精益管理的十大工具知识讲解
精益生产管理的十大改善工具
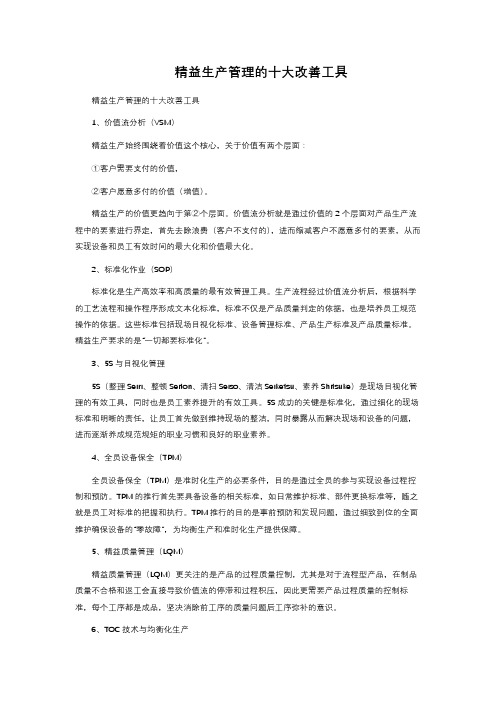
精益生产管理的十大改善工具精益生产管理的十大改善工具1、价值流分析(VSM)精益生产始终围绕着价值这个核心,关于价值有两个层面:①客户需要支付的价值,②客户愿意多付的价值(增值)。
精益生产的价值更趋向于第②个层面。
价值流分析就是通过价值的2个层面对产品生产流程中的要素进行界定,首先去除浪费(客户不支付的),进而缩减客户不愿意多付的要素,从而实现设备和员工有效时间的最大化和价值最大化。
2、标准化作业(SOP)标准化是生产高效率和高质量的最有效管理工具。
生产流程经过价值流分析后,根据科学的工艺流程和操作程序形成文本化标准,标准不仅是产品质量判定的依据,也是培养员工规范操作的依据。
这些标准包括现场目视化标准、设备管理标准、产品生产标准及产品质量标准。
精益生产要求的是“一切都要标准化”。
3、5S与目视化管理5S(整理Seiri、整顿Seiton、清扫Seiso、清洁Seiketsu、素养Shitsuke)是现场目视化管理的有效工具,同时也是员工素养提升的有效工具。
5S成功的关键是标准化,通过细化的现场标准和明晰的责任,让员工首先做到维持现场的整洁,同时暴露从而解决现场和设备的问题,进而逐渐养成规范规矩的职业习惯和良好的职业素养。
4、全员设备保全(TPM)全员设备保全(TPM)是准时化生产的必要条件,目的是通过全员的参与实现设备过程控制和预防。
TPM的推行首先要具备设备的相关标准,如日常维护标准、部件更换标准等,随之就是员工对标准的把握和执行。
TPM推行的目的是事前预防和发现问题,通过细致到位的全面维护确保设备的“零故障”,为均衡生产和准时化生产提供保障。
5、精益质量管理(LQM)精益质量管理(LQM)更关注的是产品的过程质量控制,尤其是对于流程型产品,在制品质量不合格和返工会直接导致价值流的停滞和过程积压,因此更需要产品过程质量的控制标准,每个工序都是成品,坚决消除前工序的质量问题后工序弥补的意识。
6、TOC技术与均衡化生产均衡化生产是准时化生产(JIT)的前提,也是消除过程积压和价值流停滞的有效工具。
精益管理十大利器之十课件

精益管理十大利器之十
34
要运用看板管理方式来提高生产效益时, 必须先具备4个必要的前提条件: 1、后工序向前工序领用方式 2、平准化生产 3、品质保证 4、严守看板运行的规则
精益管理十大利器之十
35
看板管理的规则
1、后工序在必需的时候,只按必需的数量,向前 工序去领取必需的物品。
a如果没有看板,领取一概不能进行。 b超过看板枚数的领取一概不能进行。 c看板必须附在被运送的实物上。 2、前工序仅生产被后工序领取数量的物品。 3、不合格品绝对不能送到后工序。 4、必须把看板枚数减小到最小程度。 5、看板必须适应小幅度的需求变化。(通过看板 对生产进行微调整)
精益管理十大利器之十
18
八、减小批量的利器—快速换模
• 经济批量不经济; • 为何现在几乎所有的企业都
使用大批量生产的方法; • 减小批量将增加均衡生产的
可能性; • 减小批量可有效的缩短制造
周期。 • 方法——快速模具交换。
精益管理十大利器之十
19
快速换模七大手法
• 方法:彻底5S 内外有别,细分详算 消除螺栓运动 手动、脚和基准不动 取消调整 将转换标准化 取消换模
精益管理十大利器之十
16
制造型企业7大浪费:
1、制造过剩(成品库存,在制堆积品) 2、等待。(工艺不平衡) 3、搬运。(路线不合理) 4、加工。(物耗,非增值作业) 5、多余动作。(动作不合理) 6、库存。(资金占用) 7、不良品。(修理,检测重复)
精益管理十大利器之十
17
各种浪费中两种浪费最为严重 第一是人太多 第二是库存太大
· 初期清扫与自主维护
零 停滞
缩短 交货期长、延迟交货多 交货期 顾客投诉多,
精益管理十大利器之八九十

精益管理十大利器之八九十介绍精益管理是一种以流程优化和减少浪费为核心的管理方法。
它起源于汽车制造业,后逐渐在其他行业得到应用。
在实践中,有一些工具和技术被广泛认可为精益管理的利器,可以帮助组织提高效率、降低成本,并提升质量。
本文将介绍精益管理的十大利器之八九十,包括8. 价值流图、9. 快速换模、10. 安全与环境保护。
我们将依次介绍每个利器的概念、使用方法和具体效益。
8. 价值流图价值流图是一种图表工具,用于可视化产品或服务的价值流程。
它能够揭示出价值流程中的浪费和非必要环节,帮助组织找出改进的机会。
价值流图的制作过程包括以下几个步骤:1.确定价值流程的起点和终点,即产品或服务的开始和结束节点。
2.绘制主要的价值流线,表示价值流程的主干。
在流线上标注每个环节的加工时间,并计算总流程时间。
3.绘制所有的分支流线,表示与主要流程相关的其他环节。
同样标注每个环节的加工时间,并计算总流程时间。
4.识别出流程中的浪费和非必要环节,并用符号标注在图表上。
5.分析图表,找出改进的机会,并制定改进措施。
通过价值流图,组织可以全面了解产品或服务的价值流程,并针对浪费或非必要环节进行优化,从而提高效率和质量。
9. 快速换模快速换模是一种将生产设备从一个产品转换到另一个产品的方法。
它通过减少换模时间,提高设备利用率,在批量生产和多品种生产中具有重要的意义。
实施快速换模需要以下几个关键步骤:1.分析当前换模过程,寻找存在的浪费和改进空间。
2.制定换模计划,明确各项任务和时间要求。
3.优化工艺流程,减少无关环节和冗余操作。
4.采用标准化工具和设备,提高换模效率。
5.建立团队合作机制,加强协同配合。
6.记录并分析换模过程中的问题和经验,经常进行复盘和总结。
通过实施快速换模,组织可以有效减少换模时间和成本,提高设备利用率和生产灵活性。
这将有助于满足顾客需求的变化和提高市场竞争力。
10. 安全与环境保护安全与环境保护是精益管理的重要组成部分。
精益生产管理的十大工具

精益生产管理的十大工具精益生产管理是一种通过优化生产过程,减少浪费和提高效率的方法。
在精益生产管理中,有许多工具和技术可用于帮助企业实现这些目标。
以下是精益生产管理的十大工具。
1. 价值流图:价值流图是一种可视化工具,用于展示产品或服务在整个价值流中的流动,包括所有的价值和非价值活动。
通过使用价值流图,企业可以识别出浪费和瓶颈,并制定改进计划。
2. 5S:5S是一个用于组织和维护工作场所的系统。
它包括整理、整顿、清扫、标准化和维持的步骤。
通过实施5S,企业可以改善工作环境,减少浪费和提高工作效率。
3. 高效供应链管理:高效供应链管理是通过优化供应链中的物流和信息流来降低成本和提高响应速度。
它包括减少库存、改善交付时间和优化供应链合作伙伴关系等方面。
4. 物料需求计划:物料需求计划是一种用于确定需要多少原材料和零部件的工具。
通过正确计划物料需求,企业可以避免库存积压和缺货的问题。
5. 单点作业:单点作业是一种通过减少从一台机器到另一台机器的传送时间来减少生产周期的方法。
这可以通过重新布局设备、改进工艺流程和优化工作站来实现。
6. 柔性生产:柔性生产是一种能够快速适应市场需求和变化的生产方式。
它包括灵活的工作组织、多功能的设备和高度培训的员工。
7. 持续改进:持续改进是一种通过不断寻找和消除浪费、改进工艺和提高质量来提升生产效率的方法。
它可以通过实施PDCA循环(计划、执行、检查、行动)和员工参与来实现。
8. 产能平衡:产能平衡是一种通过平衡生产线上的工作负荷来避免瓶颈和过度生产的方法。
这可以通过调整生产节奏、提高设备利用率和优化工艺来实现。
9. 供应商合作:供应商合作是一种与供应商建立长期合作关系,并与其共同努力改进质量、交付和成本的方法。
这可以通过共享信息、共同制定目标和进行持续改进活动来实现。
10. 质量管理工具:质量管理工具是一系列用于识别和解决质量问题的方法和技术。
其中包括流程图、因果图、直方图、散点图等。
精益生产培训之十大工具

精益生产工具之九---快速换模
快速换模的目标 1.减少换模时间 2.提高换模作业的可重复性,确保生产合格产品之前,换 模作业在几分钟之内完成。 3.促使使用者减少生产批量和降低库存水平而不影响正常 的生产作业
精益生产工具之九---快速换模
换模时间:上一个产品的最后一个合格品到下一个产品的第一
个合格品之间的时间。 换模时间=内部换模时间+外部换模时间
4个步骤(快速换模)
2. 内部时间转移到外部
精益生产工具之九---快速换模
4个步骤(快速换模)
3. 缩短内部时间
精益生产工具之九---快速换模
4个步骤(快速换模)
4. 改善外部时间
精益生产工具之九---快速换模
6步曲(外部换模) 1:观察
精益生产工具之九---快速换模
6步曲(外部换模) 2:记录
A生产
停机时间
B生产
切换时间
外部切换
内部切换
内部换模时间:机器停止当前作业到生产下一个合格产品的时间。期间,机器没 有产生附加值。
外部换模时间:作业人员在线外做换模准备的时间,期间机器仍在正常工作,产
生附加值。
精益生产工具之九---快速换模
4个步骤(快速换模)
1. 区分内外部时间
精益生产工具之九---快速换模
精益生产工具之六---现场改善 什么是现场?
现场:在制造型 企业里,现场是 生产产品或提供 服务的地方。
精益生产工具之六---现场改善
5 要管好 个方面:
Safety 安全
Morale 士气
现场 改善
Quality 质量
Delivery 交期
Cost 成本
精益生产工具之六---现场改善
精益生产培训之十大工具
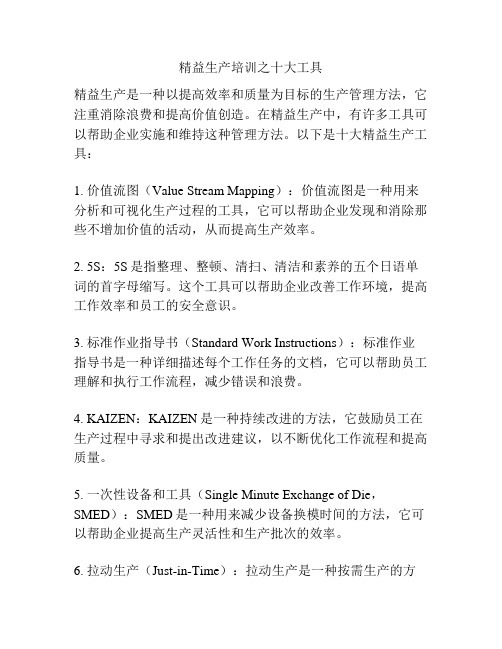
精益生产培训之十大工具精益生产是一种以提高效率和质量为目标的生产管理方法,它注重消除浪费和提高价值创造。
在精益生产中,有许多工具可以帮助企业实施和维持这种管理方法。
以下是十大精益生产工具:1. 价值流图(Value Stream Mapping):价值流图是一种用来分析和可视化生产过程的工具,它可以帮助企业发现和消除那些不增加价值的活动,从而提高生产效率。
2. 5S:5S是指整理、整顿、清扫、清洁和素养的五个日语单词的首字母缩写。
这个工具可以帮助企业改善工作环境,提高工作效率和员工的安全意识。
3. 标准作业指导书(Standard Work Instructions):标准作业指导书是一种详细描述每个工作任务的文档,它可以帮助员工理解和执行工作流程,减少错误和浪费。
4. KAIZEN:KAIZEN是一种持续改进的方法,它鼓励员工在生产过程中寻求和提出改进建议,以不断优化工作流程和提高质量。
5. 一次性设备和工具(Single Minute Exchange of Die,SMED):SMED是一种用来减少设备换模时间的方法,它可以帮助企业提高生产灵活性和生产批次的效率。
6. 拉动生产(Just-in-Time):拉动生产是一种按需生产的方法,它可以帮助企业减少库存和生产浪费,并且能够更好地满足顾客需求。
7. 故障模式与影响分析(Failure Mode and Effects Analysis,FMEA):FMEA是一种用来分析和评估潜在故障模式和其影响的方法,它可以帮助企业识别潜在风险,并采取措施进行预防和改进。
8. 委托管理(Gemba Walk):委托管理是一种通过实地走访生产现场来了解问题和挑战的方法,它可以帮助管理层与现场员工保持沟通,并及时解决问题。
9. PDCA循环:PDCA循环是指计划、实施、检查和行动的四个步骤,它是一种持续改进的管理方法,可以帮助企业不断优化工作流程和提高绩效。
精益生产十大工具
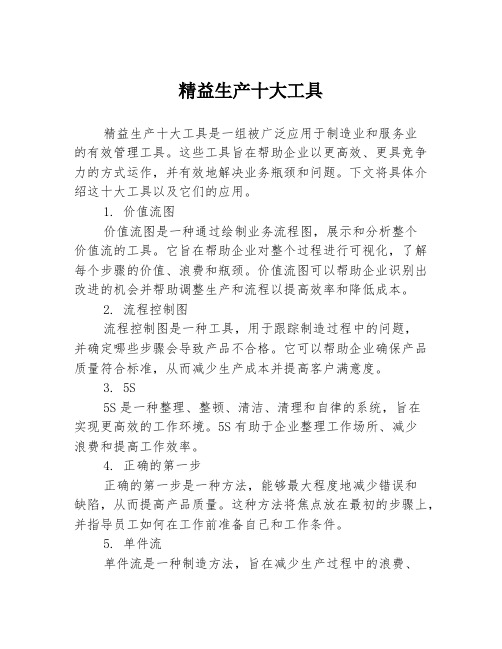
精益生产十大工具精益生产十大工具是一组被广泛应用于制造业和服务业的有效管理工具。
这些工具旨在帮助企业以更高效、更具竞争力的方式运作,并有效地解决业务瓶颈和问题。
下文将具体介绍这十大工具以及它们的应用。
1. 价值流图价值流图是一种通过绘制业务流程图,展示和分析整个价值流的工具。
它旨在帮助企业对整个过程进行可视化,了解每个步骤的价值、浪费和瓶颈。
价值流图可以帮助企业识别出改进的机会并帮助调整生产和流程以提高效率和降低成本。
2. 流程控制图流程控制图是一种工具,用于跟踪制造过程中的问题,并确定哪些步骤会导致产品不合格。
它可以帮助企业确保产品质量符合标准,从而减少生产成本并提高客户满意度。
3. 5S5S是一种整理、整顿、清洁、清理和自律的系统,旨在实现更高效的工作环境。
5S有助于企业整理工作场所、减少浪费和提高工作效率。
4. 正确的第一步正确的第一步是一种方法,能够最大程度地减少错误和缺陷,从而提高产品质量。
这种方法将焦点放在最初的步骤上,并指导员工如何在工作前准备自己和工作条件。
5. 单件流单件流是一种制造方法,旨在减少生产过程中的浪费、减少库存和减少制造时间。
它可以帮助企业以更高效的方式生产各种产品,并根据客户的需求提供服务。
6. 智能制造智能制造是一种制造技术,旨在将传统的制造过程与先进的计算机技术结合起来,以实现更高效、更可靠且更精确的生产。
智能制造的目标是提高质量、降低成本并增强企业的竞争力。
7. 按需制造按需制造是一种生产模式,在该模式下,生产和服务是根据客户需求实时产生的。
按需制造可以大大减少库存,避免过剩的库存和减少过时产品,从而提高效率和降低成本。
8. JidokaJidoka是一种制造方法,旨在通过自动化控制制造过程和机器上的检测,实现实时可视化生产过程。
Jidoka可帮助企业有效地识别和纠正制造过程中的错误,并最大限度地减少损失和产品缺陷。
9. KaizenKaizen是一种改进方法,旨在不断优化生产过程。
精益管理有哪十大工具?
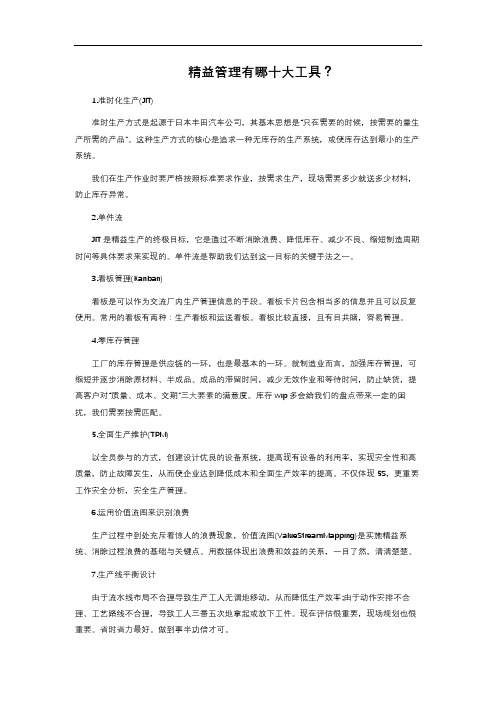
精益管理有哪十大工具?1.准时化生产(JIT)准时生产方式是起源于日本丰田汽车公司,其基本思想是“只在需要的时候,按需要的量生产所需的产品”。
这种生产方式的核心是追求一种无库存的生产系统,或使库存达到最小的生产系统。
我们在生产作业时要严格按照标准要求作业,按需求生产,现场需要多少就送多少材料,防止库存异常。
2.单件流JIT是精益生产的终极目标,它是通过不断消除浪费、降低库存、减少不良、缩短制造周期时间等具体要求来实现的。
单件流是帮助我们达到这一目标的关键手法之一。
3.看板管理(Kanban)看板是可以作为交流厂内生产管理信息的手段。
看板卡片包含相当多的信息并且可以反复使用。
常用的看板有两种:生产看板和运送看板。
看板比较直接,且有目共睹,容易管理。
4.零库存管理工厂的库存管理是供应链的一环,也是最基本的一环。
就制造业而言,加强库存管理,可缩短并逐步消除原材料、半成品、成品的滞留时间,减少无效作业和等待时间,防止缺货,提高客户对“质量、成本、交期”三大要素的满意度。
库存wip多会给我们的盘点带来一定的困扰,我们需要按需匹配。
5.全面生产维护(TPM)以全员参与的方式,创建设计优良的设备系统,提高现有设备的利用率,实现安全性和高质量,防止故障发生,从而使企业达到降低成本和全面生产效率的提高。
不仅体现5S,更重要工作安全分析,安全生产管理。
6.运用价值流图来识别浪费生产过程中到处充斥着惊人的浪费现象,价值流图(ValueStreamMapping)是实施精益系统、消除过程浪费的基础与关键点。
用数据体现出浪费和效益的关系,一目了然,清清楚楚。
7.生产线平衡设计由于流水线布局不合理导致生产工人无谓地移动,从而降低生产效率;由于动作安排不合理、工艺路线不合理,导致工人三番五次地拿起或放下工件。
现在评估很重要,现场规划也很重要。
省时省力最好。
做到事半功倍才可。
8.拉系统与补充拉系统所谓拉动生产是以看板管理为手段,采用“取料制”即后道工序根据“市场”需要进行生产,对本工序在制品短缺的量从前道工序取相同的在制品量,从而形成全过程的拉动控制系统,绝不多生产一件产品。
精益生产管理十大工具

精益生产管理十大工具
1. 展开-收缩图:用于分析流程中的重复性工作和非必要步骤,并将不必要的步骤剔除。
2. 生产可视化:通过对生产情况进行实时可视化,能够更好地理解生产过程中存在的问题,以及如何纠正问题。
3. 价值流图:用于识别和分析流程中的不必要步骤,以便于合理安排人力、物力和资源。
4. 精益5S管理:通过建立整洁、易于清洁、安全和方便操作的工作环境,有效提高生产效率。
5. 六大白帽子:指的是6个基本的精益思想:标准化、流程改进、定期检查、及时应对、数据分析和精益文化。
6. 生产线平衡:用于识别和分析生产线上的瓶颈,保证生产过程中每一道工序都能够得到有效的利用。
7. 改善小组:建立一组小组来改善当前的生产过程,以提高效率,降低成本。
8. 标准化:建立标准的流程,以确保每一道工序都能够稳定、高效地完成。
9. 重复性分析:分析企业的生产过程中存在的重复性工作,以便确定可以剔除的不必要步骤。
10. 精益工厂:将精益管理思想贯彻到整个企业,改善整体的生产流程,以达到高效运营的目的。
精益生产管理的十大工具和实施步骤

精益生产管理的十大工具和实施步骤一、价值流分析(Value Stream Mapping):价值流分析是了解和改进产品或服务的价值流程的方法。
通过绘制价值流地图,可以清楚地看到从原料到最终交付的整个价值流程,以及其中存在的浪费和瓶颈。
通过分析和改进价值流程,可以实现生产过程的优化。
二、5S整理法:5S整理法是一种是一种工作环境整理和管理方法。
通过整理、整顿、清扫、标准化和维护这五个步骤,可以创造一个整洁、有序、高效的工作环境,提高工作效率和质量。
三、流程改进活动(Kaizen):Kaizen是一种小创新的方法,通过持续改善工作流程,减少或消除浪费,提高效率和质量。
它鼓励员工提出改进建议,并通过小规模试验和迭代改进的方式,不断优化工作流程。
四、单点教导法(One-Piece Flow):单点教导法是一种用来实现流程连续化和缩短生产周期的方法。
通过将生产任务拆分为较小的单元,并且一个接一个地完成,可以减少库存和等待时间,提高生产效率和质量。
五、标准化工作(Standardized Work):标准化工作是一种明确工作内容和作业要求的方法。
通过对工作流程进行详细的规范和记录,包括工作步骤、所需时间和所需材料等,可以确保工作一致性和质量,减少浪费和错误。
六、自动化(Automation):自动化是一种利用机械装置和技术来替代人力的方法。
通过引入自动化设备和技术,可以实现生产过程的标准化和高度自动化,提高生产效率和稳定性。
七、质量管控(Quality Control):质量管控是一种确保产品或服务质量的方法。
通过建立质量控制流程和标准,进行检验和测试,可以及时发现和纠正质量问题,保证产品或服务的一致性和可靠性。
八、产能平衡(Capacity Balancing):产能平衡是一种调整生产线中各个工位和机器的产能,以适应需求变化的方法。
通过平衡各个工位和机器的产能,可以避免瓶颈和浪费,提高整个生产线的效率。
九、持续改进(Continuous Improvement):持续改进是一种通过不断寻找和解决问题,优化工作流程和提高效率的方法。
精益生产十大工具

工具讲解| 咱们来聊聊精益生产的这10大工具今天想跟大家聊聊精益,说起这个词:精益,也许很多人第一时间先把它的英文Lean搬出来,然后大谈Lean,天花乱坠的到最后还是剑指日本。
其实精益的产生源于对浪费的零容忍,因此精益的整改也都不是什么高深莫测的科学,反而其整改的基础都来源于人们的常识和人们对其生产环境的思考。
作为SQE,我们经常会提及一句话“供应商,请把你的改善报告给我",当我们向供应商要改善报告的时候,我们到底希望供应商干啥?这个问题,SQE你是否思考过?其实,我们在做供应商管理的过程中,如果能把杜绝浪费作为我们唯一的出发宗旨,问题也就迎刃而解。
项目不能够按时完成,这是一种浪费:你投入了人力,物力和时间,但是在计划的时间内没有完成任务,这是不是浪费?答案是肯定的。
供应商交付的产品出现质量问题,需要换货,退货,挑选,我们给供应商开事故,让供应商提交8D,最终我们要在8D中看到有效的永久措施:发生原因整改措施,流出原因整改措施,管理原因整改措施。
所有的整改是为了预防问题再次发生,其实就是为了防止再次出现浪费。
中国的古人说的,亡羊补牢为时未晚就是这个意思。
当我们把工作的终点定义为遏制和防止浪费出现,那么自然而然地将精益思想揪出来,因为精益的核心就是减少浪费提高效率防止错误产生。
一提精益,大家立刻想到日本,我觉得很正常,说明你还是了解精益的,因为如果一提到精益,你想到的是印度,我想说哥们儿你应该不了解精益。
为了防止浪费,日本将精益工具化,思想化甚至生活化。
先给大家举个例子,这是发生在我身边的真实的事情。
我老婆去日本旅游,带回来一袋日本的乌冬面。
一天,我心血来潮想尝尝这日本的乌冬面,于是乎在锅中烧开水,然后撕开袋口将一坨面顺势从包装袋中挤出去了,在滚滚的废水中,我突然看到了调味包在沸水中翻滚,这时候我郁闷了:因为我是从事塑料件供应商管理多年的SQE,职业的直觉让我觉得塑料制品在废水中浸泡会释放出有毒物质,我再深入地联想了一下,有毒物质可能致癌,于是乎提起右手狠狠地抽了自己一个耳光,大老远飘洋过海的乌冬面我要倒掉啦!!!因为我胆小惜命,面对可疑0容忍。
10个必备精益生产管理工具

10个必备精益生产管理工具精益生产是当前工业界最佳的一种生产组织体系和方式,这里分享10个精益生产管理工具,希望对大家有所帮助!1.OEE设备综合效率衡量一个制造过程损失的综合指标只需要将以下三个指标进行相乘即可:设备利用率(停机问题);设备效率(节拍问题);质量率(缺陷问题)。
100%的OEE则意味着完美的生产:无停机,高节拍和无缺陷。
2.防错通过预防和探测缺陷以便实现最终(客户端)的零缺陷。
3.根本原因分析找到问题的根本原因,而非表面现象:比如5-Why方法。
通过纠正措施消除问题的根本原因,使得问题更好更彻底地解决。
4.标准化作业基于最佳实践的,细化到每一个步骤的,可以归档的作业流程,可以用动态文件来支持必要时的更新。
5.SMART目标设定以下目标:Specific具体化的,Measurable可衡量性的,Attainable可达成的,Relevant与战略相关的,Time-Specific与时间期限相关的。
6.Takt Time节拍时间基于顾客需求的生产节拍:节拍时间=计划生产时间(有效时间)/顾客需求数量。
如果按照顾客节拍进行生产,既能够满足顾客又可以减少浪费。
7.可视化工厂通过使用电子看板,控制器,物理看板等装置来实现工厂的可视化,透明化,并且还可以增强信息的沟通。
如果将制造过程的状态快速有效的展现给大家,可以减少不必要的浪费。
8.价值流图将当前和未来的生产流进行可视化的对比,以便可以寻找改进空间的方法。
能够解决暴露当前过程的浪费,同时以便绘制出未来改善路线图。
9.六大损失在制造过程中往往会存在六大生产率损失:机器故障,计划外停工,需要换线,损坏,速度降低,质量缺陷。
10.SMED快速换模一种可以将换模时间减少到10分钟以下的技术。
快速换模使得小批量在生产时,大大减少了换模时间的损失,降低了库存,加大了客户响应。
精益生产管理十大工具

精益生产管理十大工具在现代制造业中,精益生产管理是一种重要的管理思想,旨在提高生产效率、降低成本、提高产品质量。
为了实现这一目标,精益生产管理应用了各种工具和技术。
以下是精益生产管理中最常用的十大工具:价值流映射价值流映射是一种识别和消除生产过程中浪费的工具。
通过绘制价值流图,生产管理者可以清晰地看到价值创造的流程,并找出其中的浪费,进而采取措施进行改善。
小批量生产采用小批量生产可以减少库存、降低生产成本,并提高生产效率。
通过减少生产周期,企业可以更加灵活地响应市场需求。
标准化工作制定和遵守标准化工作流程可以确保生产过程稳定、高效。
员工们在遵循标准操作流程的情况下工作,有助于减少产生的错误和浪费。
5S整理法5S整理法是一种工厂管理方法,通过整顿、清扫、清洁、清理、素养的五个步骤,使工作环境整洁有序,提高工作效率。
建议箱建议箱是鼓励员工提出改进建议的工具。
通过员工的参与,可以发现生产过程中存在的问题和改进的机会,从而不断优化生产流程。
好的团队沟通有效的团队沟通是实现精益生产管理的重要前提。
通过团队沟通,可以加强团队协作,促进信息共享,提高生产效率。
周生产会议定期召开周生产会议可以及时跟踪生产进度,识别问题并制定解决方案。
通过会议记录和持续改进,可以提高生产计划的准确性。
一体化生产计划一体化生产计划是整合市场需求、生产能力、物流等因素的生产计划模式。
通过一体化计划,企业可以优化资源配置,提高生产效率。
质量控制质量控制是确保产品质量符合标准的一系列措施。
通过质量控制,可以降低次品率,提高产品质量,增强企业竞争力。
持续改进持续改进是精益生产管理的核心理念。
通过不断地发现问题、分析原因、提出改进建议并实施改进措施,企业可以不断提高生产效率和产品质量。
以上就是精益生产管理中最常用的十大工具。
通过合理应用这些工具,企业可以不断优化生产流程,提高生产效率,降低成本,实现持续增长。
精益生产十大工具

精益生产十大工具精益生产是一种旨在提高生产效率和减少浪费的管理方法。
它包含了许多工具和技术,旨在帮助组织更好地管理资源、提高产能和优化流程。
在这篇文章中,我将介绍精益生产的十大工具,以帮助读者更好地了解和应用这些工具。
1.5S法则:5S法则是一种用于组织工作环境和提高效率的方法。
它包括整理、整顿、清扫、标准化和自律五个步骤。
通过实施5S法则,组织可以改善工作环境,减少浪费和失误,并提高生产效率。
2.价值流图:价值流图是一种用于分析和改善生产流程的工具。
它可以帮助组织识别价值和非价值活动,并定位瓶颈和浪费。
通过分析价值流图,组织可以找到改进的机会,并优化流程以提高产出和客户满意度。
3.流程映射:流程映射是一种用于图形化表示和分析流程的工具。
它可以帮助组织识别和理解整个流程的各个步骤和关键决策点。
通过流程映射,组织可以更好地了解流程,并找出改进的机会。
4.持续改善:持续改善是精益生产的核心原则之一。
它强调从小改进开始,通过反复模拟和实验,逐步提高流程和产品的质量。
持续改进要求组织保持开放和灵活,不断追求更高的效率和产品质量。
5.单点故障:单点故障是指在生产过程中存在可能导致整个流程中断或崩溃的单一关键节点。
通过识别和消除单点故障,组织可以提高生产线的稳定性和可靠性,并降低因故障引起的停产和成本。
6.稳定性:稳定性是指生产流程的可靠性和一致性。
通过确保设备和工艺的稳定性,组织可以减少因工艺变异而导致的浪费和不良品,提高生产效率和质量。
7.柔性制造:柔性制造是指组织能够快速适应市场需求变化,并在不降低质量和效率的情况下生产不同类型的产品。
通过实施柔性制造,组织可以更好地利用资源、减少库存和满足客户需求。
8.精细化:精细化是指组织对生产过程中每一个环节和细节进行深入分析和控制。
通过精细化,组织可以更好地了解产品和生产线的性能,并找到改进的机会,以提高生产效率和质量。
9.标准化:标准化是指通过制定和执行标准,确保生产过程和产品的一致性和质量。
精益生产管理十大工具和实施步骤

精益生产管理是一种强调持续改善、降低成本和提高效率的管理方法。
在这篇文章中,我将重点介绍精益生产管理的十大工具和实施步骤,以此来帮助你更好地理解这一管理方法。
一、价值流映射价值流映射是精益生产的关键工具之一,它可以帮助企业了解整个生产流程,找出生产中的浪费,从而进行优化和改进。
通过价值流映射,企业可以更好地理解价值创造的流程,识别出不必要的步骤和活动,从而精简生产流程,提高生产效率。
二、5S整理法5S整理法是指整理、整顿、清扫、清洁、素养的五个日语单词的头字母缩写。
这是一个用于管理和改善工作环境的工具,通过规范化工作环境,提高工作效率,减少浪费。
三、持续流生产持续流生产是指通过对生产流程进行优化,实现产品的快速、按需生产,减少库存和等待时间,提高生产效率。
通过持续流生产,企业可以更好地满足客户需求,降低成本,提高竞争力。
四、柔性生产柔性生产是指企业能够在不增加成本和不降低质量的前提下,快速对生产进行调整和变更,适应市场需求的能力。
通过柔性生产,企业可以更好地应对市场变化,提高生产灵活性和适应性。
五、标准化工作标准化工作是指对工作流程进行规范和标准化,以确保工作质量和效率。
通过标准化工作,企业可以更好地控制生产过程,减少变动和浪费,提高生产稳定性和质量。
六、JIT精益库存JIT精益库存是指“按需生产、零库存”的原则,通过精细的生产计划和供应链管理,实现产品的快速交付和零库存管理,从而减少库存成本和压力。
七、故障预防维护故障预防维护是指通过定期检查和维护设备,预防设备故障和停机时间,提高生产设备的稳定性和可靠性。
通过故障预防维护,企业可以降低维修成本,提高生产效率。
八、持续改善持续改善是精益生产的核心理念之一,通过不断地对生产流程进行分析和改进,实现持续的提升和创新。
通过持续改善,企业可以不断提高生产效率和质量,降低成本,提高竞争力。
九、价值链管理价值链管理是指对整个价值链进行优化和管理,从供应商到客户的整个生产和销售过程。
精益生产之现场管理十大工具课件
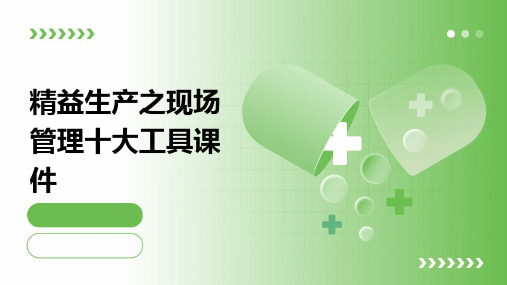
设计看板样式
根据信息内容,设计 看板的样式和布局, 确保信息清晰易懂。
制作看板
根据设计好的样式, 制作看板,并确保信 息的实时更新。
培训员工
培训员工如何使用看 板,了解看板上的信 息含义和作用。
监控与改进
定期检查看板的运行 情况,发现问题及时 处理和改进,以提高 生产效率和管理水平 。
08
价值流图析
精益生产之现场 管理十大工具课 件
目录
• 5S管理 • 目视化管理 • 标准化管理 • 快速换模 • 防错法
目录
• 单元化生产 • 看板管理 • 价值流图析 • 全员生产维护(TPM) • 持续改进活动(Kaizen)
01
5S管理
定义与特点
5S管理是一种现场管理方法,包括整理(Sort)、整 顿(Straighten)、清扫(Sweep)、清洁( Sanitize)和素养(Sustain)五个方面。
5S管理旨在创造一个整洁、有序、安全的工作环境, 提高工作效率,降低浪费和成本。
5S管理强调标准化、规范化和持续改进,通过不断的 整理、整顿和清扫,保持现场整洁有序,提高工作效
率和员工素养。
5S管理的重要性
提高工作效率
整洁有序的工作环境有助于减少寻找物品的 时间,提高工作效率。
提升员工素养
通过实施5S管理,培养员工养成规范、有序 的工作习惯,提高员工素养。
优化流程
通过价值流图析,企业可以全面 了解产品或服务的整个流程,从 而发现潜在的优化点,提高生产 效率。
战略规划
价值流图析可以为企业提供战略 规划的依据,帮助企业制定更加 科学、合理的生产计划。
价值流图析的实施步骤
确定研究对象
明确要分析的产品或服务,了解其整个生 产流程。
- 1、下载文档前请自行甄别文档内容的完整性,平台不提供额外的编辑、内容补充、找答案等附加服务。
- 2、"仅部分预览"的文档,不可在线预览部分如存在完整性等问题,可反馈申请退款(可完整预览的文档不适用该条件!)。
- 3、如文档侵犯您的权益,请联系客服反馈,我们会尽快为您处理(人工客服工作时间:9:00-18:30)。
企业精益生产培训
准时化生产(JIT)
准时生产方式是起源于日本丰田汽车公司, 其基本思想是“只在需要的时候,按需要的量生 产所需的产品”。这种生产方式的核心是追求一 种无库存的生产系统,或使库存达到最小的生产 系统。
企业精益生产培训
标准作业
有效地组合物质、机器和人,“丰田生产方 式”称这种组合过程为作业组合,这一组合汇总 的结果就是标准作业。
企业精益生产培训
持续改善
当开始精确地确定价值,识别价值流,使为 特定产品创造的价值的各个步骤连续流动起来, 并让客户从企业拉动价值时,奇迹就开始出现了。
虽然精益生产管理是一个循序渐进、不断改 善的过程,但是熟悉这些工具对精益生产的实施 将会起到很大的帮助。
企业精益生产培训
此课件下载可自行编辑修改,仅供参考! 感谢您的支持,我们努力做得更好!谢谢
防错装置的用途:一是杜绝产生特定产品缺 陷的原因,二是通过廉价的手段对产品进行逐一 的检查,以确定其是否合格。
是操作者在执行的过程中完成的, 它们对操作者应该是透明的。也就是说,只要防 错的条件不满足,操作就无法继续进行下去。
企业精益生产培训
快速换型/模(SMED)
SMED:习惯称之为快速换模, 也被称作快速 生产准备,该原则能被用于任何环境, SMED是一 种持续改进生产准备的方法,达到尽可能低的时 间(最终达到一触即可或无需生产准备),它是一 种能够减少更换工装、材料时间的方法,它通过 换模过程中简化、协调操作等方式来实现。
企业精益生产培训
看板管理
常作“Kanban管理,是丰田生产模式中的重 要概念,指为了达到准时生产方式(JIT)控制现 场生产流程的工具。准时生产方式中的拉式 (Pull)生产系统可以使信息的流程缩短,并配 合定量、固定装货容器等方式,而使生产过程中 的物料流动顺畅。 准时生产方式的看板旨在传达 信息:“何物,何时,生产多少数量,以何方式 生产、搬运”。
企业精益生产培训
价值流分析
生产过程中到处充斥着惊人的浪费现象,价 值流图(Value Stream Mapping)是实施精益系统、 消除过程浪费的基础与关键点。
企业精益生产培训
拉式系统
所谓拉动生产是以看板管理为手段,采用道 工序取相同的在制品量,从而形成全过程的拉 “取料制”即后道工序根据“市场”需要进行生 产,对本工序在制品短缺的量从前动控制系统, 绝不多生产一件产品 。 JIT需要以拉动生产为基 础,而拉系统操作是精益生产的典型特征。精益 追求的零库存,主要通过拉系统的作业方式实现 的。
标准作业是以人的动作为中心、以没有浪费 的操作顺序有效地进行生产的作业方法。它由节 拍时间(Take Time,T﹒T)、作业顺序、标准手 持三要素组成。
防错
企业精益生产培训
所谓防错Error Proofing(Pokayoke),它可 以是一种机械或电子装置,能够防止人为的错误 或者让人一眼就看出出现错误的位置。
企业精益生产培训
持续改善
持续改善(Kaizen)是指“对企业不同领域 或工作位置上所做的不断的改进和完善”Kaizen 意味着改进,涉及每一个人、每一环节的连续不 断的改进:从最高的管理部门、管理人员到工人。
“持续改善”的策略是日本管理部门中最重 要的理念,是日本人竞争成功的关键。 Kaizen实 际上是生活方式哲学。它假设,应当经常改进我 们的生活的每个方面。
企业精益生产培训
精益管理的十大工具
企业精益生产培训
精益生产的主要工具
1、5S与目视化管理 2、全员生产维护(TPM) 3、准时化生产 4、标准作业 5、防错
企业精益生产培训
精益生产的主要工具
6、快速换型 7、看板管理 8、价值流分析 9、拉式系统 10、持续改善
企业精益生产培训
5S与目视管理
“5S”是整理(Seiri)、整顿(Seiton)、清扫 (Seiso)、清洁(Seikeetsu)和素养(Shitsuke)这5 个词的缩写“5S”,起源于日本。
5S是创建和保持组织化,整洁和高效工作场 地的过程和方法,可以教育、启发和养成良好 “人性”习惯,目视管理可以在瞬间识别正常和 异常状态,又能快速、正确的传递讯息。
企业精益生产培训
全员生产维护(TPM)
TPM(Total Productive Maintenance),这 是日本人在70年代提出的,是一种全员参与的生 产维修方式,其主要点就在“生产维修”及“全 员参与”上。通过建立一个全系统员工参与的生 产维修活动,使设备性能达到最优。