铝合金的凝固和组织中的晶粒
铝合金的凝固和组织中的晶粒

铝合金的凝固和组织中的晶粒一、 熔体的凝固过程在半连续铸造过程中,熔体的浇铸和凝固是同时连续地进行的。
对铸锭而言,冷却是分两次实现的。
一次冷却是在结晶器内完成的,熔体进入结晶器后靠结晶器导热,在结晶器内形成一定厚度的凝固壳。
此后随着铸造机下降,被拉出结晶器,遇到结晶器底部浇出的冷却水(称之为二次冷却)从此完成凝固的全部过程。
这个凝固过程在金属学中称为金属结晶。
二、 铸锭的正常晶粒组织从理论上讲,在工业生产条件下,铸锭的晶粒组织由三个区域组成:即外层表面的细等轴晶区,由此往里的柱状晶区和中心等轴晶区。
但在实际铝合金生产中铸锭在强度大的冷却条件下,经过Al-Ti-B的细化处理,铝合金铸锭的组织往往全部是等轴晶。
铸锭晶粒的大小将直接影响铝加工制品的力学性能和加工性能,所以它被作为衡量铸锭质量的一个主要指标。
三、 影响铸锭晶粒的因素1、 熔体结晶的条件:熔体结晶有两个条件是必不可少的,其一是结晶必需要先形成晶核,熔体中的晶核分两种。
自发晶核是在低于结晶温度时,熔体由于能量起伏或液相起伏形成的晶核。
非自发晶核是外来粒子进入熔体后而形成的晶核。
其二是要有过冷度才可能发生结晶,所谓过冷度就是熔体的温度只有在冷却到低于熔点的温度下才能结晶,温度越低过冷度越大。
2、 晶粒的细化:控制过冷度;一般情况下增大过冷度,熔体中的生核率和晶粒的长大速度都增加,但生核速度大于晶粒的增长速度,所以一般情况下金属结晶时过冷度越大,所得到晶粒越细小。
在半连续铸造生产中增加过冷度的主要途径是有降低铸造速度使单位时间内铸锭冷却量增加;降低冷却水的温度使单位时间内铸锭的温降增加;加大冷却水的水压使单位时间内浇到铸锭上的水量增加使铸锭的温降增加;降低铸造温度使铸锭的结晶过程缩短。
3、 动态细化晶粒:对熔体采用机械搅拌、电磁搅拌、超声波振动等,这样一方面可以靠输入的能量使晶核提前生成,另一方面可以使成长中的树枝状晶破碎增加晶核的数目(在这里就要讲一下晶粒的形成,晶粒是先有一个晶核、晶核按多个方向晶轴成长,象树枝一样称之为枝晶,当众多的枝晶共同生长到一定程度互相顶撞,此时熔体添补到枝晶中,围绕它形成了一个枝晶粒)4、 变质处理细化晶粒:向熔体中加入少量的活性物质,促进熔体内部生成晶核或改变晶粒的成长过程,在变形铝合金中一般选用Ti、Zr、B、C等作为晶粒细化剂,我公司铸造时加入Al-Ti-B丝就属于变质处理的方法。
铝合金材料中的晶粒尺寸对性能的影响研究

铝合金材料中的晶粒尺寸对性能的影响研究铝合金是一种非常常见的金属材料,它广泛应用于各种领域,如航空、汽车、建筑和电子等。
铝合金具有良好的重量比、耐腐蚀性和导电性能等优点,因此在许多场合中代替传统的钢铁材料使用。
然而铝合金材料的性能问题也是困扰着制造业的一个难题。
其中一个非常重要的因素就是晶粒尺寸。
晶粒尺寸是指铝合金中晶界的大小,它的大小对材料的力学性能和腐蚀性能等方面有着非常直接和重要的影响。
本文将探讨铝合金材料中的晶粒尺寸对性能的影响研究。
晶粒尺寸对材料性能的影响在铝合金材料中,晶粒尺寸是决定材料性能的一个非常重要的因素。
根据晶粒尺寸的大小,铝合金材料的力学性能、热性能、腐蚀性能等各种性能都会有所不同。
通常情况下,晶粒尺寸越小,材料的性能越好。
首先,晶粒尺寸对铝合金材料的力学性能有着非常重要的影响。
由于存在晶界,晶粒尺寸越小,晶界的数量就会越多。
晶界是固体材料中的缺陷,会对材料的力学性能产生不利影响。
但是,由于晶界的存在可以提高材料的强度和韧性,因此适当增加晶界数量可以使铝合金材料的强度和韧性达到最优化的状态。
因此,晶粒尺寸越小,晶界数量越多,材料的强度和韧性也会越好。
其次,晶粒尺寸还会对铝合金材料的热性能产生影响。
对于金属材料来说,热稳定性是评价其综合性能的一个重要指标。
晶粒尺寸越小,由于晶界对材料的热稳定性有着一定的负面影响,因此材料的热稳定性也会降低。
但是,晶粒尺寸较小的材料其热稳定性可以通过定向凝固等工艺手段进行改善,因此并不是所有情况下晶粒尺寸越小,材料的热稳定性就会越差。
最后,晶粒尺寸还会对铝合金材料的腐蚀性能产生影响。
晶界是金属材料中的电化学反应活动中心,因此处于晶界的区域会更容易发生腐蚀。
晶粒尺寸越小,晶界面积就会增大,从而使得材料的腐蚀速率加快。
因此,如果铝合金材料需要具有较好的耐腐蚀性能,那么需要适当调整晶粒尺寸,以达到平衡解决材料强度和耐腐蚀性能之间的矛盾。
晶粒尺寸控制方法上面已经讨论了晶粒尺寸对铝合金材料性能的影响,接下来就是如何控制晶粒尺寸。
铝及铝合金在熔铸热轧冷轧退火过程中晶粒的演变

7.0mm厚5005热轧卷1/2晶粒
Zhejiang Yongjie Aluminum
7.0mm厚5005热轧卷1/2晶粒
包覆率对钎焊和产品质量的影响
批号117120364热轧终轧温度320℃,为目前正常热终轧温度,该试样在冷轧开 坯阶段取样,热精轧过程中铝板发生动态再结晶,热轧出来的晶粒部分已经再 结晶,晶粒结构为块状晶粒与纤维状晶粒共存。
50
5
0
0
0
100
200
300
400
500
0
100
200
300
400
500
3003铸轧料退火软化试样晶粒组织演变
0.35mm3003-H18晶粒
0.35mm340℃退火晶粒
0.35mm360℃退火晶粒
0.35mm380℃退火晶粒
0.35mm400℃退火晶粒
Zhejiang Yongjie Aluminum
1060S铸锭边部显微组织 1060S铸锭边部50倍晶粒组织
1060S铸锭四分之一50倍晶粒组织
1060S—H14成品200倍晶粒组织
Zhejiang Yongjie Aluminum
3xxx系铝及铝合金晶粒组织形貌
3004铸锭显微组织 3004铸锭100倍晶粒组织
3003-O退火200倍晶粒组织
Zhejiang Yongjie Aluminum
5005热轧卷晶粒组织形貌
批号117120363热轧终轧温度280℃,比正常终轧温度稍低,热轧出来 的晶粒呈长条纤维状。
7.0mm厚5005热轧卷边部
7.0mm厚5005热轧卷边部晶粒 7.0mm厚500热轧卷边部晶粒
7.0mm厚5005热轧卷1/2
金属的结晶过程及纯铝铸锭组织观察

金属的结晶过程及纯铝铸锭组织观察金属的结晶过程是指在高温下,金属原子受到热运动的影响,不断地重新组合,形成晶体的过程。
在这个过程中,金属原子不断地进行扩散、聚集,形成各种大小不同、形状不同的晶粒。
晶粒的大小和形状与金属的温度、冷却速度、成分、合金化元素等因素有关,不同的因素对晶粒的影响程度也不同。
纯铝铸锭组织观察是通过光学显微镜或电子显微镜对纯铝铸锭进行研究和观察,以了解其晶粒大小、形状、分布和组织特征等,并结合铸造工艺参数控制等措施,优化铸造过程,改善铸造品质。
纯铝铸锭是指铝含量高于99.5%的铝合金,常用于电子、航空、汽车、建筑等领域的制造。
在铸造过程中,纯铝铸锭的组织特征对其性能具有重要影响,因此需要对其进行结晶过程和组织特征的研究和观察。
在铸造纯铝铸锭的过程中,一般采用直接液态铸造或半连续铸造的方式,即将铝液直接浇注入铸模中,经过一定的冷却后形成固态铝铸锭。
在冷却过程中,铝液逐渐冷却凝固,金属原子开始重新组合形成晶体。
其结晶过程可分为三个阶段。
第一阶段:铝液开始凝固,开始形成晶核。
晶核的形成是依靠同种金属原子的凝聚,在液相中出现降低的过饱和度,使得最先凝结的一些原子能够将周围的金属原子聚集到一起,形成一个微小的晶体。
这个阶段的晶体是以一定的方向生长的。
第二阶段:晶核的数目急剧增加,晶粒逐渐生长到一定大小,但是晶界还存在一些小角度的错配。
这些小角度错配是随着晶粒的生长正常发生的,直到晶粒长大到一定程度,晶界产生完全的二次错配,才会停止晶粒的生长,形成完整的晶体。
第三阶段:晶界转动,系统达到最低能量状态,晶粒尺寸相对比较均匀。
在铸造中,晶粒尺寸的均匀性对铸造质量的影响很大,一般采用铸造工艺中的一些控制措施来影响晶粒尺寸的均匀程度。
通过光学显微镜或电子显微镜对纯铝铸锭进行观察,可以看到其组织结构呈现出多边形晶粒形态,晶粒大小大致相同。
这是因为纯铝铸锭的晶粒生长受到一定程度的限制,即较小的晶核可以生长到较大的尺寸,但生长的速度较慢。
热处理对铝合金的晶粒细化和织构演化的影响

热处理对铝合金的晶粒细化和织构演化的影响热处理在金属材料的制备过程中起着至关重要的作用。
对于铝合金来说,热处理不仅可以调控其晶粒的尺寸和分布,还可以影响其织构演化。
本文将探讨热处理对铝合金晶粒细化和织构演化的具体影响,并介绍几种常见的热处理方法。
1. 热处理对铝合金晶粒细化的影响热处理是通过控制铝合金的受热过程来实现晶粒细化的一种方法。
热处理过程中,铝合金的晶粒尺寸会发生变化,从而影响其力学性能和电化学性能。
晶粒细化可以提高材料的强度和韧性,改善其塑性变形能力。
在热处理过程中,常用的晶粒细化机制主要包括两种:再结晶和晶界退化。
再结晶是指在加热过程中,原有的晶粒重新长大形成新的晶粒,这样可以得到更小且更均匀的晶粒尺寸。
而晶界退化则是在退火处理过程中,晶粒尺寸逐渐减小,晶界面积增加,从而使晶粒变得更细。
2. 热处理对铝合金织构演化的影响织构是指材料中晶粒取向的统计分布。
对于铝合金来说,织构的形成与其晶粒的取向有着密切的关系。
晶粒的取向对铝合金的力学性能和物理特性有着重要影响。
热处理过程中,晶粒的重新排列会导致织构演变。
例如,在时效处理过程中,晶粒的取向会趋向于与应力场或热流场平行,从而形成特定的织构。
不同的热处理方法会导致铝合金织构的差异,进而影响其力学性能和加工性能。
3. 常见的热处理方法在铝合金的制备过程中,常用的热处理方法包括固溶处理、时效处理和退火处理。
固溶处理是指将铝合金加热至固溶温度,使固溶体中的溶质原子溶解在基体中,形成固溶体。
这一步可以使晶粒细化,提高材料的塑性变形能力。
时效处理是在固溶处理之后,将铝合金加热至时效温度并保持一段时间,使溶质原子重新聚集,形成新的相。
时效处理可以进一步调控晶粒的尺寸和分布,改善材料的强度和韧性。
退火处理是指将铝合金加热至退火温度并保持一段时间,然后缓慢冷却至室温。
退火处理主要用于消除材料中的内应力和组织缺陷,提高其塑性和韧性。
4. 结论通过热处理可以有效地调控铝合金的晶粒细化和织构演化。
铝合金金相组织晶粒度
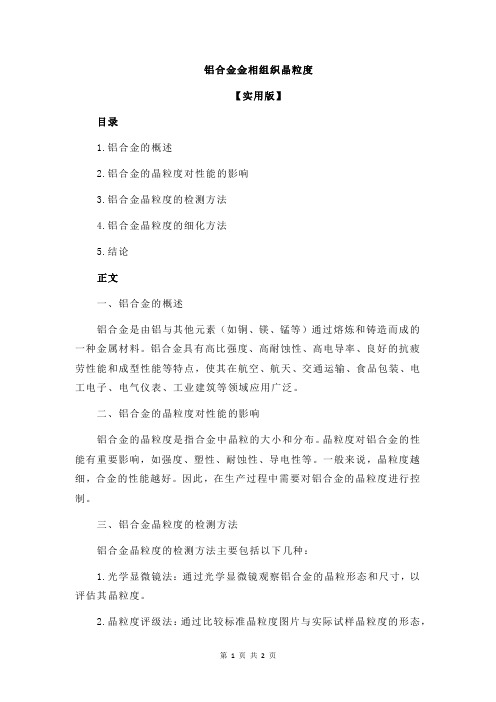
铝合金金相组织晶粒度【实用版】目录1.铝合金的概述2.铝合金的晶粒度对性能的影响3.铝合金晶粒度的检测方法4.铝合金晶粒度的细化方法5.结论正文一、铝合金的概述铝合金是由铝与其他元素(如铜、镁、锰等)通过熔炼和铸造而成的一种金属材料。
铝合金具有高比强度、高耐蚀性、高电导率、良好的抗疲劳性能和成型性能等特点,使其在航空、航天、交通运输、食品包装、电工电子、电气仪表、工业建筑等领域应用广泛。
二、铝合金的晶粒度对性能的影响铝合金的晶粒度是指合金中晶粒的大小和分布。
晶粒度对铝合金的性能有重要影响,如强度、塑性、耐蚀性、导电性等。
一般来说,晶粒度越细,合金的性能越好。
因此,在生产过程中需要对铝合金的晶粒度进行控制。
三、铝合金晶粒度的检测方法铝合金晶粒度的检测方法主要包括以下几种:1.光学显微镜法:通过光学显微镜观察铝合金的晶粒形态和尺寸,以评估其晶粒度。
2.晶粒度评级法:通过比较标准晶粒度图片与实际试样晶粒度的形态,对其进行评级,以评估铝合金的晶粒度。
3.测量法:利用测量仪器(如粒度仪)对铝合金的晶粒度进行测量。
四、铝合金晶粒度的细化方法为了获得良好的铝合金性能,需要对其晶粒度进行细化。
常见的铝合金晶粒度细化方法包括:1.调整熔炼温度:通过控制熔炼温度,使晶粒细化。
2.控制铸造速度:在铸造过程中,适当降低铸造速度,使晶粒细化。
3.添加变质剂:在合金中添加一定量的变质剂,可以使晶粒细化。
4.陶瓷过滤板过滤:在浇铸过程中,使用陶瓷过滤板过滤,可以有效地细化晶粒。
五、结论铝合金的晶粒度对其性能具有重要影响。
通过采用合适的检测方法和细化方法,可以有效地控制铝合金的晶粒度,从而提高其性能。
铸造铝合金断口结晶组织等级标准

铸造铝合金断口结晶组织等级标准一、引言在铸造行业中,铝合金是一种常用的材料,在许多领域都有广泛的应用。
而对于铝合金的质量评定来说,断口结晶组织等级是一个重要的评定标准。
本文将从深度和广度两个角度,探讨铸造铝合金断口结晶组织等级标准的相关内容。
二、浅谈铸造铝合金的断口结晶组织铝合金是一种具有轻质、高强度、良好的耐腐蚀性和导电性的金属材料,因此在航空航天、汽车制造、建筑和电子等领域得到了广泛应用。
而铸造铝合金的断口结晶组织是评定其质量的重要标准之一。
1. 铸造铝合金的结晶组织分类铸造铝合金的结晶组织通常可以分为等轴晶、柱状晶和板条状晶三种类型。
等轴晶是指铸造过程中,晶粒在各个方向上长短基本相等;柱状晶是指晶粒呈柱状,沿着铸件的凝固方向生长;板条状晶则是晶粒呈板条状排列。
不同的结晶组织类型会直接影响铝合金的力学性能和物理性能。
2. 断口结晶组织等级评定标准铝合金的断口结晶组织等级评定标准主要根据晶粒的尺寸、形状和分布情况来进行评定。
晶粒尺寸的大小、形状的规整度以及分布的均匀性都是评定断口结晶组织等级的重要指标。
在实际应用中,通常会采用金相显微镜、扫描电子显微镜等工具对铝合金的断口结晶组织进行观察和评定。
三、深入探讨铸造铝合金断口结晶组织等级标准1. 晶粒尺寸的影响晶粒尺寸是评定断口结晶组织等级的重要指标之一。
通常来说,晶粒尺寸越小,材料的强度和韧性就越好,耐疲劳性和耐腐蚀性也会有所提升。
铝合金的断口结晶组织等级标准中,晶粒尺寸往往是评定材料性能优劣的重要依据之一。
2. 晶粒形状的影响晶粒形状的规整度对铝合金的力学性能也有着重要的影响。
规整的晶粒形状能够使材料的强度更加均匀,提高材料的延展性和塑性。
在评定断口结晶组织等级时,晶粒形状的规整度也是一个重要的考量因素。
3. 晶粒分布的影响晶粒分布的均匀性对铝合金的性能也有着重要的影响。
均匀的晶粒分布能够减少材料中的应力集中现象,提高材料的抗拉强度和抗压强度。
铝合金的组织结构与性能分析

铝合金的组织结构与性能分析铝合金是一种广泛使用的金属材料,其具有良好的耐腐蚀性、高强度、轻量化等特性,被广泛应用于航空航天、汽车、建筑等领域。
铝合金的组织结构与性能是影响其在不同应用领域中性能表现的重要因素。
铝合金的组织结构主要由铝基体和加入的合金元素组成,其中合金元素的种类和含量对铝合金的性能有很大的影响。
常见的铝合金中,掺入铜、锌、镁等元素,通过不同的制造过程,可以得到各具特色的组织结构和性能。
以铜铝合金为例,铜对铝的作用主要是增加合金的强度和热处理稳定性。
在普通状态下,铝合金中的铜元素会溶解在铝基体中,形成固溶体结构。
但当铜元素的含量达到一定程度时,铜元素就会与铝形成非均匀的固溶体,出现脆化现象。
为了避免这种情况的发生,需要对铝合金进行适当的时效处理,使合金中的铜元素重新溶解并沉积到铝基体中,形成均匀的固溶体结构。
除了合金元素的影响外,铝合金的制造工艺也对其组织结构和性能有很大的影响。
例如,在加热、变形等过程中,铝合金的晶粒结构会发生变化。
合适的加热温度和保温时间可以促进铝合金中的晶粒长大,增加其晶粒尺寸,从而提高其力学性能。
但过高的加热温度和过长的保温时间也会引起晶粒过粗,导致铝合金产生裂纹和变形等缺陷。
另外,铝合金的热处理工艺也是影响其组织结构和性能的重要因素。
常见的热处理方式包括固溶处理和时效处理。
固溶处理是将铝合金加热至一定温度,使合金元素溶解在铝基体中,然后快速冷却,形成固溶体结构。
时效处理则是在固溶处理后,将铝合金再次加热,使固溶体结构中的合金元素重新沉淀,形成更为均匀的微观结构,从而提高铝合金的强度和韧性。
总的来说,铝合金的组织结构与性能是相互作用的,不只是由某一因素决定的。
在选择铝合金应用于特定领域时,需要考虑其组织结构和性能特点,选用合适的合金元素和制造工艺,从而最大限度地发挥其优良的性能表现。
铝 粗枝晶偏析-概述说明以及解释
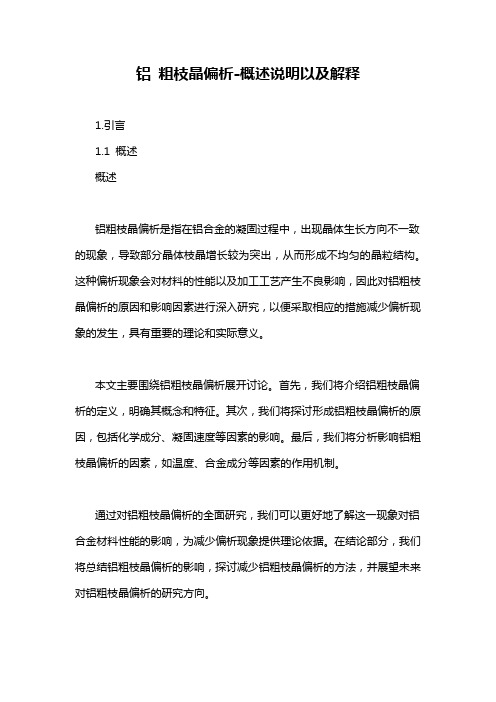
铝粗枝晶偏析-概述说明以及解释1.引言1.1 概述概述铝粗枝晶偏析是指在铝合金的凝固过程中,出现晶体生长方向不一致的现象,导致部分晶体枝晶增长较为突出,从而形成不均匀的晶粒结构。
这种偏析现象会对材料的性能以及加工工艺产生不良影响,因此对铝粗枝晶偏析的原因和影响因素进行深入研究,以便采取相应的措施减少偏析现象的发生,具有重要的理论和实际意义。
本文主要围绕铝粗枝晶偏析展开讨论。
首先,我们将介绍铝粗枝晶偏析的定义,明确其概念和特征。
其次,我们将探讨形成铝粗枝晶偏析的原因,包括化学成分、凝固速度等因素的影响。
最后,我们将分析影响铝粗枝晶偏析的因素,如温度、合金成分等因素的作用机制。
通过对铝粗枝晶偏析的全面研究,我们可以更好地了解这一现象对铝合金材料性能的影响,为减少偏析现象提供理论依据。
在结论部分,我们将总结铝粗枝晶偏析的影响,探讨减少铝粗枝晶偏析的方法,并展望未来对铝粗枝晶偏析的研究方向。
通过本文的深入探讨,我们期望能够为铝合金材料的制备和加工提供一定的理论指导,从而提高铝合金的质量和性能。
1.2 文章结构文章结构部分的内容:本文将按照以下结构进行论述:1. 引言:首先对铝粗枝晶偏析进行概述,包括对其定义、形成原因以及影响因素的简要介绍,同时明确本文的目的和意义。
2. 正文:重点分析铝粗枝晶偏析的相关内容,分为以下几个方面进行论述:2.1 粗枝晶偏析的定义:详细解释粗枝晶偏析的概念,包括铝材料中晶粒的生长过程以及晶粒偏析所导致的现象和问题。
2.2 形成铝粗枝晶偏析的原因:深入探讨形成铝粗枝晶偏析的各种原因,包括温度、合金元素含量、凝固速度等因素对晶粒生长和偏析程度的影响。
2.3 影响铝粗枝晶偏析的因素:进一步分析影响铝粗枝晶偏析程度的各种因素,包括材料处理、合金化改性、凝固条件等对晶粒溶质分配和偏析行为的影响。
3. 结论:总结铝粗枝晶偏析对铝材料性能和工艺加工的影响,并提出减少铝粗枝晶偏析的方法和措施。
金相显微组织下的一些缺陷及图片说明
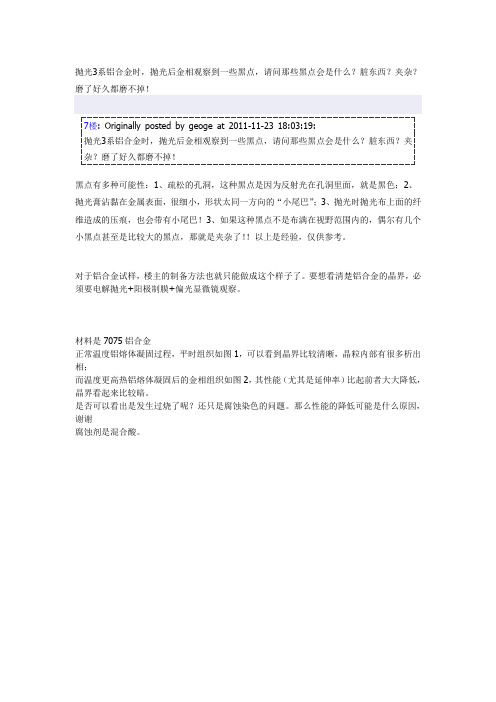
抛光3系铝合金时,抛光后金相观察到一些黑点,请问那些黑点会是什么?脏东西?夹杂? 磨了好久都磨不掉!7楼: Originally posted by geoge at 2011-11-23 18:03:19: 抛光3系铝合金时,抛光后金相观察到一些黑点,请问那些黑点会是什么?脏东西?夹 杂?磨了好久都磨不掉! 黑点有多种可能性:1、疏松的孔洞,这种黑点是因为反射光在孔洞里面,就是黑色;2、 抛光膏沾黏在金属表面,很细小,形状太同一方向的“小尾巴” ;3、抛光时抛光布上面的纤 维造成的压痕,也会带有小尾巴!3、如果这种黑点不是布满在视野范围内的,偶尔有几个 小黑点甚至是比较大的黑点,那就是夹杂了! !以上是经验,仅供参考。
对于铝合金试样,楼主的制备方法也就只能做成这个样子了。
要想看清楚铝合金的晶界,必 须要电解抛光+阳极制膜+偏光显微镜观察。
材料是 7075 铝合金 正常温度铝熔体凝固过程,平时组织如图 1,可以看到晶界比较清晰,晶粒内部有很多析出 相; 而温度更高热铝熔体凝固后的金相组织如图 2, 其性能 (尤其是延伸率) 比起前者大大降低, 晶界看起来比较暗。
是否可以看出是发生过烧了呢?还只是腐蚀染色的问题。
那么性能的降低可能是什么原因, 谢谢 腐蚀剂是混合酸。
在金相观察中有些问题困扰我很久了,希望大家帮忙哦 1、相关参考书中说,7 系列铝合金微观组织是枝晶网络组织,那么枝晶网络结构和晶粒有 什么关系?我在腐蚀后好像只能看到枝晶, 那么晶粒就是枝晶网络结构包裹的区域吗?另外 枝晶间距如何测量? 还是以我的照片为例吧, 我死活看不出来那部分是晶粒。
。
。
是腐蚀的问题吗?希望高手帮忙 标示出来一个晶粒,谢谢 2、铝合金晶粒的观察是否最好通过阳极覆膜再偏振光来进行?还是通过更换腐蚀剂也能很 好的观察晶粒大小?偏光和普通光的区别是什么?为什么标准中说腐蚀 10 几秒钟,而我腐 蚀 1 分多效果不好。
快速凝固铝合金的组织与性能
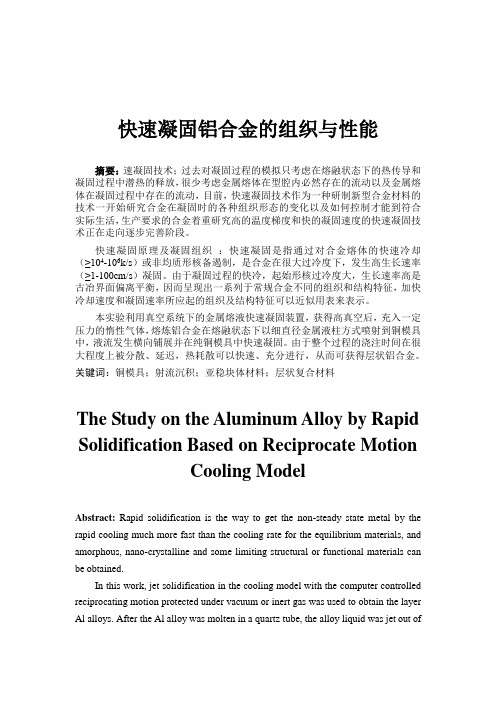
快速凝固铝合金的组织与性能摘要:速凝固技术;过去对凝固过程的模拟只考虑在熔融状态下的热传导和凝固过程中潜热的释放,很少考虑金属熔体在型腔内必然存在的流动以及金属熔体在凝固过程中存在的流动,目前,快速凝固技术作为一种研制新型合金材料的技术一开始研究合金在凝固时的各种组织形态的变化以及如何控制才能到符合实际生活,生产要求的合金着重研究高的温度梯度和快的凝固速度的快速凝固技术正在走向逐步完善阶段。
快速凝固原理及凝固组织:快速凝固是指通过对合金熔体的快速冷却(≥104-106k/s)或非均质形核备遏制,是合金在很大过冷度下,发生高生长速率(≥1-100cm/s)凝固。
由于凝固过程的快冷,起始形核过冷度大,生长速率高是古冶界面偏离平衡,因而呈现出一系列于常规合金不同的组织和结构特征,加快冷却速度和凝固速率所应起的组织及结构特征可以近似用表来表示。
本实验利用真空系统下的金属熔液快速凝固装置,获得高真空后,充入一定压力的惰性气体,熔炼铝合金在熔融状态下以细直径金属液柱方式喷射到铜模具中,液流发生横向铺展并在纯铜模具中快速凝固。
由于整个过程的浇注时间在很大程度上被分散、延迟,热耗散可以快速、充分进行,从而可获得层状铝合金。
关键词:铜模具;射流沉积;亚稳块体材料;层状复合材料The Study on the Aluminum Alloy by Rapid Solidification Based on Reciprocate MotionCooling ModelAbstract:Rapid solidification is the way to get the non-steady state metal by the rapid cooling much more fast than the cooling rate for the equilibrium materials, and amorphous, nano-crystalline and some limiting structural or functional materials can be obtained.In this work, jet solidification in the cooling model with the computer controlled reciprocating motion protected under vacuum or inert gas was used to obtain the layer Al alloys. After the Al alloy was molten in a quartz tube, the alloy liquid was jet out ofa little hole under the tube inside a copper die by high pressure Ar gas, and alloy liquid lateral spread and solidify in the model. The process were repeated foe many times, and accumulation like a wall growing up. Since the pouring time of the entire process was delay and dispersed, heat was quickly and fully dissipated, so the bulk layer Al alloy was obtained. The alloy be with the high density and fine structure.Microstructure observation, hardness testing, tensile test were carried out for the alloy. The aluminum alloyBy precise control of the working parameter, the test was adjust to obtained the needed materials. The interface of multi-layer homogeneous composite was studied, such as superheat of the molten metal, the relationship between the liquid jetting parameters and solidification process, metallurgical complex process, heat dissipation process and control of the materials deposition growth process were also analyzed. The experiences was obtained for the fabrication of multi-layer deposition composites of high melting point metals and alloys.Keywords:reciprocating motion; jetting sediment; metestable bulk materials;composite materials目录第1章绪论 (1)1.1 引言 (1)1.2 铝合金及其主要分类 (1)1.2.1 铝合金的分类 (1)1.2.2 变形铝合金 (2)1.2.3 铸造铝合金 (2)第2章实验方法 (2)2.1实验原理 (2)2.2实验设备 (3)2.3实验过程 (4)第3章实验结果与讨论 (5)3.1铝合金试样的制备 (5)3.2层状铝合金的组织 (6)3.3硬度测试实验结果 (6)3.4快速凝固的冷速 (6)第4章结论 (7)第1章绪论1.1非晶材料简介非晶合金具有长程无序、短程有序的结构,与晶态合金相比,具备许多特有的性能,如高硬度、高强度、高电阻、耐蚀及耐磨等,为材料科研工作者开发高性能的功能材料和结构材料提供了巨大的潜力。
铝合金偏析
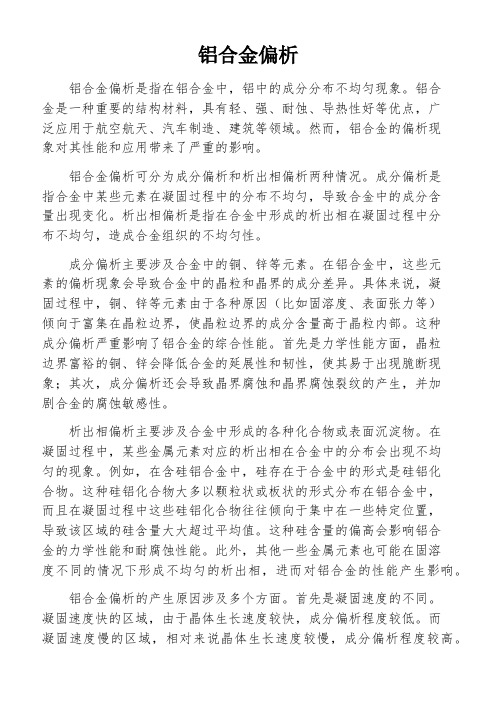
铝合金偏析铝合金偏析是指在铝合金中,铝中的成分分布不均匀现象。
铝合金是一种重要的结构材料,具有轻、强、耐蚀、导热性好等优点,广泛应用于航空航天、汽车制造、建筑等领域。
然而,铝合金的偏析现象对其性能和应用带来了严重的影响。
铝合金偏析可分为成分偏析和析出相偏析两种情况。
成分偏析是指合金中某些元素在凝固过程中的分布不均匀,导致合金中的成分含量出现变化。
析出相偏析是指在合金中形成的析出相在凝固过程中分布不均匀,造成合金组织的不均匀性。
成分偏析主要涉及合金中的铜、锌等元素。
在铝合金中,这些元素的偏析现象会导致合金中的晶粒和晶界的成分差异。
具体来说,凝固过程中,铜、锌等元素由于各种原因(比如固溶度、表面张力等)倾向于富集在晶粒边界,使晶粒边界的成分含量高于晶粒内部。
这种成分偏析严重影响了铝合金的综合性能。
首先是力学性能方面,晶粒边界富裕的铜、锌会降低合金的延展性和韧性,使其易于出现脆断现象;其次,成分偏析还会导致晶界腐蚀和晶界腐蚀裂纹的产生,并加剧合金的腐蚀敏感性。
析出相偏析主要涉及合金中形成的各种化合物或表面沉淀物。
在凝固过程中,某些金属元素对应的析出相在合金中的分布会出现不均匀的现象。
例如,在含硅铝合金中,硅存在于合金中的形式是硅铝化合物。
这种硅铝化合物大多以颗粒状或板状的形式分布在铝合金中,而且在凝固过程中这些硅铝化合物往往倾向于集中在一些特定位置,导致该区域的硅含量大大超过平均值。
这种硅含量的偏高会影响铝合金的力学性能和耐腐蚀性能。
此外,其他一些金属元素也可能在固溶度不同的情况下形成不均匀的析出相,进而对铝合金的性能产生影响。
铝合金偏析的产生原因涉及多个方面。
首先是凝固速度的不同。
凝固速度快的区域,由于晶体生长速度较快,成分偏析程度较低。
而凝固速度慢的区域,相对来说晶体生长速度较慢,成分偏析程度较高。
其次,合金中各元素的固溶度差异也是造成成分偏析的重要原因。
合金中比较难溶解的元素往往在凝固过程中首先析出,并富集在晶粒边界上。
铝合金金相观察资料

1)铸造组织:
铸造金属在冷却时由于局部负温度梯度,导致过冷度不同,金属晶粒多呈树枝晶生长。
又由于冷却的速度较快,各组分析晶温度不同,固相中的原子来不及扩散,以至于结晶分先后顺
序,在枝晶间产生成分偏析。
所以在凝固后的铸造组织中,可观察到树枝状晶粒。
在高倍显微镜下观察时,还能明显地观察到枝晶间的成分偏析现象,表现为颜色深度不同的带状分界,颜色深度不同是因为其中的铜元素含量不同,因而在腐蚀液作用下产生颜色梯度,在局部还能看到CuAl2存在于枝晶间。
(2)固溶处理:
固溶处理将金相组织中的成分逐渐均匀化。
由于温度再次升高,导致晶粒长大。
高倍镜下晶界间有黑色小点(CuAl2杂质),这是由于冷却过程中得到过饱和固溶体,固溶处理保温的时间较短,铸态组织中的树枝状晶粒并未完全转化,枝晶偏析未完全消除,存在杂质CuAl2。
(3)固溶处理+轧制:
轧制是通过应力使金属内部的位错产生运动从而发生塑性变形。
在金相组织中,可观察到晶粒呈纤维状,顺着轧制方向被拉长,而沿其他方向的尺寸无明显变化。
在高倍镜下可观察到大量明显的位错。
(4)固溶处理+轧制+时效:
时效是过饱和固溶体的脱溶分解,析出第二相的过程。
但实验中在低倍显微镜观察下时只发现很少的第二相。
其金相组织与固溶处理+轧制后的金相组织没有明显的区别。
铝合金晶粒细化

设备复杂 特殊合金
盐类细化 操作简单 污染严重 炉内处理 块式添加 剂
Al-Ti基 细化剂
适合连续 成本较高 炉外处理 在线添加 生产
100~250
冶 金 作 用
取0.01%Ti的添加量作为标准添加量,用Al-5Ti-1B细化剂在730℃ 时对99.7%的工业纯铝进行细化处理
标准添加量下保持时间与晶粒大小的关系
Ti的添加量对晶粒大小的影响
不 同 添 加 量 对 99. 7% Al 细 化 效 果
盐类细化剂
吸附变质剂的特点是熔点低,能显著降低合金的液相线温度,原子
快速凝固细晶
采用很高的凝固速度,使合金在凝固过程中形成细小的微观组 织结构,且分布均匀。 原理:控制过冷度
影响因素:凝固速率和合金成分
动态晶粒细化Байду номын сангаас
机械场凝固细晶:
机械搅拌或机械振 动 形成复杂的三维空 间流动
细化或球化合金 组织
改变熔体的结构和 能量起伏
磁场凝固细晶
磁场对铝合金能量体系 产生扰动 产生涡流,和洛伦磁力与 外加磁强破坏产生的树枝 晶
产生新的晶核,达到细化目的
电场凝固细晶
原理:利用电迁移现象改变溶质有效分配系数及凝固界面前沿溶质 分布。
主要影响因素:晶核和母相的电导率,球形晶核的半径 密度 ,质量电容 通电时间
超声场凝固细晶
声空化和声流作用形 成空化泡
吸收热量, 造成局部 过冷
空化泡破裂会 破碎正在长大 的晶体
形成新的晶体质点
变质细晶
变质细晶又称为外来形核质点法,即通过向铝合金熔体中加入中间
合金晶粒细化剂,产生大量有效异质形核核心,提高晶体的形核率,
从而细化晶粒
铝合金的组织与力学性能关系研究

铝合金的组织与力学性能关系研究铝合金是一种优良的轻质材料,在航空、汽车、船舶等领域得到广泛应用。
铝合金具有较高的强度、优良的耐腐蚀性和可焊性,这些优异的性能得益于其复杂的组织结构与力学性能。
因此,深入研究铝合金的组织与力学性能的关系是非常必要的。
一、铝合金组织结构铝合金的组织结构是指它的晶粒形态、晶粒大小、颗粒分布和相分布等,这对铝合金的力学性能有着重要的影响。
目前,常见的铝合金分为变形铝合金和时效硬化铝合金两大类。
变形铝合金的组织结构主要是由基体和强化相组成。
基体由纯铝和杂质元素组成,强化相则由合金元素与铝元素相互作用而形成。
强化相通常为等轴晶、纤维状、条状、球形等多种形态,它们在基体中的分布状态对铝合金的强度、韧性等力学性能有着显著的影响。
此外,变形铝合金的晶粒尺寸和晶界纯度也会对其力学性能产生影响。
时效硬化铝合金的组织结构主要是由基体、淬火相、时效相和溶质组成。
基体与变形铝合金相似,淬火相是因固溶元素的高浓度而形成的均匀分布的固溶体,时效相经过时效后在淬火相中析出。
时效相形态多样,它的数量、尺寸、分布、化学成分等都会影响铝合金的力学性能。
二、铝合金力学性能铝合金的力学性能包括屈服强度、伸长率、断裂韧性、冲击韧性、疲劳强度等多方面信息。
这些性能既与铝合金的组织结构有关,也与铝合金的制备工艺和热处理条件有关。
铝合金的屈服强度是指在应力逐渐增大时,材料发生塑性变形时的应力值。
屈服强度受到晶粒尺寸的影响,晶粒尺寸小的铝合金具有更高的屈服强度。
铝合金的伸长率是指材料在断裂前能够承受的变形量。
伸长率随晶粒尺寸的增大而降低,因为晶粒尺寸大的铝合金在变形时容易产生裂缝。
铝合金的断裂韧性是指材料在试验中近似弹性的状态下,承受弯曲外载荷时试件发生破坏的能力。
铝合金的断裂韧性与晶粒尺寸、晶界状态、铝合金成分和热处理条件等有关。
铝合金的冲击韧性是指材料在低温条件下,承受冲击载荷破坏的能力。
铝合金中的杂质元素和强化相对其冲击韧性有重要影响。
6061铝合金微观组织特点
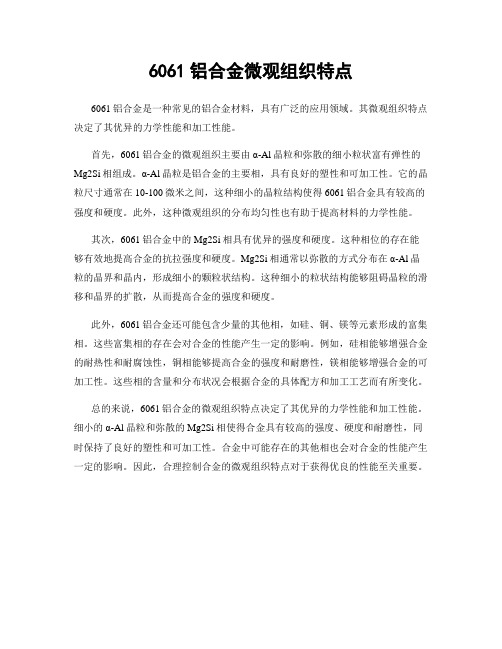
6061铝合金微观组织特点
6061铝合金是一种常见的铝合金材料,具有广泛的应用领域。
其微观组织特点决定了其优异的力学性能和加工性能。
首先,6061铝合金的微观组织主要由α-Al晶粒和弥散的细小粒状富有弹性的Mg2Si相组成。
α-Al晶粒是铝合金的主要相,具有良好的塑性和可加工性。
它的晶粒尺寸通常在10-100微米之间,这种细小的晶粒结构使得6061铝合金具有较高的强度和硬度。
此外,这种微观组织的分布均匀性也有助于提高材料的力学性能。
其次,6061铝合金中的Mg2Si相具有优异的强度和硬度。
这种相位的存在能够有效地提高合金的抗拉强度和硬度。
Mg2Si相通常以弥散的方式分布在α-Al晶粒的晶界和晶内,形成细小的颗粒状结构。
这种细小的粒状结构能够阻碍晶粒的滑移和晶界的扩散,从而提高合金的强度和硬度。
此外,6061铝合金还可能包含少量的其他相,如硅、铜、镁等元素形成的富集相。
这些富集相的存在会对合金的性能产生一定的影响。
例如,硅相能够增强合金的耐热性和耐腐蚀性,铜相能够提高合金的强度和耐磨性,镁相能够增强合金的可加工性。
这些相的含量和分布状况会根据合金的具体配方和加工工艺而有所变化。
总的来说,6061铝合金的微观组织特点决定了其优异的力学性能和加工性能。
细小的α-Al晶粒和弥散的Mg2Si相使得合金具有较高的强度、硬度和耐磨性,同时保持了良好的塑性和可加工性。
合金中可能存在的其他相也会对合金的性能产生一定的影响。
因此,合理控制合金的微观组织特点对于获得优良的性能至关重要。
铝合金金相组织晶粒度
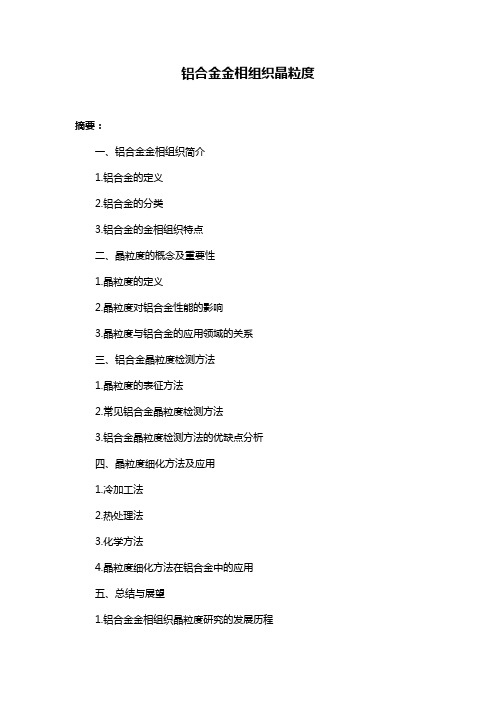
铝合金金相组织晶粒度
摘要:
一、铝合金金相组织简介
1.铝合金的定义
2.铝合金的分类
3.铝合金的金相组织特点
二、晶粒度的概念及重要性
1.晶粒度的定义
2.晶粒度对铝合金性能的影响
3.晶粒度与铝合金的应用领域的关系
三、铝合金晶粒度检测方法
1.晶粒度的表征方法
2.常见铝合金晶粒度检测方法
3.铝合金晶粒度检测方法的优缺点分析
四、晶粒度细化方法及应用
1.冷加工法
2.热处理法
3.化学方法
4.晶粒度细化方法在铝合金中的应用
五、总结与展望
1.铝合金金相组织晶粒度研究的发展历程
2.当前研究的局限性及未来发展方向
正文:
铝合金是一种广泛应用于各个领域的金属材料,因其具有高比强度、高耐蚀性、高电导率、良好的抗疲劳性能和成型性能等特点,而受到广泛关注。
在铝合金的研究中,金相组织晶粒度是一个重要的参数。
晶粒度是指金属材料中晶粒的大小和分布。
晶粒度的大小对铝合金的性能有着重要的影响。
一般来说,细小的晶粒有利于提高铝合金的强度、硬度和耐蚀性,而粗大的晶粒则有利于提高铝合金的塑性和韧性。
铝合金晶粒度的检测方法有很多种,例如:光学显微镜法、X 射线衍射法、扫描电子显微镜法等。
这些方法各有优缺点,需要根据具体的应用场景选择合适的方法。
为了获得理想的晶粒度,人们研究了许多晶粒度细化方法。
冷加工法、热处理法、化学方法等是常见的晶粒度细化方法。
这些方法在铝合金中的应用,可以有效地提高铝合金的性能。
总的来说,铝合金金相组织晶粒度研究是一个多领域的交叉课题,涉及材料学、金属学、化学等多个学科。
铝合金缺陷——精选推荐
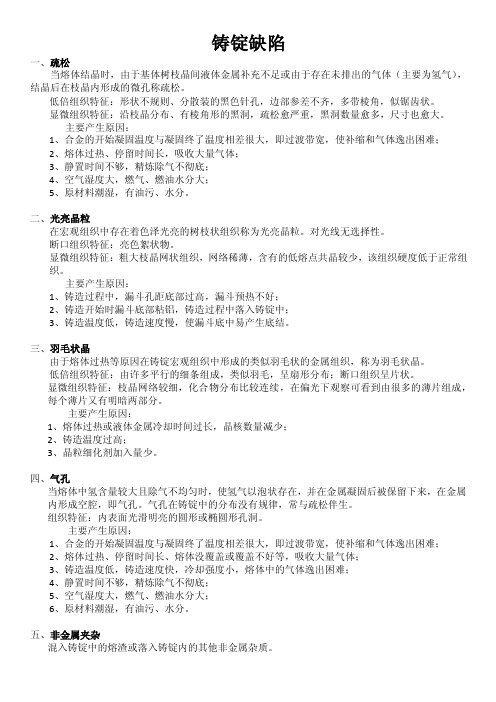
铸锭缺陷一、疏松当熔体结晶时,由于基体树枝晶间液体金属补充不足或由于存在未排出的气体(主要为氢气),结晶后在枝晶内形成的微孔称疏松。
低倍组织特征:形状不规则、分散装的黑色针孔,边部参差不齐,多带棱角,似锯齿状。
显微组织特征:沿枝晶分布、有棱角形的黑洞,疏松愈严重,黑洞数量愈多,尺寸也愈大。
主要产生原因:1、合金的开始凝固温度与凝固终了温度相差很大,即过渡带宽,使补缩和气体逸出困难;2、熔体过热、停留时间长,吸收大量气体;3、静置时间不够,精炼除气不彻底;4、空气湿度大,燃气、燃油水分大;5、原材料潮湿,有油污、水分。
二、光亮晶粒在宏观组织中存在着色泽光亮的树枝状组织称为光亮晶粒。
对光线无选择性。
断口组织特征:亮色絮状物。
显微组织特征:粗大枝晶网状组织,网络稀薄,含有的低熔点共晶较少,该组织硬度低于正常组织。
主要产生原因:1、铸造过程中,漏斗孔距底部过高,漏斗预热不好;2、铸造开始时漏斗底部粘铝,铸造过程中落入铸锭中;3、铸造温度低,铸造速度慢,使漏斗底中易产生底结。
三、羽毛状晶由于熔体过热等原因在铸锭宏观组织中形成的类似羽毛状的金属组织,称为羽毛状晶。
低倍组织特征:由许多平行的细条组成,类似羽毛,呈扇形分布;断口组织呈片状。
显微组织特征:枝晶网络较细,化合物分布比较连续,在偏光下观察可看到由很多的薄片组成,每个薄片又有明暗两部分。
主要产生原因:1、熔体过热或液体金属冷却时间过长,晶核数量减少;2、铸造温度过高;3、晶粒细化剂加入量少。
四、气孔当熔体中氢含量较大且除气不均匀时,使氢气以泡状存在,并在金属凝固后被保留下来,在金属内形成空腔,即气孔。
气孔在铸锭中的分布没有规律,常与疏松伴生。
组织特征:内表面光滑明亮的圆形或椭圆形孔洞。
主要产生原因:1、合金的开始凝固温度与凝固终了温度相差很大,即过渡带宽,使补缩和气体逸出困难;2、熔体过热、停留时间长、熔体没覆盖或覆盖不好等,吸收大量气体;3、铸造温度低,铸造速度快,冷却强度小,熔体中的气体逸出困难;4、静置时间不够,精炼除气不彻底;5、空气湿度大,燃气、燃油水分大;6、原材料潮湿,有油污、水分。
铝合金材料的显微组织与力学性能研究

铝合金材料的显微组织与力学性能研究铝合金是一种常见而重要的金属材料,其具有良好的机械性能和广泛的应用领域。
在铝合金的研究中,显微组织与力学性能之间的关系一直是一个重要的研究方向。
本文将从显微组织和力学性能两个方面探讨铝合金材料的研究进展和相关问题。
一、铝合金的显微组织研究铝合金的显微组织主要由晶粒、相分布和晶界等组成。
晶粒是组成铝合金材料的基本单元,晶粒的尺寸和形态与材料的力学性能密切相关。
随着材料制备方法和热处理工艺的不同,铝合金的晶粒尺寸和形态会发生变化。
研究表明,晶粒尺寸越小,材料的强度和硬度越高,但韧性和塑性会相应降低。
相分布是指铝合金中不同相的分布情况。
铝合金中常见的相有析出相、溶固相和沉淀相等。
这些相的存在与晶粒的尺寸、形态和分布密切相关。
相分布的研究有助于了解铝合金的相变和相互作用规律,从而指导制备和改性铝合金材料。
晶界是晶粒之间的界面区域,是铝合金中的强度和韧性的重要因素。
晶界的特征和稳定性决定材料的抗拉强度、断裂韧性和疲劳寿命。
研究表明,晶界的结构、平衡和迁移行为对铝合金材料的性能具有重要影响。
因此,晶界的研究对于理解铝合金的显微组织演化和力学性能提升具有重要意义。
二、铝合金的力学性能研究铝合金的力学性能包括强度、硬度、韧性和塑性等参数。
随着显微组织的改变,铝合金的力学性能也会相应变化。
强度是材料抵抗变形和断裂的能力,与晶粒尺寸、相分布和晶界特性等因素密切相关。
硬度是材料抵抗切削和磨损的能力,与晶粒大小和晶界特征有关。
韧性是材料抵抗断裂和剪切的能力,主要受晶界和析出相的影响。
塑性是材料变形和变型的能力,也与晶界的稳定性和迁移性有关。
为了提高铝合金材料的力学性能,研究人员通过改变制备方法、热处理工艺和合金配方等途径进行了大量的研究。
针对不同应用领域的需求,开发出了一系列具有优异力学性能的铝合金。
同时,利用计算模拟方法对铝合金进行力学性能预测也成为了研究的热点。
这些研究工作为铝合金的应用提供了重要的理论和实践基础。
热处理对铸造铝合金材料的晶粒尺寸和晶界特性的影响

热处理对铸造铝合金材料的晶粒尺寸和晶界特性的影响热处理是一种常用的金属材料改善性能的方法,对于铸造铝合金材料而言也是如此。
热处理可以通过改变材料的晶粒尺寸和晶界特性,显著地影响材料的力学性能和高温稳定性。
本文将探讨热处理对铸造铝合金材料晶粒尺寸和晶界特性的影响。
一、热处理介绍热处理是通过控制材料的加热、保温和冷却过程,改变材料的组织结构和性能。
对于铸造铝合金材料而言,热处理通常包括固溶处理和时效处理两个阶段。
1. 固溶处理固溶处理是将铸造铝合金材料加热到固溶温度,使各种合金元素尽可能地溶解在α铝晶格中。
在这个过程中,因为加热时间的增加,晶粒的尺寸将会增大。
2. 时效处理时效处理是在固溶处理后,将材料保持在一定温度下的一段时间,使合金元素重新析出,形成强化相,并为材料提供额外的强度和稳定性。
时效处理可以进一步影响铸造铝合金材料的晶粒尺寸和晶界特性。
二、热处理对晶粒尺寸的影响1. 固溶处理的作用固溶处理主要通过加热和高温保持时间的延长,促使合金元素溶解和扩散,从而引起晶粒尺寸的增大。
晶粒的尺寸对铸造铝合金的力学性能和塑性变形能力起着重要的影响。
2. 固溶处理参数的影响固溶处理中的加热温度和保温时间是影响铸造铝合金晶粒尺寸的重要因素。
较高的加热温度和延长的保温时间会导致晶粒尺寸的增大。
然而,过高的加热温度和过长的保温时间也会引起晶粒粗化和组织不均匀性。
三、热处理对晶界特性的影响1. 固溶处理的作用热处理可以改变铸造铝合金材料的晶界特性,主要体现在晶界的清晰度、晶界角度和晶界能量等方面。
固溶处理可以减少晶界的含溶负荷,促使晶界清晰度的提高。
2. 时效处理的作用时效处理会使强化相沿晶界析出,形成细小的颗粒,从而增强晶界的稳定性。
这种强化相可以阻碍晶界的滑移和扩展,提高材料的强度和耐热性。
四、热处理优化策略为了更好地控制铸造铝合金材料的晶粒尺寸和晶界特性,需要进行热处理的优化设计。
1. 固溶处理条件的优化根据不同铝合金的成分和应用要求,选择适当的固溶处理温度和保温时间,以实现晶粒尺寸的控制和优化。
- 1、下载文档前请自行甄别文档内容的完整性,平台不提供额外的编辑、内容补充、找答案等附加服务。
- 2、"仅部分预览"的文档,不可在线预览部分如存在完整性等问题,可反馈申请退款(可完整预览的文档不适用该条件!)。
- 3、如文档侵犯您的权益,请联系客服反馈,我们会尽快为您处理(人工客服工作时间:9:00-18:30)。
铝合金的凝固和组织中的晶粒
一、熔体的凝固过程:
在半连续铸造过程中,熔体的浇铸和凝固是同时连续地进行的。
对铸锭而言,冷却是分两次实现的。
一次冷却是在结晶器内完成的,熔体进入结晶器后靠结晶器导热,在结晶器内形成一定厚度的凝固壳。
此后随着铸造机下降,被拉出结晶器,遇到结晶器底部浇出的冷却水(称之为二次冷却)从此完成凝固的全部过程。
这个凝固过程在金属学中称为金属结晶。
二、铸锭的正常晶粒组织
从理论上讲,在工业生产条件下,铸锭的晶粒组织由三个区域组成:即外层表面的细等轴晶区,由此往里的柱状晶区和中心等轴晶区。
但在实际铝合金生产中铸锭在强度大的冷却条件下,经过Al-Ti-B的细化处理,铝合金铸锭的组织往往全部是等轴晶。
铸锭晶粒的大小将直接影响铝加工制品的力学性能和加工性能,所以它被作为衡量铸锭质量的一个主要指标。
三、影响铸锭晶粒的因素
1、熔体结晶的条件:熔体结晶有两个条件是必不可少的,其一是结晶必需要先形成晶核,熔体中的晶核分两种。
自发晶核是在低于结晶温度时,熔体由于能量起伏或液相起伏形成的晶核。
非自发晶核是外来粒子进入熔体后而形成的晶核。
其二是要有过冷度才可能发生结晶,所谓过冷度就是熔体的温度只有在冷却到低于熔点的温度下才能结晶,温度越低过冷度越大。
2、晶粒的细化:控制过冷度;一般情况下增大过冷度,熔体中的生核率和晶粒的长大速度都增加,但生核速度大于晶粒的增长速度,所以一般情况下金属结晶时过冷度越大,所得到晶粒越细小。
在半连续铸造生产中增加过冷度的主要途径是有降低铸造速度使
单位时间内铸锭冷却量增加;降低冷却水的温度使单位时间内铸锭的温降增加;加大冷却水的水压使单位时间内浇到铸锭上的水量增加使铸锭的温降增加;降低铸造温度使铸锭的结晶过程缩短。
3、动态细化晶粒:对熔体采用机械搅拌、电磁搅拌、超声波振动等,这样一方面可以靠输入的能量使晶核提前生成,另一方面可以使成长中的树枝状晶破碎增加晶核的数目(在这里就要讲一下晶粒的形成,晶粒是先有一个晶核、晶核按多个方向晶轴成长,象树枝一样称之为枝晶,当众多的枝晶共同生长到一定程度互相顶撞,此时熔体添补到枝晶中,围绕它形成了一个枝晶粒)
4、变质处理细化晶粒:向熔体中加入少量的活性物质,促进熔体内部生成晶核或改变晶粒的成长过程,在变形铝合金中一般选用Ti、Zr、B、C等作为晶粒细化剂,我公司铸造时加入Al-Ti-B 丝就属于变质处理的方法。
四、粗大晶粒
在宏观组织中出现的均匀或不均匀的大晶粒均称为粗大晶粒。
1、粗大晶粒的宏观组织:粗大晶粒在铸锭的低倍试片检查时很容易发现,为了便于区别根据其直线尺寸,分别为五个级别:一级晶粒 1.17mm、
二级晶粒1.59mm、三级晶粒2.16mm、四级晶粒2.78mm、五级晶粒3.76mm。
正常情况下铸锭的晶粒度一般控制在二级以上。
有时由于工艺控制不当,铸锭中可出现超大晶粒,其尺寸有时可以超过正常晶粒的几倍,乃至几十倍。
2、粗大晶粒产生的原因:主要原因是,当铸造冷却速度慢时过冷度小,生成晶核的数量小,晶粒成长速度快则会产生均匀的粗大晶粒。
其次是熔铸工艺的影响,如熔体过烧或局部过热使熔体中的非自发晶核急剧熔解,结晶核减少;熔体在炉内停留时间过长,
大量的非自发晶核活性减弱;铸造温度高,熔体中的晶核生成困难,相对晶粒的增长速度增加;铸造漏斗尺寸不合适或摆放不正和漏斗堵眼,造成液流分配不均匀,使液穴中温度不均匀,温度高的地方晶粒成长速度快而形成大晶粒;Al-Ti-B等细化剂加入方式不正确或在熔体中停留时间过长,使细化效果降低。
五、防止产生粗大晶粒的措施
1、加强操作,严格控制熔体过烧或局部过热,熔炼过程中要加强搅拌,经常测温。
2、防止熔体在炉内停留进间过长,一般不允许超过4小时。
如超时必须重新精炼和增加Al-Ti-B细化剂用量。
3、根据实际情况选择合理的铸造温度。
因为低温铸造虽然缩短了结晶时间而使铸锭晶粒细化,但铸造温度低也会使熔体粘度增大不利于熔体中的氧化夹杂物和气体上浮和逸出,而使铸锭产生夹渣和疏松。
根据我公司的实际情况建议每年5月-9月采用下限铸造温度,11月-来年4月采用上限铸造温度。
4、铸造检查好漏斗不得有堵眼,漏斗眼尺寸因长期使用损坏,大小相差悬殊时修补后再用。
在使用时漏斗要放在中心部位.
5、根据不同的合金合理选择Al-Ti-B的加入量。
六、羽毛状晶
羽毛状晶属于畸形晶粒,因其型状在低倍试片中酷似羽毛故称之为羽毛状晶。
该组织严重地影响铸锭质量和加工制品性能,所以应严格控制,其形成机理理论性较强,所以在这里就不讲了,但其预防措施恰巧和预防粗大晶粒一致,所以我们只要掌握了预防粗大晶粒的措施,也就能完全防止铸锭中羽毛状晶的产生。