质量损失函数
基于质量损失函数的质量管理研究

基于质量损失函数的质量管理研究在现代竞争激烈的市场环境下,企业对于产品质量的要求越来越高。
为了保持竞争优势,许多企业都采取了质量管理的策略。
其中,基于质量损失函数的质量管理方法已经成为各行各业广泛应用的一种手段。
质量损失函数是质量管理领域中的一个重要概念,它代表了企业由于质量问题而产生的直接和间接成本。
换句话说,它衡量了产品质量不达标对企业经济利益的影响程度。
基于质量损失函数的质量管理方法通过量化质量问题的经济损失,帮助企业制定有效的质量控制措施和优化生产过程。
首先,基于质量损失函数的质量管理方法可以帮助企业识别影响产品质量的关键因素。
企业生产过程中存在着各种各样的变量和环节,而每一个环节都可能对产品质量产生影响。
通过建立质量损失函数模型,企业可以对不同的质量问题进行定量分析,从而找出造成质量问题的主要因素。
这一结果对于企业改进生产过程和提高产品质量具有重要意义。
其次,基于质量损失函数的质量管理方法可以帮助企业确定适当的质量控制限制。
通过对不同质量问题的损失函数进行分析,企业可以确定出不同质量水平下的经济损失。
在实际生产过程中,企业往往会面临质量水平和成本之间的权衡。
基于质量损失函数的方法可以帮助企业确定一个最佳的质量水平,使得经济损失最小化。
同时,企业还可以根据不同的质量要求和顾客需求,制定相应的质量控制限制,以保证产品质量符合市场需求。
此外,基于质量损失函数的质量管理方法还可以帮助企业评估质量改进的效果。
在质量管理过程中,企业通常会采取一系列的质量改进措施,如调整生产参数、优化工艺流程等。
基于质量损失函数的方法可以帮助企业量化不同改进措施对经济损失的影响,从而评估改进效果的好坏。
这对于企业不断优化产品质量和生产效率具有重要意义。
综上所述,基于质量损失函数的质量管理研究在现代企业中具有广泛应用前景。
通过量化质量问题的经济损失,这一方法可以帮助企业识别关键因素、确定质量控制限制以及评估改进效果。
{品质管理品质知识}质量损失函数

{品质管理品质知识}质量损失函数质量损失函数日本质量管理学家田口玄一(Taguchi)认为产品质量与质量损失密切相关,质量损失是指产品在整个生命周期的过程中,由于质量不满足规定的要求,对生产者、使用者和社会所造成的全部损失之和。
田口用货币单位来对产品质量进行度量,质量损失越大,产品质量越差;反之,质量损失越小,产品质量越好。
一、质量特性产品质量特性是产品满足用户要求的属性,包括产品性能、寿命、可靠性、安全性、经济性、可维修性和环境适应性等。
(与前描述是否一致)(一)质量特性分类田口先生为了阐述其原理,对质量特性在一般分类的基础上作了某些调整,分为计量特性和计数特性,如图1所示。
1、望目特性。
设目标值为m,质量特性y围绕目标值m波动,希望波动愈小愈好,则y就被称为望目特性,例如加工某一轴件图纸规定φ10±0.05(mm),加工的轴件的实际直径尺寸y就是望目特性,其目标值m=10(mm)。
2、望小特性。
不取负值,希望质量特性y愈小愈好,波动愈小愈好,则y 被称为望小特性。
比如测量误差,合金所含的杂质、轴件的不圆度等就属于望小特性。
3、望大特性。
不取负值,希望质量特性y愈大愈好,波动愈小愈好,则y 被称为望大特性。
比如零件的强度、灯泡的寿命等均为望大特性。
(二)质量特性波动产品在贮存或使用过程中,随着时间的推移,发生材料老化变质、磨损等现象,引起产品功能的波动,我们称这种产品由于使用环境,时间因素,生产条件等影响,产品质量特性y偏离目标值m,产生波动。
引起产品质量特性波动的原因称为干扰源。
主要有以下三种类型:1、外干扰(外噪声)使用条件和环境条件(如温度,湿度,位置,输入电压,磁场,操作者等)的变化引起产品功能的波动,我们称这种使用条件和环境条件的变化为外干扰,也称为外噪声。
2、内干扰(内噪声)材料老化现象为内干扰,也称为内噪声。
3、随机干扰(产品间干扰)在生产制造过程中,由于机器、材料、加工方法、操作者、计测方法和环境(简称5MIE)等生产条件的微小变化,引起产品质量特性的波动,我们称这种在生产制造过程中出现的功能波动为产品间波动。
什么是质量损失

什么是质量损失质量损失是指企业在生产、经营过程和活动中,由于产品的质量问题而导致的损失,即由于质量低劣而产生的内、外部损失。
质量损失的存在在于资源的潜力没能得到充分的发挥,质量损失的存在也正是质量改进的意义所在或质量改进的机会所在。
[编辑]质量损失的类型质量损失可分为两种形式:有形损失和无形损失。
(1)有形损失指由于内部故障而直接发生的费用,如返工、低效的人机控制、丧失机会等而引起的低工作效率而造成的资源和材料的浪费等。
(2)无形损失是指由于顾客不满意而发生的未来销售的损失,如因顾客不满意而失去顾客,丧失信誉,从而失去更多销售机会或增值机会所造成的损失。
无形损失不是实际的费用支出,常常难以统计和定量,并且它对组织的影响大且长久,因而,它是一种很重要的损失。
[编辑]质量损失函数[1]日本质量管理专家田口玄一给出了质量损失函数的表达式——一个“二次方程式”及其平衡的条件。
L(x) = K(x− m)2其中:L(x)——质量损失,m——质量特性标准,x——质量特性值, k——常数,一般可以由“机能界限”确定。
企业的损失函数为:要使用户的质量损失和企业的损失之和最小,则必须满足条件:当x=m时,有最小值,即质量特性值x等于目标值m时,则表明此时质量最好。
当时,L(x) < A当时,L(x)>A,上述关系可用下图表示。
图:制造容差与质量损失[编辑]参考文献1. ↑质量管理学,第八章质量经济性管理第一节质量的经济性,中国地质大学(武汉)网络教育学院课件本条目对我有帮助4如果您认为本条目还有待完善,需要补充新内容或修改错误内容,请编辑条目。
本条目由以下用户参与贡献Cabbage,Vulture.页面分类: 质量术语评论(共0条)提示:评论内容为网友针对条目"质量损失"展开的讨论,与本站观点立场无关。
发表评论。
mpdiou损失函数公式含义

mpdiou损失函数公式含义
M模型预测的视在质量损失 (\text{MPDIou}) 简称为MPDIou 损失,表示目标分割与估计分割之间的相互信息。
MPDIou损失是通过计算两个分割掩码的交集和并集之间的IoU (Intersection over Union) 差异来衡量模型的性能。
MPDIou损失的公式如下:
\text{MPDIou} = \frac{{\text{IoU}(P, G)}}{{\text{IoU}(P, G) + \delta + (1 - \text{IoU}(P, G))}} \times (\delta + (1 - \text{IoU}(P, G)))
其中,P代表模型预测的分割掩码,G代表目标分割的掩码,IoU(P, G)表示模型预测与目标分割的IoU。
MPDIou损失通过使用一个可调整的参数\delta,来平衡IoU差异的重要性,当IoU(P, G)较高时,MPDIou损失较低,表示模型与目标分割的匹配较好;当IoU(P, G)较低时,MPDIou损失较高,表示模型与目标分割的差异较大。
最新质量损失函数

产品质量特性是产品满足用户要求的属性,包括产品性能、寿命、可靠性、安全性、经济性、 可维修性和环境适应性等。 (与前描述是否一致)
(一)质量特性分类 田口先生为了阐述其原理,对质量特性在一般分类的基础上作了某些调整,分为计量特性和 计数特性,如图 1 所示。
望目特性
质量特性
静态特性
计量特性
3、随机干扰(产品间干扰)
在生产制造过程中,由于机器、材料、加工方法、操作者、计测方法和环境(简称
5MIE)等
生产条件的微小变化,引起产品质量特性的波动,我们称这种在生产制造过程中出现的功能波动
为产品间波动。
以电视机电源电路为例,其输出特性的干扰分类及抗干扰性能如 1 表所示。
二、质量损失函数
干扰引起了产品功能的波动,有波动就会造成质量损失。如何度量由于功能波动所造成的损
3、望大特性。不取负值,希望质量特性 y 愈大愈好,波动愈小愈好,则 y 被称为望大特性。
比如零件的强度、灯泡的寿命等均为望大特性。
(二)质的推移,发生材料老化变质、磨损等现象,引起产品功
能的波动,我们称这种产品由于使用环境,时间因素,生产条件等影响,产品质量特性
失,田口先生提出了质量损失函数的概念,它把功能波动与经济损失联系起来。田口先生把产品
(或工艺项目)看作一个系统,这个系统的因素分为输入因素(可再分为可控因素
X 和不可控因
素 Z)和输出因素(即质量特性或响应) y,如图 2 所示。系统的设计目标值为 m。
干扰
外部干扰(温度、湿度、尘
特
性
埃、输入电压等环境条件波
量损失函数,给我们提供了很多重要信息,从图 3 的曲线可以看出。
第一,质量损失函数如连续的二次函数曲线所示,质量特性仅仅在规范( T)以内并不一定表
质量损失函数

质量损失函数
质量损失函数是一个损失函数,用来衡量模型在预测过程中拥有的质量,它衡量的是模型的准确性。
质量损失函数由质量指标组成,这些指标可以是数据准确性、预测准确性、生产效率等。
质量损失函数的基本原理是:实际的预测结果与模型期望结果之间的差距,而这个差距应该尽可能的小,从而提升模型预测的效率和准确性。
用来计算质量损失函数的公式可以是任意函数,通常可以用均方差(MSE)来衡量质量损失。
MSE是一种平均偏差的可量化衡量,它表示模型输出值与真实值之间的差距。
另外,贝叶斯损失函数也可以用来衡量质量损失,它是一种按比例降低异常结果的方法,能够较好地衡量模型的质量。
在实际的机器学习和数据挖掘系统中,质量损失函数是一个重要的概念,它能够帮助模型追求更大的精度和准确性。
模型的优化过程需要连续更新质量损失函数,以获得更好的预测结果,这就决定了质量损失函数在机器学习和数据挖掘中的重要性。
质量损失函数讲

质量损失函数日本质量管理学家田口玄一(Taguchi)认为产品质量与质量损失密切相关,质量损失是指产品在整个生命周期的过程中,由于质量不满足规定的要求,对生产者、使用者和社会所造成的全部损失之和。
田口用货币单位来对产品质量进行度量,质量损失越大,产品质量越差;反之,质量损失越小,产品质量越好。
一、质量特性产品质量特性是产品满足用户要求的属性,包括产品性能、寿命、可靠性、安全性、经济性、可维修性和环境适应性等。
(与前描述是否一致)(一)质量特性分类田口先生为了阐述其原理,对质量特性在一般分类的基础上作了某些调整,分为计量特性和计数特性,如图1所示。
图1 质量特性的分类计数特性请查阅有关书籍,这里主要对计量特性进行描述。
1、望目特性。
设目标值为m,质量特性y围绕目标值m波动,希望波动愈小愈好,则y就被称为望目特性,例如加工某一轴件图纸规定φ10±0.05(mm),加工的轴件的实际直径尺寸y就是望目特性,其目标值m=10(mm)。
2、望小特性。
不取负值,希望质量特性y愈小愈好,波动愈小愈好,则y 被称为望小特性。
比如测量误差,合金所含的杂质、轴件的不圆度等就属于望小特性。
3、望大特性。
不取负值,希望质量特性y愈大愈好,波动愈小愈好,则y被称为望大特性。
比如零件的强度、灯泡的寿命等均为望大特性。
(二)质量特性波动产品在贮存或使用过程中,随着时间的推移,发生材料老化变质、磨损等现象,引起产品功能的波动,我们称这种产品由于使用环境,时间因素,生产条件等影响,产品质量特性y偏离目标值m,产生波动。
引起产品质量特性波动的原因称为干扰源。
主要有以下三种类型:1、外干扰(外噪声)使用条件和环境条件(如温度,湿度,位置,输入电压,磁场,操作者等)的变化引起产品功能的波动,我们称这种使用条件和环境条件的变化为外干扰,也称为外噪声。
2、内干扰(内噪声)材料老化现象为内干扰,也称为内噪声。
3、随机干扰(产品间干扰)在生产制造过程中,由于机器、材料、加工方法、操作者、计测方法和环境(简称5MIE)等生产条件的微小变化,引起产品质量特性的波动,我们称这种在生产制造过程中出现的功能波动为产品间波动。
容差设计

(15)
10.5.2容差的确定方法 容差的确定方法
1.由安全系数确定容差 由安全系数确定容差 本节引入的安全系数的定义是田口博士提出的, 本节引入的安全系数的定义是田口博士提出的,与通常 工程技术中的安全系数不是完全相同的概念, 工程技术中的安全系数不是完全相同的概念,应注意两 者的区别。 者的区别。 (1).安全系数定义 安全系数定义 为达到功能界限的平均损失,主要是用户的损失; 设A0为达到功能界限的平均损失,主要是用户的损失; A为不合格品时的工厂损失,则安全系数 为不合格品时的工厂损失, 为不合格品时的工厂损失 &=(A0/A)1/2 ( ) (17) ) 由于A0﹥A,因此安全系数&大于1。安全系数&越大, 由于 ,因此安全系数&大于 。安全系数&越大, 说明丧失功能时的损失也越大。因此, 说明丧失功能时的损失也越大。因此,对于要求有很高 安全性的产品,相应的安全系数&比较大。 安全性的产品,相应的安全系数&比较大。一般采用安 全系数& ~ 。 全系数&=4~5。
容差设计
1
10.5.1质量损失函数 质量损失函数
按照田口提出的理论,要评价产品设计质量的好坏, 按照田口提出的理论,要评价产品设计质量的好坏,只要 计算损失函数就够了。 计算损失函数就够了。本章主要介绍运用质量损失函数确 定产品容差的方法。 定产品容差的方法。 望目特性的损失函数 设产品的质量特性y为望目特性,m为望目值。称下述函 为望目值。 设产品的质量特性 为望目特性, 为望目值 为望目特性 数为望目特性的损失函数。 数为望目特性的损失函数。 L(y)=k(y-m)2 (5) ) 式中, 为与 无关的常数,它可以按下述方法确定: 为与y无关的常数 式中,k为与 无关的常数,它可以按下述方法确定: K=A0/△02=A/△2 (6) △ △ 式中, 为产品的功能界限; 式中,△0为产品的功能界限;A0为产品丧失功能时的损 为产品的容差; 为产品不合格的损失 为产品不合格的损失。 失;△为产品的容差;A为的质量特性y为望大特性 为望大特性, 不取负值, 设产品的质量特性 为望大特性,则y不取负值,且理想值 不取负值 为无限大。此时,只要将1/y视为望小特性 视为望小特性, 为无限大。此时,只要将 视为望小特性,便可得到望 大特性的损失函数和平均质量损失。 大特性的损失函数和平均质量损失。 L(y)=k/y2 (13) K= A0△02=A△2 (14) △ n L--(y)=k1/n∑1/yi2=kVT ) I=1 式中, 式中, n VT=1/n∑1/yi2 I=1 (16) )
质量损失函数

质量损失函数
质量损失函数是一种统计方法,可以在预测任务中用来衡量质量损失程度。
它通常用来衡量模型预测准确度,以及这些预测中可能存在的偏差和误差。
质量损失函数可以衡量预测误差,以便能够判断出哪种预测是更有效的,也可以使用来衡量模型性能,以便可以根据质量损失降低模型的性能。
质量损失函数的类型主要有两种:回归损失和分类损失。
回归损失有均方误差(MSE)和平均绝对误差(MAE)等,而分类损失有交叉熵损失和Hinge损失等。
均方误差(MSE)是一种常用的回归损失函数,它衡量的是实际值与预测值之间的差异,它的计算公式是:MSE =(实际值 -测值)/ N,其中N代表损失函数的总个数。
MSE可以用来衡量模型的拟合度,它的值越小,拟合度越强,因此,我们可以通过降低MSE的值来提高模型的精度。
另一种类型的质量损失函数是Hinge损失,它是一种分类损失函数,它可以用来衡量分类准确度,它的计算公式是:Hinge损失 = max (0, 1 -签测值),其中标签是指预测样本的实际标签,而预测值是预测的值。
Hinge损失可以用来判断模型的准确性,它的值越小,说明模型的准确度越高。
此外,还有一种质量损失函数,称为正则化损失函数,它可以用来降低模型的复杂性,从而降低训练误差和测试误差,从而提高模型
的精度。
正则化损失函数是一种特殊的质量损失函数,它可以抑制模型过拟合,保持模型稳定,以达到更好的性能。
总之,质量损失函数是一种用来衡量模型预测的准确度的统计方法,它可以为我们提供一种有效的方法来衡量模型的性能,以及预测中可能存在的偏差和误差。
它可以帮助我们判断出更有效的预测,并可以用来提高模型的准确度,从而达到更好的性能。
质量方法论之质量损失函数

【科普】质量方法论之质量损失函数质量损失是指企业在生产、经营过程和活动中,由于产品的质量问题而导致的损失,即由于质量低劣而产生的内、外部损失。
质量损失的存在在于资源的潜力没能得到充分的发挥,是质量改进的机会所在。
质量损失可分为两种形式:有形损失和无形损失。
有形损失指由于内部故障而直接发生的费用,如返工、低效的人机控制、丧失机会等而引起的低工作效率而造成的资源和材料的浪费等。
无形损失是指由于顾客不满意而发生的未来销售的损失,如因顾客不满意而失去顾客,丧失信誉,从而失去更多销售机会或增值机会所造成的损失。
无形损失不是实际的费用支出,常常难以统计和定量,并且它对组织的影响大且长久,因而,它是一种很重要的损失。
质量损失函数:日本质量管理专家田口玄一给出了质量损失函数的表达式——一个“二次方程式”及其平衡的条件。
其中:L(x)——质量损失,m——质量特性标准,x——质量特性值, k——常数,一般可以由“机能界限”确定。
应用损失函数在实践中最重要的运用,在于协助我们通过过程的改善而持续减少目标值的变异,并非仅仅追求符合逻辑。
现在举个例子:某个工厂人员的产出,以每小时多少元来计算,而损失函数所显示的,是产出以室内通风条件而改变的情形。
厂内工作的每个人,都有自己的损失函数。
为了简化说明,假设每个人的损失函数均为一条抛物线,其底部一点代表产出值最大时的通风条件,把所有人员的损失函数进行叠加,公司整体的损失函数也必然是一条抛物线。
如果通风条件偏离这个最佳水准,就会有额外损失发生。
该抛物线与横轴相切时,切点的左右各有一小段与横轴几近重合。
也就是说,有最适点偏离一小短距离,损失小到可以忽略不计。
因此,当室内通风条件稍稍偏离均衡点,发生的损失可以忽略不计。
但是远离均衡点时,总是有人必须支付这损失。
如果我们能够导出有具体数字的损失函数,我们就可以计算出最有均衡点,在均衡点中最适合的通风条件如何,以及达到要求的费用支出是多少。
ssim损失函数公式

ssim损失函数公式SSIM(Structural Similarity)是一种用于衡量图像质量的损失函数,它是基于人眼感知的视觉质量度量。
SSIM损失函数的公式如下:SSIM(x,y)=[l(x,y)^α*c(x,y)^β*s(x,y)^γ]其中x和y是输入的两幅图像,SSIM(x,y)是这两幅图像之间的相似度。
l(x,y)是亮度相似度,c(x,y)是对比度相似度,s(x,y)是结构相似度。
α、β和γ是权重参数,一般设置为1下面将对l(x,y)、c(x,y)和s(x,y)以及SSIM的计算过程进行详细介绍。
1. 亮度相似度(luminance similarity):亮度相似度反映了两幅图像的亮度级别之间的相似程度。
它的计算公式如下:l(x,y)=(2μxμy+C1)/(μx^2+μy^2+C1)其中μx是图像x的均值,μy是图像y的均值,C1是一个常数,用于防止分母为零。
2. 对比度相似度(contrast similarity):对比度相似度衡量了两幅图像的对比度之间的相似程度。
它的计算公式如下:c(x, y) = (2σxy + C2) / (σx^2 + σy^2 + C2)其中σx是图像x的方差,σy是图像y的方差,σxy是图像x和图像y的协方差,C2是一个常数,用于防止分母为零。
3. 结构相似度(structural similarity):结构相似度度量了两幅图像的结构之间的相似程度。
它的计算公式如下:s(x, y) = (σxy + C3) / (σxσy + C3)其中σx是图像x的标准差,σy是图像y的标准差,σxy是图像x 和图像y的协方差,C3是一个常数,用于防止分母为零。
4.权重参数(α、β和γ):权重参数用于调节亮度相似度、对比度相似度和结构相似度在SSIM 计算中的贡献程度。
一般情况下,三个参数都被设置为15.SSIM计算过程:首先,计算两幅图像的亮度相似度、对比度相似度和结构相似度。
质量损失函数

望小特性
不取负值,希望质量特性y愈小愈好,波动愈小愈好,则y 被称为望小特性。比如测量误差,合金所含 的杂质、轴件的不圆度等就属于望小特性。
望大特性
不取负值,希望质量特性y愈大愈好,波动愈小愈好,则y被称为望大特性。比如零件的强度、灯 泡的寿命等均为望大特性。 衡量望大特性稳定性的信噪比公式: η= -101g*1/n*Σ1/y²(dB)
分类
设目标值为m,质量特性y围绕目标值m波动,希望波动愈小愈好,则y就被称为望目特性,例如 加工某一轴件图纸规定φ10±0.05(mm),加工的轴件的实际直径尺寸y就是望目特性,其目标值 m=10(mm)。 望目特性的质量损失函数 根据功能界限Δ0和相应损失A0求k。产品输出特性 y目标值m,则当ly-ml≤Δ0时,产品可以正常发挥功 能;而当ly-ml>Δ0时产品将丧失功能,且造成经 济损失A0得 A0=k·Δ0²或k=A0/Δ0² 根据容差Δ和相应损失A求k,当ly-ml>Δ时,产 品不合格相应损失A得 A=kΔ²
品的出场容差。
解 :已知∆0=20mg, A0=70元, A=10元,则: Ø=
A0 A
=
70 10
=2.646 和
∆= ∆0/Ø= 20mg/2.646=7.559mg
所以工厂验收的合格标准为y≤7.559mg
质量损失函数
定义
干扰引起了产品功能的波动,有波动就会造成质量损失。如 何度量由于功能波动所造成的损失,田口先生提出了质量损失函 数的概念,它把功能波动与经济损失联系起来。田口先生把产品
(或工艺项目)看作一个系统,这个系统的因素分为输入因素
(可再分为可控因素X和不可控因素Z)和输出因素(即质量特性 或响应)y。
质量损失函数: L(y)=(AοΔο²)/y² 若已知不合格损失A,即y=Δ时, L(y)=A 则A=AοΔο²*1/Δ² 所以 Δ=√(Aο/A)Δο=ΦΔο
质量损失函数

日本质量管理学家田口玄一(Taguchi)认为产品质量与质量损失密切相关,质量损失是指产 品在整个生命周期的过程中,由于质量不满足规定的要求,对生产者、使用者和社会所造成的全 部损失之和。
田口用货币单位来对产品质量进行度量,质量损失越大,产品质量越差;反之,质 量损失越小,产品质量越好。
产品质量特性是产品满足用户要求的属性,包括产品性能、寿命、可靠性、安全性、经济性、 可维修性和环境适应性等。
(与前描述是否一致)(一)质量特性分类田口先生为了阐述其原理,对质量特性在普通分类的基础上作了某些调整,分为计量特性和计数特性,如图 1 所示。
计数特性请查阅有关书籍,这里主要对计量特性进行描述。
1、望目特性。
设目标值为 m ,质量特性 y 环绕目标值 m 波动,希翼波动愈小愈好,则 y 就 被称为望目特性,例如加工某一轴件图纸规定φ 10±0.05(mm),加工的轴件的实际直径尺寸 y 就 是望目特性,其目标值 m=10(mm)。
2、望小特性。
不取负值,希翼质量特性 y 愈小愈好,波动愈小愈好,则y 被称为望小特性。
比如测量误差,合金所含的杂质、轴件的不圆度等就属于望小特性。
3、望大特性。
不取负值,希翼质量特性 y 愈大愈好,波动愈小愈好,则 y 被称为望大特性。
比如零件的强度、灯泡的寿命等均为望大特性。
(二)质量特性波动产品在贮存或者使用过程中,随着时间的推移,发生材料老化变质、磨损等现象,引起产品功 能的波动,我们称这种产品由于使用环境,时间因素,生产条件等影响,产品质量特性 y 偏离目 标值 m ,产生波动。
引起产品质量特性波动的原因称为干扰源。
主要有以下三种类型:望目特性望小特性望大特性质量特性计件特性动态特性 计数特性计点特性计量特性 静态特性1、外干扰(外噪声)使用条件和环境条件(如温度,湿度,位置,输入电压,磁场,操作者等)的变化引起产品 功能的波动,我们称这种使用条件和环境条件的变化为外干扰,也称为外噪声。
田口正交实验方法
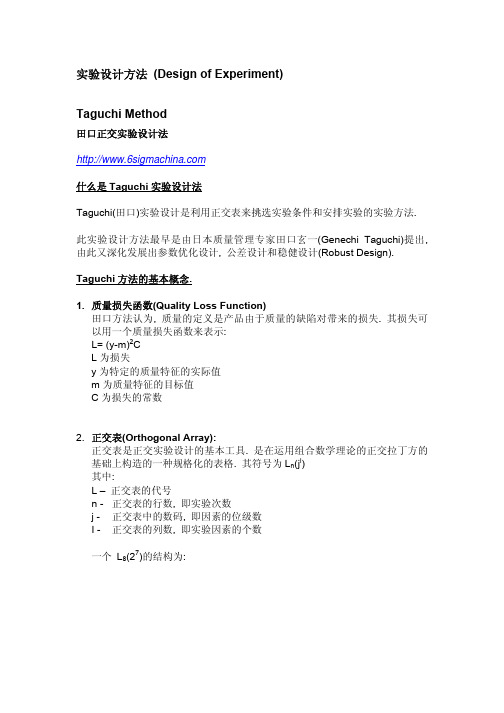
实验设计方法(Design of Experiment)Taguchi Method田口正交实验设计法什么是Taguchi实验设计法Taguchi(田口)实验设计是利用正交表来挑选实验条件和安排实验的实验方法.此实验设计方法最早是由日本质量管理专家田口玄一(Genechi Taguchi)提出, 由此又深化发展出参数优化设计, 公差设计和稳健设计(Robust Design).Taguchi方法的基本概念.1. 质量损失函数(Quality Loss Function)田口方法认为, 质量的定义是产品由于质量的缺陷对带来的损失. 其损失可以用一个质量损失函数来表示:L= (y-m)2CL为损失y为特定的质量特征的实际值m为质量特征的目标值C为损失的常数2. 正交表(Orthogonal Array):正交表是正交实验设计的基本工具. 是在运用组合数学理论的正交拉丁方的基础上构造的一种规格化的表格. 其符号为L n(j i)其中:L – 正交表的代号n - 正交表的行数, 即实验次数j - 正交表中的数码, 即因素的位级数I - 正交表的列数, 即实验因素的个数一个L8(27)的结构为:正交表L8(27)此表为7个因素, 2个位级的8个实验组合的正交表.在这个正交表中, 你可以看到, 任意一个因素的任意一个位级出现的次数都是4次, 也就是说他们出现的机会是平均的, 同时, 任意两列的位级的组合是(1, 1), (2, 2), (1, 2), (2, 1)各出现2次, 也是均衡的.这是比较常用的两个位级的正交表之一, 还有3个位级, 4个位级和5个位级以及混合位级的正交表.3个位级的正交表(例)混合位级的正交表(例)3. 信噪比(Signal to Noise Ratio)信噪比和稳健(Robustness)的概念紧密相关, 稳健的概念追求产品或流程的表现在受到因素的波动时候的稳定性.这个比用S/N来表示.S/N可以是:! 望目值 – 某个目标值! 望大值 – 比如合格率! 望小值 – 比如维修时间利用Minitab进行Taguchi实验方法的实例一个接触器的使用寿命的实验设计Y = 寿命(衡量指标为: 次)因素:A = 触片形状(标准, 长)B = 支撑长度(全长, .25mm间隙)C = 材料厚度(0.012 , 0.011)D = 方向(标准, 横向)在Minitab中, Stat>DOE>Taguchi > Create Taguchi Experiment选择正交表输入因素的名称和位级得到Taguchi方法的实验表收集实验数据分析Stat > DOE > Taguchi > Analyze Taguchi Design同时考察S/N, Mean 和 Standard Deviation这里的S/N是望大(寿命)结果\对分析的结果来看,当需要提高接触器的寿命时, 各因素的设置为较长的长度, 25毫米的支撑间隙, 0.11的材料厚度和标准方向.。
容差设计_精品文档
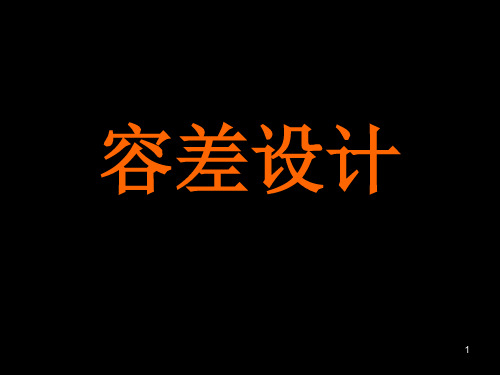
解:&=(A0/A)1/2 =(500/2)1/2=15.8
△=△0/&=(0.25*120)/15.8=1.9(V)
合格品范围m±△=120±1.9=(118.1V 121.9V)
6
(3)望大特性情形
望大特性的容差△和丧失功能的界限△0之间具有如下关 系式:
△=(A0/ A)1/2△0
(20)
系由数公&式时(,17则)容和差公△式为(:20),当已知功能界限△0和安全
因此所用型材的强度不限为63Mpa
7
2.下位特性容差的确定
现在让我们来看一看如何根据上位特性(结果特性)的容差或功能界限, 确定下位特性的容差。
设产品的上位特性为y,下位特性为x,考虑最简单的情况,设当下位特性 x变化单位量时,相应上位特性y的变化量为b,则y与x之间存在如下线性 关系:
y=a+bx
m
m-Bt
t
T
图10-17 当y0=m时的老化特性
老化系数B的容差△ *的计算公式如下:
△*=(3A*/A0)1/2*(△0/ T) (27)
11
例10-11 某机械零件尺寸y的设计初始值为目标值 m,设计寿命T=10年,当磨损量达到300Um时就 不损降能失级A正使0常 用=8使 的0元用 损。,失若即A*每功=5年能元平界,均限求磨△B损的0=量3容0B差0不U△m合*,格此,时产的品
6.94
31.51 0.3
20
表10-6中,总损失为: LTi=Pi+Li, i=1,2,3 从最达表佳到1材平0-料 衡6中。 ,可而 两看且者出采之,用比材接A2料近时A1,。2的质总量损损失失L和T2成最本小之,间是
例年1时0,-12零在件例尺1寸0-y1等1中于,目设标初值始m值,其y他0不条等件于不目变标,值求,每当年t=平5 均磨损B的容差△ 解:△=(12A*/A0)1/2*△0/T =2(3A*/A0)1/2*△0/T=2△*=2*13=26(Um/年) 因此,每年平均磨损B的容差为26Um/年
质量方法论之质量损失函数

质量方法论之质量损失函数在质量管理领域,损失函数是一种方法论,用于评估质量问题的严重程度和影响,并帮助确定改善措施。
损失函数是指将质量问题转化为经济损失或风险的数值化指标,目的是为了帮助决策者衡量质量问题的重要性,优化资源分配和决策过程。
首先,损失函数需要明确定量的损失评估指标。
损失指标可以是直接经济损失,如产品召回或客户赔偿费用;也可以是间接经济损失,如声誉受损导致市场份额的下降。
除了经济损失,还可以考虑其他非经济因素,如环境影响和公司形象。
通过量化损失指标,能够更加准确地评估质量问题的重要性和紧迫程度。
最后,损失函数需要将损失评估结果与质量改进措施相对比。
通过损失函数,企业可以清楚地了解质量问题的严重程度和影响,从而确定改进措施的优先级和资源分配。
企业可以比较不同质量问题的损失评估结果,将资源集中于造成最大经济损失或风险的问题上。
同时,损失函数还能够帮助企业评估质量改进措施的经济效益,确定措施的可行性和优先级。
损失函数方法论在质量管理中具有重要的意义和应用价值。
通过数值化指标,损失函数帮助企业准确评估质量问题的重要性和影响,优化资源分配和决策过程。
它可以帮助企业提高质量管理效能,减少经济损失和风险。
同时,损失函数也可以帮助企业实现持续质量改进,提高产品和服务的质量水平,增强市场竞争力。
尽管损失函数方法论在质量管理中具有重要的应用价值,但也存在一些问题和挑战。
首先,建立准确的质量问题与损失之间的关联模型是一个复杂的任务,需要考虑多个因素和变量的影响。
其次,损失函数方法论需要大量的数据支持,包括质量问题和经济损失的历史数据,以及相关变量和因素的数据。
在一些情况下,数据的获取和分析可能存在困难。
此外,损失函数方法论还依赖于企业对质量问题和经济损失的准确估计,这对于一些难以量化的因素来说可能是挑战性的。
总之,损失函数是一种质量管理的方法论,通过将质量问题转化为经济损失或风险的数值化指标,帮助企业衡量质量问题的重要性,优化资源分配和决策过程。
质量损失函数范文

质量损失函数范文质量损失函数是一个衡量产品或服务质量的度量,用于评估和量化产品或服务在生产和交付过程中可能发生的质量损失。
质量损失函数通常被用于帮助企业识别和解决潜在的质量问题,以最小化质量损失并提高产品或服务的质量水平。
质量损失函数可以应用于各个行业和领域,从传统的制造业到服务行业、金融机构和医疗保健等领域。
在制造业中,质量损失函数可以用于衡量产品生产过程中可能发生的缺陷和损失。
在服务行业中,质量损失函数可以用于评估服务过程中可能出现的问题和不满意度。
质量损失函数的具体形式可以根据具体问题和行业的需求来确定。
一种常见的质量损失函数形式是线性函数,其中质量问题的发生率和严重程度与质量损失呈线性关系。
另一种常见的形式是指数函数,在这种情况下,质量问题的发生率和严重程度与质量损失呈指数关系。
质量损失函数的应用有助于企业进行质量管理和质量改进。
通过对质量损失函数进行分析,企业可以确定造成质量问题的主要原因,并采取相应的措施来减少质量损失。
这包括改进生产过程、优化供应链管理、加强员工培训和质量控制等。
此外,质量损失函数还可以用于评估和比较不同产品或服务的质量水平。
通过分析不同产品或服务的质量损失函数,企业可以了解其在市场中的竞争地位,并制定相应的市场策略。
总之,质量损失函数是一个重要的工具,用于评估和量化产品或服务质量的损失。
通过对质量损失函数进行分析,企业可以识别和解决潜在的质量问题,并通过改进质量管理和质量控制来提高产品或服务的质量水平。
这对企业来说非常重要,因为它可以帮助企业提高客户满意度,增加市场竞争力,进而提高企业的绩效和盈利能力。
qc小组,质量控制点,田口方法,质量损失函数,检验依据

田口质量观--田口方法 •质量定义:产品上市后给社会造成的损失
•提出质量三次设计(系统设计、参数设计、容差设计)
摩托罗拉6σ质量观: •1986年提出6σ管理模式 •出版:《质量控制》、《质量控制指南》
石川磬: •QC小组之父 •出版:《质量控制》、《质量控制指南》
其它质量观
控制用控制图的判断规则
1、控制图上的点子不超在控制界限即在控制范围内; 以上的补充: 连续25点以上处于控制界限内;
连续35点中,仅有1点超出控制界限;
连续100点中,不多于2点超出控制界限;
虽合格,已经要注意异常点
控制图处于控制状态的分析
分析用控制图的判断规则2:没有处于控制状态
点子排列出现异常现象: • 连续7点或更多点在中心线同一侧(7点链); • 连续7点或更多点的单调上升或单调下降(7点单调链) • 连续11点中至少有10点在中心线同一侧; • 连续14点中至少有12点在中心线同一侧; • 连续17点中至少有14点在中心线同一侧; • 连续20点中至少有16点在中心线同一侧; • 连续3点中至少有2点落在二倍标准差与三倍标准差控制 界限之间; I. 连续7点中至少有3点落在二倍标准差与三倍标准差控制 界限之间。
实施全面质量管理的技术
质量检验的依据
•国家质量法律和法规;
•技术标准; •质量承诺; •产品图样; •工艺文件; •技术协议 。
质量检验的依据
1、设计质量控制的重要性 2、田口的质量保证理论
概述
田口质量观:
核心思想是在产品设计阶段就进行质量控制, 将质量与经济性紧密地联系在一起,并用质量 损失函数来表示,使质量变成一种可量化度量 的量。
- 1、下载文档前请自行甄别文档内容的完整性,平台不提供额外的编辑、内容补充、找答案等附加服务。
- 2、"仅部分预览"的文档,不可在线预览部分如存在完整性等问题,可反馈申请退款(可完整预览的文档不适用该条件!)。
- 3、如文档侵犯您的权益,请联系客服反馈,我们会尽快为您处理(人工客服工作时间:9:00-18:30)。
2010.1.1
质量 管理学
二三、、研正究内交容试、验创设新点计
1
正交试验设计的步骤
正交试验的极差分析法的一般步骤是:
(1)定指标,确定因素,选水平; (2)选用适当的正交表,表头设计,确定试验方案; (3)严格按条件做试验,并记录试验结果; (4)计算各列的同一水平的数据和与极差R j; (5)按极差大小排出因素的主次; (6)选取较优生产条件; (7)进行验证性试验,做进一步分析。
2 因子:将试验中要加以考察而改变状态的因素
因子:将试验中要加以考察而改变状态的因素称为因子,如在 工业生产中,影响产品质量的因子有原材料、工艺条件、工人 技术水平等,常用A,B,C等大些英文字母表示。
2010.1.1
质量 管理学
二一、、研基究内本容概、念创新点
3
水平 :把因素变化的各种状态和条件
结构特点: 1、每列有四个“1” ,四个“2” 2、每任意两列的8个数中(横组合)的 (1,1)
(1,2)(2,1)(2,2) 正好各出现两次
常见的还有:L12(211) 、 L16(215) 、 L4(23) 、 L18(37)、L18(21×37) 、 L18(61×36) 、 L12(31×24)等
二第、一研节究内正容、交创试新验点设计
基本概念 正交表及其特点 正交试验设计
2010.1.1
质量 管理学
二一、、研基究内本容概、念创新点
• 20世纪30年代,由于农业试验的需要, 费歇 (R. A. Fisher) 在试验设计和统计分 析方面做出了一系列先驱工作,从此试 验设计成为统计科学的一个分支。
具体的正交试验设计思路及例题答案见教材内容
2010.1.1
质量 管理学
二第、二研节究内质容、量创功新能点展开
质量功能展开的原理 质量屋
2010.1.1
质量 管理学
二一、、研质究内量容功、能创展新点开的原理
1
质量功能展开的定义
目前尚一个没有统一的QFD定义。但对QFD
的一些认识是共同的。
《美国空军R&M2000大纲》对QFD的说明
是:“QFD是保证用户、消费者需求,并能
推动产品设计和生产工序设计改进的一种方
法,也即把用户、消费者需求变换成产品特
性和工序特性,并由全企业来完成这些要求
的系统方法。”
质量
2010.1.1
管理学
二一、、研质究内量容功、能创展新点开的原理
1
质量功能展开的定义
QFD的本质就是要求企业不断地倾听顾客的心声,并通过 合适的方法、采取适当的措施在产品形成的全过程中予以体 现这些顾客的需求。 QFD是在实现顾客需求的过程中,帮助在产品形成过程中 所涉及到的企业各职能部门制订出各自相应的技术要求的实 施措施,并使各职能部门协同地工作,共同采取措施保证和 提高产品质量。 QFD的应用涉及了产品形成全过程的各个阶段,尤其是产 品的设计和生产阶段。被认为是一种在产品开发阶段进行质 量保证的方法。
2010.1.1
质量 管理学
二三、、研正究内交容试、验创设新点计
2
正交试验设计的例子
【例5-2】 某工厂为了提高产品的转化率,决定进行试 验,寻找较好(或最好)的生产工艺条件。根据历史资料, 认为影响转化率的因素可能有四个,分别是反应温度 (℃)、反应时间(分)、用碱量(㎏)和反应压力 (个大气压),依次记为A、B、C和D(设因素之间 没有交互作用)。由经验,确定了各因素的三个不同 水平,见表5-2。问应如何安排试验?
2010.1.1
质量 管理学
二三、、研正究内交容试、验创设新点计
2
正交试验设计的例子
【例5-2】 某工厂为了提高产品的转化率,决定进行试 验,寻找较好(或最好)的生产工艺条件。根据历史资料, 认为影响转化率的因素可能有四个,分别是反应温度 (℃)、反应时间(分)、用碱量(㎏)和反应压力 (个大气压),依次记为A、B、C和D(设因素之间 没有交互作用)。由经验,确定了各因素的三个不同 水平,见表5-2。问应如何安排试验?
2010.1.1
质量 管理学
二二、、研正究内交容表、及创其新点特点
1
正交表
正交表是一些已经制作好的规格化的表, 是正交实
验设计的基本工具,它给出了各种因素和水平的代表 性很强的实验组合。
正交表代号
表的纵向列数 (因素数)
L8(27)
表的横行数 (试验数)
表的字码数 (位级数)
2010.1.1
质量 管理学
• 20世纪60年代,日本统计学家田口玄一 将试验设计中应用最广的正交设计表格 化
2010.1.1
质量 管理学
二一、、研基究内本容概、念创新点
1
试验指标:衡量试验条件好坏的特性
试验指标 :衡量试验条件好坏的特性(可以是质量特性也可以 是产量特性或其它)称为指标,它是一个随机变量。为了方便 起见,常用x表示。
水平 :因子在试验中所取得状态称为水平,如果一个因子在 试验中取k个不同状态,就称该因子有k个不同水平。因子A 的k个水平常用A1, A2,…Ak表示。
4
正交试验设计
所谓正交试验设计,就是利用一套现成的规格化的表—正交 表来安排多因素试验,并对试验结果进行统计分析,找出较 优(或最优)试验方案的一种科学方法。
二二、、研正究内交容表、及创其新点特点
L8(27)表
列行 1 2 3 4 5 6 7
号
1 1111111 2 1112222 3 1221122 4 1222211 5 2121212 6 2122121 7 2211221 8 2212表、及创其新点特点
2010.1.1
质量 管理学
二一、、研质究内量容功、能创展新点开的原理
2
QFD瀑布式分解模型
实施QFD的关键是将顾客需求分解到产 品形成的各个过程,将顾客需求转换成 产品开发过程具体的技术要求和质量控 制要求。通过对这些技术和质量控制要 求的实现来满足顾客的需求。
2010.1.1
质量 管理学
二二、、研正究内交容表、及创其新点特点
2
正交表的特点
均衡分散性 能够较全面地反映出试验的结果,试验结果得好点, 即使不是最好点,也是相当好的点和相当好的生产 条件。 整齐可比性 多因素的可比,在一个因素处于一种位级时,其他 各种因素的位级变化是有规律的和均匀的。对一种 因素的对比,找出级差,确定它处于是否是主要因 素,可看出灵敏度的问题。