美国专利申请模板 冲击扳手(文)
金属外观专利申请书模板
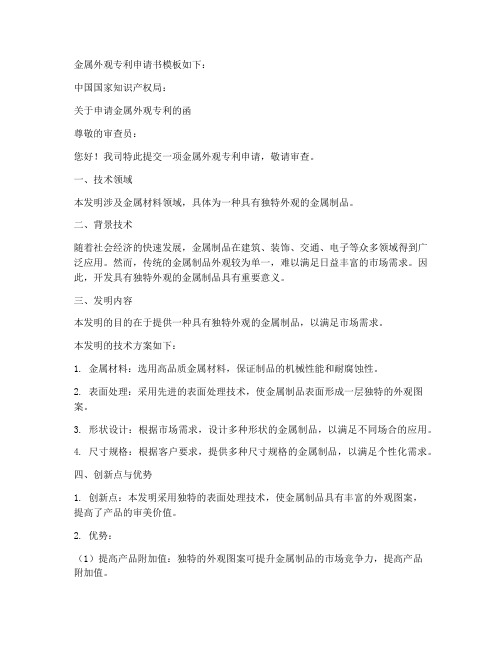
金属外观专利申请书模板如下:中国国家知识产权局:关于申请金属外观专利的函尊敬的审查员:您好!我司特此提交一项金属外观专利申请,敬请审查。
一、技术领域本发明涉及金属材料领域,具体为一种具有独特外观的金属制品。
二、背景技术随着社会经济的快速发展,金属制品在建筑、装饰、交通、电子等众多领域得到广泛应用。
然而,传统的金属制品外观较为单一,难以满足日益丰富的市场需求。
因此,开发具有独特外观的金属制品具有重要意义。
三、发明内容本发明的目的在于提供一种具有独特外观的金属制品,以满足市场需求。
本发明的技术方案如下:1. 金属材料:选用高品质金属材料,保证制品的机械性能和耐腐蚀性。
2. 表面处理:采用先进的表面处理技术,使金属制品表面形成一层独特的外观图案。
3. 形状设计:根据市场需求,设计多种形状的金属制品,以满足不同场合的应用。
4. 尺寸规格:根据客户要求,提供多种尺寸规格的金属制品,以满足个性化需求。
四、创新点与优势1. 创新点:本发明采用独特的表面处理技术,使金属制品具有丰富的外观图案,提高了产品的审美价值。
2. 优势:(1)提高产品附加值:独特的外观图案可提升金属制品的市场竞争力,提高产品附加值。
(2)丰富应用场景:多种形状和尺寸规格的金属制品可广泛应用于建筑、装饰、交通、电子等领域。
(3)易于清洁和维护:表面处理技术保证了金属制品的耐腐蚀性,便于清洁和维护。
五、技术方案的实施1. 金属材料的选用:根据产品用途和性能要求,选用合适的金属材料,如不锈钢、铝合金等。
2. 表面处理:采用电镀、喷涂、氧化等表面处理技术,形成独特的外观图案。
3. 形状设计:根据市场需求,设计多种形状的金属制品,如方形、圆形、异性等。
4. 尺寸规格:根据客户要求,提供多种尺寸规格的金属制品。
六、权利要求书1. 一种具有独特外观的金属制品,其特征在于,所述金属制品采用高品质金属材料,表面处理技术形成独特的外观图案。
2. 根据权利要求1所述的金属制品,其特征在于,所述金属制品具有多种形状和尺寸规格。
美国专利临时专利申请书(精选3篇)

美国专利临时专利申请书(第一篇)此文档协议是通用版本,可以直接使用,符号*表示空白。
(1)美国专利主要分三类:(外观)设计专利designpatent;有用专利utilitypatent;还有植物专利plantpatent.其中有用专利utilitypatent是一般美国人所指的专利。
(2)为获得一个utilitypatent必需提交的专利申请,美国法称其为Non-provisionalPatentApplication.这种申请形式比较严格,需要符合如下条件:一份书面文件,至少包含一个权利要求和说明书;一份声明;—附图(假如必需);—申请费。
看得出来,Non-provisionalPatentApplication就是我国一般的专利申请,跟我国专利法接受申请、确定申请日的条件全都。
(3)但在1995年6月,美国商标专利局开了临时专利申请的头。
允许提交一份专利申请,并保留12个月。
且这份申请不必遵循上述有用专利申请的要件。
由于专利局并不立刻审查该专利申请。
申请人必需在12个月内,提交一份非临时申请,才能启动程序,并最终获得专利,否则临时申请就作废。
由于这一制度的启动,这两个对应的词和两种程序的区分,就消失了:新的申请,既然叫做临时申请provisionalPatentApplication,老的申请就叫做Non-provisionalPatentApplication.美国专利临时专利申请书(第二篇)合同标题: 美国专利临时专利申请书(第二篇)合同摘要:本合同旨在提供一份简洁且具体的美国专利临时专利申请书(第二篇)范文,以确保申请书的正确撰写,并促进合同双方的合作。
正文:一、申请人信息申请人姓名:申请人地址:联系电话:电子邮件:二、发明名称发明名称:[发明名称]三、摘要本申请旨在针对美国专利法规定的临时专利申请书进行排版,并包含以下内容:1. 发明背景简要描述发明的技术背景和相关领域的现有技术。
五金工具产品中英文对照

两用扳手CONBINATION SPANNER两用扳手套装COMBINATION SPANNER SET加长型两用扳手COMBINATION SPANNER EXTRA LONG梅花棘轮开口扳手OPEN ENDED SPANNER WITH RING RATCHET梅花棘轮开口扳手套装OPEN ENDED SPANNER WITH RING RATCHET SET 两用棘轮扳手COMBINATION RATCHET SPANNER两用棘轮扳手套装COMBINATION RATCHET SPANNER SET1/4'连接物ADAPTOR 1/4'组合支架工具COMBINATION HOLDING TOOL小型发光二极管MINIATURE LED LAMP活动扳手SINGLE OPEN ENDED SPANNER扳手套装MAGNETO SPANNER SET单开口扳手/呆扳手SINGLE ENDED OPEN JAW SPANNER双开口扳手DOUBLE OPEN ENDED SPANNER双开口扳手套装DOUBLE OPEN ENDED SPANNER SET扩口螺母扳手PLARE NUT SPANNER(OPEN)半月型梅花扳手HALF-MOON RING SPANNER双头梅花扳手(短)DOUBLE ENDED SPANNER(SHORT)双头梅花扳手(长)DOUBLE ENDED SPANNER(LONG)平头梅花扳手(直)FLAT RING SPANNER STRAIGHT PATTERN开口敲击扳手OPEN ENDED SLOGGING SPANNER梅花敲击扳手RING SLOGGING SPANNER高颈梅花敲击扳手DEEP AFFSET RING SLOGGING SPANNER直头梅花扳手DEEP RING SPANNER(STRAIGHT PATTERN)延长管EXTENSION TUBE爪型扳手CROWFOOT SPANNER两用活头扳手COMBINATION SWIVEL HEAD WRENCH活结T型扳手SWIVEL HANDLE WITH SLIDING T套筒扳手SOCKET WRENCH弯头套筒扳手ANGLED SOCKET WRENCH双头套筒扳手DOUBLE ENDED SOCKET WRENCH旋棒TOMMY BAR分节旋棒STEPPED TOMMY BAR3C把手套筒扳手SOCKET WRENCH WITH 3C-HANDLET型及磁性套筒扳手SOCKET WRENCH WITH T-HANDLE AND MAGNET钩头扳手HOCK SPANNER WITH LUG带销扳手PIN SPANNER可调式两爪钩扳手CALIPER FACE SPANNER WITH ADJUSTABLE1/4'标准六角套筒HEXAGON SOCKET1/4'加长六角套筒HEXAGON LONG PATTERN SOCKET棘轮扳手RATCHETS套筒SOCKETS套筒套装SOCKETS SETS摩擦棘轮扳手FRICTION RATCHETS冲击工具IMPACT TOOLS旋具头BITS扭矩扳手TORQUE WRENCHES1/4梅花套筒SOCKET UD PROFILE1/4六角套筒星型套筒SOCKET FOR PROTRUDING HEAD SCREWS1/4一字,十字,星型,内六角旋具套筒1/4’双向棘轮套筒扳手1/4’REVERSIBLE RATCHETT柄棘轮扳手RATCHET WITH T-HANDLE手用棘轮头HAND RATCHET WITHOUT HANDLE1/4转3/8转换接头CONVERTER 1/4 TO 3/8T型滑动头手柄TOMMY BAR WITH SLIDING T活动延长杆FLEXIBLE EXTENSION通用延长杆UNIVERSAL-JOINT EXTENSION1/4四方驱动连接头SQUARE-DRIVE COUPLER1/4万向接头UNIVERSAL JOINT活动头手柄SWIVEL HANDLE套筒固定夹SOCKET RAIL WITH MAGNETIC3/8一字,十字,星型,内六角旋具套筒3/8六角套筒SOCKET HEXAGON 3/83/8梅花套筒SOCKET UD PROFILE塑料棘轮扳手PLASTIC RATCHET3/4' ..旋具头接头BIT ADAPTOR旋具头棘轮扳手BIT RATCHET旋具头螺丝起子BIT SCREWDRIVER旋具头延长杆BIT EXTENSION旋具头SCREWDRIVER BITS风动套筒IMPACT SOCKET风动套筒附件ACCESSORIES FOR IMPACT SOCKET手动操作冲击手柄HAND-OPERATED INPACT DRIVER摩擦式梅花棘轮扳手FRICTION TYPE RATCHET WITH RING WITH BI-HEXAGON 摩擦式四方棘轮扳手FRICTION TYPE RATCHET WITH SQUARE RING安装扳手/尖尾扳手CONSTRUCTION RATCHET BI-HEXAGON0.6-5.4NM扭力螺丝起子TORQUE SCREWDRIVER HANDLE 0.6-5.4NM 3C一字螺丝起子3C-SCREWDRIVER FOR SLOTTED HEAD SCREWS3C十字PH螺丝起子3C-SCREWDRIVER FOR CRUCIFORM HEAD PH3C米字螺丝起子3C星型螺丝起子3C球头六角螺丝起子5件/6件/7件/155件螺丝起子套装SET FOR HEAD SCREWS电工螺丝旗子ELECTRONIC SCREWDRIVER木柄螺丝起子SCREWDRIVERS WITH WOODEN HANDLE磁化/消磁器MAGNETIZER AND DEMAGNETIZER方刃锥子SQUARE BLADED AWLT型六角螺丝起子HEXAGON SCREWDRIVER WITH T-HANDLET型内六角扳手HEXAGON SOCKET KEY WITH T-HANDLE内六角扳手HEXAGON SOCKET KEY加长内六角扳手EXTRA LONG HEXAGON SOCKET KEY加长球头内六角扳手内六角扳手套装HEXAGON SOCKET KEY SETT型星形螺丝起子SCREWDRIVER WITH T-HANDLE曲柄螺丝起子CRANKED SCREWDRIVER量规GARGE车灯测电笔CAR LIGHT TESTER6-24伏测电笔VOLTAGE TESTER 6-24V150-250伏测电笔VOLTAGE TESTER 150-250V钳子3件套装PLIERS SET,3-PIECE万能手钳48件套UNIVERSAL PLIERS ASSORTMENT WITH 48 PIECE 小钢丝钳SMALL COMBINATION PLIERS钢丝钳(德式)COMBINATION PLIERS(GERMAN PATTERN)钢丝钳(欧式)COMBINATION PLIERS(EURO PATTERN)强力钢丝钳POWER COMBINATION PLIERS塑料水口钳SIDE CUTTERS FOR PLACTIC剪钳(瑞典款式)SIDE CUTTERS(SWEDISH PATTERN)电工剪钳ELECTRICIAN’S SIDE CUTTERS剪钳(美国款式)POWER SIDE CUTTERS(AMERICAN PATTERN)杠杆剪钳LEVER-ACTION SIDE CUTTERS杠杆顶剪钳LEVER-ACTION END CUTTING NIPPERS核头钳TOWER PINCERS拨钉钳PINCERS平头钳FLAT NOSE PLIERS圆头钳ROUND NOSE PLIERS直头尖嘴钳LONG NOSE PLIERS弯头尖嘴钳电话钳TELEPHONE PLIERS强力尖嘴钳TRIPLE-FUNCTION PLIERS直口机修工钳MECHANICS PLIERS STRAIGHT PATTERN曲口机修工钳MECHANICS PLIER ANGLED PATTERN偏口机修工钳MECHANICS PLIER OFFSET PATTERN30度平圆机修钳MECHANICS PLIER WITH 30电缆刀CABLE KNIFE电工电缆刀ELECTRICIAN’S CABLE KNIFE防静电专用钳子电子钳ELECTRONIC PLIERS迷你电子钳MINIATURE ELECTRONIC PLIERS防静电尖嘴钳/防静电顶切钳/电子平头钳/电子剪钳/防静电剪钳/电子剥线钳电缆剪钳CABLE CUTTERS小型万用剪SMALL UNIVERSAL SCISSORS万用电缆刀UNIVERSAL CABLE KNIFE自动剥线钳STRIPPING PLIERS ANTOMATIC剥线钳STRIPPING PLIERS固定剥线钳STRIP-FIX STRIPPING PLIERS剥线工具WIRE STRIPPER高效剥线钳HIGH-PERFORMANCE WIRE STRIPPER数据传输电缆精确剥线钳PRECISION WIRE STRIPPER FOR DATA CABLES同轴电缆剥线钳WIRE STRIPPER FOR COAXIAL CABLES绝缘剥漆钳INSULATING VARNISH STRIPPER剥线刀WIRE STRIPPING KNIFE绝缘胶带INSULATING TAPE压线钳CRIMPING PLIERS锁把式压线钳LOCK-GRIP CRIMPING PLIERS端子压线钳WIRE END-SLEEVE PLIERS模块压线夹钳MODULAR LOCK-GRIP CRIMPING PLIERS模块压线钳MODULAR CRIMPING PLIERS精确压线钳PRECISION CRIMPING PLIERS外卡簧钳(轴用)EXTERNAL CIRCLIP PLIERS(ON SHAFTS)直头/弯头外卡簧钳(轴用)内卡簧钳(孔用)INTERNAL CIRCLIP PLIERS(IN BORES)直头/弯头内卡簧钳(孔用)大型/重型卡簧钳X型把X-GRIP大力钳LOCK-GRIP PLIERS平行钳夹大力钳PARALLEL JAW LOCK-GRIP PLIERS宽口大力钳WIDE JAW LOCKING PLIERS滑行杆式大力钳LOCK-GRIP SLIDE CLAMP固定大力钳GRIP WRENCH FOR GLUEING机械工作台钳MACHINE WORKBENCH CLAMP焊接大力钳LOCK-GRIP WELDING CLAMP管子焊接大力钳LOCK-GRIP TUBE WELDING CLAMPC型大力钳LOCK-GRIP C CLAMP水泵钳UNIVERSAL PLIERS(7种设置/5种设置)水泵钳WATER PUMP PLIERS特殊水泵钳SPECIAL WATER PUMP PLIERS可调式高速管子钳HIGH-SPEED PIPE WRENCH WITH SCREW ADJUSTER高速曲口管子钳HIGH-SPEED PIPE WRENCH CURVED迷你链式管子钳MINI CHAIN PIPE WRENCH链钳CHANIN PIPE WRENCH重型管子钳STILLSON PIPE WRENCH断线钳BOLT CUTTERS钳子套装(3件/4件/6件/8件)VDE绝缘安全电工工具VDE INSULA TED SAFETY TOOLSVDE绝缘标准符合DIN EN 60900 IEC 60900:2004以及VDE680 适合在高压区安全工作(AC1000V DC1500V)VDE绝缘螺丝起子VDE SCREWDRIVER(一字/十字/米字/星型/内六角)VDE绝缘起子套装电压传感器/电压测试器VOLTAGE DETECTOR/TESTER绝缘扭力扳手VDE TORQUE WRENCH绝缘双向棘轮扳手VDE REVERSIBLE RA TCHET绝缘六角套筒VDE SOCKET HEXAGONAL绝缘旋具头套筒VDE SCREWDRIVER BIT SLCKETT型绝缘扳手VDE T-HANDLE绝缘延长杆VDE EXTENSION绝缘电工工具组套(3件/8件/14件/108件)VED 3C绝缘手柄套筒扳手VDE SOCKET WRENCH WITH 3C HANDLE绝缘梅花扳手VDE SINGLE-ENDED RING SPANNER WITH DEEP OFFSET绝缘开口扳手VDE SINGLE-ENDED OPEN SPANNERVDE绝缘钢锯HACKSA W绝缘电缆刀VDE CABLE KNIFE绝缘电缆剪CABLE SHEARS棘轮式绝缘电缆剪钳CABLE CUTTERSVDE绝缘电缆剪VDE CABLE SHEARS绝缘剥线钳/绝缘固定剥线钳/绝缘水泵钳/绝缘强力钢丝钳/绝缘斜口钳/绝缘电工斜口钳/绝缘平口钳/绝缘圆头钳/绝缘直头尖嘴钳/绝缘弯头尖嘴钳VDE绝缘橡胶垫VDE RUBBER COVER SHEETVDE绝缘电工安全手套VDE ELECTRICIANS’S SAFETY GLOVES绝缘塑料夹VDE PLASTIC CLAMPS车轮扳手WHEEL WRENCHES十字扳手4 W AY WHEEL WRENCH撬棒TYRE LEVER轮毂罩移除工具HUBCAP RENOVING TOOS配重钳BALANCE-WEINHT PLIERS制动弹簧钳BRAKE-SPRING PLIERS闸线弹簧钳PLIERS FOR BRAKE-CABLE SPRINGS制动钳刷BRAKE-CALIPER BRUSH放油塞扳手(四方)DRAIN-PLUG WRENCH WITH SQUARE油壶OIL CANS过滤器扳手UNIVERSAL FILTER WRENCH皮带钳PULLEY WRENCH阀门研磨机V ALVE GRUNDER阀门研磨工具V ALVE LAPPING TOOS油封钳V ALVE-SEAL PLIERS GUNMETAL FINISH汽缸/活塞环压缩器V ALVE SPRING COMPRESSOR BRIGHT NICKEL-PLA TDE 活塞环钳PISTON RING PLIERS软管夹钳HOSE CLIP PLIERS电极拉马BA TTERY TERMINAL PULLER电池测试器BA TTERY TESTER火花塞套筒SPARK PLUG SOCKET火花塞套筒扳手SPARK PLUG SOCKET WRENCH火花塞刷SPARK-PLUG BRUSH特殊尖冲凿SPECIAL PIN PUNCH弹簧撑开器SPRING SPREADER球头拉拔器UNIVERSAL BALL JOINT REMOVER通用罐UMIVERSAL CANISTER防冻测试器ANTI-FREEZE TESTER安装钳INSTALLA TION PLIERS吸盘SUCTION LIFTER磁性拾取工具MAGNETIC PICK-UP TOOL金属片切割器NIBBER杠杆剪切机LEVER-ACTION TIN SNIPS打孔钳PUNCH PLIERS橡胶锤RUBBER HAMMER塑料锤PLASTIC HAMMER无后坐力锤RECOILLESS HAMMER钳工球头锤ENGINEERS’S BALL PEIN HAMMER钳工锤ENGINEERS’S HAMMER平面刮刀FLA T SCRAPER三角空心刮刀THREE-EDGED HOLLOW-GROUND SCRAPER三角实心刮刀THREE-EDGED FLA T-GROUND SCRAPER密封刮刀GASKET SCRAPER平锉HAND FILE圆锉ROUND FILE三角锉TRIANGULAR FILE半圆锉HALF-ROUND FILE锉类6件套装中心冲/凿/开口销冲CENTRE PUNCHES/CHISELS/DRIFT PUNCHES 钢锯HACKSA W栓孔锯KEYHOLE SA W小金属锯SMALL METAL SA W小PUK钢锯PUK JUNIOR HACKSA WHOBBY锯台钳/台虎钳METALWORKING VICE(100/125/150mm)钢卷尺STEEL TAPE MEASURE(3米/5米/8米)阀塞尺V ALVE FEELER GAUGE塞尺火花塞塞尺SPARK PLUG GAUGE螺纹规THREAD GAUGE游标卡尺POCKET VERNIER CALLIPER数显游标卡尺DIGITAL CALLIPER划线器SCRIBER镊子TWEEZERS十字镊子CROSSLOCK TWEEZERS螺钉取出器BOLT EXTRACTOR断螺钉取出器套装SCREW EXTRACTOR SET机械螺母破开器MECHANICAL NUT SPLITTER螺栓插入及取出器STUD INSERTER AND EXTRACTOR丝锥THREAD FILE管子割刀PIPE CUTTER自动切割机AUTOMA TIC PIPE CUTTER链式切管机CHAIN PIPE CUTTER虹吸扳手SIPHON TRAP PLIERS钢丝刷WIRE BRUSH锉刀清洁刷FILE CLEANING BRUSH裁缝剪TAILORS SCISSORS发光二极管井下检查灯LED INSPECTION LAMP井下检查灯INSPECTION LAMP发光二极管工作灯LED WORK LIGHT工程锤ENGINEERS HAMMER ROTBAND-PLUS工程圆头锤ENGINEERS’BALL PEIN HAMMER胡桃木备用手柄SPARE HANDLE HICKORY工匠锤JOINERS’HAMMER ROTBAND-PLUS石匠锤CLUB HAMMER双面石匠锤DOUBLE FACED CLUB HAMMER ROTBAND-PLUS大锤SLEDGE HAMMER大碎石锤STONE SLEDGE HAMMER劈木锤WOOD SPLITTING HAMMER铺路锤PA VING HAMMER单板锤VENEER HAMMER磁性锤MAGNETIC HAMMER ROTBAND玻璃装配工锤GLAZIERS HAMMER炭化合金瓦锤CARBIDE TILE HAMMER羊角锤CLA W HAMMER电焊敲锤SCALING HAMMER ROTBAND-PLUS无弹力安全锤RECOILLESS HAMMER安全锤SAFETY HAMMER SOFT-PLUS塑料锤PLASTIC HAMMER橡皮锤RUBBER MALLET HARD尼龙锤NYLON HAMMER木锤WOOLEN MALLET铜锤COPPER HAMMER CLUB SHAPE铝锤ALUMINIUM HAMMER ROTBAND桶形铝锤LEAD HAMMER SARREL SHAPE冷凿锤COLD CHISEL HAMMER热凿锤HOT CHISEL HAMMER平底压摸锤SET HAMMER TOP PART压槽铁锤TOP FULLER上型模锤BOTTOM FULLER冲锤PUNCH HAMMER镰刀锤SCYTHE HAMMER锻工钳BLACKSMITH’S TONGS铆钉钳RIVETTING TONGS锥型冲子/中心冲子/销式冲子DRIFT PUNCHES/CENTRE PUNCHES/PIN PUNCHES 自动中心冲子AUTOMA TIC CENTRE PUNCH WITH TIP冲子组套DRIFT PUNCH SET铆钉装配器RIVET SETTER字母及数字冲子LETTER AND NUMBER PUNCHES装配冲子SETTING PUNCH撬杆PRVBAR起钉器NAIL FIFER OCTAGONAL撬棍CROWBAR通用拉马UNIVERSAL PULLER两爪拉马PULLER 2-ARM PA TTERN三爪拉马PULLER 3-ARM PA TTERN防腐蚀拉马COROSTOP PULLER PA TTERN快速拉马QUICK-ACTION PULLER两爪液压拉马UNIVERSAL 2-ARM PULLER拉马延长杆EXTENSION FOR PULLERS液压轴杆HYDRAULIC PRESSURE SPINDLE三爪液压拉马UNIVERSAL 2-ARM PULLER拉马套装PULLER SET螺母劈开器NUT SPLITTER液压螺母劈开器NUT SPLITTER HYDRAULIC螺栓提取器STUD EXTRACTOR轴承提取器BALL BEARING EXTRACTOR滚珠轴承提取器套装BALL BEARING EXTRACTOR SET内提取器INTERNAL EXTRACTOR冲击轴承拉马IMPACT BEARING PULLER汽缸拉马CYLINDER LINER PULLER COMPLETE WITH SUPPORT BRACE分离拉马SEPARA TOR PULLER轴承分离器BEARING SEPARA TOR传动轴轴承拉马DRIVE SHAFT BEARING PULLER分离器及拉马套装SEPARA TOR AND PULLER SET拉拔卡盘PULLING CHUCK液压泵HYDRAULIC PUMP液压手泵HYDRAULIC HAND PUMP液压工具拉马1.50 PULLER FOR HUDRAULIC IMPLEMENT1.50液压增力器HYDRAULIC PRESS轮毂拉马WHEEL-HUB PULLER传动轴拉马DRIVE-SHAFT PULLER方向盘拉马STEERING-WHEEL PULLER装配叉DISMANTLING AND ASSEMBLY FORK球头拉拔器BALL JOINT PULLER三爪机滤扳手OIL FILTER HOOK弹簧撑SPRING SPREADER塑料轴承安装套装PROFESSINAL PLASTIC BEARING INSTALLA TION SET法兰分离器FLANGE SEPARA TORS轨距测量器TRACK ALIGNMENT GAUGE扳手WRENCHES管子切割器PIPE CUTTERS扩口工具FLARING TOOLS弯管机PIPE BENDERS管子工具PLUMBING TOOLS铁皮剪/断线钳TIN SNIPS/BOLT CUTTERS管子清洁设备PIPE CLEANING EQUIPMENT弯管系统PIPE BENDING SYSTEMSSNAP管道扳手PIPE WRENCH ECK-SNAP钢管切割器PIPE CUTTER TUBEX FOR STEEL PIPES生铁管切割器PIPE CUTTER TUBEX FOR CAST IRON PIPES不锈钢管切割器RA TCHET PIPE CUTTER NIRO FOR STAINLESS STEEL PIPES 管子修边器PIPE DEBURRING REAMER不锈钢管修边器PIPE DEBURRING REAMER FOR STAINLESS STEEL PIPES 扩口工具套装FLARING TOOL SET BOERDEX钢管扩口钳EXPANDER PLIERS FOR COPPER PIPES带滑轨的弯管机PIPE BENDER WITH SLIDE RAIL带滚轴的弯管机PIPE BENDER WITH ROLLER弯管钳PIPE BENDING PLIERS带滑轨的弯管钳PIPE BENDING PLIERS WITH SLIDE RAIL带滚轴的弯管钳PIPE BENDING PLIERS WITH ROLLER手动弯管机MANUAL BENDING TOOL液压弯管机HYDRAULIC PIPE BENDER手动液压弯管机PIPE BENDING MACHINE FOR MANUAL HYDRAULIC OPERA TION 电动液压弯管机PIPE BENDING MACHINE FOR ELECTRO HYDRAULIC OPERA TION 管道矫直工具PIPE STRAIGHTENING TOOL金属片弯边钳SHEET METAL CRINPING PLIERS折边钳SEAMING PLIERS快速夹取扳手QUICK-CLAMP WRENCH夹管钳GRIPPING PLIERS分级扳手STEPPED KEY复合分级扳手COMBINA TION STEPPED KEY铁皮剪TIN SNIPS /HOLE CUTTING SNIPS /PELICAN PA TTERN SNIPS断线钳BOLT CUTTER管道清洁软轴FLEXIBLE PIPE CLEANING SHAFT排水管清洁器DRAIN PIPE CLEANER工作台几工作桌WORKBENCHES AND WORK TABLES工具车TOOL TROLLEYS工具柜TOOL CABINETS车间推车WORKSHOP TROLLEYS抽屉柜/箱DRA WER-CABINETS/BOXES衣柜/工作服柜W ARDROBES矮橱LOWER CUPBOARD UNIT图纸夹DRA WING HOLDER电源面板PWER SUPPLY PANEL防酸放腐蚀工作台面板六边形工作台HEXAGONAL WORKBENCH带抽屉工作台WORKBENCH WITH DRA WER CABINET塑料抽屉插件PLASTIC DRAWER INSERT工作桌推车WORKSHOP TABLE TROLIEYS工作台WORKBENCH带背板工作台坚固推车TROUGH TROLLEY平板车PLA TFORM TROLLEY带手柄平板车PLA TFORM TROLLYE WITH HANDLE维护推车SERVICE TROLLEY带工具箱车间推车WORKSHOP TROLLEY WITH TOOL CHEST工具箱TOOL CHEST存放斗STORAGE TRAY卷纸架PAPER ROLL HOLDER垃圾桶W ASTE BASKET移动架写字板LECTERN WORKTOP存储盒STORAGE BOXES带门库架CUPBOARD WITH SHELVING WITH DOORS开敞式壁板COMPLETE PANEL SYSTEM WITH SLOTTED PANELS存物柜LOCKER WITH HINGED DOORS滑门橱CUPBOARD WITH SLIDING DOORS电脑柜COMPUTER CABINET桌上设备DESK INSTALLA TION移动电脑架PC STAION MOBILE电脑车间组合PC WORKPLACE COMBINA TION更衣室条凳CHANGING CUBICLE SEA T BENCH安全橱SAFETY CUPBOARD衣橱CLOTHES LOCKER带凳子的衣橱CLOTHES LOCKER WITH SEA T BENCH消防员衣橱FIREFIGHTER’S CUPBOARD工具橱TOOL CABINET移动式可回收物品垃圾收集箱RECYCLING WASTE-COLLECTION CONTAINER MOBILE 固定可回收物品垃圾收集箱RECYCLING WASTE-COLLECTION CONTAINER STA TIONARY 分类垃圾收集站W ASTE-COLLECTION STA TION CONTAINER立式烟灰缸STAND ASHTRAYOCHSENKOPF系列斧头欧洲ILTIS型斧制图用刮刀专业伐木斧快劈斧抢险袖珍刀CAROLUS特殊工具KLANN汽车专用工具弹簧压缩器横杆球头拉拔器轮轴拉马液压手用压力器轴衬提取器发动机锁定工具套装扳手Wrenches/套筒Sockets开口扳手 Open End Wrenches梅花扳手 Spline End Wrenches块扳手 Crowfoot Wrenches开口/梅花扳手 Combination Wrenches内六角扳手 Hex Wrenches平板棘轮扳手 Slab Ratchet棘轮扳手 Ratchet Wrenches力矩扳手 Torque Wrenches管钳 Pipe Wrenches活动扳手 Adjustable Wrenches六角套筒 Six Point Sockets梅花套筒 Twelve Point Sockets万向套筒 Universal Socketsadjustable wrench 活(动)扳手, 可调扳手coach wrench 活(动)扳手, 可调扳手monkey wrench 活(动)扳手, 可调扳手adjustable flat wrench 扁平活动扳手adjustable tap wrench 可调丝锥扳手Allen wrench 通用板手alligator wrench 管扳手, 管钳angle wrench 斜口扳手bent wrench 弯头板手box wrench 套筒扳手brace wrench 曲柄头扳手breaker point wrench 电流开关扳手bulldog wrench 管子扳手carriage wrench 套筒板手chuck wrench 卡盘扳手circular ended wrench 套筒扳手claw wrench 钩形扳手closed-end wrench 闭口扳手coach wrench 活动扳手construction wrench 大型安装扳手cylinder wrench 圆筒扳手deep socket wrench 长套管型套筒板手diagonal wrench 活扳手, 瑞典式扳手double end "alligator type "wrench 双头鳄口扳手, 双头管扳手double hexagon end cap wrench 六角螺帽双头扳手double hexagon opening double offset box socket wrench 双头弯脖梅花扳手double hexgonal S-shaped closed double head wrench 套六角环形两头固定扳手double square closed single head wrench 套方环形一头固定扳手double-head wrench 双头扳手electric socket wrench 套筒电扳手electrode wrench 电极扳手end wrench 平板手flange wrench 凸缘扳手fork wrench 叉形板手free box wrench 活套筒扳手free lever hexagonal fixed socket wrench 活柄六角固定套筒扳手free lever swinging socket wrench 活柄活动套筒扳手fuse wrench 引信扳手grip wrench 管子钳head bent adjustable wrench 弯头活动扳手hexagonal closed double bead wrench 六角环形双头扳手hexagonal inserted handle box wrench 六角插柄套筒扳手hexagonal socket wrench 六角套筒扳手hose wrench 软管扳手hub wrench 轮毂螺母扳手impact wrench 拧紧扳手, 套筒[机动]板手, 冲头machine wrench 机器板手main bearing wrench 主轴承扳手male wrench 套筒扳手monkey wrench 管子钳, 活动板手monkey adjustable wrench 活动扳手monkey screw wrench 活扳手motor wrench 管子钳multiple-dimensioned double head wrench 多尺度双头扳手nozzle wrench 喷嘴扳手nut wrench 螺母扳手, 扳子offset wrench 斜口扳手off-set pattern socket wrench 弯脖套筒扳手open end wrench 开口板手packing nut wrench 填密螺母扳手pin face wrench 叉形带销扳手pipe wrench 管扳手, 管钳子pipe spanner wrench 管(子)钳piston wrench 活塞扳手plug wrench 火花塞专用扳手pneumatic nut wrench 风动螺母扳手propeller shaft turning wrench 螺旋桨轴扳手ratchet wrench 棘轮扳手rear suspension wrench 后悬挂螺母扳手rear-wheel bearing nut wrench 后轮轴承螺母扳手rim wrench 轮缘扳手roll grip pipe wrench 链条管子钳screw wrench 螺钉扳手set-screw wrench 止动螺钉扳手, 固位螺钉板手shifting wrench 活口扳手single-pin type spanner wrench 单销式扳手sleeve-pipe wrench 套筒扳手snap-on socket wrench 有爪套筒扳手socket off-set wrench 弯头套筒扳手socket ratchet wrench 套筒棘轮扳手solid wrench 死扳手, 呆板手spanner wrench 活动扳手, 开脚板手, 插头[销]板手spark plug socket wrench 火花塞(套筒)扳手spider wrench 星形套筒扳手square box wrench 方套筒扳手square head wrench 方头螺栓扳手square inserted handle box wrench 四方插柄套筒扳手square normal closed double head wrench 四方环形双头扳手square single end tubular wrench 四方单头套筒扳手square socket wrench 方套筒扳手square S-shaped closed double head wrench S形四方环形双头扳手straddle wrench 叉形扳手straight shank socket wrench 直柄套筒扳手tap wrench 铰杠; 丝锥扳手, 螺丝攻板手T-handle square fixed socket wrench 丁字柄四方固定套筒扳手tommy wrench 螺旋头部用(活动)杆(如虎钳上)套筒扳手tool-post wrench 刀架扳手torque wrench 转矩扳手torque measuring wrench 转矩指示扳手track wrench 轨道扳钳union wrench 联管节扳手, 管接头板手universal socket wrench 万能套筒扳手wheel wrench 轮扳手。
实验室器材专利申请书模板(3篇)
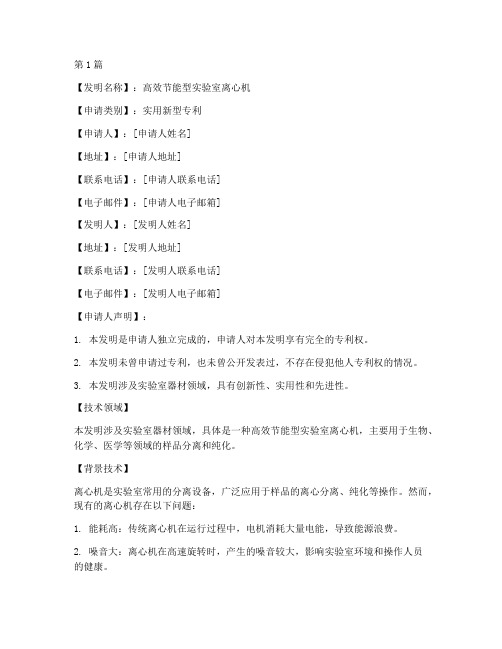
第1篇【发明名称】:高效节能型实验室离心机【申请类别】:实用新型专利【申请人】:[申请人姓名]【地址】:[申请人地址]【联系电话】:[申请人联系电话]【电子邮件】:[申请人电子邮箱]【发明人】:[发明人姓名]【地址】:[发明人地址]【联系电话】:[发明人联系电话]【电子邮件】:[发明人电子邮箱]【申请人声明】:1. 本发明是申请人独立完成的,申请人对本发明享有完全的专利权。
2. 本发明未曾申请过专利,也未曾公开发表过,不存在侵犯他人专利权的情况。
3. 本发明涉及实验室器材领域,具有创新性、实用性和先进性。
【技术领域】本发明涉及实验室器材领域,具体是一种高效节能型实验室离心机,主要用于生物、化学、医学等领域的样品分离和纯化。
【背景技术】离心机是实验室常用的分离设备,广泛应用于样品的离心分离、纯化等操作。
然而,现有的离心机存在以下问题:1. 能耗高:传统离心机在运行过程中,电机消耗大量电能,导致能源浪费。
2. 噪音大:离心机在高速旋转时,产生的噪音较大,影响实验室环境和操作人员的健康。
3. 效率低:传统离心机分离效果不佳,需要较长时间才能完成分离操作。
针对上述问题,本发明提供了一种高效节能型实验室离心机,具有以下优点:1. 节能降耗:采用新型电机和节能设计,降低运行过程中的能源消耗。
2. 降低噪音:采用隔音材料和优化设计,降低离心机运行时的噪音。
3. 提高效率:采用高效分离技术,缩短分离时间,提高工作效率。
【发明内容】本发明提供一种高效节能型实验室离心机,包括以下技术特征:1. 主体:由金属或塑料材料制成,具有足够的强度和稳定性。
2. 电机:采用高效节能电机,具有较低的能耗和噪音。
3. 轴承:采用高性能轴承,具有较长的使用寿命和良好的旋转性能。
4. 离心杯:采用耐腐蚀、耐磨材料制成,具有足够的强度和稳定性。
5. 控制系统:包括电源、电机驱动器、显示屏、按键等,用于控制离心机的运行参数。
6. 隔音装置:采用隔音材料和结构,降低离心机运行时的噪音。
美国迈诺MTT扭矩扳手
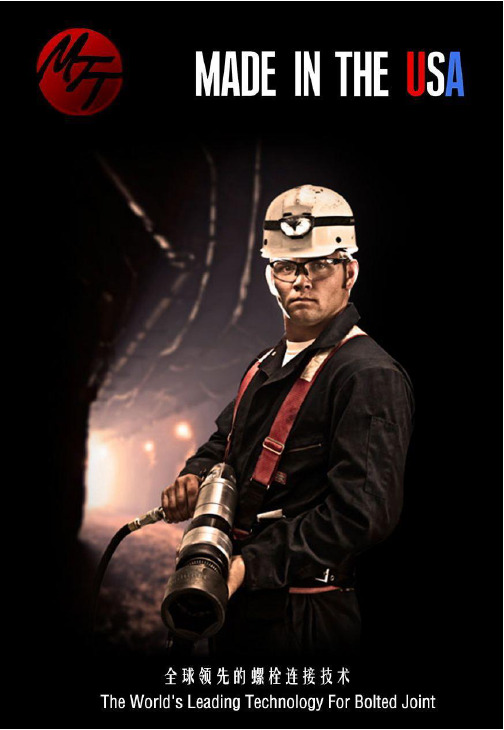
气动扭矩扳手专利的高速齿轮箱技术,操作更高效。
全球最高精度保证:扭矩精度:±3%。
AQ 70 航空专用铝合金外壳,轻便耐用。
扭矩过载保护系统,有效保护齿轮及机械系统。
两速机械换挡,适应更多工况需求。
最大功率下耗气量 0.67 m ³/m(680L/min)。
N.I.S.T (美国国家标准技术协会)可溯源的检验认证型号 MTT 7 MTT 13 MTT30 MTT40 MTT50扭矩范围Nm80-900 135-1760 339-3392 475-5020 678-6785驱动方身L3/4〞 1〞 1〞 11/2〞11/2〞直径D74 93 98 99 120外形尺寸 mm 长度 A307 319 367 402 434高度B190 190 190 190 190空载转速 RPM60 25 10 8 6本体重量Kg4.98 6.35 8.15 8.61 13.15电动扭矩扳手电源要求:220V/50Hz 。
可靠的行星齿轮系统。
耐用稳定的电机系统。
全球最高精度保证:扭矩精度:±3%。
符合人体工程学的设计,使用更方便。
N.I.S.T (美国国家标准技术协会)可溯源的检验认证 型号 MTT 7 E MTT 13 E MTT30EMTT40EMTT50E扭矩范围 Nm 100-825 251-1752 502-2852 800-4703 1200-6505驱动方身 L 3/4〞 1〞 1〞 1〞或11/2〞1 1/2〞直径 D74 93 98 99 120外形尺寸mm长度 A484 496 545 565 611高度B140 140 140 140 140空载转速 RPM64 27 10 7 6本体重量kg6.34 6.79 9.06 9.51 14.05所有 MTT 产品出厂前均经完整测试,符合 N.I.S.T 可溯源的检验认证。
所有校准符合 ISO/IEC 17025:2005/ ANSI/NCSL/Z-5401-1994及10CFR50. App. B.要求时风工业技术(上海)有限公司时风工业技术(上海)有限公司。
- 1、下载文档前请自行甄别文档内容的完整性,平台不提供额外的编辑、内容补充、找答案等附加服务。
- 2、"仅部分预览"的文档,不可在线预览部分如存在完整性等问题,可反馈申请退款(可完整预览的文档不适用该条件!)。
- 3、如文档侵犯您的权益,请联系客服反馈,我们会尽快为您处理(人工客服工作时间:9:00-18:30)。
PLUNGER TYPE WATER PUMPFIELD OF THE INVENTIONThe present disclosure generally relates to the technical field of positive5displacement hydraulic pumps, and particularly, to a plunger type water pump. More particularly, the present disclosure relates to a fully water-lubricated ultra-high-pressure plunger type water pump.BACKGROUND OF THE INVENTION10With the advent of the worldwide energy crisis and enhancement of people’s environmental protection awareness, water hydraulic technologies have been found to have advantages over oil hydraulic systems in many application fields (e.g., duringunderwater operations, or in buoyancy adjustment of manned submersibles) owing to the special physicochemical properties of the water medium. Accordingly, water hydraulic 15technologies have experienced a rapid development.However, because viscosity of the water is only about 1/30~1/50 of that of the commonly used hydraulic oil, it is less apt to form a water film and also has poorlubricity. Meanwhile, because of the strongly corrosive nature of the water andparticularly the sea water, selection of materials used in water hydraulic systems is20limited. This imposes great difficulties in design of friction couplings of waterhydraulic elements. For these reasons, in contrast to oil hydraulic pumps, matured axial water hydraulic pumps are mostly designed to work at a medium or high pressure, which is usually 12 MPa ~21 MPa.A fully water-lubricated sea-water/fresh-water pump in the prior art adopts a plate25valve for flow distribution, and has a flow rate of 10 L/min~170 L/min, a pressure of 14 MPa~16 MPa and an overall efficiency of higher than 82%. A schematic structuralview of such a pump is shown in FIG. 1. As shown, this fully water-lubricatedsea-water/fresh-water pump features a compact structure, full water lubrication of thefriction couplings, and easy maintenance. Unfortunately, such a pump also suffers from the following shortcomings:1. The maximum working pressure is 16 MPa, which cannot satisfy the needs inparticular applications, for example, in the buoyancy adjusting system of a large-depth(i.e., the submerging depth exceeds 3,000 meters) manned submersible.52. Distributing the flow by use of a valve plate is, on one hand, unsuitable foropen systems because the valve plate is sensitive to pollutants, and on the other hand,makes it difficult to ensure the volumetric efficiency when the water is high-pressurized.3. As a mechanism comprised of a swash plate and a shoe is used, a large lateralforce is applied by the plunger to the cylinder. Hence, serious abrasion will occur to the 10friction coupling after the water is high-pressurized.For water hydraulic pumps of higher pressures, a crank-shaft and connecting-rod structure is usually adopted, and a mineral oil lubricated structure with the oil and thewater being separated is used for the primary frictional coupling. Water hydraulicpumps of this structure are one of the kinds that are the most widely used around the15world, an example of which is a triple plunger pump in the prior art whose pressure range is 55 MPa~275 MPa. However, the water hydraulic pumps of this structure mainly have the following problems:1) They have a low rotation speed (100 rev/min ~500 rev/min), a bulky volume,and a small power-to-weight ratio. If the rotation speed is increased to decrease the20volume of the pump, the seal between the water cavity and the lubricant oil cavity would be overheated and even fail, which is particularly the case under high-pressureconditions. Meanwhile, the temperature of the oil in the closed lubricant oil cavity may also increase due to poor heat dissipation to cause degradation of the oil.2) Lubricant oil must be used for lubrication, which tends to cause oil pollution;25furthermore, when the water hydraulic pumps are used in deep sea environments, anadditional pressure compensation device must be used, which makes the whole structure very complex.SUMMARY OF THE INVENTIONAn objective of embodiments of the present disclosure is to provide a plunger type water pump that can achieve water lubrication of all friction couplings, surely have a high volumetric efficiency and a high power-to-weight ratio under ultra-high-pressureworking conditions, and reduce the frictional abrasion of the friction couplings under5high-speed heavy-load conditions so as to prolong the service life of the pump. Theplunger water pump can suitably adopt the sea water or fresh water as a working medium, and can also suitably adopt other fluids of a low viscosity as a working medium.To achieve the aforesaid objective, the plunger type water pump of the present disclosure comprises a pump body, a rotary unit and a plunger flow-distributing unit.10The pump body comprises a cavity body, a water pump inlet and a water pump outlet; the rotary unit comprises a rotary main shaft and is disposed in the pump body; and theplunger flow-distributing unit is disposed in the pump body. The plungerflow-distributing unit comprises a flat valve assembly, a plunger-shoe assembly and asupporting valve assembly. The plunger-shoe assembly is disposed inside the cavity15body and divides the cavity body into a high-pressure cavity, a low-pressure cavity and a lubrication cavity independent of each other; the supporting valve assembly is in fluidcommunication with the low-pressure cavity; the flat valve assembly is in fluidcommunication with the high-pressure cavity; and the rotary unit is disposed inside the lubrication cavity and is in fluid communication with the low-pressure cavity via a flow 20passage and the supporting valve assembly. Driven by the rotary main shaft, theplunger-shoe assembly reciprocates to impel the flat valve assembly and the supporting valve assembly to cooperate with each other so that the flat valve assembly takes in and discharges water through the water pump inlet and the water pump outlet respectively and the supporting valve assembly provides fluid lubrication for the rotary unit at the same25time.According to a preferred embodiment of the present disclosure, the flat valve assembly comprises an intake valve and a delivery valve formed integrally, an inlet of the intake valve is in fluid communication with the water pump inlet, an outlet of the deliveryvalve is in fluid communication with the water pump outlet, and an outlet of the intakevalve is in fluid communication with an inlet of the delivery valve.According to a preferred embodiment of the present disclosure, the rotary unitfurther comprises a reset spring, a set plate and a swash plate disposed in sequence on therotary main shaft; the plunger-shoe assembly comprises a stepped plunger, a connecting 5rod and a shoe, wherein the connecting rod is movably connected to the stepped plungerand the shoe respectively at both ends thereof by means of ball friction couplings; and aplunger passage is further disposed in the cavity body, with an end of the stepped plungerbeing slidably disposed in the plunger passage, wherein: one side of the set plate makescontact with the reset spring, the other side of the set plate makes contact with the shoe, 10and under the action of the reset spring, the set plate presses a bottom of the shoe tightlyagainst a surface of the swash plate so that rotating movement of the swash plate istransferred by the shoe and the connecting rod to the stepped plunger to impel the steppedplunger to reciprocate in the plunger passage, and the high-pressure cavity and thelow-pressure cavity independent of each other are formed between a small-diameter end 15of the stepped plunger and the plunger passage and between a large-diameter end of thestepped plunger and the plunger passage respectively.According to a preferred embodiment of the present disclosure, the plunger-shoeassembly further comprises a stepped plunger casing disposed in the plunger passage, andthe stepped plunger is disposed inside and slidably makes direct contact with the stepped 20plunger casing.According to a preferred embodiment of the present disclosure, the steppedplunger comprises recesses disposed on a surface thereof and damping holes that aredisposed radially and in fluid communication with the high-pressure cavity, and therecesses are in communication with the damping holes.25According to a preferred embodiment of the present disclosure, the surface of theswash plate that makes contact with the bottom of the shoe is applied with a polymericwear-resistant layer, and the polymeric wear-resistant layer is made of one ofpolyetheretherketone (PEEK) and polytetrafluoroethylene (PTFE).According to a preferred embodiment of the present disclosure, a ball end of the connecting rod that forms one of the ball friction couplings with the stepped plunger is formed of two semi-spherical rings tightened together, a surface of each of thesemi-spherical rings is formed with threads, and the semi-spherical rings are connected with one of the stepped plunger and the connecting rod by means of the threads.5According to a preferred embodiment of the present disclosure, the supporting valve assembly comprises a supporting intake valve and a supporting delivery valve, and the low-pressure cavity is in fluid communication with an outlet of the supporting intake valve and an inlet of the supporting delivery valve; the rotary unit further comprises an axial slide bearing and a radial slide bearing that mate with the rotary main shaft; and a 10fluid passage is disposed in the rotary main shaft and the pump body respectively toallow the supporting delivery valve to keep in fluid communication with the axial slide bearing and the radial slide bearing so that lubrication and supporting are achieved for the axial slide bearing and the radial slide bearing.According to a preferred embodiment of the present disclosure, a stepped15supporting cavity in fluid communication with the low-pressure cavity is disposed at the bottom of the shoe of the plunger-shoe assembly; and the rotary unit further comprises a damper disposed inside the pump body, the axial slide bearing is formed with an annular groove on an end surface thereof, the annular groove is in fluid communication with the damper, and the damper is further in fluid communication with an outlet of the supporting 20delivery valve through a flow passage formed inside the pump body.The embodiments of the present disclosure have but are not limited to the following technical benefits:1. Because all the friction couplings of the pump are lubricated by water as aworking medium, the volume of the pump is reduced, and the heat generated during25operation of the pump can be carried away by the working medium to ensure a lowthermal equilibrium temperature of the pump. Because the full water lubrication makes it unnecessary to replace the lubricant oil of the pump periodically, the maintenance issimplified and the operational cost is reduced; meanwhile, the potential environmentalpollution caused by leakage of the lubricant oil is avoided, which makes the pumpenvironment friendly.2. As the two closed cavities formed between the stepped plunger and the steppedplunger casing communicate respectively with the flat valve assembly and the supportingvalve assembly that are independent of each other, the high-pressure water output by the 5ultra-high-pressure pump and the low-pressure water used for static-pressure supportingand lubrication are separated from each other, which can ensure a high volumetricefficiency of the ultra-high-pressure water pump under ultra-high-pressure conditions andsurely provide the fluid supporting and lubrication for the friction couplings underhigh-speed heavy-load conditions.103. Through the static- and dynamic-pressure mixed fluid supporting, the problemof serious frictional abrasion of the slide bearings lubricated by water under high-speedheavy-load conditions is solved, and full water lubrication is achieved for thehigh-pressure water pump. The fully water-lubricated ultra-high-pressure water pump isenvironment friendly and easy to maintain; and particularly when used in deep sea15environments, it eliminates the need of an additional pressure compensation device ascompared to the conventional high-pressure water pump where the oil and the water areseparated from each other, and this can simplify the structure and improve the reliability.4. The drive mechanism in the form of a swash plate and a connecting rod canreduce the lateral force applied by the plunger to the stepped plunger casing, thus easing 20the abrasion of this friction coupling.5. The stepped plunger can reduce the contact specific pressure between the ballend of the connecting rod and the shoe under ultra-high-pressure conditions and increasethe fluid supporting area of the shoe, thus improving the fluid supporting and lubricationperformance between the shoe and the swash plate.256. The spherical recesses formed on the plunger further communicate with thehigh-pressure cavity via fine damping holes to form a dual damping effect between theplunger and the stepped plunger casing, which can prevent sticking of the plunger andreduce the direct abrasion therebetween. The recesses on the surface of the plunger alsohelps to reduce the contact pressure between mating surfaces, restrict movement ofabrasive particles and locally form a dynamic-pressure supporting effect, thus solving the problem of abrasion of the plunger coupling under high-speed heavy-load conditions and prolonging the service life of the ultra-high-pressure pump.7. The flat valve is an integrated assembly in which the intake valve and the5delivery valve are formed integrally, so it can be replaced promptly during maintenance to shorten the maintenance time. The flat valve is of a compact ball valve structure and adopts a soft material and a hard material in combination for sealing. Specifically, the valve seat is made of polyetheretherketone (PEEK) and the valve core is made of aceramic material. This not only improves the sealing reliability under high-pressure10conditions, but also reduces the impacting noise between the valve core and the valveseat, thus reducing the noise of the overall pump. The valve core is made of anengineering ceramic material. Because of the higher hardness and lower density of the ceramic material as compared to metal materials, this improves the resistance tocavitation corrosion, decreases the weight of the valve core, and improves the response 15characteristics and shortens the lagging time of the flat valve, thus improving thevolumetric efficiency under high-speed conditions.BRIEF DESCRIPTION OF THE DRAWINGS20In order to more clearly describe the technical solutions of the embodiments of the present disclosure, attached drawings to be used in the detailed description of thedisclosure will be briefly described hereinbelow. Obviously, the attached drawingsdescribed hereinbelow only illustrate some of the embodiments of the present disclosure, and those of ordinary skill in the art can also obtain other attached drawings therefrom 25without the need of making inventive efforts, wherein:FIG. 1 is a schematic structural view of a plunger type pump in the prior art.FIG. 2 is a schematic structural view of a plunger type water pump according to an embodiment of the present disclosure, wherein FIG. 2a shows a status in which thehigh-pressure cavity has the minimum volume and FIG. 2b shows a status in which the high-pressure cavity has the maximum volume.FIG. 3 is a schematic structural view of a flat valve assembly of the plunger type water pump shown in FIG. 2.FIG. 4 is a schematic structural view of a plunger-shoe assembly of the plunger5type water pump shown in FIG. 2.FIG. 5 is a schematic structural view of a semi-spherical ring of the plunger-shoe assembly shown in FIG. 4.FIG. 6 is a schematic partial structural view of a stepped plunger of the plunger-shoe assembly shown in FIG. 4, which illustrates an anti-sticking damping10structure in detail.DETAILED DESCRIPTION OF THE INVENTIONVarious embodiments of the disclosure are now described in detail. Referring to the drawings, like numbers indicate like parts throughout the views. As used in the15description herein and throughout the claims that follow, the meani ng of “a,” “an,” and “the” includes plural reference unless the context clearly dictates otherwise. Also, as used in the description herein and throughout the claims that follow, the meaning of “in”includes “in” and “on” unless the context clearly dictat es otherwise.A schematic structural view of a plunger type water pump according to an20embodiment of the present disclosure is shown in FIG. 2. The plunger type water pump comprises a pump body, a rotary unit and a plunger flow-distribution unit. The pump body comprises a cavity body, a water pump inlet and a water pump outlet. The rotary unit comprises a rotary main shaft 1. The plunger flow-distributing unit mainlycomprises a plunger-shoe assembly 23, a flat valve assembly 13 and a supporting valve 25assembly. The supporting valve assembly comprises a supporting intake valve 17 and a supporting delivery valve 18. The plunger-shoe assembly 23 is disposed in the cavity body and divides the cavity body into a high-pressure cavity 16, a low-pressure cavity 19 and a lubrication cavity 28 independent of each other. The supporting valve assembly isin fluid communication with the low-pressure cavity 19, the flat valve assembly 13 is in fluid communication with the high-pressure cavity 16, and the rotary unit 28 is disposed inside the lubrication cavity 28 and is in fluid communication with the low-pressurecavity via a flow passage and the supporting valve assembly.As shown, the pump body is mainly comprised of an end cover 10, a cylinder 95and an enclosure 3. An end of the cylinder 9 is connected to the enclosure 3, and theother end of the cylinder 9 is provided with the end cover 10. Cavities in the end cover 10, the cylinder 9 and the enclosure 3 together form the aforesaid cavity body. Therotary main shaft 1 is fixed in the lubrication cavity 28 formed by the cylinder 9 and the enclosure 3. A plurality of plunger flow-distributing units (generally there are three to 10seven plunger flow-distributing units depending on different requirements on flowpulsing of the water hydraulic pump in different service environments) are uniformlydistributed along a same circumference with the rotary main shaft 1 as a center.Hereinbelow, the structure and the operation process will be detailed.A left end surface of the back end cover 10 is formed with two threaded holes for15use as an inlet and an outlet of the ultra-high-pressure water pump respectively, and aright end surface of the back end cover 10 is formed with a flow hole 11 and an annular flow groove 14. Stepped holes, a number of which is equal to the number of the plunger flow-distributing units, are formed in a radial direction and uniformly distributed in acircumferential direction of the back end cover 10. Each of the stepped holes is formed 20with threads at the outer side for installing and fixing the flat valve assembly 13. Once the flat valve assembly is installed in place, a locking nut 12 is used to lock the flat valve assembly 13 so that loosing of the flat valve assembly 13 under the action of the cycling hydraulic pressure can be prevented, thus improving the reliability in use of the seawater/fresh water pump in underwater environments.25As shown in FIG. 3, the flat valve assembly comprises a valve body 27, an intake valve and a delivery valve. An inlet of the intake valve communicates with an inlet of the water pump via the annular flow groove 14, an outlet of the intake valvecommunicates with an inlet of the delivery valve, and an outlet of the delivery valvecommunicates with an outlet of the water pump. As shown, the delivery valve isinstalled at a top portion of the valve body 27, and the intake valve is installed at abottom portion of the valve body 27. The delivery valve comprises, in sequence from top to bottom, a delivery valve locking nut 35, a delivery valve spring 34, a deliveryvalve core 33 and a delivery valve seat 32; and the intake valve comprises, in sequence 5from top to bottom, an intake valve spring 31, an intake valve core 30, an intake valve seat 29 and an intake locking nut 28. An interface between the delivery valve and an intake valve serves as both the outlet of the intake valve and an inlet of the deliveryvalve. By designing the intake valve and the delivery valve into a single assembly, the flat valve assembly can be replaced as a whole during the maintenance period to shorten 10the mean time to repair (MTTR) and to improve the on-site maintenanceability.The radial arrangement of the flat valve assembly reduces the axial dimension of the water pump and increases the power-to-weight ratio. The flat valve adopts a seal form of a ball valve and adopts a soft material and a hard material in combination forsealing; specifically, the valve seat is made of PEEK and the valve core is made of15ceramic. Such a compact structure not only improves the sealing reliability underhigh-pressure conditions, but also reduces the impacting noise between the valve coreand the valve seat, thus reducing the noise of the overall pump. Because the valve core is made of a ceramic material which has a higher hardness and a lower density than metal materials, this improves the resistance to cavitation corrosion, decreases the weight of the 20valve core, and improves the response characteristics and shortens the lagging time of the flat valve, thus improving the volumetric efficiency under high-speed conditions.The cylinder 9 is formed with a flow passage 8 in order for the water pump inlet to communicate with the lubrication cavity. In the axial direction, the cylinder 9 isformed with a stepped hole in communication with the plunger piston, and in the radial 25direction, stepped holes twice as many as the plunger flow-distribution units aredistributed and communicate with the axial stepped hole in groups of two. The stepped plunger casing 7 is installed in the axial stepped hole, and each group of radiallydistributed stepped holes is used to install the supporting intake valve 17 and thesupporting delivery valve 18. The inlet of the supporting intake valve 17 communicates with an inlet of the ultra-high-pressure sea water pump via the flow passage 15 and the annular flow groove 14 of the back end cover. The stepped plunger assembly 23 isinstalled in the stepped plunger casing 7, as shown in FIG. 4. The stepped plungerassembly 23 comprises a stepped plunger 36, semi-spherical rings 38, a connecting rod537 and a shoe 39. The connecting rod 37 is formed with an elongate damping hole thatcommunicates with the supporting cavity 42 located at the bottom of the shoe 39, and the supporting cavity 42 is of a multi-step structure. At a large-diameter end of the stepped plunger is formed with a stepped threaded hole, and a ball socket is formed at the bottom of the threaded hole. Each of the stepped plunger assemblies 23 has two semi-spherical 10rings 38 as shown in FIG. 5, which are formed by fabricating a part having male threads and a ball socket and then splitting the part into two pieces. The male threads of the two semi-spherical rings 38 mate with female threads of the plunger, and the ball socketmates with the ball end of the connecting rod. The two ends of the connecting rod 37 are ball ends of different sizes, with the smaller ball end being adapted to mate with the 15ball socket of the plunger. Then, the pair of semi-spherical rings is threaded into thethreads of the stepped plunger 36 so that the connecting rod is connected to the stepped plunger 36 with a ball friction coupling being formed therebetween. This structureeliminates the plastic deformation that would occur on the plunger surface when thesmaller ball end of the connecting rod is connected to the plunger by means of the20common rolling process, so the accuracy of fit between the plunger surface and theplunger hole is improved to result in both an improved sealing performance andimproved friction behaviors. The larger ball end of the connecting rod and the ballsocket of the shoe mate with each other, and may be connected together through a rolling process to form a ball friction coupling. The stepped plunger 36 is formed with25spherical recesses 41 and fine damping holes 40 on a surface of the small-diameter end, as shown in FIG. 6.The drive mechanism in the form of a swash plate and a connecting rod mainly helps to reduce the lateral force between the stepped plunger 36 and the stepped plungercasing 7 as well as the bending moment borne by the stepped plunger 36. Between the small-diameter end of the plunger and the stepped plunger casing 7 is formed thehigh-pressure cavity 16, which communicates with the water pump outlet via the flatvalve located on the end cover so as to output the ultra-high-pressure water; and between the large-diameter end of the plunger and the stepped plunger casing 7 is formed the5low-pressure cavity 19, which communicates with the supporting cavity 42 of the shoe 39 so as to provide the static-pressure supporting between the shoe 39 and the swash plate.The static-pressure supporting and the dynamic-pressure supporting generated by thesupporting cavity 42 of the multi-step structure at the bottom of the shoe 39 coact toimprove the supporting performance between the shoe and the swash plate. The water 10medium used for supporting flows through an axial gap between the shoe 39 and theswash plate into the lubrication cavity 28 (as shown in FIG. 2) which communicates with the pump inlet. The low-pressure cavity 19 further communicates with the outlet of the supporting intake valve 17 and the inlet of the supporting delivery valve 18 to providepressure supporting for the axial slide bearing 6 and the radial slide bearings 5 and 20 via 15the supporting delivery valve 18, thus accomplishing the static- and dynamic-pressuremixed supporting and lubrication. The spherical recesses 41 on the surface of thestepped plunger 36 communicates with the high-pressure cavity 16 via the fine damping holes 40 and a row of recesses located on an end of the stepped plunger so as to provide a dual damping effect between the stepped plunger 36 and the stepped plunger casing 7.20This solves the problem of sticking of the plunger caused by reducing the gap between the stepped plunger casing 7 and the stepped plunger 36 in order to improve thevolumetric efficiency of the ultra-high-pressure pump, and makes it less likely for thestepped plunger 36 and the stepped plunger casing 7 to make direct contact with eachother. These recesses not only reduce the contact stress between the mating surfaces25and restrict movement of abrasive particles, but also locally form a dynamic-pressuresupporting effect. By means of the connecting rod mechanism, the two-stage damping and appropriate design of the surface morphology, abrasion of the plunger frictioncoupling under high-speed heavy-load conditions is avoided.。