首钢高炉造渣制度的几点认识
钢铁企业高炉炉渣处理管理制度

钢铁企业高炉炉渣处理管理制度随着我国工业化进程的不断加快,钢铁行业作为重要的基础产业之一,在国民经济中起着举足轻重的作用。
然而,钢铁生产过程中产生的大量高炉炉渣,给环境保护和资源利用带来了严峻挑战。
因此,建立并完善钢铁企业高炉炉渣处理管理制度显得尤为重要。
首先,钢铁企业应建立科学合理的高炉炉渣处理流程。
在高炉运行过程中,产生的炉渣主要分为炉缸炉渣、炉缸渣、煤气渣和底渣等。
这些炉渣的特性各异,因此需要根据具体情况制定不同的处理方案。
例如,对于含铁较高的炉缸炉渣,可以采用回收铁矿石的方式进行资源化利用,以降低资源浪费和环境污染。
对于废渣中的有害物质,应使用先进的技术手段进行处理,确保达到环保标准要求。
其次,钢铁企业应加强高炉炉渣处理的技术研发和创新。
当前,国内外研究机构已经在高炉炉渣处理领域取得了一些研究成果。
钢铁企业应与科研机构、高校等合作,加大技术研发力度,推动炉渣处理技术的革新。
例如,可以发展高炉炉渣块状化技术,将炉渣加工成块状产品,便于运输和储存,同时也有利于资源回收利用。
另外,可以探索高炉炉渣在建筑材料、土壤修复、水泥生产等领域的应用,为炉渣的资源化利用提供更多的可能性。
第三,钢铁企业应建立高炉炉渣处理的监督机制。
在炉渣处理过程中,企业需要确保操作符合相关法律法规,并具有可追溯性。
因此,建立起健全的监督机制势在必行。
相关监督机构应加强对钢铁企业的监督力度,随时检查与核查企业的炉渣处理情况,确保企业按照规定进行炉渣处理。
同时,钢铁企业也应主动加强自身的监管,建立起内部管理制度,加强对炉渣处理流程的控制和监督,确保炉渣处理合规合法。
最后,钢铁企业应加大对员工的培训和教育力度。
高炉炉渣处理是一个复杂而技术性较强的工作,需要员工具备相关的专业知识和操作技能。
因此,企业应加强对员工的培训和教育,提高他们的技能水平和工作质量。
只有如此,员工才能更好地处理高炉炉渣,降低处理过程中的环境污染和资源浪费。
综上所述,钢铁企业高炉炉渣处理管理制度的建立与完善,对于保护环境、节约资源,提高工业生产效益具有重要意义。
高炉渣的冶金性能及造渣制度

第41卷 第4期 2006年4月钢铁Iron and Steel Vol.41,No.4April 2006高炉渣的冶金性能及造渣制度李福民1,2, 吕 庆2, 胡宾生2, 于 勇3, 陶 文3(1.东北大学材料与冶金学院,辽宁沈阳110004; 2.河北理工大学冶金与能源学院,河北唐山063009;3.唐山钢铁公司炼铁厂,河北唐山063000)摘 要:针对唐钢高炉大量采用高品位、低SiO 2含量、高Al 2O 3含量的外矿的特点,研究了在新的配矿结构下,炉渣碱度(CaO/SiO 2)、MgO 含量和Al 2O 3含量对唐钢高炉炉渣的粘度、熔化性温度、脱硫能力的影响。
唐钢高炉合理的造渣制度为:保持炉渣温度稳定,碱度控制在1110左右,MgO 的质量分数控制在11%左右,通过合理配煤,适当使用部分冀东矿的方法尽量降低炉渣的Al 2O 3含量。
关键词:外矿;高炉渣;冶金性能;造渣制度中图分类号:TF53411 文献标识码:A 文章编号:04492749X (2006)0420019204Metallurgical Properties of BF Slag and Slagging R egimeL I Fu 2min 1,2, L ΒQing 2, HU Bin 2sheng 2, YU Y ong 3, TAO Wen 3(1.School of Materials and Metallurgy ,Northeastern University ,Shenyang 110004,Liaoning ,China ;2.School of Metallurgy and Energy ,Hebei Polytechnic University ,Tangshan 063009,Hebei ,China ;3.Ironmaking Plant ,Tangshan Iron and Steel Co.,Ltd.,Tangshan 063000,Hebei ,China )Abstract :For charging large amount of imported high grade iron ore with low SiO 2and high Al 2O 3,the influence of basicity ,MgO and Al 2O 3content on viscosity ,melting temperature and desulf urizing capacity of BF slag was stud 2ied.The optimal slagging regime is :CaO/SiO 2is about 1110,MgO content about 11%,and Al 2O 3is reduced to a minimum by rational coal blending and use of Jidong iron ore.K ey w ords :foreign iron ore ;blast f urnace slag ;metallurgical property ;slagging regime基金项目:河北省自然科学基金项目(E2005000431)作者简介:李福民(19712),男,博士生,副教授; E 2m ail :lq @heut 1edu 1cn ; 修订日期:2005206211 唐钢高炉的外矿使用比例(包括烧结使用的粉矿和高炉使用的块矿比例)已经超过了冀东矿。
首钢转炉“留渣-双渣”炼钢工艺技术开发与应用
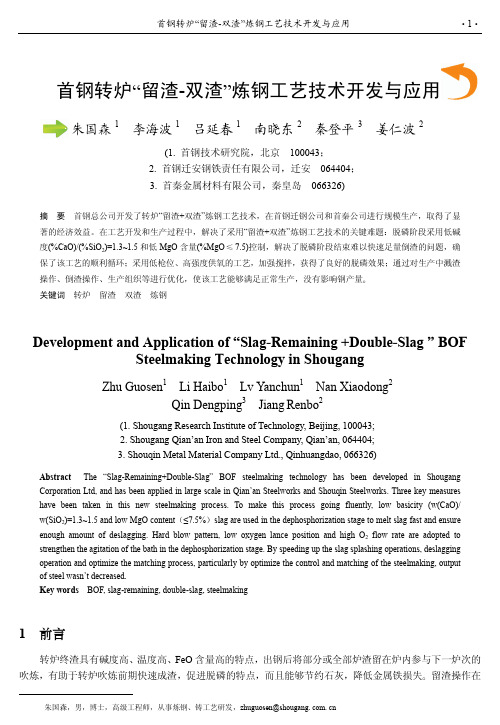
首钢转炉“留渣-双渣”炼钢工艺技术开发与应用朱国森1李海波1吕延春1南晓东2秦登平3姜仁波2(1. 首钢技术研究院,北京 100043;2. 首钢迁安钢铁责任有限公司,迁安 064404;3. 首秦金属材料有限公司,秦皇岛 066326)摘要首钢总公司开发了转炉“留渣+双渣”炼钢工艺技术,在首钢迁钢公司和首秦公司进行规模生产,取得了显著的经济效益。
在工艺开发和生产过程中,解决了采用“留渣+双渣”炼钢工艺技术的关键难题:脱磷阶段采用低碱度(%CaO)/(%SiO2)=1.3~1.5和低MgO含量(%MgO≤7.5)控制,解决了脱磷阶段结束难以快速足量倒渣的问题,确保了该工艺的顺利循环;采用低枪位、高强度供氧的工艺,加强搅拌,获得了良好的脱磷效果;通过对生产中溅渣操作、倒渣操作、生产组织等进行优化,使该工艺能够满足正常生产,没有影响钢产量。
关键词转炉留渣双渣炼钢Development and Application of “Slag-Remaining +Double-Slag ” BOFSteelmaking Technology in ShougangZhu Guosen1Li Haibo1 Lv Yanchun1 Nan Xiaodong2Qin Dengping3Jiang Renbo2(1. Shougang Research Institute of Technology, Beijing, 100043;2. Shougang Qian’an Iron and Steel Company, Qian’an, 064404;3. Shouqin Metal Material Company Ltd., Qinhuangdao, 066326)Abstract The “Slag-Remaining+Double-Slag” BOF steelmaking technology has been developed in Shougang Corporation Ltd, and has been applied in large scale in Qian’an Steelworks and Shouqin Steelworks. Three key measures have been taken in this new steelmaking process. To make this process going fluently, low basicity (w(CaO)/ w(SiO2)=1.3~1.5 and low MgO content(≤7.5%)slag are used in the dephosphorization stage to melt slag fast and ensure enough amount of deslagging. Hard blow pattern, low oxygen lance position and high O2 flow rate are adopted to strengthen the agitation of the bath in the dephosphorization stage. By speeding up the slag splashing operations, deslagging operation and optimize the matching process, particularly by optimize the control and matching of the steelmaking, output of steel wasn’t decreased.Key words BOF, slag-remaining, double-slag, steelmaking1前言转炉终渣具有碱度高、温度高、FeO含量高的特点,出钢后将部分或全部炉渣留在炉内参与下一炉次的吹炼,有助于转炉吹炼前期快速成渣,促进脱磷的特点,而且能够节约石灰,降低金属铁损失。
高炉矿渣的再生利用途径探讨

高炉矿渣的再生利用途径探讨高炉矿渣的再生利用途径探讨摘要:本文介绍了首钢水城钢铁(集团)有限责任公司高炉矿渣的产生和堆放现状,分析了高炉矿渣对环境的污染和影响,分析了高炉矿渣的再生利用途径,阐述了高炉矿渣再生利用中就注意的主要问题。
关键词:高炉矿渣;再生利用;途径1.引言高炉矿渣是冶炼生铁时从高炉中排出的一种废渣。
在高炉冶炼生铁时,从高炉加入的原料,除了铁矿石和燃料(焦炭)外,还要加入助熔剂。
当炉温达到1400一1600℃时,助熔剂与铁矿石发生高温反应生成生铁和矿渣。
高炉矿渣是由脉石、灰分、助熔剂和其他不能进入生铁中的杂质组成的,是一种易熔混合物。
从化学成分来看,高炉矿渣是属于硅酸盐质材料。
每生产1t生铁,大约产生高炉矿渣0.3 吨~1.0 吨。
2.首钢水城钢铁(集团)有限公司的高炉矿渣产生和堆放现状首钢水城钢铁(集团)有限公司至上世纪60年代建成投产以来产生了1000多万吨高炉矿渣,而且该公司还在以每年上100万吨的速度排放高炉矿渣。
这些露天储存的高炉矿渣堆存侵占土地,污染毒化土壤、水体和大气,严重影响生态环境,造成明显或潜在的经济损失和资源浪费。
据有关资料估算,每吨冶炼废渣堆存的经济损失约14.25元,仅首钢水城钢铁(集团)有限公司每年新增高炉矿渣造成的经济损失在710~1420万元之间。
所以,高炉废渣的无害化、资源化处理是首钢水城钢铁(集团)有限公司十分重视的焦点,也是钟山区推进循环经济的中心内容之一。
3.高炉矿渣的再生利用途径3.1 加工炼钢生铁水钢高炉矿渣进入渣场,经过第一道磁选加工,产生的磁选粉、磁选铁、人工选铁含铁品位高,一般在58%以上,可直接送入水钢炼铁厂使用。
近年来随着国际市场上铁矿石价格的大幅攀升,水钢与专业公司合作,对高炉矿渣进行了第二道磁选,主要方法是对经过第一道磁选后的高炉矿渣进一步破碎,加大设备的磁场强度,每月通过第二道磁选工序加工出含铁物质约5000吨,品位在30%~52%,不能直接供给水钢炼铁厂使用,因此必须对第二道磁选工序加工出品位低的含铁物质进一步深加工,成为高品位的磁选粉、铁精粉或铸件,深加工的主要工艺有水洗球磨和热风炉冶炼。
高炉炼铁中的铁口炉渣处理技术研究

高炉炼铁中的铁口炉渣处理技术研究炼铁工艺是钢铁生产中至关重要的环节之一,而铁口炉渣处理技术在高炉炼铁过程中发挥着重要作用。
本文将从铁口炉渣的形成原因、渣料特性以及渣料处理技术等方面展开讨论。
该研究旨在帮助企业更好地理解高炉炼铁中的铁口炉渣处理技术,并提供行之有效的解决方案和建议。
1. 铁口炉渣的形成原因高炉冶炼过程中,煤炭和焦炭燃烧产生的高温煤气吹入高炉,高炉内的生铁析出,在冶炼过程中伴随着铁口炉渣的形成。
铁口炉渣中包含了非金属夹杂物、硅酸盐和氧化物等成分,这些成分来自于铁矿石、焦炭灰分和高炉燃料等。
2. 渣料特性铁口炉渣具有一定的粘度和流动性,并且在高温下具有一定腐蚀性。
渣料的粘度与其成分、温度和渣氧化性有关。
渣料中的硅酸盐、铝酸盐等成分会影响渣料的粘度和流动性,而硅酸盐和铝酸盐的含量又与矿石类型和熔和程度有关。
此外,渣料的流动性对高炉运行的稳定性有着重要影响。
3. 渣料处理技术为了保证高炉冶炼的正常进行,必须对铁口炉渣进行有效处理。
渣料处理技术主要包括渣铁分离、渣料冷却和渣料利用等环节。
3.1 渣铁分离渣铁分离是将渣料中的炉渣与生铁分离的过程。
目前,常用的渣铁分离方法包括重力分离、磁力分离和磁流体分离等。
通过选择合适的分离方法,可以有效降低渣铁中的渣料含量,提高炼铁效率。
3.2 渣料冷却渣料冷却是将高温的铁口炉渣迅速冷却至合适温度的过程。
冷却后的渣料不仅便于处理,还可以降低对设备的腐蚀性。
常见的渣料冷却方法包括水冷、空气冷却和喷水冷却等。
根据具体情况采取合适的冷却方式,可以提高炼铁工艺的效率和稳定性。
3.3 渣料利用渣料利用是将处理后的渣料充分利用的过程,以降低环境污染和资源浪费。
处理后的渣料可以用于制备水泥、填充材料和道路基础等。
通过渣料的合理利用,既可以减少对自然资源的需求,又可以降低企业的生产成本。
4. 渣料处理技术的应用高炉炼铁中的铁口炉渣处理技术已经得到广泛应用。
通过合理选择渣料处理技术,可以改善高炉冶炼过程中的渣料处理效果,提高炼铁工艺的稳定性和效率。
对高炉的一点认识

对高炉的一点认识我叫骆志国,是炼铁厂一名员工,现在在炼铁厂生产技术科工作,负责炼铁厂能源介质的管理工作。
我于2007年1月份进厂,最早在喷煤车间工作,中间去河北理工大学对钢铁冶金进行了脱产学习,对钢铁冶炼有了一个较深入的了解,并由此喜欢上了高炉工作。
后来在炼铁厂1#高炉炉前工作,无论是炉前出铁还是应付突发情况,都具备了一定的能力。
还有在生产技术科工作的这段时间里,对高炉生产产生的一点认识如下:一、高炉的基本操作制度是:装料制度、送风制度、炉缸热制度和造渣制度。
1炉缸热制度炉温一般指高炉炉渣和铁水的温度,即“物理热”。
一般铁水温度为1350~1550℃,炉渣温度比铁水温度高50~100℃。
生产中常用生铁含硅量的高低来表示高炉炉温水平,即“化学热”。
我厂的内控率是0.25-0.55,上、下两炉[Si]含量波动应小于0.1%。
炉缸热制度直接反映炉缸的工作状态,稳定均匀而充沛的热制度是高炉稳定顺行的基础。
原燃料强度差、粉末多、含硫高、稳定性较差时,应维持较高的炉温;反之在原燃料管理稳定、强度好、粉末少、含硫低的条件下,可维持较低的生铁含硅量。
原燃料性质变化主要包括焦炭灰分、含硫量、焦炭强度、矿石品位、还原性、粒度、含粉率、熟料率、熔剂量等的变化。
矿石品位提高1%,焦比约降低2%,产量提高3%。
烧结矿中FeO含量增加l%,焦比升高l.5%。
矿石粒度均匀有利于透气性改善和煤气利用率提高。
焦炭含硫增加0.1%,焦比升高l.2%~2.0%;灰分增加l%,焦比上升2%左右。
随着高炉煤比的提高,还应充分考虑煤粉发热量、含硫量和灰分含量的波动对热制度的影响。
2送风制度原燃料条件好,能改善炉料透气性,利于高炉强化冶炼,允许使用较高的鼓风动能。
料速超过正常规定应及时减少风量。
当高炉出现悬料、崩料或低料线时,要及时减风,并一次减到所需水平。
渣铁未出净时,减风应密切注意风口状况,防止风口灌渣。
当炉热难行需要撤风温时,幅度要大些,一次撤到高炉需要的水平;炉况恢复时逐渐将风温提高到需要的水平,提高风温速度不超过50℃/h。
炼铁厂排渣安全管理制度
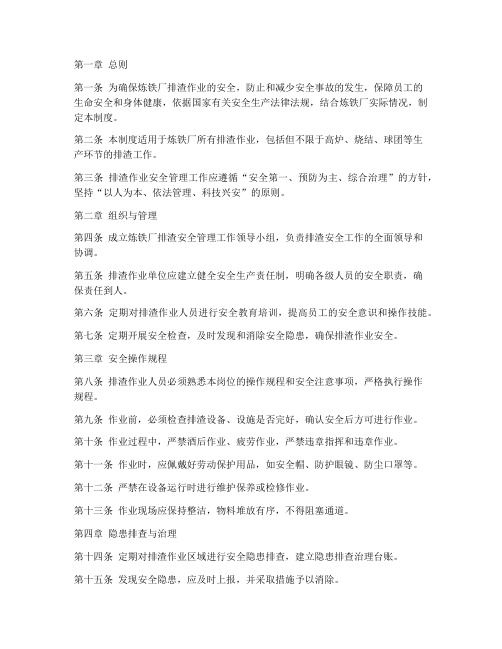
第一章总则第一条为确保炼铁厂排渣作业的安全,防止和减少安全事故的发生,保障员工的生命安全和身体健康,依据国家有关安全生产法律法规,结合炼铁厂实际情况,制定本制度。
第二条本制度适用于炼铁厂所有排渣作业,包括但不限于高炉、烧结、球团等生产环节的排渣工作。
第三条排渣作业安全管理工作应遵循“安全第一、预防为主、综合治理”的方针,坚持“以人为本、依法管理、科技兴安”的原则。
第二章组织与管理第四条成立炼铁厂排渣安全管理工作领导小组,负责排渣安全工作的全面领导和协调。
第五条排渣作业单位应建立健全安全生产责任制,明确各级人员的安全职责,确保责任到人。
第六条定期对排渣作业人员进行安全教育培训,提高员工的安全意识和操作技能。
第七条定期开展安全检查,及时发现和消除安全隐患,确保排渣作业安全。
第三章安全操作规程第八条排渣作业人员必须熟悉本岗位的操作规程和安全注意事项,严格执行操作规程。
第九条作业前,必须检查排渣设备、设施是否完好,确认安全后方可进行作业。
第十条作业过程中,严禁酒后作业、疲劳作业,严禁违章指挥和违章作业。
第十一条作业时,应佩戴好劳动保护用品,如安全帽、防护眼镜、防尘口罩等。
第十二条严禁在设备运行时进行维护保养或检修作业。
第十三条作业现场应保持整洁,物料堆放有序,不得阻塞通道。
第四章隐患排查与治理第十四条定期对排渣作业区域进行安全隐患排查,建立隐患排查治理台账。
第十五条发现安全隐患,应及时上报,并采取措施予以消除。
第十六条对重大安全隐患,应立即停产整改,直至安全隐患消除。
第五章应急处置第十七条建立健全排渣作业事故应急预案,定期组织演练。
第十八条发生排渣作业事故时,应立即启动应急预案,采取有效措施进行处置。
第十九条事故发生后,应迅速上报,查明事故原因,追究相关责任。
第六章奖励与处罚第二十条对在排渣安全工作中表现突出的单位和个人,给予表彰和奖励。
第二十一条对违反本制度,造成安全事故的,依法追究相关责任。
第七章附则第二十二条本制度由炼铁厂安全生产管理部门负责解释。
首钢水钢三号高炉冲渣系统的改造与探索

·问题探讨·作者简介:廖胜权(1971~),男,电器技术员,铁焦事业部辅助作业区副主任。
首钢水钢三号高炉冲渣系统的改造与探索廖胜权(首钢水钢铁焦事业部贵州六盘水553028)摘要:本文主要针对首钢水钢三号高炉冲渣系统的缺点和生产运行过程中存在的问题,经过多次现场调查研究进行技术攻关,制定改进措施并予以实施,取得了较好的效果。
关键词:高炉;水冲渣;改造Reformation and Exploration of Slag Water-Quenching System of No.3BlastFurnace in Shuigang of ShougangLiao Shengquan(Industrial Department of Ironmaking and Coking,Shougang Shuicheng Iron &Steel (Group)Co.,Ltd.,Liupanshui 553028,Guizhou,China)1简述首钢水钢三号高炉冲渣系统采用嘉恒法进行高炉熔渣的粒化与脱水过滤,设东、西两个出铁场各对应一个冲渣水粒化冲制箱。
冲渣时,冲渣泵将循环水池内的水通过加压送到冲制箱与高炉熔渣充分接触,对熔渣进行水淬、冷却,粒化后的渣水混合物经渣沟进入脱水器(东、西渣沟汇合共用一台脱水器),进行渣水分离,渣进入运输皮带和卸渣皮带后进入储渣仓外运。
水则经集水槽流入返渣池,部分细颗粒渣沉淀于返渣池底部,由返渣泵加压送入脱水器进行二次过滤。
返渣池的水则平流到循环水池内作为冲渣水循环再利用。
由于该系统存在一定缺陷,致使冲渣过程中,耽误比较多,不仅冲渣率相对较低,而且出现跑水跑渣现象,严重影响环保工作,同时也间接给高炉生产带来影响。
为此借助三高炉一代炉龄大修的机会,成立冲渣系统技术改造攻关组,主要改进方案有:(1)在现有基础上增设一台脱水器,并增大脱水器过滤面积;(2)对冲渣沟的衬板进行更换并收窄渣沟宽度;(3)将冲渣泵输水管道直径增大;(4)增安一台脱水器外清洗泵;(5)增安一台立式返渣泵;Abstract:As for defects and problems in slag water-quenching system in production and operation of No.3blast furnace,many times of field investigation are done by my workshop team,technical break⁃through is carried out,reformation measures are made and put into use,and good effect is obtained.Keywords:blast furnace;water-quenching slag;reformation1··(6)改进冲渣箱的安装角度;(7)返渣泵进口管道上增安一台检修球阀。
高炉渣处理技术的现状及发展趋势

高炉渣处理技术的现状及发展趋势高炉渣处理技术是钢铁工业中重要的环保环节,其主要目的是降低对环境的污染,并回收利用其中的有价值物质。
以下是高炉渣处理技术的现状及发展趋势的详细介绍。
目前,高炉渣处理技术主要分为物理处理、化学处理和综合利用三个方面。
物理处理主要包括磁选、重选、筛分等技术。
磁选是利用磁性物质的不同特性,将磁性物质与非磁性物质分离,从而达到回收有价值物质的目的。
重选则是通过重力分离原理,将密度较大的物质与密度较小的物质分离。
筛分是利用不同颗粒大小的渣粒通过筛网,实现不同颗粒大小的渣粒分离。
这些物理处理技术具有操作简便、成本较低的优点,但对渣中的有机物和有毒物质的去除效果有限。
化学处理是利用化学反应将渣中的有害物质转化为无害物质。
目前常用的化学处理技术包括酸浸、碱浸和氧化还原等。
酸浸和碱浸是通过酸或碱溶液对渣进行处理,将其中的有害物质溶解或沉淀,达到净化渣的目的。
氧化还原则是通过氧化还原反应,将有害物质转化为无害物质。
化学处理技术对渣中的有机物和有毒物质有较好的去除效果,但处理过程中会产生大量废液,对环境造成二次污染,且处理成本较高。
综合利用是将高炉渣转化为有用的建筑材料或再生资源。
目前常见的综合利用技术有水泥制备、路基材料制备和填埋材料制备等。
水泥制备是将高炉渣与适量的石灰石和石膏混合煅烧,制成水泥熟料,再经过研磨制成水泥。
路基材料制备是将高炉渣与适量的砂、石等材料混合,经过加工制备成路基材料。
填埋材料制备是将高炉渣加工成一定颗粒度的颗粒,用于填埋场的建设。
综合利用技术能够最大限度地回收利用高炉渣中的有价值物质,减少对环境的污染,但需要在处理过程中加入其他原材料,增加了生产成本,并且需要充分考虑高炉渣的物理性能和化学性能。
未来,高炉渣处理技术的发展趋势将主要集中在绿色、环保和高效利用方面。
绿色化学处理技术将会更加重视对废液的处理和回收利用,减少对环境的污染。
同时,高炉渣综合利用技术将会更加注重资源的回收利用率和产品质量的提升,开发更多的高附加值产品。
高炉富锰渣生产的基本操作制度(造渣制度)

高炉富锰渣生产的基本操作制度(造渣制度)
高炉富锰渣生产的基本操作制度(造渣制度)
合理的造渣制度是高炉冶炼有效进行的基础。
在高炉中冶炼富锰渣是选择性还原,日常生产中通过控制炉渣碱度和其他氧化物含量来控制产品成分和生产顺利进行。
高炉冶炼富锰渣对炉渣有如下的要求:1.在高炉冶炼富锰渣过程中锰和铁的还原方向是一致的,关键在于程度的不同。
铁的还原条件在高炉中容易得到满足,所以炉渣成分的选择重点在于有利于抑制锰的还原提高锰的入渣率。
2.渣的成分必须满足在低温下有较好的流动性,以利于在低温冶炼条件下渣铁的分离。
目前在我国高炉富锰渣在冶炼过程中都采用高MnO的低碱度或自然碱度炉渣。
碱度一般都在0.3以下。
在实际生产中,当渣中Al2O3大于20%,MnO大于58%时渣的碱度大,流动性差,造成渣铁分离困难和炉况失常。
通常的办法是加碱性氧化物(CaO或MgO)或萤石来改善炉渣性能。
但加入碱性氧化物易造成锰回收率降低,加入萤石可以增加渣的流动性而不降低锰的回收率。
一般加入量使渣中CaF2达到2%左右为宜。
项目六 造渣制度

实例计算说明其应用。 举例
设渣量为金属装入量的12%,炉衬侵蚀量为装入量的1%,炉衬中含MgO 为40%。 铁水成分:Si为0.7%,P为0.2%,S为0.05%; 石灰成分:CaO 90%,MgO 3%,SiO2 2% ; 白云石成分:CaO40%,MgO35%,SiO23%; 终渣要求:(MgO)为8%,碱度为3.5。
=5.4 kg/t 4) 实际白云石加入量:
W白 27.4 11.4 5.4 10.6
(3) 白云石带入渣中CaO折算的石灰数量: 10.6×40%/90%=4.7 kg/t
kg/t
(4) 实际入炉石灰数量:
石灰加入量W—白云石折算石灰量=
2.14 0.7% 3.5 1000 4.7 58.5 90% 3.5 2%
解:
1) 白云石理论应加入量:
12% 8% W白 1000 27.4 35%
kg/t
2) 炉衬侵蚀进入渣中MgO折算的白云石数量:
W衬 1% 40% 1000 11.4 35%
kg/t
3) 石灰中带入MgO折算的白云石数量:
2.14 0.7% 3% W灰 W(MgO灰 / MgO白) 3.5 1000 90% 3.5 2% 35%
入量时要考虑它们的相互影响。
(1) 白云石应加入量 W白
W白 渣量% %MgO) ( 1000 %MgO白
kg/t
式中 %MgO白——白云石中MgO含量。
W白 (2) 白云石实际加入量
白云石实际加入量中,应减去石灰中带入的MgO量折算的白云石数 量W灰和炉衬侵蚀进入渣中的MgO量折算的白云石数量W衬 。下面通过
项目六 造渣操作
高炉四大操作制度讲义
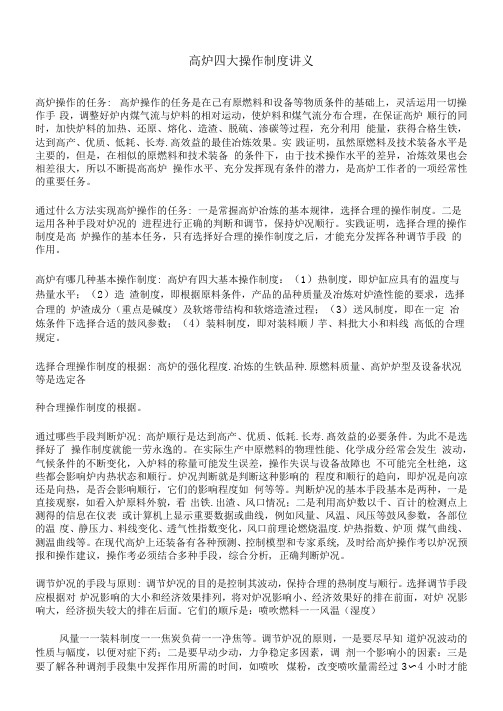
高炉四大操作制度讲义高炉操作的任务: 高炉操作的任务是在己有原燃料和设备等物质条件的基础上,灵活运用一切操作手段,调整好炉内煤气流与炉料的相对运动,使炉料和煤气流分布合理,在保证高炉顺行的同时,加快炉料的加热、还原、熔化、造渣、脱硫、渗碳等过程,充分利用能量,获得合格生铁,达到高产、优质、低耗、长寿.高效益的最佳冶炼效果。
实践证明,虽然原燃料及技术装备水平是主要的,但是,在相似的原燃料和技术装备的条件下,由于技术操作水平的差异,冶炼效果也会相差很大,所以不断提高高炉操作水平、充分发挥现有条件的潜力,是高炉工作者的一项经常性的重要任务。
通过什么方法实现高炉操作的任务: 一是常握高炉冶炼的基本规律,选择合理的操作制度。
二是运用各种手段对炉况的进程进行正确的判断和调节,保持炉况顺行。
实践证明,选择合理的操作制度是高炉操作的基本任务,只有选择好合理的操作制度之后,才能充分发挥各种调节手段的作用。
高炉有哪几种基本操作制度: 高炉有四大基本操作制度:(1)热制度,即炉缸应具有的温度与热量水平;(2)造渣制度,即根据原料条件,产品的品种质量及冶炼对炉渣性能的要求,选择合理的炉渣成分(重点是碱度)及软熔带结构和软熔造渣过程;(3)送风制度,即在一定冶炼条件下选择合适的鼓风参数;(4)装料制度,即对装料顺丿芋、料批大小和料线高低的合理规定。
选择合理操作制度的根据: 高炉的强化程度.冶炼的生铁品种.原燃料质量、高炉炉型及设备状况等是选定各种合理操作制度的根据。
通过哪些手段判断炉况: 高炉顺行是达到高产、优质、低耗.长寿.髙效益的必要条件。
为此不是选择好了操作制度就能一劳永逸的。
在实际生产中原燃料的物理性能、化学成分经常会发生波动,气候条件的不断变化,入炉料的称量可能发生误差,操作失误与设备故障也不可能完全杜绝,这些都会影响炉内热状态和顺行。
炉况判断就是判断这种影响的程度和顺行的趋向,即炉况是向凉还是向热,是否会影响顺行,它们的影响程度如何等等。
高炉渣处理技术的现状及发展趋势

高炉渣处理技术的现状及发展趋势1. 引言高炉渣是指在炼铁过程中产生的固体废弃物,主要由铁矿石中的非金属成分经冶炼后形成。
高炉渣处理是炼铁行业中的一个重要环节,不仅涉及环保问题,还能通过有效处理提取出有价值的资源,对于实现循环经济具有重要意义。
本文将介绍高炉渣处理技术的现状及发展趋势。
2. 高炉渣处理技术的现状目前,高炉渣处理技术主要分为物理方法和化学方法两大类。
2.1 物理方法物理方法是利用高炉渣的物理性质来实现处理和利用,常见的有磁选法、风选法和重选法等。
2.1.1 磁选法磁选法利用高炉渣中的磁性物质与非磁性物质的差异,通过磁力对高炉渣进行选择性分离。
这种方法可以实现高炉渣中铁资源的回收,但对于非磁性物质的处理效果较差。
2.1.2 风选法风选法是利用高炉渣中的颗粒间的比重、形状和粒径等差异,通过风力对高炉渣进行分离和分类。
这种方法处理效果较好,可以实现高炉渣的资源化利用和减少对环境的污染。
2.1.3 重选法重选法是利用高炉渣中成分的密度差异进行分离,将密度大的部分分离出来。
这种方法可以有效分离出高炉渣中的重金属等有价值的资源。
2.2 化学方法化学方法主要是利用化学反应和物质间的相互作用来实现高炉渣的处理和利用,常见的有酸浸法、碱浸法和微生物处理法等。
2.2.1 酸浸法酸浸法利用酸性溶液对高炉渣进行溶解和分离。
这种方法可以高效地分离出高炉渣中的有价值金属资源。
2.2.2 碱浸法碱浸法是利用碱性溶液对高炉渣进行溶解和分离。
这种方法可以有效地去除高炉渣中的有毒物质和污染物,并实现高炉渣的资源化利用。
2.2.3 微生物处理法微生物处理法利用特定的微生物对高炉渣中的某些成分进行代谢和转化。
这种方法对于处理高炉渣中的有机物具有一定的效果,但对于无机物的处理效果较差。
3. 高炉渣处理技术的发展趋势随着社会对环保和资源利用的要求越来越高,高炉渣处理技术也在不断创新和发展。
3.1 综合利用未来的高炉渣处理技术将更加注重综合利用,将其作为资源而不是废物来处理。
造渣制度

造渣制度1.合理的造渣制度1.1造渣制度造渣制度应适合高炉冶炼要求,有利于稳定顺行,有利于冶炼优质生铁。
各厂资源和生产条件不同,应根据原燃料条件选择合理的造渣制度。
(1)选择合理造渣制度的目的是:①保证生铁成分合格,有利于促进有益元素的还原,抑制有害元素进入生铁中;②保证渣铁分离良好,液态渣铁顺畅地从渣铁口流出;③有利于炉况顺行和热制度稳定;④在高炉下部形成保护渣皮,有利于延长炉体寿命。
(2)合理的造渣制度应满足什么要求合理的造渣制度应满足如下要求:①足够的脱S能力,保证生铁在低[Si]情况下低[S]。
一般条件下,硫在渣和≥40。
在炉温和碱度适宜的条件下,硫负荷<5kg/t时,硫的铁中的分配系数LS分配系数可控制在25-30。
②良好的流动性和较好的稳定性。
炉渣熔化温度在1300-1400℃,在1400℃时,黏度<10泊,可操作的温度范围大于150℃。
③对高炉衬砖侵蚀能力较弱。
④选择炉料结构时,应考虑让初渣生成较晚,软熔带温度区间较窄,这对炉料透气性有利,初渣中FeO含量也少。
1.2造渣制度选择规律(1)炉渣特性在高温下有良好的流动性和稳定性及较强的脱硫能力,且侵蚀性较弱的炉渣,称为一般炉渣或普通炉渣。
我国宝钢、鞍钢、武钢、首钢、济钢等大中型钢铁厂的炉渣都属于一般炉渣。
这种炉渣在碱度小于1.2,大部分的熔化性温度较低,具有良好的流动性和稳定性,脱硫效果好。
据统计,冶炼制钢铁时,二元碱度CaO/SiO2在1.05-1.15范围,三元碱度CaO+Mgo/SiO2在1.2-1.32范围。
国外日本、德国渣量小,硫负荷5-6kg/t,二元碱度大于1.2,三元碱度1.45。
特殊炉渣一般都是由于特殊铁原料决定的。
如酒泉钢铁厂的含钡炉渣,矿石含BaSO4、BaSO3,以BaO形态进入炉渣。
包头钢铁厂的含氟渣,熔化温度比普通炉渣低100-200℃。
攀钢有高钛渣,重钢有低钛渣。
(2)根据炉渣特性,造渣制度应遵循如下规律:①若渣量少,AL2O3偏高时,二元碱度应高些,一般为1.15-1.2。
高炉造渣管理制度

高炉造渣管理制度一、高炉造渣管理原则(一)科学合理。
高炉造渣管理必须遵循科学合理的原则,根据高炉的生产规律和炉渣的物理化学特性,制定符合实际情况的造渣管理制度。
(二)安全环保。
高炉造渣管理要以安全第一、环保为主导,严格按照国家相关法律法规和环保要求进行管理,确保对环境的影响尽可能减少。
(三)节能减排。
高炉造渣管理要遵循节约能源、减少废气排放的原则,降低造渣工艺过程中的能耗和排放。
(四)炉渣利用。
高炉造渣管理要充分考虑炉渣的再利用价值,采取有效措施进行炉渣的综合利用,实现资源化、无害化和减量化。
二、高炉造渣管理制度(一)造渣监测。
建立高炉造渣监测系统,对高炉造渣的成分、质量和渣量等进行实时监测和分析,及时发现问题并采取措施予以解决。
(二)造渣工艺控制。
根据高炉的生产情况和工艺特点,制定严格的造渣工艺控制参数,对造渣过程进行控制和调节,确保炉渣的质量符合要求。
(三)造渣设备维护。
对造渣设备进行定期维护和检修,保证设备的正常运转,减少设备故障对造渣过程的影响。
(四)造渣操作规范。
制定严格的造渣操作规范,对造渣人员进行培训和考核,提高操作技能和素质,保证造渣操作的安全和规范。
(五)炉渣分类处置。
对高炉产生的炉渣进行分类处置,根据炉渣的成分和性质采取相应的处理措施,满足环保要求并最大限度地实现炉渣的资源化利用。
(六)炉渣质量跟踪。
建立炉渣质量跟踪制度,对炉渣的质量进行全程跟踪监控,并及时反馈信息,对质量异常进行分析和处理。
(七)炉渣利用技术研究。
开展炉渣利用技术的研究和开发,探索炉渣在建筑材料、道路铺设、水泥生产等领域的利用途径,扩大炉渣的综合利用范围。
三、高炉造渣管理的关键控制(一)合理控制高炉操作参数。
对高炉操作参数进行合理控制,包括风温、风量、炉焙区压力、生铁温度、炉料品位、炉渣量等,确保高炉的正常运行。
(二)控制炉料成分及比例。
对高炉炉料的成分和比例进行严格的控制,保证炉料的品位和配比符合要求,减少对造渣过程的干扰。
高炉工艺造渣制度

造渣制度1.造渣制度的要求造渣有如下要求:◆要求炉渣有良好的流动性和稳定性,熔化温度在1300~1400℃,在1400℃左右黏度小于lPa·S,可操作的温度范围大于150℃。
◆有足够的脱硫能力,在炉温和碱度适宜的条件下,当硫负荷小于5 kg/t时,硫分配系数Ls为25~30,当硫负荷大于5kg/t时,Ls为30~50。
◆对高炉砖衬侵蚀能力较弱。
◆在炉温和炉渣碱度正常条件下,应能炼出优质生铁。
2.对原燃料的基本要求为满足造渣制度要求,对原燃料必须有如下基本要求:◆原燃料含硫低,硫负荷不大于5.0kg/t。
◆原料难熔和易熔组分低。
◆易挥发的钾、钠成分越低越好。
◆原料含有少量的氧化锰、氧化镁。
3.炉渣的基本特点◆根据不同的生铁品种规格,选择不同的造渣制度。
生铁品种与炉渣碱度的关系见表4—6。
表4—6生铁品种与炉渣碱度的关系碱度高的炉渣熔点高而且流动性差,稳定性不好,不利于顺行。
但为了获得低硅生铁,在原燃料粉末少、波动小、料柱透气性好的条件下,可以适当提高碱度。
◆根据不同的原燃料条件,选择不同的造渣制度。
渣中适宜MgO含量与碱度有关,CaO/SiO,愈高,适宜的MgO应愈低。
若Al2O3含量在17%以上,CaO/SiO2含量过高时,将使炉渣的黏度增加,导致炉况顺行破坏。
因此,适当增加MgO含量,降低CaO/SiO2,便可获得稳定性好的炉渣。
◆我国高炉几种有代表的炉渣成分见表4—7。
表4—7不同高炉炉渣化学成分(质量分数) (%)4.炉渣碱度的调整◆因炉渣碱度过高而产生炉缸堆积时,可用比正常碱度低的酸性渣去清洗。
若高炉下部有黏结物或炉缸堆积严重时,可以加入萤石(CaF2),以降低炉渣黏度和熔化温度,清洗下部黏结物。
◆根据不同铁种的需要利用炉渣成分促进或抑制硅、锰还原。
冶炼硅铁、铸造铁时,应选择较低的炉渣碱度。
冶炼炼钢生铁时,应选择较高的炉渣碱度。
冶炼锰铁时需要较高的碱度。
◆利用炉渣成分脱除有害杂质。
转炉造渣制度概要
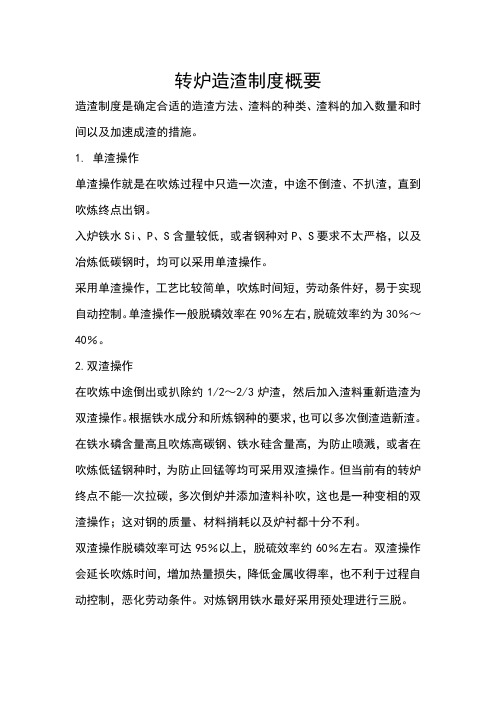
转炉造渣制度概要
造渣制度是确定合适的造渣方法、渣料的种类、渣料的加入数量和时间以及加速成渣的措施。
1. 单渣操作
单渣操作就是在吹炼过程中只造一次渣,中途不倒渣、不扒渣,直到吹炼终点出钢。
入炉铁水Si、P、S含量较低,或者钢种对P、S要求不太严格,以及冶炼低碳钢时,均可以采用单渣操作。
采用单渣操作,工艺比较简单,吹炼时间短,劳动条件好,易于实现自动控制。
单渣操作一般脱磷效率在90%左右,脱硫效率约为30%~40%。
2.双渣操作
在吹炼中途倒出或扒除约1/2~2/3炉渣,然后加入渣料重新造渣为双渣操作。
根据铁水成分和所炼钢种的要求,也可以多次倒渣造新渣。
在铁水磷含量高且吹炼高碳钢、铁水硅含量高,为防止喷溅,或者在吹炼低锰钢种时,为防止回锰等均可采用双渣操作。
但当前有的转炉终点不能—次拉碳,多次倒炉并添加渣料补吹,这也是一种变相的双渣操作;这对钢的质量、材料捎耗以及炉衬都十分不利。
双渣操作脱磷效率可达95%以上,脱硫效率约60%左右。
双渣操作会延长吹炼时间,增加热量损失,降低金属收得率,也不利于过程自动控制,恶化劳动条件。
对炼钢用铁水最好采用预处理进行三脱。
3. 留渣操作
留渣操作就是将上炉终渣的一部分留给下炉使用。
终点熔渣的碱度高,温度高,并且有一定(TFe)含量,留到下一炉,有利于初期渣尽早形成,并且能提高前期去除P、S的效率,有利于保护炉衬,节省石灰用量。
采用留渣操作时,在兑铁水前首先要加石灰或者先加废钢稠化冷凝熔渣,当炉内无液体渣时方可兑入铁水,以避免引发喷溅。
溅渣护炉技术在某种程度上可以看作是留渣操作的特例。
炉渣拉运管理制度

炉渣拉运管理制度一、制度的重要性1. 炉渣的管理对生产和环保都有重要意义。
炉渣不仅对于冶金工业的生产过程有着重要的影响,还可能对环境造成污染。
因此,制定一套科学的炉渣拉运管理制度,对于促进工作顺利进行,提高生产效率,保护环境都有着十分重要的作用。
2. 制度的建立可以规范工作流程,提高工作效率。
通过建立炉渣拉运管理制度,可以规范炉渣的收集、运输、处理等环节,明确各项工作的职责和要求,确保工作有序进行,避免出现混乱和错误,提高工作效率。
3. 制度的建立可以降低工作风险,保障安全生产。
炉渣的处理过程中存在着一定的危险性,如果没有科学的管理制度,容易导致事故的发生。
通过建立炉渣拉运管理制度,可以明确工作的安全要求,加强对工作人员的培训和监督,降低操作风险,保障安全生产。
4. 制度的建立可以减少资源浪费,节约成本。
科学的炉渣拉运管理制度能够使炉渣的处理更加规范和高效,降低能耗和成本,减少资源浪费,节约生产成本,提高企业的经济效益。
二、制度的内容1. 炉渣的收集和堆放管理:明确炉渣的收集方式和地点,规定收集容器的种类和规格,规范炉渣的堆放方式和堆放高度,确保炉渣的收集和堆放符合相关标准和要求。
2. 炉渣的运输管理:规定炉渣的运输方式和工具,明确运输路线和安全要求,规范运输人员的行为和操作规程,确保炉渣的运输过程安全、高效。
3. 炉渣的处理管理:明确炉渣的处理方式和设备,规定操作流程和安全措施,确保炉渣的处理符合环保要求和生产需要。
4. 炉渣的处置管理:规定炉渣的最终处置方式和地点,明确处置标准和程序,确保炉渣的最终处置符合环保法规,保护环境。
5. 监督检查和责任追究:建立监督检查制度,明确监督责任和频次,规定对违反制度的行为进行责任追究,确保炉渣拉运管理制度有效执行。
6. 培训和教育:加强对从业人员的培训和教育,提高其对炉渣拉运管理制度的认识和执行能力,提高工作效率和安全水平。
三、制度执行的保障1. 加强领导管理,形成合力。
- 1、下载文档前请自行甄别文档内容的完整性,平台不提供额外的编辑、内容补充、找答案等附加服务。
- 2、"仅部分预览"的文档,不可在线预览部分如存在完整性等问题,可反馈申请退款(可完整预览的文档不适用该条件!)。
- 3、如文档侵犯您的权益,请联系客服反馈,我们会尽快为您处理(人工客服工作时间:9:00-18:30)。
摘要本文以首钢高炉现有造渣制度及冶炼实际为基础,介绍了首钢高炉造渣制度的几点认识,促进了首钢造渣制度的研究。
关键词高炉炉渣造渣制度
A few viewpoint of slagging system in BF of Shougang Corporation
Zhang Heshun Ma Hongbin Chen Jun
(Shougang Corporation)
Abstract This article introduces a few viewpoint of slagging system in BF of Shougang Corporation in the basic of exiting slagging system and practical smelting of Shougang Corporation, and promotes the research of slagging system in BF of Shougang Corporation.
Keywords blast furnace slag slagging system
前言
高炉造渣制度由高炉资源条件和生产条件决定,应适合高炉冶炼要求,有利于稳定顺行,有利于冶炼优质生铁。
首钢炼铁技术人员对高炉送风制度与装料制度比较重视,研究较多,但对造渣制度认识存在不足,高炉炼铁必须深入分析造渣制度内涵、合理掌握造渣制度原则,才能确保高炉炉况的稳定顺行。
本文介绍了首钢炼铁技术人员高炉造渣制度的几点认识,高炉技术管理应高度重视造渣制度对高炉炉况的影响,高炉技术人员应加深对高炉造渣制度的研究。
1造渣制度的控制理念
1.1使用四元碱度
随着国内钢铁工业的发展,高炉炼铁的原燃料资源日益紧张,高炉冶炼面临炉渣高Al2O3的考验,近几年,首钢高炉炉渣Al2O3含量维持在16.5±1.0%。
面对炉渣高Al2O3的现实,造渣制度控制理念方面出现了“降低炉渣碱度,以降低炉渣黏度”的观点,但炼铁技术人员分析认为:炉渣是由SiO2、CaO、Al2O3、MgO等多种成分组成的,在Al2O3、MgO含量基本不变的情况下,造渣制度控制可以使用二元碱度,但若Al2O3、MgO含量出现较大变化,必然导致渣系性能的改变,二元碱度将不能满足高炉实际生产的需要。
高炉生产逐步引入四元碱度控制理念,其能够综合反应SiO2、CaO、Al2O3、MgO等炉渣四种主要成分对炉渣性能的影响,首钢高炉炉渣四元碱度控制在1.00±0.03范围,四元碱度的使用避免了单纯使用二元碱度造成的造渣制度控制目标混乱。
1.2坚持低渣比
面对炉渣高Al2O3的现实,造渣制度控制理念方面也出现了“提高渣比、降低炉渣Al2O3含量,以维持高炉冶炼水平”的观点,但高炉渣比的增加必然面临两方面的问题:一,渣比的增加必然带来燃料比的上升,对高炉炼铁节能降耗带来较大挑战;二,渣比的增加必然带来炉内下部透气性的恶化。
因此,提高渣比、降低炉渣Al2O3含量,并不能带来高炉炉况的稳定顺行,高炉冶炼应坚持“精料”原则,积极降低渣比。
特殊炉况,例如高炉开炉,由于开炉过程燃料比高,炉渣Al2O3含量常超过22.0%,为了降低炉渣Al2O3含量,可以适当提高渣比、降低炉渣Al2O3含量至20.0%以下,确保高炉开炉过程炉渣具有良好的流动性。
1.3渣比计算
高炉冶炼多采用比较科学的CaO平衡法计算渣比,但高炉生产过程化学成分检验经常出现偏差,CaO平衡法计算过程,一旦炉渣CaO含量检验出现偏差,渣比计算结果就将出现较大偏差,高炉技术人员难于准确把握高炉技术指标。
炉渣以SiO2、CaO、Al2O3、MgO四种成分为主,由各种原燃料的SiO2、CaO、Al2O3、MgO量出发,计算其进入炉渣的量,得到高炉冶炼的渣比,可以最大限度消除化学成分检验偏差对渣比计算的影响,更能准确反应高炉冶炼的实际状况。
2造渣制度的应用
2.1炉缸热度是减少高铝因素对炉渣性能影响的主要措
施
高炉冶炼虽然面对炉渣高Al2O3的威胁,但仍应坚持低渣比的原则,而通过提高炉缸热度来改善渣系的流动性,炉缸热度是指铁水的物理热,而不是铁水含硅量。
首钢高炉在一定的铁水含硅量基础上,通过提高煤气利用率在一定程度上提高了铁水物理热,铁水物理热保持在1500~ 1510℃,缓解了炉渣高Al2O3含量对炉内透气性能的影响,保持了高炉的重负荷顺稳生产。
2.2热制度与造渣制度的失调是高炉送风恢复困难的主
要原因
高炉休风过程,铁水在炉内的还原时间延长,铁水含硅量升高,导致炉渣碱度升高、流动能力变差,影响炉内下部透气性。
因此,高炉送风恢复困难的主要原因是热制度与造渣制度的失调,而不是送风时炉缸热度高造成的。
休风前准确预估休风料下达炉缸时的铁水含硅量,使炉渣碱度低于正常水平0.03~0.05,能够解决高炉送风恢复困难的问题。
2.3烧结矿碱度波动是高炉炉内透气性波动的重要原因
由于烧结矿在入炉炉料结构中占绝对地位,因此烧结矿碱度的波动,直接影响炉内下部透气性。
若确定是由于烧结矿碱度波动造成高炉炉内透气性波动,高炉操作可以主动控制风量适应,不宜频繁采用降低风温适用透气性指数变化的操作方法。
对于烧结矿碱度波动造成高炉炉内透气性波动的炉况变化,应长期观察、综合分析,以稳定烧结矿质量为主要措施,切忌调整高炉煤气分布。
3首钢特殊炉况下造渣制度的研究
3.1洗炉炉况下造渣制度的研究
高炉利用萤石造成熔化温度低、流动性好的炉渣,清洗炉墙黏结物。
首钢高炉炉渣二元碱度1.20、MgO=8.5%、Al2O3=16.5%、TiO2=2.0%水平下,炉渣CaF2含量从0.0%增加到2.5%,炉渣黏度减小幅度较小,熔化性温度下降幅度较小(1383℃↘1364℃),CaF2含量每增加1.0%,炉渣的熔化性温度平均下降约7.0~8.0℃;而CaF2含量从2.5%增加到5.0%时,炉渣黏度减小幅度急剧增大,熔化性温度下降幅度急剧增大(1364℃↘1314℃),CaF2含量每增加1.0%,炉渣的熔化性温度平均下降约20.0℃。
首钢高炉冶炼条件下,炉渣CaF2含量保持在2.5%以上才能起到较好的洗炉效果。
图 1 不同CaF2含量下炉渣的黏度-温度曲线
3.2护炉炉况下造渣制度的研究
含钛炉料护炉时,炉渣中TiC、TiN在炉缸温度范围内不能熔化,以固态微粒悬于渣中,使炉渣流动能力恶化,TiC和TiN越多,炉渣越黏,严重时失去流动性。
首钢高炉炉渣MgO=8.5%、Al2O3=16.5%水平下,二元碱度1.15时,在熔化性温度“拐点”处和中、高温下炉渣黏度以
TiO2=2.0~3.0%为最低;二元碱度1.20时,炉渣黏度变化较均匀,以TiO2=3.0~4.0%为低;二元碱度1.25时,中、高温下炉渣黏度虽变化不大,但仍以TiO2=2.0~3.0%为低、TiO2=4.0%时黏度增大明显。
首钢高炉冶炼条件下,炉渣TiO2含量在2.0~3.0%对炉渣流动性并没有较大影响,但TiO2含量达到4.0%,则炉渣黏度出现明显的升高,对维持高炉的透气性不利,难于实现护炉条件下的高炉重负荷顺稳生产。
图 2 不同TiO2含量下炉渣的黏度-温度曲线(二元碱度1.15)
图 3 不同TiO2含量下炉渣的黏度-温度曲线(二元碱度1.20)
图 4 不同TiO2含量下炉渣的黏度-温度曲线(二元碱度1.25)
4造渣制度的管理
4.1提升造渣制度的管理意识
高炉操作必须高度重视造渣制度的管理,将造渣制度管理提升至与送风制度、装料制度、热制度管理同等重要的位置,炉渣碱度超出规定范围,必须及时调整。
日常操作要严格防止低炉温、高碱度和高炉温、高碱度,以及过低碱度,并应经常观察渣铁样、渣铁流动性及渣铁热度变化。
在硫负荷增高时,提高炉渣碱度要与炉渣的流动性相适应,否则应提高炉温以保持脱硫效果。
4.2健全造渣制度的管理指标
造渣制度的管理指标应从二元碱度扩展至四元碱度,管理指标要囊括化学成分、碱度、渣比、硫分配比等,切实加强对炉渣实际流动能力的监测,保持炉渣化学成分在一定的范围波动。
5结语
高炉造渣制度是与送风制度、装料制度及热制度并列的高炉基本冶炼制度,但长期以来炼铁技术人员对造渣制度的重视不足,研究较少,导致对部分高炉冶炼现象无法正确解释,也就无法解决影响高炉稳定顺行的因素。
因此,高炉生产必须提升造渣制度的管理意识,健全造渣制度的管理指标,深入研究造渣制度对炉况的影响,促进高炉炼铁技术的进步。