数控车床的切削振动分析与控制方案
车削加工中的振动及防控措施

2 车NJ j n - r 中振动产生 的原 因
2 . 1 强迫振 动产 生 的原 因
强 迫振 动来 自于系统 内部 或外 部非 切削 因素 的干 扰力 , 如下 所述 :
( 1 ) ) 车床 回转零件 的离心惯性力. 机床工作时 , 高速旋转的主轴、 皮带轮 、 联轴节和工件等存在微
量 或少 数相 对 比较严 重 的质量偏 心 , 由离 心力 作用 引起 强迫 振动 . ( 2 ) 车床 运动传 递 机构 的缺 陷. 如 变 速 操 纵机 构 中 的齿轮 的制 造 、 安装 误 差 , 带 传 动 中平皮 带 的接 头、 三角 皮带 的厚 薄或 长短 不一 致 , 滑动轴 承 和滚动 轴 承尺 寸及形 位误 差 等都会 在运 动传 递过 程 中引起
1 . 1 强 迫振 动
在 工艺 系统 内部或 外部 周期性 干扰 力持 续作 用下 引起 的振动 称为 强迫振 动 , 其 主要 特点 如下 : ( 1 ) 强迫 振动 的干扰 力来 自于非切 削 因素 , 一般 与切 削过 程无关 , 振 动本 身不能 改变 干扰力 . ( 2 ) 强迫 振动 的振 幅在干 扰力 的频率 与 系统 固有频 率相 同或 接 近时 产生 共振 幅值最 大 , 此外 , 影 响 因素还 有干扰 力 的大小 、 工 艺系统 刚度及 其 阻尼 系数 .
切削力的突然变化 , 工艺系统的平衡被破坏而引起 的振动 , 一般去除外力冲击等 因素后, 因工艺系统存 在阻尼 可迅 速衰 减 , 对 加工 过程影 响较 小 ; 而 强迫 振动 和 自激 振动 都是 机械加 工过 程 中常见 的不能 自然 衰减而 且危 害较 大 的振 动类 型 , 因此 , 本 文重 点分 析车 削加工 中产 生 的两种 主要振 动类 型—— 强迫 振动 和 自激 振 动.
浅谈如何控制车削加工中的振动现象

浅谈如何控制车削加工中的振动现象机械加工过程中由于加工刀具、夹具、机床以及工件的动态特性会产生相应的振动,这些振动的产生又会反作用到工艺系统。
文章通过对振动的类型进行分析,并对振动的危害进行了详细的探讨,分别从夹具方面、刀具方面以及工艺方面对消除切削的振动现象做出一定合理的建议,并提出了一些意见。
标签:高频振动;低频振动;车削加工前言切削的过程中由于刀具工件以及夹具会相互之间产生作用力,在这种力的作用下相互之间产生了振动,这种振动在工件的加工中不可避免的会产生,但是其产生会对切削的过程造成干扰,会使得工件表面的加工质量受到严重的影响,同时受到振动影响刀具以及机床的寿命也会相应的缩短。
同时,振动的产生会相应的造成噪音,这种噪声的产生也影响着操作人员的健康以及情绪,这些都会对正常的工作造成负面的影响。
通过对加工的进刀量进行减少可以相应的降低振动的产生,但是这样一来生产的效率就会受到影响。
本人从事切削加工工作多年,在工作中通过观察、实践、分析,总结出一些关于如何在不影响生产效率的基础上有效的降低振动的产生的措施,在此同各位相互探讨。
1 振动的分类对于振动,在机械的加工过程中,由于各个部件相互会在机械运作中产生作用,这种作用力下产生的振动主要有受迫振动以及自激振动,这和夹具、机床以及道具、工件的动态特性相关。
对于机床,主要的振动来自回转组件和传动系统,在对此类振动进行消除后,车削加工中所产生的振动就不是由于速度变化而产生的,而是自激振动,而自激振动是同工件所具有的频率相接近的低频振动,主要是由于加工过程中工件的弯曲所造成的,弯曲震动不仅仅会产生在工件的弯曲变化上,同时在车刀上也会存在,这种车道上的变形振动同车刀自身的频率相近,即是高频振动。
2 产生的原因振动的主要特点就是频率不同,低频振动顾名思义就是具有较低的振频,其振动产生的声音相对低沉,并且振动幅度较大,其作用的结果就是会在加工的工件表面留下宽而深的痕迹,这就是振动痕迹。
车削加工中振动的控制方法研究
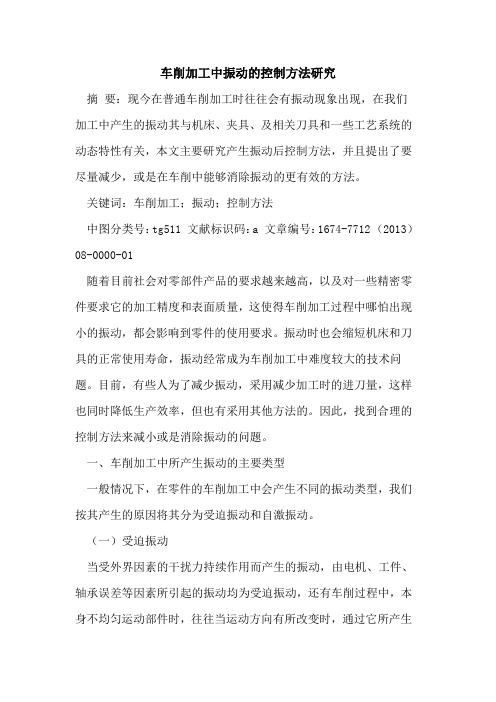
车削加工中振动的控制方法研究摘要:现今在普通车削加工时往往会有振动现象出现,在我们加工中产生的振动其与机床、夹具、及相关刀具和一些工艺系统的动态特性有关,本文主要研究产生振动后控制方法,并且提出了要尽量减少,或是在车削中能够消除振动的更有效的方法。
关键词:车削加工;振动;控制方法中图分类号:tg511 文献标识码:a 文章编号:1674-7712 (2013)08-0000-01随着目前社会对零部件产品的要求越来越高,以及对一些精密零件要求它的加工精度和表面质量,这使得车削加工过程中哪怕出现小的振动,都会影响到零件的使用要求。
振动时也会缩短机床和刀具的正常使用寿命,振动经常成为车削加工中难度较大的技术问题。
目前,有些人为了减少振动,采用减少加工时的进刀量,这样也同时降低生产效率,但也有采用其他方法的。
因此,找到合理的控制方法来减小或是消除振动的问题。
一、车削加工中所产生振动的主要类型一般情况下,在零件的车削加工中会产生不同的振动类型,我们按其产生的原因将其分为受迫振动和自激振动。
(一)受迫振动当受外界因素的干扰力持续作用而产生的振动,由电机、工件、轴承误差等因素所引起的振动均为受迫振动,还有车削过程中,本身不均匀运动部件时,往往当运动方向有所改变时,通过它所产生的惯性压迫都能产生受迫振动。
而这种振动一般不会自行进行衰减,反而会逐渐引起机床的共振,从而使得对加工过程会产生许多不必要的影响。
(二)自激振动当在车削加工时,有一些振动它主要是由系统本身在车削振动过程中所激发产生的,不随车削速度变化的自激振动,那么它的频率就等同于系统的自身频率。
在工件切削表面会留下一些细小的痕迹,这种情况下,只有刀具自身在振动,而工件及机床等部件却很平静。
二、振动的控制方法研究在车削加工时,如何判断系统是否发生切削颤振,那么它既与切削过程有关,还是与系统的基本结构有关,但绝大部分情况下工件系统的振动较大,针对振动的特点,提出以下控制方法。
数控机床车削加工质量控制方法

数控机床车削加工质量控制方法摘要:随着经济的发展,数控机床车削加工技术是一种基于数字化技术与智能化终端的生产加工技术。
此项技术在零件的加工生产中,可以实现数控生产的高精度控制,保证加工生产的成果具有较高的质量与验收通过率。
根据目前数控机床车削加工技术的应用现状可以看出,我国大部分数控操作的技术人员自身水平较高,他们在实际应用中可以根据加工中的突发性情况,及时采取有效措施进行处理。
但随着行业的持续化发展,机械设备与生产加工零件结构越来越复杂,仅按照单一的生产加工技术难以满足组合零件的高精度生产需求。
在多种外界因素的联合作用下,产出的零件会出现不同程度上的质量问题,尤其是在零件批量生产过程中,一旦编定程序出现误差,便会对产出的零件造成不可逆的损伤,最终导致生产的成果质量不达标而被废弃或返修。
采取可行的措施,对生产中各项参数进行实时把控,提升数控机床车削加工质量与综合水平。
关键词:数控机床;车削加工;质量控制;方法引言为了进一步提升数控机床车削加工的质量与水平,提高零件加工验收的通过率,文章梳理了数控机床车的内容,分析了数控机床车削加工质量控制的重要意义,提出了数控机床车削加工质量控制措施,包括慎重考量工艺因素,如刀具材料和刀具几何参数的选择、切削液的合理选用、工件装夹方法的合理选择,也包括正确进行加工程序的编制和熟练掌握数控机床车的操作技能。
1数控机床车削加工质量控制的重要意义一般的机械加工都是应用普通机床通过手动操作的方法完成的,随着时代的发展,这种传统的车床已经不能满足现代化零件加工的需求。
传统车床已经逐渐被现代化工业机床中的数字化控制机床所取代,数控机床车的应用范围越来越广泛。
懂得数控技术的工作人员可以通过预先编制好的程序开展部件的加工生产。
在机械发展领域,数控机床得以广泛应用,进一步提升数控机床车削加工质量,对于整个行业发展影响深远。
数控机床车加工质量控制成为国家工业高质量生产、持续发展的根本保证,尤其是数控机床车削加工的质量控制,作为工业生产最基础、最根本的生产加工环节,是有效提升工业整体加工质量的有效方法,是大幅度提升工业的国际竞争力,开拓国际市场的有效途径,更是数控机床车加工领域能够在激烈的市场竞争中得以生存下来的保护伞。
数控机床震动的原因及控制方法
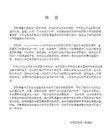
1:机床振动,因你是简式数控,传动箱相对复杂,齿轮传递较多,且主轴轴承精度肯定不如数控机床,故高速切削有振动;
2:另,如果不是标准的轴类零件,夹具配重很关键,如果不能保证主轴(夹具)的动平衡,再好的机床也会有振动
3:机床在快速移动时震动或冲 击,原因是伺服电机内的检测接触不良
4:机床以低速运行时,机床工作台是蠕动着向前运动;机床要以高速运行时,就出现震动。
采用这些方法后,还做不到完全消除振动,甚至是无效的,就要考虑对速度调节器板更换或换下后彻底检查各处波形。
解决办法:
机床爬行和振动问题是属于速度的问题。既然是速度的问题就要去找速度环,我们知道机床的速度的整个调节过程是由速度调节器来完成的。特别应该着重指出,速度调节器的时间常数,也就是速度调节器积分时间常数是以毫秒计的,因此,整个机床的伺服运动是一个过渡过程,是一个调节过程。 凡是与速度有关的问题,只能去查找速度调节器。因此,机床振动问题也要去查找速度调节器。可以从以下这些地方去查找速度调节器故障:一个是给定信号,一个是反馈信号,再一个就是速度调节器的本身。 第一个是由位置偏差计数器出来经D/A转换给速度调节器送来的模拟是VCMD,这个信号是否有振动分量,可以通过伺服板上的插脚(FANUC6系统的伺服板是X18脚)来看一看它是否在那里振动。如果它就是有一个周期的振动信号,那毫无疑问机床振动是正确的,速度调节器这一部分没有问题,而是前级有问题,向D/A转换器或偏差计数器去查找问题。如果我们测量结果没有任何振动的周期性的波形。那么问题肯定出在其他两个部分。 我们可以去观察测速发电机的波形,由于机床在振动,说明机床的速度在激烈的振荡中,当然测速发电机反馈回来的波形一定也是动荡不已的。但是我们可以看到,测速发电机反馈的波形中是否出现规律的大起大落,十分混乱现象。这时,我们最好能测一下机床的振动频率与电机旋转的速度是否存在一个准确的比率关系,譬如振动的频率是电机转速的四倍频率。这时我们就要考虑电机或测速发电机有故障的问题。 因为振动频率与电机转速成一定比率,首先就要检查一下电动机是否有故障,检查它的碳刷,整流子表面状况,以及机械振动的情况,并要检查滚珠轴承的润滑的情况,整个这个检查,可不必全部拆卸下来,可通过视察官进行观察就可以了,轴承可以用耳去听声音来检查。如果没有什么问题,就要检查测速发电机。测速发电机一般是直流的。 测速发电机就是一台小型的永磁式直流发电机,它的输出电压应正比于转速,也就是输出电压与转速是线性关系。只要转速一定,它的输出电压波形应当是一条直线,但由于齿槽的影响及整流子换向的影响,在这直线上附着一个微小的交变量。为此,测速反馈电路上都加了滤波电路,这个滤波电路就是削弱这个附在电压上的交流分量。 测速发电机中常常出现的一个毛病就是炭刷磨下来的炭粉积存在换向片之间的槽内,造成测速发电机片间短路,一旦出现这样的问题就避免不了这个振动的问题。 这是因为这个被短路的元件一会在上面支路,一会在下面支路,一会正好处于换向状态,这3种情况就会出现3种不同的测速反馈的电压。在上面支路时,上面支路由于少了一个元件,电压必然要小,而当它这个元件又转到了下面支路时,下面的电压也小,这时不论在上面支路,还是在下面支路中,都必然使这两条支路的端电压下降,且有一个平衡电流流过这两条并联的支路,又造成一定的电压降。当这个元件处于换向,正好它也处于短路,这时上下两个支路没有短路元件,电压得以恢复,且也无环流。这样,与正常测速发电机状态一样。为此,三种不同情况下电压做了一个周期地变化,这个电压反馈到调节器上时,势必引起调节器的输出也做出相应地,周期地变化。这是仅仅说了一个元件被短路。特别严重时有一遍换向片全部被碳粉给填平了,全部短路,这样就会更为严重的电压波动。 反馈信号与给定信号对于调节器来说是完全相同的。所以,出现了反馈信号的波动,必然引起速度调节器的反方向调节,这样就引起机床的振动。 这种情况发生时,非常容易处理,只要把电机后盖拆下,就露出测速发电机的整流子。这时不必做任何拆卸,只要用尖锐的勾子,小心地把每个槽子勾一下,然后用细砂纸光一下勾起的毛刺,把整流片表面再用无水酒精擦一下,再放上炭刷就可以了。这里特别要注意的是用尖锐的勾子去勾换向片间槽口时,别碰到绕组,因为绕组线很细,一旦碰破就无法修复,只有重新更换绕组。再一个千万不要用含水酒精去擦,这样弄完了绝缘电阻下降无法进行烘干,这样就会拖延修理期限。
数控机床加工过程中的振动问题分析与解决方法

数控机床加工过程中的振动问题分析与解决方法摘要:数控机床在现代制造业中扮演着至关重要的角色。
然而,数控机床加工过程中常常会出现一些振动问题,对加工质量和机床寿命产生不利影响。
本文将对数控机床加工过程中的振动问题进行分析,并提出一些解决方法,以帮助生产厂商和操作工人提高加工效率和质量。
1. 引言数控机床是一种高效、精度高的自动化加工工具,广泛应用于航空航天、汽车制造、模具加工等领域。
然而,由于机床部件的不完美和操作过程中的一些因素,振动问题成为数控机床加工过程中的一大难题。
振动问题不仅会降低加工质量,还可能导致零件和机床的损坏。
2. 振动问题的分析2.1 振动的类型数控机床加工过程中主要有三种振动类型:一是切削振动,即刀具与工件之间的相互振动;二是结构振动,即机床各个部件之间的振动;三是外界扰动引起的振动,如地震、风噪等。
2.2 振动的影响因素数控机床加工过程中振动问题的产生受到多种因素的影响,包括刀具磨损、工件材料、切削参数、机床刚性等。
其中,刀具磨损是导致振动问题的主要原因之一,它会导致切削力的不稳定,进而引起振动。
3. 振动问题的解决方法针对数控机床加工过程中的振动问题,以下是几种常见的解决方法:3.1 刀具磨损的监测与更换刀具磨损是导致振动问题的主要因素之一。
因此,监测刀具磨损状态非常重要。
可以使用传感器监测切削力和振动信号,通过专业软件进行分析,及时判断刀具磨损情况,一旦发现刀具磨损过大,应及时更换刀具,以保证加工质量和机床的稳定性。
3.2 提高机床刚性机床刚性对振动问题的解决至关重要。
在设计和制造过程中,应注重机床的刚性要求,尤其是在剧烈振动的切削区域,适当增加机床的刚性,减小振动的幅度。
此外,还可以采用补偿措施,如增加减振材料或采用补偿装置,以减少机床振动。
3.3 切削参数的优化切削参数是影响振动问题的重要因素之一。
通过优化切削参数,如切削速度、进给速度、切削深度等,可以减小振动的幅度。
数控机床切削时振动的消减方法探讨

数控机床切削时振动的消减方法探讨作者:李玉洁来源:《读天下》2019年第15期摘要:在生产加工过程中,数控机床切削时难免会产生不同程度的振动,其中包括有害振动和可利用振动。
有害的振动对加工工艺和工件的加工质量以及数控机床寿命都有很大影响,而且还会影响生产效率。
因此,减少数控机床振动的产生,对控制产品的质量非常关键。
本文主要从机械加工的工艺层面对数控机床切削加工时产生振动的各种原因进行归纳总结,分析了数控机床振动对产品加工质量造成的影响,并提出了有力的解决措施,在机械制造领域有一定的参考作用。
关键词:数控机床;振动;消减措施随着我国机床工业的飞速发展,机床的振动问题也就越来越引起人们的重视。
机床在切削过程中振动,最常见于车床,镗床加工过程中,造成工件表面有颤纹,返工率、废品率高,伴有震刀打刀现象,这样会影响其工件的精度。
机床工作时产生的振动,不仅会影响机床的动态精度和被加工零件的质量,而且还要降低生产效率和刀具的耐用度,振动剧烈时甚至会降低机床的使用性能,伴随振动所发出的噪音会影响机床工人的健康。
一、数控机床切削加工振动产生的原因数控机床切削加工过程中所发生的振动是非常复杂的,引起振动的原因也是多方面的,主要有以下几个方面:(一)操作人员的因素机床操作人员业务水平不高,缺乏丰富实践生产经验,部分技术人员责任心不强,设备维护水平低,缺乏正确使用和保养数控机床设备的意识。
(二)机床的因素一些厂家生产的数控机床自身的抗振性能较差,没有具备生产加工所需要的系統刚性;数控机床零件加工和装配质量方面缺乏合理保养数控机床;数控机床活顶尖伸出过长,轴承已受损而继续切削等。
(三)刀具的因素刀具选用过程中没有利用成型刀片进行成形车削;刀具的角度特别是主偏角,后角,前角等误差较大;刀刃的锋利程度不够;刀尖圆弧半径过大;切削参数不合适等。
这些因素会使刀具磨损加剧或引起切屑瘤、拉毛工件表面或出现打刀引起振动而影响产品质量。
机床振动原因分析及控制方法

机床振动原因分析及控制方法摘要:机床在工作过程中常会出现一种不利因素—振动,它不仅影响工件的表面质量和加工精度,还会影响刀具的耐用度和机床寿命,恶化工作环境,影响工人健康。
关键词:振动原因控制方法1、机床振动的影响及原因分析1.1机床方面在金属的切削加工过程中,工件的几何形状精度、表面粗糙度、尺寸精度都出现超差等质量问题,这些问题都与机床的振动有关系,而引起机床振动有时是由机床本身存在的故障造成的。
下面以车床为例进行说明车床哪些原因会产生振动及产生的影响:1.1.1工件几何形状精度超差(1)工件出现圆度超差主要原因有主轴轴颈、轴承内滚道或箱体孔圆度超差或者轴承磨损、主轴轴承间隙过大等。
(2)工件圆柱度超差主要原因为车床导轨磨损引起主轴轴线与床身导轨不平行或导轨水平方向直线度超差。
1.1.2工件表面粗糙度达不到要求(1)精车后,表面有螺旋状振纹产生的原因有:主轴齿轮精度降低,啮合不良;主轴与主轴轴承的间隙过大,主轴轴颈的圆度超差,轴承制造精度不够。
(2)精车后,表面出现乱纹产生的原因可能是主轴轴承磨损,也可能是游隙过大。
(3)精车端面平面度超差由于主轴轴向窜动量超差或者床鞍横向导轨对主轴轴线不垂直或平行度超差造成的。
(4)切断困难切断时发生振动,原因主要是主轴径向间隙过大,刀架滑板间隙过大,横向进给丝杠螺母间隙未消除,切断刀装夹时伸出过长,三爪自定心卡盘与主轴配合定位面间隙过大。
(5)车削螺纹时螺纹表面有波纹原因是主轴轴向游隙过大,传动链中的挂轮间隙过大,溜板箱的长丝杠轴向游隙过大,开合螺母滑道间隙过大,跟刀架太松或太紧等。
1.2刀具方面刀具的材料不合适,刚性差、切削刃角度选择不合适是引起振动的主要原因。
切削时由于刃口高度的误差或因断续切削引起的冲击,容易产生振动。
出现振动会降低刀具的使用寿命:影响了刀具的正常切削条件,加快了刀具磨损,还可能引起刀具的崩裂,机床、夹具连接部分松动,缩短刀具及机床、夹具的使用寿命。
车床的震动及预防措施
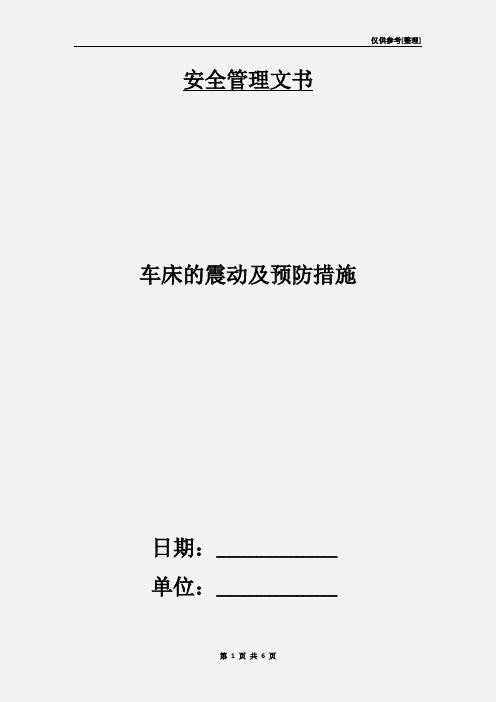
仅供参考[整理] 安全管理文书车床的震动及预防措施日期:__________________单位:__________________第1 页共6 页车床的震动及预防措施1振动车削加工过程中,工件和刀具之间常常发生强烈的振动,破坏和干扰了正常的切削加工,是一种极其有害的现象。
当车床发生震动时,工件表面质量恶化,产生明显的表面振纹,工件的粗糙度增大,这时必须降低切削用量,使车床的工作效率大大降低。
强烈振动时,会时车床产生崩刃现象,使切削加工过程无法进行下去。
由于振动,将使车床和刀具磨损加剧,从而缩短车床和刀具的使用寿命;振动并伴随有噪音,危害工人身心健康,使工作环境恶化。
车床振动可公为自由振动、强迫振动和自系振动,据测算,这三类振动分别5%,30%,65%。
当振动系统的平衡被破坏,弹性力来维持系统的振动,称为自由振动(如图1),在外界周期性干扰力持续作用下,被迫产生的振动称为强迫振动(如图2),由振动过程本身引起切削力周期性变化,又由这个周期性变化的切削力反过来加强和维持的振动称为自激振动(如图3)。
图1图2图32车床振动的振源寻找振动的来源,并加以排除或限制,是有效控制振动的途径。
振源来自车床内部的,称为机内振源;来自车床外部的,称为机外振源。
由于自由振动是由切削力的突然变化或其它外力冲击引起的,可快速衰减,对车床加工过程影响非常小,可以忽略不计。
强迫振动的振源机内振源:车床上各个电动机的振动,包括电动机转子旋转不平衡及电磁力不平衡引起的振动;机床回转零件的不平衡,如皮带轮、卡盘、刀盘和工件不平衡引起的振动;运动传递过程中引起的振动,如变速操纵机机构中的齿轮啮合时的冲击力,卸荷带轮把径向载荷卸给箱体时的振动,三角皮带的厚度不均匀,皮带轮质量偏心,双向多片摩擦离合器,滑动轴承和滚动轴承尺寸及形位误差引起的振动;往复第 2 页共 6 页部件运动的惯性力,如离和器控制箱体的正反转引起的惯性力振动;切削时的冲击振动,如切削带有键槽的工件表面时循环冲击载荷引起的振动;车床液压传动系统的压力脉动。
金属切削加工中的振动分析及控制途径

金属切削加工中的振动分析及控制途径摘要:在金属切削加工过程中,如果产生振动,会造成很多不良的影响,不仅严重影响机器和零部件本身的性能和工艺,而且振动中产生的噪音还会对操作者本身的身体健康产生有害的影响。
本文将通过分析金属切削加工中产生振动的原因、主要类型和特点,重点提出控制甚至消除振动的有效途径,以促进金属切削加工技术的发展。
关键词:切削加工振动原因振动类型振动特点控制途径引言:近些年来,随着机械制造行业的不断发展,各种先进的制造技术也不断被研发出来,金属切削加工则是这些技术中的佼佼者,已经被应用到各个领域的机械制造和生产中。
在设计机床和刀具、制订机器零件的切削工艺及其定额、合理地使用刀具和机床以及控制切削过程时,都要利用金属切削原理的研究成果,使机器零件的加工达到经济、优质和高效率的目的。
金属切削加工过程中,刀具与工件之间相互作用和各自的变化规律现已经成为了一门学科。
在金属切削加工过程中,如果产生振动,会造成很多不良的影响,不仅严重影响机器和零部件本身的性能和工艺,而且振动中产生的噪音还会对操作者本身的身体健康产生有害的影响。
下面本文将通过分析金属切削加工中产生振动的原因、主要类型和特点,重点提出控制甚至消除振动的有效途径。
一、振动的基本类型从一般情况而言,在金属切削加工过程中所产生的振动大致可以分为两种类型,即:自激振动和强迫振动。
相比较而言,这两种振动中自激振动的概论一般低于40%,而强迫振动则占主要方面,大约为60%。
二、产生振动的主要原因通过统计分析我们可以清晰的看出,金属切削加工过程中产生振动的类型基本分为两种:自激振动和受迫振动。
因此,在机械制造过程中,根据这两种不同类型的振动,可以通过机床不同的运行状态来分析振动产生的原因。
(一)空转时存在的振动及原因分析当机床在空转时也有可能产生一定的振动。
造成振动的主要原因可能是床鞍导轨之间的爬行,也可能是是由于外部传来的振动,例如:地基周期或者非周期的干扰力。
机床切削时的振动分析
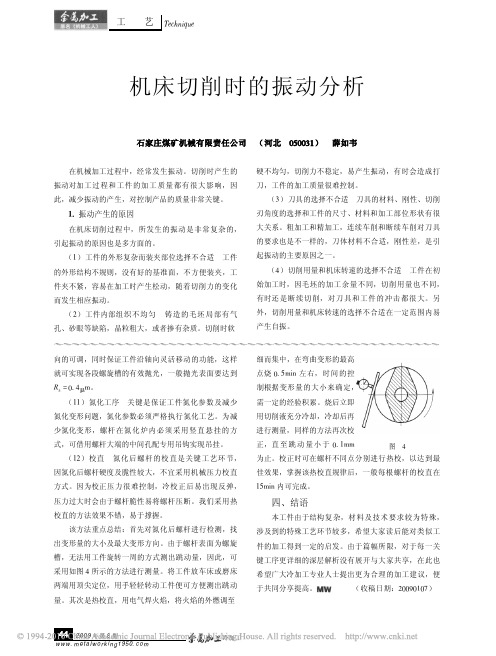
!" 振动产生的原因
在机床切削过程中,所发生的振动是非常复杂的, 引起振动的原因也是多方面的。 ( " ) 工件的外形复杂而装夹部位选择不合适 ! 工件 的外形结构不规则,没有好的基准面,不方便装夹,工 件夹不紧,容易在加工时产生松动,随着切削力的变化 而发生相应振动。 ( # ) 工件内部组织不均匀 ! 铸造的毛坯局部有气 孔、砂眼等缺陷,晶粒粗大,或者掺有杂质。切削时软
由于篇幅所限对于每一关键工序更详细的深层解析没有展开与大家共享在此也希望广大冷加工专业人士提出更为合理的加工建议便于共同分享提高
! ! ! ! ! ! !
工! ! 艺
!"#$%&’("
! ! !
机床切削时的振动分析
石家庄煤矿机械有限责任公司! ( 河北 ! "#""$% ) ! 薛如韦
! ! 在机械加工过程中,经常发生振动。切削时产生的 振动对加工过程和工件的加工质量都有很大影响,因 此,减少振动的产生,对控制产品的质量非常关键。 硬不均匀,切削力不稳定,易产生振动,有时会造成打 刀,工件的加工质量很难控制。 ( $ ) 刀具的选择不合适! 刀具的材料、刚性、切削 刃角度的选择和工件的尺寸、材料和加工部位形状有很 大关系。粗加工和精加工,连续车削和断续车削对刀具 的要求也是不一样的,刀体材料不合适,刚性差,是引 起振动的主要原因之一。 ( % ) 切削用量和机床转速的选择不合适 ! 工件在初 始加工时,因毛坯的加工余量不同,切削用量也不同, 有时还是断续切削,对刀具和工件的冲击都很大。另 外,切削用量和机床转速的选择不合适在一定范围内易 产生自振。
!" 振动对加工质量的影响
振动对加工质量的影响是非常大的,主要表现在以 下几个方面: ( $ ) 振动降低了加工表面的质量! 加工过程中的振 动,引起加工表面的振动波纹,表面粗糙度值大。它还 会使工件和刀具之间产生相对位移,影响正常的运动轨 迹。这样,就降低了加工表面的质量和尺寸精度。 ( % ) 降低了刀具的使用寿命! 由于振动的产生,影 响刀具的正常切削条件,加快了刀具的磨损,甚至会引 起切削刃的崩裂,大大降低了刀具的使用寿命。 ( & ) 影响和降低了生产效率 ! 为了避免剧烈的振 动,不得不降低切削用量。同时,由于降低了刀具的使 用寿命,频繁换刀、磨刀,使生产效率下降。 ( ’ ) 使机床的原始精度下降! 由于振动使机床的运 动元件之间松动,间隙增大,加快了机床零件的磨损, 造成机床精度下降,影响切削质量,降低机床的使用寿 命。 ( " ) 影响工作环境! 因振动会产生刺耳的噪声,使 操作者的身心健康受到损害,降低工作效率。
数控机床加工过程中的振动问题分析与解决方法

数控机床加工过程中的振动问题分析与解决方法摘要:数控机床作为现代制造业中不可或缺的设备,在加工过程中常常会出现振动问题,影响加工质量和工件精度。
本文将通过分析数控机床加工过程中的振动问题,探讨其成因,并提出相应的解决方法,帮助读者深入了解振动问题的本质,有效提高加工效率和质量。
一、引言数控机床在现代制造业中起着重要的作用,它能够实现高精度、高效率的加工,大大提高了生产效率。
然而,随着加工要求的不断提高,数控机床加工过程中的振动问题日益凸显。
振动不仅会降低加工精度,还可能对设备和工具产生损坏,给生产带来困扰。
因此,对数控机床加工中的振动问题进行深入研究和解决具有重要意义。
二、振动问题分析1. 振动的成因数控机床加工过程中的振动主要来自以下几个方面:(1) 机床结构:数控机床的结构设计和制造精度直接影响振动的程度。
结构刚性不足、材料强度不足等因素都可能引发振动问题。
(2) 切削力:切削过程产生的切削力对机床和工件均会引起振动。
过大的切削力会导致机床振动加剧,影响加工质量。
(3) 刀具状况:刀具的质量和磨损情况对振动问题有直接影响。
使用损坏的刀具或过长的刀具都会引发振动。
(4) 工件形状:工件的不规则形状也会导致振动产生。
尤其是工件不平衡时,会产生不均匀的振动。
2. 振动对加工质量的影响数控机床加工过程中的振动问题会对加工质量产生显著的影响:(1) 表面粗糙度:振动导致切削过程受到干扰,使得工件表面粗糙度增加。
(2) 尺寸偏差:振动会导致加工过程中的切削位置偏移,使得工件尺寸产生偏差。
(3) 加工精度:振动会使得机床无法精确控制切削过程,从而降低加工精度。
三、解决方法为解决数控机床加工过程中的振动问题,可以采取以下方法:1. 提高机床结构刚性通过改进机床结构设计和加强结构材料的强度,提高机床的刚性。
这样可以减少机床在加工过程中的变形,降低振动的产生。
2. 优化切削参数和工具选择合理设置切削参数,控制切削速度、进给速度和切削深度等参数。
fanuc数控机床剧烈抖动
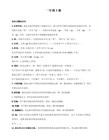
1)切断驱动器电源,将设定端S1置TEST。
2)接通驱动器电源。
3)同时按住MODE、UP、DOWN、DATASET4个键
4)当显示器由全暗变为“FFFFF”后,松开全部键, 并保持1s以上。
5)同时按住MODE、UP键,使参数显示FC-22。
分析与处理过程:为了判别主轴过电流报警产生的原因,维修时首先脱开了主轴电动机与主轴间的联接,检查机械传动系统,未发现异常,因此排除了机械上的原因。
接着又测量、检查了电动机的绕组、对地电阻及电动机的连接情况,在对换向器及电刷进行检查时,发现部分电刷已到达使用极限,换向器表面有严重的烧熔痕迹。
1)取下直流母线熔断器F7,合上交流电源,输入旋转指令。
2)按表7-26、表7-27的引脚,通过驱动器的连接插座CN6、CN7,测定8个晶体管(型号为ETl91)的基极B与发射极E间的控制电压,并根据CN6、CN7插脚与各晶体管管脚的对应关系逐一检查(以发射极为参考,测量B-E正常值一般在2V左右)。检查发现1C~lB之间电压为0V,证明C~B极击穿,同时发现二极管D27也被击穿。
2)电动机连续过载。
3)电动机绕组存在局部短路。
在以上几点中,根据现场实际加工情况,电动机过载的原因可以排除。考虑到换上元器件后,驱动器可以正常工作数天,故主轴驱动器控制板不良的可能性亦较小。因此,故障原因可能性最大的是电动机绕组存在局部短路。
由于实际机床发生报警时,只是Z轴向下移动,主轴电动机并没有旋转,同时也不发热。考虑到主轴电动机是伴随着Z轴一起上下移动,据此可以大致判定故障是由于Z轴移动,引起主轴电动机电缆弯曲,产生接触不良所致。
打开主轴电动机接线盒检查,发现接线盒内插头上的主轴电动机热敏电阻接线松动;重新连接后,故障排除,机床恢复正常。