电液伺服阀测试方法
电液伺服阀,比例阀的试验与维修

电液伺服阀,比例阀的试验与维修
虞勤俭;徐水镜
【期刊名称】《液压气动与密封》
【年(卷),期】1998(000)004
【摘要】本文主要介绍宝钢主作业线使用最广泛的电液伺服阀、电液比例阀的试验方法与维修。
【总页数】4页(P30-32,42)
【作者】虞勤俭;徐水镜
【作者单位】宝钢设备检修有限公司;宝钢设备检修有限公司
【正文语种】中文
【中图分类】TG333
【相关文献】
1.斯太尔汽车感载比例阀的使用与维修 [J], 陆涛
2.电液伺服阀的一种特殊故障的判断与维修 [J], 王军政;徐长生;李金仓;温志国
3.电液比例阀与电液伺服阀性能比较及前景展望 [J], 苏东海;任大林;杨京兰
4.电液伺服阀,比例阀及系统在宝钢的应用 [J], 肖凯鸣;甄欢溢
5.依维柯汽车感载比例阀的使用与维修 [J], 党平芳;王岩峰
因版权原因,仅展示原文概要,查看原文内容请购买。
电液位置伺服控制系统实验
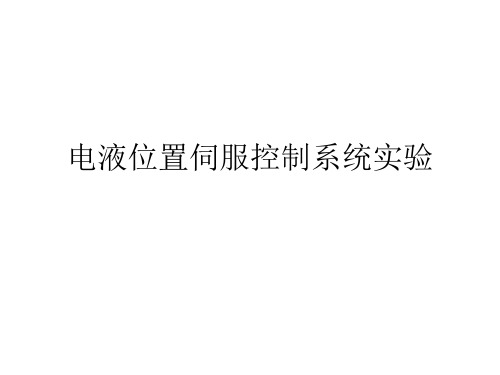
2
s2
2.834 2 0.866 1 2 s s s 1 2 14 .726 14 .726
正常参数时的ωc=2.78, ωh=14.8,Kg=19.1
增大Ki
正常参数
C (s) 4.611 R( s) 1 2 0.866 2 s 14 .726 2 s 14 .726 s 1
斜坡输入1
正弦输入
正弦输入,幅值5,频率1
正弦输入,幅值5,频率2.95
3 液压系统原理
压力传感器2
伺服缸
压力传感器3
平衡阀 电磁换向阀
蓄能器
电液伺服阀 压力传感器1
流量计2
流量计1 精滤器 电磁溢流阀
电机泵组
M
粗滤器 精滤器
4 系统控制原理
数据采集
参考输入
控制器
数模转换
功率放大
伺服阀
伺服缸
K i 73.746 KV 2.834 K d 1 26.022
K d1 h 代入系数得到 K d 1 26 .022 14 .726 h a a 0.12 (b K d 2 ) (b K d 2 ) (0.2 2.861) h h 0.866 2 K d1 a 2 K d 1 a 2 26.022 0.12
mmax 为能量输出单元在线 性范围内的最大值
r0,ml 为输入信号在线性范 围内的最大值
阶跃输入2.5
阶跃输入5
阶跃输入9
阶跃输入12
系统开环传递函数
KV C (s) R(s) 1 2 2 h s 2 s s 1 h h
Ki KV K d1
2)阀控缸微分方程
高频响电液伺服阀的静态与动态特性测试方法

高频响电液伺服阀的静态与动态特性测试方法引言:高频响电液伺服阀是一种广泛应用于工业自动化系统中的重要元件。
为了确保其正常运行和稳定性,需要对其静态与动态特性进行测试。
本文将介绍高频响电液伺服阀的静态与动态特性测试的具体方法。
第一部分:高频响电液伺服阀的静态特性测试方法静态特性测试是评估伺服阀性能的重要手段之一。
以下是高频响电液伺服阀静态特性测试的步骤和方法:步骤一:准备测试装置与仪器a. 确保测试装置能够提供足够的压力和流量,并且具备快速响应的能力。
b. 安装测试仪器,包括流量计、压力计和温度计等。
步骤二:测试前的准备工作a. 检查伺服阀的连接是否牢固,并进行必要的润滑和清洁。
b. 确定测试所需的工作条件,包括压力、温度和流量等。
步骤三:进行静态特性测试a. 断电,确保伺服阀处于关闭状态。
b. 通过调节控制仪对伺服阀进行一定的输入信号。
c. 测量伺服阀的流量、压力和阀芯位置等数据。
d. 循环进行不同输入信号的测试,记录测试数据。
步骤四:数据处理与分析a. 对测试得到的数据进行整理和处理。
b. 绘制流量-压力曲线和流量-阀芯位置曲线等图形。
c. 分析测试结果,评估伺服阀的静态特性表现。
第二部分:高频响电液伺服阀的动态特性测试方法动态特性测试能够评估伺服阀的响应速度和稳定性。
以下是高频响电液伺服阀动态特性测试的步骤和方法:步骤一:准备测试装置与仪器a. 确保测试装置能够提供足够的压力和流量,并具备高频响应的能力。
b. 安装测试仪器,包括快速采集系统、压力计和位移传感器等。
步骤二:测试前的准备工作a. 检查伺服阀的连接是否牢固,并进行必要的润滑和清洁。
b. 确定测试所需的工作条件,包括压力、温度和流量等。
步骤三:进行动态特性测试a. 通过控制系统向伺服阀输入一系列具有不同频率和振幅的信号。
b. 使用快速采集系统记录伺服阀的输出压力和阀芯位置等数据。
c. 观察测试数据,评估伺服阀的响应速度和稳定性。
步骤四:数据处理与分析a. 对测试得到的数据进行整理和处理。
射流管式电液伺服阀环境试验分析
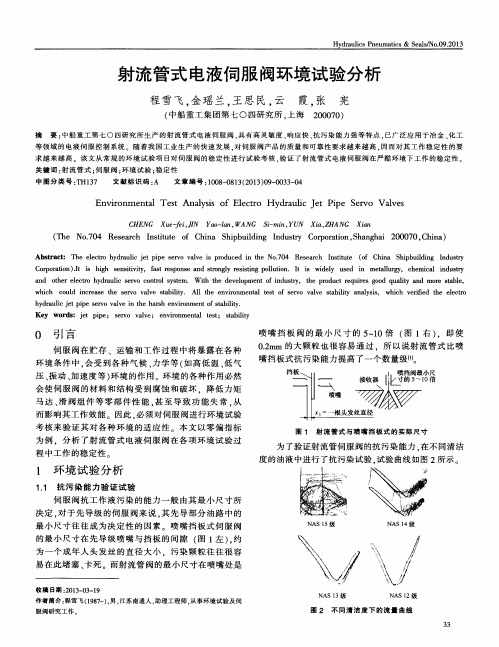
E n v i r o n me n t a l Te s t An a l y s i s o f E l e c t r o Hy d r a u l i c J e t P i p e S e r v o Va l v e s
C H E N G Xu e - f e i , 】 I N Y a o - l a n , WA NG S i - mi n , Y U N X i a 。 Z H A NG X i a n
h y d r a u l i c j e t p i p e 8 e r v 0 v a l v e i n t h e h a r s h e n v i r o n m e n t o f s t a b i l i t y .
Ke y wo r d s :j e t p i p e ;s e r v o v l a v e ;e n v i on r me n t l a t e s t ;s t bi a l i t y
摘
2 0 0 0 7 0 )
要: 中船 重 工 第 七 。 四研 究 所 生 产 的射 流管 式 电 液伺 服 阀 , 具有高灵敏度 、 响应 快 、 抗污染能力强等特点 , 已广泛应用于冶金 、 化 工
等 领 域 的 电 液伺 服 控 制 系 统 。 随 着 我 国 工 业 生 产 的 快 速 发 展 , 对 伺 服 阀产 品 的质 量 和 可靠 性 要 求 越 来 越 高 , 因而 对 其 工 作 稳 定 性 的要
0 引言
伺 服 阀 在贮 存 、运输 和工 作 过程 中将 暴露 在 各 种
环 境条 件 中 , 会 受 到各 种 气 候 、 力学等( 如 高低 温 、 低 气 压、 振动、 加 速 度等 ) 环 境 的作用 。环境 的各 种作 用 必然
伺服阀标准
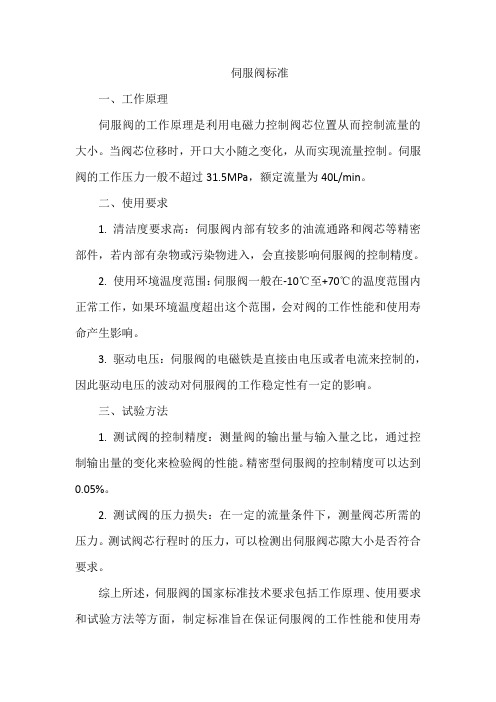
伺服阀标准
一、工作原理
伺服阀的工作原理是利用电磁力控制阀芯位置从而控制流量的大小。
当阀芯位移时,开口大小随之变化,从而实现流量控制。
伺服阀的工作压力一般不超过31.5MPa,额定流量为40L/min。
二、使用要求
1. 清洁度要求高:伺服阀内部有较多的油流通路和阀芯等精密部件,若内部有杂物或污染物进入,会直接影响伺服阀的控制精度。
2. 使用环境温度范围:伺服阀一般在-10℃至+70℃的温度范围内正常工作,如果环境温度超出这个范围,会对阀的工作性能和使用寿命产生影响。
3. 驱动电压:伺服阀的电磁铁是直接由电压或者电流来控制的,因此驱动电压的波动对伺服阀的工作稳定性有一定的影响。
三、试验方法
1. 测试阀的控制精度:测量阀的输出量与输入量之比,通过控制输出量的变化来检验阀的性能。
精密型伺服阀的控制精度可以达到0.05%。
2. 测试阀的压力损失:在一定的流量条件下,测量阀芯所需的压力。
测试阀芯行程时的压力,可以检测出伺服阀芯隙大小是否符合要求。
综上所述,伺服阀的国家标准技术要求包括工作原理、使用要求和试验方法等方面,制定标准旨在保证伺服阀的工作性能和使用寿
命,以满足各种工业生产领域的需求。
哈工大机电液系统测试技术大作业 电液伺服阀性能测试

H a r b i n I n s t i t u t e o f T e c h n o l o g y机电液系统实验测试技术大作业(二)设计方案:电液伺服阀性能测试系统学院:机电工程学院专业:机械设计制造及其自动化班级:学号:姓名:指导老师:时间:哈尔滨工业大学目录前言 (2)系统组成及功能 (2)电液伺服阀测试系统原理 (2)电液伺服阀特性测试 (3)静态测试 (3)动态测试 (9)传感器选型 (10)体会与心得 (10)参考文献 (11)1.前言电液控制伺服阀简称伺服阀,相对于普通液压系统中的常规阀来说,伺服阀是一种高级的、精密的液压元件。
伺服阀既是信号转换元件,又是功率放大元件。
在电液伺服控制系统中,伺服阀将系统的电气部分与液压部分连接起来,实现电液信号的转换与放大,对液压执行元件进行控制,具有控制精度高、响应速度快、信号处理灵活、输出功率大和结构紧凑等优点。
为了更好地利用电液伺服阀,必须对它进行充分的实验。
2.系统组成及功能电液伺服阀测试系统主要由泵站系统、测试台、计算机测控系统等组成。
小泵额定压力为21 MPa,流量10 L/min;大泵额定压力为7 MPa,流量90 L/min。
测试台设计成两个工位,即电液伺服阀静态测试工位和动态测试工位。
测控系统主要包括:电源开关电路、信号调理器、Avant测试分析仪、控制软件(液压CAT控制测试软件)和计算机系统。
测控系统实施对液压能源、液压测试台的控制,实现对电液伺服阀某项或多项液压参数测试的油路转换,同时采集各项所需的液压参数,经软件处理获得符合电液伺服阀试验规范要求的曲线、数据、报表等。
实现了对电液伺服阀的动、静态特性的实时显示及描绘,并自动进行相关数据分析和处理。
3.电液伺服阀测试系统原理电液伺服阀测试系统原理图如图1所示。
4.电液伺服阀特性测试4.1静态测试测试系统示意图如图2:图2 静态实验装置典型回路(1)空载流量特性测试用下列实验步骤测出输入电流与负载压降的变化关系,从而绘制空载流量特性曲线。
电液伺服阀测试系统精度分析

电液伺服阀测试系统精度分析宋静(安庆师范学院计算机系,安徽安庆246011)摘要:本文从静态特性测试和软件两个方面分析了电液伺服阀测试系统的精度,得出了系统精度满足实用要求的结论。
关键词:电液伺服阀;静态特性;测试软件;精度分析中图分类号:T H13715 文献标识码:A 文章编号:1001-3881(2006)11-181-2The Error Ana lys is of Exper i m en ta l System for Electr on i c-hydra ulic Ser vo Va lveS ONG Jing(Computer Dep t1of Anqing Teache rs College,Anqing Anhui246011,China) Ab stra ct:The error analysis of ex peri menta l syste m for electronic-hydraulic servo valve was presented for stati c characte risti c s and soft wa re1Re sult sh ows tha t t he system can be put int o p rac tical applica tion1Keywor ds:Electronic-hydrauli c serv o valve;Sta tic cha racte ristics;S oft w a re;Err or ana l ysis0 引言计算机控制对电液伺服阀的测试要求整个系统具有很高的精度,否则测试结果就有可能与其实际性能产生偏差。
笔者所研究的电液伺服阀测试系统[1]主要可完成空载流量特性试验、压力增益特性试验、内泄漏特性试验和频率响应试验等。
前三项为静态试验,而频率响应为动态测试。
为高效完成测试与分析过程,笔者采用V isual C++编制了测试软件[2]。
电液伺服阀静动态性能测试系统的研制

!!!!!!!!!!!!!!!!!!!!!!!!!!!!!!!!!!!!!!!!!!!!!!!! 流均为 DCC )Q。 而现有的用手动阀控制的试验 S BT 的试验精度要求, 图 L 中的节流阀 F 用于调整液压缸的空行程速 机的精度仅为 S LT 。这种电液比例控制的试验机不 度, 换向阀 BB 的 R 型中位机能用于动载试验, 其回油 口上设置单向阀 BC 是为了防止在承载试验时液压缸 的有杆腔泄空。 $ 结束语 采用电液比例控制技术实现的闭环压力控制, 完 成了手动控制无法胜任的功能, 其可靠性比电液伺服 控制高, 维 比 较 容 易, 在长时间保压时能够满足 万护 方数据
BD
液压与气动
ACCL 年第 A 期
" " " " " " " " " " " " " " " " " " " " " " " " " " " " " " " " " " " " " " " " " " " " " " " " " " " " " " " " " " " " " " " " " "
- 1、下载文档前请自行甄别文档内容的完整性,平台不提供额外的编辑、内容补充、找答案等附加服务。
- 2、"仅部分预览"的文档,不可在线预览部分如存在完整性等问题,可反馈申请退款(可完整预览的文档不适用该条件!)。
- 3、如文档侵犯您的权益,请联系客服反馈,我们会尽快为您处理(人工客服工作时间:9:00-18:30)。
电液伺服阀自动测试方法的研究
广州博玮伺服科技有限公司
•摘要:研究了电液伺服阀自动测试的方法。
给出了液压系统的工作原理,介绍了自动测控单元的硬件构成,详细论述了软件设计的核心算法和自动功能的实现。
1 前言
电液伺服控制系统在控制领域中占有重要的地位,特别是在大功率、快速、精确的控制系统中起到重要作用。
电液伺服阀是其中的主要执行机构。
在阀出厂前和维修后进行性能测试是必不可少的环节。
传统的测试系统大都由分立的模拟仪表组成,在测试过程中,一般由模拟仪器在纸上记录模拟试验曲线或由试验人员记录试验数据,然后把数据进行手工处理得到性能指标。
显然,该方法工作量大、速度慢、效率低、精度差。
随着微电子技术和计算机技术的飞速发展,计算机辅助测试(CAT)技术在液压系统测试中得到了广泛的应用。
它具有测试精度高、速度快、性价比高、测试的重复性和可靠性高等优点,有着很好的应用前景。
因此,本文基于CAT技术,研究了实现电液伺服阀自动测试的方法。
2 自动测试系统工作原理
根据GB/T15623—1995B标准,电液伺服阀的自动测试需要完成静态性能测试(空载特性、压力增益特性、负载特性)和动态性能测试(幅频特性、相频特性),在性能曲线上直接读出性能指标,并可以把曲线保存成可以随时调用的数据文件。
液压测试原理和国标相同。
自动测试就是利用现代的传感器技术、电子技术和计算机技术,原来由试验人员手工单点测试、读取模拟仪表、记录数据、描绘曲线的过程用自动测试系统迅速地自动连续地对各点进行测试、保存数据文件并自动生成性能曲线,从而得出电液伺服阀的各个性能指标。
其中,空载特性、负载特性、动态特性的测试最具代表性。
为实现自动测试功能,测试系统在结构上分为测试台液压系统和自动测控单元。
图1 测试台液压系统原理图
测试台液压系统结构原理如图1所示。
在对电液伺服阀进行不同的特性测试时闸阀的开关状态如表1所示。
闸阀采用手动开关阀可以很好地密封液压回路,避免电磁开关阀有时出现行程不到位的缺点,减少测试误差。
电液伺服阀8的各个测试点的自动变换由自动测控单元控制,完成空载特性测试和负载特性测试时被测阀开口度变换的自动化过程。
为实现系统的自动加载,采用比例溢流阀5做背压阀,自动调节系统负载压力,完成压力增益特性和负载特性测试的自动化过程,克服了手动加载的随机干扰和量化不准确、耗时长等缺点。
表1 闸阀开关状态
本系统采用液压缸和位移传感器的方式计算电液伺服阀的工作流量,计算的流量不仅精确,而且克服了大流量流量计误差偏大、有最小流量限制的缺点。
静态缸23在限位开关22、24和电磁换向阀21的控制下,在静态性能测试时相当于缸有无限长的行程。
对位移传感器25的位移信号进行微分与静态缸23的有效面积的积即得电液伺服阀的工作流量,流量的正负由控制被测阀的电信号的正负决定。
动态性能的自动测试采用频域扫频法。
动态缸12的工作频率为400Hz,满足被测电液伺服阀的动态性能测试要求。
自动测控单元给电液伺服阀0~200Hz的正弦激励信号,根据位移传感器20记录的动态缸的位移规律,从而得出电液伺服阀的动态特性。
2 基于CAT技术的自动测控单元
采用“工控机+DA/AD采集卡”及相应的传感、变换电路组成信号发生和采集的典型硬件系统,结合编制的专用软件组成电液伺服阀的自动测控单元。
自动测控单元可以自动控制被测阀8和背压阀5的开口度按测试要求减小或增大,并记录保存每个测试点的压力、流量、电流等数据,自动生成性能曲线。
2.1 硬件构成
电液伺服阀自动测控单元的硬件采用“传感器+数据采集卡+工控机+电控器”的结构,如图2所示。
其中的压力传感器采用压阻式传感器,位移传感器采用差动变压器式传感器。
A/D数据采集卡采用研华的PCL-818L,其采样速度每通道可达40kHz,采用差分输入接线法,有8个输入通道,D/A数据采集卡采用研华的PCL-726,可以输出DC±10V,有6个输出通道,输入输出通道的盈余可以用来检测其它液压系统时扩展之用。
该测试结构的优点是方便灵活,通用性强。
图3 自动测控程序流程式图
图3是实现产生自动控制信号和自动准确采集稳定数据并保存的程序设计流程。
U1、U2设定控制液压阀电压信号上、下限,n设定曲线的测试点数。
ΔU是自动产生控制电压信号的变化步长,大小由(U1-U2)/n决定。
U是控制液压阀的电压信号,按U=U2+iΔU的递增规律自动输出以控制液压阀的测试点变化。
q 是根据静态缸和位移传感器计算所得的被测阀工作流量。
在控制信号U输出后,程序内设定了延时环节,其大小可根据正常液压阀测试点变换时稳定时间来经验设定,一般为2~5s。
当系统稳定时,系图3 自动测控程序流程图统能从数据采集卡读取相应的传感器的稳定数据,并自动保存成数据表文件,同时自动生成相应的性能曲线。
图4是根据传感器数据自动判断液压系统是否稳定的程序设计流程。
判断的依据是流量的变化和程序的运行时间,算法上通过实现。
a、b是程序运行的中间变量,t是计时器,n设定判断稳定时对数据进行比较的点数,τ设定判断稳定时程序的最大运行时间,δ设定稳定信号允许的误差,q是静态缸的流量。
程序中的延时环节决定了所要判断的n个点的时差性,进一步保证了流量q的稳定性判断。
从自动测试系统的实际工作情况来看,若n取10,延时40~60ms效果较好。
取值太小,不能准确判断稳定,取值太大,则浪费系统的运行时间。
从以上的程序设计核心算法可以看出,该算法通用性强,适用面广,可以用不同的计算机语言来开发电液伺服阀自动测试的软件系统。
3 实验
图4 判断液压系统稳定的程序流程图
LabVIEW作为一种比较规范、成熟的图形化编程语言,可以方便地开发出虚拟面板、自动控制信号的产生和实现数据的采集、分析、处理和存储等功能。
为了对所作的研究做进一步的验证,作者基于LabVIEW软件平台,按照以上的测试方法,对电液伺服阀自动测试系统做了部分开发。
在搭建的简易试验台上用型号为34B-H10/25B电液比例换向阀代替电液伺服阀做了部分性能测试,所测的性能曲线如图5和图6所示。
图5 空载流量曲线
图6 压力流量曲线
4 结论
通过实验研究表明,本文所述的电液伺服阀自动测试的方法是完全可行的,开发的系统是稳定的,大大提高了测试精度和测试速度。
另外,该方法还可以灵活地应用于其它一些液压元件及系统的自动测试。