砂型铸造说明书
铸造工艺设计说明书

铸造⼯艺设计说明书铸造⼯艺设计说明书课程设计:机械⼯艺课程设计设计题⽬:底座铸造⼯艺设计班级:机⾃1103设计⼈:学号:指导教师:张锁梅、贾志新前⾔学⽣通过设计能获得综合运⽤过去所学过的全部课程进⾏机械制造⼯艺及结构设计的基本能⼒,为以后做好毕业设计、⾛上⼯作岗位进⾏⼀次综合训练和准备。
它要求学⽣全⾯地综合运⽤本课程及有关选修课程的理论和实践知识,进⾏零件加⼯⼯艺规程的设计和机床夹具的设计。
其⽬的是:(1)培养学⽣综合运⽤机械制造⼯程原理课程及专业课程的理论知识,结合⾦⼯实习、⽣产实习中学到的实践知识,独⽴地分析和解决机械加⼯⼯艺问题,初步具备设计中等复杂程度零件⼯艺规程的能⼒。
(2)培养学⽣能根据被加⼯零件的技术要求,运⽤夹具设计的基本原理和⽅法,学会拟订夹具设计⽅案,完成夹具结构设计,进⼀步提⾼结构设计能⼒。
(3)培养学⽣熟悉并运⽤有关⼿册、图表、规范等有关技术资料的能⼒。
(4)进⼀步培养学⽣识图、制图、运算和编写技术⽂件的基本技能。
(5)培养学⽣独⽴思考和独⽴⼯作的能⼒,为毕业后⾛向社会从事相关技术⼯作打下良好的基础。
⽬录⼀、⼯艺审核 (1)1.数量与材料 (1)2.图样 (1)3.零件的结构性 (1)⼆、成形⼯艺设计 (1)1.确定⼯艺⽅案 (1)(1)浇注位置的选择 (2)(2)分型⾯的选择 (2)2.确定铸造⼯艺参数 (4)(1)机械加⼯余量和铸出孔 (4)(2)浇注位置的选择 (5)(3)拔模斜度 (5)(4)铸造收缩率 (6)3.砂芯设计 (6)4.浇注系统的设计 (6)5. 冷铁的设置 (6)三、⼼得体会 (7)⼀、⼯艺审核1、数量与材料由零件图可知,该零件结构⽐较简单,但是形状不是很规则,⼯作条件⼀般以承受压⼒为主,故要求该零件有良好的刚性和强度。
另外,根据零件图的要求,该底座零件为单件⼩批量⽣产,另外材料选⽤灰铸铁HT200,流动性较好,适于铸造。
2、图样该零件图给出了主视图、左视图、俯视图3个视图。
87砂型铸造PPT课件

(一)铸造工艺对铸件结构的要求
悬臂支架
闭式结构
开式结构
以垛代砂芯
凸缘外伸
凸缘内伸
28
避免使用活块
未延伸凸台
结构斜度
延伸凸台
29
(二)合金铸造性能对铸件结构的要求
铸件的壁 厚且均匀
结构圆角
壁间大角 度连接
30
交叉接头
交错接头
环状接头
圆角过渡
倾斜过渡
复合过渡
31
写在最后
经常不断地学习,你就什么都知道。你知道得越多,你就越有力量 Study Constantly, And You Will Know Everything. The More
带轮的三箱造型
用外砂芯将三箱改为两箱
9
(二)机器造型
机器造型是将填砂、紧实和起模等主要工序实现了机 械化,并组成生产流水线。机器造型生产率高,铸型质量好, 铸件质量高,适用于中小型铸件的大批量生产。
造型生产线示意图
造型生产线
10
机器造型方法一
机器造型方法:振压造型、高压造型、抛砂造型。
1、振压造型工作原理
1、支座
方案Ⅱ 沿底面分型,铸件全部在 下箱,不会产生错箱,铸 件易清理。但轴孔内凸台 必须采用活块或下芯且轴 孔难以铸出。
方案Ⅰ 沿底版中心分型。轴 孔下芯方便,但底版上 四个凸台必须采用活块 且铸件在上、下箱各半。
23
(五)实例分析
2、C6140车床进给箱体
分型面和 浇注位置选 择方案?
重量:35kg 材料:HT150 保证基准面不得有 缺陷,以便定位。 勿需考虑补缩。
柔性造型单元流程:
待工作模板进入 模板快换机构
调整造型机 工作参数
2018-砂型铸造作业指导书-范文模板 (6页)
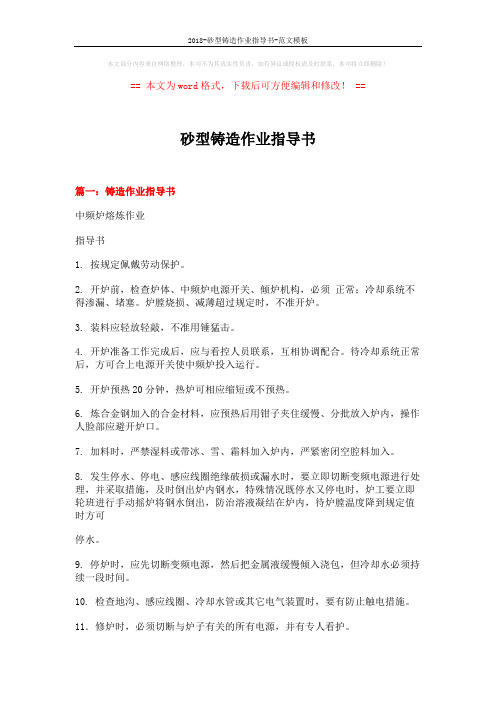
本文部分内容来自网络整理,本司不为其真实性负责,如有异议或侵权请及时联系,本司将立即删除!== 本文为word格式,下载后可方便编辑和修改! ==砂型铸造作业指导书篇一:铸造作业指导书中频炉熔炼作业指导书1. 按规定佩戴劳动保护。
2. 开炉前,检查炉体、中频炉电源开关、倾炉机构,必须正常;冷却系统不得渗漏、堵塞。
炉膛烧损、减薄超过规定时,不准开炉。
3. 装料应轻放轻敲,不准用锤猛击。
4. 开炉准备工作完成后,应与看控人员联系,互相协调配合。
待冷却系统正常后,方可合上电源开关使中频炉投入运行。
5. 开炉预热20分钟,热炉可相应缩短或不预热。
6. 炼合金钢加入的合金材料,应预热后用钳子夹住缓慢、分批放入炉内,操作人脸部应避开炉口。
7. 加料时,严禁湿料或带冰、雪、霜料加入炉内,严紧密闭空腔料加入。
8. 发生停水、停电、感应线圈绝缘破损或漏水时,要立即切断变频电源进行处理,并采取措施,及时倒出炉内钢水,特殊情况既停水又停电时,炉工要立即轮班进行手动摇炉将钢水倒出,防治溶液凝结在炉内,待炉膛温度降到规定值时方可停水。
9. 停炉时,应先切断变频电源,然后把金属液缓慢倾入浇包,但冷却水必须持续一段时间。
10. 检查地沟、感应线圈、冷却水管或其它电气装置时,要有防止触电措施。
11.修炉时,必须切断与炉子有关的所有电源,并有专人看护。
浇注作业指导书1. 作业前,应戴口罩、长皮手套、鞋苫,扎好护腿。
鞋苫严禁扎在裤角外。
2. 浇注现场应无易燃易爆物品,无潮湿和积水,通道畅通,场地平整,照明及通风良好。
3. 较高的铸型,应合箱置于干燥的地坑中。
浇注时,地坑中不得有人。
金属铸型在浇注前,应先预热到工艺规定的温度。
4. 浇注前,盛钢水的浇包必须烤干,决不允许有潮层。
5. 准备投放到金属液中的合金以及与金属液接触的挡渣辊、扒渣板等铁器必须预热烘烤。
禁止用空心管状物与金属液相接触。
6. 起重机吊运的浇包,在盛装金属液之前,应先扣牢防止浇包倾斜的保险卡。
砂型铸造作业指导书
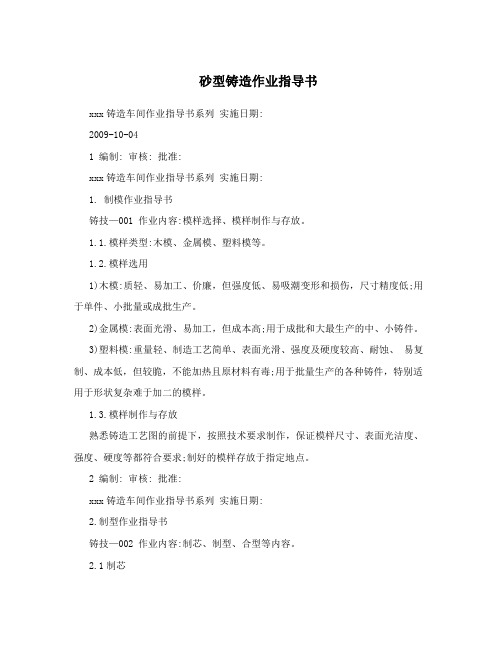
砂型铸造作业指导书xxx铸造车间作业指导书系列实施日期:2009-10-041 编制: 审核: 批准:xxx铸造车间作业指导书系列实施日期:1. 制模作业指导书铸技—001 作业内容:模样选择、模样制作与存放。
1.1.模样类型:木模、金属模、塑料模等。
1.2.模样选用1)木模:质轻、易加工、价廉,但强度低、易吸潮变形和损伤,尺寸精度低;用于单件、小批量或成批生产。
2)金属模:表面光滑、易加工,但成本高;用于成批和大最生产的中、小铸件。
3)塑料模:重量轻、制造工艺简单、表面光滑、强度及硬度较高、耐蚀、易复制、成本低,但较脆,不能加热且原材料有毒;用于批量生产的各种铸件,特别适用于形状复杂难于加二的模样。
1.3.模样制作与存放熟悉铸造工艺图的前提下,按照技术要求制作,保证模样尺寸、表面光洁度、强度、硬度等都符合要求;制好的模样存放于指定地点。
2 编制: 审核: 批准:xxx铸造车间作业指导书系列实施日期:2.制型作业指导书铸技—002 作业内容:制芯、制型、合型等内容。
2.1制芯2.2.1材料及混砂工艺1.水玻璃自硬砂1)原料原砂(福建水洗海砂,40/70筛号)100%;水玻璃 2.8%;有机酯 0.28%。
2)混砂工艺:原砂 + 有机酯,水玻璃,混砂速度快、混合均匀。
2.树脂砂1)原料新砂(SC40-70目,含泥及微粉量<1.5%,含水量<0.2%)100%;呋喃树脂 1-2%;固化剂加入量为呋喃树脂的30%左右;2)混制工艺:原砂 + 固化剂(匀混60秒)? 树脂(匀混35-40秒),随混随用。
3)将型芯清理时的残砂及时拉走。
2.2.2制芯1.制芯方法:手工制芯:刮板造芯,机器造芯:震实式、挤压式、壳芯式、自硬砂流水线。
2.型芯制作步骤1)型砂与芯骨组装好放入芯盒内。
2)确定型芯气道:对型芯应设置排气道;型芯排气道应与铸型排气口相通。
3.要求:型芯含水量、强度、透气性符合工艺要求。
砂型铸造说明书
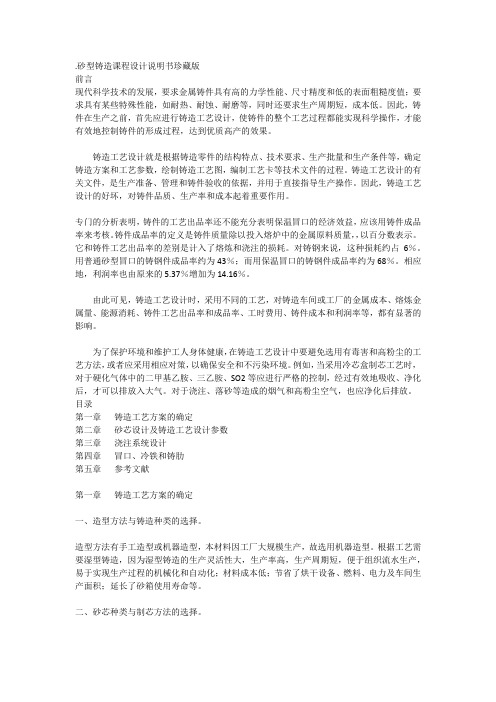
.砂型铸造课程设计说明书珍藏版前言现代科学技术的发展,要求金属铸件具有高的力学性能、尺寸精度和低的表面粗糙度值;要求具有某些特殊性能,如耐热、耐蚀、耐磨等,同时还要求生产周期短,成本低。
因此,铸件在生产之前,首先应进行铸造工艺设计,使铸件的整个工艺过程都能实现科学操作,才能有效地控制铸件的形成过程,达到优质高产的效果。
铸造工艺设计就是根据铸造零件的结构特点、技术要求、生产批量和生产条件等,确定铸造方案和工艺参数,绘制铸造工艺图,编制工艺卡等技术文件的过程。
铸造工艺设计的有关文件,是生产准备、管理和铸件验收的依据,并用于直接指导生产操作。
因此,铸造工艺设计的好坏,对铸件品质、生产率和成本起着重要作用。
专门的分析表明,铸件的工艺出品率还不能充分表明保温冒口的经济效益,应该用铸件成品率来考核。
铸件成品率的定义是铸件质量除以投入熔炉中的金属原料质量,,以百分数表示。
它和铸件工艺出品率的差别是计入了熔炼和浇注的损耗。
对铸钢来说,这种损耗约占6%。
用普通砂型冒口的铸钢件成品率约为43%;而用保温冒口的铸钢件成品率约为68%。
相应地,利润率也由原来的5.37%增加为14.16%。
由此可见,铸造工艺设计时,采用不同的工艺,对铸造车间或工厂的金属成本、熔炼金属量、能源消耗、铸件工艺出品率和成品率、工时费用、铸件成本和利润率等,都有显著的影响。
为了保护环境和维护工人身体健康,在铸造工艺设计中要避免选用有毒害和高粉尘的工艺方法,或者应采用相应对策,以确保安全和不污染环境。
例如,当采用冷芯盒制芯工艺时,对于硬化气体中的二甲基乙胺、三乙胺、SO2等应进行严格的控制,经过有效地吸收、净化后,才可以排放入大气。
对于浇注、落砂等造成的烟气和高粉尘空气,也应净化后排放。
目录第一章铸造工艺方案的确定第二章砂芯设计及铸造工艺设计参数第三章浇注系统设计第四章冒口、冷铁和铸肋第五章参考文献第一章铸造工艺方案的确定一、造型方法与铸造种类的选择。
《砂型铸造》课件

历史与发展
历史
起源于古代中国,至今已有数千年的 历史。
发展
随着科技的不断进步,砂型铸造工艺 不断改进,提高了铸造质量和效率。
应用领域
01
汽车制造
发动机、底盘、刹车系统等。
02
机械制造
机床、泵、阀等。
03
航空航天
飞机、火箭、卫星等。
04
船舶制造
船体、发动机、配件等。
PART 02
砂型铸造工艺流程
REPORTING
模具设计与制作
模具设计
根据产品需求和铸造工艺要求,进行 模具设计,包括模具结构、尺寸、材 料选择等。
模具制作
根据设计图纸,采用合适的材料和工 艺,制作出符合要求的模具。
砂型制作
准备砂料
选择合适的砂料,进行筛选和干燥。
砂型制作
将砂料填入模具中,经过振动、夯实、排气等工序,制成砂型。
PART 06
砂型铸造案例分析
REPORTING
案例一:某复杂铸件的生产过程
总结词
工艺流程复杂
详细描述
由于该铸件结构复杂,对铸造技术要求较高,需要采用特 殊的铸造工艺和材料,以确保铸件的质量和性能。
详细描述
该案例介绍了某复杂铸件的生产过程,涉及到模具设计、 砂型制备、浇注、冷却和清理等工艺流程,其中每个环节 都需要精细的操作和严格的质量控制。
总结词
环保与可持续发展
总结词
智能化与自动化趋势
详细描述
该案例介绍了智能化与自动化在新型砂型铸造技术中的应 用趋势,通过引入智能化技术和自动化设备,可以提高铸 造生产的效率和稳定性,降低人工成本和操作风险。
THANKS
感谢观看
REPORTING
砂型铸造说明书
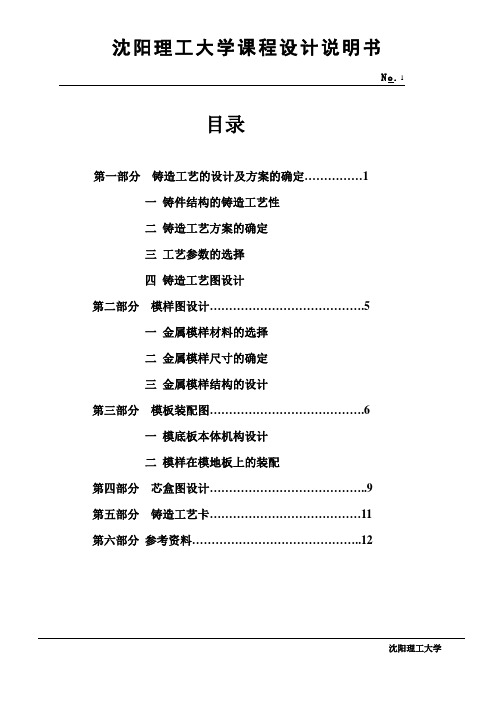
N o.1目录第一部分铸造工艺的设计及方案的确定 (1)一铸件结构的铸造工艺性二铸造工艺方案的确定三工艺参数的选择四铸造工艺图设计第二部分模样图设计 (5)一金属模样材料的选择二金属模样尺寸的确定三金属模样结构的设计第三部分模板装配图 (6)一模底板本体机构设计二模样在模地板上的装配第四部分芯盒图设计 (9)第五部分铸造工艺卡 (11)第六部分参考资料 (12)N o.2第一部分铸造工艺的设计及方案的确定一铸件结构的铸造工艺性生产铸件,不仅需要采用先进的合理的铸造工艺和设备,而且还要使零件结构本身符合铸造的生产要求。
铸造结构是否合理,和铸造合金的种类,产量的多少,铸造方法和生产条件等有密切关系。
1、铸件质量对零件结构的要求1 )铸件的壁厚应合理每一种铸造合金的铸件,都有其合适的壁厚范围,如果是选择适当,既能保证逐渐的机械性能要求,又方便铸造生产还可以简便地消除许多缺陷。
2)铸造斜度在铸件壁的内外侧面顺着拔模的方向应该带有斜度,以便起模和简化铸造工艺。
3)保证铸件质量的合理结构2、铸造合金对零件结构的要求1)合金种类:灰铸铁件2)性能特点:流动性好,体收缩和线收缩小,缺口敏感性小。
综合机械性能低,抗压强度抗拉强度高约3~4倍。
吸震性好,比钢约大10倍。
弹性模数较低。
3)结构特点:因流动性好,可铸壁较薄,形状复杂的铸件。
铸件残余应力小,吸震性好。
二铸造工艺方案的确定铸造工艺方案概括地说明了铸造生产的基本过程和方法。
确定合理而先进的铸造工艺方案,对获得优质铸件,简化工艺过程,提高生产率,改善劳动条件,以及降低生产成本等起着决定性的作用。
1、造型、造芯方法及铸型种类1)造型方法:砂箱造型。
主要特点是在砂箱内造型,操作方便,劳动量较小。
应用于大、中、小铸件,大量成批和单件上产。
2)造芯方法:芯盒造芯。
主要特点是用芯盒内表面形成砂芯的形状,砂芯尺寸准确,可制造小而复杂的砂芯。
应用于各种形状、尺寸和批量的砂芯。
2.2砂型铸造

合成树脂 有机粘结剂 桐油
油类粘结剂
亚麻仁油
3 附加物 煤粉、重油:防粘砂。 木屑:加入到需要烘烤的砂型中,增加铸 型的孔隙率,提高其透气、退让性。 4水
三、涂料及扑料
为防止铸件表面粘砂,并使铸件表面光滑,常在 铸型型腔表面覆盖一层耐火材料。 1 涂料 石墨+粘土水剂:用于铸铁干型 石英+粘土水剂:用于铸钢干型 2 扑料 石墨粉、滑石粉:用于铸铁湿型 石英粉:用于铸钢湿型。
700 800 900
420 480 600
2 2 2
225~305 245~335 280~360
柴油机、汽油机曲 轴;磨床、铣床、车床 的主轴;空压机、冷冻 机缸体、缸套
汽车、拖拉机传动齿 轮
球化处理工艺有冲入法和型内球化法
铁水 出铁槽
冒口
积渣包
铁水包 草木灰 硅铁粉 合金球化剂 铸件 反应室
浇 注
铸 件 热 处 理
2.2.1 造型材料
造型材料:砂型铸造中用来制作铸行的原材 料以及由各种原材料按一定比例 配置而成的混合料。 型 砂:用来制作砂型的造型混合料。 芯 砂 :用来制作砂芯的造芯混合料。
一、型(芯)砂的主要性能
1 强度 型砂抵抗外力破坏的能力,有干强度和 湿强度。强度过低,易造成:塌箱、冲砂、 砂眼等缺陷。 型砂的强度取决于:粘结剂的种类、紧 实度、原砂粒度、水的含量。
★灰口铸铁的孕育处理
应用:静载下要求较高强度、高耐磨性或高气密性的铸件, 特别是厚大铸件。
180
硬度HB
170
160
150
140 150
100
50
0
50
100
150
表面
底座铸造说明书
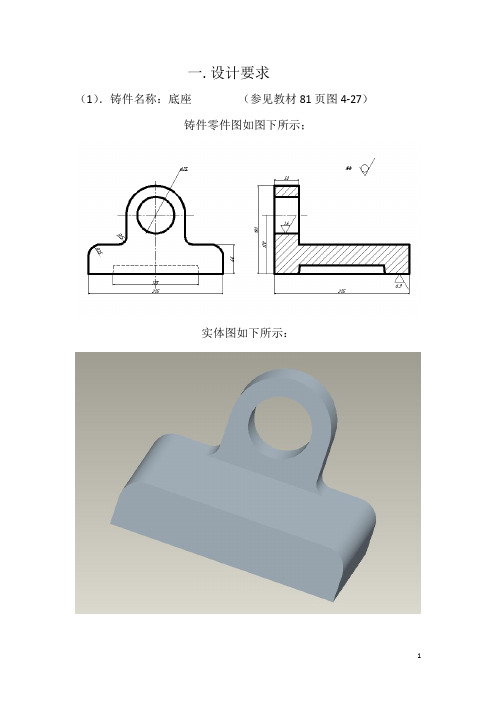
一.设计要求(1).铸件名称:底座(参见教材81页图4-27)铸件零件图如图下所示;实体图如下所示:(2).铸件材质:采用HT200;铸件重量:3.5kg(3).数量:大批量。
二.铸造工艺方案确定1.浇注位置的确定铸件的浇注位置是指浇注时铸件在铸型中所处的位置。
浇注位置是根据铸件的结构特点、尺寸、技术要求、铸造合金特性、铸造方法以及生产车间的条件决定的。
分析该铸件,铸出孔为重要加工面,所以选择放在底部,而底座侧立,防止产生砂眼,气孔和夹渣等缺陷。
铸件的浇注位置如下图:2.分型面的确定铸造分型面是指铸型组员间的接合面。
该铸件为大批量生产,选择用机器造型,所以分型面应该尽量少,其分型面如下图所示:三.铸造工艺参数确定1.铸件质量对零件结构的要求(1).铸件的最小壁厚铸件的最小壁厚为22.5mm,查表可知满足最小壁厚条件。
(参见《铸造工艺设计》李弘英P11)(2).最小铸出孔;查表1-7,可知最小铸出孔为φ10-φ15mm,该铸件铸出孔为φ75mm,(参见《铸造工艺设计》李弘英P11)满足条件。
(3).起模斜度非加工铸造壁的内、外两侧,沿着起模方向应该设计出适当的斜度,即结构斜度,以便于起模和简化铸造工艺。
其简图如下:由于铸件的起模方向的尺寸h=(250-500)mm,所以对于木模样α为0°25′,a为1.8mm。
(参见《铸造工艺设计》李弘英P19 表1-15)(4).尺寸公差等级CT查表可得可知取CT8-CT12,取CT8;(参见《铸造工艺设计》李弘英P13 表1-11)(5).机械加工余量毛坯铸件典型的机械加工余量参见《铸造工艺设计》李弘英P17表1-13)灰铸铁(采用砂型铸造)要求机械加工余量E-G,选G;查表1-12,P16,可知加工余量为:孔的加工余量:3.5mm;侧面加工余量:0.7mm;顶面加工余量:3.5mm;底面加工余量:3.5mm;(6).铸造收缩率参见《铸造工艺设计》李弘英P17表1-14)受阻收缩率0.9%;自由收缩率1.0%;(7).铸造圆角铸件上相邻两壁间的交角,做成铸造圆角,防止在尖角处产生裂纹及冲砂等缺陷。
《砂型铸造工艺及工装》课程设计说明书
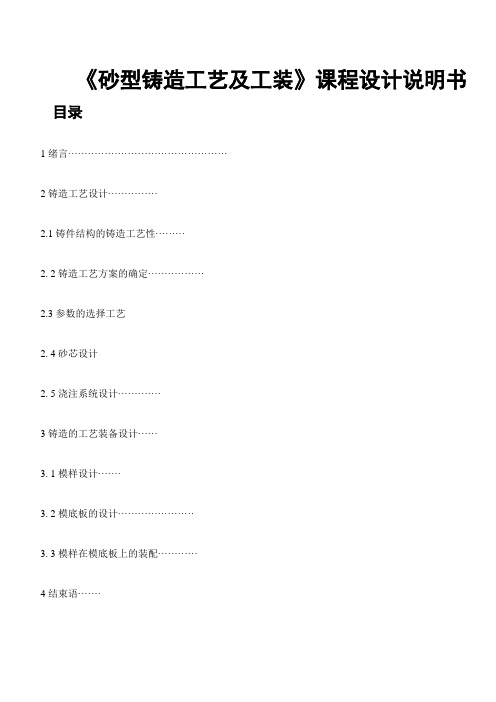
《砂型铸造工艺及工装》课程设计说明书目录1绪言················································2铸造工艺设计···············2.1铸件结构的铸造工艺性·········2. 2铸造工艺方案的确定·················2.3参数的选择工艺2. 4砂芯设计2. 5浇注系统设计·············3铸造的工艺装备设计······3. 1模样设计·······3. 2模底板的设计·······················3. 3模样在模底板上的装配············4结束语·······参考文献1绪言我本次课程设计的任务是对灰铸铁支承座进行铸造工艺及工装设计。灰铸铁具有良好的铸造性能良好的减振性、良好的耐磨性能良好的切削加工性能、低的缺口敏感性。灰铸铁的抗拉强度、塑性和韧性远低于钢,力学性能较差,但抗压强度与钢相当。铸造是指将液态合金注入铸型中使其冷却、凝固,并进行后处理,最终成为金属制品的一种生产方法。铸件的生产过程,也就是从零件图开始,一直到铸件成品检验合格入库为止,要经过很多道工序,铸件的生产过程称为铸造生产工艺过程。本次设计采用砂型铸造,其最大优点就是生产成本低,为机械制造行业中广泛应用的毛坯生产工艺方法。在砂型铸造的过程中,考虑到铸件的结构,生产条件以及加工批量等因素,要对铸件工艺的设计作全面分析,为避免铸件的缺陷,我们要根据标准选择合理的工艺设计方法。由于每个铸件的生产任务和要求不同,生产条件不同,因此铸造工艺及工装设计的内容也不同。一般情况下,铸造工艺设计包括以下几种技术文件:铸造工艺图,铸造工艺卡,铸型装配图,铸件图,模样图,‘芯盒图,砂箱图,模板图。铸造工艺及工装设计的过程如下:(1)对零件图纸进行审查和进行铸造工艺性分析(2)选择铸造方法,确定铸造工艺方法(3)绘制铸造工艺图(4)绘制铸件图(5)绘制铸型装配图(6)绘制各种铸造工艺装配图工装图要以铸造工艺图为主要设计依据。2铸造工艺设计2. 1铸件结构的铸造工艺性生产铸件,不仅需要采用先进的合理的铸造工艺和设备,而且还要使零件结构本身符合铸造生产的要求,易于保证铸件品质,简化铸造工艺过程和降低成本。这种对于铸造工艺过程来说的铸件结构的合理性,称为铸件的“铸造工艺性’,它和铸造合金的种类,产量的多少,铸造方法和生产条件等有密切的关系。2. 1 .1审查铸件结构(一)铸件应有合适的壁厚避免浇不到、冷隔等缺陷,铸件不应太薄。本次设计的铸件材料为HT200,最大尺寸为194 X 155mm。查表得,铸件尺寸在200 X 200mm以下时,灰铸铁最小允许壁厚为x-6mm,铸件最小壁厚满足情况。从合金的结晶特点可知,随着壁厚的增加,中心部分的晶粒变粗大,常出现缩孔、缩松等缺陷,导致力学性能降低。表2-1指出,随着壁厚的增加,灰铸铁件的相对强度不断的降低。表2-1 壁厚与灰铸铁相对强度的关系所以铸件也不应设计得太厚,各种合金铸件的临界壁厚可按最小壁厚的3倍来考虑,铸件最大壁厚不满足情况,但由于铸型刚度要求较低,所以设计可行。(二)铸件有最小铸出孔最小铸出孔的尺寸和铸件的生产批量、合金种类、铸件大小、孔处铸件壁厚、孔的长度以及孔的直径有关。1.加工圆孔表2-2灰铸铁铸件的最小铸出孔(mm)<50mm,零件上的加工孔直径均小于30mm,所以均不用铸出。2.不加工孔一般情况下应尽量铸出。但是孔径<30毫米(小批生产),或孔的长度和孔的直径之比大于4时,则不便铸出。本设计中有一个可切削出来的的孔槽,因槽深度只有6mm,不用铸造出来。工艺图上有说明。(三)铸件结构不应造成严重的收缩阻碍注意壁厚过渡和圆角两壁交接若呈直角形,翔形成热节,铸件收缩时阻力较大,在此处经常出现热裂。铸件薄、厚壁的相接、拐弯、等厚度的壁与壁的各种交接,都应采用逐渐过渡和转变的形式,使用较大的圆角相连接,避免因应力集中导致裂纹缺陷。铸件有一处两壁成直角交接,该用圆角过渡,如工艺图所示.其余地方成直角相接的两壁,薄、厚壁相接都用圆角过渡,满足情况。(四)铸件内壁应薄于外壁铸件的内壁和肋等,散热条件较差,应薄于外壁,以使内壁、外壁能均匀的冷却,减轻内应力和防止裂纹。此铸件没有内壁和肋,不予考虑。(五)壁厚力求均匀,减少肥厚部分,防止形成热节薄厚不均的铸件在冷却过程中会形成较大的内应力,在热节处易于造成缩孔、缩松和热裂纹,因此应取消那些不必要的厚大部分。因零件的结构要求不可改变铸件的内外壁形状,不能达到厚度均匀,铸件各个部分不同壁厚的连接采用的是逐渐过渡。(六)利于补缩和实现顺序凝固对于铸钢等体收缩大的合金铸件,易于形成收缩缺陷,应仔细审查零件结构实现顺序凝固的可能性。但是此次设计的灰铸铁的结晶范围窄,更接近于层状凝固。凝固时的膨胀和液态收缩趋于相互补偿,补缩效果好,铸件品质良好。(七)防止铸件翘曲变形某些壁厚均匀的细长形铸件、较大的平板形铸件及壁厚不均的长形箱体,会产生翘曲变形。主要原因是结构刚度差,铸件各面冷却条件的差别引起的内应力,或者是壁厚相差悬殊,冷却过程中引起较大的内应力,造成铸件变形。本次设计的铸件结构不会翘曲变形。(八)避免浇注位置上有水平的大平面结构在浇注时,如果型腔内有较大的水平面存在,当金属液上升到该位置时,由于断面突然扩大,金属液面上升速度变得非常小,灼热的金属液面较长时间地、近距离烘烤顶面型壁,极易造成夹砂、渣孔、砂孔或浇不到等缺陷。应尽可能把水平壁改进为稍带倾斜的壁或曲面壁。本次设计的浇注位置上无水平大平面,符合条件,见工艺图。2.1.2从简化铸造工艺方面改进零件结构(一)改进妨碍起模的凸台、凸缘和肋板的结构铸件侧壁上的凸台(搭子)、凸缘和肋板等常妨碍起模,为此,机器造型中不得不增加砂芯。设计中由于分型面横切肋的最大截面和铸件的形状特点,不存在妨碍起模的问题。(二)取消铸件外表侧凹铸件外侧壁上有凹入部分必然妨碍起模,需要增加砂芯才能形成铸件形状。常可稍加改进,即可避免凹入部分。但由于此铸件结构不能改变,因此工艺图上必须设计1#砂芯。(三)改进铸件内腔结构以减少砂芯铸件内腔的肋条,凸台和凸缘的结构欠妥,常是造成砂芯多、工艺复杂的重要原因。改进后需简化工艺、工装设计,降低铸件成本。本次设计的铸件内腔无复杂形状,无需改进。(四)减少和简化分型面若铸件必须采用不平分型面,增加了制造模样和模板的工作量,尽量改进用一平直的分割面进行造型。铸件平面分型,所容易选择地分型面位置如图所示,上下型形状相同。(五)有利于砂芯的固定和排气工艺图上的2#砂芯,原本是一个水平轴孔砂芯和一个悬臂式砂芯,悬臂砂芯需用芯撑固定,改进后,悬臂砂芯和轴孔砂芯,连成一体,变成一个砂芯,取消了芯撑。(六)减少清理铸件的工作量铸件清理包括:消除表面粘砂、内部残留砂芯,上除浇注系统、冒口和飞翅等操作。这些操作劳动量大且环境恶劣,铸件结构设计应注意减轻清理的工作量。(七)简化模具的制造单件、小批生产中,模样和芯盒的费用占铸件成本的很大比例。为节约模具制造工时和材料,铸件应设计成规则的、容易加工的形状。这次设计的铸件形状易加工,无需改变其形状。(八)大型复杂件的分体铸造和简单小件的联合铸造有些大而复杂的铸件可考虑分成几个简单的铸件,铸造后再用焊接方法或用螺栓将其连接起来。一些很小的零件,如小轴套等,常可把许多小件毛坯连接成为一个较长的大铸件,这种方法称为联合铸造。这次设计的铸件为小铸件,但是也无需联合铸造。2. 2铸造工艺方案的确定铸造工艺方案概括地说明了铸件生产的基本过程和方法,包括造型和造芯方法、铸型类型、浇注位置和分型面等的方案确定。确定合理而先进的铸造工艺方案,对获得优质铸件,简化工艺过程,提高生产率,改善劳动条件,以及降低生产成本等起着决定性的作用。2. 2. 1造型、造芯方法及铸型种类砂型铸造不受零件形状、大小及其复杂程度的限制,原材料来源广,见效快、成本低。(一)造型和造芯方法及其选择选择铸造方法时应该根据铸件的结构特点、合金种类、铸件的生产批量和数量、铸件的尺寸精度及其车间的生产条件等进行。虽然手工造型和造芯所使用的工艺装备简单,灵活多样,适用性强,对小批量或成批量以及形状复杂的铸件有着广泛的用途,但是他的生产率低,铸造出来的铸件不易稳定,所以此次设计采用机器造型和造芯,从而提高效率保证铸造的要求,适用于成批或大批量生产中。在本次设计过程中,造型采用砂型造型,砂型铸造是一种以砂作为主要造型材料,制作铸型的传统铸造工艺。砂型铸造的适应性很广,小件、大件,简单件、复杂件,单件、大批量都可采用。砂型比金属型耐火度更高,但是砂型铸造也有一些不足之处:每个砂质铸型只能浇注一次,获得铸件后铸型即损坏,必须重新造型,所以砂型铸造的生产效率较低;又因为砂的整体性质软而多孔,所以砂型铸造的铸件尺寸精度较低,表面也较粗糙。(二)铸型的选择砂型铸造常用的铸型有干型,表面干燥型,湿型,自硬型和铁模复砂型。其中干型,表面干燥型,自硬型可适用于很多铸件,但一般用于中大型铸件。在本次设计中,结合铸件的尺寸分析,属于中小型铸件,采用的铸型为湿型。其特点为铸型不烘干,优点是成本低,生产率高,劳动条件得到改善易于实现机械化自动化。但是铸型水分多、强度低,易产生呛火、夹砂、气孔、冲砂、粘砂、涨箱等铸造缺陷。主要应用于单件、成批和大量生产的中小件,机械化,自动化的流水线生产中。在一般情况下,中小型铸件应尽可能的选用湿型,因为大批大量机械化的流水线生产中不可能采取干型,所以此次设计采用湿型。2.2.2浇注位置和分型面的确定浇注位置是指浇注时铸件所处的位置,分型面是指两半个铸型相互接触的表面。一般先从保证铸件的质量出发来确定浇注位置,然后从工艺操作方便出发确定分型面。一些质量要求不高或者外形复杂,生产批量又不大,为了简化工艺操作,也可以优先考虑分型面。铸件浇注位置要符合铸件的凝固方式,保证铸型的充填,注意以下几个原则:(1)一般情况下铸件浇注位置的上面比下面缺陷多,所以应将铸件的重要加工面或者主要受力使用面等要求较高的部位放在下面,若有困难则可放在侧面或斜面。(2)浇注位置的选择应有利于铸型的充填和型腔中气体的排除,所以,薄壁铸件应将大的平面放在下面或者侧立、倾斜,以防出现浇不足和冷隔等缺陷。(3)当铸件壁厚不均,需要补缩时,应从顺序凝固的原则出发,将厚大部分放在上面或者侧面,以便于安放冒口和冷铁。对于收缩较小的灰铸铁件,当壁厚差别不大时,也可以将厚部分放在下面靠自身上部的铁水补缩而不用冒口(4)确定浇注位置时应尽量减少砂芯的数量,同时有利于砂芯的定位、稳定、排气和检验方便。因此,较大的砂芯应尽可能使芯头朝下,尽可能避免砂芯吊在上箱或仅靠芯撑来固定。可采用多个铸件共用一个砂芯。根据以上的浇注位置的选择原则,设计的铸件的浇注位置选在铸件的侧面,如工艺图所表示的位置。分型面确立的基本原则是:(1)为了起模方便,分型面一般选在铸件的最大截面处,但是注意不要使模样在一箱内过高。(2)尽量将铸件的重要加工面或大部分加工面和加工基准面放在同一个砂箱内,而且尽可能放在下箱。以保证铸件尺寸的精确,减少铸件的飞边毛刺。(3)为简化操作过程,保证铸件尺寸精度应尽量减少分型面的数目,减少活块的数目。(4)为了便于生产,减少制造工艺装备的费用,分型面应尽量采用平直面。(5)分型面的选择应尽量减少砂芯的数目。(6)分型面的确定尽可能考虑到内浇口的引入位置,并使合箱后与浇注位置一致,以避免盒箱后再翻动铸型。综合上述,在本次设计中,铸件是对称的结构,对称的部分也方便取模,若是在最大截面分型铸件不易取出,将分型面选在对称面处,将整体均分放入上下箱,如工艺图所示。2. 2. 3砂箱中铸件数目的确定当铸件的造型方法、浇注位置和分型面确定后,应当初步确定一箱中放几个铸件,作为进行浇冒口设计的依据。一箱中的铸件数目,应该是在保证铸件质量的前提下越多越好。本铸件在一砂箱中高约97mm,长约202mm,宽约163mm,重约13. 47Kg。这里选用一箱一件,根据本铸件分型面的确定,可以先确定下箱的尺寸。根据铸件重量在11-}-25kg时,查得模型的最小吃砂量a=30mm,h=50mm, c=60mm, d或e=50mm, f=30mm, g=30mm,先确定下箱的尺寸,再根据表格我们可以选择标准的砂箱。选用Z145A顶杆式起模的震实式造型机,砂箱最大内尺寸为500mm X 400mm X 300mm。根据本铸件的大概尺寸,在本次设计中采用一箱一件,因为浇注系统位于上箱,所以上砂箱的高度我们还要考虑到浇注系统才可以确定。2. 3参数的选择工艺铸件的工艺设计,除了根据铸件的特点和具体的生产条件正确地选择铸造方法和确定铸造工艺方案以外,还应该正确地选择合适的工艺参数。2. 3. 1铸造收缩率的确定铸件在冷却和凝固过程中,体积一般都要收缩。由于铸件的固态收缩(线收缩)在使铸件各部分的尺寸小于模样原来的尺寸,为了使铸件冷却后的尺寸与铸件图示尺寸一致,则需要在模样或者芯盒上加上其收缩的尺寸。增加的这部分尺寸为铸件的收缩量,一般用铸造收缩率表示:k=(L模样一L铸件)/L铸件X 100% 式中:L模样—模样尺寸;L 铸件—铸件尺寸铸造收缩率主要和铸造合金的种类及成分有关,同时还取决于铸件在收缩时受到阻碍的大小等因素。在本次工装设计中模样材料为铸铝,铸造收缩率选为1%。而灰铸铁的结晶范围窄,更接近于层状凝固,凝固时的膨胀和液态收缩趋于相互补偿,所以铸造工艺设计时可不考虑灰铸铁的收缩给尺寸带来的影响。2. 3. 2机械加工余量的确定机械加工余量是指在铸件加工表面上留下的、准备用机械加工方法切去的金属层的厚度,目的是获得精确的尺寸和光洁的表面,以符合设计的要求。铸件加工余量的大小,要根据铸件的合金种类,生产方法,尺寸大小和复杂程度,以及加工面的要求和所处的浇注位置等因素来确定。表2-3 二级精度灰铸铁件机械加工余量(mm)查表得,顶面加工余量为5mm,底、侧面为4mm。2. 3. 3拔模斜度的确定为了在造型和制芯时便于起模而不致损坏砂型和砂芯,应该在模样或芯盒的出模方向带有一定的斜度。如果零件本身没有设计出相应的结构斜度时,就要在铸型工艺设计时给出拔模斜度。拔模斜度的大小应根据模样的高度,模样的尺寸和表面光洁度以及造型方法来确定,见表2-4表2-4 拔模斜度金属模测量高度在20- 50mm,a=0.5-1.2mm,α=0°45′-2°;测量高度在x-100mm, a=1.0一1. 5mm,a =0°45′-1°。2. 4砂芯设计砂芯主要用于形成铸件的内腔和孔,影响铸件的质量,铸造工艺过程和铸造工艺装备。一个铸件所需要的砂芯数量,主要取决于铸件的结构和铸造工艺方案。在满足砂芯支撑稳固、定位准确和排气通畅的情况下,芯头的数量越少越好,本铸件决定使用2个砂芯。芯头是砂芯的重要组成部分,其作用一般为定位、支撑和排气。定位主要是通过芯头与芯座的配合,便于将砂芯准确的安放在砂型中;支撑主要是砂芯通过芯头支撑在铸型中,保证砂芯在它本身的重力和金属液的浮力作用下位置不变;排气主要是在浇注凝固过程中,保证砂芯中产生的大量气体能够及时的从芯头排出铸型。一个砂芯的芯头能否满足这三方面的要求,主要是由芯头的形式、个数、形状和尺寸决定的。根据芯头在砂型中的位置,可分为垂直芯头和水平芯头。考虑铸件结构将砂芯设计为两个,砂芯1#和2#配合在一起,砂芯2#为铸件内的水平大砂芯,砂芯1#为悬臂砂芯。表2-5 水平芯头的长度(mm)2#最长两端,芯头长40mm,短端芯头长30mm, 1#为悬臂砂芯,另外查得芯头长30~40mm.在大量的生产中,为了加速下芯合箱及保证铸件质量,在芯头的模样上常常做出压环、防压环和集砂槽。压环用来阻止金属液钻进砂芯的通气道;防压环用来防止芯头压坏芯座的边缘后,散砂落入型肿:集砂槽用于存放散落的砂粒。表2一6 压环、防压环和集砂槽的尺寸(mm)芯头横截面的尺寸,一般决定于铸件相应部位孔眼的尺寸,为了便于下芯合箱,芯头应有一定的斜度,芯头和芯座之间应留一定的间隙。表2-7 芯头斜度经查表得下芯头的斜度为1°30',芯头与芯座的间隙为0. 5mm。本次设计过程中砂芯1#和2#芯头的尺寸较小,作用在芯头上的重力和浮力不大,因此不必验算芯头的尺寸。2. 5浇注系统设计芯头浇注系统是砂芯中引导液态合金流入型腔的通道。生产中常常因浇注系统设计安排不合理,造成砂眼、夹砂、气孔、粘砂、缩孔、缩松、浇不足、变形、裂纹、偏析等缺陷。浇注系统与获得优质铸件,提高生产效率和降低铸件成本的关系是密不可分的。常用的浇注系统大多由浇口杯、直浇道、横浇道、内浇道等部分组成。2. 5. 1浇注系统的类型选择表2-8浇注系统各组元选择浇注系统分为开放式,封闭式,半封闭式,封闭一开放式几种类型,考虑本铸件采用湿型铸造且铸件本身较小的特点,以及浇注系统各组元的断面比关系,内浇道对铸件型腔的引注高度,浇道的结构等,选择封闭式浇注系统,断面F直>F横>F内。浇注开始时液态合金很快充满浇注系统,铸件成品率高,撇渣能力较强,浇注初期也有一定的撇渣能力。2. 5. 2浇注系统断面尺寸的确定(1)水力学近似计算公式:计算浇注系统,主要是确定最小断面积(阻流断面),然后按经验比例确定其他组元的断面积。封闭式浇注系统的最小断面是内浇道,以伯努利方程为基础的水力学近似计算公式是:F内=G/(μ×t×0. 31 √Hp) ( cm2)式中:F内—内浇道总断面积(cm2);G—流经内浇道的液态合金重量(Kg );μ—流量总耗损系数;t—浇注时间(s);Hp—平均静压力头(cm).(2)液态合金重量:灰铸铁的密度为7. 8kg/cm3,算出铸件的质量为12.47kg,加上浇注系统中金属液的损耗,铸件G=12.47kg X (1+20% ) =14.965kg.(3)浇注时间t:G==14.965kg,铸件壁厚在8-15mm,系数S取2. 2 。t=S G=8. 51s(4)流量系数μ:a =0. 5(铸型阻力小)按表修正:有两个内浇道,阻力加大,μ值取0. 05.得μ=0. 5-0. 05=0. 45。确定平均压头Hp:中间注入,p=c/2, c=194cm.由Hp=H0-p2/2c=Ho-c/8, Ho=H M+c/2>Ltan a +c/2其中,L=200mm,铸件壁厚在8 ~15mm,压力角α=9°~10°,取10°,得H0>131mm,取H0=150mm,H0为上砂箱高度。得Hp=12.6cm, H M= 53mm。F内=14.965/(0. 45 X 8. 51X 0. 31 X √12.6) =3. 55cm2。设置两个内浇道,则每个内浇道截面积为1. 78cm2。查表得选择II型内浇道,取F内=1.8cm2。则内浇道总截面积为3.6 cm2截面尺寸:A=16mm, B=12mm, C=13mm由封闭式系统各组元的断面比为:F内: F横: F直=1: 1. 1: 1. 15。则F横=3. 96cm2,查表得选择II型横浇道,取F横=4cm2截面尺寸:A=30mm, B=18mm, R=13mmF直= 4.14cm2,圆形截面,查表可得,直浇道下部最小直径为25mm。查表得,浇口杯尺寸:D1=66mm, D2=62mm, h=50mm.-.(6)核算最小剩余压头HMH M=-上砂箱的高度,直浇道中心到铸件最高最远点距离L=200mm,若压力角α=10°,我们只需要H M大于35.3mm即可,这样进行浇铸,就能得到轮廓清晰的完整铸件。考虑到浇注系统的高度,我们取上箱高度为150mm,即上箱的尺寸为500x400x150mm。2.5.3冒口的设计常见的铸造缺陷如缩孔、缩松、裂纹等都与铸件的凝固和收缩有关,在铸件的厚实部位常设置冒口,并按顺序凝固原则使冒口最后凝固。灰铸铁的结晶范围窄,更接近于层状凝固。凝固时的膨胀和液态收缩趋于相互补偿。故灰铸铁件补缩所需要的铁水的量少,铸型刚度要求较低,一般灰铸铁件可不设置冒口。3铸造的工艺装备设计3. 1模样设计本次设计的是下模样。本设什中来用就是金属模样,选ZL102铸造铝合金,其收缩率为1%模样结构的设计过程如下:1)模样尺寸的确定模样的尺寸=铸件尺寸X (1+K);式中,K为铸件收缩率。计算得模样外尺寸:A=273.1mm, B=256.1mm, H=98.0mm。对于芯头及冒口尺寸按原工艺图计算。因模样壁厚为8mm,查表得模样非工作面圆角半径为3mm。2)模样的壁厚和加强筋模样平均轮尺寸(A+B) /2=(273.1+256.1)/2mm=246.6mm<500mm,查表得,铝合金模样壁厚8mm。模样加强筋取知道分型面上的筋,一般将加强筋的厚度设计为模样壁厚8mm,查表加强筋下端厚度为6mm,铸造圆角为5mm。因模样形状属于非圆形截面,加强筋的布置属II类,根据(A+B) /2在250-500mm, A/B=273.1/256.1=1.1,查得,a=140mm, b=175mm因为a>A/2, b>B/2,则仅在模样长度和宽度中心轴上设有交叉十字形加强筋。模样高度98. 0mm< 100mm,查得筋的斜度取1°30'。3)模样类型的选择本次设计采用机器造型用金属单面模样。4)模样技术要求模样表面光洁度:模样工作表面为▽6,模样分型面为▽4,模样定位销孔为▽6~▽7。模样装配凸耳采用外凸耳。3. 2模底板的设计本次设计的是下模板,单面模板采取的是顶杆式,模底板材料决定为灰铸铁。本次设计选用的Z145A造型机为可调节顶杆式起模的镇压式造型机,顶杆起模行程为150mm。Z145A 造型机砂箱最大内形尺寸为500 X 400mm 。模样外尺寸:A=273.1mm, B=256.1mm,H=98.0mm。根据铸件重量在11~25kg,查得模型的最小吃砂a=30mm,b=50mm,c=60mm,d=50mm,H=98. 0mm。砂箱最大尺寸适合,且其内只能放一个模样,砂箱高度>98.0mm+60mm=158mm.造型选用的砂箱尺寸500 X 400 X 180mm。材料为铸铁。砂箱平均尺寸<500mm,高度<200mm,查表得b=18mm。其配合的模底板尺寸:A0=A+2b=536mm,B0=B+2b=436mm 模底板的材料为铸铁,高度在80~150mm,取90mm,小于顶杆的起模行程。加强筋的距离由模板的平均轮廓尺寸决定,查表为K=300mm,K1=250mm.因模底板尺寸A0= 536mm,B0=436mm,所以在模底板上将加强筋布置成工装图上所示。表3-1 壁厚和加强筋(单位:mm)模底板定位销孔中心距应根据所配用砂箱销套的中心距C来确定,用同一钻模钻出。表3-2(单位:mm )本设计中选用直径20mm的定位销。M的值取75mm,则C=A+2M=600+2 X 75=750mm。模底板与砂箱之间常常用定位销和销套定位,此处只设计定位销。在造型过程中为使砂箱不被卡死常。
铸造工艺说明书
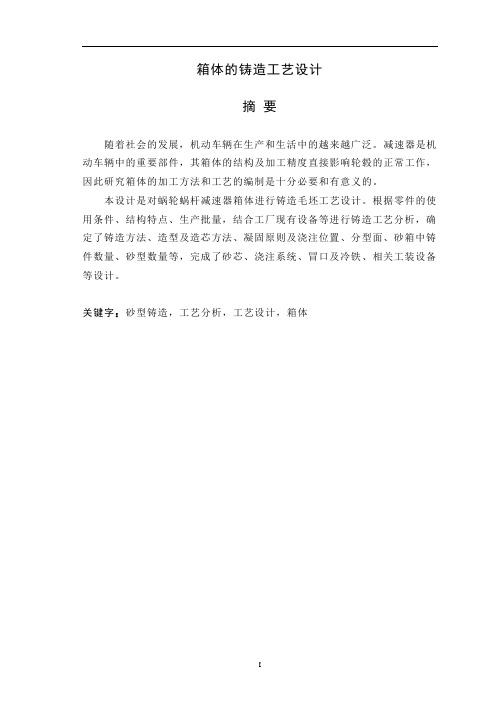
箱体的铸造工艺设计摘要随着社会的发展,机动车辆在生产和生活中的越来越广泛。
减速器是机动车辆中的重要部件,其箱体的结构及加工精度直接影响轮毂的正常工作,因此研究箱体的加工方法和工艺的编制是十分必要和有意义的。
本设计是对蜗轮蜗杆减速器箱体进行铸造毛坯工艺设计。
根据零件的使用条件、结构特点、生产批量,结合工厂现有设备等进行铸造工艺分析,确定了铸造方法、造型及造芯方法、凝固原则及浇注位置、分型面、砂箱中铸件数量、砂型数量等,完成了砂芯、浇注系统、冒口及冷铁、相关工装设备等设计。
关键字:砂型铸造,工艺分析,工艺设计,箱体目录前言................................................................. 错误!未定义书签。
第一章铸造工艺设计.. (4)§1.1 零件概述 (4)§1.1.1 零件信息 (4)§1.1.2 技术要求 (4)§1.2 铸造工艺方案的确定 (5)§1.2.1 造型、造芯方法及铸型种类的确定 (5)§1.2.2 浇注位置和分型面的确定 (5)§1.2.3 砂箱中铸件数目的确定......... 错误!未定义书签。
§1.3工艺参数的选择 (7)§1.3.1 铸造收缩率 (8)§1.3.2 机械加工余量 (8)§1.3.3 拔模斜度的确定 (8)§1.3.4 铸造圆角的确定 (8)§1.3.5 最小铸出口 (8)§1.4 浇注系统的设计 (8)§1.4.1 浇注系统的概述 (8)§1.4.2 浇注系统类型的选择 (9)§1.4.3 浇注系统的设计与计算 (10)§1.4.4 出气孔的设计 (10)§1.5 砂芯的设计 (11)§1.5.1 砂芯的概述 (11)§1.5.2 砂芯数量的确定 (11)§1.5.3 芯头的设计 (11)§1.5.4 壳芯的制备 ............................ 错误!未定义书签。
机体支架铸造树脂砂手工造型作业指导书

树脂砂手工造型作业指导书1 范围本规程适用于采用树脂砂手工造型生产的Q700-2材质类铸件。
2 型(芯)砂制备2.1 原材料准备1、普通湿型用砂:SiO2≥90%,泥份≦2%,粒度75/150、100/200。
2、粘土技术条件:不得结块,受潮。
3、煤粉技术条件:光泽碳析出能力≥7%,挥发份≥30%,无大颗粒,结块现象。
2.2 型砂混制1、配砂前首先检查设备(混砂机)是否正常,润滑是否足够,电器是否安全,出砂门是否开关灵活关闭严密。
2、混砂机碾轮与底盘的间隙10-30毫米,内外刮刀与底盘的间隙<10毫米。
3、检查配所用材料是否全部备齐,是否符合技术要求,并估算所需配砂的用量。
4、加料顺序如下:普通湿型:新砂→旧砂→粘土(煤粉) →水;干混2—3分钟,湿混3—5分钟。
5、先开混砂机后加料,所加混合料不得超过混砂机的额定混砂量。
6、混砂过程中不准用手在机内直接取样。
2.3 型(芯)砂的质量控制:紧实率控制在50%左右,可凭手感检测,用手捏一把型(芯)砂,感到有潮的感觉但不粘手,柔软易变形,捏成砂团放开手后可看到清晰的手纹,掰断时断面不粉碎,有足够的强度。
面砂的有效煤粉含量一般控制在3—8%,小件取下限,大件取上限,以铸件不粘砂,不出现铸件表面发蓝为好。
型砂中的活性粘土的含量一般控制在5—9%,不可过高或过低。
3 手工造型3.1 造型前的准备3.1.1 操作者应了解所生产铸件的工艺要求。
3.1.2 检查模样是否完好,有下列情况者应修复后再用:a) 缺角,变形及尺寸不符合图纸规定。
b) 活块残缺不全。
c) 模样的定位销,孔配合松紧不合适。
3.1.3 需用底板时,检查底板是否平直,大小是否符合要求。
3.1.4 选择的砂箱吃砂量是否符合要求,吃砂量可参照表3.1.4 。
表3.1.4 砂箱吃砂量表(mm)3.1.5 砂箱有下列情况不能使用:a)箱把脱落或有严重变形。
b)箱壁破裂未经修补。
c)砂箱翘曲变形严重。
铸造工艺设计说明书

铸造工艺设计说明书一、铸造工艺设计的目的和意义铸造是将液态金属浇注到与零件形状、尺寸相适应的铸型型腔中,待其冷却凝固,以获得毛坯或零件的生产方法。
铸造工艺设计则是根据零件的结构特点、技术要求、生产批量等因素,确定铸造方法、铸型分型面、浇注系统、冒口和冷铁等工艺参数,以保证获得高质量的铸件,并提高生产效率、降低成本。
良好的铸造工艺设计具有重要意义。
首先,它能够保证铸件的质量,减少铸造缺陷的产生,如气孔、缩孔、夹渣等。
其次,合理的工艺设计可以提高生产效率,降低生产成本,缩短生产周期。
此外,还能为后续的机械加工提供良好的基础,减少加工余量,提高材料利用率。
二、零件分析1、零件结构对需要铸造的零件进行结构分析,包括形状、尺寸、壁厚均匀性等。
例如,形状复杂的零件可能需要采用复杂的分型面和浇注系统;壁厚不均匀的零件容易产生缩孔、缩松等缺陷,需要合理设置冒口和冷铁。
2、技术要求明确零件的技术要求,如材质、力学性能、表面质量等。
不同的材质和性能要求会影响铸造工艺的选择和参数的确定。
3、生产批量生产批量的大小直接影响铸造方法的选择。
大批量生产时,通常采用金属型铸造、压力铸造等高效率的铸造方法;小批量生产则多采用砂型铸造。
三、铸造方法的选择1、砂型铸造砂型铸造是应用最广泛的铸造方法,其优点是成本低、适应性强,可生产各种形状和尺寸的铸件。
但砂型铸造的生产效率较低,铸件的表面质量相对较差。
2、金属型铸造金属型铸造的生产效率高,铸件的精度和表面质量好,但模具成本高,适用于大批量生产形状简单、尺寸较小的铸件。
3、压力铸造压力铸造能生产出形状复杂、薄壁的高精度铸件,但设备投资大,主要用于生产大批量的有色金属铸件。
4、熔模铸造熔模铸造适用于生产形状复杂、精度要求高、难以机械加工的小型零件。
根据零件的结构、技术要求和生产批量,综合考虑选择合适的铸造方法。
四、铸型分型面的选择分型面的选择直接影响铸型的制造、造型操作的难易程度以及铸件的质量。
底板砂型铸造设计及模拟说明书
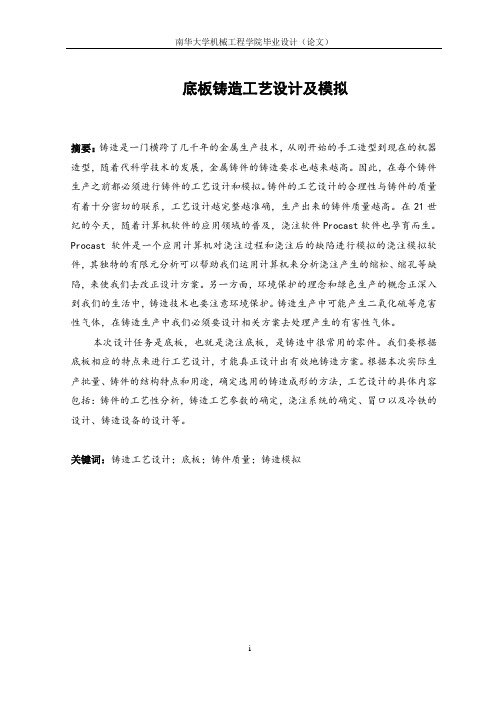
底板铸造工艺设计及模拟摘要:铸造是一门横跨了几千年的金属生产技术,从刚开始的手工造型到现在的机器造型,随着代科学技术的发展,金属铸件的铸造要求也越来越高。
因此,在每个铸件生产之前都必须进行铸件的工艺设计和模拟。
铸件的工艺设计的合理性与铸件的质量有着十分密切的联系,工艺设计越完整越准确,生产出来的铸件质量越高。
在21世纪的今天,随着计算机软件的应用领域的普及,浇注软件Procast软件也孕育而生。
Procast软件是一个应用计算机对浇注过程和浇注后的缺陷进行模拟的浇注模拟软件,其独特的有限元分析可以帮助我们运用计算机来分析浇注产生的缩松、缩孔等缺陷,来使我们去改正设计方案。
另一方面,环境保护的理念和绿色生产的概念正深入到我们的生活中,铸造技术也要注意环境保护。
铸造生产中可能产生二氧化硫等危害性气体,在铸造生产中我们必须要设计相关方案去处理产生的有害性气体。
本次设计任务是底板,也就是浇注底板,是铸造中很常用的零件。
我们要根据底板相应的特点来进行工艺设计,才能真正设计出有效地铸造方案。
根据本次实际生产批量、铸件的结构特点和用途,确定选用的铸造成形的方法,工艺设计的具体内容包括:铸件的工艺性分析,铸造工艺参数的确定,浇注系统的确定、冒口以及冷铁的设计、铸造设备的设计等。
关键词:铸造工艺设计;底板;铸件质量;铸造模拟Slab casting process design and simulationAbstract:Casting is a spanning thousands of years of metal production technology, from the beginning of the manual to the machine model, with the development of the generation of science and technology, metal casting foundry is becoming more and more demanding. Therefore, before each casting production must be casting process design and simulation. The rationality of the design of casting process has a very close relation with the quality of the casting, the process design more complete more accurately, to produce the higher the casting quality. In the 21st century, with the popularity of the application field of computer software, pouring software Procast software can also breed. Procast software is an application of computer to casting process and casting defects after the simulation of casting simulation software, the finite element analysis of its unique use computer can help us to analyze the casting defects such as shrinkage, shrinkage cavity, to make us to correct design.The design task is the base plate, also is the bottom board, is very commonly used in casting parts. We will according to the characteristics of the floor corresponding to technological design, can design the casting solution effectively. According to the actual production batch, casting structural characteristics and USES, and the selection of the casting, the method of process design of the concrete content includes: the casting technology of analysis, the determination of casting technological parameters, the determination of pouring system, riser and chill design, the design of the casting equipment, etc.Key word:casting proess design;slab;casting quality;casting simulation目录1概述 (1)2 零件铸造工艺方法 (2)2.1设计任务及要求……………….................................................................... ..22.2造型造芯方法的选择 (3)2.3浇注位置和分型面的确定 (3)3铸造工艺参数设计 (6)3.1铸件的尺寸公差 (6)3.2机械加工余量 (7)3.3铸造收缩率 (8)3.4起模斜度 (8)3.5最小铸出孔和槽 (9)3.6工艺正补量 (9)3.7 分型负数 (10)3.8反变形量 (10)3.9 浇注温度 (11)4 浇注系统的设计 (12)4.1浇注系统的基本要求 (12)4.2浇注系统的基本类型 (12)4.3浇注系统的基本组元 (13)4.4 浇注系统的尺寸设计 (15)5铸造工艺设备设计 (18)5.1模样设计 (18)5.2模板选择 (18)5.3砂箱及附件的选择 (21)6 ProCAST软件模拟 (22)6.1 ProCAST软件模拟操作 (22)6.2 温度场分布 (27)7 铸件缺陷分析与解决方案 (29)7.1 ProCAST缺陷模拟结果 (28)7.2缺陷产生的原因及处理方法 (28)参考文献 (31)谢辞 (33)1概述我国古代的铸造技术一直在世界先进行列,但是由于几千年的封建社会制度严重影响了科学技术的发展,也导致了铸造技术的停滞不前。
- 1、下载文档前请自行甄别文档内容的完整性,平台不提供额外的编辑、内容补充、找答案等附加服务。
- 2、"仅部分预览"的文档,不可在线预览部分如存在完整性等问题,可反馈申请退款(可完整预览的文档不适用该条件!)。
- 3、如文档侵犯您的权益,请联系客服反馈,我们会尽快为您处理(人工客服工作时间:9:00-18:30)。
N o.1目录第一部分铸造工艺的设计及方案的确定 (1)一铸件结构的铸造工艺性二铸造工艺方案的确定三工艺参数的选择四铸造工艺图设计第二部分模样图设计 (5)一金属模样材料的选择二金属模样尺寸的确定三金属模样结构的设计第三部分模板装配图 (6)一模底板本体机构设计二模样在模地板上的装配第四部分芯盒图设计 (9)第五部分铸造工艺卡 (11)第六部分参考资料 (12)N o.2第一部分铸造工艺的设计及方案的确定一铸件结构的铸造工艺性生产铸件,不仅需要采用先进的合理的铸造工艺和设备,而且还要使零件结构本身符合铸造的生产要求。
铸造结构是否合理,和铸造合金的种类,产量的多少,铸造方法和生产条件等有密切关系。
1、铸件质量对零件结构的要求1 )铸件的壁厚应合理每一种铸造合金的铸件,都有其合适的壁厚范围,如果是选择适当,既能保证逐渐的机械性能要求,又方便铸造生产还可以简便地消除许多缺陷。
2)铸造斜度在铸件壁的内外侧面顺着拔模的方向应该带有斜度,以便起模和简化铸造工艺。
3)保证铸件质量的合理结构2、铸造合金对零件结构的要求1)合金种类:灰铸铁件2)性能特点:流动性好,体收缩和线收缩小,缺口敏感性小。
综合机械性能低,抗压强度抗拉强度高约3~4倍。
吸震性好,比钢约大10倍。
弹性模数较低。
3)结构特点:因流动性好,可铸壁较薄,形状复杂的铸件。
铸件残余应力小,吸震性好。
二铸造工艺方案的确定铸造工艺方案概括地说明了铸造生产的基本过程和方法。
确定合理而先进的铸造工艺方案,对获得优质铸件,简化工艺过程,提高生产率,改善劳动条件,以及降低生产成本等起着决定性的作用。
1、造型、造芯方法及铸型种类1)造型方法:砂箱造型。
主要特点是在砂箱内造型,操作方便,劳动量较小。
应用于大、中、小铸件,大量成批和单件上产。
2)造芯方法:芯盒造芯。
主要特点是用芯盒内表面形成砂芯的形状,砂芯尺寸准确,可制造小而复杂的砂芯。
应用于各种形状、尺寸和批量的砂芯。
3)铸型的种类及选择采用铸型湿型。
主要特点是铸型不烘干。
成本低、生产率高、易实现机械自动化。
但铸型水分多、强度低,有夹砂、粘砂等铸造缺陷。
应用于成批和大量生产的中小件,机械化,自动化的流水线生产中。
2、浇注位置和分型面的确定在保证铸件的质量的前提下来确定浇注位置,然后从工艺操作N o.31) 浇注位置的确定原则A 铸件的重要部分应尽量置于下部B 重要加工面应朝下或呈直立状态C 使铸件大平面朝下,避免夹砂结疤类缺陷D 应保证铸件能充满E 应有利于铸件的补缩F 避免用吊砂、吊芯或悬臂式砂芯,便于下芯、合箱及检验G 应使合箱位置、浇注位置和铸件冷却位置相一致2) 分型面的选择分型面一般在确定浇注位置后在选择。
但分析各种分型面方案优劣之后,可能需重新调整浇注位置。
有时浇注位置和分型面可同时确定。
选择分型面应注意以下原则: A 应使铸件全部或大部置于同一半型内 B 尽量减少分型面数量 C 分型面尽量选用平面D 便于下芯、合箱和检查型腔尺寸E 不使砂箱过高F 受力件的分型面的选择不应削弱铸件结构强度G 注意减轻铸件清理和机械加工量三 工艺参数的选择1、铸造收缩率100%M JJL L K L -=⨯ 式中 M L →模样(或芯盒)工作面的尺寸; J L →铸件尺寸。
灰铸铁 中小型铸件自由收缩率取1%。
2、起模斜度为了方便起模,在模样、芯盒的出模方向留有一定的斜度以免损坏砂型或砂芯。
起模斜度为1°。
砂芯设计3、对砂芯的要求:A 形状尺寸及其在砂型中的位置符合铸件的要求。
B 具有足够的强度和刚度。
C 在铸件的浇注凝固过程中,砂芯中产生的气体能够及时地排出铸型。
D 铸件收缩时,砂芯的阻力要小。
E 清砂容易。
N o.4铸件的浇注系统由浇口杯、直浇道、直浇道窝、横浇道和内浇道等部分组成。
1)浇注系统类型及选择 采用封闭式浇注系统:封闭式浇注系统的阻渣能力好,可防止金属液卷入气体,消耗金属少,清理方便。
不足是易产生喷溅和冲砂使金属氧化,因此采用不易氧化的铸铁件。
按内浇道在铸件上的位置分类:采用中间注入式浇注系统。
2)计算阻流截面积奥赞公式S =阻式中 m →流经阻流的金属总质量kg ;τ→ 充填型腔的总时间s ;ρ→充填全部型腔时,浇注系统阻流截面的流量系数;p H →充填型腔时的平均计算压力头cm 。
可取支撑架的工艺出品率约为70%,可估计铸型中铁水总重量mm=2.96×4/70%=16.92Kg初步计算浇注时间t=S L G 其中 S=2.2 G=16.92Kgt=2.2×92.16=9s由砂型铸造工艺及工装设计手册,P24表5-5,取得6.0=μ 6.0=ρkg N g /10=取,H 0=50mm P=24mm C=48mmC P H H P /20-=N o.5式中 0H →阻流以上金属液的总压头;C →铸件高度。
→P 上箱铸件的高度将以上数据带入S 阻=4.822cm即设置八个内浇道,则每个内浇道截面积为S∑内=4.82/6=0.602cm故取A=11mm B=9mm C=6mm3) 直浇道的位置和高度t M H L g α≥式中 M H →最小剩余压力头;L →直浇道中心到铸件最高最远的水平投影距离; α→压力角010;150=≈αL 所以M H ≥40mm4 ) 确定浇口比并计算各组元截面积封闭式 浇口比1:1.1:1.15 根据浇口比S∑横=5.302cm故取A=24mm B=18mm C=20mm由于设计成一箱四件S∑直=3.542cm故取D=26mm L=150mmN o.61)浇注系统用红色笔画 2)分型面用红色笔画 3)芯子用蓝色笔画浇注系统示意图第二部分 模样图设计一 金属模样材料的选择金属模样所用材料有铝合金、铸铁、铜合金等。
铸铁较坚固,强度高,耐磨性好,加工性能好,而且成本低,但重量较大,易生锈。
三 金属模样结构的设计金属模样示意图N o.7由于机械加工用的是普通尺,因此凡是形成铸件的模样尺寸,一律要根据铸件尺寸依铸造收缩率进行放大。
金属模样尺寸有工艺尺寸确定。
1、模样本体结构第三部分 模板装配图模板也称型板,是由模底板和模样、浇冒口系统及定位销等装配而成,模板主要的作用是在铸型中形成铸件外轮廓及芯头等部分的型腔和分型面。
采用模板造型不仅可以简化 工序,而且铸件尺寸精确。
设计模板的主要依据:已经确定的铸造工艺图;选用造型机(Z148B );一箱中铸件的数目以及模板本身加工制造的可能性。
一 模底板本体机构设计 1、模底板本体结构设计1) 模底板材料:铸铁HT15 2) 模底板平面尺寸的确定模底板的平面尺寸根据所选用的造型机和已定的砂箱内尺寸确定。
Z2410造型机规定砂箱最大内尺寸(长⨯宽⨯高):1000800400cm ⨯⨯002;2A A b B B b =+=+ A 和B 是砂箱内框尺寸;b 是分型面上砂箱两边缘的宽度。
A=700mm ; B=450mm ; b=25mm .02A A b =+=700+2⨯25=750mm ; 02B B b =+=450+2⨯25=500mm 下砂箱高度=150mm .N o.82、模底板高度的确定普通平面模底板高度H=100mm.3、模底板定位销孔中心距C=A+2M=700+2 70=840mm。
模板装配图示意图N o.9下砂箱示意图4、模底板的壁厚和加强图1 模底板厚和加强筋尺寸图示5、模底板和砂箱的定位1) 模底板用定位销及导向销结构尺寸图2 模底板用定位销N o.10图3 模底板用导向销3)导销套及定位销套手册P265,图示结构尺寸选取得:图4 定位销套4)箱耳结构尺寸图5 箱耳尺寸结构6、模底板的搬运结构1)吊轴结构尺寸N o.11图7 吊轴结构尺寸2)地板紧固耳尺寸手册P269,表10-9选取得:图 8 模底板紧固耳尺寸7、浇冒口模在模底板上的固定装配直浇口固装用滑动销钉N o.12图9 滑动销钉第四部分芯盒图设计1、芯盒装配图示按手册P405,图示结构设计画图。
2、芯盒主要零件尺寸的选择设计1)固定板尺寸:H取10mm2)盖板尺寸: H取10mm3)顶芯杆尺寸:图10 顶芯杆尺寸4)回位导杆结构尺寸图11 回位导杆尺寸N o.13热芯盒示意图N o.14第六部分参考资料[1]《砂型铸造工艺及工装设计》联合编写组,《砂型铸造工艺及工装设计》,北京出版社出版,1980[2]王君卿,《铸造手册》,机械工业出版社,2003[3]王文清,李魁盛,《铸造工艺学》,机械出版社,2002。