高酸值原油加工综述学习资料
高酸原油及加工

中海石油炼化有限责任公司
13
二 、高酸原油加工存在的问题
含酸原油的典型特性、工艺挑战与解决方案
原料的典型污染物
工艺挑战
解决方案
可过滤固体含量高
\\
\
结垢 发泡 脱盐效率 环保
\
贮罐脱水 脱盐(也列为工艺挑战)
\工艺阻垢剂\废水处理
含水量大
脱盐\产品质量\腐蚀\发泡\能耗
贮罐脱水\脱盐(同上) \塔顶腐蚀控制
0.9283 <-20 54.83 6.54 0.691 4439
酸值 mgKOH/g 1.12
4.51
1.4
0.51
1.9
沥青质 % 胶质 % 蜡含量 %
Fe
4.12 16.56 6.37 2.45
12.58*
5.42 19.14 13.55 12.51
1.632 14.16
高酸原油酸值分布图
100
200
蓬莱19-3-2原油 克拉玛依1号 单家寺
300
400
沸点,℃
蓬莱19-3-4
苏丹Fulan2a 新疆混合原油
500
600
哈萨克斯坦 苏丹Fulan2b
中海石油炼化有限责任公司
12
前言 一、高酸原油的资源、性质及酸分布 二、含酸原油加工存在的问题 三、加工高酸原油常减压装置的设计与做法 四、运行效果的评价 五、装置目前存在的问题及改进措施 六、结束语
金属负荷大 (钙、汞、 铁、硒…)
\
\
\
结垢 催化剂中毒 产品质量
SH&E
去除脱盐装置杂质\工艺阻垢剂\废水处理
镍/钒含量大 原料兼容性差
\
催化剂中毒
FCCU操作
高酸原油加工防腐蚀技术(山东讲课)
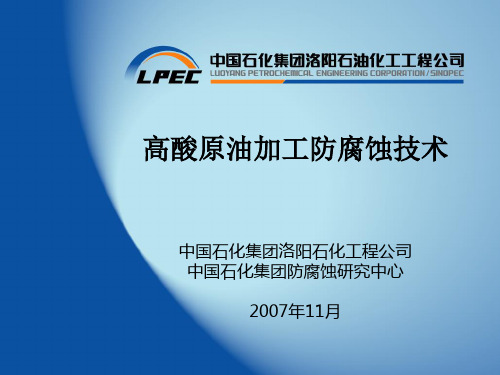
辽河原油
渤海锦州 9-3
喀麦隆 Lokele
巴西 Marlim
乍得 Doba
蜡含量, %
6.0
7.5
4.30
1.55
2.92
-
胶质+沥青质, % 17.7 12.58 18.54 18.16 12.50 16.98
22.8
硫含量 %
0.32 0.131 0.20
0.27
0.42
0.68
0.16
氮含量 %
18
加工高酸原油的 主要腐蚀
19
三、加工高酸原油的主要腐蚀
在加工过程中的腐蚀突出表现在以下几个方面: 1)酸值高,存在严重的高温环烷酸腐蚀; 2)电脱盐难度增加,低温部位腐蚀程度增加; 3)原油中氮含量高,在加工过程中形成含氮腐 蚀介质; 4)高酸原油的盐含量高,重金属含量高,尤其 是金属钙、镍的含量高,容易引起二次加工装置的 催化剂中毒、催化剂床层堵塞以及高温换热器等结 垢、结焦。
汽油酸度
煤油酸度
柴油酸度 蜡油酸值 渣油酸值
mgKOH/100ml mgKOH/100ml mgKOH/100ml mgKOH/g mgKOH/g
3.95
8.28
127.4
5.67
0.80
6.98
61.1
126.6
2.93
6.65
88.25
3.33
153.44
12.98
36.00
9.92
9.40
152.3
23
温度
环烷酸腐蚀受温度的影响比较大,在200℃以下环烷酸 对设备几乎不造成腐蚀,而当温度升高至200℃以上时,随 着温度升高腐蚀逐渐加剧。
Gutzeide等人的实验表明:温度每升高55℃,碳钢和低 合金钢腐蚀速度增加2倍。
石油加工中的石油酸腐蚀
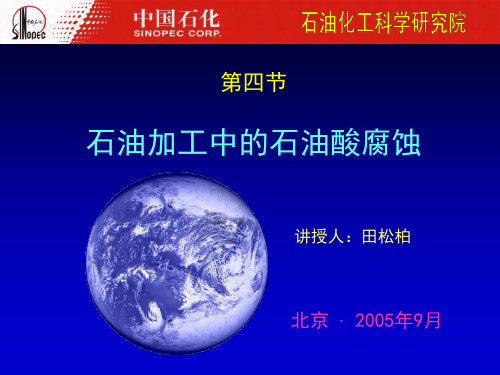
7 影响环烷酸腐蚀的因素
8 防腐措施 结语
1 高酸原油加工涉及的 几个基本概念
脂肪酸和环烷酸 酸值 环烷酸值
总酸值
酸度
含酸原油的分类
环烷酸的腐蚀
脂肪酸和环烷酸
CH3(CH2)n-COOH
CR2 R2C CR(CH2)n-COOH
S 1.9%)
高酸高钙原油:辽河稠油(TAN 2.10 mgKOH/g;
Ca 284ppm)
环烷酸的腐蚀
一般认为,原油中酸的腐蚀主要是占原油90%左
右的环烷酸的腐蚀。高温环烷酸的腐蚀主要发生 在220~425℃范围内。
环烷酸在220℃以下腐蚀很轻,在沸程为270~
280℃、350~400℃时腐蚀最严重。
第四节
石油加工中的石油酸腐蚀
讲授人:田松柏
北京 ·2005年9月
主要内容
前言
1 高酸原油加工涉及的几个基本概念
2 高酸原油的资源 3 高酸原油的特性分析
4 石油酸的表征
5 原油中石油酸的分布规律 6 石油酸的类型及其腐蚀性
7 影响环烷酸腐蚀的因素
8 防腐措施 结语
前言
石油酸对炼油装置的腐蚀的认识由来以久。
<200℃收率 <350℃收率 >500℃收率 硫(含量) 氮(含量) 铁(含量) 镍(含量)
18.55 46.57 38.36
3.09
0.09 1.9 16.7
钒(含量)
钙(含量)
ppm
ppm
2.5
16.7
1.80
283.5
0.2
0.6
6.7
【实例】高酸重质原油加工废水处理工艺的分析和改造

【实例】高酸重质原油加工废水处理工艺的分析和改造惠州某公司加工高含酸重质原油产生的加工污水成分复杂,污染物、无机盐和难生物降解有机酸浓度高,处理难度大。
多年来,该公司污水处理设施出水需调和部分达标含油污水(COD≤30 mg/L),无法实现直接达标排放。
经过改造,在原工艺的基础上增加了生物曝气滤池(RBF)、水解酸化罐和臭氧催化氧化工艺,停用原工艺中的活性炭吸附工艺,实现了达标排放或回用,增加了经济效益和环保效益。
高酸重质原油属于环烷中间基类原油,密度大、黏度大、残炭高、酸值高、乳化重、脱盐困难,加工时需要添加大量的破乳剂。
惠州某公司加工高酸重质原油产生的废水成分复杂,COD为3 500~4 500 mg/L、氨氮为80 mg/L、总氮为100~120 mg/L,难生物降解有机酸类占有机污染物总量的60.26%。
这类含油污水乳状液油水难以分层,水中含油量大,导致污水处理场生化系统的水面易产生大量泡沫,污水回用设施运转不正常,处理效果降低,处理难度变大。
排放污水中含油量超标,严重污染了环境,还造成了大量油品的损失。
惠州某公司原高酸重质原油加工污水处理设施流程为:调节罐—油水分离器—涡凹气浮—溶气气浮—A/O生化池—MBR—臭氧活性炭,此工艺处理后的出水COD(二级生化MBR出水)仍为260 mg/L左右,无法达到GB 31570—2015《石油炼制工业污染物排放标准》的排放标准要求(COD≤50 mg/L),需调和部分达标含油污水(COD≤30 mg/L)才能达标排放。
另外,工艺中需消耗大量的活性炭,增加了处理成本,造成了二次污染。
为解决高酸重质原油加工污水处理设施存在的问题,本研究根据污水水质特点对污水处理设施进行了改造,在处理工艺中增加了生物曝气滤池(RBF)、水解酸化罐和臭氧催化氧化工艺,停用了原工艺中的活性炭吸附工艺,改造后的污水处理设施出水COD 为40 mg/L左右,达到污水排放标准要求,解决了出水长期无法达标的现状。
加工高酸值原油的方法及防腐措施

加工高酸值原油的方法及防腐措施随着高酸、高硫原油加工量的不断增加,炼油厂设备腐蚀日趋严重,已影响到炼油装置的安全、稳定、长周期、满负荷、优质生产。
重油装置高温部位通常采用耐腐蚀材料,而蒸馏塔顶低温轻油部位受HCl-H2S-H2O体系的腐蚀,若采用奥氏体不锈钢,则存在Cl-应力腐蚀开裂的问题,因此一般采用化学注剂防腐工艺,即用中和剂降低冷凝系统的酸性物,用缓蚀剂使它在金属表面形成一层保护膜。
传统的做法是采用注氨水的方法中和冷凝液中的酸性物,但露点部位的腐蚀仍会发生。
早在八十年代初我国许多炼油厂即开始了“一脱四注”并取得了较好的效果。
随着时间的推移,在美国到九十年代初已约有80%的炼油厂把注氨改为注有机胺,我国在九十年代已陆续有些炼油厂改注有机胺,有的还同时加入缓蚀剂和分散剂等助剂。
近几年来,随着工艺防腐理论的发展和技术的进步,国内外炼厂开始逐渐采用一剂多用的中和缓蚀剂技术来控制塔顶冷凝系统的腐蚀。
性能良好的中和缓蚀剂既具有中和塔顶冷凝区酸性物的作用,又具有在金属表面成膜的功效,能解决露点腐蚀及铵盐沉积造成的结垢和二次腐蚀问题。
二、防止腐蚀措施1. 脱盐。
目前大多数炼油厂采用二级脱盐工艺,个别厂已采用三级脱盐工艺,使脱后原油含盐达到石化企业规定标准——小于3mgNaCl/L。
但是在这里需说明一点,即目前的脱盐工艺仅仅是脱除原油中可溶于水的无机盐类,由于其中以碱金属及碱土金属的氯化物为主,故将氯化钙、氯化镁和氯化钠均换算为氯化钠含量并以mgNaCl/L表示,但其中的盐并不一定都是氯化物,也可能是硫酸盐,碳酸盐和石油酸盐,如已发现在新疆及华北一些原油中含有较高的石油酸钙,而氯化物也不一定都是无机氯化物,如上所述原油中还含有氯代烃,这些有机金属化合物和氯代烃,目前的脱盐工艺是不能将其脱除的,它们将带入常压塔,金属盐类将浓缩于渣油中,而氯代烃及硫化物则部份分解进入塔顶馏分而造成腐蚀。
2. 注入中和剂控制塔顶pH值。
高酸原油加工的腐蚀与防护

高酸原油加工的腐蚀与防护引言随着原油资源的日益紧缺,高酸原油的加工及利用已成为当前炼油行业的一项重要工作。
然而,高酸原油会对加工设备产生腐蚀,从而对生产带来不利影响。
本文将探讨高酸原油加工过程中的腐蚀问题及其防护方法。
高酸原油的定义高酸原油是指含有较高酸值的原油。
一般来说,酸值越高,腐蚀性就越大。
在高酸原油中,主要的酸类成分是硫酸、硝酸、有机酸等。
此外,含有杂质和硫化物的原油也具有较高的腐蚀性。
高酸原油加工中的腐蚀问题由于高酸原油具有较强的酸性,其在加工中会对设备和管线产生严重的腐蚀问题,导致设备寿命缩短、性能下降、安全隐患增加等问题。
腐蚀类型高酸原油加工中常见的腐蚀类型如下:•粘附腐蚀:高酸原油中的酸类成分会粘附到金属表面上,形成一层薄膜,这层薄膜中的有机物和金属中的氧发生反应,从而引发腐蚀。
•晶间腐蚀:高酸原油中的酸性物质会促进晶间腐蚀的发生,从而使设备和管道产生脆化和断裂。
•点蚀腐蚀:高酸原油中的杂质和硫化物等物质会形成点蚀,从而导致设备表面出现小孔和凸起。
腐蚀影响高酸原油加工过程中的腐蚀问题会对设备和管线的使用寿命和性能造成不良的影响,具体表现如下:•设备寿命缩短:高酸原油加工对设备产生的腐蚀作用会导致设备寿命缩短,从而增加了生产成本。
•性能下降:高酸原油加工对设备的腐蚀作用会导致设备的性能下降,生产效率降低。
•安全隐患:高酸原油加工过程中,管道和设备的腐蚀会导致破裂和泄漏,可能会产生严重的安全隐患。
防腐保护技术在高酸原油加工中,防腐保护技术的应用非常重要。
以下是一些有效的防腐保护技术。
1. 涂层技术针对高酸原油的腐蚀问题,涂层技术是一种重要的防护方法。
所选涂层应具有耐酸蚀、耐磨损、耐高温等特点,并需经过专业检测。
将这些涂层应用于设备和管道表面,则能有效地防止高酸原油产生腐蚀作用。
2. 材料选择正确认识原油的酸性,根据酸值和组成选择适合的材料,如含锆或钛的合金结构,操作期间需要引起关注。
高酸值原油加工探讨

当
代
化
工
C n e o a y C e c lI d s r o t mp r r h mi a n u t y
V 14 . N . o .0 05 M y, 0 a 2 1l
酸 值 原 油 加 工 探 讨
张 洪 庆
Z HANG n q n Ho g— i g
( NP gn o ay Taj 0 2 0 C ia C CDaa gC mpn , i i 3 0 8 , hn) nn
Ab t a t s r c :Ditiu in o l i cd i r d i wi i h a i au s i to u e s we la i r b e n s b t f o ec a i n cu e o l t h g c d v l e wa n r d c d a l s man p o lms i r o h
v l e . w o v e iu o r so r b e fc d i wi i h a i au re i i g e u p n si e n n a u Ho t s l e s ro sc ro i n p o lms o r e o l t h g c d v l e f x s n q i me t n r f i g o u h o t i
i r v c n mi e e t mp o ee o o cb n f . i
Ke r s Cr d i wi i h a i au ; P o e sn c n l g ywo d : u eo l t h g cd v le h r c si gt h o o y; An i o r so e h o o y e t ro i 外主 要高酸原油 品种
炼油厂加工高硫高酸值原油遇到的问题及对策
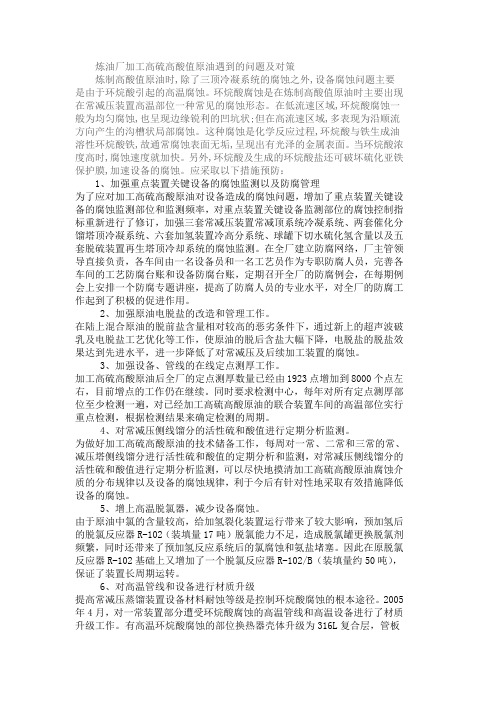
炼油厂加工高硫高酸值原油遇到的问题及对策炼制高酸值原油时,除了三顶冷凝系统的腐蚀之外,设备腐蚀问题主要是由于环烷酸引起的高温腐蚀。
环烷酸腐蚀是在炼制高酸值原油时主要出现在常减压装置高温部位一种常见的腐蚀形态。
在低流速区域,环烷酸腐蚀一般为均匀腐蚀,也呈现边缘锐利的凹坑状;但在高流速区域,多表现为沿顺流方向产生的沟槽状局部腐蚀。
这种腐蚀是化学反应过程,环烷酸与铁生成油溶性环烷酸铁,故通常腐蚀表面无垢,呈现出有光泽的金属表面。
当环烷酸浓度高时,腐蚀速度就加快。
另外,环烷酸及生成的环烷酸盐还可破坏硫化亚铁保护膜,加速设备的腐蚀。
应采取以下措施预防:1、加强重点装置关键设备的腐蚀监测以及防腐管理为了应对加工高硫高酸原油对设备造成的腐蚀问题,增加了重点装置关键设备的腐蚀监测部位和监测频率,对重点装置关键设备监测部位的腐蚀控制指标重新进行了修订,加强三套常减压装置常减顶系统冷凝系统、两套催化分馏塔顶冷凝系统、六套加氢装置冷高分系统、球罐下切水硫化氢含量以及五套脱硫装置再生塔顶冷却系统的腐蚀监测。
在全厂建立防腐网络,厂主管领导直接负责,各车间由一名设备员和一名工艺员作为专职防腐人员,完善各车间的工艺防腐台账和设备防腐台账,定期召开全厂的防腐例会,在每期例会上安排一个防腐专题讲座,提高了防腐人员的专业水平,对全厂的防腐工作起到了积极的促进作用。
2、加强原油电脱盐的改造和管理工作。
在陆上混合原油的脱前盐含量相对较高的恶劣条件下,通过新上的超声波破乳及电脱盐工艺优化等工作,使原油的脱后含盐大幅下降,电脱盐的脱盐效果达到先进水平,进一步降低了对常减压及后续加工装置的腐蚀。
3、加强设备、管线的在线定点测厚工作。
加工高硫高酸原油后全厂的定点测厚数量已经由1923点增加到8000个点左右,目前增点的工作仍在继续。
同时要求检测中心,每年对所有定点测厚部位至少检测一遍,对已经加工高硫高酸原油的联合装置车间的高温部位实行重点检测,根据检测结果来确定检测的周期。
高酸原油

本世纪以来,随着国际原油价格的一路攀升,国内许多炼油厂在成本压力下开始炼制价格较低的高酸值原油,设备防环烷腐蚀问题也同时提到议事日程。
腐蚀监测技术是掌握设备腐蚀状态的有效手段,炼制高酸值原油设备的腐蚀程度可以通过不同的腐蚀监测方法进行跟踪,从而指导生产的安全运行。
l 环烷酸腐蚀彰晌因素影响环烷酸高温腐蚀的主要因素有原油的总酸值(TAN)、温度、硫含量、流速和设备材质等。
物料的物性、流动状态、气液相状态、压力及物料中环烷酸盐等也会间接影响环烷酸腐蚀速率的大小。
1。
1 酸值酸值是影响环烷酸高温腐蚀最主要的因素。
一般认为当原油的TAN大子0。
5 mgKOH/g时,就存在环烷酸腐蚀,且TAN值越高,腐蚀越严重。
由于TAN 值只代表整体酸性(包括环烷酸以外的酸性),而油品中环烷酸是混合酸,沸点也不同,因此,对设备的某一具体位置来说,工艺物料中的真实酸值才真正反映其腐蚀性。
这一事实对腐蚀监测有一定的指导意义,实施腐蚀监测之前要了解环烷酸在各种馏分中的分布情况。
1。
2 温度(l~3]温度也是影响环烷酸高温腐蚀的主要因素,在177℃就能发现环烷酸的腐蚀现象。
在生产实践中,当温度达到232℃以上时,碳钢的腐蚀速率比较明显,随着温度升高,腐蚀速率加快。
在一定的酸值下,温度每上升55.5℃,环烷酸对碳钢和低合金钢的腐蚀速率增加3倍。
当温度在370℃左右时环烷酸腐蚀最严重,超过400℃时,由于环烷酸开始热分解,腐蚀速率下降。
生产实践中,腐蚀速率随温度的变化还受到高温硫腐蚀的影响。
环烷酸腐蚀有两个显著的温度区,第一是274℃左右的碱三线蜡油,第二是345~385℃的常压塔进料段、常底、减四线、减压塔进料和减压塔底。
l。
3 流速阳[4~5]流速和流态是影响环烷酸腐蚀非常重要的因素。
在高温及高流速下,酸值在很低水平(0.3KOHmg/g)的油液,比高酸值(1.5~1。
8 KOHmg/g)的油液更有腐蚀性。
实践表明在炼油设备的弯头、三通和泵中产生的湍流会加速设备的腐蚀。
谈含酸原油加工

11 世 界 含 酸 原 油 分 布 .
含酸原油主要 分布在美洲 、 远
东、 两北欧及西非等地 区 19 年 , 98 世界高酸 原油产 量约 为 1 . 吨, 4亿
呈逐年下降的趋势 ( 见罔 1 罔 2) 、 : 但也有人认为 , 今后 1 2 年含酸 5~ 0 原油产量仍会逐年增加 ( 见罔 3 = )
3 55 9 .
维普资讯
代石 ・ l l : .
表 2 世 界 主 要含 酸/ 酸 原油 产 地 高
东、 单家寺 等 均为高 酸 原油 , 合计 产量约 6 0万 吨 , 酸值为 1 7~ 5 其 . 3 2 5m O /。大港油 田 2 0 . g Hg 9 K 0 4年
酸值 高达 3 1 . O /, . ~6 2 K Hg 硫 6 0 mg
含 量均在 0 %以下 ,属于典 型 的 . 5
低硫 高酸原油 。 渤海海域是我 国 目 前 高酸原 油最有增产潜力 的地 区 ,
见 图 4 。
注: 括弧 中数 据为不 同资料来 源。
东 胜利 油 田 、 华北 大 港 油 田 、 疆 新
2 55 9 . 3 00 3 . 3 9.2年 毕 16 业于
学 院 炼制 系 . 授 级 高级 工 程 师 , 教
石 化 集 团公 司科 技委 咨询 委 副 主
务院 政 府专 家 津 贴 长期 从 事炼
Z - 管理 工 作 , - R术 已发 表论 文 81 l
产 量 为 4 83 吨 ,其 中高凝 原 8. 7万
油酸值 为 08 8 a O /, 凝羊 . g H g低 2n K
三木 原 油 酸 值 为 1 7m O /, . gK H g 2 亦 属于低硫含 酸 / 高酸原油 。新疆
高酸值原油加工综述[1]
![高酸值原油加工综述[1]](https://img.taocdn.com/s3/m/e3bb7e9151e79b89680226d3.png)
高温缓蚀剂技术近几年发展较快,许多加工高酸、高硫原油的炼厂都在积极使用,防腐效果还是比较明显的,但是对一些高温高速部位使用的效果则较差。
3.6全面料是防止环烷酸腐蚀最有效的措施之一。在没有理想的工艺防腐蚀手段的情况下,提高设备材质的耐蚀等级是减轻环烷酸腐蚀最有效的方法。提高材质耐蚀等级的实质就是采用加入一定量的合金元素如Cr、Ni、Ti的合金钢,以便形成有一定效果的氧化物保护膜,该氧化物保护膜对金属离子扩散有着强烈的阻滞作用,从而保护金属不受进一步腐蚀。对于有机酸腐蚀的环境,在设备选材时应充分考虑介质的温度、流速以及是否会出现涡流、湍流和相变等因素,对流速超过30 m/s、出现涡流、湍流和相变的部位应采用更高级别的材质。据资料介绍,不同材质对环烷酸具有不同的耐蚀性。具体材料的耐蚀性为:碳钢<低合金钢(铬钼钢:Cr5Mo<Cr9Mo=<1Cr13<18-8不锈钢<含钼奥氏体不锈钢。所以选用含钼奥氏体不锈钢可有效地控制环烷酸的腐蚀;对于典型的含钼奥氏体不锈钢316和315L,含钼量应高于2.3%,低于此值将降低其耐蚀性[5]。
表1、我国各油田含酸原油产品性质
原油名称 酸值/mgKOH?g-1 硫含量,%
北疆 4.51 0.13
高酸值原油加工综述:
介绍了原油中石油酸的分布规律、环烷酸腐蚀机理及影响环烷酸腐蚀的因素。综述了近年来高酸原油的加工方法及国内一些炼油厂炼制高酸值原油情况及防护措施。重点介绍了茂名分公司炼制高酸值原油的情况,分析了高酸值原油各馏分的酸分布规律,提出了炼制高酸值原油的对策。
高酸值原油加工方案探讨

2 . 环 烷 的腐 蚀机 理 :
环烷 酸具 有一 元脂肪 酸的全 部特点 , 腐 蚀大 多发生在 液相 , 如果 环烷 酸在 汽相 中产 生冷凝 液 , 将形成汽 相腐蚀 , 腐蚀 的程度 与酸 值有 关。 环 烷酸在低 温时 腐 蚀 不强烈 , 一 旦沸 腾 , 特别是 在高 温无水 环境 中 , 腐蚀最 强烈 , 环烷酸 与金 属 的腐 蚀反 应为 : 2 RC O O H + F e— F e ( RC O O ) 2 + H2 F e S +2 R C O OH — F e ( RC OO ) 2 +H 2 S 由于F e ( RC O O) 2 是 一种 油溶性 腐蚀产 物 , 能为 油流所 带走 , 因此不易 在金 属设 备表 面上 形成 保护 膜 , 即使设 备表 面有 F e S保 护膜 , 也 会与 环烷酸 发 生 反应 , 使 新 的金属 表面 暴露 , 腐 蚀继 续进 行 。
生 明显的腐 蚀 。 2. 温 度 的影 响 环烷 酸的腐 蚀受温 度影 响很大 , 环烷 酸在常 温下对 金属 没有腐蚀 性 , 但在 高温 下能和铁 反 应生成 环烷 酸铁 , 引起强 烈的腐 蚀 。 试验 表 明 : 2 2 0 0 C 时环烷 酸开 始腐 蚀 , 并 随温度 的升高 腐 蚀加剧 。 2 7 0  ̄ 2 8 0 0 C 时腐 蚀速 度 已经很 大 , 以后 随温度 上升 而减 弱 3 5 0  ̄ 4 0 0 0 C 时腐蚀 速度 又 急剧增 加 3. 流 速 的影 响
一
、
以需对V G O 经过的设备采用抗腐蚀材质 , 减少铁离子含量。 三. 影响 环烷 酸腐蚀 的 因素 1. 酸 值 的 影 响 表示原油 中环烷酸 浓度的指标 是酸值 。 所谓酸值 是指 中和一 克原油所 需氢 氧化钾 的毫 克数 ( r o g K OH/ g ) 。 最 新的研 究 结果表 明 : 原油 的总酸 值 与原 油的
加工高硫高酸原油的高温防腐技术综述

高温腐 蚀 主 要发 生在 重 油加 工部 位 , 常减 压 如
装置减 压塔减 压泵 和 转油 线 、 化装 置分 流塔 及 其 焦
泵体管 线 、 催化 装置 的加热 炉等 。
2 主 要防腐措 施 2 1 原 油 品种 的优化 混炼 .
摘 要: 针对高硫高酸原 油加工带来的腐蚀 问题 , 综合分析 了高温硫和环烷酸的腐蚀机理 , 并对几种防腐措施 进行 了对 比分 析 , 提出抑制环烷酸腐蚀是高温防腐 的根本 , 而采用注加高温缓蚀剂是一种经济可行的 有效手段。通过 比较 国内外不同类 型的高温缓蚀剂 , 出了咪唑啉型高温缓蚀剂研 发的主要影 响因 提 素, 并对缓蚀剂的注入方式提 出了几点建议。 关键词 : 原油加工 高硫 高酸 高温腐蚀 缓蚀
即通过采 取加碱 中和 以及加氢脱 硫 的方式改 善 原 油 品质 , 降低 原 油 的酸 值 与硫 含 量 。但 加碱 中和
环烷酸 生成 的环烷 酸盐 或 者 难 以溶 解 , 或者 易 造 成
逐 渐减弱 。腐蚀 反应 主要生成 F S e。
1 2 环烷 酸 的腐蚀 .
环烷 酸 的 腐 蚀 作 用 受 温 度 影 响 比 较 大 。在 20 2 ℃前几 乎没有 腐 蚀作 用 , 随着 温度 的升 高 , 蚀 腐
性剂 , 对金属 表 面具 有很强 的清洗 作用 , 可将高 温硫 反应生 成 的 FS溶解 , e 使设 备露 出新 的表 面 , 到新 受 的腐 蚀 。在环 烷 酸 、 元素 硫 、 硫化 氢 的互 相作 用 下 , 环烷 酸 的腐 蚀 加 剧 , 到 4 0 后 , 烷 酸气 化 完 直 0℃ 环 毕 , 蚀作 用减 缓 J 其腐 。
超重质高酸值原油的加工进行探讨

超重质高酸值原油的加工进行探讨1、前言随着原油的不断勘探和开发,重质高酸值原油会被不断的发现和开采,这部分原油的加工方法也逐渐引起人们的重视。
通常把比重较大的原油称为重质原油。
酸值低于0.3 mgKOH/g的原油称为低酸值原油,酸值为0.5~1.0 mgKOH/g的原油称为含酸原油,酸值大于1.0 mgKOH/g的原油称为高酸值原油。
针对硫含量大于1.0%的高硫原油的加工方法国内已积累了许多宝贵的经验,含酸原油和高酸值原油也已在许多炼油厂进行了掺炼,但是重质高酸值原油的独立加工,国内还没成熟的经验,本文就采用延迟焦化工艺对超重质高酸值原油的加工进行探讨。
2、原油性质及特点下表为几种重质高含酸原油的性质。
该类原油的主要特点是密度大、酸值高、粘度大、胶质含量高、重金属含量高、硫含量低。
该类原油的加工难度主要体现在①酸值高,对设备及管线腐蚀严重;②常压石脑油、煤油、柴油的收率偏低,且柴油的酸值较高。
另外还有其它多项指标不合格;③蜡油酸值高、难裂化、做催化原料时轻油收率偏低;④金属含量较高,对电脱盐带来困难。
3、加工方案选择确定原油加工方案一般是根据原油的性质和对目的产品的要求通过优化比较寻找目的产品多、产品质量好、加工流程短、投资低、能耗低、经济效益好的加工流程。
根据上述原油的特点,针对常减压拔出率较高的高酸值原油,应先采用常减压装置进行分馏,石脑油通过重整处理后生产高辛烷值汽油,煤油、柴油去加氢精制,蜡油去加氢裂化,减压渣油通过延迟焦化工艺处理。
针对常压拔出率较高,减压拔出率较低的高酸值原油。
可以只进行常压分馏、常压渣油直接进延迟焦化装置处理。
针对常减压拔出率均较低的重质高酸值原油,如辽河超稠油、苏丹稠油,可以直接采用延迟焦化装置进行加工。
延迟焦化装置生产的石脑油经加氢处理后可作为重整原料或乙烯裂解原料,焦化柴油经加氢精制后作为优质柴油外销,焦化蜡油作为加氢裂化原料或作为催化裂化原料。
由于高酸值原油的硫含量较低,可生产低硫优质焦炭,焦化富气可作为制氢装置的原料。
含酸原油加工腐蚀状况及对策
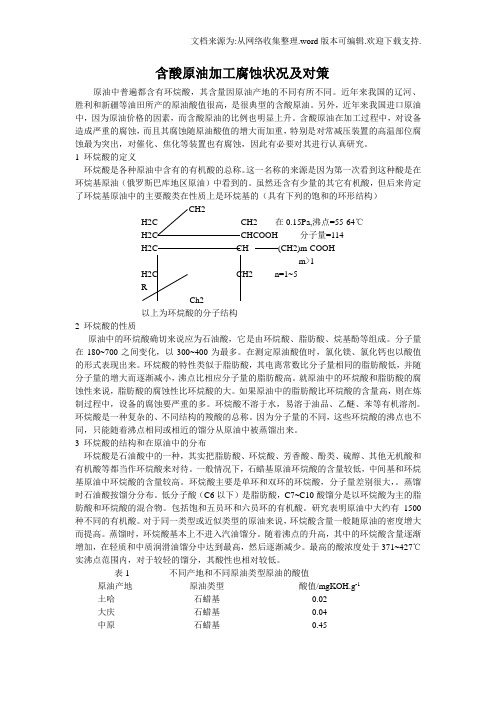
含酸原油加工腐蚀状况及对策原油中普遍都含有环烷酸,其含量因原油产地的不同有所不同。
近年来我国的辽河、胜利和新疆等油田所产的原油酸值很高,是很典型的含酸原油。
另外,近年来我国进口原油中,因为原油价格的因素,而含酸原油的比例也明显上升。
含酸原油在加工过程中,对设备造成严重的腐蚀,而且其腐蚀随原油酸值的增大而加重,特别是对常减压装置的高温部位腐蚀最为突出,对催化、焦化等装置也有腐蚀,因此有必要对其进行认真研究。
1 环烷酸的定义环烷酸是各种原油中含有的有机酸的总称。
这一名称的来源是因为第一次看到这种酸是在环烷基原油(俄罗斯巴库地区原油)中看到的。
虽然还含有少量的其它有机酸,但后来肯定了环烷基原油中的主要酸类在性质上是环烷基的(具有下列的饱和的环形结构)CH2H2C CH2 在0.15Pa,沸点=55-64℃H2C CHCOOH 分子量=114H2C CH-(CH2)m-COOHm>1H2C CH2 n=1~5RCh2以上为环烷酸的分子结构2 环烷酸的性质原油中的环烷酸确切来说应为石油酸,它是由环烷酸、脂肪酸、烷基酚等组成。
分子量在180~700之间变化,以300~400为最多。
在测定原油酸值时,氯化镁、氯化钙也以酸值的形式表现出来。
环烷酸的特性类似于脂肪酸,其电离常数比分子量相同的脂肪酸低,并随分子量的增大而逐渐减小,沸点比相应分子量的脂肪酸高。
就原油中的环烷酸和脂肪酸的腐蚀性来说,脂肪酸的腐蚀性比环烷酸的大。
如果原油中的脂肪酸比环烷酸的含量高,则在炼制过程中,设备的腐蚀要严重的多。
环烷酸不溶于水,易溶于油品、乙醚、苯等有机溶剂。
环烷酸是一种复杂的、不同结构的羧酸的总称。
因为分子量的不同,这些环烷酸的沸点也不同,只能随着沸点相同或相近的馏分从原油中被蒸馏出来。
3 环烷酸的结构和在原油中的分布环烷酸是石油酸中的一种,其实把脂肪酸、环烷酸、芳香酸、酚类、硫醇、其他无机酸和有机酸等都当作环烷酸来对待。
一般情况下,石蜡基原油环烷酸的含量较低,中间基和环烷基原油中环烷酸的含量较高。
炼油厂防腐蚀培训资料加工高酸值原油腐蚀与防护对策
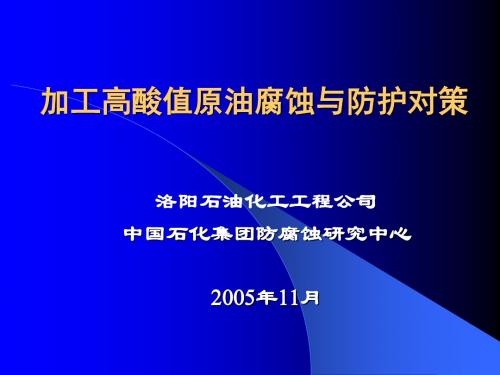
2.3.1 H2S-HCN-H2O型腐蚀
腐蚀形态 在该环境下,对碳钢为均匀减薄、氢鼓 泡及硫化物应力腐蚀开裂;对奥氏体不 锈钢为硫化物应力腐蚀开裂。 防护措施 采用水洗的办法,将氰化物脱出;或者 注入多硫化物有机缓蚀剂。
2.3.2 NOx-H2S- H2O型腐蚀
NOx-H2S-H2O型腐蚀体系给催化裂化再生 器、三旋等设备造成腐蚀开裂,产生穿 透性裂纹,严重威胁装置的正常生产。 防护措施 增加保温材料,提高壁温,防止结露; 或采用内喷合金涂层的电化学防护方法, 防止裂纹开裂。
该类型腐蚀应以工艺腐蚀为主,材料防 腐为辅 工艺防腐采用“一脱三注” 材料升级双相不锈钢、钛材或Monel合金
2.2 环烷酸高温腐蚀
2.2.1 环烷酸高温腐蚀的特点
腐蚀特点 发生在220-400℃,腐蚀产物溶于油,腐 蚀的金属表面粗糙而光洁,呈沟槽状。 影响因素 温度、流速和环烷酸含量(酸值)
24.3
25.28 172.4
0.05
0.03 0.03
1.75
4.76 1.69
痕迹
痕迹 痕迹
2005.4.9
2005.4.9 2005.4.9 2005.4.10 2005.4.10 2005.4.11 2005.4.11
加工高酸值原油腐蚀与防护对策
洛阳石油化工工程公司 中国石化集团防腐蚀研究中心 2005年11月
目录
1 高酸原油性质特点 2 加工高酸原油的典型问题 3 防腐中心开展的工作 4 加工高酸原油其它注意事项 5 需要进一步研究的内容 6 结束语
1 高酸原油性质特点
原油
渤海 蓬莱 19-3
密度,kg/m3(20℃)
渤海 锦州 9-3
高酸化值原油的加工与利用研究
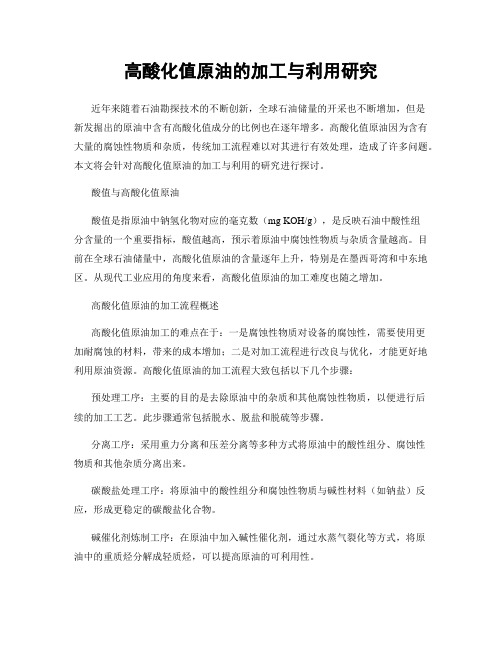
高酸化值原油的加工与利用研究近年来随着石油勘探技术的不断创新,全球石油储量的开采也不断增加,但是新发掘出的原油中含有高酸化值成分的比例也在逐年增多。
高酸化值原油因为含有大量的腐蚀性物质和杂质,传统加工流程难以对其进行有效处理,造成了许多问题。
本文将会针对高酸化值原油的加工与利用的研究进行探讨。
酸值与高酸化值原油酸值是指原油中钠氢化物对应的毫克数(mg KOH/g),是反映石油中酸性组分含量的一个重要指标,酸值越高,预示着原油中腐蚀性物质与杂质含量越高。
目前在全球石油储量中,高酸化值原油的含量逐年上升,特别是在墨西哥湾和中东地区。
从现代工业应用的角度来看,高酸化值原油的加工难度也随之增加。
高酸化值原油的加工流程概述高酸化值原油加工的难点在于:一是腐蚀性物质对设备的腐蚀性,需要使用更加耐腐蚀的材料,带来的成本增加;二是对加工流程进行改良与优化,才能更好地利用原油资源。
高酸化值原油的加工流程大致包括以下几个步骤:预处理工序:主要的目的是去除原油中的杂质和其他腐蚀性物质,以便进行后续的加工工艺。
此步骤通常包括脱水、脱盐和脱硫等步骤。
分离工序:采用重力分离和压差分离等多种方式将原油中的酸性组分、腐蚀性物质和其他杂质分离出来。
碳酸盐处理工序:将原油中的酸性组分和腐蚀性物质与碱性材料(如钠盐)反应,形成更稳定的碳酸盐化合物。
碱催化剂炼制工序:在原油中加入碱性催化剂,通过水蒸气裂化等方式,将原油中的重质烃分解成轻质烃,可以提高原油的可利用性。
高酸化值原油的利用高酸化值原油难以直接用于工业生产和民用。
不过,虽然高酸化值原油的加工难度较高,但其仍具有一定的利用价值。
目前高酸化值原油的利用途径主要包括以下几个方面:化学品生产:高酸化值原油中的酸性组分可以用来制造酸酐、酸酯、酸酣等化学品,这些化学品广泛应用于合成树脂、涂料、塑料、弹性体、印刷油墨等行业。
工业燃料:高酸化值原油中的轻质烃可以作为工业燃料,在加工过程中能够带来一定的经济效益。
加工高酸原油的防腐蚀技术综述_刘良
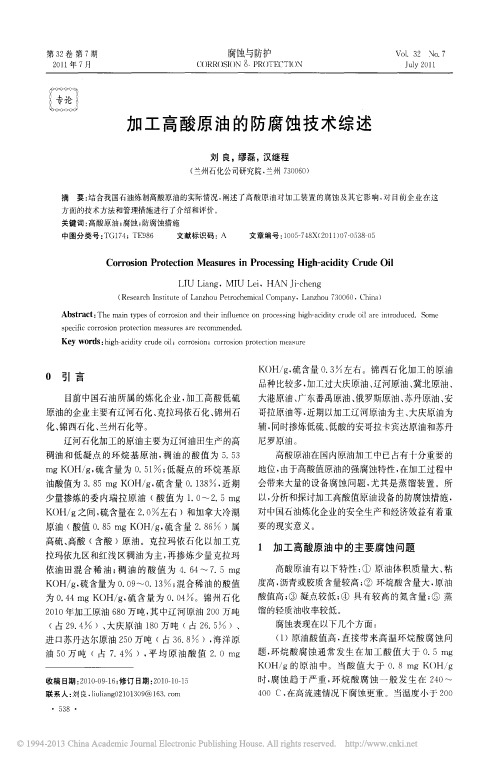
I一 L iang . M IU L ei, H A N Ji eheng IU 一
(R eseareh In stitute o f L anzh ou P etro eh em i eal C o m pan y , L a n ho u 730 060 . C hiz a ) z 飞
A b stra c t :T h e m a i typ es o f eo rro sl and th ei i fl en ee on p ro ees !i g h i - aei i eru de 0 1 aro I trod u eed . S m e n on r n u n gh d ty 1 n o spe eifi eorro si proteeti n m easu res are reeor m end ed. e on o n K ey w o d r s : hi h一 g aeidity eru d e 0 1 eorrOSI n ; CO rros - p ro teC t- m easu re 1; O On On
高酸原油在国内原油加工中已占有十分重要的 地位, 由于高酸值原油的强腐蚀特性, 在加工过程中 会带来大量的设 备腐蚀 问题 , 尤其是蒸馏装 置 "所
少量掺炼的委 内瑞 拉原油 ( 酸值 为 1. " 一2.5 m g
K O H /g 之间, 硫含量在 2.0% 左右 ) 和加拿大冷湖
ห้องสมุดไป่ตู้
以, 分析和探讨加工高酸值原油设备的防腐蚀措施,
为成熟 ,但还是存在一些缺点田 "如克拉玛依石化
公司 2 世纪 9 年代初开发了氨醇脱酸技术 , 并对 0 0 减四线馏分油进行 了脱酸精制工业应用 "当前其工 业运行的基本情况及问题是 :溶剂用量大, 剂油 比达 1.1一1.2, 溶剂回收能耗较高 ,得到的环烷酸产品纯 度较 低 , 酸纯 度在 6 % 一6 % 范 围 " 0 5
- 1、下载文档前请自行甄别文档内容的完整性,平台不提供额外的编辑、内容补充、找答案等附加服务。
- 2、"仅部分预览"的文档,不可在线预览部分如存在完整性等问题,可反馈申请退款(可完整预览的文档不适用该条件!)。
- 3、如文档侵犯您的权益,请联系客服反馈,我们会尽快为您处理(人工客服工作时间:9:00-18:30)。
高酸值原油加工综述高酸值原油加工综述[]高酸值原油加工综述:介绍了原油中石油酸的分布规律、环烷酸腐蚀机理及影响环烷酸腐蚀的因素。
综述了近年来高酸原油的加工方法及国内一些炼油厂炼制高酸值原油情况及防护措施。
重点介绍了茂名分公司炼制高酸值原油的情况,分析了高酸值原油各馏分的酸分布规律,提出了炼制高酸值原油的对策。
随着原油的不断开发利用,重质原油的产量越来越大,其密度、粘度及酸值也随之上升。
近几年来,全球高酸原油的产量每年约增加0.3%。
2001年,酸值(TAN)大于1 mgKOH/g的高酸原油的产量占全球原油总产量的5.0%,到2006年将达到5.5%。
国内含酸原油的品种和数量也呈上升趋势。
由于含酸原油在加工过程中会对生产设备造成较大的腐蚀,因此造成国际和国内市场上高酸原油供过于求,价格偏低。
在原油采购成本占总成本90%的情况下,适当采购低酸值原油对经济效益具有较大的贡献。
因此,如何进行高酸值原油的加工就显得十分重要。
1、原油中石油酸及其分布规律原油酸值的大小反映了原油中环烷酸、脂肪酸以及酚类等酸性氧化物(总称石油酸)的多少。
原油的酸值是1g原油中各种酸性组分所消耗的KOH的总量,以mgKOH/g表示。
原油酸性物质除了环烷酸外,还有脂肪酸、芳香酸、无机酸、硫醇、硫化氢和苯酚等。
当原油酸值大于0.5 mgKOH/g即能引起设备腐蚀,故通常将酸值大于0.5 mgKOH/g的原油称之为高酸值原油。
在原油的酸性物质中,以环烷酸最为重要,含量也高,它约占原油酸性物质的90%。
环烷酸是一种带有五元或六元环的十分复杂的羧酸混合物,相对分子量变化范围很大,但以300~400居多。
低分子量的环烷酸在水中有一定溶解度,而高分子量环烷酸几乎不溶于水。
环烷酸在原油中的分布规律十分特殊,中间馏分(250~500℃)环烷酸含量最高,而在低沸馏分和高沸馏分中环烷酸含量都比较低。
也就是说环烷酸含量一般从煤油馏分开始逐渐增加,至柴油馏分其含量几乎达到最高峰,然后有所下降。
2、加工高酸值原油引起的腐蚀加工高酸值原油的炼厂,设备的腐蚀主要是由环烷酸引起的。
其蒸馏装置的高温部位腐蚀严重,腐蚀主要发生在高温部位的设备和管线,例如常压炉、减压炉的炉出口管弯头,炉出口阀门,转油线高速段和低速段、常压塔和减压塔的进料蒸发段、塔壁、塔盘、主梁、支梁等部位。
环烷酸的腐蚀与硫腐蚀不同,它不是均匀腐蚀,而是局部腐蚀或点蚀,而且环烷酸腐蚀受酸值、温度、流速、介质、物态变化等多方面因素的影响,因此不容易检测。
2.1环烷酸腐蚀机理环烷酸在石油炼制过程中,随原油一起被加热、蒸馏,并与其沸点相同的油品一起冷凝,而且溶于其中,从而造成该馏分对设备材料的腐蚀。
目前,一般认为环烷酸腐蚀的反应机理如下:2RCOOH+Fe→Fe(RCOO)2 +H2现场经验表明:环烷酸腐蚀经常发生在酸值大于0.5 mgKOH/g、温度在270~400℃之间高流速的工艺介质中。
它与金属表面或硫化铁膜直接反应生成环烷酸铁。
环烷酸铁是油溶性的,再加上介质的流动,使金属表面不断暴露并受到腐蚀。
故环烷酸腐蚀的金属表面清洁、光滑无垢。
在物料的高温高流速区域,环烷酸腐蚀呈顺流向产生的尖锐边缘的流线沟槽;在低流速区域,则呈边缘锐利的凹坑状。
环烷酸腐蚀均发生在塔盘、塔壁、转油线等部位。
另外,由于环烷酸盐具有表面活性,会造成原油严重乳化,从而引起装置操作波动,并造成塔顶腐蚀。
2.2影响环烷酸腐蚀的因素2.2.1温度的影响环烷酸的腐蚀受温度影响很大。
环烷酸在常温下对金属没有腐蚀性,但在高温下能和铁生成环烷酸铁,引起强烈的腐蚀。
220℃环烷酸开始腐蚀,并随温度的升高腐蚀加剧。
270~280℃腐蚀已经很严重,以后随温度上升而减弱,但在350~400℃腐蚀急剧增加。
2.2.2流速的影响流速和流态是影响环烷酸腐蚀的非常重要的因素。
在炼油设备的弯头、三通和泵中产生的湍流加速设备的腐蚀。
当气量大于60%,蒸汽流速大于60 m/s的射流,腐蚀最严重。
在这样的条件下,某些设备,如炉管、弯头、管线的腐蚀速度可增大两个数量级。
在高温、高流速的情况下,酸值在很低的水平(0.3 mgKOH/g),对碳钢仍有很高的腐蚀速率。
2.2.3原油硫含量的影响环烷酸与金属的腐蚀反应产物为油溶性的Fe(RCOO)2,它能被油流所带走,因此不易在金属设备表面上形成保护膜,腐蚀产物易从金属表面解离下来,使腐蚀向纵深处发展。
当金属长期与环烷酸接触,原油流速很大时,在金属表面可观察到特有的沟槽状腐蚀。
这是区别环烷酸腐蚀与其它腐蚀的标记。
若原油中含有活性硫化物时,高温下,活性硫化物开始分解,产生硫化氢。
硫化氢与金属的反应为:H2S+Fe→FeS+H2生成的腐蚀产物FeS膜,在一定的条件下具有一定的保护作用。
而在环烷酸中FeS膜被溶解,其反应为:FeS+2RCOOH →Fe(RCOO)2+H2S生成的硫化氢又引起下游设备的腐蚀,如此形成的腐蚀循环,加剧了金属的腐蚀。
3、高酸原油加工的防腐对策3.1、碱中和3.1.1用NaOH或KOH水溶液脱酸碱洗是经典的脱酸工艺。
用氢氧化钠溶液与环烷酸进行中和反应,所得环烷酸钠盐从油品中分离出来,经酸化得到游离的环烷酸。
反应过程可在瞬间完成,但在反应过程中容易产生乳化现象。
大量的研究工作就是基于如何防止处理过程中生成乳化液以及破坏已形成的乳化液来展开的。
研究表明:通过调整操作参数(油与碱液的混合强度、碱液浓度、操作温度、电精制电场强度),或采用非分散性接触技术以及加入添加剂等方法可以部分改善乳化现象。
这种工艺的优点是:投资少,运行成本低,操作简单。
但也存在一些缺点:碱液随同加工产品大量流失,氢氧化钠试剂不能再生,分离环烷酸所生成的硫酸钠污染严重;为防止废物污染所建的焚烧设备和防止二次污染的回收设备,增加了系统的投资;而且如果没有充分脱除油品中的碱液,残存在油品中的少量环烷酸皂对燃料油和润滑油的使用性能将带来不良影响。
3.1.2用氨/醇溶液脱酸用氨水代替苛性碱将石油酸从油相中抽提出来,实质上是将石油酸转化为铵盐,从油品中分离出来;铵盐加热分解释放出氨气同时回收石油酸,氨气可以回收再利用。
醇的加入主要是用于改善乳化现象。
文献表明,采用氨水一甲醇溶液、氨水一乙醇溶液、氨水一异丙醇溶液等氨水一乙醇复合溶剂体系进行脱酸实验,最高脱酸率可达99﹪。
另外,胺类、烷氧基胺或季铵盐类等也可以用作中和剂进行脱酸反应,得到较好的脱酸效果,但成本较高。
氨/醇脱酸可以在较广的范围内选择操作条件,脱酸效果好,环境污染小,但溶剂回收能耗较高,脱酸油色度受到一定的影响。
3.1.3用金属氧化物及有机酸钠(或钾)盐脱酸用氧化钙、磺酸钙或其它金属氧化物,以及小分子有机酸的碱金属盐同样可以脱酸,但是也存在产生大量的碱渣和含盐污水的问题。
随着环保法规的日益健全和严格,污水和碱渣的治理问题越来越严重,碱中和法的劣势也越来越明显。
3.2抽提分离采用选择性溶剂,可从石油馏分中提取环烷酸。
文献指出,甲酰替二甲胺、乙睛、工业三甘醇等作为萃取溶剂都可有效地脱去油中的石油酸。
利用甲酰替二甲胺作为选择性溶剂,采用连续4次抽提,当原油酸值为2.65 mgKOH/g时,酸值依次降低1.82 、0.40 、0.22 和0.08 mgKOH/g;采用工业三甘醇作为选择性溶剂,分离柴油馏分中的环烷酸,当溶剂比1:1.5时,环烷酸的分离度达到99.9%。
除上述溶剂外,还可以采用的其它选择性溶剂,包括双甘醇、聚丙烯乙二醇、二甲基亚砜、N-甲基毗咯烷酮和乙二醇、聚丙二醇醚、三乙二醇醛等。
但是,多数可选择溶剂对油中的芳烃尤其是多环芳烃也具有相当的溶解性,特别是对于重质馏分油,大分子的石油酸与烃类的性质差异缩小,给抽提剂的选择带来较大困难。
因此,寻找选择性好、价廉、沸点较低的溶剂(或混合溶剂)是这种技术能否具有实用性的关键。
3.3加氢法脱除原油中的环烷酸无论是馏分油加氢脱硫、脱氮,还是渣油加氢处理,在加氢过程中都可以有效地除去环烷酸,但由于环烷酸的强腐蚀性,在炼油过程中应尽可能早地将其脱除。
在非常缓和的条件下(反应温度较低,氢压较小)采用传统的加氢催化剂进行加氢脱酸处理,脱酸效果显著。
近年来,又开发出多种油溶性和水溶性的分散型催化剂如环烷酸钼、环烷酸钴、磷钼酸铵等,用于环烷酸的加氢脱酸反应,也取得了较好的脱酸效果。
在油溶性催化剂中二烷基二硫代氨基甲酸钼和二烷基二硫代磷酸钼具有较高的催化活性,而在水溶性催化剂中,钼酸铵、磷钼酸铵和硫代钼酸铵同样具有较高的加氢活性和抑制生焦能力。
加氢法脱除原油中的环烷酸可以说是最彻底的脱酸手段,而且避免了碱渣污染等问题,但是反应需要使用大量氢气,工艺建设投资和操作成本较高[1]。
3.4混炼混炼是防止环烷酸腐蚀有效的而且是低成本的方法,它不需要额外的支出或投资,只需要对计划和运行进行合理安排。
把混合原油酸值进行有目的的调整,做到合理、均衡地安排进入装置的混合原油酸值小于0.5 mgKOH/g时,就可以有效地控制环烷酸腐蚀。
3.5采用高温缓蚀剂技术采用高温缓蚀剂技术也是解决高温环烷酸腐蚀的一种经济、简便有效的途径。
目前国内解决炼油装置高温部位腐蚀的方法主要是更换材质,尤其对于低硫高酸值原油;而国外在重视选材的同时,也常采用注入高温缓蚀剂。
用高温缓蚀剂抑制有机酸(主要是环烷酸)的腐蚀,其用量小,不影响油品质量,不影响后续加工,克服了原油注碱的缺点,可作为更换材质的补充。
高温缓蚀剂技术近几年发展较快,许多加工高酸、高硫原油的炼厂都在积极使用,防腐效果还是比较明显的,但是对一些高温高速部位使用的效果则较差。
3.6全面提高装置设备材质等级3.6.1装置设备材质升级选用耐腐蚀材料是防止环烷酸腐蚀最有效的措施之一。
在没有理想的工艺防腐蚀手段的情况下,提高设备材质的耐蚀等级是减轻环烷酸腐蚀最有效的方法。
提高材质耐蚀等级的实质就是采用加入一定量的合金元素如Cr、Ni、Ti的合金钢,以便形成有一定效果的氧化物保护膜,该氧化物保护膜对金属离子扩散有着强烈的阻滞作用,从而保护金属不受进一步腐蚀。
对于有机酸腐蚀的环境,在设备选材时应充分考虑介质的温度、流速以及是否会出现涡流、湍流和相变等因素,对流速超过30 m/s、出现涡流、湍流和相变的部位应采用更高级别的材质。
据资料介绍,不同材质对环烷酸具有不同的耐蚀性。
具体材料的耐蚀性为:碳钢<低合金钢(铬钼钢:Cr5Mo<Cr9Mo=<1Cr13<18-8不锈钢<含钼奥氏体不锈钢。
所以选用含钼奥氏体不锈钢可有效地控制环烷酸的腐蚀;对于典型的含钼奥氏体不锈钢316和315L,含钼量应高于2.3%,低于此值将降低其耐蚀性[5]。
3.6.2材料表面改性渗铝技术作为材料的表面改性处理方法,可以显著提高金属材料表面的防腐蚀性能。