金属脱脂剂的制备方法的制作方法
金属管材脱脂加工
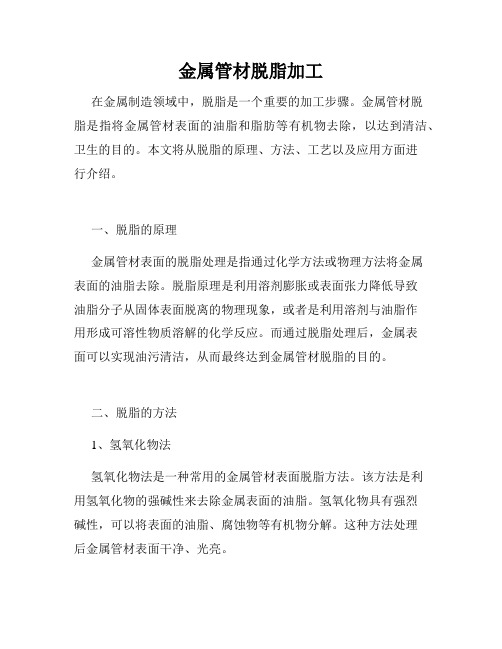
金属管材脱脂加工在金属制造领域中,脱脂是一个重要的加工步骤。
金属管材脱脂是指将金属管材表面的油脂和脂肪等有机物去除,以达到清洁、卫生的目的。
本文将从脱脂的原理、方法、工艺以及应用方面进行介绍。
一、脱脂的原理金属管材表面的脱脂处理是指通过化学方法或物理方法将金属表面的油脂去除。
脱脂原理是利用溶剂膨胀或表面张力降低导致油脂分子从固体表面脱离的物理现象,或者是利用溶剂与油脂作用形成可溶性物质溶解的化学反应。
而通过脱脂处理后,金属表面可以实现油污清洁,从而最终达到金属管材脱脂的目的。
二、脱脂的方法1、氢氧化物法氢氧化物法是一种常用的金属管材表面脱脂方法。
该方法是利用氢氧化物的强碱性来去除金属表面的油脂。
氢氧化物具有强烈碱性,可以将表面的油脂、腐蚀物等有机物分解。
这种方法处理后金属管材表面干净、光亮。
2、碱性物理清洗法碱性物理清洗法是一种利用强碱性或较强碱性的清洗剂清洗金属表面油污的方法。
这种方法的优点是易于控制、适用面广,但是对人体有一定的危害性。
3、有机溶剂法有机溶剂法是涂装前常用的金属管材表面脱脂方法。
常用的有机溶剂有三氯乙烷、四氯化碳、去污液等。
该方法适用于油污较重的金属管材。
这种方法处理后,表面油污极少,但有机溶剂会对环境造成严重的污染。
三、脱脂的工艺1、清洗界面的选择脱脂前必须将材料的表面清洗干净,清洗液中最好添加适当的表面活性剂或抗水硬性剂。
另外还需要根据材料的特性来选择清洗界面,比如表面有流组织的材料,清洗界面最好选择流组织的方向,这样可以保证清洗效果的一致性。
2、去除材料表面的油脂在进行金属管材的脱脂处理时,要先将油脂和一些脂肪物质识别出来,然后进行去除。
对于一些难以去除的油脂,可以采取加热或者加强化学药剂的方法去除。
3、优化脱脂工艺在进行金属管材脱脂处理时,可以通过控制清洗液的配制和控制温度、时间等条件来优化脱脂工艺。
通过适当的优化工艺,可以提高脱脂效率、减少清洗液的消耗,并且可以减少一些对环境的污染。
铝材脱脂工艺及酸性脱脂剂的研发
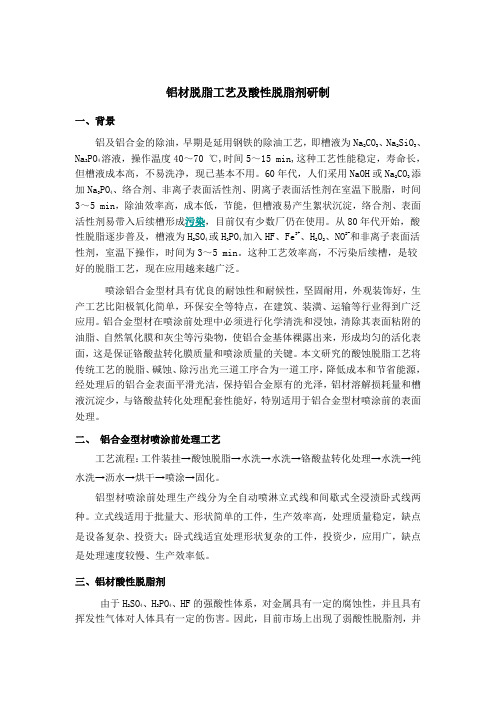
铝材脱脂工艺及酸性脱脂剂研制一、背景铝及铝合金的除油,早期是延用钢铁的除油工艺,即槽液为Na2CO3、Na2SiO3、Na3PO4溶液,操作温度40~70 ℃,时间5~15 min,这种工艺性能稳定,寿命长,但槽液成本高,不易洗净,现已基本不用。
60年代,人们采用NaOH或Na2CO3添加Na3PO4、络合剂、非离子表面活性剂、阴离子表面活性剂在室温下脱脂,时间3~5 min,除油效率高,成本低,节能,但槽液易产生絮状沉淀,络合剂、表面活性剂易带入后续槽形成污染,目前仅有少数厂仍在使用。
从80年代开始,酸性脱脂逐步普及,槽液为H2SO4或H3PO4加入HF、Fe3+、H2O2、NO2-和非离子表面活性剂,室温下操作,时间为3~5 min。
这种工艺效率高,不污染后续槽,是较好的脱脂工艺,现在应用越来越广泛。
喷涂铝合金型材具有优良的耐蚀性和耐候性,坚固耐用,外观装饰好,生产工艺比阳极氧化简单,环保安全等特点,在建筑、装潢、运输等行业得到广泛应用。
铝合金型材在喷涂前处理中必须进行化学清洗和浸蚀,清除其表面粘附的油脂、自然氧化膜和灰尘等污染物,使铝合金基体裸露出来,形成均匀的活化表面,这是保证铬酸盐转化膜质量和喷涂质量的关键。
本文研究的酸蚀脱脂工艺将传统工艺的脱脂、碱蚀、除污出光三道工序合为一道工序,降低成本和节省能源,经处理后的铝合金表面平滑光洁,保持铝合金原有的光泽,铝材溶解损耗量和槽液沉淀少,与铬酸盐转化处理配套性能好,特别适用于铝合金型材喷涂前的表面处理。
二、铝合金型材喷涂前处理工艺工艺流程:工件装挂→酸蚀脱脂→水洗→水洗→铬酸盐转化处理→水洗→纯水洗→沥水→烘干→喷涂→固化。
铝型材喷涂前处理生产线分为全自动喷淋立式线和间歇式全浸渍卧式线两种。
立式线适用于批量大、形状简单的工件,生产效率高,处理质量稳定,缺点是设备复杂、投资大;卧式线适宜处理形状复杂的工件,投资少,应用广,缺点是处理速度较慢、生产效率低。
金属脱脂剂配方(网络资料)
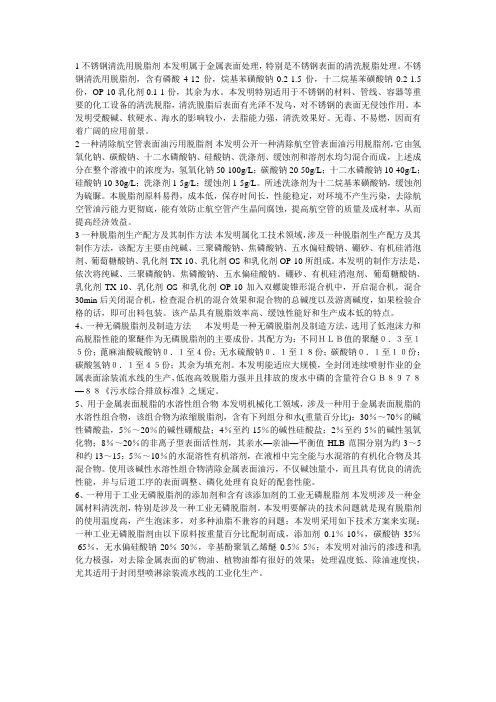
1不锈钢清洗用脱脂剂本发明属于金属表面处理,特别是不锈钢表面的清洗脱脂处理。
不锈钢清洗用脱脂剂,含有磷酸4-12份,烷基苯磺酸钠0.2-1.5份,十二烷基苯磺酸钠0.2-1.5份,OP-10乳化剂0.1-1份,其余为水。
本发明特别适用于不锈钢的材料、管线、容器等重要的化工设备的清洗脱脂,清洗脱脂后表面有光泽不发乌,对不锈钢的表面无侵蚀作用。
本发明受酸碱、软硬水、海水的影响较小,去脂能力强,清洗效果好。
无毒、不易燃,因而有着广阔的应用前景。
2一种清除航空管表面油污用脱脂剂本发明公开一种清除航空管表面油污用脱脂剂,它由氢氧化钠、碳酸钠、十二水磷酸钠、硅酸钠、洗涤剂、缓蚀剂和溶剂水均匀混合而成,上述成分在整个溶液中的浓度为,氢氧化钠50-100g/L;碳酸钠20-50g/L;十二水磷酸钠10-40g/L;硅酸钠10-30g/L;洗涤剂1-5g/L;缓蚀剂1-5g/L。
所述洗涤剂为十二烷基苯磺酸钠,缓蚀剂为硫脲。
本脱脂剂原料易得,成本低,保存时间长,性能稳定,对环境不产生污染,去除航空管油污能力更彻底,能有效防止航空管产生晶间腐蚀,提高航空管的质量及成材率,从而提高经济效益。
3一种脱脂剂生产配方及其制作方法本发明属化工技术领域,涉及一种脱脂剂生产配方及其制作方法,该配方主要由纯碱、三聚磷酸钠、焦磷酸钠、五水偏硅酸钠、硼砂、有机硅消泡剂、葡萄糖酸钠、乳化剂TX-10、乳化剂OS和乳化剂OP-10所组成。
本发明的制作方法是,依次将纯碱、三聚磷酸钠、焦磷酸钠、五水偏硅酸钠、硼砂、有机硅消泡剂、葡萄糖酸钠、乳化剂TX-10、乳化剂OS和乳化剂OP-10加入双螺旋锥形混合机中,开启混合机,混合30min后关闭混合机,检查混合机的混合效果和混合物的总碱度以及游离碱度,如果检验合格的话,即可出料包装。
该产品具有脱脂效率高、缓蚀性能好和生产成本低的特点。
4、一种无磷脱脂剂及制造方法本发明是一种无磷脱脂剂及制造方法,选用了低泡沫力和高脱脂性能的聚醚作为无磷脱脂剂的主要成份。
不锈钢管除油脂清洗剂配制方法及应用

不锈钢管除油脂清洗剂配制方法及应用不锈钢管是一种用途广泛的金属管材,广泛应用于石油、化工、医药、食品等行业。
由于长时间使用或者生产过程中,不锈钢管会积聚一些油脂和污垢,影响其工作效果和使用寿命,因此需要定期进行清洗。
下面将介绍一种不锈钢管除油脂的清洗剂配制方法及应用。
配方和材料:1.生石灰:2千克2.碱矾:1千克3.苏打粉:0.5千克4.脱脂粉:0.5千克5.合成洗涤剂:0.3千克6.去垢剂:0.3千克7.纯净水:适量步骤:1.将生石灰、碱矾、苏打粉、脱脂粉、合成洗涤剂和去垢剂按照配方比例加入一个大容器中,搅拌均匀。
2.慢慢加入适量的纯净水,同时搅拌,直至形成均匀的清洗液体。
3.将配制好的清洗剂倒入一个储存容器中,密封保存。
应用方法:1.首先将不锈钢管表面的大颗粒污垢用水冲洗干净。
2.将配制好的清洗剂倒入一个大容器中,加入适量的纯净水,混合均匀。
3.将不锈钢管放入清洗液中,确保管子完全浸没。
4.静置清洗剂,使其充分渗透和溶解油脂,根据油脂的程度不同,清洗时间可长达数小时。
5.使用软毛刷或者海绵刷,轻轻擦拭不锈钢管表面,去除油脂和污垢。
6.清洗完毕后,用水彻底冲洗不锈钢管,确保清洗剂和残留污垢完全清除。
7.完全晾干或用干净的纱布擦拭干燥管子。
不锈钢管除油脂清洗剂的应用能够有效去除不锈钢管表面的油脂和污垢,保持其光洁度和良好的工作状态。
清洗剂中的生石灰和碱矾能起到去油脂、吸附异味和抗菌的作用,苏打粉和脱脂粉则能加强清洗效果。
合成洗涤剂和去垢剂能增加清洗剂的浸透性和去污能力。
清洗剂的配方经过合理的比例调配,确保清洗能力强同时对不锈钢管材料没有腐蚀性。
脱脂剂生产工艺

脱脂剂生产工艺脱脂剂是一种用于去除油脂和污渍的化学制剂。
它广泛应用于工业领域,如汽车修理、金属加工和电子生产等。
本文将介绍脱脂剂的生产工艺。
脱脂剂的生产工艺涉及多个步骤,主要包括原料准备、混合、反应、过滤和包装等。
首先是原料准备。
脱脂剂的主要原料是有机溶剂、表面活性剂和功能添加剂。
有机溶剂是脱脂剂的溶剂基础,常用的有丙酮、甲醇和醚类溶剂等。
表面活性剂是使脱脂剂能有效地去除油脂和污渍的关键成分,常用的有吉酰胺类、醇类和酸类表面活性剂等。
功能添加剂根据不同的要求添加,例如防锈剂、防腐剂和增稠剂等。
接下来是混合步骤。
将准备好的原料按照一定比例加入混合槽中,并通过搅拌器进行充分混合。
混合的目的是使各种成分充分均匀地分布,确保脱脂剂的质量稳定。
然后是反应步骤。
将混合好的原料送入反应釜中,加热并进行化学反应。
反应的时间和温度根据不同的配方和脱脂剂种类而定。
化学反应是使各种成分发生相应作用,生成具有脱脂效果的物质。
接下来是过滤步骤。
将反应后的物料通过过滤器进行过滤,去除其中的杂质和固体颗粒,并保持脱脂剂的清洁和透明度。
最后是包装步骤。
将经过过滤的脱脂剂装入包装容器中,如瓶装、桶装或罐装等,并进行封口。
包装的目的是保护脱脂剂不受外部环境的污染,并方便使用和运输。
除了以上基本的生产步骤,脱脂剂的生产过程中还需要注意安全和环保。
在操作过程中,要严格遵守安全操作规程,确保操作人员的人身和财产安全。
另外,要注意防止溶剂挥发和泄漏,以保护环境不受污染。
综上所述,脱脂剂的生产工艺包括原料准备、混合、反应、过滤和包装等步骤。
通过合理的工艺流程和严格的控制条件,可以生产出质量稳定、安全环保的脱脂剂产品。
这些脱脂剂对于实现工业生产中的油脂和污渍的有效去除起到了重要作用。
金属脱脂剂配方成分分析,技术研发及案例分享

金属脱脂剂配方成分分析,技术研发及案例分享导读:本文详细介绍金属脱脂剂的研究背景,理论基础,参考配方等,本文中的配方数据经过修改,如需更详细资料,可咨询我们的技术工程师。
金属脱脂剂广泛使用于各种金属表面处理,禾川化学专业从事金属脱脂剂成分分析、配方还原、研发外包服务,为脱脂剂相关企业提供一整套配方技术解决方案。
一、背景金属脱脂除油是机械涂装行业前处理工艺中最关键的工序之一,金属表面脱脂的程度将直接影响磷化序和涂装质量。
它利用高效液体脱脂剂对油脂和污物的皂化、润湿、乳化、渗透、卷离、分散和增溶等作用把工件表面的各种油脂、灰尘泥沙、金属粉末手汗及其工件在加工过程中所粘附的油性脏物高效的去除脱离彻底。
金属材料的脱脂可分为碱性水溶液脱脂、有机溶剂脱脂及酸性脱脂。
酸性脱脂剂因除油水平有限,对金属有一定腐蚀问题,应用领域较窄。
溶剂型脱脂剂应用非常广泛,但是溶剂型脱脂剂要么是ODS溶剂对臭氧层有破坏作用,要么有毒有害对人体有损伤,要么易燃易爆对生产环境有威胁,只有碱性水基脱脂剂无毒无味、不燃不爆,对清洗部件无损伤,清洗废液可以生化处理,应用非常广泛,是国际金属脱脂技术的发展总趋势,但是大部分碱性脱脂剂高磷、高氮、不易生物降解,易对水系造成污染,是传统的重污染行业之一。
随着环保要求的提高,目前比较流行研究应用生物可降解表面活性剂,对于活性剂,清洗剂要求无磷、无硅和低COD/BOD排放。
虽然此方面的研究工作已开展30多年,但是目前还没有一种无磷助剂能够同时保证去污能力、对人体和环境无危害和潜在危害、成本较低这3项要求。
现在已研究出无磷脱脂剂,但成本高,应用还有一定的阻力。
禾川化学技术团队具有丰富的分析研发经验,经过多年的技术积累,可以运用尖端的科学仪器、完善的标准图谱库、强大原材料库,彻底解决众多化工企业生产研发过程中遇到的难题,利用其八大服务优势,最终实现企业产品性能改进及新产品研发。
样品分析检测流程:样品确认—物理表征前处理—大型仪器分析—工程师解谱—分析结果验证—后续技术服务。
MIM脱脂工艺流程
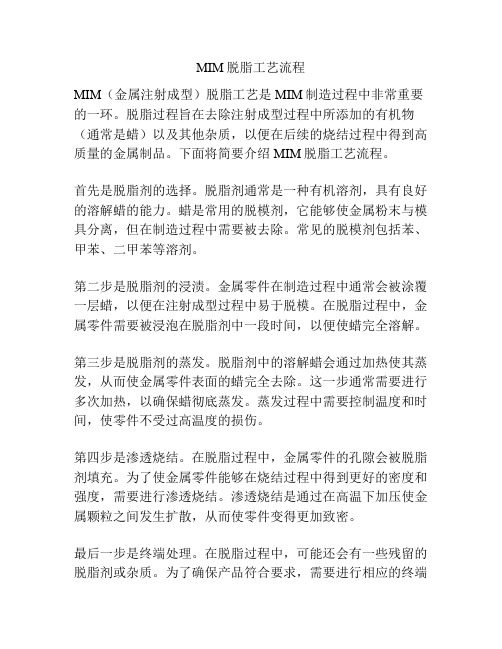
MIM脱脂工艺流程MIM(金属注射成型)脱脂工艺是MIM制造过程中非常重要的一环。
脱脂过程旨在去除注射成型过程中所添加的有机物(通常是蜡)以及其他杂质,以便在后续的烧结过程中得到高质量的金属制品。
下面将简要介绍MIM脱脂工艺流程。
首先是脱脂剂的选择。
脱脂剂通常是一种有机溶剂,具有良好的溶解蜡的能力。
蜡是常用的脱模剂,它能够使金属粉末与模具分离,但在制造过程中需要被去除。
常见的脱模剂包括苯、甲苯、二甲苯等溶剂。
第二步是脱脂剂的浸渍。
金属零件在制造过程中通常会被涂覆一层蜡,以便在注射成型过程中易于脱模。
在脱脂过程中,金属零件需要被浸泡在脱脂剂中一段时间,以便使蜡完全溶解。
第三步是脱脂剂的蒸发。
脱脂剂中的溶解蜡会通过加热使其蒸发,从而使金属零件表面的蜡完全去除。
这一步通常需要进行多次加热,以确保蜡彻底蒸发。
蒸发过程中需要控制温度和时间,使零件不受过高温度的损伤。
第四步是渗透烧结。
在脱脂过程中,金属零件的孔隙会被脱脂剂填充。
为了使金属零件能够在烧结过程中得到更好的密度和强度,需要进行渗透烧结。
渗透烧结是通过在高温下加压使金属颗粒之间发生扩散,从而使零件变得更加致密。
最后一步是终端处理。
在脱脂过程中,可能还会有一些残留的脱脂剂或杂质。
为了确保产品符合要求,需要进行相应的终端处理。
常见的终端处理方法包括超声波清洗、热处理等。
总而言之,MIM脱脂工艺流程是MIM制造过程中不可或缺的一部分。
通过选取适当的脱脂剂,进行浸渍、蒸发、渗透烧结和终端处理等步骤,可以得到高质量的MIM制品。
脱脂过程的良好控制对于最终产品的质量至关重要。
铝脱脂剂配方
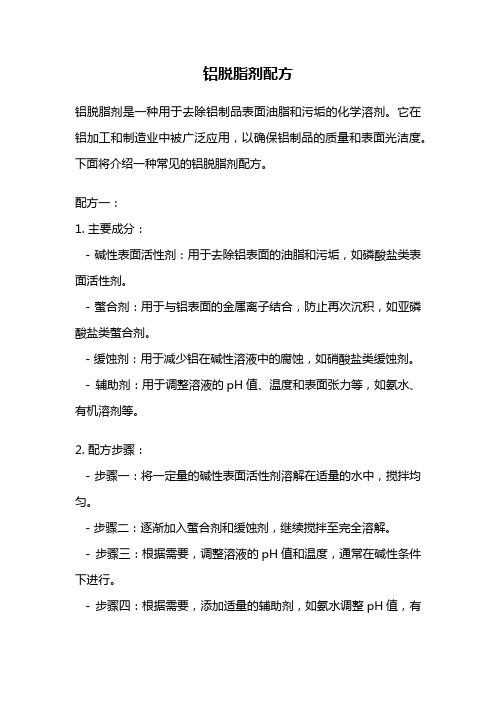
铝脱脂剂配方铝脱脂剂是一种用于去除铝制品表面油脂和污垢的化学溶剂。
它在铝加工和制造业中被广泛应用,以确保铝制品的质量和表面光洁度。
下面将介绍一种常见的铝脱脂剂配方。
配方一:1. 主要成分:- 碱性表面活性剂:用于去除铝表面的油脂和污垢,如磷酸盐类表面活性剂。
- 螯合剂:用于与铝表面的金属离子结合,防止再次沉积,如亚磷酸盐类螯合剂。
- 缓蚀剂:用于减少铝在碱性溶液中的腐蚀,如硝酸盐类缓蚀剂。
- 辅助剂:用于调整溶液的pH值、温度和表面张力等,如氨水、有机溶剂等。
2. 配方步骤:- 步骤一:将一定量的碱性表面活性剂溶解在适量的水中,搅拌均匀。
- 步骤二:逐渐加入螯合剂和缓蚀剂,继续搅拌至完全溶解。
- 步骤三:根据需要,调整溶液的pH值和温度,通常在碱性条件下进行。
- 步骤四:根据需要,添加适量的辅助剂,如氨水调整pH值,有机溶剂调整温度等。
- 步骤五:搅拌至溶液均匀,即可用于铝脱脂处理。
3. 注意事项:- 严格按照配方比例进行配制,避免成分超量或不足。
- 在配制的过程中,注意安全操作,避免溶剂的接触和吸入。
- 配置好的铝脱脂剂应储存在防腐蚀容器中,避免与空气和水分接触。
- 使用时,应根据具体情况确定脱脂剂的浸泡时间和温度,避免过长或过短的处理时间。
- 处理完铝制品后,应及时清洗和中和残留的脱脂剂,以免对环境和下一步工序造成影响。
铝脱脂剂的配方可以根据具体的需求和工艺要求进行调整,适当调整各种成分的比例和添加辅助剂,可以改善脱脂效果和处理速度。
同时,配方的参数也需要根据不同铝制品的特性和表面状态进行调整,以达到最佳的脱脂效果。
铝脱脂剂是铝加工和制造业中不可或缺的化学品。
正确配制和使用铝脱脂剂可以有效去除铝表面的油脂和污垢,提高铝制品的质量和表面光洁度。
但在使用过程中,也要注意安全操作和环境保护,避免对人体和环境造成不良影响。
- 1、下载文档前请自行甄别文档内容的完整性,平台不提供额外的编辑、内容补充、找答案等附加服务。
- 2、"仅部分预览"的文档,不可在线预览部分如存在完整性等问题,可反馈申请退款(可完整预览的文档不适用该条件!)。
- 3、如文档侵犯您的权益,请联系客服反馈,我们会尽快为您处理(人工客服工作时间:9:00-18:30)。
本技术公开了一种金属脱脂剂的制备方法,属于金属表面化学处理剂技术领域。
按重量份数计,依次称取20~35份基液,10~15份混合剂,8~10份改性活性炭,3~5份膨润土,3~5份乳化剂,3~5份柠檬酸,2~4份硅酸钠和4~8份混合表面活性剂,将基液与改性活性炭混合于混料机中,并依次向混料机中加入乳化剂,混合剂,膨润土,柠檬酸,硅酸钠和混合表面活性剂,于温度为35~45℃,转速为280~380r/min的条件下搅拌混合45~65min后,得金属脱脂剂。
本技术技术方案制备的金属脱脂剂具有优异的脱脂性能及稳定性的特点。
技术要求1.一种金属脱脂剂的制备方法,其特征在于具体制备步骤为:(1)将活性炭与无水乙醇按质量比1:5~1:8混合,并加入活性炭质量0.4~0.7倍的氧化钠粉末,搅拌混合后,超声振荡,过滤,得预处理活性炭;(2)将预处理活性炭与石蜡按质量比1:4~1:8混合,冷冻粉碎,过筛,得改性活性炭;(3)将碳酸氢钠与水按质量比2:5~2:7混合,得基础液;(4)将海泡石与无水乙醇按质量比1:5~1:8混合,并加入海泡石质量1~2倍的异氰酸酯,搅拌混合后,过滤,得预处理海泡石;(5)将(N-脒基)十二烷基丙烯酰胺与聚乙二醇衍生物按质量比2:1~4:1混合,并加入聚乙二醇衍生物质量0.2~0.4倍的对二氯苯和聚乙二醇衍生物质量0.12~0.18倍的二茂铁,搅拌混合,得处理剂;(6)将预处理海泡石与处理剂按质量比1:3~1:5混合,并加入预处理海泡石质量1~2倍的石蜡,搅拌混合后,冷冻粉碎,得混合剂;(7)按重量份数计,依次称取20~35份基液,10~15份混合剂,8~10份改性活性炭,3~5份膨润土,3~5份乳化剂,3~5份柠檬酸,2~4份硅酸钠和4~8份混合表面活性剂,将基液与改性活性炭混合,并依次加入乳化剂,混合剂,膨润土,柠檬酸,硅酸钠和混合表面活性剂,搅拌混合后,得金属脱脂剂。
2.根据权利要求1所述的一种金属脱脂剂的制备方法,其特征在于:所述石蜡为碳原子数在16~26之间的石蜡混合物。
3.根据权利要求1所述的一种金属脱脂剂的制备方法,其特征在于:步骤(5)所述聚乙二醇衍生物为聚乙二醇-对甲苯磺酸酯或聚乙二醇水杨酸酯中任意一种。
4.根据权利要求1所述的一种金属脱脂剂的制备方法,其特征在于:步骤(7)所述乳化剂为壬基酚聚氧乙烯醚,辛基酚聚氧乙烯醚或月桂纯聚氧乙烯醚中任意一种。
5.根据权利要求1所述的一种金属脱脂剂的制备方法,其特征在于:步骤(7)所述混合表面活性剂的制备方法为将十二烷基苯磺酸钠和单硬脂酸甘油酯按质量比2:1~3:1混合,得混合表面活性剂。
技术说明书一种金属脱脂剂的制备方法技术领域本技术公开了一种金属脱脂剂的制备方法,属于金属表面化学处理剂技术领域。
背景技术在金属材料表面处理中,脱脂是重要的工艺过程,金属制件表面的脱脂程度将直接影响到制件的后续处理质量。
据统计,在表面处理中由于脱脂不彻底而导致镀层、转化膜不良的比例,一般占60%~80%。
金属制件表面油脂成分比较复杂,一类是以脂肪酸甘油脂为主的皂化油,可通过与碱的皂化作用去除;另一类是矿物油(非皂化油),可通过乳化作用脱除。
金属材料的脱脂可分为碱性水溶液脱脂、有机溶剂脱脂及酸性脱脂。
酸性脱脂剂因除油水平有限,对金属有一定腐蚀问题,应用领域较窄。
溶剂型脱脂剂应用非常广泛,但是溶剂型脱脂剂要么是ODS溶剂对臭氧层有破坏作用,要么有毒有害对人体有损伤,要么易燃易爆对生产环境有威胁,只有碱性水基脱脂剂无毒无味、不燃不爆,对清洗部件无损伤,清洗废液可以生化处理,应用非常广泛,是金属脱脂技术的发展总趋势,但是大部分碱性脱脂剂高磷、高氮、不易生物降解,易对水系造成污染,是传统的重污染行业之一。
目前,多数高效水基金属脱脂剂的助洗剂仍以磷酸盐为主,这是由于磷酸盐在脱脂剂中既有螯合作用,又有去污作用,并具有良好的水洗性和使用成本低等特点。
但此类脱脂剂的废液排放中含有的大量磷会造成环境污染。
磷元素的排放受到环保方面的严格限制,因此适合在工业上使用的无磷脱脂剂急需得到解决。
除此之外,传统脱脂剂在生产中遇到的问题是大量液体表面活性剂不易与固体清洗助剂混合均匀,在高低温环境下容易板结,导致脱脂效率不高影响使用效果。
因此,如何改善传统脱脂剂脱脂性能及稳定性不佳的缺点,以获取更高综合性能的脱脂剂,是其推广与应用,满足工业生产需求亟待解决的问题。
技术内容本技术主要解决的技术问题是:针对传统脱脂剂脱脂性能及稳定性不佳的缺点,提供了一种金属脱脂剂的制备方法。
为了解决上述技术问题,本技术所采用的技术方案是:(1)将活性炭与无水乙醇按质量比1:5~1:8混合,并加入活性炭质量0.4~0.7倍的氧化钠粉末,搅拌混合后,超声振荡,过滤,得预处理活性炭;(2)将预处理活性炭与石蜡按质量比1:4~1:8混合,冷冻粉碎,过筛,得改性活性炭;(3)将碳酸氢钠与水按质量比2:5~2:7混合,得基础液;(4)将海泡石与无水乙醇按质量比1:5~1:8混合,并加入海泡石质量1~2倍的异氰酸酯,搅拌混合后,过滤,得预处理海泡石;(5)将(N-脒基)十二烷基丙烯酰胺与聚乙二醇衍生物按质量比2:1~4:1混合,并加入聚乙二醇衍生物质量0.2~0.4倍的对二氯苯和聚乙二醇衍生物质量0.12~0.18倍的二茂铁,搅拌混合,得处理剂;(6)将预处理海泡石与处理剂按质量比1:3~1:5混合,并加入预处理海泡石质量1~2倍的石蜡,搅拌混合后,冷冻粉碎,得混合剂;(7)按重量份数计,依次称取20~35份基液,10~15份混合剂,8~10份改性活性炭,3~5份膨润土,3~5份乳化剂,3~5份柠檬酸,2~4份硅酸钠和4~8份混合表面活性剂,将基液与改性活性炭混合,并依次加入乳化剂,混合剂,膨润土,柠檬酸,硅酸钠和混合表面活性剂,搅拌混合后,得金属脱脂剂。
所述石蜡为碳原子数在16~26之间的石蜡混合物。
步骤(5)所述聚乙二醇衍生物为聚乙二醇-对甲苯磺酸酯或聚乙二醇水杨酸酯中任意一种。
步骤(7)所述乳化剂为壬基酚聚氧乙烯醚,辛基酚聚氧乙烯醚或月桂纯聚氧乙烯醚中任意一种。
步骤(7)所述混合表面活性剂的制备方法为将十二烷基苯磺酸钠和单硬脂酸甘油酯按质量比2:1~3:1混合,得混合表面活性剂。
本技术的有益效果是:(1)本技术在制备金属脱脂剂时加入混合剂,一方面,混合剂中加入处理剂,处理剂中含有两嵌段的共聚物聚乙二醇-b-聚(N-脒基)十二烷基丙烯酰胺,聚乙二醇-b-聚(N-脒基)十二烷基丙烯酰胺共聚物具有双亲性质,在加入产品中后,可在产品使用过程中,亲油基团与金属表面油污结合,亲水基团与水结合,将油污从金属表面去除,从而使产品的脱脂效果提高,另一方面混合剂中加入预处理海泡石,在产品使用过程中,预处理海泡石中的异氰酸酯遇水反应产生二氧化碳气体,二氧化碳气体可促使两嵌段共聚物聚乙二醇-b-聚(N-脒基)十二烷基丙烯酰胺中的囊泡结构扩大,从而使产品的脱脂效果进一步提高,并且海泡石在极性溶剂中形成密集的纤维束,吸附性增强,使脱离下的油污聚集于水中,从而使产品的脱脂效果提高;(2)本技术在制备金属脱脂剂时加入改性活性炭,首先活性炭表面的石蜡可与乳化剂一同使改性活性炭均匀分布于体系中,从而使产品稳定性提高,其次,改性活性炭中含有氧化钠,在产品使用过程中,石蜡包覆层破裂,氧化钠与水反应,生成氢氧化钠,并产生大量热量,氢氧化钠可使体系处于碱性环境中,从而使产品的脱脂效果提高,而产生的热量可使产品中的碳酸氢钠分解,产生的气体可使金属表面油污快速脱离,从而提高脱脂效率,并且产生的碳酸钠可进一步提高脱脂效果。
具体实施方式~0.7倍的氧化钠粉末,于温度为25~35℃,转速为280~380r/min的条件下搅拌混合25~35min后,得活性炭混合物,将活性炭混合物移入超声振荡仪,于频率为45~55kHz的条件下超声振荡15~25min后,过滤,得预处理活性炭;将预处理活性炭与石蜡按质量比1:4~1:8混合,于温度为35~55℃,转速为200~300r/min的条件下,搅拌混合30~45min后,冷冻粉碎,过200~320目筛,得改性活性炭;将碳酸氢钠与水按质量比2:5~2:7混合,于温度为25~35℃,转速为250~350r/min,搅拌混合25~35min后,得基础液;将海泡石与无水乙醇按质量比1:5~1:8混合于烧瓶中,并向烧瓶中加入海泡石质量1~2倍的异氰酸酯,于温度为20~30℃,转速为230~330r/min的条件下,搅拌混合25~35min后,得海泡石混合物,将海泡石混合物过滤,得预处理海泡石;将(N-脒基)十二烷基丙烯酰胺与聚乙二醇衍生物按质量比2:1~4:1混合于反应釜中,并向反应釜中加入聚乙二醇衍生物质量0.2~0.4倍的对二氯苯和聚乙二醇衍生物质量0.12~0.18倍的二茂铁,于温度为25~45℃,转速为280~350r/min的条件下,搅拌混合1~2h后,得处理剂;将预处理海泡石与处理剂按质量比1:3~1:5混合,并向预处理海泡石与处理剂的混合物中加入预处理海泡石质量1~2倍的石蜡,于温度为45~55℃,转速为220~320r/min的条件下,搅拌混合25~35min后,得海泡石处理剂混合物,将海泡石处理剂混合物冷冻粉碎,得混合剂;按重量份数计,依次称取20~35份基础液,10~15份混合剂,8~10份改性活性炭,3~5份膨润土,3~5份乳化剂,3~5份柠檬酸,2~4份硅酸钠和4~8份混合表面活性剂,将基础液与改性活性炭混合于混料机中,并依次向混料机中加入乳化剂,混合剂,膨润土,柠檬酸,硅酸钠和混合表面活性剂,于温度为25~30℃,转速为250~380r/min的条件下搅拌混合25~35min后,得金属脱脂剂。
所述石蜡为碳原子数在16~26之间的石蜡混合物。
所述聚乙二醇衍生物为聚乙二醇-对甲苯磺酸酯或聚乙二醇水杨酸酯中任意一种。
所述乳化剂为壬基酚聚氧乙烯醚,辛基酚聚氧乙烯醚或月桂纯聚氧乙烯醚中任意一种。
所述乳化剂为壬基酚聚氧乙烯醚,辛基酚聚氧乙烯醚或月桂纯聚氧乙烯醚中任意一种。
实例1化钠粉末,于温度为35℃,转速为380r/min的条件下搅拌混合35min后,得活性炭混合物,将活性炭混合物移入超声振荡仪,于频率为55kHz的条件下超声振荡25min后,过滤,得预处理活性炭;将预处理活性炭与石蜡按质量比1:8混合,于温度为55℃,转速为300r/min的条件下,搅拌混合45min后,冷冻粉碎,过320目筛,得改性活性炭;将碳酸氢钠与水按质量比2:7混合,于温度为35℃,转速为350r/min,搅拌混合35min后,得基础液;将海泡石与无水乙醇按质量比1:8混合于烧瓶中,并向烧瓶中加入海泡石质量2倍的异氰酸酯,于温度为30℃,转速为330r/min的条件下,搅拌混合35min后,得海泡石混合物,将海泡石混合物过滤,得预处理海泡石;将(N-脒基)十二烷基丙烯酰胺与聚乙二醇衍生物按质量比4:1混合于反应釜中,并向反应釜中加入聚乙二醇衍生物质量0.4倍的对二氯苯和聚乙二醇衍生物质量0.18倍的二茂铁,于温度为45℃,转速为350r/min的条件下,搅拌混合2h后,得处理剂;将预处理海泡石与处理剂按质量比1:5混合,并向预处理海泡石与处理剂的混合物中加入预处理海泡石质量2倍的石蜡,于温度为55℃,转速为320r/min的条件下,搅拌混合35min后,得海泡石处理剂混合物,将海泡石处理剂混合物冷冻粉碎,得混合剂;按重量份数计,依次称取35份基础液,15份混合剂,10份改性活性炭,5份膨润土,5份乳化剂,5份柠檬酸,4份硅酸钠和8份混合表面活性剂,将基础液与改性活性炭混合于混料机中,并依次向混料机中加入乳化剂,混合剂,膨润土,柠檬酸,硅酸钠和混合表面活性剂,于温度为30℃,转速为380r/min的条件下搅拌混合35min后,得金属脱脂剂。