产品部件生产加工工艺流程讲解学习
加工工艺流程

加工工艺流程加工工艺流程是指对原材料进行一系列的加工和处理,使原材料转化为成品的过程。
不同的产品需要不同的加工工艺流程,下面就以汽车零部件的加工工艺流程为例,介绍一下整个流程的步骤和注意事项。
1.材料准备:首先要准备好所需的原材料,例如钢材、铝材等。
材料的选择要根据产品的要求来确定,包括强度、韧性、耐腐蚀性等等。
在准备材料的过程中,需要检查材料的质量和尺寸是否符合要求,以确保加工的产品的质量。
2.切割:将准备好的材料按照要求的尺寸进行切割。
切割的方法有很多种,常见的有剪切、割在等。
在切割过程中,要注意切割的位置和角度,以及切割的速度和力度,以保证切割面的平整和尺寸的准确。
3.成型:根据产品的要求,对切割好的材料进行成型。
成型的方法有很多种,例如冲压、折弯、拉伸等。
在成型过程中,要根据产品的形状和尺寸要求,选择适当的成型工艺和模具,以确保成型件的质量。
4.焊接:将成型好的零部件进行焊接。
焊接的方法有很多种,例如气焊、电焊、激光焊等。
在焊接过程中,要注意焊接的温度和时间,以及焊接的位置和角度,以确保焊接点的质量,避免焊接产生裂纹或变形。
5.表面处理:对焊接好的零部件进行表面处理。
表面处理的目的是保护零部件的表面免受腐蚀和磨损,并提高外观质量。
常见的表面处理方法有热镀锌、喷涂、电镀等。
在表面处理过程中,要注意处理的温度、时间和涂层的均匀性,以确保处理效果的质量。
6.装配:将经过表面处理的零部件进行组装。
装配的目的是将不同的零部件按照一定的顺序和方法组装在一起,形成成品。
在装配过程中,要注意零部件之间的配合精度和装配的紧固力度,以确保装配的质量和功能性。
7.检验:对装配好的成品进行检验。
检验的目的是确保成品的质量和功能达到标准要求。
常见的检验方法有尺寸检验、力学性能检验、外观检验等。
在检验过程中,要根据产品的要求,选择合适的检验方法和仪器设备,以确保检验结果的准确性和可靠性。
8.包装:将检验合格的成品进行包装。
产品加工工艺流程

产品加工工艺流程产品加工工艺流程是指把原材料加工转化为成品的一系列工艺流程。
它是生产过程中的重要环节,直接关系到产品质量和生产效率。
下面我将以手机加工工艺流程为例,介绍产品加工工艺流程的主要步骤。
首先,原材料准备是整个加工工艺流程的第一步。
手机的主要原材料包括金属、塑料、电路板和显示屏等。
生产厂家根据产品设计要求,采购这些原材料,并对其进行质量检验和分类分配。
第二,零件加工。
原材料经过切割、铣削、钻孔、冲压等加工工艺,转化为各个手机零部件。
例如,金属外壳通过剪切和钻孔等工艺,加工成相应的形状和尺寸;塑料外壳通过注塑成型等工艺,获得所需的外形和结构。
在这一步,需要使用各种机械设备和工具进行加工,如数控机床、注塑机等。
第三,组装。
经过零件加工的各个零部件,将根据产品设计要求进行组装。
手机组装工艺主要包括电路板焊接、贴附显示屏、安装电池等步骤。
焊接是将各个电子元件连接到电路板上的过程,常见的有手工焊接和机器焊接两种方式。
贴附显示屏是将已经生产好的显示屏粘贴到手机外壳上的过程。
电池是手机的重要组成部分,需要在手机内部进行安装。
第四,测试和调试。
产品组装完成后,需要经过一系列的测试和调试工艺,以确保产品的质量和功能正常。
常见的测试工艺有外观检查、硬件测试、软件测试等。
外观检查主要是检查产品的外观是否完好无损,有无划痕、凹陷等缺陷。
硬件测试是测试产品的各个功能是否正常,如打电话、收发短信、摄像、录音等。
软件测试是测试产品的操作系统和应用程序是否稳定可靠。
第五,质量检验和包装。
经过测试和调试的产品,需要进行质量检验。
质量检验主要包括外观质量、功能性能、电池寿命和通讯信号等方面的检查。
通过质量检验合格的产品,将进行最后一道手续——包装。
手机包装通常包括外包装和内包装,外包装是指手机的盒子和包装盒,内包装是指手机的保护膜、说明书和配件等。
以上就是手机加工工艺流程的主要步骤。
不同产品的加工工艺流程会有所不同,但总的来说,都会包括原材料准备、零件加工、组装、测试和调试、质量检验和包装等环节。
(完整)产品部件生产加工工艺流程
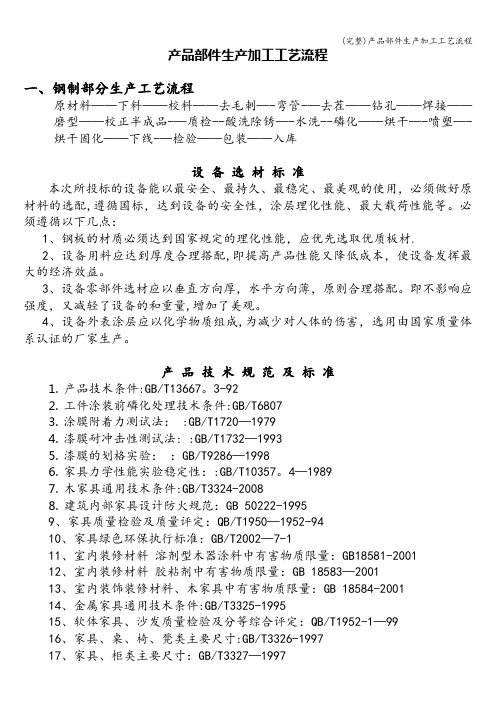
产品部件生产加工工艺流程一、钢制部分生产工艺流程原材料——下料——校料——去毛刺—-弯管-—去茬——钻孔——焊接——磨型——校正半成品-—质检--酸洗除锈—-水洗--磷化——烘干—-喷塑—-烘干固化——下线-—检验——包装——入库设备选材标准本次所投标的设备能以最安全、最持久、最稳定、最美观的使用,必须做好原材料的选配,遵循国标,达到设备的安全性,涂层理化性能、最大载荷性能等。
必须遵循以下几点:1、钢板的材质必须达到国家规定的理化性能,应优先选取优质板材.2、设备用料应达到厚度合理搭配,即提高产品性能又降低成本,使设备发挥最大的经济效益。
3、设备零部件选材应以垂直方向厚,水平方向薄,原则合理搭配。
即不影响应强度,又减轻了设备的和重量,增加了美观。
4、设备外表涂层应以化学物质组成,为减少对人体的伤害,选用由国家质量体系认证的厂家生产。
产品技术规范及标准1.产品技术条件:GB/T13667。
3-922.工件涂装前磷化处理技术条件:GB/T68073.涂膜附着力测试法: :GB/T1720—19794.漆膜耐冲击性测试法: :GB/T1732—19935.漆膜的划格实验::GB/T9286—19986.家具力学性能实验稳定性::GB/T10357。
4—19897.木家具通用技术条件:GB/T3324-20088.建筑内部家具设计防火规范:GB 50222-19959、家具质量检验及质量评定:QB/T1950—1952-9410、家具绿色环保执行标准:GB/T2002—7-111、室内装修材料溶剂型木器涂料中有害物质限量:GB18581-200112、室内装修材料胶粘剂中有害物质限量:GB 18583—200113、室内装饰装修材料、木家具中有害物质限量:GB 18584-200114、金属家具通用技术条件:GB/T3325-199515、软体家具、沙发质量检验及分等综合评定:QB/T1952-1—9916、家具、桌、椅、凳类主要尺寸:GB/T3326-199717、家具、柜类主要尺寸:GB/T3327—199718、家具五金、拉手安装尺寸:QB/T1241-1991磷化喷塑工艺介绍(一)、磷化因钢板、钢管在制造和储运过程中,都加入有防护油,在生产成产品过程中其表面也都不可避免地沾有各种污物,如:润滑油,金属氧化层,与人接触而带来的汗渍以及灰尘等.这些污物的存在,对涂装工艺十分不利,并将最终影响涂层的内在综合质量。
工业产品生产工艺流程

工业产品生产工艺流程工业产品的生产工艺流程是指在工业生产过程中,从原材料准备到最终产品的制造过程。
它是一个复杂而精细的过程,需要各种设备和技术的协调配合。
本文将详细介绍工业产品生产工艺流程的各个环节。
一、原材料准备生产工艺流程的第一步是原材料的准备。
原材料可以是金属、塑料、玻璃、纺织品等各种材料,根据不同的产品需求进行选择。
在这一阶段,原材料需要进行采购、检验和储存,确保其质量和数量符合生产要求。
二、加工与成型在原材料准备完成后,下一步是加工与成型。
这个阶段通常包括以下几个步骤:1. 切割:将原材料根据产品设计要求进行切割,得到所需的形状和尺寸。
2. 成型:将切割后的原材料进行成型,可以通过冲压、铸造、注塑等方法实现。
这些方法根据不同的材料和产品类型而定。
3. 焊接/粘接:将成型后的零部件进行焊接或粘接,使其成为一个完整的产品结构。
三、加工与表面处理在加工与成型完成后,产品可能需要进行进一步的加工和表面处理。
这个阶段的目的是增加产品的功能性和美观性。
常见的加工与表面处理方法包括:1. 磨削:通过磨削工艺去除表面的毛刺和不平整,使产品表面更加光滑。
2. 镀层:在产品表面涂覆一层金属或非金属的薄膜,以增加产品的耐腐蚀性和美观性。
3. 喷涂:使用喷涂设备将颜料或涂层喷涂到产品表面,以增加产品的色彩和保护性能。
四、组装与调试在加工与表面处理完成后,产品的各个零部件需要进行组装和调试。
这个阶段的目的是将各个零部件组装成一个完整的产品,并确保其正常运行。
组装与调试通常包括以下几个步骤:1. 零部件组装:将各个零部件按照产品设计要求进行组装,使用螺丝、螺母、焊接等方法进行连接。
2. 功能测试:对组装完成的产品进行功能测试,确保各个部件的正常工作和产品的符合设计要求。
3. 调试:对产品进行调试,调整各个部件的位置和参数,使其达到最佳工作状态。
五、质量检验与包装在组装与调试完成后,产品需要进行质量检验和包装。
质量检验的目的是确保产品的质量符合标准和客户要求,包装的目的是保护产品在运输和储存过程中不受损坏。
加工生产工艺流程

加工生产工艺流程工艺流程是指将原材料经过一系列的加工操作和工艺控制,最终转化为成品的过程。
在加工生产中,正确的工艺流程对于保证产品质量、提高生产效率和降低成本非常重要。
本文将介绍一个典型的加工生产工艺流程,并详细描述每个步骤的操作和控制。
1. 原材料准备原材料准备是工艺流程的第一步,它决定了后续加工过程的质量和效率。
在这一步中,需要对原材料进行检验和筛选,确保其符合加工要求。
同时,还需要对原材料进行预处理,如清洗、除杂等,以确保原材料的纯净度和稳定性。
2. 切割和成型在这一步中,原材料将根据产品的要求进行切割和成型。
切割可以采用机械切割、水切割或激光切割等方式,成型可以采用冲压、挤压、铸造等方式。
在切割和成型过程中,需要根据产品的尺寸和形状要求进行精确控制,以确保产品的准确性和一致性。
3. 加工和加工控制加工是工艺流程中的核心步骤,它包括各种机械加工、热处理、表面处理等操作。
在加工过程中,需要根据产品的要求选择合适的加工设备和工艺参数,并进行严格的加工控制。
例如,对于机械加工,需要控制切削速度、进给量和切削深度等参数;对于热处理,需要控制加热温度、保温时间和冷却速度等参数。
通过合理的加工和加工控制,可以确保产品的精度和性能。
4. 组装和装配在这一步中,将加工好的零部件进行组装和装配,形成最终的成品。
组装和装配过程需要严格按照产品的装配图和工艺要求进行操作,确保每个零部件的正确安装和连接。
同时,还需要进行必要的调试和检验,以确保成品的功能和质量。
5. 检验和质量控制检验和质量控制是工艺流程中的重要环节,它用于验证产品是否符合设计要求和标准。
在这一步中,需要进行各种检验和测试,如尺寸检验、力学性能测试、化学成分分析等。
同时,还需要建立完善的质量控制体系,包括质量管理制度、工艺标准和检验规程等,以确保产品质量的稳定性和可追溯性。
6. 包装和出厂在工艺流程的最后一步,将成品进行包装和出厂。
包装是保护产品免受损坏和污染的重要手段,需要根据产品的特点选择合适的包装材料和方式。
机械加工工艺流程解析

机械加工工艺流程解析机械加工是一种常见的制造方法,通过对原材料进行加工,将其转变为所需形状和尺寸的零部件。
机械加工广泛应用于各个行业,如汽车制造、航空航天、电子设备等。
本文将对机械加工的工艺流程进行详细解析,以帮助读者更好地了解该过程。
一、加工前准备在进行机械加工之前,需要进行一系列的准备工作。
首先,需要明确所要加工的零部件的图纸和技术要求。
图纸提供了所需零件的尺寸、形状和加工要求,而技术要求规定了所需零件的材料、硬度等特性。
在准备阶段,还需要选择合适的机械设备和工具,并进行检查和保养,确保其正常运行和良好的工作状态。
二、工艺规划在加工前,需要进行工艺规划。
工艺规划是确定加工过程中所需的切削工艺、切削参数和工艺流程的过程。
首先,需要根据零部件的形状和尺寸选择适当的切削工艺,如铣削、车削、钻削等。
然后,根据工件材料的硬度和性质,确定适当的切削参数,如切削速度、进给速度和切削深度等。
最后,制定详细的工艺流程,包括各道工序的顺序和具体操作方法。
三、材料准备机械加工过程中所用的原材料通常是金属材料,如钢、铝、铜等。
在材料准备阶段,需要对原材料进行切割和整形,使其符合加工要求。
切割通常采用剪切、锯切等方法进行,而整形则可以通过锻造、热处理等工艺来实现。
在进行材料准备时,需要检查原材料的质量和尺寸,确保其符合要求,并按照图纸上规定的零件尺寸进行切割和整形。
四、工艺操作工艺操作是机械加工的核心环节,包括各道工序的加工和加工参数的控制。
根据工艺流程,按照图纸上规定的形状和尺寸要求,通过机床和工具进行切削、钻削、铣削等操作,将原材料逐步加工成所需零部件。
在工艺操作中,需要注意操作的安全性和精确性,确保零部件的质量和加工效率。
五、加工检验加工完成后,需要对零部件进行检验。
检验的目的是验证零部件的形状、尺寸和质量是否符合要求。
检验常用的方法有量具测量、光学测量、三坐标测量等。
在进行检验时,需要使用适当的检测工具和仪器,并按照图纸上的要求进行检验。
生产工艺流程(3篇)
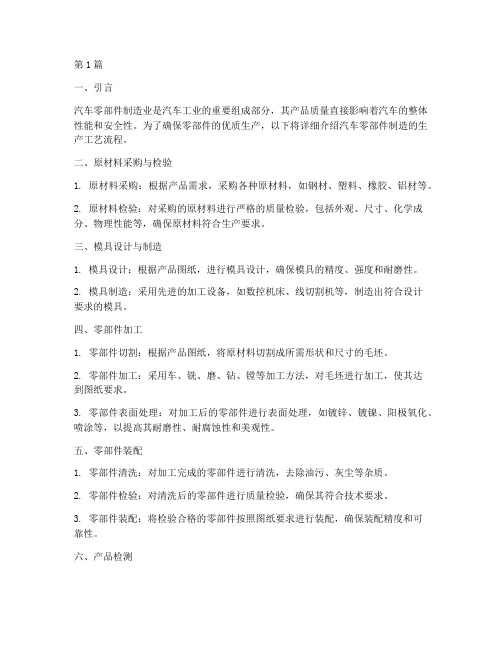
第1篇一、引言汽车零部件制造业是汽车工业的重要组成部分,其产品质量直接影响着汽车的整体性能和安全性。
为了确保零部件的优质生产,以下将详细介绍汽车零部件制造的生产工艺流程。
二、原材料采购与检验1. 原材料采购:根据产品需求,采购各种原材料,如钢材、塑料、橡胶、铝材等。
2. 原材料检验:对采购的原材料进行严格的质量检验,包括外观、尺寸、化学成分、物理性能等,确保原材料符合生产要求。
三、模具设计与制造1. 模具设计:根据产品图纸,进行模具设计,确保模具的精度、强度和耐磨性。
2. 模具制造:采用先进的加工设备,如数控机床、线切割机等,制造出符合设计要求的模具。
四、零部件加工1. 零部件切割:根据产品图纸,将原材料切割成所需形状和尺寸的毛坯。
2. 零部件加工:采用车、铣、磨、钻、镗等加工方法,对毛坯进行加工,使其达到图纸要求。
3. 零部件表面处理:对加工后的零部件进行表面处理,如镀锌、镀镍、阳极氧化、喷涂等,以提高其耐磨性、耐腐蚀性和美观性。
五、零部件装配1. 零部件清洗:对加工完成的零部件进行清洗,去除油污、灰尘等杂质。
2. 零部件检验:对清洗后的零部件进行质量检验,确保其符合技术要求。
3. 零部件装配:将检验合格的零部件按照图纸要求进行装配,确保装配精度和可靠性。
六、产品检测1. 检测项目:根据产品特性,进行相应的检测项目,如尺寸检测、性能检测、外观检测等。
2. 检测设备:采用先进的检测设备,如三坐标测量仪、力学性能试验机、高精度转速仪等,确保检测结果的准确性。
七、产品包装与运输1. 产品包装:将检验合格的产品进行包装,确保产品在运输过程中不受损坏。
2. 产品运输:采用合适的运输方式,将产品运输至客户指定地点。
八、售后服务1. 售后咨询:为客户提供产品使用、维护等方面的咨询服务。
2. 售后维修:对客户反馈的问题,及时进行维修,确保产品质量。
九、总结汽车零部件制造的生产工艺流程涉及多个环节,包括原材料采购与检验、模具设计与制造、零部件加工、零部件装配、产品检测、产品包装与运输以及售后服务。
产品生产工艺流程(3篇)
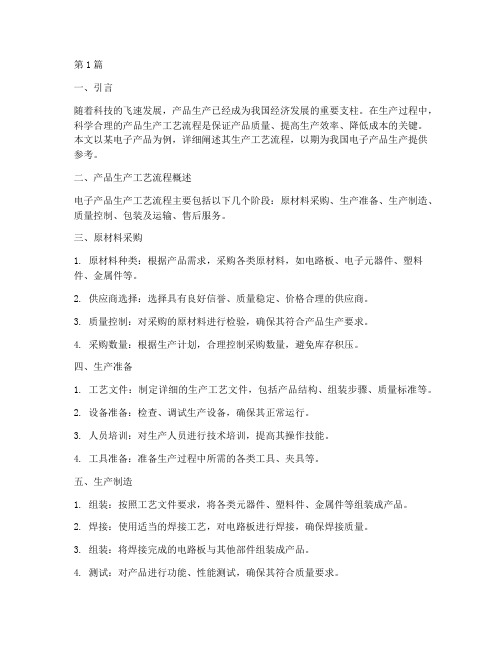
第1篇一、引言随着科技的飞速发展,产品生产已经成为我国经济发展的重要支柱。
在生产过程中,科学合理的产品生产工艺流程是保证产品质量、提高生产效率、降低成本的关键。
本文以某电子产品为例,详细阐述其生产工艺流程,以期为我国电子产品生产提供参考。
二、产品生产工艺流程概述电子产品生产工艺流程主要包括以下几个阶段:原材料采购、生产准备、生产制造、质量控制、包装及运输、售后服务。
三、原材料采购1. 原材料种类:根据产品需求,采购各类原材料,如电路板、电子元器件、塑料件、金属件等。
2. 供应商选择:选择具有良好信誉、质量稳定、价格合理的供应商。
3. 质量控制:对采购的原材料进行检验,确保其符合产品生产要求。
4. 采购数量:根据生产计划,合理控制采购数量,避免库存积压。
四、生产准备1. 工艺文件:制定详细的生产工艺文件,包括产品结构、组装步骤、质量标准等。
2. 设备准备:检查、调试生产设备,确保其正常运行。
3. 人员培训:对生产人员进行技术培训,提高其操作技能。
4. 工具准备:准备生产过程中所需的各类工具、夹具等。
五、生产制造1. 组装:按照工艺文件要求,将各类元器件、塑料件、金属件等组装成产品。
2. 焊接:使用适当的焊接工艺,对电路板进行焊接,确保焊接质量。
3. 组装:将焊接完成的电路板与其他部件组装成产品。
4. 测试:对产品进行功能、性能测试,确保其符合质量要求。
5. 后处理:对产品进行外观处理、防潮处理等。
六、质量控制1. 质量检验:在生产过程中,对每个环节的产品进行检验,确保其质量。
2. 质量控制点:设置关键质量控制点,如焊接、组装、测试等环节。
3. 不良品处理:对不合格产品进行返工、报废或修复。
4. 质量改进:根据质量反馈,对生产工艺进行改进,提高产品质量。
七、包装及运输1. 包装:按照产品特点,选用合适的包装材料,确保产品在运输过程中不受损坏。
2. 运输:选择可靠的物流公司,确保产品安全、及时送达客户。
加工工艺流程
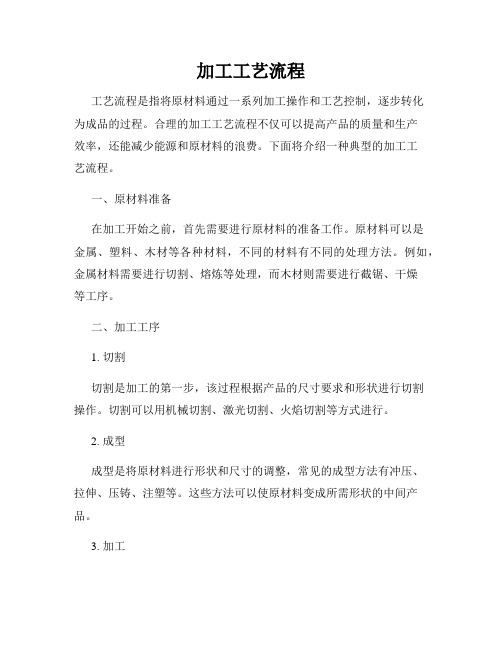
加工工艺流程工艺流程是指将原材料通过一系列加工操作和工艺控制,逐步转化为成品的过程。
合理的加工工艺流程不仅可以提高产品的质量和生产效率,还能减少能源和原材料的浪费。
下面将介绍一种典型的加工工艺流程。
一、原材料准备在加工开始之前,首先需要进行原材料的准备工作。
原材料可以是金属、塑料、木材等各种材料,不同的材料有不同的处理方法。
例如,金属材料需要进行切割、熔炼等处理,而木材则需要进行截锯、干燥等工序。
二、加工工序1. 切割切割是加工的第一步,该过程根据产品的尺寸要求和形状进行切割操作。
切割可以用机械切割、激光切割、火焰切割等方式进行。
2. 成型成型是将原材料进行形状和尺寸的调整,常见的成型方法有冲压、拉伸、压铸、注塑等。
这些方法可以使原材料变成所需形状的中间产品。
3. 加工加工是针对成型产品进一步进行精细加工和处理的过程。
常见的加工方法有铣削、车削、刨削、钻孔等,可根据产品的要求进行选择。
4. 焊接与焊接控制对于由多个零部件组成的产品,需要进行焊接操作。
焊接是将不同材料的零部件通过熔化和凝固的方式进行连接,可使用电弧焊、气焊、激光焊等方法。
5. 表面处理表面处理是提高产品表面质量和增加附加功能的工序。
例如,金属制品可以进行抛光、镀铬、镀锌等表面处理,塑料制品可以进行喷涂、涂装等表面处理。
6. 装配与检验装配是将各个零部件按照设计要求进行组装的过程,检验是确保产品质量的关键环节。
在装配过程中,需要进行结构的检查和功能的测试,确保产品的性能符合要求。
三、质量控制在整个加工工艺流程中,质量控制非常重要。
通过建立质量控制体系和制定相应的标准,可以及时发现和纠正工艺上的问题,以确保产品的质量。
1.过程控制在加工过程中,需要对每个环节进行严格的控制,包括温度、压力、时间等参数的监测和调整。
通过实施过程控制,可以保证产品的稳定性和一致性。
2.实时监测利用现代化的仪器设备和传感器,对关键参数进行实时监测和记录。
通过实时监测,可以及时掌握过程中的变化,避免出现问题。
零件加工工艺步骤

零件加工工艺步骤在零件加工过程中,正确的工艺步骤是确保产品质量和提高生产效率的关键。
本文将介绍零件加工的一般工艺步骤,以帮助读者更好地理解这一过程。
1. 设计和规划在加工工艺开始之前,首先需要进行设计和规划。
根据产品的要求,绘制出详细的零件图纸,并确定所需的材料和机械设备。
同时,考虑到生产成本和时间,确保设计方案的可行性和优化。
2. 材料准备在加工过程中,正确的材料选择和准备是至关重要的。
根据零件图纸要求,选择适当的材料,并确保其质量和供应。
材料准备包括切割、锻造、热处理等步骤,以确保材料达到所需的硬度和强度。
3. 加工工序在零件加工的实际步骤中,通常会包括以下几种工序:3.1 车削车削是一种通过旋转工件并用刀具去除材料的工艺。
它可以用于加工各种形状的零件,如轴、套筒等。
车削过程中需要根据零件图纸操作机床,实现精确的尺寸和表面质量要求。
3.2 铣削铣削是一种通过旋转刀具进行切削的工艺。
它可以用于加工平面、曲面以及一些特殊形状的零件。
铣削过程中需要进行刀具的选型和刀具路径的规划,以确保加工出理想的形状和尺寸。
3.3 钻削钻削是一种通过旋转刀具进行穿孔的工艺。
它常用于加工孔洞、螺纹等零件。
钻削前需要进行定位和固定零件,根据图纸确定孔洞的位置和尺寸,然后进行钻孔操作。
3.4 焊接焊接是一种通过高温熔化填充材料使两个零件连接的工艺。
焊接常用于加工金属零件,在零件加工过程中常涉及到的是电弧焊和气体保护焊等方法。
4. 表面处理在零件加工完成之后,有时需要进行表面处理以改善零件的外观和耐腐蚀性能。
常见的表面处理包括电镀、喷涂和抛光等。
根据零件的要求选择合适的表面处理方法,并进行相应的操作。
5. 检验和质量控制最后,零件加工的工艺步骤还包括检验和质量控制。
在每个加工步骤完成后,应进行相应的检验,确保零件尺寸和质量满足要求。
同时,建立完善的质量控制体系,监控整个加工过程的质量,并及时进行调整和改进。
总结零件加工工艺步骤的正确执行对保证产品质量和生产效率至关重要。
零件加工工艺流程图

零件加工工艺流程图零件加工工艺流程图主要是指将原材料通过一系列加工工艺和工序加工成最终产品的过程。
下面是一个典型的零件加工工艺流程图,包含以下几个关键工艺和工序。
第一步:原材料准备1. 初步检查原材料质量和规格是否符合要求;2. 使用机械设备将原材料进行截断,确保尺寸符合工艺要求;3. 为了提高材料的切削性能,可以对原材料进行火焰热处理。
第二步:粗加工1. 使用加工中心或车床将原材料进行初步加工,包括车削、铣削、钻孔等工序;2. 根据设计要求,进行粗磨和刨削,以形成基本的几何形状;3. 进行相关表面处理,如打磨、抛光等。
第三步:精加工1. 进一步进行车削、铣削、钻孔等精细加工工序;2. 对产品进行精磨和研磨,以提高几何和尺寸精度;3. 进行光洁度检测和表面质量检查。
第四步:热处理1. 对零件进行热处理,包括淬火、回火、退火等工艺;2. 通过热处理改变零件的物理和化学性质,提高其强度和耐磨性。
第五步:表面处理1. 零件经过镀铬、电镀、镀镍等表面处理;2. 通过表面处理提高零件的抗腐蚀性能、耐磨损性能等。
第六步:装配和焊接1. 将多个零件进行装配,使用螺栓、焊接等方法进行固定;2. 进行装配过程中的调试和检测,确保零件装配正确。
第七步:质量检验1. 对加工完成的零件进行质量检验,包括尺寸检测、硬度测试、金属组织分析等;2. 检查零件表面的光洁度、毛刺等。
第八步:包装和运输1. 将加工完成的零件进行包装,以防止零件在运输过程中受到损坏;2. 运输零件到目的地。
以上是一个典型的零件加工工艺流程图,包括原材料准备、粗加工、精加工、热处理、表面处理、装配和焊接、质量检验、包装和运输等关键工艺和工序。
不同的零件加工流程可能会有所不同,但大致流程是相似的。
通过合理的工艺流程和工序控制,可以确保零件加工的质量和精度,提高零件的整体性能和寿命。
零件生产工艺过程基本知识

零件生产工艺过程基本知识零件生产工艺是指将原材料加工成符合设计要求的零件的过程。
在制造业中,零件生产工艺是非常重要的环节,它直接影响着产品的质量、成本和交货周期。
因此,了解零件生产工艺的基本知识对于提高生产效率和产品质量至关重要。
1. 材料选择零件生产工艺的第一步是材料选择。
不同的零件需要选择不同的材料,常见的材料包括金属、塑料、陶瓷等。
在选择材料时,需要考虑零件的使用环境、负荷、耐磨性等因素,以确保零件具有良好的性能和耐久性。
2. 设计在确定了材料之后,需要进行零件的设计。
设计师需要根据零件的功能要求和使用环境,绘制出详细的零件图纸。
在设计过程中,需要考虑到材料的加工性能、成本和生产工艺等因素,以确保设计的合理性和可制造性。
3. 加工工艺加工工艺是零件生产的核心环节,它包括多种加工方法,如铣削、车削、钻孔、磨削等。
不同的零件需要采用不同的加工工艺,以确保零件的精度和表面质量。
在加工过程中,需要根据零件的特点和要求,选择合适的工艺参数和加工设备,以确保加工质量和效率。
4. 检测与质量控制在零件生产过程中,需要进行多次检测和质量控制,以确保零件的质量符合设计要求。
常见的检测方法包括三坐标测量、硬度测试、表面粗糙度检测等。
通过严格的质量控制,可以及时发现和解决生产过程中的质量问题,确保零件的合格率和稳定性。
5. 表面处理一些零件需要进行表面处理,以提高其耐腐蚀性、耐磨性和美观性。
常见的表面处理方法包括镀锌、喷涂、阳极氧化等。
通过合适的表面处理,可以提升零件的使用寿命和外观质量。
6. 组装最后一步是零件的组装。
在组装过程中,需要将各个零件按照设计要求进行组合,以形成最终的产品。
在组装过程中,需要注意零件之间的配合精度和间隙,以确保产品的功能和性能。
总之,零件生产工艺是一个复杂而严谨的过程,它涉及材料选择、设计、加工工艺、检测与质量控制、表面处理和组装等多个环节。
只有在每个环节都做到精益求精,才能生产出高质量、高性能的零件和产品。
零件加工工艺流程_零件加工工序过程【详解(参考模板)

零件加工工艺流程_零件加工工序过程内容来源网络,由深圳机械展收集整理!零件加工工艺过程的基本知识在制造生产过程中,由于零件的要求和生产条件等不同,其制造工艺方案也不相同。
相同的零件采用不同的工艺方案生产时,其生产效率、经济效益也是不相同的。
在确保零件质量的前提下,拟定具有良好的综合技术经济效益、合理可行的工艺方案的过程称为零件的工艺过程设计。
一、生产过程和工艺过程1. 生产过程由设计图纸变为产品,要经过一系列的制造过程。
通常将原材料或半成品转变成为产品所经过的全部过程称作生产过程。
生产过程通常包括:(1)技术准备过程包括产品投产前的市场调查、预测、新产品鉴定、工艺设计、审查等。
(2) 或工艺过程指直接改变原材料半成品的尺寸、形状、表面的相互位置、表面粗糙度或性能,使之成为成品的过程。
例如液态成形、塑变成形、焊接、粉末成形、切削加工、热处理、表面处理、装配等,都属于工艺过程。
将合理的工艺过程编写成用以指导生产的技术文件,这份技术文件称作工艺规程。
(3)辅助生产过程指为了基本生产过程的正常进行所必须的辅助生产活动。
(4)生产服务过程指原材料的组织、运输、保管、储存、供应及产品包装、销售等过程。
2. 工艺过程的组成零件的切削加工工艺过程由许多工序组合而成,每个工序又由工位、工步、走刀和安装组成。
(1)工序指在一台机床上或在同一个工作地点对一个或一组工件连续完成的那部分工艺过程。
划分工序的依据是工作地点是否变化和工作是否连续。
图2-1所示阶梯轴的加工工艺过程见表2-1。
表2一1工序的划分,是由一个人在一台车床上连续完成车两端面、钻两顶尖孔后,便换一个工件加工,重复以上内容,则这部分工艺过程为一个工序。
该人又在同一台车床上连续完成粗车各外圆、半精车各外圆、倒角后,便换一个工件加工,重复以上内容,则这部分工艺过程又为一个工序。
如果是由一个人在一台车床上连续完成车两端面、钻两顶尖孔、粗车各外圆、半精车各外圆、倒角后再换第二个工件重复这些内容,则这部分工艺过程是一个工序,而不是两个工序。
机械零部件制造工艺流程分析

机械零部件制造工艺流程分析随着科技的不断进步,机械零部件在各个行业中扮演着重要的角色。
机械零部件的制造工艺流程对于产品的质量和性能有着至关重要的影响。
因此,深入分析机械零部件的制造工艺流程,对于提高生产效率和产品质量具有重要意义。
一、材料准备阶段机械零部件的制造工艺流程开始于材料的准备阶段。
首先,根据零部件的设计要求,选择适合的材料。
常见的机械零部件材料包括金属和非金属材料。
选择合适的材料可以确保零部件的强度和耐久性。
在获得所需材料后,需要进行材料的切割和锯割。
这一步骤旨在将材料切割成适当的形状和尺寸,为后续工艺步骤做好准备。
二、加工制造阶段1. 数控加工数控加工是机械零部件制造过程中常用的一种加工方式。
通过数控机床,可以实现对零部件进行精确的加工和切割。
数控加工具有高精度、高效率的特点,能够满足各种复杂零部件的加工需求。
2. 热处理在制造过程中,一些机械零部件需要进行热处理,以改善材料的性能。
常见的热处理方式包括淬火、回火和表面处理。
热处理可以提高零部件的硬度、强度和耐磨性能,从而增加其使用寿命。
3. 精加工精加工是机械零部件制造工艺流程中的关键步骤之一。
通过精密的切削和加工技术,可以使零部件的尺寸和形状达到设计要求。
常见的精加工方式包括车削、铣削、磨削和钻孔等。
精加工可以提高零部件的精度和表面质量。
4. 装配和检验在零部件制造的最后阶段,需要进行装配和检验工作。
装配是将各个加工好的零部件组装成完整的机械零部件的过程。
在装配过程中,需要确保各个零部件的尺寸和配合精度满足要求。
完成装配后,需要进行零部件的检验。
检验的目的是验证零部件的质量和性能是否符合设计要求。
常用的检验方法包括尺寸检验、外观检验和功能检测等。
三、表面处理阶段为了提高零部件的防腐蚀性和美观度,常常需要进行表面处理。
常见的表面处理方式包括电镀、喷涂和阳极氧化等。
表面处理可以提高零部件的抗氧化能力和耐久性,同时赋予零部件不同的外观效果。
制造工艺流程 - 详解产品制造加工的工艺流程

制造工艺流程 - 详解产品制造加工的工艺流程简介制造工艺流程是指将原材料转化为最终产品的一系列步骤和方法。
它涵盖了从设计到生产,再到包装和交付的整个过程。
本文将详细介绍产品制造加工的工艺流程,并解释每个环节的重要性和相关技术。
原材料准备在制造过程中,首先需要准备合适的原材料。
原材料可以是金属、塑料、木材等各种不同类型的物质。
选择合适的原材料至关重要,因为它们将直接影响产品的质量和性能。
在这一阶段,通常会进行采购、检验和储存等操作。
设计与建模在有了合适的原材料后,下一步就是进行产品设计与建模。
这涉及到使用CAD 软件等工具进行三维模型设计,并确定所需零部件及其尺寸、形状等特征。
通过建立精确而可靠的模型,可以更好地规划后续加工步骤。
切削加工切削加工是将原材料切割或去除多余部分来获得所需形状和尺寸的加工方法。
常见的切削加工包括铣削、刨削、车削等。
这些加工方法都需要使用刀具来实现,通过控制刀具在原材料上的运动轨迹来达到特定的形状要求。
成型加工除了切削加工,成型加工也是常见的一种制造方式。
它通过将原材料置于模具中,并施加压力或温度来使其变形为所需形状。
常见的成型加工方法有注塑成型、冲压成型等。
这些方法适用于不同类型的产量和复杂度要求。
焊接与连接在某些情况下,产品需要不同部分之间的连接。
这可能涉及到焊接、螺栓固定、黏合等技术。
焊接是将两个或多个零部件通过熔化边缘并让它们冷却后相互结合的过程。
表面处理表面处理是为了提高产品外观和性能而进行的一系列过程。
其中包括喷涂、电镀、阳极氧化等,以增强产品的耐久性、抗腐蚀性或美观性。
装配与调试在完成各个零部件的加工后,接下来是将它们组装在一起,并确保产品能够正常运行。
这通常需要进行一些调试和测试,以验证产品性能是否符合要求。
包装与交付最后一个环节是对成品进行包装和交付。
适当的包装有助于保护产品免受损坏,并提供方便的储存和运输方式。
交付可以通过不同方式进行,如送货、邮寄、航空运输等,取决于生产规模和客户需求。
典型零件加工工艺过程PPT课件

.
22
CA6140. 车床主轴图
23
主轴的机械加工工艺过程
➢主轴加工工艺过程制订的依据 主轴的结构;技术要求;生产批量;
设备条件 ➢主轴加工工艺过程 批量:大批;材料:45钢;毛坯:模
锻件
.
24
➢工艺过程: 分为三个阶段(参见表5-5):
粗加工:工序 1~6 半精加工:工序 7~13(7为预备) 精加工:工序 14~26(14为预备)
.
63
箱孔与孔的位置精度 引起轴安装歪斜,致使主轴径向跳动 和轴向窜动,加剧轴承磨损 同一轴线上各孔的同轴度误差 孔端面对轴线垂直度误差
.
64
孔和平面的位置精度
主要是规定主要孔和主轴箱安装基 面的平行度
主要平面的精度
影响主轴箱与床身的连接刚度
规定底面和导向面必须平直和相互 垂直
平面度、垂直度公差等级为5级
第二节
典型零件加工 工艺过程
机械制造工程——第五章
.
1
一、轴(杆)类零件的加工
1.轴类零件的分类、技术要求
➢轴类零件的作用 支撑传动零件; 承受载荷; 传递扭矩。
.
2
➢轴类零件的特点 长度大于直径; 加工表面为内外圆柱面、圆锥面、
螺纹、花键、沟轴 阶梯轴 空心轴 异形轴(曲轴、齿轮轴、偏心轴、
.
38
➢加工顺序的安排和工序的确定
三种方案
粗加工外圆→钻深孔→精加工外圆→ 粗加工锥孔→精加工锥孔
粗加工外圆→钻深孔→粗加工锥孔→ 精加工锥孔→精加工外圆
粗加工外圆→钻深孔→粗加工锥孔→ 精加工外圆→精加工锥孔
.
39
工序确定的两个原则
➢工序中所用的基准应在该工序前加工
完整产品部件生产加工工艺流程
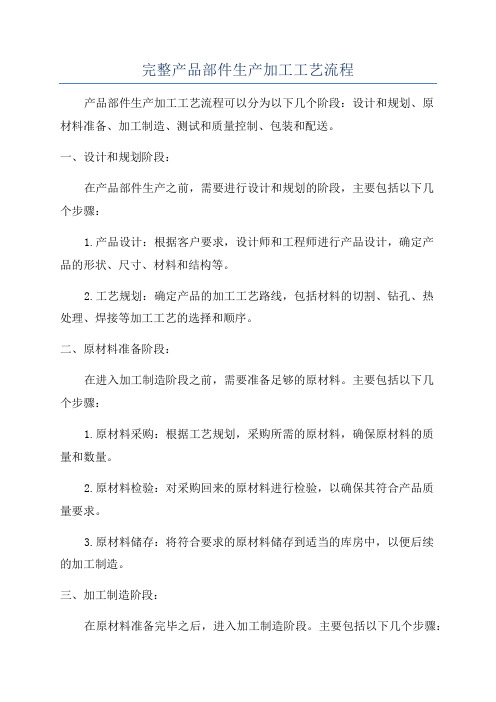
完整产品部件生产加工工艺流程产品部件生产加工工艺流程可以分为以下几个阶段:设计和规划、原材料准备、加工制造、测试和质量控制、包装和配送。
一、设计和规划阶段:在产品部件生产之前,需要进行设计和规划的阶段,主要包括以下几个步骤:1.产品设计:根据客户要求,设计师和工程师进行产品设计,确定产品的形状、尺寸、材料和结构等。
2.工艺规划:确定产品的加工工艺路线,包括材料的切割、钻孔、热处理、焊接等加工工艺的选择和顺序。
二、原材料准备阶段:在进入加工制造阶段之前,需要准备足够的原材料。
主要包括以下几个步骤:1.原材料采购:根据工艺规划,采购所需的原材料,确保原材料的质量和数量。
2.原材料检验:对采购回来的原材料进行检验,以确保其符合产品质量要求。
3.原材料储存:将符合要求的原材料储存到适当的库房中,以便后续的加工制造。
三、加工制造阶段:在原材料准备完毕之后,进入加工制造阶段。
主要包括以下几个步骤:1.加工准备:根据工艺规划,准备所需的设备、工具和人员,并进行必要的调试和检验。
2.加工加工:根据工艺规划,进行材料的切割、钻孔、热处理、焊接等加工工艺的操作,制造产品部件的形状和结构。
3.表面处理:对制造好的产品部件进行抛光、喷涂、电镀等表面处理工艺,以提高产品的外观和耐腐蚀性。
4.组装测试:将不同的部件进行组装,并进行必要的测试和调试,确保产品的功能和性能达到要求。
四、测试和质量控制阶段:在加工制造完毕之后,需要进行测试和质量控制,以确保产品的质量和可靠性。
主要包括以下几个步骤:1.功能测试:对产品进行功能测试,确保产品能够正常工作,并满足客户的需求。
2.质量检验:对产品进行质量检验,包括外观检查、尺寸精度检测、材料强度测试等,以确保产品的质量符合标准和要求。
3.整理包装:对合格的产品进行整理和包装,以便于运输和配送。
五、包装和配送阶段:在测试和质量控制完毕之后,产品需要进行包装和配送。
1.包装准备:准备适当的包装材料和容器,保护产品免受损坏和污染。
零件的加工工艺流程

零件的加工工艺流程零件的加工工艺流程是指将原材料按照要求进行加工和组装,制造成最终的零件产品的一系列工艺流程。
下面以某个零件的加工工艺流程为例,介绍零件加工的大致步骤。
首先,进行材料的选择。
根据零件的要求和使用环境,选择合适的材料进行加工。
材料的选择要考虑到强度、耐磨性、耐腐蚀性等因素,确保最终产品的质量和可靠性。
第二步,进行原材料的切割。
根据零件的尺寸和形状要求,使用切割设备(如剪切机、钢板切割机等)将原材料切割成适当的尺寸。
这一步骤需要精确测量和准确操作,确保切割出的原材料大小和形状与设计要求相符。
第三步,进行零件的粗加工。
在粗加工阶段,使用机床(如车床、铣床、镗床等)对原材料进行粗加工,以得到大致的形状和尺寸。
粗加工需要根据设计图纸进行操作,控制好工件的尺寸和表面质量。
第四步,进行零件的精加工。
在精加工阶段,使用精密机床(如磨床、铣床等)对零件进行加工,以获得更高的精度和表面质量。
精加工通常需要采用多道工序,如车削、钻孔、镗孔、镗座等,确保零件的尺寸、平整度和精度达到要求。
第五步,进行零件的热处理。
针对不同的材料性质和零件要求,在加工过程中可能需要进行热处理。
热处理过程通常包括淬火、回火、退火、正火等,以改变材料的组织结构和性能,提高零件的强度和硬度。
第六步,进行零件的表面处理。
为了提高零件的耐腐蚀性、表面光洁度和装饰效果,常常需要进行表面处理。
常见的表面处理方法包括镀锌、电镀、喷涂、抛光、喷砂等,使零件的外观更加美观并且延长使用寿命。
第七步,进行零件的装配。
在零件加工的最后阶段,根据设计要求和生产流程,使用合适的方法将零件组装起来。
组装过程需要仔细分析和操作,保证零件之间的配合度和安装质量。
最后,对零件加工的质量进行检测和检验。
通过检测和检验,确保加工出的零件满足设计要求和产品标准。
常用的检测方法包括尺寸测量、硬度测试、化学检验、无损检测等。
以上就是零件加工的大致流程,不同类型和要求的零件加工过程可能会有所不同。
制造生产工艺流程

制造生产工艺流程一、引言制造生产工艺流程是指在产品制造过程中,根据工艺要求和产品特性,按照一定的顺序和方法进行加工加工和组装的过程。
该流程的设计和执行对于保证产品质量、提高生产效率至关重要。
本文将详细介绍一个通用的制造生产工艺流程。
二、装配工艺1. 零部件准备在开始装配之前,需要准备好所有所需的零部件。
这包括对零部件进行清洁和检查,确保其质量符合要求。
同时,需要确保零部件数量准确并分类妥善,以方便后续的装配工作。
2. 组装顺序根据产品的结构和装配要求,确定装配的顺序。
通常情况下,先进行主要部件的装配,再进行次要部件的装配,最后进行附件的装配。
在进行装配时,要注意不同部件之间的配合精度和装配间隙,确保装配的正确性和紧密性。
3. 装配工具和设备根据产品的特性和装配要求,选择适当的装配工具和设备。
这些工具和设备应具备正确的功能和性能,以提高装配效率和质量。
同时,要确保工具和设备的操作人员具备相应的技能和经验,以避免人为因素对装配过程的影响。
4. 装配工艺控制在装配过程中,进行严格的工艺控制是非常重要的。
这包括对每个装配工序进行监控和记录,及时发现和解决可能出现的问题。
同时,要定期进行工艺评审和改进,以提高整体的装配质量和效率。
三、加工工艺1. 加工设备准备在开始加工之前,需要准备好相应的加工设备。
这些设备应具备符合产品要求的精度和稳定性,以确保加工的准确性和一致性。
同时,要对加工设备进行维护和保养,确保其正常运行和安全使用。
2. 加工工序安排根据产品的结构和加工要求,确定加工的工序和顺序。
在进行加工时,要根据工序要求和产品特性,选择适当的加工方法和工艺参数。
同时,要确保各道工序之间的衔接和协调,以避免出现加工误差和质量问题。
3. 加工工艺控制在加工过程中,进行严格的工艺控制是必要的。
这包括对每个加工工序进行监控和记录,及时发现和解决可能出现的问题。
同时,要定期进行加工工艺评审和改进,以提高整体的加工质量和效率。
- 1、下载文档前请自行甄别文档内容的完整性,平台不提供额外的编辑、内容补充、找答案等附加服务。
- 2、"仅部分预览"的文档,不可在线预览部分如存在完整性等问题,可反馈申请退款(可完整预览的文档不适用该条件!)。
- 3、如文档侵犯您的权益,请联系客服反馈,我们会尽快为您处理(人工客服工作时间:9:00-18:30)。
产品部件生产加工工艺流程一、钢制部分生产工艺流程原材料——下料——校料——去毛刺——弯管——去茬——钻孔——焊接——磨型——校正半成品——质检——酸洗除锈——水洗——磷化——烘干——喷塑——烘干固化——下线——检验——包装——入库设备选材标准本次所投标的设备能以最安全、最持久、最稳定、最美观的使用,必须做好原材料的选配,遵循国标,达到设备的安全性,涂层理化性能、最大载荷性能等。
必须遵循以下几点:1、钢板的材质必须达到国家规定的理化性能,应优先选取优质板材。
2、设备用料应达到厚度合理搭配,即提高产品性能又降低成本,使设备发挥最大的经济效益。
3、设备零部件选材应以垂直方向厚,水平方向薄,原则合理搭配。
即不影响应强度,又减轻了设备的和重量,增加了美观。
4、设备外表涂层应以化学物质组成,为减少对人体的伤害,选用由国家质量体系认证的厂家生产。
产品技术规范及标准1.产品技术条件:GB/T13667.3-922.工件涂装前磷化处理技术条件:GB/T68073.涂膜附着力测试法: :GB/T1720-19794.漆膜耐冲击性测试法: :GB/T1732-19935.漆膜的划格实验: :GB/T9286-19986.家具力学性能实验稳定性::GB/T10357.4-19897.木家具通用技术条件:GB/T3324-20088.建筑内部家具设计防火规范:GB 50222-19959、家具质量检验及质量评定:QB/T1950-1952-9410、家具绿色环保执行标准:GB/T2002-7-111、室内装修材料溶剂型木器涂料中有害物质限量:GB18581-200112、室内装修材料胶粘剂中有害物质限量:GB 18583-200113、室内装饰装修材料、木家具中有害物质限量:GB 18584-200114、金属家具通用技术条件:GB/T3325-199515、软体家具、沙发质量检验及分等综合评定:QB/T1952-1-9916、家具、桌、椅、凳类主要尺寸:GB/T3326-199717、家具、柜类主要尺寸:GB/T3327-199718、家具五金、拉手安装尺寸:QB/T1241-1991磷化喷塑工艺介绍(一)、磷化因钢板、钢管在制造和储运过程中,都加入有防护油,在生产成产品过程中其表面也都不可避免地沾有各种污物,如:润滑油,金属氧化层,与人接触而带来的汗渍以及灰尘等。
这些污物的存在,对涂装工艺十分不利,并将最终影响涂层的内在综合质量。
本公司全自动9工位喷淋式前处理机组全长50米,就是为了清洗钢板上的各种污物和增强金属基体自身的防护能力,增加与涂层的结合力。
(磷酸盐处理)确保金属制品的综合质量和耐用性,保证产品达到国家《GB6807-86涂装腔作势前的表面处理技术落后要求》标准。
磷化工艺流程:热水洗--预脱脂---脱脂---水洗--水洗表面---调整磷酸盐----处理水洗---纯水洗。
封闭式9工位前处理机组,能在一个全封闭的空间内自动连续完成工件的清洗、调整、磷化处理,克服了手工作业质量无稳定之弊端,保证了各种质量指标的稳定性和可靠性。
热水洗起到预先湿润工件上的固态油脂和浮锈以及洗掉工件上的灰尘,为工件清除出党洗彻底打下了基础。
预脱脂、脱脂。
在经过三工位的药液清洗(在喷淋的机械冲击和药物的双重作用下),能彻底清洗掉工件上的各种油脂和腐蚀物,温度由电子仪器自动跟踪检测,自动补偿,始终保证药液的工艺温度,确保清洗质量的稳定。
四和五工位为大小工位清洗。
工件经脱脂后,其表面带有的残留药液(碱),经中和清洗后为七工位的磷酸盐处理奠定了坚实的基础。
表面调整:在脱脂处理中,对金属基本体表面的化学成分,物进性能在一不定的损坏。
为使钢铁有更高的物理性能和提高磷化膜的质量,利有胶体磷酸钛对磷化前的工件进行表面调整,使工件形成一层钛离子,使磷化膜致密,均匀,同时也提高了磷化速度。
磷酸盐磷化处理:使用锌系磷化液,工件经磷化,涂装后的防腐,附着力耐氧化性更好,符合GB6807-86国家标准。
水洗、纯水洗:工件经磷酸盐处理后,形成一层致密,均匀的磷化膜,但也带来了一定的磷酸盐残液,这将影响涂装后的质量。
经水洗掉残余的药液,但自来水也含有一定量的钙镁离子,沾附在工作的表面上,将会影响涂层的结合能力,所以用去离子纯水做最后的清洗,使工作的表面更清洁,使涂装后的工作综合质量更有保证,更可靠。
(二)、喷塑我公司采用先进的静电喷塑工艺涂装,其原理是粉末在压缩空气的吸引下,经喷枪使之雾化,当雾化后的粉末经过由喷枪产生的高压负电场时,粉末粒子就均匀地捕集到大量的负电荷。
因工件是接地的,这样就形成了正负相吸的原理,在此原理的作用下,粉末就均匀的积聚在工件上。
工件进入烘干后,经熔化、流平、固化、降温、下架。
经检验合格后,本工序结束。
表面涂装工艺流程产品工艺流程、技术规范缺陷分析及检验标准(一)、涂装前工件应符合一下列要求:1、检测验工件无弯曲、翘曲现象。
2、冲压件表面无毛刺、裂痕。
3、处表焊缝应磨光,无焊潭、飞溅等现象。
(二)、涂装工艺流程脱脂—水洗—除锈—水洗—表调—磷化—水洗—烘干—喷涂(三)、涂装前处理配槽用量及管理标准脱脂:yp4358 药剂0-100公斤总碱度18-22点时间6—10分钟水洗:工业用水碱污染≤0.5 水宜溢流时间1分钟水洗后快速进行下道工序。
除锈:yp5301 药剂1000公斤总碱度450-500点时间10-30分钟水洗:工业用水碱污染≤0.5 水宜溢流时间1分钟工件起落不小于5次表调:ypA药剂6公斤ph值7.5 时间1分钟磷化:yp3502 药剂180公斤30-35点NaoH1.6公斤FA0.6-1.5点yp131药剂6公斤AC3-5点时间3-5分钟水洗:工业用水质量中性不宜溢流时间1分钟烘干:温度不宜太高目的:快速脱水,以便磷化膜进入稳定状态。
(四)、前处理药剂补加及浓度调整除锈槽总酸度:每补加药剂yp-5301 20公斤总酸度上升一个点。
磷化槽总酸度:每补加yp-3502A药剂2-2.4公斤总酸度上升一个点,游离酸度每补加NaoH药剂0.12公斤FA下降0.1个点,每补加yp131药剂0.5公斤,AC上升1个点。
(五)、前处理技术规范除油除锈时,一般低温进行,油、锈严重的,应提高温度并延长时间。
熔液使用一段时间后,分析Fe2+含量,若不超过20g/t可补加新液,超过120g/t时更抽象新液。
水洗时应除尽除锈液并快速进行下道工序。
加表调剂时,要在空气搅拌下缓慢加入,使用过程中PH≤7时,加Na2co2每处理1000M2工件,应补加yp-A药剂0.5-1公斤。
磷化时必须控制酸比TA30:FA0.6,同时控制促进剂浓度3-5,并注意经常维护溶液清洁。
(六)、磷优膜的检验外观检验:检测工作磷化膜表面颜色呈现灰色到深灰色或采色,腊层结品致密、均匀、连续。
不应有表面严重挂灰,锈蚀或绿斑,磷化抗腐蚀性能检验。
点滴法:用酒精控试磷化过工件表面,待挥发完后,在15℃--25℃下,滴上数滴硫酸铜溶液,(CHSO4.5H2O 41g/1 Nacl 35g/l Hcl 13g/L三者混合使用),同时启动秒表,若在1分钟工件表面不泛红,说明磷化膜抗腐蚀性能合格。
经外观检验和抗腐蚀性能检验不合格的工件,需在除锈溶液中浸泡1-1.5分钟,在经水洗、表调后重新磷化。
(七)、工件磷化膜缺陷分析工件产生锈膜原因,酸比低、水洗不净,空气中暴露时间过长或水污染严重等。
工件产生采斑原因,促进剂浓度高或分布不均。
工件产生黑条纹或磷化膜黑而粗糙原因,促进剂浓度低.工件表面挂灰原因,糟液含渣量太多或糟液温度高,根据工件缺陷,应细心分析原因,补救时应按可能原因逐条排除。
(八)、表面喷涂(喷漆、喷塑)经检验磷化膜合格的工件,必须在磷化后16小时对其表面进行喷涂(喷漆、喷塑)。
对特殊加工序及特殊零件可适当延长间隔的时间,但此期间内工件的表面不得被污染或重新锈蚀。
喷涂后工件,必须经红外线烤炉烘烤,烘烤温度在90 -120度,时间不低于20分钟。
(九)、涂层的检验外观检验:目测平整光滑、色泽均匀一致;不应有挂流、漏底、剥落、伤痕、皱皮等现象。
物理性能检验:涂层应大于20um,涂层不应太厚,太厚既浪费材料又降低涂层的冲击强度,涂层光泽度应为60%-70%,近似亚光。
涂层硬度大于0.4。
涂层冲击强度大于0.4gb.m涂层附着力不低于2级。
抗腐蚀性能检验:取样板7*150 3件,用18号缝纫机针将少层划成12cm的交叉线(划痕深至钢铁基体,对角线步贯穿对角),划痕面朝上。
将样板隔开放入温度为15度、25度,溶液浓度3%NacL中,浸泡100小时。
100小时内,样板划痕两侧3mm以外无气泡产生。
100小时后样板划痕两侧3mm以外无锈迹、剥落、皱皮、变色等现象。
说明涂层抗腐蚀性能合格。
采购人可对本次产品的制作进行现场考察及对产品进行发货前的检测,本公司对采购人进行产品检测提供方便,我方在生产10组后,由采购人进行检验确认后,方能大规模进行生产,在生产开始后我方在每星期及时向采购人报送生产进度表,提供具体、真实、详细的生产数量、库存数量、发货数量等相关数字。
在供货期间,如果我方提供的产品质量不符合要求,采购人可拒绝支付货款,我方无条件调换符合质量要求的产品,如我方仍无法提供合格的产品,采购人和采购代理机构将有权取消其我方资格。
货物验收在货物到达安装地点后进行,验收时供需双方派员一起当场开箱验货,如发现货物短缺、质次、损坏、产地和规格不符等问题,应作详细记录,由我方立即无条件为需方调换或补齐,同时由我方承担因此而产生的一切后果。
安装的产品无刺激性气味,否则可一律退货。
投标产品全部安装完毕后,对全部产品进行检验。
二、木制部分生产工艺流程:东北桦木—旋切—分类—烘干—(自然烘干、人工烘干)—再整理—铺装—高频热压—检验—加工(锯边—铣边—磨边)—再检验—抛光—油漆—验收—包装—入库A、用料要求一般有以下几个标准:1、木材含水≤8-12%2、采用的树种质地应相似,针、阔叶材不得混合使用3、虫蛀材须经杀虫处理4、外表不得使用腐朽材,内部或封闭部位用材轻微腐朽,面积不超过零件面积的15%,深度不得超过材厚25%5、外表及存放物品部位的用材不得有树脂囊6、只要受力部位用材和斜纹程度超过20%的不得使用7、节子宽不超过可见宽1/3,直径不超过12mm,经修补加工后来不影响产品结构强度或外观的可以使用8、其他轻微材质缺陷,如裂纹等,应进行修补加工,不影响产品结构强度和外观的可以使用9、各种木质零件不得有贯通、裂缝B、木工要求一般有以下几个标准:1、产品外表的倒枝、圆角、圆线应均匀一致2、榫及自装配件、拆装产品零件结合应严密、牢固3、塞角、拉屉条支承零件等的结合应牢固。