轮胎生产过程中常见问题点及解决方案
26872641_半钢子午线轮胎断面常见缺陷原因分析及解决措施

作者简介:刘国英(1981-),工程师,主要负责半钢钢子午线轮胎成型工艺管理方面的工作。
收稿日期:2021-05-31半钢子午胎的部分缺陷无法通过外观检查及机检发现,而这些缺陷却可以通过轮胎断面发现,轮胎断面的尺寸对轮胎的均匀性、高速、耐久等使用性能起到至关重要的作用,为此本文对常见的半钢子午胎断面缺陷原因进行分析,并提出相应的解决措施。
1 带束层波浪带束层是子午线轮胎的重要部件,影响着轮胎的诸多性能。
带束层波浪如图1所示,严重的带束层波浪可导致胎里不平废品,外观检查中容易发现,但是轻微的带束层波浪,很难从外观检查中发现,一旦流入市场,将影响轮胎的耐久性、抓地性以及乘坐舒适性能等。
图1 带束层波浪1.1 原因分析(1)胎冠形状、厚度、长度设计不合理。
胎冠厚度不合理,轮胎硫化充满模具后,冠部厚度厚的部位带束层外凸,冠部厚度不足的部位带束层内凹;胎冠形状设计不合理也可导致带束层波浪,以沟槽平台结构的胎冠形状最为明显,半成品胎冠形状与模具形状不吻合,如胎冠的平台位置与模具的沟槽位置贴合,带束层将外凸。
半钢子午线轮胎断面常见缺陷原因分析及解决措施刘国英,张凤杰,赵辉(桦林佳通轮胎有限公司,黑龙江 牡丹江 157032)摘要:分析半钢子午胎断面常见缺陷的产生原因,并提出相应的解决措施。
带束层波浪、冠带层打褶、材料端点集中、耐磨胶打褶可通过优化结构设计、生产过程的合理管控,设备及工艺参数确定,标准作业执行等措施解决此问题。
关键词:半钢子午线轮胎;结构设计;带束层波浪;冠带层打褶;材料端点集中;耐磨胶打褶中图分类号:TQ330.491文章编号:1009-797X(2022)04-0039-04文献标识码:B DOI:10.13520/ki.rpte.2022.04.008(2)二段胎胚生胎外周过大。
成型二段轮胎的生胎外周大大超越了模具的花纹沟底周长,硫化时,在合模力的作用下,胎肩过剩的材料就会流向胎面中部,造成整个轮胎断面成拱形,带束层成波浪状。
翻新轮胎存在问题及整改措施

翻新轮胎存在问题及整改措施一、问题描述:翻新轮胎是指将旧轮胎经过一系列工艺处理后重新使用的轮胎,其主要目的是延长轮胎的使用寿命,降低成本。
然而,在翻新轮胎的过程中,存在一些常见问题,需要采取相应的整改措施来解决。
1. 胎面不均匀磨损:翻新轮胎在使用过程中,由于胎面磨损不均匀,可能导致轮胎在行驶过程中产生不稳定的情况,影响行车安全。
2. 胎纹深度不足:胎纹深度是轮胎与地面之间的重要接触面,对于车辆的抓地力和制动性能至关重要。
如果翻新轮胎的胎纹深度不足,可能导致车辆在湿滑路面上的抓地力不足,增加行车风险。
3. 轮胎内部结构损伤:翻新轮胎在使用过程中,由于内部结构的损伤,可能导致轮胎在行驶过程中出现爆胎等严重安全问题。
4. 胎面与胎体粘接不良:翻新轮胎的胎面与胎体之间的粘接质量直接影响轮胎的使用寿命和安全性能。
如果粘接不良,可能导致胎面脱落,造成危险。
二、整改措施:为了解决翻新轮胎存在的问题,以下是一些常见的整改措施:1. 加强生产质量管理:制定严格的翻新轮胎生产标准,确保每个环节都符合质量要求。
加强对原材料的检测和选择,确保使用的原材料符合相关标准。
2. 提高工艺技术水平:加强对翻新轮胎生产工艺的研发和改进,引进先进的生产设备和技术,提高轮胎的整体质量和性能。
3. 加强质量检测:建立完善的质量检测体系,对翻新轮胎进行全面、严格的检测。
包括胎面均匀磨损检测、胎纹深度检测、轮胎内部结构检测等。
4. 提高胶料质量:选择高质量的胶料,确保胎面与胎体之间的粘接质量。
加强胶料的储存和使用管理,防止胶料老化或污染。
5. 加强售后服务:建立健全的售后服务体系,及时解决用户反馈的问题。
对于出现质量问题的翻新轮胎,及时进行召回和更换。
6. 加强宣传教育:加强对用户的宣传教育,提高用户对翻新轮胎的认知和使用技巧,引导用户正确使用和保养翻新轮胎。
三、总结:翻新轮胎存在问题及整改措施是为了解决翻新轮胎在使用过程中可能出现的安全隐患和质量问题。
子午线轮胎胎体稀线不良率的解决对策

作者简介:章远甲(1984-),男,本科,助理工程师,主要从事半钢轮胎生产质量管理和工艺研究。
收稿日期:2020-09-111 问题简介1.1 胎体帘稀线的危害半钢子午线轮胎胎体稀线问题是轮胎生产制造过程中的常见缺陷,影响轮胎安全使用性能,严重时诱发轮胎漏气、断裂爆胎等质量问题发生。
1.2 胎体稀线问题现况胎体稀线是轮胎生产过程中的常见问题,该缺陷主要集中在轮胎生产过程中的成型、硫化环节。
2019年市场售后反馈中因帘布稀线问题导致的问题占比59.5%(稀线问题264条,其他问题180条)。
胎体稀线问题(图1、图2)给企业造成巨额经济损失的同时也严重影响了产品质量信誉,所以解决胎体稀线问题是公司当前重要的工作之一。
图1 稀线缺陷1.3 工序简介轮胎生产流程如图3所示。
子午线轮胎胎体稀线不良率的解决对策章远甲,路丹丹,李海艳(山东丰源轮胎制造股份有限公司,山东 枣庄 277300)摘要:本文主要分析轮胎生产过程中常见的胎体稀线这一质量问题,分析该缺陷主要集中的成型、硫化两个环节。
通过进行可行性,制定相应的措施,结合问题,采用 “5M1E ”分析法,对人、机、料、法、测五个方面进行研究,采用制作关联图的方式对产生此类质量问题的末端因素进行分析。
措施开展后,2020年废品率逐月下降,效果明显,因稀线问题导致的废品率由2019年的0.8‰,降低到2020年5月份的0.23‰,1~5月份节约7.7万元。
关键词:轮胎;胎体稀线;5M1E ;废品中图分类号:TQ336.1文章编号:1009-797X(2021)05-0052-06文献标识码:B DOI:10.13520/ki.rpte.2021.05.0112 选题依据从上级要求、生产现状两个主要方面确定课题的选定,如图4所示。
图2 稀线诱发的质量问题图3 轮胎生产流程3 对目标的可行性分析3.1 掌握现状对市场反馈的质量问题进统计,将数据绘制成排列图后进行分析。
轮胎行业质量培训 子午胎质量缺陷及原因分析 轮胎缺陷分析

胎圈部位
★子口部位露线
1、缺陷描述: 轮胎子口部位一侧或两侧有胎体帘线露
出的现象。 2、缺陷原因及纠正办法: 1)缺胶缺料
—检查胎侧宽度和定位(可能非常窄 或定位出差错)
2)帘线伸张过大 —检查帘线压延张力 —检查机头宽度,必要时增加。 3)生胎在模型中定位出差错 —检查装胎器定中情况 4)硫化胶囊膨大 —检查硫化胶囊情况如必要加以更换
漏 —检查中心机构有无蒸汽泄漏 4)胎体帘布不正常 —检查帘布中胶料渗入帘线的情况,厚度
重量 —把帘布裁断时或压延时不正常部分剔出
报废 5)在二段时定型压力过大 —检查二段成型机的定型压力
13
胎里部位
★胶囊打折
1、缺陷描述: 因硫化胶囊打折(局部伸张不好)轮胎胎里出现下述
夹挤痕迹:1)橡胶;2)胶与胎体帘线。 2、缺陷原因及纠正办法: 1)胶囊规格出错 —检查硫化胶囊尺寸是否符合规定(可能硫化胶囊太
6
胎圈部位
★子口撕裂
1、缺陷描述: 轮胎子口部位在下列部位出
现撕裂现象: 1)橡胶部分; 2)橡胶和帘布 2、缺陷原因及纠正办法: 1)硫化机动作不正常 —检查卸胎顺序 —检查抽真空效果 2)修边时受到损伤 —检查修边工具及工艺过程
7
胎圈部位
★子口变形
1、缺陷描述: 轮胎子口部位出现径向及侧向周长
·一般必须提高前10个周期的预定型和 定型压力
5)生胎喷涂欠量 —送生胎去重新喷涂
24
胎里部位
★胎里肩部周向裂口
1、缺陷描述: 轮胎胎里肩部周向裂口 。 2、缺陷原因及纠正办法: 1)周向裂口 —检查成型机头 —压延帘线品种和性能
25ቤተ መጻሕፍቲ ባይዱ
胎侧部位
★胎侧缺胶
轮胎生产过程中常见问题点及解决方案

缺陷名称
造成原因
预防措施
胎面缺胶(花纹、 1. 主要是胎面胶料流动性差; 1. 提高胎面胶料的可塑度
胎肩、胎侧)
2. 胎面形状不合适;
2. 改进胎面押出口金的形状
3. 胎面厚薄不均匀;
3. 严格执行工艺技术标准
4. 硫化内压低或不足;
4. 提高硫化内压
5. 模型太脏;
5. 定期清洗模型,适当涂刷润滑剂
初始加料温度有差异;冷却水流动和(或)温度有差异;上顶栓压力有 差异;配合剂称量中 有误差;不同批号之间配合剂的差异;使用替用用配合剂;排胶时间和 (或)排胶温度的变 化;不同的操作者采用不同的方法在压片机上加工胶料;捣胶时间的变化;分散程度不同。 辊温选用不当;辊温和辊筒速比及辊筒速度的控制失灵;胶料的门尼粘度太低;增粘剂过量; 粘性填充剂(如陶土)填充量过高;粘性增塑剂量太大;配方中缺少适 当的操作助剂;装料 不足或过量;弹性体的粘度选择错误;分散不良;胶料易焦烧;胶料留 在开炼机上的时间太 长。
或缩短
硬度过高、过低 或不均匀 喷霜 硫化起点慢 欠硫 分层 粘辊或脱辊
污染
物理机械性能 不合格或不一 致 各批胶料间性 能差异 压延性能差
促进剂品种弄错、少加;氧化锌漏加;炭黑品种弄错,软化剂品种弄错;陶土多加。 B.焦烧时间缩短
促进剂多加或品种搞错;炭黑品种用错;碳酸钙过量。 配合剂称量不准,如补强剂、硫化剂和促进剂称量过多,则硫化胶硬度 偏高;相反,则硬度 偏低;增塑剂和橡胶称量过多,则硬度偏低;混炼不均匀,硫化胶硬度不均。 胶料混炼不足、不均匀;配合剂称量不准;硫黄结团或用量超过其常温 在橡胶中的溶解度; 加硫时胶温过高;软化剂用量过多;胶料停放时间过长;制品欠硫等。 促进剂称量不准,(过少)或漏加氧化锌或硬脂酸;炭黑品种搞错。 促进剂、硫化剂和氧化锌等漏配或少配;混炼操作不当,硫化剂和促进剂飞扬损失过多。 天然橡胶胶料中混入丁基胶或相反。(或 PE 膜熔点过高,未分散完全) A.粘辊
汽车轮胎生产过程中的质量控制

汽车轮胎生产过程中的质量控制随着汽车产业的发展,汽车轮胎作为汽车的重要组成部分,其质量也成为了消费者关注的重点。
对于厂商而言,确保产品质量不仅能增强企业竞争力,更能提高消费者满意度。
因此,针对汽车轮胎生产过程中的质量控制,厂商们日益重视,采用了一系列的技术手段保证了汽车轮胎的质量。
一、材料选用与检测作为汽车轮胎的主要材料,橡胶的质量对于轮胎的性能至关重要。
并且,不同的橡胶需要选择不同的硫化剂、促进剂以及填料等成分。
在材料选用时,厂商需仔细选择材料的供应商,避免材料出现质量问题。
同时,在使用材料前,厂商需要对该批材料进行一系列的检测,以判断材料的质量是否符合要求。
例如,对于橡胶,则需进行拉伸强度、硬度、磨损等指标的测试,以确保材料的质量。
二、模具制造与维护对于轮胎的成型而言,模具的质量和维护也非常重要。
毫无疑问,模具的制造需要选取优质的材料并结合先进的制造工艺。
不仅如此,在模具的维护方面,厂商也要时刻注意模具表面状态。
如果模具表面存在划痕等问题,则可能导致轮胎成型时的凹痕毛刺等质量问题。
为缓解这个问题,厂商们采用了数字化模具制造技术,以提高模具制造的精度和质量。
三、质量监控在汽车轮胎的生产过程中,厂商需要控制各个环节的产品质量。
因此,汽车轮胎生产厂商采用了多种质量监控手段。
例如,通过使用自主生产的测试装置,对轮胎的静态和动态平衡性能进行检测,以保证轮胎在高速行驶时的平稳性。
其次,对于轮胎的尺寸、硬度、密度等数据,厂商也会采用雷射测量、X光成像等先进技术进行检测。
通过对轮胎的质量进行多个维度的监控,企业可以减少产品缺陷和召回问题,提高企业形象和消费者认可度。
四、人员培训与材料、模具等因素相比,人员因素在轮胎生产中也占有重要地位。
为确保生产人员掌握相关技能,厂商需要对其进行专业的培训。
该培训包括橡胶工艺、模具的使用和维护、产品质量检测等方面。
通过这些培训,厂商可以提高员工业务水平和生产技能,从而提高产品质量,减少不必要的管理费用。
轮胎的常见问题及成因分析

轮胎的常见问题及成因分析一、一般质量问题的分析1、胎冠出胶边也称为流失胶边,是硫化时上下模合缝口不严所造成的胎面胶流出而形成的胶边,这是由于高压不稳定或掉压所引起。
2、胎冠出沟在胎面冠部形成沟状下凹因内压过热水压力下降所造成。
3、花纹错位上下模型花纹不能吻合,是模型安装时上下模没有对准花线或稳钉而引起。
4、花纹和模缝毛边是由于花纹和模型间有缝隙胶料流进缝隙间而产生的。
5、花纹棱角或缺胶成圆角主要是模型排气孔阻塞并窝藏了空气而形成花纹圆角,内压不足也会产生此类毛病。
6、胎冠侧部表面杂质或气泡表面杂质是胎坯或模型受到污染,气泡则是半成品有空气聚集,硫化出模后空气膨胀而产生的表面气泡。
7、胎侧重皮或裂口产生原因为胎侧部隔离剂涂擦过多过浓,半成品形状与模具不相吻合以及胶料流动过大等。
8、胎侧缺胶亦称为明疤,模型积水未吹干或模温过高升温过快等均会引起此类毛病。
9、胎圈凹凸不平由于水胎牙子凹凸不平或包布不平所引起。
10、胎圈包布打褶翘起或破损由于胎坯包布松散没有整修就进模硫化或出模不当刮坏所致。
11、胎圈出边产生原因与上一条相似,如果水胎牙子老化变宽也能造成这些毛病。
12、胎圈宽窄不一主要是半成品不按施工标准操作所致,如果布筒长度不足,成型第一个布筒时没有用成型棒致成型鼓张口处伸张过大,帘布宽度局部变窄造成局部材料不足,又如水胎或胶囊定型定歪也会产生这种毛病。
13、胎圈成圆形主要发生在以水胎定型硫化的外胎上,是由于水胎进出水嘴子漏水或牙子部漏水所致。
橡胶技术网14、第一层帘线裂缝因胎里隔离剂带水分或水胎沾有水分油污等,硫化时这些水分在压力作用下把胎里油皮胶挤破把帘线挤疏成裂缝状,严重的第二层帘线也受影响。
15、第一层帘线弯曲也叫帘线打弯,主要是帘线伸张不足造成,如施工设计不当或成型鼓宽度过宽,如用错成型鼓等均能引起该毛病。
16、胎里帘线凹凸不平主要是胎里杂质,或因水胎舒展不开产生打褶造成的,越野花纹或拖拉机人字花纹允许有凹坑故不在此例。
全钢载重子午线轮胎质量缺陷问题分析
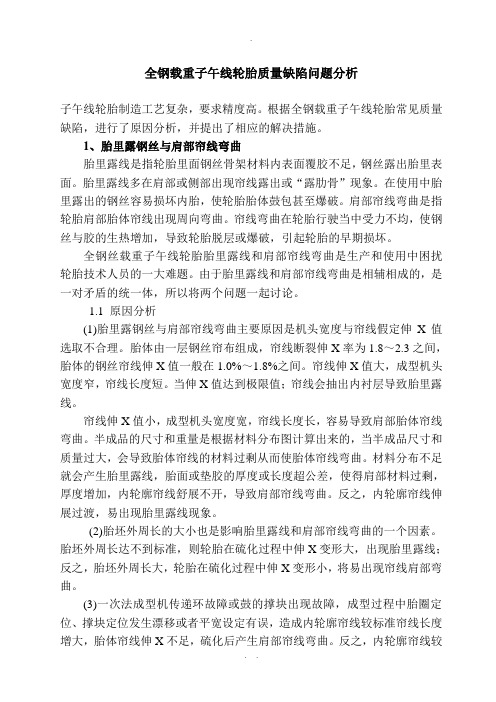
全钢载重子午线轮胎质量缺陷问题分析子午线轮胎制造工艺复杂,要求精度高。
根据全钢载重子午线轮胎常见质量缺陷,进行了原因分析,并提出了相应的解决措施。
1、胎里露钢丝与肩部帘线弯曲胎里露线是指轮胎里面钢丝骨架材料内表面覆胶不足,钢丝露出胎里表面。
胎里露线多在肩部或侧部出现帘线露出或“露肋骨”现象。
在使用中胎里露出的钢丝容易损坏内胎,使轮胎胎体鼓包甚至爆破。
肩部帘线弯曲是指轮胎肩部胎体帘线出现周向弯曲。
帘线弯曲在轮胎行驶当中受力不均,使钢丝与胶的生热增加,导致轮胎脱层或爆破,引起轮胎的早期损坏。
全钢丝载重子午线轮胎胎里露线和肩部帘线弯曲是生产和使用中困扰轮胎技术人员的一大难题。
由于胎里露线和肩部帘线弯曲是相辅相成的,是一对矛盾的统一体,所以将两个问题一起讨论。
1.1 原因分析(1)胎里露钢丝与肩部帘线弯曲主要原因是机头宽度与帘线假定伸X值选取不合理。
胎体由一层钢丝帘布组成,帘线断裂伸X率为1.8~2.3之间,胎体的钢丝帘线伸X值一般在1.0%~1.8%之间。
帘线伸X值大,成型机头宽度窄,帘线长度短。
当伸X值达到极限值;帘线会抽出内衬层导致胎里露线。
帘线伸X值小,成型机头宽度宽,帘线长度长,容易导致肩部胎体帘线弯曲。
半成品的尺寸和重量是根据材料分布图计算出来的,当半成品尺寸和质量过大,会导致胎体帘线的材料过剩从而使胎体帘线弯曲。
材料分布不足就会产生胎里露线,胎面或垫胶的厚度或长度超公差,使得肩部材料过剩,厚度增加,内轮廓帘线舒展不开,导致肩部帘线弯曲。
反之,内轮廓帘线伸展过渡,易出现胎里露线现象。
(2)胎坯外周长的大小也是影响胎里露线和肩部帘线弯曲的一个因素。
胎坯外周长达不到标准,则轮胎在硫化过程中伸X变形大,出现胎里露线;反之,胎坯外周长大,轮胎在硫化过程中伸X变形小,将易出现帘线肩部弯曲。
(3)一次法成型机传递环故障或鼓的撑块出现故障,成型过程中胎圈定位、撑块定位发生漂移或者平宽设定有误,造成内轮廓帘线较标准帘线长度增大,胎体帘线伸X不足,硫化后产生肩部帘线弯曲。
实心轮胎生产过程中常见的质量问题和解决方法

实心轮胎生产过程中常见的质量问题和解决
方法
哇塞,实心轮胎啊,这可是个很重要的东西呢!那咱就来好好聊聊实心轮胎生产过程中常见的质量问题和解决方法吧!
生产实心轮胎,那可不是随随便便就能搞定的事儿!首先得选好材料,就像做饭得挑好食材一样,这可不能马虎!然后在加工过程中,要严格控制温度、压力等各种参数,稍有偏差可能就会出问题。
还有啊,模具的设计和维护也超级重要,这就好比是给轮胎塑造一个完美的“家”。
在操作的时候,工人们得打起十二分精神,小心翼翼地进行每一个步骤,不能有一丝懈怠呀!注意这些点,才能生产出高质量的实心轮胎呢!
在这个过程中,安全性和稳定性那是必须要保证的呀!想想看,如果生产过程中出了什么岔子,那多吓人啊!所以每一个环节都要严格把关,不能有任何疏漏。
就像走钢丝一样,必须稳稳当当的,稍有不慎就可能掉下去啦!只有这样,才能让我们放心地使用这些实心轮胎呀!
实心轮胎的应用场景那可多了去了!比如在一些恶劣的环境下,像工地啦、矿山啦,它们就能大显身手啦!它们的优势也很明显呀,耐磨损、不怕扎,就像一个坚强的小战士!这可比普通轮胎厉害多了吧!而且它们还能承载更重的重量,这多了不起呀!
我就知道一个实际案例,有个工厂之前用的普通轮胎老是出问题,不是爆胎就是磨损得厉害。
后来换成了实心轮胎,哇,那效果简直太棒啦!生产效率大大提高了,也不用担心轮胎出问题影响工作啦!这可真是实实在在的好处呀!
所以呀,实心轮胎生产真的很重要,我们一定要重视质量问题,找到解决方法,这样才能让实心轮胎更好地为我们服务呀!。
翻新轮胎存在问题及整改措施

翻新轮胎存在问题及整改措施一、问题描述翻新轮胎是指对原有轮胎进行翻新处理,以延长其使用寿命和降低成本。
然而,在翻新轮胎的过程中,可能会出现一些问题,影响其质量和安全性。
以下是翻新轮胎常见的问题:1. 翻新层附着力不足:翻新轮胎的翻新层附着力不足会导致翻新层与轮胎胎面的脱层现象,增加轮胎在使用过程中的风险。
2. 翻新层质量不合格:翻新层的质量不合格可能会导致轮胎在使用过程中出现破裂、爆胎等安全隐患。
3. 胎面花纹设计不合理:翻新轮胎的胎面花纹设计不合理可能会导致轮胎在湿滑路面上的抓地力下降,增加了车辆行驶的风险。
4. 轮胎平衡不良:翻新轮胎在使用过程中可能出现平衡不良的问题,导致车辆在高速行驶时产生震动,影响驾驶的舒适性和安全性。
二、整改措施为解决翻新轮胎存在的问题,以下是一些整改措施的建议:1. 加强翻新层附着力:在翻新轮胎的翻新层制作过程中,应确保翻新层与轮胎胎面之间的附着力充分,可以采用合适的胶水和工艺来提高附着力。
2. 严格控制翻新层质量:对于翻新轮胎的翻新层,应严格按照相关标准进行质量控制,确保翻新层的强度、密度等指标符合要求,降低轮胎出现安全隐患的可能。
3. 合理设计胎面花纹:在翻新轮胎的胎面花纹设计上,应考虑不同路面条件下的抓地力需求,合理选择花纹类型和深度,提高轮胎在湿滑路面上的抓地力,减少潜在的安全风险。
4. 精确平衡轮胎:在翻新轮胎安装后,应进行精确的轮胎平衡调整,确保轮胎与车轮的质量分布均匀,减少车辆在高速行驶时的震动,提高驾驶的舒适性和安全性。
5. 强化质量监控:对于翻新轮胎的整个生产过程,应建立严格的质量监控体系,包括原材料采购、生产工艺控制、成品检测等环节,确保翻新轮胎的质量符合相关标准和要求。
6. 加强售后服务:对于已经销售出去的翻新轮胎,厂家应加强售后服务,及时解决用户反馈的问题,确保用户的使用安全和满意度。
通过以上整改措施的实施,可以有效解决翻新轮胎存在的问题,提高翻新轮胎的质量和安全性,保障车辆行驶的安全。
实心轮胎生产过程中常见的质量问题和解决方法

实心轮胎生产过程中常见的质量问题和解决方法宋国星,左义军,路瑞彪,张 烁,冯瑞东,冯守贤[YOKOHAMA TWS特瑞堡轮胎工业(河北)有限公司,河北邢台054000]摘要:分析实心轮胎生产过程中常见的质量问题,并提出相应的解决方法。
常见的质量问题主要包括轮胎表面气泡、胎侧重皮、橡胶与金属粘合不良、表面撕裂和胶须断裂、变色、花纹块窝气、冠部裂口、冠部露中间层,通过调整操作工艺规程,使操作标准化、制度化、稳定化,及对出现问题较多的规格产品制定专用生产工艺,重新确定硫化条件,调整和优化胶料配方硫化速率匹配性等措施,成品轮胎一次合格率由99.1%提高到99.8%,退赔率由0.2%降低到0.05%。
关键词:实心轮胎;质量问题;外观缺陷;解决方法中图分类号:TQ336.1+3;U463.341+.5 文章编号:2095-5448(2024)01-0030-07文献标志码:A DOI:10.12137/j.issn.2095-5448.2024.01.0030实心轮胎以不需要充气、不存在刺穿漏气、负荷下变形小、载荷量大、启动阻力小以及使用维修方便等优点而广泛应用于叉式起重机和载货拖车等工程机械车辆上,尤其适用于易燃易爆环境及苛刻路面低速高载环境,而充气轮胎无法满足这些使用环境和车辆的要求。
实心轮胎按材料可以分为橡胶实心轮胎、聚氨酯轮胎和填充轮胎。
实心轮胎是非公路型轮胎,结构特殊,为避免轮胎使用过程中因过热导致损坏,不得用于公路运输及超速、长距离、长时间连续运行。
实心轮胎生产工艺精简,硫化是其重要的工序,虽然很多问题出现在硫化工序,但实际上与前面工序有着密切的关系,甚至与设计也存在着本质的关联。
根据多年的工作经验,本研究主要介绍橡胶实心轮胎(以下简称实心轮胎)在硫化工序中呈现出来的主要问题,分析问题产生的原因,并提出相应的解决方法[1-5]。
1 胶层气泡或脱层实心轮胎气泡问题主要出现在胎冠,局部有明显鼓泡现象,轻者用手按压有回弹感,一般不会很深,如图1所示;严重的鼓泡(见图2)是按压不动的,无回弹感,切开断面后会发现其在偏中心位置,且至少有2层胶片脱开,伴有蜂窝状气孔。
实芯轮胎常见质量问题及解决措施

* 中图分类号: $ % & & ’ ( ) &
文献标识码: +
文章编号: ( ) ) " " ’ , # ) ) ! " " ! " . , " ! & / , " &
实芯轮胎由于具有高负荷能力、 耐刺扎、 行驶 平稳、 无需经常修补等优点而在各类搬运叉车和 拖车等车辆上广泛应用。实芯轮胎分为轮辋式和 压配式两种。 轮辋式实芯轮胎由耐磨的胎面层、 起缓冲作 用的中间层和能紧固轮辋并支撑轮胎负荷的高模 量基部层组成。其中高弹性缓冲层可在轮胎行驶 时有效地吸收因地面不平而引起的车辆跳动, 使 负荷量和速度达到极限时轮胎仍能保持良好的稳 定性和低生热性; 基部层由具有高模量、 高硬度、 低扯断伸长率和扯断永久变形的胶片组成, 在接 近轮胎内径处配置高强度金属圈, 使轮胎压入轮 辋后不产生打滑, 支撑整个轮胎。 压配式实芯轮胎在使用时压入同规格轮辋即 可, 它包括内外两层, 其中内层由将钢板卷成规定 内径尺寸经焊接的钢圈或车削铸钢件组成; 外层 为胎面。 实芯轮胎的胎面厚度一般为充气工程机械轮 胎的)倍以上, 轮辋式实芯轮胎中因有弹性层的 支撑, 故胎面的有效使用率为 ) 而压配式实 " " 0, 芯轮胎胎面的有效使用率仅为 " 0 !1 0。胎 面胶不仅要耐磨, 而且应具有较低的滚动阻力, 以 降低车辆行驶中的能量损耗及驱动时的功率消 耗, 同时胎面的接地面积越大, 地面承受的单位压 力越小, 使轮胎更具有经济性。
全钢工程胎常见质量缺陷、产生原因及解决措施

全钢工程胎常见质量缺陷、产生原因及解决措施全钢工程胎常见质量缺陷、产生原因及解决措施(草稿)一、常见内在质量缺陷(X光检验)1、带束层1.1、差级不均或齐边带束层差级不均或齐边,会使轮胎两侧肩部材料分布不均,造成轮胎行驶时受力不均,较厚的一侧生热大,易产生脱空;较薄的一侧易发生肩部裂开。
产生原因:①辅助鼓的定中心装置错误,灯光标尺偏离中心线。
②带束层部件喷霜、粘合性能差,滚压时造成移位。
③成型定型时压力及宽度不合格,使胎体与带束层定型时差合不上,滚压胎冠时造成带束层偏歪。
④带束层斜边长度不合格或带束层宽窄不一。
解决措施:①检查辅助鼓定中心装置,灯光标尺必须定位于中心,供料架不许偏歪。
②带束层部件喷霜及粘合性能差的,甩出不使用。
③检查成型定型压力及宽度,不符合施工标准的应及时调整。
④对于带束层斜边长度不合格或宽窄不一的部件要甩出不使用。
1.2散线带束层断线后用胶条包边,其主要目的:一是裁断后至成型前防止帘线端边受潮;二是避免钢帘布端头处松散和提高裁断后端部与其它部件的粘合性。
散线主要产生在第二、三层带束层,带束层散线的轮胎在行驶中易局部生热大,产生脱层。
产生原因:①成型后压辊定位偏高,低压设定不合理,滚压时高压使用过早。
②带束层粘性差,不能很好地与其它带束层成为一体,在滚压时产生移位。
③垫胶贴合偏移或左右贴反。
④垫胶过薄。
⑤胎冠肩部超厚。
解决措施:①成型操作前要检查平面宽度是否符合工艺要求,防止因扇形块风压不稳定而引起组合件移位。
②调整设定好定型风压,使其符合工艺要求。
③滚压胎冠时,检查后压辊的位置,使用低风压或高风压时要掌握好风压及滚压时间。
④贴合带束层时,第二、三层带束层接头后压实,并用胶片对两侧端点包边。
⑤校正供料架、灯标(贴合部件手工加以调整)。
贴合垫胶时要注意,梯形长斜面靠向外侧。
⑥过薄的垫胶停止使用。
⑦胎冠肩部超厚停止使用。
2、胎体2.1接头开接头开主要是指钢丝帘布接头拼接不牢,在成型充气膨胀和硫化内压的作用下,拼接不牢的部位断裂开缝,缺少钢丝。
汽车轮胎的突出质量问题与解决措施建议
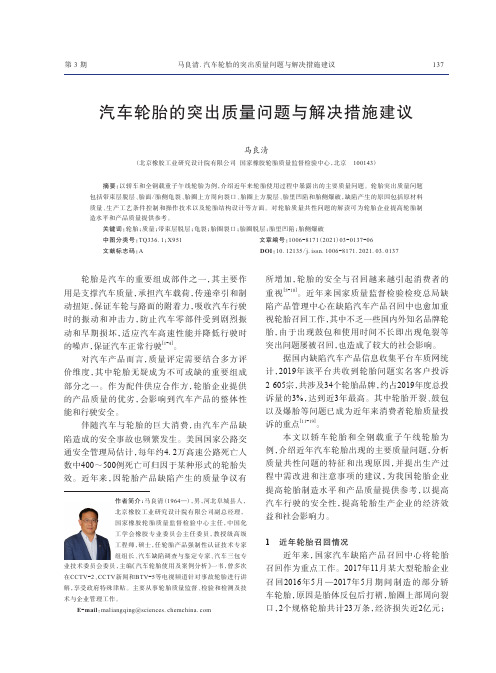
汽车轮胎的突出质量问题与解决措施建议马良清(北京橡胶工业研究设计院有限公司 国家橡胶轮胎质量监督检验中心,北京 100143)摘要:以轿车和全钢载重子午线轮胎为例,介绍近年来轮胎使用过程中暴露出的主要质量问题。
轮胎突出质量问题包括带束层脱层、胎面/胎侧龟裂、胎圈上方周向裂口、胎圈上方脱层、胎里凹陷和胎侧爆破,缺陷产生的原因包括原材料质量、生产工艺条件控制和操作技术以及轮胎结构设计等方面。
对轮胎质量共性问题的解读可为轮胎企业提高轮胎制造水平和产品质量提供参考。
关键词:轮胎;质量;带束层脱层;龟裂;胎圈裂口;胎圈脱层;胎里凹陷;胎侧爆破中图分类号:TQ336.1;X951 文章编号:1006-8171(2021)03-0137-06文献标志码:A DOI :10.12135/j.issn.1006-8171.2021.03.0137轮胎是汽车的重要组成部件之一,其主要作用是支撑汽车质量,承担汽车载荷,传递牵引和制动扭矩,保证车轮与路面的附着力,吸收汽车行驶时的振动和冲击力,防止汽车零部件受到剧烈振动和早期损坏,适应汽车高速性能并降低行驶时的噪声,保证汽车正常行驶[1-4]。
对汽车产品而言,质量评定需要结合多方评价维度,其中轮胎无疑成为不可或缺的重要组成部分之一。
作为配件供应合作方,轮胎企业提供的产品质量的优劣,会影响到汽车产品的整体性能和行驶安全。
伴随汽车与轮胎的巨大消费,由汽车产品缺陷造成的安全事故也频繁发生。
美国国家公路交通安全管理局估计,每年约4.2万高速公路死亡人数中400~500例死亡可归因于某种形式的轮胎失效。
近年来,因轮胎产品缺陷产生的质量争议有所增加,轮胎的安全与召回越来越引起消费者的重视[5-10]。
近年来国家质量监督检验检疫总局缺陷产品管理中心在缺陷汽车产品召回中也愈加重视轮胎召回工作,其中不乏一些国内外知名品牌轮胎,由于出现鼓包和使用时间不长即出现龟裂等突出问题屡被召回,也造成了较大的社会影响。
汽车轮胎常见的故障及维修方法

汽车轮胎常见的故障及维修方法导语:作为一名专业销售人员,了解和掌握汽车轮胎常见的故障及维修方法是至关重要的。
本文将介绍几种常见的轮胎故障,并提供一些实用的维修方法,以帮助车主更好地解决问题。
第一部分:胎压问题胎压不足是最常见的轮胎故障之一。
胎压不足会导致轮胎磨损不均匀,增加燃油消耗,并可能引发爆胎等危险情况。
车主可以通过以下方法解决胎压不足的问题:1. 定期检查胎压:建议车主每个月检查一次轮胎的胎压,确保胎压符合汽车制造商的建议数值。
2. 使用胎压计:车主可以购买一个胎压计,随时检查轮胎的胎压,并在需要时进行充气。
3. 充气站:如果车主不方便自行充气,可以选择去加油站或汽车维修店的充气站进行充气。
第二部分:胎面磨损胎面磨损是另一个常见的轮胎故障。
胎面磨损不仅会影响行驶安全性,还会降低汽车的操控性能。
以下是几种常见的胎面磨损情况及其维修方法:1. 磨损不均匀:如果轮胎的胎面磨损不均匀,可能是由于悬挂系统问题或轮胎定位不正确引起的。
车主应及时进行轮胎定位和悬挂系统的检查和维修。
2. 磨损过度:如果轮胎的胎面磨损过度,可能是由于行驶过长时间或胎压不足引起的。
车主应及时更换磨损过度的轮胎,并保持适当的胎压。
第三部分:胎侧磨损胎侧磨损是指轮胎的侧面出现磨损,通常是由于车辆转弯时过度摩擦引起的。
以下是几种常见的胎侧磨损情况及其维修方法:1. 内侧磨损:如果轮胎的内侧出现磨损,可能是由于悬挂系统问题或轮胎定位不正确引起的。
车主应及时进行轮胎定位和悬挂系统的检查和维修。
2. 外侧磨损:如果轮胎的外侧出现磨损,可能是由于过度转弯或行驶过崎岖路面引起的。
车主应减少过度转弯的频率,并尽量避免行驶崎岖路面。
第四部分:胎面刺孔胎面刺孔是指轮胎胎面上出现的小刺孔或钉子。
以下是几种常见的胎面刺孔情况及其维修方法:1. 小刺孔:如果刺孔较小且没有引发漏气,车主可以使用轮胎修补胶进行修补。
修补后,车主应定期检查修补处是否漏气。
2. 大刺孔:如果刺孔较大或引发漏气,车主应及时更换轮胎。
实心轮胎常见质量问题的分析及纠正预防措施

作者简介:王其营,男,1989年毕业于青岛化工学院(现青岛科技大学)橡胶机械专业,高级工程师,现任天津国际联合橡胶有限公司总经理,已发表轮胎专业论文220余篇,并多次获奖。
收稿日期:2019-12-03按照目前轮胎的最新分类,轮胎分为全钢子午线轮胎、半钢子午线轮胎、斜交轮胎和工程轮胎四大类,而且能源消耗和胶料消耗等指标的统计也是按照这四类轮胎的重量来进行核算和考核的。
这四类轮胎共同的特点都是在使用过程中需要按照载荷大小在轮胎内腔充进一定压力的压缩空气,所以统称为充气胎。
与充气胎相对应的就是实心轮胎,本文就实心胎的分类和特点进行简单介绍,对实心胎常见的质量问题进行分析,并提出相应的纠正预防措施,同时建议正确安装和使用,才能充分发挥实心胎的优势。
1 实心胎的分类和特点实心轮胎是一种适应于低速、高负载运行车辆的工业用轮胎,一般用于起升车辆、牵引车辆和平板车等工业车辆,如各种叉车、港口和机场的拖挂车辆等;同时用于工矿、码头、钢铁冶金、机场、军事、建筑工程机械等领域,还广泛用于医药、食品、造纸、纺织、电子等领域。
1.1 实心胎的分类根据结构不同,实心轮胎分为充气轮胎轮辋式实心胎、钢圈压配式实心胎、黏结一体式(辐板一体式)实心胎、无印痕实心胎等类型。
1.1.1 充气轮胎轮辋式实心胎充气轮胎轮辋式实心胎所用的轮辋与相同规格充气轮胎的相同或相近,故称为充气轮胎轮辋式实心胎,其外观形状见图1,装配轮辋后的形状见图2;其组成部分由外及里分别是胎面胶、缓冲层、基部胶、钢丝(钢实心轮胎常见质量问题的分析及纠正预防措施王其营1,王伟琳2(1.天津国际联合轮胎橡胶股份有限公司,天津 300452;2.烟台宏业橡胶有限公司,山东 栖霞 265300)摘要:本文就实心胎的分类和特点进行简单介绍,对实心胎常见的质量问题进行分析,并提出相应的纠正预防措施;同时建议正确安装和使用,才能充分发挥实心胎的优势。
关键词:实心轮胎;分类及特点;质量问题;纠正预防措施中图分类号:TQ330文章编号:1009-797X(2020)09-0001-06文献标识码:B DOI:10.13520/ki.rpte.2020.09.001环)骨架等,其断面图见图3。
翻新轮胎存在问题及整改措施
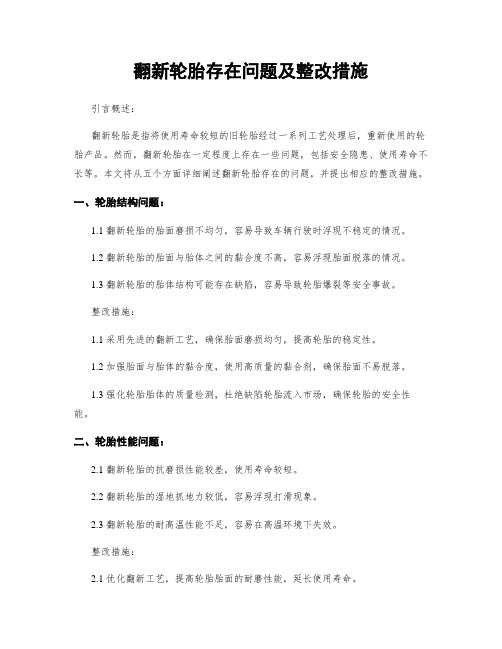
翻新轮胎存在问题及整改措施引言概述:翻新轮胎是指将使用寿命较短的旧轮胎经过一系列工艺处理后,重新使用的轮胎产品。
然而,翻新轮胎在一定程度上存在一些问题,包括安全隐患、使用寿命不长等。
本文将从五个方面详细阐述翻新轮胎存在的问题,并提出相应的整改措施。
一、轮胎结构问题:1.1 翻新轮胎的胎面磨损不均匀,容易导致车辆行驶时浮现不稳定的情况。
1.2 翻新轮胎的胎面与胎体之间的黏合度不高,容易浮现胎面脱落的情况。
1.3 翻新轮胎的胎体结构可能存在缺陷,容易导致轮胎爆裂等安全事故。
整改措施:1.1 采用先进的翻新工艺,确保胎面磨损均匀,提高轮胎的稳定性。
1.2 加强胎面与胎体的黏合度,使用高质量的黏合剂,确保胎面不易脱落。
1.3 强化轮胎胎体的质量检测,杜绝缺陷轮胎流入市场,确保轮胎的安全性能。
二、轮胎性能问题:2.1 翻新轮胎的抗磨损性能较差,使用寿命较短。
2.2 翻新轮胎的湿地抓地力较低,容易浮现打滑现象。
2.3 翻新轮胎的耐高温性能不足,容易在高温环境下失效。
整改措施:2.1 优化翻新工艺,提高轮胎胎面的耐磨性能,延长使用寿命。
2.2 使用高性能的胎面胶料,提高轮胎的湿地抓地力,减少打滑现象。
2.3 选用高温耐受性较好的材料,提高轮胎的耐高温性能,确保在高温条件下轮胎的正常使用。
三、市场监管问题:3.1 翻新轮胎市场缺乏有效的监管机制,存在乱象。
3.2 一些不良商家使用低质量的材料进行翻新,严重影响轮胎品质。
3.3 消费者对翻新轮胎的认知度较低,容易被不良商家误导。
整改措施:3.1 建立健全的翻新轮胎监管机制,加强对翻新轮胎市场的监督。
3.2 加大对翻新轮胎生产企业的执法力度,严厉打击使用低质量材料的不良商家。
3.3 提高消费者对翻新轮胎的认知度,加强宣传教育,引导消费者正确选择轮胎产品。
四、环境污染问题:4.1 翻新轮胎生产过程中产生的废胶处理不当,对环境造成污染。
4.2 翻新轮胎使用寿命较短,导致轮胎的更新频率较高,增加了废轮胎的数量。
全钢载重子午线轮胎常见质量缺陷原因分析及解决措施

全钢载重子午线轮胎常见质量缺陷原因分析及解决措施叶 斌(银川佳通轮胎有限公司,宁夏银川750011)摘要:分析全钢载重子午线轮胎常见质量缺陷原因,并提出相应解决措施。
通过采取检查整经辊和压力辊、裁断修边刀、喂料装置、自动定中系统及接头机接头轮的工艺参数和稳定性及严格控制成型平宽、半成品部件尺寸、挤出机各段温度、机头挤出压力和0°带束层胶料门尼粘度等措施,有效减少了全钢载重子午线轮胎生产过程中容易出现的胎体劈缝、肩弯和0°带束层散丝等质量缺陷,大幅提高了轮胎质量和生产合格率。
关键词:全钢载重子午线轮胎;质量缺陷;原因分析;解决措施中图分类号:U463.341+.3/.6;TQ330.6+6 文章编号:2095-5448(2020)01-0044-04文献标志码:A DOI:10.12137/j.issn.2095-5448.2020.01.0044随着我国经济的迅猛和持续发展,以及国家对全钢载重子午线轮胎的政策性支持,在交通运输业和汽车工业中起着重要作用的轮胎,特别是子午线轮胎近年来呈现快速发展的态势[1]。
全钢载重子午线轮胎由于生产工艺复杂,在生产过程中常会出现一些质量问题[2-4],下面从工艺控制及操作等方面分析质量缺陷产生的原因,并提出相应的解决措施。
1 胎体劈缝胎体劈缝是指胎体帘线钢丝排列不均、局部密度变小不符合标准要求。
胎体劈缝会导致胎侧起鼓甚至爆胎,劈缝严重时轮胎充气后即可观察到局部鼓包,严重影响成品轮胎的使用寿命及安全性能。
1.1 原因分析(1)压延时由于钢丝帘线导开张力不均或气泡、熟胶等将帘线挤疏造成覆胶钢丝帘布密度不均,硫化后钢丝帘布局部伸张过大产生劈缝现象。
(2)帘布裁断修边工艺不稳定,露钢丝或多胶,造成接头虚接。
(3)裁断机喂料装置及自动定中系统不稳定;接头机接头轮间隙和压力等调整不当,使裁断接头虚接或搭接。
(4)成型使用了粘性不好或喷霜严重的内衬层、胎体帘布等半成品;为提高半成品粘性或处理粘合在一起的半成品部件等而涂刷过多汽油导致帘布拉伸。
轮胎常见缺陷原因及解决方法

压杂胶解决方法:1、每班接班第一锅装锅前,彻底清理一遍活络模,每一锅装锅前仔细检查清理活络模间残留胶边。
原因:1、模具花纹块模缝间,上一锅胶边未清理干净(肩、冠压杂胶);2、合模活络模伸出时,模缝间小胶边掉落在胎胚上(侧压杂胶)。
子口上抽解决方法:1、控制定型压力;2、上环顶的机台,更换葫芦头或活塞杆密封。
原因:1、定型压力控制过大;2、定性时上环往上顶。
正常锥子眼解决方法:1、检查侧板和胎胚,发现有水及时清理;2、更换密封;3、把关胎胚,锥子眼大的胎胚返修。
原因:1、侧板或胎胚上有水;2、密封泄漏;3、锥子眼过大,胶料流动性差。
临票问题解决方法:1、装锅合模时注意检查临票。
原因:1.临票放歪,放错地方,放反;2、定性时吹动或刮碰。
解决方法:1、出锅时检查挡胎滑道上是否有胎,防止两胎相挤;2、硫化结束及时出锅。
胎体变形原因:1、刚出锅时,小车或运输带运输挤压;2、长时间焖锅;3、抽真空时间过长。
解决方法:1、检查胎胚里是否有杂物,如发现气泡及时刺扎。
胎里气泡原因:1、密封层有杂物;2、胎胚密封层有气泡大边露丝解决方法:1、按顺序拉胎,发现轻微变形的及时清理;2、发现机械手不对正的及时调整维修;3、出锅检查轮胎,发现大边而不上抽的及时联系上工序,检查半部件。
原因:1、胎胚变形;2、机械手不正,对中性不好;3、钢圈直径小;4、子口胶料半部件厚解决方法:1、检查胎胚时发现胎侧有气泡及时刺扎,不能扎透。
胎侧气泡原因:1、压胎侧时,刷油过多;2、有杂物;3、胎侧里带水。
花纹缺胶解决方法:1、模具透眼;2、装锅时发现反蒸汽或者出锅时锅内存水多,及时联系设备维修。
原因:1、模具排气孔堵;2、倒门反蒸汽、疏水阀堵塞。
解决方法:1、合模时首先检查风压,风压压力不得低于四公斤;2、找设备人员排查阀门维修。
双压痕原因:1、硫化过程中出现掉压现象或合模无风压不跑步;2、硫化结束后重新打入压力、蒸锅式硫化机撤外压慢。
解决方法:1、更换模具时,手锅必须检查左右合模力,调节左右合模力。
- 1、下载文档前请自行甄别文档内容的完整性,平台不提供额外的编辑、内容补充、找答案等附加服务。
- 2、"仅部分预览"的文档,不可在线预览部分如存在完整性等问题,可反馈申请退款(可完整预览的文档不适用该条件!)。
- 3、如文档侵犯您的权益,请联系客服反馈,我们会尽快为您处理(人工客服工作时间:9:00-18:30)。
成品外胎常见缺陷及预防措施缺陷名称造成原因预防措施胎面缺胶(花纹、胎肩、胎侧)1.主要是胎面胶料流动性差;2.胎面形状不合适;3.胎面厚薄不均匀;4.硫化内压低或不足;5.模型太脏;6.模型排气槽阻塞;7.模型内留存空气1.提高胎面胶料的可塑度2.改进胎面押出口金的形状3.严格执行工艺技术标准4.提高硫化内压5.定期清洗模型,适当涂刷润滑剂6.定期疏通模型内上下排气槽7.调整气囊与外胎的配合8.调整配方设计胎面起泡 1.胎面押出时潜有气泡2.原材料含水率过高并含有挥发物质3.胎面押出时辊温太高1.严格控制原材料质量2.严格控制半制品质量3.严格掌握胎面押出辊温4.改进配方设计,掺用再生橡胶胎里起泡 1.尼龙帘布热收缩性大2.胎体未压实3.轮胎欠硫4.帘布太密且太细,无法排气1.结构设计时,应考虑帘线假定伸张值2.胎面与帘布层应层层压紧、压实3.严格控制硫化时,装气囊的温度不高于70℃4.改进气囊成型接头方法,控制接头处壁厚5.严格控制轮胎正硫化点6.严格控制尼龙帘布的含水率7.胎面和帘布采用刺孔的工艺方法(孔的大小以依稀透光为主,且成型时仍保持原来大小)胎体脱层 1.硫化温度太低,硫化时间及内压不足2.成型时胎体未压实3.半制品沾有杂质、水迹、油迹等4.胶帘布存放时间过长,不粘1.严格掌握正硫化条件(时间、温度、压力)2.成型时层层压实3.加强现场工艺管理,保持半制品清洁4.控制胶帘布存放时间5.硫化时经常开放回气阀帘线弯曲 1.帘线伸张不足2.胎体膨胀大1.调整施工设计(成型筒直径与成型微周长)2.控制胎面和胶帘布厚度3.气囊与外胎应合理配合4.涂刷隔离剂不应过浓或太湿胎耳不满 1.硫化时外胎胎耳不贴模 1.控制和提高硫化内压力2.调整施工设计(成型筒直径与成型微周长)3.提高胎耳包布胶可塑度4.调整胎耳施工设计,使之与模型配合胎圈(唇)变形 1.胎圈直径过大或过小2.硫化操作不当微信公众号:poly-sky 1.调整施工设计(成型筒直径与成型胎圈间距)2.气囊与外胎配合合理3.控制装囊机尺寸4.提高硫化操作技术水平5.增加气囊装胎润滑性重皮 1.模型不清洁2.胎面表面沾污3.胎面形状不合适4.胶料流速太快1.定期清洗模型,保持半制品清洁2.改进胎面押出口金形状3.调整配方4.改进结构设计中胎侧轮廓曲线胎冠刺伤 1.轮胎在行驶过程中,碰到尖、硬、锋口等物体1.增强轮胎刚性2.增强轮胎胎体缓冲性能3.提高胶料定伸强度4.调正H/B中的H值5.增加花纹基部厚度,改进花纹设计,花纹沟改为开放式6.提高硫化内压力7.严格掌握正硫化点胎体垫伤 1.轮胎在负重或快速行驶过程中,碰到尖、硬的物体1.加固胎体强度2.增强轮胎胎体缓冲性能3.提高胶料定伸强度4.增加帘布复胶厚度5.提高骨架材料的强度6.调正H/B中的H值7.正确选取δ,减小帘布伸张率8.提高硫化内压力胎体脱层 1.轮胎欠硫,胶帘布间及胶帘布与胎面间密性能差,半制品不清洁,沾有杂物,水份、油迹等1.严格控制正硫化点2.提高胶帘布间或胶帘布与胎面间附着强度3.增加帘布复胶厚度4.提高硫化内压力5.严格控制半制品标准,加强现场管理6.调正结构设计参数比值,减小应力集中帘线折断 1.轮胎在缺气下或超负荷状态下行驶1.轮胎应在规定的负荷、内压下使用2.提高帘线强度3.增加帘布复胶厚度4.增强轮胎刚性胎唇烧边 1.轮辋与外胎胎唇不配合,轮胎在超负荷下行驶1.改进胎唇设计,使胎唇与轮辋紧密配合2.提高胎唇强度3.提高胎唇包布耐疲劳性能4.增加胎唇包布复胶厚度钢丝断裂 1.钢丝圈制造的质量问题或轮胎在超负荷下行驶1.提高钢丝圈制造工艺质量2.改进钢丝圈制造工艺3.严格控制钢丝圈制造质量4.轮胎应在规定的负荷下行驶滑圈 1.轮胎着合直径与轮辋尺寸配合不符或装配不当1.轮辋尺寸、几何形状应符合标准2.轮胎在标准内压下行驶3.轮胎着合直径不能太大,应符合标准4.轮胎胎圈结构设计应合理5.钢丝圈制造尺寸应严格控制,防止变形跳动、偏摆1、帘布接头太大2、卷上交叠偏差大3、帘子布边纱过密混炼胶主要质量问题及其原因质量问题可能原因分散不良 A.混炼过程:混炼时间不够;卸料温度过高或过低;同时添加酸性配合剂和碱性配合剂(如将硬脂酸和防焦剂ESEN与氧化锌一起加入);塑炼不充分;配合剂添加的顺序不恰当;混炼周期中填充剂加得太迟;同时加入小粒径炭黑和树脂或粘性油;金属氧化物分散时间不够,在胶料已经开始撕裂或碎裂后加入液态增塑剂,容积量太小或太大.B.工艺没有遵循所制订的混炼程序;油性材料和干性材料的聚集体粘在上顶栓和进料斗边上;转了速度不恰当;胶料从压片机上卸下时太快;没有正确使用压片机上的翻胶装置。
C.设备密炼机温度控制失效;上顶栓压力不够;混炼室中焊层部位磨损过度;压片机辊温控制失效;压片机上的高架翻胶装置失灵。
D.材料橡胶过期存放和有部分胶凝;三元乙丙橡胶可丁基橡胶太冷;冷冻天然橡胶;天然橡胶预塑炼不充分;填充剂中水分过量(结块);在低于倾倒点温度下加入粘性配合剂;配合剂使用不适当。
E.配方设计使用的弹性体门尼粘度差异太大;增塑剂与橡胶选配不适当;硬粒配合剂太多;小粒径填料过量;使用熔点过高的树脂;液态增塑剂不够;填充剂和增塑剂过量。
焦烧 A.配合硫化剂、促进剂用量太多;硫化体系作用太快;配合剂称量不正确;小粒径填料过量;液态增塑剂不够。
B.混炼操作装料容量过大;密炼机冷却不够;转了速度过高;初始加料温度太高;排胶温度太高;促进剂加入密炼机中的时间不对;或过早地加入硫磺、或分散不均而造成硫化剂和促进剂局部高度集中;促进剂和(或)硫化机分散不良;树脂堆积在转子上;漏加防焦剂;未经薄通散热就过早地打卷,或卷子过大,或者下片后未充分冷却,C.停放在胶料还呈热、湿状态时,堆积胶料;胶料停放过久;停放场所温度太高,或空气不流通。
D.防止焦烧的措施严格控制辊温,改进冷却条件,按照操作规定加料,加强胶料管理等;调整硫化体系,添加防焦剂。
如防焦剂PVI(CTP);防焦剂的添加顺序应在硫化剂和促进剂之前。
配合剂结团生胶塑料不充分;辊距过大,辊温过高,粉剂落到辊筒面上压成片状;装料容量过大;粉状配合剂含粗粒或结团物;凝胶太多。
收缩大 A.无硫胶料可塑度过低,混炼时间太短或密炼机混炼时间过长,导致结聚。
B.加硫胶料胶料开始焦烧.麻面(胶粒) A.无硫胶料密炼机混炼时间过长,炭黑凝胶量太多。
B.加硫胶料胶温、辊油温过高引焦烧;混入一些已焦烧胶料。
可塑度过高过低或不均塑料胶可塑度不适当;混炼时间过长或过短;混炼温度不当;并用胶未掺合好;增塑剂多加或少加;炭黑多加、少加或品种胶错相对密度过大过小或不均匀配合剂称量不准、漏配和错配;炭黑、氧化锌、碳酸钙等多于规定用量或油类增塑剂等少于规定用量时,均会出现胶料相对密度超过规定值;混炼时粉剂飞扬损失过多、粘附于容器壁过多或加料盛器未倒干净;混炼不均匀。
焦烧时间过长 A.焦烧时间延长或缩短促进剂品种弄错、少加;氧化锌漏加;炭黑品种弄错,软化剂品种弄错;陶土多加。
B.焦烧时间缩短促进剂多加或品种搞错;炭黑品种用错;碳酸钙过量。
硬度过高、过低或不均匀配合剂称量不准,如补强剂、硫化剂和促进剂称量过多,则硫化胶硬度偏高;相反,则硬度偏低;增塑剂和橡胶称量过多,则硬度偏低;混炼不均匀,硫化胶硬度不均。
喷霜胶料混炼不足、不均匀;配合剂称量不准;硫黄结团或用量超过其常温在橡胶中的溶解度;加硫时胶温过高;软化剂用量过多;胶料停放时间过长;制品欠硫等。
硫化起点慢促进剂称量不准,(过少)或漏加氧化锌或硬脂酸;炭黑品种搞错。
欠硫促进剂、硫化剂和氧化锌等漏配或少配;混炼操作不当,硫化剂和促进剂飞扬损失过多。
分层天然橡胶胶料中混入丁基胶或相反。
(或PE膜熔点过高,未分散完全)粘辊或脱辊 A.粘辊辊温过高、辊距过小;可塑度过高;软化剂过多;混炼时间过长或违反加料顺序。
B.脱辊含胶率过低;胶质硬;混炼时辊矩大;含有合成胶。
污染由灰尘、污垢、砂粒及其它物质所致的弹性体和橡胶药品的物理污染;由其它弹性体(如天然橡胶和丁腈橡胶)所致的丁基橡胶和三元乙丙橡胶的化学污染;对不同的配合剂未分别使用铲勺;使用不适当的配合剂;以前用过的料盘中残留有配合剂;密炼机油封渗油;余留胶料粘在转子、卸料门、进料斗和上顶栓上,如果定期用清洁的胶料清扫,可减少这类问题的发生;余留胶料粘卸料料槽、接料盘、导向槽和高架翻胶装置上;余胶堆积在密封圈处;密炼机和压片机周围区域整齐。
物理机械性能不合格或不一致配合剂称量不准,特别是补强剂。
硫化剂和促进剂漏配和错配;混炼过度;加料顺序不合理和混炼不均匀,易引起性能不一致。
各批胶料间性能差异初始加料温度有差异;冷却水流动和(或)温度有差异;上顶栓压力有差异;配合剂称量中有误差;不同批号之间配合剂的差异;使用替用用配合剂;排胶时间和(或)排胶温度的变化;不同的操作者采用不同的方法在压片机上加工胶料;捣胶时间的变化;分散程度不同。
压延性能差辊温选用不当;辊温和辊筒速比及辊筒速度的控制失灵;胶料的门尼粘度太低;增粘剂过量;粘性填充剂(如陶土)填充量过高;粘性增塑剂量太大;配方中缺少适当的操作助剂;装料不足或过量;弹性体的粘度选择错误;分散不良;胶料易焦烧;胶料留在开炼机上的时间太长。
微信公众号:poly-sky,高分子天空压延工艺常见质量问题及改进措施质量问题产生原因改进措施有气泡、气孔胶温辊温过高;配合剂含水过多;供胶卷过松;压延存胶过多。
严格控制工艺条件有杂质针孔、色斑、污点原材料不纯;设备打扫不彻底加强原材料质量管理;加强设备保养粘辊、焦烧配合不当;辊温过高改进配方及温度条件厚度、宽度不符热炼胶温度波动;压延机辊温波动;胶料可塑度不一致;卷取松紧不一致;辊距未调准;压延机振动或轴承不良;压延存胶调节不当改进热炼条件;控制好辊温;加强胶料可塑度控制;固定返回胶掺用比;调整卷取机构;调节辊距;改进设备防震;改变压延存胶量。
表面粗糙热炼不足,辊温过低;热炼不均,辊辊不均;胶料自流改进热炼,控制好辊温;降低热炼温度及压延机辊温。
两边不齐挡板不适当或割胶刀未掌握好调换挡板胶料与布附着不好,掉皮布料未干燥好;压延温度太低;胶料可塑性太小;布料表面有油点或粉尘;布面温度太低布料含水率降到3%以下;提高压延温度;热炼补充加工;布面清理干净;加强织物预热帘布跳线弯曲纬线松紧不一;胶料软硬不一;中辊压延存放胶太多,局部受力过大;布卷过松控制帘线张力,使均匀;控制胶料可塑度,热炼做到均匀一致;减少中辊压延存放;做到均匀卷取帘布中部松长中辊积胶过多;下辊温度过高,使胶面粘附下辊的力量较大;织物浸胶时吸湿过大,干燥不充分,出现两边收缩,中间凸出(人造丝帘布)控制余胶量;降低下辊辊温;控制浸胶后的干燥率胶布出现硫化粒机械生热引起胶料焦烧;环境高温引起胶料焦烧;硫化剂分散不均匀不使机械生热,不产生较大部分余胶(边胶);随上辊连续滚转,在压延机前两侧,安装两个小辊,使边胶自然落盘,冷却;适当控制加硫磺混炼温度,避免过早加入硫磺,并使硫化剂分散均匀常见压出质量问题及解决方法质量问题形成原因解决方法压出物不光滑 1.温度低,表面呈粗细不匀或麻面状2.焦烧3.牵引运输带速度慢于压出速度4.胶料预热不均或返回胶未掺炼均匀5.压出速度过快,使表面出现皱纹1.提高机头温度2.紧急冷却3.提高牵引速度4.延长热炼时间5.调整螺杆转速焦烧 1.胶料配合不当,焦烧时间太短2.积胶或死角引起3.流胶口太小4.机头温度太高5.螺杆冷却不足6.喂料中断形成空车滞料1.调整配方2.改正口型锥角,定期清除积胶3.加开流胶口4.降低机头温度5.加强螺杆冷却6.防止供料脱节起泡与海绵 1.车速太快2.原料中水分、挥发物多3.热炼时夹入空气4.机头温度过高5.胎面双层压出时,层与层之间贴合不实1.调慢车速2.加强原材料检验3.改进热炼操作,采取收敛式螺纹4.冷却机头厚薄不均芯型偏位用支架螺旋调整口型或芯型条痕裂口 1.杂质引起2.热炼不足3.畸形产品,各部位应力不一致1.松开口型,让杂质排出2.延长热炼时间3.改进口型设计规格不符合要求1.宽度和直径符合,但厚度超过2.宽度和直径符合,但厚度不足3.厚度符合,但宽度不合格4.宽、厚均超过要求5.宽、厚度均低于要求6.厚度不对称1.提高机头、机身温度2.降低机头、机身温度3.调节牵引速度:宽加快、窄减慢,或调整机头温度:宽提高、窄降低4.提高牵引速度5.降低牵引速度6.调整口型与芯型常见硫化质量缺陷的成因与一般改进方法缺陷产生原因一般改进方法缺胶(明疤) 1.橡胶与模具表面之间的空气无法逸出2.压力不足3.胶料流动性太差4.模温过高5.胶料的焦烧时间太短6.装胶量不足1.加开逃气槽或改进模具结构2.加压后回松让空气逸出3.提高压力4.胶料表面涂洒硬脂酸锌及提高胶料可塑性5.胶料中加石蜡6.调整配方,减慢硫速对合线开裂 1.液压不足或波动2.焦烧时间太短3.坯胶或模具沾油污1.加压,检查液压系统2.调整硫化体系3.做好半制品及模具的清洁工作起泡、发孔、呈海绵状1.欠硫或硫化压力不足2.挥发分或水分太多3.模内积水不干或胶料沾水、沾污4.压出或压延中夹入空气5.硫化温度太高1.提高压力2.调整配方3.坯胶预热干燥,对原材料加强管理4.改进压延、压出条件5.进模前用针挑破气泡6.增加合模后的回松次数重皮、重叠或表面裂开1.胶料硫化速度太快,流动不充分2.模具不净,胶料表面沾污3.成型形状不合理4.隔离剂选用或涂擦不当1.调整配方,减慢硫化速度2.加强模具与半制品管理,不使沾污3.改变成型形状,使各部位同时与模具接触4.减少隔离剂用量喷硫、喷霜 1.欠硫2.某种配合剂用量超过它在胶料中的溶解度3.混炼辊温太高1.增加硫化时间2.调整配合剂用量3.混炼时辊温要适宜色泽不均 1.升温过急,受冷凝水或湿蒸汽的冲击2.压缩空气中带水(指硫化罐硫化)3.平板温度不均匀1.适当减慢升温2.压缩空气经过干燥及去水处理撕裂 1.过硫2.模温过高3.脱模剂不足4.出模方法不妥5.模具结构不合理1.采用以下三种措施之一来调整:降低硫化温度、缩短硫化时间及改变配方设计2.冷启模3.在易撕处多涂脱模剂4.改变启模及取出方式分层 1.表面沾污2.喷霜1.保持胶面清洁2.减少喷霜物的用量制品模口扯裂(高温硫化或大型制品硫化后启模时)1.操作失当2.配方不合理1.提高模型精度,按最小量加料,以减少胶边2.预热胶料3.采用低温长时间硫化4.容易扯裂的丁苯橡胶等并用顺丁橡胶5.适当降低含胶率低于60%6.避免使用快速硫化体系7.选用高温下补强性大的填充剂。