涂层技术的发展及应用
纳米涂层行业报告
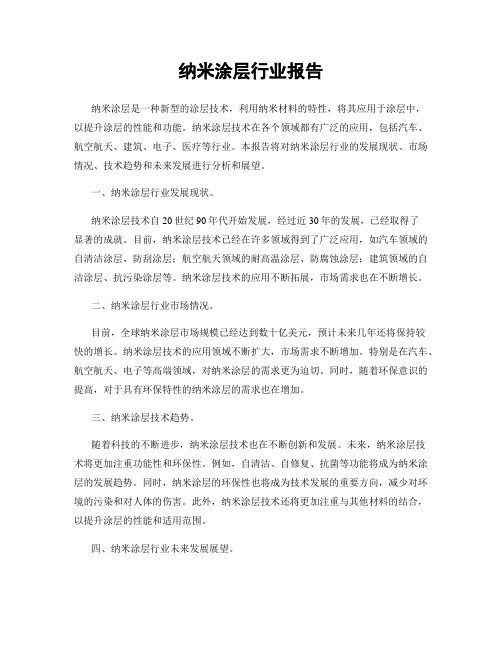
纳米涂层行业报告纳米涂层是一种新型的涂层技术,利用纳米材料的特性,将其应用于涂层中,以提升涂层的性能和功能。
纳米涂层技术在各个领域都有广泛的应用,包括汽车、航空航天、建筑、电子、医疗等行业。
本报告将对纳米涂层行业的发展现状、市场情况、技术趋势和未来发展进行分析和展望。
一、纳米涂层行业发展现状。
纳米涂层技术自20世纪90年代开始发展,经过近30年的发展,已经取得了显著的成就。
目前,纳米涂层技术已经在许多领域得到了广泛应用,如汽车领域的自清洁涂层、防刮涂层;航空航天领域的耐高温涂层、防腐蚀涂层;建筑领域的自洁涂层、抗污染涂层等。
纳米涂层技术的应用不断拓展,市场需求也在不断增长。
二、纳米涂层行业市场情况。
目前,全球纳米涂层市场规模已经达到数十亿美元,预计未来几年还将保持较快的增长。
纳米涂层技术的应用领域不断扩大,市场需求不断增加。
特别是在汽车、航空航天、电子等高端领域,对纳米涂层的需求更为迫切。
同时,随着环保意识的提高,对于具有环保特性的纳米涂层的需求也在增加。
三、纳米涂层技术趋势。
随着科技的不断进步,纳米涂层技术也在不断创新和发展。
未来,纳米涂层技术将更加注重功能性和环保性。
例如,自清洁、自修复、抗菌等功能将成为纳米涂层的发展趋势。
同时,纳米涂层的环保性也将成为技术发展的重要方向,减少对环境的污染和对人体的伤害。
此外,纳米涂层技术还将更加注重与其他材料的结合,以提升涂层的性能和适用范围。
四、纳米涂层行业未来发展展望。
纳米涂层技术作为一种新型的涂层技术,具有广阔的发展前景。
随着科技的不断进步和市场需求的不断增加,纳米涂层行业将迎来更大的发展机遇。
未来,纳米涂层技术将在汽车、航空航天、电子、医疗等领域得到更广泛的应用,为这些行业带来更多的创新和发展机会。
同时,纳米涂层技术还将在环保领域发挥更大的作用,为人类的可持续发展做出更大的贡献。
总之,纳米涂层行业作为一种新兴的涂层技术,具有广阔的发展前景。
随着科技的不断进步和市场需求的不断增加,纳米涂层技术将在各个领域得到更广泛的应用,为社会的发展和进步带来更多的机遇和挑战。
涂层技术的发展及应用

涂层技术的发展及应用涂层技术是一种在基材表面形成一层覆盖物的制造技术。
随着科学技术的不断进步,涂层技术的发展和应用也得到了长足的进展。
下面将从涂层技术的发展趋势、应用领域和未来发展方向三个方面进行讨论。
1.薄膜涂层技术:随着纳米科技的发展,薄膜涂层技术得到了广泛应用。
薄膜涂层技术可以使基材表面具有一定的功能,如防腐、防刮擦、抗氧化等,同时还可以对基材进行改性,提高其力学性能和化学稳定性。
2.多功能涂层技术:涂层技术的发展逐渐由单一功能向多功能方向发展,如具有防水、防污、防紫外线和抗菌等多种功能于一体的复合涂层。
多功能涂层技术可以满足人们对材料性能的多样化和个性化需求。
3.环保涂层技术:随着环保意识的提高,涂层技术的环保性也受到了广泛关注。
传统的有机溶剂型涂料中含有有机溶剂,对环境和人体健康有害。
因此,发展环保涂层技术成为当前的趋势之一,如水性涂料、无溶剂涂料等,这些涂料对环境污染少,能够降低有机溶剂的排放。
1.汽车工业:涂层技术在汽车制造中扮演着重要角色。
汽车的外观涂层能够提供防腐、抗刮擦、美观等功能,同时还可以改善车辆的燃油效率。
另外,涂层技术在汽车零部件的制造中也有广泛应用。
2.建筑工业:涂层技术在建筑工业中主要应用于墙面、天花板、地板等室内外装饰材料的涂装。
这些涂料可以提高建筑物的耐候性、耐火性和美观度。
3.电子工业:涂层技术在电子工业中用于保护电子元器件和电路板。
电子元器件的涂层可以提高其防潮、防腐、绝缘和散热性能。
4.能源工业:涂层技术在能源工业中应用广泛,如太阳能电池板涂层、涂层燃料电池、涂层光伏薄膜等。
5.医疗工业:涂层技术在医疗器械、假体等医疗领域也有重要应用,如具有抗菌、生物相容性和生物降解性的医用涂层。
未来涂层技术的发展方向主要包括以下几个方面:1.纳米涂层技术:由于纳米颗粒的特殊性质,纳米涂层技术在涂层领域具有广阔的应用前景。
未来纳米涂层技术将得到更广泛的研究和应用。
2.智能涂层技术:随着智能材料的发展,涂层也将发展成为具有智能功能的材料。
PVD涂层技术的发展与

PVD涂层技术在其他领域的应用案例
要点一
总结词
要点二
详细描述
拓宽应用领域、满足多样化需求
除了上述领域,PVD涂层技术还广泛应用于其他领域,如 珠宝首饰、光学仪器、医疗器械等。在珠宝首饰领域, PVD涂层可以用于制造各种彩色宝石和金属饰品的外观效 果;在光学仪器领域,PVD涂层可以提高镜片的抗反射性 能和耐磨损性能;在医疗器械领域,PVD涂层可以用于制 造人工关节、牙科材料等医疗器械,提高其耐磨性和生物 相容性。
航天器涂层
PVD涂层技术可以为航天器提供良 好的耐高温、抗氧化和耐辐射等性 能,保证航天器的长期稳定运行。
电子工业领域的应用
磁头涂层
PVD涂层技术可以为磁头提供耐磨、耐腐蚀和抗氧化等性能,提 高磁头的稳定性和寿命。
太阳能电池涂层
PVD涂层技术可以为太阳能电池提供高反射性和高耐候性等性能, 提高太阳能电池的光电转换效率和长期稳定性。
在制备硬质涂层、耐磨涂层等领域应 用广泛。
溅射镀膜
广泛应用于制备陶瓷、金属复合涂层 等。
PVD涂层技术的选择
根据应用需求选择
不同的PVD涂层技术适用于不同 的应用领域,需要根据具体需求 进行选择。
根据材料性质选择
不同材料的物理和化学性质不同, 需要选择合适的PVD涂层技术以 获得最佳的涂层效果。
根据工艺参数选择
PVD涂层技术的发展 与应用
目 录
• PVD涂层技术的概述 • PVD涂层技术的种类 • PVD涂层技术的应用领域 • PVD涂层技术的发展趋势与挑战 • PVD涂层技术的应用案例
01
PVD涂层技术的概述
PVD涂层技术的定义
01
PVD涂层技术是指通过物理气相 沉积的方法,将金属或非金属材 料涂覆在基体表面,形成一层具 有特殊性能的涂层的技术。
涂层技术在钢铁制造中的应用
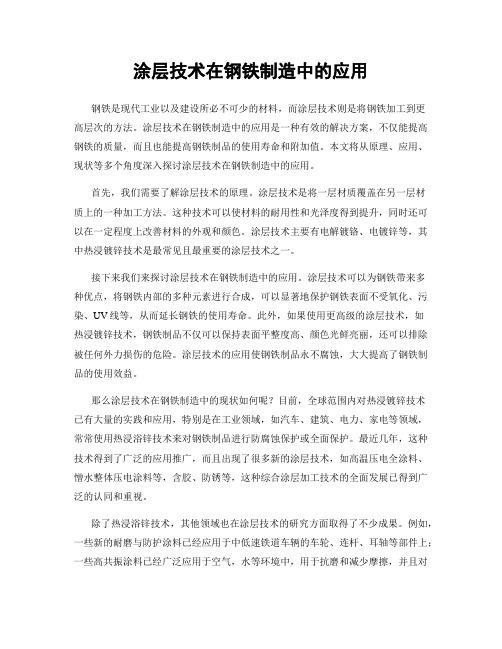
涂层技术在钢铁制造中的应用钢铁是现代工业以及建设所必不可少的材料,而涂层技术则是将钢铁加工到更高层次的方法。
涂层技术在钢铁制造中的应用是一种有效的解决方案,不仅能提高钢铁的质量,而且也能提高钢铁制品的使用寿命和附加值。
本文将从原理、应用、现状等多个角度深入探讨涂层技术在钢铁制造中的应用。
首先,我们需要了解涂层技术的原理。
涂层技术是将一层材质覆盖在另一层材质上的一种加工方法。
这种技术可以使材料的耐用性和光泽度得到提升,同时还可以在一定程度上改善材料的外观和颜色。
涂层技术主要有电解镀铬、电镀锌等,其中热浸镀锌技术是最常见且最重要的涂层技术之一。
接下来我们来探讨涂层技术在钢铁制造中的应用。
涂层技术可以为钢铁带来多种优点,将钢铁内部的多种元素进行合成,可以显著地保护钢铁表面不受氧化、污染、UV线等,从而延长钢铁的使用寿命。
此外,如果使用更高级的涂层技术,如热浸镀锌技术,钢铁制品不仅可以保持表面平整度高、颜色光鲜亮丽,还可以排除被任何外力损伤的危险。
涂层技术的应用使钢铁制品永不腐蚀,大大提高了钢铁制品的使用效益。
那么涂层技术在钢铁制造中的现状如何呢?目前,全球范围内对热浸镀锌技术已有大量的实践和应用,特别是在工业领域,如汽车、建筑、电力、家电等领域,常常使用热浸浴锌技术来对钢铁制品进行防腐蚀保护或全面保护。
最近几年,这种技术得到了广泛的应用推广,而且出现了很多新的涂层技术,如高温压电全涂料、憎水整体压电涂料等,含胶、防锈等,这种综合涂层加工技术的全面发展已得到广泛的认同和重视。
除了热浸浴锌技术,其他领域也在涂层技术的研究方面取得了不少成果。
例如,一些新的耐磨与防护涂料已经应用于中低速铁道车辆的车轮、连杆、耳轴等部件上;一些高共振涂料已经广泛应用于空气,水等环境中,用于抗磨和减少摩擦,并且对各种各样的机器和设备都适用。
所有这些新的涂层技术已经成为了钢铁制品行业的一个重要细分市场。
在钢铁行业中,涂层技术不仅被广泛应用,而且发展势头良好。
纳米涂层的市场前景与应用研究

纳米涂层的市场前景与应用研究在当今科技飞速发展的时代,纳米技术作为一项具有革命性的创新领域,正不断地为各个行业带来全新的机遇和变革。
其中,纳米涂层以其独特的性能和广泛的应用前景,逐渐成为了市场关注的焦点。
纳米涂层,顾名思义,是将涂层材料以纳米尺度进行处理和应用,从而赋予涂层前所未有的性能和功能。
与传统涂层相比,纳米涂层具有更优异的耐磨、耐腐蚀、防水、防污、抗菌等特性,这使得它在众多领域展现出了巨大的应用潜力。
从市场前景来看,纳米涂层的发展呈现出一片繁荣的景象。
随着制造业的不断升级和对产品质量要求的日益提高,对于具有高性能保护涂层的需求持续增长。
例如,在汽车工业中,纳米涂层可以用于提高汽车零部件的耐磨和耐腐蚀性能,延长使用寿命,减少维修成本。
在电子行业,纳米涂层能够增强电子产品的防水和防尘能力,提高产品的可靠性和稳定性。
此外,航空航天、医疗器械、能源等领域对纳米涂层的需求也在不断扩大。
据市场研究机构预测,未来几年纳米涂层市场将保持较高的增长率。
这主要得益于技术的不断进步、成本的逐渐降低以及市场对高性能涂层的持续需求。
同时,政府对环保和可持续发展的重视也为纳米涂层的发展提供了政策支持。
例如,一些国家出台了严格的环保法规,要求企业减少污染物排放,而纳米涂层在某些情况下可以替代传统的化学处理方法,减少对环境的污染。
在应用方面,纳米涂层已经取得了众多令人瞩目的成果。
在建筑领域,纳米涂层可以应用于玻璃表面,使其具有自清洁功能。
这种自清洁玻璃能够利用阳光中的紫外线分解表面的污垢,雨水一冲即可保持干净,大大降低了建筑物的清洁成本。
同时,纳米涂层还可以用于提高建筑材料的防水和抗风化性能,延长建筑物的使用寿命。
在纺织行业,纳米涂层可以赋予纺织品防水、防油、防污和抗菌等功能。
例如,户外运动服装经过纳米涂层处理后,可以在恶劣的天气条件下保持干爽和清洁,同时具有抗菌性能,减少异味和皮肤感染的风险。
在能源领域,太阳能电池板表面的纳米涂层可以提高其光吸收效率,从而增加发电量。
纳米涂层技术的研究及应用

纳米涂层技术的研究及应用在当今的现代社会,纳米科技是一个备受瞩目的领域,它涵盖了物理学、化学、材料科学、生物学等多个学科,广泛应用于生物、环境、电子、通讯、医疗等诸多领域。
而纳米涂层技术作为纳米科技的重要分支,不仅在产品的性能和质量上有了突破性的进展,也为未来的科技发展带来了无限可能。
一、纳米涂层技术的定义及分类纳米涂层技术是指以纳米粒子为原料,通过化学、物理方法在表面形成一层薄膜的技术。
它不仅能在产品表面形成密闭的防护层,而且能保持好的光滑度、透明度、导电性和导热性等。
根据涂层的材料和用途等方面的不同,纳米涂层技术可以分为以下几类:1. 金属纳米涂层技术金属纳米涂层技术是指将金属纳米粒子应用于涂层中,形成具有金属纳米结构的表面修饰技术。
这种技术可以制造出很多新材料,如金属黏着剂、导电、光学薄膜以及各种材料的防腐蚀层等。
2. 无机纳米涂层技术无机纳米涂层技术是指以无机纳米粒子为主要原料,通过特殊工艺加工成涂料,赋予其他材料附加的特性的技术。
在防火、耐磨、防腐、防污等诸多方面得到了广泛的应用。
3. 有机纳米涂层技术有机纳米涂层技术是指以有机材料的纳米粒子为主要原料,制备出一种紧密而完整的有机薄膜的技术。
这种技术可以制备出各种具有高防护性、高透明度、耐酸碱、遮光、耐水的薄膜,如塑料、橡胶、纸张等各种材料的防护层。
二、纳米涂层技术应用领域1. 汽车制造业在汽车制造业中应用纳米涂层技术能够加强汽车表面的硬度、降低密度、增强耐蚀性,提高涂层的附着力和粘合力。
同时,在减少外观漆膜厚度的情况下,能够提升光泽度、降低摩擦损失、提高车身质量,从而提高了汽车的耐用性和市场竞争力。
2. 电子工业在电子制造领域,纳米涂层技术可以应用于电子元器件、液晶显示器及其他电器制造领域中,使电子产品具有防水、防油污、防磨损、防氧化等特性,同时也可以降低产品能量消耗、提高机械精度及可靠性等方面的指标。
3. 航空航天领域在航空航天领域,纳米涂层技术是一项极其重要的技术,可以有效地提高飞机表面的耐腐蚀、耐磨损性能,从而可以减少飞行过程中的机械损耗,增强机体的防腐能力和强度,为飞机的空气动力性能和机体气动设计做出了重要贡献。
涂层加工技术的发展与应用

涂层加工技术的发展与应用近年来,随着科学技术的不断进步,涂层加工技术的发展也日益成熟。
涂层加工技术是指在材料表面形成一层保护膜,以改变其特性、提高抗腐蚀性、耐磨性、耐热性等性能的一种处理方式。
涂层加工技术具有广泛的应用领域,如汽车、航空航天、建筑、电子、能源等行业都离不开涂层加工技术的应用。
一、涂层加工技术的发展历程早在古代,人们就开始采用一些简单的方法来保护金属器物,例如用蜡质涂层、镀金、镀银等方法。
但是这些方法都有其局限性,效果有限。
直到20世纪60年代,涂层加工技术才开始真正的起步。
此时,德国研究人员发明了一种新型的涂层加工技术——热喷涂技术,得到了广泛的应用。
二、不同类型的涂层加工技术1、化学镀工艺化学镀是指将金属阳极溶解于电解液中,在阴极表面上沉积出金属离子的一种电化学过程。
化学镀工艺不要求零件的形状结构,可以镀扁、弯、曲、细、小的空洞和板材加工件等,所以使用广泛,特别适用于微型和精密器件。
2、电镀工艺电镀是指将一种金属或合金沉积在另一种金属或合金表面的一种化学反应,即在电解质溶液中,用作阴极的物体上,有一层均匀的、粘附的金属层沉积下来,形成具有一定厚度的覆盖层。
电镀处理可以提高材料的表面光洁度、硬度和耐磨性。
3、热喷涂工艺热喷涂工艺是指将一些合金材料、陶瓷材料等通过高速喷出来的射流,在零件表面上形成涂层,从而起到保护和改善材料性能的作用。
热喷涂工艺具有涂层厚度可控、形状规则、工艺简单等优点,被广泛应用于航空航天、能源、化工等领域。
4、物化镀工艺物化镀是指将陶瓷、高分子、金属等材料通过物理或化学方法,使其形成独立的涂层。
物化镀工艺可以提高材料的抗磨损、耐蚀和耐高温性能,因此在锅炉、热交换器、配电装置等设备上使用广泛。
三、涂层加工技术的应用领域涂层加工技术的应用已经涉及了多个领域,如汽车、建筑、电子、能源等。
1、汽车汽车是涂层加工技术应用最广泛的领域之一。
目前汽车零部件大多采用镀铬、喷涂等涂层技术,可以起到强化与美化的作用。
纳米级涂层技术的优势与应用场景
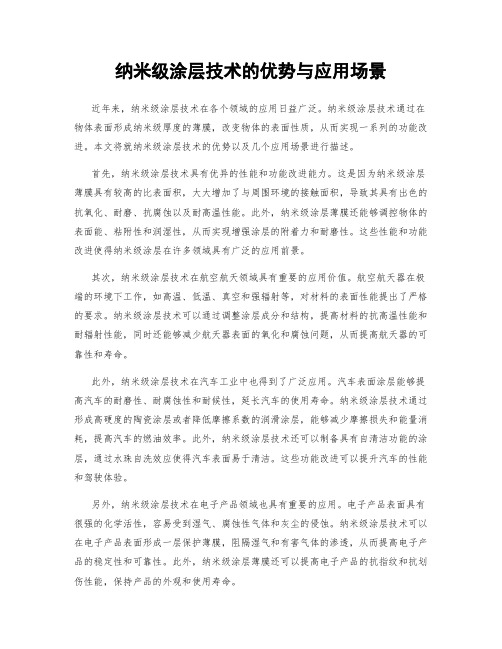
纳米级涂层技术的优势与应用场景近年来,纳米级涂层技术在各个领域的应用日益广泛。
纳米级涂层技术通过在物体表面形成纳米级厚度的薄膜,改变物体的表面性质,从而实现一系列的功能改进。
本文将就纳米级涂层技术的优势以及几个应用场景进行描述。
首先,纳米级涂层技术具有优异的性能和功能改进能力。
这是因为纳米级涂层薄膜具有较高的比表面积,大大增加了与周围环境的接触面积,导致其具有出色的抗氧化、耐磨、抗腐蚀以及耐高温性能。
此外,纳米级涂层薄膜还能够调控物体的表面能、粘附性和润湿性,从而实现增强涂层的附着力和耐磨性。
这些性能和功能改进使得纳米级涂层在许多领域具有广泛的应用前景。
其次,纳米级涂层技术在航空航天领域具有重要的应用价值。
航空航天器在极端的环境下工作,如高温、低温、真空和强辐射等,对材料的表面性能提出了严格的要求。
纳米级涂层技术可以通过调整涂层成分和结构,提高材料的抗高温性能和耐辐射性能,同时还能够减少航天器表面的氧化和腐蚀问题,从而提高航天器的可靠性和寿命。
此外,纳米级涂层技术在汽车工业中也得到了广泛应用。
汽车表面涂层能够提高汽车的耐磨性、耐腐蚀性和耐候性,延长汽车的使用寿命。
纳米级涂层技术通过形成高硬度的陶瓷涂层或者降低摩擦系数的润滑涂层,能够减少摩擦损失和能量消耗,提高汽车的燃油效率。
此外,纳米级涂层技术还可以制备具有自清洁功能的涂层,通过水珠自洗效应使得汽车表面易于清洁。
这些功能改进可以提升汽车的性能和驾驶体验。
另外,纳米级涂层技术在电子产品领域也具有重要的应用。
电子产品表面具有很强的化学活性,容易受到湿气、腐蚀性气体和灰尘的侵蚀。
纳米级涂层技术可以在电子产品表面形成一层保护薄膜,阻隔湿气和有害气体的渗透,从而提高电子产品的稳定性和可靠性。
此外,纳米级涂层薄膜还可以提高电子产品的抗指纹和抗划伤性能,保持产品的外观和使用寿命。
最后,纳米级涂层技术在医疗领域也有广泛的应用。
医疗器械表面容易受到细菌和病原微生物的侵袭,导致交叉感染的风险增加。
功能化陶瓷涂层在机械工程中的应用及发展趋势

功能化陶瓷涂层在机械工程中的应用及发展趋势引言:随着科技的不断发展,机械工程领域对材料的要求也越来越高。
纳米材料的应用为机械工程带来了巨大的创新和发展机会。
功能化陶瓷涂层作为一种纳米材料的应用,不仅在表面硬度和耐磨性方面具有优势,还可以提供更多功能性特征。
本文将介绍功能化陶瓷涂层在机械工程中的应用,并探讨其发展趋势。
一、功能化陶瓷涂层的概述功能化陶瓷涂层是一种在金属表面上制备的陶瓷涂层,其主要成分为陶瓷颗粒和粉末。
功能化陶瓷涂层在机械工程中具有优异的性能,如高硬度、耐磨性、耐高温等。
它们可以应用于各种机械零件和工具,增加其使用寿命和性能。
二、功能化陶瓷涂层在机械工程中的应用1.增强材料的硬度和耐磨性:功能化陶瓷涂层可以在金属表面形成一层陶瓷涂层,提高材料的硬度和耐磨性。
这使得机械零件在摩擦和磨损环境下更加耐用,并减少维护和更换成本。
2.降低摩擦系数和磨损:功能化陶瓷涂层可以减少金属之间的摩擦系数,降低能量损耗,并延长机械零件的使用寿命。
在高速运动部件和复杂传动系统中的应用,功能化陶瓷涂层也能够有效减少磨损。
3.提供热稳定性和耐蚀性:功能化陶瓷涂层具有良好的热稳定性和耐蚀性,因此可以在高温和腐蚀环境中得到应用。
例如,在航空航天领域中,功能化陶瓷涂层能够提供绝缘和耐热功能,保护机械零件免受腐蚀和高温破坏。
4.提高材料的粘附性和质量:功能化陶瓷涂层能够在金属表面形成致密的结构,提高涂层与基材的粘附性。
这将增加机械零件的质量和可靠性,并提高工作效能。
三、功能化陶瓷涂层的发展趋势1.多功能化陶瓷涂层的研发:随着技术的不断进步,未来的功能化陶瓷涂层将不仅仅具备硬度和耐磨性等基本特性,还能提供更多的功能性特征。
例如,目前研究人员正在探索具有自润滑、自修复和智能感应功能等多功能化陶瓷涂层的应用。
2.纳米技术的应用:纳米技术对功能化陶瓷涂层的应用具有巨大的潜力。
通过精确控制纳米颗粒的尺寸和组成,可以改变涂层的性能和功能特征。
金属表面涂层技术的发展与应用

金属表面涂层技术的发展与应用随着科学技术的不断发展和社会经济的快速发展,各种先进材料和技术被广泛应用于各行各业。
其中,金属表面涂层技术是一种十分重要的表面处理技术,被广泛应用于机械工程、航空航天、汽车工业、建筑装饰等领域。
本文将从金属表面涂层技术的发展历程、分类及应用等方面进行分析和阐述。
一、金属表面涂层技术的发展历程金属表面涂层技术在我国起步较晚,大多数金属制品在生产时无法满足使用要求,而抛光、电镀、喷涂、热处理等表面处理技术能有效提高金属制品的抗腐蚀性、耐磨性和美观度。
随着应用范围的不断扩大,研究人员逐渐深入研究表面处理技术的应用,除了简单表面处理外,还能在表面形貌或结构方面进行改造。
自20世纪80年代以来,表面工艺的发展日益突出,在表面改性领域开发出了一种新的技术——金属表面技术,其主要是通过一系列表面处理工艺来改变金属表面结构和化学组成,从而提高金属表面的性能。
下面是金属表面涂层技术的发展历程:1. 人工电镀技术人工电镀技术是最早应用的表面涂层技术之一,其主要特点是在金属表面上电沉积一层金属外覆层,利用外层金属材料的优异性能来提高金属表面的耐腐蚀性、硬度和抗磨损性。
但是这种方法存在较为严重的环境污染问题。
2. 物理气相沉积技术物理气相沉积技术是一种通过在真空下加热和放电的方式沉积金属薄膜的方法,可以在金属表面形成具有特殊性能的薄膜。
该技术逐渐得到了广泛应用,包括熔蒸沉积、离子镀、快速淀积、溅射沉积等方法,可以用于制备氧化铝、氮化硅、碳化硅等种类的薄膜。
3. 化学镀方法化学镀方法是一种在无电源条件下在基底上沉积自由金属的一种表面处理技术。
其原理是将氧化金属还原成自由金属,然后在其表面沉积一层金属薄膜。
该技术具有很好的附着力和均匀性,可以用于制备气敏元件、火花塞、电感等。
4. 电弧离子镀技术电弧离子镀技术是一种应用较广泛的表面精加工工艺,主要是通过在真空环境下加热金属,使其被蒸发,然后离子化,用高能电子对加速离子进行强制沉积,形成稳定的固体涂层。
金属材料表面涂层的研究与应用

金属材料表面涂层的研究与应用引言金属材料表面涂层的研究与应用一直是材料科学领域的热门研究方向之一。
金属材料的表面涂层可以改善材料的性能和使用寿命,并扩展其应用领域。
本文将从涂层种类、涂层制备技术以及涂层的应用范围等方面进行探讨。
一、涂层种类1. 金属薄膜涂层金属薄膜涂层是一种常见的涂层种类,它可以通过物理气相沉积(PVD)或化学气相沉积(CVD)等方法制备。
金属薄膜涂层可以提高材料的耐腐蚀性、硬度和耐磨性,广泛应用于工具、汽车零部件和电子设备等领域。
2. 陶瓷涂层陶瓷涂层是一种常用的高温涂层,它可以提供良好的耐高温和耐腐蚀性能。
常见的陶瓷涂层材料包括氧化铝、氧化锆和碳化硅等。
陶瓷涂层广泛应用于航空航天、燃气涡轮和热能转换等领域。
3. 有机涂层有机涂层是一种以有机化合物为基础的涂层种类,它可以提供良好的耐腐蚀性和装饰性能。
有机涂层通常通过涂覆、浸渍或喷涂等方法施工在金属表面。
有机涂层广泛应用于建筑、汽车和电子产品等领域。
二、涂层制备技术1. 物理气相沉积(PVD)物理气相沉积是一种通过蒸发或溅射等方法在金属表面形成涂层的技术。
常见的PVD技术包括磁控溅射、电子束蒸发和激光蒸发等。
PVD制备的涂层具有高纯度、致密性好和粘附性强的特点。
2. 化学气相沉积(CVD)化学气相沉积是一种通过化学反应在金属表面形成涂层的技术。
常见的CVD技术包括低压CVD和热CVD等。
CVD制备的涂层可以控制成分和结构,具有良好的化学稳定性和高温稳定性。
3. 溶液法涂层溶液法涂层是一种通过将溶液中的活性物质浸渍到金属表面形成涂层的技术。
常见的溶液法涂层包括热浸渍、阳极氧化和化学镀等。
溶液法涂层具有制备成本低、适用范围广的优点。
三、涂层的应用范围1. 耐磨涂层耐磨涂层是一种常见的应用涂层,它可以提高金属材料的耐磨性能。
耐磨涂层广泛应用于工具、模具和机械零件等领域。
常见的耐磨涂层材料包括碳化钨、碳化钛和氮化硅等。
2. 防腐蚀涂层防腐蚀涂层是一种用于保护金属材料免受腐蚀的涂层。
国外金属涂层领域的的发展现状

国外金属涂层领域的的发展现状
国外金属涂层领域目前处于快速发展阶段,主要体现在以下几
个方面:
1. 技术创新,国外金属涂层领域不断推出新的技术和材料,如
纳米涂层、多功能涂层、环保涂层等。
这些新技术和新材料的应用
使得金属涂层的性能得到了显著提升,包括耐腐蚀性、耐磨性、导
热性等方面。
2. 应用领域拓展,金属涂层的应用领域逐渐拓展到航空航天、
汽车制造、建筑等多个领域。
例如,在航空航天领域,金属涂层可
以提高飞机零部件的耐腐蚀性能,延长使用寿命;在汽车制造领域,金属涂层可以提高汽车外表面的耐磨性和耐腐蚀性。
3. 环保要求,国外对金属涂层的环保要求日益严格,推动了金
属涂层技术的升级和转型。
例如,水性涂料、粉末涂料等环保型金
属涂层得到了广泛应用,以满足环保标准。
4. 自动化生产,国外金属涂层领域在生产工艺上不断引入自动化、智能化技术,提高生产效率和产品质量,并且降低生产成本。
5. 国际合作,国外金属涂层领域的企业和研究机构之间开展了
广泛的国际合作,促进了技术交流和创新。
总的来说,国外金属涂层领域正处于技术不断创新、应用领域
不断拓展、环保要求不断提高的发展阶段,展现出蓬勃的发展态势。
材料表面涂层技术的研究与应用

材料表面涂层技术的研究与应用近年来,随着科技的不断发展,材料科学领域也取得了巨大的突破。
材料表面涂层技术作为其中的一项重要技术,广泛应用于各个领域。
本文将探讨材料表面涂层技术的研究与应用,从理论到实践,从材料的特性到涂层的功能,全面展示这一领域的进展。
首先,我们来了解一下材料表面涂层技术的定义和原理。
材料表面涂层技术是通过在材料表面形成一层薄膜,改变其表面性质和功能的一种方法。
这种薄膜可以是金属、陶瓷、聚合物等材料,通过不同的制备方法,如物理气相沉积、化学气相沉积、溶液法等,将薄膜均匀地涂覆在材料表面上。
涂层的形成可以改善材料的机械性能、耐腐蚀性能、导热性能等,提高材料的使用寿命和性能。
其次,我们来看一下材料表面涂层技术的研究方向和应用领域。
在研究方向方面,材料表面涂层技术主要集中在涂层的制备方法、涂层的结构与性能之间的关系以及涂层的应用等方面。
研究者们通过改变制备方法、调控涂层的成分和结构,以及对涂层进行性能测试和表征,不断探索涂层的优化方法和应用领域。
在应用领域方面,材料表面涂层技术已经广泛应用于各个行业。
例如,在汽车工业中,涂层技术可以提高汽车外观的美观度和耐久性,增加车身的抗腐蚀性能;在航空航天领域,涂层技术可以改善飞机零部件的耐高温性能和抗磨损性能;在电子领域,涂层技术可以提高电子元器件的导电性能和抗氧化性能;在建筑领域,涂层技术可以增加建筑材料的耐候性和防水性能。
可以说,材料表面涂层技术在各个领域都起到了至关重要的作用。
此外,材料表面涂层技术的研究还涉及到环境保护和可持续发展。
随着人们对环境问题的重视,绿色涂层技术逐渐兴起。
绿色涂层技术是指无毒、无害、无污染的涂层技术,它可以降低涂层制备过程中的能源消耗和废物排放,减少对环境的影响。
研究者们通过改进制备方法、开发新型材料,致力于推动绿色涂层技术的发展,为环境保护做出贡献。
最后,我们来总结一下材料表面涂层技术的前景和挑战。
随着科技的不断进步和需求的不断增加,材料表面涂层技术将会有更广阔的应用前景。
纳米涂层的市场前景与应用研究探讨

纳米涂层的市场前景与应用研究探讨在当今科技飞速发展的时代,纳米技术已经成为众多领域的研究热点,纳米涂层作为其中的一个重要分支,正逐渐展现出其巨大的市场潜力和广泛的应用前景。
纳米涂层,顾名思义,是指通过特殊的工艺在物体表面形成一层厚度在纳米级别的涂层。
这看似微不足道的一层薄膜,却蕴含着强大的功能和性能优势。
从市场前景来看,纳米涂层行业正处于快速发展的阶段。
随着人们对产品性能和质量要求的不断提高,纳米涂层在多个领域的需求持续增长。
例如,在电子行业,纳米涂层可以提高电子设备的防水、防尘和防腐蚀性能,延长设备的使用寿命。
在汽车工业中,纳米涂层能够增强汽车零部件的耐磨、耐腐蚀和抗划伤能力,提升汽车的整体性能和外观质量。
此外,在家居用品、医疗器械、航空航天等领域,纳米涂层也有着广阔的应用空间。
纳米涂层之所以能够在市场上受到青睐,主要得益于其独特的性能优势。
首先,纳米涂层具有优异的耐磨性。
它能够在物体表面形成一层坚硬的保护膜,有效抵抗外界的摩擦和磨损,使物体表面长时间保持光滑和完好。
其次,纳米涂层具备出色的耐腐蚀性能。
无论是面对酸、碱还是其他化学物质的侵蚀,纳米涂层都能为物体提供可靠的防护,大大延长物体的使用寿命。
再者,纳米涂层还具有良好的防水、防油和防尘性能。
这使得经过纳米涂层处理的物品易于清洁和维护,保持良好的工作状态。
在应用方面,纳米涂层已经取得了显著的成果。
在电子设备领域,智能手机、平板电脑等电子产品的屏幕和外壳常常采用纳米涂层技术,以提高其抗指纹和抗划伤能力。
同时,纳米涂层还可以使电子设备具备更好的防水性能,让用户在使用过程中更加放心。
在汽车行业,发动机部件、轮毂、车身等部位都可以应用纳米涂层,不仅能够提高汽车的外观美观度,还能增强其机械性能和耐久性。
在家居用品方面,纳米涂层可以用于厨房电器、家具表面等,使其更易于清洁和保养。
然而,纳米涂层的发展也并非一帆风顺。
目前,纳米涂层技术仍面临一些挑战。
一方面,纳米涂层的制备成本相对较高,这在一定程度上限制了其大规模的应用。
保护涂层的现状及未来五至十年发展前景

保护涂层的现状及未来五至十年发展前景保护涂层是一种应用广泛的材料,用于保护物体表面免受外界环境的影响和损害。
随着科技的不断发展和人们对物体保护需求的增强,保护涂层行业也在不断壮大和创新。
本文将介绍保护涂层的现状,并展望未来五至十年的发展前景。
目前,保护涂层已经广泛应用于各个领域,包括建筑、汽车、航空航天、电子、能源等。
它们能够有效地保护物体表面免受腐蚀、氧化、磨损、紫外线辐射等因素的影响,延长物体的使用寿命,降低维护成本。
目前市场上流行的保护涂层种类繁多,如防水涂料、防腐蚀涂层、防撞涂层等,这些涂层通过不同的材料组成和制造工艺,具备了各自独特的防护功能。
然而,传统的保护涂层仍然存在一些不足之处。
首先,它们的防护效果难以长久保持,需要定期维护和重新涂覆。
其次,一些保护涂层的制造过程对环境造成一定的污染。
此外,如何在保护物体的同时保持其原本的外观和质感也是一个挑战。
因此,保护涂层行业需要不断进行创新和改进,以满足不断变化的市场需求。
未来五至十年,保护涂层行业将面临许多机遇和挑战。
首先,随着环保意识的增强,市场对环境友好型保护涂层的需求将不断增加。
这种涂层应具备低污染性、易降解性和可再生性等特点,以减少对自然环境的负面影响。
其次,随着智能科技的快速发展,保护涂层也将与智能化技术相结合。
例如,将传感器嵌入涂层中,实现对物体表面状况的实时监测和反馈,以及对涂层防护性能进行智能调控。
这将大大提高保护涂层的使用效果和可靠性。
另外,纳米科技的应用将给保护涂层带来新的突破。
纳米材料的引入可以使得涂层具备更高的硬度、更好的耐磨损性和耐高温性能。
同时,纳米涂层还具备自清洁、抗菌等特性,可以满足人们对物体清洁和卫生的要求。
此外,保护涂层行业还将受益于材料科学、涂料技术和表面工程等领域的进一步发展。
新材料和新涂层技术的出现将为保护涂层带来更多的选择和应用领域。
综上所述,保护涂层作为一种重要的功能材料,其现状已经相当成熟,但仍有提升空间。
机械零件的表面涂层技术研究与应用

机械零件的表面涂层技术研究与应用一、引言机械零件是现代工业生产中不可或缺的重要组成部分。
为了提升机械零件的耐磨性、耐腐蚀性和抗疲劳性等特性,表面涂层技术应运而生。
本文将探讨机械零件表面涂层技术的研究现状和应用前景。
二、常见涂层技术1. 热喷涂技术热喷涂技术是一种通过高温将粉末或线材熔化并喷射到零件表面形成涂层的技术。
常见的热喷涂技术包括火焰喷涂、电弧喷涂和等离子喷涂等。
热喷涂技术具有成本低、涂层结合力强的优点,被广泛应用于航空航天、汽车制造、能源等领域。
2. 等离子喷涂技术等离子喷涂技术是一种利用高能等离子体将涂层材料离子化并喷射到零件表面的技术。
等离子喷涂技术具有涂层致密性好、粘结力强和成本低廉等优点。
它在航空航天、电子器件、光学设备等领域有着广泛的应用前景。
三、表面涂层技术的研究进展1. 涂层材料研究随着科技的进步,新型的涂层材料不断涌现。
目前,金属、陶瓷和聚合物等材料被广泛用于表面涂层。
例如,碳纳米管涂层具有重量轻、硬度高和导电性优良的特点,被广泛应用于电子设备和航空航天领域。
2. 涂层性能研究涂层性能的研究成为表面涂层技术发展的重要方向。
例如,研究人员通过改变涂层材料和涂层工艺,提高涂层的硬度、耐磨性和耐腐蚀性等性能。
此外,还有学者研究了涂层与基材的结合力和热膨胀系数等性能。
四、表面涂层技术的应用案例1. 汽车制造表面涂层技术在汽车制造领域有着广泛的应用。
通过在发动机零件和底盘等部位进行涂层处理,可以提升汽车的耐磨性和耐腐蚀性,延长零件的使用寿命。
2. 航空航天航空航天领域对零件表面涂层技术的要求更加严苛。
涂层需要具备耐高温、耐氧化和抗磨损等特性。
通过涂层技术,飞机发动机的性能和安全性得到了显著提升。
3. 电子器件随着电子器件的迅猛发展,对表面涂层技术的需求也日益增加。
涂层技术可以提供电子器件的绝缘、导电和防尘等功能,同时提高器件的可靠性和稳定性。
五、面临的挑战和发展方向尽管表面涂层技术在各个领域有着广泛的应用,但仍面临着一些挑战。
刀具涂层技术的应用

刀具涂层技术的应用刀具涂层技术的应用引言:刀具涂层技术是一种在刀具表面附加一层薄膜的技术,以增加刀具的寿命、提高切削性能和减少切削力。
它在制造业中被广泛应用。
本文将深入探讨刀具涂层技术的原理、常见的应用领域以及未来的发展趋势。
一、刀具涂层技术的原理刀具涂层技术的原理是在刀具表面形成一层涂层,这个涂层可以提供刀具的耐磨性、高速切削能力和抗热性能。
常见的涂层材料包括碳化物、氧化物和氮化物。
涂层可以通过物理蒸发沉积、化学气相沉积和物理气相沉积等方法制备。
二、刀具涂层技术的应用领域1. 汽车制造业:在汽车制造业中,刀具涂层技术可以应用于汽车零部件的加工过程中,例如发动机零部件的铣削、钻孔和车削等。
刀具涂层技术可以提高刀具的寿命,减少生产成本,并提高生产效率。
2. 航空航天工业:在航空航天工业中,刀具涂层技术可以应用于飞机零部件的加工和维修过程中。
刀具涂层技术可以提高刀具的高温抗氧化性能和抗磨损性能,保证零部件的质量和安全性。
3. 电子制造业:在电子制造业中,刀具涂层技术可以应用于半导体和电子元件的加工过程中。
刀具涂层技术可以提高切削质量,减少切削力和加工成本,提高生产效率。
4. 刀具制造业:在刀具制造业中,刀具涂层技术可以应用于刀具的制造过程中。
刀具涂层技术可以提高刀具的硬度、耐磨性和耐蚀性,延长刀具的使用寿命。
三、刀具涂层技术的未来发展趋势1. 纳米涂层技术的应用:随着纳米材料的发展和应用,纳米涂层技术将成为刀具涂层技术的重要发展方向。
纳米涂层可以提供更高的硬度、更好的耐磨性和更低的摩擦系数。
2. 多功能涂层技术的发展:多功能涂层技术是指在刀具表面涂层上添加功能性材料,以实现多种性能的综合应用。
未来,多功能涂层技术将成为刀具涂层技术的主要发展方向,以满足不同应用领域的需求。
3. 智能涂层技术的应用:智能涂层技术是指通过在刀具表面涂层上添加传感器或微电子设备,实现对刀具状况的实时监测和控制。
智能涂层技术将提高刀具的自动化程度和可靠性,减少刀具的维护和更换。
2024年金属涂层市场前景分析

2024年金属涂层市场前景分析简介金属涂层是一种应用广泛的表面处理技术,通过将金属材料施加到基材表面,可以提高其耐腐蚀性、抗磨损性和美观性。
随着工业发展和技术进步,金属涂层市场逐渐壮大,并呈现出良好的发展前景。
本文将对金属涂层市场的前景进行分析。
国内金属涂层市场现状目前,我国金属涂层市场规模逐年增长。
金属涂层在汽车、航空航天、电子、建筑等领域的应用日益广泛。
随着国内制造业的发展,金属涂层需求量不断增加,市场前景广阔。
同时,我国金属涂层行业技术水平不断提高,部分企业已具备自主研发能力,能够提供高质量的金属涂层产品。
这些都为金属涂层市场的快速发展创造了有利条件。
国际金属涂层市场趋势国际金属涂层市场也呈现出良好的发展态势。
随着全球经济一体化的加深,国际市场对金属涂层产品的需求不断增加。
尤其是在航空航天、能源、电子等高技术产业领域,金属涂层作为保护和装饰材料得到广泛应用。
同时,国际金属涂层领域的创新技术也在不断涌现,为市场的发展带来新的机遇和动力。
市场竞争状况金属涂层市场竞争激烈,主要由国内外大型企业和中小企业主导。
大型企业具备雄厚的资金实力和技术实力,在市场竞争中具有明显的优势。
中小企业主要通过技术创新和产品差异化来获取竞争优势。
金属涂层市场的竞争还存在一定程度的价格竞争,企业需要通过提高产品质量和服务水平来取得竞争优势。
市场前景分析金属涂层市场前景广阔。
随着工业技术的进步和国内外市场的扩大,金属涂层的应用范围将进一步扩展。
特别是在高科技产业领域,如航空航天、电子、能源等,对金属涂层产品的需求将持续增长。
此外,随着环境保护意识的提高,对环保型金属涂层产品的需求也将逐渐增加。
因此,金属涂层市场未来具有较大的发展潜力。
总结综上所述,金属涂层市场具有良好的发展前景。
国内外市场的扩大和技术的不断创新将推动金属涂层市场的发展。
各个领域对金属涂层产品的需求将继续增长,为企业提供了广阔的发展空间。
企业应重视技术创新,提高产品质量,以满足市场需求,抓住发展机遇,获取竞争优势。
材料表面涂层技术的研究与开发

材料表面涂层技术的研究与开发随着科技的不断发展,材料表面涂层技术已成为现代工业中不可缺少的一部分。
作为一种能够为材料赋予新的性能和特性的先进加工工艺,表面涂层技术可以广泛应用于机械、电子、化工等领域。
本文将探讨表面涂层技术的相关研究和开发,并从不同的角度分析其影响和前景。
一. 表面涂层技术的概述表面涂层技术是指对材料表面进行加工处理,涂上一层特定的材料,以赋予其新的性能,同时保护材料本身。
通过表面涂层,可以改变材料的外观、化学性质、机械性质和电学性质等。
表面涂层可以采用不同的方式,例如:化学沉积、热喷涂、电镀等。
其中,最常用的方式是物理气相沉积,包括蒸发沉积和磁控溅射等。
二. 表面涂层技术的分类目前,表面涂层技术可以根据不同的标准进行分类。
从材料的角度来看,可分为无机涂层和有机涂层;从涂层的功能来看,可分为保护型涂层、表面改性涂层和功能性涂层;从涂层的制备方式来看,可分为物理气相沉积和化学气相沉积等。
无论是哪种涂层方式,都要求涂层具有均匀、致密、无明显气孔和缺陷等特点。
同时,涂层的耐腐蚀性、耐磨性、导电性、隔热性等性能也是需要考虑的因素。
三. 表面涂层技术的应用表面涂层技术在许多领域都有广泛的应用。
其中,机械行业是最主要的应用领域之一。
在机械行业中,表面涂层技术可以增强机械零部件的耐磨性和耐腐蚀性,延长机械的使用寿命。
电子和光学领域的应用也在不断扩展。
表面涂层技术可以用于制造半导体材料、微电子元件和光学镜片等。
此外,表面涂层技术在医疗器械领域也有很大的应用前景。
医疗器械的表面涂层可以增加生物兼容性,防止细菌的滋生,从而提高医疗器械的使用效果和安全性。
同时,表面涂层技术还可以用于太阳能电池板制造、建筑材料防水、防火涂层和食品包装等领域。
四. 表面涂层技术的发展趋势表面涂层技术的发展趋势主要呈现出以下两个方面:一是涂层材料的多样化。
涂层技术的发展一直在寻求更多样化的涂层材料,以应对不断增长的市场需求。
涂层技术在工业领域中的应用现状及未来发展

涂层技术在工业领域中的应用现状及未来发展随着科技的不断进步和发展,涂层技术在工业领域中的应用逐渐得到普及,成为了工业制造中不可或缺的一环。
涂层技术包含很多种类,涵盖了涂装、电镀、化学镀、物理气相沉积等多个方面。
这些技术的应用范围从飞机、汽车、电子设备、钢铁到塑料、橡胶等各个领域。
本文将从应用现状、未来发展等几个角度出发,探讨涂层技术在工业领域中的应用。
一、涂层技术在工业领域中的应用现状1. 涂层技术在汽车领域的应用汽车是近年来涂层技术应用最广泛的领域之一。
在汽车生产过程中,除了普通漆面贴膜,涂层技术还可以实现汽车表面的防腐、抗磨、隔热等效果,提高汽车的安全性和舒适性。
例如,对于汽车螺栓等小零件,使用电镀技术可以增强它们的耐腐蚀性;对于高档车型,使用纳米陶瓷涂层技术可以增加车漆的硬度和光泽度,提高抗刮擦的能力。
2. 涂层技术在建筑领域的应用涂层技术在建筑领域中的应用范围同样广泛。
在建筑装饰中,调色漆是一种运用最广泛的涂层材料,它可以通过调配不同颜色的颜料、填料和树脂来实现色彩、质感、耐久性等不同方面的要求。
此外,建筑涂料还可以具有隔热、防水、防腐等特殊效果,例如环氧地坪的防水、POSCO墙体涂料的隔热等。
3. 其他领域的应用除了汽车和建筑领域,涂层技术在其他领域的应用也越来越广泛。
例如,在电子设备中,由于小巧轻便的需求,需要将各种功能紧凑地集成到一起,这时就需要使用一些特殊的涂层技术来保护电子元器件,并防止其受到水、气体和一些腐蚀性介质的侵蚀。
另外,对于一些特殊的材料,比如钨丝、铜等,需要先进行镀锌处理才能使用。
二、涂层技术在未来的发展1. 环保技术趋势的发展随着全球经济的发展和环保政策的不断加强,在未来的涂层技术中,越来越多的环保技术将被采用。
例如,水基涂料是一种新型的涂料,在不影响环境的情况下,可以实现对涂层的功能加强。
因此,随着环保意识的不断加强,水基涂料在未来将成为涂层技术的主流。
2. 纳米技术的应用纳米技术是未来涂层技术的一个重要发展方向。
- 1、下载文档前请自行甄别文档内容的完整性,平台不提供额外的编辑、内容补充、找答案等附加服务。
- 2、"仅部分预览"的文档,不可在线预览部分如存在完整性等问题,可反馈申请退款(可完整预览的文档不适用该条件!)。
- 3、如文档侵犯您的权益,请联系客服反馈,我们会尽快为您处理(人工客服工作时间:9:00-18:30)。
目录摘要: (2)Abstract: (2)1. 绪论 (3)2. 涂层技术的发展及现状 (3)2.1 CVD技术的发展 (3)2.2 PVD技术的发展 (4)2.3 我国涂层技术的发展及现状 (5)3. 切削刀具涂层技术研究进展 (6)3.1 多元涂层 (6)3.2 多层涂层 (6)3.3 纳米涂层 (7)3.4 超硬材料涂层 (8)4. 涂层刀具在金属切削加工中的应用 (8)4.1. 初期试验阶段 (9)4.2 试验总结分析 (11)4.3 成本改善及创效分析 (12)参考文献 (13)刀具涂层技术在机械加工中的应用赵剑(中国第一拖拉机股份有限公司齿轮厂工装部)摘要:切削刀具表面涂层技术是应机械加工性能需求发展起来的材料表面改进性技术。
涂层技术可有效提高切削刀具使用寿命,降低刀具消耗,使刀具获得优良的综合机械性能,从而大幅度提高经济效益和机械加工效率。
为满足现代机械加工对高效率、高精度、高可靠性的要求,尤其是机械传动行业,世界各国制造业对涂层技术的发展及其在刀具制造中的应用日益重视。
关键词:涂层技术,切削刀具,PVD,机械性能,经济效益。
Abstract:Surface coating technology for cutting tool is an improving technology with the demand of maching property development. Coating technology can effectively improve the service life of tool , reduce the tool consumption and make the tool getting excellent comprehensive mechanical properties. Thus , it can improve economic returns and working effiency. In order to satisfy the requirements for high efficiency, high precision and high reliability, especially in the mechanical drive industry. Every country of manufacturing industy in the world should pay more attention to the development of coating technology and application in the tooling manufacturingKeywords: Coating Technology,Cutting Tool,PVD,Mechanical properties,Economic benefit。
1. 绪论切削刀具表面涂层技术是近几十年应市场需求发展起来的材料表面改进性技术。
涂层刀具比未涂层刀具具有高速、高效、高精度、高质量、低成本及长寿命的优点,使刀具获得优良的综合机械性能,从而大幅度提高机械加工效率。
可以说,涂层刀具的出现是刀具材料发展的一次革命,因为它解决了刀具强度和韧性之间的矛盾。
因此,涂层技术与材料、切削加工工艺一起并称为切削刀具制造领域的三大关键技术。
为满足现代机械加工对高效率、高精度、高可靠性的要求,世界各国制造业对涂层技术的发展及其在刀具制造中的应用日益重视,并有了长足的发展,为刀具切削性能的提高开创了新的历史篇章。
我国的刀具涂层技术经过多年发展,目前正处于关键时期,即原有技术已不能满足切削加工日益提高的要求,而国内各大工具厂的涂层技术也远落后于世界其他国家,到了必须更新换代的时期。
因此,充分了解国内外刀具涂层技术的现状及发展趋势,瞄准国际涂层技术先进水平,有计划、按步骤地发展刀具涂层技术(尤其是PVD 技术),对于提高我国切削刀具制造水平具有重要意义。
2. 涂层技术的发展及现状刀具涂层技术通常可分为化学气相沉积(CVD)技术和物理气相沉积(PVD)技术两大类,分别评述如下。
2.1 CVD技术的发展二十世纪六十年代以来,CVD技术被广泛应用于硬质合金可转位刀具的表面处理。
由于CVD工艺气相沉积所需金属源的制备相对容易,可实现TiN、TiC、TiCN、TiBN、TiB2、AL2O3等单层及多元多层复合涂层的沉积,涂层与基体结合强度较高,薄膜厚度可达7-9μm,因此到八十年代中后期,美国已有85%的硬质合金工具采用了表面涂层处理,其中CVD涂层占到99%;到九十年代中期,CVD涂层硬质合金刀片在涂层硬质合金刀具中仍占80%以上。
尽管CVD涂层具有很好的耐磨性,但CVD工艺亦有其先天缺陷:一是工艺处理温度高,易造成刀具材料抗弯强度下降;二是薄膜内部呈拉应力状态,易导致刀具使用时产生微裂纹;三是CVD工艺排放的废气、废液会造成较大环境污染。
因此自九十年代中期以来,高温CVD技术的发展和应用受到一定制约。
九十年代中后期,中温化学气相沉积(MT—CVD)技术的出现使CVD技术发生了革命性变革。
采用MT—CVD技术可获得致密纤维状结晶形态的涂层,涂层厚度可8—10μm,(新型MT—CVD涂层的剖面结构见图1)。
这种涂层结构具有极高的耐磨性、抗热震性及韧性,并可通过高温化学气相沉积工艺在刀片表面沉积AL2O3等抗高温氧化性能好、与被加工材料亲和力小、自润滑性能好的材料。
MT—CVD 涂层刀片适于在高速、高温、大负荷、干式切削条件下使用,其寿命可比普通涂层刀片提高一倍左右。
图12.2 PVD技术的发展PVD技术出现于二十世纪七十年代末,由于其工艺处理温度可控制在500°以下,因此可作为最终处理工艺用于高速钢类刀具的涂层。
由于采用PVD工艺可大幅度提高高速钢刀具的切削性能,所以该技术得到了迅速推广,至八十年代末,工业发达国家高速钢复杂刀具的PVD涂层比例已超过60%。
研究结果表明:与CVD工艺相比,PVD工艺处理温度低,在600°以下时对刀具材料的抗弯强度无影响(试验结果见表1);表1 不同温度下PVD涂层对硬质合金材料抗弯强度的影响随着高速切削加工时代的到来,高速钢刀具应用比例逐渐下降、硬质合金刀具和陶瓷刀具应用比例上升已成必然趋势,因此,工业发达国家自九十年代初就开始致力于硬质合金刀具PVD涂层技术的研究,至九十年代中期取得了突破性进展,PVD涂层技术已普遍应用于硬质合金立铣刀、钻头、阶梯钻、油孔钻、铰刀、丝锥、可转位铣刀片、异形刀具、焊接刀具等的涂层处理。
经过几十年的研究和开发,各种刀具涂层工艺已广泛应用于硬质合金和高速钢切削刀具。
涂层工艺的主要发展阶段及应用领域见表2。
表2 主要涂层工艺发展时段及应用领域2.3 我国涂层技术的发展及现状我国从二十世纪七十年代初开始研究CVD涂层技术,由于该项技术专用性较强,国内从事研究的单位并不多,导致在随后的十多年里发展较为缓慢。
到八十年代初期,我国开始致力于PVD涂层技术的研究,至八十年代中期研制成功中小型空心阴极离子镀膜机,并开发了高速钢刀具TiN涂层工艺技术。
在此期间,国内先后有七家大型工具厂从国外引进了大型PVD涂层设备(均以高速钢TiN涂层工艺为主)。
技术及设备的引进调动了国内PVD技术的开发热潮,许多科研单位和各大真空设备厂纷纷展开了大型离子镀膜机的研制工作,并于九十年代初开发出多种PVD涂层设备。
但由于多数设备性能指标不高,无法保证刀具涂层质量,同时预期的市场效益未能实现,因此大多数企业未对PVD 刀具涂层技术作进一步深入研究,导致国内PVD刀具涂层技术的发展徘徊不前。
尽管九十年代末国内成功开发出多元复合涂层工艺技术并达到实用水平,CNX涂层技术的研发也有重大突破,但与国际发展水平相比,我国的刀具PVD涂层技术仍落后十年左右。
目前国外刀具PVD涂层技术已发展到第四代,而国内尚处于第二代水平,且仍以单层TiN 涂层为主。
3. 切削刀具涂层技术研究进展由于单涂层其性脆,不耐冲击,结合力较弱等缺点,所以无法满足现代加工的要求。
随着科技的发展,多元涂层和多层涂层相继出现,较好的弥补了单涂层的不足。
3.1 多元涂层单涂层刀具由于基材与涂层两者的硬度,弹性模量及热膨胀系数相差较远,晶格类型也不尽相同,导致残余应力增加,结合力较弱。
在单涂层中加入新的元素(如加入Cr 和Y提高抗氧化性,加入Zr、V、B和Hf提高抗磨损性,加入Si提高硬度和抗化学扩散)制备出多元的刀具涂层材料,大大提高了刀具的综合性能。
最常用的多元刀具涂层是TiCN、TiA1N涂层。
TiCN涂层兼有TiC和TiN涂层的良好韧性和硬度,它在涂覆过程中可通过连续改变C和N的成份来控TiCN的性质,降低涂层的内应力,提高韧性,增加涂层厚度,阻止裂纹扩展,减少崩刃。
近年来,以TiCN为基的四元成分新涂层材料(如TiZrCN、TiAlCN、TiSiCN等)也纷纷出现。
TiA1N涂层材料是目前应用最广泛的高速硬质合金刀具涂层之一,TiA1N有很高的高温硬度和优良的抗氧化能力,抗氧化温度为800℃,在高速加工中表面会产生一层非晶态A12O3薄膜,对涂层起保护作用。
目前人们将研究重点放在对TiA1N涂层的改进上,以满足应用领域对诸如抗氧化性能、热稳定性能及热硬度等需求的不断提高。
3.2 多层涂层随着涂层技术的发展,单层多元涂层也逐渐被多层的复合涂层所取代。
根据不同涂层材料的性能和切削条件,涂覆不同的涂层组合,以发挥各种涂层的优越性能。
TiC/TiN双层涂层兼有TiC涂层的高硬度和高耐磨性,并有TiN涂层良好的化学稳定性和高抗月牙洼磨损性能。
由于TiC的热膨胀系数比TiN更接近基体,涂层的残余应力较小,与基体结合牢固,所以常用作多层涂层的底层。
其它的双层涂层有TiN/CBN、Al203/CBN、TiC/TiBN及Al203/Ti2O3等。
三层涂层的组合方式很多,例如TiC/TiCN/TiN、TiC/TiCN/Ti2O3、TiC/TiN/Al203、TiC/Al23/TiN等,都是利用各个单涂层的优点根据不同的切削条件组合而成的。
最常见是TiC/TiCN/TiN涂层,这种涂层与TiC/TiN涂层相同,切削性能优于单层TiC 和TiN涂层。
大多数刀具涂层厂家都有这种组合方式的涂层牌号,如美国Carmet公司的CA9443、CA9721;Kennametal公司的KC210、KC250等。
在TiC/TiCN/TiN涂层组合中再加入Al203涂层,成为更现代化的涂层。
如瑞典Sandvik Coromant公司在CIMT2005上新的GC2015牌号刀具是具有TiCN—TiN/Al203/TiN结构的复合涂层,其中底层的TiCN与基体的结合强度高,并有良好的耐磨性。