窑中控作业指导书
水泥厂窑中控室作业指导书

烧成车间窑中控室作业指导书中控室窑操作员作业指导书1、目的:使烧成系统在受控状态下运行,合理地控制系统参数,稳定热工制度,煅烧出质量合格的熟料,完成熟料生产任务,保护好窑衬及炉衬,树立质量、环境、计量、安全意识,达到防治污染、节能降耗和安全生产的目的。
2、范围:适用于中控室窑操作员。
3、职责与权限:3.1负责窑系统设备的开停,有权利对突发事件紧急停车,力求收尘设备与主机设备同步运行,发现异常及时处理或上报班长及有关人员。
3.2负责窑系统参数的监视、控制,保证生产、计量设备安全有效地运行,运行中力求高效、低耗,有必要时以口头或书面的形式向技术人员提出操作参数修改及其他建议。
3.3负责窑产、质量指标的完成。
严格按照生产部、化验室要求进行监视、控制,负责熟料产量、质量指标的完成,力争控制消耗在合理范围之内。
3.4负责窑系统操作过程中出现的安全、环境、计量等不符合体系要求情况的调整、处理,并及时通知巡检工检查。
3.5熟悉并理解ISO9001、GB/T28001、ISO14001、GB/T28001各质量体系的名词术语、方针、目标。
3.7熟悉本系统或本岗位环境因素、危险源,熟悉应急与响应方案。
3.8完成管理人员临时交办的任务。
3.9记录书写工整、规范,交接班清楚。
3.9、负责搞好本班卫生。
3.10.检修时参与检修工作。
4、技术要求:4.1、参数控制:4.1.1、投料量330t/h。
4.1.2、一级预热器出口≤360℃。
4.1.3、五级预热器出口温度850-890℃。
4.1.4、分解炉出口温度860-900℃。
4.1.5、窑尾烟室温度950-1050℃。
4.1.6、窑头电收尘温度≤250℃。
4.1.7、三次风温≥800℃。
4.1.8、出篦冷机熟料温度<100℃,不见红料。
4.1.9、220℃<窑筒体温度<350℃。
4.1.10、一级预热器负压4500-6000Pa。
4.1.11、窑尾烟室负压200-400 Pa。
回转窑中控操作余热锅炉的作业指导书
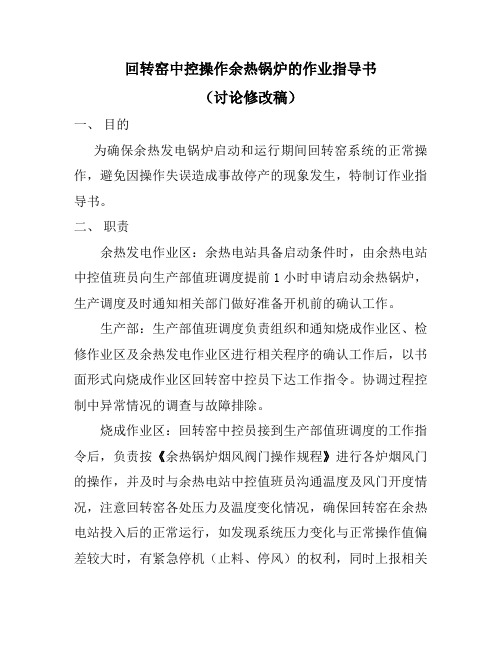
回转窑中控操作余热锅炉的作业指导书(讨论修改稿)一、目的为确保余热发电锅炉启动和运行期间回转窑系统的正常操作,避免因操作失误造成事故停产的现象发生,特制订作业指导书。
二、职责余热发电作业区:余热电站具备启动条件时,由余热电站中控值班员向生产部值班调度提前1小时申请启动余热锅炉,生产调度及时通知相关部门做好准备开机前的确认工作。
生产部:生产部值班调度负责组织和通知烧成作业区、检修作业区及余热发电作业区进行相关程序的确认工作后,以书面形式向烧成作业区回转窑中控员下达工作指令。
协调过程控制中异常情况的调查与故障排除。
烧成作业区:回转窑中控员接到生产部值班调度的工作指令后,负责按《余热锅炉烟风阀门操作规程》进行各炉烟风门的操作,并及时与余热电站中控值班员沟通温度及风门开度情况,注意回转窑各处压力及温度变化情况,确保回转窑在余热电站投入后的正常运行,如发现系统压力变化与正常操作值偏差较大时,有紧急停机(止料、停风)的权利,同时上报相关领导,并做好相关记录。
三、启动和运行调整原则⑴余热锅炉运行应不影响回转窑生产,锅炉启动和维护必须坚持“副业服从主业,主业兼顾副业”的原则,既要保证生产安全顺行,也要保证锅炉的经济运行。
⑵统筹兼顾,安全第一,保证回转窑及余热锅炉稳定。
⑶首先满足回转窑正常生产的需求,其次是最大限度的回收剩余余热。
四、操作指导与注意事项⑴、AQC炉投入后会造成窑头除尘器入口温度低、负压大和窑头3#排风机电流大,应及时调整余热锅炉入口风门开度,保持窑头负压,避免负压过大,造成燃烧器(喷煤管)回火事故。
⑵、AQC炉受热管受高速含尘烟气的冲刷与磨损,会导致穿孔和爆管的事故。
一旦事故发生,应积极采取措施,防止水流入拉链机,造成入库熟料结块。
⑶、由于篦冷机料层有波动,导致AQC炉进口废气温度波动很大,产生的蒸汽压力和温度变化也很大。
采用开启窑头冷风门的方法,虽能降低废气温度,但不经济。
建议操作上稳定篦冷机料层及各室风量,避免发生管道内保温层的脱落。
中控窑操作员作业指导书
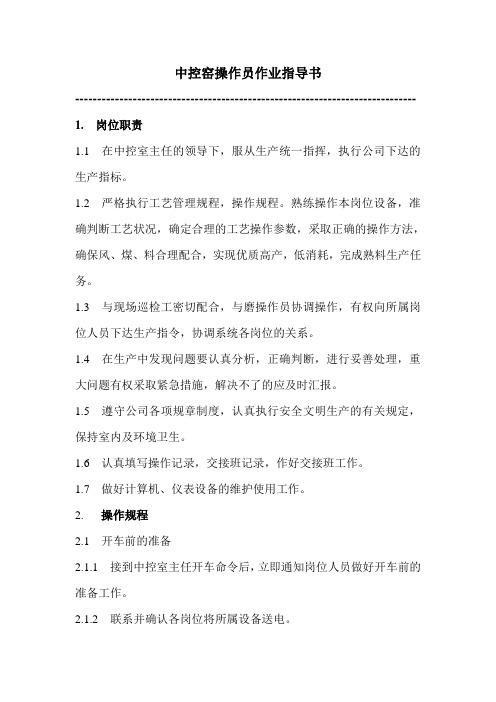
中控窑操作员作业指导书----------------------------------------------------------------------------- 1.岗位职责1.1 在中控室主任的领导下,服从生产统一指挥,执行公司下达的生产指标。
1.2 严格执行工艺管理规程,操作规程。
熟练操作本岗位设备,准确判断工艺状况,确定合理的工艺操作参数,采取正确的操作方法,确保风、煤、料合理配合,实现优质高产,低消耗,完成熟料生产任务。
1.3 与现场巡检工密切配合,与磨操作员协调操作,有权向所属岗位人员下达生产指令,协调系统各岗位的关系。
1.4 在生产中发现问题要认真分析,正确判断,进行妥善处理,重大问题有权采取紧急措施,解决不了的应及时汇报。
1.5 遵守公司各项规章制度,认真执行安全文明生产的有关规定,保持室内及环境卫生。
1.6 认真填写操作记录,交接班记录,作好交接班工作。
1.7 做好计算机、仪表设备的维护使用工作。
2. 操作规程2.1 开车前的准备2.1.1 接到中控室主任开车命令后,立即通知岗位人员做好开车前的准备工作。
2.1.2 联系并确认各岗位将所属设备送电。
2.1.3 通知化验室、工程师站给予必要配合。
2.1.4 确认所有设备备妥,确认现场准备工作完毕。
2.2 开车顺序2.2.1 启动点火烟囱,调整其高度,使窑头负压在0—-20Pa。
2.2.2 启动窑头一次风机,调节风机转速使其具备点火条件。
2.2.3 通知岗位给油点火。
2.2.4 适时启动喂煤罗茨风机。
2.2.5 启动窑头喂煤设备组,严格按照升温曲线控制喂煤量,坚持“慢升温,不回头”原则,适时启动窑中稀油站组,窑尾风机稀油站组,窑尾高温风机组。
2.2.6 启动生料入窑收尘组。
2.2.7 启动熟料输送组。
2.2.8 启动磨主传动。
2.2.9 启动冷却机组。
2.2.10 启动冷收尘风机。
2.2.11 启动冷却机风机组。
2.2.12 点火烘窑后,通知现场用辅助电机慢转窑,烟室温度850℃时,开主传动。
窑 作 业 指 导 书

窑作业指导书1岗位职责a)完成规定的质量指标,并保持质量稳定b)加强工艺操作,保持工况稳定c)负责所属设备的操作和维护保养,及时处理设备故障,参加设备检修和验收。
d)执行生产指令,完成生产任务e)认真操作,严格执行作业指导书和安全操作规程,严密注视窑系统各参数的变化,做到及时发现问题,及时通知现场及有关人员,及时调整、处理,确保窑热工制度的稳定,实现“优质高产低消耗”,保证系统的负压操作,严禁正压操作,造成环境污染f)负责中控室操作台的整洁和卫生。
g)负责紧急情况(职业健康安全、环保、设备等方面)时采取必要的应急措施,防止事态进一步扩大和恶化h)对本岗位各种职业健康安全危险源进行有效控制,降低或消除各种职业健康安全风险i)节约能源资源,杜绝浪费j)按时填写,保证各操作记录的真实性和准确性,同时做好各记录的保管和上交工作k)遵守厂规厂纪,认真执行交接班制度,做到交班清楚,接班明确;l)完成领导交给的各种临时任务认真遵守劳动纪律,厂规厂纪,确保熟料质量和产量的完成,服从中控室主任调动和指挥;m)负责中控室操作台的整洁和卫生。
2现场管辖区域中控室、休息室及操作台、筒体扫描仪等设备和窑操作系统3作业标准及要求3.1质量要求3.1.1熟料fCaO≤1.5%。
3.1.2熟料28天抗压强度月平均值≥52.0MPa。
3.2工艺3.2.1保证煅烧1450℃以上。
3.2.2窑炉燃料重量比为4:6。
3.2.3入窑生料表现分解率85~95%。
3.3设备3.3.1杜绝重大设备事故3.3.2所辖设备达到设备完好标准3.4职业健康安全3.4.1杜绝重大及以上人身、安全事故的发生3.4.2按规定穿戴劳动保护用品3.5环保3.5.1各种污染物排放符合规定要求新线窑头电收尘排放浓度≤150mg/m3N。
3.5.2要求新一线窑尾电收尘排放浓度≤150mg/m3N。
3.5.3要求新二线窑尾袋收尘排放浓度≤50mg/m3N。
3.6能源资源消耗3.6.1努力降低能源资源消耗,要求新一线熟料单位电耗在70度以下;新二线熟料单位电耗在65度以下。
麦尔兹窑(MAERZ)中控岗位作业指导书

麦尔兹双膛竖窑中控岗位作业指导书中控岗位作业指导书(试用版)1 主题内容和适用范围1.1 本作业指导书含中控岗位技术操作、安全操作、设备使用及维护和环境保护等方面的内容。
1.2 本作业指导书适用于天博辰业中控岗位。
2 岗位职责2.1 严格执行公司、厂、车间的各项规章制度,按要求完成车间班组下达的任务。
2.2 负责本岗位范围内设备的安全正确使用、检查、维护,检修时积极配合协助检修人员,做好检修后的试车、验收工作。
2.3 负责本岗位安全装置、附属设施检查、维护,发现问题及时处理或报告。
2.4负责突发重大事件的紧急处理,一般性事故处理及提出检修项目及更换易损件。
2.5负责设备和岗位的文明卫生,认真做好交接班工作。
2.6 熟悉并掌握本岗位安全危害及环境因素及其控制措施。
2.7 发生事故立即报告有关部门。
3 作业程序与要求上班前准备穿戴劳动保护用品1)班前休息充分,确保精神状态良好,严禁饮酒。
2)提前15分钟进入工作岗位。
3)按规定穿戴好劳动保护用品,做到穿戴齐全,方法正确。
4)换下的服装及所携带的物品按规定摆放,保持环境整洁。
接班前准备1、参加班前会a.按规定时间参加班前会,听取上一班情况通报,了解本班次的作业任务和要求。
b.如有身体不适,必须提出,制订相应安全措施及注意事项。
2、生产工具准备准备好工作中所需的各类工具,保证各类装置完好,安全性能达标。
接班1、检查设备运行及环境卫生状况a.按照设备点检的路线和要求检查设备运行状况,并在点检记录本中作好相应记录。
b.发生环境卫生不符合规定和有关要求的,向交班人员提出,并督促交班人员整改。
2、清点公用工具并检查完好情况对上班移交的工具进行清点,检查确认其完好,并在交接班记录本中作好记录。
3、接班a.发现问题向交班者提出,交班者要给予处理、答复,交接双方签字认可后接班。
接班者未来或接班者没同意,交班者不得擅自离岗。
b.交接班时,双方发生争议的问题,应立即妥善协商解班中作业1、设备启动/停止操作石灰窑开窑的顺序(1)开窑时换向闸板位置正确(关闭燃烧膛换向闸板);(2)开主除尘器;(3)保证氮气,压缩空气压力在5Kg以上;(4)开液压泵2台;(停窑时开一台,开窑时增加一台)(5)开煤粉输送风机一台;(6)如停窑时悬挂缸冷却风AC109打开时,开AC107,AC108停AC109;(7)将停窑前开启的助燃风机和冷却风机打到“预选”模式,开启喷枪冷却风机;(8)开窑(窑操作打为“开”)。
窑系统中控作业指导书

1 范围本规程适用于烧成车间中控室窑操作,即从窑尾高温风机至熟料库顶并包括增湿塔设备的中控操作。
2目的本规程旨在树立安全第一的观点,统一操作思想,生产合格熟料,实现环保设备稳定达标排放,力求生产中达到优质、稳产、高产、低耗的目的。
3 操作指导思想1)树立安全生产、质量第一的观念,整定出系统最佳操作参数,确保窑长期安全运转并且实现:优质、高产、低消耗。
2)树立全局观念,与原料系统、煤磨系统、质控处互相协调,密切配合。
3)统一操作思想,精心操作,不断摸索总结操作方法,总结操作经验。
4)处理问题要沉着冷静,使问题处理正确及时,确保系统安全稳定。
5)操作中力求系统热工制度稳定,注意风、料、煤、窑速的配合以消除热工波动。
6)听从上级指挥,并对现场岗位合理引导指挥,积极处理本班发生的事情。
有问题及时的向领导汇报。
4 窑系统工艺流程简介1)入窑生料生料由生料库内经斜槽和手动阀板、气动阀、电动流量阀(42.07)进入喂料缓冲仓,从喂料缓冲仓卸出后,经气动截止阀、电动流量阀后,由冲击固体流量计计量后至喂料斜槽,再经高效斗提(52.10)提升至预热器顶进入斜槽,通过分料器(52.11)、分隔轮(52.13)进入预热器内。
2)预热器部分在预热器A列、B列中,生料和热气流进行热交换。
生料到A列、B列三级筒后进入分解炉内进行850-900℃预分解,然后进入四级旋风筒共13 页第1 页进行料气分离,最后入窑煅烧。
3)在窑旋转过程中,生料入窑后经过窑尾1000℃高温预烧和窑内1450℃高温煅烧,进入第四代高效篦冷机内急速冷却,篦冷机回收的高温余热被窑和分解炉利用。
低温气体经电收尘(57.15)净化后,被窑头排风机(57.17)排入大气。
熟料冷却后被篦冷机推送到破碎机(57.02),破碎机破碎至25mm左右颗粒经熟料斗式拉链和裙板拉链送入熟料库。
4)废气处理:预热器的高温气体经被高温风机(54.01)送入增湿塔(54.02)。
5000td回转窑中控(巡检)操作手册
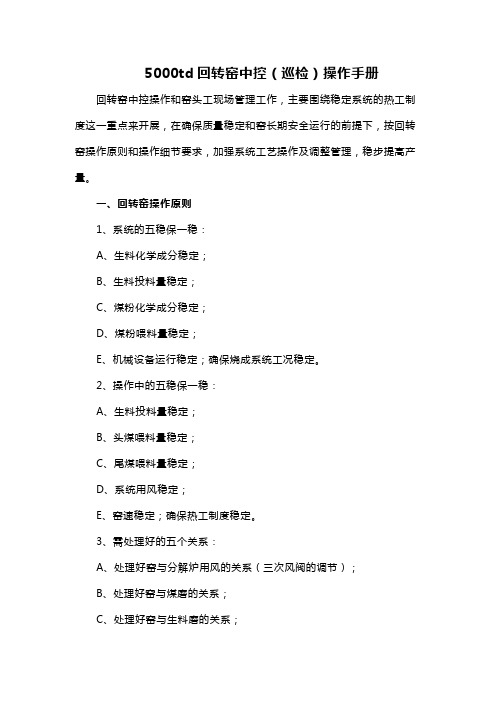
5000td回转窑中控(巡检)操作手册回转窑中控操作和窑头工现场管理工作,主要围绕稳定系统的热工制度这一重点来开展,在确保质量稳定和窑长期安全运行的前提下,按回转窑操作原则和操作细节要求,加强系统工艺操作及调整管理,稳步提高产量。
一、回转窑操作原则1、系统的五稳保一稳:A、生料化学成分稳定;B、生料投料量稳定;C、煤粉化学成分稳定;D、煤粉喂料量稳定;E、机械设备运行稳定;确保烧成系统工况稳定。
2、操作中的五稳保一稳:A、生料投料量稳定;B、头煤喂料量稳定;C、尾煤喂料量稳定;D、系统用风稳定;E、窑速稳定;确保热工制度稳定。
3、需处理好的五个关系:A、处理好窑与分解炉用风的关系(三次风阀的调节);B、处理好窑与煤磨的关系;C、处理好窑与生料磨的关系;D、处理好余热发电与窑用风的关系(篦冷机用风);E、处理好生料入库与回灰入库的关系;4、稳定窑温,前后兼顾,先动风煤,后动窑速。
5、风煤需合理配合,合理使用,控制火焰长度、力度、位置。
6、均匀喂料,稳定窑速,保持物料负荷稳定。
7、注意维护窑皮,实现长期安全运行。
8、先提窑速后提产量9、禁止漏风现象。
8、三个班操作统一,也就是三班保一窑。
二、中控操作注意重点1、分解炉出口温度。
2、窑电流。
3、生料喂料量及输料系统。
4、头、尾煤喂料量及输送系统。
5、窑前温度,熟料结粒。
6、C1出口压力、温度、O2、CO、NO x含量。
7、生料、熟料成分变化情况。
8、筒体温度及变化情况。
9、篦冷机冷却情况、料层厚度、篦板温度等。
10、窑头、窑尾收尘器入口温度、压力参数等。
11、各台套设备电机电流情况。
12、各处温度、压力情况。
三、窑头岗位工作重点1、看窑前火焰形状、力度、温度;2、看窑前熟料温度、带料高度、结粒情况,窑皮温度、平整度情况;3、看窑头罩内飞砂情况(篦冷机一段用风);4、看链斗机内熟料结粒、煅烧结晶、温度情况,窑皮掉落情况;5、看烟室缩口温度,结皮颜色。
6、检查窑筒体温度(窑皮及耐火砖)、预热器下料和温度情况;7、检查各岗位工作情况和各台套设备运行情况。
窑中控作业指导书

目录1.总则2.工艺流程简介3.职责与权限4.操作规程4.1.点火前的准备4.2.升温投料操作4.3.运行中的监控4.3.1.操作指导思想4.3.2.操作的关键参数及其范围4.3.3.操作中的调节参数4.3.4.窑操作中的控制4.3.5.紧急情况的处理4.4.停窑操作5.安全注意事项安全6.交接班制度7.考察与考核1总则1.1本规程规定了窑操作员的职责范围,工作内容与要求,操作及注意事项,交接班制度以及考核办法。
1.2本规程仅适用于中控室窑操作员.2工艺流程简介当窑、磨正常运行时,来自生料磨的生料及窑尾废气处理收尘下来的料粉经入库提升机、六嘴分料器,不间断地输送入规格为Φ15×45的生料均化库,在库内进行重力及气力均化。
均化库底采用固体冲板流量计对入窑生料进行计量。
生料经斗式提升机送入窑尾预热器内,生料均化库的有效储量5800t,储存期1.1天。
窑尾系统由五级旋风筒和连接旋风筒的联接管道、卸料管以及分解炉构成。
生料粉经计量后由提升机送入二级旋风筒气体出口管道,在气流作用下立即分散、悬浮在气流中,并进入一级旋风筒。
气料分离后,料粉通过重锤翻板阀转到三级旋风筒气体出口管道,并随气流进入二级旋风筒。
这样经过四级热交换后,生料粉得到了充分预热,然后物料进入分解炉内。
来自窑头罩的三次风、窑尾热风为分解炉提供氧气使煤粉燃烧,生料与燃烧后的高温气体进行热交换,其碳酸钙得以充分分解。
预分解后的生料,随气流进入五级旋风筒,经分离后喂入窑内;而废气沿着逐级旋风筒及气体出口管道上升,最后由一级旋风筒出风管排出,经高温风机和增湿塔送往原料粉磨和废气处理系统。
预热分解的料粉喂入窑尾烟室,并借助窑的斜度和旋转、慢慢地向窑头运动,发生一系列物理、化学反应,形成高温熟料。
煅烧后的高温熟料通过窑头罩进入篦冷机冷却。
出窑熟料温度为1350℃,冷却后的出冷却机熟料温度可降至100℃以下。
熟料通过篦冷机活动推板的往复推动,进入冷却机尾部的锤式破碎机,经打碎后落到熟料链斗输送机上,送入熟料库内。
中控窑作业指导

中控窑作业指导一、中控窑操作的一般原则:新型干法窑系统操作的一般原则,就是根据系统各环节条件变化,及时调整系统各工艺操作参数,最大限度地实现系统"均衡、稳定"运行的目标;在实际生产过程中,由于各种因素的干扰,系统原有的平衡稳定状态会被破坏,窑操作员应该根据具体情况,全面分析,正确判断,做出适当调整,尽快恢复系统均衡、稳定的状态;烧成系统应以保持合理煅烧制度,充分发挥窑的煅烧能力为宗旨,根据原、燃料条件及设备状况合理控制各主要参数,在保证熟料质量的前提下,最大限度地提高窑的运转率。
操作中坚持"抓两头,保重点,求稳定,创全优"这一原则; "抓两头",就是要重点抓好窑尾预热器系统和窑头熟料烧成两大环节,前后兼顾、协调运转;"保重点",就是要重点保证系统喂煤、喂料设备的安全正常运行,为熟料烧成的"动平衡"创造条件;"求稳定",就是在参数调节整程中,适时适量,小调渐调,以及时的调整克服大的波动,维持系统热工制度的稳定。
"创全优",就是要通过一段时间的操作,认真总结,结合现场热工标定等测试工作,总结出适合本厂实际的操作参数且不断优化,取得优质、高产、低耗、长期安全稳定文明生产的优异成绩;二、正常操作下过程变量的控制:正常操作,是指窑系统经点火、投料、挂窑皮阶段后,已达到正常额定投料量,到出现较大故障而必须转入停窑操作这一时期,正常操作的主要任务就是运用风、煤、料及窑速等操作变量的调节,保持合理的热工制度,使下述过程变量基本稳定:①窑主传动负荷: 正常喂料量下,窑主传动负荷是衡量窑运行正常与否的主要参数,正常的窑功率曲线应粗细均匀。
无尖峰、毛刺,随窑速度变化而改变,在稳定的煅烧条件下,如投料量和窑速未变而窑负荷曲线变细、变粗,出现尖峰或下滑,均表明窑工况有变化,需调整喂煤量或系统风量,如曲线持续下滑,则需高度监视窑内来料,必要时需减料减窑速,防止跑生料。
水泥厂中控室(回转窑)操作员作业指导书

通过本岗位认真操作完成以下目标:
1、无人为的责任操作事故;
2、设备各处均无正压现象,环保设备达到要求标准;
3、在保证产量的基础上减小系统的用风量,降低生产成本;
4、及时发现操作上不正常的现象,及时处理,处理不了的及时上报;
5、在稳产、高产的基础上,使其产量、质量、电耗、成本达到较高的水平。
职位权限:
8、对公司内不符合安全规定的行为,有制止权、否决权;
对相关部门岗位工作有监督权、建议权;
业绩考核
主要指标:
1、操作事故;
2、安全操作
3、台时产量
安全责任:
真遵守公司的安全政策及各项安全规章制度;
及时制止发现的各种安全违章行为。
工艺流程简介
一、生料均化库及入窑喂料设备简介
参照:工艺设备表
二、生料均化库及入窑喂料工艺图
参照工艺设备表
八、烧成系统工艺流程简介
参照工艺流程总图
九、烧成系统工艺流程简介
预热器由双系列五级旋风预热器和管道型分解炉构成,生料在C1—C2的风管处进入预热器。生料自上而下与热气体悬浮换热升温,入分解炉进行碳酸盐分解后,经C5收集后,从窑尾烟室喂入回转窑。入窑物料经回转窑高温煅烧,在1250-1280℃产生液相,物料在高温液相的情况下产生物理化学变化,形成高温熟料。高温熟料出窑入篦冷机快速冷却。在回转窑内煤粉燃烧后,生成高温废气经烟室从分解炉底部入炉。在分解炉内,煤粉、三次风、预热后的生料及回转窑的高温废气,通过旋流和喷腾,实现气体充分混合,完成燃烧、分解。分解炉排出的气料,在C5内气料分离,物料入窑,废气经各级旋风筒,自下而上与生料悬浮换热降温,最后从C1排出,窑尾高温风机将废气送入废气处理系统,或部分入生料磨烘干用。
中控室窑操作员作业指导书

中控室窑操作员作业指导书1质量要求1.熟料f-c a o≤1.5%,合格率≥85%。
2.熟料立升重1100±75/L,合格率≥85%。
3.熟料三天强度≥28M p a,二十八天强度≥56M p a,合格率≥90%。
2工艺要求2.1窑头火焰活泼有力,但不扫窑皮。
2.2系统不漏风、不漏料、不喷尘。
2.3窑系统热工稳定,风煤料合理分配,窑炉燃烧比例控制在4:6左右。
2.4入窑物料表现分解率≥90%3作业程序3.1开停车顺序:开机顺序:窑中稀油站——窑头一次风机——点火油泵——窑头喷煤罗茨风机——窑头喂煤称——熟料输送系统——窑头袋收尘系统——冷却机干油泵——破碎机——冷却机——组风机——高温风机稀油站及液力耦合器加油站——窑主电机——高温风机——喂料系统——均化库底充气系统——均化库卸料电磁阀——窑尾一次风机——分解喂煤称——冷却机一、二、三段传动——冷却机二、三组风机。
停机顺序:止料、止分解炉喂煤后的顺序基本相反,但冷却机风机、窑头袋收尘排风机、窑头、窑尾一次风机、高温风机视冷却情况,燃烧器冷却情况而定。
3.2点火操作:3.2.1通知现场巡检工关闭和密封好所有的检查门,检查确认各旋风筒的下料管通畅、翻板阀灵活并将其吊起,测试各空气炮是否正常。
3.2.2检查各机组是否有备妥,确认各设备可正常投入使用。
3.2.3检查窑头点火燃油系统,通知巡检将油嘴清洗干净,油罐油量80%,将油枪架好,进油、回油管接好。
3.2.4煤粉仓要有足够的煤粉储备,够窑、炉升温和投料用(50吨左右)3.2.5启动喂料机组进行倒库,同时检查要喂料输送设备是否正常。
3.2.6启动测试冷却机及熟料输送系统,运行30分钟无异常后停机。
3.2.7启动窑的润滑、冷却系统、检查窑齿轮、托轮的润滑情况,试启动窑主电机(0.6转|分钟)3.2.8启动测试喂料系统及窑头一次风机。
3.2.9做好点火前的准备后,按照指令点火烘窑。
3.2.10启动窑头一次风机,给定适量转速。
窑中控操作岗位作业指导书

窑中控操作岗位作业指导书重庆拉发基水泥有限公司LAFARGE CHONGQING CEMENT LIMITEDLIABILITY COMPANY窑中控操作岗位作业指导书编号:版次:发布日期:200年月日实施日期:200年月日本手册版权属重庆拉法基水泥有限公司所有,未经允许不得复制目录1.总则2.工艺流程简介3.职责与权限4.操作规程4.1开车前的准备4.2开车顺序4.3 运行中的检查4.4停车顺序4.5停车后的检查4.6维护和保养6.安全注意事项7.交接班制度8.附录附录一:常见故障原因及处理方法附录二:设备表:1. 总则1.1本规程规定了窑操作员的职责范围,工作内容与要求,操作及注意事项,交接班制度以及考核办法。
1.2本规程仅适用于中控室窑操作员。
1.3执行重庆拉法基水泥有限公司《员工手册》。
2.工艺流程简介2.1生料均化及窑尾喂料生料均化库采用TP-1控制流连续式均化库,其规格为?15×47m,有效储量6400吨,储存期1.6天。
来自生料磨的生料和窑尾废气处理系统的回灰经空气输送斜槽一同送至斗式(228BE.07),提升卸入空气输送斜槽(228.AS08)入生料均化库顶中央进料口,由于生料的流动性可保证刚进库的生料平均分布于同一料层上,使得不同时间生产的生料形成不同的料层。
库内底部设有一减压锥,当库底卸料时,会形成漏斗装料流,垂直切割各层物料,达到重力均化目的。
卸料区上部设有减压锥,旨在降低卸料区料压,使不同料层的生料均匀流出,达到较理想均化效果。
均化库设有六个卸料口,相应的环形库底分成六大卸料区,每一个大区又分成两个充气区(即卸料区),两个充气小区是轮流充气的,相对应的卸料区卸料。
重力均化库卸料时通过中心线的两个对顶卸料口同时卸料,卸料时间可调,初定为20分钟,即对每个大区对应充气时间是20分钟,相应每一对卸料小区卸料10分钟,进入下一对大区卸料20分钟,依次类推,则完成一个卸料周期为1小时。
5000t中控窑操作业指导书
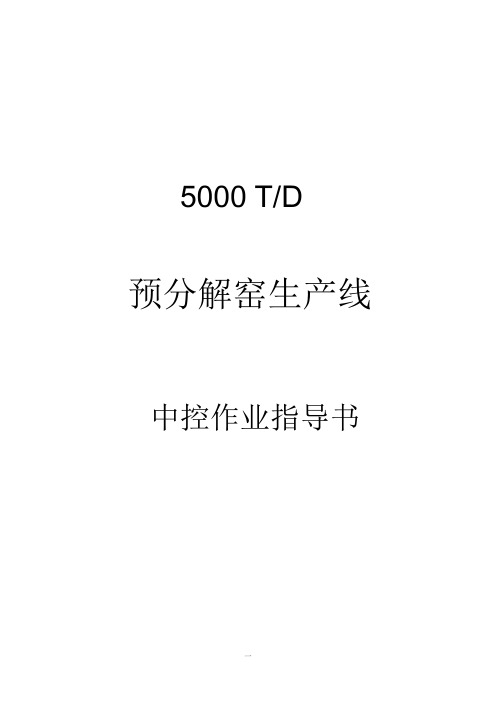
5000 T/D预分解窑生产线中控作业指导书一职责与权限及相互关系1.职责1.1 严格遵守各项操作规程,保证生产正常进行,防止事故发生。
1.2 负责并保证产质量的完成,努力提高各工序质量。
1.3 确保部门下达的各生产任务经济指标的完成。
1.4 协助中控主任做好各系统的工作,监督、指挥各系统巡检工处理好本系统设备至正常运行。
1.5 负责本系统操作记录的填写工作,要求数据准确填写及时,字迹工整不乱涂乱改保证记录完整、不损坏。
1.6 熟练掌握本系统生产工艺,不断提高操作水平。
1.7 负责本岗位各工艺参数在规定范围内。
2.权限2.1 有权制止非本岗位工作人员的违章操作及行为。
2.2 有权制止非工作人员进入中控室。
2.3 有权对部门提出合理化建议。
2.4 有权对物料均化工作和取料点进行监督。
2.5 有权指挥相关巡检工开展工作。
3.相互关系3.1 直接对生产部负责。
3.2 与窑系统相关各岗位相互配合。
3.3 协助中控主任完成部门下达的各项生产任务。
3.4 开停机时,须和中控主任取得联系,经同意后,方可开停机。
二窑系统操作规程及指导思想1,树立安全生产、质量第一观念,精心操作,不断总结经验教训,以生产实际情况为依据,充分运用先进的计算机仪表监测系统,稳定最佳操作参数,实现优质、稳定、高效、低耗、长期安全运转的目的。
2,以保持烧成系统发热能力和传热能力,以及烧结能力和预热分解能力平衡稳定为宗旨,操作中要做到前后兼顾、炉窑协调,稳定烧成温度和分解温度,保证窑炉合理的热工制度。
3,对于分解炉系统的正常操作,则要求及时准确调整分解炉系统的煤量和通风量,掌握负压变化的规律;及时调整分解炉燃烧器的喷煤量,保持分解炉出口气体温度的稳定和炉内温度的平衡;防止局部温度过高或过低,确保生料分解率,达到分解炉系统安全运转的目的。
4,对窑的正常操作,要求重点稳定烧成带及烟室温度,掌握四风道燃烧器径向风、轴向风以及燃料的配比规律,保证合理的火焰形状和火焰位置,不损坏窑皮,不窜黄料。
窑系统中控作业指导书
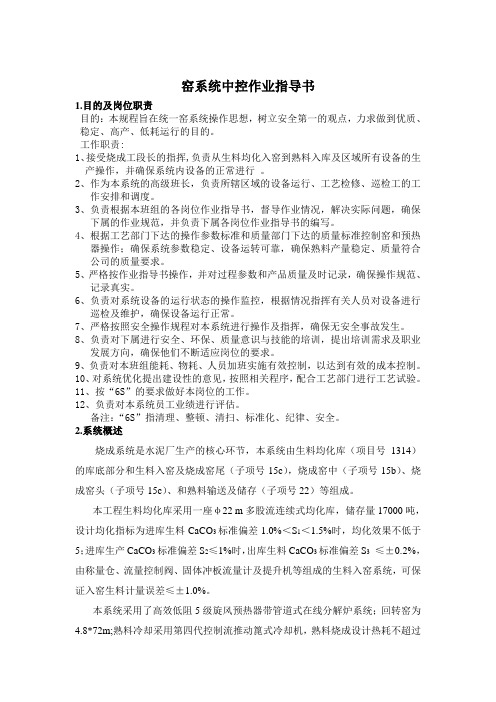
窑系统中控作业指导书1.目的及岗位职责目的:本规程旨在统一窑系统操作思想,树立安全第一的观点,力求做到优质、稳定、高产、低耗运行的目的。
工作职责:1、接受烧成工段长的指挥,负责从生料均化入窑到熟料入库及区域所有设备的生产操作,并确保系统内设备的正常进行。
2、作为本系统的高级班长,负责所辖区域的设备运行、工艺检修、巡检工的工作安排和调度。
3、负责根据本班组的各岗位作业指导书,督导作业情况,解决实际问题,确保下属的作业规范,并负责下属各岗位作业指导书的编写。
4、根据工艺部门下达的操作参数标准和质量部门下达的质量标准控制窑和预热器操作;确保系统参数稳定、设备运转可靠,确保熟料产量稳定、质量符合公司的质量要求。
5、严格按作业指导书操作,并对过程参数和产品质量及时记录,确保操作规范、记录真实。
6、负责对系统设备的运行状态的操作监控,根据情况指挥有关人员对设备进行巡检及维护,确保设备运行正常。
7、严格按照安全操作规程对本系统进行操作及指挥,确保无安全事故发生。
8、负责对下属进行安全、环保、质量意识与技能的培训,提出培训需求及职业发展方向,确保他们不断适应岗位的要求。
9、负责对本班组能耗、物耗、人员加班实施有效控制,以达到有效的成本控制。
10、对系统优化提出建设性的意见,按照相关程序,配合工艺部门进行工艺试验。
11、按“6S”的要求做好本岗位的工作。
12、负责对本系统员工业绩进行评估。
备注:“6S”指清理、整顿、清扫、标准化、纪律、安全。
2.系统概述烧成系统是水泥厂生产的核心环节,本系统由生料均化库(项目号1314)的库底部分和生料入窑及烧成窑尾(子项号15c),烧成窑中(子项号15b)、烧成窑头(子项号15c)、和熟料输送及储存(子项号22)等组成。
本工程生料均化库采用一座φ22 m多股流连续式均化库,储存量17000吨,设计均化指标为进库生料CaCO3标准偏差1.0%<S1<1.5%时,均化效果不低于5;进库生产CaCO3标准偏差S2≤1%时,出库生料CaCO3标准偏差S3≤±0.2%,由称量仓、流量控制阀、固体冲板流量计及提升机等组成的生料入窑系统,可保证入窑生料计量误差≤±1.0%。
窑系统操作作业指导书

阿克苏天山多浪水泥公司喀什分公司2000t/d熟料生产线项目窑操岗位作业指导书第 1 版编制:审核:批准:文件编号:受控状态:受控发放编号:2008年月日发布2008年月日实施1、目的:保证窑和预热器系统操作工、巡检工安全正确地操作窑和预热器岗位所属设备,确保人身安全和设备安全及生产达标达产。
2、适用范围适用于2000t/d熟料生产线窑和预热器岗位。
3、岗位职责负责操作、巡检和维护回转窑和预热器系统所属主辅机设备,合理调整操作方案,确保系统生产正常稳定生产,实现达标达产目标。
4、工作内容4.1.质量标准:f-cao<1.5% 合格率>90% 分解率92±2% 合格率>90%。
4.2.技术要求:窑尾温度:1020-1180摄氏度。
分解炉温度:840-900摄氏度。
一级温度:<340摄氏度。
4.3.操作规程:4.3.1点火前的准备工作:4.3.1.1预热器大面积镶砖的情况下。
点火前要求窑尾将预热器各级下料挡板吊起。
4.3.1.2检查油箱油位。
4.3.1.3.点火前,通知计量人员检查所有的计量仪表设备是否正常。
4.3.1.4.通知仪表工作人员检查温度,压力仪表是否正常。
4.3.1.5.通知预热器工作人员检查各级预热器及分解炉入口门捅灰孔是否关闭。
4.3.1.6.确认三次风阀是否处于关闭状态。
4.3.1.7.确认窑喷煤嘴位置处于零位,并做好记录。
4.3.1.8.根据工艺要求按升温曲线升温。
4.3.1.9.窑操作员应全面了解设备变更等现场实况。
仔细落实点火的必要条件,要掌握窑系统耐火材料和窑灰情况,了解窑内物料的残留量,要将准备工作的检查全面真实的写入交班记录,并将存的问题通知有关部门(岗位)处理。
4.3.2窑启动运行的操作:4.3.2.1接到点火指令后,通知车间相关岗位将设备送电,通知中控仪表自动经人员对仪表计算机上电。
4.3.2.2检查各组设备有无备妥,无备妥时,通知自动化人员备妥。
窑中岗位作业指导书(1)

淄博山水水泥有限公司熟料工段窑中岗位作业指导书(初稿)二零零九年二月十日窑中岗位作业指导书一、目的明确岗位责任范围正确操作,处理一些常见事故,维护系统设备正常运转。
二、范围适用于生产运行部窑中岗位巡检操作及其它操作。
三、所辖区域负责窑中系统从窑尾密封至窑头密封的相关设备、区域。
四、岗位职责1、负责设备的现场监护(包括日常检查、开停机检查等),及时发现并消除设备隐患、杜绝设备事故,确保设备安全运转。
除定检时间外,不允许因所管辖区域的设备、工艺故障原因影响连续生产,否则将按照故障情节严重程度予以处罚。
2、负责设备的润滑检查(包括油量、油温等润滑状况),以及简单的润滑维护,保证所辖设备润滑正常。
3、及时擦拭设备壳体,要求所辖设备表面清洁,无积灰、无油污。
4、对本区域内的地面卫生进行清扫,确保地面清洁。
5、负责本区域内的设备完好率,不得擅自拆卸或毁坏设备零部件及相关设施。
6、对本区域内的安全负责,保证安全防护设施完好、牢靠,安全标识清晰、醒目,坚决制止非本岗位人员启停设备。
对设备、环境等方面存在的安全隐患进行排查并及时上报片长,提出整改要求及建议。
7、认真、及时、准确、完整、整洁清晰地填写《岗位巡检记录表》。
8、认真完成各项临时性工作。
五、工作目标1、设备、工艺故障率为“零”:在非定检时间内,因设备或工艺故障造成回转窑停机的时间为零。
2、设备完好率达到100%。
六、操作流程岗位工应熟知本岗位操作流程,认真执行“润滑、紧固、擦拭、密封”设备巡检八字方针,严格按照操作流程的指导进行作业。
1、设备、工艺巡检1.1、巡检前的准备工作岗位工巡检前要穿戴好劳保用品,并随身携带工具包,内装10#或12#活扳手1把,200mm平口螺丝刀1把,手钳1把,手电筒1个,以及适量棉纱。
所配备巡检工具的具体使用要求:①、10#或12#活扳手:用于临时紧固M20mm以内设备底座螺栓、法兰连接螺栓;此外,还可将扳手手柄端部,轻轻敲击斜槽风箱或收尘管道等部位,用于判断内部是否存有积料。
中控室窑操作员作业指导书

烧成车间窑中控室作业指导书中控室窑操作员作业指导书1 、目的:使烧成系统在受控状态下运行,合理地控制系统参数,稳定热工制度,煅烧出质量合格的熟料,完成熟料生产任务,保护好窑衬及炉衬,树立质量、环境、计量、安全意识,达到防治污染、节能降耗和安全生产的目的。
2 、范围:适用于中控室窑操作员。
3 、职责与权限:3.1 负责窑系统设备的开停,有权利对突发事件紧急停车,力求收尘设备与主机设备同步运行,发现异常及时处理或上报班长及有关人员。
3.2 负责窑系统参数的监视、控制,保证生产、计量设备安全有效地运行,运行中力求高效、低耗,有必要时以口头或书面的形式向技术人员提出操作参数修改及其他建议。
3.3 负责窑产、质量指标的完成。
严格按照生产部、化验室要求进行监视、控制,负责熟料产量、质量指标的完成,力争控制消耗在合理范围之内。
3.4 负责窑系统操作过程中出现的安全、环境、计量等不符合体系要求情况的调整、处理,并及时通知巡检工检查。
3. 5熟悉并理解 ISO9001 、 GB/T28001 、 ISO14001 、 GB/T28001 各质量体系的名词术语、方针、目标。
3.7 熟悉本系统或本岗位环境因素、危险源,熟悉应急与响应方案。
3.8 完成管理人员临时交办的任务。
3.9记录书写工整、规范,交接班清楚。
3.9、负责搞好本班卫生。
3.10.检修时参与检修工作。
4 、技术要求:4.1 参数控制:4.1.1 投料量 340 t/h 。
4.1.2 一级预热器出口≤ 340 ℃。
4 . 1.3 五级预热器出口温度 850-890 ℃。
4.1.4 分解炉出口温度 860-900 ℃。
4.1.5 窑尾烟室温度950 -1 0 50 ℃。
4.1.6 窑头电收尘温度≤ 250 ℃。
4.1.7 三次风温≥80 0 ℃。
4.1. 8出篦冷机熟料温度<100 ℃,不见红料。
4.1. 9 220℃<窑筒体温度<350 ℃。
4.1.1 0一级预热器负压 4 5 00- 60 00Pa 。
- 1、下载文档前请自行甄别文档内容的完整性,平台不提供额外的编辑、内容补充、找答案等附加服务。
- 2、"仅部分预览"的文档,不可在线预览部分如存在完整性等问题,可反馈申请退款(可完整预览的文档不适用该条件!)。
- 3、如文档侵犯您的权益,请联系客服反馈,我们会尽快为您处理(人工客服工作时间:9:00-18:30)。
窑中控作业指导书编号:XXXX水泥有限公司一、总则1、本指导书由XXXX公司XXXX部编制。
2、本指导书规定了窑中控岗位的,工作内容与要求,操作及注意事项,交接班制度。
3、本指导书仅适用于中中央控制室窑中控岗位。
4、执行XXXX公司《管理手册》及《安全生产管理制度汇编》。
二、工艺流程简介出库生料经库底部的卸料口卸至生料计量仓,生料计量仓带有荷重传感器、充气装置。
仓下设有流量控制阀和固体流量计,经计量后的生料通过空气输送斜槽、斗式提升机、回转下料器、电动闸板阀通过下料管进入C2出口到C1进口的连接风管,在随热气流进入C2并分离,依次类推。
生料由上向下,在与热气流的换热过程中温度逐渐增高。
至C4物料经分离预热后喂入分解炉,进入分解炉的燃料和预热的生料被高速的气流携带,悬浮于炉内,一面旋流向上,一面进行燃烧、分解。
燃料的燃烧放热过程与生料的吸热分解过程同时在悬浮状态下极其迅速地进行,生料在入窑前已基本完成碳酸钙的分解,使物料分解率达到90%~95%左右。
完成大部分分解反应的物料由C5旋风筒经下料管入窑。
窑尾烟气与来自三次风管的高温废气经管道在线型分解炉、C1至C5旋风筒进行换热分离。
气流在与生料的热交换过程中由下向上温度逐渐降低,最后由C1出风口排出,经余热锅炉、高温风机排出的窑尾废气分成两路。
第一路去往原料磨,烘干磨内物料水分。
另一路与出原料磨的废气汇和入窑尾袋收尘器,净化后经窑尾排风机排入大气。
入窑斗式提升机前设有取样器,通过对出库生料的取样、制样分析,实现对烧成系统的操作进行指导。
熟料煅烧采用一台Φ4.8×72m的回转窑,回转窑采用三档支撑,斜度为3.5%(正弦),转速为0.36~4.56r/min。
窑尾带双系列五级旋风预热器和TTF分解炉,日产熟料4500t。
窑头配有四通道燃烧器,窑和分解炉用煤比例为40%~45%和60%~55%,入窑物料的碳酸钙分解率大于90%。
分解炉用三次风从篦冷机抽取,通过管道直接送至分解炉。
熟料冷却采用第四代行进式稳流冷却机,冷却机出口设有熟料破碎机,出破碎机的熟料经槽式输送机送入熟料库。
冷却机废气经窑头余热锅炉、电收尘器净化处理后排入大气。
三、作业指导书1 操作指导思想1.1 树立安全生产、质量第一观念,精心操作,不断总结经验教训,以生产实际情况为依据,充分运用先进的计算机仪表监测系统,稳定最佳操作参数,实现优质、稳定、高效、低耗、长期安全运转的目的。
1.2 以保持烧成系统发热能力和传热能力,以及烧结能力和预热分解能力平衡稳定为宗旨,操作中要做到前后兼顾、炉窑协调,稳定烧成温度和分解温度,保证窑炉合理的热工制度。
1.3 对于分解炉系统的正常操作,则要求及时准确调整分解炉系统的煤量和通风量,掌握负压变化的规律;及时调整分解炉燃烧器的喷煤量,保持分解炉出口气体温度的稳定和炉内温度的平衡;防止局部温度过高或过低,确保生料分解率,达到分解炉系统安全运转的目的。
1.4 对窑的正常操作,要求重点稳定烧成带及烟室温度,掌握四风道燃烧器径向风、轴向风以及燃料的配比规律,保证合理的火焰形状和火焰位置,不损坏窑皮,不窜黄料。
综上所述,概括为:三固、四稳、六兼顾。
固定窑速、喂料量、篦冷机篦床上料层厚度;稳定C5出口气体温度(分解炉喂煤)、预热器排风量(高温风机转速)、烧成带温度(窑头喂煤)、窑头负压;兼顾窑尾O2含量及气体温度、C1出口温度及压力、分解炉内温度及压力、筒体表面温度、篦冷机废气量、废气处理及收尘系统。
2 开车前的准备2.1 接到开车指令后,要与有关部门进行联系,配合做好各项准备工作。
2.2 联系电气,对全部设备送电,各仪器仪表进行复位,要求现场气体分析仪、比色高温计和摄像机等备妥待用,确保中控室的计算机及其它设备备妥待用,进行现场仪表检查,做到仪表显示正确,与中控显示一致。
2.3 联系机修部门,确认设备是否具备启动条件。
2.4 联系巡检工,确认熟料的入库情况。
2.5 通知预热器巡检,仔细检查预热器、分解炉及系统连接管道内有无异物,确保畅通。
2.6 空压机站能正常运转,压缩空气管路各阀门转动灵活,开关位置正确。
管路畅通、不泄漏、各吹堵孔畅通。
2.7 点火前将预热器各级重锤阀阀板吊起。
2.8 通知回转窑和篦冷机巡检岗位,检查窑内、冷却机内无杂物,具备开车条件。
2.9 通知各巡检岗位,关好所有的人孔门、观察孔、捅料孔。
确保其能密闭不漏风。
2.10通知各巡检岗位,仔细检查本岗位设备的润滑点按规定加油。
油量、牌号正确,油路畅通,油压、油温正常。
水冷却设备水路畅通,流量和水质符合要求。
管路无渗漏,将检查结果及时报告中控室。
2.11了解生料和煤粉的准备情况,是否有足够的储量,确认轻油罐内的油料是否有足够储量。
2.12 通知窑巡检岗位,检查燃烧器的风、煤管道连接情况,将燃烧器送至合适位置。
2.13 联系好后,各设备进行单机和联动试车,试车无误后,准备点火。
3窑系统升温3.1升温曲线按照熟料部点火通知中的升温曲线进行升温。
3.2点火升温3.2.1确认高温风机入口阀门、窑头电收尘排风机入口阀门、篦冷机各风机入口阀门、窑尾排风机入口阀门、各人孔门全关。
窑头喷煤管各风道手动阀全开。
3.2.2将点火烟囱帽开至一定的开度。
3.2.3用一根5-6米长的钢管,端部缠上油棉纱,点燃后自窑门罩伸到喷煤管端部。
3.2.4开启燃油系统,点焰雾化油。
注意先喷油后点焰,很容易返火伤人。
3.2.5开启一次风机调节风量,使火焰不发飘即可。
3.3在燃油火焰稳定后,即可煤、油混烧继续升温。
因煤粉焰烧不稳定有暴焰回火危险,窑头操作应防止烫伤。
3.3.1设喂煤量为0.5t/h,启动窑头喂煤组。
为防止尾温剧升,应慢慢加大喷煤量。
3.3.2不断调整一次风量及点火烟囱帽开度,保持火焰稳定燃烧,不灭火、不返火。
如果煤油火焰很难稳定,可控制窑头罩微正压,局部烧热后再控制为负压。
3.3.3启动回转窑主减速机稀油站,按转窑制度,现场用慢驱动转窑。
升温期间要定期检查回转窑托轮,减速机、大齿圈润滑状况。
当窑尾温度到250℃时,启动窑辅传电机,定时盘窑,盘窑方案如下:窑尾烟室温度(℃) 转窑间隔转窑量100~250 60min 90°250~450 30min 90°450~650 20min 90°650~800 10min 90°800以上连续慢转如遇下雨,须连续转窑或时间减半;如在窑砖使用中后期,也可根据回转窑砖及窑衬情况制定具体盘窑方案。
3.3.4随烟室温度升高,要逐渐减油增煤,调整一次风量、点火烟囱帽开度,保持火焰形状,避免局部高温,以及窑尾温度不能大起大落。
当烟室温度大于400℃时,可考虑断油,但煤火焰需能自行稳定。
3.4随着燃料量增大,尾温沿设定趋势上升,窑尾烟室温度在400℃时,当燃烧空气不足或窑头负压较高时,启动篦冷机一室平衡风机,逐步加大风机进口阀门开度,当开度至60%,仍感风量不足时,逐步启动一室乃至二室风机,增加入窑风量,同时注意风量的调节,风量不能过大,以免影响火焰的形状。
3.5根据升温曲线及窑尾烟气的氧含量(>2%,窑内燃烧状况)当窑尾预热器点火烟囱不能满足窑头负压的调整时,判定是否可启动窑尾袋收尘排风机,打开入口阀门及高温风机入口阀门。
按升温曲线,逐渐增加喂煤量,调整一次风量(注意内外风的比例)和窑尾废气风机的排风量,保证煤粉燃烧完全。
并视情况启动窑口密封圈冷却风机。
3.6当尾温升到600℃时,做好如下准备工作:3.6.1预热器各级翻板阀要人工活动,间隔1小时,以防受热变形卡死,启动分解炉喂煤罗茨风机,送冷风冷却喷嘴,以防过热。
3.6.2烘干后期仪表调校人员应重新校验系统的各点温度。
在800℃恒温期间,由于没有窑皮保护,筒体温度较高(420℃)且观察到筒体暗红或更严重。
说明内部衬料出了问题,应灭火、停风、关闭各阀门,使系统自然冷却并注意转窑。
如发现有掉砖现象应降低砖窑频次及幅度。
窑冷却后要进行认证检查,衬料损坏厚度超过1/3时,应考虑挖补或衬料,再点火按正常升温操作。
3.6.3升温过程中,随时注意观察高温风机入口温度,当入口温度大于320℃时,应调整烟囱帽开度增大冷风掺入量以降低气体温度,如已达极限可开启管道喷淋水系统,喷水降温,保护窑尾大布袋收尘器。
4窑系统投料4.1启动稀油站组,窑的辅助传动改为主传动,在最慢转速连续转窑。
注意窑速是否平稳,电流是否稳定、正常。
不正常时应进行调整。
4.2将生料均化库打向倒库方向,开启窑尾喂料组,开启均化库卸料组,设定喂料量进行倒库。
4.3依次启动窑尾废气处理系统各回灰组、高温风机组、篦冷机各风机组、熟料输送组、窑头排风机组及回灰设备(调节各风机风门,保持窑头负压20~50Pa)、窑头、窑尾收尘器组。
4.4投料前10~30分钟放下吊起的翻板阀,调整阀板配重。
4.5启动窑尾空气炮组,防止预热器旋风筒锥体部位结皮。
4.6分解炉点火4.6.1当烟室温度升至900℃以上时,高温风机转速开至650~680r/min,入口阀调至80%。
分解炉喂煤,开始时喂煤量1~1.5t/h,注意分解炉出口温升情况,如长时间不升时,可以关小三次风阀门开度,借助窑内高温气体点燃煤粉。
无效时,要停止喂煤,进行检查。
4.6.2如分解炉温升较快时,根据烟室CO含量及O2含量调整入炉风量,加大三次风阀门开度。
视情况减少喂煤量或加大高温风机阀门开度。
4.7投料前几个主要参数及检查:4.7.1 C5出口温度860℃,分解炉出口温度880~900℃,C1出口温度小于400℃,烟室温度950~1050℃。
4.7.2 预热器应自上而下用压缩空气吹扫一遍。
低产时应1小时吹扫一次,稳定生产时应4小时吹扫一次。
4.8投料量确定4.8.1窑头黑火头很长,火焰突明突暗,尾温900~950℃时,投料量为设计能力的50%左右。
4.8.2窑头黑火头较长,火焰尚能稳定,尾温950~1050℃时,投料量为设计能力的65%左右。
4.8.3窑内有料,有窑皮,且火焰明亮稳定,尾温较高时,投料量为设计能力的75%左右,甚至更高。
4.9投料过程中调整:根据窑内情况确定投料量,设定投料量,将倒库改为入窑。
4.9.1 当观察到C1出口温度有下降趋势,可关小烟囱帽开度,同时注意高温风机入口温度不超过400℃4.9.2增加分解炉喂煤量,使分解炉出口温度不低于860℃。
同时观察烟室温度有下降趋势,增大窑头喂煤量5~10%,调整整个系统用风量,保证煤粉完全燃烧。
一般情况投料40分钟,窑头即可看到料影,在这之前可根据窑功率调整窑速,以免生料窜出。
4.9.3在投料后的2个小时内要严密注意预热器各级翻板阀闪动情况,可设专人看管,及时调整重锤人工帮助排料。
4.9.4当熟料出窑后,二次风温升高,窑头火焰顺畅有力,料影渐渐消失,应注意窑电流变化,可适当减少窑头喂煤量,增加窑速。