溶剂再生装置主要设备材料的选择探讨
溶剂再生培训资料

1.新建溶剂再生的原料来自哪里?装置规模是多少?操作弹性是多少?答:新建溶剂再生Ⅰ,规模300吨/小时:处理全厂所有脱硫单元(包括循环氢、干气、液化石油气、硫磺回收尾气等)脱硫的富溶剂,再生后贫溶剂返回各生产装置脱硫单元循环使用。
油品质量升级改造工程总流程规划实施时,再新建溶剂再生Ⅱ:单独处理硫磺回收装置尾气处理部分脱硫的富溶剂。
溶剂再生采用常规汽提再生工艺,再生塔底重沸器热源采用0.3MPa蒸汽,技术立足于国内。
操作弹性:50%-110%。
2.溶剂再生的原料来自哪些装置?答:溶剂再生的原料为全厂所有脱硫单元(包括循环氢、干气、液化石油气、硫磺回收尾气等)脱硫的富溶剂。
自延迟焦化、加氢处理、催化裂化及硫磺回收等装置排放的混合富液,性质见下表。
混合富液的组成3.溶剂再生装置主要工艺技术特点是什么?答:1)溶剂再生采用常规蒸汽汽提再生工艺。
2)溶剂选用复合型MDEA溶剂,该溶剂具有良好的选择吸收性能、酸性气负荷大、腐蚀轻、溶剂使用浓度高、循环量小、能耗低等特点。
再生后的贫液返回上游装置使用,酸性气送至硫磺回收部分。
3)为方便操作,增加灵活性,MDEA溶剂浓度按30%(wt)进行设计。
4)再生塔采用高性能塔盘的先进设备技术,具有压降低、效率高、操作弹性大等优点,适应长周期运转。
5)装置内需要冷却的工艺介质尽量采用空冷,以减少循环水用量。
6)集中后的富溶剂采用中温(60~65℃)低压闪蒸,保证装置稳定操作,降低再生酸性气烃含量。
7)富溶剂及部分贫溶剂设置过滤设施,以防止溶剂发泡和降解。
8)设置完善的溶剂回收系统,降低溶剂消耗。
9)设置较大有溶剂缓冲罐,贮存停检修时上游脱硫单元、系统管线及本装置退出的溶剂。
4.溶剂再生装置基本工艺原理是什么?答:MDEA是一种弱碱,其碱性随温度下降而增强,因此,在较低的温度下,MDEA可以与H2S、CO2等酸性物质起中和反应生成胺盐,在较高的温度下,胺盐可以分解,析出酸性气,MDEA得以再生从而循环使用。
溶剂再生装置胺液系统热稳定盐脱除与腐蚀防护

溶剂再生装置胺液系统热稳定盐脱除与腐蚀防护【摘要】胺液溶剂再生脱硫装置包括两套再生系统,供上游装置脱硫使用。
胺液杂质多,热稳定盐含量高降低了脱硫效率,对系统产生了严重腐蚀。
必须通过热稳定盐的脱除来提高溶剂活性,降低系统腐蚀。
【关键词】胺液系统腐蚀热稳定盐1.腐蚀产物的产生和危害1.1胺液系统流程简介辽阳石化溶剂再生系统设计循环总量500t/h,外送贫液至上游干气脱硫、液化气脱硫、循环氢脱硫、恶臭气体脱硫和火炬气脱硫等,系统流程复杂。
近期胺液系统发生设备和管道腐蚀,部分塔还发生了发泡现象。
可以判断溶剂系统受到了降解和污染,腐蚀产物主要为固体污染物和热稳定盐。
1.2腐蚀产物的原因1.2.1上游装置多,胺液中存在微量沉淀受到污染,随着污染物(或机械杂质)以及降解产物的积累进一步加剧胺液的劣化降解,形成热稳定盐。
原料气夹带CO、催化剂粉尘、CO、CS2等进入胺液形成热稳定盐阴离子。
1.2.2含硫烃类气体的氧化和衍生物形成热稳定盐阴离子。
1.2.3胺液净化系统能力严重不足,200t/h溶剂再生胺液净化处理能力为2t/h,300t/h溶剂再生胺液净化处理能力为0.3t/h,远远达不到净化处理500t/h胺液系统(且总藏量3800t)的要求。
1.2.4胺液有部分发泡现象,在某循环氢脱硫装置发泡严重。
部分发泡的溶剂消泡后携带阴离子进入胺液中,形成热稳定盐。
1.3危害1.3.1冲刷腐蚀:固体颗粒虽管道不断循环,在流速快的区域,尤其是弯头、变径处对薄弱部位产生严重腐蚀。
1.3.2热稳定性盐(HSS)腐蚀:HSS的生成与积累是导致碳钢设备腐蚀加剧的重要原因。
常见阴离子有:草酸根离子、甲酸根离子、乙酸根离子、氯离子、氰根离子。
这些离子与碳钢表面的FeS钝化层反应,形成相应的铁络合物,加速钝化层的破坏,形成管道腐蚀和设备腐蚀,降低设备使用寿命。
FeS + HSS- =FeHSS + S2-。
1.3.3降低胺液对酸性气体的吸附能力,造成吸收效果下降,净化尾气不达标。
炼油过程胺液的再生利用

炼油过程胺液的再生利用摘要:催化脱硫、加氢及硫磺回收装置采用醇胺法工艺吸收瓦斯、液化气、轻烃及硫磺还原气中的H2S,但溶剂也和系统中其他非挥发性酸反应生成热稳盐,胺液中的热稳盐含量较高时会导致气体脱硫后H2S质量不合格、设备腐蚀等问题。
公司溶剂再生装置使用HT-825A胺液净化再生设备,结果表明溶剂中热稳盐含量稳定在较低水平,再生溶剂性能良好,满足加催化脱硫、加氢及硫磺回收装置脱硫生产能力。
关键词:热稳盐,胺液净化,再生,脱硫1 前言催化脱硫、加氢及硫磺回收装置采用醇胺法工艺吸收瓦斯、液化气、轻烃及硫磺还原气中的H2S,富液进入溶剂再生系统,再生后的贫液经冷却后循环使用,再生塔顶出来的酸性气经冷却、分离后去硫磺回收装置。
热稳盐主要是由原料气以及胺降解等原因造成的,其产生和累积后会产生装置腐蚀加快、胺液发泡(胺液损耗的主要途径)、脱硫效果变差等严重影响装置正常运行的问题。
随着高含硫原油加工比例的增加,气体脱硫装置原料气中H2S浓度进一步上升,为保证装置长周期运行,必须确保溶剂质量。
公司溶剂再生装置HT-825A胺液净化再生设备采用北京思践通科技发展有限公司专利技术,该设备是根据公司溶剂再生的特点而设计,包括去除悬浮物过滤单元和脱除热稳盐、降解产物的离子交换工艺单元,设计贫液热稳盐脱除能力为3~5Kg/循环,处理弹性为60%~120%。
设备投运后能够将胺液中的热稳盐含量降到指标以下,有效降低了设备腐蚀、胺液发泡等问题,并提高了胺液的脱硫效率,满足装置脱硫生产要求。
2 胺液净化再生设备简述2.1设备介绍HT-825A胺液净化处理设备适用于干气、液化气脱硫系统,在线连续脱除贫胺液中的热稳盐(HSS)。
溶剂再生装置的贫胺液被系统压力送到本设备,进入离子交换树脂床净化,净化后的胺液返回到胺液储罐中。
离子交换树脂经再生、水洗和废物排放完成一个循环操作,本设备为全自动操作。
2.2设备设计参数及运行要求表1 设备设计基础数据3 加氢胺液净化设备运行情况及效果3.1 设备运行情况HT-825A胺液净化再生设备于2010年安装完毕,2011年试运行后备用。
溶剂再生装置溶剂发泡问题分析及预防措施

其次 , 在装 置长期运行过 程 中, 由 于 贫 液 与 富
液吸收了 H S和 C O , 对 碳 钢 是 有 腐 蚀 的 。管 道 中 的钢渣 、 硫化铁 、 硫 化 亚 铁 等 腐 蚀 产 物 在 气 体 和 液 体 的长 期 冲刷下 会逐 渐溶 解到 胺液 中 ] 。
1 . 2 胺液 中溶 解 了有机 物 这 些有 机 物 主 要 是 烃 类 凝 液 、 表 面活性 、 润 滑
分析 , 并 提出预防措 施 , 保障溶剂再生装置长周期 、 安全 、 稳定运行 。 关键词 : 溶剂再生 胺液 发泡 预防措施
溶剂再 生装 置 作 为煤焦 油 深加 工项 目下游 的配 套装置 , 主要 处理 来 自干气 、 液 化气 脱 硫塔 和 来 自硫 磺 回收装 置尾气 脱 硫塔 吸 收的 大量硫 化 氢或 二 氧化 碳 的胺液 ( 以下简称 富胺 液 ) 。溶剂 再生 采用 常规 蒸 汽汽 提 再 生 工 艺 , 溶 剂 采 用 N一 甲 基 二 乙 醇 胺 ( MD E A) 脱硫剂 , 通过汽提分 离 出富胺 液 中 的硫 化氢
或二氧化碳 , 得到净 化后 的胺 液 ( 以下 简称 贫胺 液 ) ,
脂 等 。烃类 凝液 主要 是 在 贫 胺 液 吸 收含 硫 干 气 、 液 化气 、 尾 气 中 的酸 性 气 时 , 被 吸收 介 质 中 携 带 的轻 烃 也会 部 分 被 吸 收 到 胺 液 系 统 中 , 并且 越积越多 。
锁, 尾 气 排放 不 达标【 2 J , 甚 至 带 来 严 重 的 环 境 污 染 , 因此 , 本 文 主要 针 对 溶 剂 再 生 装 置 溶 剂 发 泡
胺 的降解分子( 氧化、 加热 ) 与醇胺反应 能生成一系
列 酸性 盐 , 如草 酸 盐 、 甲酸 盐 、 乙酸盐、 硫 酸盐 、 硫 氰
芳烃抽提装置的节能优化探讨

芳烃抽提装置的节能优化探讨摘要:在石化工业中,苯、甲苯和硅烷(统称为BTX,轻芳香化合物)及其衍生物被广泛用于生产化学纤维、塑料、树脂、橡胶、清洗剂、芳香剂等精细化学品,具有不可替代的重要性。
汽油和再生油是芳香族碳氢化合物生产的重要原料;芳香族碳氢化合物萃取是主要的生产工艺,按分离原理主要分为液-液抽提和芳烃抽提。
液-液抽提是通过萃取溶剂将组分分离,以确定组分溶解度的差异;提取高纯度的芳香碳氢化合物。
芳烃抽提工艺对溶剂萃取具有较高的选择性,原料通用性高,溶剂损耗较小。
基于此,对芳烃抽提装置的节能优化进行研究,以供参考。
关键词:芳烃抽提;节能;优化引言装置关键设备溶剂回收塔的主要作用是将芳烃和溶剂分离,来自抽提塔的富溶剂在回收塔内进行减压、水蒸气汽提蒸馏,分离出混合芳烃和贫溶剂。
回收塔在减压下操作,残压由塔顶的压力控制器通过回收塔顶的真空泵吸入量来调节压力,减压操作的目的是为降低塔底操作温度,减少溶剂降解。
1芳烃抽提装置芳烃抽提装置目前主要有原料脱重,抽提系统,精馏系统组成,乙烯加氢大单元来的原理主要使C6-C8组分,其中包括芳烃和非芳烃部分,一般芳烃抽提装置选取的溶剂是环丁砜,主要是环丁砜的对于芳烃和非芳烃的选择性好,同时价格相对较低。
选择环丁砜的同时,也要考虑到环丁砜与C9组分分离困难,随着时间的累积,C9组分和循环的溶剂在一起会出现分层现象,影响溶剂的使用。
因此目前的芳烃抽提装置都是首先进行原料脱重,将C9组分进行脱除之后在进入抽提系统,精馏系统,生产合格的苯、甲苯但是由于芳烃抽提装置本身考虑能耗低,相对与液-液抽提减少了回收塔和水洗塔等主要设备,导致芳烃抽提工艺很难生产处合格的混合二甲苯。
只能生产甲苯和混合二甲苯的混合物。
2装置能耗分析从芳烃抽提装置能源消耗上看,3.5Mpa蒸汽和电是影响芳烃抽提装置的主要能耗指标,其中3.5Mpa蒸汽的能耗占比总能耗接近95%,电的能耗占比大约4%,其特点是每月用电消耗基本持平,随着处理量的波动,电的能耗指标小幅度波动。
废塑料再生造粒装置的物质流分析及优化

废塑料再生造粒装置的物质流分析及优化随着世界人口不断增加和经济的快速发展,塑料制品的需求也呈现出爆发式的增长。
然而,塑料制品的大量使用也导致了废塑料的产生量剧增,给环境造成了严重的影响。
为了解决这一问题,废塑料再生造粒装置应运而生。
本文将对废塑料再生造粒装置的物质流进行分析及优化的研究。
1. 物质流分析废塑料再生造粒装置是将废塑料进行处理,再经过特定工艺转化为再生塑料颗粒的设备。
整个过程涉及到多种物质的流动,包括废塑料原料、添加剂、溶剂和能源等。
首先,废塑料原料是该装置的关键输入物质。
不同种类的废塑料在再生造粒过程中需要进行分类和分选,以确保质量稳定和生产效益最大化。
废塑料原料通常通过回收、收购等渠道获取,其数量和质量直接影响到再生塑料颗粒的产量和质量。
其次,添加剂是再生塑料颗粒生产过程中的另一个重要物质流。
添加剂的使用可以改善再生塑料的性能,比如增强强度、耐热性等。
常见的添加剂包括增塑剂、稳定剂、色素等。
在物质流分析中,需要将添加剂的种类和用量进行记录,并评估其对于再生塑料的影响。
此外,溶剂和能源也是再生造粒过程中不可或缺的物质流。
溶剂主要用于塑料原料的清洗和分离,能源则用于驱动再生装置的运转。
分析溶剂和能源的使用情况可以帮助寻找节能减排的潜力,提高生产效率和资源利用率。
2. 优化策略针对废塑料再生造粒装置的物质流分析结果,我们可以提出一些优化策略,以提高装置的能效和环境表现。
首先,通过对废塑料原料的分类和分选,可以降低再生塑料的杂质含量,提高再生塑料的质量。
这样一来,可以减少添加剂的使用量,降低生产成本,并减少废料产生。
对于难以分类的塑料废料,可以考虑采用其他再利用方式,比如能源回收等。
其次,优化添加剂的使用。
针对不同种类的塑料废料,可以研究调整添加剂的种类和用量,以获得最佳的性能和经济效益。
此外,还可以探索替代性添加剂的使用,比如生物基添加剂,从而降低对有害化学物质的依赖。
此外,在溶剂和能源的使用上,可以考虑采用节能减排的措施。
提高富硫溶剂再生装置效果的研究
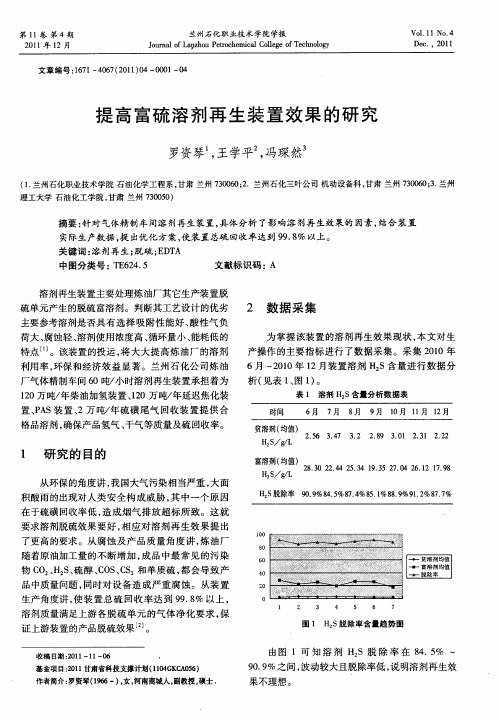
H s / 2/sL
1 研 究 的 目的
从 环保 的角 度讲 , 国大气 污染 相 当严重 , 面 我 大 积酸雨 的出现对人 类 安 全构 成 威 胁 , 中一 个 原 因 其 在 于硫 磺 回收率 低 , 成 烟气 排 放 超 标 所致 。这 就 造 要求溶 剂脱 硫效 果 要 好 , 应 对 溶 剂再 生 效 果 提 出 相
2 数 据 采 集
产操作 的主要指标进行了数据采集。采集 2 1 0 0年
6月 ~ 00年 1 21 2月装 置 溶 剂 H: 量 进 行 数 据 分 S含
析( 见表 1 图 1 。 、 )
表 1 溶剂 H S含量分析数据 表
时间 6月 7 月 8 9月 1 月 O月 1 月 1 1 2月
3 5
频
7 0
6 0
5 0
3 0 2 5 2 O 1 5 l 0
5 0
4 0 3 0 20 l 0
0
6.6 1
70 .7
8 2l .
91 .5
l 22 0.
图 3 不 同溶剂浓度下脱硫化 氢效果对比图
图 2 因 素排 列 图
其 操作 条件 是 ( ) 生 塔底 液 位 :0~6 % ; 1再 4 0 再 生 塔 顶 温 度 :0 10—1O ; 生 塔 底 温 度 :2 l℃ 再 10~ 10C; 却 后 酸 性 气 温 度 : 5C。 ( 液 位 , 3 ̄ 冷 ≤4  ̄ 2) 温
摘要 : 对 气体 精 制 车 间溶 剂再 生装 置 , 体分 析 了影响 溶 剂 再 生效 果的 因素 , 针 具 结合 装 置
实际生产 数据 , 出优 化 方案 , 装置 总硫 回收 率 达到 9 . % 以上 。 提 使 98
操作指南:实验室溶剂的再生与精制
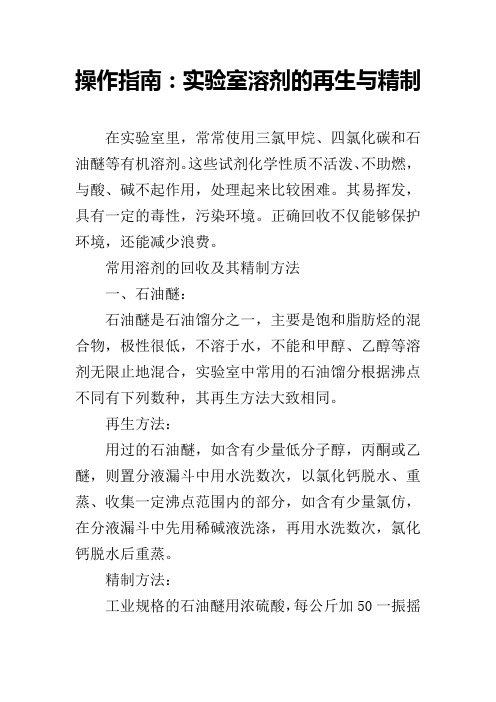
操作指南:实验室溶剂的再生与精制在实验室里,常常使用三氯甲烷、四氯化碳和石油醚等有机溶剂。
这些试剂化学性质不活泼、不助燃,与酸、碱不起作用,处理起来比较困难。
其易挥发,具有一定的毒性,污染环境。
正确回收不仅能够保护环境,还能减少浪费。
常用溶剂的回收及其精制方法一、石油醚:石油醚是石油馏分之一,主要是饱和脂肪烃的混合物,极性很低,不溶于水,不能和甲醇、乙醇等溶剂无限止地混合,实验室中常用的石油馏分根据沸点不同有下列数种,其再生方法大致相同。
再生方法:用过的石油醚,如含有少量低分子醇,丙酮或乙醚,则置分液漏斗中用水洗数次,以氯化钙脱水、重蒸、收集一定沸点范围内的部分,如含有少量氯仿,在分液漏斗中先用稀碱液洗涤,再用水洗数次,氯化钙脱水后重蒸。
精制方法:工业规格的石油醚用浓硫酸,每公斤加50一振摇后放置一小时,分去下层硫酸液,可以溶去不饱和烃类,根据硫酸层的颜色深浅,酌情用硫酸振摇萃取二、三次。
上层石油醚再用5%稀碱液洗一次,然后用水洗数次,氯化钙脱水后重蒸,如需绝对无水的,再加金属钠丝或五氯化二磷脱水干燥。
二、环乙烷:沸点,性质与石油醚相似。
再生方法:再生时先用稀碱洗涤。
再用水洗,脱水重蒸。
精制方法将工业规格环乙烷加浓硫酸及少量硝酸钾放置数小时后,分去硫酸层,再以水洗,重蒸,如需绝对无水的,再用金属钠丝脱水干燥。
三、苯:沸点,比重0.879,不溶于水,可与乙醚、氯仿、丙酮等在各种比例下混溶,纯苯在时固化为结晶,常利用此法纯化。
再生方法:用稀碱水和水洗涤后,氯化钙脱水重蒸。
精制方法:工业规模的苯常含有噻吩、吡啶和高沸点同系物如甲苯等,可将苯1000毫升,在室温下用浓硫酸每次80毫升振摇数次,至硫酸层呈色较浅时为止,再经水洗,氯化钙脱水重蒸,收集79℃馏分。
对于甲苯等高沸点同系物,则用二次冷却结晶法除去,苯在固化成为结晶,可以冷却到,滤取结晶,杂质在液体中。
四、氯仿:比重1.488,不溶于水,易与乙醚、乙醇等混溶,在日光下易氧化分解成Cl2、HCl、CO2及光气(COCl2),后者有毒,故应贮在棕色瓶中。
废有机溶剂的再生利用

.
10
回收利用的价值
减少原料
减少危害
增加收入
.
11
再生利用的方法
1
蒸馏法再生废有机溶剂
2 活性炭吸附法再生废有机溶剂
3 溶剂萃取法再生废有机溶剂
4
超滤法再生有机溶剂
5 废碱液中有机溶剂再生技术
.
12
3.3.1蒸馏法再生废有机溶剂
蒸馏法:利用液体混合物中各组分挥发度的差别,使液体混合物 部分汽化并随之使蒸气部分冷凝,从而实现其所含组分的分离。
.
24
3.3.3溶解萃取法再生废有机溶剂
溶剂萃取是分离液体混合物的一种方法,利用液体混合物各组分 在某溶剂中溶解度的差异而实现分离。即溶液与对杂质有更高亲 和力的另一种互不相溶的液体相接触,使其中某种成分分离的过 程。这分离可以是由于两种溶剂之间溶解度不同或是发生了某种 化学反应。溶剂萃取应被视为是一个废水浓度处理丶选择分离的 过程,分离过程回收的物质能够补偿分离过程的费用。
与普遍采用的有机废液焚烧方法比较,该系统的设备投资及运行成本相差不大 ;但采用废有机溶剂 再生处理系统,回收的化工产 品每年可增加700多万元的销售收入,具有明显的经济效益。
.
22
3.3.2活性炭吸附法再生废有机溶剂
活性炭吸附由吸附和脱附两大部分组成,吸附的原理是吸附剂有 较大的比表面积,对危险废物中的有机物发生吸附,此吸附多为 物理吸附,过程可逆;当吸附达到饱和后,再用适当方法脱附, 再生的活性炭循环使用。
.
29
3.3.4超滤法再生废有机溶剂
由于轻质石油资源减少,因而重质渣油的加工备受关注。重油中 含有大量的沥青质,而沥青质中富集了原油中大部分的金属及杂 原子,从而为重油的加工造成极大的困难,因此有人称沥青质为 “石油的胆固醇”
炼油厂溶剂再生装置及其主要控制方案概要

1前言近年来,我国加工进口原油量在逐年增加,炼厂的加工装置规模也在不断扩大,尤其是原油含硫量的增加,国家对油品质量和环保要求日益严格,需要脱硫的介质也越来越多。
在催化裂化装置、延迟焦化装置和加氢裂化装置等一般均需设置胺液脱硫,脱硫后的富液须经溶剂再生装置进行再生,溶剂再生的好坏直接关系到脱硫效果,所以溶剂再生是胺液脱硫中很重要的一部分。
溶剂再生发展经历了3个阶段:第一阶段:1995年前,国内炼厂规模较小,加工装置较少,原油的硫含量较低,需要脱硫的介质也较少,因此都采用装置内单独设置脱硫再生,溶剂再生产生的酸性气集中输送至硫磺回收装置。
第二阶段:1995年,我国炼油设计行业学习国外先进经验,首次为安庆石化分公司设计了溶剂集中再生装置,即每套主体装置仅设置脱硫部分,而再生部分全厂集中设置,而且平面布置紧靠硫磺回收装置。
这种设置模式迅速被设计单位和建设单位认可,成为新建炼厂或老厂改造的主要模式。
第三阶段:为进一步降低投资和操作费用,新建炼厂还采用相似气体集中处理的方式,即把压力、温度、组成相近的气体,或用途相同的气体混合在一个吸收塔内进行脱硫,溶剂集中再生。
“脱硫适当集中,溶剂集中再生”中指的集中再生,并不是指全厂富液都集中在一套再生系统进行再生,只是相对集中。
溶剂再生装置套数除考虑常减压装置套数外,还需根据全厂总流程、原油硫含量及装置组成等因素综合考虑确定。
目前硫磺回收装置内的再生单元仍以单独设置为主。
2技术特点及工艺流程溶剂再生装置工艺过程可分为溶剂配制、溶剂换热、溶剂再生和退溶剂等4部分。
其中换热部分又分为低温闪蒸、中温闪蒸和高温闪蒸,原以高温闪蒸为主,但因后者在闪蒸时H 2S 较前者更易被闪蒸出来,造成设备腐蚀和硫的损失,所以现国内大多选用中温闪蒸。
以中温闪蒸为例,装置外的富液经贫富液二级换热器与自贫液加压泵来的贫液换热至60℃左右后,进入富液闪蒸罐,闪蒸出大部分的溶解烃(闪蒸出的烃至火炬管网后,经富液加压泵与贫富液一级换热器换热至98℃,进入溶剂再生塔上部。
溶剂再生塔操作异常原因分析及策略

201 溶剂再生塔操作异常原因分析1.1 溶剂再生塔操作异常在分析溶剂再生塔操作异常的过程中,以甲基二乙醇胺(MDEA)再生塔底为例进行简要探索。
在该装置操作过程中出现了MDEA再生塔底液位有规律的波动,其呈现的规律为每隔8min塔底会出现1个波峰以及1个波谷,随之而来改变的是塔顶的压力,整体的波动范围在85~110kPa,塔底温度也会随之变化,整体的变化波动范围在119~127℃。
在炼油厂,如果溶剂再生塔装置出现了操作异常会直接影响到胺液质量以及脱硫效果。
贫胺液硫化氢质量浓度会出现明显的改变,从原来的2~3g/L升至4~6g/L,而贫胺液中二氧化碳质量浓度也会改变,即由原来的1~2g/L升至2~3g/L。
1.2 溶剂再生塔操作异常的原因分析为了进一步探究溶剂再生塔操作异常的原因需要在贫/富液换热器进出口选择样本,并对样本进行分析,探索样本胺液中的H 2S和CO 2质量分数,其目的是更好地判断胺液质量同时分析其质量改变的原因。
可以得到贫/富液换热器进出口贫液样质量中的换热器进口贫液的电导率为0.906s/m、总胺质量分数为27.82%、热稳定性盐质量分数为0.96%、束缚胺质量分数为1.39%、强阳离子质量浓度为3.677mg/L、硫化氢质量浓度为4.157mg/L、氯离子质量浓度为265mg/L;贫换热器出口贫液的电导率为0.732s/m、总胺质量分数为28.04%、热稳定性盐质量分数为1.13%、束缚胺质量分数为0.61%、强阳离子为4.042mg/L、硫化氢质量浓度为3.039mg/L、氯离子质量浓度为17mg/L。
(1)再生塔内胺液发泡导致塔底压力升高。
对溶剂再生塔整体运行工艺进行分析,发现在设备使用过程存在胺液发泡的情况,会生成本身相对不稳定的泡沫,这种生成物会导致工艺运行整体质量显著下降,并且在该工艺生产过程中,再生塔的压力会有明显的升高,在运行过程中压力变化的波动非常大,甚至出现了再生塔底液位的大幅度变化的情况。
脱硫溶剂MDEA的再生工艺_符秀兰

富胺液组分
硫化氢含量
2. 5~ 10. 0 g /L
二氧化碳含量
5~ 20 g /L
2、再生后贫胺液品质要求
贫胺液 w ( MDEA)
\ 28%
硫化氢含量
[ 2 g /L
冷后温度
[ 45 e
计算结果见表 1。
# 32#
硫磷设计与粉体工程
S P & BMH RELATED ENG INEER ING
复合型甲基二乙醇胺 (M DEA ) 溶剂是近年来国 内外研究、发展最 快的一种脱硫 溶剂, 该溶 剂是以 MDEA 为基础组分, 加入适量添加剂改善胺溶液的 脱硫选择性和抗降解能力, 此外还加入微量辅助添 加剂, 以增加溶剂的抗氧化和抗发泡能力。到目前 为止, 我国已有 30 多套工业 脱硫装置采用 复合型 MDEA 溶剂, 普遍收到较好的使用效果。
< 900 mm A = 220 m2, 2 台
<900 mm A = 220 m2, 2台
向梯形浮阀塔盘, 具有压降低、效率高、操作弹性大 等优点, 适应长周期运转。
4、装置内需要冷却的工艺介质尽量采用空冷, 以减少循环水用量。
5、防止胺液降解。醇胺类物质降解主要有热降 解、化学降解、氧化降解。MDEA 相比其他醇胺热稳 定性能要好, 同时再生塔底重沸器出口温度控制在 125 e 左右, 较其他醇胺类再生温度低。再生塔底 重沸器加热介质为减温后的蒸 汽, 温度控制在 148 e , 以防止重沸器管束壁温过高, 可进一步缓解 MDEA 的热降解。MDEA 为叔胺, 不具备与 CO2 反 应产生化学降解的条件。
胺液再生装置节能降耗的探讨
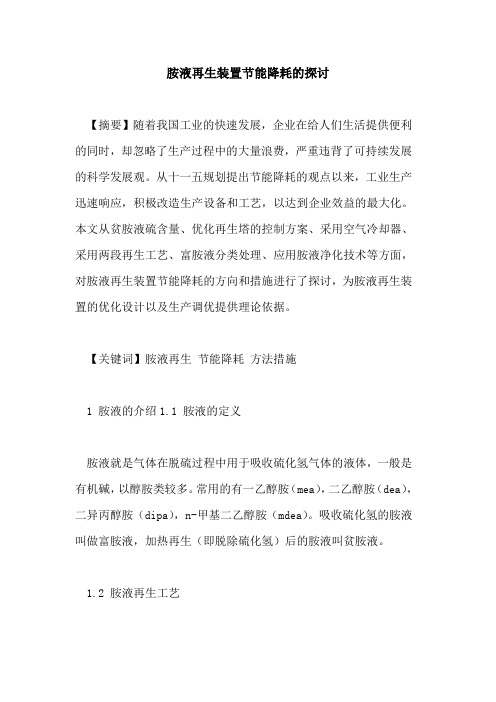
胺液再生装置节能降耗的探讨【摘要】随着我国工业的快速发展,企业在给人们生活提供便利的同时,却忽略了生产过程中的大量浪费,严重违背了可持续发展的科学发展观。
从十一五规划提出节能降耗的观点以来,工业生产迅速响应,积极改造生产设备和工艺,以达到企业效益的最大化。
本文从贫胺液硫含量、优化再生塔的控制方案、采用空气冷却器、采用两段再生工艺、富胺液分类处理、应用胺液净化技术等方面,对胺液再生装置节能降耗的方向和措施进行了探讨,为胺液再生装置的优化设计以及生产调优提供理论依据。
【关键词】胺液再生节能降耗方法措施1 胺液的介绍1.1 胺液的定义胺液就是气体在脱硫过程中用于吸收硫化氢气体的液体,一般是有机碱,以醇胺类较多。
常用的有一乙醇胺(mea),二乙醇胺(dea),二异丙醇胺(dipa),n-甲基二乙醇胺(mdea)。
吸收硫化氢的胺液叫做富胺液,加热再生(即脱除硫化氢)后的胺液叫贫胺液。
1.2 胺液再生工艺富胺液吸收了硫化氢后从气体脱硫装置中来,再与贫胺液交换热后才进入富胺液闪蒸罐,当大部分溶解烃被闪蒸出后,再经过贫/富胺液换热后进再生塔进行再生,由0.35mpa蒸汽给塔底重沸器供热,再将塔顶气相产品中富含硫化氢的酸性气去除硫磺来回收装置制硫,再回流全部的液相,最后将塔底部产品贫胺液经贫/富胺液换热回收能量,冷却后,可以将它放置到去气体脱硫装置循环使用。
根据实验模拟结果分析得到,在满足脱硫要求的前提下应尽量提高再生后贫胺液中硫化氢的含量,但通常不应超过0.02%。
1.3 胺液工业的发展任重道远胺法气体脱硫仍是目前研究的重点与应用最活跃的领域。
目前大多数工业都采用的是二甲胺(mdea),而该工艺中的能耗主要集中在胺液再生装置,其能耗的高低直接影响脱硫的成本,然而在该行业中,我国所掌握的技术仍落后于国际水平,这也引起了国家相关部门的高度中重视。
在”十二五”阶段,我国将继续处于重要战略机遇期。
机遇和挑战都是前所未有,但是机遇要大于挑战。
3号溶剂再生装置的腐蚀问题及应对策略
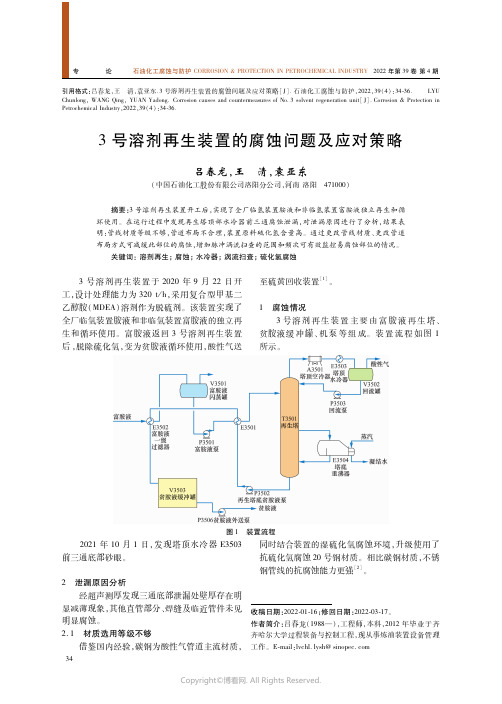
引用格式:吕春龙,王 清,袁亚东.3号溶剂再生装置的腐蚀问题及应对策略[J].石油化工腐蚀与防护,2022,39(4):34 36. LYUChunlong,WANGQing,YUANYadong.CorrosioncausesandcountermeasuresofNo.3solventregenerationunit[J].Corrosion&ProtectioninPetrochemicalIndustry,2022,39(4):34 36.3号溶剂再生装置的腐蚀问题及应对策略吕春龙,王 清,袁亚东(中国石油化工股份有限公司洛阳分公司,河南洛阳 471000)摘要:3号溶剂再生装置开工后,实现了全厂临氢装置胺液和非临氢装置富胺液独立再生和循环使用。
在运行过程中发现再生塔顶部水冷器前三通腐蚀泄漏,对泄漏原因进行了分析,结果表明:管线材质等级不够,管道布局不合理,装置原料硫化氢含量高。
通过更改管线材质、更改管道布局方式可减缓此部位的腐蚀,增加脉冲涡流扫查的范围和频次可有效监控易腐蚀部位的情况。
关键词:溶剂再生;腐蚀;水冷器;涡流扫查;硫化氢腐蚀收稿日期:2022 01 16;修回日期:2022 03 17。
作者简介:吕春龙(1988—),工程师,本科,2012年毕业于齐齐哈尔大学过程装备与控制工程,现从事炼油装置设备管理工作。
E mail:lvchl.lysh@sinopec.com 3号溶剂再生装置于2020年9月22日开工,设计处理能力为320t/h,采用复合型甲基二乙醇胺(MDEA)溶剂作为脱硫剂。
该装置实现了全厂临氢装置胺液和非临氢装置富胺液的独立再生和循环使用。
富胺液返回3号溶剂再生装置后,脱除硫化氢,变为贫胺液循环使用,酸性气送至硫黄回收装置[1]。
1 腐蚀情况3号溶剂再生装置主要由富胺液再生塔、贫胺液缓冲罐、机泵等组成。
装置流程如图1所示。
图1 装置流程 2021年10月1日,发现塔顶水冷器E3503前三通底部砂眼。
炼厂溶剂再生装置运行中存在的问题及思考
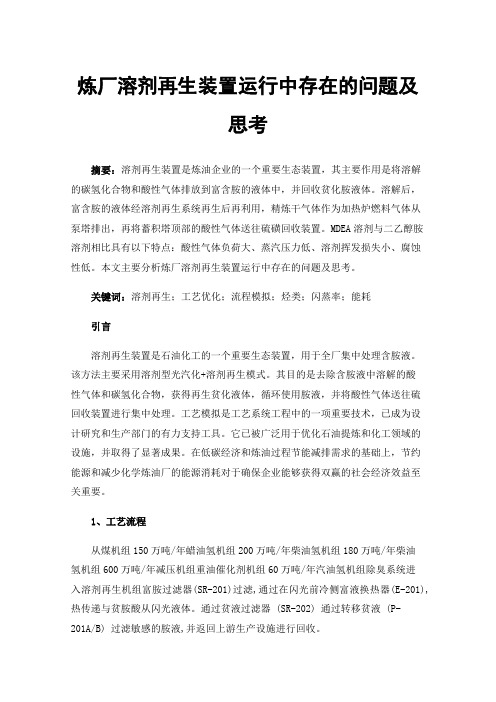
炼厂溶剂再生装置运行中存在的问题及思考摘要:溶剂再生装置是炼油企业的一个重要生态装置,其主要作用是将溶解的碳氢化合物和酸性气体排放到富含胺的液体中,并回收贫化胺液体。
溶解后,富含胺的液体经溶剂再生系统再生后再利用,精炼干气体作为加热炉燃料气体从泵塔排出,再将蓄积塔顶部的酸性气体送往硫磺回收装置。
MDEA溶剂与二乙醇胺溶剂相比具有以下特点:酸性气体负荷大、蒸汽压力低、溶剂挥发损失小、腐蚀性低。
本文主要分析炼厂溶剂再生装置运行中存在的问题及思考。
关键词:溶剂再生;工艺优化;流程模拟;烃类;闪蒸率;能耗引言溶剂再生装置是石油化工的一个重要生态装置,用于全厂集中处理含胺液。
该方法主要采用溶剂型光汽化+溶剂再生模式。
其目的是去除含胺液中溶解的酸性气体和碳氢化合物,获得再生贫化液体,循环使用胺液,并将酸性气体送往硫回收装置进行集中处理。
工艺模拟是工艺系统工程中的一项重要技术,已成为设计研究和生产部门的有力支持工具。
它已被广泛用于优化石油提炼和化工领域的设施,并取得了显著成果。
在低碳经济和炼油过程节能减排需求的基础上,节约能源和减少化学炼油厂的能源消耗对于确保企业能够获得双赢的社会经济效益至关重要。
1、工艺流程从煤机组150万吨/年蜡油氢机组200万吨/年柴油氢机组180万吨/年柴油氢机组600万吨/年减压机组重油催化剂机组60万吨/年汽油氢机组除臭系统进入溶剂再生机组富胺过滤器(SR-201)过滤,通过在闪光前冷侧富液换热器(E-201),热传递与贫胺酸从闪光液体。
通过贫液过滤器 (SR-202) 通过转移贫液 (P-201A/B) 过滤敏感的胺液,并返回上游生产设施进行回收。
同时将5-10t/h贫胺酸放入氨基酸在线清洗系统(SR-203)中,除去热稳定盐后,氨酸放在溶剂储存塔(T-291)的底部再生塔(C-201)由收集器放入塔冷却器(E-203A/B),用低蒸汽加热,为富胺酸的再生提供热源;塔式搅拌机(E-203A/B)产生的冷凝水输送到冷凝水容器(D-203,D-208),在整个机组的冷凝水输送到冷凝水回收系统后,冷凝水从机组引入冷凝水管网。
某连续重整装置关键设备腐蚀问题分析及控制措施

某连续重整装置关键设备腐蚀问题分析及控制措施摘要:某石化公司连续重整装置由于长期运行,装置内设备腐蚀情况严重,造成装置多次停工,对装置运行安全与效益带来了不利影响。
为彻底解决这些问题,本文针对重整装置腐蚀机理及防腐措施进行简要阐述,并针对装置内相关设备的腐蚀现象进行了针对性防腐及控制措施攻关,应用效果明显,达到了处理及缓解装置腐蚀的目的。
关键词:装置腐蚀;硫化氢;氯化氢;腐蚀控制1装置内设备腐蚀介质连续重整装置内预加氢原料中硫、氮、氯及反再系统中注入的聚氯乙烯通过,HCN与水后形成酸碱性物质,从而造成预加氢反应后形成硫化氢、氯化氢、NH3加氢及反再系统腐蚀,抽提中加单乙醇氨,环丁砜降解后形成酸与水后形成酸性物质,从而造成抽提系统腐蚀。
2腐蚀机理及情况调查2.1露点腐蚀S和HCN、HCl对金属起腐蚀作用,预加氢汽提塔C-102在催化重整系统中H2C1溶解在水中,由于此时温度较高,导致大量的HCl在水中后,气相生成的NH4聚集,形成局部强酸,导致强烈的H+去极化腐蚀。
FeS+2H+Fe2++HS2Fe+2H+Fe2++H2Fe2+与C1-结合生成FeCl2,与反应产物中的H2S反应,产生硫化铁和盐酸,由此形成成盐酸与硫化氢的循环腐蚀,其中C1-一起的作用尤其大,这种腐蚀体系的腐蚀速度要比单纯的盐酸或硫化氢腐蚀严重的多。
2.2冲刷腐蚀冲刷本身即可破坏FeS膜,而在腐蚀介质的作用下,金属不断以离子状态被冲刷离去。
一方面,冲刷带走腐蚀产物,暴露处新鲜的金属表面,另一方面,使腐蚀介质在流体中更加分散而与金属表面接触的机会增多,因此这些部位的金属壁会很快变薄。
2.3应力腐蚀重整装置的应力腐蚀是金属在固定拉应力和特定介质NH3+HCl+H2S+H20共同作用下所引起的破裂。
金属或合金发生应力腐蚀时,大部分表面并未遭受腐蚀,只在局部出现一些由表及里的细裂纹,这些裂纹可能是穿过晶粒的,也可能是沿着晶界延伸的,随着裂纹的扩展,材料的受力截面减小。
- 1、下载文档前请自行甄别文档内容的完整性,平台不提供额外的编辑、内容补充、找答案等附加服务。
- 2、"仅部分预览"的文档,不可在线预览部分如存在完整性等问题,可反馈申请退款(可完整预览的文档不适用该条件!)。
- 3、如文档侵犯您的权益,请联系客服反馈,我们会尽快为您处理(人工客服工作时间:9:00-18:30)。
溶剂再生装置主要设备材料的选择探讨
摘要:阐述了溶剂再生装置工艺流程,分析溶剂再生装置设备腐蚀生成的原因和腐蚀类型,提出了主要设备的选材方案。
关键词:溶剂再生;胺腐蚀;MDEA
溶剂再生装置采用常规蒸汽汽提再生工艺,溶剂采用复合型MDEA溶剂。
MDEA具有良好的选择性吸收性能,酸性气负荷、腐蚀轻,使用浓度高、循环量小、能耗低。
再生酸性气送至硫磺回收装置。
一、溶剂再生工艺原理与流程
(一)工艺原理
干气、液化气、焦化富气及加氢精制来的低压含硫瓦斯,硫磺回收装置的尾气,其脱硫的工艺原理是相同的。
首先其中H2S和CO2在低温下与溶剂进行化学反应,生成一种不稳定的络和物,使干气、液化气、富气、瓦斯得以净化。
而这种络和物又在高温下分解脱出H2S、CO2使溶剂得以再生,循环使用。
如以乙醇胺为例它能吸收气体中的硫化氢生成硫化物和酸式硫化物;吸收二氧化碳生成碳酸盐和酸式碳酸盐。
(二)工艺流程特点
1.集中后的富溶剂采用中温(60~65℃)低压闪蒸,保证装置稳定操作,降低再生塔顶酸性气中的烃含量。
2.再生塔底重沸器热源由0.7MPa(180℃)蒸汽减温减压至0.3MPa(143℃)蒸汽,以防止重沸器管束壁温过高,造成溶剂的热降解。
3.溶剂配制及溶剂系统补水均采用装置内产出的凝结水,溶剂缓冲罐设有氮气保护系统,避免溶剂因氧化而变质。
(三)工艺流程简述
1.自上游装置和硫磺回收部分来的混合富液,经富液过滤器过滤后与贫液经贫富液二级换热器换热至60℃,进入富液闪蒸罐,闪蒸出大部分溶解烃,再经富溶剂泵加压,并经贫富液一级换热器换热至98℃,进入再生塔,塔底由重沸器供热,进行间接蒸汽加热。
塔顶气体经酸性气空气冷却器、再生塔顶冷凝器冷凝冷却、酸性气分液罐分液后,酸性气送至硫磺回收部分,冷凝液经回流泵返塔作为回流。
2.为了减少溶剂损失,设计中采用以下措施:①再生塔底重沸器热源用0.7MPa(180℃)蒸汽减温减压至0.35MPa(147℃)蒸汽,以防止重沸器管束壁温过高,造成溶剂的热降解。
②溶剂配制及溶剂系统补水均采用除氧水,溶剂缓冲罐设有氮气保护系统,避免溶剂氧化变质。
③富溶剂进装置设置富液过滤器,
混合富液进行全量过滤,除去管道内因腐蚀等原因产生的杂质。
溶剂循环泵出口设置高效组合式在线胺液过滤装置,过滤15%~20%的贫溶剂,以除去溶剂中的降解物质,避免溶剂发泡。
二、主要设备
(一)再生塔
主要腐蚀类型:塔顶H2S-CO2-H2O硫化物应力腐蚀,其余部分RNH2(乙醇胺)-H2S-CO2-H2O胺腐蚀。
胺腐蚀机理:①损伤机理。
胺腐蚀并非直接由胺本身造成,而是胺液中溶解酸性气体(二氧化碳和硫化氢)、胺降解产物、耐热胺盐(HSAS)和其它腐蚀性杂质引起。
②损伤形态。
碳钢和低合金钢遭受胺腐蚀时可表现为均匀减薄或局部减薄,以及沉积物垢下腐蚀;介质流速较低时,多为均匀减薄,介质高流速并伴有紊流时,多为局部减薄。
③敏感材料碳钢、低合金钢。
④主要影响因素。
介质:对碳钢和低合金钢的侵蚀性从大到小的次序为单乙醇胺(MEA)、二甘醇胺(DGA)、二异丙胺(DIPA)、二乙醇胺(DEA)和甲基二乙醇胺(MDEA);耐热胺盐:浓度超过2%(质量比)时,腐蚀性较强,且腐蚀能力随浓度的增大而上升;杂质:氨、硫化氢和HCN(氰化氢)等杂质会加速腐蚀;温度:腐蚀速率随着温度升高而增大。
温度高于104℃时可因酸性气体闪蒸导致严重局部腐蚀;流速:低流速区一般呈均匀减薄,高流速区尤其存在强紊流时会造成局部减薄。
⑤易发设备。
胺处理系统再生塔塔底再沸器和再生器,尤其位于高温且介质流速高的区域,易发生严重腐蚀。
2.再生塔材料选择
塔设计温度较高,胺腐蚀较严重,壳体选用复合钢板Q245R+S30403,塔盘材料选用S30403。
(二)再生塔底重沸器
腐蚀机理和材料选择。
与再生塔底部腐蚀相同主要为RNH2(乙醇胺)-H2S-CO2-H2O胺腐蚀,因工作温度较高(约120℃),有气相逸出,对换热管壁冲刷腐蚀较严重,胺盐可能引起在换热管上结污垢,导致管壁温度升高,同时,污垢与换热管之间又存在间隙,形成垢下腐蚀,加速设备的损坏。
换热管材料选用S30403,壳程和管程筒体材料都选用不锈钢复合钢板Q245R+S30403。
(三)富液闪蒸罐
1.腐蚀机理
贫液的主要成分是甲基二乙醇胺(MDEA),含有少量的H2S、CO2、H2O。
其中MDEA是一种弱碱,其碱性随温度降低而增强,因此在低温条件下可用于
在吸收塔中脱除液态烃和干气中的H2S,这样贫胺液就生成了富液,在高温条件下富液中的硫化氢又在再生塔中解析出来,使富液又生成贫胺液,达到了溶剂的循环使用。
2.材料选择。
一级贫富液换热器的工作温度正好90℃以上,二级贫富液换热器工作温度在90℃以下。
为避免上述的应力腐蚀,一级贫富液换热器换热管材料选用S30403,壳程和管程筒体材料都选用不锈钢复合钢板Q245R+S30403;二级贫富液换热器换热管可以选用耐湿硫化氢应力腐蚀专用无缝钢管,壳体材料用Q245R,正火状态使用,超声检测,焊后进行消除焊接应力热处理。
三、总结和建议
由于溶剂再生装置原料来源多、组分复杂、又是全厂性配套装置,因此溶剂再生装置设备的腐蚀问题是不可避免的,因为腐蚀介质几乎贯穿全装置。
有时设备的腐蚀不仅仅是一种类型,而是多种腐蚀类型共同存在。
因此对溶剂再生装置腐蚀产生的原因和机理认真研究,采取有效的防护措施,合理选择设备材质,相对减慢腐蚀速度,才能既考虑经济性又保证装置安全平稳长周期安全运行。
参考文献
[1]炼油设备工程师手册(第二版),中国石油和石化工程研究会编著,中国石化出版社,2009,ISBN 978-7-80229-971-9第十五章15.9.1,P843-853。