焙烧炉能耗分析与优化
焙烧炉节能措施分析
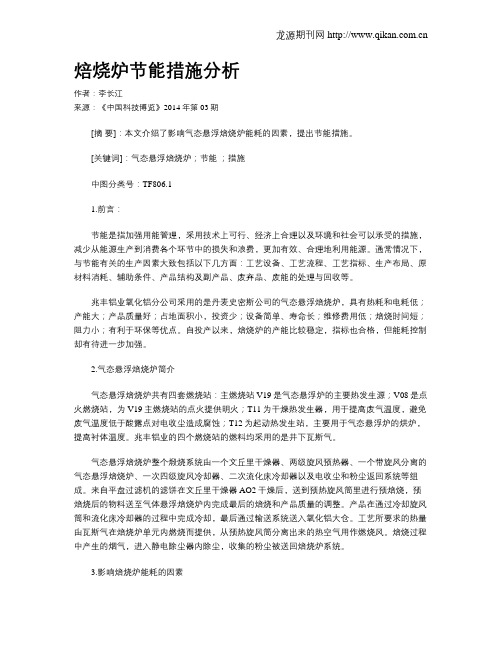
焙烧炉节能措施分析作者:李长江来源:《中国科技博览》2014年第03期[摘要]:本文介绍了影响气态悬浮焙烧炉能耗的因素,提出节能措施。
[关键词]:气态悬浮焙烧炉;节能;措施中图分类号:TF806.11.前言:节能是指加强用能管理,采用技术上可行、经济上合理以及环境和社会可以承受的措施,减少从能源生产到消费各个环节中的损失和浪费,更加有效、合理地利用能源。
通常情况下,与节能有关的生产因素大致包括以下几方面:工艺设备、工艺流程、工艺指标、生产布局、原材料消耗、辅助条件、产品结构及副产品、废弃品、废能的处理与回收等。
兆丰铝业氧化铝分公司采用的是丹麦史密斯公司的气态悬浮焙烧炉,具有热耗和电耗低;产能大;产品质量好;占地面积小,投资少;设备简单、寿命长;维修费用低;焙烧时间短;阻力小;有利于环保等优点。
自投产以来,焙烧炉的产能比较稳定,指标也合格,但能耗控制却有待进一步加强。
2.气态悬浮焙烧炉简介气态悬浮焙烧炉共有四套燃烧站:主燃烧站V19是气态悬浮炉的主要热发生源;V08是点火燃烧站,为V19主燃烧站的点火提供明火;T11为干燥热发生器,用于提高废气温度,避免废气温度低于酸露点对电收尘造成腐蚀;T12为起动热发生站,主要用于气态悬浮炉的烘炉,提高衬体温度。
兆丰铝业的四个燃烧站的燃料均采用的是井下瓦斯气。
气态悬浮焙烧炉整个煅烧系统由一个文丘里干燥器、两级旋风预热器、一个带旋风分离的气态悬浮焙烧炉、一次四级旋风冷却器、二次流化床冷却器以及电收尘和粉尘返回系统等组成。
来自平盘过滤机的滤饼在文丘里干燥器AO2干燥后,送到预热旋风筒里进行预焙烧,预焙烧后的物料送至气体悬浮焙烧炉内完成最后的焙烧和产品质量的调整。
产品在通过冷却旋风筒和流化床冷却器的过程中完成冷却,最后通过输送系统送入氧化铝大仓。
工艺所要求的热量由瓦斯气在焙烧炉单元内燃烧而提供,从预热旋风筒分离出来的热空气用作燃烧风。
焙烧过程中产生的烟气,进入静电除尘器内除尘,收集的粉尘被送回焙烧炉系统。
阳极焙烧炉节能降耗的对策(1)(1)

阳极焙烧炉节能降耗的对策唐林、高守磊(索通发展股份有限公司山东德州251500)摘要:焙烧炉经过4年以上运行后,炉室密封不好,漏风系数高,造成燃料利用效率低,能耗高,制品温度下降,影响了产品质量。
本文从改进焙烧工艺以及焙烧操作等方面采取相应的对策,改善焙烧炉保温措施,降低焙烧炉燃料消耗、提高焙烧产品质量。
关键词:焙烧炉;燃料利用效率;产品质量METHODS TO IMPROVE FUEL UTILIZATION FOR OPEN TOPANODE BAKING FURNACESLin Tang,Shoulei GaoSunstone Development Co.,Ltd,Shandong Dezhou251500Abstract t:As a baking furnace ages,cracks and openings develop in the furnace Abstracwhich allow outside air to enter.Unless proper corrective actions are implemented, gas consumption can increase,final baking temperatures can decrease,and baked anode properties can deteriorate.In this paper,methods are presented for improving the efficiency of fuel utilization for aging furnaces,and thereby lowering fuel consumption,while maintaining or improving anode finishing temperatures and anode properties.Keywords:Baking furnace,Fuel utilization,Products quality一、前言铝用预焙阳极生产过程中,焙烧是最后和最重要的工序之一[1]。
氧化铝焙烧项目节能分析

氧化铝焙烧项目节能分析首先,节能分析需要从设备方面入手。
氧化铝焙烧设备主要包括烧结机、窑灶和烟气处理系统。
对于烧结机,可以通过优化烧结机结构设计,改进燃料供给方式,提高燃烧效率,减少能源浪费。
而对于窑灶,可以通过加强隔热措施,减少热损失。
此外,烧结机和窑灶的运行维护也需要合理规范,确保设备的正常运行,提高设备利用率。
其次,节能分析需要从能源方面入手。
氧化铝焙烧过程中主要使用的能源是煤炭和天然气。
为了节约能源,可以采取以下措施:一是改进燃料选择和供应方式,选择高热值、低硫和低氮的燃料,减少废气的排放;二是优化燃料燃烧过程,提高燃烧效率,减少能源浪费;三是使用余热回收技术,将烟气余热用于预热燃料或提供热能给其他工艺流程,提高能源利用效率。
再次,节能分析需要从工艺方面入手。
氧化铝焙烧工艺中,热交换是一个重要环节。
通过合理设计热交换器,提高热交换效果,减少热能的浪费;同时,还可以采用节能型的辅助设备,如高效的风机和泵等,减少能耗。
另外,还可以优化生产计划,减少停炉、开炉的次数,提高生产过程的稳定性,降低能耗。
最后,节能分析还需要从管理方面入手。
在氧化铝焙烧项目中,建立完善的能源管理体系是非常重要的。
通过制定能源消耗标准、能源消耗指标和能源消耗限额,建立能耗监测和统计体系,对能源消耗进行监控和分析,及时发现问题并采取相应的措施。
此外,还要加强员工的能源管理培训,提高员工的节能意识,形成全员参与、共同节能的氛围。
综上所述,氧化铝焙烧项目的节能分析涉及设备、能源、工艺和管理等多个方面。
通过优化设备结构和运行维护,选择合适的燃料和提高燃烧效率,加强热交换和使用节能型设备,建立完善的能源管理体系等措施,可以实现氧化铝焙烧过程的节能降耗。
焙烧炉节能措施分析
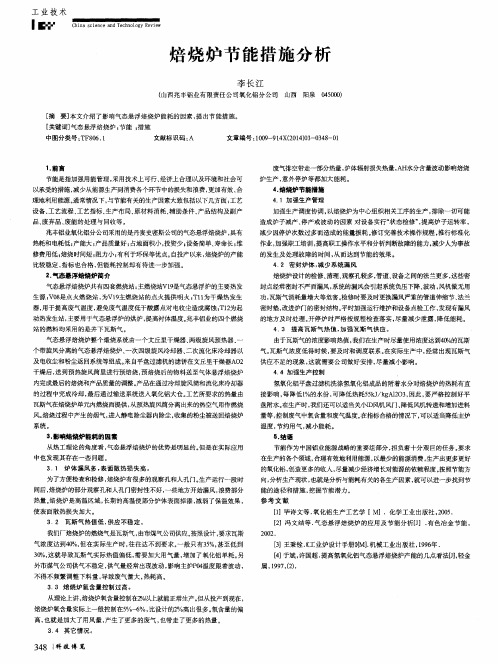
3 . 影响焙 烧 炉能 耗的 因素
工 业技 术
I ■
C h i n aቤተ መጻሕፍቲ ባይዱ s c i e n c e a n d T e c h n o l o g y R e v i e w
焙 烧 炉 节 能措 施 分 析
李长 江
( 山西 兆 丰铝业 有 限责 任 公司 氧化 铝分 公 司 山西 [ 摘 要] 本 文介 绍 了影响 气态 悬浮 焙烧 炉能 耗 的 因素 , 提 出节 能措施 。 [ 关键 词] 气 态悬 浮焙 烧炉 ; 节能 ; 措 施
系统
4 . 焙烧炉节能措施
4 . 1加 强生产 管理
加强 生产调 度协调 , 以焙烧 炉为 中心组 织相 关工序 的生产 , 排 除一切 可能 造成炉 子减 产 、 停产 或波动 的因素 对设备 实行 “ 状 态检 修” , 提 高炉 子运 转率 , 减 少 因停炉 次数过 多而 造成 的能量 损耗 。 修订 完善 技术操 作规 程 , 推行标 准化
封点经常密封不严而漏风, 系统的漏风会引起系统负压下降、 波动 , 风机做无用
功, 瓦斯气 消耗量增 大等苊 害 。 检 修时要 及时更换 漏风严重 的管道 伸缩节 、 法 兰 密封 垫 , 改进 炉 门的密封结 构 。 平 时加强 运行维 护和设备 点检工作 , 发 现有漏 风 的地 方及 时处 理 。 开停 炉 时严格 按规 程检 查落 实 , 尽量 减少 泄露 , 降低能 耗 。
节能 是指 加强用 能管 理 , 采用技术 上 可行 、 经济上 合理 以及环 境和社 会 可
以承受的措施, 减少从能源生产到消费各个环节中的损失和浪费, 更加有效、 合
理 地利 用能源 通常情 况下 , 与节 能有 关 的生产 因素大致包 括 以下 几方面 : 工 艺 设备 、 工 艺流程 、 工 艺指 标 、 生产布 局 、 原材 料消 耗 、 辅助条 件 、 产 品结构及 副产 品、 废弃 品 、 废 能的 处理 与回 收等 。 兆 丰铝 业氧 化铝分公 司采用 的是丹麦 史密 斯公司 的气态悬浮 焙烧炉 , 具有 热耗 和电耗低 ; 产 能大 ; 产品质量 好 ; 占地 面积小 , 投资少 ; 设备 简单 、 寿命 长 ; 维 修费 用低 , 焙烧 时间短 ; 阻力小 ; 有 利于环保 等优点 。 自投产 以来 , 焙烧 炉的产 能 比较稳定 , 指标 也合格 , 但能耗 控制 却有 待进 一步 加强 。 2 . 气态 悬 浮焙烧 炉简 介 气态悬 浮焙烧 炉共有 四套燃 烧站 : 主燃烧 站V1 9 是气 态悬浮 炉 的主 要热 发 生源; V 0 8 是点火 燃烧 站 , 为V1 9 主 燃烧 站的 点火 提供 明火 ; T 1 1 为干 燥热 发生 器, 用于 提高废 气 温度 , 避免废 气温 度低于 酸露 点对 电收尘造成 腐蚀 ; T 1 2 为起 动 热发生 站 , 主要 用于 气态悬浮 炉的烘炉 , 提 高衬体温 度。 兆 丰铝业 的 四个 燃烧 站 的燃料 均 采用 的是 井下 瓦斯 气 。 气态悬 浮焙烧 炉 整个煅烧 系统 由一个 文丘 里干燥 器、 两级旋 风预 热器 , 一 个 带旋 风分 离的气 态悬 浮焙烧 炉 、 一次 四级旋 风冷 却器 、 二次 流化 床冷却器 以 及 电收尘 和粉尘 返回系 统等组成 。 来 自平盘 过滤机 的滤饼在 文丘里 干燥器 A O 2 干 燥后 , 送 到预 热旋风 筒里进 行预 焙烧 , 预焙 烧后 的物料 送至 气体 悬浮焙 烧炉 内完成最 后的焙烧 和产 品质量的调 整 。 产 品在通 过冷却旋 风筒和 流化床冷 却器 的过程 中完 成冷 却 , 最后通 过输送 系统 送人 氧化铝 大仓 工 艺所要 求的 热量 由 瓦斯气在 焙烧炉 单元 内燃烧而提供 , 从 预热旋 风筒分离 出来的热 空气用作 燃烧 风。 焙烧 过程 中产生 的烟气 , 进入静 电 除尘器 内除尘 , 收集 的粉尘 被送 回焙 烧炉
敞开式焙烧炉能耗水平和产品质量影响因素分析
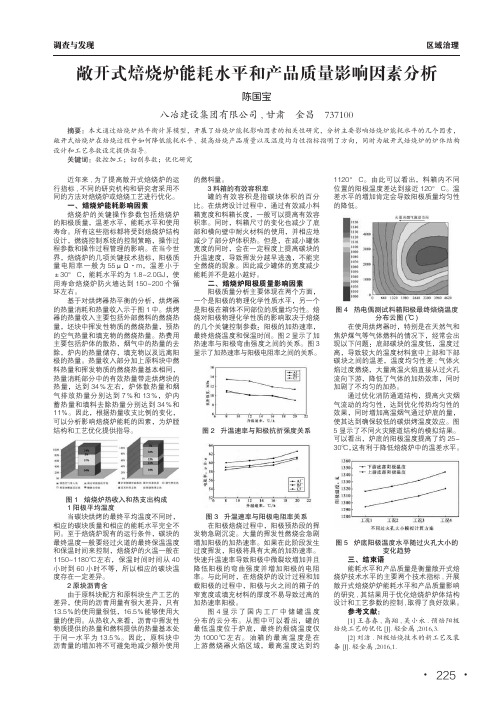
· 225 ·区域治理调查与发现敞开式焙烧炉能耗水平和产品质量影响因素分析陈国宝八冶建设集团有限公司,甘肃 金昌 737100摘要:本文通过焙烧炉热平衡计算模型,开展了焙烧炉能耗影响因素的相关性研究,分析主要影响焙烧炉能耗水平的几个因素,敞开式焙烧炉在焙烧过程中如何降低能耗水平、提高焙烧产品质量以及温度均匀性指标指明了方向,同时为敞开式焙烧炉的炉体结构设计和工艺参数设定提供指导。
关键词:数控加工;切削参数;优化研究近年来,为了提高敞开式焙烧炉的运行指标,不同的研究机构和研究者采用不同的方法对焙烧炉或焙烧工艺进行优化。
一、焙烧炉能耗影响因素焙烧炉的关键操作参数包括焙烧炉的阳极质量,温差水平,能耗水平和使用寿命。
所有这些指标都将受到焙烧炉结构设计,燃烧控制系统的控制策略,操作过程参数和操作过程管理的影响。
在当今世界,焙烧炉的几项关键技术指标,阳极质量电阻率一般为55μΩ·m,温差小于±30°C,能耗水平约为1.8~2.0GJ,使用寿命焙烧炉防火墙达到150~200个循环左右。
基于对烘烤器热平衡的分析,烘烤器的热量消耗和热量收入示于图1中。
烘烤器的热量收入主要包括外部燃料的燃烧热量,坯块中挥发性物质的燃烧热量,预热的空气热量和填充物的燃烧热量。
热费用主要包括炉体的散热,烟气中的热量的去除,炉内的热量储存,填充物以及远离阳极的热量。
热量收入部分加上原料块中燃料热量和挥发物质的燃烧热量基本相同,热量消耗部分中的有效热量带走烘烤块的热量,达到34%左右,炉体散热量和烟气排放热量分别达到7%和13%,炉内蓄热量和填料去除热量分别达到34%和11%。
因此,根据热量收支比例的变化,可以分析影响焙烧炉能耗的因素,为炉膛结构和工艺优化提供指导。
图1 焙烧炉热收入和热支出构成1阳极平均温度当碳块烘烤的最终平均温度不同时,相应的碳块质量和相应的能耗水平完全不同。
至于焙烧炉现有的运行条件,碳块的最终温度一般要经过火道的最终保温温度和保温时间来控制,焙烧炉的火温一般在1150~1180℃左右,保温时间时间从40小时到60小时不等,所以相应的碳块温度存在一定差异。
炭素焙烧炉改造节能减排分析
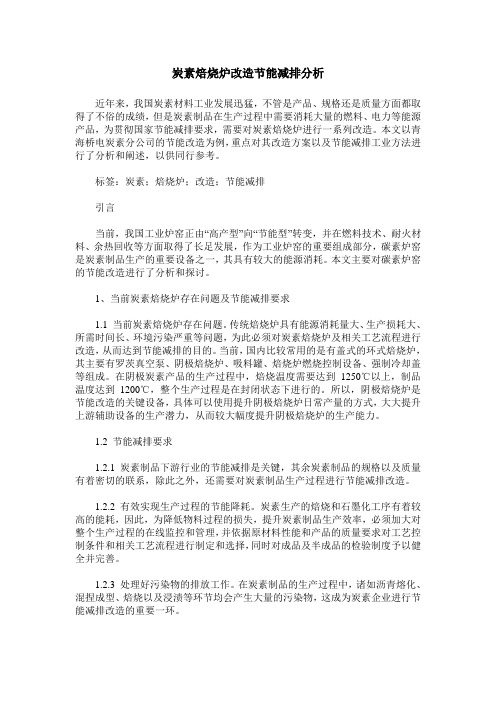
炭素焙烧炉改造节能减排分析近年来,我国炭素材料工业发展迅猛,不管是产品、规格还是质量方面都取得了不俗的成绩,但是炭素制品在生产过程中需要消耗大量的燃料、电力等能源产品,为贯彻国家节能减排要求,需要对炭素焙烧炉进行一系列改造。
本文以青海桥电炭素分公司的节能改造为例,重点对其改造方案以及节能减排工业方法进行了分析和阐述,以供同行参考。
标签:炭素;焙烧炉;改造;节能减排引言当前,我国工业炉窑正由“高产型”向“节能型”转变,并在燃料技术、耐火材料、余热回收等方面取得了长足发展,作为工业炉窑的重要组成部分,碳素炉窑是炭素制品生产的重要设备之一,其具有较大的能源消耗。
本文主要对碳素炉窑的节能改造进行了分析和探讨。
1、当前炭素焙烧炉存在问题及节能减排要求1.1 当前炭素焙烧炉存在问题。
传统焙烧炉具有能源消耗量大、生产损耗大、所需时间长、环境污染严重等问题,为此必须对炭素焙烧炉及相关工艺流程进行改造,从而达到节能减排的目的。
当前,国内比较常用的是有盖式的环式焙烧炉,其主要有罗茨真空泵、阴极焙烧炉、吸料罐、焙烧炉燃烧控制设备、强制冷却盖等组成。
在阴极炭素产品的生产过程中,焙烧温度需要达到1250℃以上,制品温度达到1200℃,整个生产过程是在封闭状态下进行的。
所以,阴极焙烧炉是节能改造的关键设备,具体可以使用提升阴极焙烧炉日常产量的方式,大大提升上游辅助设备的生产潜力,从而较大幅度提升阴极焙烧炉的生产能力。
1.2 节能减排要求1.2.1 炭素制品下游行业的节能减排是关键,其余炭素制品的规格以及质量有着密切的联系,除此之外,还需要对炭素制品生产过程进行节能减排改造。
1.2.2 有效实现生产过程的节能降耗。
炭素生产的焙烧和石墨化工序有着较高的能耗,因此,为降低物料过程的损失,提升炭素制品生产效率,必须加大对整个生产过程的在线监控和管理,并依据原材料性能和产品的质量要求对工艺控制条件和相关工艺流程进行制定和选择,同时对成品及半成品的检验制度予以健全并完善。
氧化铝焙烧项目节能分析

氧化铝焙烧项目节能分析氧化铝焙烧是将铝矿石经过破碎、选矿等预处理后,放入阴阳燃烧器内进行高温焙烧,将铝石中的氧化铝还原成金属铝的过程。
这个过程中需要大量的能量消耗,因此对氧化铝焙烧项目进行节能分析非常重要。
首先,氧化铝焙烧项目的主要能耗包括燃烧炉的燃料消耗、电力消耗和风机消耗等。
在进行节能分析时,首先要对这些能耗进行准确的测量和计量,以便得出准确可靠的数据。
其次,对于燃料消耗方面,可以通过优化燃料选择和燃烧过程来降低能耗。
例如,可以选择高效率的燃料,如天然气和液化石油气,以替代传统的煤炭燃料。
同时,可以通过优化燃烧过程,如提高燃烧炉的燃烧效率,减少燃料的浪费等方式来降低能耗。
另外,对于电力消耗方面,可以通过优化电力设备的使用来降低能耗。
例如,可以使用高效的电机和变压器,减少电力损耗;合理安排电力设备的使用时间,避免低负载运行等。
此外,还可以利用余热发电技术,将燃烧过程中产生的高温余热转化为电能,提高能源利用效率。
最后,风机消耗也是影响能耗的重要因素。
在氧化铝焙烧过程中,需要使用大量的风机来提供燃烧所需的氧气和将燃料燃烧产生的废气排出。
因此,通过优化风机系统的设计和运行,来减少能耗也是非常有效的。
例如,可以通过调整风机的转速和叶片角度,提高风机效率,降低能耗;合理安排风机的使用时间,避免低负载运行等。
综上所述,针对氧化铝焙烧项目的节能分析,可以从燃料消耗、电力消耗和风机消耗等多个方面进行优化。
通过合理选择燃料和燃烧工艺,优化电力设备的使用,以及优化风机系统的设计和运行,可以降低氧化铝焙烧过程中的能耗,实现节能减排的目标,并降低企业的运营成本。
阳极炭素焙烧炉节能降耗技术探讨秦庆福倪清宗月雄

阳极炭素焙烧炉节能降耗技术探讨秦庆福倪清宗月雄发布时间:2021-11-03T02:23:22.141Z 来源:基层建设2021年第23期作者:秦庆福倪清宗月雄[导读] 在环境问题和资源与能源问题迟迟得不到有效解决的情况下,环境保护与治理以及节能降耗成为整个社会的重要责任与义务,在工业领域中,铝生产企业的能源消耗是非常严重的,炭素阳极焙烧是铝生产过程中能源消耗最为严重的环节,因此下文就以炭素阳极焙烧节能降耗技术研究为核心内容,对自动回收蓄能技术引入、炭素阳极焙烧炉结构改进以及操作控制系统改进几个重要环节进行详细分析,并在文章的最后客观的探讨实验结果论证,旨在给予铝生产一些帮助和参考云南源鑫炭素有限公司云南红河 661100摘要:在环境问题和资源与能源问题迟迟得不到有效解决的情况下,环境保护与治理以及节能降耗成为整个社会的重要责任与义务,在工业领域中,铝生产企业的能源消耗是非常严重的,炭素阳极焙烧是铝生产过程中能源消耗最为严重的环节,因此下文就以炭素阳极焙烧节能降耗技术研究为核心内容,对自动回收蓄能技术引入、炭素阳极焙烧炉结构改进以及操作控制系统改进几个重要环节进行详细分析,并在文章的最后客观的探讨实验结果论证,旨在给予铝生产一些帮助和参考。
关键词:阳极炭素焙烧炉;节能降耗;技术分析引言铝生产行业在目前的工业领域中占据一定地位,在工业领域繁荣发展方面发挥了关键性的助推作用,但是铝生产企业炭素阳极焙烧环节的能源过度消耗也逐渐引起相关方面的高度重视,在能源与资源紧张问题日益严重的当前时刻,炭素阳极焙烧环节的节能降耗可以说是刻不容缓,而探寻阳极炭素焙烧炉节能降耗技术也成为铝生产企业的当务之急,炭素阳极焙烧过程中会产生大量烟气,如果任由烟气随意排放,不仅会带来环境污染问题,也会形成热量不必要浪费,自动回收蓄能技术的引入可避免以上问题的出现,而且合理改进焙烧炉结构和优化操作控制系统也是节能降耗的有效举措,铝生产企业很有必要对此进行研究探讨。
降低焙烧炉能耗提高经济效益
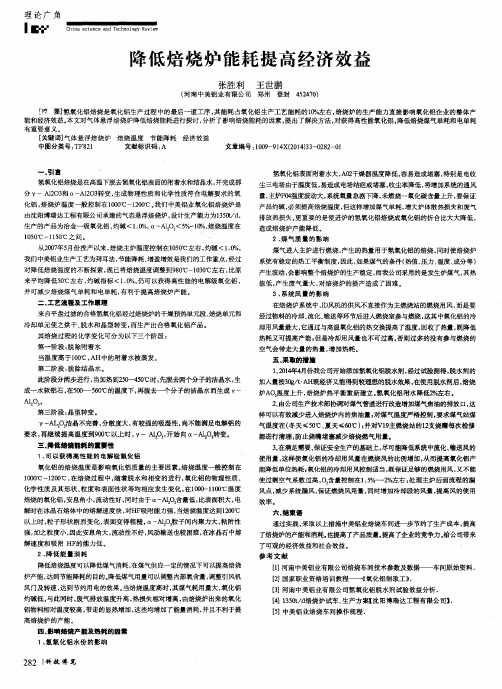
A L O 3 。
第 三 阶段 : 晶型转 变 。 Y— AL ) 0 洁 晶不完善 , 分散 度大 , 有 较强 的吸 湿性 , 尚不能 满足 电解铝 的
却用风量最大, 它通过与高温氧化铝的热交换提高了温度, 回收了热量, 既降低 热耗又可提高产能 ・ 但是冷却用风量也不可过高. 否则过多的没有参与燃烧的
空气会 带走 大量 的热 量 , 增 加热耗 。
五 采取的措施
1 、 2 0 l 4 = q 1 4 月份 我公司开 始添 加氢氧 化铝脱水 剂 , 经过试验 测得 , 脱水 剂的
1 0 5 0 " C- 1 1 5 0 ℃ 之间 。
从2 0 0 7 年5 月份投产以来, 焙烧主炉温度控制在1 0 5 0 " C左右 , 灼碱<1 . 0 %, 我们中美铝业生产工艺为拜耳法 , 节能降耗、 增盈增效是我们的工作重点, 经过
对 降低焙 烧温 度的 不断探 索 , 现 已将焙 烧温度 调整 到9 8 0 " ( 2 -1 0 3 0 " ( 2 左右 , 比原 来 平均 降低 5 0 " ( 2 左右, 灼碱 指标 <1 . O %, 仍可 以获得 高性 能 的电解级 氧化 铝 ,
理论广角
I ■
降 低 焙 烧 炉 能耗 提 高 经 济 效 益
张胜 利 王世鹏
( 河南中美铝业有限公司 郑州
登封 4 5 2 4 7 0 ) 要】 氢 氧化 铝 焙烧 是氧 化铝 生产 过程 中的最后 一道 工序 , 其 能耗 占氧 化铝 生产 工艺 能耗 的 1 0 %2  ̄ 右, 焙烧 炉 的生产 能力 直接 影 响氧化 铝 企业 的整 体产 能和经济效益。 本文对气体悬浮焙烧炉降低焙烧能耗进行探讨 , 分析了影响焙烧能耗的因素, 提 出了解决方法 , 对获得高l 『 生能氧化铝, 降低焙烧煤气单耗和 电单耗 有 重要 意义 。 [ 关键词 ] 气体 悬 浮焙 烧 炉 焙烧 温 度 节能 降耗 经济 效益 中 图分类 号 : T F 8 2 1 文献标 识码 : A 文章 编号 : 1 0 0 9 — 9 1 4 X( 2 0 1 4 ) 3 3 — 0 2 8 2 一 O l
焙烧炉月总结范文

一、前言本月,我单位焙烧炉运行情况良好,生产任务完成较为顺利。
现将本月焙烧炉运行情况及存在的问题进行总结,以便为下月工作提供参考和改进方向。
二、本月主要工作及完成情况1. 焙烧炉运行稳定本月,焙烧炉整体运行稳定,各项指标均达到设计要求。
通过加强设备维护保养,确保了焙烧炉的长期稳定运行。
2. 产量达标在保证设备稳定运行的前提下,本月焙烧炉产量达到计划目标,满足了市场需求。
3. 能耗降低通过优化操作工艺和设备管理,本月焙烧炉能耗较上月有所降低,为公司节约了生产成本。
4. 质量稳定本月焙烧炉产品质量稳定,各项检测指标均符合国家标准,客户满意度较高。
三、存在的问题及改进措施1. 设备故障率较高本月,焙烧炉设备故障率较高,影响了生产进度。
针对这一问题,我们将采取以下措施:(1)加强设备日常维护保养,提高设备运行稳定性;(2)定期对设备进行检查,及时发现并排除潜在隐患;(3)提高操作人员技能水平,降低人为故障发生概率。
2. 能耗仍有下降空间虽然本月能耗较上月有所降低,但仍有下降空间。
为此,我们将:(1)优化操作工艺,降低能耗;(2)提高设备运行效率,减少能源浪费;(3)加强员工节能意识培训,倡导绿色生产。
3. 质量波动本月,焙烧炉产品质量波动较大,影响了客户满意度。
为解决这一问题,我们将:(1)加强对生产过程的质量监控,确保产品质量稳定;(2)优化生产配方,提高产品质量;(3)提高操作人员对质量问题的敏感度,及时处理异常情况。
四、下月工作计划1. 加强设备维护保养,降低设备故障率;2. 优化操作工艺,降低能耗;3. 提高产品质量,确保客户满意度;4. 加强员工培训,提高整体素质。
总之,本月焙烧炉运行情况良好,但仍存在一些问题。
在今后的工作中,我们将继续努力,不断改进,为公司创造更多价值。
炭素焙烧炉节能研究与应用分析

炭素焙烧炉节能研究与应用分析摘要:随着社会经济的高速发展以及群众日常生活水平的不断提升,社会已经进入到了全新的发展阶段中,这也为炭素材料工业的发展起到了良好的促进作用,无论是在产品、质量还是规格等方面,其都取得了十分优异的效果。
然而,炭素制品在实际生产阶段中,往往会消耗大量的能源,为了进一步响应国家方面的节能减排需求,就必须要针对所用的炭素焙烧炉展开全面的改进优化,在不影响原本生产效率的同时,大幅度降低资源消耗。
因此,文章首先对目前炭素焙烧炉存在的问题以及节能需求展开深入分析;在此基础上,提出炭素焙烧炉节能的具体优化措施。
关键词:炭素焙烧炉;节能研究;优化措施引言:炭素焙烧炉,其属于炭素产品生产过程中至关重要的生产设备,并且在实际生产阶段中起到了十分关键的作用,通过炭素焙烧炉,生阳极在填充料保护下(防止氧化以及变形)进行高热处理,使煤沥青炭化的工艺过程称为焙烧。
焙烧是生产炭阳极最重要的热处理工序之一,煤沥青炭化生成的沥青焦把骨料和粉料颗粒牢固的连接成整体,炭质生块的物理化学性质发生一系列变化,如挥发分已基本排尽、质量减少、体积收缩、真密度增加,导电及导热性能提高。
阳极焙烧是阳极生产中的最后和最重要的工序,其目的是通过焙烧使阳极达到必要的质量特性。
焙烧把物理过程和化学过程结合在同一个工序中进行,其中有些过程是同时进行的,有些则是随着温度的升降依次进行的。
制品的焙烧过程,主要是粘结剂沥青的焦化过程,即是沥青进行分解、环化、芳构化和缩聚等反应的综合过程。
焙烧的过程变化决定着制品物理、化学性能的变化,是焙烧控制作业的理论依据,因此认识焙烧的过程非常重要。
同时,炭素焙烧炉所采用的焙烧工艺,以及其自身的炉型结构,这些都会对焙烧产品的质量产生直接影响,站在实际情况的角度上来看,目前我国大部分厂家当中所采用的主要为敞开式环式焙烧炉,而随着生产规模的逐步拓展,以及产能方面的增加,如果在实现节能减排的同时进行清洁生产,已经成为了目前炭素生产过程中需要主要考虑的目标。
焙烧车间节能降耗及合理化建议
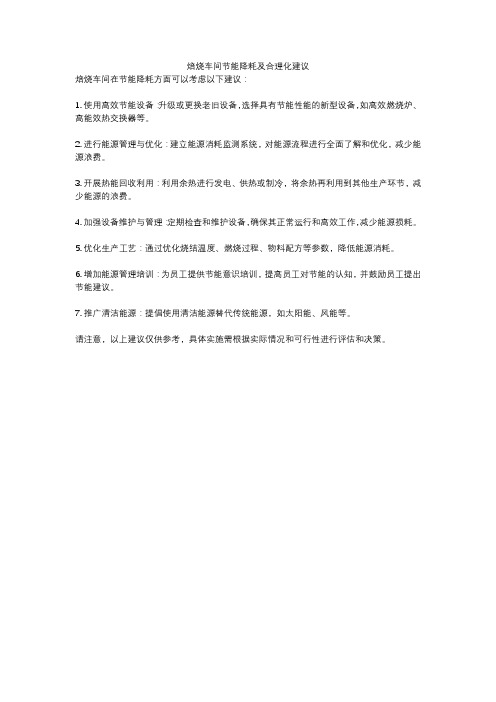
焙烧车间节能降耗及合理化建议
焙烧车间在节能降耗方面可以考虑以下建议:
1. 使用高效节能设备:升级或更换老旧设备,选择具有节能性能的新型设备,如高效燃烧炉、高能效热交换器等。
2. 进行能源管理与优化:建立能源消耗监测系统,对能源流程进行全面了解和优化,减少能源浪费。
3. 开展热能回收利用:利用余热进行发电、供热或制冷,将余热再利用到其他生产环节,减少能源的浪费。
4. 加强设备维护与管理:定期检查和维护设备,确保其正常运行和高效工作,减少能源损耗。
5. 优化生产工艺:通过优化烧结温度、燃烧过程、物料配方等参数,降低能源消耗。
6. 增加能源管理培训:为员工提供节能意识培训,提高员工对节能的认知,并鼓励员工提出节能建议。
7. 推广清洁能源:提倡使用清洁能源替代传统能源,如太阳能、风能等。
请注意,以上建议仅供参考,具体实施需根据实际情况和可行性进行评估和决策。
影响阳极焙烧炉重油消耗的因素分析

影响阳极焙烧炉重油消耗的因素分析吴仕献张文生摘要:本文阐述了影响阳极焙烧炉热耗的主要因素,并从能耗的角度,对阳极在焙烧过程中影响重油消耗进行了详细和全面的分析。
关键词:焙烧炉;能耗;重油;挥发分;预热空气在现代铝用炭素工业中,用敞开式环式焙烧炉生产预焙阳极已十分普遍。
而采用的燃料一般为天然气、煤气、重油等,而如何降低能耗,提高热效率已成为其技术进步的关键。
国外敞开式阳极焙烧炉(PECHINEY)每吨阳极能耗已经降至2.0×106kJ/t水平, 目前国内大多采用此焙烧炉、用重油做燃料的,能耗普遍在(2.6~3.0)×106kJ/t (重油65~70 kg/t.c),最好水平达到(2.0~2.2)×106kJ/t(折合重油约50~55kg/t.c),我公司焙烧II系列2007年油耗平均在63 kg 左右,经过多年的摸索、实践,目前的油耗每t熟阳极油耗约在53.5kg 左右。
现就影响阳极焙烧炉重油消耗的主要因素进行如下探讨。
1 影响焙烧炉热耗的主要因素法国SATRUM公司曾对其在法国的某焙烧炉作过详细的热平衡计算:1.从整台炉来看,热收入源于重油燃烧(56%)、沥青挥发分燃烧(38%)和填充焦燃烧(6%)等三部分.热支出包括阳极和填充焦残留(30%)、排烟损失(27%)、炉面散热(27%)、炉壳散热(9%)及冷却阳极空气带走热量(7%)等。
其中,阳极和填充焦残留以及冷却阳极空气带走热量都与固体蓄热(包括阳极、填充焦、横墙和火道墙)的回收即一次空气的预热密切相关,大量漏风渗入造成的附加排烟量(数倍于理论排烟量)成为排烟损失的主体.影响焙烧炉重油消耗的因素基本可用以下四项来概括:重油是否充分燃烧、挥发分的量及充分燃烧与否、预热空气的充分利用、炉子漏风。
2、重油燃烧情况重油的点火温度温度一般在550℃—650℃,而影响重油是否充分燃烧的因素主要有:足够高的火道温度以利于重油的燃烧,合理的重油供给量,足够的燃烧时间和空间,重油在燃烧时所需要的足够氧气,因随着焙烧的循环使用,急剧升温、急剧降温,重油在火道内燃烧造成局部高温,导致焙烧炉产生不同程度的变形,甚至将火道堵塞,导致重油在火道不能得到充足的氧气和燃烧空间,从而导致重油在火道内得不到充分燃烧。
氧化铝气态悬浮焙烧炉节能技术分析
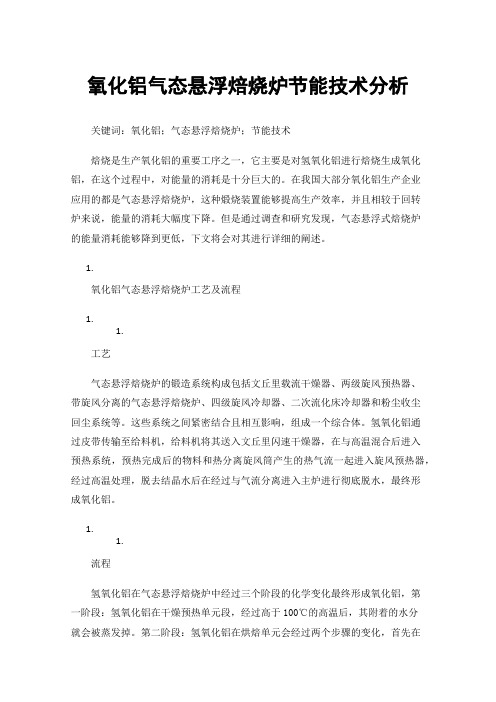
氧化铝气态悬浮焙烧炉节能技术分析关键词:氧化铝;气态悬浮焙烧炉;节能技术焙烧是生产氧化铝的重要工序之一,它主要是对氢氧化铝进行焙烧生成氧化铝,在这个过程中,对能量的消耗是十分巨大的。
在我国大部分氧化铝生产企业应用的都是气态悬浮焙烧炉,这种煅烧装置能够提高生产效率,并且相较于回转炉来说,能量的消耗大幅度下降。
但是通过调查和研究发现,气态悬浮式焙烧炉的能量消耗能够降到更低,下文将会对其进行详细的阐述。
1.氧化铝气态悬浮焙烧炉工艺及流程1.1.工艺气态悬浮焙烧炉的锻造系统构成包括文丘里载流干燥器、两级旋风预热器、带旋风分离的气态悬浮焙烧炉、四级旋风冷却器、二次流化床冷却器和粉尘收尘回尘系统等。
这些系统之间紧密结合且相互影响,组成一个综合体。
氢氧化铝通过皮带传输至给料机,给料机将其送入文丘里闪速干燥器,在与高温混合后进入预热系统,预热完成后的物料和热分离旋风筒产生的热气流一起进入旋风预热器,经过高温处理,脱去结晶水后在经过与气流分离进入主炉进行彻底脱水,最终形成氧化铝。
1.1.流程氢氧化铝在气态悬浮焙烧炉中经过三个阶段的化学变化最终形成氧化铝,第一阶段:氢氧化铝在干燥预热单元段,经过高于100℃的高温后,其附着的水分就会被蒸发掉。
第二阶段:氢氧化铝在烘焙单元会经过两个步骤的变化,首先在250-450℃的加热过程中,脱去两个分子的结晶水,生成一水软铝石,紧接着在500-560℃的高温中,再脱去一个分子的结晶水,生成γ- Al2O3 。
第三阶段:这个阶段主要是晶型的转变,γ- Al2O3 结晶不完善,它具有较强的吸湿性,且分散度较大,不能满足电解铝的要求,因此将γ- Al2O3 晶体继续加热至900℃以上,就会产生γ- Al2O3 向α- Al2O3的转变。
1.影响氧化铝气态悬浮焙烧炉能耗的因素气态悬浮焙烧炉可以看作是一个敞开的热力学体系,它的炉内热加工过程十分的复杂,原料、燃料、系统风量等都是影响焙烧炉能耗的主要因素,以下我们进行详细的分析。
浅谈降低焙烧炉热能耗的实践工艺措施

282管理及其他M anagement and other浅谈降低焙烧炉热能耗的实践工艺措施姚智博(陕西有色榆林新材料集团有限公司阳极分公司,陕西 榆林 719000)摘 要:焙烧炉炭块焙烧过程中热能耗的高低,主要体现在燃料的使用量上,其在焙烧生产成本中占有较大比例。
如何降低焙烧炉热能耗,成为减少焙烧生产成本的一项重要措施。
本文主要从对焙烧生产过程中的工艺管控,论述降低焙烧炉燃气能耗的一些具体措施,为同行业阳极焙烧的节能工作提供有益借鉴。
关键词:焙烧炉;焙烧炉燃料;焙烧节能;焙烧过程中图分类号:TF821 文献标识码:A 文章编号:11-5004(2021)18-0282-2收稿日期:2021-09作者简介:姚智博,男,生于1987年,汉族,陕西蒲城人,本科,助理工程师,研究方向:碳素焙烧工艺。
在阳极的整个生产工序中,焙烧工序的成本是最大的[1]。
阳极焙烧是在填充料保护下进行高温热处理,使煤沥青炭化的工艺过程[2]。
焙烧过程直接决定焙烧阳极的质量,从而影响到电解用阳极的消耗、电流效率、电耗等。
通过焙烧,生阳极发生一系列的物理化学变化,粘接剂沥青碳化生成的沥青焦把骨料和粉料结合成为牢固的整体[3]。
焙烧过程热能源消耗大,直接影响企业的生产成本和经济效益。
为降低焙烧炉热能耗,很多预焙阳极生产厂家都在不断进行探索,但受炉体参数、炉况、工艺参数、人员操作等因素的影响,各生产厂家采取的措施较为多样,取得的成效也存在较大差异。
陕西某公司为降低焙烧炉燃气能耗,积极探索新工艺、新方法,成功使焙烧过程中的燃气耗量由81Nm³/t 降低到61Nm³/t,其中采取的一些措施,可为同行业其他生产厂家提供一些借鉴。
1 焙烧炉室热平衡状况分析 焙烧炉的装炉料箱端壁是由实心耐火砖砌成,侧壁是由空心耐火砖火道所组成,燃烧在火道内进行,热量通过砖墙和填充料层在火道和炉室内传递。
在加热过程中,由于负压作用,阳极在焙烧过程中产生的挥发分被吸入火道内和燃料一同燃烧,挥发分的燃烧与燃料的燃烧为焙烧过程的主要热量来源。
浅谈阳极焙烧的节能降耗

浅谈阳极焙烧的节能降耗随着时间的推移,我公司的预焙阳极生产也有以前的”煤制气”改为现在使用纯天然气焙烧阳极炭块。
顾名思义,焙烧就是把生坯块装入焙烧炉中,由低温慢慢升至1050°c时进行保温的整个控制过程,中间发生一系列物理化学变化和很多能量消耗。
如何节能,如何降耗,已是首要工作。
焙烧车间在2月份的气耗管理上,狠下功夫,采取很多方法和措施,通过努力,气耗有明显下降。
一、重视焙烧炉相关设备设施的保养、维修并严格装炉质量。
在装炉前各车间都把炉子的火道墙、端墙连接缝隙用耐火泥密封一遍,看是否有漏风漏气现象。
并随时掌握相关设备设施运行情况,减少由于设备设施故障或者密封不严而导致天然气浪费。
对生坯装炉时,要最大程度砸碗、捣实,焦粒中不应有焦面儿掺入,以免造成热传递不及时,同时炉室密封口用专用盖子,减少热量损失。
二、优化焙烧工艺,控制合理参数。
阳极焙烧是由低温升起,根据炉子情况,设置焙烧升温曲线。
技术的关键就是如何让阳极块挥发分在炉内充分燃烧,并对燃烧时间和位置充分优化。
挥发分排出时,火道温度也达到燃点,充分燃烧完毕。
在这个过程中,各车间合理控制升温曲线,加强热电偶座及喷嘴座的密封,改善喷嘴与火道墙体温度测试点,保证天然气的利用率和测试温度真实、准确。
三、利用冷却炉室热量,提高天然气燃烧的利用率。
车间适时调整助燃风机,增加预热空气的供应量,提高炉室天然气的充分燃烧。
适当增加负压,防止冷空气大量进入,延长了产品在1050°c的保温时间。
四、提高产品出炉产量,也是节能降耗的最有效方法。
当焙烧炉子保温到一定时间,必须出炉,否则能耗大,成本高,严重影响产品质量和公司经济效益。
2月份,焙烧各车间增加了出炉数量,提高了产量,节约能源,降低成本,为公司的发展打下良好的基础。
复杂难处理金矿循环流态化焙烧设备的节能减排优化

复杂难处理金矿循环流态化焙烧设备的节能减排优化随着工业化进程的加速,金矿资源的开采与利用成为了当代社会的重要课题。
然而,金矿的开采过程中产生的废弃物及废气排放给环境造成了巨大的负担。
为了减少对环境的不良影响,提高金矿开采过程中的能源利用效率,需要对复杂难处理金矿循环流态化焙烧设备进行节能减排优化。
金矿循环流态化焙烧设备是一种关键的金矿提取设备,该设备通过高温下的氧化反应使金矿石中的金属元素得以分离并转化成有价值的金属产物。
然而,这一过程中需要高温与大量的能源供应,导致能源消耗量巨大,同时产生的废弃物和废气大量排放。
为了解决这个问题,可采取一系列的节能减排优化措施。
首先,优化金矿循环流态化焙烧设备的工艺参数。
通过合理调整氧化反应的温度、氧气浓度和物料的流速等参数,可以达到最佳的反应效果,从而减少能源消耗和废气排放。
其次,采用先进的废气处理技术。
利用高效的废气处理设备,如湿法洗涤、催化剂等,可以有效去除废气中的有害物质,降低对环境的污染。
同时,还可以通过对废气的回收利用,提高能源利用效率。
再次,开展循环利用研究。
将焙烧过程中产生的废弃物进行分类和处理,选择性地回收其中有价值的金属元素,减少资源浪费,实现资源的循环利用。
最后,加强能源管理和监测。
建立完善的能源管理体系,通过对能源消耗情况的实时监测和分析,及时发现并纠正能源浪费问题,促进节能减排工作的开展。
在实施上述措施的同时,还需要加强科技研发和创新。
通过引进和开发更先进的金矿循环流态化焙烧设备,减少能源消耗和废弃物排放。
同时,还可以利用先进的模拟和优化软件对焙烧过程进行模拟和优化,进一步降低能源消耗和废气排放。
除了上述技术措施,还需要加强对金矿循环流态化焙烧设备的培训和管理。
提高操作人员的专业技能,确保设备的正常运行。
同时,建立健全的管理制度,加强对设备运行情况的监督和检查,及时发现并解决问题,确保设备的节能减排效果持久。
综上所述,复杂难处理金矿循环流态化焙烧设备的节能减排优化是一个复杂而重要的课题。
- 1、下载文档前请自行甄别文档内容的完整性,平台不提供额外的编辑、内容补充、找答案等附加服务。
- 2、"仅部分预览"的文档,不可在线预览部分如存在完整性等问题,可反馈申请退款(可完整预览的文档不适用该条件!)。
- 3、如文档侵犯您的权益,请联系客服反馈,我们会尽快为您处理(人工客服工作时间:9:00-18:30)。
焙烧炉能耗计算与分析
陆敏,吴海文
中国铝业广西分公司,广西 百色 531400
摘要:焙烧炉的能源消耗在生产消耗中占有较大的比重,通过对焙烧炉的热平衡计算,分析影响焙烧炉能耗的几个因素,并提出了进一步降低能源消耗的主要途径。
关键词:焙烧炉;能耗;热平衡
1.前言
氧化铝生产中,焙烧过程最常用的设备主要有气体悬浮焙烧炉、回转窑等。
其中气体悬浮焙烧炉以工艺的先进性和能源的高效利用在行业有广泛的应用。
目前气体悬浮焙烧炉的燃料采用重油等液态燃料或者发生炉煤气、天然气等气体燃料,采用多级换热的方式对热量进行梯级回收,能源转换效率高(见图1)。
但是,受世界范围内能源紧缺的制约,如何进一步降低焙烧炉的能源消耗,是节约能源的一个重要发展方向。
2.焙烧炉热平衡计算
焙烧炉的热量主要来源于燃料(本文中以发生炉煤气进行计算)燃烧提供的热量。
产生的热量主要用来提供氢氧化铝转变成氧化铝所需要的化学能以及结晶水、附着水气化所需要的能量,最终以烟气和焙烧氧化铝为载体将热量带出系统,还有少量能量通过设备表面辐射、换热的形式流失。
通过热平衡计算,可得到各种热支出的分布情况。
以我厂的1#焙烧炉为例,采用发生炉煤气作为燃料。
原始条件如下(2011年):
空气
AO 出料
图1 焙烧炉工艺简图
表1 焙烧炉操作条件
进料量 进料附水 进料温度 煤气流量 煤气温度 剩余氧含量
106t/h
2.60%
61℃ 33420Nm3 34℃
2.20%
表2 煤气成分
在热平衡计算中,氢氧化铝的反应热可根据下面的公式计算:
)()1001868.42.191001868.43.117821000γα⋅⨯+⋅⨯⋅⨯⋅=M Q
式中, M —干氢氧化铝量, kg/t.AO ;
α—成品氧化铝中 -Al2O3的质量分数,%;
γ—成品氧化铝中 -Al2O3的质量分数,%;
78—氢氧化铝的分子量,g/mol ;
11.3×4.1868—2mol 氢氧化铝反应生成 -Al2O3的吸热量,kJ/mol ; 19.2×4.1868—2mol 氢氧化铝反应生成 -Al2O3的吸热量,kJ/mol 。
烟气的流量可通过经验公式或根据燃烧反应方程式进行计算,在本文中就不详细介绍。
表3中就是根据热平衡计算得出的1#焙烧炉热收入和支出的详细情况。
表 3 1#焙烧炉热平衡表(2011年)
热收入 热支出 项目 数值 项目 数值
空气显热(MJ/t.AO) 21.0 电收尘出口烟气(MJ/t.AO) 669.9 干AH 显热(MJ/t.AO) 118.3 CO4出料AO(MJ/t.AO) 345.7 AH 附水显热(MJ/t.AO) 10.5 附水和结晶水蒸发热(MJ/t.AO) 1440.9 煤气显热(MJ/t.AO) 27.8 表面散热(MJ/t.AO) 200.0 煤气燃烧反应热((MJ/t.AO) 3513.8 AH 变成AO 的反应热(MJ/t.AO) 787.1 其他计算误差 247.8 合计(MJ/t.AO) 3691.5 合计(MJ/t.AO) 3691.5
3.主要影响因素 3.1 燃料热值
煤气热值对焙烧炉的能耗由巨大的影响。
热值的高低主要体现在燃料成分的不同。
根据表2中的数据可以看出,燃料中的可燃物质主要包括CO 、H2、甲烷(CH4)和多元烷。
但这些可燃成分的比重远未能达到总成分的50%。
主要的成分被N2所取代。
这就意味着一半以上的气体需要用燃料燃烧进行加热,最终以烟气(180℃)成分排入大气。
其次,煤气中含有的水分对煤气热值也有很大的影响。
由于煤气在制造过程中不可避免的存在机械水和饱和水蒸汽汽。
在输送过程中,如果温度升高,则机械水将转变成饱和水蒸汽直接以煤气成分的形式存在,将极大的影响到煤气的热
值。
图2中显示的是在相同压力下,不同的温度中水蒸汽可占据的最高体积比例。
可见煤气温度越高,煤气中含有的水分就有可能越高,越不利于煤气热值的提升。
0%
10%20%30%40%50%60%70%80%
0℃
20℃
40℃60℃80℃
100℃
温度(℃)
含水率(%)
3.2 氢氧化铝附水
氢氧化铝的附水对焙烧炉的能耗影响很大。
主要原因为水的潜热远远大于水的显热(见表4)。
表3中可以看到附水和结晶水蒸发热是热支出的一个主要方向。
在这过程中,由于结晶水是氢氧化铝本身固有的特性,在实际生产中,由于附水的增加,在系统中,需要投用额外的能量进行加热使其改变成水蒸气并最终以烟气成分的形式排入大气。
表4 水的物理性质
烟气温度 对应饱和压力 对应饱和水焓值 对应蒸汽焓值 对应汽化潜热 180℃ 10.019bar 783.2kJ/kg 2777.7kJ/kg 2014.5kJ/kg
根据计算,氢氧化铝中含水率越高,煤气需要消耗的煤气量越大,平均每改变1%的含水率,热值为5.6MJ/ Nm 3的煤气单位消耗量大约改变7Nm 3(具体关系见下图)。
20406080100
1
2
3
4567
8
910
含水率 %
煤气量 N 3m /t .A O
3.3 剩余氧含量
焙烧炉属于工业炉窑,在运行过程中为了保证燃烧质量,确保不发生不完全反应导致安全事故,必须要求一定的空气过剩系数。
在焙烧炉中体现为剩余氧含
图2 不同温度下煤气的最高含水率
图3 氢氧化铝含水率对煤气消耗的影响
量。
理论已经证明,较大的剩余氧含量(空气过剩系数)对能耗消耗是不利的。
主要原因是较大的氧含量意味着炉膛中进入了过多的空气量,这部分多出来的空气会破坏整个系统的热平衡,降低炉内的温度。
在这个过程中,如果需要进入新的热平衡,必须通入更多量的能量(即燃料)才能维持新的平衡。
因此,剩余氧含量必须要控制在一个合理的范围。
4.改进措施
从以上的分析可知,焙烧炉的消耗降低可以从3个方面入手:
一是提高煤气的热值。
通过对煤气发生炉进行更加精细的操作,根据不同的煤种进行不同的反应温度的控制,使得生产出来的煤气成分中可燃成分比重增加。
或者采用新技术,如采用富氧代替空气进行反应、两段法煤气产生技术等替代目前的工艺。
在部分天然气供应充分的地方,可以选择使用天然气代替煤气进行生产。
二是降低氢氧化铝中的含水率。
目前较为常用的办法是使用脱水剂进行强化脱水。
通过调整脱水剂的用量,可以最大幅度的降低含水率。
其次是根据工艺条件尽量增大氢氧化铝的粒度,这样有利于平盘过滤机的过滤效果,保证含水率的降低。
三是适当下调焙烧炉的氧含量。
目前国内外先进的控制范围在1.0至1.5%之间。
在保证燃烧反应充分的前提下,通过适当的下调可以对能耗由一定的帮助。
5.结语
焙烧氧化铝过程的能源消耗在氧化铝工艺中占有很大的比例。
虽然气体悬浮焙烧炉是目前能耗最低的设备,但是如何进一步挖掘节能降耗,仍然有很大的潜力。
由于焙烧炉是一个大系统,其中的过程反应机理仍在探索中,如何对设备进行进一步的优化,需要更进一步的探索。