铜冶炼水平与工艺水平
铜的精炼与冶炼
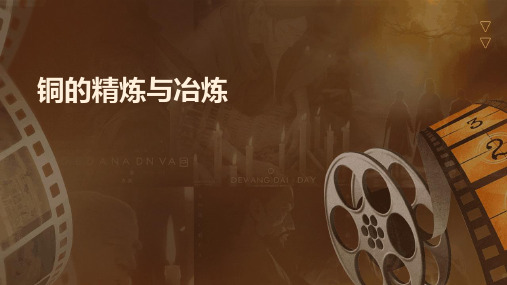
利用电解原理将粗铜提纯为高纯度铜,具有工艺成熟、操作简便的优势。
THANK YOU
鼓风炉熔炼
将铜矿石、熔剂和燃料放 入鼓风炉中,通过鼓入空 气进行氧化熔炼。
电炉熔炼
利用电能将矿石熔化,再 通过加入还原剂进行还原 熔炼。
铜的湿法冶炼
浸出
将矿石中的有用成分浸出到溶液 中,再通过化学反应将其提取出
来。
萃取
利用不同物质在两种不混溶液体中 的溶解度差异,实现有用成分的分 离和提取。
电积
将溶液中的铜离子还原成金属铜, 并收集沉积的铜粉。
03
铜的精炼工艺
粗铜的熔炼与铸造
熔炼
将铜矿石、返回料和熔剂等原料放入高温熔炉中熔化,形成粗铜。
铸造
将熔融的粗铜注入模具中,冷却凝固后形成阳极铜块。
铜的电解精炼
电解液制备
将硫酸和铜阳极板溶解在水中, 制成硫酸铜溶液作为电解液。
电解过程
将阳极铜块作为电解的阳极,阴 极为纯铜,通过直流电进行电解 。在电解过程中,阳极上的铜逐 渐溶解,并在阴极上析出纯铜。
全球铜资源分布广泛,但主要集中在 智利、美国、中国、秘鲁等国家和地 区。这些国家的铜矿储量和产量均居 世界前列。
铜的冶炼历史与现状
铜的冶炼历史
铜的冶炼技术可以追溯到公元前4000年左右的美索不达米亚文明时期。随着时 间的推移,铜的冶炼技术不断发展,逐渐形成了现代的冶炼工艺。
铜的冶炼现状
目前,全球铜冶炼产能主要集中在中国、美国、智利等国家。由于环保要求的 提高和资源的日益枯竭,现代冶炼工艺趋向于更加环保、节能和高效。
杂质去除
电解过程中,阳极上的其他金属 杂质也会溶解进入电解液中,通
过适当的处理方法将其去除。
铜冶炼技术对比解析

1992 1999 5家投产 16万吨/年矿 铜
单炉最高 产能
原料适应 性
原料预处 理
较差
粒度<1mm, 深度干燥, H2O<0.3%
适应性强
制粒或增湿, H2O 9%~11%
强
干燥,H2O< 1%
适应性强
适应性强
适应性强
粒度<100mm, 粒度<100mm, 制粒或增湿, H2O 10%~12% 不需要干燥。 不需要干燥。
S捕集率 炉寿命
150天
业内认可的先进熔炼工艺
闪速熔炼和熔池熔炼: ※Outokumpu闪速熔炼 ※ 浸没喷枪式熔炼(ISA/Ausmelt) ※ 三菱熔炼
闪速熔炼技术的进展
闪速炼铜工艺
●第一座炼铜闪速炉于1949年在芬兰哈里亚瓦尔塔 冶炼厂投入工业生产;目前还用于镍精矿的熔炼 ;1978年开始进行铜精矿的一步炼铜;1995年开 始进行冰铜的吹炼。 ●至今已有40台炼铜闪速炉建成投产,目前在运行 的有37台(其中有3台一步炼铜闪速炉,2台冰铜 吹炼闪速炉),6台炼镍闪速炉在生产。 ●炉体冷却结构的改进、冷却强度的提高,闪速炉 的单炉产能提高,最大达到原设计的3.65倍;闪 速炉的炉寿命延长,最长达到15年,一般10年左 右
产能大:单套系统最大铜产能超过40万吨/年
送风氧浓高:闪速熔炼氧浓达90%,ISA、
三菱、诺兰达熔炼氧浓达到65%,55%和 45%
自热或半自热熔炼:有效利用硫化矿物燃烧
所产生的热量;
冰铜品位高:均超过60%,可以高达75%
现代强化熔炼工艺的特点
高熔炼强度:闪速熔炼单炉铜精矿处理量首先突 破100万吨/年以上;Isa炉单炉铜精矿处理量达到 130万吨/年;三菱炉精矿处理量将超过100万吨/年 (温山)。 硫捕集率高,环保好:一般均超过95%。闪速熔 炼和三菱熔炼超过了99%,吨铜S的排放量不到 2kg,是最清洁的铜冶炼工艺 工艺控制自动化程度高:闪速炉实现了计算机在 线控制。
铜冶炼技术

铜冶炼过程中会产生大量的废水,这些废水中含有重金属 离子和有害物质,如果未经处理直接排放,会对水体造成 严重污染。
固体废弃物处理
铜冶炼过程中会产生大量的固体废弃物,包括炉渣、污泥 等,这些废弃物如果未经处理随意堆放,会对土壤和环境 造成污染。
铜冶炼过程中的安全问题
高温熔炼过程
铜冶炼过程中需要将铜矿石高温熔炼成铜液,这个过程中如果操作 不当,会造成高温烫伤和爆炸等安全事故。
同时将铜提取出来。
熔炼设备
采用鼓风炉、电炉或反射炉进行 熔炼。
熔炼过程
熔炼过程中需加入适量的熔剂, 以除去杂质和调节熔融物的成分
。
铜的吹炼
吹炼目的
01
通过向熔融物中鼓入空气,使杂质氧化并从熔融物中分离出去
,得到粗铜。
吹炼设备
02
采用转炉或连续吹炼炉进行吹炼。
吹炼过程
03
吹炼过程中需控制温度和气氛,以保证杂质的有效去除和粗铜
的质量。
铜的电解精炼
电解精炼目的
通过电解过程,使粗铜中的杂质进入阳极泥中, 得到纯度较高的电解铜。
电解设备
采用电解槽进行电解精炼。
电解过程
电解过程中需控制电流密度、电解液成分和温度 等参数,以保证电解铜的质量。
03
铜冶炼的环保与安全
铜冶炼过程中的环保问题
废气排放
铜冶炼过程中会产生大量的废气,包括二氧化硫、氮氧化 物等,这些废气如果未经处理直接排放,会对大气环境造 成严重污染。
铜精矿的焙烧与制团
焙烧目的
通过高温焙烧,使铜精矿 中的硫氧化,生成二氧化 硫气体,同时去除部分杂 质。
焙烧方式
采用回转窑或沸腾焙烧炉 进行焙烧。
制团
铜冶炼水平与工艺水平

铜冶炼水平与工艺水平1)火法冶炼工艺当前,全球矿铜产量的75%-80%是以硫化形态存在的矿物经开采、浮选得到的铜精矿为原料,火法炼铜是生产铜的主要方法,特别是硫化铜精矿,基本全部采用火法冶炼工艺。
火法处理硫化铜精矿的主要优点是适应性强,冶炼速度快,能充分利用硫化矿中的硫,能耗低。
其生产过程一般由以下几个工序组成:备料、熔炼、吹炼、火法精炼、电解精炼,最终产品为电解铜。
原料制备工序:将铜精矿、燃料、熔剂等物料进行预处理,使之符合不同冶炼工艺的需要。
熔炼工序:通过不同的熔炼方法,对铜精矿造硫熔炼,炼成含铜、硫、铁及贵金属的冰铜,使之与杂质炉渣分离;补出的含二氧化硫烟气经收尘后用于制造硫酸或其他硫制品,烟尘返回熔炼炉处理。
吹炼工序:除去冰铜中的硫铁,形成含铜及贵金属的粗铜,炉渣和烟尘返回上一工序处理。
火法精炼工序:将粗铜中硫等杂质进一步去除,浇铸出符合电解需要的阳极板。
电解精炼工序:除去杂质,进一步提纯,生产出符合标准的阴极铜成品,并把金银等贵金属富集在阳极泥中。
传统熔炼方法如鼓风炉熔炼、反射炉熔炼和电炉熔炼,由于效率低、能耗高、环境污染严重而逐渐被新的富氧强化熔炼工艺所代替[[3]新的富氧强化熔炼可分为闪速熔炼和熔池熔炼两大类,前者包括奥托昆普型闪速熔炼和加拿大国际银公司闪速熔炼等,后者包括诺兰达法、三菱法、艾萨法、奥斯麦特法和瓦纽可夫法以及我国自主开发的水口山法、白银炉熔炼、金峰炉熔炼等技术。
铜铳吹炼方法有传统的卧式转炉、连续吹炼炉、虹吸式转炉。
新型吹炼技术包括艾萨吹炼炉、三菱吹炼炉和闪速吹炼炉等。
粗铜的火法精炼在阳极炉内进行,对于转炉产出的液态粗铜采用回转式阳极炉或固定式反射炉精炼,经氧化、还原等作业进一步脱除粗铜中的铁、铅、锌、砷、锑、铋等杂质,并浇铸成含铜99.2%-99.7%的阳极板。
铜电解工艺有传统电解法、永久阴极电解法和周期反向电流电解法3种。
目前大多数电解铜厂都使用传统电解法,永久阴极电解法和周期反向电流电解法是20世纪70年代以来发展的新技术。
我国铜冶炼技术的进步及发展
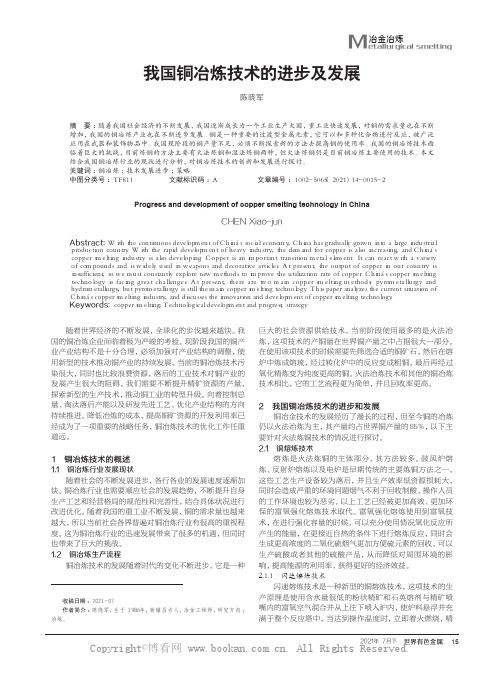
冶金冶炼M etallurgical smelting 我国铜冶炼技术的进步及发展陈晓军(新疆五鑫铜业有限责任公司,新疆 昌吉 831100)摘 要:随着我国社会经济的不断发展,我国逐渐成长为一个工业生产大国,重工业快速发展,对铜的需求量也在不断增加,我国的铜冶炼产业也在不断进步发展。
铜是一种重要的过渡型金属元素,它可以和多种化合物进行反应,被广泛应用在武器和装饰物品中。
我国现阶段的铜产量不足,必须不断探索新的方法去提高铜的使用率。
我国的铜冶炼技术面临着巨大的挑战,目前炼铜的方法主要有火法炼铜和湿法炼铜两种,但火法炼铜仍是目前铜冶炼主要使用的技术。
本文结合我国铜冶炼行业的现状进行分析,对铜冶炼技术的创新和发展进行探讨。
关键词:铜冶炼;技术发展进步;策略中图分类号:TF811 文献标识码:A 文章编号:1002-5065(2021)14-0015-2Progress and development of copper smelting technology in ChinaCHEN Xiao-jun(Xinjiang Wuxin Copper Co., Ltd., Changji 831100, China)Abstract: With the continuous development of China's social economy, China has gradually grown into a large industrial production country. With the rapid development of heavy industry, the demand for copper is also increasing, and China's copper smelting industry is also developing. Copper is an important transition metal element. It can react with a variety of compounds and is widely used in weapons and decorative articles. At present, the output of copper in our country is insufficient, so we must constantly explore new methods to improve the utilization rate of copper. China's copper smelting technology is facing great challenges. At present, there are two main copper smelting methods: pyrometallurgy and hydrometallurgy, but pyrometallurgy is still the main copper smelting technology. This paper analyzes the current situation of China's copper smelting industry, and discusses the innovation and development of copper smelting technology.Keywords: copper smelting; Technological development and progress; strategy随着世界经济的不断发展,全球化的步伐越来越快。
铜冶炼工艺(3篇)

第1篇一、引言铜是人类历史上最早使用的金属之一,具有优良的导电性、导热性、耐腐蚀性和可塑性。
随着科技的进步和工业的发展,铜在各个领域的应用越来越广泛。
铜冶炼工艺是指从铜矿石中提取铜金属的一系列物理和化学过程。
本文将详细介绍铜冶炼工艺的原理、流程以及主要设备。
二、铜矿石的类型铜矿石主要分为两大类:硫化铜矿石和氧化铜矿石。
硫化铜矿石主要含有黄铜矿(CuFeS2)、辉铜矿(Cu2S)等硫化物,氧化铜矿石主要含有赤铜矿(Cu2O)、孔雀石(CuCO3·Cu(OH)2)等氧化物。
三、铜冶炼工艺流程1. 铜矿石破碎与磨矿铜矿石破碎与磨矿是将铜矿石从原生矿石中分离出来的第一步。
通过破碎机将矿石破碎成一定粒度,再通过磨矿机将矿石磨成细粉,以利于后续的浮选和冶炼。
2. 浮选浮选是将铜矿石中的硫化物和氧化物进行分离的过程。
将磨好的矿石加入浮选剂,通过调整pH值和搅拌,使硫化物与水形成泡沫,从而实现铜矿物与其他矿物的分离。
3. 精选精选是将浮选得到的铜精矿进行进一步处理,以提高铜的品位。
精选方法有火法精选、湿法精选等。
4. 炼铜炼铜是将精选后的铜精矿进行熔炼,提取铜金属。
炼铜方法主要有火法炼铜、湿法炼铜等。
(1)火法炼铜火法炼铜是将铜精矿在高温下进行熔炼,使铜与硫反应生成硫化铜,然后通过吹炼氧化硫化铜,使铜转化为氧化铜。
火法炼铜主要包括熔炼、吹炼、精炼等过程。
熔炼:将铜精矿加入熔炼炉中,加入助熔剂(如石灰石)和燃料(如焦炭),在高温下熔炼,使铜精矿中的硫化物转化为硫化铜。
吹炼:将熔炼得到的熔融硫化铜吹入转炉中,通过吹入空气,使硫化铜氧化成氧化铜,同时将硫氧化成二氧化硫气体排出。
精炼:将吹炼得到的氧化铜熔融,加入氧化剂(如氧气)和还原剂(如碳),使氧化铜还原成铜金属,同时将杂质氧化去除。
(2)湿法炼铜湿法炼铜是将铜精矿经过溶解、氧化、结晶等过程,提取铜金属。
湿法炼铜主要包括浸出、氧化、结晶、电解等过程。
浸出:将铜精矿加入浸出槽中,加入浸出剂(如硫酸、硝酸)和氧化剂(如氧气、空气),使铜精矿中的铜溶解于浸出剂中。
夏朝的冶金技术古代冶炼与铸造的工艺突破
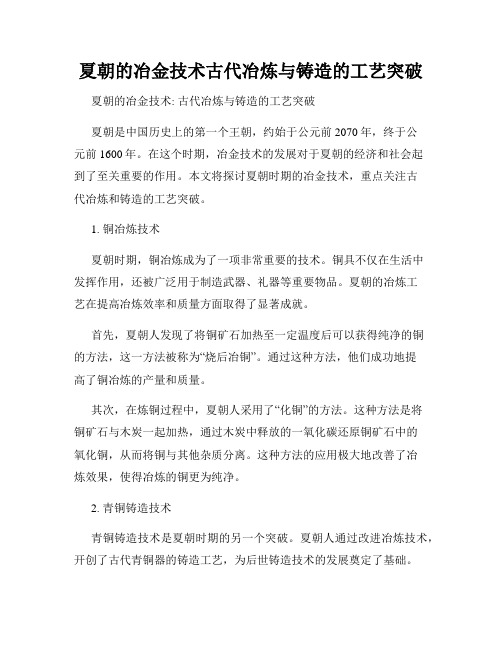
夏朝的冶金技术古代冶炼与铸造的工艺突破夏朝的冶金技术: 古代冶炼与铸造的工艺突破夏朝是中国历史上的第一个王朝,约始于公元前2070年,终于公元前1600年。
在这个时期,冶金技术的发展对于夏朝的经济和社会起到了至关重要的作用。
本文将探讨夏朝时期的冶金技术,重点关注古代冶炼和铸造的工艺突破。
1. 铜冶炼技术夏朝时期,铜冶炼成为了一项非常重要的技术。
铜具不仅在生活中发挥作用,还被广泛用于制造武器、礼器等重要物品。
夏朝的冶炼工艺在提高冶炼效率和质量方面取得了显著成就。
首先,夏朝人发现了将铜矿石加热至一定温度后可以获得纯净的铜的方法,这一方法被称为“烧后冶铜”。
通过这种方法,他们成功地提高了铜冶炼的产量和质量。
其次,在炼铜过程中,夏朝人采用了“化铜”的方法。
这种方法是将铜矿石与木炭一起加热,通过木炭中释放的一氧化碳还原铜矿石中的氧化铜,从而将铜与其他杂质分离。
这种方法的应用极大地改善了冶炼效果,使得冶炼的铜更为纯净。
2. 青铜铸造技术青铜铸造技术是夏朝时期的另一个突破。
夏朝人通过改进冶炼技术,开创了古代青铜器的铸造工艺,为后世铸造技术的发展奠定了基础。
在夏朝时期,青铜器的制作工艺经历了从单一铸造到多种复合工艺的转变。
初期的青铜器多是以铸铁为主,铸造方法相对简单。
然而,随着冶炼技术的发展,夏朝人逐渐掌握了铜和锡的合金比例,使得铸造更加精细。
此外,夏朝时期的铸造技术还涉及到砂型铸造的应用。
夏朝人使用砂质材料制作模具,将熔化的青铜倒入模具中进行铸造。
这一工艺的应用使得铸造过程更为灵活,为制作更复杂的青铜器提供了可能。
3. 对社会经济的影响夏朝的冶金技术突破不仅对工艺领域产生了重要的影响,也对当时的经济和社会发展起到了积极的推动作用。
首先,冶金技术的进步提高了生产力水平。
稳定的铜冶炼和青铜铸造工艺为生产工具的制造提供了基础,促进了农业生产和手工业的发展。
由于夏朝人能够制造更多更高质量的农具和生活用具,农田耕作效率得到了提高,人民生活质量也得到了改善。
废杂铜冶炼工艺及发展趋势
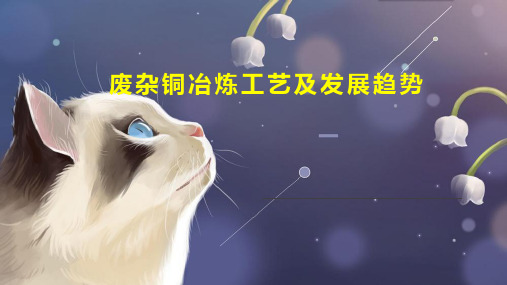
本研究创新点
本研究通过设计和实施一个全面的废杂铜冶炼过程污染物迁移转化实验,旨在 深入探讨污染物之间的相互转化机制及其影响因素。同时,结合现代分析技术 和数值模拟方法,对冶炼过程中的污染物排放进行精准预测与评估,为优化污 染控制策略提供科学依据。
研究方法
本研究采用实验模拟与数值模拟相结合的方法进行。首先,设计不同工艺参数 下的废杂铜冶炼实验,收集各工况下的烟气、废水和固体废物样本。其次,利 用ICP-AES、GC-MS等现代分析技术对样本中的污染物成分进行定性与定量分 析。最后,结合实验数据,运用CDE(Coupled Discrete Element)模型对 废杂铜冶炼过程中的污染物迁移转化进行数值模拟,以揭示各因素对污染物排 放的影响规律。
2、控制反应条件:冶金炉可以提供适当的化学环境,例如控制炉内气氛(氧 气、氮气等),以促进或抑制某些化学反应。
3、分离和纯化金属:通过冶金炉内的熔炼和精炼过程,可以有效地分离和纯 化金属铜,去除其中的杂质。
4、提高能源效率:冶金炉通常使用燃料(如煤、石油或天然气)作为热源, 这些燃料在炉内燃烧产生的热量被有效利用,提高了能源效率。
2、湿法冶炼技术:该技术主要采用化学还原剂将铜从废杂铜中还原出来。在 浸出过程中,加入酸或碱将废杂铜中的金属溶解出来,再通过置换反应得到金 属铜。湿法冶炼技术具有环保性能好、金属回收率高等优点,但生产成本较高 且对技术要求严格。未来,应进一步探索低成本、高效率的湿法冶炼技术,并 加强自动化技术的应用。
结论
本次演示通过对废杂铜冶炼过程中污染物迁移转化规律的研究,揭示了各因素 对污染物排放的影响规律及其相互转化机制。研究结果对于制定全过程污染控 制策略,优化废杂铜冶炼工艺具有重要指导意义。然而,本研究仍存在一定的 局限性,例如实验样本的代表性不足和数值模型简化等。
2024年铜冶炼市场分析现状

铜冶炼市场分析现状引言铜冶炼是一项重要的金属冶炼工艺,旨在从铜矿石中提取纯铜。
铜作为一种重要的工业金属,在建筑、电气、交通等众多领域有广泛应用。
本文将对铜冶炼市场的现状进行深入分析。
市场规模根据国际铜研究小组(ICSG)的数据,铜冶炼市场在过去几年中保持了稳定的增长。
2019年,全球铜冶炼产量为约20,000万吨,而2020年则达到了25,000万吨。
这一增长主要得益于中国和印度等新兴市场的快速发展以及电子和电气设备行业的增长。
市场发展趋势1. 新兴市场需求增长中国和印度等新兴市场的快速发展推动了铜冶炼市场的增长。
随着这些地区的城市化进程加快,对建筑和基础设施的需求不断增长,增加了对铜冶炼产品的需求。
2. 电动汽车行业的崛起随着电动汽车行业的迅速崛起,对铜的需求也大幅增加。
电动汽车的电动驱动系统中广泛使用铜线和铜箔,这进一步推动了铜冶炼市场的发展。
3. 可持续发展趋势环保和可持续发展已经成为全球范围内的关注焦点。
铜冶炼行业也面临着减少环境影响的压力。
为了适应市场需求,许多企业开始采用更环保的生产技术和设备,以减少废水、废气和固体废弃物的排放。
竞争格局目前,全球铜冶炼行业呈现出较高的集中度。
少数大型企业占据着市场的主要份额。
其中,智利的国际铜业公司(Codelco)是全球最大的铜冶炼企业,其占据了全球约10%的市场份额。
此外,美国的自由港麦克莱根(Freeport-McMoRan)和中国的江西铜业也是该行业的重要参与者。
市场挑战1. 高成本铜冶炼面临着原材料和能源成本上涨的挑战。
铜矿石的供应量有限,且越来越难以开采,这导致铜矿石价格上涨。
同时,能源价格的不断上涨也增加了铜冶炼的成本。
2. 环境压力随着环境保护意识的提高,铜冶炼企业面临着减少排放和处理废物的要求。
这需要企业进行技术升级和投资,增加了企业的运营成本。
展望未来尽管铜冶炼市场面临一些挑战,但其前景依然广阔。
随着全球新兴市场的快速发展和电动汽车行业的崛起,对铜的需求将持续增长。
铜冶炼的工艺与应用
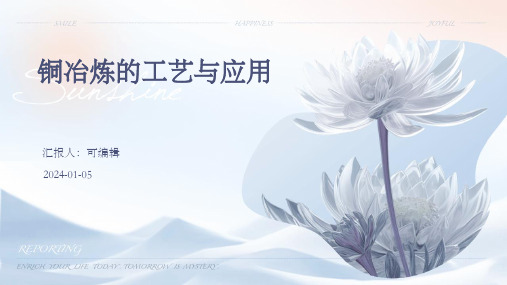
铜冶炼的技术发展
环保要求
随着环保要求的提高,铜冶炼技术不 断向绿色化、低碳化方向发展,如采 用低品位矿石、提高资源利用率、降 低能耗和减少污染物排放等。
智能化控制
随着信息技术的发展,铜冶炼技术不 断向智能化方向发展,如采用自动化 设备、物联网技术、大数据分析等手 段提高生产效率和产品质量。
02
铜冶炼的工艺流程
还原过程
在高温还原气氛下,氧化亚铜被还原为金属铜。
烟气处理
氧化和还原过程中产生的烟气需经过处理,以减 少对环境的污染。
粗铜的熔炼
01
02
03
粗铜的配料与混合
熔炼所需的原料需经过精 确配料和混合,以确保熔 炼过程的稳定性和产品质 量。
熔炼过程
将原料加入熔炼炉中,在 高温下将粗铜熔化并与其 他杂质分离。
铜冶炼的基本原理基于化学反应和物 理变化,包括氧化还原反应、沉淀反 应、溶解与结晶等。
铜冶炼的主要方法
火法冶炼
将铜矿石在高温下进行熔炼,使 铜元素从矿石中还原出来,主要 采用闪速熔炼、熔池熔炼等方法 。
湿法冶金
利用酸、碱、盐等化学溶剂溶解 矿石,通过化学反应将铜元素从 矿石中提取出来,主要采用浸出 、萃取、电积等方法。
减少废弃物排放
通过改进工艺和设备,降低铜冶炼过程中的废弃物排放量,减轻 对环境的压力。
废弃物资源化利用
对铜冶炼过程中产生的废弃物进行资源化利用,如回收有价金属、 制备建筑材料等。
节能减排
推广节能技术和设备,降低铜冶炼过程中的能耗和污染物排放量, 实现绿色生产。
发展新型铜冶炼技术
探索新型冶炼工艺
01
固体废弃物的处理与利用
总结词
铜冶炼过程中产生的固体废弃物主要包括炉渣、污泥和 废石等,这些废弃物需要得到妥善处理与利用。
铜冶炼工艺及其应用
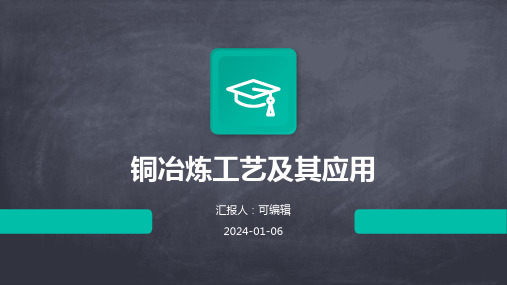
硫酸与其它副产品
要点一
硫酸
铜冶炼过程中产生的副产品,可用于生产化肥、农药、化 工原料等。
要点二
其他副产品
如烟尘、炉渣等,可进一步回收利用或进行环保处理。
副产品的综合利用
烟尘回收
通过回收烟尘中的有价金属,如 金、银、钴等,实现资源再利用
。
炉渣处理
将炉渣进行再加工,提取其中的有 价组分,如铁、锌等,降低环境污 染。
铜精矿的品质
高品质的铜精矿含铜量高,杂质元素 少,能够提高铜冶炼的效率,降低能 耗和污染。
燃料的选择与利用
燃料种类
铜冶炼过程中常用的燃料包括煤炭、天然气和重油等,不同燃料对铜冶炼工艺 和能耗有不同的影响。
燃料利用
合理选择和利用燃料,可以提高燃料的燃烧效率,减少能源浪费和污染排放。
原料的预处理与配料
铜在建筑行业的应用
管道系统
铜管具有优良的耐腐蚀性和延展性,常用于建筑管道系统,如冷热水管、空调管道等。
建筑装饰
铜板、铜条等铜制品可用于建筑内外装饰,提高建筑的美观度和质感。
铜在交通行业的应用
汽车零部件
铜在汽车零部件制造中广泛应用,如发动机 、刹车系统等,能够提高汽车的安全性和性 能。
铁路电气化
铜是铁路电气化工程中的主要材料之一,用 于制造接触网、电线等。
原料预处理
为了提高铜精矿的冶炼效果,需要对 原料进行破碎、磨细、干燥等预处理 ,以调整原料的粒度和水分等指标。
配料工艺
根据不同的冶炼工艺和原料品质,需 要进行配料调整,以获得最佳的冶炼 效果和经济效益。
03
铜冶炼的设备与设施
Chapter
熔炼炉与精炼炉
熔炼炉
熔炼炉是铜冶炼过程中的主要设备之一,用于将铜 矿石、硫化铜矿等含铜物料熔炼成粗铜。熔炼炉通 常分为鼓风炉、反射炉和电炉等类型,根据不同的 原料和生产条件选择合适的熔炼炉。
铜冶炼 工艺

铜冶炼工艺铜是我国文化遗产中使用最广泛的金属之一,其在人类历史中应用已有数千年的历史。
目前,铜的产量约占全球金属产量的 1/3 左右,其中矿石铜约占产量的 70% 左右,废铜约占 30% 左右。
铜的优良性能使得它得到广泛应用,例如用于电线、管道、制酸、制造自行车、汽车、火车、飞机、船舶、家电等设备和机械件等。
铜的产量与品质受到各种因素的影响,其中最关键的因素之一就是铜的冶炼技术和生产工艺。
铜的冶炼工艺可以分为多个阶段,通常包括挖掘矿石、粉碎、选矿、冶炼、炼铜,铜的产量和质量取决于每个阶段的技术和工艺。
铜矿通常以硫化矿的形式存在于地下,其含量一般在 2%-3% 左右。
因此在冶炼铜之前需要将地下矿石挖掘出来。
首先需要在地面上建造一系列金属结构,例如运输带、露天开采设备和排水设备等,以便将挖掘出来的矿石从地下输送到地面上进行处理。
在挖掘出来的矿石经过初步分选和粉碎之后,需要对其进行选矿处理,以去除掉非铜矿物和其他杂质,获得含铜较多的矿石。
选矿可采用不同的方法,其中包括重砂选、气浮选、泡沫浮选等方法。
这些方法的目的是通过物理和化学方式,将含铜矿石从其他矿物中分离出来。
选矿过程中获得的含铜矿石经过多次粉碎和筛选之后,需要将其送进冶炼炉中。
常用的冶金炉有三种类型:闪速炉、电炉和转炉。
闪速炉是最常见的冶炼设备,它不仅可以冶炼铜,还可以冶炼其他金属。
炉内需要加入大量的煤和氧气,以便将炉内铜矿石加热到足够高的温度,使铜矿石中的铜被氧化并变成铜氧化物。
这个过程中需添加熔剂来降低熔点,加速熔化,一般使用碳包裹铝的方案来达到此目的。
接下来,铜氧化物与硫化物反应,产生了二氧化硫和铜。
这个过程是一个放热反应,因此需要控制炉子的温度和通入氧气的量,以避免产生过量的二氧化硫和产生副产物。
冶炼完成后,铜和其他杂质分离,生成高纯度铜。
高纯度铜的生产过程中涉及到多个工艺,依次包括冷却、烧结、电解和精炼等步骤。
冷却和烧结是将铜矿石熔化之后冷却,形成固态块状的铜的过程。
铜冶炼的主要工艺
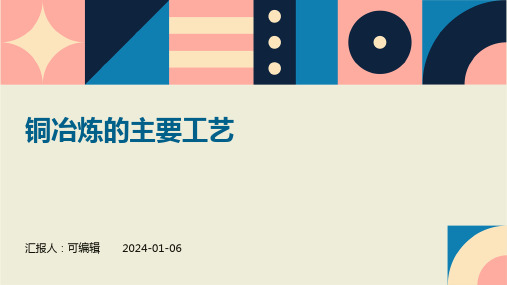
04
铜冶炼的环境影响与处理措施
大气污染
铜冶炼过程中会产生大量的烟尘和废气,主要成分包括二 氧化硫、氮氧化物、颗粒物等。这些污染物不仅对人体健 康有害,还会对大气环境造成严重污染。
处理措施:采用高效烟气治理技术,如湿法脱硫、活性炭 吸附、布袋除尘等,对烟气进行净化处理,减少污染物排 放。同时,加强生产过程的密闭性和自动化程度,降低无 组织排放。
精矿经过熔炼、吹炼、精炼等 化学反应过程,将铜从硫化物 状态转化为单质状态,并除去 杂质元素。
精炼后的铜通过浇铸或轧制等 方法制成各种规格的铜材。
02
铜冶炼的原料
铜精矿
铜精矿是铜冶炼的主要原料,是从铜矿中开采出来的原矿经过选矿、破碎、磨细等 工序后得到的含铜量较高的矿粉。
铜精矿中铜的含量一般在20%左右,同时含有其他的有价元素,如金、银、钴、镍 等。
05
铜冶炼的未来发展趋势与挑战
提高资源利用率
01
02
03
强化矿石品位
通过提高矿石品位,减少 杂质元素,提高铜金属的 回收率。
优化选矿工艺
采用先进的选矿技术和设 备,提高有价金属的回收 率,降低尾矿损失。
强化冶炼过程控制
通过精确控制金属的提取率 和回收率。
生物冶金技术
利用微生物资源进行铜的提取和分离,具有环保 、低能耗等优势。
非传统冶炼技术
研究开发非传统冶炼技术,如等离子体熔炼、电 化学沉积等,提高铜金属的提取率和回收率。
THANKS
感谢观看
铜冶炼的重要性
铜是一种重要的工业原料,广泛应用于电气、建筑、制造、 交通运输等领域,因此铜冶炼是保障铜材供应的重要环节。
铜冶炼工艺介绍
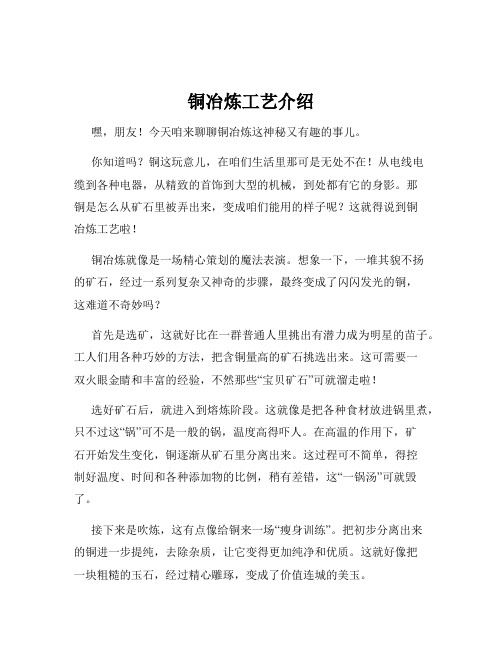
铜冶炼工艺介绍嘿,朋友!今天咱来聊聊铜冶炼这神秘又有趣的事儿。
你知道吗?铜这玩意儿,在咱们生活里那可是无处不在!从电线电缆到各种电器,从精致的首饰到大型的机械,到处都有它的身影。
那铜是怎么从矿石里被弄出来,变成咱们能用的样子呢?这就得说到铜冶炼工艺啦!铜冶炼就像是一场精心策划的魔法表演。
想象一下,一堆其貌不扬的矿石,经过一系列复杂又神奇的步骤,最终变成了闪闪发光的铜,这难道不奇妙吗?首先是选矿,这就好比在一群普通人里挑出有潜力成为明星的苗子。
工人们用各种巧妙的方法,把含铜量高的矿石挑选出来。
这可需要一双火眼金睛和丰富的经验,不然那些“宝贝矿石”可就溜走啦!选好矿石后,就进入到熔炼阶段。
这就像是把各种食材放进锅里煮,只不过这“锅”可不是一般的锅,温度高得吓人。
在高温的作用下,矿石开始发生变化,铜逐渐从矿石里分离出来。
这过程可不简单,得控制好温度、时间和各种添加物的比例,稍有差错,这“一锅汤”可就毁了。
接下来是吹炼,这有点像给铜来一场“瘦身训练”。
把初步分离出来的铜进一步提纯,去除杂质,让它变得更加纯净和优质。
这就好像把一块粗糙的玉石,经过精心雕琢,变成了价值连城的美玉。
然后是精炼,这可是铜冶炼的“重头戏”。
通过电解等方法,让铜的纯度达到极高的水平。
这时候的铜,就像是经过严格训练的运动员,状态绝佳,准备在各个领域大显身手。
在整个铜冶炼的过程中,每一个环节都至关重要。
就像一场接力赛,每一棒都要跑得又快又稳,才能最终赢得胜利。
如果有一个环节出了问题,那整个过程都可能前功尽弃。
而且,铜冶炼可不只是技术活,还得考虑环保问题。
可不能为了得到铜,把咱们的环境弄得乌烟瘴气。
这就像做饭不能把厨房弄得乱七八糟,得收拾干净一样。
所以说啊,铜冶炼工艺既是一门技术,也是一门艺术。
它需要精湛的技艺,严谨的态度,还得有环保的意识。
只有这样,咱们才能源源不断地得到高质量的铜,让它为咱们的生活增光添彩。
怎么样,朋友,是不是觉得铜冶炼很神奇呢?。
国内外铜精矿先进铜冶炼工艺技术综述
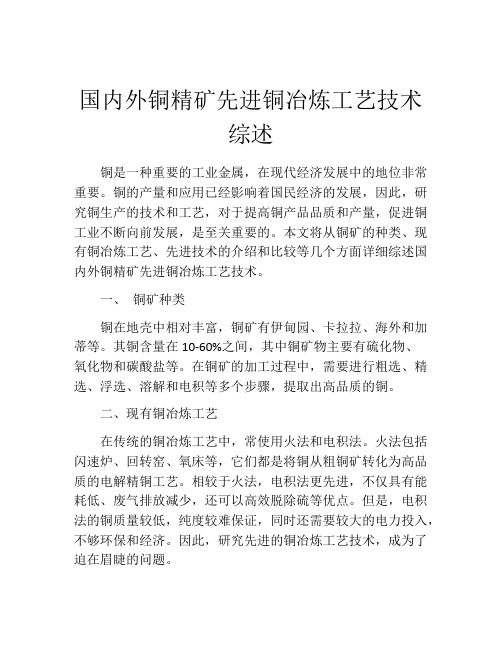
国内外铜精矿先进铜冶炼工艺技术综述铜是一种重要的工业金属,在现代经济发展中的地位非常重要。
铜的产量和应用已经影响着国民经济的发展,因此,研究铜生产的技术和工艺,对于提高铜产品品质和产量,促进铜工业不断向前发展,是至关重要的。
本文将从铜矿的种类、现有铜冶炼工艺、先进技术的介绍和比较等几个方面详细综述国内外铜精矿先进铜冶炼工艺技术。
一、铜矿种类铜在地壳中相对丰富,铜矿有伊甸园、卡拉拉、海外和加蒂等。
其铜含量在10-60%之间,其中铜矿物主要有硫化物、氧化物和碳酸盐等。
在铜矿的加工过程中,需要进行粗选、精选、浮选、溶解和电积等多个步骤,提取出高品质的铜。
二、现有铜冶炼工艺在传统的铜冶炼工艺中,常使用火法和电积法。
火法包括闪速炉、回转窑、氧床等,它们都是将铜从粗铜矿转化为高品质的电解精铜工艺。
相较于火法,电积法更先进,不仅具有能耗低、废气排放减少,还可以高效脱除硫等优点。
但是,电积法的铜质量较低,纯度较难保证,同时还需要较大的电力投入,不够环保和经济。
因此,研究先进的铜冶炼工艺技术,成为了迫在眉睫的问题。
三、先进技术介绍和比较1、溶浸法技术溶浸法是一种绿色的铜冶炼技术,该技术将铜精矿和酸浸剂反应,产生硫酸铜浸液,然后通过萃取将其转化为纯度高的铜产品。
与火法和电积法相比,溶浸法更加环保,而且能有效地提高铜品质。
同时,经过处理的溶液中可以回收多种金属,实现资源化利用。
不足之处在于,铜矿中的杂质可能会影响到铜的萃取和回收,难以控制生产成本。
2、氧化部分浸出技术氧化部分浸出技术,在我国铜工业的应用尚处于起步阶段。
该技术依靠高温氧化氯化物来将铜氧化,溶解出铜盐浸液,然后通过补充高牛顿液和硫酸等,使铜再降级氧化还原反应中不停地迁移,最终得到纯度较高的铜。
这种技术还可以回收水溶性铜、锌、贵金属等,具有较好的经济和环保性能。
但是,该技术需要较高的温度和氧化剂投入,会消耗较大的能源。
3、氧化整浸技术氧化整浸技术属于特种化学浸出方法,它能够够充分利用硫化型铜矿中的微生物进行矿石反应。
铜冶炼工艺介绍全解

铜冶炼工艺介绍全解
首先是选矿阶段。
在选矿过程中,首先需要对矿石进行破碎和磨矿,以便更好地释放有价金属和非有价金属,并提供给后续工艺中的分选和浸出等步骤使用。
破碎和磨矿过程中要选择适当的设备和操作参数,以保证矿石颗粒大小的合理分布。
接下来是浸出阶段。
铜矿石中的铜一般以硫化铜的形式存在,所以在浸出过程中,一般采用浸出法将硫化铜转化为可溶性的铜离子。
常用的浸出法有硫酸浸出法、氨浸出法和酸氢氧化法等。
通过浸出,可将铜矿石中的铜分离出来,并转化为铜离子。
然后是溶液处理阶段。
通过浸出法得到的铜离子溶液通常含有其他金属离子和杂质离子。
为了提高铜的纯度,需要对溶液进行一系列的处理工艺,如中和、沉淀、反应离子交换等。
这些工艺可以将溶液中的其他金属和杂质离子去除,使铜的含量得到进一步提高。
接下来是电镀阶段。
通过电镀法,将溶液中的铜离子电解沉积在阴极上,得到纯铜。
电镀是铜冶炼中的一种常用工艺,可获得纯度较高的铜金属。
最后是熔炼阶段。
在熔炼过程中,将电镀得到的纯铜或其他含铜物料经过高温熔炼,除去杂质和有害物质,得到高纯度的铜金属。
熔炼过程中需要控制温度和气氛,以确保铜金属的纯度和质量。
总的来说,铜冶炼工艺包括选矿、浸出、溶液处理、电镀和熔炼等阶段。
每个阶段都有其特定的工艺和设备要求,通过一系列的处理和操作,可将铜矿石中的铜分离出来,并转化为纯度较高的铜金属。
铜冶炼工艺的优化和改进对于提高铜的冶炼效率和纯度具有重要意义。
- 1、下载文档前请自行甄别文档内容的完整性,平台不提供额外的编辑、内容补充、找答案等附加服务。
- 2、"仅部分预览"的文档,不可在线预览部分如存在完整性等问题,可反馈申请退款(可完整预览的文档不适用该条件!)。
- 3、如文档侵犯您的权益,请联系客服反馈,我们会尽快为您处理(人工客服工作时间:9:00-18:30)。
铜冶炼水平与工艺水平1)火法冶炼工艺当前,全球矿铜产量的75%-80%是以硫化形态存在的矿物经开采、浮选得到的铜精矿为原料,火法炼铜是生产铜的主要方法,特别是硫化铜精矿,基本全部采用火法冶炼工艺。
火法处理硫化铜精矿的主要优点是适应性强,冶炼速度快,能充分利用硫化矿中的硫,能耗低。
其生产过程一般由以下几个工序组成:备料、熔炼、吹炼、火法精炼、电解精炼,最终产品为电解铜。
原料制备工序:将铜精矿、燃料、熔剂等物料进行预处理,使之符合不同冶炼工艺的需要。
熔炼工序:通过不同的熔炼方法,对铜精矿造硫熔炼,炼成含铜、硫、铁及贵金属的冰铜,使之与杂质炉渣分离;补出的含二氧化硫烟气经收尘后用于制造硫酸或其他硫制品,烟尘返回熔炼炉处理。
吹炼工序:除去冰铜中的硫铁,形成含铜及贵金属的粗铜,炉渣和烟尘返回上一工序处理。
火法精炼工序:将粗铜中硫等杂质进一步去除,浇铸出符合电解需要的阳极板。
电解精炼工序:除去杂质,进一步提纯,生产出符合标准的阴极铜成品,并把金银等贵金属富集在阳极泥中。
传统熔炼方法如鼓风炉熔炼、反射炉熔炼和电炉熔炼,由于效率低、能耗高、环境污染严重而逐渐被新的富氧强化熔炼工艺所代替[[3]新的富氧强化熔炼可分为闪速熔炼和熔池熔炼两大类,前者包括奥托昆普型闪速熔炼和加拿大国际镍公司闪速熔炼等,后者包括诺兰达法、三菱法、艾萨法、奥斯麦特法和瓦纽可夫法以及我国自主开发的水口山法、白银炉熔炼、金峰炉熔炼等技术。
铜锍吹炼方法有传统的卧式转炉、连续吹炼炉、虹吸式转炉。
新型吹炼技术包括艾萨吹炼炉、三菱吹炼炉和闪速吹炼炉等。
粗铜的火法精炼在阳极炉内进行,对于转炉产出的液态粗铜采用回转式阳极炉或固定式反射炉精炼,经氧化、还原等作业进一步脱除粗铜中的铁、铅、锌、砷、锑、铋等杂质,并浇铸成含铜99.2%-99.7%的阳极板。
铜电解工艺有传统电解法、永久阴极电解法和周期反向电流电解法3种。
目前大多数电解铜厂都使用传统电解法,永久阴极电解法和周期反向电流电解法是20世纪70年代以来发展的新技术。
2)熔炼工序(1)富氧强化熔炼工艺富氧强化熔炼工艺是目前铜火法冶炼的主流技术,包括闪速熔炼工艺和熔池熔炼工艺,其中熔池熔炼工艺又分为顶吹、底吹和侧吹工艺。
a.闪速熔炼工艺闪速熔炼的生产过程是用富氧空气或热风,将干精矿喷入专门设计的闪速炉的反应塔,精矿粒子在空间悬浮1-3s时间,与高温氧化性气流迅速发生硫化矿物的氧化反应,并放出大量的热,完成熔炼反应即造锍的过程。
反应的产物落入闪速炉的沉淀池中进行沉降,使铜锍和渣得到进一步的分离。
该工艺技术具有生产能力大、能耗低、污染少等优点,单套系统最大矿铜产能可达40万t/a以上,适用于规模20万t/a以上的工厂。
但是要求原料进行深度干燥到含水<0.3%,精矿粒度<1mm,原料中杂质铅加锌不宜高于6%。
工艺的缺点是设备复杂、烟尘率较高,渣含铜比较高,需要进行贫化处理。
闪速熔炼工艺技术在能效和环保方面的特点:闪速熔炼的铜精矿氧化反应迅速,单位时间内放出的热量多,加快了熔炼速度,使熔炼的生产率大幅度提高,为反射炉与电炉熔炼的两倍。
采用了富氧工艺后,在铜精矿含硫正常情况下可实现自热熔炼,大大降低了燃料的消耗。
由于精矿中硫化物的氧化反应程度高,且采用高浓度的富氧空气熔炼,烟气量少,烟气中的SO2浓度可提高到30%以上,有利于烟气制硫酸过程中硫的回收和环境保护。
闪速法铜冶炼工艺技术为《国家重点行业清洁生产技术导向目录》(第二批)中公布推广的清洁生产技术。
对比闪速炉反应塔的熔炼过程,熔池熔炼也是一个悬浮颗粒与周围介质的热与质的传递过程。
所不同的是,悬浮粒子是处在一个强烈搅动的液一气两相介质中,受液体流动、气体流动及两种流体间的相互作用以及动量交换的影响。
由于熔池熔炼过程的传热与传质效果好,可大大强化冶金过程,达到提高设备生产率和降低冶炼过程能耗的目的,因此,20世纪70年代后熔池熔炼得到了迅速发展。
富氧顶吹熔炼工艺熔炼系统由3个炉b.富氧顶吹熔池熔炼工艺富氧顶吹熔池熔炼工艺是通过喷枪把富氧空气强制鼓入熔池,使熔池产生强烈搅动状态加快了化学反应的速度,充分利用了精矿中的硫、铁氧化放出的热量进行熔炼,同时产出高品位冰铜。
熔炼过程中不足的热量由燃煤和燃油提供。
子组成,即熔炼炉、贫化炉和吹炼炉。
铜精矿、熔剂、返料、燃料煤经配料仓按预定要求计量配料后送制粒机加水制粒,以含水9%-10%的勃团料方式,由加料皮带从炉子顶加料口投入炉内。
经过制粒混有燃料煤的混合铜精矿,一旦粒料加入熔融层,粒料中水分马上就挥发掉,粒料变成粉末与冰铜和渣激烈地搅动并进行反应,形成一个气、固、液三相快速的传质传热,熔炼炉就变成一个高速的反应器。
熔炼需要的富氧空气通过喷枪鼓入熔池,为了便于生产期间的温度控制,还可从喷枪加入燃油对炉温进行微调,熔炼产生的冰铜和炉渣混熔体由炉子底部的放铜口(或虹吸硫口)及溜槽放出,进入贫化电炉澄清分离。
熔炼炉含尘烟气经余热锅炉降温和粗收尘后(其中余热锅炉部分豁结烟尘在锅炉的振打作用和重力影响下回到熔炼炉)进入电收尘器进一步除尘,出口烟气进入硫酸厂制酸。
余热锅炉收下的烟尘返配料系统,电收尘器收下的烟尘实现开路单独处理,贫化炉渣定期水淬。
冰铜分批送吹炼炉吹炼成粗铜:吹炼渣返贫化炉或水淬,水淬渣返回熔炼配料,粗铜进精炼炉。
吹炼炉烟气与熔炼一样,经余热锅炉、电收尘后,与熔炼炉净化烟气合并一起送硫酸车间制酸。
目前主要富氧顶吹熔炼工艺为奥斯迈特炉和艾萨炉熔炼技术。
富氧顶吹熔炼工艺具有以下特点:熔炼速度快,生产率高。
其中,艾萨炉用于铜精矿熔炼,床能力最高已达238t/(m2·d),一般达到190.8t/(m2·d),是目前炼铜方法中床能力最高的一种。
这种炉子在提高富氧浓度时,生产能力可以成倍增加。
年产10万t/a的工厂与年产20万t/a的工厂在炉子直径和高度上变化不大,只是富氧浓度不同。
系统建设投资少,生产费用低。
由于处理能力大,炉子结构简单,因此,建设速度快,投资少。
建设一座顶吹浸没炉的投资,一般只有相同规模的闪速熔炼炉投资的60%-70%。
原料的适应性强,可处理铜精矿、大块含铜原料,含铜电子废料等。
原料制备简单,铜精矿原料不需要经过特别准备,将含水量小于10%的精矿制成颗粒或混捏后直接入炉。
操作简便,自动化程度高,生产过程用计算机在线控制1台炉子,每班仅需要4-6名操作人员。
燃料适应性广,喷枪可以使用粉煤、碳粉、油和天然气,燃料调节比大。
有良好的劳动卫生条件,除喷枪口和加料口外,熔炼炉为密闭式生产,烟气外排少。
熔池熔炼过程是负压进行,余热锅炉和电收尘密封好,冶炼烟气不会外溢,烟气中的SO2浓度稳定且含量高,有利于烟气制硫酸过程中硫的回收和环境保护。
c.富氧侧吹熔炼工艺富氧侧吹熔池熔炼的生产过程是通过侧吹炉两侧的风口向炉内鼓入富氧压缩空气,在富氧压缩空气的作用下,熔体在侧吹炉内形成剧烈搅拌,由炉顶加入混矿,通过炉气干燥后,在熔体内形成气一液一固三相间的传质、传热过程,完成造渣、造锍反应,形成的渣锍共熔体在贫化前床内澄清分离,得到水淬渣和冰铜。
形成的高温烟气经余热锅炉生产蒸汽,烟气送制酸。
该工艺技术具有效率高、能耗低、对原料的适应性强、处理能力大、环保、操作简单、投资少等优点。
单台熔炼炉的粗铜产能可达15万t/a。
富氧侧吹熔池熔炼是一种富氧强化炼铜工艺,这就使得熔炼炉烟气量大大减少,提高了熔炼炉的热效率。
由于可以充分利用熔炼的反应热,大大减少了燃料消耗。
熔炼烟气SO2浓度8%-14%,有利于采用二转二吸技术制酸,硫的总捕集率达到98.45%。
d.氧气底吹熔炼工艺该工艺技术为我国自主开发的铜熔炼工艺技术。
混合矿料不需要干燥、磨细,配料后由皮带传输,连续从炉顶加料口加入炉内的高温熔池中,氧气和空气通过底部氧枪连续送入炉内的铜流层,氧气以大量的小气泡动态的悬浮于熔体中,有很大的气一液相接触面积,有极好的反应动力学条件,连续加入的铜精矿不断地被迅速氧化、造渣。
硫生成的二氧化硫烟气从炉子的排烟口连续地进入余热锅炉,经电收尘后制酸处理。
炉内形成的炉渣从底部定期放出,由渣包吊运至缓冷场,缓冷后进行渣选矿。
形成的铜锍从侧面放锍口定期放出,由铜毓包吊运到P-S转炉吹炼。
工艺特点:工艺过程简单、原料适应性强、能源消耗低、投资相对省、噪声低、操作环境好、劳动强度低、容易掌握和操作,产能规模在5万-25万t/a。
底吹熔炼技术最显著的特点就是能耗低、环保好:由于氧浓度高(富氧空气氧浓度可达75%),因而排出烟气量小,热损失少,反应强度高,因此很容易实现无碳自热熔炼,炉料中不需要另外配煤,节省了燃料以及煤燃烧所用的氧气,保证了氧气的充分有效利用,能耗很低。
该技术整套系统采用较高负压操作且密封性好,无烟气外溢现象,无低空污染。
(2)密闭鼓风炉熔炼工艺鼓风炉熔炼工艺是一种历史悠久的冶炼方法。
由于这种工艺能耗较高,熔炼烟气SO2浓度低,不宜有效回收,造成对大气的严重污染,所以我国己要求在2007年底以前,全部淘汰该冶炼工艺。
3)吹炼工序(1)P-S转炉吹炼技术1905年Peirce和Smith成功应用碱性耐火材料内衬卧式吹炼转炉,用于铜的吹炼,近百年来该技术己成为世界上普遍采用的成熟工艺。
转炉的铜锍吹炼过程中,向转炉中连续吹入空气,当熔体中FeS氧化造渣被除去后,炉内仅剩Cu2S (即白冰铜),Cu2S继续吹炼氧化生成Cu2O,Cu2O再与未被氧化的Cu2S发生交互反应获得金属铜。
该工艺成熟可靠,设备和操作简单,投资低,不加燃料吹炼,可用空气和低浓度的富氧空气。
能够利用剩余热量处理工厂中的含铜中间物料(粗铜壳、残阳极、烟尘、冷冰铜等),还能够处理外购的冷杂铜,生产成本低。
该工艺适用范围广,无论生产规模大小,铜锍品位高低均可应用该工艺:P-S转炉吹炼工艺为分周期、间断作业;其缺点是炉体密闭差,漏风大,烟气S02浓度低,设备台数多,物料进出需要吊车装运,低空污染较严重。
(2)闪速吹炼工艺闪速吹炼工艺技术发明于1979年,在奥托昆普闪速熔炼直接生产粗铜的技术基础上发展而成,20世纪80年代中期在美国肯尼柯特应用成功。
闪速吹炼工艺技术是将熔炼炉产出的熔融的铜毓进行水淬,磨细干燥后在闪速炉中用富氧空气进行吹炼得到粗铜,基本原理和工艺过程同闪速熔炼,但是加入的是高品位铜锍,吹炼过程连续作业。
该工艺适用于年产20万t 粗铜以上大规模工厂。
(3)顶吹浸没吹炼工艺顶吹浸没吹炼炉由炉顶加料孔加入干铜毓、熔剂,或底部溶池面上流入铜毓。
富氧空气或空气进行吹炼作业。
吹炼炉喷枪垂直插入固定的炉身,即奥斯迈特炉。
闪速吹炼与闪速熔炼炉搭配使用即双闪工艺,由于该工艺为连续吹炼技术,取消一般吹炼工艺用吊车吊装铜包及渣包等操作,且设备密封性能好,无烟气泄漏,彻底解决铜冶炼行业吹炼工序低空污染问题,大大降低无组织排放造成的SO2和含重金属烟尘污染程度。