防止跳废料的方法
钣金加工厂的模具跳废料解决方法
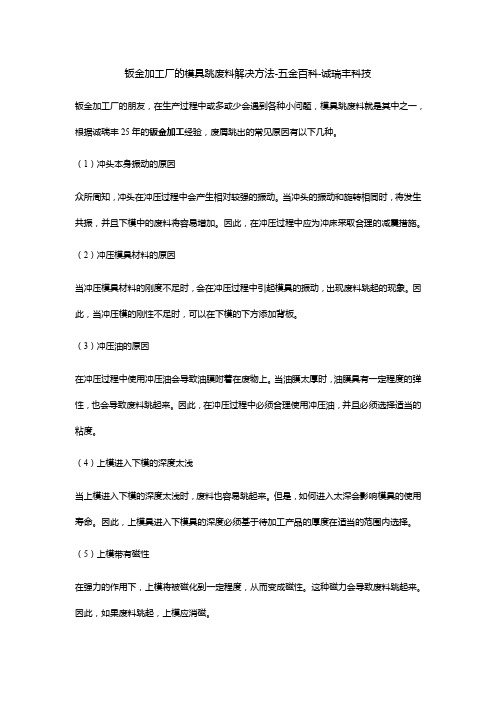
钣金加工厂的模具跳废料解决方法-五金百科-诚瑞丰科技钣金加工厂的朋友,在生产过程中或多或少会遇到各种小问题,模具跳废料就是其中之一,根据诚瑞丰25年的钣金加工经验,废屑跳出的常见原因有以下几种。
(1)冲头本身振动的原因众所周知,冲头在冲压过程中会产生相对较强的振动。
当冲头的振动和旋转相同时,将发生共振,并且下模中的废料将容易增加。
因此,在冲压过程中应为冲床采取合理的减震措施。
(2)冲压模具材料的原因当冲压模具材料的刚度不足时,会在冲压过程中引起模具的振动,出现废料跳起的现象。
因此,当冲压模的刚性不足时,可以在下模的下方添加背板。
(3)冲压油的原因在冲压过程中使用冲压油会导致油膜附着在废物上。
当油膜太厚时,油膜具有一定程度的弹性,也会导致废料跳起来。
因此,在冲压过程中必须合理使用冲压油,并且必须选择适当的粘度。
(4)上模进入下模的深度太浅当上模进入下模的深度太浅时,废料也容易跳起来。
但是,如何进入太深会影响模具的使用寿命。
因此,上模具进入下模具的深度必须基于待加工产品的厚度在适当的范围内选择。
(5)上模带有磁性在强力的作用下,上模将被磁化到一定程度,从而变成磁性。
这种磁力会导致废料跳起来。
因此,如果废料跳起,上模应消磁。
(6)模具间隙的不对称当上模具和下模具对准时,间隙是不对称的,这使得在冲压过程中废料周围的横截面不一致,从而导致在整个废料上的力不均匀并且使废料跳上。
因此,设置切刀时,打孔间隙要对称。
(7)刀口出现磨损在冲压过程中,刀刃被磨损,模具刀刃产生倒锥,这也将导致废料跳起。
因此,在模具磨损时,刀刃应及时变尖。
(8)钣金加工厂的模具设计问题在模具设计的开始,考虑还不够全面,导致模具设计不合理。
高速冲压中防止废料回升的几个解决方法

冲
模 技 术
・
以P G 方式加工 , 凹模刃 口为分体式 的 , 才能实现 上述结构 , 图3 a 中H值一般为 凸模切人深度 的 7 0 %,
件
且适合 于 冲裁 间隙< O . O l m m; 图3 b 适合 于冲裁间 隙>
0. O1 5mm 。
3 . 3 外形 简单 光滑 的 凸模 刃 口设 计 ( p r o i f l e d i e
表1 给 出了沟槽角度与宽度 的推荐值 ( 凹模镶件
厚度为 6 . 5 am时 , r D i e i n s e r t t h i c k n e s s = 6 . 5 m m) 。
料 厚
“
x3
4
表 1 沟槽 角度 与宽度的推荐值
角度参考 值( 凹模 厚度= 6 . 5 0 0 )
n= = = ¨U №
板厚 … t ’ x 3
压 入 部“ ” O . 2 O - 2 0 - 2 O - 3 0 . 4 0 _ 4 O . 5 0 . 5 O . 5 0 . 5 0 . 6 O . 6 O . 6 O . 6
图 6 冲 裁 外 形 的 凸 凹 模 参 数
・
冲
模 技
术
・
就 占据 了他 们 6 0 %以上 的修 模 时间 , 通常处 理跳 废 料 的方 法有 凸模 加 气 孔 , 漏料 孔 加装 吸尘 器 , 凸模 的平 刃 口改 为斜 刃 口或锥形 刃 口, 凹模刃 口钓鱼 法 等等 , 这 些 都是 冲 压工 厂 处理 跳 屑 常用 方法 , 不 再 赘述 , 在 此本 文将 主要介 绍几种 基 于 凹模 刃 口不 同
. 1 5 m m; 当板 厚 > 0 . 5 mm, R = 0 . 3 5 mm。 ( 2 ) 冲裁外形的加工方式为光学 曲线磨 ( P G ) , 如 0 ( 3 ) 沟槽 深 度 : 一般的 , 其 值 等 于 冲 切 间 隙 图5 所示 。 ( c u t t i n g c l e a r a n c e ) 或取 板 厚 的 5 %。
高速级进冲压中废料回跳问题的解决方案

高速级进冲压中废料回跳问题的解决方案近年来,随着工业生产的持续发展,高速级进冲压成为传统级进冲压的淘汰,其中废料回跳问题也逐渐出现,严重影响冲压生产率和质量。
废料回跳指的是在高速级进冲压过程中,由于模具的废料板积聚在模具表面,当模具运动到最高点时,废料板弹起,被模具表面弹起至上一个模具表面,从而影响冲压质量,并损害设备。
二、问题分析
废料回跳主要是由于模具设计原因造成,模具制造过程中模具本身质量可能存在缺陷,从而导致模具表面缺乏摩擦力,废料板在模具表面堆积,其冲压膨胀率大于模具,这样废料板就容易被模具表面弹起至上一个模具表面,制造过程中废料会被不断叠加,造成废料回跳问题。
此外,在冲压过程中,由于模口大小不同,加上模具不同的运动速度,会导致冲压力度及冲压水平的不均匀,不仅会增加冲压失效率,也容易使冲压件面出现较大的凹脊,导致废料回跳问题。
三、解决方案
(1)模具制造方面:改进模具设计,将模具表面改为模具边缘,使模具表面能有足够的摩擦力,防止废料板积聚,减少废料回跳现象。
(2)冲压过程方面:根据情况,采取不同冲压力度和冲压水平,将应力平均分布在冲压制件上,避免冲压失效,减少废料回跳现象。
(3)模具清理方面:经常清理模具表面,定期更换模具零件,以确保模具表面摩擦力充足,及时清理废料残留,防止废料回跳。
四、结论
高速级进冲压中废料回跳问题是一个很复杂的问题,解决这个问题需要从模具制造,冲压过程和模具清理三个方面入手,综合运用这些技术,可以有效解决高速级进冲压中废料回跳问题。
薄板冲模排样设计及防跳废料解决方案

薄板冲模排样设计及防跳废料解决方案一、引言介绍薄板冲模排样设计及防跳废料解决方案的研究意义,阐明本文的主题和目的。
二、薄板冲模设计原则1. 薄板冲模设计的特点和要求2. 薄板冲模设计的主要原则3. 薄板冲模设计的工艺路线三、薄板冲模排样设计1. 薄板冲模排样的概念和意义2. 薄板冲模排样的最优化设计方法3. 实际案例分析四、防跳废料解决方案1. 防止跳废料的现象及原因2. 解决跳废料的方法和措施3. 实际案例分析五、结论与展望总结薄板冲模排样设计及防跳废料解决方案的研究成果和启示,探讨未来的研究方向和应用前景。
第一章引言薄板冲模技术是现代制造业中应用广泛的一项成形工艺。
因其具有形状复杂、速度快、高效率等特点,被广泛用于制造汽车、电子设备、航空航天、建筑材料等领域。
薄板冲模排样设计及防跳废料解决方案,是目前薄板冲压产业中比较重要的问题。
因此,深入研究和探索薄板冲模排样设计与防跳废料解决方案,对于提升薄板冲压产业的发展和技术水平具有非常重要的意义。
本论文将分为五个章节对薄板冲模排样设计及防跳废料解决方案进行阐述。
第一章是引言,主要介绍本文研究的背景、目的及研究价值。
第二章是薄板冲模设计原则,将从薄板冲模设计的特点和要求、主要原则和工艺路线三个方面对该技术进行介绍。
第三章是薄板冲模排样设计,主要针对薄板冲模的最优化设计方法进行探讨,并结合实际案例进行分析。
第二章薄板冲模设计原则1. 薄板冲模设计的特点和要求薄板冲模设计是一项较为复杂和高度技术性的工作,其具有以下的特点:(1)成形过程难以掌控:冲压工艺中,许多因素都会对成形过程产生影响,例如材料锁紧、模具刚度、润滑和摩擦等。
这些因素会影响零件的尺寸、成形质量和形状精度等。
(2)生产环节复杂:备料、冲床调整、模具调整等生产环节都需要精心的配合,一旦环节出现一些小的疏漏都可能导致失败。
(3)工艺参数要求精确:薄板冲模生产中,需要控制多个工艺参数以确保生产的质量。
冲孔跳废料的解决方案
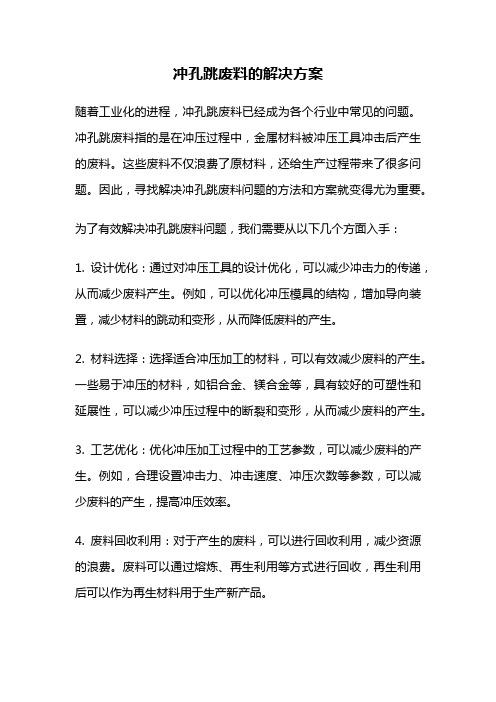
冲孔跳废料的解决方案随着工业化的进程,冲孔跳废料已经成为各个行业中常见的问题。
冲孔跳废料指的是在冲压过程中,金属材料被冲压工具冲击后产生的废料。
这些废料不仅浪费了原材料,还给生产过程带来了很多问题。
因此,寻找解决冲孔跳废料问题的方法和方案就变得尤为重要。
为了有效解决冲孔跳废料问题,我们需要从以下几个方面入手:1. 设计优化:通过对冲压工具的设计优化,可以减少冲击力的传递,从而减少废料产生。
例如,可以优化冲压模具的结构,增加导向装置,减少材料的跳动和变形,从而降低废料的产生。
2. 材料选择:选择适合冲压加工的材料,可以有效减少废料的产生。
一些易于冲压的材料,如铝合金、镁合金等,具有较好的可塑性和延展性,可以减少冲压过程中的断裂和变形,从而减少废料的产生。
3. 工艺优化:优化冲压加工过程中的工艺参数,可以减少废料的产生。
例如,合理设置冲击力、冲击速度、冲压次数等参数,可以减少废料的产生,提高冲压效率。
4. 废料回收利用:对于产生的废料,可以进行回收利用,减少资源的浪费。
废料可以通过熔炼、再生利用等方式进行回收,再生利用后可以作为再生材料用于生产新产品。
5. 自动化技术:引入自动化技术可以提高冲压加工的精度和效率,减少废料的产生。
例如,采用数控冲床、机器人等自动化设备,可以实现精确控制和高效生产,减少废料的产生。
6. 质量控制:加强冲压加工过程的质量控制,可以减少废料的产生。
通过严格控制冲压工艺参数、加强设备维护和保养、加强操作培训等措施,可以提高产品质量,减少废料的产生。
冲孔跳废料问题不仅涉及到生产效率和资源利用的问题,还涉及到环境保护和可持续发展的问题。
有效解决冲孔跳废料问题,对于提高生产效率、降低生产成本、保护环境都具有重要意义。
因此,各个行业应该重视冲孔跳废料问题,积极寻找解决方案,推动冲压加工技术的发展和进步。
解决冲孔跳废料问题需要综合考虑设计优化、材料选择、工艺优化、废料回收利用、自动化技术和质量控制等方面的因素。
跳屑原因及对策

Page: 9
E. 刀口的内宽加工成比废料的长度小0.02-0.04mm, 使废料 承弯曲状卡在刀里面,防止跳料.(如图八)
Page: 10
2. 因冲头长度不够而长生跳料:
把握一个原则:按图纸的要求. 但对于冲头与废料接触面积 太大所造成的跳料,可改变冲头形状。(如图九) 以减少接 触面积。
A
B
沖 頭 GAP=T(4~6)%
Page: 4
B模具很顺畅的情况下,由于废料与刀口的内面摩擦次数 多,而把刀口的内面磨损,造成刀口间隙过大. (如图三)
2.冲头的长度太短及冲头与落料接触面太大.
Page: 5
3.刀口的松动.
(如图四)
模板
刀口
模板
间隙
间隙
4.端子油加得太多或端子油黏度太大.
Page: 6
A.设计时把刀口的间隙放在下限上.即GAP=(4%~6%)T. B.把刀口的上端设计为2~3mm的直刀位, 下部加工成斜度 (0.5°-1.0°),增强刀口的耐磨度. (如图五) 直刀位
Page:8
C.把刀口由整体式设计为分体式. (如图六)
A
A
B
D.把刀口的厚度设计为2~3mm,便于废料及时脱落,减少 跳料机会. (如图七)
2.凸模加工斜度角。A或B,C使废料形变或减少与凸模的接触面积,针对1,2,5.
3.凸模加弹钉销。将废料始终按压在凹模腔内,对所有原因造成跳废料皆有效。
4. 安装吸废料机。
page 15
0.002~0.005MM
Page: 13
6. 对于新换过的刀口和研磨过的刀口产生跳料 对策为:
A.在刀口的棱角处用铜片来回刮.
B.用红宝石抛刀口棱角处.
冲孔跳废料的解决方案

冲孔跳废料的解决方案1. 方案目标冲孔跳废料是制造业中常见的废料问题之一。
解决这个问题的目标是降低废料产生量,提高生产效率,减少成本,并且对环境友好。
2. 实施步骤2.1 分析冲孔跳废料产生原因首先,需要对冲孔跳废料产生的原因进行分析。
可能的原因包括: - 设计问题:产品设计不合理,导致冲孔跳废料的产生。
- 工艺问题:制造过程中的冲孔工艺不合理,导致冲孔跳废料的产生。
- 材料问题:使用的材料质量不佳,容易产生冲孔跳废料。
2.2 优化产品设计根据冲孔跳废料产生的原因,可以通过优化产品设计来减少废料的产生。
具体步骤如下: - 与设计团队合作,分析产品设计中存在的问题。
- 优化产品设计,减少冲孔跳废料的产生。
- 使用先进的设计软件和工具,模拟冲孔过程,以预测和避免冲孔跳废料的产生。
2.3 优化冲孔工艺除了产品设计,冲孔工艺也是冲孔跳废料产生的重要原因之一。
优化冲孔工艺可以减少废料的产生。
具体步骤如下: - 分析当前的冲孔工艺,找出存在的问题。
- 优化冲孔工艺,采用合适的冲孔参数和工艺流程。
- 使用先进的冲孔设备和工具,提高冲孔的精度和效率。
2.4 优化材料选择材料的选择对废料产生有重要影响。
选择合适的材料可以减少冲孔跳废料的产生。
具体步骤如下: - 与供应商合作,了解不同材料的特性和适用范围。
- 选择质量较好的材料,避免杂质和缺陷。
- 针对不同的产品和工艺要求,选择适合的材料。
2.5 建立废料回收系统即使经过优化,仍然难以完全消除冲孔跳废料的产生。
建立废料回收系统可以有效减少废料的浪费,并且对环境友好。
具体步骤如下: - 设计并建立废料收集设备和系统,将产生的废料进行收集和分类。
- 开发废料处理方法,例如回收、再利用、再加工等。
- 与废料处理公司合作,确保废料得到妥善处理,符合环保标准。
2.6 培训和监督为了确保方案的可行性和效率,培训和监督是必不可少的。
具体步骤如下: - 为相关员工提供培训,使其了解冲孔跳废料问题和解决方案。
防废料回跳型凹模
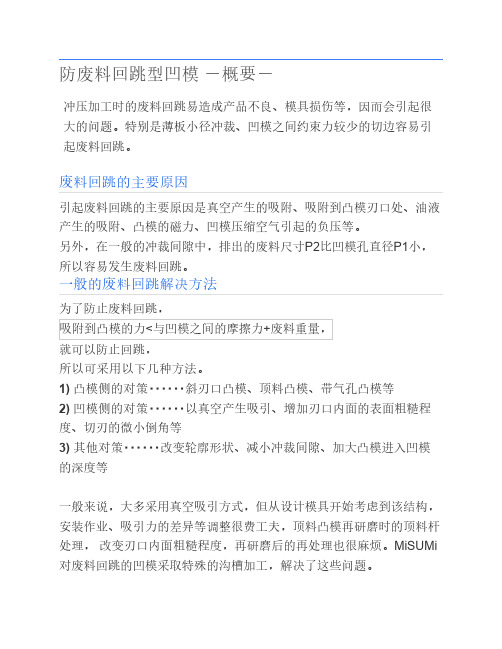
防废料回跳型凹模-概要-冲压加工时的废料回跳易造成产品不良、模具损伤等,因而会引起很大的问题。
特别是薄板小径冲裁、凹模之间约束力较少的切边容易引起废料回跳。
废料回跳的主要原因引起废料回跳的主要原因是真空产生的吸附、吸附到凸模刃口处、油液产生的吸附、凸模的磁力、凹模压缩空气引起的负压等。
另外,在一般的冲裁间隙中,排出的废料尺寸P2比凹模孔直径P1小,所以容易发生废料回跳。
一般的废料回跳解决方法为了防止废料回跳,吸附到凸模的力<与凹模之间的摩擦力+废料重量,就可以防止回跳,所以可采用以下几种方法。
1) 凸模侧的对策・・・・・・斜刃口凸模、顶料凸模、带气孔凸模等2) 凹模侧的对策・・・・・・以真空产生吸引、增加刃口内面的表面粗糙程度、切刃的微小倒角等3) 其他对策・・・・・・改变轮廓形状、减小冲裁间隙、加大凸模进入凹模的深度等一般来说,大多采用真空吸引方式,但从设计模具开始考虑到该结构,安装作业、吸引力的差异等调整很费工夫,顶料凸模再研磨时的顶料杆处理,改变刃口内面粗糙程度,再研磨后的再处理也很麻烦。
MiSUMi 对废料回跳的凹模采取特殊的沟槽加工,解决了这些问题。
图1 防废料回跳型冲模的沟槽形状防废料回跳型凹模的原理和特长1) 防废料回跳型凹模的原理在凹模内侧面,将2处以上的倾斜沟从中心开始向反方向加工。
在冲裁工序初期,冲裁废料会形成和凹模倾斜沟相对应的小突起。
随着凸模下降,若进一步向下面压入,突起部分会被凹模侧面压缩(压平作用),摩擦力增大,从而防止废料回跳。
另外,倾斜沟不是以螺旋状,而是向反方向加工,所以不会随着凸模上升,引起旋转和废料回跳。
2) 刃口形状以及凹模的种类本产品可以有效用于容易产生废料回跳的圆形以及各种异形,而且对和凹模之间约束力较小的边缘切割形状(切边)也很有效果。
3) 操作简单,总体成本降低只要将防废料回跳型凹模装入模具中,就可以发挥作用,所以也可以用于原有模具中,不需要另费功夫再研磨,也不需要再研磨后的再处理。
连续冲压中跳废料的防止措施课件

根据冲压工艺和产品要求,选用具有良好润滑性能和分离性 能的专用冲压油。冲压油能够有效降低废料与模具之间的摩 擦,减少跳动现象。
定时喷涂润滑剂
在连续冲压过程中,定时喷涂润滑剂于模具表面,保持模具 的良好润滑状态,减少废料的粘附和跳动。喷涂润滑剂的时 间和频率需要根据实际情况进行调整,以确保最佳效果。
连续冲压中跳废料的 防止措施课件
目录
• 连续冲压工艺简介 • 跳废料问题描述 • 防止跳废料的技术措施 • 操作管理及注意事项 • 案例分析与实践 • 总结与展望
01
连续冲压工艺简介
连续冲压工艺定义
• 定义描述:连续冲压工艺是一种金属加工方法,通过在冲床上使用连续模具对金属板材进行 连续的冲裁、弯曲、拉伸等成形操作,从而生产出具有特定形状和功能的零部件。
THANKS
感谢观看
06
总结与展望
课程总结
系统性与实践性兼具的课件
• 课件内容结合了实际生产经验和专业研究成果,确保 学员能够深入了解跳废料问题的本质,并能在实际工 作中运用所学知识进行有效应对。
• 课件采用了讲解、案例分析、实践操作等多种教学 方法,使学员在多角度、多层次上掌握跳废料的防 止措施。
• 本课件详细介绍了连续冲压过程中跳废料的产生原 因和影响,通过系统性的理论分析和实践性的防范 策略,为学员提供了一套全面且实用的学习资料。
案例三:操作管理在防止跳废料中的作用
操作管理重要性
加强操作管理可以有效减少操作失误,避免因操作不当引 起的跳废料问题。
管理措施
制定严格的操作规程,加强员工培训,建立奖惩制度等。
实践经验
通过实施有效的操作管理,可以显著提高员工操作的规范 性和准确性,降低跳废料现象的发生概率。同时,也有助 于提升企业的整体管理水平和市场竞争力。
五金冲压的废料是什么材质

五金冲压废料形成的原因
所谓废料是指冲压设备在运行时,五金冲压模具本应冲至下模的现象,而通过下模废孔掉落的废料被带到模具表面影响生产的现象。
一旦模具出现跳跃,废料就会冲破皮带或冲头、刀口,影响冲压件的质量,降低模具的使用寿命,降低生产效率,这是最常见也是最令人担心的问题。
五金冲压时废料形成原因
其它因素造成
1 真空吸尘器,将吸尘器用于清除废物,防止跳跃废物。
2 必须保持冲头和刀刃的锋利度,适量添加冲压油,都有助于防止跳跃浪费。
预防跳废料的方法
1.减少冲头与五金冲压件的接触面积
2 在产品的接触面上插入冲孔。
3 对于大但形状不规则的冲头,可以在冲头中间挖一个洞以减少接触面积。
4 冲头磨异形。
5 在模具的设计中,在冲头中间加入吹气孔,防止带材的吹气。
6 即如果打孔材料是SKD11,可以在打孔器上添加弹簧销以防止碎裂。
7 增加刀刃和废料之间的摩擦力
8 对于嵌入物或组合刀口,可在刀片边缘下1mm左右用盖针“覆盖”,以增加刀口中废料的摩擦。
9 对于侧边、进料站边缘等工艺辅助步骤,可适当复杂废料的形状,以增加废料在凹模中的夹紧力,防止切屑跳跃。
10 在高速冲压过程中,由于冲裁速度高(800 m/s以上)和冲裁过程中的冲压油等因素,冲头与废料位置之间形成局部真空,尤其是冲压材料非常薄时。
由于废料本身重量轻,具有刀刃
的摩擦力很小,在冲裁过程中,会用冲床将废料带到模具表面,并出现跳料浪费的现象。
11 冲角,钝化或过度使用冲压油,薄料和冲孔的有效冲压等都太短,都会造成跳槽浪费。
高速冲压防冲孔废料回跳法
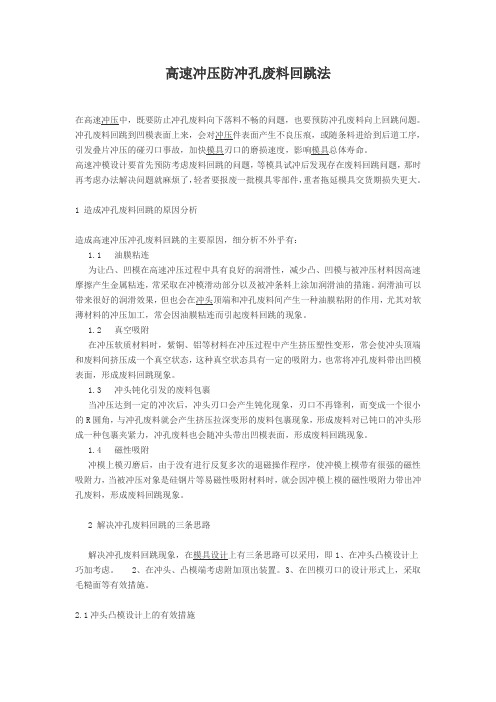
高速冲压防冲孔废料回跳法在高速冲压中,既要防止冲孔废料向下落料不畅的问题,也要预防冲孔废料向上回跳问题。
冲孔废料回跳到凹模表面上来,会对冲压件表面产生不良压痕,或随条料进给到后道工序,引发叠片冲压的碰刃口事故,加快模具刃口的磨损速度,影响模具总体寿命。
高速冲模设计要首先预防考虑废料回跳的问题,等模具试冲后发现存在废料回跳问题,那时再考虑办法解决问题就麻烦了,轻者要报废一批模具零部件,重者拖延模具交货期损失更大。
1 造成冲孔废料回跳的原因分析造成高速冲压冲孔废料回跳的主要原因,细分析不外乎有:1.1 油膜粘连为让凸、凹模在高速冲压过程中具有良好的润滑性,减少凸、凹模与被冲压材料因高速摩擦产生金属粘连,常采取在冲模滑动部分以及被冲条料上涂加润滑油的措施。
润滑油可以带来很好的润滑效果,但也会在冲头顶端和冲孔废料间产生一种油膜粘附的作用,尤其对软薄材料的冲压加工,常会因油膜粘连而引起废料回跳的现象。
1.2 真空吸附在冲压软质材料时,紫铜、铝等材料在冲压过程中产生挤压塑性变形,常会使冲头顶端和废料间挤压成一个真空状态,这种真空状态具有一定的吸附力,也常将冲孔废料带出凹模表面,形成废料回跳现象。
1.3 冲头钝化引发的废料包裹当冲压达到一定的冲次后,冲头刃口会产生钝化现象,刃口不再锋利,而变成一个很小的R圆角,与冲孔废料就会产生挤压拉深变形的废料包裹现象,形成废料对已钝口的冲头形成一种包裹夹紧力,冲孔废料也会随冲头带出凹模表面,形成废料回跳现象。
1.4 磁性吸附冲模上模刃磨后,由于没有进行反复多次的退磁操作程序,使冲模上模带有很强的磁性吸附力,当被冲压对象是硅钢片等易磁性吸附材料时,就会因冲模上模的磁性吸附力带出冲孔废料,形成废料回跳现象。
2 解决冲孔废料回跳的三条思路解决冲孔废料回跳现象,在模具设计上有三条思路可以采用,即1、在冲头凸模设计上巧加考虑。
2、在冲头、凸模端考虑附加顶出装置。
3、在凹模刃口的设计形式上,采取毛糙面等有效措施。
裁切模跳废料的解决方法

裁切模跳废料的解决方法全文共四篇示例,供读者参考第一篇示例:裁切模是一种常用于生产工业制品的模具设备,它能够将原材料按照设计要求裁切成所需尺寸和形状。
裁切模在使用过程中难免会产生一些废料,这些废料如果不得当处理可能会给生产过程和环境带来一定影响。
有效解决裁切模产生的废料问题,是提高生产效率和保护环境的关键之一。
一、裁切模产生废料的原因1. 设计不合理:裁切模的设计不合理,导致裁切后产生大量废料无法利用。
2. 材料选择不当:原材料质量差或者材料种类不合适,导致裁切模裁切效果不佳,产生大量废料。
3. 模具磨损:长时间使用或操作不当会导致裁切模的磨损,影响裁切效果,增加废料产生。
4. 人为因素:操作人员技术不过硬或者操作不规范,也会导致裁切模产生大量废料。
二、裁切模废料的解决方法1. 优化设计:通过优化裁切模的设计,减少废料产生。
合理设计模具结构,减少裁切余料,提高利用率。
2. 选择优质材料:选用质量好的原材料,减少裁切损耗,降低废料率。
3. 定期维护:定期对裁切模进行维护保养,保持模具表面的平整度和尺寸精度,减少因磨损而产生的废料。
4. 技术培训:加强操作人员的培训和技术水平提高,规范操作流程,减少因人为因素而产生的废料。
5. 废料回收利用:对裁切模产生的废料进行分类、收集和处理,实现资源的再利用。
可以将废料回收用于再加工或者其他用途,减少资源浪费。
6. 环保意识:公司应加强环保意识,建立环保管理制度,减少裁切模产生的废料对环境的影响。
通过以上方法的合理应用,可以有效解决裁切模产生废料的问题,提高生产效率,降低成本,保护环境,实现可持续发展。
公司在使用裁切模的过程中应积极探索新的技术和方法,不断优化生产流程,提高裁切模的利用率,为企业发展和社会进步做出更大的贡献。
第二篇示例:裁切模具在制造行业中起着非常重要的作用,能够帮助生产出符合设计要求的产品。
在使用过程中会产生大量的废料。
为了减少废料对环境的影响,提高资源利用效率,解决裁切模具废料的问题变得尤为重要。
3如何防止跳屑

如何預防跳屑﹑堵屑在產品類別日益增多的情況下,為了滿足客戶對產品的大量需求,衝壓加工逐步的向高速化生產發展,在日常的工作中由於人,地,物料,沖床,模具,管理等的種種差異與變化,衍生出許多技術障礙,模具在大量生產中的跳屑和堵屑便是其中一例.隨著衝壓團隊經驗的不斷累積,對較易發生跳屑和堵屑的變因已基本掌握並加以控制,以下是針對模具在生產中發生跳屑和堵屑的原因及改善的措施,希望藉此機會與同行共同探討衝壓加工的特性,使既有的技術得到擴展.什麼是跳屑?由於衝壓模具在高速衝切時,衝頭沖入材料, 衝頭四周壓縮材料,而衝頭引起跳屑的主要原因:b.衝切間隙不當:衝切間隙過大或不均時,沖頭對材料沖切力較小.沖下的廢料外形尺寸比模仁小.這樣廢料對模仁的咬合力也就較小.所以廢料就易從下模模仁中跳出.c.切削油選用及用量:切削油選用:一般根據材質的不同选用不同的切削油.例如預鍍材和磷青銅就要使用不同粘度的切削油.在生產時跳屑嚴重的話一般只把切削油加在材料的下表面,以防止廢料被下料沖子粘住.切削油的用量: 切削油的用量與衝切速度有很大的關係.SPM<400時每隔4秒一滴400<SPM<700時每隔3秒一滴SPM>700時每隔2秒一滴d.衝切速度过高易造成跳屑.e.下料沖子及下料刀口过於鋒利,廢料的切斷面光亮帶多而毛刺很少,與入塊之間的磨擦力过小,易被下料沖子吸附出入塊造成跳屑.f.下料沖子研磨后總長度过短造成衝切深度过淺,廢料接近下料入塊的上表面,極易被下料沖子吸附出入塊造成跳屑.g.因下料入塊在設計時是做成有落料斜度的,經常研磨后高度过低間隙變大造成跳屑.異h.異物附在銅材上被帶進入模具.i.材質越硬越容易產生跳屑.j.因振動而使模仁內原本粘在一起的廢料分散產生跳屑.下料沖子與下料入塊的間隙5%以下時: 可以增加切斷面,而切斷面與模仁之間的接觸面積也可以增大.下料沖子外形有小於2倍料厚的弧度.并且是凹角的話. 可以得到較長的切斷面.下料沖子與下料入塊的間隙為5%以上時:大部分的材料沖切出來的尺寸會比下料入塊外形尺寸小.所以可以推定其和模仁的咬合力會較小.i. 下料入塊選用適當的落料斜度:用光學磨床研磨的分割式入塊落料斜度為0.1°用線割的整體式入塊落料斜度為0.5°(如圖10)k.增設跳屑檢知:在下模板(D05A)上加裝檢知器.若發生跳屑,機台則會馬上停機.避免造成擠料.崩沖子等情況的發生.什麼是堵屑?模具在高速運動中,被沖切下來的廢料附著在模仁側壁而產生屑料堵塞.堵屑造成的影響:由於模具在高速運動,所以一旦堵屑就會發生擠料,沖頭崩斷下模入塊崩裂.堵屑對模具的損害很大.引起堵屑的主要原因:a.切削油用量過大造成被沖切下來的廢料附著在模仁側壁而產生屑料堵塞.b.下模落料框口尺寸過小或錯位使廢料不能順暢落下.(如圖12.13)以上改善的措施僅僅是很少的一部份,還有更多更加新穎的方法來等待我們去發掘.這就要求我們不能默守陳規,只有突破才能發展.愿以上談到的一些經驗能和同行們一起分享.審閱:。
冲压模具跳废料的原因分析,冲压模具跳料怎么修时间
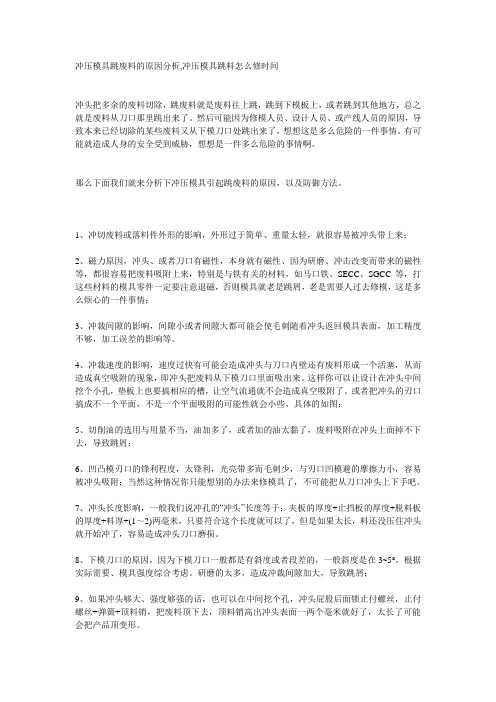
冲压模具跳废料的原因分析,冲压模具跳料怎么修时间冲头把多余的废料切除,跳废料就是废料往上跳,跳到下模板上,或者跳到其他地方,总之就是废料从刀口那里跳出来了。
然后可能因为修模人员、设计人员、或产线人员的原因,导致本来已经切除的某些废料又从下模刀口处跳出来了,想想这是多么危险的一件事情。
有可能就造成人身的安全受到威胁,想想是一件多么危险的事情啊。
那么下面我们就来分析下冲压模具引起跳废料的原因,以及防御方法。
1、冲切废料或落料件外形的影响,外形过于简单、重量太轻,就很容易被冲头带上来;2、磁力原因,冲头、或者刀口有磁性,本身就有磁性、因为研磨、冲击改变而带来的磁性等,都很容易把废料吸附上来,特别是与铁有关的材料,如马口铁、SECC、SGCC等,打这些材料的模具零件一定要注意退磁,否则模具就老是跳屑,老是需要人过去修模,这是多么烦心的一件事情;3、冲裁间隙的影响,间隙小或者间隙大都可能会使毛刺随着冲头返回模具表面,加工精度不够,加工误差的影响等。
4、冲裁速度的影响,速度过快有可能会造成冲头与刀口内壁还有废料形成一个活塞,从而造成真空吸附的现象,即冲头把废料从下模刀口里面吸出来。
这样你可以让设计在冲头中间挖个小孔,垫板上也要搞相应的槽,让空气流通就不会造成真空吸附了。
或者把冲头的刃口搞成不一个平面,不是一个平面吸附的可能性就会小些,具体的如图:5、切削油的选用与用量不当,油加多了,或者加的油太黏了,废料吸附在冲头上面掉不下去,导致跳屑;6、凹凸模刃口的锋利程度,太锋利,光亮带多而毛刺少,与刃口凹模避的摩擦力小,容易被冲头吸附;当然这种情况你只能想别的办法来修模具了,不可能把从刀口冲头上下手吧。
7、冲头长度影响,一般我们说冲孔的“冲头”长度等于:夹板的厚度+止挡板的厚度+脱料板的厚度+料厚+(1~2)两毫米,只要符合这个长度就可以了,但是如果太长,料还没压住冲头就开始冲了,容易造成冲头刀口磨损。
8、下模刀口的原因,因为下模刀口一般都是有斜度或者段差的,一般斜度是在3~5°,根据实际需要、模具强度综合考虑。
防止冲压生产中跳屑的措施

防止冲压生产中跳屑的措施我在这冲压生产的车间里摸爬滚打这么多年了,跳屑这事儿啊,就像个调皮捣蛋的小鬼,时不时就冒出来给咱添乱。
我就寻思着,咋能把这跳屑给制住呢?咱先说说这模具。
模具就像咱干活的家伙事儿,得拾掇得利利索索的。
我瞅着那模具的间隙,这间隙要是不合适,就跟人穿的鞋子不合脚似的,那跳屑就有了可乘之机。
我就跟旁边的小李说:“小李啊,你看这模具间隙,得好好调整调整,大一点小一点都不行,就跟咱做饭放盐似的,得恰到好处。
”小李挠挠头,看着那模具,眼睛瞪得大大的,像是要把那模具看穿了似的,说:“刘师傅,这可不好把握啊。
”我就拍拍他的肩膀,说:“小伙子,这就得靠经验喽,多摸摸,就像摸自家孩子的脾气一样。
”还有那冲裁速度,这速度啊,快了慢了都可能引起跳屑。
我就想起有一次,新来的小王,冒冒失失的,把冲裁速度调得飞快。
我当时就急眼了,脸涨得通红,像个熟透的柿子,大声喊道:“小王,你这是干啥呢?速度这么快,那跳屑不得跟下雪似的啊。
”小王被我这一嗓子吓得一哆嗦,脸都白了,结结巴巴地说:“刘师傅,我以为快就能多干活呢。
”我叹了口气,说:“你这傻小子,这不是快就能行的事儿,得稳当。
”我就手把手地教他,一点点调整速度,就像在调教一匹不听话的马。
润滑也很关键啊。
这润滑油就像给模具和材料之间铺了一层滑溜溜的毯子。
我每次看到润滑油没加够或者加得不均匀的时候,就忍不住嘟囔:“这可咋行呢?就跟炒菜没放油一样,干巴巴的。
”我自己就拿着油壶,小心翼翼地加着油,眼睛紧紧盯着那些需要润滑的部位,那神情就像在照顾一个刚出生的婴儿,生怕有一点闪失。
这时候要是有人在旁边不小心碰了我一下,我就会皱着眉头,不耐烦地说:“别捣乱,这油加不好,跳屑就又该冒出来了。
”再就是那材料本身了。
材料要是表面不平整,就像那坑坑洼洼的路面,这跳屑也容易出现。
我记得有一回,进了一批材料,表面粗糙得很。
我就对着材料直摇头,嘴里念叨着:“这材料,看着就不让人省心。
”我就跟仓库的老张说:“老张啊,你这材料可得好好把关啊,这么粗糙的材料,到了咱这冲压生产,那跳屑就像苍蝇似的赶都赶不走。
防止五金模具跳废料的方法

防止五金模具跳废料的方法浮料现象在五金冲压模具中是一种常见的不良之现象,浮料产生的原因是多种的,因此其解决方法也是多样的。
下面,店铺为大家分享防止五金模具跳废料的方法,希望对大家有所帮助!防止跳废料的方法废料上移,是指在冲裁加工过程中,材料被剪断分离后,滞留在凹模内的材料随着凸模的上升一起被带出,接着又落在凹模表面的现象。
在冲压加工生产时,如果发生废料上移现象,一方面会因操作者粗心而发生人身事故;另一方面,也会造成产品报废,模具损坏等重大的质量问题。
所以,必须采取相应预防措施以预防废料上移。
1.废料上移的原因造成废料上移的.根本原因在于“废料与凸模之间的吸附力>废料与凹模之间的磨擦力+废料重力”。
特别是薄板小径冲裁,滞留在凹模内的材料与凹模之间摩擦力较小容易引起废料上移。
在实际生产过程中,具体原因较为复杂,主要有以下几种。
(1)凸模与凹模之间的间隙过大时容易发生废料上移。
(2)由于对凹模的直壁进行了抛光或高精度磨削,凹模直壁部分过于光滑,容易发生废料上移。
(3)凹模的直壁过高,存储的废料过多,向下的摩擦力增大,容易发生废料上移。
(4)废料下落不顺畅,碰到凹模刃口下面的其它零件,造成废料堵塞易于发生废料上移。
(5)薄板冲裁时,冲裁废料的形状大而薄,紧紧吸附在冲头下面。
(6)由于使用高粘度润滑油,因粘附力较大而产生粘附现象。
(7)凹模研模后,刃口过于锋利。
(8)卸料板的位置、功能不合适,与凸模周边的间隙不均匀。
(9)在模具加工或冲压生产过程中,凸模上面产生磁性而产生吸附现象。
(10)冲压生产过程中,凸模插入凹模的深度削、。
(11)凹模加工形状有误差,冲裁时,排出的废料尺寸d比凹模孔直径尺寸D小,容易发生废料上移。
冲压模具防跳废料的处理,拿去,不要客气

冲压模具防跳废料的处理,拿去,不要客气
防跳废料的处理
01
处理废料上冲头防跳废料
1.冲头上加卡槽防止跳废料
2.规则废料上加挂钩可有效的防止跳废料
02
冲头做内脱料销防跳废料
(FLX优先选用)
使用时要注意顶料销的顶出高度,保证在开模状态下顶料销的高度不能露出脱料板,反之易将材料顶变形,影响产品质量.
03
加内吹防跳废料
设计时需注意在做小吹气孔时保证冲头的强度.
04
下垫板做气孔抽废料
下垫板做气管,工作时使刀口内形面真空,使废料在空气的流动中被带出而达到防止废跳料的目的.
05
处理下模刀口防跳废料
1.刀口入子分上下两层,刀口直身位做短,下垫块做逃孔.(图一)
2.小圆孔下模入子做逃孔,单边+0.2~0.
3. (图二)
3.刀口间隙局部做小一半,此方法一般用在刀口间隙大于0.01时选用,对加工要求很高.(图三)。
- 1、下载文档前请自行甄别文档内容的完整性,平台不提供额外的编辑、内容补充、找答案等附加服务。
- 2、"仅部分预览"的文档,不可在线预览部分如存在完整性等问题,可反馈申请退款(可完整预览的文档不适用该条件!)。
- 3、如文档侵犯您的权益,请联系客服反馈,我们会尽快为您处理(人工客服工作时间:9:00-18:30)。
防止跳废料的方法。
前言
废料上移,是指在冲裁加工过程中,材料被剪断分离后,滞留在凹模内的材料随着凸模的上升一起被带出,接着又落在凹模表面的现象。
在冲压加工生产时,如果发生废料上移现象,一方面会因操作者粗心而发生人身事故;另一方面,也会造成产品报废,模具损坏等重大的质量问题。
所以,必须采取相应预防措施以预防废料上移。
1废料上移的原因
造成废料上移的根本原因在于“废料与凸模之间的吸附力>废料与凹模之间的磨擦力+废料重力”。
特别是薄板小径冲裁,滞留在凹模内的材料与凹模之间摩擦力较小容易引起废料上移。
在实际生产过程中,具体原因较为复杂,主要有以下几种。
(1)凸模与凹模之间的间隙过大时容易发生废料上移。
(2)由于对凹模的直壁进行了抛光或高精度磨削,凹模直壁部分过于光滑,容易发生废料上移。
(3)凹模的直壁过高,存储的废料过多,向下的摩擦力增大,容易发生废料上移。
(4)废料下落不顺畅,碰到凹模刃口下面的其它零件,造成废料堵塞易于发生废料上移。
(5)薄板冲裁时,冲裁废料的形状大而薄,紧紧吸附在冲头下面。
(6)由于使用高粘度润滑油,因粘附力较大而产生粘附现象。
(7)凹模研模后,刃口过于锋利。
(8)卸料板的位置、功能不合适,与凸模周边的间隙不均匀。
(9)在模具加工或冲压生产过程中,凸模上面产生磁性而产生吸附现象。
(10)冲压生产过程中,凸模插入凹模的深度削、。
(11)凹模加工形状有误差,冲裁时,排出的废料尺寸d比凹模孔直径尺寸D 小,容易发生废料上移。
2废料上移的应对措施
在实际生产过程中,为防止废料上移,通常的采取以下几种应对措施。
2.1在凸模上采取改进措施
(1) 材料很薄时,由于油的粘附力、磁性、真空等原因而极易吸附于凸模的
底部,对凸模采取改进措施,以减少凸模与废料的接触面积,从而减少凸模对废料的吸附。
在实际生产中常常应用图1所示的带突起型凸模、凹坑型凸模、加强筋型凸模等几种形式。
(2) 弹销器顶料凸模,如图2所示。
在凸模内加工阶孔,设置打料销及弹簧。
冲裁时,板料的挤压将销压入凸模内。
卸料时,打料销被弹簧顶出,将吸凸模上的废料顶落在凹模内部,不会产生废料上移。
(3
气(3)带气孔凸模,如图3所示。
在凸模中心加工一气孔,气孔与高压空气相连接,冲裁结束后,高压空气将废料吹落,吹出模具工作范围
(4)斜刃口凸模,如图4所示。
将凸模刃口加工成料面,冲裁时,刃口一端先接触材料,随着凸模的深入将料切断,废料与凸模不易形成真空,防止废料上移。
(5)批量生产时,凸模刃口因磨擦会产生磁性而吸附废料,所以要定期消磁。
2.2在凹模上采取改进措施
如图5 A、B所示。
废料不易堵塞,便于落下,具有防止废料上移的效果。
(2) 在凹模内侧壁,将2处以上的倾斜沟从中心开始向反方向加工,其深
度大约0.005mm—0.1 mm。
在冲裁初期,冲裁废料会形成和凹模倾斜沟
相对应的小突起。
随着凸模进一步压入,突起部分会被凹模侧面压缩,
摩擦力增大,从而防止废料上移。
凹模形状如图6所示。
(3)模内侧壁深度方向2mm一3mm处设计成凸起,厚度大约0.01 mm,随着凸模进一步压人,废料在此处挤压,摩擦力增大,可防止废料上移。
凹模形状如图7所示。
(4)尺寸精度要求不高的冲孔,研磨凹模直壁时使用粗粒度砂轮,使凹模直壁
部分的粗糙度不要太高,减少废料上移的可能;
(5)由于废料与凹模刃口下部碰撞会产生毛刺堵塞,进而产生废料上移,所以凹模直壁下部需加以修光。
(6)凹模的直壁部分太长,易于产生废料上移,所以在保证强度的前提下,可尽量减小凹模的深度。
2. 3其它改进措施
(1)易于产生废料上移时,使凸模插人凹模的深度应控制在3mm--5mm之间,
堵塞的废料限于三片之内。
(2)选择合理的冲裁间隙值,并加以修正。
(3)批量生产时,因凸模和凹模的摩擦会产生磁
E,应定期对刃口进行消磁处理。
(4)以真空产生吸引、增加凹模刃口内面的表面
且糙度、对凹模切刃进行微小倒角,改变轮廓形状,减
I、冲裁间隙。
(5)凹模下部的漏料部分应保持畅通,结构合理,
#晦料易千j E常惭禾Il的落下。