镀铝锌机组底渣的清除与控制
铸铝技术:废铝重炼怎样去除杂质

铸铝技术:废铝重炼怎样去除杂质再生铝合金的生产过程可划分为预处理、熔炼(包括精炼)、铸锭三个阶段,熔炼的过程是将废铝加入熔炼炉内升温使之融化为液态,经过扒渣、测温和成分检测等工序,转入精炼炉中,加入硅、铜等元素,经过除气、除渣精炼等步骤。
再生铝熔体中有害金属元素主要有Fe、Mg、Zn、Pb等,针对不同的有害金属元素,需采取不同的去除方法。
1、除铁技术铁是再生铝生产中常见杂志,对铝及铝合金的质量及性能产生极不利的影响。
因此,除在对废铝经过预处理除铁外,在熔炼过程中要尽量清除夹杂的铁,防止其微溶于铝和铝合金熔体中。
一般采用以下几种方法除掉铁夹杂物。
1.1加锰除铁法锰在铝合金溶体中能有效的形成高熔点的富铁相化合物并沉积在炉底,从而达到除铁的目的,其发生的反应如下:Al9Fe2Si2+Mn→AlSiMnFe除去1kg的铁的用锰量为6.7-8.3kg,而且能使残留的粗大片状、既硬又脆的Al9Fe2Si2相转变为片状的AlSiMnFe相,从而削弱铁的有害作用。
但加锰除铁法会使铝合金的含锰量增加,对锰含量有限制的铝合金不宜采用,并且加锰除铁法的成本较高。
1.2加铍除铁法铍在铝合金熔体中与Al9Fe2Si2相发生反应,从而降低铁的有害影响,其发生的反应如下:Al9Fe2Si2+Be→Al5BeFeSi在铝及铝合金熔体中加入0.05%—0.1%的铍,可促使粗大片状的Al9Fe2Si2相转变为点状的Al5BeFeSi,明显消除铝合金的脆性。
但铍的价格较高,且铍蒸汽有毒,对人体有伤害,对工作环境造成污染,因此加铍除铁法应慎用。
1.3沉降除铁法沉降除铁法是利用Mn、Cr、Ni、Zr四种物质配制的多元中间合金的综合作用,与铝合金熔体中粗大的富铁化合物发生作用,形成新的多元富铁化合物。
多元富铁化合物随着温度的降低逐步长大,当长大到足以克服沉降阻力后,就会产生沉降,从而除去铁。
当Mn、Cr、Ni、Zr四中物质的用量分别为2.0%、0.8%、1.2%和0.6%时,经过沉降除铁法处理的铝及铝合金熔体中含铁量可以由1%降至0.2%。
镀铝锌机组工艺流程

镀铝锌机组工艺流程一、基本技术参数:(一):原料工艺参数1、原料材质:优质冷轧低碳钢2、钢种:SPCC、SPCD、08F、08AL、Q195、Q215、ST12、08YU3、抗拉强度:800N/mm2(max),屈服强度:735N/mm2(max)4、原料规格:厚度:0。
20-2。
0mm,(现最大上机厚度1。
5mm)宽度:700-1270mm5、钢卷外径:Φ900—Φ1950mm,钢卷内径:Φ508mm6、钢卷重量:最大重量:23吨,最小重量:7。
5吨,(吊车设计卷重20吨)7、带钢条件:7.1、表面乳液含油量:小于600mg/m2 单面7.2、表面铁粉附着量:小于150mg/m2 单面7.3、不平度:每1米不大于12mm7.4、镰刀弯:每2米不大于6mm7.5、边部:平直、无毛刺、无皱折、无裂纹和破裂7。
6、钢卷塔形:小于20mm(二)、镀铝成品工艺参数1、钢种:SPCC、SPCD、08F、08AL、Q195、Q215、ST12、08YU2、抗拉强渡:560N/mm2(max),屈服强渡:250-450N/mm2(max),4、成品规格:厚度:0.20-2。
0mm,宽度:700-1250mm5、钢卷内径:Φ508mm6、钢卷重量: 5—10吨,7、镀层厚度: 60—180g/m28、生产能力:20万吨/年9、退火级别:CQ板二、机组工艺流程图原料卷开包开卷机上卷横切剪切带头焊机焊接脱脂段脱脂入口活套连续退火炉还原退火锌锅热镀铝锌冷却塔快冷带钢拉矫机拉矫直带钢钝化机钝化钢板表面出口活套出口横切剪分卷卷取机卷取卸卷小车卸卷称重台称重打包成品卷三、机组工艺流程说明1、入口段成品冷轧卷进入原料库之后,吊到开包区进行开包,然后用吊车吊到鞍座上等待上卷,开卷机卷筒的钢卷甩尾后,上卷小车将钢卷上到开卷机卷筒上进行上卷,通过卷筒旋转和导板的作用,把头部破损带钢进入横切剪进行剪切,等另一个开卷机生产完带尾停在焊机后,将剪切好的头部带钢与在线带钢进行焊接.焊接后的带钢经过1#S辊进入脱脂段,脱脂段用50度以上的碱水两级清洗冷轧板表面油污杂质,再由60度以上清水清洗带钢表面,带钢经挤干后进入烘干机,烘干机对带钢进行80度蒸汽热风烘干。
连续热镀锌机组锌液出渣原因分析及控制对策
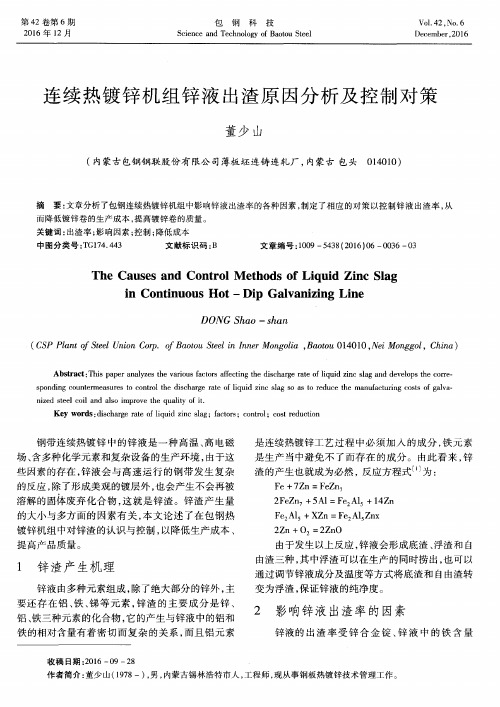
Fe+ 7 Zn = Fe Zn
溶解 的固体废 弃 化 合 物 , 这 就 是 锌 渣 。锌 渣 产 生 量
2Fe Zn 7+5A1= F e 2 A1 5+ 1 4Zn
的大小 与多 方面 的 因 素有 关 , 本 文 论 述 了在 包 钢 热
n i z e d s t e e l c o i l a n d a l s o i mp r o v e t h e qu a l i t y o f i t .
Ke y wo r d s : d i s c h a r g e r a t e o f l i q u i d z i n c s l a g ;f a c t o r s ;c o n t r o l ;c o s t r e d u c t i o n
DoNG S h a o—s h an
( C S P P l a n t o fS t e e l U n i o n C o r p .o fB a o t o u S t e e l i n I n n e r Mo n g o l i a, B a o t o u 0 1 4 0 1 0 , N e i Mo n g g o l , C h i n a )
第4 2卷 第 6期
2 0 1 6年 l 2月
包
钢
科
技
Vo 1 . 4 2, No . 6 De c e mbe r , 2 01 6
S ci e n c e a n d Te c hn o l o g y o f Ba o t o u St e e l
连 续 热 镀 锌 机 组 锌 液 出渣 原 因分 析 及 控 制 对 策
带钢连续热镀锌镀铝锌机组操作规程

带钢连续热镀锌/镀铝锌机组操作规程目录1原料库2上料3上卷及开卷4切头操作5甩尾及卸卷芯操作6焊接操作7清洗段操作8入口主控9退火炉操作9.1操作要求9.2点炉操作9.3炉子穿带9.4炉子HN气体供应9.5机组启动9.6停炉9.7事故处理9.7.1停电事故操作9.7.2异常压力事故9.7.2.1.助燃空气压力下降9.7.2.2.主烧嘴燃气压力下降9.7.2.3.点火烧嘴燃气压力下降9.7.2.4.N2压力下降9.7.2.5.HN压力下降9.7.2.6.炉压下降9.7.2.7.冷却水压力下降9.7.3断带事故操作9.7.4点火烧嘴失灵的操作10锌锅操作11工艺段启动操作12光整操作13拉矫操作14钝化15静电涂油16出口段的启动操作17卷取操作(以1#卷取机为例)带钢连续热镀锌/镀铝锌机组操作规程1原料库1.1操作要求1.1.1按照镀铝锌钢卷原料技术要求对轧硬钢卷进展验收;1.1.2严格按料场规定放置钢卷,严禁随便乱放钢卷;1.1.3必须及时做好钢卷相应记录;1.1.4确保机组间物流信息流运行畅通。
1.2收料:1.2.1在轧后库按镀铝锌原料技术条件要求对轧硬钢卷进展验收。
1.3指吊落库1.3.1钢卷验收合格后,现场指挥吊车将钢卷吊放到镀锌前库正常卷区库位。
1.3.2钢卷只能落在有垫板的指定位置,制止直接堆放在水泥地上。
1.4钢卷记录1.4.1将钢卷规格、材质、钢卷号、生产合同号、重量准确记录到收料台账上。
1.4.2钢卷落到相应库位后,将钢卷库位号记录到收料台帐上。
1.4.3将收料钢卷质量信息填写在信息传递卡上,并进展准确的信息传递。
1.5考前须知1.5.1假设发现来料不符合技术要求,不能直接收料,必须经相应的处理后,才能收料。
1.5.2假设钢卷标号不准确必须与轧钢核对清楚,重新标记后,才能吊往库。
1.5.3吊运钢卷过程中,必须轻吊轻放。
1.5.4假设库钢卷需倒到其它道次上,必须按要求在收料台账上注明新道次2上料2.1操作要求2.1.1根据生产方案到料场找料。
热镀铝锌锌渣缺陷的形成及控制

・ 1・ 6
在带 钢 的下表 面 , 一 点 在 生产 全硬 钢 时 特 别 明 这
显 。此外 , 于梅 钢 热 镀 铝锌 的产 品厚 度 最 薄 为 由
03 m, 厚达到 20m 厚度 跨度较 大 , .5m 最 . m, 而不 同
厚度 的控制参 数 也不 尽 相 同 , 薄带 钢 ( . m) ≤1 2m 运行 速度 较快 , 带走 锌 液热 量也较 多 , 相应 的带 钢 人 锌锅 温 度要 较 高 ; 反之 , 带 钢 (>1 21n) 厚 . l 运 T1
起, 即定义 为大 颗粒 的锌 渣粘 在带 钢 表面 , 直径 大
于 3mT, l 一般容 易 产生 于带 钢 的下表 面 。 l
1 1 带钢 表面 锌渣 的形 成过 程 .
合 了铝 的优异耐蚀 性与锌 的阴极腐 蚀保 护性 , 有 具
优 良的耐大气腐蚀能力 , 其耐蚀性是同样镀层厚度 的热镀锌 钢板 的 2~ 6倍 ¨ 。此外 , 铝 锌镀 层 还 J 镀
Ke r y wo ds: o — i — av n zng;i lg;c n r l h td p Zn A1g l a ii znc sa o to
高铝锌 合金镀 层 产 品是 美 国伯 利恒 钢 铁公 司
于2 0世 纪 7 O年代 开发 的高耐蚀Байду номын сангаас性镀层 产 品 , 它综
曹博 蕊 热镀 铝锌 锌渣 缺 陷的形成及 控 制 度 , 里 主要 是 指 带 钢表 面 的残 铁 含 量 。 因为 带 这 钢 表 面少 量 的铁 屑 在 退 火 炉 内 D S段 被 氧 化 成 F F , 变 成 浮 渣 , 大 部 分 是 以活 性 铁 进 入 锌 锅 eO 但 的 , 锌液 中的 A 元 素反应 后会 形 成大 量 的悬 浮 与 l 渣 。因此 , 加强 对 来 料 表 面 残铁 量 的控 制 对 减 少 锌 渣量 是有 好处 的。
镀铝一锌合金生产线锌锅中底渣形成的研讨
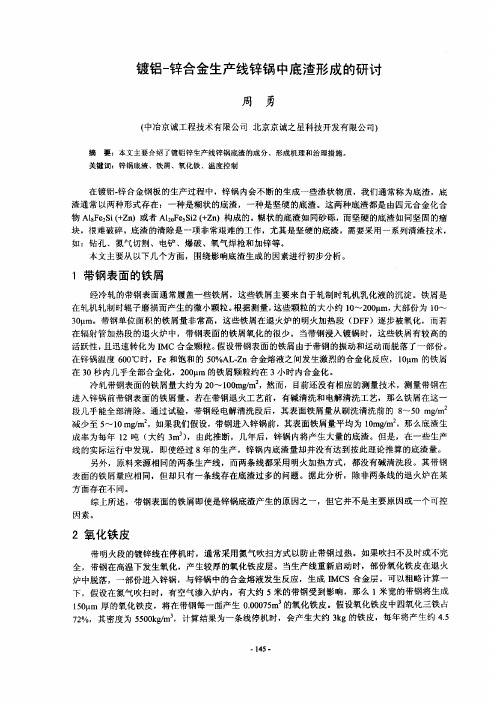
块,很难破碎。底渣的清除是一项非常艰难的工作,尤其是坚硬的底渣,需要采用一系列清渣技术, 如:钻孔、氮气切割、电铲、爆破、氧气焊枪和加锌等。 本文主要从以下几个方面,围绕影响底渣生成的因素进行初步分析。
和溶解的不对称现象而导致的底渣生成的原因。 锌锅内熔液的温度在 5 度的范围内 波动是经常可见的。如果 8 吨锌锅的温度在 60 0 0 ℃时,每 6
小时温度降低5 这样将析出1.g 铁或5k 的I C 度, 7k 的 2 4g M 合金。 如果只有其中 少量的 进入底渣,
当温度升高时,这些铁不能重新溶解到熔液中,那么随着温度在这个范围内的反复波动,将产生大
因素。
2氧化铁皮
带明 镀锌线在停机时,通常采用氮气吹扫方式以 火段的 防止带钢过热。 如果吹扫不及时或不完 全,带钢在高温下发生氧化, 产生较厚的氧化铁皮层。当生产线重新启动时, 部份氧化铁皮在退火 炉中脱落,一部份进入锌锅, 与锌锅中的 合金熔液发生反应, 生成 I C 合金层。 M S 可以 粗略计算一 下,假设在氮气吹扫时,有空气渗入炉内,有大约 5 米的带钢受到影响,那么 1 米宽的带钢将生成
量的 底渣。 例如, 如果5 g 只有5 的IC 4 中 k % M 进入底渣, 就意味 着产生3g M 大约为底 k 的IC( 渣的
k) 如果温度波动的 g。 频率为6 小时一次, 每年将产生8 吨的底渣。 . 5 温度的 波动是否是产生底渣的主要原因, 仍需要做大量的试验。 我们需要进一步研究各种不同
在辐射管加热段的退火炉中,带钢表面的铁屑氧化的很少。当带钢浸入镀锅时,这些铁屑有较高的 活跃性, 且迅速转化为I MC合金颗粒。 假设带钢表面的铁屑由于带钢的振动和运动而脱落了一部份。
连续热镀铝锌工艺要点和技术诀窍
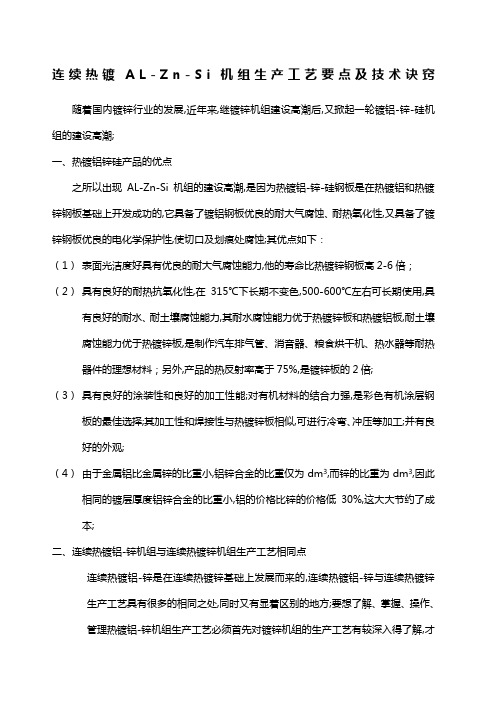
连续热镀A L-Z n-S i机组生产工艺要点及技术诀窍随着国内镀锌行业的发展,近年来,继镀锌机组建设高潮后,又掀起一轮镀铝-锌-硅机组的建设高潮;一、热镀铝锌硅产品的优点之所以出现AL-Zn-Si机组的建设高潮,是因为热镀铝-锌-硅钢板是在热镀铝和热镀锌钢板基础上开发成功的,它具备了镀铝钢板优良的耐大气腐蚀、耐热氧化性,又具备了镀锌钢板优良的电化学保护性,使切口及划痕处腐蚀;其优点如下:(1)表面光洁度好具有优良的耐大气腐蚀能力,他的寿命比热镀锌钢板高2-6倍;(2)具有良好的耐热抗氧化性,在315℃下长期不变色,500-600℃左右可长期使用,具有良好的耐水、耐土壤腐蚀能力,其耐水腐蚀能力优于热镀锌板和热镀铝板,耐土壤腐蚀能力优于热镀锌板,是制作汽车排气管、消音器、粮食烘干机、热水器等耐热器件的理想材料;另外,产品的热反射率高于75%,是镀锌板的2倍;(3)具有良好的涂装性和良好的加工性能;对有机材料的结合力强,是彩色有机涂层钢板的最佳选择;其加工性和焊接性与热镀锌板相似,可进行冷弯、冲压等加工;并有良好的外观;(4)由于金属铝比金属锌的比重小,铝锌合金的比重仅为dm3,而锌的比重为dm3,因此相同的镀层厚度铝锌合金的比重小,铝的价格比锌的价格低30%,这大大节约了成本;二、连续热镀铝-锌机组与连续热镀锌机组生产工艺相同点连续热镀铝-锌是在连续热镀锌基础上发展而来的,连续热镀铝-锌与连续热镀锌生产工艺具有很多的相同之处,同时又有显着区别的地方;要想了解、掌握、操作、管理热镀铝-锌机组生产工艺必须首先对镀锌机组的生产工艺有较深入得了解,才能更好的操作、管理好镀铝-锌机组;1、机组工艺流程是相同的,都具有如下工艺流程:开卷—焊接—脱脂立式、卧式—脱脂烘干—入口活套——热浸镀—镀后冷却—水淬—光整—拉矫—钝化—耐指纹—钝化或耐指纹后烘干—出口活套—卷取2、传动控制系统是相同的,都是为了实现机组的连续运行;3、前处理和镀后表面处理的目是相同的,都是为了原料钢带表面清洁干净和产品板型好,防氧化;4、产品的用途也是基本相同的:民用、彩涂基板等镀铝-锌产品用途要广泛一些5、原料钢卷标准是相同的;6、产品的检验标准是相同的;7、机组设备的操作和实现的功能是相同的三、连续热镀铝-锌机组与连续热镀锌机组生产工艺不同点不同点集中体现在以下几个方面:1、脱脂工艺1)对脱脂的要求更严格一些,要求板面洗的更干净,钢带上油污、铁粉附着更少一些;在锌锅工艺有更详细的阐述;2)脱脂工艺流程如下:碱浸洗槽—碱刷洗槽—电解脱脂槽——水刷洗槽—水喷洗槽—清水漂洗槽;3)脱脂对镀铝-锌工艺的重要性2、退火炉工艺1)热镀锌带钢入锌锅温度根据带钢厚度,一般要高于锌锅温度465℃-540℃;与热镀锌不同的是,热镀铝-锌带钢入锅温度低于锌锅温度30-40℃;原因在锌锅工艺在做阐述;2)锌锅温度一般控制在595℃-610℃,那么带钢入锅温度应该控制在570℃-590℃;为了满足这一要求,退火炉必须在冷却段后增加均衡段,均衡段的的作用是:1经过冷却段冷却后的带钢板面和板内部、边部和中部温度不均匀,也有可能总体温度较低,必须进行补偿加热,经过均衡段使带钢温度均匀,平衡带钢温度满足入锌锅要求;2改善带钢的退火机械性能;3启动生产时均衡段与加热段提前升温起到烘炉的作用,同时提高带钢温度,减少废次品产出量;均衡段一般采用电加热方式立式炉采用电辐射管、卧式炉采用上电辐射管和下电阻带;增加均衡段对立式炉尤其必要;生产过程中均衡段温度设置在570-600℃,根据入锅带温灵活设定,启动生产时适当高一些,只有温度低于设定温度时,电加热才开始工作;3)带钢经过热张紧辊室后也会降温,必须在热张紧辊室增设电辐射管加热装置;是带钢入锅温度的最后保障,也起到启动生产时的烘炉作用;温度设定和均衡段一样,控制原则也一样;4)退火炉第一次烘炉要求要高一些,退火炉检漏要求也要严格一些;烘炉合格的标准是:热张紧辊室露点-35℃以下;加热前段露点<-15℃;氧含量<2ppm;5)生产过程中,热张紧辊室露点-35℃以下;加热前段露点<-15℃;氧含量<2ppm;保护气体氢含量25-30%;炉压控制在100-120Pa;下斜槽、退火炉入口密封氮气流量各30-40m3/h;炉辊密封氮气10-20m3/h;6)做好每次炉子穿带后的密封、检漏工作,尤其是热张紧辊室和下斜槽;3、锌锅工艺1)锌锅成分控制,铝-锌-硅合金液成分指标:AL55%±;%±;%±;% 饱和浓度.(1)铝-锌-硅合金锭成分:AL55%±;%±;%±;杂质成分Fe≤%;Cd<%;Cu<%;Pb<%;合金锭重量:850±50Kg;(2)调整用合金锭:AL-Si锭,含Si3%,其余为AL,8Kg/块;0纯锌锭,25Kg/块; (3)每天化验一次合金液成分,主要检测项目为:AL、Zn、Si、Fe;加调整用合金锭进行调整,总结规律,每天加合金锭多少;以后可一周化验一次;铝、硅消耗大一些,平时主要加AL-Si锭,锌锭消耗少一些,一般较少加0锌锭;(4)AL含量不要偏离标准成分过多,AL高的过多,合金液流动性变坏,同样情况下,镀层量会提高;AL高的过多时,要及时加入0锌锭进行调配;要改变镀锌时的思路;(5)Fe的饱和浓度是%,Fe的浓度超过%,就会结晶析出渣子下沉形成底渣;表渣很少,就是一些铝的氧化层;铁和铝、锌反映形成的铝-铁合金FeAL13、Fe2AL5、锌-铁合金FeZn7都比合金液的比重大;合金液的比重为m3,锌的比重为m3;从以上的铝铁合金、锌铁合金的分子式可以看到,一份的铁可以消耗13份的铝,7份的锌,铁的危害性很大;铁的来源一是沉没件,二是钢带与合金液反应,三是钢带清洗不干净残留的铁粉;所以,前面讲过要在普通镀锌基础上进一步提高脱脂效果,加强脱脂能力;锌锅内上部铝含量高一些,下部铁含量高一些,中部成分较均匀,取样时应从中部取样;2)锌锅的温度控制锌锅温度一般控制在600-610℃,锅温低于595℃时,合金液就会出现“凝固”现象,因为合金液多元合金,凝固温度不是一个温度点,而是一个温度区间,595℃时其中的铝因为熔点高所以首先出现结晶析出,即“凝固”,使合金液中的铝含量降低;“凝固”现象一般在锌锅温度较低的地方发生,例如:锌锅的四壁、四个角等处,因为这些地方的温度最低;3)带钢入锅温度低于锌锅温度30-40℃,即560-590℃,这与普通镀锌相反;之所以这样,是有重要考虑的;前面说过,镀铝-锌-硅锌锅产生渣子较多,生产过程中会沉积在感应体喉口和熔沟内;其次,铝的比重较轻,铝、锌、硅三组分不是充分固溶,有分离现象,锅内成分不均匀;所以,要求感应体频繁或持续高功率工作,以对感应体熔沟进行冲刷,防止堵塞熔沟或使熔沟截面变小直至感应体损坏,同时使锌锅温度均匀、成分均匀;带钢入锅温度低于锌锅温度,带走热量,为了维持锌锅工艺温度感应体必须高功率工作,实现上述目的;4)镀铝-锌-硅的锌锅配置感应体功率较大,根据设计产量或锌锅容量而定;15-20万吨机组,锌锅容量70-90吨,感应体功率为340-400KW×4,四个感应体在锌锅的四个侧面布置,目的是感应体工作使锌锅内温度、成分更均匀;那么高的功率配置是因为锌锅温度较高,需要的热量大;镀铝-锌-硅锌锅容量不宜太大,小一些有利于通过磁力搅拌使温度、成分更加均匀;热量散失也少,有利于节能;5)镀铝-锌-硅锌锅的内部形状也与普通镀锌锌锅不同,四个角均为R600的园弧,便于锅内锌液的流动、温度传导,不形成死角,因温度低而凝结;有利于温度、成分均匀;6)镀铝-锌-硅机组,一般都配置有预熔锌锅,预熔锅的形式有多种;一种是熔炼金属用的中频感应炉10吨,带液压翻转机构,可以把合金液全部倒出或部分倒出,也可以通过加合金锭后溢流出来,通过一个带电加热装置的耐火材料砌筑的流槽流入镀锌主锅;一种是容积较小的10吨工频陶瓷感应加热预熔锅,带有两个感应体功率为300KW×2,和普通镀锌锌锅一样;一种是联体预熔锅,和主锅隔一道耐火材料砌筑的墙,墙的上沿留有溢流口,通过加合金锭合金液流入主锅,左右两侧各配置一个感应体,功率为300KW×2;前两种形式的预熔锅布置在主锅的传动侧后下角;7)加锌作业(1)镀铝-锌-硅机组,一般都配置有预熔锌锅,国内厂家为节约电费很多都不使用,而是把合金锭直接加入锌锅;使用预熔锅当然好,对稳定锌锅温度,均匀锌锅成分很有好处,避免局部、某时段温度降低造成的锌渣不均匀沉降,有利于改善三辊的粘渣,延长换辊周期,提高作业率;原因是:向锅内加锌锭时,锌锅温度会在局部降低,进而影响其他区域,Fe在合金液中的溶解度与温度有着直接的关系,温度降低溶解度降低,合金液由不饱和变成饱和,由饱和变成过饱和析出,形成渣子下沉至锅底,有的附着在沉没辊、稳定辊上形成粘渣;加锌锭的部位的底渣厚一些,锅壁凝结也严重一些;(2)向预熔锅中加锌锭时要从两个部位交替加入,不要一次将锌锭浸入合金液太多,分多次浸入,间隔时间稍长一些,待液面以下的锌锭完全熔化一定时间后,再进行下一次加入;同时,要保持锌锅液面高度相对稳定,不能忽高忽低;由于合金液的腐蚀能力很强,尽管下斜槽下部的浸入管是耐腐蚀的合金材料316L,时间长了也会腐蚀穿;一般机组投产前期液面控制低一些,几个月以后根据腐蚀情况再提高液面,可延长浸入管的使用寿命;当浸入管较短时,切记液面不能接近更不能浸过浸入管,以免合金液腐蚀碳钢材料的下斜槽,那样会很快腐蚀穿,造成危险;8)捞渣作业镀铝-锌-硅机组锌锅底渣较多,要定期捞渣,不能因赶产量而长时间不捞渣,要形成制度,生产组织、生产计划、检修计划安排要考虑这一重要因素,这是该类机组的规律,不能违背,否则就要吃亏;(1)捞渣的原因;前面讲过镀铝-锌-硅机组锌锅底渣较多,长时间不捞渣,底渣在锅底沉积很厚,甚至渣子接近沉没辊,沉没辊粘渣会很严重,使用周期很短,产品质量下降;同时,合金液中铁含量很高,锌液流动性变坏,镀层重量增加会提高,镀层缺陷会增加;其次,底渣沉积很厚,渣子会进入感应提喉口和熔沟内沉积,使熔沟截面变小,工作效率下降,严重时感应体工作产生的热量不能通过熔沟合金液传出,熔沟热膨胀,导致熔沟破裂漏锌,感应体报废;(2)捞渣工具和捞渣方法;a)用专用捞渣器捞渣——气动开合震动抓斗式捞渣器;b)捞渣前适当降低锌锅温度590℃,铁过饱和,使铁与AL 、Zn的合金以渣子的形式析出下沉,降低合金液中的铁含量;c)按从前到后的顺序捞渣,最后捞不到时,用钢板、钢管、链条焊接的工具把下斜槽后面、锌锅四周、四个角落的底渣聚拢到便于捞取的地方;d)捞渣器用锅面吊车吊着,捞渣器第一次下锅时要慢下,进行预热,抓斗开合数次,开合灵活后,打开抓斗落入锅底;打开震动器震动片刻后,合拢抓斗,把捞渣器慢慢提起,出液面后停留一段时间,把锌液充分淋干后移出锅面打开抓斗倒入锌渣槽;e)每次捞渣后,用铁铲子清理锌锅四壁凝结的渣子,并清理每个感应体的喉口结渣,用铁耙子扒出喉口内沉积的渣子,再用铁棒分别插入每个感应体的熔沟中搅拌,感应体设置高功率冲刷,把熔沟内的渣子冲刷出来;如果熔沟内渣子沉积比较严重,可以用瓶装氩气接一长钢管插入熔沟,打开气阀吹扫;f)捞渣结束后,向锌锅中加入锌锭,使液面升至规定液位,重新设置锌锅温度600℃,待液位、锌锅温度满足工艺要求时,按正常操作程序下沉没辊、锌锅穿带准备生产; (3)捞渣周期a)一般连续生产10-15天捞一次底渣,或生产5000-7000吨捞一次底渣,捞渣安排要和换辊、检修结合起来考虑,不能绝对;捞渣太勤也不是好事,捞渣会造成合金液浪费; b)根据经验每次捞渣可捞出4-5吨底渣;9)锌锅穿带作业铝-锌-硅合金液对铁的腐蚀是很快的,的钢带在合金液中20多分钟就可以腐蚀断,在合金液中浸泡20分钟的钢带即使不断也会因机组加张而断掉;1 锌锅穿带前准备要充分,焊接工具、材料、人员要全部到位后再进行穿带;2 穿带料厚度不小于;活套内要有足够的套量供带钢点动;3 焊接过程较长时,停止焊接把带钢从锌锅中拉出5-6米,然后继续焊接;焊接方法采用钢捆带对折把带钢的头尾夹在中间,用焊机点焊,如此不少于三道;焊好后立即拉紧,再点动出一段带钢后,减小工艺段张力设置,机组加张间断运行;10分钟点动一次;4 最好采取先把三辊六臂和前后气刀安装就位,然后进行锌锅穿带;这样可以节约很多时间,减少带钢在锌锅的时间和点动次数;10锌锅内辊子的粘渣控制1 因为镀铝-锌-硅锌锅产生的渣子比普通镀锌多,沉没辊、稳定辊粘渣是很正常的现象;所不同的是辊子上粘渣很快、很厚,沉没辊使用5-6天后,带钢经过的区域厚度达到20-25mm,很致密,辊子两端带钢不经过的区域厚度较厚度达到30-35mm,较疏松;带钢稍微左右跑偏时边部会出现浪边,所以,换新辊子时要先安排生产宽规格1250-1200mm的产品,生产3-4天后再安排生产窄规格1000mm的产品,这样可以延长辊子的使用时间,延长换辊周期,提高作业率;2 后稳定辊易粘渣,前稳定辊轻一些,后稳定辊粘渣的特点是,带钢经过的辊子区域中间厚,两边薄,辊子呈腰鼓形;稳定辊两端部没有带钢经过,粘渣又很厚,端部辊面带排气孔时更严重,排气孔会全部被堵死,厚度达30-35mm;3 新沉没辊、稳定辊表面要光滑,进行磨床加工;与普通镀锌沉没辊不同的是辊面没有沟槽,为光辊;辊子越粗糙越容易粘渣;4 处理事故掉出前稳定辊时要把辊面清理干净,否则板面会有鼓包;5 后稳定辊呈腰鼓形后,出锅后带钢板面中间瓢区,气刀靠不上,镀层厚,板面锌花不一致,色差大,观感不好,这时就要换辊了;如果换辊不具备条件,原料板型较好,可以退出前稳定辊,出锅带钢板形比投入稳定辊还好一些;6 生产中要加大刮沉没辊、后稳定辊的次数,每2小时刮一次;改善后稳定辊粘渣的方法是,适当加大锅区张力,稳定辊压入深度加大;锌锅温度要稳定,不要低于600℃;11 镀层重量的控制1 AL-Zn-Si合金的比重,Zn的比重,小近一倍,同样的镀层厚度镀层重量减小近一倍;目前,镀锌企业镀锌量控制较低,一般控制在60-70g/m2,对应的镀AL-Zn-Si镀层应为30-35g/m2;但目前AL-Zn-Si镀层厂家均控制在25- 30g/m2,有的厂家甚至控制在20g/m2左右;2 镀层控制方法与普通镀锌基本一样;不一样的是,在辊子粘渣不严重的情况下,的气刀风压就可以获得25g/m2的镀层量,太高的风压会造成严重的飞溅,因为AL-Zn-Si合金的比重小很多;3 在其他条件不变的情况下,获得低镀层量关键要控制出锅板形;但是有一种非常规、不太可取的方法是:适当降低锌锅温度590-595℃,其他情况不变,可以有效的降低镀层量,试验证明是有效的;原因是:锌锅温度降低,Fe的溶解度降低,Fe会变成锌渣析出,AL也会因进入凝固温度区域而结晶析出,AL含量降低,两者均有改善锌液流动性的作用,流动性提高同样的气刀参数情况下,镀层量就会降低;这种方法会带来很大的问题,长期这样,AL在锅壁结晶析出,Fe形成底渣沉于锅底,底渣增多,辊子粘渣严重,感应体高功率工作的时间减少,感应体喉口、熔沟沉积渣子并堵塞的危险性增大;12 三辊六臂更换后的处理1 三辊六臂吊出后,要趁热用锤头和钢钎敲击辊面,可以大块去除较厚的粘渣层,外层凝固不要紧,内层与辊面接触的还不会凝固,一般出锅后40-50分钟内很好剥离,一旦内层也凝固后就不容易清理了;支臂上的粘渣更容易清理;沉没辊内壁也可以用较长的钢钎清理;2 趁热把轴瓦、轴套处粘的渣子清理干净;固定轴瓦的合金棒趁热取出;稳定辊的排气孔用钢钎冲开,把稳定辊内的合金液流出;3 拆下三辊六臂,放在酸槽内酸洗,这样很快就可以洗干净;如果不趁热清理干净,辊子很难拆下来,并且在酸洗槽中泡4-5天还洗不干净;辊子洗干净后, 要先在车床上少量车削,检查辊子是否弯曲、变形、偏心、跳动,否则要重新校正,然后上磨床修磨;弯曲变形严重就要报废,否则辊子下锅后不转;所以新辊子下锅前一定要预热;13 三辊六臂的组装与预热1 为了防止辊子左右串动造成在一端卡死不转,在辊子两端的支臂上焊有防串装置,组装时要留出辊子膨胀间隙10-12mm;2镀AL-Zn-Si锌锅温度较高,与室温辊子的温差较大,此类机组一定要配备三辊六臂烘箱,下锅前一定要预热,预热温度为500-550℃;换辊前4-5小时提前加热,逐渐升高设定温度,保温1-2小时;烘箱最好是可移动式,避免吊出烘箱后长时间吊运降温较多;14 锌锅下斜槽1 由于镀AL-Zn-Si锌锅温度较高为600℃,Zn的熔点为419℃,在锌锅下斜槽内的合金液面上,生产中会有锌被汽化成为锌“蒸汽”,锌“蒸汽”随气流向上,在较低的环境温度下,在下斜槽、热张紧辊室凝结成“锌灰”沉积;经验表明,连续生产一个月后下斜槽内和液面上沉积的“锌灰”量有几十公斤;2 镀AL-Zn-Si下斜槽与普通镀锌不同,在两侧面液面以上各留有一个可以开闭的清灰孔;必须每月清理一次下斜槽和液面上“锌灰”,可以安排在捞渣时清理;3 为了减少“锌灰”进入炉内,镀AL-Zn-Si下斜槽上部设置一对上、下翻板,翻板可以打开和关闭,生产中一对翻板关闭,可以防止锌“蒸汽”上行进入炉内附着在钢带上影响镀层的附着性能;穿带时打开翻板,使钢球落入锌锅;在一些机组上还在下斜槽内布置电加热辐射管,防止锌“蒸汽”凝结;“锌灰”中有一部分是氧化锌;下斜槽中通入精氮,不要通入掺有氢的保护气体,因为氢会使液相和固相界面的表面张力增大,影响合金液对钢板的浸润性,合金液对钢板的浸润性是热镀的先决条件和必要条件;5、镀后冷却与锌花控制1镀层组成:富铝的树枝晶、富铝树枝晶间铝-锌共晶相、针状富硅相、合金层四个部分组成;2富铝树枝状晶是镀层结构的主体,占镀层体积的80% 左右;其次是树枝晶间隙的铝-锌球团状共晶,占20%;再次,是树枝晶中间的针状富硅相;然后,就是镀层与钢基结合部位的合金层;3冷却速度镀铝-锌-硅带钢出锅后,要求快速冷却,冷却速度30-40℃/min,目的是控制富铝树枝状晶体长大锌花长大,较大的富铝树枝状晶体破坏了镀层优良的耐腐蚀性能,必须快速冷却,控制锌花长大;所以,镀铝-锌-硅带钢出锅后的气刀上方,设置一套可移动的垂直变频调速快冷风机箱;生产时像行车一样开进带钢运行线,断带、停机、停产、换辊、捞渣时开出带钢运行线;4希望锌花大一点,可以减小变频器频率减小风量、减小冷却速度;反之,可以增大变频器频率增大风量、减小冷却速度;5带钢出新锅温度600℃,出快冷风机温度为420-380℃,带钢到冷却塔第一个转向辊低于300℃,带钢进水淬温度150-180℃,出水淬带钢温度低于40℃;6、光整光整机有三种作用:一是改善表面光洁度;二是镀AL-Zn-Si对炉内气氛、脱脂质量要求很严格,经常会出现针空漏镀现象,通过光整对镀层压延弥合针空;三是一定程度地消除屈服平台,改善机械性能;光整机是镀AL-Zn-Si机组必备的工艺设备,不象普通镀锌机组的光整机的作用;三、铝-锌-硅合金液的浸蚀机理、镀层结构分析、底渣的物相分析参考文献1、实验条件镀液成分:AL55% ,% ,%1)钢板:普通低碳钢C: %冷轧退火钢板2)试样:801103)浸镀温度:600℃4)浸镀时间:分别为2、10、20、30、40、50min5)设备:锌埚电阻炉2、实验过程1试样前处理、干燥称重、碱洗除油、、酸洗除锈、涂覆助镀液并烘干;2热镀过程中需对镀液进行搅拌,以增加浸蚀效果;3实验结束后,用盐酸洗去试片上的铝锌硅镀层,干燥后称重;4利用电子扫描显微镜对铝锌硅镀层全貌及截面处微观结构进行观察;5通过能谱附件对镀层微观组织中不同相进行了微区成析;6利用X射线衍射,对热镀过程产生的底渣进行了物相分析;3、实验结果与分析1铝锌硅镀层对钢板的浸蚀试样平均减薄速度与浸镀时间之间大致呈线性关系;2分钟时试样没有减薄反而增加了,2分钟后开始减薄;大致7μm/min;这说明2分钟内和2分钟外的腐蚀机理不一样;(1)Fe、AL首先反应生成液相合金层;(2)富铁合金层被冲刷走,离开试样达到平衡;(3)AL,Si与进入镀液的Fe反应生成底渣;(4)浸蚀后板面凸凹不平,30分钟的试样出现了穿孔,边部参差不齐;结论:点蚀与均匀腐蚀共存,点蚀的危害更大,生产中停机时应避免断带;2镀层微观结构与微区成分1 镀铝-锌-硅钢板表面很平坦,没有镀锌一样的锌花和由结晶产生的不平,没有捷径形成的结晶学表面,已而反射率高;2截面微观结构a)镀层组成:富铝的树枝晶、富铝树枝晶间铝-锌共晶相、针状富硅相、合金层四个部分组成;b)富铝树枝晶是镀层结构的主体,占镀层体积的80% 左右;其次是树枝晶间隙的铝-锌球团状共晶,占20%;再次,是树枝晶中间的针状富硅相;然后,就是镀层与钢基结合部位的合金层;3底渣的X射线衍射物相分析(1)底渣中的重要成分是AL、Fe、Si;(2)控制底渣量关键要控制镀液中的铁含量;(3)减少浸镀时间,保证表面清洁,清洗干净;四、热镀过程的物理化学机理和热力学原理热镀的过程就是液相和固相间浸润和液相在固相表面上漫流的过程;合金液对钢带的浸润性与固液两相间的表面张力有关,固相钢带的清洁度和表面化学附着物如氧化膜、硅酸盐膜等,使固液两相间的表面张力增大;还与合金液的流动性有较密切的关系,流动性又与合金液的温度存在着密切的关系,合金液温度越高流动性越好,表面张力减小,也就是说合金液温度越高,液相与固相间的表面张力越小,浸润性越好;液相在固相表面的漫流是固相金属原子溶解与固液两相金属原子相互扩散的过程;液相在固相表面的漫流速度与固液两相间金属原子溶解、扩散反应速度有关,固液两相间金属原子溶解、扩散反应速度又与反应产生的合金相和热动力决定的,也就是说固液两相间金属原子溶解、扩散反应的动力是固液两相的温度;固液两相温度越高金属原子的扩散反应越快,但是固相金属原子的溶解反应也越快,即铁溶解于合金液的越快,这是与我们的愿望相反的;。
镀锌板锌渣生成与控制

镀锌板锌渣生成与控制作者:卢禹龙孟静来源:《中小企业管理与科技·下旬刊》2016年第02期摘要:本文针对镀锌板发生的锌渣缺陷,通过大量现场跟踪及理论分析,发现了锌渣产生的原因和规律。
结合热镀锌生产的整个生产工艺流程,分析了锌渣的主要影响因素,并在生产各工序制定了锌渣生成、控制的对策,取得了较好的控制效果。
关键词:热镀锌;锌渣;锌液;锌锅;Al含量1 概述随着热镀锌板代替电镀锌板不断进入家电板市场,用户对家电镀锌板的表面质量要求也不断提高,镀锌产品表面质量成为各镀锌板厂家竞争的关键。
沙钢同信镀锌机组采用的是改良森吉米尔法工艺,产品定位于建筑板和家电板。
由于镀锌家电板产量不断提高,锌渣不良品缺陷一直比较高,占到不良品率的20%以上。
为了解决镀锌板锌渣表面质量缺陷对产品质量所造成的影响,本文对镀锌家电板锌渣缺陷产生的原因进行了系统分析和研究,提出解决镀锌板表面锌渣缺陷的控制方法。
2.2 锌渣的分类锌锅中Zn含量在99%以上,由表一可知,Fe2Al5、ZnO、Al2O3密度低于Zn(7.3)降上浮;FeZn7、Fe5Zn21、FeZn13由于密度接近或超过Zn密度,这三种物质将悬浮或下沉。
故锌锅中的锌渣可大致分为三种,浮渣Fe2Al5、ZnO、Al2O3;悬浮渣FeZn7;底渣Fe5Zn21、FeZn13。
由上述可知,锌渣的生成与锌锅中的Fe有直接关系,如果锌锅中没有Fe或者Fe含量较低,那么锌渣的生成会大大降低。
控制锌渣生成的关键还是控制锌锅中Fe的含量。
2.3 锌锅中Fe的产生锌锅中Fe产生有原材料Fe粉残留、锌锅中设备的腐蚀、带钢入锌锅发生的反应等。
但就带入量而言,主要还是带钢入锌锅是Fe的铁损(如图四所示)。
Fe的溶出影响因素有:POT温度、成分、材质、入POT带钢温度。
首先,Fe2Al5层的以极快的速度形成,阻止Fe进一步的析出。
其次,溶出的Fe与POT中的Al、Zn发生反应生成dross。
锌渣产生原因及控制措施

正 常情况 下 , 生产 普通镀 锌 产品 时 , 液 温度 控 锌 制在 4 5~ 6 5 4 5℃ 。锌 液 温 度 在 4 0~ 9 5 4 5℃ 时 , 铁 锌之 间 的反应 是 扩 散 反应 , 成 的 细 小 的 F Z , 生 e n 游
及周 围环 境 的灰 尘 等 , 常将 带 钢 表 面 每平 方 米 残 通
性强 。
关键词 : 热镀 锌 ; 渣 ; 生 原 因 ; 制 措施 锌 产 控 中 图分 类 号 : G14 4 T 7 . 文献标识码 : A 文 章编 号 :0 6— 0 8 2 1 ) 9— 0 0—0 10 5 0 (0 2 0 0 6 2
REAS ON FOR ZD S A LAG BROUGHT ABOUT AND TS CONTRoL EAS I M URES
( 北 钢 铁 集 团 唐 钢 公 司 检 修工 程 公 司 , 北 唐 山 0 3 1 ) 河 河 6 0 6
摘 要 : 镀 锌 生 产 过 程 中 , 渣 的 产 生是 不 可 避 免 的 , 渣 的 大量 产 生 不仅 造 成 锌 消 耗 的增 加 , 且 会 影 在 锌 锌 而 响 产 品 质 量 。结 合 生 产 实 际 和 理论 研 究 , 要 介 绍 了 热 镀 锌 生 产 过程 中锌 渣 产 生 的 原 因 及分 类 , 出 了 简 提 减 少 锌 渣 的措 施 和 建 议 , 效 提 高 了镀 锌 产 品 质 量 , 少 锌 消 耗 , 实 际 生 产有 一定 的指 导 意 义 , 操 作 有 减 对 可
r d e o u p i n of z n e uc s c ns m t o i c.
Ke or s: otgav niai yW d h la z t on;zn sa ic lg;c u e a s s;c to e s r s onr lm a u e
镀铝锌硅GL生产时快速去除板结浮渣的方法[发明专利]
![镀铝锌硅GL生产时快速去除板结浮渣的方法[发明专利]](https://img.taocdn.com/s3/m/43c63a42d1f34693dbef3e15.png)
专利名称:镀铝锌硅GL生产时快速去除板结浮渣的方法专利类型:发明专利
发明人:孙力,张鹏,刘需,吝章国,刘宏强,梁媛媛,杨士弘申请号:CN201710452281.8
申请日:20170615
公开号:CN107338405A
公开日:
20171110
专利内容由知识产权出版社提供
摘要:本发明公开了一种镀铝锌硅GL生产时快速去除板结浮渣的方法,其在清渣前,加入铝锌硅使锌锅液面浸没板结浮渣,再将锌锅锌液温度提高至640℃~660℃,保温使板结浮渣软化,然后进行清渣。
本方法采用逆向思维,通过锌液温度和液面工艺控制,浸泡浮渣,先使浮渣板结疏松再集中清理,缩短浮渣清理时间,降低清理难度。
本方法可以节省清浮渣2至4小时作业时间,并减轻工人劳动强度,提高浮渣的打捞率,提高产品表面质量。
申请人:河钢股份有限公司
地址:050023 河北省石家庄市体育南大街385号
国籍:CN
代理机构:石家庄冀科专利商标事务所有限公司
代理人:赵红强
更多信息请下载全文后查看。
一种连续热镀铝锌生产线铝锌锅底锌渣清理储存装置[发明专利]
![一种连续热镀铝锌生产线铝锌锅底锌渣清理储存装置[发明专利]](https://img.taocdn.com/s3/m/bd79d7f10b4e767f5bcfce19.png)
专利名称:一种连续热镀铝锌生产线铝锌锅底锌渣清理储存装置
专利类型:发明专利
发明人:安龙龙
申请号:CN202011305069.7
申请日:20201120
公开号:CN112371237A
公开日:
20210219
专利内容由知识产权出版社提供
摘要:本发明公开了工业生产领域的一种连续热镀铝锌生产线铝锌锅底锌渣清理储存装置,包括包括箱体,所述箱体上端右部安装有滑板,箱体内上部安装有两个粉碎轮,粉碎轮中部均安装有第一丝杆,第一丝杆前端均安装有第一转动电机,箱体内侧壁中部均安装有斜板,箱体内左侧壁下部安装有粉碎室,斜板下端与粉碎室上端中部连通,粉碎室内中部安装有第二丝杆,第二丝杆上安装有多个粉碎叶片,第二丝杆右端穿过粉碎室连接有固定室,固定室内部安装有第二转动电机;本发明中,锌渣通过斜板移动到粉碎室内,第二转动电机转动,带动第二丝杆转动,带动粉碎叶片转动,对锌渣进行再次粉碎,使其粉碎达到标准,提高了作业的效率。
申请人:山东富海材料科技有限公司
地址:256600 山东省滨州市博兴县经济开发区富源二路96号
国籍:CN
代理机构:青岛博浩知识产权代理事务所(普通合伙)
代理人:张慧芳
更多信息请下载全文后查看。
- 1、下载文档前请自行甄别文档内容的完整性,平台不提供额外的编辑、内容补充、找答案等附加服务。
- 2、"仅部分预览"的文档,不可在线预览部分如存在完整性等问题,可反馈申请退款(可完整预览的文档不适用该条件!)。
- 3、如文档侵犯您的权益,请联系客服反馈,我们会尽快为您处理(人工客服工作时间:9:00-18:30)。
徐
勇 镀 铝锌机 组底 渣 的 清除与控 制
・ 5・ 1
悬 浮 渣 尺 寸 小 于 5 m, 液 有 合 适 的搅 动 情 况 锌
下 , 浮渣 可 以大 量 的 被 带 钢带 走 且 又不 影 响产 悬 品 的表 面质 量 。
2 除渣经 过
1 2
机械 除渣 包 括 使用 抓 斗 进 行 捞 渣 、 用 氮气 使 管 吹渣 、 橇 棒撬 渣 、 耙 子 扒 渣等 方 法 , 械 除 用 用 机 渣 可 以清 除锅 底 淤 泥状 底 渣 , 块 状 底 渣 效果 甚 对
1 背 景
5 % A 一Z 5 1 n锌 液 中含 有 一 定 溶 解 度 的 铁 , 铁会 和锌液 中的铝锌反 应生 成悬 浮渣悬 浮在 锌液 中 , 部分 悬浮 渣被带 钢带 走形成 锌渣 缺 陷 , 一 还有
一
A 、5 0 D+ Z等牌 号 。 Z S5 G A
本 机组设 置 预 熔 锅 和 主锌 锅 , 锅 采 用 无 芯 锌 感 应 加热技 术 , 主锌 锅直 径 35m, 2 1m, . 深 . 预熔
有明显 的锌渣 富集成层 状 , 响产 品质 量。在 影 21 00年 1 1月 2 日, 钢 在 锌 锅 处 断 带 , 机 捞 9 带 停
渣 , 过定 点 测量 , 锅 底部 已经 结成 块 状底 渣 , 经 锌 离沉 没辊 辊面 仅 1 m, 5e 在生 产 和 合 同 的压力 下 , 采取 了垫 高沉 没辊 1 m 的方 法 维 持 , 1 0e 于 2月 3 日开 机 生产 ,2月 5 日再 次在 锌 锅 处 断带 , 确 1 并 认 断带 原 因是 由于底渣结 块 已经碰 到 了沉 没辊 底 部, 当时决定停 机 除渣 。
流动 , 阻止锌 液 中悬浮 渣 的沉 积 , 效 防止镀 铝锌 有
底渣 的结块 。
锡、 热镀锌、 热镀铝锌等机组 , 立足于 “ 以宝钢 为 主自主集 成 , 国内负责 自主设 计 、 制造 , 分 引 部 进” 的原则 , 除连退和电镀锡机组引进外 , 其它机 组定 位 国内 自主开发 。其 中的热 镀铝锌 机组 由宝 钢工程技术公司总承包 , 立足 自主设计和集成 , 关 键单体设备引进 , 以工艺集成为主体完成整条线 的设 计 、 工 、 装 和 调 试 。机 组 按 照 年 产 量 2 施 安 5
Ke r s h tdp Z ・ 1 b t m lg 5 % A1 n l u d y wo d : o - i n- ; ot sa ; 5 - A o ・ i i ・ Z q
梅 钢公 司冷轧 厂是 宝钢 股份 公司 自主集 成创 Байду номын сангаас 的示 范 工 程 和试 点 项 目, 括 酸 轧 、 包 连退 、 电镀
结 块的过 程进行 了分析和 讨论 , 对今 后如 何监 控镀 铝锌 机 组 底 渣 结块提 出了相 应 的对 策 和措 施 。最后 , 理论 上提 出了锌 渣缺 陷控 制的措 施和 减 少底 渣 形成 的工 艺方 法。 从 关键 词 : 铝 锌 ; 渣 ;5 I— n锌 液 镀 底 5 %A Z
形成难以去除的块状底渣 , 严重影 响镀铝锌 的稳 定生成 。通过工艺改进可以使镀铝锌稳定生成并 且悬 浮渣 少 , 论上 可 以从 以下几 个 方面 人手 : 理 ① 降低锌液中铁的溶解量 ; ②减少悬浮渣的形成量; ③ 减少 悬浮渣 向锌 锅底部 的沉 积 , 有文献 指 出 , 当
・
l 4・
梅 山科技
21 0 2年第 4期
镀 铝锌 机 组 底渣 的 清除 与控 制
徐 勇
( 山钢 铁公 司冷轧厂镀 锌 车 间 南京 2 0 3 ) 梅 10 9 摘 要: 主要 介 绍 了2 1 0 0年 1 2月份 梅 钢公 司镀 铝锌底 渣 结块后 的去 除经过 , 同时对底 渣
部 分悬 浮渣会 沉积 到锌锅 底部 形成 底渣 。底渣
沉 积时 间长 了以 后会 在 锌锅 底部 聚 集 成 块 , 终 最
锅直径 14m, 主锌锅功率 2 0 W, . 深2m, 0 0 k 预熔
锅 功率 100k 0 W。带 钢 人 锌 锅 温 度 按 6 0℃设 0 计 , 锅熔 液温 度也按 照 60o设 计 , 锌 0 C 锌液 成分则 按 照 5 %铝 、35 锌 、.% 硅 设计 。根 据 无 芯 5 4.% 15 锌 锅理 论 , 镀铝 锌 过 程 中会 在 锌 液 内部 形 成 涡 流
计 的 0 3 2 0m 宽度 达 到 8 0—1 8 m, .5— . m, 0 2m 产 2
品品种 包括 D 5 D+ Z、 C 2 C 1 A D 5 D+A 、3 0 D+ Z S5 G
从 21 00年 6月开始 , 镀铝 锌 主锅 底渣 逐 渐结
块 , 渐影 响到 机组 的生产 。期 间 , 没辊 系表 面 逐 沉
万 t 行 设 计 , 品定位 上 和 宝 钢 股份 公 司原 有 进 产 的热 镀铝 锌机 组 进行 分 工 , 以厚 规 格镀 铝 锌 板 为 主。梅钢 镀铝 锌机组 从 2 0 0 7年 7月 开始 打桩 , 到 20 0 8年 6月开 始 设 备 安装 ,09年 8月 2 日开 20 8 始热 试 , 目前 已稳定 生产 了两 年 , 品厚度 达 到设 产
Re v la d Co t o fBo t m l g o td p Zn Al l a ii g Li e mo a n n r l to S a fHo - i - o Ga v n zn n
Xu y 0
( a a in rso f o o igPat f i a rn& Sel o , aj g2 0 3 ) G l nz gWokhpo l R ln ln s nI v i C d l o Me h o t . N ni 10 9 eC n