普通磨削通常都容易出现这种类型 图6-12(d)为Ⅳ硬度曲线,最表面由于磨削热很高而造成表面淬 火硬化,硬度高于磨前硬度,在淬硬层下较深的范围内收高温软化 的影响,硬度低于磨前硬度。磨削深度过大或砂轮钝化易产生这种 类型的硬度分布
(3)残余应力对零件耐腐蚀性能的影响 残余压应力可增加材料的耐腐蚀性能。 残余拉应力则明显降低材料的耐腐蚀性能。 原因是 :一是残余压应力对腐蚀过程中钝化膜的破坏较小,而拉 引力则对钝化膜产生较强的破坏作用。使腐蚀介质连续不断地深入 零件的内部而对其进行腐蚀。 二是残余压应力可使电极电位变小,而残余拉应力则使得电极电位 向高电位变化,这种电极电位的差别形成了富士微电池,因此电位 高的电极就会被腐蚀 磨削裂纹的产生会使得零件的耐腐蚀性能大大降低。因为在裂 纹的 前端总美国存在着较大的拉应力集中,从而使腐蚀介质容 易从裂纹端部进入并沿着应力集中最大的方向不断地腐蚀,极 大地加剧了零件的腐蚀速度
2、残余应力产生的原因 1)磨削力造成工件表面的弹塑性变形 2)磨削热产生的热应力 3)组织转变导致的组织应力
磨削力产生的表面残余应力
磨削热产生的表面残余应力
3.残余应力对零件使用性能的影响。
1)残余应力对零件加工精度的影响 残余应力在没有外力和外力矩的作用下构成物体内部暂时的平衡, 同时导致材料内部产生变形。使工件难以达到加工精度。及时当时 达到了加工精度,由于残余应力具有自然释放能力这种加工精度也 不能保持, 2)对零件疲劳强度的影响 零件的疲劳破坏都经历了裂纹萌生、扩展、断裂三个阶段。当零件 表面局部开裂,裂纹萌生;在周期性交变载荷作用下裂纹不断扩展、 扩大知道剩余有效断面承受的实际应力大于其断裂极限时,材料发 生一次性断裂。残余应力对零件的疲劳强度影响是最大了 磨削表面的残余压应力可以抵消一部分外加的拉应力,从而有 效地抑制了裂纹的产生和扩展。使零件的疲劳强度大大提高。 生产中常采取一些辅助工序(表面喷丸、滚压等)
图6-12(a)为Ⅰ类硬度曲线,这种类型的硬度分布完全受加工硬 化作用,磨削后的部门硬度高于磨前硬度,产生明显的加工硬化。 在材料较软以及用较钝砂轮进行紧密磨削时长出新这种类型 图6-12(b)为Ⅱ类硬度曲线,磨后硬度仍可高于磨前硬度,有明 显的加工硬化 但此时由于部门温度较高,受热软化作用大于加工硬化,因此,最 表层发生受热软化,硬度低于磨前硬度,材料硬度不高以及半精磨 时易出现这种类型
二、磨削烧伤 磨削时,由于磨削区的瞬时高温(一般为900~1500℃)形成零件 表层组织局部变化,并在表面的某些部分出现氧化变色 这种现象 称为磨削烧伤 磨削深度/μ m 17 烧伤颜色 银白色 氧化膜厚度/μ m 未烧伤