冲压模具防跳废料
冲压安全作业方式及内容(三篇)

冲压安全作业方式及内容冲压作业包括送料、定料、操纵设备、出件、清理废料、工作点的布置等操作动作。
这些动作常常互相联系,对制件的质量、作业的效率和人身安全都有直接影响。
下面重点分析几个与安全关系较大的工序。
(l)送料将坯料送入模内的操作称为送料。
送料操作是在滑块即将进入危险区之前进行,所以必须注意操作的安全。
一般操作者的送料动作节奏与滑块能够快调一致。
操作者不需用手在模区内操作,这时是安全的。
但当进行尾件加工时或手持坯件入模进料时,手要进入模区,这时具有较大的危险性,因此要实行重点保护。
(2)定料将坯料限制在某一固定位置上的操作称为定定料操作是在送料操作完成后进行的,它处在滑块即将的时刻,因此比送料更具有危险性。
由于定料的方便程度直接影响到作业的安全,所以决定定位方式时要考虑其安全程度。
定位方式主要有:挡料销定位,定位板、导板定位,导正销定位,定距侧刃几种方式。
(3)出件出件是指从冲楼内取出制件的操作。
出件是在滑块回程期间完成的。
对行程次数少的压机来说,滑块处~安全区内,不易面接伤手;对行程次数较多的开式压机,则仍具有较大危险。
出件方法主要有:下漏出件、弹性卸料入件、打料式出件。
(4)清除废料指清除模区内的冲压废料。
废料是分离工序中不可避免的。
如果在操作过程中不能及清理,就会影响作业正常进行,甚至会出现复冲和叠冲.有时也会发生废料,模片飞弹伤人的现象。
(5)操纵指操纵者控制冲压设备动作的方式。
常用的操纵方式有两种,即:按钮开关和脚踏开关。
当单人操作按钮开关时一般不易发生危险.但多人操作时,会因照顾不周或配合不当,造成伤害事故。
因此多人作业时。
必须采取相应的安全措施。
脚踏开关虽然容易操作,但也容易引起手脚配料失调。
发生失误.造成事故。
冲压安全作业方式及内容(二)冲压是一种通常通过应用外力将板材变形成所需形状的工艺,广泛应用于金属加工行业。
随着冲压技术的广泛应用,相关的安全工作也越来越重要。
在冲压作业中,安全是第一位的,因为涉及到的设备、工艺和操作环境都存在一定的风险。
高速冲压中防止废料回升的几个解决方法

冲
模 技 术
・
以P G 方式加工 , 凹模刃 口为分体式 的 , 才能实现 上述结构 , 图3 a 中H值一般为 凸模切人深度 的 7 0 %,
件
且适合 于 冲裁 间隙< O . O l m m; 图3 b 适合 于冲裁间 隙>
0. O1 5mm 。
3 . 3 外形 简单 光滑 的 凸模 刃 口设 计 ( p r o i f l e d i e
表1 给 出了沟槽角度与宽度 的推荐值 ( 凹模镶件
厚度为 6 . 5 am时 , r D i e i n s e r t t h i c k n e s s = 6 . 5 m m) 。
料 厚
“
x3
4
表 1 沟槽 角度 与宽度的推荐值
角度参考 值( 凹模 厚度= 6 . 5 0 0 )
n= = = ¨U №
板厚 … t ’ x 3
压 入 部“ ” O . 2 O - 2 0 - 2 O - 3 0 . 4 0 _ 4 O . 5 0 . 5 O . 5 0 . 5 0 . 6 O . 6 O . 6 O . 6
图 6 冲 裁 外 形 的 凸 凹 模 参 数
・
冲
模 技
术
・
就 占据 了他 们 6 0 %以上 的修 模 时间 , 通常处 理跳 废 料 的方 法有 凸模 加 气 孔 , 漏料 孔 加装 吸尘 器 , 凸模 的平 刃 口改 为斜 刃 口或锥形 刃 口, 凹模刃 口钓鱼 法 等等 , 这 些 都是 冲 压工 厂 处理 跳 屑 常用 方法 , 不 再 赘述 , 在 此本 文将 主要介 绍几种 基 于 凹模 刃 口不 同
. 1 5 m m; 当板 厚 > 0 . 5 mm, R = 0 . 3 5 mm。 ( 2 ) 冲裁外形的加工方式为光学 曲线磨 ( P G ) , 如 0 ( 3 ) 沟槽 深 度 : 一般的 , 其 值 等 于 冲 切 间 隙 图5 所示 。 ( c u t t i n g c l e a r a n c e ) 或取 板 厚 的 5 %。
高速级进冲压中废料回跳问题的解决方案

高速级进冲压中废料回跳问题的解决方案近年来,随着工业生产的持续发展,高速级进冲压成为传统级进冲压的淘汰,其中废料回跳问题也逐渐出现,严重影响冲压生产率和质量。
废料回跳指的是在高速级进冲压过程中,由于模具的废料板积聚在模具表面,当模具运动到最高点时,废料板弹起,被模具表面弹起至上一个模具表面,从而影响冲压质量,并损害设备。
二、问题分析
废料回跳主要是由于模具设计原因造成,模具制造过程中模具本身质量可能存在缺陷,从而导致模具表面缺乏摩擦力,废料板在模具表面堆积,其冲压膨胀率大于模具,这样废料板就容易被模具表面弹起至上一个模具表面,制造过程中废料会被不断叠加,造成废料回跳问题。
此外,在冲压过程中,由于模口大小不同,加上模具不同的运动速度,会导致冲压力度及冲压水平的不均匀,不仅会增加冲压失效率,也容易使冲压件面出现较大的凹脊,导致废料回跳问题。
三、解决方案
(1)模具制造方面:改进模具设计,将模具表面改为模具边缘,使模具表面能有足够的摩擦力,防止废料板积聚,减少废料回跳现象。
(2)冲压过程方面:根据情况,采取不同冲压力度和冲压水平,将应力平均分布在冲压制件上,避免冲压失效,减少废料回跳现象。
(3)模具清理方面:经常清理模具表面,定期更换模具零件,以确保模具表面摩擦力充足,及时清理废料残留,防止废料回跳。
四、结论
高速级进冲压中废料回跳问题是一个很复杂的问题,解决这个问题需要从模具制造,冲压过程和模具清理三个方面入手,综合运用这些技术,可以有效解决高速级进冲压中废料回跳问题。
汽车冲压模具设计标准:废料的处理原则_解释说明

汽车冲压模具设计标准:废料的处理原则解释说明1. 引言1.1 概述汽车冲压模具设计是汽车制造过程中不可或缺的一环。
而随着环保意识的增强,废料的处理成为重要的问题。
本文将探讨汽车冲压模具设计中废料处理原则及其重要性,并通过实际案例分析来展示如何在设计过程中有效应用废料处理方法。
1.2 文章结构本文共分为五个主要部分,依次为引言、汽车冲压模具设计标准、废料处理原则与注意事项、废料处理在汽车冲压模具设计中的应用案例分析以及结论。
首先将介绍文章背景和目的,并对文章结构进行说明,然后详细探讨汽车冲压模具设计标准和特殊要求以及相关国际标准和规范概述。
接下来将重点关注废料的分类与性质分析、废料处理的环境影响与法规要求以及废料处理方法与技术选择。
随后通过实际案例来展示废料处理在汽车冲压模具设计中的应用情况,并对这些案例进行深入分析。
最后,我们将总结主要观点并展望未来发展方向。
1.3 目的本文的目的是通过对汽车冲压模具设计标准和废料处理原则的研究和分析,提供有关废料处理在汽车冲压模具设计中的重要性以及应用案例分析,旨在引起更多人对环境保护和资源利用的关注。
同时,本文也致力于为冲压模具设计者提供相关实践指南和技术选择建议,以促进可持续发展并推动汽车制造行业朝着更加环保、高效的方向发展。
2. 汽车冲压模具设计标准:2.1 冲压模具设计的基本原则:在汽车冲压模具设计中,需要遵循一些基本原则,以确保模具能够满足生产需求,并且能够保证产品的质量和尺寸精度。
这些基本原则包括:- 合理布置工作部位:将各个工作部位(如送料、下料、成形等)合理布置在模具上,使得整个冲压过程能够顺利进行,并且减少不必要的人力劳动。
- 优化材料选择:根据工件的材料特性和使用环境,合理选择模具材料,以提高耐磨性、硬度和导热性等特性。
- 设计结构简洁:冲压模具应当尽可能地减少部件数量和组装难度,以便于维护和修理。
同时还应注意减少创伤风险,并提高生产效率。
冲孔跳废料的解决方案
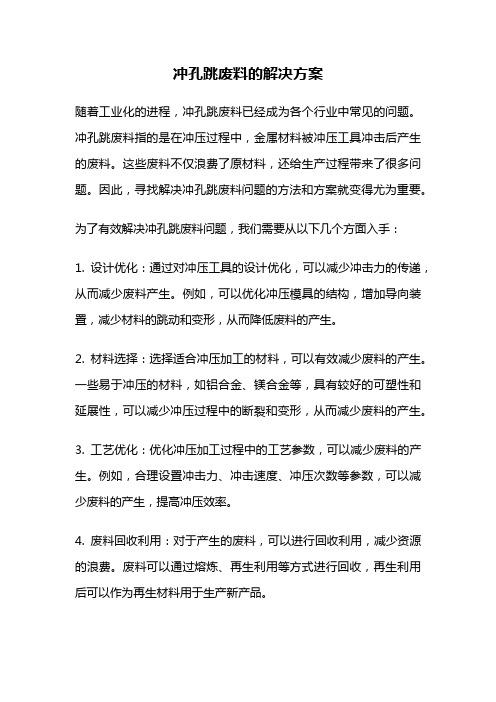
冲孔跳废料的解决方案随着工业化的进程,冲孔跳废料已经成为各个行业中常见的问题。
冲孔跳废料指的是在冲压过程中,金属材料被冲压工具冲击后产生的废料。
这些废料不仅浪费了原材料,还给生产过程带来了很多问题。
因此,寻找解决冲孔跳废料问题的方法和方案就变得尤为重要。
为了有效解决冲孔跳废料问题,我们需要从以下几个方面入手:1. 设计优化:通过对冲压工具的设计优化,可以减少冲击力的传递,从而减少废料产生。
例如,可以优化冲压模具的结构,增加导向装置,减少材料的跳动和变形,从而降低废料的产生。
2. 材料选择:选择适合冲压加工的材料,可以有效减少废料的产生。
一些易于冲压的材料,如铝合金、镁合金等,具有较好的可塑性和延展性,可以减少冲压过程中的断裂和变形,从而减少废料的产生。
3. 工艺优化:优化冲压加工过程中的工艺参数,可以减少废料的产生。
例如,合理设置冲击力、冲击速度、冲压次数等参数,可以减少废料的产生,提高冲压效率。
4. 废料回收利用:对于产生的废料,可以进行回收利用,减少资源的浪费。
废料可以通过熔炼、再生利用等方式进行回收,再生利用后可以作为再生材料用于生产新产品。
5. 自动化技术:引入自动化技术可以提高冲压加工的精度和效率,减少废料的产生。
例如,采用数控冲床、机器人等自动化设备,可以实现精确控制和高效生产,减少废料的产生。
6. 质量控制:加强冲压加工过程的质量控制,可以减少废料的产生。
通过严格控制冲压工艺参数、加强设备维护和保养、加强操作培训等措施,可以提高产品质量,减少废料的产生。
冲孔跳废料问题不仅涉及到生产效率和资源利用的问题,还涉及到环境保护和可持续发展的问题。
有效解决冲孔跳废料问题,对于提高生产效率、降低生产成本、保护环境都具有重要意义。
因此,各个行业应该重视冲孔跳废料问题,积极寻找解决方案,推动冲压加工技术的发展和进步。
解决冲孔跳废料问题需要综合考虑设计优化、材料选择、工艺优化、废料回收利用、自动化技术和质量控制等方面的因素。
跳屑原因及对策

Page: 9
E. 刀口的内宽加工成比废料的长度小0.02-0.04mm, 使废料 承弯曲状卡在刀里面,防止跳料.(如图八)
Page: 10
2. 因冲头长度不够而长生跳料:
把握一个原则:按图纸的要求. 但对于冲头与废料接触面积 太大所造成的跳料,可改变冲头形状。(如图九) 以减少接 触面积。
A
B
沖 頭 GAP=T(4~6)%
Page: 4
B模具很顺畅的情况下,由于废料与刀口的内面摩擦次数 多,而把刀口的内面磨损,造成刀口间隙过大. (如图三)
2.冲头的长度太短及冲头与落料接触面太大.
Page: 5
3.刀口的松动.
(如图四)
模板
刀口
模板
间隙
间隙
4.端子油加得太多或端子油黏度太大.
Page: 6
A.设计时把刀口的间隙放在下限上.即GAP=(4%~6%)T. B.把刀口的上端设计为2~3mm的直刀位, 下部加工成斜度 (0.5°-1.0°),增强刀口的耐磨度. (如图五) 直刀位
Page:8
C.把刀口由整体式设计为分体式. (如图六)
A
A
B
D.把刀口的厚度设计为2~3mm,便于废料及时脱落,减少 跳料机会. (如图七)
2.凸模加工斜度角。A或B,C使废料形变或减少与凸模的接触面积,针对1,2,5.
3.凸模加弹钉销。将废料始终按压在凹模腔内,对所有原因造成跳废料皆有效。
4. 安装吸废料机。
page 15
0.002~0.005MM
Page: 13
6. 对于新换过的刀口和研磨过的刀口产生跳料 对策为:
A.在刀口的棱角处用铜片来回刮.
B.用红宝石抛刀口棱角处.
防废料回跳型凹模
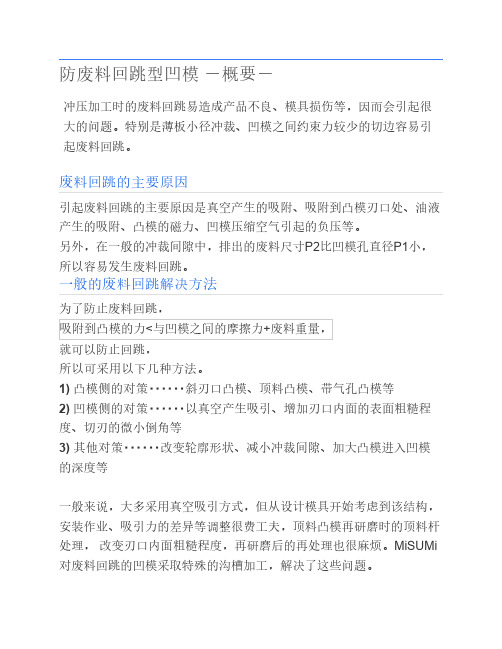
防废料回跳型凹模-概要-冲压加工时的废料回跳易造成产品不良、模具损伤等,因而会引起很大的问题。
特别是薄板小径冲裁、凹模之间约束力较少的切边容易引起废料回跳。
废料回跳的主要原因引起废料回跳的主要原因是真空产生的吸附、吸附到凸模刃口处、油液产生的吸附、凸模的磁力、凹模压缩空气引起的负压等。
另外,在一般的冲裁间隙中,排出的废料尺寸P2比凹模孔直径P1小,所以容易发生废料回跳。
一般的废料回跳解决方法为了防止废料回跳,吸附到凸模的力<与凹模之间的摩擦力+废料重量,就可以防止回跳,所以可采用以下几种方法。
1) 凸模侧的对策・・・・・・斜刃口凸模、顶料凸模、带气孔凸模等2) 凹模侧的对策・・・・・・以真空产生吸引、增加刃口内面的表面粗糙程度、切刃的微小倒角等3) 其他对策・・・・・・改变轮廓形状、减小冲裁间隙、加大凸模进入凹模的深度等一般来说,大多采用真空吸引方式,但从设计模具开始考虑到该结构,安装作业、吸引力的差异等调整很费工夫,顶料凸模再研磨时的顶料杆处理,改变刃口内面粗糙程度,再研磨后的再处理也很麻烦。
MiSUMi 对废料回跳的凹模采取特殊的沟槽加工,解决了这些问题。
图1 防废料回跳型冲模的沟槽形状防废料回跳型凹模的原理和特长1) 防废料回跳型凹模的原理在凹模内侧面,将2处以上的倾斜沟从中心开始向反方向加工。
在冲裁工序初期,冲裁废料会形成和凹模倾斜沟相对应的小突起。
随着凸模下降,若进一步向下面压入,突起部分会被凹模侧面压缩(压平作用),摩擦力增大,从而防止废料回跳。
另外,倾斜沟不是以螺旋状,而是向反方向加工,所以不会随着凸模上升,引起旋转和废料回跳。
2) 刃口形状以及凹模的种类本产品可以有效用于容易产生废料回跳的圆形以及各种异形,而且对和凹模之间约束力较小的边缘切割形状(切边)也很有效果。
3) 操作简单,总体成本降低只要将防废料回跳型凹模装入模具中,就可以发挥作用,所以也可以用于原有模具中,不需要另费功夫再研磨,也不需要再研磨后的再处理。
连续冲压中跳废料的防止措施课件

根据冲压工艺和产品要求,选用具有良好润滑性能和分离性 能的专用冲压油。冲压油能够有效降低废料与模具之间的摩 擦,减少跳动现象。
定时喷涂润滑剂
在连续冲压过程中,定时喷涂润滑剂于模具表面,保持模具 的良好润滑状态,减少废料的粘附和跳动。喷涂润滑剂的时 间和频率需要根据实际情况进行调整,以确保最佳效果。
连续冲压中跳废料的 防止措施课件
目录
• 连续冲压工艺简介 • 跳废料问题描述 • 防止跳废料的技术措施 • 操作管理及注意事项 • 案例分析与实践 • 总结与展望
01
连续冲压工艺简介
连续冲压工艺定义
• 定义描述:连续冲压工艺是一种金属加工方法,通过在冲床上使用连续模具对金属板材进行 连续的冲裁、弯曲、拉伸等成形操作,从而生产出具有特定形状和功能的零部件。
THANKS
感谢观看
06
总结与展望
课程总结
系统性与实践性兼具的课件
• 课件内容结合了实际生产经验和专业研究成果,确保 学员能够深入了解跳废料问题的本质,并能在实际工 作中运用所学知识进行有效应对。
• 课件采用了讲解、案例分析、实践操作等多种教学 方法,使学员在多角度、多层次上掌握跳废料的防 止措施。
• 本课件详细介绍了连续冲压过程中跳废料的产生原 因和影响,通过系统性的理论分析和实践性的防范 策略,为学员提供了一套全面且实用的学习资料。
案例三:操作管理在防止跳废料中的作用
操作管理重要性
加强操作管理可以有效减少操作失误,避免因操作不当引 起的跳废料问题。
管理措施
制定严格的操作规程,加强员工培训,建立奖惩制度等。
实践经验
通过实施有效的操作管理,可以显著提高员工操作的规范 性和准确性,降低跳废料现象的发生概率。同时,也有助 于提升企业的整体管理水平和市场竞争力。
五金冲压的废料是什么材质

五金冲压废料形成的原因
所谓废料是指冲压设备在运行时,五金冲压模具本应冲至下模的现象,而通过下模废孔掉落的废料被带到模具表面影响生产的现象。
一旦模具出现跳跃,废料就会冲破皮带或冲头、刀口,影响冲压件的质量,降低模具的使用寿命,降低生产效率,这是最常见也是最令人担心的问题。
五金冲压时废料形成原因
其它因素造成
1 真空吸尘器,将吸尘器用于清除废物,防止跳跃废物。
2 必须保持冲头和刀刃的锋利度,适量添加冲压油,都有助于防止跳跃浪费。
预防跳废料的方法
1.减少冲头与五金冲压件的接触面积
2 在产品的接触面上插入冲孔。
3 对于大但形状不规则的冲头,可以在冲头中间挖一个洞以减少接触面积。
4 冲头磨异形。
5 在模具的设计中,在冲头中间加入吹气孔,防止带材的吹气。
6 即如果打孔材料是SKD11,可以在打孔器上添加弹簧销以防止碎裂。
7 增加刀刃和废料之间的摩擦力
8 对于嵌入物或组合刀口,可在刀片边缘下1mm左右用盖针“覆盖”,以增加刀口中废料的摩擦。
9 对于侧边、进料站边缘等工艺辅助步骤,可适当复杂废料的形状,以增加废料在凹模中的夹紧力,防止切屑跳跃。
10 在高速冲压过程中,由于冲裁速度高(800 m/s以上)和冲裁过程中的冲压油等因素,冲头与废料位置之间形成局部真空,尤其是冲压材料非常薄时。
由于废料本身重量轻,具有刀刃
的摩擦力很小,在冲裁过程中,会用冲床将废料带到模具表面,并出现跳料浪费的现象。
11 冲角,钝化或过度使用冲压油,薄料和冲孔的有效冲压等都太短,都会造成跳槽浪费。
高速冲压防冲孔废料回跳法
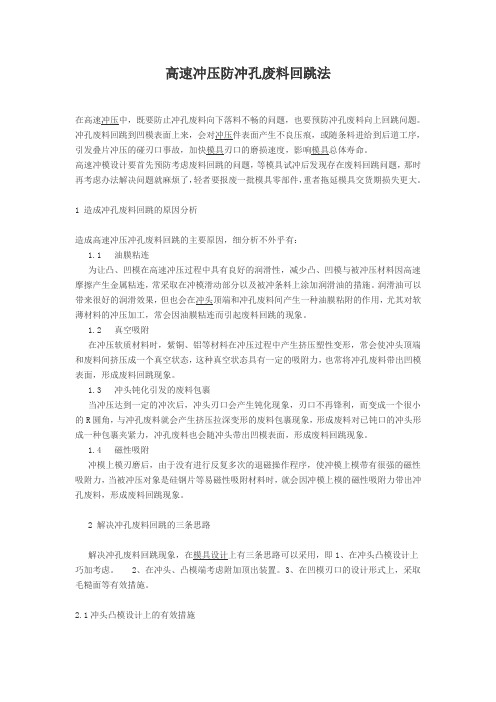
高速冲压防冲孔废料回跳法在高速冲压中,既要防止冲孔废料向下落料不畅的问题,也要预防冲孔废料向上回跳问题。
冲孔废料回跳到凹模表面上来,会对冲压件表面产生不良压痕,或随条料进给到后道工序,引发叠片冲压的碰刃口事故,加快模具刃口的磨损速度,影响模具总体寿命。
高速冲模设计要首先预防考虑废料回跳的问题,等模具试冲后发现存在废料回跳问题,那时再考虑办法解决问题就麻烦了,轻者要报废一批模具零部件,重者拖延模具交货期损失更大。
1 造成冲孔废料回跳的原因分析造成高速冲压冲孔废料回跳的主要原因,细分析不外乎有:1.1 油膜粘连为让凸、凹模在高速冲压过程中具有良好的润滑性,减少凸、凹模与被冲压材料因高速摩擦产生金属粘连,常采取在冲模滑动部分以及被冲条料上涂加润滑油的措施。
润滑油可以带来很好的润滑效果,但也会在冲头顶端和冲孔废料间产生一种油膜粘附的作用,尤其对软薄材料的冲压加工,常会因油膜粘连而引起废料回跳的现象。
1.2 真空吸附在冲压软质材料时,紫铜、铝等材料在冲压过程中产生挤压塑性变形,常会使冲头顶端和废料间挤压成一个真空状态,这种真空状态具有一定的吸附力,也常将冲孔废料带出凹模表面,形成废料回跳现象。
1.3 冲头钝化引发的废料包裹当冲压达到一定的冲次后,冲头刃口会产生钝化现象,刃口不再锋利,而变成一个很小的R圆角,与冲孔废料就会产生挤压拉深变形的废料包裹现象,形成废料对已钝口的冲头形成一种包裹夹紧力,冲孔废料也会随冲头带出凹模表面,形成废料回跳现象。
1.4 磁性吸附冲模上模刃磨后,由于没有进行反复多次的退磁操作程序,使冲模上模带有很强的磁性吸附力,当被冲压对象是硅钢片等易磁性吸附材料时,就会因冲模上模的磁性吸附力带出冲孔废料,形成废料回跳现象。
2 解决冲孔废料回跳的三条思路解决冲孔废料回跳现象,在模具设计上有三条思路可以采用,即1、在冲头凸模设计上巧加考虑。
2、在冲头、凸模端考虑附加顶出装置。
3、在凹模刃口的设计形式上,采取毛糙面等有效措施。
冲压模具设计中注意事项

一、使用长方形切断刀的注意事项1、步距尽量大,要大于整个刀具长度的80%。
2、最好通过编程来实现跳跃步冲。
3、建议选用斜刃口模具。
二、在不超过机器公称力的情况下如何冲孔生产过程中需要冲大于114.3mm直径的圆孔。
如此大的孔会超出机器公称力上限,特别对于高剪切强度材料。
通过多次冲孔的方法冲出大尺寸孔可以解决这一问题。
使用小尺寸模具沿大圆周长剪切可以降低一半或更多的冲压力,在你已经拥有的模具中可能大部分模具都能做到。
三、一个冲大圆孔的简易方法这种凸透镜的模具可被制成你所需半径尺寸。
如果孔径超出冲床公称力,我们推荐使用(A)方案。
用此模具冲出圆形的周边。
如果孔径能在冲床公称力范围内冲成,那么一个放射形模具和一凸透镜模具就能在四次之内冲压出所需的孔而无须旋转模具(B)四、最后才向下成形当选用成形模具时,应避免进行向下成形操作,因为这样会占用太多垂直空间和导致额外的平整或弯曲板材工序。
向下成形也可能陷入下模,然后被拉出转塔,然而,如果向下成形是唯一的工艺选择,那么应该把它作为对板材的最后一步处理工序。
五、防止材料扭曲如果你需要在板材上冲切大量孔而板材又不能保持平整,成因可能是冲压应力累积。
冲切一个孔时,孔周边材料被向下拉伸,令板材上表面拉应力增大下冲运动也导致板材下表面压应力增大。
对于冲少量的孔,结果不明显,但随着冲孔数目的增加,拉应力和压应力也成倍增加直到令板材变形。
正全科技微信内容真不错,值得关注!!消除这种变形的方法之一是:每隔一个孔冲切,然后返回冲切剩余的孔。
这虽然在板材上产生相同的应力,但瓦解了因同向连续一个紧接一个地冲切而产生拉应力/压应力积聚。
如此也令第一批孔分担了第二批孔的部变形效应。
六、如果你的不锈钢翻边变形在制造翻边之前向材料施用优质成形润滑剂,这能令材料更好地从模具中分离出来,在成形时顺畅地在下模表面移动。
如此给予材料一个更好的机会去分布被弯曲和被拉伸时产生的应力,防止在成形翻边孔边上出现的变形和翻边孔底部的磨损。
冲压模具跳废料的原因分析,冲压模具跳料怎么修时间
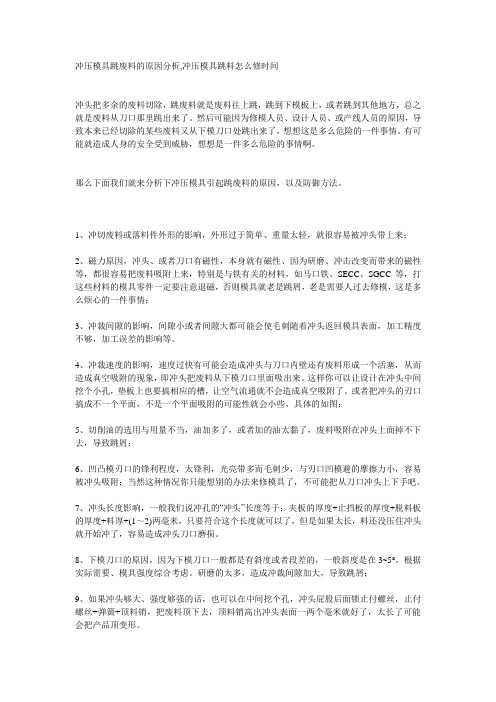
冲压模具跳废料的原因分析,冲压模具跳料怎么修时间冲头把多余的废料切除,跳废料就是废料往上跳,跳到下模板上,或者跳到其他地方,总之就是废料从刀口那里跳出来了。
然后可能因为修模人员、设计人员、或产线人员的原因,导致本来已经切除的某些废料又从下模刀口处跳出来了,想想这是多么危险的一件事情。
有可能就造成人身的安全受到威胁,想想是一件多么危险的事情啊。
那么下面我们就来分析下冲压模具引起跳废料的原因,以及防御方法。
1、冲切废料或落料件外形的影响,外形过于简单、重量太轻,就很容易被冲头带上来;2、磁力原因,冲头、或者刀口有磁性,本身就有磁性、因为研磨、冲击改变而带来的磁性等,都很容易把废料吸附上来,特别是与铁有关的材料,如马口铁、SECC、SGCC等,打这些材料的模具零件一定要注意退磁,否则模具就老是跳屑,老是需要人过去修模,这是多么烦心的一件事情;3、冲裁间隙的影响,间隙小或者间隙大都可能会使毛刺随着冲头返回模具表面,加工精度不够,加工误差的影响等。
4、冲裁速度的影响,速度过快有可能会造成冲头与刀口内壁还有废料形成一个活塞,从而造成真空吸附的现象,即冲头把废料从下模刀口里面吸出来。
这样你可以让设计在冲头中间挖个小孔,垫板上也要搞相应的槽,让空气流通就不会造成真空吸附了。
或者把冲头的刃口搞成不一个平面,不是一个平面吸附的可能性就会小些,具体的如图:5、切削油的选用与用量不当,油加多了,或者加的油太黏了,废料吸附在冲头上面掉不下去,导致跳屑;6、凹凸模刃口的锋利程度,太锋利,光亮带多而毛刺少,与刃口凹模避的摩擦力小,容易被冲头吸附;当然这种情况你只能想别的办法来修模具了,不可能把从刀口冲头上下手吧。
7、冲头长度影响,一般我们说冲孔的“冲头”长度等于:夹板的厚度+止挡板的厚度+脱料板的厚度+料厚+(1~2)两毫米,只要符合这个长度就可以了,但是如果太长,料还没压住冲头就开始冲了,容易造成冲头刀口磨损。
8、下模刀口的原因,因为下模刀口一般都是有斜度或者段差的,一般斜度是在3~5°,根据实际需要、模具强度综合考虑。
冲孔模如何防止废料堆积

冲孔模如何防止废料堆积废料堆积的原因:废料堆积的原因,一般有以下几点。
•凹模刃口直线部过长•内表面让位形状不适合(呈反锥形状)•凹模内部的表面较粗糙•凹模、模具垫板、模座的孔中心偏离造成台阶•冲裁废料相互连接,呈棍状下落时,堆积住让位孔•废料带有磁性特别是对薄板和小孔等进行冲裁时,因冲裁废料重量较轻,即使是一些小障碍也会导致废料堆积。
]关于防废料堆积型凹模:1) 防废料堆积型凹模的原理和特长作为防废料堆积的一个方法废料排出阻力(废料堆积的原因)<>三住的防废料堆积型凹模是因为切刃附近设有空气导入孔,通过和吸出装置并用,引发凹模内部方向朝下的压缩空气。
该压缩空气加强了废料排出力,起到进一步抑制废料堆积的作用。
作为吸出装置,请使用真空泵和吸尘器(提桶型吸尘器),或废料吸出装置。
[图2]2) 适用范围材质让位孔的形状杆径刃口直径标准形锥形DP钢相当于SKD11○-6~101.00 ~6.00SKH51○-3~50.50 ~2.50粉末高速钢○-6~101.00 ~6.00硬质合金V40○○3~100.50 ~6.00硬质合金精密级V40-○3~100.500~6.000超微粒子-○3~100.500~6.0003) 用于防废料回跳时通过追加工BC,缩短切刃(直线部的长度),增加凸模的嵌入量,通过压缩空气一片一片地吹落冲裁废料,起到防止废料回跳的作用。
(图3)原来的防废料回跳型凹模,不适用于断面修正以及被加工材料厚度不足0.1mm的场合。
而这些用途正可作为防废料回跳的对策使用。
(BC追加工仅适用于锥度型凹模。
)4) 注意事项•防废料堆积型凹模是和真空泵等吸出装置等组合使用作为前提条件的产品。
凹模本身并不能起到防废料堆积的效果。
•如果凹模上部的进气孔堆积了润滑油、切屑、垃圾等,将不能起到充分的防废料堆积的效果,所以请定期对凹模进行维护。
对于长期保管后的凹模,请在清除固体化了的润滑油和垃圾后再使用。
冷冲压连续模中防止废料回升措施的探讨

具工作部件 的寿命 , 而影 响模 具的精度 。为此 , 从 防止废料 回
升, 将有 利于生产 的顺利进行 , 有利于提高产品 品质 。本 文通 过对废料 回升原 因的分析 , 并结合生产实践 中的应 用 , 出数 提 种防止废料 回升措施 , 并分别 阐述其特点及适 用场合。
图 3 带顶料装 置的凸模
() 4 冲压规则 形状的废料 , 通过使 镶拼式凹模镶块型腔部 分互相错开 一定距离 , 或使 凹模 型腔上作卡料 凸起 , 留住废 而
料, 以保 证 冲头 形 状 保 持 不 变 , 冲压 件 上 的轮 廓 不 变 。 其 缺 点 但
( ) 于 较 大 的 冲 头 , 把 其 断 面 中 间 部 分 挖 空 , 减 少 冲头 中间的效果更佳 。 这样 这种措施适用于 冲头面
I . 凸模 2凹模 .
A真空带 .
积较 大 , 冲压材料较厚的情况下。图 3所示具有顶料装置的凸 模, 直接将废料顶下 , 使之不 能与 凸模粘 附着上升 。
图 1 冲孔 废料 回升示意 图
收 稿 日期 :0 0 0 - 5 2 1- 2 0
() 2 排样 时 , 通过改变切 废料 的顺 序 , 尽量将 形状规则 的 废料变成封闭轮廓 , 增加 整个 轮廓 的卡料力 , 废料不易跳 出。
22 冲 头设 计 时采 取 的 措 施 .
1 产 生原 因
在正 常的冲孔落料 的冲压工序 中,废料卡 紧在 凹模 的型 腔里 , 在后续废料 的推 动下 , 从模具 的落料孑 中落下。但 当凸 L 模 冲头对废料 的吸附力 大于 凹模 型腔对废料 的卡 紧力 时 , 废 料便随着凸模冲头 的上行 , 而跳 到模具 凹模表 面 , 产生 了废料 回升的现象。 主要原 因 , 冲压过程中凸模 冲头下表 面与废 其 是
- 1、下载文档前请自行甄别文档内容的完整性,平台不提供额外的编辑、内容补充、找答案等附加服务。
- 2、"仅部分预览"的文档,不可在线预览部分如存在完整性等问题,可反馈申请退款(可完整预览的文档不适用该条件!)。
- 3、如文档侵犯您的权益,请联系客服反馈,我们会尽快为您处理(人工客服工作时间:9:00-18:30)。
五金冲压模具跳废料的解决办法
浮料现象在五金冲压模具中是一种常见的不良之现象,浮料产生的原因是多种的,因此其解决方法也是多样的。有的废料是由于模具设计不良产生的,有的是由于原材料不良造成的,有的是因为冲压操作者造成的。需作出一个有效的快速的解决方案时,应先仔细研究其种类及原因。下面以鄙人在五金模具设计之中的经验与各位朋友分享与交流,有不当或不足之外请指教。
1、冲切冲头里加顶料针
在容易发生浮料的冲头里加装顶料针与弹簧,在分模的时候利用顶料针把废料顶在下模入子里。这种方法适合冲切形装比较大而原材料比较厚的场合。
2、下模入子与冲头做尖角凹坑
即本身的正常步距应该是等于冲头切离形状面,但是在冲切形状面靠近送料一端故意做成一个如三角形等异形凹坑而另一个切边按正常边设计,这样在一步冲切的时候,需要切离边由于有凹坑而会多出微小三角形的凸起而大于(实际上是超出)另一个切离边,这样再把相对应的冲头做圆角处理不形成冲切效果,多出来的三角边就会被拉进下模入子而强力抵住下模入子增大摩擦力从而防止反弹或抵止真空吸料。
二、浮料之原因
1、废料上扬之浮料
废料上扬的原因首先来分析一下力的来源,废料由于一般与冲头或下模刀口的形状相同,因此,废料在模具的入子内应该有一定的摩擦力存在,从冲切的原理上来说,废料在切离以后由于材料的塑性或者说弹性变形的存在其会恢复组织结构,换句话说其在无约束实际形状应该大于下模刀口形状,这也是为什么当把废料从入子里面取出来的后再也不能轻松的把废料再填充到下模入子里去的原因。如果促使废料上扬应该有一个往上的力量而且大于该摩擦力及张力总和。这个力量有可能来自两个方向,一是废料材料本身存在的张力或弹力,由于废料在冲切的过程中有折曲(简单说)塑形变形,因此当冲头脱离它时,其内部的张力会有一个反弹的力量,或许是向下或许是向上;二是来自外部的力量,这个力量也有两个方面,在冲头与下模入子切离时,冲头表面与原材料(及废料)紧密贴合在
业吸料器里;什么废料废屑通通进去,保险可靠。呵呵。
9、极薄材料0.10以下简单形状防浮
由于极薄材料的冲压间隙较小,上面一些防止废料浮料的方法不是十分合适,如顶针顶料、下模做凸点、工业吸料器等。
对于这种材料来说,一般是把下模入子设计成8-12'无直身,然后通过试模测试出哪些下模入子容易跳屑。再把模具拆下来,用长细顶针加金刚粉(钻石膏)小心在下模入子做成几个对称粗糙点。这种方法很管用的,不过需要钳工水平很高。
有利于废料落料。4、把冲头的切离面做成波纹形或者说粗糙面,可以用锉刀或电磨加工,增加空气量而减少真空量。
C、对于所有有可能或者产生浮料的冲切形状
上面B种方法(大多数是钳工加工的)有时候并不是可以完全解决问题的时,这时应该从设计上靠考虑加以解决
[废屑浮料之对策]
废悄浮料最主要是由于设计的不合理或者材料本身的原因造成的。
1、设计不合理方面
在冲切工序排样的时候尽量避免有重切、过切现象。由于五金模具一般都是用CAD来做设计的,在做一些工序的时候没有照顾好前面的工序已经有半加工。
பைடு நூலகம்
3、下模入子孔边作对称挤压点
通常在设计下模入子的时候会与冲头对等间隙配合,而为了防止浮料,在下模入子做出1对或2对对称点分别小于冲压间隙1/2左右,这样在冲切废料的时候由于小间隙冲压而把废料卡住在下模入子里,这种文法可以且放电加瘤或者线割方式来完成。
4、把下模入子做成无直边形
这种方法比较适合薄材料。一般在设计下模入子(刀口)的时候都会留有3-5mm的直边。而这种方法是没有直边直接做成8-15'斜度,因此废料是越向上间隙越小,而越往下间隙越大也就不容易向上跑料反弹了。
2、废屑上扬之浮料
废屑是如何产生的?它有几种情况,一是产品或废料的毛刺(或者称为毛头)的脱落;一是冲头或模具的其它部分与原材料的不正常刮伤或撞伤造成细小废料,这最主要是由于冲头在需要对原材料作出过度作用时而没有相对应的结构;三是由于原材料在冲压之前已经做了表面处理,而表面处理层与材料本身还是存在一定的非结构融合性的现象而会使材料的边缘分离脱落;还有一种是由于模具设计的不合理,存在二次冲切(重切)或者过小废料切削,一般来说冲切的宽度不应该小于1/3材料的厚度,这些过小的切削废料容易与主体大废料脱离或由于硬化崩断形成废屑。
B、冲切孔本身是形状简单
如圆孔、方孔等。这种情况下从废料浮料形成原因着手,一是改变反弹方向,二是减少真空面积。常有的方法如,1、把冲头磨成单边斜面或双边斜面,这样一可以使材料变形,使材料内部与外部的反弹力降低,二是降低了真空面积。2、还可在冲圆孔的时候在圆形冲头中央磨一个小的凸台,其作用与斜面一样,不过这种方法对圆孔比较有效一些。3、当切离边为三边或两边时,不需切离的冲头边做成一定的台阶,这样在冲压的时候可以先做一个有点折弯的动作使废料向下变形
3、废粉上扬的原因
废粉是原材料结构性原因造成的,前面有说过是铝基与黄铜基材料容易发生这种状况。对于原材料来说是没有办法,而形成这种的原因是冲头或入子的表面有粗糙度存在也就是说在一定放大的程度下其表面有凹坑。当冲头或入子接触原材料的时候,就会摩擦原材料(像锉刀锉铁一样)产生废粉了。
三、浮料之对策
一起与下模入子组成一个封闭的空间产生一个真空状态,当冲头上升的时候,破坏这一个真空状态因此在空气的负压的作用诱使废料与冲头一起上升产生废料上扬的现象;其次,在一般冲压过程中,在下模入子里面都有废料重叠的现象,当最新一片废料加入时,其它的废料本身的内力(反弹力)也会促使新废料上扬。所以当冲压速度非常低,而且无废料积料的现象存在的进候,废料类的浮料现象很少发生。这也是其原由之一。
这一种与冲头吹气原理相似又有不同,具体做法是在下模垫板做出气道,然后在需要吹气的落料孔钻向下45的斜孔贯穿落料孔,而气道与落料孔不通(切记这一点),利用空气住下吹的时候形成一个负压空间把废料吸下去。这种方法适用薄材料。
[浮料之对策]
8、采用外吸力吸废料
方法是在下模模座下再增加一块下模辅助板把所有有可能甚至所有冲切部位的落料孔在辅助板上做成一个大落料框,焊上一个类似漏斗的料管,然后用工业吸料器的连接在料管上。通过吸料器的吸力把所有的废料都吸入工
一、浮料之种类
二、浮料之原因
三、浮料之对策
今天先讲浮料之种类,对于浮料来说,本人依据其大小与形成因素把其分为三种
1、废料之上扬现象
废料是指在单一冲切(成型)工序中脱离产品之部分。其大小一般情况下与下模刀口形状相同。其面积与危害在三种现象中是最大的。当这种现象出现的时候有可能使冲头或刀口崩裂甚至崩断,有可能使产品之导正针断裂,还有可能使模板产生裂纹。
1、废料浮料之对策
通过以上两则的现象与形成原因,因此可以分析出模具的对策。先对每一种废料浮料的方法来做一下说明。
A、排料设计不当之引起的浮料
这种浮料最主要出现在排料的过程中,大多数产生了比较简单的冲切形状。如方形、较小边异形废料。
这个时候一般应该在设计时候故意做成工艺缺口,如梯形、燕尾形。使简单的冲切形状复杂,加大废料的摩擦力阻止废料反弹与真空吸料。
5、把下模入子留用3mm切离直边余下部分用放电的方法把落料部分加大使废料无积累,加长冲切冲头的长度。每一次冲切都把废料冲离到落料区,使废料不可能向上浮料。
6、冲头如加装顶针一样加吹气孔与吹气装置。由于吹气装置可以和冲床联动控制吹气的时间,因此可以适用较薄材料上,这一点是顶针防浮料无法比拟的。
7、下模或下模垫板加吹气槽
2、废屑之上扬现象
废屑是指单一工序中产生的非整体产品或是非整体废料。其大小相对比较小,像产品之毛边(毛刺)脱落形成;冲切废料细丝等。出现这种情况时反映在产品出现擦伤、刮伤、凹坑或凹痕的现象。这种情况最主要是对产品造成不良,但这种情况在模具生产是最为常见也是比较隐蔽的。
3、废粉之上扬现象
废粉是指单一工序中因冲头与产品之间的摩擦产生的微细粉屑。这种现象在产生初期肉眼一般难以发现,只有当积累一种程度时,冲头与入仔发生颜色变化时才容易辨别。当废粉达到一定程度时,容易造成冲头断裂或者入模入子崩裂。最容易发生在黄铜基与铝基材中。