复合材料真空灌注成型制造流程
【收藏】复合材料真空导入工艺

【收藏】复合材料真空导入工艺真空导入技术自引入到我国后,经过十多年来的发展,在国内已经是一项非常成熟的工艺了。
近几年由于环保严查,闭模工艺越来越受到大家的重视,原先很多做手糊工艺的企业都在谋求工艺上的转型。
本文从真空导入的原理入手,对于整个工艺流程进行了完整的描述,也从力学性能和优势方面跟其它工艺进行了比对,让大家对真空导入工艺有比较清晰的了解。
1、真空导入工艺(Vacuum infusion process,VIP)真空导入工艺,简称VIP,在模具上铺增强材料(玻璃纤维,碳纤维,夹心材料等,有别于真空袋工艺),然后铺真空袋,并抽出体系中的空气,在模具型腔中形成一个负压,利用真空产生的压力把不饱和树脂通过预铺的管路压入纤维层中,让树脂浸润增强材料最后充满整个模具,制品固化后,揭去真空袋材料,从模具上得到所需的制品。
VIP采用单面模具(就象通常的手糊和喷射模具)建立一个闭合系统。
真空导入工艺公诸于世很久了,这个工艺在1950 年出现了专利记录。
然而,直到近几年才得到了发展。
由于这种工艺是从国外引入,所以在命名上有多种称呼,真空导入,真空灌注,真空注射等。
2、理论真空导入工艺能被广泛的应用,有其理论基础的,这就是达西定律:Darcy’s Law)t =ℓ2h/(2 kDP )t 是导入时间,由四个参数来决定;h-树脂粘度从公式上可以看出所用树脂的粘度越低,则所需导入时间就越短,因此真空导入所用的树脂粘度一般不能太高。
这样可以使树脂能够快速的充满整个模具。
ℓ-注射长度,指的树脂进料口与到达出料口的之间的距离,距离长当然所需的时间亦长。
DP-压力差, 体系内与体系外压力差值越大,对树脂的驱动力也越大,树脂流速越快,当然所需导入时间也越短。
k= 渗透性,指玻纤,夹心材料等对树脂浸润好坏的参数。
k 值大说明浸润好,像多向毡要比方格布,短切毡易被树脂浸润。
因此为了使得树脂在增强材料被压实的情况下能方便的充满体系,一般会人为设置一些导流槽,比如在夹心泡沫上下打孔等。
复合材料成型加工技术---
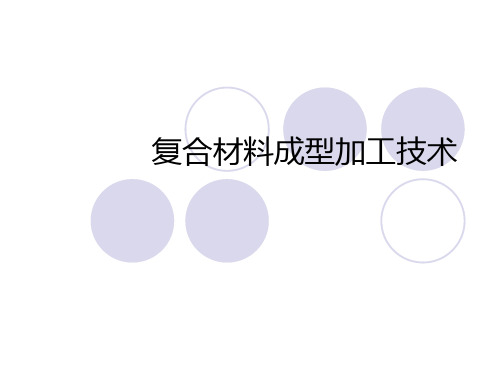
真空袋
1. 过程
制品毛坯 真空袋密封 抽真空 固化 制品
2. 特征 1)工艺简单,不需要专用设备; 2)压力较小,最大为0.1MPa,只适
用厚度1.5mm以下复合材料制品
压力袋成型
压力为0.25~0.5MPa
真空袋-热压罐成型
预浸料成型
预浸料成型(prepreg lay-up)
基本步骤:
设备:要求比RTM高,投资大
模压成型(Compression Molding)
将复合材料片材或模塑料放入金属对模中, 在温度和压力作用下,材料充满模腔,固 化成型,脱模制得产品的方法。
模具预热 模压料称量
涂刷脱模剂 预热
装模
压制 脱模
制品 检验 后处理
BMC模压 SMC、TMC模压 预浸料模压(层压)
多孔膜 密实膜 多孔织物
多孔膜
真空封装系统:透气、隔离、吸胶、透胶系统
适合加工高纤维含量(>60%)复合材料 简单和复杂构型构件均可以加工 高强度和高刚度复合材料均可以加工 劳动强度大,不适于大量加工 构件成本高 在航空和军事用先进复合材料上用途广泛
喷射成型(spray-up process)
包括:
干法缠绕: 预浸纱 湿法缠绕: 纤维纱 半干法缠绕: 纤维纱
加热软化 缠绕 浸胶 缠绕 浸胶 烘干 缠绕
非常适合制作管 状制品,如压力 容器、管道、火 箭发动机壳体、 喷管、化学品储 存罐等
配合CAD系统, 可以制作外形更 为复杂的构件
基本步骤
① 粗纱线轴放置在粗纱架上; ② 几根粗纱从导纱沟中穿过; ③ 固化剂和树脂在容器中混合后倒入树脂浸渍槽中; ④ 在卷绕滚筒上涂覆脱模剂、凝胶涂层,并将卷绕滚筒放
复合材料注射成型工艺

复合材料注射成型工艺
复合材料注射成型工艺是一种将纤维增强树脂复合材料注射到模具中,通过加热和压力使其固化形成所需的产品或零件的制造方法。
以下是复合材料注射成型工艺的一般步骤:
1. 材料准备:选择适当的纤维和树脂,并按照特定的配比进行混合和预处理。
2. 模具设计和制造:根据产品或零件的要求,设计和制造出适应的模具。
3. 模具准备:在开始注射成型之前,需要对模具进行准备,如涂抹模具表面的防粘剂,以确保成品的顺利脱模。
4. 注射成型:将预处理好的纤维增强树脂复合材料通过注射机注入到模具的空腔中。
注射时,可以施加一定的压力来促进树脂充填和纤维排列。
5. 固化:注射完成后,通过加热和固化剂等方式,使树脂快速固化。
固化过程中,可以控制温度、压力和时间等参数,以确保复合材料的质量。
6. 脱模和后处理:在树脂固化完全后,打开模具并取出成品。
根据需要进行修整、修边、打磨等后处理工序,以达到最终的产品要求。
复合材料注射成型工艺具有高效率、自动化程度高、产品质量稳定等优点,广泛应用于航空航天、汽车、电子、体育用品等领域的零部件制造中。
1。
新材料真空灌注工艺
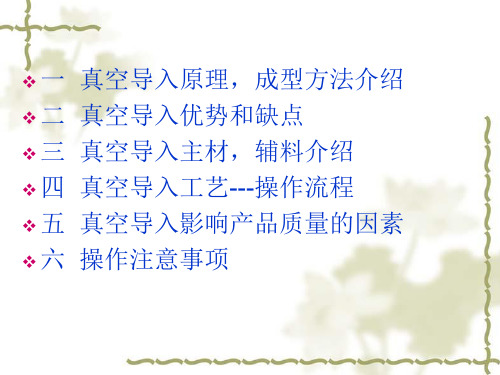
纤维布不需要预浸,树脂气味挥发很少。
二 真空导入的 缺点 1、繁琐的准备工作 脱模层 导流层 进胶主管道 抽气缠绕管 2、容易报废 如果进胶时发生漏气,即使少量空气进入,也可能导致产品中夹杂气泡降 低强度,甚至产品缺胶报废。
制成与工件相同的形状。 ❖ (4)质量均匀性好。
三 导流介质的选择—导流网
导流介质是在真空导入下有的概念。在真空导入工艺中,树脂从某一注入点 进入铺层,树脂在腔内的这个流动过程是有方向的。因为树脂总是倾向于进 入阻力最小的区域。但许多增强材料会形成很强的阻力,妨碍树脂的流动。 流动介质就是用来协助树脂的流动。 尽管将树脂注入不加导流介质的增强材料中是可能的,但成功的例子是很少 的。导流介质放在铺层结构上面,为树脂提供一个容易流动的通道。导流网 是我们在真空灌注中选择的一种传递树脂的辅材。
常用铺设距离距离产品边缘5公分
❖ (3)导流管 欧米茄管
导流管引导树脂流动的主方向。管径的大小直接影响树脂在其中的流动速度,管壁的 厚度不要太薄,如果太薄会在抽真空时被薄膜压扁,从而影响树脂的流动。导流管的布设 方式有多种,根据不同产品的需要,有平行布管、“丰”字型布管,“回”字型布管等。
导流管与产品边缘最大距离,不宜超过630mm,阻燃性树脂530mm
4 .铺设导流网,导流管,缠绕管(螺旋管),注胶三通,进胶管,抽气 管,
❖ 5. 法兰边铺双面棉胶条,铺密封胶条
❖ 6. 铺袋膜,袋膜适度要有余量,不要留下太大的褶皱,但也要给铺 管道的区域留下空间,太松或太紧都会造成树脂淤积或异常灌注。
❖ 7.抽气管连接树脂收集器,再连接真空泵。
更大功率的泵将帮助灌注更快地进行。 收集器是一个密封容器,一端连接铺层,收集器的作用是防止树脂进入真 空泵,注:使用树脂回收罐之前,将一些脱模蜡涂在罐的内部,以保证固化的树 脂可以很容易地移除。
复合材料真空灌注-RTM成型工艺及应用

复合材料真空灌注-RTM成型⼯艺及应⽤概述真空辅助树脂灌注成型⼯艺(VacuumAssisted Resin Infusion Molding)简称VARIM⼯艺,是在RTM(Resin Transfer Molding)⼯艺基础上发展起来的⼀种⾼性能、低成本的复合材料成型⼯艺。
⾃80年代末开发出来,VARIM⼯艺作为⼀种新型的液体模塑成型技术(Liquid Composite Molding,简称LCM),得到了航空航天、国防⼯程、船舶⼯业、能源⼯业、基础结构⼯程等应⽤领域的⼴泛重视,并被美国实施的低成本复合材料计划(Composite AffordabilityInitiative,简称CAI)作为⼀项关键低成本制造技术进⾏研究和应⽤。
如图1所⽰,VARIM⼯艺的基本原理是在真空负压条件下,利⽤树脂的流动和渗透实现对密闭模腔内的纤维织物增强材料的浸渍,然后固化成型。
VARIM⼯艺的基本流程包括:(a) 准备阶段。
包括单⾯刚性模具的设计和加⼯、模具表⾯的清理和涂覆脱模剂、增强材料(纤维织物、预成型件、芯材等)和真空辅助介质(脱模介质、⾼渗透导流介质、导⽓介质等)的准备等。
(b) 铺层阶段。
在单⾯刚性模具上依次铺设增强材料、脱模布、剥离层介质、⾼渗透导流介质、树脂灌注管道、真空导⽓管道等。
(c) 密封阶段。
⽤密封胶带将增强材料及真空辅助介质密封在弹性真空袋膜内,并抽真空,保证密闭模腔达到预定的真空度。
(d) 灌注阶段。
在真空负压下,将树脂胶液通过树脂灌注管道导⼊到密闭模腔内,并充分浸渍增强材料。
(e) 固化阶段。
继续维持较⾼的真空度,在室温或加热条件下液体树脂发⽣固化交联反应,得到产品预成型坯。
(f) 后处理阶段。
包括清理真空袋膜、导流介质、剥离层介质、脱模布等真空辅助介质和脱模修整等,最终得到制品。
图1 真空辅助模塑成型(VARIM)⼯艺⽰意图和传统的开模成型⼯艺以及RTM⼯艺相⽐,VARIM⼯艺具有以下优点:(1) 模具成本低。
真空灌注成型工艺流程

真空灌注成型工艺流程嘿,朋友!你有没有想过那些看起来超级酷炫的复合材料制品是怎么制造出来的呢?今天我就来给你讲讲真空灌注成型这个超有趣的工艺流程。
我有个朋友叫小李,他就在一家做复合材料产品的工厂工作。
有一次我去他那儿参观,才真正见识到真空灌注成型的奇妙之处。
一般来说,这个流程的第一步是模具准备。
这就像是给即将诞生的“宝贝”准备一个舒适的“摇篮”。
模具得非常干净、光滑,不能有任何瑕疵或者灰尘。
小李他们厂里,那些工人师傅们可仔细了,拿着干净的布,一遍又一遍地擦拭模具,就好像在对待世界上最珍贵的东西一样。
我当时就想,这模具这么重要吗?后来才明白,如果模具不干净,就好比你做饭的时候锅没洗干净,做出来的东西肯定有问题啊!模具准备好之后呢,就得开始铺放增强材料了。
这增强材料啊,就像是建筑物里的钢筋一样,是整个产品的骨架。
可以是玻璃纤维布、碳纤维布之类的材料。
工人们就像细心的裁缝一样,把这些材料一层一层地铺在模具里,按照特定的方向和顺序。
有时候,还会在这个过程中加入一些芯材,这芯材就像是三明治中间的那层美味的馅料,让产品不仅有强度,还有一定的厚度和特殊的性能。
我好奇地问小李:“这材料铺得不齐或者方向不对会怎样呢?”小李笑着说:“哎呀,那就好比你盖房子的时候大梁放歪了,房子能结实吗?”接下来就是重中之重的灌注树脂环节啦。
在灌注之前,要先把整个模具周围密封好,这密封得严严实实的,就像把宝藏锁在一个密不透风的宝箱里一样。
然后呢,通过特殊的设备把树脂抽进这个密封的空间里。
这树脂就像有生命一样,缓缓地流淌到每一个角落,填满增强材料之间的空隙。
这个时候,你可以想象一下,就像是给干枯的河床注入了水流,树脂在增强材料里穿梭、渗透,把所有的部分都连接起来。
我在旁边看着,心里直犯嘀咕:“这树脂要是灌不满可咋办呢?”小李告诉我:“要是灌不满啊,那做出的产品就会有缺陷,就像一个没吃饱饭的人,没力气干活一样。
”在树脂灌注的过程中,真空可是起着至关重要的作用呢。
真空灌注低成本成型工艺及其应用研究
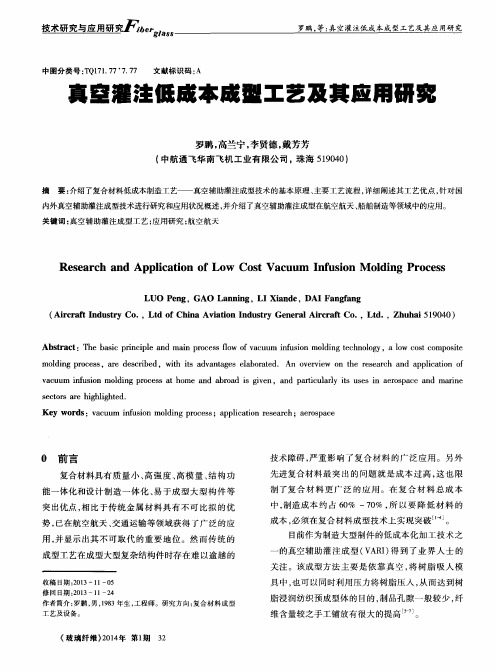
常环境温度为 1 5~ 2 5℃ , 相对湿度为 6 0 % 以下 。
( 2 )根据天线 罩尺 寸和成 型要 求 , 分 批次 配制 适量的环氧树脂体系胶液 , 搅拌均匀 。 ( 3 )根据某翼型机载天线罩 的外形尺 寸及壁厚 裁剪无碱玻璃纤维织物 , 置于 6 0℃ ± 5 o C的烘箱 中 干燥 4 h以上 。成 型前取 出增 强织 物 , 待其 降 至室 温后使用 。 ( 4 )在天 线罩 模具 ( 已涂 覆好脱 模 剂 ) 表 面按
Re s e a r c h a nd Ap pl i c a t i o n o f Lo w Co s t Va c uu m I n f u s i o n Mo l d i ng Pr o c e s s
LUO Pe n g,GAo La nn i ng,LI Xi a nd e,DAI Fa n g f a ng
一
用, 并显示 出其 不可 取代 的重要地 位 。然 而传 统 的 成 型工艺 在成 型大型复 杂结构件 时存 在难以逾越 的
收稿 日期 : 2 0 1 3一l 1 一 O 5 修 回 日期 : 2 0 1 3—1 1 —2 4
的真空辅助 灌注成 型 ( V A R I ) 得 到了业 界人 士 的
豳 堕
匦
e 榔
罗 鹏, 等: 真空灌注低本成型工艺 及其应用 研究
中图分类号 : T Q 1 7 1 . 7 7 7 . 7 7
文献标识码 : A
真窒灌洼低成本成蟹工艺及 其应用研究
罗鹏 , 高兰宁 , 李贤德 , 戴芳芳
( 中航通 飞 华南 飞机 工业有 限公 司 。珠海 5 1 9 0 4 0 )
摘 要 : 介 绍了复合材料低成本制造工艺——真空辅助灌注成型技术 的基本原理 、 主要工艺流程 , 详细 阐述其工艺优点 , 针对 国
复合材料真空辅助成型工艺总结

复合材料真空辅助成型工艺总结复合材料真空辅助成型工艺是一种将纤维增强复合材料与真空技术相结合的成型方法,具有高效、高质量和节能环保的特点。
以下是复合材料真空辅助成型工艺的几个主要步骤和工艺特点的总结:1. 原材料准备:选择适当的纤维增强材料、树脂基体材料和其他辅助材料。
确保材料的质量和性能符合要求。
2. 堆叠定型:根据产品的几何形状和规格,将纤维增强材料进行叠放定型。
确保纤维增强材料的层压顺序和方向合理。
3. 气压控制:通过真空泵将工作环境内部的气压降至一定的负压。
保持气压稳定,确保材料与模具之间的质量紧密接触。
4. 树脂注入:在成型过程中,通过真空泵将树脂基体材料注入到纤维增强材料之间的空隙中。
保持树脂基体材料的均匀分布。
5. 硬化固化:将注入树脂基体材料的复合材料放置在恒温和恒湿环境中,使其硬化和固化。
确保树脂基体材料具有良好的硬度和强度。
6. 产品后处理:对成型的复合材料进行必要的加工和后处理,如修剪、打磨和表面处理等。
确保产品的最终质量和外观符合要求。
复合材料真空辅助成型工艺具有以下几个特点:1. 高效节能:使用辅助真空辅助成型工艺可以大大减少树脂的浪费和能耗。
由于真空辅助成型可在低温下实现材料固化,使得能耗大大降低。
2. 产品质量高:真空辅助成型有助于减少空气和树脂中可能存在的气泡和缺陷,提高了成型复合材料的密实度和强度。
3. 成本降低:真空辅助成型工艺可以减少工作场地的需求,节省材料和能源的使用,从而降低了生产成本。
4. 克服形状限制:真空辅助成型工艺可以适应各种形状和尺寸的复合材料产品的生产需求,且适用于多种纤维增强材料和树脂基体材料的组合。
总之,复合材料真空辅助成型工艺通过真空技术的应用,使得复合材料的成型工艺更加高效、质量更好、能耗更低,具有广泛的应用前景。
复合材料制备工艺

用作基体材料的树脂以热固性树脂为 主,要求树脂的粘度低和适用期长等。
大量使用的基体材料有不饱和聚酯树 脂和环氧树脂等。
在拉挤成型工艺中,目前常用的方法如热 熔涂覆法和混编法。
热熔涂覆法是使增强材料通过熔融树脂, 浸渍树脂后在成型模中冷却定型;
混编法中,首先按一定比例将热塑性聚合物 纤维与增强材料混编织成带状、空芯状等几何形 状的织物;
由于模压制品质量可靠,在兵器、飞机、导 弹、卫星上也都得到应用。
3. 层压成型工艺
层压成型工艺,是把一定层数的浸胶布(纸) 叠在一起,送入多层液压机,在一定的温度和压 力下压制成板材的工艺。
层压成型工艺属于干法压力成型范畴,是复 合材料的一种主要成型工艺。
层压成型工艺生产的制品包括各种 绝缘材料板、人造木板、塑料贴面板、 覆铜箔层压板等。
最常用的树脂是在室温或稍高温度下即可 固化的不饱和聚酯等。
喷射法使用的模具与手糊法类似, 而生产效率可提高数倍,劳动强度降低, 能够制作大尺寸制品。
用喷射成型方法虽然可以制成复杂 形状的制品,但其厚度和纤维含量都较 难精确控制,树脂含量一般在60%以上, 孔隙率较高,制品强度较低,施工现场 污染和浪费较大。
然后,在一定压力作用下加热固化成 型(热压成型)或者利用树脂体系固化时 放出的热量固化成型(冷压成型),最后 脱模得到复合材料制品。其工艺流程如下 图所示:
模具 准备
树脂胶 液配制
增强材 料准备
涂脱模剂
手糊成型
固化
脱模
手糊成型工艺流程图
制品 检验 后处理
为了得到良好的脱模效果和理想 的制品,同时使用几种脱模剂,可以 发挥多种脱模剂的综合性能。
在加工过程中,由于熔体混合物的流动 会使纤维在树脂基体中的分布有一定的各向 异性。
真空密封铸造工艺流程
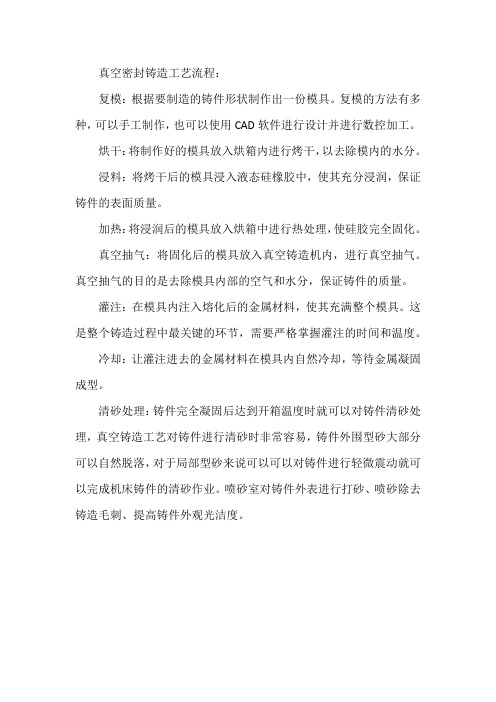
真空密封铸造工艺流程:
复模:根据要制造的铸件形状制作出一份模具。
复模的方法有多种,可以手工制作,也可以使用CAD软件进行设计并进行数控加工。
烘干:将制作好的模具放入烘箱内进行烤干,以去除模内的水分。
浸料:将烤干后的模具浸入液态硅橡胶中,使其充分浸润,保证铸件的表面质量。
加热:将浸润后的模具放入烘箱中进行热处理,使硅胶完全固化。
真空抽气:将固化后的模具放入真空铸造机内,进行真空抽气。
真空抽气的目的是去除模具内部的空气和水分,保证铸件的质量。
灌注:在模具内注入熔化后的金属材料,使其充满整个模具。
这是整个铸造过程中最关键的环节,需要严格掌握灌注的时间和温度。
冷却:让灌注进去的金属材料在模具内自然冷却,等待金属凝固成型。
清砂处理:铸件完全凝固后达到开箱温度时就可以对铸件清砂处理,真空铸造工艺对铸件进行清砂时非常容易,铸件外围型砂大部分可以自然脱落,对于局部型砂来说可以可以对铸件进行轻微震动就可以完成机床铸件的清砂作业。
喷砂室对铸件外表进行打砂、喷砂除去铸造毛刺、提高铸件外观光洁度。
- 1、下载文档前请自行甄别文档内容的完整性,平台不提供额外的编辑、内容补充、找答案等附加服务。
- 2、"仅部分预览"的文档,不可在线预览部分如存在完整性等问题,可反馈申请退款(可完整预览的文档不适用该条件!)。
- 3、如文档侵犯您的权益,请联系客服反馈,我们会尽快为您处理(人工客服工作时间:9:00-18:30)。
1.模具表面处理
1.1模具表面检查
检查模具表面有无缺陷,如砂眼、伤痕等。
如有则避开此位置(伤痕处做好标识,待以后修补)。
1.2模具表面清洁
先用高压气体把表面吹干净,保证气体不能带水分。
然后用干净的布把表面擦拭干净。
1.3脱模材料处理
1.3.1表面依次打洁模剂、封孔剂、脱模剂
2、结构铺层
2.1玻纤铺层
将玻纤平整地铺设在模具上搭接的区域不超过1cm,注意每层接缝错开50mm 左右。
2.2辅料(脱模布+带孔隔离膜+导流网)铺层
2.2.1将脱模布平整的铺在最上层复合毡的上面,注意脱模布要平整,无折痕。
脱模布有效尺寸为产品长/宽方向各+15cm。
2.2.2将带孔隔离膜、导流网依次按顺序平整铺在脱模布上面,并用豆粒大小的
密封胶条将其固定平整。
带孔隔离膜、导流网有效尺寸为产品长/宽方向
各-3cm。
2.3胶条+缠绕管+欧姆管+真空袋铺设
2.3.1在美纹纸外侧周围5到6厘米的位置铺设一圈缠绕管并用豆粒大小的密封
胶条将其固定住。
用覆盖在产品上最外侧的脱模布将缠绕管盖住,尺寸须刚刚完全遮住缠绕管。
2.3.2在缠绕管外侧四周距离5到6厘米的位置铺设一圈密封胶条,注意先不要
将隔纸撕下。
2.3.3注胶口设在顶部中间位置,欧姆管即设在顶部一条。
截取一根Ω管并将Ω
管边缘的毛刺打磨光滑,再将Ω管从中间锯断,套上三通,三通与欧姆管连接的地方贴一层胶条。
然后缠绕3-4圈密封胶条于三通直通底部上
2.3.4剪取一块长宽均大于密封胶条粘接区域20cm的真空袋膜,将真空袋膜抬到
产品上侧慢慢放下,从一边开始留足2cm余量后慢慢边扯掉缠绕管四周的密封胶条上的隔纸边铺好真空袋膜。
2.3.5使用抽气管将真空系统与树脂收集器连接。
2.4 真空保压
2.4.1开启真空泵,把真空袋膜理顺留足余量后,再把三通进胶口位置的真空袋膜
剪个口,然后在三通底座端头用密封胶条缠绕两圈,将真空袋膜与三通完全密闭,再将进胶管与欧姆管连接密封,最后用硬纸封住进气口。
2.4.2将真空表密封固定抽气管的抽气口。
2.4.3开启真空泵,检测真空系统的密封性,真空系统压力抽至20mbr以下,关闭
真空泵保压15分钟后检测压力,若压力增加不超过5mbr,方可进入下一步骤,如真空压力未达到上述要求则需不停检漏,直至无漏气点达到上述的要求。
注意:①收集器,真空泵,管连接真空密封必须保证密封②整个真空袋膜系统保证不漏气③压力必须达到标准后在灌注树脂。
3、产品制造
3.1配置树脂
配制环氧树脂:固化剂。
每次配制需使用干净无杂质的配胶桶,将树脂与固化剂搅拌均匀,搅拌次数不得低于三次。
3.2真空灌注
将进胶管端部折三折,保证不漏气,然后将进胶口插入树脂中,然后再慢慢松开弯折。
注意整个过程需不断检查,不要漏气。
3.3固化
3.4脱模
撕去真空辅材,注意操作时要小心,避免产品变形。
然后将产品轻抬脱模,注意不要损伤产品面。
4、后处理
4.1产品切割
画好产品切割线。
注意保证切割线水平垂直。