烧结机头电除尘灰简介
烧结机头电除尘灰的处理与利用
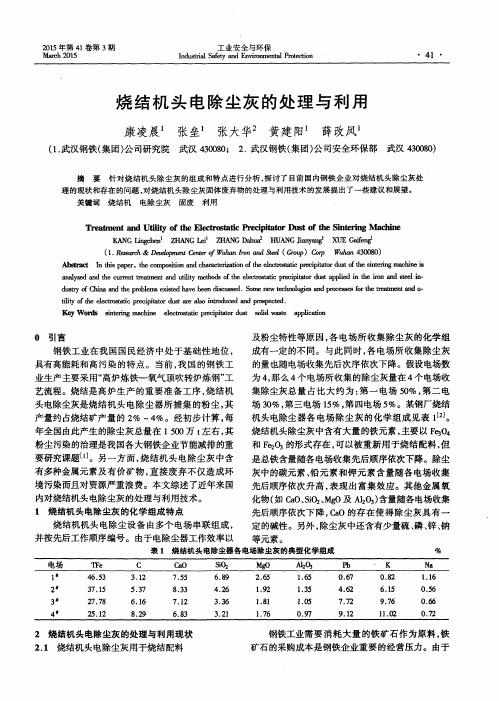
粉尘污染的治理是我 国各大钢铁企业节能减排 的重 要研究课题…。另一方面 , 烧结机头 电除尘 灰中含 有多种金属元素及有价矿物 , 直接废弃不仅造成环 境污染而且对资源严重浪费。本文综述了近年来国 内对烧结机头电除尘灰的处理与利用技术 。 1 烧 结机 头电 除尘灰 的化 学 组成 特 点
理的现状 和存 在的问题 , 对烧 结机头除尘灰 固体废弃 物的处理 与利 用技 术的发展提 出了一些 建议 和展望。 关键 词 烧 结机 电除尘 灰 固废 利用
பைடு நூலகம்
Tr e a  ̄ n e n t a n d Ut i l i t y o f t h e El e c t r o s t a t i c P r e c i p i t a t o r Du s t o f t h e S i n t e r i n g Ma c h i n e
KA NG L i n g c h e n I Z HAN G L e i Z H ANG Da h u a 2 HUA NG J i a n y a n g 1 X UE G a n
( 1 . R e s e a r c h&D e v e l o p m e n t C e n t e r o fW u h a n I r o n a n d S t e e l ( G r o u p )C o r p W u h a n 4 3 0 o 8 o )
Ab s t r a c t I nt h i s p a p e r ,t h e c o mp o s i t i o n a n d c h a r a c t e r i z a i t o n o ft h e e l e c t os r t a i t c p r e c i p i t a t o rd u s t o ft h e s i n t e r i n gma c h i n ei s
简介除尘灰及价格

本文摘自再生资源回收-变宝网()简介除尘灰及价格变宝网8月18日讯除尘灰可以分为烟气除尘灰和环境除尘灰,例如烧结机头高温烟气、高炉和转炉煤气系统的除尘,这类除尘灰是烟气除尘灰。
今天小编带大家去了解除尘灰的相关信息。
一、除尘灰的概括工业企业等排放的大气污染物经过布袋除尘器等除尘设备处理,大部分颗粒物废气经收集得到的飞灰,其成分与所收集的颗粒物气体有关,钢铁企业会产生大量除尘灰、氧化铁皮等等,一般都有很好的利用价值。
环境除尘是为减少环境粉尘污染所设置的,例如原料装卸、转运等岗位的除尘,这类除尘灰是环境除尘灰。
一般来说,环境除尘灰是在常温下聚集的,其介质粉尘性质无大变化,比较好利用,对生产基本无危害。
工艺除尘灰则是高温物化反应的产物,形成于高温之中,其理化性质发生变异,利用难度较大,对生产危害较大。
高炉煤气除尘全部采用了干法除尘,产生的一次除尘灰(重力除尘器)和二次除尘灰(煤气净化布袋除尘器)主要成分是铁和碳,全部返烧结作为烧结原料。
转炉煤气电除尘灰含铁量50%以上,一次除尘(设备:蒸发冷却器,作用:除尘、降温)灰(粒度较粗〕作为烧结原料,二次除尘(除尘设备:静电除尘器,作用:除尘降温)灰(粒度较细)一部分作为烧结原料回收利用,一部分作为竖炉球团原料回收利用。
作为球团原料配比控制在服以下对球团矿产质量指标影响不大。
电炉除尘灰含铁量利用冷压块技术部分回收利用。
长期以来大量除尘灰、泥在烧结循环利用,存在着许多问题。
一是除尘灰品种、数量多,成分复杂差异大,难以做到定量配料,造成烧结矿物化性能指标下降。
二是除尘灰、泥烧结性能差,钢铁企业多年来的生产经验。
烧结生产能力降低。
三是烟气除尘灰中K、Na、CLZn 等元素富集危害烧结炼铁生产,造成烧结台车糊蓖条,风机叶片挂泥,除尘器效率降低,烟尘污染加重,设备维护量加大,高炉因有害元素富集而影响顺行和寿命甚至造成事故也是不乏先例的.四是除尘灰、泥一直用敞车运输、落地,在装、卸现场及运输途中造成多次扬尘,污染环境。
烧结机头电除尘灰简介
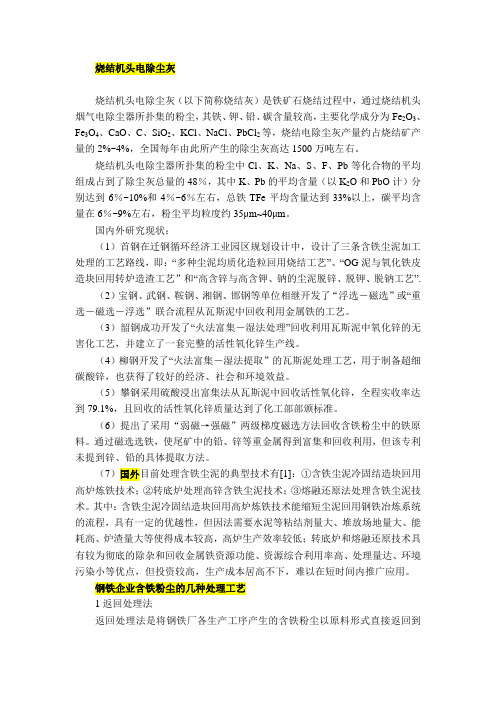
烧结机头电除尘灰烧结机头电除尘灰(以下简称烧结灰)是铁矿石烧结过程中,通过烧结机头烟气电除尘器所扑集的粉尘,其铁、钾、铅、碳含量较高,主要化学成分为Fe2O3、Fe3O4、CaO、C、SiO2、KCl、NaCl、PbCl2等,烧结电除尘灰产量约占烧结矿产量的2%~4%,全国每年由此所产生的除尘灰高达1500万吨左右。
烧结机头电除尘器所扑集的粉尘中Cl、K、Na、S、F、Pb等化合物的平均组成占到了除尘灰总量的48%,其中K、Pb的平均含量(以K2O和PbO计)分别达到6%~10%和4%~6%左右,总铁TFe平均含量达到33%以上,碳平均含量在6%~9%左右,粉尘平均粒度约35μm~40μm。
国内外研究现状:(1)首钢在迁钢循环经济工业园区规划设计中,设计了三条含铁尘泥加工处理的工艺路线,即:“多种尘泥均质化造粒回用烧结工艺”、“OG泥与氧化铁皮造块回用转炉造渣工艺”和“高含锌与高含钾、钠的尘泥脱锌、脱钾、脱钠工艺”.(2)宝钢、武钢、鞍钢、湘钢、邯钢等单位相继开发了“浮选-磁选”或“重选-磁选-浮选”联合流程从瓦斯泥中回收利用金属铁的工艺。
(3)韶钢成功开发了“火法富集-湿法处理”回收利用瓦斯泥中氧化锌的无害化工艺,并建立了一套完整的活性氧化锌生产线。
(4)柳钢开发了“火法富集-湿法提取”的瓦斯泥处理工艺,用于制备超细碳酸锌,也获得了较好的经济、社会和环境效益。
(5)攀钢采用硫酸浸出富集法从瓦斯泥中回收活性氧化锌,全程实收率达到79.1%,且回收的活性氧化锌质量达到了化工部部颁标准。
(6)提出了采用“弱磁→强磁”两级梯度磁选方法回收含铁粉尘中的铁原料。
通过磁选选铁,使尾矿中的铅、锌等重金属得到富集和回收利用,但该专利未提到锌、铅的具体提取方法。
(7)国外目前处理含铁尘泥的典型技术有[1]:①含铁尘泥冷固结造块回用高炉炼铁技术;②转底炉处理高锌含铁尘泥技术;③熔融还原法处理含铁尘泥技术。
其中:含铁尘泥冷固结造块回用高炉炼铁技术能缩短尘泥回用钢铁冶炼系统的流程,具有一定的优越性,但因法需要水泥等粘结剂量大、堆放场地量大、能耗高、炉渣量大等使得成本较高,高炉生产效率较低;转底炉和熔融还原技术具有较为彻底的除杂和回收金属铁资源功能、资源综合利用率高、处理量达、环境污染小等优点,但投资较高,生产成本居高不下,难以在短时间内推广应用。
用转动电极电除尘器治理烧结机头粉尘达标排放

用转动电极电除尘器治理烧结机头粉尘达标排放1、概述烧结机头烟尘治理是当前我国大气污染控制的一个难题,现用的电除尘器由于自身的缺陷,不少经过改造仍是达不到国家烟气排放50 mg/Nm3的现行标准,关键是常规电除尘器不能同时彻底解决电极清灰和二次扬尘两个问题,而江苏瑞帆环境工程设备有限公司研制的转动电极式电除尘器对这两个问题能彻底的同时给与解决。
烧结机头除尘主要特点如下:工作压力大:一般为-10~-20KPa,主要根据机上混合料料层厚度而定,当料层600~650mm,则工作负压-15~-17KPa。
烟气湿度高:烧结混合料中含有8~10%的水分,在烧结过程中,大量的水分被蒸发成水蒸气,通过电除尘器而排入大气中,烟气的露点温度为50~60℃。
烟气温度波动大:正常运转温度为120~150℃(有时高达180~200℃,最低80℃)。
烟尘碱度和比电阻高:碱度为1.8~2.0,粉尘比电阻为1010~1012Ω•cm。
烟尘中含有:K2O、Na2O、CH及氯化物。
2、机头电除尘器存在的问题和分析21世纪初,我国钢铁工业快速大发展,短短数年时间,从年产一亿吨钢达到四亿多吨,占世界总产量的1/3左右,成为世界第一钢铁大国,同时由于配套设施不当,重视程度不够,钢铁的发展也带来了环境污染问题,而其中烧结机头电除尘器粉尘排放超标严重,成为许多冶金企业的一项老大难问题,一直没有得到很好的解决,通过多年对烧结工艺烟尘治理和调查,认为有以下原因造成烧结机头电除尘器严重超标:原料的影响:钢铁大发展,进口大量外国铁矿粉,这些矿粉中含有较多碱金属K2O、Na2O,这些碱金属矿物质随烧结过程进行,产生大量细微颗粒进入烟气当中,形成特定的粉尘性质,给除尘器收集造成了很大的困难。
电场风速的影响:国内机头电除尘器内的电场风速较高(1.0~1.4m/s),虽然把尘粒子收集到极板上,但振打下来的粉尘因容重极轻有不少粉尘随气流而逸出设备外(形成二次扬尘)。
烧结机头电除尘器的特点与应用
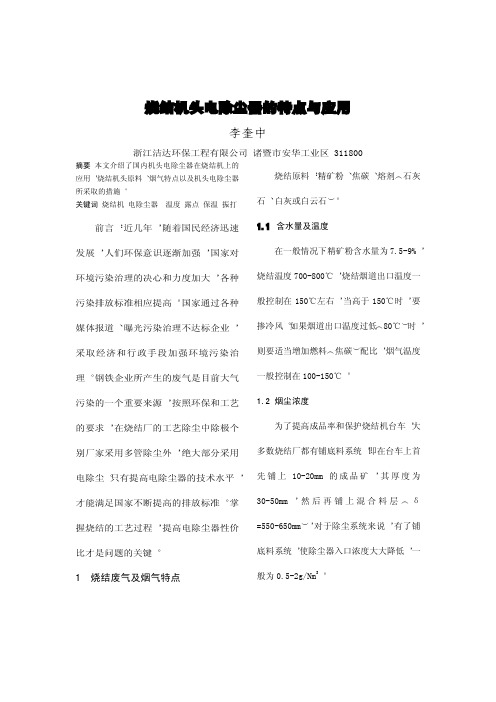
一方面:这些成分的增加会降低粉尘的比电
阻,有利于收尘;另一方面:这些成分的比 2 国内烧结机头电除尘运转情况
重小,不利于清灰,更容易产生粉尘的二次
为了搞好机头电除尘,提高除尘效率,
飞扬。通过全国几个大钢厂烧结运转证明, 我们考察了国内几个大型钢厂的电除尘运
这些成分一般情况下电场不易把它们除下 转情况,发现电除尘器的运转电压均较低
用:一是有助于气流在电场内均匀通过,二 尘器灰斗的加热方式中,采用蒸汽加热和电
是可以起收尘作用,通过长期使用证明其效 加热是最为普遍的加热方式。不管采用哪种
果不容忽视。末电场粉尘特点是颗粒细,粘 加热方式,我认为加热原理应该是一样的:
性大,大部分在 5μ左右,烟温低(比前电 加热是把灰斗壁加热,使灰斗壁上的灰温度
虑较大的卸灰角度,并在灰斗四角设置圆弧
国内大多数电除尘器的进、出口,均与
板,防止灰斗结灰起拱。更重要的在于灰斗 电场中心线相一致,也有少数电除尘器进口
的良好保温,充分保证灰斗壁温度在烟气露 高于出风口(电场中心线以下),在 100m2
点以上 10°C 左右,防止灰尘结露粘结而发 机头电除尘器试车中偶然发现,一电场下的
器)运行数据可以看出:随着废气温度的提 除尘器,在没有采用声波清灰时排放不达
高,电场的电流也随着大幅度的提高,这样 标。2004 年配声波清灰后排放浓度下降了
对电除尘器的运转会有利,运转证明只要把 75-80%左右,效果明显。
废气温度控制在 100~130 ℃以内,电除尘
3.采用固定钢刷
器的正常运转是不容置疑的。
清灰:是目前解决烧结机头电除尘器冒白烟
第二、为了提高电场清灰效果,我们采 的最好措施。钢刷清灰起源于 1972 年鞍钢
烧结机头除尘灰的处理方法
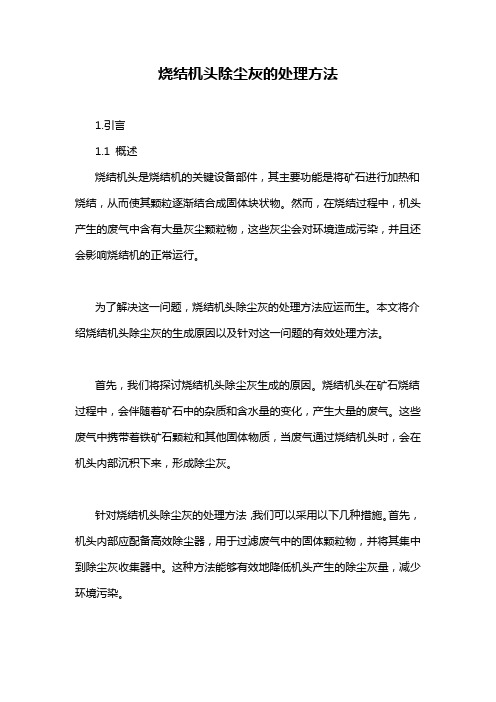
烧结机头除尘灰的处理方法1.引言1.1 概述烧结机头是烧结机的关键设备部件,其主要功能是将矿石进行加热和烧结,从而使其颗粒逐渐结合成固体块状物。
然而,在烧结过程中,机头产生的废气中含有大量灰尘颗粒物,这些灰尘会对环境造成污染,并且还会影响烧结机的正常运行。
为了解决这一问题,烧结机头除尘灰的处理方法应运而生。
本文将介绍烧结机头除尘灰的生成原因以及针对这一问题的有效处理方法。
首先,我们将探讨烧结机头除尘灰生成的原因。
烧结机头在矿石烧结过程中,会伴随着矿石中的杂质和含水量的变化,产生大量的废气。
这些废气中携带着铁矿石颗粒和其他固体物质,当废气通过烧结机头时,会在机头内部沉积下来,形成除尘灰。
针对烧结机头除尘灰的处理方法,我们可以采用以下几种措施。
首先,机头内部应配备高效除尘器,用于过滤废气中的固体颗粒物,并将其集中到除尘灰收集器中。
这种方法能够有效地降低机头产生的除尘灰量,减少环境污染。
其次,在除尘灰收集器中,可以采用物理、化学或生物方法对除尘灰进行处理。
物理方法包括筛分、洗涤和烘干等,用于分离和去除除尘灰中的有害物质。
化学方法主要是利用化学反应将有害物质转化为无害物质,从而达到除尘灰净化的目的。
而生物方法则利用微生物的作用将有害物质降解、转化为无害物质。
最后,在除尘灰处理过程中,应注意遵守相关的环保法规和标准。
同时,应加强废气治理技术的研发和应用,不断提高除尘效率和灰尘处理的安全性。
总之,烧结机头除尘灰的处理方法是解决烧结工艺中环境污染问题的关键措施。
通过合理选择和应用除尘器、采用物理、化学和生物方法对除尘灰进行处理,可以有效地降低除尘灰对环境的影响,保障烧结机的正常运行。
在未来,我们需要继续加强研究和推广相关技术,为烧结工艺的环保发展做出更大的贡献。
文章结构部分的内容应该包括对整篇文章的分段和组织的介绍,以及每个部分的主要内容。
以下是对文章结构部分的一个示例内容:1.2 文章结构本文共分为三个部分:引言、正文和结论。
再论烧结机头电除尘器的应用及其特点

再论烧结机头电除尘器的应用及其特点预览说明:预览图片所展示的格式为文档的源格式展示,下载源文件没有水印,内容可编辑和复制再论烧结机头电除尘器的应用及其特点康进花丁秀清摘要本文通过对烧结机头的特点和烧结用料的成分的分析,探讨了机头电除尘器在应用中应注意的几个问题,并采取相应的措施,以满足排放标准、烧结工艺要求,最终达到净化烟气的目的,从而保护人类赖以生存的环境。
关键词高效率高负压高比电阻二次飞扬2、机头电除尘器的基本原理、特点2.1 基本原理利用负高压尖端放电,释放出电子,电子吸附在中性的粉尘上,使其带负电荷,然后在电场力的作用下,带负电荷的粉尘向正极移动并吸附,带正电荷的粉尘向负极移动并吸附,从而完成收尘。
通过振打,使灰落入下部的灰斗中并定期排出。
2.2 机头电除尘器的特点2.21 高负压:16000Pa—23000Pa;常规电除尘器,如烧结机机尾、整粒、配料、熔剂以及电厂锅炉等配置的电除尘器,烟气负压均为4000—7000Pa之间。
机头除尘器则不同,随着高碱度烧结工艺的广泛应用,烧结机容量的加大,烧结机的料层也在普遍加厚,而且采用国外进口大风量风机,高负压操作,所以烟气负压相当高,一般均在16000—23000Pa,这就对烧结机机头除尘器的强度和刚度提出更高的要求。
2.2.2 高比电阻:1011—1013Ω·Cm,不易收尘;表1 对武钢机头粉尘比电阻测试结果实践表明:烟气中粉尘比电阻值维持在10~5×10Ω·Cm时,最有得电除尘器对粉尘的捕食,并能取得理想的除尘效果。
当比电阻小于1×104Ω·Cm时,除尘效率随着比电阻的降低而大幅降低,造成二次飞扬;当比电阻大于5×1010Ω·Cm时,造成反电晕现象,电除尘器的性能却随着比电阻的增高而下降。
2.2.3 粉尘细:氧化钾、氧化钠含量高,且粒径小,比重轻,易产生二次飞扬;表2 对武钢各类除尘灰分检验报告表3 武钢机头电除尘器灰分检验报告从表中可以看出:烧结机头除尘中K2O、Na2O含量明显高于其它各类除尘;且后置电场更高。
烧结机头电除尘灰资源化利用技术
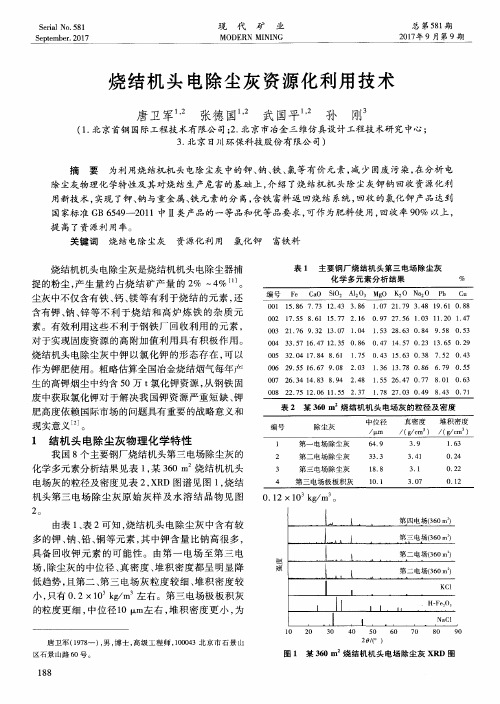
除 尘灰物理 化 学特性 及 其对烧 结 生产危 害的基础 上 , 介 绍 了烧 结机 机 头 除 尘灰 钾钠 回收 资 源化 利 用新技 术 , 实现 了钾 、 钠 与重金 属 、 铁 元 素 的分 离, 含铁 富料返 回烧 结 系统 , 回收 的 氯化 钾 产 品达 到 国家标 准 G B 6 5 4 9 -2 0 1 l中 Ⅱ类产 品的一 等 品和优 等 品要 求 , 可作 为肥 料使 用 , 回收率 9 0 % 以上 ,
烧 结 机机 头 电除尘灰 是烧 结机 机 头 电除尘器 捕
捉 的粉尘 , 产 生 量 约 占烧 结 矿 产 量 的 2 % ~4 %…。
%
C u
尘灰 中不 仅含有 铁 、 钙、 镁 等 有 利 于烧 结 的元 素 , 还 含有 钾 、 钠、 锌 等 不 利 于 烧 结 和 高 炉 炼 铁 的 杂 质 元 素 。有效 利用 这些 不利 于钢 铁 厂 回收利 用 的元 素 , 对 于实现 固废 资 源 的 高 附加 值 利 用 具有 积 极 作 用 。 烧结 机头 电除尘灰 中钾 以氯 化 钾 的形 态存 在 , 可 以
提 高 了资源利 用率 。
关键 词 烧 结电除 尘灰
资 源化 利用 氯化 钾
富铁 料
表1 主 要钢 厂 烧 结 机 头 第 三 电场 除 尘灰
口 弓 一 1 ∞ 2 ∞ ∞ 3 4 ∞ 5 ∞ 6 ∞ 7 ∞ 8 ∞ 化 学 多元 素 分 析 结 果
F e Ca O S i O2 A1 2 O3 Mg O K2 0 Na 2 0 P b
作为钾肥使用 。粗略估算全 国冶金烧结烟气每年产 生的高钾烟尘 中约含 5 O 万t 氯化钾资源 , 从钢铁 固
废 中获取 氯化 钾对 于解 决 我 国钾 资 源严 重 短 缺 、 钾 肥 高度依 赖 国 际市 场 的 问题 具有 重要 的战略意 义 和
烧结机电除尘

随着烧结设备的大型化和对环境质量要求的日趋严格,国内外已成功地将电除尘技术应用于烧结机机头烟气的净化上,并取得了显著的效果。
烧结烟气具有负高压、含湿量大、化学成分复杂等特点,且产生的粉尘比电阻较高,电除尘技术应用于该行业有一定的难度。
济钢第二烧结厂成功地将电除尘器宽间距技术用于烧结机头烟气除尘,有利于烧结机机头负高压,含湿量大,粉尘比电阻偏高,且含有钾、钠离子的易结疤的粉尘环境特质,通过采取加大电极间距,提高工作电压,抑制电场闪络,减少反电晕的发生,并可以提高电场工作电压,对电场的运行和粉尘的有效捕集效果十分显著。
济钢第二烧结厂320m2烧结机机头烟气净化采用两台220m2电除尘器,下面将使用、故障分析及改进情况简单介绍。
一、电除尘器设计参数及工艺布置根据除尘系统的布置要求、烧结机产生的烟气量,选择了两台220m2三电场的电除尘器,并联使用两台除尘器分别有自己的一套输灰系统,单台电除尘器的设计参数见表,两台电除尘器工艺布置见图。
二、电除尘的优化设计在电除尘的优化设计中,采用了国内外先进技术。
根据烧结机头烟气量大、负压高、含尘浓度低、粉尘较细等特点,选择了390mm的C型阳极板配星型线,同极距为600mm的宽间距极配形式。
此种极配起晕电压高,均在20KV以上。
电流强度小,火花电压高,电流密度及场强分布均匀。
国内外的研究结果表明:增大阴极间距离,可以抑制电场闪络,减少反电晕的发生,并可以提高电场工作电压,从而使驱进速度有所提高。
电除尘器的设计参数————————————————————项目单位数量————————————————————有效断面积m2 220处理烟气量m3/h7 9.2~105温度、压力、含尘浓度同工艺设计效率%98电场风速m/s 1.3有效电场长度m 3×4.1有效停留时间s 10同极距mm 600设计电压KV 90漏风率%<1收尘极型式c-390电晕型式星型线电场数个 3————————————————————三.机头电场的故障分析及改进措施1.灰斗漏风问题及相应对策因为除尘器是负压操作,如果灰斗漏风就会从外部漏入冷空气,使通过电除尘的风速增大,烟气温度降低,使的烟气露点发生变化,其结果是粉尘比电阻增高,使收尘性能下降。
钢铁企业除尘灰的综合利用

钢铁企业除尘灰的综合利用钢铁企业的除尘灰是指从烧结到轧钢的各个工序通过电除尘器、重力除尘器和布袋除尘器等除尘设备提供的灰尘。
据统计,钢铁企业除尘灰产生总量约为钢产量的10%。
所述除尘灰分为烧结机头灰、高炉布袋灰和转炉灰三种。
目录1.除尘灰的性质 (1)1.1.烧结机头除尘灰 (1)1.2.高炉布袋除尘灰 (1)1.3.转炉除尘灰 (2)1.4.电炉除尘灰 (2)2.资源化利用 (3)2.1.研究现状 (3)3.2.产业化现状 (3)3.结语 (4)1.除尘灰的性质1.1.烧结机头除尘灰烧结机头灰是指在烧结工序中,烧结烟气通过大烟道到电除尘器产生的灰尘。
其中所含有害元素主要为钾、钠和氯,局部钢厂的烧结机头灰里氧化钾含量高达30%。
烧结机头灰的粒度极细,呈灰白色,平均粒径在100 um左右,堆密度在0.5〜lg/cn? o烧结机头灰中的铁主要以氧化铁和磁铁矿的形式存在,钾和钠主要以氯化钾和氯化钠的形式存在,同时也存在氯化钙、氯化镁、氯化铅和氯化锌等氯化物。
烧结机头灰如果返回烧结使用,会造成碱金属富集,常见的影响是烧结“糊篦条,引起烧结矿产量、质量降低。
烧结机头灰因有价元素含量较低,利用价值不高。
1.2.高炉布袋除尘灰高炉布袋灰,也称为高炉瓦斯灰或高炉二次灰,是在高炉冶炼过程中从炉第1页共5页顶产生的烟气经重力除尘器、布袋除尘提供的灰尘。
高炉布袋灰中的有害元素主要是锌、钾、钠和氯,同时含有较多的铁和碳,其产生量为3〜6kg/t铁水。
高炉布袋灰的粒度较烧结机头灰粗,呈黑灰色,平均粒径在130u m左右,堆密度在0.7〜l.lg/cn?,外观类似于磁铁精粉。
高炉布袋灰中的铁主要以氧化铁和磁铁矿的形式存在,碳那么以单质碳的形式存在。
高炉布袋灰中的钾和钠同样主要以氯化钾和氯化钠的形式存在,锌那么以氧化锌、铁酸锌和氯化锌的形式存在。
高炉布袋灰中锌含量<1%时可以返回烧结配料使用。
但大局部钢厂高炉布袋灰含锌量在1%以上,如果返回烧结工序继续使用,会造成烧结矿中的锌富集,导致高炉锌负荷超标,易产生降低焦炭强度,侵蚀耐火砖,形成炉瘤,破坏风口等问题。
冶金烧结企业的防尘除尘措施
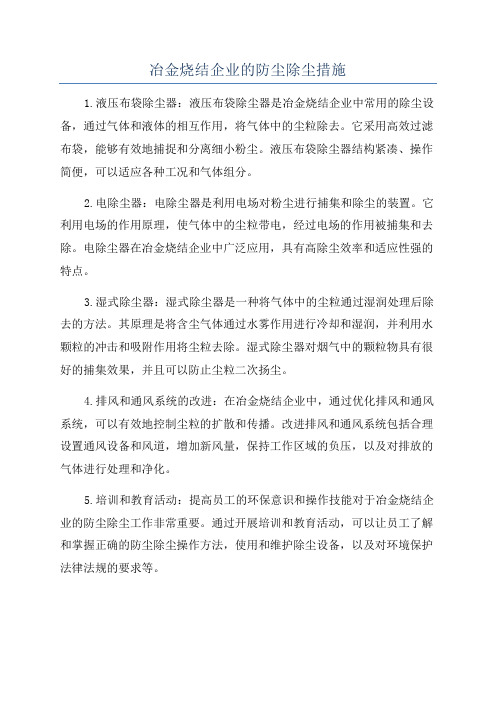
冶金烧结企业的防尘除尘措施1.液压布袋除尘器:液压布袋除尘器是冶金烧结企业中常用的除尘设备,通过气体和液体的相互作用,将气体中的尘粒除去。
它采用高效过滤布袋,能够有效地捕捉和分离细小粉尘。
液压布袋除尘器结构紧凑、操作简便,可以适应各种工况和气体组分。
2.电除尘器:电除尘器是利用电场对粉尘进行捕集和除尘的装置。
它利用电场的作用原理,使气体中的尘粒带电,经过电场的作用被捕集和去除。
电除尘器在冶金烧结企业中广泛应用,具有高除尘效率和适应性强的特点。
3.湿式除尘器:湿式除尘器是一种将气体中的尘粒通过湿润处理后除去的方法。
其原理是将含尘气体通过水雾作用进行冷却和湿润,并利用水颗粒的冲击和吸附作用将尘粒去除。
湿式除尘器对烟气中的颗粒物具有很好的捕集效果,并且可以防止尘粒二次扬尘。
4.排风和通风系统的改进:在冶金烧结企业中,通过优化排风和通风系统,可以有效地控制尘粒的扩散和传播。
改进排风和通风系统包括合理设置通风设备和风道,增加新风量,保持工作区域的负压,以及对排放的气体进行处理和净化。
5.培训和教育活动:提高员工的环保意识和操作技能对于冶金烧结企业的防尘除尘工作非常重要。
通过开展培训和教育活动,可以让员工了解和掌握正确的防尘除尘操作方法,使用和维护除尘设备,以及对环境保护法律法规的要求等。
6.定期检查和维护:对冶金烧结企业的除尘设备进行定期检查和维护是保证除尘效果的关键。
定期检查除尘设备的运行状况,清理和更换损坏的滤芯和滤袋,保持设备的正常运转。
7.使用低尘材料和工艺:在冶金烧结生产过程中使用低尘材料和工艺也是降低尘粒排放的有效措施。
通过优化原料选择和产品工艺,减少尘粒的产生和扩散。
总之,冶金烧结企业的防尘除尘措施是多方面综合考虑的,需要结合具体的工艺流程和排放要求来确定。
通过采取适当的防尘除尘措施,可以有效降低尘粒的排放,保护环境,提高生产效率和员工的健康安全。
烧结机头电除尘器的特点与应用
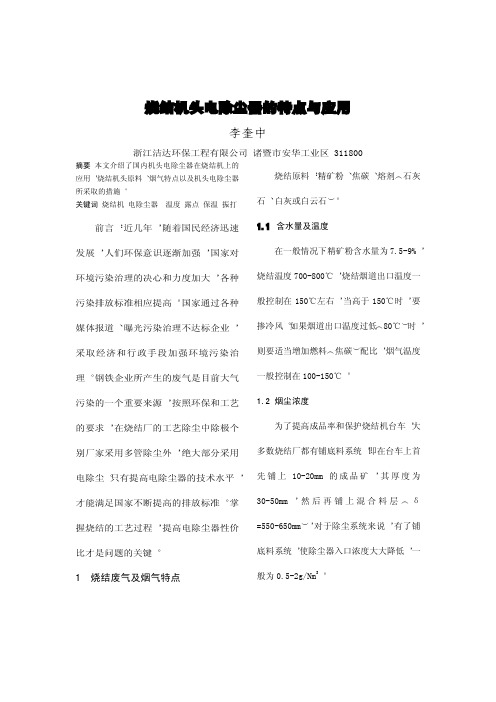
它能长期保证电场长期处于良好状态,使除
第三、杜绝粉尘进入陶瓷管内,保证陶
尘器效率高、运转稳定、并且减小了收尘面 瓷管在废气处于露点时,也不会在陶瓷管内
积,一般情况下两、三个电场即可满足排放 部产生拉弧现象,以免把陶瓷管炸裂或炸
要求(普通电除尘器则需三、四个电场才 碎,发生安全事故。这是必须注意的。
行)。
清灰:是目前解决烧结机头电除尘器冒白烟
第二、为了提高电场清灰效果,我们采 的最好措施。钢刷清灰起源于 1972 年鞍钢
取了以下办法:
三烧机尾除尘工程,当时国内电除尘器普遍
1.完善振打方式:阴阳极振打均采用侧部振 产生刚投产时,除尘效率很高,运转一阶段
打方式,加大振打力度和均匀性。且不同电 (3 月~1 年)后,由于电场积灰多、电压低、
电流就急剧下降。
时电压 65KV 相对应的电场电流趋近为零,
3.2 废气温度的影响
此时排放浓度较高。
烧结废气温度是保证机头电除尘器正
为了改善上述情况,我们采取如下措
常运转的先决条件。
施:
混合料中的精矿粉,正常情况下磁铁矿
第一:必须提高废气温度,当温度上升
和赤铁矿为主的混合料含水量为 7-8%。以 到 100℃以上时,经过一段时间烘烤,把电
灰一样轻(根据新抚钢机头 100m2 除尘器所 除尘器投产半年,电压 40KV,电流已趋近
取的粉尘观察);从成分分析来看,Na2O、 为零。
K2O 等成分的含量,由 0.7%一直上升到 36.3% 左右(如首钢烧结机头电除尘器)。
3 情况分析及采取相应措施
另外我们从阴极芒刺针上尘瘤成分分
我们对于上述国内机头电除尘运转情
以便清除出灰口咽喉处的积灰。
烧结厂部分设备技术参数
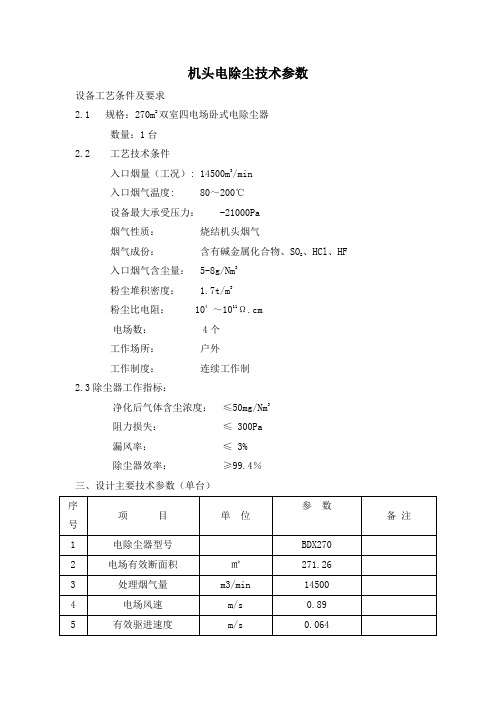
机头电除尘技术参数设备工艺条件及要求2.1 规格:270m2双室四电场卧式电除尘器数量:1台2.2 工艺技术条件入口烟量(工况): 14500m3/min入口烟气温度: 80~200℃设备最大承受压力: -21000Pa烟气性质:烧结机头烟气烟气成份:含有碱金属化合物、SO、HCl、HF2入口烟气含尘量: 5-8g/Nm3粉尘堆积密度: 1.7t/m3粉尘比电阻: 104~1011Ω.cm电场数: 4个工作场所:户外工作制度:连续工作制2.3除尘器工作指标:净化后气体含尘浓度:≤50mg/Nm3阻力损失:≤ 300Pa漏风率:≤ 3%除尘器效率:≥99.4%三、设计主要技术参数(单台)烧结机技术参数132㎡烧结机技术性能表烧结主抽风机技术简介一. 风机技术参数风机型式:双吸入离心式风机用途:烧结主抽风机布置方式:进气135°、出气0°旋转方向: 左旋支撑方式:双支撑(叶轮在轴承中间)输送介质:烧结烟气机械设计温度: 250℃转子动平衡品质等级: G2.5转子振动均方根有效值: 4.0 mm/s驱动方式:由电机通过膜片联轴器驱动流量调节方式:入口调节门调节主轴临界转速: ≥1.3n (n为工作转速,r/min)风机型号: SJ14500-13T叶轮直径: 3800mm叶轮最高周速: 198.96m/s风机转子重量 : 17500 kg风机总重: 57500 kg (不包括电机及润滑油站)转子飞轮矩GD2: 48500 kg-m2二.气动性能参数进口容积流量(m3/min): 14500风机入口压力(Pa): -16500风机出口压力(Pa): 500进口温度(℃): 80~200(正常120) 进口密度(kg/m3): 0.739风机转速(r/min): 1000风机最高内效率 ( % ) : 86风机轴功率 (kW) : 4575(120℃)风机轴功率 (kW) : 4780(80℃)您只需提供相关数据,详细填写于下表中,我们将为您量身订制详尽的脱硫技术方案注:以上红色的部分为我公司需要测量数据。
钢厂烧结机头灰中钾、铅、铁的分离回收技术简介

钢厂烧结机头灰中钾、铅、铁的分离回收技术简介烧结机头灰是烧结过程产生的烟尘之一,随烧结烟气进入除尘系统,然后由电除尘器收集得到。
因烧结生产所用矿石大多含有钾、钠、铅、氯等元素,在烧结的高温过程中极易挥发形成氯化物等烟气,而后冷却为极细的粉尘,被电除尘器收集,从而得到烧结机头灰。
传统处理方法:传统工艺中,烧结机头灰作为除尘灰的一种,直接用于返烧结使用,但因其粒度细,不易润湿,碱金属含量高,成分波动大,易再次进入除尘系统,对烧结过程的稳定运行存在负面影响。
更重要的是碱金属及铅难以找到出口而在烧结工序恶性循环,不仅加重除尘器的负担,增加烧结工序能耗,还使烧结矿中碱金属含量偏高,进入高炉后极易导致高炉壁腐蚀,对高炉的使用寿命和钢铁的质量都有一定影响。
其他一些资源回收方法:1)机头灰水浸-固液分离-双碱法除杂-分步结晶工艺,回收机头灰中氯化钾资源。
将机头灰加入水和添加剂进行浸出,浸出液净化后分步结晶,母液循环, 浸渣洗涤后返烧结,洗液用于浸出。
2)种利用烧结机头灰制取硫酸钾及氮磷钾复合肥的工艺。
基本流程:1)机头灰水洗后磁选,得到铁精矿;2)含铅尾泥和含钾溶液,铁精矿与返烧结使用;3)含钾溶液经循环含集钾后经除杂、活性炭脱色,配入硫酸镂经蒸发结晶得到硫酸钾,母液继续蒸发后与磷肥复合得到氮磷钾复合肥;4)含铅尾泥则采用氯化钠-盐酸体系浸出,所得含铅溶液经冷却结晶-再溶解净化后用纯碱沉淀,然后煨烧得到一氧化铅产品。
本文介绍的烧结机头灰成分基本情况:PbO(3〜30%), Cl(5〜30%),K20(5^30%], Na2O(1^5%], TFe(IO〜35%)。
烧结机头灰通过两次调浆,相当于两次浸出过程,配合调浆时的固液配比、温度、搅拌时间等参数最大限度提升了钾的浸出率。
详细步骤如下:1)第一步:将烧结机头灰加入水调制成矿浆;2)第二步:矿浆固液分离,得到含钾溶液和浸出渣;3)第三步:浸出渣中加入水,再次调制成矿浆;4)第四步:在重选设备中重选分离,得到含铁料矿浆和含铅料矿浆; 5)第五步:含铅料矿浆过滤,得到含铅料及其滤液;6)第六步:含铁料矿浆过滤,得到含铁料及其滤液。
烧结除尘灰的来源与利用
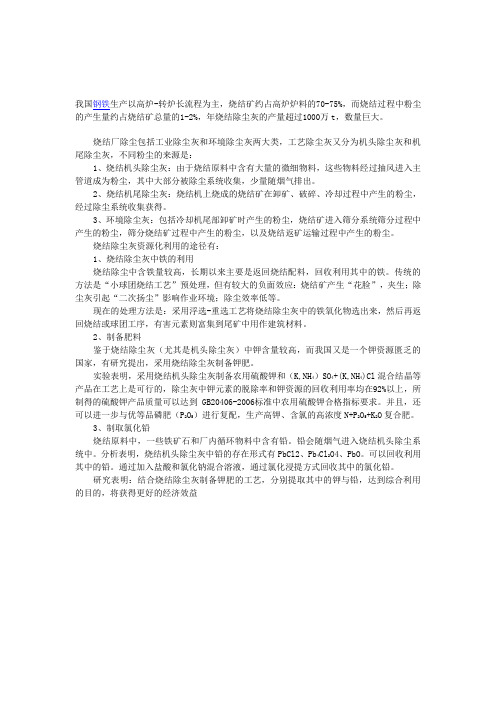
我国钢铁生产以高炉-转炉长流程为主,烧结矿约占高炉炉料的70-75%,而烧结过程中粉尘的产生量约占烧结矿总量的1-2%,年烧结除尘灰的产量超过1000万t,数量巨大。
烧结厂除尘包括工业除尘灰和环境除尘灰两大类,工艺除尘灰又分为机头除尘灰和机尾除尘灰,不同粉尘的来源是:1、烧结机头除尘灰:由于烧结原料中含有大量的微细物料,这些物料经过抽风进入主管道成为粉尘,其中大部分被除尘系统收集,少量随烟气排出。
2、烧结机尾除尘灰:烧结机上烧成的烧结矿在卸矿、破碎、冷却过程中产生的粉尘,经过除尘系统收集获得。
3、环境除尘灰:包括冷却机尾部卸矿时产生的粉尘,烧结矿进入筛分系统筛分过程中产生的粉尘,筛分烧结矿过程中产生的粉尘,以及烧结返矿运输过程中产生的粉尘。
烧结除尘灰资源化利用的途径有:1、烧结除尘灰中铁的利用烧结除尘中含铁量较高,长期以来主要是返回烧结配料,回收利用其中的铁。
传统的方法是“小球团烧结工艺”预处理,但有较大的负面效应:烧结矿产生“花脸”,夹生;除尘灰引起“二次扬尘”影响作业环境;除尘效率低等。
现在的处理方法是:采用浮选-重选工艺将烧结除尘灰中的铁氧化物选出来,然后再返回烧结或球团工序,有害元素则富集到尾矿中用作建筑材料。
2、制备肥料鉴于烧结除尘灰(尤其是机头除尘灰)中钾含量较高,而我国又是一个钾资源匮乏的国家,有研究提出,采用烧结除尘灰制备钾肥。
实验表明,采用烧结机头除尘灰制备农用硫酸钾和(K,NH4)SO4+(K,NH4)Cl混合结晶等产品在工艺上是可行的,除尘灰中钾元素的脱除率和钾资源的回收利用率均在92%以上,所制得的硫酸钾产品质量可以达到GB20406-2006标准中农用硫酸钾合格指标要求。
并且,还可以进一步与优等品磷肥(P2O5)进行复配,生产高钾、含氯的高浓度N+P2O5+K2O复合肥。
3、制取氯化铅烧结原料中,一些铁矿石和厂内循环物料中含有铅。
铅会随烟气进入烧结机头除尘系统中。
分析表明,烧结机头除尘灰中铅的存在形式有PbCl2、Pb4Cl2O4、PbO。
菲达烧结机头电除尘器特点讲解
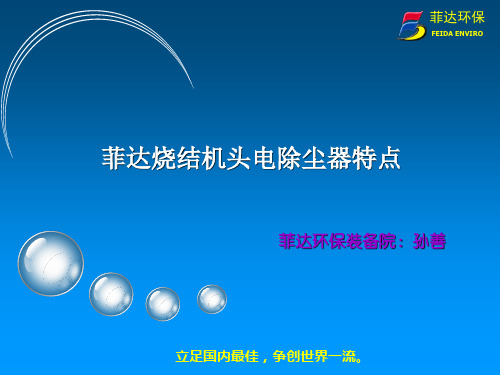
壳体立柱的变形。
立足国内最佳,争创世界一流。
菲达环保
FEIDA ENVIRO
菲达烧结机头电除尘器特点
11、本体密封技术
电除尘器本体密封的好坏直接影响到电除尘器的除尘效率,对于烧结机 头电除尘器,与常规除尘器相比负压高得多(一般均在 14000~23000Pa)、
而且压力不稳定,冲击压力大这对机头电除尘器的强度和刚度提出了更高的
加热)保证灰斗下口不积灰结块而造成堵灰;如果是电加热,菲达公司多采用管式
的,灰斗下部制作成双层结构形成一个密闭的空腔,每只灰斗灰斗下部设有多个 1.5KW的灰斗专用管式电加热器插入该空腔来加热空气,加热均匀、效果好能耗低, 而且加热器采用抽屉式的结构,检修、更换非常方便(该加热方式为菲达公司自行
研发设计的);另外还设有高、低料位计,高料位计保证灰斗里的灰能及时排出,
菲达环保
FEIDA ENVIRO
菲达烧结机头电除尘器特点
8、进口气流分布设置
菲达公司对于平进接口的喇叭进口气流分布设一层
阻流加两层导流,通过菲达公司特有的气流分布实验
(菲达公司专利)(即通过先进的 CDF 软件用电脑进行 三维数字模拟或 1 : 10 实物模拟)来设计、布置开孔率
和导流叶片,保证各封头分配流量差小于5%、气流分布
而低料位计保证了灰斗下部留有一定的灰不至于排空、否则会造成冷空气被吸入, 这对电除尘器特别是烧结机头电除尘器尤其重要,一旦冷空气被吸入,烧结机头烟 气中含有大量Na20、K20等碱性氧化物,一遇到冷空气中极易结成块粘在极线、极板
影响放电、收尘,也容易造成灰斗下部结块而造成堵灰。
立足国内最佳,争创世界一流。
立足国内最佳,争创世界一流。
菲达环保
- 1、下载文档前请自行甄别文档内容的完整性,平台不提供额外的编辑、内容补充、找答案等附加服务。
- 2、"仅部分预览"的文档,不可在线预览部分如存在完整性等问题,可反馈申请退款(可完整预览的文档不适用该条件!)。
- 3、如文档侵犯您的权益,请联系客服反馈,我们会尽快为您处理(人工客服工作时间:9:00-18:30)。
烧结机头电除尘灰
烧结机头电除尘灰(以下简称烧结灰)是铁矿石烧结过程中,通过烧结机头烟气电除尘器所扑集的粉尘,其铁、钾、铅、碳含量较高,主要化学成分为Fe2O3、Fe3O4、CaO、C、SiO2、KCl、NaCl、PbCl2等,烧结电除尘灰产量约占烧结矿产量的2%~4%,全国每年由此所产生的除尘灰高达1500万吨左右。
烧结机头电除尘器所扑集的粉尘中Cl、K、Na、S、F、Pb等化合物的平均组成占到了除尘灰总量的48%,其中K、Pb的平均含量(以K2O和PbO计)分别达到6%~10%和4%~6%左右,总铁TFe平均含量达到33%以上,碳平均含量在6%~9%左右,粉尘平均粒度约35μm~40μm。
国内外研究现状:
(1)首钢在迁钢循环经济工业园区规划设计中,设计了三条含铁尘泥加工处理的工艺路线,即:“多种尘泥均质化造粒回用烧结工艺”、“OG泥与氧化铁皮造块回用转炉造渣工艺”和“高含锌与高含钾、钠的尘泥脱锌、脱钾、脱钠工艺”.
(2)宝钢、武钢、鞍钢、湘钢、邯钢等单位相继开发了“浮选-磁选”或“重选-磁选-浮选”联合流程从瓦斯泥中回收利用金属铁的工艺。
(3)韶钢成功开发了“火法富集-湿法处理”回收利用瓦斯泥中氧化锌的无害化工艺,并建立了一套完整的活性氧化锌生产线。
(4)柳钢开发了“火法富集-湿法提取”的瓦斯泥处理工艺,用于制备超细碳酸锌,也获得了较好的经济、社会和环境效益。
(5)攀钢采用硫酸浸出富集法从瓦斯泥中回收活性氧化锌,全程实收率达到79.1%,且回收的活性氧化锌质量达到了化工部部颁标准。
(6)提出了采用“弱磁→强磁”两级梯度磁选方法回收含铁粉尘中的铁原料。
通过磁选选铁,使尾矿中的铅、锌等重金属得到富集和回收利用,但该专利未提到锌、铅的具体提取方法。
(7)国外目前处理含铁尘泥的典型技术有[1]:①含铁尘泥冷固结造块回用高炉炼铁技术;②转底炉处理高锌含铁尘泥技术;③熔融还原法处理含铁尘泥技术。
其中:含铁尘泥冷固结造块回用高炉炼铁技术能缩短尘泥回用钢铁冶炼系统的流程,具有一定的优越性,但因法需要水泥等粘结剂量大、堆放场地量大、能耗高、炉渣量大等使得成本较高,高炉生产效率较低;转底炉和熔融还原技术具有较为彻底的除杂和回收金属铁资源功能、资源综合利用率高、处理量达、环境污染小等优点,但投资较高,生产成本居高不下,难以在短时间内推广应用。
钢铁企业含铁粉尘的几种处理工艺
1返回处理法
返回处理法是将钢铁厂各生产工序产生的含铁粉尘以原料形式直接返回到
烧结工序或原工艺进行处理,其主要目的是回收粉尘中可用于钢铁生产的铁、焦炭等有价资源,减少粉尘数量,但粉尘的配比和加入量不宜多,难以有效地除去有害杂质。
2火法处理法
火法处理工艺是在一定的高温下,利用金属氧化的还原温度及融沸点的差异,采用粉尘中的碳粉作为还原剂,还原粉尘中金属氧化物并加以回收部分或者全部有价元素的一种处理方法。
火法处理的方法较多,列举一些较为成熟的处理工艺如下:回转窑工艺法(简称SPM法)、BRS法、环形炉工艺法又称Inmetco 法(是将含铁尘泥、碳粉和粘结剂混合制成球团)、
3湿法(水力)处理法
含铁粉尘的湿法工艺,亦称水冶工艺,是一种不同于火法处理,利用湿法冶金原理处理粉尘的方法。
一般采用酸、碱或氨盐溶液来浸出分离锌、铅等物质,所得锌、铅等产品质量高,可直接销售。
包括:(1)氯铵(NH4Cl)法、(2)水力旋流脱锌法。
4火法-湿法联合处理技术
火法-湿法联合工艺是结合含铁粉尘处理中火法与湿法工艺各自优点(即利用火法反应速度快、生产效率高等优点,湿法工艺所得产品质量高、分离彻底等优点),联合处理粉尘的方法。
包括:(1)MRT处理法、(2)火法富集-湿法分离法。
5稳定化处理法
近几年,粉尘稳定化处理法发展迅速,它是包括玻璃化工艺和固态化处理,属于一独特的处理方法。
包括:(1)SuperDetox处理法、(2)IRC处理法6选冶处理技术
(1)弱磁—强磁选矿法
含铁粉尘中主要矿物为磁铁矿、其次为赤铁矿,且铁矿物的单体解离度高,而含铁粉尘中Na2O、K2O、ZnO等有害杂质,基本上无磁性。
故用“弱磁—强磁”梯度磁选方法回收粉尘中铁精矿,并可降低铁精矿中Na、K等有害成分的含量。
(2)磁选—摇床联合选矿法
根据高炉瓦斯泥的矿物特性,通过弱磁选初步实现瓦斯泥中铁矿与碳、锌等物料的分离,所得铁矿在经脱磁、脱水、摇床等工序后得到铁精矿和含锌、碳较高的尾矿。