如何判断铝合金挤压制品生产难度
铝合金挤压工序中的主要缺陷分析及质量控制方法(DOC)
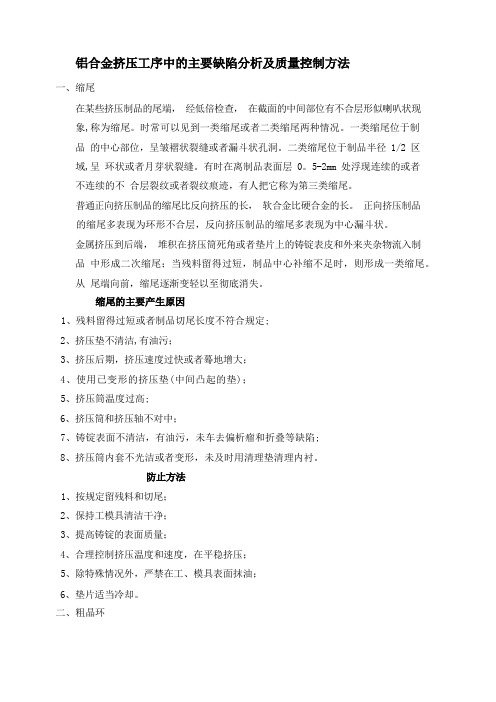
一、缩尾在某些挤压制品的尾端,经低倍检查,在截面的中间部位有不合层形似喇叭状现象,称为缩尾。
时常可以见到一类缩尾或者二类缩尾两种情况。
一类缩尾位于制品的中心部位,呈皱褶状裂缝或者漏斗状孔洞。
二类缩尾位于制品半径 1/2 区域,呈环状或者月芽状裂缝。
有时在离制品表面层 0。
5-2mm 处浮现连续的或者不连续的不合层裂纹或者裂纹痕迹,有人把它称为第三类缩尾。
普通正向挤压制品的缩尾比反向挤压的长,软合金比硬合金的长。
正向挤压制品的缩尾多表现为环形不合层,反向挤压制品的缩尾多表现为中心漏斗状。
金属挤压到后端,堆积在挤压筒死角或者垫片上的铸锭表皮和外来夹杂物流入制品中形成二次缩尾;当残料留得过短,制品中心补缩不足时,则形成一类缩尾。
从尾端向前,缩尾逐渐变轻以至彻底消失。
1、残料留得过短或者制品切尾长度不符合规定;2、挤压垫不清洁,有油污;3、挤压后期,挤压速度过快或者蓦地增大;4、使用已变形的挤压垫(中间凸起的垫);5、挤压筒温度过高;6、挤压筒和挤压轴不对中;7、铸锭表面不清洁,有油污,未车去偏析瘤和折叠等缺陷;8、挤压筒内套不光洁或者变形,未及时用清理垫清理内衬。
1、按规定留残料和切尾;2、保持工模具清洁干净;3、提高铸锭的表面质量;4、合理控制挤压温度和速度,在平稳挤压;5、除特殊情况外,严禁在工、模具表面抹油;6、垫片适当冷却。
二、粗晶环有些铝合金的挤压制品在固溶处理后的低倍试片上,沿制品周边形成粗大再结晶晶粒组织区,称为粗晶环.由于制品外形和加工方式不同,可形成环状、弧状及其他形式的粗晶环。
粗晶环的深度同尾端向前端逐渐减小以至彻底消失。
期形成机理是由热挤压后在制品表层形成的亚晶粒区,加热固溶处理后形成粗大的再结晶晶粒区。
1、挤压变形不均匀‘2、热处理温度过高,保温时间过长,使晶粒长大;3、便金化学成份不合理;4、普通的可热处理强化合金经热处理后都有粗晶环产生,特别是 6A02,2A50 等合金的型、棒材最为严重,不能消除,只能控制在一定范围内 ;5、挤压变形小或者变形不充分,或者处于临界变形范围,易产生粗晶环。
铝及铝合金管材的加工性能及其特征
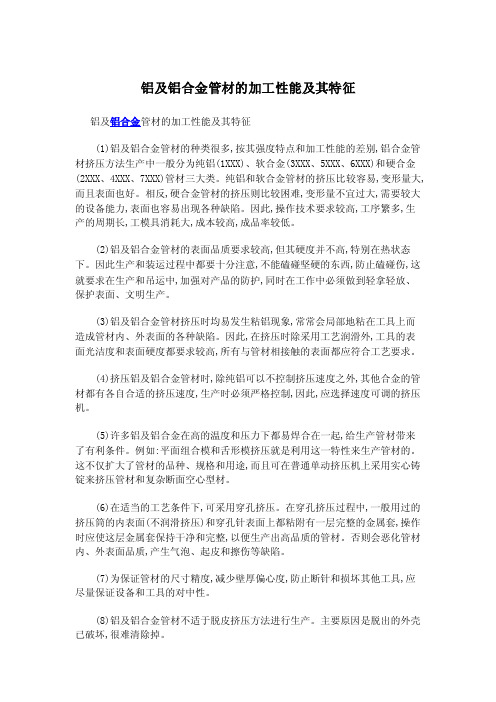
铝及铝合金管材的加工性能及其特征铝及铝合金管材的加工性能及其特征(1)铝及铝合金管材的种类很多,按其强度特点和加工性能的差别,铝合金管材挤压方法生产中一般分为纯铝(1XXX)、软合金(3XXX、5XXX、6XXX)和硬合金(2XXX、4XXX、7XXX)管材三大类。
纯铝和软合金管材的挤压比较容易,变形量大,而且表面也好。
相反,硬合金管材的挤压则比较困难,变形量不宜过大,需要较大的设备能力,表面也容易出现各种缺陷。
因此,操作技术要求较高,工序繁多,生产的周期长,工模具消耗大,成本较高,成品率较低。
(2)铝及铝合金管材的表面品质要求较高,但其硬度并不高,特别在热状态下。
因此生产和装运过程中都要十分注意,不能磕碰坚硬的东西,防止磕碰伤,这就要求在生产和吊运中,加强对产品的防护,同时在工作中必须做到轻拿轻放、保护表面、文明生产。
(3)铝及铝合金管材挤压时均易发生粘铝现象,常常会局部地粘在工具上而造成管材内、外表面的各种缺陷。
因此,在挤压时除采用工艺润滑外,工具的表面光洁度和表面硬度都要求较高,所有与管材相接触的表面都应符合工艺要求。
(4)挤压铝及铝合金管材时,除纯铝可以不控制挤压速度之外,其他合金的管材都有各自合适的挤压速度,生产时必须严格控制,因此,应选择速度可调的挤压机。
(5)许多铝及铝合金在高的温度和压力下都易焊合在一起,给生产管材带来了有利条件。
例如:平面组合模和舌形模挤压就是利用这一特性来生产管材的。
这不仅扩大了管材的品种、规格和用途,而且可在普通单动挤压机上采用实心铸锭来挤压管材和复杂断面空心型材。
(6)在适当的工艺条件下,可采用穿孔挤压。
在穿孔挤压过程中,一般用过的挤压筒的内表面(不润滑挤压)和穿孔针表面上都粘附有一层完整的金属套,操作时应使这层金属套保持干净和完整,以便生产出高品质的管材。
否则会恶化管材内、外表面品质,产生气泡、起皮和擦伤等缺陷。
(7)为保证管材的尺寸精度,减少壁厚偏心度,防止断针和损坏其他工具,应尽量保证设备和工具的对中性。
有难度型材挤压生产控制与影响

力尔铝业股份有限公司 技术部
2015/7/11
30
框料 大面定位
力尔铝业股份有限公司 技术部
2015/7/11
31
框与中梃拼 接 高低差
力尔铝业股份有限公司 技术部
2015/7/11
32
装配尺寸,就是与其它产品需要安装配合的尺寸。 公差,超高精级。 不合格的现象:不能安装;不好安装; 举例:安装角码、角片、压线、盖板、锁条。
力尔铝业股份有限公司 技术部
2015/7/11
26
锯切后,长度不齐
力尔铝业股份有限公司 技术部
2015/7/11
27
力尔铝业股份有限公司 技术部
2015/7/11
28
下料锯 倒“八” 字形锯 大面定位
力尔铝业股份有限公司 技术部
2015/7/11
29
扇 锯切定位图 带圆弧翅内倾,垂直方面 高度减低,造成按原定尺 下料尺寸会短。
2015/7/11
9
与盖板配合 上面的三点 与侧面为配 合点
力尔铝业股份有限公司 技术部
2015/7/11
10
易出现开口尺寸超标。 悬臂大的型材,通常是开口腔深度大于3倍或3倍以 上的开口尺寸。 其原理: 腔体空心部位对应的受力支撑由开口部位金属承担, 开口部位会断裂。
力尔铝业股份有限公司 技术部
2015/7/11
11
开口尺寸29.3 空腔深度 106.5
力尔铝业股份有限公司 技术部
2015/7/11
12
易出现壁厚偏, 有腔体的产品腔体壁厚就易出现壁厚不均。 型材产品的空腔个数过多(5个), 空腔部位对应的模具工头会因模具受力而发生摆动, 从而造成产品的壁厚不均, 一边薄,一边厚。
铝合金挤压速度的限制因素
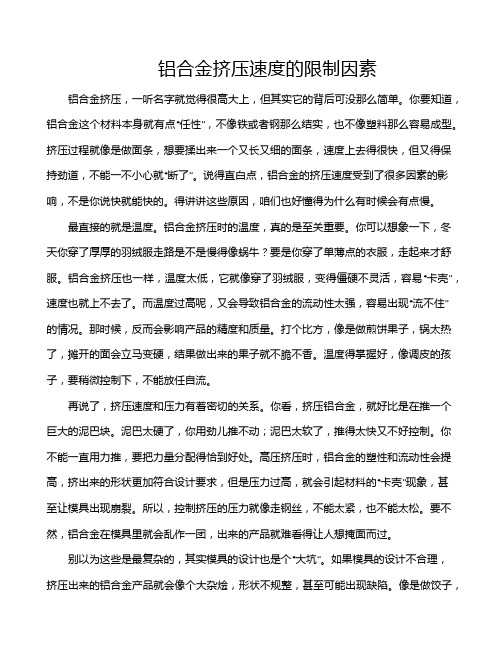
铝合金挤压速度的限制因素铝合金挤压,一听名字就觉得很高大上,但其实它的背后可没那么简单。
你要知道,铝合金这个材料本身就有点“任性”,不像铁或者钢那么结实,也不像塑料那么容易成型。
挤压过程就像是做面条,想要揉出来一个又长又细的面条,速度上去得很快,但又得保持劲道,不能一不小心就“断了”。
说得直白点,铝合金的挤压速度受到了很多因素的影响,不是你说快就能快的。
得讲讲这些原因,咱们也好懂得为什么有时候会有点慢。
最直接的就是温度。
铝合金挤压时的温度,真的是至关重要。
你可以想象一下,冬天你穿了厚厚的羽绒服走路是不是慢得像蜗牛?要是你穿了单薄点的衣服,走起来才舒服。
铝合金挤压也一样,温度太低,它就像穿了羽绒服,变得僵硬不灵活,容易“卡壳”,速度也就上不去了。
而温度过高呢,又会导致铝合金的流动性太强,容易出现“流不住”的情况。
那时候,反而会影响产品的精度和质量。
打个比方,像是做煎饼果子,锅太热了,摊开的面会立马变硬,结果做出来的果子就不脆不香。
温度得掌握好,像调皮的孩子,要稍微控制下,不能放任自流。
再说了,挤压速度和压力有着密切的关系。
你看,挤压铝合金,就好比是在推一个巨大的泥巴块。
泥巴太硬了,你用劲儿推不动;泥巴太软了,推得太快又不好控制。
你不能一直用力推,要把力量分配得恰到好处。
高压挤压时,铝合金的塑性和流动性会提高,挤出来的形状更加符合设计要求,但是压力过高,就会引起材料的“卡壳”现象,甚至让模具出现崩裂。
所以,控制挤压的压力就像走钢丝,不能太紧,也不能太松。
要不然,铝合金在模具里就会乱作一团,出来的产品就难看得让人想掩面而过。
别以为这些是最复杂的,其实模具的设计也是个“大坑”。
如果模具的设计不合理,挤压出来的铝合金产品就会像个大杂烩,形状不规整,甚至可能出现缺陷。
像是做饺子,皮子不均匀,你包进去的馅儿就不匀,最后包出来的饺子就是“金针菇”形状,吃了也不好看。
模具设计得不合适,挤出来的铝合金就容易发生流动不畅,速度也会因此受限。
挤压成型质量评估

有关“挤压成型”的质量评估
有关“挤压成型”的质量评估如下:
1.尺寸精度:挤压成品的尺寸精度是评估其质量的重要指标。
通过测量成品的关键尺寸
并与标准尺寸进行比较,可以确定其尺寸精度是否满足要求。
2.表面质量:挤压成品的表面质量也是评估其质量的重要因素。
表面应光滑、平整,无
明显的划痕、凹陷、气泡等缺陷。
3.机械性能:挤压成品的机械性能是评估其质量的另一个关键指标。
例如,抗拉强度、
屈服强度、延伸率等,这些性能指标可以通过拉伸试验等方法进行测量。
4.内部结构:挤压成品的内部结构也是评估其质量的重要因素。
通过X射线、超声波等
无损检测方法可以检测成品内部的缺陷、不均匀性等。
5.稳定性:挤压成品的生产过程中需要保持稳定的工艺参数,以确保成品质量的稳定。
评估挤压成品的稳定性时,可以对其不同批次之间的质量差异进行比较,并检查工艺参数是否稳定可控。
铝挤压成型的工艺特点及其优缺点分析

铝挤压成型的工艺特点及其优缺点分析首先,铝挤压成型具有高效性。
由于挤压成型是通过挤出机将铝合金材料从模具中挤压出来,整个过程可以实现自动化操作,大大提高了生产效率。
挤压成型速度快,生产速度大大加快,能够满足大批量生产的需求。
其次,铝挤压成型具有灵活性。
通过改变挤出机和模具的组合,可以制造出各种截面形状不同的铝制品。
从简单的杆状、管状产品到复杂的异型型材,挤压成型都可以实现。
这种灵活性使得铝挤压成型能够满足各种不同应用领域对铝制品的需求。
最后,铝挤压成型具有良好的可塑性。
铝合金材料在挤压过程中可以通过模具的挤压力将其塑造成各种复杂的形状。
挤压后的铝制品表面光滑,尺寸精确,质量稳定。
此外,铝合金具有良好的可加工性,可通过热处理进行强度调控,满足不同领域的使用要求。
1.低能耗:挤压成型是一种热成形加工方法,其能耗相对于其他金属加工方法较低,能够节约能源。
2.高生产效率:挤压成型能够实现大批量自动化生产,生产速度快,效率高。
3.成型精度高:挤压成型能够实现复杂形状的精确塑造,产品尺寸精度高,表面光滑。
4.良好的机械性能:挤压后的铝制品具有良好的强度和韧性,能够满足各种应用领域的需求。
5.可回收性:铝是一种可回收利用的金属材料,挤压成型过程中产生的废料可以回收再利用。
然而,铝挤压成型也存在一些缺点:1.模具制造成本较高:挤压成型需要使用专用模具,模具的制造和维护成本较高,对生产企业的投资较大。
2.适用性受限:铝挤压成型适用于中低压成型,对于高压的挤压成型需求无法满足。
3.变形控制难度较大:由于挤压成型是通过对铝合金材料施加挤压力来实现塑性变形,因此在挤压过程中控制材料的变形也是一项难度较大的工作。
总体而言,铝挤压成型具有高效性、灵活性和可塑性等显著特点,能够满足各种不同领域的需求。
随着工艺和设备的不断进步,铝挤压成型在铝制品加工领域的应用前景更加广阔。
铝合金挤压型材检验内控标准
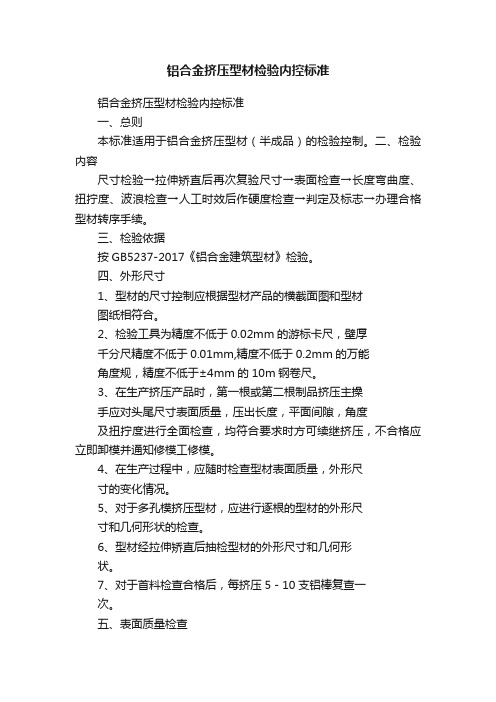
铝合金挤压型材检验内控标准铝合金挤压型材检验内控标准一、总则本标准适用于铝合金挤压型材(半成品)的检验控制。
二、检验内容尺寸检验→拉伸矫直后再次复验尺寸→表面检查→长度弯曲度、扭拧度、波浪检查→人工时效后作硬度检查→判定及标志→办理合格型材转序手续。
三、检验依据按GB5237-2017《铝合金建筑型材》检验。
四、外形尺寸1、型材的尺寸控制应根据型材产品的横截面图和型材图纸相符合。
2、检验工具为精度不低于0.02mm的游标卡尺,壁厚千分尺精度不低于0.01mm,精度不低于0.2mm的万能角度规,精度不低于±4mm的10m钢卷尺。
3、在生产挤压产品时,第一根或第二根制品挤压主操手应对头尾尺寸表面质量,压出长度,平面间隙,角度及扭拧度进行全面检查,均符合要求时方可续继挤压,不合格应立即卸模并通知修模工修模。
4、在生产过程中,应随时检查型材表面质量,外形尺寸的变化情况。
5、对于多孔模挤压型材,应进行逐根的型材的外形尺寸和几何形状的检查。
6、型材经拉伸矫直后抽检型材的外形尺寸和几何形状。
7、对于首料检查合格后,每挤压5-10支铝棒复查一次。
五、表面质量检查1、锯切后型材的表面质量用肉眼逐据进行检查。
2、表面检查内容:裂纹、起皮、汽泡、夹渣、划伤、碰伤等缺陷存在为不合格品。
六、间隙的检查1、平面间隙检查:把直尺放在型材被测水平面上,用塞尺测量型材平面与直尺之间的最大距离。
将标准样板紧贴在型材的曲面上〈备注:要求检查曲面间隙的型材标准样板由需方提供〉。
七、角度检查型材的角度差采用专用角度规或万能角度规检查。
八、长度尺寸检查每次锯切前应先检查锯切定尺档板位置是否正确,并在锯切过程中经常用钢卷尺抽检长度尺寸。
九、平直度检查1、弯曲度检查:将型材放在检验平台上,检查型材底面与平台间最大间隙。
每批型材锯切过程中,应检验弯曲度。
2、扭拧度检查,将型材放在平台上,以平台平面作基准面,用万能角度规则型材端部的扭拧度,每批型材在锯切过程中应抽检扭拧度。
铝挤压3c产品标准
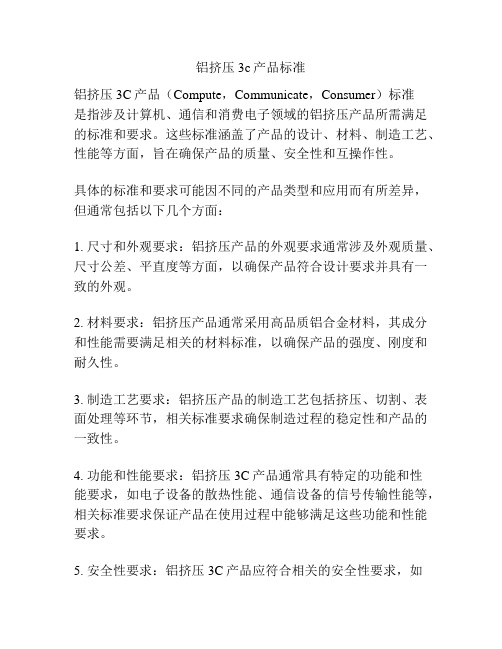
铝挤压3c产品标准
铝挤压3C产品(Compute,Communicate,Consumer)标准
是指涉及计算机、通信和消费电子领域的铝挤压产品所需满足的标准和要求。
这些标准涵盖了产品的设计、材料、制造工艺、性能等方面,旨在确保产品的质量、安全性和互操作性。
具体的标准和要求可能因不同的产品类型和应用而有所差异,但通常包括以下几个方面:
1. 尺寸和外观要求:铝挤压产品的外观要求通常涉及外观质量、尺寸公差、平直度等方面,以确保产品符合设计要求并具有一致的外观。
2. 材料要求:铝挤压产品通常采用高品质铝合金材料,其成分和性能需要满足相关的材料标准,以确保产品的强度、刚度和耐久性。
3. 制造工艺要求:铝挤压产品的制造工艺包括挤压、切割、表面处理等环节,相关标准要求确保制造过程的稳定性和产品的一致性。
4. 功能和性能要求:铝挤压3C产品通常具有特定的功能和性
能要求,如电子设备的散热性能、通信设备的信号传输性能等,相关标准要求保证产品在使用过程中能够满足这些功能和性能要求。
5. 安全性要求:铝挤压3C产品应符合相关的安全性要求,如
电子设备的电气安全性、通信设备的辐射安全性等,以确保产品在正常使用过程中不会对人体和环境造成危害。
总体而言,铝挤压3C产品的标准旨在确保产品在设计、制造、使用等方面具有一定的可靠性、稳定性和安全性,以满足用户的需求并保障市场的竞争力。
铝型材挤压模具制模技术重难点详解

铝型材挤压模具制模技术重难点详解关键词:金属材料铝型材挤压模具制备技术铝型材挤压是铝型材加工的重要工艺之一,而铝型材挤压工艺模具的制造直接关系铝挤型材的品质和使用寿命。
商品经理人指出,因为铝挤压工艺模具拥有一系列特点,所以铝型材模具制模技术需要满足一些特殊的要求:首先我们需要认识到,铝合金挤压工艺模具的工作条件十分恶劣,在挤压过程中需要经受高温、高压、高摩擦的作用,因此,模具的材料需要使用高强耐热的合金钢,而这些钢材的熔炼、铸造、锻造、热处理、电加工、机械加工和表面处理等工艺过程都比较复杂,这给模具制造加工增加了不少的困难。
其次,为了提高工模具的使用寿命和保证铝型材产品的表面品质,就必须要求模腔工作带的粗糙度达到0.8-0.4μm,而模子平面的粗糙度达到1.6μm以下,因此,在制模时需要采取特殊的抛光工艺和抛光类机械设备。
再则,目前客户对铝挤压产品的要求越来越高,逐渐向高、精、尖的趋势发展,有的型材和管材的壁厚要求降到0.5mm左右,其挤压制品公差要求达到±0.05mm,为了挤压这种超高精度的产品,要求模具的制造精度达到0.01mm,采崩传统的工艺足根本无法制造出来的,因此,要求更新工艺和采用新型专用设备。
第四,铝型材断面十分复杂,特别是超高精度的薄壁空心铝型材和多孔空心壁板铝型材,要求采用特殊的挤压模具结构,往往在一块模子上同时开设有多个异形孔腔,各截面的厚度变化急剧,相关尺寸复杂,圆弧拐角很多,这给模具的加工和热处理带来了很多麻烦。
第五,铝型材挤压产品的品种繁多,批量小,换模次数频繁,要求模具的适应性强,因此,要求提高制模的生产效率,尽量缩短制模周期,能很快变更制模程序,能准确无误地按图纸加工出合格的模了,把修模的工作量减少到最低程度。
第六,现如今铝合金挤压产品应用范围日趋广泛,规格范围十分宽广,因此,有轻至数千克的外形尺寸为100mm×25mm的小模子,也有重达2000kg以上的外形尺寸为1800mm×450mm的大模子。
挤压铝型材与切削铝型材差异及要求
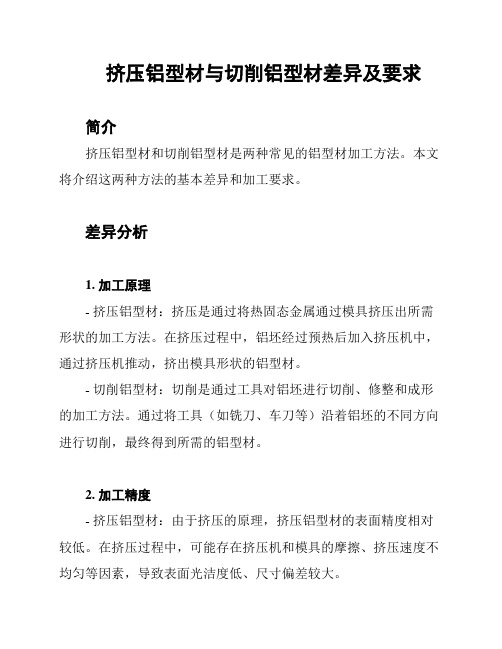
挤压铝型材与切削铝型材差异及要求简介挤压铝型材和切削铝型材是两种常见的铝型材加工方法。
本文将介绍这两种方法的基本差异和加工要求。
差异分析1. 加工原理- 挤压铝型材:挤压是通过将热固态金属通过模具挤压出所需形状的加工方法。
在挤压过程中,铝坯经过预热后加入挤压机中,通过挤压机推动,挤出模具形状的铝型材。
- 切削铝型材:切削是通过工具对铝坯进行切削、修整和成形的加工方法。
通过将工具(如铣刀、车刀等)沿着铝坯的不同方向进行切削,最终得到所需的铝型材。
2. 加工精度- 挤压铝型材:由于挤压的原理,挤压铝型材的表面精度相对较低。
在挤压过程中,可能存在挤压机和模具的摩擦、挤压速度不均匀等因素,导致表面光洁度低、尺寸偏差较大。
- 切削铝型材:切削铝型材的加工精度相对较高。
通过调整切削工具的刀具进给速度、冷却剂的喷射等方式,可以控制切削过程中的加工精度,得到表面光滑、尺寸稳定的铝型材。
3. 加工效率- 挤压铝型材:挤压铝型材的加工过程相对简单,一次挤压可以得到较长的铝型材,因此加工效率较高。
但是,由于需要进行铝坯的预热等前置准备,整体加工周期相对较长。
- 切削铝型材:切削铝型材的加工过程相对复杂,需要通过多次切削、修整来达到所需形状。
因此加工效率较低,但是由于不需要进行预热等前置准备,整体加工周期相对较短。
加工要求1. 材质选择根据具体使用要求选择适合的铝合金材料。
不同的材质具有不同的强度、耐腐蚀性、加工性能等特点,需要根据具体应用场景进行选择。
2. 精确的尺寸控制在加工过程中,需要严格控制铝型材的尺寸精度。
采用精确的数控机床、高精度的刀具等工艺手段,确保铝型材的尺寸与设计要求一致。
3. 表面质量铝型材表面的质量对于后续的使用具有重要影响。
通过合理的切削速度,合适的切削深度和进给量等条件,确保铝型材表面光滑、无划痕、无氧化物和夹杂物。
4. 工艺控制加工铝型材需要进行良好的工艺控制。
包括合适的加工温度、合理的冷却剂使用、适当的加工速度和压力等条件的控制,以确保加工过程中的稳定性和一致性。
铝合金板冲压工艺技术概述

铝合⾦板冲压⼯艺技术概述来源:冲压帮不同于传统⽅式,全铝车⾝制造⼯艺有其特殊性、复杂性和多样性。
⼀、铝合⾦板冲压件的⼯艺难点及常见缺陷1.成形性差2.起皱倾向严重与钢板相⽐,铝合⾦板的起皱与开裂之间的窗⼝较窄,起皱倾向严重。
3.回弹量⼤,零件精度控制困难铝合⾦板的弹性模量仅为钢板的三分之⼀,零件更易回弹。
4.包边性差,易开裂和产⽣“桔⽪”缺陷5.板材表⾯氧化层粘性强,影响模具使⽤寿命铝合⾦板表⾯氧化层在板料拉延过程中与模具表⾯摩擦较⼤,易剥落并粘在模具表⾯造成模具损伤。
6.修边后⽑刺较⼤并碎屑堆积严重,零件⾯品受到影响且模具维护成本增加⽑刺:修边残屑:⼆、铝合⾦板冲压件的产品设计准则1.铝合⾦板的零件的形状不宜太复杂,深度不宜太深,形状、深度的过渡尽可能平缓。
产品半径;产品侧壁拔模⾓;沿凹坑截⾯的最⼤线长变化。
2.通过增加内外板的⽀撑点,增强铝合⾦外板的抗弯曲能⼒。
3.翻边设计铝合⾦板四门两盖的总成⼯艺通常采⽤滚轮包边。
外板翻边⾼度要求;翻边⾼度的公差要求。
三、铝合⾦板冲压⼯艺设计指南1、冲压成形⽅法种类传统冲压液压成形温热成形2.传统冲压的⼯艺设计冲压⼯艺设计是连结产品结构设计和模具设计制造的纽带。
精益制造的实现来源于精益的⼯艺设计。
⼯艺⽅案的选择冲压⽅向的确定;压边圈的设计和优化;模⼝线的设定;⼯艺补充的细化;拉延筋的设计。
⼯艺设计需严格遵循以下原则,⼒求⼯艺设计的最优化:以保证冲压件质量为前提条件的⼯序最少化;模具简单化、⽣产成本最少化;材料成本最⼩化(如考虑板料的合理排样、拉延⼯艺补充最⼩化);满⾜冲压⽣产设备;充分利⽤冲压成形仿真技术,科学优化零件结构。
压边圈设计⼯艺型⾯设计的⾸要任务是确保压边圈型⾯的设计质量。
不当的压边圈型⾯设计会造成压边圈合模时板料起皱,直接影响冲压件品质。
压边圈型⾯要求表⾯光顺,采⽤可延展的型⾯形状,如单曲⾯或锥形⾯避免采⽤双曲⾯和球⾯,否则板料会在压边圈闭合时由于积料⽽影响表⾯质量压边圈型⾯尽量随零件形状以保证各处的拉深⾼度⼀致采⽤“蝴蝶翅”压边圈设计理念对于铝合⾦冲压零件,应当避免将产品部分设计在压边圈型⾯上⼯艺补充⾯铝⽐钢更容易材料硬化,建议产品形状⼀次成型到位,不要采⽤整形最⼩凸 / 凹模圆⾓半径拔模⾓度修边线采⽤吸料筋和凸筋消除 / 减⼩起皱缺陷借助凸筋形状对开裂风险区的材料进⾏局部保护,消除开裂风险拉延筋设计拉延筋的⾛向拉延筋的形状尺⼨拉延筋 CAD 型⾯的⾃动⽣成四、冲压模具设计关键事项1.拉延模实验证明,表⾯镀铬处理⽅法相⽐其它⽅法更能有助于减⼩铝合⾦板表⾯擦伤和降低因表⾯氧化层剥落⽽造成的模具磨损。
铝合金挤压制品常见缺陷分析及预防措施.ashx
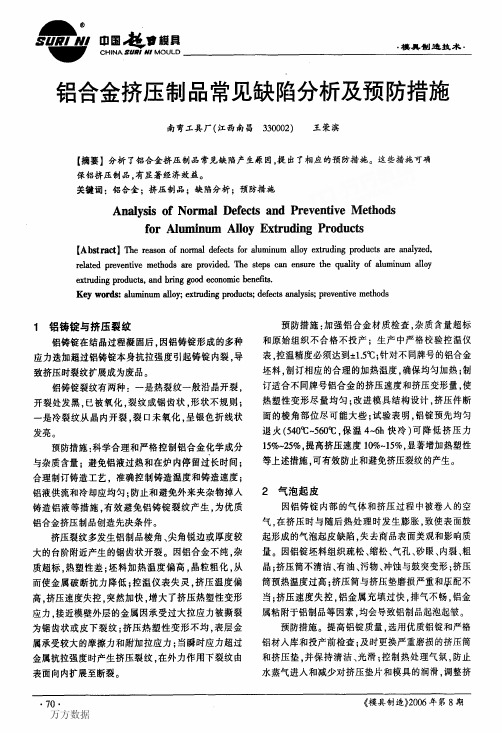
·70·
万方数据
《模具制造》2006牟第8期
·模具制造技术·
压机使其动作均匀协调,制订合理的挤压速度和挤压 变形量,确保排气畅通;挤压筒预热温度应低于铝坯 加热温度25℃~35℃;防止润滑剂过量,及时清除铝金 属氧化壳及腐蚀污物等措施。能有效防止铝制品起泡 起皮。达到质量指标。
预防措施。对挤压模具进行表面改性强硬化处 理,提高红硬性、耐磨性和抗擦伤能力;选用优质精炼 模具钢,具有纯清度高、杂质少、晶粒细、碳化物小、等 向性能优、化学成分和组织均匀等特点;或用钢结硬 质合金制造模具,经镦造与复合强硬化热处理,使模 具工作型面具有高硬度、红硬性、耐磨性、抗疲劳、抗 咬合、抗粘结、抗腐蚀和抗擦伤等特性,而钢基体具有 高强硬性,表硬内刚赋予高寿命;选择最佳工作带宽 度,生产一定铝制品后,抛光模具型面与工作带;确保 工模具与挤压设备装配精度;经常润滑导路与导管。 采用上述措施能有效防止铝制品表面擦伤,确保铝制 品内在质量和表面质量优良。
1铝铸锭与挤压裂纹 铝铸锭在结晶过程凝固后,因铝铸锭形成的多种
应力迭加超过铝铸锭本身抗拉强度引起铸锭内裂,导 致挤压时裂纹扩展成为废品。
铝铸锭裂纹有两种:一是热裂纹一般沿晶开裂, 开裂处发黑,已被氧化,裂纹成锯齿状,形状不规则; 一是冷裂纹从晶内开裂,裂口未氧化,呈银色折线状 发亮。
预防措施:科学合理和严格控制铝合金化学成分 与杂质含量:避免铝液过热和在炉内停留过长时间; 合理制订铸造工艺,准确控制铸造温度和铸造速度; 铝液供流和冷却应均匀:防止和避免外来夹杂物掉人 铸造铝液等措施,有效避免铝铸锭裂纹产生,为优质 铝合金挤压制品创造先决条件。
如何判断铝合金挤压制品生产的难度
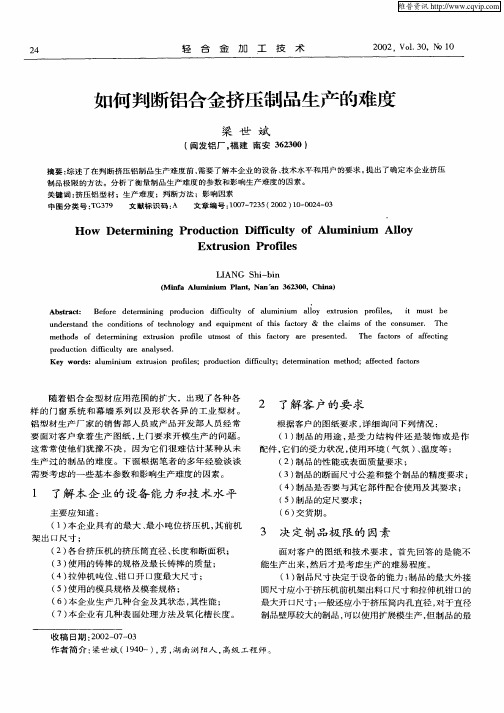
2 4
轻
合
金
加
工Leabharlann 技术 2 0 V 13 ,N 0 0 2, o.0 o1
如何 判断铝合 金挤压制 品生 产 的难 度
粱 世 斌
( 闽发铝 厂 , 建 南 安 3 2 0 福 6 3 0)
摘 要 : 述 了 在 判 断 挤 压 铝 制 品 生 产 难 度 前 , 要 了 解 本 企 业 的 设 备 、 术 水 平 和 用 户 的要 求 。 出 了确 定 本 企 业 挤 压 综 需 技 提
随着 铝 合 金 型 材 应用 范 围 的扩 大 ,出现 了各 种 各 样 的 门窗 系 统 和幕 墙 系 列 以 及 形 状各 异 的 工 业 型 材 。
铝 型 材 生产 厂 家 的 销 售部 人 员 或 产 品开 发 部人 员 经 常 要 面 对 客户 拿 着 生 产 图纸 , 门要 求 开模 生 产 的 问题 。 上 这 常 常 使 他们 犹 豫 不 决 ,因为 它 们 很难 估 计 某 种从 未 生 产过 的 制 品 的难 度 。下 面根 据 笔 者 的 多年 经 验 谈 谈
( 各 台挤 压 机 的挤 压 简 直径 、 度 和 断面积 ; 2) 长 ( 使 用 的 铸棒 的 规格 及最 长铸 棒 的质 量 ; 3)
( 拉 仲 机 吨位 、 口开 口度最 大尺 寸 ; 4) 钳
( 使 用 的模 具规 格及 模 套规 格 ; 5)
( ) 企业 生 产几 种 合金 及其 状态 , 性 能 ; 6本 其 ( 本 企业 有 几种 表 面处 理方 法及 氧 化槽 长 度 。 7)
u e tnd h c n iin f t c o o y nd q i me t o h s a tr & t e c ams o he o u r Th nd r a t e o d to s o e hn l g a e u p n f t i fco y s h li f t c ns me . e meh d o dee i n e t so prfl u mo t f h s a tr a e r s ntd. to s f t r nig xr in m u o e t s o t i fc o i y r p e e e p o uci fiu t a e a ay e rd t on di c ly r n ls d. Ke r s l y wo d :aumi i m e tu in prfls nu xr so o e ;prdu to d f c ly i o c in if u t ;dee mi ai n m eh d fe td a tr i tr n t t o ;a ce fco o s The a tr o af ci g fc o s f fe tn
生产难易程度及机台判断
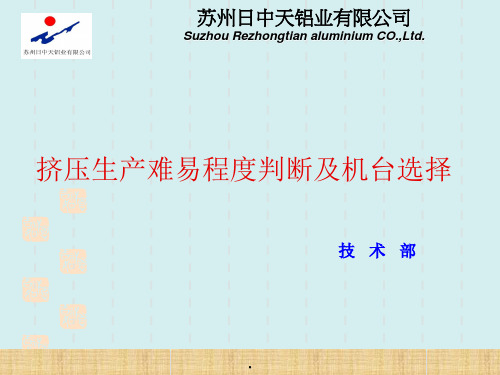
2.1 按米重计算 注:①按米重计算需要考虑到供货长度和使用量,如果用量 不大的产品尽量开在小机台。供货长度短的产品也可以开在 小机台。 ②按米重选择机台时,还要注意平衡各机台的工作量。 ③按米重选择机台时,还要注意每台机的铝棒最大长度以及 压于长短。所需的铝棒长度L计算公式如下:
L= [型材米重×(长度×支数+切头尾长)]÷铝棒米重+压余长度+工艺余量
2
3
*7±0.2
50
.
7.5
*45±0.4
35.5
29.5
± *7 3 0.
外接 圆直 径
H尺寸
实体金属部 分不小于 75%的H尺寸 的允许偏差 g、h,±
2栏
0.13 0.15 0.17 0.21
实体金属部分小于75%的H尺寸对应于下列E尺寸的 允许偏差a、b、c、d、e、f,±
>6~15 >15~ 30 >30~ 60 >60~ 100 > 100~ 150 > 150~ 200
1.27 2.03 2.03 2.79 3.56 4.32
苏州日中天铝业有限公司
Suzhotd.
扭拧度:将型材置于平台上,并使其一端紧贴平台。型材 借自重达到稳定时,测量型材翘起端的两侧端点与平台间 的间隙值T1和T2,如图19所示,T2与T1的差值即为型材 的扭拧度。(注意扣除端头弯曲度以后)
Drawing No.
Su Zhou Ri Suzhou Zhong Tian Aluminium Co.,Ltd Rezhongtian aluminium
型材外接圆
Inscribed Circle
RZT-SZ1444 CO.,Ltd.
无
?177.81
铝合金零件加工难点与对策探析
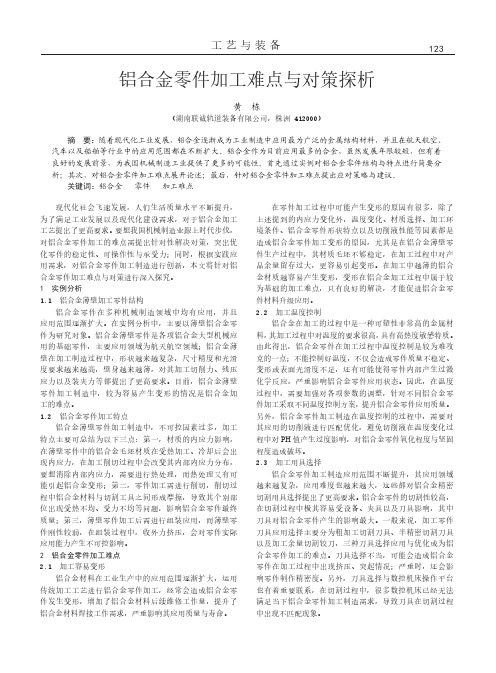
现代化社会飞速发展,人们生活质量水平不断提升,为了满足工业发展以及现代化建设需求,对于铝合金加工工艺提出了更高要求。
要想我国机械制造业跟上时代步伐,对铝合金零件加工的难点需提出针对性解决对策,突出优化零件的稳定性、可操作性与承受力;同时,根据实践应用需求,对铝合金零件加工制造进行创新,本文将针对铝合金零件加工难点与对策进行深入探究。
1 实例分析1.1 铝合金薄壁加工零件结构铝合金零件在多种机械制造领域中均有应用,并且应用范围逐渐扩大。
在实例分析中,主要以薄壁铝合金零件为研究对象。
铝合金薄壁零件是各项铝合金大型机械应用的基础零件,主要应用领域为航天航空领域;铝合金薄壁在加工制造过程中,形状越来越复杂,尺寸精度和光滑度要求越来越高,壁身越来越薄,对其加工切削力、残压应力以及装夹力等都提出了更高要求。
目前,铝合金薄壁零件加工制造中,较为容易产生变形的情况是铝合金加工的难点。
1.2 铝合金零件加工特点铝合金薄壁零件加工制造中,不可控因素过多,加工特点主要可总结为以下三点:第一,材质的内应力影响,在薄壁零件中的铝合金毛坯材质在受热加工、冷却后会出现内应力,在加工削切过程中会改变其内部内应力分布,要想消除内部内应力,需要进行热处理,而热处理又有可能引起铝合金变形;第二,零件加工需进行削切,削切过程中铝合金材料与切割工具之间形成摩擦,导致其个别部位出现受热不均、受力不均等问题,影响铝合金零件最终质量;第三,薄壁零件加工后需进行组装应用,而薄壁零件刚性较弱,在组装过程中,收外力挤压,会对零件实际在零件加工过程中可能产生变形的原因有很多,除了上述提到的内应力变化外,温度变化、材质选择、加工环境条件、铝合金零件形状特点以及切削液性能等因素都是造成铝合金零件加工变形的原因,尤其是在铝合金薄壁零件生产过程中,其材质毛坯不够稳定,在加工过程中对产品余量留存过大,更容易引起变形。
在加工中越薄的铝合金材质越容易产生变形,变形在铝合金加工过程中属于较为基础的加工难点,只有良好的解决,才能促进铝合金零件材料升级应用。
铝合金挤压生产知识

一、铝合金的挤压生产1.挤压时金属的变形过程分为几个阶段?分为:⑴填充挤压阶段;⑵平流压由阶段;⑶紊流压由阶段。
2、什么是挤压比(入)?挤压6063型材时,挤压比(入)在什么范围内最合适?挤压筒内铝棒的截面积与挤由型材的截面积之比,称为挤压比(入)或挤压系数(入)。
挤压系数是挤压工艺最重要的内容,根据制品外形和截面面积选择挤压筒的直径。
挤压系数一般〉9。
平模当入=9〜40时使用寿命较长,分流模的挤压系数应在20〜70范围内。
系数过小会产生焊接不良。
所以挤压空心型材的挤压系数比实心型材的大。
如挤压①101X25管材,当入=15时焊合不好,选择入=38时管材焊合良好。
挤压系数太大,挤压困难,而且因铝棒较短造成产品的成品率太低,影响经济技术指标。
3.生产过程中如何控制挤压温度?铝棒温度应保持在440〜520c之间(以6063为例),加热时间均在6小时以上。
挤压筒加热到400〜440C。
模具温度为400〜510C,保温时间1〜4小时。
4、选择挤压温度应遵循哪些原则?6063合金铝棒的挤压温度通常在470〜510之间,有时也可在较低温度下挤压。
选择铝棒温度的原则:⑴为获得较高的机械性能,应选择较高的挤压温度;⑵当挤压机能力不足,可通过提高铝棒温度来提高挤压速度;⑶当模具悬臂过大时,可提高铝棒温度,以减小铝棒对模具的压力及摩擦力;⑷挤压温度过高会使产生气泡、撕裂及由于模具工作带粘铝造成表面划痕严重;⑸为了获得高表面质量的产品,宜在较低温度下挤压5、如何控制挤压速度?挤压速度是影响生产率的一个重要指标。
挤压速度取决于合金种类、几何形状、尺寸和表面状态,同时也与铸锭质量息息相关。
要提高挤压速度,必需合理控制铝棒温度、模具温度、挤压筒温度。
6063铝合金挤压速度范围为:9〜80M/min,其中实心型材为:20〜80M/min,空心型材的挤压速度一般为实心型材挤压速度的0.5〜0.8倍。
6、什么是均匀化?通常将6063铝棒在560c保温6〜8小时,使合金的Mg2si相以细小质点均匀分布在整个金属基体中,且消除铸造应力,铸锭由炉后以较高速度冷却(水冷或风冷),这种热处理工艺称作均匀化。
生产难易程度及机台判断资料
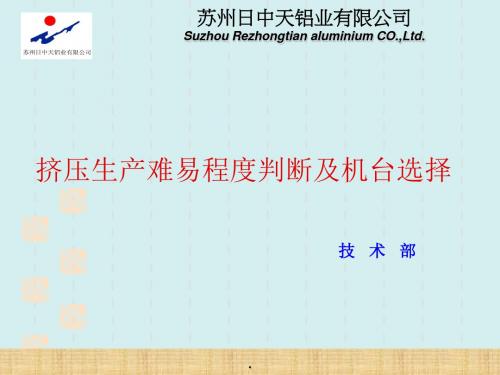
1.5 尺寸精度
包括壁厚尺寸、非壁厚尺寸和形位尺寸三部分。 根据GB5237-2008(建筑铝型材)和GB/T14846-2008
(工业用铝型材)的难度等级,出口料可能还要符合外国 标准如日本的H4100-2006,欧洲的DIN-EN755。 普通难度:普通级 中等难度:高精级 高 难 度:超高精级或稍严于超高精级 超高难度:严于超高精级
Suzhou Rezhongtian aluminium CO.,Ltd.
1.2 舌比
如下图所示,舌比=T/W= A / W2(A表示阴影处面积) 普通难度:舌比≤4(当舌比≥3就要考虑导流模) 中等难度:4<舌比≤5.6 高 难 度: 6<舌比≤10 超高难度:舌比>10
.
.
苏州日中天铝业有限公司
Suzhou Rezhongtian aluminium CO.,Ltd.
1.6 挤压比λ
挤压比λ=挤压筒横截面积÷型材横截面积
注1:挤压比越大,所需的挤压力越大,模具变形越严重,越难挤压。
(1)越大的机台,挤压比应该设计得越小; (2)难度越大的产品,挤压比应该设计得越小; (3)越软的合金,挤压比可以设计得越大; (4)挤压比越大的合金,挤压温度越高。
型材外接圆D ≤60
60~90 90~130 130~180 180~295
模具最小外径 实际模具规格
平模:D+80 分流:D+90
Φ150×100 Φ160×100
平模:D+80 分流:D+90
Φ180×120 Φ190×130
平模:D+90 分流:D+120
铝型材工艺难度评估
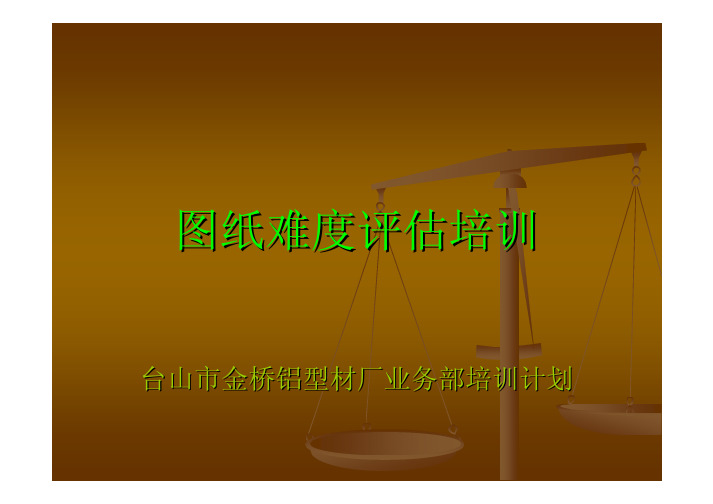
图纸难度评估培训台山市金桥铝型材厂业务部培训计划1.型材与挤压机对应关系实心型材或棒材空心型材或有缝管穿心针无缝管挤压方式图解2.基本公式实心型材(平模)槽型模具的一般挤型(除高倍齿散热片外) A<3 可做AB注:槽型可以是一个型材(平模)或型材(包括平模和分流模)的一部分。
实例分析两个槽形并存于一个截面上,而且槽与槽相接,产快,否则变化更大。
出料后仍须整形才能达到要求。
空心型材(分流模)可做分流模最小可做程度6.0mm (小公头)实例分析3.必须考虑的因素型材截面积)表面问题(厚薄悬殊在同一部位线面上,相邻的厚壁÷薄壁>2.5就开始难做,而且随着倍数的增大,就越难控制壁薄实例分析速不均,易变形,挤压比计算公式:盛锭筒截面积÷型材截面积30-6060-100比压厘米因此型状太细,挤压比大,需要出多支才能挤压出料。
由于出多实例分析机台淬火(过水料)系列合金一般可以通过机台淬火达到固溶热处理的效果,再通过后续的时效处理达到需要的机械性能。
但往往矛盾在这6082/T6,模具成型无问题,性能要求较高需过水,因实例分析硬合金空心型材,在现有的设备上)关于粗晶环由于硬合金成分关系,很实例分析7075/T6,ABS阀体。
要求粗晶环小于0.3mm,实际挤压中,可以达到,但较难多公头体为灌料均衡和公头偏转的控制,以致难以表面问题型材较薄,在T界的表面,容易因流关于螺丝孔厚,太薄将难以成型开口角度最好50度以上(槽3mm公差基本上遵循以上原则,而且在各国挤压标准的公差要求范围内都可以做模具。
但比高精级标准如国标高精级、日本特殊级还要严格,加上形状复杂,实际开发周期较长,生产很难控制,成品率低。
实例分析反向机异型无缝管4.你也可以评估图纸6060/T6你也可以评估图纸6082/T6你也可以评估图纸你也可以评估图纸你也可以评估图纸你也可以评估图纸。
- 1、下载文档前请自行甄别文档内容的完整性,平台不提供额外的编辑、内容补充、找答案等附加服务。
- 2、"仅部分预览"的文档,不可在线预览部分如存在完整性等问题,可反馈申请退款(可完整预览的文档不适用该条件!)。
- 3、如文档侵犯您的权益,请联系客服反馈,我们会尽快为您处理(人工客服工作时间:9:00-18:30)。
如一个企业的最大挤压机为 16MN,铸锭的最大质量为 43.3KG,残料质量为 1.9KG,制品每米质量为 6.8KG,切头尾共 1.0m。 43.3 − 1.9 最大交货长度 = − 1.0 = 5.1m 6.8 对于中、小断面型材,其最大交货长度则决定于氧化槽的长度:如该企业氧 化槽长度为 8.1m,则氧化着色材的最大交货长度为 7.6m 左右。
如何判断铝合金挤压制品生产的难度 1. 了解本企业的设备能力和技术水平 主要应知道: (1) 本企业具有的最大、最小吨位挤压机、其前端机架出口尺寸; (2) 各台挤压机的挤压筒直径、长度和断面面积; (3) 使用的铸件的规格及最长铸锭的质量; (4) 拉伸机吨位、钳口开口度最大尺寸; (5) 使用的模具规格及模套规格; (6) 本企业生产几种合金及其状态性能; (7) 本企业有几种表面处理方式及氧化槽长度。 2. 了解客户的要求 根据客户的图纸要求,详细询问下列情况: (1) 制品的用途、是受力结构件还是装饰或是装配件,他们的手里情况,使用 环境温度等; (2) 制品的性能和表面质量要求; (3) 制品的断面尺寸公差和整个制品的精度要求; (4) 制品是否要与其他部件配合使用及其要求; (5) 制品的定尺要求; (6) 交货期。 3. 决定制品极限的因素 面对客户的图纸和技术要求,首先回答的是能不能生产出来,然后是生产的 难易程度。 (1) 制品尺寸决定于设备的能力: 制品的最大外接圆尺寸应小于挤压机前机架 出料口尺寸和拉伸机钳口的最大开口尺寸; 一般还应小于挤压筒内孔直径, 对于直径制品壁厚较大的制品,可以使用扩展模生产,但制品的最大外接 圆直径应小于模套直径-100mm。 设备的这三种尺寸中取其最小的一种尺寸,及时企业能生产的最大断面尺寸。 (2) 制品的力学性能(以韦氏硬度 HW 表示)决定于合金及其状态: 工业纯铝 HW4-7; 6063 合金 HW8-14; 6061 合金 HW11-18; 2024 合金 HW23-26; 7075 合金 HW25-30.对于同一合金而言,其力学性能一般 T6>T5>T4. 本企业生产哪些合金及状态, 其中某合金的最大性能值就是本企业能保证 的最大性能值。 (3) 大断面型材制品截面积(或每米质量)决定最大交货长度: 最大交货长度 = 最大铸锭质量 − 残料质量 制品的每米质量 − (0.7 − 1.5m 切头尾)
空心型材: 难于空心为规则形状的便于计算,可以只计算其外周长来确定 k 值,进而确定其难度;对于多空心型材,可在单空心型材难度系数的基 础上,补加难度附加值 0.2-1.0 来确定多空心型材的难度系数 k 值。 需要指出的是 k 值是表征制品本身的生产难度,并不代表制模的难度,可 能一个具有几个空心的制品,制模难度很大,而其难度系数并不大。 (4) 影响制品生产难度的其他因素: 1)壁厚差,壁厚差增大会使难度增加,特别是壁厚差大于 5 以上。难度明显 增加,同时也会影响时效效果。 2)深宽比,即深度/宽度比值越大其生产难度增加。 3)制品有半岛 (悬臂) , 收颈处越小难度越大, 因为易在收颈处断裂或变形。 4)开口,不对称性对难度的影响,开口的圆形或方形比封闭的圆形或方形其 生产难度大一些。对称制品比非对称制品易于生产。 5)制品的配合,需要配合的制品比单一制品难度大;相关配合(两个以上的 配合) 比单一配合的制品生产难度大。 工业型材最怕的就是多件组合相配, 有时单一的制品容易生产,但要多件符合组装要求就很难。 6)制品的精度要求。有的制品看起来生产难度很小,但精度要求过高就很难 生产。 7)空心制品随空心复杂程度和空心数目增多而生产难度增加。空心形状越复 杂,制模难度增加;空心数目越多,制模越困难,制模费用越高,所以空 心工业型材要比实心工业型材价格贵。
(4) 制品难度决定于模具的制作水平:多空心型材能否生产,主要取决于模具 生产厂家的设备和设计的先进水平,有些制品看起来难度很大,但如果模 具设计先进、合理,模具制造精细,会使制品生产起来变得比较容易,因 此应与模具生产厂家的设计人员联系,多听取他们的意见。 4. 决定制品生产难度的因素 (1) 制品的外接圆直径: 根据挤压机吨位的大小不同,型材外接圆距挤压筒内 壁的最小距离应保持在 15-30mm 之间,对于多孔模,模孔间距应保持 20-30mm。允许最大外接圆直径参考表 1。 制品的外接圆愈接近挤压筒直径,生产难度愈大;制品外接圆直径等于或 超过挤压筒直径,用一般的模具无法生产,只有扩展模才可以生产,但但 最大外接圆之间必须小于模套外径-100mm。 不是所有的大断面型材都可以做扩展模,只有挤压系数较小(一般 30 以 内),壁厚较大(2.0mm 以上)的才可以做扩展模。对于挤压系数较大, 壁厚小的制品,即使制作了扩展模,恐怕也无法生产出来。 挤压筒直径 80-110 120-140 150-200 210-280 /mm 到挤压筒内壁 15 20 25 30 最小距离/mm 模孔间最小距 20 20 25 30 离/mm 制品允许最大 外接圆直径 50-80 80-100 100-150 150-220 /mm 扩展模最大外 70-100 100-220 180-220 210-320 接圆直径/mm (2) 挤压系数的影响:挤压系数越大,反映制品的变形越大,所需的挤压力也 越大,说明挤压难度越大;反之,挤压系数越小,制品越易挤压;但挤压 系数太小,会使制品保留铸造组织,降低制品性能,一般要求>8。 挤压系数太大,除易产生闷车外,还会引起挤压效应的消失,也会降低制 品的强度。 不同合金允许的最大挤压系数不同。 如: 工业纯铝可达 500-800, 一般在 300-120 之间; 6063 合金可达 200-250, 一般在 15-120 之间; 6061 合金可达 100-180,一般在 10-80 时间;硬铝或超硬铝可达 60-80,一般 在 10-50 之间。 更换挤压筒或更换挤压机可改变挤压系数,从而可以改变生产难度。如生 产 28*25*1mm 扁管:在 16MN 挤压机上生产(挤压筒只讲为 173mm),挤压 系数为 192.6, 难生产; 在 7.8MN 挤压机上生产 (挤压筒直径为 127mm) , 挤压系数为 103.8, 可以生产; 在 4.9MN 挤压机上生产 (挤压筒直径为 94mm) , 挤压系数为 56.8,容易生产。 (3) 难度系数: 制品断面的周长和其面积的比是确定制品难易程度的指标,叫 难度系数 (k ) 。 它与生产条件无关, 比较真实地反映了制品生产的难度。 K 值越大生产难度越大。 实心型材:k 值在 1.0 以内容易生产,k 值在 1.0-2.0 范围内较易生产,k 值在 2。0-3.0 范围内较难生产,k 值大于 3.0 难生产。