直拉单晶硅的制备 掺杂
直拉单晶硅工艺技术黄有志

直拉单晶硅工艺技术黄有志直拉单晶硅工艺技术是制备单晶硅材料的一种重要方法。
该技术的发展,对于现代半导体产业的推动和发展具有重要意义。
黄有志博士是在该领域取得突破性进展的科学家之一。
以下是对其工艺技术的一些介绍。
直拉单晶硅工艺技术是制备高纯度、高晶质结构的单晶硅材料的关键技术之一。
它是将多晶硅材料通过高温熔融状态下拉制而成的。
在这个过程中,使用的原料是通常用石英砂进行还原制备的多晶硅材料,通过特定的工艺参数控制,使其在高温下逐渐冷却凝固,形成单晶硅材料。
直拉单晶硅工艺技术具有高效、高质量的特点。
首先,该工艺技术能够有效地提高单晶硅材料的纯度。
在熔融状态下,通过控制氧气处理时间和掺杂剂的加入,可以有效地去除杂质。
其次,该工艺技术能够制备出高质量的单晶硅材料。
通过控制拉伸速度和温度梯度,可以减少晶体结构的缺陷,提高晶体的完整性和结晶度。
最后,该工艺技术还具有高效率的特点。
相比于其他制备单晶硅材料的方法,直拉工艺技术可以大规模生产,并且成本低廉,适用于工业化生产。
黄有志博士在直拉单晶硅工艺技术的研究领域做出了突出的贡献。
他主要关注在工艺参数的优化和工艺过程的监控控制方面。
通过对熔融硅的温度、拉伸速度、氧气处理时间等参数的研究,他成功地优化了工艺参数,提高了单晶硅材料的质量和产量。
同时,他还研发了一套先进的监控系统,可以实时监测熔融硅的温度和拉伸速度等参数,确保工艺过程的稳定性和可控性。
黄有志博士的工艺技术在半导体产业中得到了广泛的应用。
单晶硅材料是半导体器件制备中不可或缺的基础材料,而直拉单晶硅工艺技术能够高效、高质量地制备出该材料,为半导体器件的生产提供了重要保障。
目前,黄有志博士的工艺技术已广泛应用于半导体材料制备企业中,并且取得了良好的经济效益和应用效果。
总之,直拉单晶硅工艺技术是制备高纯度、高质量的单晶硅材料的关键技术之一。
黄有志博士在该领域的研究和创新,为该技术的发展和应用做出了重要贡献。
他的工艺技术在半导体产业中得到了广泛应用,为半导体器件的制备提供了重要支持。
直拉单晶硅的制备-掺杂讲课讲稿

直拉单晶硅的制备-掺杂直拉单晶硅的制备硅、锗等单晶制备,就是要实现由多晶到单晶的转变,即原子由液相的随机排列直接转变为有序阵列;由不对称结构转变为对称结构。
但这种转变不是整体效应,而是通过固液界面的移动而逐渐完成的。
为实现上述转化过程,多晶硅就要经过由固态到熔融态,然后又由熔融态硅到固态晶体硅的转变。
这就是从熔体硅中生长单晶硅所遵循的途径。
从熔体中生长硅单晶的方法,目前应用最广泛的主要有两种:有坩埚直拉法和无坩埚悬浮区熔法。
在讨论这两种制备方法之前,还应讨论在制备单晶过程中必不可少的一些准备工序。
包括掺杂剂的选择、坩埚的选择、籽晶的制备等,分别介绍如下:一、掺杂在制备硅、锗单晶时,通常要加入一定数量杂质元素(即掺杂)。
加入的杂质元素决定了被掺杂半导体的导电类型、电阻率、少子寿命等电学性能。
掺杂元素的选择必须以掺杂过程方便为准,又能获得良好的电学性能和良好晶体完整性为前提。
1掺杂元素的选择(1)根据导电类型和电阻率的要求选择掺杂元素制备N型硅、锗单晶,必须选择Ⅴ族元素(如P、As、Sb、Bi);制备P型硅、锗单晶必须选择Ⅲ族元素(如B、Al、Ga、In、Ti)。
杂质元素在硅、锗晶体中含量的多少决定了硅、锗单晶的电阻率。
电阻率不仅与杂质浓度有关,而且与载流子的迁移率有关。
当杂质浓度较大时,杂质对载流子的散射作用,可使载流子的迁移率大大降低,从而影响材料的导电能力。
考虑到以上因素,从理论上计算了电阻率与杂质浓度的关系曲线,如图9-5所示。
在生产工艺上按电阻率的高低分档。
掺杂有三档:轻掺杂(适用于大功率整流级单晶)、中掺杂(适用于晶体管级单晶)、重掺杂(适用于外延衬底级单晶)。
(2)根据杂质元素在硅、锗中溶解度选择掺杂元素各种杂质元素在硅、锗中溶解度相差颇大。
例如,采用大溶解度的杂质,可以达到重掺杂的目的,又不会使杂质元素在晶体中析出影响晶体性能。
下表列出了常用掺杂元素在硅、锗单晶生长时掺入量的极限,超过了极限量,单晶生长不能进行。
直拉法单晶硅 -回复
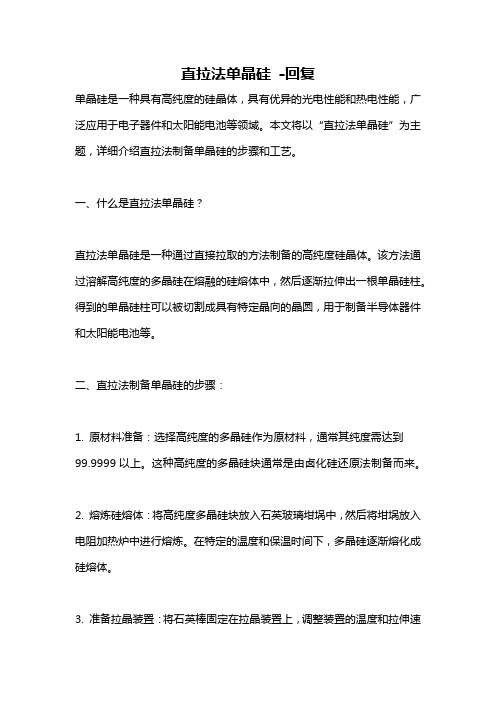
直拉法单晶硅-回复单晶硅是一种具有高纯度的硅晶体,具有优异的光电性能和热电性能,广泛应用于电子器件和太阳能电池等领域。
本文将以“直拉法单晶硅”为主题,详细介绍直拉法制备单晶硅的步骤和工艺。
一、什么是直拉法单晶硅?直拉法单晶硅是一种通过直接拉取的方法制备的高纯度硅晶体。
该方法通过溶解高纯度的多晶硅在熔融的硅熔体中,然后逐渐拉伸出一根单晶硅柱。
得到的单晶硅柱可以被切割成具有特定晶向的晶圆,用于制备半导体器件和太阳能电池等。
二、直拉法制备单晶硅的步骤:1. 原材料准备:选择高纯度的多晶硅作为原材料,通常其纯度需达到99.9999以上。
这种高纯度的多晶硅块通常是由卤化硅还原法制备而来。
2. 熔炼硅熔体:将高纯度多晶硅块放入石英玻璃坩埚中,然后将坩埚放入电阻加热炉中进行熔炼。
在特定的温度和保温时间下,多晶硅逐渐熔化成硅熔体。
3. 准备拉晶装置:将石英棒固定在拉晶装置上,调整装置的温度和拉伸速度等参数,使其适合拉晶过程。
4. 开始拉晶:将熔融的硅熔体与石英棒接触,通过向上拉伸石英棒,使熔体附着在棒的一端,并由此逐渐形成硅晶体。
拉晶过程中需要控制温度、拉伸速度以及拉伸方向等参数,以保证拉晶产生单晶硅。
5. 晶柱切割:拉晶结束后,得到的硅晶体为一根长柱状,可以根据具体需要切割成不同规格和方向的晶圆。
切割过程需要使用专业的切割设备和切割工艺,以获得所需的单晶硅片。
三、直拉法制备单晶硅的工艺特点:1. 高纯度:直拉法制备的单晶硅可以达到非常高的纯度要求,这对于一些对杂质含量极为敏感的电子器件非常重要。
2. 大尺寸:直拉法制备的单晶硅柱可以达到较大的尺寸,使得每次拉晶得到的单晶硅片面积更大,提高了生产效率。
3. 较低的缺陷密度:直拉法制备的单晶硅的晶界和缺陷密度较低,有利于提高电子器件的性能。
4. 可重复性好:直拉法制备单晶硅的过程相对稳定,能够实现较好的生产批量一致性和可重复性。
四、直拉法制备单晶硅的应用:1. 半导体器件:直拉法制备的单晶硅片广泛应用于集成电路、晶体管、场效应晶体管等半导体器件的制造。
直拉法生产单晶硅
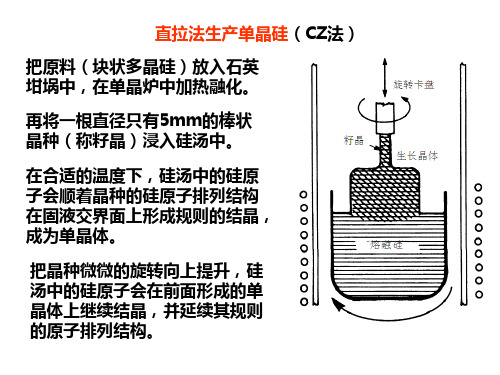
直拉法生产单晶硅
设备:直拉单晶炉
直拉单晶炉
直拉单晶炉
直拉单晶炉
直拉单晶炉主要由炉体、电气部分、加热系统、水冷 系统、真空系统和氩气装置六大部分组成。 一、炉体
炉体包括主架、主炉室、副炉室等部件 。
主架由底座、立柱组成,是炉子的支撑机构。
主炉室是炉体的心脏,有炉底 盘、下炉筒、上炉筒以及炉盖组 成,他们均为不锈钢焊接而成的 双层水冷结构,用于安装生长单 晶的热系统、石英坩埚及原料等。
直拉法的特点
设备和工艺简单,生产效率高,易于制造大直径 单晶硅。 易于控制单晶中的杂质浓度,可以制备低阻单晶。
生产温度高,硅料易被坩埚污染,使晶体的纯度 下降。
直拉法生产单晶硅
1、清 炉
冷却停加热6-8 小时后,打开炉 膛清理挥发物。
2、装料
3、抽空、通氩气 4、加热、熔硅
5、种晶 籽晶相当于在硅熔体中加入了一个定向晶核,使晶体按 晶核的晶向定向生长,制得所需晶向单晶。
先将籽晶降至液面数毫米处暂停片刻,使籽晶温度尽量 接近熔硅温度,然后将籽晶浸入熔硅,使头部熔解,接 着籽晶上升,生长单晶硅。
6、缩颈(引晶) 将籽晶快速提升,缩小结晶直径 目的:抑制位错从籽晶向晶体延伸
7、放肩 放慢生长速度,晶体硅直径增大
8、等径
等直径生长
9、收尾 单晶拉完时,由于热应力作用,尾部会产生大量位错,并 沿着单晶向上延伸,延伸的长度约等于一个直径。
三、加热系统
四、水冷系统
水冷系统包括总进水管道、分水器、各路冷却水管 道以及回水管道。由循环水系统来保证水循环正常运 行。 水冷系统的正常运行非常重要,必须随时保持各部 位冷却水路畅通,不得堵塞或停水,轻者会影响成晶 率,严重会烧坏炉体部件,造成巨大损失。
直拉单晶硅的制备掺杂

直拉单晶硅的制备硅、锗等单晶制备,就是要实现由多晶到单晶的转变,即原子由液相的随机排列直接转变为有序阵列;由不对称结构转变为对称结构。
但这种转变不是整体效应,而是通过固液界面的移动而逐渐完成的。
为实现上述转化过程,多晶硅就要经过由固态到熔融态,然后又由熔融态硅到固态晶体硅的转变。
这就是从熔体硅中生长单晶硅所遵循的途径。
从熔体中生长硅单晶的方法,目前应用最广泛的主要有两种:有坩埚直拉法和无坩埚悬浮区熔法。
在讨论这两种制备方法之前,还应讨论在制备单晶过程中必不可少的一些准备工序。
包括掺杂剂的选择、坩埚的选择、籽晶的制备等,分别介绍如下:一、掺杂在制备硅、锗单晶时,通常要加入一定数量杂质元素(即掺杂)。
加入的杂质元素决定了被掺杂半导体的导电类型、电阻率、少子寿命等电学性能。
掺杂元素的选择必须以掺杂过程方便为准,又能获得良好的电学性能和良好晶体完整性为前提。
1掺杂元素的选择(1)根据导电类型和电阻率的要求选择掺杂元素制备N型硅、锗单晶,必须选择Ⅴ族元素(如P、As、Sb、Bi);制备P型硅、锗单晶必须选择Ⅲ族元素(如B、Al、Ga、In、Ti)。
杂质元素在硅、锗晶体中含量的多少决定了硅、锗单晶的电阻率。
电阻率不仅与杂质浓度有关,而且与载流子的迁移率有关。
当杂质浓度较大时,杂质对载流子的散射作用,可使载流子的迁移率大大降低,从而影响材料的导电能力。
考虑到以上因素,从理论上计算了电阻率与杂质浓度的关系曲线,如图9-5所示。
在生产工艺上按电阻率的高低分档。
掺杂有三档:轻掺杂(适用于大功率整流级单晶)、中掺杂(适用于晶体管级单晶)、重掺杂(适用于外延衬底级单晶)。
(2)根据杂质元素在硅、锗中溶解度选择掺杂元素各种杂质元素在硅、锗中溶解度相差颇大。
例如,采用大溶解度的杂质,可以达到重掺杂的目的,又不会使杂质元素在晶体中析出影响晶体性能。
下表列出了常用掺杂元素在硅、锗单晶生长时掺入量的极限,超过了极限量,单晶生长不能进行。
直拉单晶硅 原辅材料的准备

目前,使用瓶装氩气拉晶的已经很少了,
因为瓶装氩气纯度低,产气少,要经常更 换空瓶,前去充灌时,钢瓶运输量很大, 而且要增加净化器等,成本较高。使用液 态氩供气尽管一次性投资大,但是积累成 本低,使用方便,1m3的液氩可气化为 780m3的氩气,1m3液态氩重约1.4t.
一台5m3的液氩储罐。上不同型号的蒸发器,
例如,重掺单晶的籽晶就不能回头再拉制轻掺单
晶了。重掺籽晶最好另加标识,严防误用。
籽晶在使用前,应按 照籽晶在夹头上的固 定方式在籽晶上切出
小口,或者开出小槽,
以使用钼丝捆绑,或
用销钉将籽晶固定在 股权头上,最后进行腐蚀、清洗、烘干,装入盒
内待用。
钼
钼是一种熔点很高(2600 ℃ ) 贵重金属,
钼丝在直拉炉上有两个用处,一是捆绑籽
晶;二是捆绑石墨毡,大多使用直径
0.3~0.5mm的钼丝;钼丝具有一定的强度和 韧性;那种脆性大、容易断裂的钼丝质量 差,不能使用。
钼丝的外表有一层黑灰色的附着物,可用 纱布蘸NaOH熔液擦去,用清水洗净,最后 用纯水冲净,自然晾干使用。至于钼棒可 以用做重锤上的籽晶夹头,钼片可以用做
检测陪片、切片料头废片、研磨废片、抛光废片
切磨加工过程中的废片须先用碱液清洗除去油污。
上述各种料按P型1~5、5~10、>10Ω· cm,N型>10
Ω· cm,>30Ω· cm进行分档,电阻率分档分选后,
再作腐蚀清洁处理。
电路废片
外延片一般衬底材料是在重掺Sb重掺As等。
这种废片不能用来拉单晶,其他电路废片
每小时产气可从几十立方米到百立方米,适合
大规模生产。高纯氩气纯度,一般为5个“9”,
毕业设计(论文)-直拉单晶硅的制备

毕业设计(论文)-直拉单晶硅的制备题目:直拉法制备单晶硅的研究摘要:单晶硅是目前最广泛应用于光电子器件和太阳能电池领域的材料之一。
本研究主要通过直拉法制备单晶硅,并对其制备过程中的影响因素进行研究和优化。
使用不同的原料、控制拉丝速度和控制拉丝温度等参数进行实验,并通过光学显微镜、扫描电子显微镜和X射线衍射仪等手段进行表征和分析。
关键词:单晶硅、直拉法、控制参数、光电子器件、太阳能电池1. 引言随着科技的快速发展,光电子器件和太阳能电池作为可再生能源领域的重要组成部分,对高纯度、大尺寸、无缺陷的单晶硅的需求越来越大。
直拉法是一种广泛应用于制备单晶硅的方法,通过控制拉丝过程中的参数,可以获得高质量的单晶硅。
2. 直拉法的工作原理直拉法制备单晶硅的过程主要包括原料准备、熔化、拉丝和固化等阶段。
在拉丝过程中,通过初始晶种的引入和拉丝速度的控制,可以实现单晶硅的制备。
3. 影响直拉法制备单晶硅的因素3.1 原料选择:原料的纯度和成分对单晶硅的质量有着重要影响,不同的原料对单晶硅的生长速率和晶体结构有不同的影响。
3.2 拉丝速度:拉丝速度对于单晶硅的形成和生长起到至关重要的作用,过快或过慢的拉丝速度都会影响单晶硅的质量。
3.3 拉丝温度:拉丝温度对单晶硅晶体的质量和纯度有很大影响,需在合适的温度范围内进行控制。
4. 实验设计和结果分析4.1 实验材料和设备的选择:选用高纯度硅片作为原料,使用恒温炉和拉丝机进行实验。
4.2 实验步骤:控制不同拉丝速度和拉丝温度下的直拉法实验。
4.3 结果分析:通过光学显微镜、扫描电子显微镜和X射线衍射仪等手段对实验结果进行表征和分析。
5. 结论本研究通过直拉法制备单晶硅的实验,得出了原料选择、拉丝速度和拉丝温度对制备单晶硅的影响,并优化了制备过程中的参数,从而获得了高质量的单晶硅。
直拉单晶硅工艺流程

直拉单晶硅工艺流程1. 原料准备直拉单晶硅工艺的第一步是原料准备。
通常使用的原料是高纯度的二氧化硅粉末。
这些二氧化硅粉末需要经过精细的加工和净化,以确保最终制备出的单晶硅质量优良。
2. 熔炼接下来是熔炼过程。
将经过净化的二氧化硅粉末与掺杂剂(通常是磷或硼)混合,然后放入石英坩埚中,在高温高压的环境下进行熔炼。
熔炼过程中,二氧化硅和掺杂剂会发生化学反应,形成多晶硅。
3. 晶棒拉制在熔炼完成后,需要进行晶棒拉制。
这一步是直拉单晶硅工艺的核心步骤。
首先,将熔融的多晶硅放入拉棒机中,然后慢慢地将晶棒拉出。
在拉制的过程中,需要控制温度和拉速,以确保晶棒的质量和直径的均匀性。
4. 晶棒切割拉制完成后,晶棒需要进行切割。
通常使用线锯或者线切割机对晶棒进行切割,将其切成薄片,即所谓的晶圆。
晶圆的直径和厚度可以根据具体的需要进行调整。
5. 晶圆抛光切割完成后,晶圆表面会有一定的粗糙度,需要进行抛光。
晶圆抛光是为了去除表面的缺陷和提高表面的光洁度,以便后续的加工和制备。
6. 接触式氧化晶圆抛光完成后,需要进行接触式氧化。
这一步是为了在晶圆表面形成一层氧化层,以改善晶圆的电学性能和机械性能。
7. 晶圆清洗最后,晶圆需要进行清洗。
清洗过程中,会使用一系列的溶剂和超声波设备,将晶圆表面的杂质和污垢清洗干净,以确保晶圆的纯净度和光洁度。
通过以上步骤,直拉单晶硅工艺就完成了。
最终得到的单晶硅晶圆可以用于制备太阳能电池、集成电路和光电器件等各种应用。
直拉单晶硅工艺流程虽然复杂,但可以制备出质量优良的单晶硅,为半导体产业的发展提供了重要的支持。
直拉法单晶硅的工艺流程
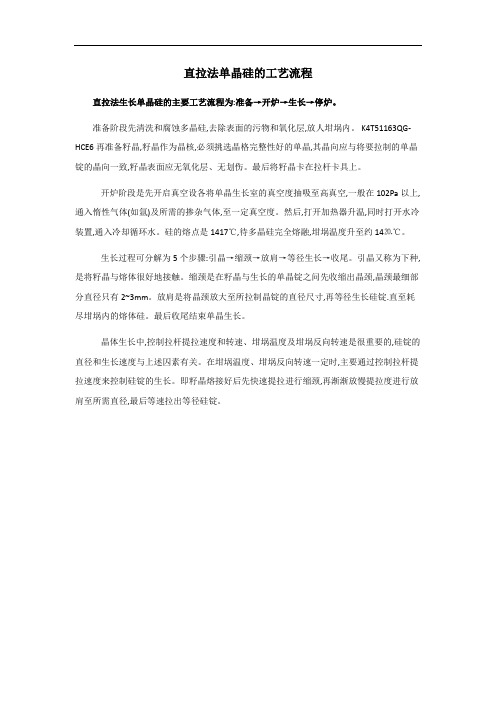
直拉法单晶硅的工艺流程
直拉法生长单晶硅的主要工艺流程为:准备→开炉→生长→停炉。
准备阶段先清洗和腐蚀多晶硅,去除表面的污物和氧化层,放人坩埚内。
K4T51163QG-HCE6再准备籽晶,籽晶作为晶核,必须挑选晶格完整性好的单晶,其晶向应与将要拉制的单晶锭的晶向一致,籽晶表面应无氧化层、无划伤。
最后将籽晶卡在拉杆卡具上。
开炉阶段是先开启真空设各将单晶生长室的真空度抽吸至高真空,一般在102Pa以上,通入惰性气体(如氩)及所需的掺杂气体,至一定真空度。
然后,打开加热器升温,同时打开水冷装置,通入冷却循环水。
硅的熔点是1417℃,待多晶硅完全熔融,坩埚温度升至约14⒛℃。
生长过程可分解为5个步骤:引晶→缩颈→放肩→等径生长→收尾。
引晶又称为下种,是将籽晶与熔体很好地接触。
缩颈是在籽晶与生长的单晶锭之问先收缩出晶颈,晶颈最细部分直径只有2~3mm。
放肩是将晶颈放大至所拉制晶锭的直径尺寸,再等径生长硅锭.直至耗尽坩埚内的熔体硅。
最后收尾结束单晶生长。
晶体生长中,控制拉杆提拉速度和转速、坩埚温度及坩埚反向转速是很重要的,硅锭的直径和生长速度与上述囚素有关。
在坩埚温度、坩埚反向转速一定时,主要通过控制拉杆提拉速度来控制硅锭的生长。
即籽晶熔接好后先快速提拉进行缩颈,再渐渐放慢提拉度进行放肩至所需直径,最后等速拉出等径硅锭。
直拉单晶硅的制备工艺

直拉单晶硅的制备工艺内容提要:单晶硅根据硅生长方向的不同分为区熔单晶硅,外延单晶硅和直拉单晶硅。
直拉单晶硅的制备工艺一般包括多晶硅的装料和熔化,种晶,缩颈,放肩,等径和收尾。
目前,单晶硅的直拉生长法已经是单晶硅制备的主要技术,也是太阳电池用单晶硅的主要制备方法。
关键词:直拉单晶硅,制备工艺一,直拉单晶硅的相关知识硅单晶是一种半导体材料。
直拉单晶硅工艺学是研究用直拉方法获得硅单晶的一门科学,它研究的主要内容:硅单晶生长的一般原理,直拉硅单晶生长工艺过程,改善直拉硅单晶性能的工艺方法。
直拉单晶硅工艺学象其他科学一样,随着社会的需要和生产的发展逐渐发展起来。
十九世纪,人们发现某些矿物,如硫化锌、氧化铜具有单向导电性能,并用它做成整流器件,显示出独特的优点,使半导体材料得到初步应用。
后来,人们经过深入研究,制造出多种半导体材料。
1918年,切克劳斯基(J Czochralski)发表了用直拉法从熔体中生长单晶的论文,为用直拉法生长半导体材料奠定了理论基础,从此,直拉法飞速发展,成为从熔体中获得单晶一种常用的重要方法。
目前一些重要的半导体材料,如硅单晶,锗单晶,红宝石等大部分是用直拉法生长的。
直拉锗单晶首先登上大规模工业生产的舞台,它工艺简单,生产效率高,成本低,发展迅速;但是,锗单晶有不可克服的缺点:热稳定性差,电学性能较低,原料来源少,应用和生产都受到一定限制。
六十年代,人们发展了半导体材料硅单晶,它一登上半导体材料舞台,就显示了独特优点:硬度大,电学热稳定性好,能在较高和较低温度下稳定工作,原料来源丰富。
地球上25.8%是硅,是地球上锗的四万倍,真是取之不尽,用之不竭。
因此,硅单晶制备工艺发展非常迅速,产量成倍增加,1964 年所有资本主义国家生产的单为晶硅50-60 吨,70年为300-350 吨,76年就达到1200吨。
其中60%以上是用直拉法生产的。
随着单晶硅生长技术的发展,单晶硅生长设备也相应发展起来,以直拉单晶硅为例,最初的直拉炉只能装百十克多晶硅,石英坩埚直径为40毫米到60毫米,拉制单晶长度只有几厘米,十几厘米,现在直拉单晶炉装多晶硅达40 斤,石英坩埚直径达350毫米,单晶直径可达150毫米,单晶长度近2米,单晶炉籽晶轴由硬构件发展成软构件,由手工操作发展成自动操作,并进一步发展成计算机操作,单晶炉几乎每三年更新一次。
九-单晶硅制备直拉法
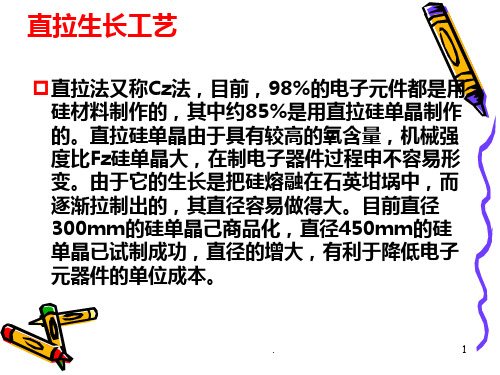
CZ各生产环节及注意事项
单晶基本作业流程
冷却
拆炉、清扫
安装热场
装料
化料
收尾
等径
转肩
放肩
引晶
稳定
直拉生长工艺
(1)原料的准备 还炉中取出的多晶硅,经破碎成块状,用HF和HNO3的混
合溶液进行腐蚀,再用纯净水进行清洗,直到中性,烘干 后备用。HF浓度40%,HNO3浓度为68%。一般HNO3: HF=5:1(体积比)。最后再作适当调整。反应式
腐蚀清洗前必须将附在硅原料上的石墨、石英渣及油污等清 除干净。
石英坩埚若为已清洁处理的免洗坩埚,则拆封后就可使用。 所用的籽晶也必须经过腐蚀清洗后才能使用。
直拉生长工艺
②装炉 选定与生产产品相同型号、晶向的籽晶,把它固定在籽晶
轴上。 将石英坩埚放置在石墨坩埚中。 将硅块料及所需掺入的杂质料放人石英坩埚中。 装炉时应注意:热场各部件要垂直、对中,从内到外、从
直拉生长工艺
⑤晶颈生长 晶颈直径的大小,要根据所生产的单晶的重量决定,
其经验公式为 d=1.608×10-3DL1/2
d为晶颈直径; D为晶体直径;L为晶体长度,cm。 目前,投料量60~90kg,晶颈直径为4~6mm。 晶颈较理想的形状是:表面平滑,从上至下直径微收
或等径,有利于位错的消除。
.
17
石墨坩埚
单个三瓣埚
三瓣埚组合后
单 个 三 瓣 埚和 埚底
单 个 三 瓣 埚和 埚底 及中 轴
加热器
➢ 左图为石墨加热器三维图。
➢ 上图为加热器脚的连接方式。加热器 脚和石墨螺丝、石墨电极间需要垫石墨纸, 目的是为了更加良性接触,防止打火。
重要的原、辅料
1、硅的基本性质
直拉单晶硅的制备流程

直拉单晶硅的制备流程英文回答:Direct-pulling Monocrystalline Silicon (Cz-Si) Fabrication Process.Introduction.Direct-pulling monocrystalline silicon (Cz-Si) is widely used in the production of silicon wafers for microelectronics devices. This process offers advantages such as high purity, low defect density, and well-controlled doping. The fabrication of Cz-Si involves several key steps:1. Crystal Growth.a. Raw Material Preparation: Polycrystalline silicon is purified through a chemical vapor deposition (CVD) process to remove impurities. This results in a high-purity siliconrod called a "seed."b. Crystal Pulling: The seed is mounted in a fused silica crucible containing molten silicon. The seed is slowly pulled upward by a mechanism while the melt is continuously replenished.c. Czochralski Process: This specific technique for crystal pulling uses a rotating seed-holder to control the crystal growth direction and prevent dislocations.2. Crystal Characterization.a. Crystal Orientation: The crystal's growth direction is determined by the seed orientation. Common orientations include <100>, <110>, and <111>.b. Impurity Characterization: The concentration of impurities is measured using techniques like glow discharge mass spectrometry (GDMS).c. Defect Characterization: Defects such asdislocations, stacking faults, and grain boundaries are analyzed through methods like X-ray topography and etch pit counting.3. Wafer Fabrication.a. Slicing: The grown crystal is sliced into thin wafers using a diamond saw. The thickness of the wafers depends on the device requirements.b. Polishing: The wafers undergo a series of mechanical and chemical polishing steps to achieve a mirror-like surface finish.c. Cleaning: The wafers are thoroughly cleaned to remove any remaining impurities or contaminants.4. Epitaxial Layer Deposition.a. Chemical Vapor Deposition (CVD): An epitaxial layer of silicon is deposited on the wafer surface through CVD. This layer is typically of higher purity and has tailoredelectrical properties.b. Oxidation: An oxide layer is grown on the epitaxial layer to enhance the device performance and prevent contamination.5. Doping.a. Diffusion: Impurities are introduced into the wafers through a diffusion process. These impurities change the electrical properties of the semiconductor, enabling the fabrication of transistors and other electronic devices.b. Ion Implantation: Precise doping profiles can be achieved by implanting specific ions into the wafers.Conclusions.The direct-pulling monocrystalline silicon (Cz-Si) fabrication process involves several meticulous steps to produce high-quality silicon wafers for microelectronics applications. By controlling the crystal growth,characterization, and wafer fabrication, this process ensures the production of wafers with the required purity, defect density, and electrical properties for advanced semiconductor devices.中文回答:直拉单晶硅(Cz-Si)的制备流程。
简述直拉法制备单晶硅棒的工艺流程
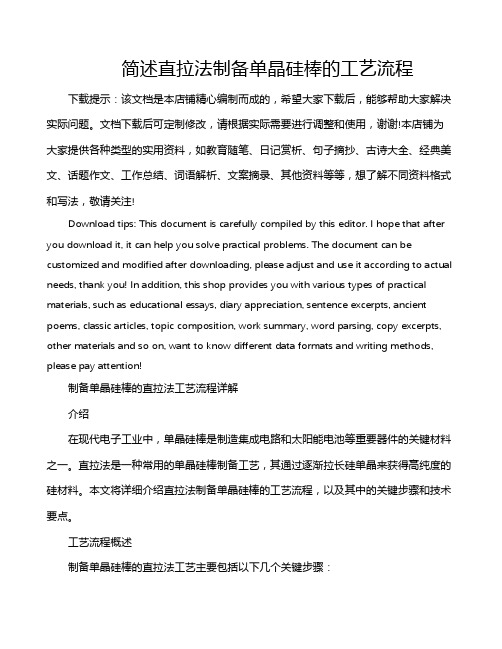
简述直拉法制备单晶硅棒的工艺流程下载提示:该文档是本店铺精心编制而成的,希望大家下载后,能够帮助大家解决实际问题。
文档下载后可定制修改,请根据实际需要进行调整和使用,谢谢!本店铺为大家提供各种类型的实用资料,如教育随笔、日记赏析、句子摘抄、古诗大全、经典美文、话题作文、工作总结、词语解析、文案摘录、其他资料等等,想了解不同资料格式和写法,敬请关注!Download tips: This document is carefully compiled by this editor. I hope that after you download it, it can help you solve practical problems. The document can be customized and modified after downloading, please adjust and use it according to actual needs, thank you! In addition, this shop provides you with various types of practical materials, such as educational essays, diary appreciation, sentence excerpts, ancient poems, classic articles, topic composition, work summary, word parsing, copy excerpts, other materials and so on, want to know different data formats and writing methods, please pay attention!制备单晶硅棒的直拉法工艺流程详解介绍在现代电子工业中,单晶硅棒是制造集成电路和太阳能电池等重要器件的关键材料之一。
直拉单晶硅工艺技术

直拉单晶硅工艺技术直拉单晶硅工艺技术是一种生产单晶硅材料的工艺方法,它能够高效地制备高纯度、高质量的单晶硅。
在电子、光伏等领域有着广泛的应用。
下面我将介绍一下直拉单晶硅工艺技术的基本原理和步骤。
直拉单晶硅工艺技术基本原理是利用熔融态下的硅液形成的“剪切层”和拉伸过程中形成的“湍流鞍点”来减小晶体发生成核的机会,实现快速生长大尺寸单晶硅。
直拉单晶硅工艺技术的步骤如下:1、硅原料准备:选择高纯度的硅原料,通常采用电石炉法或氯气法制备。
2、硅液制备:将硅原料放入特殊的熔化炉中,在高温下将硅原料熔化成液态硅。
3、净化处理:通过添加掺杂剂和进行化学处理等方式,对硅液进行净化,去除杂质和不纯物质。
4、晶体成核:将净化后的硅液脱氧,并添加少量的晶种,形成晶体的初步成核。
5、晶体生长:将晶种固定在拉伸机上,通过控制温度和拉拔速度,使晶体逐渐生长。
6、晶体拉伸:在晶体生长过程中,通过拉伸机的拉拔和旋转,将晶体朝着一个方向上不断拉长,直到达到目标长度。
7、光洁处理:将拉伸后的晶体进行光洁处理,使其表面变得光滑。
8、切割整理:将拉伸后的晶体切割成适当大小的小晶体,用于制造半导体晶体管等器件。
直拉单晶硅工艺技术的优点在于能够生长大尺寸的单晶硅,提高了生产效率和晶体质量。
同时,它还具有晶体控制性好、成本低等特点,为单晶硅领域的发展提供了重要的技术支持。
然而,直拉单晶硅工艺技术也存在一些问题。
首先,大尺寸单晶的生产周期较长,需要耗费大量的能源和物资。
其次,工艺要求严格,操作技术要求高,一旦出现操作失误,就会导致晶体质量下降。
总而言之,直拉单晶硅工艺技术是一种优质、高效的制备单晶硅材料的方法。
通过不断的技术创新和工艺改进,相信直拉单晶硅工艺技术能够继续优化,提高生产效率和质量,为电子、光伏等领域的应用提供更好的支持。
直拉单晶硅的八个过程
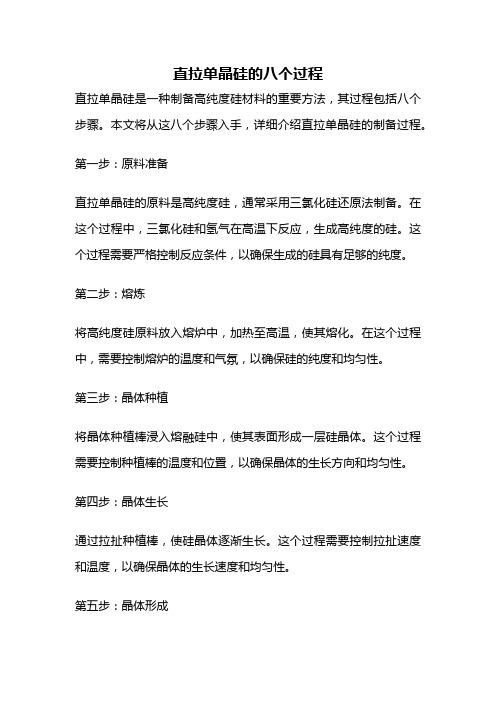
直拉单晶硅的八个过程直拉单晶硅是一种制备高纯度硅材料的重要方法,其过程包括八个步骤。
本文将从这八个步骤入手,详细介绍直拉单晶硅的制备过程。
第一步:原料准备直拉单晶硅的原料是高纯度硅,通常采用三氯化硅还原法制备。
在这个过程中,三氯化硅和氢气在高温下反应,生成高纯度的硅。
这个过程需要严格控制反应条件,以确保生成的硅具有足够的纯度。
第二步:熔炼将高纯度硅原料放入熔炉中,加热至高温,使其熔化。
在这个过程中,需要控制熔炉的温度和气氛,以确保硅的纯度和均匀性。
第三步:晶体种植将晶体种植棒浸入熔融硅中,使其表面形成一层硅晶体。
这个过程需要控制种植棒的温度和位置,以确保晶体的生长方向和均匀性。
第四步:晶体生长通过拉扯种植棒,使硅晶体逐渐生长。
这个过程需要控制拉扯速度和温度,以确保晶体的生长速度和均匀性。
第五步:晶体形成当晶体生长到一定长度时,将其从熔融硅中取出,形成一根硅晶棒。
这个过程需要控制取出的速度和位置,以确保晶体的形状和尺寸。
第六步:切割将硅晶棒切成一定长度的硅晶棒坯。
这个过程需要控制切割的位置和角度,以确保硅晶棒坯的尺寸和形状。
第七步:研磨将硅晶棒坯进行研磨,使其表面光滑。
这个过程需要控制研磨的压力和速度,以确保硅晶棒坯的表面质量。
第八步:抛光将硅晶棒坯进行抛光,使其表面更加光滑。
这个过程需要控制抛光的压力和速度,以确保硅晶棒的表面质量。
通过以上八个步骤,就可以制备出高纯度、高质量的直拉单晶硅。
这种材料在半导体、太阳能电池等领域有着广泛的应用。
12英寸半导体级直拉单晶硅的制备

12英寸半导体级直拉单晶硅的制备摘要:本文介绍了一种制备12英寸半导体级直拉单晶硅的方法,采用了Czochralski法生长单晶硅,在成分设计、生长条件和熔体净化等方面进行了优化。
通过精密测量和分析,获得了12英寸半导体级直拉单晶硅的物理和化学性质,并对其品质进行了评估。
结果表明,本方法可以制备出高质量、低成本的半导体级直拉单晶硅,可用于半导体工业的生产。
关键词:直拉单晶硅;Czochralski法;生长;半导体级;质量评估1. 引言单晶硅是制备半导体材料的重要原材料,在集成电路、太阳能电池等领域得到广泛应用。
直拉法是制备单晶硅的常见方法之一,可以获得高纯度、高结晶度的单晶硅。
本文介绍了一种制备12英寸半导体级直拉单晶硅的方法,并对其质量进行了评估。
2. 实验方法2.1 材料成分设计本实验采用Ta掺杂技术,控制晶体内杂质含量,提高单晶硅的纯度。
同时,在生长过程中加入氧气气氛,利用氧的还原性减少杂质的含量。
2.2 生长条件的优化在生长过程中,优化生长温度、生长速率、气氛控制等因素,获得良好的单晶硅晶体。
具体参数如下:生长温度:1450℃生长速率:10mm/h气氛:Ar气+2%O22.3 熔体净化通过预熔、净化、过滤等工艺处理,去除杂质,提高单晶硅的纯度。
3. 实验结果与分析3.1 物理性质经过精密测量,获得12英寸半导体级直拉单晶硅的导电率为10-3Ω·cm,晶格常数为5.4305×10-10m,折射率为3.429。
结果表明,本实验制备的单晶硅具有较好的物理性质,在生产中可用于制备高质量的半导体材料。
3.2 化学性质采用ICP-MS等化学分析方法,获得12英寸半导体级直拉单晶硅的杂质元素含量,其中杂质Fe、Ni、Cr等含量低于10-10wt%。
结果表明,本实验制备的单晶硅在化学性质上符合半导体工业的要求。
3.3 品质评估通过收集并分析半导体工业中的参考品质数据,与本实验制备的单晶硅进行对比评估。
- 1、下载文档前请自行甄别文档内容的完整性,平台不提供额外的编辑、内容补充、找答案等附加服务。
- 2、"仅部分预览"的文档,不可在线预览部分如存在完整性等问题,可反馈申请退款(可完整预览的文档不适用该条件!)。
- 3、如文档侵犯您的权益,请联系客服反馈,我们会尽快为您处理(人工客服工作时间:9:00-18:30)。
直拉单晶硅的制备硅、锗等单晶制备,就是要实现由多晶到单晶的转变,即原子由液相的随机排列直接转变为有序阵列;由不对称结构转变为对称结构。
但这种转变不是整体效应,而是通过固液界面的移动而逐渐完成的。
为实现上述转化过程,多晶硅就要经过由固态到熔融态,然后又由熔融态硅到固态晶体硅的转变。
这就是从熔体硅中生长单晶硅所遵循的途径。
从熔体中生长硅单晶的方法,目前应用最广泛的主要有两种:有坩埚直拉法和无坩埚悬浮区熔法。
在讨论这两种制备方法之前,还应讨论在制备单晶过程中必不可少的一些准备工序。
包括掺杂剂的选择、坩埚的选择、籽晶的制备等,分别介绍如下:一、掺杂在制备硅、锗单晶时,通常要加入一定数量杂质元素(即掺杂)。
加入的杂质元素决定了被掺杂半导体的导电类型、电阻率、少子寿命等电学性能。
掺杂元素的选择必须以掺杂过程方便为准,又能获得良好的电学性能和良好晶体完整性为前提。
1掺杂元素的选择(1)根据导电类型和电阻率的要求选择掺杂元素制备N型硅、锗单晶,必须选择Ⅴ族元素(如P、As、Sb、Bi);制备P型硅、锗单晶必须选择Ⅲ族元素(如B、Al、Ga、In、Ti)。
杂质元素在硅、锗晶体中含量的多少决定了硅、锗单晶的电阻率。
电阻率不仅与杂质浓度有关,而且与载流子的迁移率有关。
当杂质浓度较大时,杂质对载流子的散射作用,可使载流子的迁移率大大降低,从而影响材料的导电能力。
考虑到以上因素,从理论上计算了电阻率与杂质浓度的关系曲线,如图9-5所示。
在生产工艺上按电阻率的高低分档。
掺杂有三档:轻掺杂(适用于大功率整流级单晶)、中掺杂(适用于晶体管级单晶)、重掺杂(适用于外延衬底级单晶)。
(2)根据杂质元素在硅、锗中溶解度选择掺杂元素各种杂质元素在硅、锗中溶解度相差颇大。
例如,采用大溶解度的杂质,可以达到重掺杂的目的,又不会使杂质元素在晶体中析出影响晶体性能。
下表列出了常用掺杂元素在硅、锗单晶生长时掺入量的极限,超过了极限量,单晶生长不能进行。
(3)根据分凝系数选择掺杂元素前面已介绍了几种掺杂元素,在硅、锗熔体生长时的平衡分凝系数的值。
可见,分凝系数小的掺杂元素,在熔体生长晶体时很难从熔体进入晶体。
因此要使K0小的杂质进行重掺杂显然是不适宜的。
所以要根据分凝系数来选择掺杂元素是很重要的条件之一。
(4)根据杂质元素在硅、锗中扩散系数选择掺杂元素考虑到整个半导体器件的热稳定性和在半导体器件制造工艺,特别是高温工艺如扩散、外延等工艺中,常常要求硅、锗单晶中掺杂元素的扩散系数要小些好。
否则当高温扩散制作器件时,衬底的杂质也同时以反扩散方式进入外延层中,影响杂质的再分布,对器件电性能不利。
在硅中,属于快扩散杂质元素的有:H、Li、Na、Cu、Fe、K、Au、He、Ag、S;属于慢扩散杂质元素的有:Al、P、B、Ga、Ti、Sb、As、Bi等。
(5)根据杂质元素的蒸发常数选择掺杂元素由于单晶制备有时在真空条件下进行,故在晶体生长过程中气液相之间处于非平衡态,杂质的挥发变得更为容易。
杂质元素的挥发往往会造成熔体中杂质量的变化,这是掺杂过程中应加以考虑的因素。
在真空条件下杂质元素的挥发程度通常用蒸发数E表示。
因为在一定温度和真空条件下,单位时间内从熔体中蒸发出的杂质数量N与熔体表面积A、以及熔体中的杂质浓度C L成正比,当浓度较低时,上述参量间的关系可用下式表示:N=EAC L(9-10) 式中比例常数E称蒸发常数。
因此可知,E的数值即单位时间从单位表面积上蒸发出去的杂质数。
因此,E的数值大小可以表征杂质蒸发速率的快慢程度。
各种杂质元素在硅熔体中的蒸发常数E的数值由表8给出。
掺杂元素的选择除上述四方面的因素外,还要考虑掺杂元素原子半径的影响。
杂质元素的原子半径与硅、锗原子半径之差是影响晶体完整性的重要因素之一,应尽量选用与硅、锗原子半径相似的杂质元素作为掺杂剂。
二、掺杂方式按掺杂剂的形式可分为元素掺杂和合金掺杂。
(1)元素掺杂 即直接将纯杂质元素加入硅中。
它适于制备电阻率10-2~10-3Ω·cm 的重掺杂硅单晶。
(2)母合金掺杂 是将掺杂元素与硅先做成母合金(例如,硅锑合金、硅硼合金),根据母合金含的杂质量相应的加入母合金量。
(3)中子辐照掺杂(NTD ) 按上述两种掺杂方式掺杂,由于杂质分凝、蒸发、温度分布等因素的影响使得杂质均匀性很难作好,尤其是高阻材料更困难。
近年来发展了一种中子嬗变掺杂技术。
可大大提高硅单晶电阻率的均匀性。
中子嬗变掺杂的主要特征是:杂质不是从外部掺进原材料中去,而是被掺材料本身的一部分原子在辐照过程中直接转变而来。
对硅材料而言,中子嬗变掺杂技术的基本原理简述如下:自然硅中有三种稳定的同位素,即i 28S 、i 29S 、i 30S ,它们所占比例分别为92.28%、4.67%和3.05%。
这些同位素在Si 中呈均匀分布。
将未掺杂的硅单晶材料放入核反应堆中辐照。
i 30S 俘获热中子后嬗变成不稳定的同位素i 31S ,并放出了γ射线;i 31S 的半衰期为2.62小时,释放出β射线后变成稳定的磷(P 31)。
这样就相当于在硅中引进了均匀分布的施主杂质磷。
由于中子嬗变是在固相低温下进行的,而且中子在硅中射程为90~100cm ,所以它们的杂质可以参杂很均匀、很准确。
被辐照的单晶应放在反应堆均匀中子流的范围内,在辐照完成后,须存放一定时间,经测定放射性后才能投入安全使用。
辐射中,产生了大量的晶格缺陷,使得硅的电阻率高达105Ω·cm ,经过900℃、3小时退火,电阻率即可达稳定值。
三、掺杂的计算掺入杂质的量,一般应考虑以下几个因素:①原材料中的杂质含量;②杂质的分凝效应;③如果是在真空系统中拉制单晶,还应考虑杂质在真空中的蒸发效应;④另外还应考虑到在生长过程中坩埚或系统内杂质的污染。
考虑了以上几个影响因素后才能正确计算该加入单晶内的杂质量。
然而,以上这些影响因素的大小是随材料的生长工艺而变动的,必须针对具体问题具体分析。
下面对两种掺杂形式分别计算如下:(1)掺杂杂质元素重量的计算 在只有分凝效应影响时,对于直拉硅或锗单晶掺杂量的计算。
因直拉晶体生长过程实际上是一个正常凝固过程,如果原材料较纯,则材料的电阻率ρ与杂质浓度C S 有如下关系μρ⋅=q 1S C (9-11) 式中μ为电子迁移率(对n 型半导体)或空穴迁移率(对p 型半导体)q 为电子电荷。
根据正常凝固的杂质分布表达式可知,对于拉出单晶的某一位置g 的电阻率和熔体里的杂质浓度C 0有如下关系:)1(0)1(/1k g C k q ---⋅⋅⋅=μρ (9-12)(9-12)式表示电阻率沿晶锭长度方向之变化。
假如我们所用的原材料是高纯硅或高纯锗,高纯原材料本身的杂质相对于掺入的杂质量可以忽略不计;又假定杂质并不蒸发,在生长过程中也没有污染,这时(9-12)式中的C 0就是(9-13) 式中d 为硅或锗的密度,N 0为阿伏伽德罗常数,A 为杂质元素的原子量,A/N 0为每个杂质原子的质在计算时,需要有确定的g 值(即相对位置),也就是说要知道所要求的电阻率的位置。
假定我们需要生长某一电阻率的单晶,可以取χ=1/2来计算;如果我们要获得某一电阻率范围例如1~3Ω·cm 的单晶,则可以取g=0(头部)处的ρ=3Ω·cm 来计算。
下面举两个例子来具体说明。
例题Ⅰ 要求拉出在g=1/2处,ρ=1Ω·cm 的锗单晶50g ,所用原材料是区熔提纯的高纯锗,问需要掺入杂质砷的质量为多少?(已知砷的分凝系数K=0.02,砷原子量为74,μ用电子迁移率为4000cm ²/v ·s ,N 0=6.03×1023/mol )。
解:用(9-12)和(9-13)式分别可求出C 0和m 为C 0≈5×1016cm -3m ≈0.057mg例题Ⅱ 若要求χ=1/2处,ρ=1Ω·cm 的n 型硅单晶50g ,问需要掺入砷杂质多少?解:经计算得到C 0≈4×1015cm -3m ≈0.01mg由该例可看出,掺入的杂质量是很少的,如此小的量在称重方面不易准确,会产生很大误差。
因此除拉制重掺杂单晶外,一般将掺的杂质与原材料先做合金,再以合金的方式掺入,这样就可更准确的控制掺杂量。
常用的母合金P-Si 、B-Si 、Ge-Sb 、Ge-Ga 等合金。
(2)采用中间合金(母合金)掺杂时对母合金重量的计算①拉制P 型硅或锗单晶时掺入母合金质量的计算:若掺入方式是掺入中间合金,比如硅硼合金的电阻率为ρ1,对应的杂质浓度C H ,若在硅中投入中间合金重为W 1,因中间合金中的杂质含量相对硅的比例来看一般是很小的。
可以把合金的密度看作和硅的密度相同,故可以硅的密度d ds 代替。
则投入的合金体积为W 1/ d ds ,那么投入多晶硅熔体中的中间合金的杂质原子总数为(W 1/ d 合)·C H 。
设投入多晶熔硅原材料的质量为M ,那么熔硅体积为M/ d ds ,(忽略合金小体积),则掺入的杂质在熔体中的浓度C S 导出如下根据杂质在合金中的总数与在硅熔体中总数不变得S S C W M C D W ds11d +=合 因为d 合= d ds ,M+W ≈M (因W 1很小可略)所以 H K H S C M K M C C W )()(---==11g 1q 1μ (9-14) 在实际拉高阻单晶过程中,拉制出的单晶,其单晶头部的杂质浓度C S (头)为:C S (头)=KC L =K MW 1C H ±C f (9-15) 式中第一项为投入的杂质在单晶头部凝固出来的杂质浓度,第二项C f 为多晶硅料(原材料)中和坩埚污染引入的杂质对单晶头部杂质的净贡献。
在拉制P 型单晶时,若多晶硅料含有杂质也是P 型的,则它起着补充P 型杂质含量的作用。
此时(9-15)式的C f 应取正号;如果多晶硅中含有N 型杂质,则它对投入的P 型杂质起补偿作用,则C f 应取负号。
因此,要拉制电阻率上限ρ上(对应C S (头))的P 型单晶,应投入含杂质浓度为C H 中间合金的重量对P 型多晶硅为H S C K C C M W ·])([f 1-头 (9-16a) 对N 型多晶硅为HS C K C C M W ·])([f 1+头 (9-16b ) 我们应用上式可计算投入中间合金的重量W 1。
②拉制N 型硅单晶时掺入母合金重量的计算:N 型硅单晶通常是在真空条件下进行的,又因从中间合金的投入到放肩生长完成,需要一段时间,在这段时间内熔硅中掺入的杂质元素必会有部分挥发,因此还应考虑蒸发作用的影响。
显然杂质蒸发量与时间、熔体表面积、熔体中杂质浓度成正比。