铸造多晶硅PPT课件
合集下载
第6章铸造多晶硅

铸造多晶硅的掺杂: 与单晶硅一样,铸造多晶硅的晶体生长过程中也要 进行掺杂,掺杂时要考虑成本、杂质的分凝系数及 后续的太阳电池制备工艺。实际生产中主要制备p型 多晶硅。 太阳电池最优电阻率1 cm 硼掺杂浓度为2×1016 cm2 2B2O2 = 4B + 3O2 硼的分凝系数为0.8,所以硼的浓度分布比较均匀,所 以铸造多晶硅电阻率分布也比较均匀。图6.13
(3)熔化。通入氩气,使炉内压力维持在 40~60kPα,逐渐增大加热功率,使石 英坩埚内的温度达到1 500℃左右,硅 原料开始熔化,熔化过程中一直保持此 温度,直至化料结束,该过程约需9~11 h。
(4)生长。硅料熔化后,降低加热功率,使石英 坩埚的温度降至1 420℃~1 440℃硅熔点。然后 石英坩埚逐渐向下移动,或者隔热装置逐渐上 升,使石英坩埚慢慢脱离加热区,使硅熔料与 周围形成热交换,同时,冷却板通水,使熔体 的温度自底部开始降低,晶体硅首先在底部形 成,并呈柱状向上生长,生长过程中固-液界面 始终保持与水平面基本平行,直至晶体生长完 成,该过程约需要20~22 h。
晶体生长工艺:
(1)装料。将装好料的坩埚放置在热交换台上, 然后炉内抽真空,使炉内压力为5~10 Pα并保 持真空。通入氩气,使炉内压力维持在40~60 kPα。
(2)加热。用石墨加热器加热,首先使石墨部 件、隔热层、硅原料等表面吸附的湿气蒸发, 然后缓慢加温,使石英坩埚的温度达到1 200℃~1 300℃,该过程约需4~5 h。
太阳电池多晶硅锭是一种柱状晶,晶体生长方向垂直向上,是 通过定向凝固(也称可控凝固、约束凝固)过程来实现的,即 在结晶过程中,通过控制温度场的变化,形成单方向热流(生长 方向与热流方向相反),并要求液固界面处的温度梯度大于0, 横向则要求无温度梯度,从而形成定向生长的柱状晶。
多晶硅铸锭炉操作与生产流程(PPT31页)名家精品课件
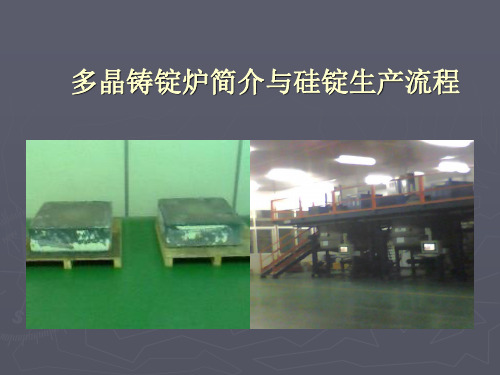
文件名。 在屏幕上还显示进气阀的设定值和实测值,出气阀 的设定值和实测值,炉内压力的设定值和实测值,8 路水流量的实测值,隔热笼的目标位置和实际位置,
瞬时电流、电压、功率、通断百分比,控制方式以 及各自的设定值和实测值等。
自动控制窗口
自动控制窗口主要包含自动运行的一些功能。操作 者可以选择正常启动或定时启动来开始一次自动加 工。 只要按下自动运行按钮,系统就会开始自动运行; 自动运行开始运行时,旁边会出现一个绿色圆图标,
度设定等。此窗口还包含隔热笼操作、下炉体运行 控制、慢速抽真空、维护操作等子窗口。
趋势图窗口
趋势图界面显示5个小时内8个变量的实时变化趋势 ,可以查看功率、3个热电偶的温度、炉腔压力、隔
热笼位置、高温计和报警。该趋势图分为实时趋势 和历史趋势2个部分。
硅锭生产流程
生产流程图:
坩埚喷涂
坩埚烘烤
检验
•
3、2021/8/20Aug-2120-Aug-21
昨天是张退票的支票20-Aug-212:36:20 AM02:36
•
4、
2021 /8/202 021/8/2 02021/ 8/20Fri day, August 20, 2021
• •
积极人格的完善是本,财富的确立是末21.8.20 5、
。20 21/8/20 2021/8 /20202 1/8/202 021/8/ 208/20/ 2021
原料进炉
进炉
步骤:
1 小心用专用叉车将装 好硅料的坩埚从小推 车上升起。
2 使用专用叉车将坩埚 放到石墨交换台上。
3 放入交换台时应缓慢下 降。
4 坩埚盒与交换台四周距 离41±2 cm.
监控
步骤: 1 合上炉体,关上夹具。 2 点慢速抽真空按钮,慢
瞬时电流、电压、功率、通断百分比,控制方式以 及各自的设定值和实测值等。
自动控制窗口
自动控制窗口主要包含自动运行的一些功能。操作 者可以选择正常启动或定时启动来开始一次自动加 工。 只要按下自动运行按钮,系统就会开始自动运行; 自动运行开始运行时,旁边会出现一个绿色圆图标,
度设定等。此窗口还包含隔热笼操作、下炉体运行 控制、慢速抽真空、维护操作等子窗口。
趋势图窗口
趋势图界面显示5个小时内8个变量的实时变化趋势 ,可以查看功率、3个热电偶的温度、炉腔压力、隔
热笼位置、高温计和报警。该趋势图分为实时趋势 和历史趋势2个部分。
硅锭生产流程
生产流程图:
坩埚喷涂
坩埚烘烤
检验
•
3、2021/8/20Aug-2120-Aug-21
昨天是张退票的支票20-Aug-212:36:20 AM02:36
•
4、
2021 /8/202 021/8/2 02021/ 8/20Fri day, August 20, 2021
• •
积极人格的完善是本,财富的确立是末21.8.20 5、
。20 21/8/20 2021/8 /20202 1/8/202 021/8/ 208/20/ 2021
原料进炉
进炉
步骤:
1 小心用专用叉车将装 好硅料的坩埚从小推 车上升起。
2 使用专用叉车将坩埚 放到石墨交换台上。
3 放入交换台时应缓慢下 降。
4 坩埚盒与交换台四周距 离41±2 cm.
监控
步骤: 1 合上炉体,关上夹具。 2 点慢速抽真空按钮,慢
硅片制备--多晶硅铸锭炉和单晶炉幻灯片PPT

• 观察窗装在直拉单晶炉膛上,由两层石英玻璃(或厚玻璃)组成,两 层玻璃中间通水,它是观察拉硅单晶过程中各种情况的窗口。
• 热电偶装在直拉单晶炉膛的测温孔上,正对加热器中部。为了使便于 测量和测量灵敏准确,一般通过聚光镜,将光聚集于热电偶堆上。
• 电极装在炉膛底部,它的作用是支撑加热器(石墨)和保温系统(或 通过石墨电极支撑),把强大的电流传给加热器,使加热器产生高温, 熔化多晶硅。电极一般由紫铜制成,两层铜管成环状,内部通水。
• 光学等直径监测器装在炉膛的光学等直径监测孔上,它象照象机,一 组光学镜头对准坩埚中心,硅单晶通过镜头将硅单晶横断面直径的正 面影象反射在毛玻璃屏幕上,屏幕上有一个光敏二极管,影象变化作 用在光敏二极管上,产生电信号,经过放大分压(或分流)处理,控 制提拉或加热功率,保证硅单晶等径生长,通过调节光敏二极管位置 可以控制生长硅单晶的粗细。
• 单晶炉的机械传动部分,包括籽晶轴(上 轴)、坩埚轴和驱动它们上升、下降或旋 转的电机。
• 籽晶轴和坩埚轴的旋转由力矩电机(或直 流电机)分别经过皮带(或齿轮)变速后 带动抱轮使其旋转。
• 籽晶轴和坩埚轴的上升或下降通过通过两 个力矩电机(或直流电机)驱动螺纹旋转 完成。
• 这四个运动各自独立,互不干扰,不同的 是坩埚轴比籽晶轴有更缓慢上升或下降速 度。
硅片制备--多晶硅铸锭炉 和单晶炉幻灯片PPT
本课件PPT仅供大家学习使用 学习完请自行删除,谢谢! 本课件PPT仅供大家学习使用 学习完请自行删除,谢谢! 本课件PPT仅供大家学习使用 学习完请自行删除,谢谢! 本课件PPT仅供大家学习使用 学习完请自行删除,谢谢!
一、 单晶炉
• 目前在所有安装的太阳电池中,超过90%以上的 是晶体硅太阳电池,因此位于产业链前端的硅锭/ 片的生产对整个太阳电池产业有着很重要的作用。
• 热电偶装在直拉单晶炉膛的测温孔上,正对加热器中部。为了使便于 测量和测量灵敏准确,一般通过聚光镜,将光聚集于热电偶堆上。
• 电极装在炉膛底部,它的作用是支撑加热器(石墨)和保温系统(或 通过石墨电极支撑),把强大的电流传给加热器,使加热器产生高温, 熔化多晶硅。电极一般由紫铜制成,两层铜管成环状,内部通水。
• 光学等直径监测器装在炉膛的光学等直径监测孔上,它象照象机,一 组光学镜头对准坩埚中心,硅单晶通过镜头将硅单晶横断面直径的正 面影象反射在毛玻璃屏幕上,屏幕上有一个光敏二极管,影象变化作 用在光敏二极管上,产生电信号,经过放大分压(或分流)处理,控 制提拉或加热功率,保证硅单晶等径生长,通过调节光敏二极管位置 可以控制生长硅单晶的粗细。
• 单晶炉的机械传动部分,包括籽晶轴(上 轴)、坩埚轴和驱动它们上升、下降或旋 转的电机。
• 籽晶轴和坩埚轴的旋转由力矩电机(或直 流电机)分别经过皮带(或齿轮)变速后 带动抱轮使其旋转。
• 籽晶轴和坩埚轴的上升或下降通过通过两 个力矩电机(或直流电机)驱动螺纹旋转 完成。
• 这四个运动各自独立,互不干扰,不同的 是坩埚轴比籽晶轴有更缓慢上升或下降速 度。
硅片制备--多晶硅铸锭炉 和单晶炉幻灯片PPT
本课件PPT仅供大家学习使用 学习完请自行删除,谢谢! 本课件PPT仅供大家学习使用 学习完请自行删除,谢谢! 本课件PPT仅供大家学习使用 学习完请自行删除,谢谢! 本课件PPT仅供大家学习使用 学习完请自行删除,谢谢!
一、 单晶炉
• 目前在所有安装的太阳电池中,超过90%以上的 是晶体硅太阳电池,因此位于产业链前端的硅锭/ 片的生产对整个太阳电池产业有着很重要的作用。
第十章讲义铸造多晶硅
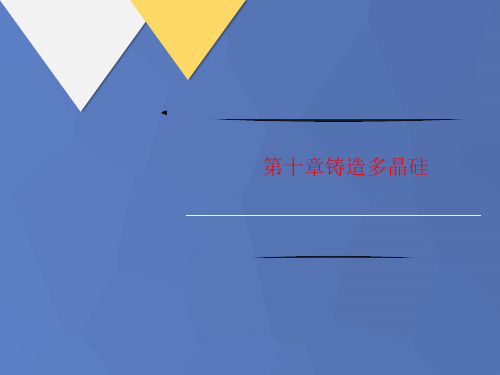
右,它以相对低成本、高效率的优势
不断挤占单晶硅的市场,成为最有竞争
力的太阳电池材料。21世纪初已占50% 以上,成为最主要的太阳电池材料。
直拉单晶硅为圆片状,而硅片制备 的圆形太阳电池不能有效地利用太阳电 池组件的有效空间,相对增加了太阳电 池组件的成本。如果将直拉单晶硅圆柱 切成方块,制备太阳电池,其材料浪费 就增加,同样也增加了太阳电池组件的 成本。
晶硅,从而降低了太阳电池的光电转换 效率。
铸造多晶硅和直拉单晶硅的比较见表 10.1
自从铸造多晶硅发明以后,技术不 断改进,质量不断提高,应用也不断广 泛。在材料制备方面,平面固液相技术 和氮化硅涂层技术等技术的应用、材料 尺寸的不断加大。
在电池方面,SiN减反射层技 术、氢钝化技术、吸杂技术的开发 和应用,使得铸造多晶硅材料的电 学性能有了明显改善,其太阳电池 的光电转换率也得到了迅速提高。
铸造多晶硅的优缺点
缺
铸造多晶硅具有晶界、高密度的位
错、微缺陷和相对较高的杂质浓度,从 而降低了太阳电池的光电转换效率。
10.1 概述 10.2 铸造多晶硅的制备工艺 10.3 铸造多晶硅的晶体生长
10.1 概述
利用铸造技术制备多晶硅,称为铸 造多晶硅(multicrystalline silicon, mc-Si)。
直熔法
由图可知,硅原材料首先在坩埚中熔 化,坩埚周围的加热器保持坩埚上部温度 的同时,自坩埚的底部开始逐渐降温,从 而使坩埚底部的熔体首先结晶。同样的, 通过保持固液界面在同一水平面并逐渐上 升。使得整个熔体结晶为晶锭。在这种制 备方法中,硅原材料的熔化和结晶都在同 一个坩埚中进行。
直熔法
图10.4 直熔法制备铸造多晶硅用 晶体生长炉的结构
直熔法的冷却方式
不断挤占单晶硅的市场,成为最有竞争
力的太阳电池材料。21世纪初已占50% 以上,成为最主要的太阳电池材料。
直拉单晶硅为圆片状,而硅片制备 的圆形太阳电池不能有效地利用太阳电 池组件的有效空间,相对增加了太阳电 池组件的成本。如果将直拉单晶硅圆柱 切成方块,制备太阳电池,其材料浪费 就增加,同样也增加了太阳电池组件的 成本。
晶硅,从而降低了太阳电池的光电转换 效率。
铸造多晶硅和直拉单晶硅的比较见表 10.1
自从铸造多晶硅发明以后,技术不 断改进,质量不断提高,应用也不断广 泛。在材料制备方面,平面固液相技术 和氮化硅涂层技术等技术的应用、材料 尺寸的不断加大。
在电池方面,SiN减反射层技 术、氢钝化技术、吸杂技术的开发 和应用,使得铸造多晶硅材料的电 学性能有了明显改善,其太阳电池 的光电转换率也得到了迅速提高。
铸造多晶硅的优缺点
缺
铸造多晶硅具有晶界、高密度的位
错、微缺陷和相对较高的杂质浓度,从 而降低了太阳电池的光电转换效率。
10.1 概述 10.2 铸造多晶硅的制备工艺 10.3 铸造多晶硅的晶体生长
10.1 概述
利用铸造技术制备多晶硅,称为铸 造多晶硅(multicrystalline silicon, mc-Si)。
直熔法
由图可知,硅原材料首先在坩埚中熔 化,坩埚周围的加热器保持坩埚上部温度 的同时,自坩埚的底部开始逐渐降温,从 而使坩埚底部的熔体首先结晶。同样的, 通过保持固液界面在同一水平面并逐渐上 升。使得整个熔体结晶为晶锭。在这种制 备方法中,硅原材料的熔化和结晶都在同 一个坩埚中进行。
直熔法
图10.4 直熔法制备铸造多晶硅用 晶体生长炉的结构
直熔法的冷却方式
硅片制备多晶硅铸锭炉和单晶炉最新课件.ppt
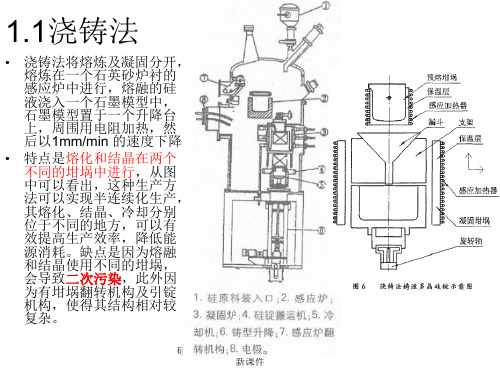
硅片制备多晶硅铸锭炉和单晶炉最 新课件
多晶硅生产过程(LDK)
硅片制备多晶硅铸锭炉和单晶炉最 新课件
硅片制备多晶单晶炉最 新课件
硅片制备多晶硅铸锭炉和单晶炉最 新课件
DSS炉
• 系统硬件包括:不锈钢 板,一对侧板,水冷铸 锭炉,供应电源,一个 真空泵系统和一个控制 柜,操作控制盘。
硅片制备多晶硅铸锭炉和单晶炉最 新课件
• 下图为一个热交换法与布里曼法相结合的结晶炉 示意图。图中,工作台通冷却水,上置一个热开 关,坩埚则位于热开关上。硅料熔融时,热开关 关闭,结晶时打开,将坩埚底部的热量通过工作 台内的冷却水带走,形成温度梯度。
• 同时坩埚工作台缓慢下降,使凝固好的硅锭离开 加热区,维持固液界面有一个比较稳定的温度梯 度,在这个过程中,要求工作台下降非常平稳, 以保证获得平面前沿定向凝固。
硅片制备多晶硅铸锭炉和单晶炉最 新课件
1.3 电磁铸锭法法(EMC或者EMCP法)
• 利用电磁感应的冷坩埚来熔化硅 原料。
• 这种熔化和凝固技术可以在不同 的部位同时进行,节约时间。而 且,熔体和坩埚不直接接触,既 没有坩埚的消耗,又减少了杂质 的污染,特别是氧浓度和金属杂 质大幅降低,另外,该技术还可 以连续浇铸。不仅如此,由于电 磁力对硅熔体搅拌作用,使得掺 杂剂在硅熔体中的分布能更均匀, 是种很有前途的铸造多晶硅技术。
• 内涂SiN的坩埚装入多晶硅料后放在导热性很强的石墨块上(即所谓 的定向固化块或者DS块)。关闭炉子后排气,接通加热器电源融化 硅料数小时以上。坩埚的四个竖直边都围有石墨加热器,DS-Block, 坩埚四周围有隔热层。隔热层的竖直边能上下移动以便露出DS-Block 的边缘,使热量辐射到下腔室的水冷四壁上。水冷却DS-Block后再返 回来冷却坩埚底部,从而使坩埚内的熔融硅周围形成了一个竖直温度 梯度。这个梯度使坩埚内的硅料从底部开始凝固,从熔体底部向顶部 开始长晶。当所有的硅料都凝固后,在程序的控制下,硅锭需要经过 退火,冷却处理以免破裂且能将(晶格)位移降到最小限度 。
多晶硅生产过程(LDK)
硅片制备多晶硅铸锭炉和单晶炉最 新课件
硅片制备多晶单晶炉最 新课件
硅片制备多晶硅铸锭炉和单晶炉最 新课件
DSS炉
• 系统硬件包括:不锈钢 板,一对侧板,水冷铸 锭炉,供应电源,一个 真空泵系统和一个控制 柜,操作控制盘。
硅片制备多晶硅铸锭炉和单晶炉最 新课件
• 下图为一个热交换法与布里曼法相结合的结晶炉 示意图。图中,工作台通冷却水,上置一个热开 关,坩埚则位于热开关上。硅料熔融时,热开关 关闭,结晶时打开,将坩埚底部的热量通过工作 台内的冷却水带走,形成温度梯度。
• 同时坩埚工作台缓慢下降,使凝固好的硅锭离开 加热区,维持固液界面有一个比较稳定的温度梯 度,在这个过程中,要求工作台下降非常平稳, 以保证获得平面前沿定向凝固。
硅片制备多晶硅铸锭炉和单晶炉最 新课件
1.3 电磁铸锭法法(EMC或者EMCP法)
• 利用电磁感应的冷坩埚来熔化硅 原料。
• 这种熔化和凝固技术可以在不同 的部位同时进行,节约时间。而 且,熔体和坩埚不直接接触,既 没有坩埚的消耗,又减少了杂质 的污染,特别是氧浓度和金属杂 质大幅降低,另外,该技术还可 以连续浇铸。不仅如此,由于电 磁力对硅熔体搅拌作用,使得掺 杂剂在硅熔体中的分布能更均匀, 是种很有前途的铸造多晶硅技术。
• 内涂SiN的坩埚装入多晶硅料后放在导热性很强的石墨块上(即所谓 的定向固化块或者DS块)。关闭炉子后排气,接通加热器电源融化 硅料数小时以上。坩埚的四个竖直边都围有石墨加热器,DS-Block, 坩埚四周围有隔热层。隔热层的竖直边能上下移动以便露出DS-Block 的边缘,使热量辐射到下腔室的水冷四壁上。水冷却DS-Block后再返 回来冷却坩埚底部,从而使坩埚内的熔融硅周围形成了一个竖直温度 梯度。这个梯度使坩埚内的硅料从底部开始凝固,从熔体底部向顶部 开始长晶。当所有的硅料都凝固后,在程序的控制下,硅锭需要经过 退火,冷却处理以免破裂且能将(晶格)位移降到最小限度 。
多晶硅硅料的生产工艺ppt课件

编辑版pppt
8
世界多晶硅主要生产企业有日本的Tokuyama、 三 菱 、 住 友 公 司 、 美 国 的 Hemlock 、 Asimi 、 SGS、MEMC公司,德国的Wacker公司等,其 年产能绝大部分在1000吨以上,其中Tokuyama、 Hemlock、Wacker三个公司生产规模最大,年 生产能力均在3000-8000吨,且产能在不断扩 展中。世界主要高纯多晶硅制造商2004-2008年 产量和生产能力如表所示:
编辑版pppt
12
从上述的推测分析,至2010年太阳电池用多晶硅 至少在30000吨以上。据国外资料分析报道,世 界 多 晶 硅 的 产 量 2005 年 为 28750 吨 , 其 中 半 导 体级为20250吨,太阳能级为8500吨,半导体 级需求量约为19000吨,略有过剩;太阳能级的 需求量为15000吨,供不应求,从2006年开始 太阳能级和半导体级多晶硅需求的均有缺口,其 中太阳能级产能缺口更大。
编辑版pppt
29
多晶硅的生产有着许多方面的壁垒
多晶硅项目的壁垒:技术,还是技术
多晶硅的生产有着许多方面的壁垒:
首先,多晶硅提纯是有很高技术壁垒。如前文所述,目 前冶炼多晶硅最重要的技术是西门子法,基本被国际七大 公司垄断。中国项目大多是准备直接或间接地引进俄罗斯 的技术。但俄罗斯目前的能力也仅限于百吨级产量的技术, 到目前为止,连俄罗斯自己仍然没有达到1000 吨产能的 最小经济规模(最佳经济规模要达到2500 吨/年)。同时俄 罗斯的技术在电能消耗上明显高于国际同行,生产每公斤 硅材料耗电量300 度,而国际水准仅为100 度。
编辑版pppt
3
编辑版pppt
4
以上四种太阳电池中,硅太阳电池一直是PV市场 上的主导产品。由于硅太阳电池具有原料丰富、 制作技术工艺成熟、电池转化效率高、性能稳定 的特点,是过去的二十年中太阳电池研究、开发 和生产的主体原料。
《铸锭培训教材》PPT课件
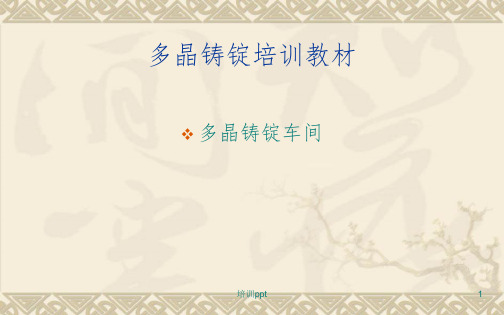
由于在流化床反应炉内参与反应的硅表面积大,故该方法生产效率高、电耗较低、成本低。 但也有安全性较差、生长速率较低、产量低等缺点。目前采用该方法生产颗粒状多晶硅的公司 主要有:REC、Wacker、Hemlock和MEMC公司等。
培训ppt
7
单晶体与多晶体
❖
大家知道,固体分为晶体和非晶体,而晶体又可以分为单晶体和多晶体。生活中,我们所
SICL4 、SIH2CL2、 SIHCL3分离提纯
晶 硅 流 程
SICL4
图
H2
Sபைடு நூலகம்CL4反应器
超纯硅
培训ppt
6
3、流化床法
该方法是美国联合碳化合物公式早年研发制备多晶硅的工艺技术,它是以SICL4(或SIF4)、 H2、HCL和冶金硅为原料,在高温高压流化床(沸腾床)内生成SIHCL3,将SIHCL3再进一 步歧化加氢反应成SIHCL2,继而生成SIH4气。将制得的SIH4气通入加有小颗粒硅粉的流化床 反应炉内进行连续热分解反应,生成粒状多晶硅产品。
用氯和氢合成氯化氢,再用氯化氢和工业硅粉在一定温度下合成三氯氢硅,然后对三氯氢硅进行分离精馏提纯,
提纯后的三氯氢硅在氢还原炉内进行CVD反应生产高纯多晶硅。
第 三 代 西 门 子 多 晶 硅 生 产 工 艺 流 程 图
培训ppt
5
❖ 2.硅烷法
硅烷法也叫硅烷热分解法它是以氟硅酸、钠、铝、氢气为主要原辅材料,通过SICL4氢化法、
区域里原子按周期性的规则排列,但不同局部区域之间原子的排列方向并不相同,因此多晶体 也可以看成是由许多取向不同的小单晶体(又称为晶粒)组成的。
硅原子
晶体
培训ppt
非晶体
单晶与多晶
8
培训ppt
7
单晶体与多晶体
❖
大家知道,固体分为晶体和非晶体,而晶体又可以分为单晶体和多晶体。生活中,我们所
SICL4 、SIH2CL2、 SIHCL3分离提纯
晶 硅 流 程
SICL4
图
H2
Sபைடு நூலகம்CL4反应器
超纯硅
培训ppt
6
3、流化床法
该方法是美国联合碳化合物公式早年研发制备多晶硅的工艺技术,它是以SICL4(或SIF4)、 H2、HCL和冶金硅为原料,在高温高压流化床(沸腾床)内生成SIHCL3,将SIHCL3再进一 步歧化加氢反应成SIHCL2,继而生成SIH4气。将制得的SIH4气通入加有小颗粒硅粉的流化床 反应炉内进行连续热分解反应,生成粒状多晶硅产品。
用氯和氢合成氯化氢,再用氯化氢和工业硅粉在一定温度下合成三氯氢硅,然后对三氯氢硅进行分离精馏提纯,
提纯后的三氯氢硅在氢还原炉内进行CVD反应生产高纯多晶硅。
第 三 代 西 门 子 多 晶 硅 生 产 工 艺 流 程 图
培训ppt
5
❖ 2.硅烷法
硅烷法也叫硅烷热分解法它是以氟硅酸、钠、铝、氢气为主要原辅材料,通过SICL4氢化法、
区域里原子按周期性的规则排列,但不同局部区域之间原子的排列方向并不相同,因此多晶体 也可以看成是由许多取向不同的小单晶体(又称为晶粒)组成的。
硅原子
晶体
培训ppt
非晶体
单晶与多晶
8
第七章 铸造多晶硅中的缺陷
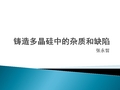
与直拉单晶硅相比,铸造多晶硅中的碳含量更多。 可超过1*1017cm-3 而直拉单晶硅为低于 5*1015cm-3 . 但碳杂质的基本性质和直拉单晶硅中的一样:分凝 系数、固溶度、扩散速度和测量方法 碳的分凝系数为0.07,因此,碳浓度随晶体的生长, 浓度变大。晶体顶部可到4*1017cm-3 ,从而生成 SiC.
EC
产生 复合
EV
受外界因素(光照、载流子注入等)影响比平衡状 态下多出来的载流子。
非平衡载流子浓度为Δn、Δp。
EC
hν
Δn = Δp
EV
在光激发下,一开始载流子产生率G大于复合率R, 导致载流子增加。到稳态时G = R,此时载流子浓 度趋于稳定。 电子和空穴浓度: n = n0 + Δ n; p = p 0 + Δ p n0 、p0分别为平衡时电子和空穴的浓度。
氮对的热稳定性:750 度全部消失 但硼氮复合体几乎不变
氮氧复合体形成一系列 能级,其能级位于倒带 之下30-60meV. 此性质和直拉单晶硅中 的性质相同
氮氧复合体是一种浅 热施主,并且为单电子 施主,但由于氮的固浓 度很低,因此其对晶体 硅中电阻率的影响几乎 没有。 直拉单晶硅中,氮能 促进氧沉淀,抑制氧施 主,但对铸造多晶硅中 还未有详细的研究。
-
μ-PCD法的测试模型
Excitation pulse
1
eff .
200 ns
1
bulk Sd
1
eff: 有效寿命, 也是测试寿命 bulk : 体寿命 sd: 表面复合影响的寿命
Detected µw signal
Sd
-t/ V = V0 e
多晶硅锭制备—铸锭多晶硅工艺ppt课件

第三小组第三小组谢海峰谢海峰一多晶硅锭产业背景二多晶硅锭的组织结构三定向凝固时硅中杂质的分凝四多晶硅锭定向凝固生长方法五热交换炉型六热交换法现行工艺讨论七结晶炉结构类型的选择一多晶硅锭产业背景一多晶硅锭产业背景太阳能电池产业是近几年发展最快的产业之一最近5年来以超过50的速度高速增在各种类型的太阳能电池中晶体硅太阳电池由于其转换效率高技术成熟而继续保持领先地位占据了90以上的份额预计今后十年内晶体硅仍将占主导地位
• 另一方面,铸锭多晶硅的生产周期大约460公斤 每60小时,5.17公斤每小时,是单晶方棒1.30公 斤每小时的4倍。
• 可见采用多晶铸锭法制备多晶硅锭,进而加工硅 片,制造成本的优势是显而易见的。
五、热交换法炉型
炉型1: 下页图为目前国内应用较多的一种热交换法炉型示
意图,采用石墨电阻在四周加热。凝固开始时通过提 升保温框〔0.12-0.2mm/分〕以增大石墨块的散热强 度。长晶速度为变数,平均为0.28mm/分。
特点:
坩埚和热源在凝固开始时作相对位移,分液 相区和凝固区,液相区和凝固区用隔热板 隔开。
液固界面交界处的温度梯度必须>0,即 dT/dx>0,温度梯度接近于常数。
ห้องสมุดไป่ตู้却水
坩埚 热源 硅液
隔热板 热开关 工作台
布里曼法示意图
液相
固液界面 固相
• 长晶速度受工作台下移速度及冷却水流量 控制,长晶速度接近于常数,长晶速度可 以调节。
多晶硅锭制备—铸锭 多晶硅工艺
第三小组 谢海峰
一、多晶硅锭产业背景 二、多晶硅锭的组织结构 三、定向凝固时硅中杂质的分凝 四、多晶硅锭定向凝固生长方法 五、热交换炉型 六、热交换法现行工艺讨论 七、结晶炉结构类型的选择
• 另一方面,铸锭多晶硅的生产周期大约460公斤 每60小时,5.17公斤每小时,是单晶方棒1.30公 斤每小时的4倍。
• 可见采用多晶铸锭法制备多晶硅锭,进而加工硅 片,制造成本的优势是显而易见的。
五、热交换法炉型
炉型1: 下页图为目前国内应用较多的一种热交换法炉型示
意图,采用石墨电阻在四周加热。凝固开始时通过提 升保温框〔0.12-0.2mm/分〕以增大石墨块的散热强 度。长晶速度为变数,平均为0.28mm/分。
特点:
坩埚和热源在凝固开始时作相对位移,分液 相区和凝固区,液相区和凝固区用隔热板 隔开。
液固界面交界处的温度梯度必须>0,即 dT/dx>0,温度梯度接近于常数。
ห้องสมุดไป่ตู้却水
坩埚 热源 硅液
隔热板 热开关 工作台
布里曼法示意图
液相
固液界面 固相
• 长晶速度受工作台下移速度及冷却水流量 控制,长晶速度接近于常数,长晶速度可 以调节。
多晶硅锭制备—铸锭 多晶硅工艺
第三小组 谢海峰
一、多晶硅锭产业背景 二、多晶硅锭的组织结构 三、定向凝固时硅中杂质的分凝 四、多晶硅锭定向凝固生长方法 五、热交换炉型 六、热交换法现行工艺讨论 七、结晶炉结构类型的选择
- 1、下载文档前请自行甄别文档内容的完整性,平台不提供额外的编辑、内容补充、找答案等附加服务。
- 2、"仅部分预览"的文档,不可在线预览部分如存在完整性等问题,可反馈申请退款(可完整预览的文档不适用该条件!)。
- 3、如文档侵犯您的权益,请联系客服反馈,我们会尽快为您处理(人工客服工作时间:9:00-18:30)。
铸造多晶硅
.
1
自20世纪80年代铸造多晶硅发明和应用 以来,增长迅速,80年代末期它仅占太阳 电池材料的10%左右,而至1996年底它已
占整个太阳电池材料的36%左右,它以相 对低成本、高效率的优势不断挤占单
晶硅的市场,成为最有竞争力的太阳电池 材料。21世纪初已占50%以上,成为最主 要的太阳电池材料。
热交换等方式,使得熔体冷却,采用定向凝固技术 制造多晶硅——热交换法(Heat Exchange Method, HEM)。 ➢ 在坩埚内直接将多晶硅溶化,然后将坩埚以一定的 速度移出热源区域,从而建立起定向凝固的条件— —布里曼法(Bridgman)。
.
10
定向凝固法
与铸锭浇注法相比,定向凝固法有以下优点:
.
12
这种技术熔化和凝固可以在不同部位同时进行,节 约生产时间;而且,熔体和坩埚不直接接触,既没 有坩埚消耗,降低成本,又减少了杂质污染程度, 特别是氧浓度和金属杂质浓度有可能大幅度降低。
该技术还可以连续浇铸,速度可达 5mm/min。不 仅如此,由于电磁力对硅熔体的作用,使得掺杂剂 在硅熔体中的分布可能更均匀。
缺点:铸造多晶硅具有晶界、高密度的位错、微缺
陷和相对较高的杂质浓度,从而降低了太阳电池的光 电转换效率。
.
3
1、概述
利用铸造技术制备多晶硅,称为铸造多晶硅 (multicrystalline silicon,Mc-Si)。
铸造多晶硅中含有大量的晶粒、晶界、位错和杂 质,但由于省去了高费用额晶体拉制过程,所以 相对成本较低,而且能耗也较低,在国际上的到 了广泛应用。
显然,这是一种很有前途的铸造多晶硅技术。
.
13
这种技术制备出的铸造多晶硅的晶粒比较细小, 约为3-5mm,而且晶粒大小不均匀。而且,由图 6.9可以看出,该技术的固液界面是严重的凹形, 会引入较多的晶体缺陷。因此,这种技术制备的 铸造多晶硅的少数载流子寿命较低,所制备的太 阳电池的效率也较低。
.
14
铸造多晶硅的原材料
高纯多晶硅
微电子工业应单 晶硅生产的剩余料
微电 子工业 应单晶 硅生产 的剩余 料
质量相对较差的高纯多晶硅
单晶硅棒的头尾料 单晶硅生长完成后剩余在石英
坩埚中的硅底料
.
15
.
16
PN结的制备方法
在一块 N型(或P型)半导体单晶上,用适当的工艺方法 把P型(或N型)杂质掺入其中,使这块单晶的不同区域分别形 成N型和P型的导电类型,两者的交界处就形成了PN结。
在电池方面,SiN减反射层技术 、氢钝化技术、吸杂技术的开发和 应用,使得铸造多晶硅材料的电学 性能有了明显改善,其太阳电池的 光电转换率也得到了迅速提高。
.
6
由于铸造多晶硅的优势,世界各发达国 家都在努力发展其工业规模。自20世纪90年代以 来,国际上新建的太阳电池和材料的生产线大部 分是铸造多晶硅生产线,相信在今后会有更多的 铸造多晶硅材料和电池生产线投入应用。目前, 铸造多晶硅已占太阳电池材料的53%以上,成为 最主要的太阳电池材料。
.
7
2、铸造多晶硅的制备工艺
➢ 铸锭浇注法 ➢ 定向凝固法 ➢ 磁感应加热连续铸造(EMCP)
.
8
铸锭浇注法
在一个坩埚内将硅原料溶化,然后浇铸在另一个经 过预热的坩埚内冷却,通过控制冷却速率,采用定 向凝固技术制备大晶粒的铸造多晶硅。
.
9
定向凝固法
直接熔融定向凝固法,简称直熔法。 ➢ 在坩埚内直接将多晶硅溶化,然后通过坩埚底部的
制备方法主要有:
➢合金法 ➢扩散法 ➢离子注入法 ➢薄膜生长法 ➢……
.
17
把一受定特主温点型度:杂,NP质区区使小中中小施球受球主放主溶杂杂在解质质一,浓浓块度然度N为后为型NN降单DA,低,晶而也温硅且是度片均均,上匀匀熔分,分体布加布;开热。始到 凝固在,交在界N面型处硅,片杂上质形浓度成由一N含A(有P高型浓)突度变受为主N杂D(质N的型P )型,硅具薄有层这,种其杂与质分N型布硅的P衬N底结称的为交突界变面结处。即为PN结。
.
18
在N型(或P型)硅片中 ,利用扩散工艺掺入相反型 例号与体中通分扩:特过从,—的基,,入解散将点程通—P在区杂体从加,到PP及常:线低2这型到O质材而温半P杂称杂 性5表沉,种半N,料构至导质为质缓面区淀结导在相成体1P补缓的变浓是在02中体局反内PO0偿变分结度逐硅50N,放在部型,~决结。布结深渐片1杂入硅区号在2定由。。扩变表0质扩片域的硅0。扩散化面℃浓散表形半表散结的并,度炉面成导面 形成含高浓度磷的N型半导 体。
➢在同一个坩埚中进行熔炼与凝固成形,避免了熔体的二次 污染;
➢通过定向凝固得到的是柱状晶,减轻了晶界的不利影响; ➢由于定向凝固过程中的杂质分凝效应,对于硅中分凝系数
与1相差较大的杂质有一定的提纯作用。
缺点:能耗大,生产效率低,操作不连续、产能较小,坩埚 耗费大,其硅锭制备设备成本较高。
.
11
其原理是利用电磁感应的冷坩埚来熔化硅 原料。
.
2
铸造多晶硅的优缺点
优点:
➢铸造多晶硅是利用特定铸造技术,在方形坩埚中制 备晶体硅材料,其生长简便,易于大尺寸生长,易 于自动化生长和控制,并且很容易直接切成方形硅 片;
➢材料的损耗小,同时铸造多晶硅生长相对能耗小, 促使材料的成本进一步降低,而且铸造多晶硅技术 对硅原料纯度的容忍度比直拉单晶硅高。
.
19
离子注入法:将N型(或P型)掺杂剂的离子束在静电 场中间加速,注入P型(或N型)半导体表面区域, 在表面形成型号与基体相反的半导体 ,从而形成 半导体。
薄膜生长法:在N型或P型半导体材料的表面,通过气 相、液相等外延技术生长一层具有相反导电类型的 半导体薄膜,从而形成PN结。
.
4
铸造多晶硅和直拉单晶硅的比较
晶体性质 晶体形态 晶体质量 能耗/(kW·h/kg) 晶体大小 晶体形状 电池效率/%
直拉硅单晶 单晶 无位错 >100
约300mm 圆形 15~17
铸造多晶硅 大颗粒多晶 高密度位错
约16 >700mm
方形 14~16
.
5
自从铸造多晶硅发明以后,技术不断改进, 质量不断提高,应用也不断广泛。在材料制备 方面,平面固液相技术和氮化硅涂层技术等技 术的应用、材料尺寸的不断加大。
.
1
自20世纪80年代铸造多晶硅发明和应用 以来,增长迅速,80年代末期它仅占太阳 电池材料的10%左右,而至1996年底它已
占整个太阳电池材料的36%左右,它以相 对低成本、高效率的优势不断挤占单
晶硅的市场,成为最有竞争力的太阳电池 材料。21世纪初已占50%以上,成为最主 要的太阳电池材料。
热交换等方式,使得熔体冷却,采用定向凝固技术 制造多晶硅——热交换法(Heat Exchange Method, HEM)。 ➢ 在坩埚内直接将多晶硅溶化,然后将坩埚以一定的 速度移出热源区域,从而建立起定向凝固的条件— —布里曼法(Bridgman)。
.
10
定向凝固法
与铸锭浇注法相比,定向凝固法有以下优点:
.
12
这种技术熔化和凝固可以在不同部位同时进行,节 约生产时间;而且,熔体和坩埚不直接接触,既没 有坩埚消耗,降低成本,又减少了杂质污染程度, 特别是氧浓度和金属杂质浓度有可能大幅度降低。
该技术还可以连续浇铸,速度可达 5mm/min。不 仅如此,由于电磁力对硅熔体的作用,使得掺杂剂 在硅熔体中的分布可能更均匀。
缺点:铸造多晶硅具有晶界、高密度的位错、微缺
陷和相对较高的杂质浓度,从而降低了太阳电池的光 电转换效率。
.
3
1、概述
利用铸造技术制备多晶硅,称为铸造多晶硅 (multicrystalline silicon,Mc-Si)。
铸造多晶硅中含有大量的晶粒、晶界、位错和杂 质,但由于省去了高费用额晶体拉制过程,所以 相对成本较低,而且能耗也较低,在国际上的到 了广泛应用。
显然,这是一种很有前途的铸造多晶硅技术。
.
13
这种技术制备出的铸造多晶硅的晶粒比较细小, 约为3-5mm,而且晶粒大小不均匀。而且,由图 6.9可以看出,该技术的固液界面是严重的凹形, 会引入较多的晶体缺陷。因此,这种技术制备的 铸造多晶硅的少数载流子寿命较低,所制备的太 阳电池的效率也较低。
.
14
铸造多晶硅的原材料
高纯多晶硅
微电子工业应单 晶硅生产的剩余料
微电 子工业 应单晶 硅生产 的剩余 料
质量相对较差的高纯多晶硅
单晶硅棒的头尾料 单晶硅生长完成后剩余在石英
坩埚中的硅底料
.
15
.
16
PN结的制备方法
在一块 N型(或P型)半导体单晶上,用适当的工艺方法 把P型(或N型)杂质掺入其中,使这块单晶的不同区域分别形 成N型和P型的导电类型,两者的交界处就形成了PN结。
在电池方面,SiN减反射层技术 、氢钝化技术、吸杂技术的开发和 应用,使得铸造多晶硅材料的电学 性能有了明显改善,其太阳电池的 光电转换率也得到了迅速提高。
.
6
由于铸造多晶硅的优势,世界各发达国 家都在努力发展其工业规模。自20世纪90年代以 来,国际上新建的太阳电池和材料的生产线大部 分是铸造多晶硅生产线,相信在今后会有更多的 铸造多晶硅材料和电池生产线投入应用。目前, 铸造多晶硅已占太阳电池材料的53%以上,成为 最主要的太阳电池材料。
.
7
2、铸造多晶硅的制备工艺
➢ 铸锭浇注法 ➢ 定向凝固法 ➢ 磁感应加热连续铸造(EMCP)
.
8
铸锭浇注法
在一个坩埚内将硅原料溶化,然后浇铸在另一个经 过预热的坩埚内冷却,通过控制冷却速率,采用定 向凝固技术制备大晶粒的铸造多晶硅。
.
9
定向凝固法
直接熔融定向凝固法,简称直熔法。 ➢ 在坩埚内直接将多晶硅溶化,然后通过坩埚底部的
制备方法主要有:
➢合金法 ➢扩散法 ➢离子注入法 ➢薄膜生长法 ➢……
.
17
把一受定特主温点型度:杂,NP质区区使小中中小施球受球主放主溶杂杂在解质质一,浓浓块度然度N为后为型NN降单DA,低,晶而也温硅且是度片均均,上匀匀熔分,分体布加布;开热。始到 凝固在,交在界N面型处硅,片杂上质形浓度成由一N含A(有P高型浓)突度变受为主N杂D(质N的型P )型,硅具薄有层这,种其杂与质分N型布硅的P衬N底结称的为交突界变面结处。即为PN结。
.
18
在N型(或P型)硅片中 ,利用扩散工艺掺入相反型 例号与体中通分扩:特过从,—的基,,入解散将点程通—P在区杂体从加,到PP及常:线低2这型到O质材而温半P杂称杂 性5表沉,种半N,料构至导质为质缓面区淀结导在相成体1P补缓的变浓是在02中体局反内PO0偿变分结度逐硅50N,放在部型,~决结。布结深渐片1杂入硅区号在2定由。。扩变表0质扩片域的硅0。扩散化面℃浓散表形半表散结的并,度炉面成导面 形成含高浓度磷的N型半导 体。
➢在同一个坩埚中进行熔炼与凝固成形,避免了熔体的二次 污染;
➢通过定向凝固得到的是柱状晶,减轻了晶界的不利影响; ➢由于定向凝固过程中的杂质分凝效应,对于硅中分凝系数
与1相差较大的杂质有一定的提纯作用。
缺点:能耗大,生产效率低,操作不连续、产能较小,坩埚 耗费大,其硅锭制备设备成本较高。
.
11
其原理是利用电磁感应的冷坩埚来熔化硅 原料。
.
2
铸造多晶硅的优缺点
优点:
➢铸造多晶硅是利用特定铸造技术,在方形坩埚中制 备晶体硅材料,其生长简便,易于大尺寸生长,易 于自动化生长和控制,并且很容易直接切成方形硅 片;
➢材料的损耗小,同时铸造多晶硅生长相对能耗小, 促使材料的成本进一步降低,而且铸造多晶硅技术 对硅原料纯度的容忍度比直拉单晶硅高。
.
19
离子注入法:将N型(或P型)掺杂剂的离子束在静电 场中间加速,注入P型(或N型)半导体表面区域, 在表面形成型号与基体相反的半导体 ,从而形成 半导体。
薄膜生长法:在N型或P型半导体材料的表面,通过气 相、液相等外延技术生长一层具有相反导电类型的 半导体薄膜,从而形成PN结。
.
4
铸造多晶硅和直拉单晶硅的比较
晶体性质 晶体形态 晶体质量 能耗/(kW·h/kg) 晶体大小 晶体形状 电池效率/%
直拉硅单晶 单晶 无位错 >100
约300mm 圆形 15~17
铸造多晶硅 大颗粒多晶 高密度位错
约16 >700mm
方形 14~16
.
5
自从铸造多晶硅发明以后,技术不断改进, 质量不断提高,应用也不断广泛。在材料制备 方面,平面固液相技术和氮化硅涂层技术等技 术的应用、材料尺寸的不断加大。