跳料屑产生的原因
模具常见问题及解决方法

本次培训到此结束,谢谢!
8、产品不容易脱出ห้องสมุดไป่ตู้
通常在对部品进行排料时就应考虑部品的出料问题。一般情况下,我们采用以下几 种出料方式: ⑴:风吹出; 对于一些较小的产品,利用吹气销将其吹出。 ⑵:在重心作用下,产品自然滑落; 在下模铣一出料缺口,利用部品的自身重力滑落。 ⑶:零件推零件; 借助条料的传送力,将冲压完成后的部品推出模具。此时应注意模具的升料高度。 ⑷:零件由条料带出; 此方式一般运用在模具在最后工步对部品的外形进行整体落料的情况下采用,通过大力 弹簧将部品重新压入到条料中,在条料送出的同时将部品一同带出。 ⑸:零件整体落料; 在考虑运用此方式之前必须确认部品的毛刺方向是否允许? 为了避免部品粘附在卸料板或凹模板表面,通常会在最后工位的卸料板或凹模板上使用 小顶杆。
80
t
5° ~10°
°~
85
°
第 一 次 弯 曲
第 二 次 弯 曲
R
回弹抵消
回弹抵消
二次弯曲加工
7、模具容易磨损
影响因素:⑴:模具材料的选用; ⑵:模具润滑不够; ⑶:模具材质热处理不良; ⑷:模具间隙太小; 解决对策:⑴:选用合理优质的模具材料; ⑵:合理的润滑; ⑶:模具材料施以表面处理;(如镀钛) ⑷:选择合理的间隙;
5、冲头容易断裂
影响因素:⑴:由于模具间隙不均匀,冲头受到横向负荷而折断; ⑵:模具间隙小使冲头在脱料时受到横向负荷而折断; ⑶:冲头因导引不良使得冲头在冲切时有偏移现象; ⑷:冲头刃部长度过长; ⑸:冲头阶段部发生应力集中; ⑹:冲头所选用的材料; ⑺:冲屑堵塞造成冲头负荷增大; ⑻:卸料板因受到侧压而倾斜; 解决对策: ⑴:模具间隙要均匀; ⑵:模具间隙取大; ⑶:正确的冲头导引; ⑷:冲头刃部长度减短; ⑸:冲头阶段部施以R角; ⑹:使用高韧性的冲头材料; ⑺:凹模直段部取短及下模有确实的逃孔设计; ⑻:防止卸料板发生倾斜;
高速级进模跳屑问题的探讨与解决对策
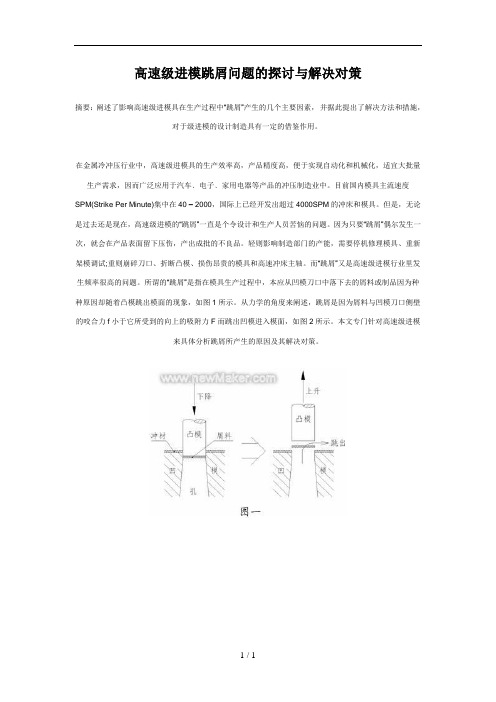
高速级进模跳屑问题的探讨与解决对策摘要:阐述了影响高速级进模具在生产过程中“跳屑”产生的几个主要因素,并据此提出了解决方法和措施,对于级进模的设计制造具有一定的借鉴作用。
在金属冷冲压行业中,高速级进模具的生产效率高,产品精度高,便于实现自动化和机械化,适宜大批量生产需求,因而广泛应用于汽车﹑电子﹑家用电器等产品的冲压制造业中。
目前国内模具主流速度SPM(Strike Per Minute)集中在40 – 2000,国际上已经开发出超过4000SPM的冲床和模具。
但是,无论是过去还是现在,高速级进模的“跳屑”一直是个令设计和生产人员苦恼的问题。
因为只要“跳屑”偶尔发生一次,就会在产品表面留下压伤,产出成批的不良品。
轻则影响制造部门的产能,需要停机修理模具、重新架模调试;重则崩碎刀口、折断凸模、损伤昂贵的模具和高速冲床主轴。
而“跳屑”又是高速级进模行业里发生频率很高的问题。
所谓的“跳屑”是指在模具生产过程中,本应从凹模刀口中落下去的屑料或制品因为种种原因却随着凸模跳出模面的现象,如图1所示。
从力学的角度来阐述,跳屑是因为屑料与凹模刀口侧壁的咬合力f小于它所受到的向上的吸附力F而跳出凹模进入模面,如图2所示。
本文专门针对高速级进模来具体分析跳屑所产生的原因及其解决对策。
1 高速级进模跳屑原因的分析前文中已经提到跳屑产生的两个力学因素,下面就从这两个方面来阐述。
(1)屑料向上的吸附力过大导致屑料跳出,包括以下几个部分。
1)屑料受凸模的真空吸附的作用。
在冲切加工时,凸模切下的材料,因受到弯矩的作用,中心部位发生弯曲,四周却与凸模紧密压着,如图3示:屑料下方受到一个大气压向上的力,上方与凸模之间是真空负压,从而产生一个压力差吸附在凸模上。
随着模具的开启,而跳出模面。
另外在高速冲切生产中,为了给模具散热以及润滑凸凹模,我们往往会在材料送入模具前,给它涂上切削油,这会产生类似吸附剂的作用。
如果切削油的挥发性差、黏度高、加的量过大,屑料与凸模的真空吸附现象会更加明显。
钣金加工厂的模具跳废料解决方法
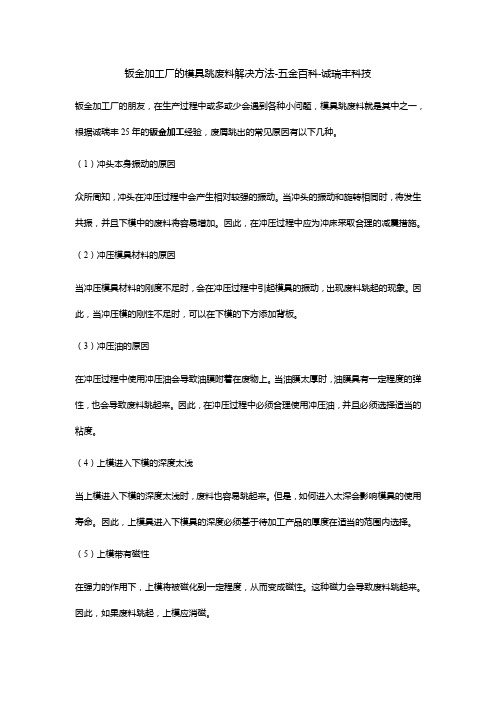
钣金加工厂的模具跳废料解决方法-五金百科-诚瑞丰科技钣金加工厂的朋友,在生产过程中或多或少会遇到各种小问题,模具跳废料就是其中之一,根据诚瑞丰25年的钣金加工经验,废屑跳出的常见原因有以下几种。
(1)冲头本身振动的原因众所周知,冲头在冲压过程中会产生相对较强的振动。
当冲头的振动和旋转相同时,将发生共振,并且下模中的废料将容易增加。
因此,在冲压过程中应为冲床采取合理的减震措施。
(2)冲压模具材料的原因当冲压模具材料的刚度不足时,会在冲压过程中引起模具的振动,出现废料跳起的现象。
因此,当冲压模的刚性不足时,可以在下模的下方添加背板。
(3)冲压油的原因在冲压过程中使用冲压油会导致油膜附着在废物上。
当油膜太厚时,油膜具有一定程度的弹性,也会导致废料跳起来。
因此,在冲压过程中必须合理使用冲压油,并且必须选择适当的粘度。
(4)上模进入下模的深度太浅当上模进入下模的深度太浅时,废料也容易跳起来。
但是,如何进入太深会影响模具的使用寿命。
因此,上模具进入下模具的深度必须基于待加工产品的厚度在适当的范围内选择。
(5)上模带有磁性在强力的作用下,上模将被磁化到一定程度,从而变成磁性。
这种磁力会导致废料跳起来。
因此,如果废料跳起,上模应消磁。
(6)模具间隙的不对称当上模具和下模具对准时,间隙是不对称的,这使得在冲压过程中废料周围的横截面不一致,从而导致在整个废料上的力不均匀并且使废料跳上。
因此,设置切刀时,打孔间隙要对称。
(7)刀口出现磨损在冲压过程中,刀刃被磨损,模具刀刃产生倒锥,这也将导致废料跳起。
因此,在模具磨损时,刀刃应及时变尖。
(8)钣金加工厂的模具设计问题在模具设计的开始,考虑还不够全面,导致模具设计不合理。
高速冲压中防止废料回升的几个解决方法

冲
模 技 术
・
以P G 方式加工 , 凹模刃 口为分体式 的 , 才能实现 上述结构 , 图3 a 中H值一般为 凸模切人深度 的 7 0 %,
件
且适合 于 冲裁 间隙< O . O l m m; 图3 b 适合 于冲裁间 隙>
0. O1 5mm 。
3 . 3 外形 简单 光滑 的 凸模 刃 口设 计 ( p r o i f l e d i e
表1 给 出了沟槽角度与宽度 的推荐值 ( 凹模镶件
厚度为 6 . 5 am时 , r D i e i n s e r t t h i c k n e s s = 6 . 5 m m) 。
料 厚
“
x3
4
表 1 沟槽 角度 与宽度的推荐值
角度参考 值( 凹模 厚度= 6 . 5 0 0 )
n= = = ¨U №
板厚 … t ’ x 3
压 入 部“ ” O . 2 O - 2 0 - 2 O - 3 0 . 4 0 _ 4 O . 5 0 . 5 O . 5 0 . 5 0 . 6 O . 6 O . 6 O . 6
图 6 冲 裁 外 形 的 凸 凹 模 参 数
・
冲
模 技
术
・
就 占据 了他 们 6 0 %以上 的修 模 时间 , 通常处 理跳 废 料 的方 法有 凸模 加 气 孔 , 漏料 孔 加装 吸尘 器 , 凸模 的平 刃 口改 为斜 刃 口或锥形 刃 口, 凹模刃 口钓鱼 法 等等 , 这 些 都是 冲 压工 厂 处理 跳 屑 常用 方法 , 不 再 赘述 , 在 此本 文将 主要介 绍几种 基 于 凹模 刃 口不 同
. 1 5 m m; 当板 厚 > 0 . 5 mm, R = 0 . 3 5 mm。 ( 2 ) 冲裁外形的加工方式为光学 曲线磨 ( P G ) , 如 0 ( 3 ) 沟槽 深 度 : 一般的 , 其 值 等 于 冲 切 间 隙 图5 所示 。 ( c u t t i n g c l e a r a n c e ) 或取 板 厚 的 5 %。
跳屑原因及对策

Page: 9
E. 刀口的内宽加工成比废料的长度小0.02-0.04mm, 使废料 承弯曲状卡在刀里面,防止跳料.(如图八)
Page: 10
2. 因冲头长度不够而长生跳料:
把握一个原则:按图纸的要求. 但对于冲头与废料接触面积 太大所造成的跳料,可改变冲头形状。(如图九) 以减少接 触面积。
A
B
沖 頭 GAP=T(4~6)%
Page: 4
B模具很顺畅的情况下,由于废料与刀口的内面摩擦次数 多,而把刀口的内面磨损,造成刀口间隙过大. (如图三)
2.冲头的长度太短及冲头与落料接触面太大.
Page: 5
3.刀口的松动.
(如图四)
模板
刀口
模板
间隙
间隙
4.端子油加得太多或端子油黏度太大.
Page: 6
A.设计时把刀口的间隙放在下限上.即GAP=(4%~6%)T. B.把刀口的上端设计为2~3mm的直刀位, 下部加工成斜度 (0.5°-1.0°),增强刀口的耐磨度. (如图五) 直刀位
Page:8
C.把刀口由整体式设计为分体式. (如图六)
A
A
B
D.把刀口的厚度设计为2~3mm,便于废料及时脱落,减少 跳料机会. (如图七)
2.凸模加工斜度角。A或B,C使废料形变或减少与凸模的接触面积,针对1,2,5.
3.凸模加弹钉销。将废料始终按压在凹模腔内,对所有原因造成跳废料皆有效。
4. 安装吸废料机。
page 15
0.002~0.005MM
Page: 13
6. 对于新换过的刀口和研磨过的刀口产生跳料 对策为:
A.在刀口的棱角处用铜片来回刮.
B.用红宝石抛刀口棱角处.
影响冷冲压模具跳屑因素分析
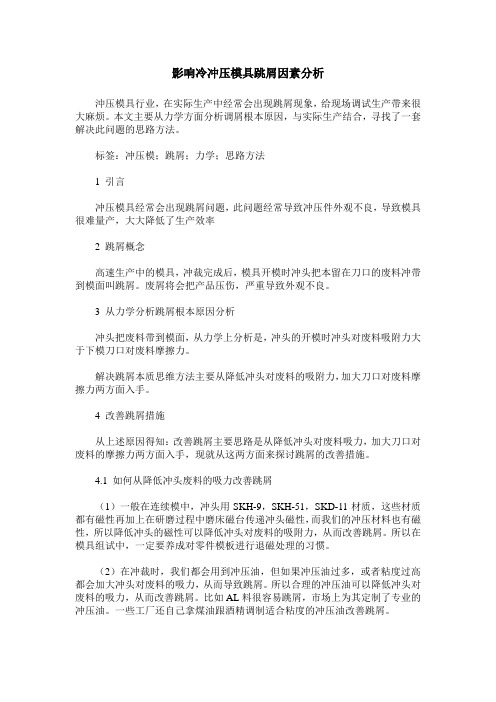
影响冷冲压模具跳屑因素分析沖压模具行业,在实际生产中经常会出现跳屑现象,给现场调试生产带来很大麻烦。
本文主要从力学方面分析调屑根本原因,与实际生产结合,寻找了一套解决此问题的思路方法。
标签:冲压模;跳屑;力学;思路方法1 引言冲压模具经常会出现跳屑问题,此问题经常导致冲压件外观不良,导致模具很难量产,大大降低了生产效率2 跳屑概念高速生产中的模具,冲裁完成后,模具开模时冲头把本留在刀口的废料冲带到模面叫跳屑。
废屑将会把产品压伤,严重导致外观不良。
3 从力学分析跳屑根本原因分析冲头把废料带到模面,从力学上分析是,冲头的开模时冲头对废料吸附力大于下模刀口对废料摩擦力。
解决跳屑本质思维方法主要从降低冲头对废料的吸附力,加大刀口对废料摩擦力两方面入手。
4 改善跳屑措施从上述原因得知:改善跳屑主要思路是从降低冲头对废料吸力,加大刀口对废料的摩擦力两方面入手,现就从这两方面来探讨跳屑的改善措施。
4.1 如何从降低冲头废料的吸力改善跳屑(1)一般在连续模中,冲头用SKH-9,SKH-51,SKD-11材质,这些材质都有磁性再加上在研磨过程中磨床磁台传递冲头磁性,而我们的冲压材料也有磁性,所以降低冲头的磁性可以降低冲头对废料的吸附力,从而改善跳屑。
所以在模具组试中,一定要养成对零件模板进行退磁处理的习惯。
(2)在冲裁时,我们都会用到冲压油,但如果冲压油过多,或者粘度过高都会加大冲头对废料的吸力,从而导致跳屑。
所以合理的冲压油可以降低冲头对废料的吸力,从而改善跳屑。
比如AL料很容易跳屑,市场上为其定制了专业的冲压油。
一些工厂还自己拿煤油跟酒精调制适合粘度的冲压油改善跳屑。
(3)适当的加长冲头长度,冲头里加顶针(顶针只适用于厚料),加大冲头上升过程中的阻力从而降低冲头对废料的吸力。
(4)废料与废料和刀口之间形成密闭空间,相当真空,而冲头上升过程中,冲头吸力破坏这种真空,产生负压,使冲头的吸力大于刀口对废料的摩擦力(相当注射器原理一样),要减少这种吸力,须先破坏这种废料与废料及刀口真空。
冲孔跳废料的解决方案

冲孔跳废料的解决方案1. 方案目标冲孔跳废料是制造业中常见的废料问题之一。
解决这个问题的目标是降低废料产生量,提高生产效率,减少成本,并且对环境友好。
2. 实施步骤2.1 分析冲孔跳废料产生原因首先,需要对冲孔跳废料产生的原因进行分析。
可能的原因包括: - 设计问题:产品设计不合理,导致冲孔跳废料的产生。
- 工艺问题:制造过程中的冲孔工艺不合理,导致冲孔跳废料的产生。
- 材料问题:使用的材料质量不佳,容易产生冲孔跳废料。
2.2 优化产品设计根据冲孔跳废料产生的原因,可以通过优化产品设计来减少废料的产生。
具体步骤如下: - 与设计团队合作,分析产品设计中存在的问题。
- 优化产品设计,减少冲孔跳废料的产生。
- 使用先进的设计软件和工具,模拟冲孔过程,以预测和避免冲孔跳废料的产生。
2.3 优化冲孔工艺除了产品设计,冲孔工艺也是冲孔跳废料产生的重要原因之一。
优化冲孔工艺可以减少废料的产生。
具体步骤如下: - 分析当前的冲孔工艺,找出存在的问题。
- 优化冲孔工艺,采用合适的冲孔参数和工艺流程。
- 使用先进的冲孔设备和工具,提高冲孔的精度和效率。
2.4 优化材料选择材料的选择对废料产生有重要影响。
选择合适的材料可以减少冲孔跳废料的产生。
具体步骤如下: - 与供应商合作,了解不同材料的特性和适用范围。
- 选择质量较好的材料,避免杂质和缺陷。
- 针对不同的产品和工艺要求,选择适合的材料。
2.5 建立废料回收系统即使经过优化,仍然难以完全消除冲孔跳废料的产生。
建立废料回收系统可以有效减少废料的浪费,并且对环境友好。
具体步骤如下: - 设计并建立废料收集设备和系统,将产生的废料进行收集和分类。
- 开发废料处理方法,例如回收、再利用、再加工等。
- 与废料处理公司合作,确保废料得到妥善处理,符合环保标准。
2.6 培训和监督为了确保方案的可行性和效率,培训和监督是必不可少的。
具体步骤如下: - 为相关员工提供培训,使其了解冲孔跳废料问题和解决方案。
冲孔跳废料原因
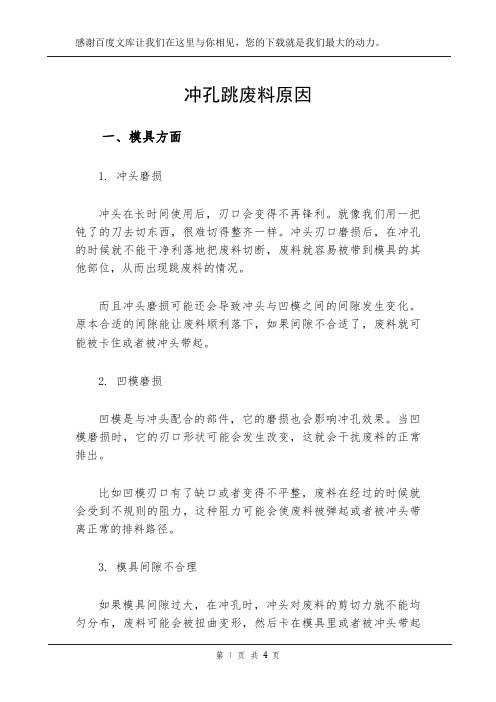
冲孔跳废料原因一、模具方面1. 冲头磨损冲头在长时间使用后,刃口会变得不再锋利。
就像我们用一把钝了的刀去切东西,很难切得整齐一样。
冲头刃口磨损后,在冲孔的时候就不能干净利落地把废料切断,废料就容易被带到模具的其他部位,从而出现跳废料的情况。
而且冲头磨损可能还会导致冲头与凹模之间的间隙发生变化。
原本合适的间隙能让废料顺利落下,如果间隙不合适了,废料就可能被卡住或者被冲头带起。
2. 凹模磨损凹模是与冲头配合的部件,它的磨损也会影响冲孔效果。
当凹模磨损时,它的刃口形状可能会发生改变,这就会干扰废料的正常排出。
比如凹模刃口有了缺口或者变得不平整,废料在经过的时候就会受到不规则的阻力,这种阻力可能会使废料被弹起或者被冲头带离正常的排料路径。
3. 模具间隙不合理如果模具间隙过大,在冲孔时,冲头对废料的剪切力就不能均匀分布,废料可能会被扭曲变形,然后卡在模具里或者被冲头带起来。
这就好比我们用剪刀剪东西,剪刀刃口太宽,剪出来的东西边缘就不整齐,还容易卡在剪刀里。
要是模具间隙过小呢,冲头和凹模之间的摩擦力就会增大,废料在这个狭小的空间里很难顺利落下,很可能被冲头强行带出,造成跳废料现象。
二、材料方面1. 材料硬度当被冲孔的材料硬度较高时,冲头在冲孔时就需要更大的力量。
如果冲床的压力不足,就可能无法将废料彻底切断,废料就会粘连在冲头上或者凹模里,最后被带出来成为跳废料。
比如说我们在冲一块很厚很坚硬的钢板时,就像要在一块大石头上打孔一样,如果力量不够,石头屑就会到处飞溅,废料也是这个道理。
2. 材料的韧性材料韧性好的话,在冲孔过程中,废料不容易被剪断,而是会被拉伸变形。
这种拉伸变形后的废料很容易缠绕在冲头上或者被带到模具的其他部位。
就像我们拉一根很有韧性的橡皮筋,很难一下子拉断,它会被拉得很长很细,废料在模具里也是这样被拉变形后到处跑。
三、冲床方面1. 冲床的精度冲床的精度不够时,冲头在上下运动过程中就会产生晃动或者偏移。
跳屑原因及对策精品PPT课件
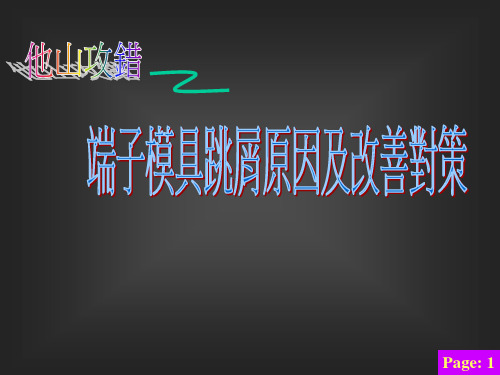
Page: 1
跳屑的定義 跳屑產生的原因 解決跳屑的對策
Page: 2
高速生產中的模具,下料剪切完成 后,本應留在刀口里面的料片卻跳出
落到模面上的現象,稱之為跳屑.A.設計段確定刀口間隙不當.(合理間隙為材料厚度 的4%~6%),即GAP=(4%~6%)t. (如圖二)
跳屑機會. (如圖七)
Page: 9
E.刀口的內寬加工成比料片的長度小0.02-0.04mm, 使料片
呈彎曲狀卡在刀口里面, 防止跳屑.( 如圖八)
Page: 10
2.因沖頭長度不夠而產生跳屑:
把握一個原則:按圖面要求. 但 對於沖頭與料片接觸面積
太大所造成的跳屑, 可改變沖頭形狀. (如圖九) 以減少接
沖 頭
GAP=T(4~6)%
Page: 4
B.模具很順暢的情況下,由於料片與刀口的內面來回 摩擦次數多,而把刀口的內面磨損,造成刀口的間隙大.
(如圖三)
2.沖頭的長度太短及沖頭與料片接觸面太大.
Page: 5
3.刀口的松動. (如圖四)
模板
刀口
模板
間隙
間隙
4.沖切油加得太多或沖切油粘度太大.
Page: 6
5.料片的形狀及重量. 一般料片的形狀越簡單(如圓形,
方形 ),就越容易產生跳屑; 重量越輕,也就越容易產生跳屑.
6.材料機械性能的影響. 若材料鋼度好,硬度好,就越
容易產生跳屑.
7.新刀口或剛研磨過的刀口容易產生跳屑.
8.沖頭帶磁性,對料片產生吸力而產生跳屑.
Page: 7
1.由於刀口間隙大而產生跳屑的五種類型:
置互相錯開0.002~0.005mm. ( 如圖十一)
裁切模跳废料的解决方法

裁切模跳废料的解决方法全文共四篇示例,供读者参考第一篇示例:裁切模是一种常用于生产工业制品的模具设备,它能够将原材料按照设计要求裁切成所需尺寸和形状。
裁切模在使用过程中难免会产生一些废料,这些废料如果不得当处理可能会给生产过程和环境带来一定影响。
有效解决裁切模产生的废料问题,是提高生产效率和保护环境的关键之一。
一、裁切模产生废料的原因1. 设计不合理:裁切模的设计不合理,导致裁切后产生大量废料无法利用。
2. 材料选择不当:原材料质量差或者材料种类不合适,导致裁切模裁切效果不佳,产生大量废料。
3. 模具磨损:长时间使用或操作不当会导致裁切模的磨损,影响裁切效果,增加废料产生。
4. 人为因素:操作人员技术不过硬或者操作不规范,也会导致裁切模产生大量废料。
二、裁切模废料的解决方法1. 优化设计:通过优化裁切模的设计,减少废料产生。
合理设计模具结构,减少裁切余料,提高利用率。
2. 选择优质材料:选用质量好的原材料,减少裁切损耗,降低废料率。
3. 定期维护:定期对裁切模进行维护保养,保持模具表面的平整度和尺寸精度,减少因磨损而产生的废料。
4. 技术培训:加强操作人员的培训和技术水平提高,规范操作流程,减少因人为因素而产生的废料。
5. 废料回收利用:对裁切模产生的废料进行分类、收集和处理,实现资源的再利用。
可以将废料回收用于再加工或者其他用途,减少资源浪费。
6. 环保意识:公司应加强环保意识,建立环保管理制度,减少裁切模产生的废料对环境的影响。
通过以上方法的合理应用,可以有效解决裁切模产生废料的问题,提高生产效率,降低成本,保护环境,实现可持续发展。
公司在使用裁切模的过程中应积极探索新的技术和方法,不断优化生产流程,提高裁切模的利用率,为企业发展和社会进步做出更大的贡献。
第二篇示例:裁切模具在制造行业中起着非常重要的作用,能够帮助生产出符合设计要求的产品。
在使用过程中会产生大量的废料。
为了减少废料对环境的影响,提高资源利用效率,解决裁切模具废料的问题变得尤为重要。
3如何防止跳屑

如何預防跳屑﹑堵屑在產品類別日益增多的情況下,為了滿足客戶對產品的大量需求,衝壓加工逐步的向高速化生產發展,在日常的工作中由於人,地,物料,沖床,模具,管理等的種種差異與變化,衍生出許多技術障礙,模具在大量生產中的跳屑和堵屑便是其中一例.隨著衝壓團隊經驗的不斷累積,對較易發生跳屑和堵屑的變因已基本掌握並加以控制,以下是針對模具在生產中發生跳屑和堵屑的原因及改善的措施,希望藉此機會與同行共同探討衝壓加工的特性,使既有的技術得到擴展.什麼是跳屑?由於衝壓模具在高速衝切時,衝頭沖入材料, 衝頭四周壓縮材料,而衝頭引起跳屑的主要原因:b.衝切間隙不當:衝切間隙過大或不均時,沖頭對材料沖切力較小.沖下的廢料外形尺寸比模仁小.這樣廢料對模仁的咬合力也就較小.所以廢料就易從下模模仁中跳出.c.切削油選用及用量:切削油選用:一般根據材質的不同选用不同的切削油.例如預鍍材和磷青銅就要使用不同粘度的切削油.在生產時跳屑嚴重的話一般只把切削油加在材料的下表面,以防止廢料被下料沖子粘住.切削油的用量: 切削油的用量與衝切速度有很大的關係.SPM<400時每隔4秒一滴400<SPM<700時每隔3秒一滴SPM>700時每隔2秒一滴d.衝切速度过高易造成跳屑.e.下料沖子及下料刀口过於鋒利,廢料的切斷面光亮帶多而毛刺很少,與入塊之間的磨擦力过小,易被下料沖子吸附出入塊造成跳屑.f.下料沖子研磨后總長度过短造成衝切深度过淺,廢料接近下料入塊的上表面,極易被下料沖子吸附出入塊造成跳屑.g.因下料入塊在設計時是做成有落料斜度的,經常研磨后高度过低間隙變大造成跳屑.異h.異物附在銅材上被帶進入模具.i.材質越硬越容易產生跳屑.j.因振動而使模仁內原本粘在一起的廢料分散產生跳屑.下料沖子與下料入塊的間隙5%以下時: 可以增加切斷面,而切斷面與模仁之間的接觸面積也可以增大.下料沖子外形有小於2倍料厚的弧度.并且是凹角的話. 可以得到較長的切斷面.下料沖子與下料入塊的間隙為5%以上時:大部分的材料沖切出來的尺寸會比下料入塊外形尺寸小.所以可以推定其和模仁的咬合力會較小.i. 下料入塊選用適當的落料斜度:用光學磨床研磨的分割式入塊落料斜度為0.1°用線割的整體式入塊落料斜度為0.5°(如圖10)k.增設跳屑檢知:在下模板(D05A)上加裝檢知器.若發生跳屑,機台則會馬上停機.避免造成擠料.崩沖子等情況的發生.什麼是堵屑?模具在高速運動中,被沖切下來的廢料附著在模仁側壁而產生屑料堵塞.堵屑造成的影響:由於模具在高速運動,所以一旦堵屑就會發生擠料,沖頭崩斷下模入塊崩裂.堵屑對模具的損害很大.引起堵屑的主要原因:a.切削油用量過大造成被沖切下來的廢料附著在模仁側壁而產生屑料堵塞.b.下模落料框口尺寸過小或錯位使廢料不能順暢落下.(如圖12.13)以上改善的措施僅僅是很少的一部份,還有更多更加新穎的方法來等待我們去發掘.這就要求我們不能默守陳規,只有突破才能發展.愿以上談到的一些經驗能和同行們一起分享.審閱:。
冲压模具跳废料的原因分析,冲压模具跳料怎么修时间
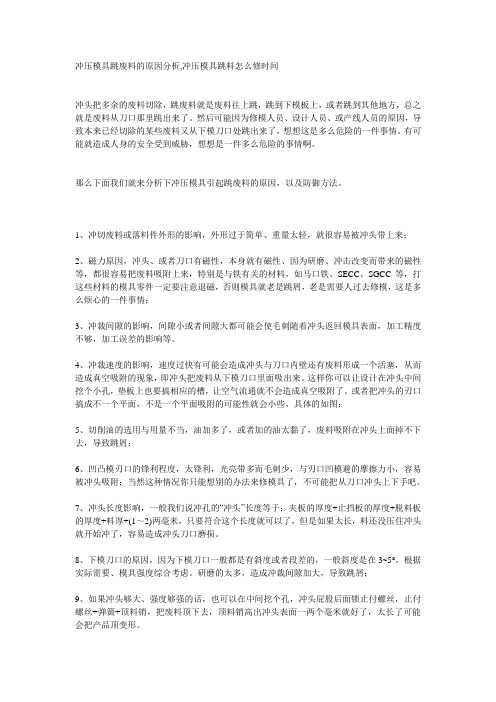
冲压模具跳废料的原因分析,冲压模具跳料怎么修时间冲头把多余的废料切除,跳废料就是废料往上跳,跳到下模板上,或者跳到其他地方,总之就是废料从刀口那里跳出来了。
然后可能因为修模人员、设计人员、或产线人员的原因,导致本来已经切除的某些废料又从下模刀口处跳出来了,想想这是多么危险的一件事情。
有可能就造成人身的安全受到威胁,想想是一件多么危险的事情啊。
那么下面我们就来分析下冲压模具引起跳废料的原因,以及防御方法。
1、冲切废料或落料件外形的影响,外形过于简单、重量太轻,就很容易被冲头带上来;2、磁力原因,冲头、或者刀口有磁性,本身就有磁性、因为研磨、冲击改变而带来的磁性等,都很容易把废料吸附上来,特别是与铁有关的材料,如马口铁、SECC、SGCC等,打这些材料的模具零件一定要注意退磁,否则模具就老是跳屑,老是需要人过去修模,这是多么烦心的一件事情;3、冲裁间隙的影响,间隙小或者间隙大都可能会使毛刺随着冲头返回模具表面,加工精度不够,加工误差的影响等。
4、冲裁速度的影响,速度过快有可能会造成冲头与刀口内壁还有废料形成一个活塞,从而造成真空吸附的现象,即冲头把废料从下模刀口里面吸出来。
这样你可以让设计在冲头中间挖个小孔,垫板上也要搞相应的槽,让空气流通就不会造成真空吸附了。
或者把冲头的刃口搞成不一个平面,不是一个平面吸附的可能性就会小些,具体的如图:5、切削油的选用与用量不当,油加多了,或者加的油太黏了,废料吸附在冲头上面掉不下去,导致跳屑;6、凹凸模刃口的锋利程度,太锋利,光亮带多而毛刺少,与刃口凹模避的摩擦力小,容易被冲头吸附;当然这种情况你只能想别的办法来修模具了,不可能把从刀口冲头上下手吧。
7、冲头长度影响,一般我们说冲孔的“冲头”长度等于:夹板的厚度+止挡板的厚度+脱料板的厚度+料厚+(1~2)两毫米,只要符合这个长度就可以了,但是如果太长,料还没压住冲头就开始冲了,容易造成冲头刀口磨损。
8、下模刀口的原因,因为下模刀口一般都是有斜度或者段差的,一般斜度是在3~5°,根据实际需要、模具强度综合考虑。
冲压产品跳屑压伤的原因及改进措施
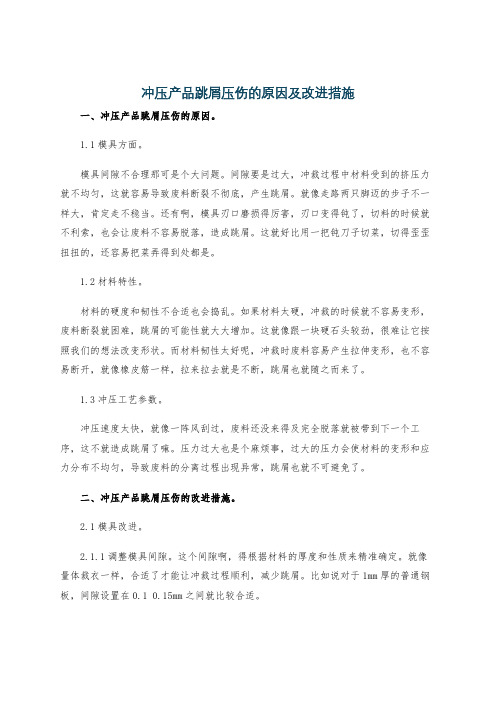
冲压产品跳屑压伤的原因及改进措施一、冲压产品跳屑压伤的原因。
1.1模具方面。
模具间隙不合理那可是个大问题。
间隙要是过大,冲裁过程中材料受到的挤压力就不均匀,这就容易导致废料断裂不彻底,产生跳屑。
就像走路两只脚迈的步子不一样大,肯定走不稳当。
还有啊,模具刃口磨损得厉害,刃口变得钝了,切料的时候就不利索,也会让废料不容易脱落,造成跳屑。
这就好比用一把钝刀子切菜,切得歪歪扭扭的,还容易把菜弄得到处都是。
1.2材料特性。
材料的硬度和韧性不合适也会捣乱。
如果材料太硬,冲裁的时候就不容易变形,废料断裂就困难,跳屑的可能性就大大增加。
这就像跟一块硬石头较劲,很难让它按照我们的想法改变形状。
而材料韧性太好呢,冲裁时废料容易产生拉伸变形,也不容易断开,就像橡皮筋一样,拉来拉去就是不断,跳屑也就随之而来了。
1.3冲压工艺参数。
冲压速度太快,就像一阵风刮过,废料还没来得及完全脱落就被带到下一个工序,这不就造成跳屑了嘛。
压力过大也是个麻烦事,过大的压力会使材料的变形和应力分布不均匀,导致废料的分离过程出现异常,跳屑也就不可避免了。
二、冲压产品跳屑压伤的改进措施。
2.1模具改进。
2.1.1调整模具间隙。
这个间隙啊,得根据材料的厚度和性质来精准确定。
就像量体裁衣一样,合适了才能让冲裁过程顺利,减少跳屑。
比如说对于1mm厚的普通钢板,间隙设置在0.1 0.15mm之间就比较合适。
2.1.2及时维修和更换刃口。
不能让刃口一直“带病工作”,一旦发现刃口磨损严重,就得赶紧维修或者换新的。
这就好比战士的武器,钝了就得磨或者换,不然上战场肯定打不了胜仗。
2.2材料选择与处理。
2.2.1根据产品要求选择合适硬度和韧性的材料。
不能盲目选择材料,要根据实际的冲压工艺和产品性能需求来挑选。
要是做个简单的小零件,就没必要选那种超硬的材料,增加成本还容易出问题。
2.2.2对材料进行预处理。
例如对硬度较高的材料可以进行退火处理,降低它的硬度,让它在冲裁的时候更“听话”,像驯服一匹烈马一样,让它温顺了,就好操作了。
模具调试设计跳废料及拉边的处理方法
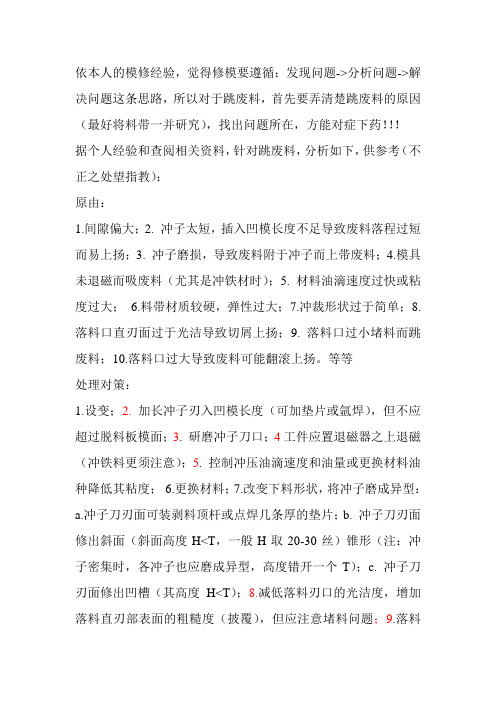
依本人的模修经验,觉得修模要遵循:发现问题->分析问题->解决问题这条思路,所以对于跳废料,首先要弄清楚跳废料的原因(最好将料带一并研究),找出问题所在,方能对症下药!!!据个人经验和查阅相关资料,针对跳废料,分析如下,供参考(不正之处望指教):原由:1.间隙偏大;2. 冲子太短,插入凹模长度不足导致废料落程过短而易上扬;3. 冲子磨损,导致废料附于冲子而上带废料;4.模具未退磁而吸废料(尤其是冲铁材时);5. 材料油滴速度过快或粘度过大;6.料带材质较硬,弹性过大;7.冲裁形状过于简单;8. 落料口直刃面过于光洁导致切屑上扬;9. 落料口过小堵料而跳废料;10.落料口过大导致废料可能翻滚上扬。
等等处理对策:1.设变;2.加长冲子刃入凹模长度(可加垫片或氩焊),但不应超过脱料板模面;3. 研磨冲子刀口;4工件应置退磁器之上退磁(冲铁料更须注意);5. 控制冲压油滴速度和油量或更换材料油种降低其粘度;6.更换材料;7.改变下料形状,将冲子磨成异型:a.冲子刀刃面可装剥料顶杆或点焊几条厚的垫片;b. 冲子刀刃面修出斜面(斜面高度H<T,一般H取20-30丝)锥形(注:冲子密集时,各冲子也应磨成异型,高度错开一个T);c. 冲子刀刃面修出凹槽(其高度H<T);8.减低落料刃口的光洁度,增加落料直刃部表面的粗糙度(披覆),但应注意堵料问题;9.落料口加大(可放电或合金钻钻大),并采用吸废料机吸废料。
10.降低冲裁速度,减缓跳屑,同时下模加吸(吹)气(必须要有斜度)。
另外可将冲子加吹气一般对策2.3.4.5.8.9较常用。
我们经常多种方法结合,屡试不爽!但有时一些怪招也很管用的,在此不再细说。
(一) 引起跳屑的原因:1.冲切废料或落料件外形形状的影响:在设计级进模排样时,下料的外形选择过于简单.与凹模之间的摩擦附著力太小.不易被凹模孔口咬住造成跳屑.2.磁力原因:1).凸模本身有磁性.若没有退磁或退磁不完全.则会残留磁性.2).凸模本身无磁性.经研磨与加工后产生了磁性.3).模具在经过多次的冲压后.因为受到冲击.会改变分子在材料内部的排列方向而产生磁力.模具磁性的存在使跳屑加剧.3.冲裁间隙的影响:1).间隙较小时.凹模内的材料与侧壁之间摩擦力较大,不易发生跳屑.但因受到的挤压力大.增加了材料与凹.凸模的摩擦磨损.实际间隙会增大.同时过小的间隙会使材料端面上产生二次剪切.易产生细小的毛刺,毛刺促使冲屑随凸模返回模面.2)间隙过大.凹模内的材料尺寸小于凹模尺寸.材料与凹模的摩擦减弱.则易发生跳屑.3)由于加工的误差.导致冲裁间隙的不均匀.易出现跳屑.4.冲裁速度的影响:当冲裁速度较高时.制件或废料也会因真空吸附作用而易导致跳屑的发生.5.切削油的选用与用量:由于油的粘度与用量不适.在冲裁过程中凸模易把料片粘住带出模面导致跳屑的发生.6.凹.凸模刃口的锋利程度:当刃口过于锋利时,冲裁后的光亮带多而毛刺小.与凹模壁的摩擦力小,易被凸模吸附而产生跳屑.当刃口相对比较钝时.冲裁阻力大.冲切断面易形成圆角.制件受凹壁的阻力也大.不易回升.7.凸模的长度的影响:凸模长度过短造成冲切深度太小.易产生跳屑.8.凹模:通常凹模有一定的落料斜度.经多次修磨后.易使间隙加大.造成跳屑.9.其他原因:1).异物粘附在材料上被带入模具内.2).材质越硬越易产生跳屑.3).因振动使凹模内原本粘在一起的废料分散产生跳屑.。
五金冲压件加工时为什么会跳屑?

五金冲压件加工时为什么会跳屑?
五金冲压件加工时会产生诸多不良的问题,跳屑是其中一种,跳屑的存在会降低生产效率、增加生产成本以及影响模具的寿命等等。
因此我们要具体分析为什么会跳屑,并能采取行之有效的处理对策,从根本上解决跳屑的问题。
1,冲压件加工跳屑的主要原因
主要原因是在高速连续冲裁过程中有切削油,间隙过大等因素的影响,使冲子与废屑之间形成瞬间局部真空,当材料很薄,废屑自身的重量与凹模刃口对其摩擦力之和小于冲子对其的吸附力时,在冲子上升过程中,废屑便吸附在冲子表面,随之上升,从而形成跳屑。
2,五金冲压解决对策
(1)间隙偏大,控制凸凹模加工精度或修改设计间隙;
(2)送料不当,送到适当位置时修剪料带并及时清理模具;
(3)冲压油滴太快,油粘控制冲压油滴油量,或更换油种降低粘度;
(4)模具未退磁,模具、研修后需退磁(冲铁料更需注意);
(5)凸模磨损,屑料压附于凸模上,研修凸模刀口,调整凸模刃入凹模长度;
(6)凸模太短,插入凹模长度不足;
(7)材质较硬,冲切形状简单;更换材料,修改设计。
凸模刃入端面装顶出或修出斜面或弧性(注意方向)。
减少凸模刃部端面与屑料之贴合面积;
(8)应急措施,减小凹模刃口的锋利度,减小凹模刃口的研修量,增加凹模直刃部表面的粗糙度(被覆),采用吸尘器吸废料。
降低冲速,减缓跳屑。
屹纬精密是一家精密金属冲压和金属嵌件注塑生产商,致力于为全球各行各业的客户提供精密金属冲压、金属拉伸和金属嵌件注塑的一站式解决方案。
我们会为您提供咨询服务并根据您的需求进行定制研发,提供电镀、阳极氧化、抛光、清洗,对表面进行光整加工等表面处理,期待与您的进一步合作。
五金模具冲压之产生跳屑的原因与防止
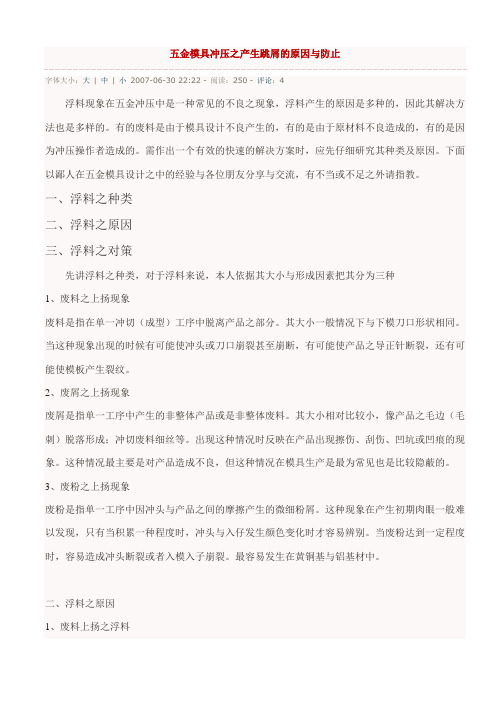
五金模具冲压之产生跳屑的原因与防止字体大小:大| 中| 小2007-06-30 22:22 - 阅读:250 - 评论:4浮料现象在五金冲压中是一种常见的不良之现象,浮料产生的原因是多种的,因此其解决方法也是多样的。
有的废料是由于模具设计不良产生的,有的是由于原材料不良造成的,有的是因为冲压操作者造成的。
需作出一个有效的快速的解决方案时,应先仔细研究其种类及原因。
下面以鄙人在五金模具设计之中的经验与各位朋友分享与交流,有不当或不足之外请指教。
一、浮料之种类二、浮料之原因三、浮料之对策先讲浮料之种类,对于浮料来说,本人依据其大小与形成因素把其分为三种1、废料之上扬现象废料是指在单一冲切(成型)工序中脱离产品之部分。
其大小一般情况下与下模刀口形状相同。
当这种现象出现的时候有可能使冲头或刀口崩裂甚至崩断,有可能使产品之导正针断裂,还有可能使模板产生裂纹。
2、废屑之上扬现象废屑是指单一工序中产生的非整体产品或是非整体废料。
其大小相对比较小,像产品之毛边(毛刺)脱落形成;冲切废料细丝等。
出现这种情况时反映在产品出现擦伤、刮伤、凹坑或凹痕的现象。
这种情况最主要是对产品造成不良,但这种情况在模具生产是最为常见也是比较隐蔽的。
3、废粉之上扬现象废粉是指单一工序中因冲头与产品之间的摩擦产生的微细粉屑。
这种现象在产生初期肉眼一般难以发现,只有当积累一种程度时,冲头与入仔发生颜色变化时才容易辨别。
当废粉达到一定程度时,容易造成冲头断裂或者入模入子崩裂。
最容易发生在黄铜基与铝基材中。
二、浮料之原因1、废料上扬之浮料废料上扬的原因首先来分析一下力的来源,废料由于一般与冲头或下模刀口的形状相同,因此,废料在模具的入子内应该有一定的摩擦力存在,从冲切的原理上来说,废料在切离以后由于材料的塑性或者说弹性变形的存在其会恢复组织结构,换句话说其在无约束实际形状应该大于下模刀口形状,这也是为什么当把废料从入子里面取出来的后再也不能轻松的把废料再填充到下模入子里去的原因。
冲压模具跳屑原因及改善对策讲义

圖七
圖八
P. 10
2. 要解決因料片形狀簡單而產生的跳屑 很困難, 因為 要解決因料片形狀簡單而產生的跳屑, 料片的形狀是由產品決定, 人為很難改變它。但若料片 的形狀很簡單,如果不影響產品功能,模具設計人員就應 該與產品設計人員溝通,將料片形狀變復雜。對於圓形 料片,除刀口做成分體式外,模具設計時可以把組成圓形 的兩個半圓圓心位置互相錯開 0.002-0.005 mm ,如圖九 所示,達成形狀設計之目的。許多同仁時常有疑問:切邊 刀口為何要做成“ 跳屑。 圖九
圖三
圖四
連結器事業處
P. 6
3. 沖頭的長度太短及沖頭料片接觸面積太大 對於端子模具,下料沖頭的長度一般以沖頭進入刀口 的深度1mm左右為宜, 但常常在修模過程中, 為防止端 子翻料, 把沖頭磨短, 以降低剪切力, 最后卻導致跳屑產 生。另外,若下料沖頭與料片的接觸面積太大,料片吸附 在沖頭上升而把料片帶到模具上。 4. 沖切油加得太多或沖切油粘度太大 沖切油太多及粘度太大,使料處极易附著在沖頭上, 隨著沖頭的上升產生跳屑。
連結器事業處
”形式,而不做成“
”
形式,這其中一個主要目的是使料片的形狀復雜化,防止
A + B A B
0.002-0.005
P. 11
3. 因衝頭長度不夠而產生的跳屑,我們把握一個原則, 因衝頭長度不夠而產生的跳屑 按圖面要求就可。但對於沖頭與料下接觸面積太大所 造成的跳屑,可改變沖慶的形狀,如圖十所示,以減少接 觸面積。 4. 對刀口鬆動而產生的跳屑 對刀口鬆動而產生的跳屑:臨時對策常在刀口的周圍 加墊片,這很不科學,永久性對策是把模板的框口加工成 可換式,如圖十一所示。 圖十一
連結器事業處
P. 13
生产精密五金冲压模具加工件,跳料怎么办?
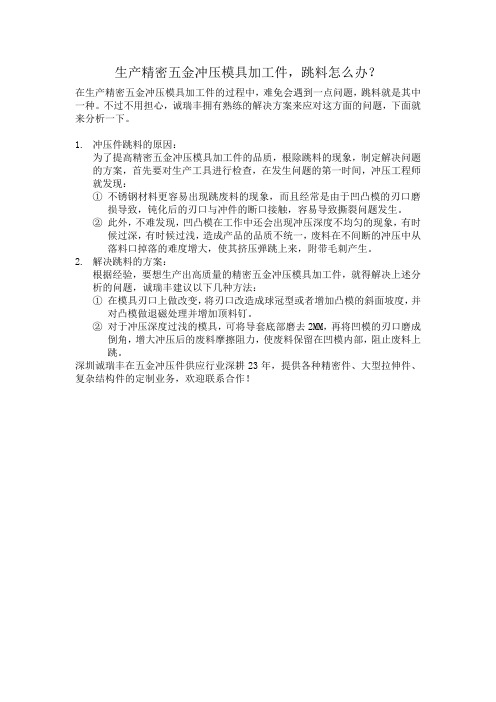
生产精密五金冲压模具加工件,跳料怎么办?
在生产精密五金冲压模具加工件的过程中,难免会遇到一点问题,跳料就是其中一种。
不过不用担心,诚瑞丰拥有熟练的解决方案来应对这方面的问题,下面就来分析一下。
1.冲压件跳料的原因:
为了提高精密五金冲压模具加工件的品质,根除跳料的现象,制定解决问题的方案,首先要对生产工具进行检查,在发生问题的第一时间,冲压工程师就发现:
①不锈钢材料更容易出现跳废料的现象,而且经常是由于凹凸模的刃口磨
损导致,钝化后的刃口与冲件的断口接触,容易导致撕裂问题发生。
②此外,不难发现,凹凸模在工作中还会出现冲压深度不均匀的现象,有时
候过深,有时候过浅,造成产品的品质不统一,废料在不间断的冲压中从落料口掉落的难度增大,使其挤压弹跳上来,附带毛刺产生。
2.解决跳料的方案:
根据经验,要想生产出高质量的精密五金冲压模具加工件,就得解决上述分析的问题,诚瑞丰建议以下几种方法:
①在模具刃口上做改变,将刃口改造成球冠型或者增加凸模的斜面坡度,并
对凸模做退磁处理并增加顶料钉。
②对于冲压深度过浅的模具,可将导套底部磨去2MM,再将凹模的刃口磨成
倒角,增大冲压后的废料摩擦阻力,使废料保留在凹模内部,阻止废料上跳。
深圳诚瑞丰在五金冲压件供应行业深耕23年,提供各种精密件、大型拉伸件、复杂结构件的定制业务,欢迎联系合作!。
- 1、下载文档前请自行甄别文档内容的完整性,平台不提供额外的编辑、内容补充、找答案等附加服务。
- 2、"仅部分预览"的文档,不可在线预览部分如存在完整性等问题,可反馈申请退款(可完整预览的文档不适用该条件!)。
- 3、如文档侵犯您的权益,请联系客服反馈,我们会尽快为您处理(人工客服工作时间:9:00-18:30)。
B.在刀口的冲切直线段下部用放电笔/被覆机(放电的原理)加工而使其粗糙增大卡屑力.
另外充分利用模具下面的吸气机,可在刀口旁开通风槽,脱料板开通风孔/或上下均加吹气孔也可起到很好的辅助作用.
跳料/屑产生的原因
1.主要是由于高速冲裁时冲头端面与材料/屑之间产生真空吸引导致跳屑, 所以废料越轻越容易跳屑.因此薄材,冲裁的面积很小,高速时更容易产生跳屑.
2.由于下模/刀口对废料的夹持力/保持力不足而产生跳屑./多是由于废料形状太简单/规则的情形.
基于以上两个方面而采取的对策
1.将冲头/凸模的冲裁端面磨成斜度/非平面而不易产生真空吸引(圆孔冲头,端子的长PIN下料冲头常采用)
2.尽量避免太简单形状的冲裁,以增大废料的保持力,万不得已时
A.可采用刀口开防跳屑槽/或凸筋来卡住废料,一般开两条相反倾斜角度的槽/凸筋(凸筋一般用于厚材,因为间隙大才可以).镶拼式/分体式刀口可通过微小的错位而产生同样的无斜度的卡屑线.