涂装生产线喷淋前处理设备设计与实现
(喷淋线)前处理操作指导规程
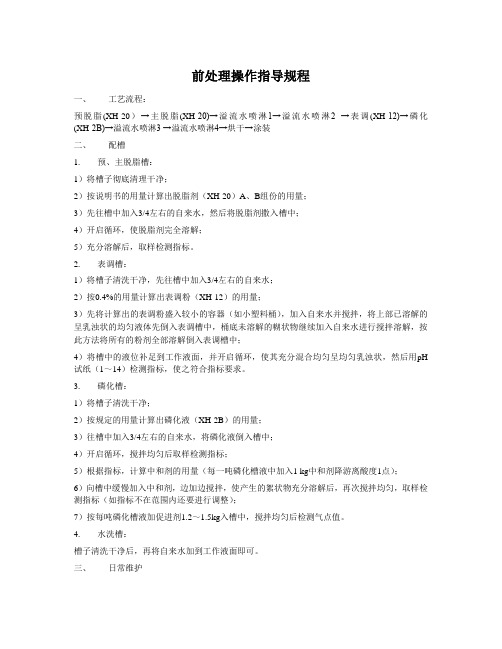
前处理操作指导规程一、工艺流程:预脱脂(XH-20)→主脱脂(XH-20)→溢流水喷淋1→溢流水喷淋2 →表调(XH-12)→磷化(XH-2B)→溢流水喷淋3 →溢流水喷淋4→烘干→涂装二、配槽1. 预、主脱脂槽:1)将槽子彻底清理干净;2)按说明书的用量计算出脱脂剂(XH-20)A、B组份的用量;3)先往槽中加入3/4左右的自来水,然后将脱脂剂撒入槽中;4)开启循环,使脱脂剂完全溶解;5)充分溶解后,取样检测指标。
2. 表调槽:1)将槽子清洗干净,先往槽中加入3/4左右的自来水;2)按0.4%的用量计算出表调粉(XH-12)的用量;3)先将计算出的表调粉盛入较小的容器(如小塑料桶),加入自来水并搅拌,将上部已溶解的呈乳浊状的均匀液体先倒入表调槽中,桶底未溶解的糊状物继续加入自来水进行搅拌溶解,按此方法将所有的粉剂全部溶解倒入表调槽中;4)将槽中的液位补足到工作液面,并开启循环,使其充分混合均匀呈均匀乳浊状,然后用pH 试纸(1~14)检测指标,使之符合指标要求。
3. 磷化槽:1)将槽子清洗干净;2)按规定的用量计算出磷化液(XH-2B)的用量;3)往槽中加入3/4左右的自来水,将磷化液倒入槽中;4)开启循环,搅拌均匀后取样检测指标;5)根据指标,计算中和剂的用量(每一吨磷化槽液中加入1 kg中和剂降游离酸度1点);6)向槽中缓慢加入中和剂,边加边搅拌,使产生的絮状物充分溶解后,再次搅拌均匀,取样检测指标(如指标不在范围内还要进行调整);7)按每吨磷化槽液加促进剂1.2~1.5kg入槽中,搅拌均匀后检测气点值。
4. 水洗槽:槽子清洗干净后,再将自来水加到工作液面即可。
三、日常维护1. 开工之前1)检查各槽液位,对液位不足的进行补水(如对脱脂槽、主脱脂槽、表调槽和磷化槽进行了补水,则应按比例补加相应产品);2)根据上一班的生产情况和检测的指标对预脱脂槽、主脱脂槽、表调槽和磷化槽进行相应产品的补加;3)对预脱脂槽、主脱脂槽的浮油进行打捞;4)如果水洗槽内的水脏,则应更换;5)开工前,将喷淋泵打开,使各槽液充分循环;6)开始挂工件时,向磷化槽液中按0.5%的比例补适量促进剂,并开启促进剂滴加装置。
(完整版)涂装生产线设计方案
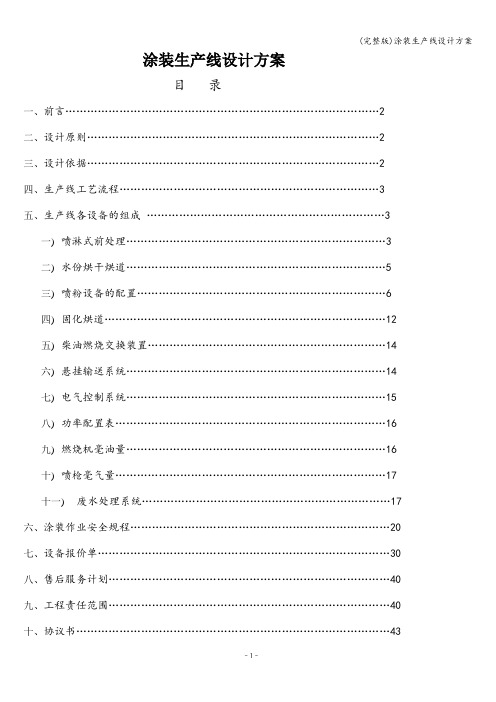
涂装生产线设计方案目录一、前言 (2)二、设计原则 (2)三、设计依据 (2)四、生产线工艺流程 (3)五、生产线各设备的组成 (3)一)喷淋式前处理 (3)二)水份烘干烘道 (5)三)喷粉设备的配置 (6)四)固化烘道 (12)五)柴油燃烧交换装置 (14)六)悬挂输送系统 (14)七)电气控制系统 (15)八)功率配置表 (16)九)燃烧机毫油量 (16)十)喷枪毫气量 (17)十一)废水处理系统 (17)六、涂装作业安全规程 (20)七、设备报价单 (30)八、售后服务计划 (40)九、工程责任范围 (40)十、协议书 (43)一、前言1.生产线工艺方案的确定考虑到技术的先进性,充分满足产品的质量要求;2.生产线工艺设备的设计、选型都考虑确保工艺及各项技术参数的实现;3.生产线的所有设备确保先进、实用、可靠、安全,主要设备及元件选用国家定点生产厂的名牌或优质名牌产品;4.凡自制设备在结构设计上尽量采用通用件和标准件,以提高自动化程度,并充分考虑改善生产工作环境和劳动卫生条件,贯彻国家和行业的有关标准及安全措施;5.生产线的总体布置设计,考虑整个生产线工艺流程的合理性,设备布置的协调、整齐、美观、便于操作、维修。
二、设计原则在满足客户的各项技术要求的基础上,尽可能减少一次性投资,并尽量降低生产线的生产能耗,从而降低生产成本.根据贵方提供的要求及场地尺寸,充分考虑到现场条件,认真做好工艺流程的设计及工艺方案的平面布局。
整个设计方案都以经济、实用、物美价廉为宗旨.希望能携手共建一条优质的生产线。
此方案如有不到之处,请多多指正.此方案中,我们负责下列设备的设计、及制造安装:①前处理;②干水炉;③喷粉设备;④固化炉及加热系统;⑤悬挂输送系统。
三、设计依据2。
生产线速度 6m/min (3~10m/min 无级可调) 3.工艺温度 160℃—180℃可调(干水) 4。
加热方式 柴油燃烧机加热 5。
燃 料 柴油 6.主要工件 钢铁管件7。
涂装前处理生产线工艺设计注意事项
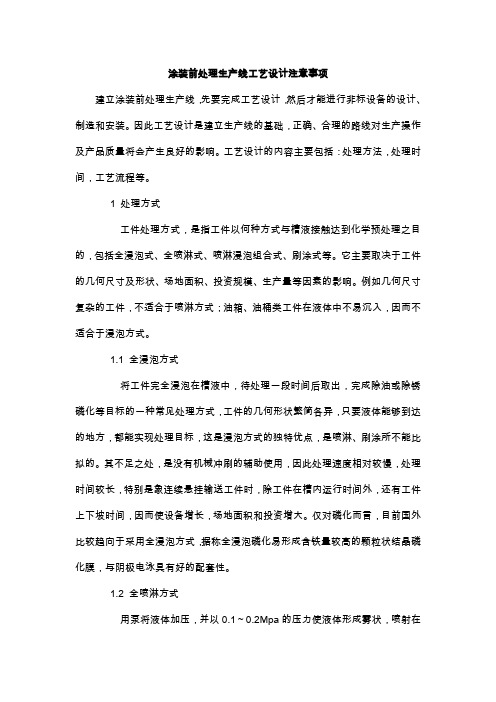
涂装前处理生产线工艺设计注意事项建立涂装前处理生产线,先要完成工艺设计,然后才能进行非标设备的设计、制造和安装。
因此工艺设计是建立生产线的基础,正确、合理的路线对生产操作及产品质量将会产生良好的影响。
工艺设计的内容主要包括:处理方法,处理时间,工艺流程等。
1 处理方式工件处理方式,是指工件以何种方式与槽液接触达到化学预处理之目的,包括全浸泡式、全喷淋式、喷淋浸泡组合式、刷涂式等。
它主要取决于工件的几何尺寸及形状、场地面积、投资规模、生产量等因素的影响。
例如几何尺寸复杂的工件,不适合于喷淋方式;油箱、油桶类工件在液体中不易沉入,因而不适合于浸泡方式。
1.1 全浸泡方式将工件完全浸泡在槽液中,待处理一段时间后取出,完成除油或除锈磷化等目标的一种常见处理方式,工件的几何形状繁简各异,只要液体能够到达的地方,都能实现处理目标,这是浸泡方式的独特优点,是喷淋、刷涂所不能比拟的。
其不足之处,是没有机械冲刷的辅助使用,因此处理速度相对较慢,处理时间较长,特别是象连续悬挂输送工件时,除工件在槽内运行时间外,还有工件上下坡时间,因而使设备增长,场地面积和投资增大。
仅对磷化而言,目前国外比较趋向于采用全浸泡方式,据称全浸泡磷化易形成含铁量较高的颗粒状结晶磷化膜,与阴极电泳具有好的配套性。
1.2 全喷淋方式用泵将液体加压,并以0.1~0.2Mpa的压力使液体形成雾状,喷射在工件上达到处理效果。
由于喷淋时有机械冲刷和液体更新使用,因此处理速度加快、时间缩短。
生产线长度缩短,相应节首了场地、设备、不足之处是,几何形状较复杂的工件,像内腔、拐角处等液体不易到达,处理效果不好,因此只适合于处理几何形状简单的工件。
喷淋方式也不太适合于酸洗除锈,它会带来设备腐蚀、工序间生锈等一系列问题,因此在选择喷淋酸洗时必须十分慎重。
据报道,全喷淋磷化易形成结晶枝状粗大、含铁量较低的磷化膜,国外不提倡作为阴极电泳漆前打底的前处理。
全喷淋方式主要应用于家用电器、零部件类的粉末涂装、静电涂漆、阳极电泳等。
喷淋式涂装工艺设计
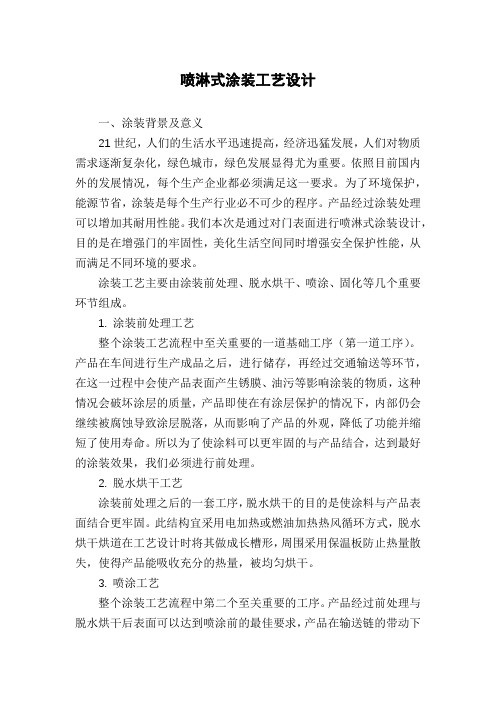
喷淋式涂装工艺设计一、涂装背景及意义21世纪,人们的生活水平迅速提高,经济迅猛发展,人们对物质需求逐渐复杂化,绿色城市,绿色发展显得尤为重要。
依照目前国内外的发展情况,每个生产企业都必须满足这一要求。
为了环境保护,能源节省,涂装是每个生产行业必不可少的程序。
产品经过涂装处理可以增加其耐用性能。
我们本次是通过对门表面进行喷淋式涂装设计,目的是在增强门的牢固性,美化生活空间同时增强安全保护性能,从而满足不同环境的要求。
涂装工艺主要由涂装前处理、脱水烘干、喷涂、固化等几个重要环节组成。
1. 涂装前处理工艺整个涂装工艺流程中至关重要的一道基础工序(第一道工序)。
产品在车间进行生产成品之后,进行储存,再经过交通输送等环节,在这一过程中会使产品表面产生锈膜、油污等影响涂装的物质,这种情况会破坏涂层的质量,产品即使在有涂层保护的情况下,内部仍会继续被腐蚀导致涂层脱落,从而影响了产品的外观,降低了功能并缩短了使用寿命。
所以为了使涂料可以更牢固的与产品结合,达到最好的涂装效果,我们必须进行前处理。
2. 脱水烘干工艺涂装前处理之后的一套工序,脱水烘干的目的是使涂料与产品表面结合更牢固。
此结构宜采用电加热或燃油加热热风循环方式,脱水烘干烘道在工艺设计时将其做成长槽形,周围采用保温板防止热量散失,使得产品能吸收充分的热量,被均匀烘干。
3. 喷涂工艺整个涂装工艺流程中第二个至关重要的工序。
产品经过前处理与脱水烘干后表面可以达到喷涂前的最佳要求,产品在输送链的带动下进入喷涂系统,经过喷枪等设备将产品的表面涂上一层漆膜,对于不同的漆膜要求,喷涂的方法与时间都是不尽相同的。
在产品表面涂附的漆膜在良好的固化条件下便形成所需要的保护膜,对产品起到很好的保护作用,达到生产处理的最终目的。
4. 固化烘干工艺固化处理是涂装生产流程线中最后一套工序。
通过传热的方式将喷涂后的产品表面涂层能够更快速高效的进行干燥,从而加强了涂层的硬度、牢固性,增强漆膜对产品表面的保护作用,使产品的外观更具有光泽,提升了产品的功能并延长了使用寿命,利用设备烘干的方式即环保又高效,对于大批量流水线生产有很大的意义。
涂装前处理设备喷淋系统中喷嘴选型常识
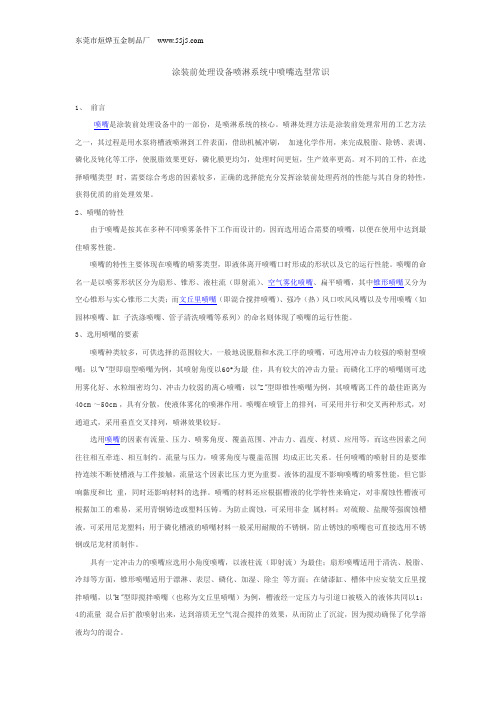
涂装前处理设备喷淋系统中喷嘴选型常识1、前言喷嘴是涂装前处理设备中的一部份,是喷淋系统的核心。
喷淋处理方法是涂装前处理常用的工艺方法之一,其过程是用水泵将槽液喷淋到工件表面,借助机械冲刷,加速化学作用,来完成脱脂、除锈、表调、磷化及钝化等工序,使脱脂效果更好,磷化膜更均匀,处理时间更短,生产效率更高。
对不同的工件,在选择喷嘴类型时,需要综合考虑的因素较多,正确的选择能充分发挥涂装前处理药剂的性能与其自身的特性,获得优质的前处理效果。
2、喷嘴的特性由于喷嘴是按其在多种不同喷雾条件下工作而设计的,因而选用适合需要的喷嘴,以便在使用中达到最佳喷雾性能。
喷嘴的特性主要体现在喷嘴的喷雾类型,即液体离开喷嘴口时形成的形状以及它的运行性能。
喷嘴的命名一是以喷雾形状区分为扇形、锥形、液柱流(即射流)、空气雾化喷嘴、扁平喷嘴,其中锥形喷嘴又分为空心锥形与实心锥形二大类;而文丘里喷嘴(即混合搅拌喷嘴)、强冷(热)风口吹风风嘴以及专用喷嘴(如园林喷嘴、缸子洗涤喷嘴、管子清洗喷嘴等系列)的命名则体现了喷嘴的运行性能。
3、选用喷嘴的要素喷嘴种类较多,可供选择的范围较大,一般地说脱脂和水洗工序的喷嘴,可选用冲击力较强的喷射型喷嘴:以"V"型即扇型喷嘴为例,其喷射角度以60°为最佳,具有较大的冲击力量;而磷化工序的喷嘴则可选用雾化好、水粒细密均匀、冲击力较弱的离心喷嘴:以"Z"型即锥性喷嘴为例,其喷嘴离工件的最佳距离为40cm~50cm,具有分散,使液体雾化的喷淋作用。
喷嘴在喷管上的排列,可采用并行和交叉两种形式,对通道式,采用垂直交叉排列,喷淋效果较好。
选用喷嘴的因素有流量、压力、喷雾角度、覆盖范围、冲击力、温度、材质、应用等,而这些因素之间往往相互牵连、相互制约。
流量与压力,喷雾角度与覆盖范围均成正比关系。
任何喷嘴的喷射目的是要维持连续不断使槽液与工件接触,流量这个因素比压力更为重要。
涂装生产流水线制造方案
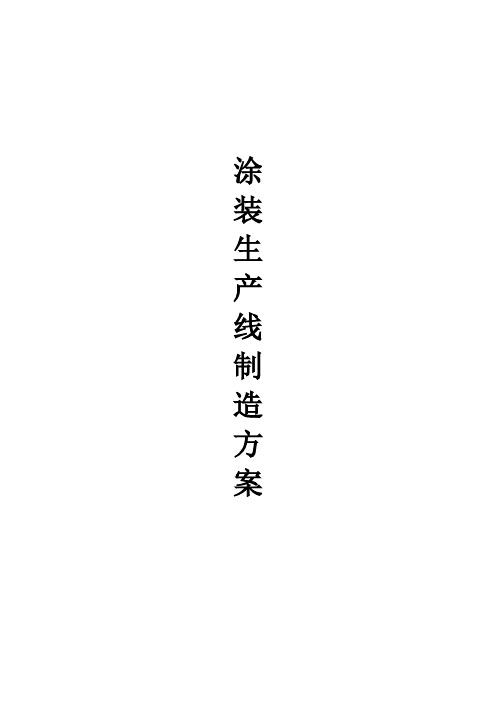
涂装生产线制造方案第一篇粉末涂装生产设计基本条件总体设计方案●涂装工件要求:●设计要求:●动力能源条件(用户负责提供)●业务范围:A.整套涂装线平面图纸B.厂内设备制作C.现场设备安装D.设备调试E.设备维护保养●粉体线涂装工艺流程:喷塑线:人工上件→喷淋前处理→预烘干→喷塑→固化→自然冷却→人工下件●流水线工艺参数表:●所需涂装设备:第二篇:前处理系统数量:1套 工艺参数表: V=2.5m/min联合前处理生产线制作规范:1前处理设备总成约为:42m×1.4m×8m(L×W×H)。
2为防止窜液,各工艺段之间有滴液区设计合理,各工序间的进出口设有可调节隔断板,以确保各不同工序段之间不窜液。
3液槽采用主、副结构,不锈钢双层过滤网,以除去液槽申的杂质,从而减少喷嘴和水泵的堵塞,为保持液槽的美观和易于清洁,槽沿和槽盖均采用不锈钢材料制作;4液槽底部做成倾斜结构,便清除槽内的溶液及槽底部沉积的污垢;液槽槽底克服焊缝腐蚀和漏液问题。
5喷淋装置由喷淋泵、开启阀门、调节阀门、压力表、喷淋主管、立喷管和万向球头喷嘴所组成。
主管——主管---- 阀门——泵(不锈钢)立管——主管(不锈钢)喷嘴一一立管(PP)●前处理工艺流程及参数流程:预脱脂——主脱脂——水洗——磷化——水洗●脱脂段第三篇:烘道系统●脱水烘道:数量:1套●脱水烘道设计参数:脱水烘道热能系统规范:脱水烘道炉体明细表:烘道结构特征:1炉体脱水烘道采用手工岩棉拼装板结构,散热面积小,保温性能好,焦炭加热,使炉内得到清洁的热空气,使整个炉体结构严谨、美观。
2送风系统热风经过循环风管,在引风机的作用下,将热风从烘道底部送入,均匀分布在整个炉内,从顶部抽风,再从烘道底部送入,实现内置式的热风循环结构。
3温控系统炉体的热风循环系统采用负抽风送风,在风管上设置均布的出风口,使炉内部温度分布均匀。
当温度低于设定温度时,循环风机开始工作,当温度高于设定温度时,循环风机停止工作。
喷粉和前处理

粉末涂料静电涂装的技术要求一、涂装环境温度和温度对涂膜厚度的影响以喷粉量为170~200g/min;电压为70KV,喷枪同被涂物的距离为20cm。
当温度在20~30℃,湿度在60~80%时粉末涂料的涂着效率较好,而且涂膜较厚。
二、涂膜的平整性在粉末涂料中,涂膜厚度越厚,表面越趋于平整。
影响粉末涂料涂膜平整性的主要因素是粒度不小及其分布,熔融粘度,颜料和固化剂的分散状态等。
对于熔融粘度高的树脂,如果要获得40μm涂膜厚度的平整涂膜,那么粉末粒度最大粒径约为60μm。
三、涂膜厚度的分布在静电粉末涂装中,由于喷出粉末的不均匀性使涂膜厚度的不均匀程度大约为溶剂涂装的2倍,要正确掌握涂装设备的有效喷束图形、控制好喷涂的间接时间,防止喷涂的不均匀性。
被涂物面积大于涂装设备的喷束图形时,采用往复式喷粉枪结构是比较适宜的。
当并联长冲程排列时,被涂物的中央部位涂膜较薄,而乐用串联短冲程排列,被涂物中央部位涂膜则较厚。
四、涂着效率影响粉末涂料涂着效率的主要因素是涂装设备对涂料的带电方式,粉末的粒度分布,涂装环境的温度和湿度等。
为此,合适的粉末涂料的范围为10~80μm。
涂装效率与粒径之间的关系粒子径与涂着效率的关系大致如下:粒子径的涂着效率:粒子径(μm)150以上为35.0、150~100为35~60 涂着效率(%)100~74为60~70,74~20为70~90,故:相对于粒子的重量,静电力随着粒子直径的减少而增加,粒子小为36~100μm,150~400目的粉体可完全附着冷态被涂物,较大的74~177μmc,80~200目)粒子在喷射后,粉体可能从被涂物掉落。
环氧树脂的粒度20~100μm,平衡的粒子径分布标准绳宜为10-80μm,最细的下限是10μm以下为10%以内,60μm以下的粒子为60%以下,宜成20~50μm的尖锐粒度分布,因20μm以下的微粉末容易飞扬,涂料损失也多。
五、涂膜的颗粒产生的原因为粉末涂料中混进胶化,难溶性粒子和杂质等造成。
涂装生产线前处理系统设计调试问题及对策探讨

Mechanical & Chemical Engineering272《华东科技》涂装生产线前处理系统设计调试问题及对策探讨陈文琛,沈 利,金子健,金长华(中国联合工程有限公司,浙江 杭州 310052)摘要:基于涂装生产线前处理系统的设计调试理论和实践,对涂装生产线前处理系统的设计和调试关键点和设计调试过程中可能出现的问题及其解决办法进行了初步分析。
将分析成果应用工程实践中,取得了较好的社会效益和经济效益,为同类型的其它涂装生产线前处理系统的设计、调试和运行工作提供了可借鉴的参考依据。
关键词:涂装生产线;前处理系统;设计;调试涂装生产线前处理系统一般包括有槽体、棚体、骨架、喷淋管路系统、控温系统、送排风系统、加料系统、除油系统等组成。
前处理系统槽体用于盛放工艺所需的处理液,槽体的体积大小的主要决定因素之一是每分钟的喷淋量;棚体起对喷淋管路的支撑及液体隔断等作用;骨架用于前处理系统及输送系统的支撑;喷淋管路系统起喷淋及搅拌的作用;控温系统是指对有温度需求的工艺槽体进行精确控温;送排风系统主要是防止前处理系统所产生的蒸汽、水雾和处理液雾外溢至车间,防止处理液雾在设备内紊乱;加料系统可根据需求配置成单目标或多目标自动在线控制;除油系统将脱脂过程中槽液中的油污分离出来,收集后集中处理。
涂装线前处理系统非标设备组成复杂,工件的涂装效果对前处理工艺要求较高。
在实际调试过程中参数的设定尤为复杂,调试的参数会在设备使用过程中存在一定的浮动。
1 涂装生产线前处理系统设计调试需要避免的问题 以某涂装生产线为例,涂装生产线前处理系统主要由7个槽体、棚体、吹水段、送排风系统、控温系统、除油系统等组成,按照工艺顺序依次是水洗1槽、脱脂槽、水洗2槽、纯水洗1槽、纯水直喷1、硅烷槽、纯水洗2槽、纯水洗3槽、纯水直喷2、自动吹水、人工吹水等组成。
[1]涂装生产线前处理系统调试中可能主要存在以下问题。
1.1 槽体之间的串液 槽体串液不仅可能会导致药剂的浪费、及导致槽液工艺成分的改变,进而影响工艺性能,而且可能会导致不同槽液间温度异常。
喷淋式前处理标准工序

喷淋式前处理标准工序以下为尺寸为工件件最大尺寸:2000×100×1500mm(L×W×H)的板件设计链速为2m/min的情况下的标准配置:标准生产线配备喷淋式清洗系统,先进的喷淋式前处理系统使工件表面清洗更彻底,全封闭的前处理系统外表美观漂亮。
脱脂槽及磷化槽配备加热系统,使表面处理的时间缩短,质量提高。
一、设计内容及概述一)八工位全封闭喷淋式前处理设备1.前处理设备结构形式为喷淋式。
2.棚体两侧及底板顶部采用A3钢板,整体防腐处理。
磷化工位所有材质(除喷嘴)均为特殊防腐处理;3.预脱脂、脱脂段、磷化段加热采用换热器。
4.选用效果良好、经济的高位沉降槽磷化除渣装置。
二、工艺流程序号工序名称温度(℃)时间(min)1预脱脂40-55 1.52脱脂40-55 1.53水洗RT 14水洗RT 15表调RT 16磷化40-55 27水洗RT 18水洗RT 1三、设备配置清单一)八工位全封闭喷淋式联合清洗机1座外形尺寸:47500×1000(1600)×3300mm(L×W×H)1.棚体47.5米——两侧顶部采用1.2mm厚A3钢板——底部采用3mm厚钢板——整体防腐处理2.槽体8只——其中磷化段为不锈钢——其他工艺段碳钢,外包不锈钢——特殊防腐处理3.喷淋管网8组——其中磷化段不锈钢——其他工位镀锌钢管4.喷淋喷嘴若干6.输液泵8台——均采用优质泵——磷化为不锈钢——其他工位碳钢7.换热器3套8.蒸汽电磁阀3套9.高位沉降槽磷化除渣装置1套10.截止阀全套——磷化段不锈钢11.棚体顶部输送链吊具通过开口封气毛刷装置1套12.气室2套13.槽顶检修通道全套14.检修门及扶梯平台全套15.逆流补水装置3套16.检修扶梯2套17.直喷回流、直喷直放装置全套18.脱脂段除油装置1套19.槽液给排系统全套20.简易检测系统全套前处理设备部分配置基本参数(16只/排,0.7 m3/h.只)四、设备结构特点一)全封闭喷淋式前处理系统外形尺寸:47500×1000(1600)×3300mm(L×W×H)1.八工位大型联合清洗机由棚体、槽体、喷淋系统、自动控温系统、磷化除渣系统、排气系统等组成。
专业喷涂生产线设计方案
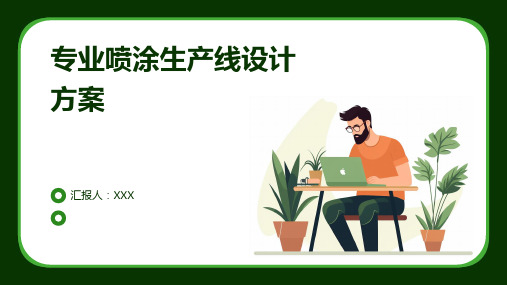
生产线平衡
对生产线各工序进行平衡分析,消除 瓶颈工序,实现生产线平衡和高效运 行。
人机工程学
考虑操作人员的工作舒适性,符合人 机工程学原理,降低操作人员的劳动 强度。
03
喷涂生产线关键技术
高效喷涂技术
高压无气喷涂
利用高压泵将涂料增压, 通过喷嘴形成高速涂料流 ,实现高效喷涂,提高涂 层质量和施工效率。
THANKS
感谢观看
提高生产效率:喷涂生产线采用 自动化设备和工艺流程,能够实 现连续、高效的生产,提高生产 效率。
降低人工成本:通过自动化设备 代替人工操作,可以降低企业的 人工成本,提高生产效益。
喷涂生产线的应用领域
01
02
03
汽车行业
汽车及其零部件的喷涂处 理是喷涂生产线的重要应 用领域,能够提高汽车外 观质量和耐腐蚀性。
生产线性能评价与持续改进
性能评价
故障分析
定期对喷涂生产线进行性能评价,包括产 能、良品率、能耗等指标。
针对生产线运行过程中出现的故障,进行 深入分析,找出根本原因,制定改进措施 。
技术升级
持续改进
关注国内外喷涂技术发展趋势,适时引入 先进技术,提升生产线技术水平。
建立持续改进机制,鼓励员工提出改进建 议,持续优化生产线性能,提高企业竞争 力。
品一致性。
喷涂参数监控
实时监测喷涂过程中的温度、湿度 、压力等关键参数,确保涂层质量 和工艺稳定性。
闭环反馈控制
通过传感器采集生产线运行数据, 经分析处理后调整喷涂参数,实现 喷涂过程的精准控制。
环保与节能技术
环保涂料
选用低VOC(挥发性有机物)环 保涂料,降低涂装过程中的环境
污染,提高生产线环保水平。
工程喷淋系统特写设计方案
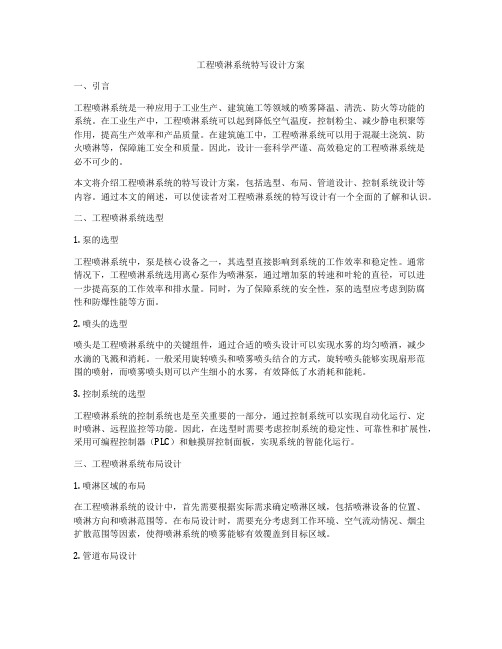
工程喷淋系统特写设计方案一、引言工程喷淋系统是一种应用于工业生产、建筑施工等领域的喷雾降温、清洗、防火等功能的系统。
在工业生产中,工程喷淋系统可以起到降低空气温度,控制粉尘、减少静电积聚等作用,提高生产效率和产品质量。
在建筑施工中,工程喷淋系统可以用于混凝土浇筑、防火喷淋等,保障施工安全和质量。
因此,设计一套科学严谨、高效稳定的工程喷淋系统是必不可少的。
本文将介绍工程喷淋系统的特写设计方案,包括选型、布局、管道设计、控制系统设计等内容。
通过本文的阐述,可以使读者对工程喷淋系统的特写设计有一个全面的了解和认识。
二、工程喷淋系统选型1. 泵的选型工程喷淋系统中,泵是核心设备之一,其选型直接影响到系统的工作效率和稳定性。
通常情况下,工程喷淋系统选用离心泵作为喷淋泵,通过增加泵的转速和叶轮的直径,可以进一步提高泵的工作效率和排水量。
同时,为了保障系统的安全性,泵的选型应考虑到防腐性和防爆性能等方面。
2. 喷头的选型喷头是工程喷淋系统中的关键组件,通过合适的喷头设计可以实现水雾的均匀喷洒,减少水滴的飞溅和消耗。
一般采用旋转喷头和喷雾喷头结合的方式,旋转喷头能够实现扇形范围的喷射,而喷雾喷头则可以产生细小的水雾,有效降低了水消耗和能耗。
3. 控制系统的选型工程喷淋系统的控制系统也是至关重要的一部分,通过控制系统可以实现自动化运行、定时喷淋、远程监控等功能。
因此,在选型时需要考虑控制系统的稳定性、可靠性和扩展性,采用可编程控制器(PLC)和触摸屏控制面板,实现系统的智能化运行。
三、工程喷淋系统布局设计1. 喷淋区域的布局在工程喷淋系统的设计中,首先需要根据实际需求确定喷淋区域,包括喷淋设备的位置、喷淋方向和喷淋范围等。
在布局设计时,需要充分考虑到工作环境、空气流动情况、烟尘扩散范围等因素,使得喷淋系统的喷雾能够有效覆盖到目标区域。
2. 管道布局设计工程喷淋系统的管道布局设计也是至关重要的一环,通过合理的管道布局可以减少水阻力和能耗,保障系统的高效运行。