高炉供料系统设计
高炉车间原料供应系统(2)(ppt10页)

• 上料皮带的倾角最小110,最 大140。
• 皮带机的宽度随高炉容积而异, 保证皮带机运行安全非常重要。
高炉车间原料供应系统(2)(ppt10页)
3rew
演讲完毕,谢谢听讲!
再见,see you again
2021/1/4
高炉车间原料供应系统(2)(ppt10页)
高炉车间原料供应系统(2)(ppt10页)
•卸料曲轨形式:
高炉车间原料供应系统(2)(ppt10页)
•4.4.2 皮带机上料系统
•优点: •①可以将贮矿槽等设施远离高炉; •②上料能力大,效率高而且灵活,炉料 破损率低;
•③减轻了设备重量,简化了控制系统。 •宝钢高炉贮矿槽的工艺布置图:
高炉车间原料供应系统(2)(ppt10页)
•三. 方式: • 有料罐式、料车式和皮带机上 料三种方式。
高炉车间原料供应系统(2)(ppt10页)
•4.4.1 斜桥料车式上料机
•1. 组成: •①提升的容器——料车; •②斜桥; •③卷扬机。
高炉车间原料供应系统(2)(ppt10页)
•2. 料车 •前后两对车轮构造不同。 •3. 斜桥 • 倾角一般为55º~65º。 • 设两个支点,下端支撑在料车坑 的墙间原料供应系统 (2)(ppt10页)
2021/1/4
高炉车间原料供应系统(2)(ppt10页)
•一. 概念: •上料机:指将炉料直接送到高炉炉顶
•
的设备。
•二. 对上料机的要求 :
•①足够的上料能力 ;
•②工作稳妥可靠;
•③最大程度的机械化和自动化。
高炉车间原料供应系统(2)(ppt10页)
•皮带机上料工艺流程
•1-贮矿槽(S-烧结矿、O-球团矿、P-块矿、M-杂矿);2-输出皮带机(一);3-输出 皮带机(二);4-贮焦槽;5-焦炭输出皮带机;6-中央称量室;7-粉焦输出皮带机;8-粉
韶钢2500m3高炉供上料系统的设计特点

高炉双排矿 、焦贮槽布置在高炉西侧,高炉所使用的
原 、燃料 ( 烧结 矿 、球 团矿 、块 矿 、杂 矿和 焦 炭) 分别 由 中 冶华 天工 程技术 有 限公 司的烧 结车 间 、原料 场和 焦化 车间 经胶 带机 运送 到高 炉原 、燃料 贮槽 。贮 槽为 双排 布置 ,共 设1 8 个 贮槽 。其 中6 个烧 结 矿 槽 ,贮 存 时 间2 0 . 5 h ;5 个 焦
图 1 槽 下 供 料 系统 工 艺 流 程
贮槽 中炉 料经 手动 闸 门、振动 筛或给 料机 、称 量漏斗 称 量 后按 上料程 序卸 在槽 下主胶 带机 上 。本系 统设 计采 用
了一些 先进 、实 用的技 术 。
槽, 贮存肘 间1 7 . 7 h ;3 个球 团矿槽, 贮存时间2 4 . 5 h ;2 个块
限公 司工作 ,高级工程 师,全 国注册咨询工程师 。E — ma i l : w a n g 的除尘罩与漏斗本体相互独立 ,提高了炉料称量的准确
y a n h i @h t z y . c n
性 。所有 称量 漏斗 闸 门均为 液压传 动 ,称 量采用 压力 传感
一
5 O 一
第5 期 总第1 4 5 期
遥控 操作 ;机旁操 动提供 故 障或调 试时 的现场操 作 。 另外 ,为 了满 足 生 产 需要 ,在 槽 下主 胶 带机 水 平 段
设置 一 套 取 样装 置 ,该装 置 为 机 旁 手动 ,可 以从 运 行 的
S HA NXI ME T A L L UR GY
N 0. 5
T ot al of1 45
器 ,称 量 漏 斗 既 可 采用 砝 码 校 秤 ,也可 采 用 标 准 压 力传 感 器校 秤 。各种 物料 均实 现称 量误 差 自动 补正 。
毕业设计---高炉原料供应系统设计
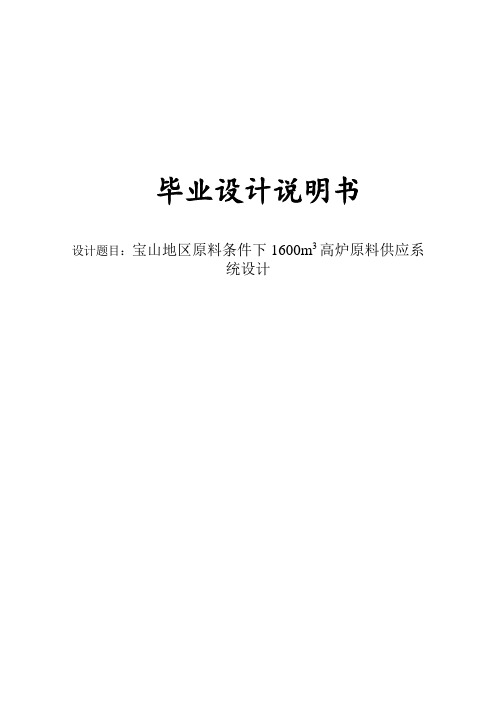
毕业设计说明书设计题目:宝山地区原料条件下1600m3高炉原料供应系统设计摘要在本设计中,槽上槽下均采用皮带供料系统,槽下胶带运输机供料与称量漏斗相配合,是高炉槽下实现自动化操作的最佳方案。
串罐式无料钟炉顶的称量料罐卸料支管中心线与波纹管中心线以及高炉中心线一致,避免了下料和布料过程中的粒度和体积偏析,通过布料溜槽的旋转和倾动、料流调节阀的排料控制,可实现多种布料方式,适应各种炉况的上部调节要求,布料均匀,使高炉装料操作简单化,有利于高炉的稳定和长寿。
关键词:高炉炉顶;串罐无料钟炉顶;供料系统;皮带上料AbstractIn this design, groove groove adopts belt feeding system, under the trough belt conveyor feeding and weighing hopper matched under BF trough, is to realize the automated operation optimal scheme.Hopper type bell-less furnace top of the weighing tank discharging branch pipe with the center line of corrugated pipe center line and center line of blast furnace, avoids the discharging and charging process in size and volume of segregation, by distributing chute rotation and tilting, material flow regulating valve discharge control, can achieve a variety of distribution mode, to adapt to a variety of furnace condition of the upper adjusting requirements, uniform distribution, so that the blast furnace charging operation is simple, is conducive to the stability and long life of blast furnace.Key words: blast furnace; bell furnace top; feeding system; belt conveyor目录摘要...................................................................................................................................... - 1 -Abstract ........................................................................................................................................ - 2 -1文献综述 (1)1.1高炉料车上料与皮带上料的比较 (1)1.1.1前言 (1)1.1.2国内外上料方式的实例 (1)1.1.3料车上料与皮带上料的投资比较 (3)1.1.4料车上料与皮带上料的运行费比较 (3)1.2无钟炉顶装料设备 (4)1.2.1串罐式无料钟炉顶设备 (4)1.2.2串罐式无料钟炉顶装置 (5)1.2.3四种布料控制方式 (7)1.3探料装置 (8)1.3.1高炉探尺工作原理 (8)1.3.2微波式料面计 (9)1.3.3激光扫描系统 (9)1.3.4高炉料面红外线摄像仪 (9)1.3.5十字测温装置 (9)1.3.6操作流程 (10)1.4确定初步方案 (10)2高炉上料系统设计计算 (12)2.1贮矿槽和贮焦槽个数、总容积及主要尺寸的确定 (12)2.2电磁振动给料机的设计 (13)2.3料批重量的确定 (13)2.4槽下筛分设备 (14)2.5称量设备 (14)2.5.1矿石称量漏斗 (14)2.5.2焦炭称量漏斗 (14)2.6槽下运输设备 (15)2.7输送胶带的选择 (15)2.7.1矿石输送胶带YK (15)2.7.2焦炭输送胶带YJ (15)2.8上料主胶带机 (15)2.8.1上料主胶带机选择 (15)2.8.2上料主胶带机上料能力的检验 ........................................................................................2.8.3碎焦和返矿胶带输送机 (16)2.9废铁清除装置 (16)3串罐式无料钟炉顶装料设备 (17)3.1串罐式无料钟炉顶 (17)3.1.1串罐式无料钟炉顶的优点 (17)3.1.2串罐式无料钟高炉的布料方式 (17)3.1.3串罐式无料钟炉顶的主要设计参数表 (17)3.1.4串罐式无料钟炉顶装料设备性能及参数计算 (17)3.1.5固定受料斗 (18)3.1.6上部料流阀和上密封阀\ (19)3.1.7称量料罐 (19)3.1.8中心喉管 (20)3.1.9布料器(传动机构)及旋转溜槽 (21)3.1.10电子秤 (21)3.1.11均压、放散装置 (21)3.1.12炉顶钢圈 (21)3.1.13探尺 (21)3.1.14高炉炉顶其它系统 (22)结论 (23)参考文献 (24)致谢 (25)1文献综述1.1高炉料车上料与皮带上料的比较1.1.1前言高炉上料方式应以满足总图布置要求和满足上料能力为前提来选择合理的上料方式,对750m3~1500m3级高炉来说,料车上料与皮带上料均能满足上料能力的要求,在这种情况下,若在总图布置与工艺布置上无优势,如无地形高差优势,无物料输送短捷优势,则宜采用料车上料方式。
高炉自动上料(配料)控制系统的设计与制作

课题:高炉自动上料(配料)控制系统的设计与制作系部:机电工程学院专业:电气自动化技术班级:姓名:李瑞学号:指导老师:2019.3.15目录摘要 (31)第一章序言 (31)1.1课题意义 (32)1.2课题来源 (33)1.3国内外高炉自动控制系统的研究现状和趋势 (33)1.3.1高炉计算机控制发展 (33)1.3.2炼铁自动化技术的现状 (34)1.3.3高炉自动化系统的发展趋势 (34)1.4毕业设计主要任务 (35)1.5本章小结 (35)第2章高炉上料生产工艺 (35)2.1高炉上料系统的组成与工作原理 (36)2.1.1高炉上料系统自动控制概述 (37)2.1.2高炉上料控制系统流程 (37)2.2高炉炼铁生产工艺简介 (39)第三章可编程控制器及PID控制 (39)3.1可编程控制器 (40)3.2PID控制 (41)第四章高炉上料系统的软件设计 (42)4.1PLC程序设计 (42)4.2槽下设备运转控制 (45)4.3主卷上料小车的连锁控制 (45)结束语 (47)谢辞 (47)参考文献 (48)在冶金企业中,高炉给料系统是一个非常重要的复杂的设备系统。
为了保证高炉进料的稳定、安全、高效工作,高炉进料计算机自动控制的设计与实现显得尤为重要。
在提高控制系统控制精度的基础上,进一步提高了高炉进给操作的可靠性、安全性和稳定性,为高炉的生产提供了可靠的保证。
本文结合实际科研项目——高炉进料系统自动改造,开发设计了一套高炉进料生产线自动控制系统。
本项目跟踪国内外先进技术,采用目前先进的无钟炉具设备,提高设备可靠性,降低备件消耗,节约成本。
在国内外生产过程控制技术发展的基础上,开发设计了可编程控制器控制系统。
在本系统中,PLC作为核心部件,对整个生产线起到监控作用,各种电磁阀等机械部件发出控制指令,并结合组态软件完成论文的要求。
根据PLC的输入和输出点进行硬件配置;根据PLC编程的特点,采用与工厂电路图最接近的方法——梯形图编制软件,并将软件划分为几个模块。
任务6高炉供料系统

电子式称量漏斗
(1)原理:漏斗受载后,传感元件受压变形, 贴在传感元件上的电阻应变片也随之产生相应变 形,因此改变了应变片的电阻值,使得原先的电 桥失去平衡,从而输出一个微小的电压信号,然 后将这个信号经仪表放大,这种电参数可从仪表 上称量读出。
(2)优点:体积小,质量轻,结构简单,装拆 方便,而且称量精度高,克服了刃口磨损的缺点 。(精度高,误差不超过5/1000)
称量漏斗的维护检查
(1)每周检查一次斗体是否有磨损、变形、 开裂等情况。 (2)每周检查一次闸门的性能状态。 (3)若是液压闸门检查液压装置是否漏油, 是否牢固。 (4)信号装置有无缺陷,显示是否正确。
称量漏斗闸门及传动装置
工作原理:通过传感器把料量信号输送给 电控室,然后经自动或手动操作闸门,把 料放入料车。
给料机是利用振动器中的偏心块旋转产生离心 力,使筛厢、振动器等可动部分作强制的连续 的圆或近似圆的运动。 给料机是由给料槽体、激振器、弹簧支座、传 动装置等组成。槽体振动给料的振动源是激振 器,激振器是由两根偏心轴(主、被动)和齿 轮副组成,由电动机通过三角带驱动主动轴, 再由主动轴上齿轮啮合被动轴转动,主、被动 轴同时反向旋转,使槽体振动,使物料连续不 断流动,达到输送物料的目的。
给料机的维护
(1)各紧固件紧固是否完好无损,弹簧是否 有移动,错位。 (2)箱体料斗不磨碰周围物体,箱体无开裂 变形,磨损是否严重。 (3)除尘密封装置是否完好。 (4)给料机是否均匀,顺畅。
振动筛
为改善高炉料柱透气性,大、中型高炉要 求将入炉焦炭小小于20一25mm的小焦块及粉 末和矿石中小于5mm的粉末筛除。
称量漏斗
称量漏斗的作用在于称量原料,使原料组成一 定成分的料批。 根据称量传感器原理,称量 漏斗可分为机械秤、电子秤和机械电子秤称量 漏斗。
高炉炼铁配料计算系统的设计和实现
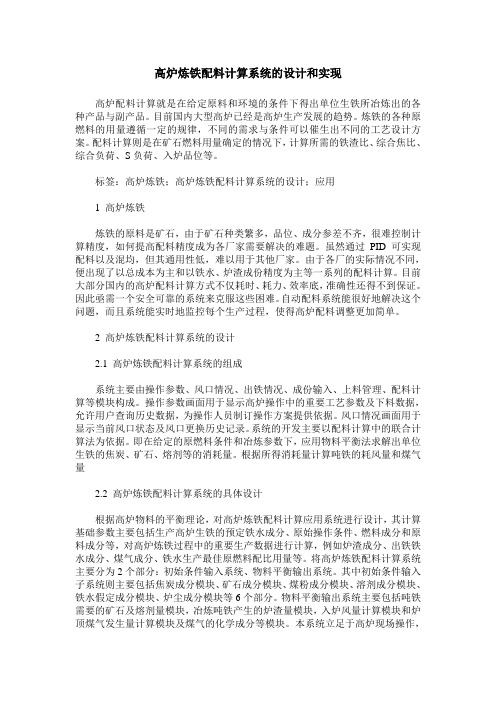
高炉炼铁配料计算系统的设计和实现高炉配料计算就是在给定原料和环境的条件下得出单位生铁所冶炼出的各种产品与副产品。
目前国内大型高炉已经是高炉生产发展的趋势。
炼铁的各种原燃料的用量遵循一定的规律,不同的需求与条件可以催生出不同的工艺设计方案。
配料计算则是在矿石燃料用量确定的情况下,计算所需的铁渣比、综合焦比、综合负荷、S负荷、入炉品位等。
标签:高炉炼铁;高炉炼铁配料计算系统的设计;应用1 高炉炼铁炼铁的原料是矿石,由于矿石种类繁多,品位、成分参差不齐,很难控制计算精度,如何提高配料精度成为各厂家需要解决的难题。
虽然通过PID可实现配料以及混均,但其通用性低,难以用于其他厂家。
由于各厂的实际情况不同,便出现了以总成本为主和以铁水、炉渣成份精度为主等一系列的配料计算。
目前大部分国内的高炉配料计算方式不仅耗时、耗力、效率底,准确性还得不到保证。
因此亟需一个安全可靠的系统来克服这些困难。
自动配料系统能很好地解决这个问题,而且系统能实时地监控每个生产过程,使得高炉配料调整更加简单。
2 高炉炼铁配料计算系统的设计2.1 高炉炼铁配料计算系统的组成系统主要由操作参数、风口情况、出铁情况、成份输入、上料管理、配料计算等模块构成。
操作参数画面用于显示高炉操作中的重要工艺参数及下料数据,允许用户查询历史数据,为操作人员制订操作方案提供依据。
风口情况画面用于显示当前风口状态及风口更换历史记录。
系统的开发主要以配料计算中的联合计算法为依据。
即在给定的原燃料条件和冶炼参数下,应用物料平衡法求解出单位生铁的焦炭、矿石、熔剂等的消耗量。
根据所得消耗量计算吨铁的耗风量和煤气量2.2 高炉炼铁配料计算系统的具体设计根据高炉物料的平衡理论,对高炉炼铁配料计算应用系统进行设计,其计算基础参数主要包括生产高炉生铁的预定铁水成分、原始操作条件、燃料成分和原料成分等,对高炉炼铁过程中的重要生产数据进行计算,例如炉渣成分、出铁铁水成分、煤气成分、铁水生产最佳原燃料配比用量等。
炼铁厂高炉进料72系统控制设计

目录引言........................................................ - 1 -第一章系统组成........................................ - 2 -第二章电气控制要求.................................... - 3 -第三章 72系统工艺流程................................. - 5 -第四章 72系统设备控制说明............................. - 6 -第五章 PLC自动控制系统配置............................ - 8 -第六章系统的软件编程................................. - 10 -第七章监控画面的组态设计............................. - 11 -结束语.................................................. - 15 -参考文献................................................ - 15 -致谢.................................................. - 16 -附:南昌航空大学自学考试毕业论文指导登记表(二)摘要:PLC控制己深入到人们的各行各业生产活动中,技术己十分成熟,其具有控制灵活、运行可靠、故障少、操作维护改进方便、便于监控、经济等许多明显的优点,已广泛应用于包括大中小型炼铁高炉等各个控制系统,在各自动控制系统中PLC的应用己成为主流及首选。
本文就炼铁厂高炉进料72系统电气控制项目的图纸设计、西门子引言(一)PLC的基本概念1、早期的可编程控制器称作可编程逻辑控制器(Programmable Logic Controller,PLC),它主要用来代替继电器实现逻辑控制。
2500m3高炉串罐式炉顶装料系统设计

2500m3高炉串罐式炉顶装料系统设计于丹① 王振虎(北京中冶设备研究设计总院有限公司 北京100029)摘 要 串罐式无料钟炉顶是高炉布料的主要方式,本文详细介绍了其系统组成,旋转溜槽是其主要工作部件,上部调节的预期目标依靠灵活的溜槽布料来实现,相关装置主要包括:称量罐、受料斗、阀箱、布料器,并配置了均排压系统、液压系统、气密系统、冷却系统等,串罐式设计保证料罐中心线与高炉中心线一致,避免了下料和布料过程中的粒度和体积偏析,使料面形状更容易控制,更能发挥布料功能潜力,有利于高炉上部块状带煤气化学能和热能的充分利用。
关键词 高炉炉顶 串罐 布料方式中图法分类号 TG57 TF573 TF542+.2 文献标识码 ADoi:10 3969/j issn 1001-1269 2023 04 009TheLoadingSystemDesignofSerial hopperBell lessTopof2500m3BlastFurnaceYuDan WangZhenhu(BeijingMetallurgicalEquipmentResearchDesignInstituteCo.,Ltd.,Beijing100029)ABSTRACT Serial hopperbell lesstopismajorequipmentforBFtodistributerawmaterial,thispaperintroduceitsconstituentpartindetail,TherotarychuteinchargeofdistributematerialinthescheduledwaytoachieveBFoperategoals,associatedequipmentincluding:weighingchargebucket、receivinghopper、valvestation、spreader,andrelevantsystemsuchasboostersystem、hydraulicsystemsealgassystemcoolingsystemalsoassembled,centerlineoftheweighingbucketisconsistentwiththecenterlineofthebellow,whichcanavoidtheparticlesegregationandthevolumesegregationduringtheblanking.Allofthesethingsmaketheoperationoftheblastfurnacesimplisticandisconducivetoenhancegasutilizationofheatandthermalenergycomefromupperpartinblastfurnace.KEYWORDS Blastfurnacetop Serial hopper Distributingmode1 前言目前,大型高炉每昼夜需要消耗大量原、燃料。
高炉上料系统施工方案

高炉上料系统施工方案1 引言高炉上料系统是高炉炼铁的关键环节之一,直接影响到生产效率和产品质量。
本文档旨在提供一个高炉上料系统施工方案,包括系统的设计、安装、调试等方面的内容。
2 系统设计2.1 系统功能高炉上料系统的主要功能包括原料的输送与配比、料斗的卸料、输送线的控制和监测等。
具体功能如下: - 原料配比:根据高炉冶炼工艺要求,将不同种类和比例的原料按照要求进行配比。
- 料斗卸料:将配制好的原料从料斗中卸下,并送入相应的输送线。
- 输送线控制:控制输送线的启停、速度调节等,确保原料的顺利输送。
- 监测:对原料的流量、温度、湿度等进行监测,以便及时调整系统参数。
2.2 系统组成高炉上料系统主要由以下几个部分组成: - 天车:用于将原料从存料仓库中取出,运送到指定的料斗。
- 料斗:用于存放原料,并通过卸料口将原料送入输送线。
- 输送线:用于将原料从料斗中输送到高炉的上料口。
- 控制系统:包括PLC控制、传感器监测和人机界面等,用于控制和监测整个系统的运行。
3 施工过程3.1 前期准备在施工之前,需要进行一系列的前期准备工作,包括: - 设计方案:根据高炉的工艺要求和现场情况,制定高炉上料系统的设计方案。
- 采购原材料和设备:根据设计方案,采购所需的原材料和设备。
- 组织人员:安排项目经理、施工人员和监理人员等,确保施工过程的顺利进行。
3.2 安装和调试安装和调试是高炉上料系统施工的关键环节,包括以下步骤: - 天车安装:将天车安装在指定位置,并进行调试,确保其正常运行。
- 料斗安装:将料斗安装在指定位置,并与天车和输送线连接,进行调试。
- 输送线安装:将输送线安装在指定位置,并与料斗和高炉上料口连接,进行调试。
- 控制系统安装:安装PLC控制器、传感器和人机界面,进行调试和联动测试。
3.3 系统验收在施工完成后,进行系统验收是必不可少的步骤。
验收过程中需要完成以下内容: - 系统功能测试:对高炉上料系统的各项功能进行测试,检查其是否满足设计要求。
钢铁厂高炉供料自动控制系统改造设计
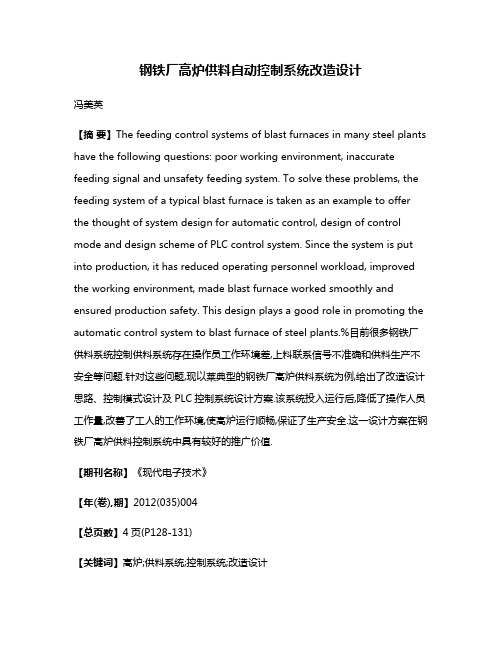
钢铁厂高炉供料自动控制系统改造设计冯美英【摘要】The feeding control systems of blast furnaces in many steel plants have the following questions: poor working environment, inaccurate feeding signal and unsafety feeding system. To solve these problems, the feeding system of a typical blast furnace is taken as an example to offer the thought of system design for automatic control, design of control mode and design scheme of PLC control system. Since the system is put into production, it has reduced operating personnel workload, improved the working environment, made blast furnace worked smoothly and ensured production safety. This design plays a good role in promoting the automatic control system to blast furnace of steel plants.%目前很多钢铁厂供料系统控制供料系统存在操作员工作环境差,上料联系信号不准确和供料生产不安全等问题.针对这些问题,现以莱典型的钢铁厂高炉供料系统为例,给出了改造设计思路、控制模式设计及PLC控制系统设计方案.该系统投入运行后,降低了操作人员工作量,改善了工人的工作环境,使高炉运行顺畅,保证了生产安全.这一设计方案在钢铁厂高炉供料控制系统中具有较好的推广价值.【期刊名称】《现代电子技术》【年(卷),期】2012(035)004【总页数】4页(P128-131)【关键词】高炉;供料系统;控制系统;改造设计【作者】冯美英【作者单位】柳州职业技术学院,广西柳州 545006【正文语种】中文【中图分类】TN911-34;TP2740 引言目前很多钢铁厂供料系统控制基本上均存在以下问题:操作员工作环境差;上料联系信号不准确;供料生产不安全等问题。
探讨高炉上料自动控制系统的设计

探讨高炉上料自动控制系统的设计1、引言高炉炼铁在钢铁冶金行业中,是最重要的组成部分。
高炉炼铁是一个连续的过程,其通过氧化还原反应,将铁矿石还原生成生铁。
各种原料包括铁矿石、焦炭和助熔剂按成分比例,由炉顶加料装置批次被送至高炉内,炉喉面要维持在一定的高度。
铁矿石和焦炭在炉中变化成为交替的层状结构,在下降的过程中,矿石逐渐变成铁水和熔渣,聚集在炉中,并定期从释放口放出。
高炉供料系统是炼铁生产的重要组成部分,供料系统通过料车分开,分为配料系统和上料系统前后两部分,本文主要阐述上料系统的硬件和软件的设计。
2、高炉上料系统自动控制概述高炉上料系统由槽下配料部分和炉顶布料部分两部分组成。
槽下配料是实现原料称量工作和称量误差补偿工作的系统设备,当炉顶料灌具备装料,同时矿槽具备排料时,原料由料车输送至炉顶,经过受料斗闸门、上密封阀送至对应料灌内。
料管内发出料满信号同时具备布料条件时,原料通过料流調节阀、下密封阀,依照设置好的布料溜槽倾动角旋和转角度进入炉中。
3、高炉上料系统的软件设计在高炉上料自动控制系统中,通过PLC编程,可以完成对高炉上料系统的槽下配料和炉顶布料的控制。
设定所需铁矿石、焦炭、溶剂的重量,振动给料筛启动进行筛料,实际重量与设定值相等时,振动给料停止。
高炉上料控制系统的软件部分采取结构化编程方法,将不同功能的程序分别寄存于不同的块中,主程序块OB1在使用时可以调用不同功能的程序。
3.1槽下设备运转控制(1)烧结、焦炭、球团、焦丁称量斗的称量控制:发出排料信号时,矿石称量斗闸门开启排料。
称量值是控制值得5%时,称量斗闸门关闭,料空信号发出。
称量斗闸门关闭并称空后,振动筛启动运行。
称量值达到经补正的控制值时,振动筛停止,进行满称量。
当达到110%的经补正控制值时,报警信号发出。
启动振动筛T秒后,一直未发出斗满信号,则认为发生上卡料情况,上卡料报警。
打开闸门打开T秒后,未出现空信号,则认为发生下卡料情况,下卡料报警。
高炉供料系统设计

第四章高炉供料系统设计4.1贮矿槽和贮焦槽个数、总容积及主要尺寸确定矿槽和焦槽的上下部均采用胶带机运输设施。
要求烧结矿和球团矿的温度不高于80℃且胶带倾角不大于16°和13°,胶带速度不大于2m/s。
焦槽、矿槽主要的作用是满足高炉生产、配料和调节的要求。
为了解决烧结设备检修时能向高炉正常供料,一般考虑原料、燃料落地贮存设施。
贮矿槽的容积和个数主要取决于高炉的有效容积、矿石品种和需要贮存的时间。
单个贮矿槽的容积也可以相同,也可以不同。
当设置主矿槽和备用矿槽时,一般是主矿槽的容积比较大。
杂矿的数目应根据杂矿的品种和需要量来确定。
贮矿槽可以是单列设置,也可以是双列设置。
双列设置时,槽下运输显得比较拥挤,工作条件差,检修设备不方便。
贮矿槽的数目在有条件时经量减少。
一般不少于10个,最多可达30个。
在本设计中槽上供料系统设有两条带式输送机,将高炉原料送至贮矿槽和贮焦槽,槽下供料系统设有烧结矿、焦炭槽、球团矿槽和杂矿槽,呈一列式布置,贮矿槽和贮焦槽下设有给料、筛分、称量设备和一条运矿、运焦主皮带机,一条返矿皮带机,一条反胶皮带机。
设有12个贮矿槽,其中六个为烧结矿槽,四个为球团矿槽,两个为杂矿槽。
2000m³高炉贮矿槽容积相当于高炉有效容积的1.6倍[21]。
则V=2000×1.6=3200m³贮矿贮存时间应满足高炉12~24h的消耗量,其中高炉烧结矿的贮存时间为9~14h,其他原料的贮存时间大于12h。
在本设计中,烧结矿的贮存时间为12h,球团矿贮存时间为28h。
槽下采用皮带上料时,矿槽长度一般为5000mm。
矿槽的高度取决于高炉容积和槽上槽下运输方式,大中型高炉一般为10~11m,不宜超过14m,矿槽宽度要能布置下2~3条胶带运输机(胶带宽度为800mm~1400mm),矿槽壁倾斜角为50o~55o。
本设计中,烧结矿槽和球团矿槽的长度定为5000mm,杂矿槽的长度定为3200mm,宽度都定为5600mm。
高炉智慧系统设计方案,1200字

高炉智慧系统设计方案智能高炉系统设计方案一、引言高炉是钢铁冶炼中非常重要的设备,其性能的优劣直接关系到冶炼质量和生产效率。
随着人工智能和物联网技术的不断发展,智能高炉系统的设计和应用已经成为了钢铁行业的研究热点。
本文将介绍一种智能高炉系统的设计方案,以提升高炉的冶炼效率和降低能耗。
二、系统结构智能高炉系统包括传感器、信号采集模块、数据处理模块、控制模块和人机界面等组件。
1. 传感器:通过安装在高炉的各个部位的传感器,实时采集高炉的各种参数,包括高炉温度、煤气成分、压力、风温风量、物料厚度等。
2. 信号采集模块:负责将传感器采集到的数据进行采集和转换,将模拟信号转换成数字信号,并通过通信接口传送给数据处理模块。
3. 数据处理模块:主要负责对采集到的数据进行分析和处理,通过算法模型对高炉的状态进行监测和预测。
该模块可以具备机器学习和深度学习的能力,通过训练模型对高炉的运行状态进行预测和优化。
4. 控制模块:根据数据处理模块的分析结果和预测结果,实时调节高炉的工艺参数,包括风温风量、喷煤量、加料量等,以实现高炉的自动化控制。
5. 人机界面:提供给操作人员进行设置参数、监控状态和报警等功能的界面,可以通过计算机、手机或者触摸屏等方式实现。
三、主要功能和特点1. 实时监测和预测:智能高炉系统通过传感器实时采集高炉的各种参数,并通过数据处理模块对高炉的状态进行监测和预测,可以及时发现并解决潜在问题,提高高炉的冶炼效率。
2. 自动调节控制:智能高炉系统根据数据处理模块的分析结果和预测结果,自动调节高炉的工艺参数,实现高炉的自动化控制,减少人为干预,降低操作风险,提高冶炼效率和产品质量。
3. 数据分析和优化:智能高炉系统通过机器学习和深度学习的算法模型对高炉的运行数据进行分析和优化,通过精确的预测和优化,调节高炉的工艺参数,提高冶炼效率,降低能耗。
4. 实时报警和故障诊断:智能高炉系统可以根据数据处理模块的分析结果,实时监测高炉的运行状态,并发出报警信号,及时预警和处理潜在问题;同时,还可以通过故障诊断模块对高炉的故障进行诊断,并给出相应的解决方案。
2800m3高炉原料及炉顶装料系统设计

包头原料条件下2800m3高炉原料及炉顶装料系统设计(专业:冶金工程班级:冶金06-1班姓名:张彩云指导老师:侯贵平)摘要:在本设计中,槽上槽下均采用皮带供料系统,槽下胶带运输机供料与称量漏斗相配合,是高炉槽下实现自动化操作的最佳方案。
串罐式无料钟炉顶的称量料罐卸料支管中心线与波纹管中心线以及高炉中心线一致,避免了下料和布料过程中的粒度和体积偏析,通过布料溜槽的旋转和倾动、料流调节阀的排料控制,可实现多种布料方式,适应各种炉况的上部调节要求,布料均匀,使高炉装料操作简单化,有利于高炉的稳定和长寿。
关键词:高炉炉顶;串罐无料钟炉顶;供料系统;皮带上料Design of 2800 m3 Blast Furnace Meterials and the Top Charging System Under the Conditions of Baotou Raw Materials Abstract:This design uses the blet for the feeding system. The best way of realizing automatic operation under tanks is the coorperation between the weighing hopper and the feeding of belt transporter under tanks.By comparison,because the center line of the weighing bucket is consistent with the center line of the bellow,the string-up bucket type bell-less top can avoid the pratide segregation and the volume segregation during the blanking and the mix feeding. Through the rotation and the tilting of the rotating chute ,and the control of the material flow gate,the furnace can achieve various distributing modes to adapt kinds of furance conditions which the upside request.All of these things make the operation of the blast furance simplistic and is conducive to the stability and longevity of BF.Key words:blast furnace top; the string-up bucket type; material supply system; belt charging前言现代大型高炉每昼夜连续需要原、燃料上万吨。
基于PLC的高炉上料自控系统设计

基于PLC的高炉上料自控系统设计摘要本设计介绍了西门子S7-200 PLC在炼铁高炉上料料控制系统中的运用,通过西门子S7-200PLC与高炉上料系统的结合,设计出可编程序控制器的控制装置,基本上完成了120m³高炉供料电气控制系统的硬件设计。
实现了布料(槽上)和槽下卷扬的实时控制和生产过程自动化的目的。
基于PLC的高炉上料自控系统的设计,提高了高炉上料控制系统的自动化水平、可靠性,实现了上料系统的实时监控和灵活方便。
具有一定的参考应用价值。
关键词:可编程序控制器高炉上料系统自动控制PLC-BASED AUTOMATIC CONTROL SYSTEM OFBLAST FURNACE DESIGNABSTRACTThe S7-200 PLC of SIMATIC Company was successfully applied in the control system of the feed-in the raw materials of the blast furnace. Siemens S7-200 PLC combine with blast furnace charging system,from a scheme of control device of programmable controller,finish the hardware design of electrical control system of 120m³blast furnace material loading.Have realized the purpose of the realtime control of material providing and production process automation under the through and rise. Have used PLC in the design,There is a growing interest for the application of PLC and its networks in the field of industrialautomation. The automatic function and reliability of the feeding system in blast furnace are improved by the application.The realtime monitoring is realized and the technological composition can be easily made.KEY WORDS plc blast furnace charging system automatic control目录中文摘要 (I)英文摘要 (II)1绪论 (1)1.1高炉上料系统的作用与地位 (1)1.2高炉上料系统的传统控制方式 (1)1.3 高炉上料系统PLC控制方式 (2)2总体方案设计 (3)2.1 炼铁工艺过程概述 (3)2.2高炉上料设备及工艺简介 (3)2.3操作方式 (5)2.4控制方式 (5)2.5设计概述 (6)3PLC控制系统设计 (7)3.1PLC简介 (7)3.1.1可编程控制器的发展史 (7)3.1.2PLC的硬件组成结构 (8)3.2I/O点分配 (9)3.3PLC控制电路的设计 (11)3.3.1PLC控制器选型及硬件配置 (11)3.3.2料车上料系统 (11)3.3.3高炉料钟装料系统 (13)3.3.4探尺系统 (15)3.3.5电气控制系统原理图 (16)4 PLC控制系统软件设计方案 (19)4.1Step7软件介绍 (19)4.2 PLC控制程序的设计 (19)4.2.1程序的基本结构 (19)4.2.2动作流程图 (19)4.2.3梯形图设计 (21)5模拟调试 (25)6结论 (29)致谢 (30)参考文献 (31)1 绪论1.1高炉上料系统的作用与地位高炉是炼铁或者炼钢生产的核心设备,是一种规模大、要素多、要求严格的冶炼过程,其良好的运行能为后续的生产过程提供充足而优质的原料保证,这对控制系统的可靠性提出了较高的要求。
邯钢老区3200m3高炉槽下上料系统设计实施

邯钢老区3200m3高炉槽下上料系统设计实施摘要:本文详细介绍了邯钢老区3200m3高炉槽下上料系统的工艺流程,控制系统功能描述,艾默生DCS控制系统OV ATION-XP的硬件组成和软件组态特点。
关键词:上料工艺Ovation Fast Ethernet自动控制1 槽下供料系统工艺流程简介1.1工艺流程槽下供料系统由矿槽、焦槽、给料机、振动筛、称量斗、皮带运输机等组成。
焦炭贮存运输系统和矿石贮存运输系统分别单独设置,构成两个独立、并列的系统。
1.1.1焦炭贮存运输系统焦槽卸下的焦炭采用分散筛分称量和集中称量。
共设有6个焦槽。
焦炭经手动闸门卸到振动筛进行筛分,合格焦炭(≥25mm)落入焦炭称量斗称量后按程序卸到供焦皮带机后运至集中称量斗进行称量,而后按程序打开集中称量斗闸门将焦炭卸到上料胶带机转运至高炉炉顶。
合格的焦丁(1025mm) 由焦丁皮带机转运至焦丁仓,并根据需要装入称量斗称量,再卸到供矿皮带机上,按装料程序与矿石混合后运至高炉炉顶。
1.1.2矿石贮存运输系统矿槽卸下的矿石采也用分散筛分称量+集中称量的工艺流程。
共设有16个矿槽,由程序控制放料顺序。
矿石经手动闸门和振动给料机卸到矿石振动筛上进行筛分,筛除=S,则烧结实际放料值为S;4 在A+B模式下,若W=S,则块杂实际放料值为W-S;4 在A+B模式下,若W<S,则块杂实际放料值为0。
3 控制系统的配置3.1网络组态Ovation网络结构采用的是一种二层网络组态方式,即为Root根级、Fanout 级两层,两级均由Fast Ethernet组成,且CPU成对配置,相应各个网络设备也采用冗余配置,而且是热冗余,一旦当前设备故障,立即切换到热备。
配置如图1:3.2软件设计3.2.1计算机操作系统该控制系统使用1台服务器,1台历史站,2台操作站,操作站操作系统使用WindowsXP-sp2。
服务器和历史站操作系统用Windows2003。
- 1、下载文档前请自行甄别文档内容的完整性,平台不提供额外的编辑、内容补充、找答案等附加服务。
- 2、"仅部分预览"的文档,不可在线预览部分如存在完整性等问题,可反馈申请退款(可完整预览的文档不适用该条件!)。
- 3、如文档侵犯您的权益,请联系客服反馈,我们会尽快为您处理(人工客服工作时间:9:00-18:30)。
第四章高炉供料系统设计4.1贮矿槽和贮焦槽个数、总容积及主要尺寸确定矿槽和焦槽的上下部均采用胶带机运输设施。
要求烧结矿和球团矿的温度不高于80℃且胶带倾角不大于16°和13°,胶带速度不大于2m/s。
焦槽、矿槽主要的作用是满足高炉生产、配料和调节的要求。
为了解决烧结设备检修时能向高炉正常供料,一般考虑原料、燃料落地贮存设施。
贮矿槽的容积和个数主要取决于高炉的有效容积、矿石品种和需要贮存的时间。
单个贮矿槽的容积也可以相同,也可以不同。
当设置主矿槽和备用矿槽时,一般是主矿槽的容积比较大。
杂矿的数目应根据杂矿的品种和需要量来确定。
贮矿槽可以是单列设置,也可以是双列设置。
双列设置时,槽下运输显得比较拥挤,工作条件差,检修设备不方便。
贮矿槽的数目在有条件时经量减少。
一般不少于10个,最多可达30个。
在本设计中槽上供料系统设有两条带式输送机,将高炉原料送至贮矿槽和贮焦槽,槽下供料系统设有烧结矿、焦炭槽、球团矿槽和杂矿槽,呈一列式布置,贮矿槽和贮焦槽下设有给料、筛分、称量设备和一条运矿、运焦主皮带机,一条返矿皮带机,一条反胶皮带机。
设有12个贮矿槽,其中六个为烧结矿槽,四个为球团矿槽,两个为杂矿槽。
2000m³高炉贮矿槽容积相当于高炉有效容积的1.6倍[21]。
则V=2000×1.6=3200m³贮矿贮存时间应满足高炉12~24h的消耗量,其中高炉烧结矿的贮存时间为9~14h,其他原料的贮存时间大于12h。
在本设计中,烧结矿的贮存时间为12h,球团矿贮存时间为28h。
槽下采用皮带上料时,矿槽长度一般为5000mm。
矿槽的高度取决于高炉容积和槽上槽下运输方式,大中型高炉一般为10~11m,不宜超过14m,矿槽宽度要能布置下2~3条胶带运输机(胶带宽度为800mm~1400mm),矿槽壁倾斜角为50o~55o。
本设计中,烧结矿槽和球团矿槽的长度定为5000mm,杂矿槽的长度定为3200mm,宽度都定为5600mm。
焦槽长度定为5600mm,宽度定为6600mm。
矿槽壁倾斜角为55o,焦槽壁倾斜角为45o,以使炉料能顺利下滑放出。
贮焦槽的数目与高炉的上料方式有关,当炉后采用称量漏斗、胶带运输机供料时,贮矿槽个数可以多些。
根据焦槽的贮存时间,本设计选焦槽数为4个。
贮焦槽的总容积应根据高炉有效容积而定,贮焦槽总容积一般为高炉有效容积的0.5~0.7。
在本设计中取贮焦槽容积为高炉有效容积的0.6倍。
=2000×0.6=1200m³,贮存时间为6~8。
则V贮焦本设计中贮矿槽和贮焦槽的尺寸设计如下表所示:表4-1 贮矿槽的主要参数原料名称个数单槽有效总有效单槽贮总贮贮存堆比重容积m³容积m³存量t 存量t 时间t/m3烧结矿 6 320 1920 704 4244 12 2.2 球团矿 4 270 1080 621 2484 28 2.3 杂矿 2 100 200表4-2 贮焦槽的主要参数原料名称个数单槽有总有效单槽贮总贮贮存堆比重效容积m³容积m³存量t 存量t 时间t/m3焦炭 4 300 1200 135 574 6 0.45 4.2 电磁振动给料机的设计一般每个贮矿槽设有两个漏嘴,漏嘴上应装有闭锁装置,叫闭锁器。
其作用是开关漏嘴,并调节流量。
为此,对其的基本要求是:应有足够的供料能力;料流均匀连续且稳定并可以调节;能正确锁住料流,不卡不漏;结构简单,易于维修。
本设计中采用目前广泛使用的电磁振动式给料机,它可以把块状、粉状物料从贮槽中定量地、均匀地、连续地给出。
不振动时,原料呈自然堆角而静止不动。
其结构主要由槽体、激振器和减震器三部分组成,激振器与槽体用弹簧连接在一起,激振器的作用是使槽体连续不断的产生振动,驱使槽内炉料连续向前跳动,由于振动频率很高,振幅很小,炉料跳起的高度也很小。
在本设计中给料机底板换成筛网式,在给料的同时还能起到筛分作用。
安装时保持横向水平,槽体一般向下0o~10o倾斜安装,最大给料能力为400~700t/h,生产能力为25m3/h,驱动功率为0.2kw,其结构如图所示:图4-1电磁振动给料机结构示意图1-给料槽;2-连接叉;3-衔铁;4-弹簧组;5-铁心;6-激振器壳体;7-减震器4.3料批重量的确定高炉有效容积:2000m³,平均利用系数2.2t/m3d;平均昼夜产量:2000×2.2=4400t/d;(一)每天需要矿石量计算如下:烧结矿:4400×1776.657×10-3×0.85=6644.70 t/d;球团矿:4400×1776.657×10-3×0.15=1172.59 t/d;硅石:4400×31.58×10-3=138.95 t/d则每天需要铁矿石量为7817.29t;喷煤操作时,每天需要的焦碳量为:4400×423.68×10-3=1864.19t故日产铁量4400吨时按冶炼每吨生铁的矿石单耗及焦比计算出每日的原料需要量如下:表4-3 高炉每日原料需要量(t/d)原料名称日产铁量烧结矿球团矿焦炭硅石每日需要量4400 6644.7 1172.59 1864.79 138.95 (二)焦炭批重、矿石批重的确定由前面的计算知道,炉喉直径:d1=7.6m,即7600m;高炉装料设备的容积应根据矿石料批重量确定。
高炉矿石料批重量宜符合下表的规定:表4-4 高炉矿石料批参照炉容级别m31000 2000 3000 4000 5000正常矿石批重t 30~60 50~95 80~125 115~140 135~170 最大矿石批重35~70 60~100 90~140 126~160 150~190本设计选取正常矿石批重56t,最小矿石批重48t,最大矿石批重68t。
所以,根据公式:V onor=0.270d12.4187=2.70×7.62.4187=36.46m3(式4-1)V omax=0.472d12.2266=0.472×7.62.2266=43.17m3 (式4-2)所以选取V onor=36.5m3;V omax=43.5m3,因此,料斗容积50m3。
由矿石批重W O计算焦炭批重W C:W C=C R×W O/O R(式4-3) 式中,O R—铁矿石消耗量,千克/吨铁;C R—焦量,千克/吨铁;W C—焦批,吨;最小焦批重:W C=423.68×48/1776.657=11.45t;正常焦炭批重:W C=423.68×56/1776.657=13.35t;最大焦炭批重:W C=423.68×68/1776.657=16.22t;4.4 槽下筛分设备对槽下筛子的要求是:耐磨性好,对炉料的破碎尽可能少,筛分效率高,筛分能力应留有高炉扩容的余量,筛分时噪声低,当采用筛子直接向称量设备供料时,还要求余振量低,以减少称量误差。
目前,常用的槽下筛分的筛子类型有辊型和振动筛。
辊型现已被淘汰,本设计中采用振动筛。
选取:矿石振动筛人字筛孔为上层14mm,下层6~7mm,振幅为7~10mm,安装倾角为20o,处理量为500~800t/h台。
因本设计中共设焦槽4个,每个焦槽容积为300m3,每个焦槽下设双层振动筛两台,筛分后的焦炭由槽下皮带运送装入集中称量漏斗,称量后放入主皮带输入高炉。
其上层孔为40mm,下层长方孔为25×35mm,振幅为7~10mm,筛面倾角上层为15o,下层为20o,筛分能力为120~170t/h台。
表4-5 振动筛的参数类型矿石振动筛焦炭振动筛筛孔尺寸上层14mm,下层6~7mm 上层孔为40mm,下层长方孔为25×35mm 振幅7~10mm 7~10mm筛面倾角安装倾角为20o上层为15o,下层为20o处理量500~800 t/h台120~170 t/h台4.5称量设备4.5.1 矿石称量漏斗称量漏斗可以用来称量烧结矿、球团矿和焦炭等。
熔剂先经槽下称量漏斗分散称量后,经Y K皮带输送至主皮带入炉。
入炉原料以槽下称量结果为主,槽下称量采用计算机进行称量补正。
本设计中槽下共设12个矿石称量漏斗,每个贮矿槽下设有一台电子称量漏斗,因为其具有不存在刀口的磨损和变钝,精确度高,体积小,结构简单,重量轻的优点。
其参数选择如下:烧结矿、球团矿的称量漏斗有效容积为7.5m3,称量范围为0~15t;杂矿的称量漏斗有效容积为4.0m3,称量范围为0~6.5t;4.5.2 焦炭称量漏斗焦炭称量漏斗用来称量经过槽下筛分后的焦炭,然后将焦炭卸入上料胶带运输机上,运往高炉炉顶。
本设计中采用的是焦炭集中称量,共4个焦槽,采用两个焦炭集中称量漏斗,按两个焦炭称量漏斗能容纳一批焦炭考虑。
其参数选择如下所示:V C=W C.max/(2γc)(式4-4)=16.22/(2×0.45)=18.02 m3其中:V C—焦炭称量漏斗容积,m3W C.max—最大焦炭批重,t/批γc—焦炭堆密度,t/ m3所以,选两个有效容积为20 m3、最大称重量为10t的焦炭称量漏斗。
4.5.3 筛下焦系统焦炭振动筛产出的筛下焦,经筛下焦筛分系统,焦丁(10~25mm)装入焦丁槽,由电子称称量后经矿槽下Y K皮带,与烧结矿混合入炉,焦粉则装入焦粉仓卸入汽车运走。
4.6 槽下运输设备槽下供料运输普遍采用胶带运输机供料,胶带运输机供料与称量漏斗称量相配合,是高炉槽下实现自动化操作的最佳方案。
由于高炉的大型化和自动化,胶带上料系统已成为一种主流设备。
胶带上料机主要由胶带、驱动卷筒、驱动电机及传动装置组成。
一般在距离高炉270~340m处称量配料,槽下用电磁振动给料器给料,振动筛筛分,称量漏斗称量,然后分别送往各自的集中漏斗,按照上料程序和装料制度,开动集中漏斗下面的电磁振动给料器,将料均匀的分布在不停运转的皮带机上,运往高炉。
一般情况下,皮带机头轮设置在炉顶上,尾轮设置在矿槽下部,机械传动装置和电器控制室设置在偏于沦为一侧的中部。
由于皮带上有炉料及其自身的荷重,在加上张紧装置的作用,皮带与中间摩擦驱动机之间产生摩擦力而被驱动。
本设计中皮带上料设备的传动装置采用装有备用电动机的多驱动方式。
由于高炉炉料提升高度比较大,倾角又不能太大,所以皮带要拉的很长。
因此要采用高强度皮带。
本设计中采用加钢丝绳芯的强张力型胶带。
因为其采用的钢丝不仅有一定的抗拉强度和疲劳强度,而且还和橡胶之间有较大的黏着力,有较好的柔软性。
下图为胶带运输机的工作示意图:图4-2 主胶带运输机的工作示意图1-炉顶头轮;2-焦炭集中漏斗;3-尾轮;5-配重;6-胶带传动装置;7-高炉;A-原料达炉顶检测;B-炉顶装料准备检测;C-矿石终点检测;D-焦炭终点检测为了准确检测原料位置,在皮带机长度方向上设有原料位置检测装置,共设四个检测点。