波峰焊焊接标准
波峰焊温度曲线图及温度控制标准

波峰焊温度曲线图及温度控制标准介绍发表于2017-12-20 16:08:55工艺/制造波峰焊是指将熔化的软钎焊料(铅锡合金),经电动泵或电磁泵喷流成设计要求的焊料波峰,亦可通过向焊料池注入氮气来形成,使预先装有元器件的印制板通过焊料波峰,实现元器件焊端或引脚与印制板焊盘之间机械与电气连接的软钎焊。
波峰焊是让插件板的焊接面直接与高温液态锡接触达到焊接目的,其高温液态锡保持一个斜面,并由特殊装置使液态锡形成一道道类似波浪的现象,所以叫“波峰焊”,其主要材料是焊锡条。
波峰焊焊接方法波峰焊方法或工艺的采用取决于产品的复杂程度以及产量,如果要做复杂的产品以及产量很高,可以考虑用氮气工艺比如CoN▼2▼Tour波峰来减少锡渣并提高焊点的浸润性。
如果使用一台中型的机器,其工艺可以分为氮气工艺和空气工艺。
用户仍然可以在空气环境下处理复杂的板子,在这种情况下,可根据客户的要求使用腐蚀性助焊剂,在焊接后再进行清洗,或者使用低固态助焊剂。
波峰焊温度曲线图介绍在预热区内,电路板上喷涂的助焊剂中的溶剂被挥发,可以减少焊接时产生气体。
同时,松香和活化剂开始分解活化,去除焊接面上的氧化层和其他污染物,并且防止金属表面在高温下再次氧化。
印制电路板和元器件被充分预热,可以有效地避免焊接时急剧升温产生的热应力损坏。
电路板的预热温度及时间,要根据印制板的大小、厚度、元器件的尺寸和数量,以及贴装元器件的多少而确定。
在PCB表面测量的预热温度应该在90~130℃间,多层板或贴片套件中元器件较多时,预热温度取上限。
预热时间由传送带的速度来控制。
如果预热温度偏低或预热时间过短,助焊剂中的溶剂挥发不充分,焊接时就会产生气体引起气孔、锡珠等焊接缺陷;如预热温度偏高或预热时间过长,焊剂被提前分解,使焊剂失去活性,同样会引起毛刺、桥接等焊接缺陷。
为恰当控制预热温度和时间,达到佳的预热温度,也可以从波峰焊前涂覆在PCB底面的助焊剂是否有粘性来进行判断。
波峰焊操作规程
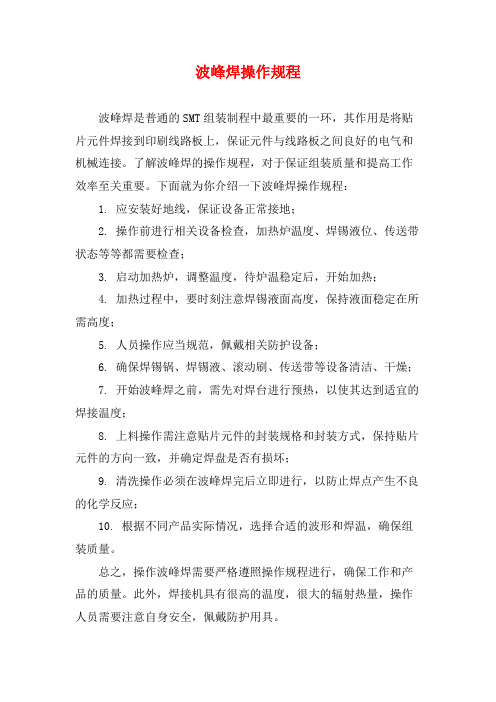
波峰焊操作规程
波峰焊是普通的SMT组装制程中最重要的一环,其作用是将贴片元件焊接到印刷线路板上,保证元件与线路板之间良好的电气和机械连接。
了解波峰焊的操作规程,对于保证组装质量和提高工作效率至关重要。
下面就为你介绍一下波峰焊操作规程:
1. 应安装好地线,保证设备正常接地;
2. 操作前进行相关设备检查,加热炉温度、焊锡液位、传送带状态等等都需要检查;
3. 启动加热炉,调整温度,待炉温稳定后,开始加热;
4. 加热过程中,要时刻注意焊锡液面高度,保持液面稳定在所需高度;
5. 人员操作应当规范,佩戴相关防护设备;
6. 确保焊锡锅、焊锡液、滚动刷、传送带等设备清洁、干燥;
7. 开始波峰焊之前,需先对焊台进行预热,以使其达到适宜的焊接温度;
8. 上料操作需注意贴片元件的封装规格和封装方式,保持贴片元件的方向一致,并确定焊盘是否有损坏;
9. 清洗操作必须在波峰焊完后立即进行,以防止焊点产生不良的化学反应;
10. 根据不同产品实际情况,选择合适的波形和焊温,确保组装质量。
总之,操作波峰焊需要严格遵照操作规程进行,确保工作和产品的质量。
此外,焊接机具有很高的温度,很大的辐射热量,操作人员需要注意自身安全,佩戴防护用具。
波峰焊温度曲线图及温度控制标准
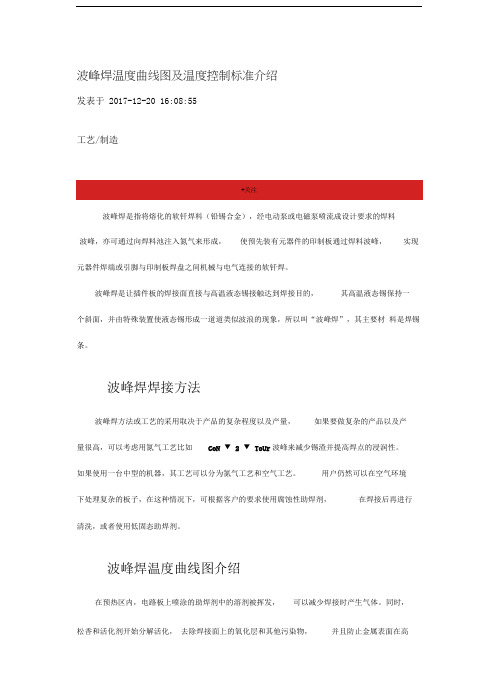
波峰焊温度曲线图及温度控制标准介绍发表于 2017-12-20 16:08:55工艺/制造波峰焊是指将熔化的软钎焊料(铅锡合金),经电动泵或电磁泵喷流成设计要求的焊料波峰,亦可通过向焊料池注入氮气来形成,使预先装有元器件的印制板通过焊料波峰,实现元器件焊端或引脚与印制板焊盘之间机械与电气连接的软钎焊。
波峰焊是让插件板的焊接面直接与高温液态锡接触达到焊接目的,其高温液态锡保持一个斜面,并由特殊装置使液态锡形成一道道类似波浪的现象,所以叫“波峰焊”,其主要材料是焊锡条。
波峰焊焊接方法波峰焊方法或工艺的采用取决于产品的复杂程度以及产量,如果要做复杂的产品以及产量很高,可以考虑用氮气工艺比如CoN ▼ 2 ▼ ToUr波峰来减少锡渣并提高焊点的浸润性。
如果使用一台中型的机器,其工艺可以分为氮气工艺和空气工艺。
用户仍然可以在空气环境下处理复杂的板子,在这种情况下,可根据客户的要求使用腐蚀性助焊剂,在焊接后再进行清洗,或者使用低固态助焊剂。
波峰焊温度曲线图介绍在预热区内,电路板上喷涂的助焊剂中的溶剂被挥发,可以减少焊接时产生气体。
同时,松香和活化剂开始分解活化,去除焊接面上的氧化层和其他污染物,并且防止金属表面在高温下再次氧化。
印制电路板和元器件被充分预热,可以有效地避免焊接时急剧升温产生的热应力损坏。
电路板的预热温度及时间,要根据印制板的大小、厚度、元器件的尺寸和数量,以及贴装元器件的多少而确定。
在PCB表面测量的预热温度应该在90~130 C间,多层板或贴片套件中元器件较多时,预热温度取上限。
预热时间由传送带的速度来控制。
如果预热温度偏低或预热时间过短,助焊剂中的溶剂挥发不充分,焊接时就会产生气体引起气孔、锡珠等焊接缺陷;如预热温度偏高或预热时间过长,焊剂被提前分解,使焊剂失去活性,同样会引起毛刺、桥接等焊接缺陷。
为恰当控制预热温度和时间,达到佳的预热温度,也可以从波峰焊前涂覆在PCB底面的助焊剂是否有粘性来进行判断。
波峰焊工艺2-双波标准曲线
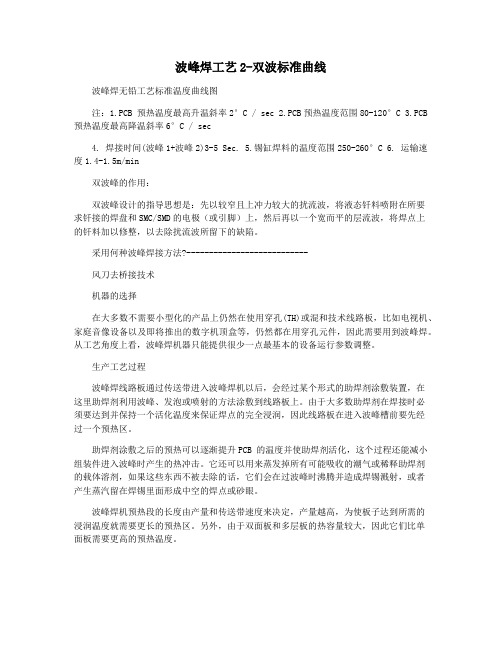
波峰焊工艺2-双波标准曲线波峰焊无铅工艺标准温度曲线图注:1.PCB 预热温度最高升温斜率2°C / sec 2.PCB预热温度范围80-120°C 3.PCB 预热温度最高降温斜率6°C / sec4. 焊接时间(波峰1+波峰2)3-5 Sec.5.锡缸焊料的温度范围250-260°C6. 运输速度1.4-1.5m/min双波峰的作用:双波峰设计的指导思想是:先以较窄且上冲力较大的扰流波,将液态钎料喷附在所要求钎接的焊盘和SMC/SMD的电极(或引脚)上,然后再以一个宽而平的层流波,将焊点上的钎料加以修整,以去除扰流波所留下的缺陷。
采用何种波峰焊接方法?---------------------------风刀去桥接技术机器的选择在大多数不需要小型化的产品上仍然在使用穿孔(TH)或混和技术线路板,比如电视机、家庭音像设备以及即将推出的数字机顶盒等,仍然都在用穿孔元件,因此需要用到波峰焊。
从工艺角度上看,波峰焊机器只能提供很少一点最基本的设备运行参数调整。
生产工艺过程波峰焊线路板通过传送带进入波峰焊机以后,会经过某个形式的助焊剂涂敷装置,在这里助焊剂利用波峰、发泡或喷射的方法涂敷到线路板上。
由于大多数助焊剂在焊接时必须要达到并保持一个活化温度来保证焊点的完全浸润,因此线路板在进入波峰槽前要先经过一个预热区。
助焊剂涂敷之后的预热可以逐渐提升PCB 的温度并使助焊剂活化,这个过程还能减小组装件进入波峰时产生的热冲击。
它还可以用来蒸发掉所有可能吸收的潮气或稀释助焊剂的载体溶剂,如果这些东西不被去除的话,它们会在过波峰时沸腾并造成焊锡溅射,或者产生蒸汽留在焊锡里面形成中空的焊点或砂眼。
波峰焊机预热段的长度由产量和传送带速度来决定,产量越高,为使板子达到所需的浸润温度就需要更长的预热区。
另外,由于双面板和多层板的热容量较大,因此它们比单面板需要更高的预热温度。
目前波峰焊机基本上采用热辐射方式进行预热,最常用的波峰焊预热方法有强制热风对流、电热板对流、电热棒加热及红外加热等。
波峰焊焊接温度标准

波峰焊焊接温度标准波峰焊(Wave Soldering)是一种常用的电子元器件焊接方法,其特点是高效、快速、自动化程度高。
在波峰焊过程中,焊接温度的控制是非常重要的,因为不合适的焊接温度可能会导致焊点质量不良,从而影响整个产品的性能和可靠性。
在波峰焊中,焊接温度的标准通常是根据焊料的熔点以及元器件和印刷电路板(PCB)的耐热温度来确定的。
一般来说,常用的焊料是锡铅合金,其熔点通常在183~215℃之间。
同时,元器件和PCB的耐热温度也要达到焊接温度或略高于焊接温度,以确保完全熔化和良好的焊接结果。
具体的焊接温度标准可以根据不同的焊接材料和焊接对象进行调整,但一般来说,以下几个方面需要考虑:1.预热温度:波峰焊之前需要将元器件和PCB进行预热,以防止温度突变对焊接结果的影响。
预热温度通常在100~150℃之间,时间一般为1~3分钟。
预热温度的选择应根据元器件和PCB的耐热温度来确定。
2.波峰温度:波峰焊的关键步骤是将焊接面放置在带有熔化焊料的波峰上。
波峰温度通常在200~260℃之间,时间一般为1~3秒。
波峰温度的选择应根据焊料的熔点来确定,以确保焊料完全熔化。
3.冷却温度:在焊接完成之后,焊点需要进行冷却,以确保焊点的结构和性能。
冷却温度一般为100℃以下,时间一般为数分钟。
冷却温度的选择应根据焊点的结构和所需的性能来确定。
除了以上几个基本的温度标准外,还需考虑以下几个因素对焊接温度进行调整:1.元器件的敏感性:有些元器件对温度非常敏感,过高的焊接温度可能会引起损坏。
在这种情况下,可以选择降低焊接温度或采取特殊的焊接保护措施,如使用热敏胶带等。
2.焊接质量要求:不同的应用对焊接质量的要求不同,有的需要焊点完全熔化,有的需要焊点的形状和外观完美。
根据具体要求,可以调整焊接温度和时间,以获得最佳的焊接效果。
3.设备的性能和稳定性:焊接设备的性能和稳定性也会对焊接温度的控制产生影响。
为了确保焊接结果的稳定性和一致性,建议选择性能稳定、控制精度高的波峰焊设备。
波峰焊工艺要求

波峰焊工艺要求波峰焊是一种常用的焊接工艺,广泛应用于电子制造、汽车制造、航空航天等行业。
本文将从波峰焊工艺的要求和特点方面进行探讨。
一、波峰焊的工艺要求波峰焊作为一种自动化焊接工艺,在实施过程中需要满足以下要求:1.1 温度控制要求波峰焊是通过在预热区使焊接材料达到熔化温度,然后在波峰中进行焊接。
因此,对于焊接温度的控制至关重要。
一方面,焊接温度过高可能会导致焊接材料烧损或热应力过大;另一方面,焊接温度过低则无法达到良好的焊接效果。
因此,波峰焊的工艺要求中通常会规定焊接温度的范围。
1.2 焊接速度控制要求波峰焊的焊接速度是指焊接头通过波峰的速度。
焊接速度的控制直接影响焊接质量。
如果焊接速度过快,可能会导致焊接不完全或者焊接瑕疵;而焊接速度过慢,则可能会导致焊接过度,造成焊接材料的变形。
因此,在波峰焊工艺要求中,通常会规定焊接速度的范围。
1.3 焊接时间控制要求波峰焊的焊接时间是指焊接头在波峰中停留的时间。
焊接时间的控制也是保证焊接质量的重要因素。
焊接时间过短可能导致焊接不完全,焊接时间过长则可能导致焊接过度。
因此,在波峰焊工艺要求中,通常会规定焊接时间的范围。
1.4 焊接压力控制要求波峰焊的焊接压力是指焊接头对焊接材料的施加的压力。
焊接压力的控制对于焊接质量也有重要影响。
焊接压力过大可能导致焊接材料的损坏;焊接压力过小则可能导致焊接不牢固。
因此,在波峰焊工艺要求中,通常会规定焊接压力的范围。
二、波峰焊的特点波峰焊相比其他焊接工艺具有以下几个特点:2.1 自动化程度高波峰焊是一种自动化的焊接工艺,通过焊接设备自动完成焊接过程,无需人工干预。
这不仅提高了焊接效率,还减少了人工操作的误差,提高了焊接质量。
2.2 焊接速度快波峰焊的焊接速度通常较快,可以在较短的时间内完成焊接任务。
这对于大批量的焊接生产具有重要意义,可以提高生产效率。
2.3 焊接质量稳定波峰焊的焊接质量相对稳定,焊接接头的质量均匀一致。
波峰焊焊接工艺
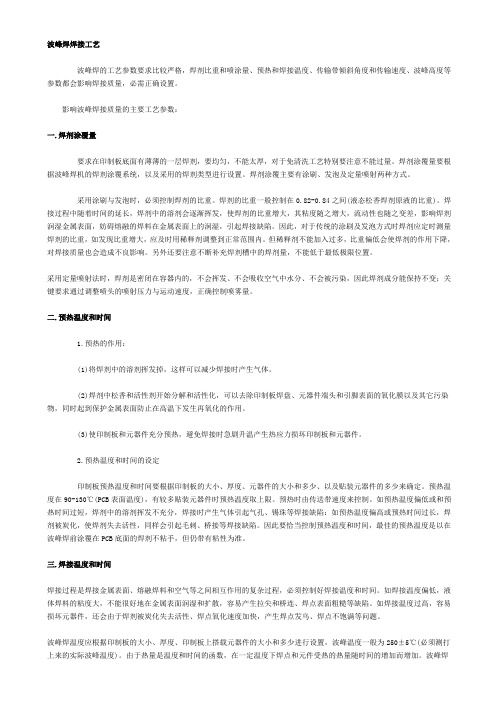
波峰焊焊接工艺波峰焊的工艺参数要求比较严格,焊剂比重和喷涂量、预热和焊接温度、传输带倾斜角度和传输速度、波峰高度等参数都会影响焊接质量,必需正确设置。
影响波峰焊接质量的主要工艺参数:一.焊剂涂覆量要求在印制板底面有薄薄的一层焊剂,要均匀,不能太厚,对于免清洗工艺特别要注意不能过量。
焊剂涂覆量要根据波峰焊机的焊剂涂覆系统,以及采用的焊剂类型进行设置。
焊剂涂覆主要有涂刷、发泡及定量喷射两种方式。
采用涂刷与发泡时,必须控制焊剂的比重。
焊剂的比重一般控制在0.82-0.84之间(液态松香焊剂原液的比重)。
焊接过程中随着时间的延长,焊剂中的溶剂会逐渐挥发,使焊剂的比重增大,其粘度随之增大,流动性也随之变差,影响焊剂润湿金属表面,妨碍熔融的焊料在金属表面上的润湿,引起焊接缺陷。
因此,对于传统的涂刷及发泡方式时焊剂应定时测量焊剂的比重,如发现比重增大,应及时用稀释剂调整到正常范围内。
但稀释剂不能加入过多,比重偏低会使焊剂的作用下降,对焊接质量也会造成不良影响。
另外还要注意不断补充焊剂槽中的焊剂量,不能低于最低极限位置。
采用定量喷射法时,焊剂是密闭在容器内的,不会挥发、不会吸收空气中水分、不会被污染,因此焊剂成分能保持不变;关键要求通过调整喷头的喷射压力与运动速度,正确控制喷雾量。
二.预热温度和时间1.预热的作用:(1)将焊剂中的溶剂挥发掉,这样可以减少焊接时产生气体。
(2)焊剂中松香和活性剂开始分解和活性化,可以去除印制板焊盘、元器件端头和引脚表面的氧化膜以及其它污染物,同时起到保护金属表面防止在高温下发生再氧化的作用。
(3)使印制板和元器件充分预热,避免焊接时急剧升温产生热应力损坏印制板和元器件。
2.预热温度和时间的设定印制板预热温度和时间要根据印制板的大小、厚度、元器件的大小和多少、以及贴装元器件的多少来确定。
预热温度在90-130℃(PCB表面温度),有较多贴装元器件时预热温度取上限。
预热时由传送带速度来控制。
波峰焊波峰高度标准
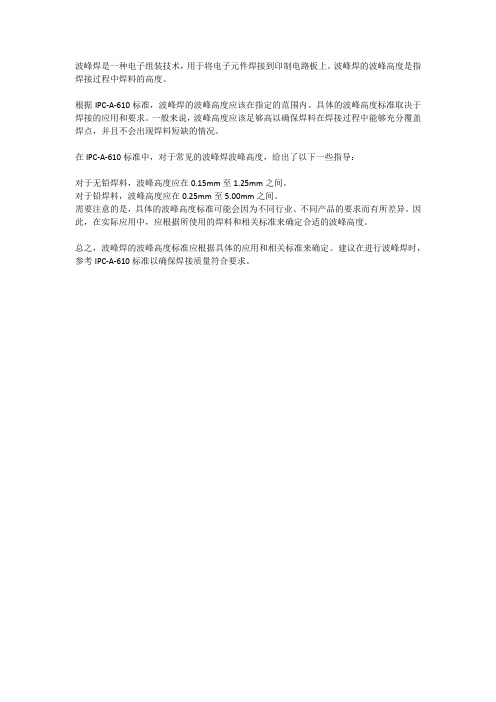
波峰焊是一种电子组装技术,用于将电子元件焊接到印制电路板上。
波峰焊的波峰高度是指焊接过程中焊料的高度。
根据IPC-A-610标准,波峰焊的波峰高度应该在指定的范围内。
具体的波峰高度标准取决于焊接的应用和要求。
一般来说,波峰高度应该足够高以确保焊料在焊接过程中能够充分覆盖焊点,并且不会出现焊料短缺的情况。
在IPC-A-610标准中,对于常见的波峰焊波峰高度,给出了以下一些指导:
对于无铅焊料,波峰高度应在0.15mm至1.25mm之间。
对于铅焊料,波峰高度应在0.25mm至5.00mm之间。
需要注意的是,具体的波峰高度标准可能会因为不同行业、不同产品的要求而有所差异。
因此,在实际应用中,应根据所使用的焊料和相关标准来确定合适的波峰高度。
总之,波峰焊的波峰高度标准应根据具体的应用和相关标准来确定。
建议在进行波峰焊时,参考IPC-A-610标准以确保焊接质量符合要求。
波峰焊焊接温度控制标准

波峰焊焊接温度控制标准
1、焊接温度
波峰焊焊接温度是影响焊接质量的一个重要的工艺参数。
当焊接温度过低时,焊料的扩展率、润湿性能变差,由于焊盘或元器件焊端不能充分的润湿,从而产生虚焊、拉尖、桥接
等缺陷;当焊接温度过高时,则加速了焊盘、元器件引脚及焊料的氧化,易产生虚焊。
焊接温度应控制在250+5℃。
2、预热温度
预热的作用是使助焊剂中的溶剂充分挥发,以免印制板通过焊锡时,影响印制板的润湿
和焊点的形成;使印制板在焊接前达到一定温度,以免受到热冲击产生翘曲变形。
一般预热温度控制在180~ 200℃,预热时间1 ~ 3分钟。
3、轨道倾角
轨道倾角对焊接效果的影响较为明显,特别是在焊接高密度SMT器件时更是如此。
当倾角太小时,较易出现桥接,特别是焊接中,SMT器件的遮蔽区更易出现桥接;而倾角过大,虽然有利于桥接的消除,但焊点吃锡量太少,容易产生虚焊。
因此轨道倾角应控制在5°~ 7°之间。
4、波峰高度
波峰的高度会因焊接工作时间的推移而有一些变化,应在焊接过程中进行适当的修正,
以保证理想高度进行焊接,以压锡深度为PCB厚度的1/2 - 1/3为准。
波峰焊操作规程

波峰焊操作规程一、引言波峰焊是一种常见的电子产品焊接方式,它通过将插件的引脚浸入熔化的焊锡中,实现焊接与固定。
为了保证焊接质量的稳定性和一致性,有必要制定一套详尽的波峰焊操作规程。
本文将介绍波峰焊操作规程的主要内容及步骤。
二、设备准备1. 检查设备在开始波峰焊操作之前,需要检查设备的工作状态。
确保焊接机、热风机和冷却装置等设备运行正常。
2. 准备焊锡及助焊剂选择合适的焊锡丝以及助焊剂,并保证其质量符合相关标准。
焊锡丝的直径、成分和熔点应根据焊接任务而确定。
三、钢网准备1. 检查钢网确保钢网的孔径、厚度和平整度符合要求。
检查钢网是否有损坏或变形,并及时更换。
2. 调整钢网高度根据焊接任务需求,调整钢网的高度。
确保钢网与插件引脚之间的距离符合要求,通常为2-3mm。
四、波峰焊操作步骤1. 设定焊接程序根据焊接任务的要求,在焊接机上设定相应的焊接程序。
确定焊接温度、波峰高度、预热时间等参数。
2. 开始预热启动焊接机,让其进行预热。
预热时间通常为5-10分钟,待设定温度达到后方可进行下一步操作。
3. 调整波峰高度根据焊接任务的要求,调整波峰高度。
通常情况下,波峰高度应略高于插件引脚的高度。
4. 准备插件将焊锡丝和助焊剂涂抹在插件的焊盘上,确保焊点涂覆均匀。
5. 插件定位将准备好的插件放置在钢网上,并调整位置,使其与焊点对齐。
6. 开始焊接将钢网缓慢地下移,插件的引脚将被浸入焊锡中。
要保持匀速下移,以确保焊接质量的稳定性。
7. 波峰焊完成当焊点完全浸入焊锡中后,继续下移一段距离,以确保焊点形成一定的柱状形态。
待上升时,焊点会被波峰除锡剂清除。
8. 冷却焊接完成后,打开冷却装置,将焊点快速冷却。
冷却时间通常为2-3分钟。
五、注意事项1. 运行时的注意事项在进行波峰焊操作时,操作人员应站立在稳定的位置上,并戴上相应的防护设备,如防静电手套、护目镜等。
2. 设备维护定期对波峰焊设备进行维护和保养,保持其正常工作状态,清理焊接头、钢网和焊炉等部件。
波峰焊焊接标准
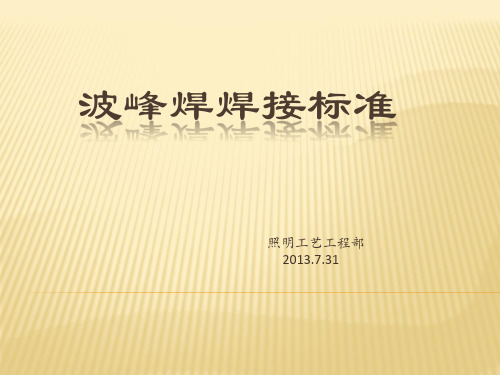
11
焊 点 接 受 要 求
可接受
缺陷(不接受)
1.由于有些成份的焊錫合金、 表面有球狀或珠 引腳或印刷板貼裝和特殊焊 粒狀物,表層凸狀, 接過程(例如,厚大的PWB的 無順暢連接的邊 慢冷卻)可能導致干枯粗糙、 緣并多錫. 灰暗、或顆粒狀外觀的焊錫, 這此焊接可接受.但必須是 當焊錫與待焊表面,形成一 個小于或等于90゜的連接角 時能明確表現出浸潤和粘附. 過量除外.
可接受
元器件的半月形涂 層可以被安裝到焊 接孔內
缺陷(不接受)
限位裝置與元件和 板面部份接觸.
5
有明顯的 距離
不可接受
參考標準: IPC-A-610C CH
序号 项目
手 插 件 引 脚 末 露 出 要 求
标准要求/图解
目標
1.元器件引腳伸出焊 盤長度(L)可依照圖紙 的要求而定.
可接受
缺陷(不接受)
波峰焊焊接标准
照明工艺工程部 2013.7.31
电子产品等级划分
1级:通用类电子产品
包括消費類電子產品、部份計算機及其外圍設備,那些對外觀要求不高而 以其使用功能为主的产品。
2级:专用服务类电子产品
包括通訊設備,復雜商業機器,高性能、長使用壽命要求的儀器。這類產 品需要持久的壽命,但不要求必須保持不間斷工作,外觀上也允許有缺陷。
2
垂 直 元 件 定 位 (續)
可接受
缺陷(不接受)
1.元器件本體與板面 元器件超出板面的 的間隙符合下表; 間隙(H)大于表格5-1 2.元器件引腿的傾斜 中所給的最大值. 度(Θ)滿足最小電氣 間隙要求.
參考標準: IPC-A-610C CH
序号 项目 垂 直 径 向 引 脚 元 件 定 位
波峰焊焊接质量检查标准
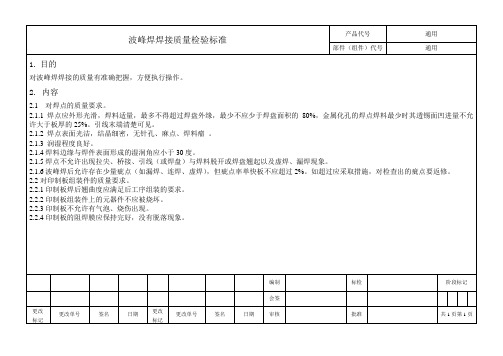
2.2.1印制板焊后翘曲度应满足后工序组装的要求。
2.2.2印制板组装件上的元器件不应被烧坏。
2.2.3印制板不允许有气泡、烧伤出现。
2.2.4印制板的阻焊膜应保持完好,没有脱落现象。
编制
标检
阶段标记
会签
更改
标记
更改单号
签名
日期
更改标记
更改单号
签名
日期
审核
批准
共1页第1页
2.1.2焊点表面光洁,结晶细密,无针孔、麻点、焊料瘤。
.3润湿程度良好。
2.1.4焊料边缘与焊件表面形成的湿润角应小于30度。
2.1.5焊点不允许出现拉尖、桥接、引线(或焊盘)与焊料脱开或焊盘翘起以及虚焊、漏焊现象。
2.1.6波峰焊后允许存在少量疵点(如漏焊、连焊、虚焊),但疵点率单快板不应超过2%。如超过应采取措施,对检查出的疵点要返修。
波峰焊焊接质量检验标准
产品代号
通用
部件(组件)代号
通用
1.目的
对波峰焊焊接的质量有准确把握,方便执行操作。
2.内容
2.1对焊点的质量要求。
2.1.1焊点应外形光滑,焊料适量,最多不得超过焊盘外缘,最少不应少于焊盘面积的80%,金属化孔的焊点焊料最少时其透锡面凹进量不允许大于板厚的25%。引线末端清楚可见。
波峰焊参数设定标准有哪些? 浅谈波峰焊参数设定标准
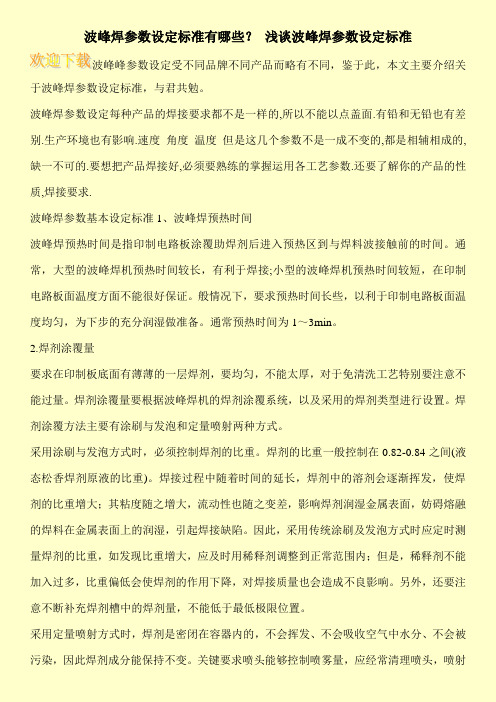
波峰焊参数设定标准有哪些?浅谈波峰焊参数设定标准波峰峰参数设定受不同品牌不同产品而略有不同,鉴于此,本文主要介绍关于波峰焊参数设定标准,与君共勉。
波峰焊参数设定每种产品的焊接要求都不是一样的,所以不能以点盖面.有铅和无铅也有差别.生产环境也有影响.速度角度温度但是这几个参数不是一成不变的,都是相辅相成的,缺一不可的.要想把产品焊接好,必须要熟练的掌握运用各工艺参数.还要了解你的产品的性质,焊接要求.波峰焊参数基本设定标准1、波峰焊预热时间波峰焊预热时间是指印制电路板涂覆助焊剂后进入预热区到与焊料波接触前的时间。
通常,大型的波峰焊机预热时间较长,有利于焊接;小型的波峰焊机预热时间较短,在印制电路板面温度方面不能很好保证。
般情况下,要求预热时间长些,以利于印制电路板面温度均匀,为下步的充分润湿做准备。
通常预热时间为1~3min。
2.焊剂涂覆量要求在印制板底面有薄薄的一层焊剂,要均匀,不能太厚,对于免清洗工艺特别要注意不能过量。
焊剂涂覆量要根据波峰焊机的焊剂涂覆系统,以及采用的焊剂类型进行设置。
焊剂涂覆方法主要有涂刷与发泡和定量喷射两种方式。
采用涂刷与发泡方式时,必须控制焊剂的比重。
焊剂的比重一般控制在0.82-0.84之间(液态松香焊剂原液的比重)。
焊接过程中随着时间的延长,焊剂中的溶剂会逐渐挥发,使焊剂的比重增大;其粘度随之增大,流动性也随之变差,影响焊剂润湿金属表面,妨碍熔融的焊料在金属表面上的润湿,引起焊接缺陷。
因此,采用传统涂刷及发泡方式时应定时测量焊剂的比重,如发现比重增大,应及时用稀释剂调整到正常范围内;但是,稀释剂不能加入过多,比重偏低会使焊剂的作用下降,对焊接质量也会造成不良影响。
另外,还要注意不断补充焊剂槽中的焊剂量,不能低于最低极限位置。
采用定量喷射方式时,焊剂是密闭在容器内的,不会挥发、不会吸收空气中水分、不会被污染,因此焊剂成分能保持不变。
关键要求喷头能够控制喷雾量,应经常清理喷头,喷射。
- 1、下载文档前请自行甄别文档内容的完整性,平台不提供额外的编辑、内容补充、找答案等附加服务。
- 2、"仅部分预览"的文档,不可在线预览部分如存在完整性等问题,可反馈申请退款(可完整预览的文档不适用该条件!)。
- 3、如文档侵犯您的权益,请联系客服反馈,我们会尽快为您处理(人工客服工作时间:9:00-18:30)。
直 元
1.元器件本體到焊盤 1.元器件本體與板面 之間的距離(H)小于 的間隙符合下表; 0.4mm,大于1.5mm.; 2.元器件引腿的傾斜 2.元器件與板面垂直; 度(Θ)滿足最小電氣 3.元器件的總高度不 間隙要求.
元器件超出板面的 間隙(H)大于表格5-1 中所給的最大值.
2
件 超過規定的範圍
向 與焊接區之間有明顯 層可以被安裝到焊 板面部份接觸.
引 的距離
接孔內
脚
元
5
件
湾
月
形
涂
层
有明顯的 距離
不可接受
7
參考標準: IPC-A-610C CH
序号 项目
标准要求/图解
手
目標
插
可接受
缺陷(不接受)
件 1.元器件引腳伸出焊 元器件引腳伸出焊 元器件引腳伸出焊
引 盤長度(L)可依照圖紙 盤的長度要符合表5- 盤的長度不符合表
7
件 出板面安裝的元件,距 離板面最少1.5mm,例
定 如,高散熱器件.
位
9
參考標準: IPC-A-610C CH
序号 项目
标准要求/图解
双列
目標
可接受
缺陷(不接受)
直插 1.所有引腳台肩緊靠 引腳伸出長度符合
焊盤;
要求,元件傾斜不超
/单 2.元器件引腳伸出焊 出元件高度的上限
列直 盤的長度要符合表5-2.
定
位
(續)
4
參考標準: IPC-A-610C CH
序号 项目
标准要求/图解
垂
目標
可接受
缺陷(不接受)
直 1.元器件垂直于板面, 元器件傾斜但仍滿 不滿足最小電氣間
径 底面與板面平行; 足電氣間隙的要求. 隙要求. 2.元器件的底面與板
向 面之間的距離在
3
引 0.3mm~2mm之間.
脚
元
件
定
位
5
參考標準: IPC-A-610C CH
直 元
1.無極性要求元件 的標識從上至下讀 取; 2.極性元件的標識 在元件的頂部.
1.標有極性元件的地線 較長; 2.極性元件的標識不可 見. 3.無極性元件的標識從
極性元件的方向安 裝錯誤.
1件
下向上讀取
定
位
3
參考標準: IPC-A-610C CH
序号 项目
标准要求/图解
垂
目標
可接受
缺陷(不接受)
元件傾斜超出元件 高度的上限,或引腳 伸出長度不符合要 求.
8 插元
件与
插座
定位
10
參考標準: IPC-A-610C CH
序号 项目
元 件 的 成 9形 弯 脚
目標
标准要求/图解
可接受
缺陷(不接受)
安裝在焊孔的元件, 從元件的本體、球 狀連接部分或引腳 焊接部份到器件引 腳折彎處的距離,至 少相當于一個引腳 的直徑或厚度或 0.8mm中的較大者.
但是未暴露出元件 層受到損傷,造成元
表
內部的金屬材質. 件內部的金屬材質 2.元件管腳的密封完 暴露在外,或元件嚴
面
成.
重孌形.
10 损
伤
(续)
13
參考標準: IPC-A-610C CH
序号
11
项目
焊
目標
点 1.焊點表層總體呈 現光滑和與焊接元
接 件有良好潤濕.2.部 件的輪廓容易分
受 辨.3.焊接部件的焊 要 點有順暢連接的邊
個小于或等于90゜的連接角
時能明確表現出浸潤和粘附.
過量除外.
ok ok NG NG
多錫
14
參考標準: IPC-A-610C CH
序号 项目
焊
目標
点
接
受
11 要
求
(续)
标准要求/图解
可接受
缺陷(不接受)
1.焊接面引腳和孔壁潤濕,至 沒錫或少錫
少270゜
2.輔面的焊盤覆蓋最少75%.
15
參考標準: IPC-A-610C CH
波峰焊焊接标准
照明工艺工程 部
2013.7.31
1
电子产品等级划分
1级:通用类电子产品
包括消費類電子產品、部份計算機及其外圍設備,那些對外觀要求不高而
。 以其使用功能为主的产品 2级:专用服务类电子产品
包括通訊設備,復雜商業機器,高性能、長使用壽命要求的儀器。這類產品 需要持久的壽命,但不要求必須保持不間斷工作,外觀上也允許有缺陷。
序号 项目
标准要求/图解
垂
目標
直
可接受
缺陷(不接受)
径 1.限位裝置與元件和 限位裝置與元件和 限位裝置與元件和
向 板面完全接觸;
板面完全接觸.
板面部份接觸.
引 2.引腳恰當彎曲.
脚
元
4
件
安
装
限
位
装
置
6
參考標準: IPC-A-610C CH
序号 项目
标准要求/图解
垂
目標
直
可接受
缺陷(不接受)
径 元器件的彎月形涂層 元器件的半月形涂 限位裝置與元件和
序号 项目
焊
目標
点
接
受
11 要
求
(续)
标准要求/图解
可接受
缺陷(不接受)
引腳折彎處的焊錫不接觸元 引腳折彎處的焊
1.封裝體上的殘缺 觸及到管腳的密封 處. 2.封裝體上的殘缺 造成封裝內部的管 腳暴露在外. 3.封裝體上的殘缺 導致裂痕使硅片暴 露.
12
參考標準: IPC-A-610C CH
序号 项目
标准要求/图解
元
目標
可接受
缺陷(不接受)
件
元件上沒有任何缺口, 1.元件表面有損傷, 1.元件表面的絕緣
破裂或表面損傷.
元件引腳彎折處距 元件體的距離,小于
引腳的直徑或 0.8mm[0.031英寸] 中的較小者.
11
參考標
元 件 表 面 损 伤
标准要求/图解
目標
可接受
缺陷(不接受)
元件上沒有任何缺口, 破裂或表面損傷.
1.封裝體有殘缺,但 殘缺未觸及引腳的 密封處. 2.封裝體上的殘缺引 起的裂痕未延伸到 引腳的密封處. 3.封裝體上的殘缺不 影響標識的完整性.
緣.4.表層形狀呈凹
求 面狀
标准要求/图解
可接受
缺陷(不接受)
1.由于有些成份的焊錫合金、 表面有球狀或珠
引腳或印刷板貼裝和特殊焊 接過程(例如,厚大的PWB的 慢冷卻)可能導致干枯粗糙、 灰暗、或顆粒狀外觀的焊錫,
粒狀物,表層凸狀, 無順暢連接的邊 緣并多錫.
這此焊接可接受.但必須是
當焊錫與待焊表面,形成一
3级:高性能电子产品
包括持續運行或嚴格按指令運行的設備和產品。這類產品在使用中不能出 現中斷,例如救生設備或飛行控制系統。符合該級別要求的組件產品適用 于高保證要求,高服務要求,或者最終產品使用環境條件異常苛刻。
2
參考標準: IPC-A-610C CH
序号 项目
标准要求/图解
垂
目標
可接受
缺陷(不接受)
脚 的要求而定.
2
5-2
末
露
6
出
要
求
8
參考標準: IPC-A-610C CH
序号 项目
标准要求/图解
水
目標
可接受
缺陷(不接受)
平 1.元器件與PCB平行, 元件體與電路板之 距離板面大于 元件本體與PCB板完 間的最大距離(D)大 1.5mm(浮高)
元 全接觸;
于0.7mm[0.028英
2.由于設計需要而高 寸]