8D报告模板PDF.pdf
8D报告范文模板

8D 报告 8D Report
供应商代码Supplier Code XXX 零件名称Part Name
完成日期Closed Date 2020/9/1
供应商名称Supplier Name
XXX 更新日期Last Update
验证Verification / Validation: 有效
D7-预防措施Prevent Recurrence Actions: 发生预防Occurrence 1.依标准XXXXX再次培训 2.XXXXXXXXXXXXXXXXXXXXXXXXXX 3.XXXXXXXXXXXXXXXXXXXXXXXXXXX,跟踪2个月,反馈结果,每天对10台车进行抽检
发生 Occurrence
人员: ①返修人员在返修时,XXX以致造成此问题流出 方法: ②返修人员未进行相关培训,XXXXX意识不强
100%
体系的Systemic 允许发生原因Why did our system allow the problem to occur ?
影响比例%Affect Percent
流出预防Escape XXXXXXXXXXXXXXXXXX发现问题做记录XXXXXXXXXXXXXXXXXXXXXXXXXXXXXXX
更新文件 D-FMEA 横向展开:是 否 D8有-受类表似彰的的产小
P-FMEA
Control Plan
Work Instruction YES
Maintenance Plan NO
人员:
在返修过程中,缺少检查确认步骤
NA
流出 Escape
流出原因Why did the problem reach CFMANJ ? 返修人XXXXXXXXXXXXXXX。
8D报告过程以及8D是指的什么讲解PDF.pdf

8D具体是指什么?什么样的情况下需出8D报告?一般什么样的情况下需出报告?在某一制程由于某种原因影响到下一制程的正常运做时,需要对此种不良原因进行分析,一般我们称为FA,即失效分析。
8D是FA的一种。
它可以完整的描述及分析不良发生的原因。
并且给出临时对策及长期对策。
对特异性原因导致的问题需要回复8D。
以防止此类问题再次发生。
8D最早是福特公司使用的很经典的分析手法1D: 成立团队公司明确团队队长由第一副总亲自担任;质保部负责召集和组织团队的活动;团队成员由包含与问题密切相关的技术人员或管理人员、相关的质量工程师组成。
2D:描述问题为了容易找到问题症结所在防止问题再发生,应使用合理的思考及统计工具来详细地描述问题:发生了什么问题?发生地点?发生时间?问题的大小和广度?从这几方面收集关键资料。
3D: 围堵行动为使外部或内部的客户都不受到该问题的影响,制定并执行临时性的围堵措施,直到已采取了永久性的改进。
要确保围堵行动可收到预期的效果。
4D: 找根本原因就问题的描述和收集到的资料进行比较分析,分析有何差异和改变,识别可能的原因,测验每一个原因,以找出最可能的原因,予以证实。
5D: 永久性纠正针对已确认的根本原因制订永久性的纠正措施,要确认该措施的执行不会造成其它任何不良影响。
6D: 验证措施执行永久性的纠正措施,并监视其长期效果7D:预防再发生修正必要的系统,包括方针、运作方式、程序,以避免此问题及类似问题的再次发生。
必要时,要提出针对体系本身改善的建议。
8D: 肯定贡献完成团队任务,衷心地肯定团队及个人的贡献,并加以祝贺。
由最高领导者签署8D的流程D1-第一步骤: 建立解决问题小组若问题无法独立解决,通知你认为有关的人员组成团队。
团队的成员必需有能力执行,例如调整机器或懂得改变制程条件,或能指挥作筛选等。
D2-第二步骤: 描述问题向团队说明何时、何地、发生了什么事、严重程度、目前状态、如何紧急处理、以及展示照片和收集到的证物。
8D报告格式(免费)

第 1 页
KONGTOP
NO.
8D报告
纠正措施(perma 日期
审核 Approved By:
审核日期 Approved Date:
6、纠正措施效果验证(Discipline 6.Verification of Effectiveness) NO. 1 2 审核 Approved By:吕曲 7、预防再现措施(Discipline 7.Prevent Recurrence) NO. 1 2 审核 Approved By:吕曲 审核日期 Approved Date:2011-1-5 预防再现措施(Prevent Recurrence) 负责人 日期 审核日期 Approved Date:2011-1-5 效果验证(Verification of Effectiveness) 确认人 日期
产品编号 (Part Number) 产品名称 (Part Name)
1、小组成员(Discipline 1.Team Members) 部门(Dept): 姓名(Name): 2、问题描述(Discipline 2. Problem Description) QA IQC 生产 工程 开发 采购 业务
备注(Memo)
第 2 页
8、客户确认及评价(Discipline 8.Customer satisfaction degree) 第一批产品满意程度:yes( 第二批产品满意程度:yes( 第三批产品满意程度:yes( ) ) ) no( no( no( ) ) ) 与客户_________联系,确认此批出货产品有/无以上不良现象。 与客户_________联系,确认此批出货产品有/无以上不良现象。 与客户_________联系,确认此批出货产品有/无以上不良现象。
完整8D报告模板

版本:产品名称Product Name 客户名称Customer Name客户型号Customer model工厂产品型号Positec model 客户订单号Order no.日期码Date code合同编号Contract No. 合同数量Quantity异常发生日期Complaint date发文部门Dispatched by 异常信息来源Message from要求完成时间Required complete dateDISCIPLINE 1: Use Team Approach (建立解决问题小组)质量改进小组组长:质量改进小组成员:□产品工程师_______________________ □研发工程师______________ □品质工程师_______________________ □制程工程师______________ □采购工程师/SQE___________________ □生产主管________________ □其他_____________________________填写人:日期:DISCIPLINE 2: Describe The Problem (问题描述)问题等级______类(填写A or B or C)□图片说明及详细信息描述:填写人:日期:DISCIPLINE 3: Implement And Verify Containment Action (执行暂时对策)□返工/补充加工(QE/PE)□质量问题通知供应商(SQE或采购)□生产计划调整(QE)□(在线/在途/库存)零部件库存处理(PE)□通知客户/QA (公司QA或工厂QE)□国外产品处理(项目主管or品质经理)□其它相应措施说明:填写人:日期:版本:DISCIPLINE 4: Define and Verify Root Cause (找出问题的真正原因)原因分析(责任部门填写)□设计缺陷/Design defects □规格、标准缺陷/criterion defects□工装设备缺陷/Equipment defects □检查判定缺陷(误判、错判)/Wrong verdict□制程及作业上缺陷(含料件)/Parts or assembling defects□模具、夹具缺陷/Fixture defects □其他/Others具体说明/Described in detail:□失效模式再现验证说明□改进失效验证说明附原因分析报告《》(插入附件, 空白表单在下面连接内)填写人:日期:DISCIPLINE 5:Choose and Verify Permanent Corrective Action (选择永久对策)相应措施进度及说明:具体内容责任人计划完成时间样品采购样品确认工程样机装配实验申请实验结果判断工装申请小批验证□ECR:(连接到文管中心下文件)□修模单:(连接到文管中心下文件)□其它填写人:日期:DISCIPLINE 6: Implement Permanent Corrective Action (执行及验证永久对策)□品质标准(品质人员提供,需明确清晰):□正向模式验证:□反向失效模式验证:实际完成情况确认人实际完成时间样品采购样品确认工程样机装配实验申请实验结果判断工装申请小批验证(工程人员提供正/反验证需包含详细数据,如实验申请号,验证结果等.)(品质)填写人:日期:(工程)填写人:日期:DISCIPLINE 7: Prevent Recurrence & Standardization (防止再发生措施及标准化)版本:产品工程师PE:□ECN□BOM□PQC检指/培训□IQC检指/培训制程工程师:□总装工艺卡/装配人员培训品质工程师QE:□FQC检指/培训采购部SQE:□供应商培训□供应商检指□供应商检具□供应商工艺□供应商库存处理其它填写人:日期:DISCIPLINE 8: Congratulate Our Team (批量验证/团队激励)改善情况的追踪:□ECN□BOM□供应商培训□供应商检指□供应商检具□供应商工艺□供应商库存处理□IQC检指/检验结果□PQC检指/检验结果□FQC检指/检验结果□总装工艺卡□试验/检验考核结果填写人:日期:经办/drafted by: 部门审核/checked by: 品质经理审核: 批准/Approved by:一、QC培训记录二、QC检指记录三、供应商方面培训、检(插入相关支持文件)指、检具、工艺、协议记录四、工艺文件备注:1.对异常问题或改进状态的描述要尽量有图片说明或详细的信息记录。
8D报告-模板

日期
日期 日期
第2页
no( ) no( ) no( )
纠正措施
负责人
效果验证
确认人
预防再现措施
负责人
与客户_________联系,确认此批出货产品有/无以上不良现象。 与客户_________联系,确认此批出货产品有/无以上不良现象。 与客户_________联系,确认此批出货产品有/无以上不良现象。
备注(Memo)
保存期限:三年
主题 发生地点
客户 供应厂商 1、小组成员 部门: 姓名: 2、问题描述
组长
8D报告
发生时间 产品编号 产品名称
总批量数 不良数
要求完成日期
质量部门
生产部门
技术部门
编号: 提出日 提出人员 修订日期
其他部门
3.1、即日纠正措施 NO. 1 2 3
注:前3D在问题发生后的24小时内回复。 3.2、即日纠正措施结果
NO. 1 2 3
4.1、问题发生的根本原因(制造原因)
暂时补救的纠正措施 即日纠正措施结果
负责人
日期
负责人5、永久性纠正措施 NO. 1
2
3
4
注:前5D在问题发生后的14个工作日内回复。 6、纠正措施效果验证
NO. 1
2 7、预防再现措施
NO. 1
2 8、客户确认及评价 第一批产品满意程度:yes( ) 第二批产品满意程度:yes( ) 第三批产品满意程度:yes( )
8D报告(物料品质信息投诉单)

物料品质信息投诉单(8D)NO:011、此报告为注塑企业物料品质异常信息报告模板,所有品质异常必须严格按照此模板进行反馈;2、根本原因分析必须清晰,彻底,措施必须涉及我司物料、供应商在库和在线品的处理方案及供应商后续的永久预防方案。
如果原因分析及改善措施比较多,供应商可以在此模板后面添加附件。
6D 效果验证(AFFIRM OF EFFECTIVENESS):责任人/日期(PRINCIPAL/DATE:供应商(SUPPLIER)发生日期(OCCURRED DATE)物料型号(PART MODEL)物料料号(PROGRAM)批量数(TOTAL QUANTITY)不良率(NONCONFORMANCE RATE)发生环节(OCCURRED FROM)异常报告编号(REPORT NO.)回复日期(RESTORE DATE)1D:问题描述(NONCONFORMANCE DESCRIPTION):提出人/日期(PRESENTER/DATE):2D:处理成员(Internal/External Members)日期(PRINCIPAL/DATE):3D:临时措施(TEMPORARY ACTIONS):责任人/日期(PRINCIPAL/DATE):4D:根本原因分析(DEFINE ROOT CAUSE OF NONCONFORMANCE):责任人/日期(PRINCIPAL/DATE):5D:改善措施(CORRECTIVE ACTIONS):责任人/日期(PRINCIPAL/DATE):7D:永久性措施(PERMANENT ACCTIONS):责任人/日期(PRINCIPAL/DATE):8D:最终确认(FINAL AFFIRMANCE BY TW):确认人/日期(AFFIRMANT/DATE):。
8D报告模板

8D 报告/8D Report 发出原因 Submit reason:□客户投诉Customer complaints: □ 供应商审核NCR NCR of Supplier audit: □ 其他,注明原因 Others,Indicate reason:发出日期Submit date:重复性发生If happen again:(是Yes□ 否No□)备注:如果重复发生,必须分析上次纠正/预防措施的有效性 Remark:ifhappen again,must analysi validity of last correct/prevent step:要求回复日期Require reply date:3D 纠正措施 Correct step 完成日期Completedate:5D 预防措施 Preventive Measure 5.1根据4.2原因分析制定对应的措施、责任责任、生效日期,针对涉及安全问题,要求立即实施 According to 4.2 root cuase analysis take preventiveMeasure,including responsibility and effective date,measure involve insafetyexecute immediately生效日期Effectivedate:8D#:1D 小组成员 Team members 生产 张某 质量 李某 技术 张某设计 王某 服务 李某Production xx ;Quality xx;Technology xx;R&D xx;Custmer service xx and so on;2D 问题描述 Problem description时间 Happen date:问题描述 Problem description :例如:2018/8/21 电机编码器无法旋转,更换编码器后故障消除,编码器序列号xx,电机序列号xx ,数量1pc 数量 Nmuber:供应商 Supply:4D 根本原因 Root cause4.1使用柏拉图确定主要问题,使用二八原则优先解决主要问题 Using Plato method find key problems,and solve key problems according to 2 8 principle4.2针对具体问题使用鱼刺图分析故障根本原因,如该报告只分析单个故障,直接使用4.2,无需使用4.1柏拉图方法 Using fishbone diagram analysis problem root cause,if this 8D reoport only analysis single problem,begin from 4.2 step not from 4.1包括涉及相关部描述:4W (where 、when 、who 、what ),尽量量化,以数据描述问采取的临时措施,例如紧急检查等,避免不合格项造成的进一步影响,根本原因分析,使用质量工具(鱼刺图、直方图、柏拉图等)进行原根据根本原因分析,提出相应的根本解决措施,并明确生效日期技术部门出具的详细的6D 效果确认 Effect Check6.1根据5.1措施实施情况,检查措施实施的效果情况,可通过制程现场、顾客反馈等方式确认 According to 5.1 measure execute situation,checkimprovement effect from process check and customer feedbac效果 Effect %:7D 标准化 Standard7.1根据6.1确认效果情况,如问题已得到有效改进,可对改进措施进行标准化,并应用于制程生产制造过程 According to 6.1 measure effect check,if problem has solved should Standardize improvement mesure,including FMEA ,control plan,work Instruction modifies 完成日期 Complete Date:8D 问题关闭 Problem close□关闭 Close□ 否,进一步验证意见 No,Further validation□ 重发 8D(新8D编号:——————)Resubmit 8D(new 8D#:————)□ 其他——————————Other——————————验证人 Check people:完成日期Complete Date:版权AIEIN质量所有,更多搜索 AIEIN质量 了解根据纠正措施的实施,确认实际的改进效果根据改进效果,对改进措施进行标准化,修改作业指导书、控制计划、。
8D报告模板

——需要有责任人和完成时间 ——需要有责任人和完成时间
96h
★说明: 原因和对策确定的原则:四不放过原则 ①原因未查清不放过 ②责任人未受到处理不放过 ③责任人和周围员工未受到教育不放过 ④制定切实可行的整改措施没有落实不放过
D6.验证纠正措施
Verify Corrective Actions
5D
24h
D3.应急措施
Containment Action(s)
风险批次
抽检排除风险
围堵措施
24h
结论
1、成品库数量及批次
抽检2K不良1k,风险极高 100%挑选使用
出厂
2、组测的数量及批次
抽检2K不良1k,风险极高 100%挑选使用
出厂
3、AA的数量及批次
正常可用
4、COB的数量及批次
正常可用
5、SMT的数量及批次
正常可用
6、原材料库的数量及批次
正常可用
7、客户端批次及数量
正常可用
8、检验点批次及数量
正常可用
小结:库存重检确认污点不良率较高,且大部分为浅污点软件不可抓,存在一定出货风险; 故厂内在制&库存品已安排全部隔离
D4.识别问题根因
Identify Root Cause of the Problem
1.1 分析流程如下: 1、头脑风暴确 定潜在原因(至 少10条)
核算质量成本
感谢您的聆听!
汇报人:XXX
结论:(措施是否有效实施)
D7.预防措施标准化
Preventive Action(s)
二、加入到LL中(必填,以附件格式插入报告中)
三、事件回溯(必填,以附件格式插入报告中) 将之前验证的3-5条发生原因和流出原因(检验工序的
8D报告格式模板

Continuous Improvement Plan持续改善计划 No.:Eight (8) Step Problem Solving(8个解决问题之步骤)类别:A() B()CUSTOMER NAME:(客户名称)PART NUMBER:(零件编号)PART DESCRIPTION:(零件名称)QUANTITY:(数量)DEPARTMENT:(部门)DATE:(日期)1. TEAM CHAMPION:(专案领队人)TEAM MEMBERS(团队成员):2. DESCRIBE THE PROBLEM: (WHAT'S WHEN'S, and WHERE'S - include samples when possible)(不良现象描述:为何、何时、何处-如有可能包含样本)3. SHORT TERM FIX: (What you will do immediately)(暂定对策措施:应急措施)Target Date:(预计完成日期)Effective Date:(实际完成日期)4. ROOT CAUSE OF PROBLEM(问题的根本原因):Indicate problem solving tools used, i.e.,Pareto-Cause/Effect Process.(说明解决问题所使用之工具:如柏拉图分析、特性要因分析等)5. LONG-TERM PERMANENT CORRECTIVE ACTION(永久对策矫正措施):Target Date:(预计完成日期)Effective Date:(实际完成日期)*6. PREVENT REOCCURENCE(预防再发对策):Modify Systems Procedures as required.Document the new procedures, removeobsolete procedures, revise standards.提示:如有必要修改系统程序、建立新程序移除、淘汰旧的程序,修订标准。
8D报告模版

负责人
日期
审核 Approved By:
审核日期 Approved Date:
6、纠正措施效果验证(Discipline 6.Verification of Effectiveness)
NO.
效果验证(Verification of Effectiveness)
1
确认人
日期
2
3
审核 Approved By:
备注(Memo)
1.1-4项由责任单位填写,并请务必在3日内回复. 2.请以此格式回复, 内容很多可自增页面, 但须具备上述项目.
表单编号: 保存期限:
第2页
KONGTOP
主题 (Subject) 发生地点 (Occurred
Site) 客户 (Customer)
供应厂商 (Supplier)
深圳市XXXXXX实业有限公司
ห้องสมุดไป่ตู้
8D报告
发生时间 (Occurred
Time)
产品编号 (Part Number)
(CA report in 8D format)
投诉类型 (Rea For CA)
日期
系统原因 起草Prepared By:
审核Approved By:
第1页
完成日期Completed Date:
KONGTOP
8D报告
5、永久性纠正措施(Discipline 5. Permanent Corrective Actions)
NO.
纠正措施(permanent Corrective Actions)
邮件投诉
提出日 (Date Raised)
提出人员 (Raised by)
要求完成日期 (Due Date)
8D报告模版PDF

D1:团队建立 Team Establishment
姓名
小组职务
职责
联系电话
电子邮件
D2:问题描述 Problem Description
5W1H
is
what
when
where
who
why How much
不良图片
D3:Containment plan: (临时对策)
序号 1
2
3 4 5
地点
客户端在线
客户端库存
在线 库存 运输途中
排查数量 不良数
400+
10
950
950
750
10
550
0
700
0
1300
0
0
0
不良率
100% 100% 1.3% 0% 0% 0% 0%
不良处理方案 责任单位/人
临时处理方案:
实际完成时间
D4:根本原因分析 Root Cause Analysis
一、导致异常的工序
工艺流程: 压凸包 → 复合切边 → 铆螺钉 → 镀锌镍 → 贴PET膜 / 热压
异常工序
折弯成型 → 烘烤 → 全检包装 → 入库
D4:根本原因分析 Root Cause Analysis
二、不良产生的原因。
人
机
料
人员是否经过培训
作业人员是否更换
使用设备是否正确
作业人员操作 是否与SOP一 致
SOP是否正确,是 否是最新版本
非要因,不影响
参数设置是否与SOP一 致
材料是否变更或更换 模具是否发生异常
测量方法是否正确
测量是否会导致不良
测量位置是否正确
8D报告标准模板

D0:准备 Preparation:
主题:
Subject:
D1:团队成员 Team:
先锋: Pioneer 成员: Team Members:
D2:问题描述 Problem Description :
责任单位: Responsible unit: D6:效果验证 Effectiveness Verification:
责任单位: Responsible unit: D7:防止再发生 Actions to Prevent Recurrence:
责任单位: Responsible unit:
D8:关闭、总结及经验 Closure - Conclusion - Learning:
经办/日期:
审核/日期:
完成日期: Completion Date:
XXX/X/XX
完成日期: Completion Date:
XXX/X/XX
/X/XX
批准/日期:
接收日期: Received Date:
组长: Team Leader:
表单编号:XX.T-8D-001 版本号:A/0
pcs % XXX/X/XX
发现 场所
□IQC □OQC
□IPQC ■客户投诉
日期: Date:
缺陷 图片
XXX/X/XX
完成日期: Completion Date:
XXX/X/XX
描述人: Descriptor:
D3:临时对策 Containment Action(s):
责任单位: Responsible unit:
8D报告模版

塑料产品气味超标 分析整改8D报告
XXXXXXXXXX有限公司 质量部
201X年X月XX日
XXXXXXXXX有限公司
目录
• 一、组成小组 • 二、问题描述 • 三、临时措施 • 四、原因分析、原因确认 • 五、永久措施 • 六、永久措施实施与效果验证 • 七、系统预防
XXXXXXXXX有限公司 一、组成小组Form Team
气味试验报告: 塑料粒子、未喷漆产品合格
已喷漆产品两箱各抽样1只 其中1只OK、1只NG
所有已喷漆产品 全部红标签并隔离
XXXXXXXXX有限公司
三、临时措施TemporaryAction
2.临时生产措施
措施 类型
临时生产措施 TemporaryAction
负责人
完成时间
Responsibility
将本次整改内容排
3
查其他塑料件评估 风险,组织类似改
进
XXX
XX-XX-XX XX-XX-XX 同类产品测试报告
1、将烘箱上层的产品和烘箱底层的产品进行气味检测对比 2、将喷了脱模剂的产品和未喷脱模剂的产品进行气味检测对比
测试结果:烘箱上层的产品:3个3.5级 、2个4级,合格 烘箱底层的产品:3个4级、 2个3.5级,不合格 喷脱模剂产品:4个4级、 1个3.5级,不合格 喷脱模剂产品:4个3.5级、 1个3级,合格 结论:分析的问题实际表现与客户投诉一致,与原因排查问题一致,主体是喷漆烘烤设备温差 超标导致底层产品气味不合格,网片是模具难脱模,喷脱模剂造成产品批次质量不一致
4.1 过程流程问题分析 4.2 原因分析与验证(因果图) 4.2 故障再现 4.3 根本原因5W分析确认
4.1过程流程问题分析
8D报告(通用模板)

引言:8D报告是一种解决问题和改进过程的方法,它采用了多个步骤和工具来识别、分析和永久解决问题。
本文将介绍8D报告的通用模板中的第二部分,包括第三到第五个大点的详细阐述。
概述:在第二部分,我们将深入探讨8D报告的剩余步骤,包括确定短期、长期措施和效果确认。
每个大点将进一步细分为59个小点,以便更全面地介绍8D报告的实施细节。
正文:第三大点:确定短期的临时措施1.确定问题的严重性:在确定短期的临时措施之前,需要评估问题的严重性,以确定采取的措施是否十分迫切。
2.制定应急计划:根据问题的性质和紧急程度,制定临时措施的计划,以及纠正和预防措施的时间表.3.计划资源和人员:确定所需的资源和人员来执行临时措施,并明确各自的职责和任务,确保计划的顺利执行.4.实施和监控措施:根据制定的计划执行临时措施,有效监控措施的执行情况,并进行必要的调整和改进.5.记录和报告:记录临时措施的执行情况,包括措施的有效性和问题解决的进展,及时向相关方报告并汇总反馈意见。
第四大点:确定长期措施和预防措施1.分析根本原因:对问题进行深入的分析,找出问题的根本原因,以便制定长期的解决方案.2.制定长期措施:根据根本原因分析的结果,制定可持续性的长期措施,以确保问题不再重复出现.3.优先级和时间表:确定长期措施的优先级和时间表,以便有条不紊地推进实施.4.资源和预算:确定所需的资源和预算来支持长期措施的实施,并进行适当的调整和分配.5.审核和验证:对长期措施进行审核和验证,确保其有效性和可持续性,并进行必要的调整和改进.第五大点:效果确认和总结1.确认问题解决:对实施的长期措施进行效果确认,确保问题已经得到解决.2.总结分析经验:总结整个问题解决过程中的经验教训,包括问题的识别、解决方法的选择和执行过程中的反馈,以便提高团队的解决问题的能力.3.客户满意度评估:对客户进行满意度评估,以了解他们对问题解决过程和结果的评价.4.结果反馈:将问题解决的结果及相关信息反馈给团队成员、管理层和其他相关方,以促进知识共享和经验沉淀.5.关闭报告和跟踪:完成8D报告,关闭报告,并跟踪后续动作,以确保问题的持续解决和改进.总结:在第二部分,我们详细介绍了8D报告的剩余步骤,包括确定短期的临时措施、确定长期措施和预防措施,以及效果确认和总结。
8D报告模板及说明
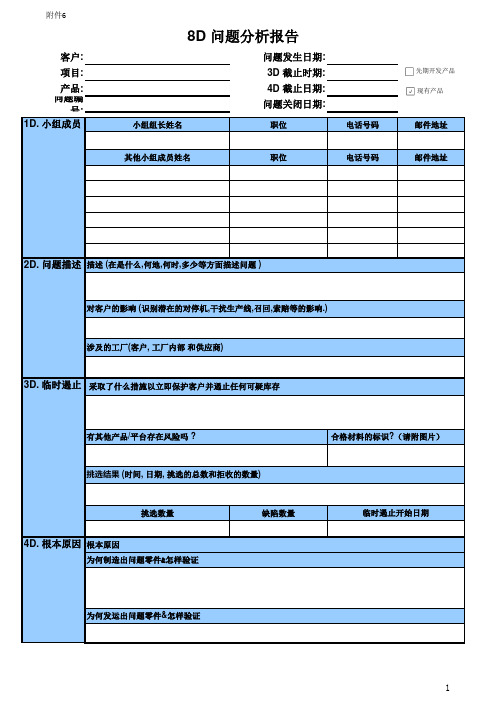
客户:
问题发生日期:项目:
3D 截止时期:产品:4D 截止日期: 问题编
号:
问题关闭日期:小组组长姓名职位电话号码邮件地址其他小组成员姓名职位电话号码邮件地址
挑选数量缺陷数量3D. 临时遏止1D. 小组成员2D. 问题描述4D. 根本原因根本原因
为何制造出问题零件&怎样验证
为何发运出问题零件&怎样验证
挑选结果 (时间, 日期, 挑选的总数和拒收的数量)
临时遏止开始日期
涉及的工厂(客户, 工厂内部 和供应商)
采取了什么措施以立即保护客户并遏止任何可疑库存
有其他产品/平台存在风险吗 ? 合格材料的标识?(请附图片)8D 问题分析报告
描述 (在是什么,何地,何时,多少等方面描述问题 )
对客户的影响 (识别潜在的对停机,干扰生产线,召回,索赔等的影响.)
先期开发产品现有产品。
2020年整理客诉8D报告格式.pdf

制成:王大大 2.团队成员: 组长:王小二(责任主管) 成员:王大大(品质专员)/张三(技术工程师)/李四(技术工程师)/王五(生产主管)
3.原因分析: a)不良品确认 1.9 月 10 日收到客退音沙不良 6pcs,观察外观无不良,如下图: 2.用音频扫描发生器把电压调至规格书要求 2.56v,频率 200-2KHZ,用声腔对客退不良进行音质确认,确 认音质音沙异常,如下图: 3.再将客诉不良品进行 BK 曲线测试,测试结果符合曲线要求,如下图: b)原因分析 1.技术员对客退不良品进行 X-ray 扫描分析,确认无不良,如下图: 2.研发工程师对客退进行拆解分析,拆去上壳,确认壳内外未不良,如下图: 3.技术员对单体拆解,稀释前盖胶,取下前盖--〉观察膜片及边缘胶--〉稀释边缘胶--〉观察音圈及磁路, 如下图: 3.1 在拆解过程中,每步拆解都对部件进行仔细观察,确认无不良再进行下一步动作,技术员打开膜片时, 发现音圈内侧有异物(用放大镜观测看出音圈内侧有异物),如图: 小结:因音圈内有异物,导致音沙不良 3.2 流出原因 ①对产线进行排查发现,6S 良好 ②对人员确认,人员走动频繁,排查发现 16 条线其中 2 位套音圈人员 2 套膜片人员未佩带手指套未配戴手 指套作业,如图: ③对工装进行排查,现场工装都干净整洁,清洗记录亦无异常 ④查询 OQC 检验记录,OQC 记录未记录检验的产品唯一编码,不能确认是否检验过 ⑤确认产线听音作业模式,2h 更换一次听音作业人员,排除疲劳作业,查看当天听音人员安排状况:有安 排新人进行听音作业=====〉怀疑为新人不熟悉听音导致漏检 小结:线上作业人员不按规范作业,人员走动频繁,导致异物落在音圈内,导致音沙,听音新人上线,导 致厂内漏检
分析人:李四/张三
4.短期对策:
- 1、下载文档前请自行甄别文档内容的完整性,平台不提供额外的编辑、内容补充、找答案等附加服务。
- 2、"仅部分预览"的文档,不可在线预览部分如存在完整性等问题,可反馈申请退款(可完整预览的文档不适用该条件!)。
- 3、如文档侵犯您的权益,请联系客服反馈,我们会尽快为您处理(人工客服工作时间:9:00-18:30)。
8D工作方法发表于2010年04月18日 16:31 阅读(1) 评论(0) 分类:方法简介8D又称团队导向问题解决方法、8D问题求解法(8D Problem Solving)是福特公司处理问题的一种方法,亦适用于制程能力指数低於其应有值时有关问题的解决,它提供了一套符合逻辑的解决问题的方法,同时对於统计制程管制与实际的品质提升架起了一座桥梁。
[编辑]8D工作方法的起源二战期间,美国政府率先采用一种类似8D的流程——“军事标准1520”,又称之为“不合格品的修正行动及部署系统”。
1987年,福特汽车公司首次用书面记录下8D法,在其一份课程手册中这一方法被命名为“团队导向的问题解决法”(Team Oriented Problem Solving)。
当时,福特的动力系统部门正被一些经年累月、反复出现的生产问题搞得焦头烂额,因此其管理层提请福特集团提供指导课程,帮助解决难题。
[编辑]8D适用范围该方法适用于解决各类可能遇到的简单或复杂的问题;8D方法就是要建立一个体系,让整个团队共享信息,努力达成目标。
8D本身不提供成功解决问题的方法或途径,但它是解决问题的一个很有用的工具;亦适用于过程能力指数低于其应有值时有关问题的解决;面对顾客投诉及重大不良时,提供解决问题的方法。
8D法是美国福特公司解决产品质量问题的一种方法,曾在供应商中广泛推行,现已成为国际汽车行业(特别是汽车零部件产家)广泛采用来解决产品质量问题最好的、有效的方法。
[编辑]8D的目标提高解决问题的效率,积累解决问题的经验;提供找出现存的与质量相关的框架;杜绝或尽量减少重复问题出现;8D格式的原则上针对出现的问题,找出问题产生的根本原因,提出短期,中期和长期对策并采取相应行动措施;8D法可跨部门建立小组来加强部门间的协调,推进问题有效解决,从而改进整个过程的质量,防止相同或类似问题的再发生,以保证产品质量。
[编辑]8D工作方法的运用不合格的产品问题。
顾客投诉问题。
反复频发问题。
需要团队作业的问题。
[编辑]8D工作方法的8个步骤8D是解决问题的8条基本准则或称8个工作步骤,但在实际应用中却有9个步骤:D0:征兆紧急反应措施D1:小组成立D2:问题说明D3:实施并验证临时措施D4:确定并验证根本原因D5:选择和验证永久纠正措施D6:实施永久纠正措施D7:预防再发生D8:小组祝贺[编辑]D0:征兆紧急反应措施目的:主要是为了看此类问题是否需要用8D来解决,如果问题太小,或是不适合用8D来解决的问题,例如价格,经费等等,这一步是针对问题发生时候的紧急反应。
关键要点: 判断问题的类型、大小、范畴等等。
与D3不同,D0是针对问题发生的反应,而D3是针对产品或服务问题本身的暂时应对措施。
[编辑]D1:小组成立目的:成立一个小组,小组成员具备工艺/产品的知识,有配给的时间并授予了权限,同时应具有所要求的能解决问题和实施纠正措施的技术素质。
小组必须有一个指导和小组长。
关键要点:成员资格,具备工艺、产品的知识目标分工程序小组建设[编辑]D2:问题说明目的:用量化的术语详细说明与该问题有关的内/外部顾客抱怨,如什么、地点、时间、程度、频率等。
“什么东西出了什么问题”方法:质量风险评定,FMEA分析关键要点:收集和组织所有有关数据以说明问题问题说明是所描述问题的特别有用的数据的总结审核现有数据,识别问题、确定范围细分问题,将复杂问题细分为单个问题问题定义,找到和顾客所确认问题一致的说明,“什么东西出了什么问题”,而原因又未知风险等级。
[编辑]D3:实施并验证临时措施目的:保证在永久纠正措施实施前,将问题与内外部顾客隔离。
(原为唯一可选步骤,但发展至今都需采用)方法:FMEA、DOE、PPM关键要点:评价紧急响应措施找出和选择最佳“临时抑制措施”决策实施,并作好记录验证(DOE、PPM分析、控制图等)[编辑]D4:确定并验证根本原因目的:用统计工具列出可以用来解释问题起因的所有潜在原因,将问题说明中提到的造成偏差的一系列事件或环境或原因相互隔离测试并确定产生问题的根本原因。
方法:FMEA、PPM、DOE、控制图、5why法关键要点:评估可能原因列表中的每一个原因原因可否使问题排除验证控制计划[编辑]D5:选择并验证永久纠正措施目的:在生产前测试方案,并对方案进行评审以确定所选的校正措施能够解决客户问题,同时对其它过程不会有不良影响。
方法:FMEA关键要点:重新审视小组成员资格决策,选择最佳措施重新评估临时措施,如必要重新选择验证管理层承诺执行永久纠正措施控制计划[编辑]D6:实施永久纠正措施目的:制定一个实施永久措施的计划,确定过程控制方法并纳入文件,以确保根本原因的消除。
在生产中应用该措施时应监督其长期效果。
方法:防错、统计控制关键要点:重新审视小组成员执行永久纠正措施,废除临时措施利用故障的可测量性确认故障已经排除控制计划、工艺文件修改[编辑]D7:预防再发生目的:修改现有的管理系统、操作系统、工作惯例、设计与规程以防止这一问题与所有类似问题重复发生。
关键要点:选择预防措施验证有效性决策组织、人员、设备、环境、材料、文件重新确定[编辑]D8:小组祝贺目的:承认小组的集体努力,对小组工作进行总结并祝贺。
关键要点:有选择的保留重要文档流览小组工作,将心得形成文件了解小组对解决问题的集体力量,及对解决问题作出的贡献必要的物质、精神奖励。
一般8D文件都是以表格形式出现。
[编辑]对8D工作方法的评价1.优点发现真正肇因的有效方法,并能够采取针对性措施消除真正肇因,执行永久性矫正措施。
能够帮助探索允许问题逃逸的控制系统。
逃逸点的研究有助于提高控制系统在问题再次出现时的监测能力。
预防机制的研究有助于帮助系统将问题控制在初级阶段。
2.缺点8D培训费时,且本身具有难度。
除了对8D问题解决流程进行培训外,还需要数据挖掘的培训,以及对所需用到的分析工具(如帕累托图、鱼骨图和流程图,等等)进行培训。
[编辑]8D和6σ的差异8D和6σ都是用于解决质量问题的有效工具,但两者之间又存在一定的差别。
1、关于工作步骤8D 解决问题的8个工作步骤和6σ解决问题的DMAIC过程大致可以分为4个部分,如表。
表 8D和6σ对照表1)第1部分对于一个未知原因的问题,8D质量方法的第一步是成立一个交叉功能小组。
小组成员应具备有关工艺、产品知识以及解决问题和采取措施的技能。
小组应指定1人为小组长以组织协调小组工作,并对小组的工作进度及成效负责。
问题说明就是陈述“什么东西出了什么问题”。
6σ也是依靠小组解决问题的方法。
6σ和8D都需要成立项目组,不同之处是8D小组长是在小组成员中指定1人担任,而6σ项目组长由黑带/绿带担任。
对于6σ来说,不是所有的问题都适合用6σ方法解决。
在选择6σ候选项目时,应该考虑以下问题:是否是反复出现的事件?范围是否狭窄?是否存在测量尺度?是否能在合理时间内确定测量系统?是否能对过程进行控制?项目是否提高了顾客满意度?如果以上所有问题的答案是“是”,那么这是一个顾客导向6σ的良好候选项目。
在确定阶段,需要采用适当的步骤来明确所选6σ项目是否符合以上要求。
项目小组首先要通过调查研究以确定顾客抱怨什么,抱怨的程度如何,并且将顾客的抱怨转化成关键质量特性(CTQ),即从顾客角度确定对顾客最重要的产品和服务特性。
并对该特性进行量化,确定该特性“好”到什么程度顾客才满意,从而编制出关键质量特性的可操作性定义。
在确定阶段6σ还提供了过程流程图、鱼骨刺图、因果矩阵等细化项目范围的工具,帮助项目小组对项目范围进行细化,以确保项目范围足够狭窄,使项目在较短的时间内(一般黑带项目为6个月)能够关闭。
2)第2部分8D在问题说明后,下一步就是确定和实施临时措施。
而6σ在确定问题后,并不急于立即采取措施,而是进行测量,用数据进行分析。
首先要对顾客抱怨的输出进行测量,以确定目前的输出处于什么水平,从而建立一个“基点”。
还要对产生输出的过程以及输入进行测量。
在这一步骤中,虽然8D 确定了要寻找并确定根本原因的一个原则,并建议可以用鱼骨图等分析工具,但可操作性不强。
但6σ却提供了一整套完整的测量和分析方法如过程能力分析、柏拉图、运行图、方框图、散点图等,并提供了专用的分析软件工具,使我们能够寻找和论证影响输出的根本原因。
3)第3部分8D在验证并确定永久纠正措施时,容易凭经验判断而缺少数据支持。
有些公司通过用户的反馈信息来验证改善措施,不但耗费时日,而且效果也难以保证。
所以难免发生永久措施实施后问题却没有改善的情况。
6σ在改善阶段提供了头脑风暴法、试验设计(DOE)等工具帮助确定改善方案。
改善方案确定后并不立即投入生产,而是要在一个小范围内试行。
并且用在测量阶段建立的测量系统对改善后的输出进行测量和分析,然后与“基点”进行对比,用数据证明改善措施是否确实改善了输出。
只有确实有效的改善措施,才能够在生产中施行。
4)第4部分8D和6σ都需要采取措施巩固小组取得的成果。
8D要求将与问题有关的管理系统、操作系统、工作惯例、设计与规程进行调整或修改,以防止这一问题和所有类似问题重复发生。
而6σ则通过防错策略控制输入并对生产产品或提供服务的过程进行持续监控以确保同样的问题不再发生。
另外,6σ强调预防的事先性,要求将生产产品或提供服务的过程设计或改造成能生产出6σ质量的产品或服务的过程,以防止缺陷产品或服务的产生。
8D 一般是用于解决已出现的问题。
2、关于改进目标8D方法提出小组通过8个步骤改善问题,但没有明确提出改进的目标。
6σ的目标非常明确,即追求零缺陷。
当然,6σ的目标并不是只通过1个6σ项目就能达到,而是通过一个又一个6σ项目,持续改进,不断地向目标迈进。
3、关于理念与文化6σ不只是一种质量改进方法,而且是一种新的理念和文化。
6σ认为质量不只是某个部门的事情,而是公司每个员工的工作。
公司要求员工“拥有”他工作的质量,强调全员参与及行为的无边界性。
追求完美成为公司每个员工的行为,从而相互协作,形成共同的目标和价值观。
因此,在某种意义上,6σ不单纯只是质量改进活动,更多的是一种业务活动。
公司的所有员工都有责任学习和贯彻6σ方法。
换句话说,6σ使公司的需求、顾客的需求和个人的需求相统一,从而克服了其他质量方法部门之间相互脱节、员工之间相互推诿、公司目标和顾客需求不一致的缺点。
同时,6σ引导公司的各项活动的决策、分析和改进必须基于对经过量化的客观数据作为事实而进行,更加强调科学性和客观性。
8D还没有上升到一种理念和文化。
6σ不仅可以用于质量改进,而且可以用于组织各个方面的改进。
管理、设计、采购、制造、市场、维修、服务等各个领域都可以应用6σ方法进行改进。
而8D则主要是用于质量改进。