伺服进给算法
数控车床工作台二维运动伺服进给系统设计

数控车床工作台二维运动伺服进给系统设计摘要:数控车床在制造业中起着至关重要的作用。
为了提高生产效率和产品质量,设计一个稳定可靠、精确灵活的二维运动伺服进给系统尤为重要。
本文将针对数控车床工作台的二维运动伺服进给系统进行设计,包括运动控制算法、驱动器选型、传感器选择等方面。
1.引言数控车床是一种以电子技术、计算机技术和车床技术为基础的现代化机床。
它通过运动控制系统实现工作台的运动,可以实现复杂的加工工艺。
二维运动伺服进给系统是数控车床的核心部件之一2.运动控制算法运动控制算法是二维运动伺服进给系统的核心技术之一、常用的运动控制算法包括PID控制算法、自适应控制算法等。
PID控制算法是一种经典的,应用广泛的控制算法,它根据测量值与期望值的差异计算出控制量,并对系统进行修正。
自适应控制算法则是根据系统的参数变化自动地调整控制参数。
在设计二维运动伺服进给系统时需要根据实际情况选择合适的控制算法。
3.驱动器选型驱动器是实现工作台运动的关键部件,它将控制信号转换为电力信号,驱动电机工作。
在选择驱动器时需要考虑工作台的负载情况、速度要求和精度要求等因素。
常用的驱动器有直流伺服驱动器、交流伺服驱动器和步进驱动器等。
在设计二维运动伺服进给系统时需要根据实际情况选择合适的驱动器。
4.传感器选择传感器可以实现对工作台位置、速度和负载等参数的测量,是二维运动伺服进给系统的重要组成部分。
根据需要可以选择位置传感器、速度传感器和负载传感器等。
常用的位置传感器有编码器、激光干涉仪等,速度传感器有霍尔传感器、光电传感器等,负载传感器有压力传感器、力传感器等。
在设计二维运动伺服进给系统时需要根据实际需求选择合适的传感器。
5.结论设计一个稳定可靠、精确灵活的二维运动伺服进给系统对于提高数控车床的加工精度、提高生产效率具有重要意义。
本文针对数控车床工作台的二维运动伺服进给系统进行了详细的设计,包括运动控制算法、驱动器选型、传感器选择等方面。
伺服控制器的运动控制算法介绍

伺服控制器的运动控制算法介绍伺服控制器在工业自动化中扮演着重要的角色,它负责实现对运动系统的精密控制。
运动控制算法是伺服控制器的核心部分,决定了系统的性能和稳定性。
下面将介绍几种常见的伺服控制器运动控制算法。
1. 位置控制算法位置控制算法主要用于将执行机构控制到预定位置。
最简单的位置控制算法是基于比例控制(P控制),该算法根据当前位置与目标位置之间的差异来调整输出信号。
然而,由于存在噪声和不确定因素,简单的P控制算法往往无法满足精确的位置控制需求。
因此,常常会结合使用微分控制(D控制)和积分控制(I控制),形成PID控制算法。
PID控制算法能够通过对位置误差的比例、微分和积分进行综合调节,实现更为精确的位置控制。
2. 速度控制算法速度控制算法用于控制执行机构的运动速度,以实现平滑且精确的速度调节。
基本的速度控制算法是通过调整电机驱动器的电压或电流来控制转速。
然而,由于负载的变化和动态过程中的突发情况可能导致速度误差,因此需要应用更高级的速度控制算法来自适应地调整输出信号。
常见的速度控制算法包括速度前馈控制和模型预测控制。
速度前馈控制通过测量负载和运动参数来提前预测运动需求,并相应地调整输出信号。
而模型预测控制则是通过建立数学模型来预测运动系统的响应,并根据预测结果进行控制。
3. 力控制算法力控制算法是一种高级控制算法,用于实现执行机构对外部力的精确调节。
在某些应用中,控制的目标并不是位置或速度,而是对物体施加特定的力。
力控制算法主要基于力-位控制或力-速控制。
力-位控制算法通过感知执行机构施加到物体上的力来调节执行机构的位置。
力-速控制算法则是通过力传感器捕捉到的力信号来调节执行机构的速度。
力控制算法广泛应用于液压系统、机器人领域以及医疗设备等需要进行力量控制的应用中。
除了上述介绍的几种常见的伺服控制器运动控制算法外,还存在其他高级的控制算法,如模糊控制、自适应控制和神经网络控制等。
这些算法能够根据不同的应用需求,以更加智能和高级的方式进行运动控制。
双伺服攻丝机计算公式

双伺服攻丝机计算公式双伺服攻丝机计算公式1. 双伺服攻丝机简介•双伺服攻丝机是一种用于加工螺纹的机床设备,通过电机驱动切削工具在工件上进行螺纹加工。
•双伺服攻丝机通常由两个伺服电机驱动,一个负责主轴转动,一个负责刀具的移动,以实现精确的螺纹加工。
2. 攻丝过程中的关键计算公式主轴转速计算公式•主轴转速是指主轴每分钟转动的圈数,通常以单位rpm表示。
•主轴转速计算公式为:主轴转速 = (切削速度 x 1000) / (刀具直径x π)。
•其中,切削速度的单位为m/min,刀具直径的单位为mm。
示例:•假设切削速度为60m/min,刀具直径为10mm。
•则主轴转速 = (60 x 1000) / (10 x ) = rpm。
进给速度计算公式•进给速度是指刀具在加工过程中每分钟移动的距离,通常以单位mm/min表示。
•进给速度计算公式为:进给速度 = 主轴转速 x 螺距。
•其中,螺距的单位为mm/圈。
示例:•假设主轴转速为2000rpm,螺距为1mm/圈。
•则进给速度 = 2000 x 1 = 2000 mm/min。
加工时间计算公式•加工时间是指完成一道螺纹加工的所需时间,通常以单位秒表示。
•加工时间计算公式为:加工时间 = (螺纹长度 / 进给速度) x 60。
•其中,螺纹长度的单位为mm。
示例:•假设螺纹长度为100mm,进给速度为2000 mm/min。
•则加工时间 = (100 / 2000) x 60 = 3 秒。
3. 总结•双伺服攻丝机的计算公式包括主轴转速、进给速度和加工时间的计算公式。
•主轴转速计算公式用于确定主轴每分钟转动的圈数。
•进给速度计算公式用于确定刀具每分钟移动的距离。
•加工时间计算公式用于确定完成一道螺纹加工所需的时间。
•通过合理使用这些计算公式,可以提高双伺服攻丝机的加工效率和精度。
4. 轴向进给量计算公式•轴向进给量是指刀具在轴向方向上每次进给的距离,通常以单位mm表示。
伺服进给

• 第五章 进给伺服系统
• • • •
• • •
§5-1 概述 §5-2 对进给伺服系统结构的要求 §5-3 传动齿轮副 §5-4 丝杠螺母副
一、滚珠丝杠螺母副 (一) 工作原理和特点 (二) 结构和类型
• §5-5 导轨 • §5-6 回转工作台
• • • • • • • • • •
(二) 结构和类型 1. 滚珠的循环方式 常用的滚珠循环方式可分为两大类: 滚珠在循环过程中,有时与丝杠脱离接触叫 外循环; 始终与丝杠保持接触叫内循环。 滚珠在同一螺母上只有一个回路管道的叫单 列循环。 有两个回路管道的叫双列循环。 多于两个回路管道的叫多列循环。 循环中的滚珠叫工作滚珠。 工作滚珠所走过的滚道圈数叫工作圈数。
• 第五章 进给伺服系统
• §5-1 概述 • §5-2 对进给伺服系统结构的要求 • §5-3 传动齿轮副
• • 一、消除传动齿轮间隙的措施 二、齿轮齿条副
• §5-4 丝杠螺母副 • §5-5 导轨 • §5-6 回转工作台
• 二、齿轮齿条副
• 常用于行程较长的,高速直线传动。 • 当传动负载小时,也可采用双片薄齿轮调整 法,分别与齿条齿槽的左、右两侧贴紧,从 而消除齿侧间隙。
• 第五章 进给伺服系统
• §5-1 概述 • §5-2 对进给伺服系统结构的要求 • §5-3 传动齿轮副
• 一、消除传动齿轮间隙的措施
• §5-4 丝杠螺母副 • §5-5 导轨 • §5-6 回转工作台
• 联轴器传动 • 在进给传动链中,轴与轴的联接必须采用刚 性联轴器,而且大部分采用套筒式结构。
• 1) 单圆弧型面 • 接触角α随轴向载荷的大小而变化。 • 当α角发生变化时,使传动效率、承载能力和 轴向刚度均不稳定。 • 为了消除间隙和施加预紧力,必须采用双螺 母结构。 • 为了保证预紧后的 α 角维 持在45°左右,还必须严 格控制径向间隙。 r0 • 脏物容易沉积于槽底,使 传动效率降低,磨损加快。 α • 便于制造。
数控车床伺服电机计算公式

数控车床伺服电机计算公式数控车床是一种通过计算机控制的自动化机床,它可以精确地加工各种金属和非金属材料。
而数控车床的核心部件之一就是伺服电机,它可以通过控制系统精确地控制车床的运动,从而实现精密加工。
在数控车床中,伺服电机的计算公式是非常重要的,它可以帮助工程师们准确地选择和设计伺服电机,从而保证数控车床的加工精度和效率。
本文将介绍数控车床伺服电机的计算公式,希望能对相关领域的工程师们有所帮助。
首先,我们需要了解数控车床伺服电机的基本参数,包括最大转矩、额定转速、最大转速等。
在选择伺服电机时,我们需要根据数控车床的工作要求和负载情况来确定这些参数。
一般来说,数控车床的负载是不稳定的,因此我们需要选择具有较大转矩和较宽转速范围的伺服电机。
接下来,我们来介绍数控车床伺服电机的计算公式。
在数控车床中,伺服电机的功率可以通过以下公式来计算:P = T n / 9550。
其中,P表示电机的功率,单位为千瓦(kW);T表示电机的转矩,单位为牛顿·米(N·m);n表示电机的转速,单位为转每分钟(rpm);9550是一个常数,用于将转速从rpm转换为每分钟。
通过这个公式,我们可以根据数控车床的负载情况和工作要求来计算出所需的伺服电机功率。
在实际应用中,我们还需要考虑一些修正系数,例如效率系数、动力系数等,以确保伺服电机的选型和设计是合理的。
除了功率外,我们还需要根据数控车床的运动特性和加工要求来选择伺服电机的型号和规格。
一般来说,数控车床的各个轴(X轴、Y轴、Z轴等)都需要配备伺服电机,因此我们需要根据各个轴的负载情况和运动特性来选择相应的电机型号和规格。
另外,我们还需要考虑伺服系统的控制精度和动态响应特性。
在数控车床中,伺服电机的控制精度和动态响应特性直接影响着车床的加工精度和效率。
因此,在选择伺服电机时,我们需要考虑其控制精度、动态响应特性以及控制系统的匹配性,以确保数控车床能够实现精密加工和高效生产。
伺服系统的一些公式
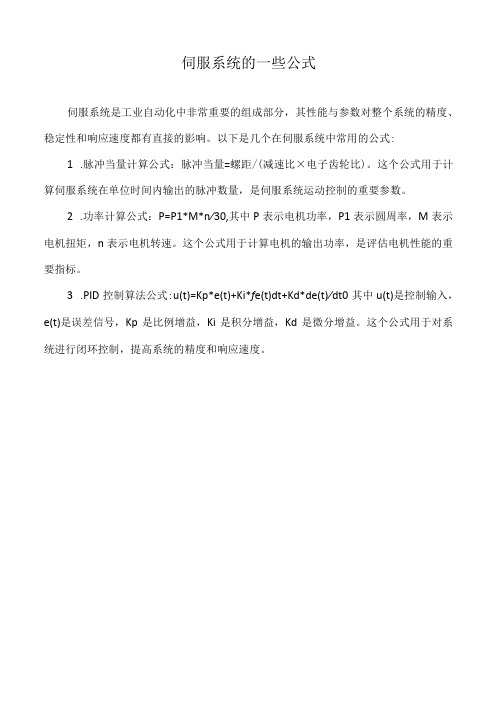
伺服系统的一些公式
伺服系统是工业自动化中非常重要的组成部分,其性能与参数对整个系统的精度、稳定性和响应速度都有直接的影响。
以下是几个在伺服系统中常用的公式:
1.脉冲当量计算公式:脉冲当量=螺距/(减速比×电子齿轮比)。
这个公式用于计算伺服系统在单位时间内输出的脉冲数量,是伺服系统运动控制的重要参数。
2.功率计算公式:P=P1*M*n∕30,其中P表示电机功率,P1表示圆周率,M表示电机扭矩,n表示电机转速。
这个公式用于计算电机的输出功率,是评估电机性能的重要指标。
3.PID控制算法公式:u(t)=Kp*e(t)+Ki*f e(t)dt+Kd*de(t)∕dt0其中u(t)是控制输入,e(t)是误差信号,Kp是比例增益,Ki是积分增益,Kd是微分增益。
这个公式用于对系统进行闭环控制,提高系统的精度和响应速度。
伺服基本原理及伺服选型计算

= 0.882 N.m
加速时所需转矩Ta = M * a * (D / 2) / R2 / R1 = 50 * (30 / 60 / 0.2) * 0.06 / 2 / 10
伺服选型计算
物理概念及公式
1
§ 力矩與轉動方程式
1. 力矩:
1) 力矩的意義:使物體轉動狀態產生變化的因素,即當物體 受到不為零的外力矩作用,原為靜止的將開始轉動,原來 已在轉動的,轉速將產生改變。 2) 力矩的定義:考慮開門的情況,如右 圖,欲讓門產生轉動,必須施一外力 F 。施力點離轉軸愈遠愈容易使門轉 動。而外力平形於門面的分力對門的 轉動並無效果,只有垂直於門面的分 力能讓門轉動。綜合以上因素,定義 力矩,以符號 τ表示。 F r θ
10
伺服选型原则
• • • • 连续工作扭矩 < 伺服电机额定扭矩 瞬时最大扭矩 < 伺服电机最大扭矩 (加速时) 负载惯量 < 3倍电机转子惯量 连续工作速度 < 电机额定转速
11
举例计算1
已知:圆盘质量M=50kg,圆盘直径 D=500mm,圆盘最高转速60rpm, 请选择伺服电机及减速机。
i
i
( mi ri )
2 i
m F
左邊的合力矩只需考慮外力所產生的力矩,由內力所產生 的力矩將會兩兩互相抵消,如右上圖所示。
括號中的量稱為剛體的轉動慣量,以符號 I 表示
I mi ri 2
i
則上面導出的轉動方程式可寫成
I
4
此方程式為繞固定軸轉動的剛體所必須遵守的基本力學方程 式,類似於移動力學中的牛頓第二運動定律。合外力對應到 合外力矩,質量對應到轉動慣量,加速度對應到角加速度。
直线电机进给系统伺服参数与控制参数的设计
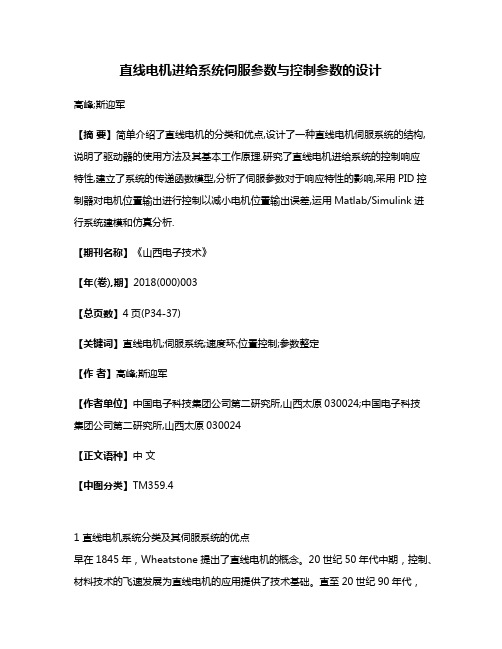
直线电机进给系统伺服参数与控制参数的设计高峰;斯迎军【摘要】简单介绍了直线电机的分类和优点,设计了一种直线电机伺服系统的结构,说明了驱动器的使用方法及其基本工作原理.研究了直线电机进给系统的控制响应特性,建立了系统的传递函数模型,分析了伺服参数对于响应特性的影响,采用PID控制器对电机位置输出进行控制以减小电机位置输出误差,运用Matlab/Simulink进行系统建模和仿真分析.【期刊名称】《山西电子技术》【年(卷),期】2018(000)003【总页数】4页(P34-37)【关键词】直线电机;伺服系统;速度环;位置控制;参数整定【作者】高峰;斯迎军【作者单位】中国电子科技集团公司第二研究所,山西太原030024;中国电子科技集团公司第二研究所,山西太原030024【正文语种】中文【中图分类】TM359.41 直线电机系统分类及其伺服系统的优点早在1845年,Wheatstone提出了直线电机的概念。
20世纪50年代中期,控制、材料技术的飞速发展为直线电机的应用提供了技术基础。
直至20世纪90年代,随着设备向高速化、精密化方向的发展,直线电机被用于设备伺服系统中,并且发展迅速[1]。
直线电机分为直线直流电动机、直线感应电动机、直线同步电动机、直线步进电动机、直线压电电动机、直线磁阻电动机。
目前使用比较广泛的是直线感应电动机和直线同步电动机。
直线同步电动机虽然比直线感应电动机工艺复杂、成本较高,但是效率较高、次级不用冷却、控制方便,更容易达到要求的性能。
因此随着钕铁硼永磁材料的出现和发展,永磁同步电机已成为主流。
在数控设备等需要高精度定位的场合,基本上采用的都是永磁交流直线同步电动机。
直线电机伺服系统的优点主要是结构简单、定位精度高、反应速度快、灵敏度高、随动性好。
2 直线电机伺服系统模型直线电机进给驱动系统结构如图1所示,主要由导轨、滑块、定子、动子、霍尔元件和光栅组成。
相对于传动的滚珠丝杠进给系统,它取消了中间的传动装置从而大大提高了电机的响应特性。
(参考资料)伺服设计计算方法

[设置示例] 求出在 HF-KP 以 3000r/min 速度运行时所需要的指令脉冲频率。 当电子齿轮比(初始参数值)为 1 时,根据 5.6 式得到以下结果:
f0
262144
N0 60
CDV CMX
(指令脉冲频率)
262144
3000 60
1
13107200[pps]
但是,由于差动线性驱动系统的最大指令脉冲频率值为 1Mpps,因此对于通用伺服,不能输入13107200pps 。 要以 3000r/min 速度运行伺服电机且指令频率低于 1Mpps,必须改变电子齿轮设置。此电子齿轮由 5.5 计算:
: 位置控制模式中输入脉冲频率
[pps]
: 位置控制模式快速进给时的输入脉冲频率 [pps]
: 位置控制模式中脉冲频率指令的
[s]
加速时间常数
: 位置控制模式中脉冲频率指令的
[s]
减速时间常数
: 位置控制增益 1
[rad/s]
: 位置控制时间常数 (Tp 1/Kp)
[s]
: 位置控制模式中每个反馈脉冲的
SM
电子齿轮 CMX CDV
Pt 262144pulse/rev
编码器
如上所示,指令脉冲乘以参数中设置的 CMX/CDV 则为位置控制脉冲。每个指令脉冲的行程值用等式 5.2 表示:
Pt CMX
0
S CDV
CMX CDV
.....................................................................................................................
(5.2)
步进、伺服电机的脉冲量和模拟量的计算方法

步进、伺服电机的脉冲量和模拟量的计算方法1、步进电机的角度控制。
首先要明确步进电机的细分数,然后确定步进电机转一圈所需要的总脉冲数。
计算“角度百分比=设定角度/360°(即一圈)”“角度动作脉冲数=一圈总脉冲数*角度百分比。
”公式为:角度动作脉冲数=一圈总脉冲数*(设定角度/360°)。
2、步进电机的距离控制。
首先明确步进电机转一圈所需要的总脉冲数。
然后确定步进电机滚轮直径,计算滚轮周长。
计算每一脉冲运行距离。
最后计算设定距离所要运行的脉冲数。
公式为:设定距离脉冲数=设定距离/[(滚轮直径*3.14)/一圈总脉冲数]3、步进电机的位置控制就是角度控制与距离控制的综合。
以上只是简单的分析步进电机的控制方式,可能与实际有出入,仅供各位同仁参考。
伺服电机的动作与步进电机的一样,但要考虑伺服电机的内部电子齿轮比与伺服电机的减速比。
有些事情说起来比较简单,但实际应用就有难度了。
请大家在实际的工作中领悟其中的道理。
模拟量的计算1、-10—10V。
-10V—10V的电压时,在6000分辨率时被转换为F448—0BB8Hex(-3000—3000);12000分辨率时被转换为E890—1770Hex(-6000—6000)。
2、0—10V。
0—10V的电压时,在12000分辨率时被转换为0—1770Hex(0—6000);12000分辨率时被转换为0—2EE0Hex(0—12000)。
3、0—20mA。
0—20mA的电流时,在6000分辨率时被转换为0—1770Hex(0—6000);12000分辨率时被转换为0—2EE0Hex(0—12000)。
4、4—20mA。
4—20mA的电流时,在6000分辨率时被转换为0—1770Hex(0—6000);12000分辨率时被转换为0—2EE0Hex(0—12000)。
以上仅做简单的介绍,不同的PLC有不同的分辨率,并且您所测量物理量实现的量程不一样。
步进伺服电机计算公式
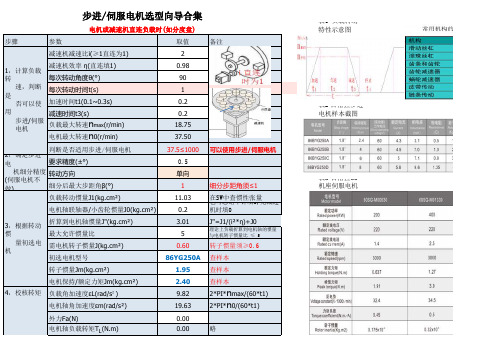
电机或减速机直连负载时(如分度盘)
步骤
参数
取值
备注
减速机减速比i(≥1直连为1)
1,计算负载 减速机效率 η(直连填1)
转
每次转动角度θ(°)
速,判断 每次转动时间t(s) 是
否可以使 加速时间t1(0.1~0.3s)
用
减速时间t3(s)
步进/伺服 电机
负载最大转速nmax(r/min)
不细分
合格
平带传送机构--常用步进电机
步骤
参数
取值
备注
A0, 工况选择 传送工况
间歇输送
每次运动距离L(mm)
500
每分停歇次数N
15
A1, 间歇输送 加速时间t1(s)
0.2
参
数(连续输 减速时间t3(s)
0.2
送不用填) 静止时间t4(s)
1
送不用填)
往返一个周期时间T(s)
负载最大线速Vmax(m/s)
2,确定步进电 机细分精
要求精度(±
mm)
度(伺服电机不 细分后最大步距角β(°)
外力Fa(N)
输送带摩擦因数μ
启动加速度a(m/s²)
3,计算皮带 电机轴角加速度εm(rad/s²) 链条/齿条 负载(含平台)总重量m1(kg) 受力 皮带总重量m2(kg)
负载与皮带总重量m(kg)
匀速运动时主滚筒拉力F(N)
负载最大线速Vmax(m/s)
电机最大转速n0max(r/min)
判断是否适用步进/伺服电机
2,确定步进电 要求精度(± mm) 机细分精
度(伺服电机不 转动方向
做)
细分后最大步距角β(°)
伺服电机速度计算公式
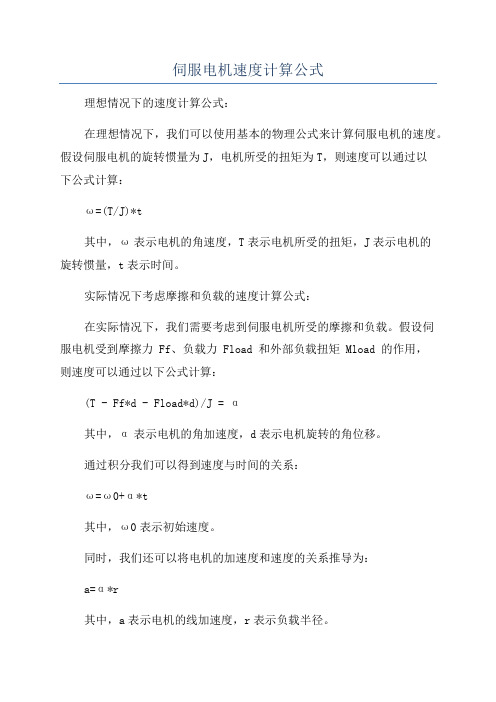
伺服电机速度计算公式
理想情况下的速度计算公式:
在理想情况下,我们可以使用基本的物理公式来计算伺服电机的速度。
假设伺服电机的旋转惯量为J,电机所受的扭矩为T,则速度可以通过以
下公式计算:
ω=(T/J)*t
其中,ω表示电机的角速度,T表示电机所受的扭矩,J表示电机的
旋转惯量,t表示时间。
实际情况下考虑摩擦和负载的速度计算公式:
在实际情况下,我们需要考虑到伺服电机所受的摩擦和负载。
假设伺
服电机受到摩擦力 Ff、负载力 Fload 和外部负载扭矩 Mload 的作用,
则速度可以通过以下公式计算:
(T - Ff*d - Fload*d)/J = α
其中,α表示电机的角加速度,d表示电机旋转的角位移。
通过积分我们可以得到速度与时间的关系:
ω=ω0+α*t
其中,ω0表示初始速度。
同时,我们还可以将电机的加速度和速度的关系推导为:
a=α*r
其中,a表示电机的线加速度,r表示负载半径。
综上所述,实际情况下考虑摩擦和负载的速度计算公式可以表示为:ω = (T - Ff * d - Fload * d) / J * t + ω0
在实际应用中,以上的速度计算公式可能需要根据具体的情况进行微调和修正,但这些公式提供了基本计算速度的方法和思路。
伺服电机相关计算和指令

伺服电子齿轮比的计算方法电子齿轮比是伺服中经常要用到的,初学者对这个参数的设置有时会不解,先介绍两个伺服电子齿轮设置方面的2个小例子,供大家参考下。
例子1:已知伺服马达的编码器的分辨率是131072 P/R,额定转速为3000r/min,上位机发送脉冲的能力为200Kpulse/s,要想达到额定转速,那么电子齿轮比至少应该设为多少?计算如下图所示:根据上图中的算法,可以算出电子齿轮比CMX/CDV的值例子2:已知伺服马达的分辨率是131072 P/R,滚珠丝杠的进给量为 Pb =8mm。
(1) 计算反馈脉冲的当量(一个脉冲走多少)?△Lo=(2) 要求指令脉冲当量为0.1um/p, 电子齿轮比应为多少?电子齿轮比=(3) 电机的额定速度为3000rpm,脉冲频率应为多少?Fc =(a) 计算反馈脉冲的当量(一个脉冲走多少)?△Lo= 8mm/131072(b) 要求指令脉冲当量为0.1um/p, 电子齿轮比应为多少?△Lo×电子齿轮比×1000=0.1(c) 电机的额定速度为3000rpm,脉冲频率应为多少?Fc×电子齿轮比=3000/60×131072DDRVI 和DDRV A的用法区别一般伺服电机使用的最多的就是位置控制模式,其说明书上的接线,不要被吓到了。
cn1是控制端口;cn2是编码器反馈端口,不用管,有专用线的。
实际上,只用控制cn1的32、33、34、35,四根线就好了,这四根线分两组,32和33作为脉冲输入,34和35作为方向输入。
举个例子:我们把32(plus+)接上+24v,把33(plus-)接上0V,把34(dir+)接上+24v,把35(dir-)接上0V,就接成了最简单的伺服系统,发现没有,其实外部三根线就可以了,我们把32和34接在一起,共用电源正极。
不过,伺服是靠脉冲控制的,我们的线路只给伺服发了一个脉冲,而本套伺服是10000脉冲/转,那么它只转动了360/10000,呵呵,几乎没动一样,要使它连续运动,就要给它持续的脉冲,脉冲快,它转得快,脉冲多,它转得多。
进给伺服系统概述

大倍数。 调速单元输出的量是速度量,这一速度量经过积分环节 1/s 后成为角 位移量。
2-1、进给伺服系统的数学模型
对控制系统的数学描述, 实际上就是首先建立系统中各环节的传 递函数,然后求出整个系统的传递函数。有速度内环的闭环系统如 图 8-4 所示:
位置检测环节是指位置传感器(光电编码器,旋转变压器等)和后置 处理电路。作用是把位置信号转换为电信号。这个环节也可以看做是 一个比例环节,比例系数是 K f 。 将各环节的传递函数置换 8-4 的框图, 就得到了动态结构图, 如图 8-5 所示:
1.静态性能分析
控制系统中,最重要的是稳定性问题。如果一台数控机床的伺服 控制系统是不稳加工的。因此,任何控制系统首先必须是稳定的。 2、稳态性能指标 位置伺服系统的稳态性能指标主要是定位精度,指的是系 统过度过程终了时实际状态与期望状态之间的偏差程度。 一般数控机 床的定位精度应不低于 0.01mm,而高性能数控机床定位精度将达到 0.001mm 以上。 影响伺服系统稳态精度的原因主要有两类, 一类是位置测量装置
伺服电机转速计算公式举例说明

伺服电机转速计算公式举例说明好嘞,以下是为您生成的关于“伺服电机转速计算公式举例说明”的文章:咱今儿就来好好唠唠伺服电机转速的那些事儿。
要说这伺服电机啊,在好多自动化设备里那可都是关键角色。
就像汽车的发动机一样,它的转速直接影响着整个系统的运行效果。
先给您说说这伺服电机转速的计算公式:n = 60f / p × (1 - s) 。
这里面的“n”呢,就是电机的转速;“f”是电源频率;“p”指的是电机的磁极对数;“s”是电机的转差率。
咱举个例子来说明。
比如说有个伺服电机,电源频率是 50Hz,磁极对数是 2,转差率是 0.05 。
那咱就来算算它的转速。
先算磁极对数这部分,2 对磁极,那转一圈就得经过 4 个磁极。
然后电源频率 50Hz ,就是说电流每秒变化 50 次。
所以理论上电机每秒应该转 50×4 = 200 圈。
但别忘了还有转差率 0.05 。
这转差率啥意思呢?就是电机实际转速和理论转速的差值比例。
所以实际转速就得是 200×(1 - 0.05) = 190 转每分钟。
我之前在一个工厂里就碰到过因为没算准伺服电机转速,导致整个生产线出问题的情况。
那是个生产小零件的厂,有台设备上的伺服电机负责精准输送零件。
一开始大家都没太在意转速的计算,觉得差不多就行。
结果呢,这电机转速不稳定,有时候快有时候慢,生产出来的零件好多都不合格。
这可把工人们急坏了,大家都在那琢磨到底是咋回事。
后来一检查,发现就是转速没算对,调整之后,生产线立马就顺溜了,生产的零件那质量也是杠杠的。
再比如说,在一些数控机床里,伺服电机的转速精度要求那是相当高。
要是转速算错了一点点,加工出来的零件尺寸可能就偏差大了,这损失可就大了去了。
所以啊,您可别小瞧这伺服电机转速的计算,算准了那是事半功倍,算不准那麻烦可就大啦!总之,搞清楚伺服电机转速的计算公式,并且能根据实际情况准确计算,对于各种需要精确控制的设备和系统来说,那真是太重要啦!无论是工业生产,还是科研实验,都离不开这准确的计算。
伺服型算方法

伺服选型计算方法(1) 机械系统的种类用可变速电机驱动的机械系统,一般有以下几类。
将伺服系统用于机械系统中时,请注意以下各点。
①减速比为了有效利用伺服电机的功率,应在接近电机的额定速度(最高旋转速度)数值的范围使用。
在最高旋转速度下连续输出转矩,还是比额定转矩小。
②预压转矩对丝杠加预压力,刚性增强,负载转矩值增大。
由预压产生的摩擦转矩,请参照滚珠丝杠规格书。
③保持转矩升降机械在停止时,伺服电机继续输出保持力。
在时间充裕的场合,建议使用保持制动。
<参考>摩擦系数μ的目标值机械效率η的目标值模数(模数) = ———————————————链条尺寸材质密度(齿数)(齿轮节圆直径)※公制齿轮※模数0.5 0.75 0.8 1 1.5 2 2.5 3 4 5 6 7(2) 容量选择计算容量选择计算,是由机械规格(构成)计算出必要的伺服电机容量的计算。
容量选择计算所需要的项目如下。
一般地说,由于不能测定系统惯性矩和负载转矩。
因此,由机械的构成计算出近似值。
容量选择计算的次序如下。
容量选择流程图・ 负载惯性矩(机械系统的惯性矩) ・ 负载转矩(驱动机械所需的转矩) ・ 加速/减速时间 ・ 运行模式①由机械构成计算负载惯性矩。
②由机械构成计算负载转矩。
③临时选定电机容量。
④确认最短加速/减速时间。
指定时间时,计算必要的加速/减速转矩。
⑤由运行模式绘制转矩特性曲线。
⑥由转矩特性曲线计算出实际转矩。
⑦如果实际转矩(T rms )比额定转矩(T R )小,则可按指定的运行模式运转。
⑧计算再生电力,必要时选择再生电阻器。
⑨在可能范围内,重新审定机械规格。
开始计算负载惯性矩计算负载转矩T L临时选定电机容量计算最短加速/减速时间(计算加速/减速转矩)绘制转矩特性曲线计算实际的转矩计算再生电重新审定机械规格, 变更运行模式结束<惯性矩计算>・形状16Jz=103D4Jx=W8W103D2+W12103L2Jy==πρ32103LD1032W=πρ4103LD1032Jz=W16A1032B1032+Jx=16W103B2+W12103L2Jy=16W103A2+W12103L2W=πρ4103A103B103LW=103A103B103Lρ12WB1032L1032+Jx=Jy=Jz=12WL1032A1032+12WA1032B1032+W =103A2103B2103Lρ103A1103B1-W2=103A2103B2103LρW1=103A1103B1103Lρ12W2B21032L1032+Jx=-12W1B11032L1032+12W2A21032L1032+Jy=-12W1A11032L1032+12W2A21032B21032+Jz=-12W1A11032B11032+W=πρ4103LD21032D11032-Jz=W8D21032D11032+=πρ32103LD21034D11034-Jx=16WD21032D11032++W12103L2Jy=・换算旋转体·转盘驱动求出惯处在离开旋转轴位置的某一物体的惯滚珠丝杠μ: 摩擦系数 BP: 丝杠螺矩[mm]W ,W 1: 可动部分重量[kg] W 2: 配重重量[kg]GL: 减速比(无单位) F: 推力[kg]・ 上升时(垂直)・ 下降时(垂直)・ 停止时(垂直)传送带·齿条和小齿轮μ: 摩擦系数 D: 直径[mm]W ,W 1: 可动部分重量[kg] W 2 : 配重重量[kg] GL: 减速比(无单位)・ 上升时(垂直)・ 下降时(垂直)・ 停止时(垂直)<负载转矩(T L )计算>移动速度 V 可动部分重量W减速比GL电机轴旋转速度N丝杠螺矩L小齿轮直径D可动部分重量 W移动速度 V减速比GL电机轴旋转速度 N①计算负载惯性矩(J L )计算对于电机轴换算的机械系统负载惯性矩(GD 2)。
伺服丝杆计算公式

伺服丝杆计算公式1.力矩计算公式:伺服丝杆传动系统的力矩可以通过以下公式计算:T=F*p*η*μ其中,T表示力矩,F表示施加在丝杆上的力,p表示丝杆的螺距,η表示传动效率,μ表示摩擦系数。
2.转矩计算公式:伺服丝杆传动系统的转矩可以通过以下公式计算:τ=T*γ其中,τ表示转矩,T表示力矩,γ表示丝杆的传动效率。
3.加速度计算公式:伺服丝杆传动系统的加速度可以通过以下公式计算:a=(F-Ff)/m其中,a表示加速度,F表示施加在丝杆上的总力,Ff表示摩擦力,m表示质量。
4.速度计算公式:伺服丝杆传动系统的速度可以通过以下公式计算:v=(p*n)/60其中,v表示速度,p表示丝杆的螺距,n表示电机的转速。
5.丝杆传动效率计算公式:伺服丝杆传动系统的传动效率可以通过以下公式计算:η=(Tm*n)/(F*p)其中,η表示传动效率,Tm表示电机输出的扭矩,n表示电机的转速,F表示施加在丝杆上的力,p表示丝杆的螺距。
6.负载惯性矩计算公式:伺服丝杆传动系统的负载惯性矩可以通过以下公式计算:Jl = Jm + (mr^2)其中,Jl表示负载惯性矩,Jm表示电机本身的惯性矩,mr表示负载的半径。
7.负载扭矩计算公式:伺服丝杆传动系统的负载扭矩可以通过以下公式计算:Tl=Jl*α其中,Tl表示负载扭矩,Jl表示负载惯性矩,α表示加速度。
以上是一些常用的伺服丝杆计算公式,可以根据实际应用和具体问题选择合适的公式进行计算。
需要注意的是,在实际应用中,根据伺服丝杆传动系统的具体结构和参数,可能还需要考虑一些其他因素,如传动间隙、动态响应等。
因此,在实际设计和计算中,建议结合具体情况进行综合分析和计算。
转速,进给参数算法(经典不要错过哦

转速,进给参数算法(经典不要错过哦!)●切削条件的计算1 转速N=(Vx 1000)/π* DeDe=2 *√(Ap * (D - Ap)) (mm)2 进给速度F = N * fR (mm/min)FR=hmax * ( (D)/(√Ap * (D -Ap)) ) (mm/rev)N=转速(rev/min)V= 实际切削速度(m/min), 见表一De= 有效刀具直径(mm), 见表二Ap=轴向切削深度Ae=切削宽度(mm)F=进给(mm/min)fR=每刃进给(mm),见表一表四h max.= 最大切屑厚度,见表三[表一]一般实际切削速度和进给速度硬度刀片材料实际切削速度(M/min) 进给(mm/rev) 刀具直径最大切削深度(mm) 最大切削宽度(mm)8 10 12 16 20 25 30 32灰铸铁(FC250,FC300) HB160-260 JC5010 JC5015 200-400 0.3 0.4 0.5 0.6 0.6 0.7 0.7 0.7 D10 D/10球墨铸铁(FCD600,FCD700) HB170-300 JC5010 JC5015 150-350 0.3 0.4 0.5 0.6 0.6 0.7 0.7 0.7 D/15 D/15碳钢(S50C,S55C) HB180-280 JC5010 JC5015 180-230 0.3 0.4 0.4 0.5 0.5 0.6 0.6 0.6 D/15 D15低合金钢(SCM440) HB180-280 JC5010 JC5015 150-200 0.3 0.4 0.4 0.5 0.5 0.6 0.6 0.6 D/15 D15模具钢(SKD11,SKD61) HB180-255 JC5010 JC5015 130-18 0.25 0.3 0.4 0.5 0.5 0.6 0.6 0.6 D/20 D/20淬火钢(SKD11,SKD61) HRC40-55 JC5010 JC5015 70-90 0.25 0.3 0.4 0.5 0.5 0.6 0.6 0.6 D/30 D/30不锈钢(SUS304,SUS316) HB150-250 JC5010 JC5015 90-130 0.25 0.3 0.4 0.4 0.4 0.5 0.5 0.5 D/20 D/20铜合金HB80-150 JC5010 KT9 150-200 0.4 0.5 0.6 0.7 0.7 0.8 0.8 0.8 D/10 D/10 铝合金HB30-100 JC5010KT9 200-300 0.4 0.5 0.6 0.7 0.7 0.8 0.8 0.8 D/6 D/6石磨JC5010KT9 200-400 0.5 0.6 0.7 0.8 0.8 0.9 0.9 0.9 D/5 D/5注意1.本表为中、短系列及直径超过Ø12mm刀具有效;2 对于加长系列及直径在Ø12mm以下的系列刀具的修正系数请参见表四[表二]有效刀具直径一览表De(mm)刀具直径(mm) 轴向切削深度:Ap(mm)0.2 0.3 0.5 1.0 1.5 2.0 2.5 3.0 3.5 4.0 4.5 5.0 5.5 6.08 2.5 3.0 3.9 5.3 6.210 2.8 3.4 4.4 6.0 7.1 8.012 3.1 3.7 4.8 6.6 7.9 8.9 9.716 3.6 4.3 5.6 7.7 9.3 10.6 11.6 12.520 4.0 4.9 6.2 8.7 10.5 12 13.2 14.3 15.2 16.025 4.5 5.4 7.0 9.8 11.9 13.6 15.0 16.2 17.3 18.3 19.2 20.030 4.9 6.0 7.7 10.8 13.1 15.0 16.6 18.0 19.3 20.4 21.4 22.4 23.2 24.032 5 6.2 7.9 11.1 13.5 15.5 17.2 18.7 20.0 21.2 22.2 23.2 24.1 25.0表三最大切屑厚度硬度最大切屑厚度:h max(mm)刀具直径<mm)8 10 12 16 20 25 30 32灰铸铁(FC250,FC300) HB160-260 0.3 0.4 0.5 0.6 0.6 0.7 0.7 0.7球墨铸铁(FCD600,FCD700) HB170-300 0.3 0.4 0.5 0.6 0.6 0.7 0.7 0.7碳钢(S50C,S55C) HB180-280 0.3 0.4 0.4 0.5 0.5 0.6 0.6 0.6低合金钢(SCM440) HB180-280 0.3 0.4 0.4 0.5 0.5 0.6 0.6 0.6模具钢(SKD11,SKD61) HB180-255 0.25 0.3 0.4 0.5 0.5 0.6 0.6 0.6淬火钢(SKD11,SKD61) HRC40-55 0.25 0.3 0.4 0.5 0.5 0.6 0.6 0.6不锈钢(SUS304,SUS316) HB150-250 0.25 0.3 0.4 0.4 0.4 0.5 0.5 0.5铜合金HB80-150 0.4 0.5 0.6 0.7 0.7 0.8 0.8 0.8铝合金HB30-100 0.4 0.5 0.6 0.7 0.7 0.8 0.8 0.8石磨0.5 0.6 0.7 0.8 0.8 0.9 0.9 0.9表四以刀具颈部长度为基准的切削参数修正系数标准系列中长系列加长系列直径(mm) ll ll/D 转速% 进给% ll ll/D 转速% 进给% ll ll/D 转速% 进给%8 35 4.4 100 100 53 6.6 60 65 75 9.4 50 5010 35 3.5 100 100 53 5.3 70 80 75 7.5 60 6512 26 2.2 100 100 53 4.4 90 90 85 7.1 65 6516 32 2.0 100 100 63 3.9 100 100 100 6.3 70 7020 38 1.9 100 100 75 3.8 100 100 115 5.8 75 7525 45 1.8 100 100 90 3.6 100 100 135 5.4 80 8030 53 1.8 100 100 106 3.5 100 100 160 5.3 80 9032 53 1.7 100 100 106 3.3 100 100 160 5.0 80 90注意:使用加长系列刀具时,必须按本表所示百分比降低切削参数。
- 1、下载文档前请自行甄别文档内容的完整性,平台不提供额外的编辑、内容补充、找答案等附加服务。
- 2、"仅部分预览"的文档,不可在线预览部分如存在完整性等问题,可反馈申请退款(可完整预览的文档不适用该条件!)。
- 3、如文档侵犯您的权益,请联系客服反馈,我们会尽快为您处理(人工客服工作时间:9:00-18:30)。
步进电机丝杆导程4mm
伺服电机丝杆导程5mm 旋转机构减速比180:1 伺服电机分辨率=131072
步进电机:
脉冲当量= 导程/细分数(mm)
脉冲数= 行程/脉冲当量
伺服:升降脉冲当量=导程*电子齿轮比/(分辨率) (mm) 当量*131072*180(100)/100(180)=5
旋转脉冲当量*131072*180(100)/100(180)=360(角度)
当量=导程*电子齿轮比/(分辨率*减速比)=360*电子齿轮比/(分辨率*减速比)
伺服每转一周的驱动脉冲数=伺服每转一周控制脉冲数×电子齿轮比
脉冲/转-----是伺服电机编码器的分辨率,这个值取决于伺服电机后面的编码器。
比如说是2500线每转的编码器,就是每转要走2500个脉冲。
当然,有些控制器可以对双相编码器的脉冲进行四倍频,即要乘以4 ,如果编码器是2500线的,那就是每转一圈要走10000个脉冲。